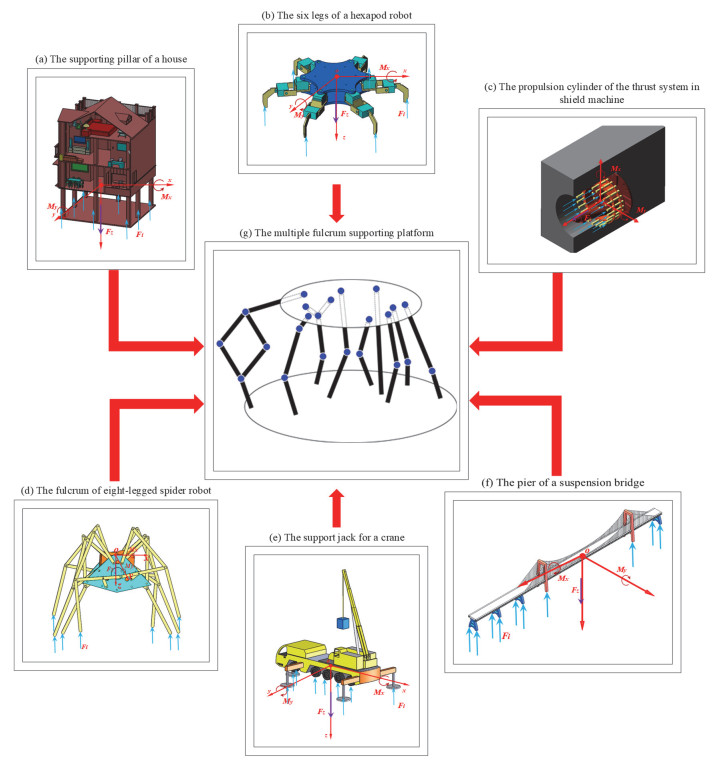
This study aims to investigate the force transmission characteristics of a multiple-fulcrum supporting platform, and the significance of this paper is to creatively put forward the law of uniform force characteristics of multiple-fulcrum supporting platform with heavy loads and layout reconfiguration methods to realize the law. In this paper, firstly, a force transmission model for the multiple-fulcrum supporting platform has been constructed, the relationship between force transmission characteristics and layout parameters for all fulcrums has been discussed in detail, and the layout law for all fulcrums with the same supporting force has been discovered. Then, layout reconfiguration methods have been proposed to realize the uniform force characteristics of all fulcrums under different types of constraint surfaces (rectangular or square constrained surface, circular constrained surface, and unconstrained surface). Finally, layout reconfiguration methods have been applied to some engineering problems by ADAMS simulation. The simulation results show that the supporting force of all fulcrums in the supporting platform is equal when the layout central point (LCP) of all fulcrums is coincident with the force equivalent point (FEP) of external loads. The results provide theoretical guidance and support for the reconfiguration of multiple-fulcrum supporting platforms that can realize uniform forces among all fulcrums.
Citation: Kongshu Deng, Yicheng Ding, Zhurong Yin, Lu Zeng, Hailaing Wu, Dilei Qian. Force transmission characteristics in a multiple-fulcrum supporting platform with heavy loads[J]. Mathematical Biosciences and Engineering, 2020, 17(4): 3329-3355. doi: 10.3934/mbe.2020189
[1] | Li-zhen Du, Shanfu Ke, Zhen Wang, Jing Tao, Lianqing Yu, Hongjun Li . Research on multi-load AGV path planning of weaving workshop based on time priority. Mathematical Biosciences and Engineering, 2019, 16(4): 2277-2292. doi: 10.3934/mbe.2019113 |
[2] | Won Man Park, Young Joon Kim, Shaobai Wang, Yoon Hyuk Kim, Guoan Li . Investigation of lumbar spine biomechanics using global convergence optimization and constant loading path methods. Mathematical Biosciences and Engineering, 2020, 17(4): 2970-2983. doi: 10.3934/mbe.2020168 |
[3] | Yongli Yan, Tiansheng Sun, Teng Ren, Li Ding . Enhanced grip force estimation in robotic surgery: A sparrow search algorithm-optimized backpropagation neural network approach. Mathematical Biosciences and Engineering, 2024, 21(3): 3519-3539. doi: 10.3934/mbe.2024155 |
[4] | Yi Yang, Lirong Liu, Changcheng Xiang, Wenjie Qin . Switching dynamics analysis of forest-pest model describing effects of external periodic disturbance. Mathematical Biosciences and Engineering, 2020, 17(4): 4328-4347. doi: 10.3934/mbe.2020239 |
[5] | S. E. Abd El-Bar, F. A. Abd El-Salam . Photogravitational perturbations in the infinitesimal orbits around the libration points in the oblate RTBP. Mathematical Biosciences and Engineering, 2019, 16(6): 8144-8161. doi: 10.3934/mbe.2019411 |
[6] | Zhicheng Song, Jinbao Chen, Chuanzhi Chen . Application of discrete shape function in absolute nodal coordinate formulation. Mathematical Biosciences and Engineering, 2021, 18(4): 4603-4627. doi: 10.3934/mbe.2021234 |
[7] | Natalia L. Komarova . Spatial stochastic models of cancer: Fitness, migration, invasion. Mathematical Biosciences and Engineering, 2013, 10(3): 761-775. doi: 10.3934/mbe.2013.10.761 |
[8] | A. Endo, H. Nishiura . Age and geographic dependence of Zika virus infection during the outbreak on Yap island, 2007. Mathematical Biosciences and Engineering, 2020, 17(4): 4115-4126. doi: 10.3934/mbe.2020228 |
[9] | Matthias Ngwa, Ephraim Agyingi . A mathematical model of the compression of a spinal disc. Mathematical Biosciences and Engineering, 2011, 8(4): 1061-1083. doi: 10.3934/mbe.2011.8.1061 |
[10] | Yong Yang, Zunxian Li, Chengyi Xia . Forced waves and their asymptotic behaviors in a Lotka-Volterra competition model with spatio-temporal nonlocal effect under climate change. Mathematical Biosciences and Engineering, 2023, 20(8): 13638-13659. doi: 10.3934/mbe.2023608 |
This study aims to investigate the force transmission characteristics of a multiple-fulcrum supporting platform, and the significance of this paper is to creatively put forward the law of uniform force characteristics of multiple-fulcrum supporting platform with heavy loads and layout reconfiguration methods to realize the law. In this paper, firstly, a force transmission model for the multiple-fulcrum supporting platform has been constructed, the relationship between force transmission characteristics and layout parameters for all fulcrums has been discussed in detail, and the layout law for all fulcrums with the same supporting force has been discovered. Then, layout reconfiguration methods have been proposed to realize the uniform force characteristics of all fulcrums under different types of constraint surfaces (rectangular or square constrained surface, circular constrained surface, and unconstrained surface). Finally, layout reconfiguration methods have been applied to some engineering problems by ADAMS simulation. The simulation results show that the supporting force of all fulcrums in the supporting platform is equal when the layout central point (LCP) of all fulcrums is coincident with the force equivalent point (FEP) of external loads. The results provide theoretical guidance and support for the reconfiguration of multiple-fulcrum supporting platforms that can realize uniform forces among all fulcrums.
For the force transmission characteristics of mechanism, Gan studied the force transmission characteristics of a metamorphic parallel mechanism (MPM) with reconfigurable 3T and 3R motions [1,2,3]. Dai proved the relationship between the screw system and its reciprocal system by combining linear algebra and advanced kinematics theory, and obtained some physical properties of the screw system [4,5]. These studies on the force transmission characteristics of the above mechanism analyzed the corresponding relationship between different positions of the actuator in space and the output force from the perspective of dynamics. Given that it is a dynamic question, the corresponding relationship between the spatial position and the output force is dynamic [6], and finding a stable state to establish the relationship between the two is difficult. When the output force of the end-effector is equal, the conditions needed by the spatial position of the actuators to meet with a unified relation are not easy to describe. Therefore, from the perspective of dynamics, the special force transmission relationship between the spatial position of the actuator and the output force (such as the spatial position relationship of the actuator corresponding to the equal output force) is complicated. It provides a new way of thinking for studying some special force transmission relations from the perspective of statics.
In vehicle engineering, the crane adopts the layout of jacks shown in Figure 1e to support the car body and prevent it from rolling over, and the truck often adopts the structure form of the rear eight wheels to provide support and prevent severe deformation of the tire due to excessive load. In shield machine construction, the hydraulic cylinder of the shield propulsion system is designed and optimized with the non-equidistant layout depicted in Figure 1c to reduce the influence caused by partial load effectively and prevent the rupture and collapse of the rear pipe segments caused by excessive partial load [7,8]. In civil engineering, the ground floor is often supported by the distribution of pillars in Figure 1a to increase the carrying capacity of the house. In robot research, the zero moment point is an important indicator to determine the dynamic and stable motion of robots [9,10,11]. The supporting part of the hexapod robot is often in the form of a circular uniform layout as shown in Figure 1b and the fulcrum of eight-legged spider robot is often in the form of layout described in Figure 1d to ensure the stability of the main body [12]. In other fields, suspension bridges are often supported as shown in Figure 1f to allow vehicles to cross the river [13]. The above discussion shows that crane jacks, truck tires, hydraulic cylinders in the shield propulsion system, the support structure of hexapod robot and eight-legged spider robot, pillars of house and the pier of suspension bridge have the same characteristics. That is, the external combined resistance and the supporting forces acting on all fulcrums are parallel and perpendicular to the same surface, and the vertical stiffness of all supporting structures remains the same. As shown in Figure 1g, the structure with the above typical characteristics is the multiple-fulcrum supporting platform, the part acted by the supporting force is the support, the point on which the supporting force acts is the fulcrum, and the distribution plane in which all fulcrums can be reconfigured is the constraint surface.
From the perspective of structural mechanics, when a multiple-fulcrum supporting platform is subjected to external loads, the distribution of forces on all fulcrums not only satisfies the equilibrium condition of Newton's second law [14,15] but also distributes forces in a way that makes the whole system achieve the minimum energy, that is, the Hamiltonian principle [16,17]. Under specific external loads, the force transmission characteristics of the multiple-fulcrum supporting platform will constantly change with the different layout positions of its fulcrums on the constraint surface. If the layout positions of the fulcrums are reconfigured so that the supporting forces provided by these fulcrums are all equal, the force transmission performance of the multiple-fulcrum supporting platform reaches the optimal when the vertical deformation of each support remains consistent, and the energy consumption of all supports achieves the minimum. The characteristics of the above optimal force transmission have the following general functions in practical engineering: ensure that the wear degree of each support is basically consistent, avoid some supports bearing too much to cause rupture, ensure that all supports are in the lowest energy state under the action of the external force, and prevent the supporting platform from turning over. In addition to the above general functions, the characteristics of the optimal force transmission of the multiple-fulcrum supporting platform in specific engineering applications also have special functions. For example, when the hydraulic cylinder of the shield propulsion system is in the optimal force transmission, all the hydraulic cylinders exert the same jacking force on the rear segments, which can effectively avoid the crushing of the rear segments due to excessive partial load [18,19]. Again for example, in one area, the load-bearing wall of a high-rise building was torn down and the whole house collapsed. It is assumed that the load-bearing column of the house can achieve the optimal force transmission performance by adding a certain load-bearing column under the condition that there is no load-bearing wall, and if the load-bearing wall is knocked down unintentionally, the whole house will not collapse due to the support function of the new added load-bearing column [20].
Considering the above-mentioned advantages of optimal force transmission, the present study focuses on how to realize the optimal force transmission of the multiple-fulcrum supporting platform by reconfiguring the position of the fulcrum under specific external loads. Therefore, the optimal force transmission model and force transmission characteristic model of the multiple-fulcrum supporting platform are established. Some layout reconfiguration methods to achieve the optimal force transmission performance of the platform are proposed, and relevant conclusions are drawn by applying these layout reconfiguration methods, which are described in detail in the following sections.
The constraint surface where the fulcrum is located is depicted in Figure 2. The external loads on the supporting platform are Fz, Mx, and My (the external loads acting on the coordinate origin o can be represented as Fz, Mx, and My). By taking the geometric center of the supporting platform as the coordinate origin o, the z-axis is parallel to all supporting forces, the y-axis is vertical to the z-axis and points to the direction depicted in Figure 2, and the direction of the x-axis is decided by the right-hand rule [21] to establish the Cartesian coordinate system o-xyz. As described in Figure 2, My is the external combined resistance moment along the positive direction of the y-axis; Mx is the external combined resistance moment along the positive direction of the x-axis; M is the external combined resistance moment; Fz is the external combined resistance along the positive direction of the z-axis; and Fi (i = 1, 2, 3, ..., N) is the supporting force provided by the ith fulcrum, whose direction is opposite to that of Fz; fi is the friction on the ith fulcrum; The structure has N supports, and the vertical stiffness coefficient of each support is k.
Three static equilibrium equations of (1)–(3) can be obtained according to the force on the multiple-fulcrum supporting platform in Figure 2:
N∑i=1Fi−Fz=0, | (1) |
N∑i=1ρρi×Fi+M=0, | (2) |
N∑i=1fi=0, | (3) |
where ρi is the polar radial vector of the ith fulcrum shown in Figure 2.
According to the principle of minimum energy [22,23], the lower the energy, the more stable the system. Eqs (1)–(3) are used as the basis to construct the optimization function (4) and minimize the energy of all supports. Supports can reach static equilibrium very quickly because the deformation of all supports is small and the damping is large [24,25]. In this process, the kinetic energy of the whole system eventually tends to zero, and the gravitational potential energy decreases while the elastic potential energy increases. Therefore, the establishment of Eq (4) only needs to consider the situation when the elastic potential energy of the system achieves the minimum.
W=N∑i=1[12k⋅(Δli)2], | (4) |
where Δli is the vertical deformation generated by the ith fulcrum, and Δli=Fi/k.
If W in the optimization function (4) achieves the minimum value, then all supports in the multiple-fulcrum supporting platform have the minimum energy, and the system is in the most stable state, which is conducive to saving the overall energy consumption of the system.
Using simultaneous optimization function (4) and static equilibrium Eqs (1)–(3), we can construct the Lagrange function of Eq (5) as follows [26]:
L=W+λ1(N∑i=1Fi−Fz)+λ2(N∑i=1xiFi+My)+λ3(N∑i=1yiFi−Mx), | (5) |
where λ1,λ2,λ3 are the Lagrange parameters; (xi, yi) refers to the coordinate point of force provided by each fulcrum in the o-xy plane.
The partial derivatives of Lagrange equation (5) are calculated to obtain Eqs (6) and (7):
∂L∂Fi=Fik+λ1+λ2xi+λ3yi=0,(i=1,2,...,N), | (6) |
∂L∂λc=0,(c=1,2,3). | (7) |
On the ground of Eqs (6) and (7), the matrix equation can be gained as follows:
[1⋯1000x1⋯xN000y1⋯yN0001⋯01x1y1⋮1⋮⋮⋮⋮0⋯11xNyN][F1⋮FNkλ1kλ2kλ3]=[Fz−MyMx0⋮0]. | (8) |
Assume that matrix D is the inverse matrix of the coefficient matrix of Eq (8), and let it be
D=[d11d12d13⋯d1N+3⋮⋮⋮⋯⋮dN+11dN+12dN+13⋯dN+1N+3dN+21dN+22dN+23⋯dN+2N+3dN+31dN+32dN+33⋯dN+3N+3], |
and
[d11d12d13⋯d1N+3⋮⋮⋮⋯⋮dN+11dN+12dN+13⋯dN+1N+3dN+21dN+22dN+23⋯dN+2N+3dN+31dN+32dN+33⋯dN+3N+3][Fz−MyMx0⋮0]=[F1⋮FNkλ1kλ2kλ3]. | (9) |
Solving Eq (9) obtains the following Lagrange parameters λ2 and λ3:
kλ2=dN+21Fz−dN+22My+dN+23Mx, | (10) |
kλ3=dN+31Fz−dN+32My+dN+33Mx. | (11) |
Considering the relationship between matrix D and its own invertible matrix [27], we can acquire,
[d11d12d13⋯d1N+3⋮⋮⋮⋯⋮dN+11dN+12dN+13⋯dN+1N+3dN+21dN+22dN+23⋯dN+2N+3dN+31dN+32dN+33⋯dN+3N+3][1⋯1000x1⋯xN000y1⋯yN0001⋯01x1y1⋮1⋮⋮⋮⋮0⋯11xNyN]=[10⋯000⋱⋮1⋮⋱0⋱00⋯01]. | (12) |
From Eq (12), the following equations can be deduced:
{N∑i=4dN+2i=0N∑i=4dN+3i=0, | (13) |
NdN+21+dN+22N∑i=1xi+dN+23N∑i=1yi+N∑i=4dN+2i=0, | (14) |
NdN+31+dN+32N∑i=1xi+dN+33N∑i=1yi+N∑i=4dN+3i=0. | (15) |
Substituting Eq (13) into Eqs (14) and (15) obtains the following two equations:
dN+21+dN+22⋅1NN∑i=1xi+dN+23⋅1NN∑i=1yi=0, | (16) |
dN+31+dN+32⋅1NN∑i=1xi+dN+33⋅1NN∑i=1yi=0. | (17) |
In a uniform force system, when the supporting force is equal to each other, the following equation must be built:
F1=F2=⋯=Fi=⋯=FN=Fz/N. | (18) |
Substituting Eq (18) into Eq (7) obtains
{MxFz=1NN∑i=1yiMyFz=−1NN∑i=1xi. | (19) |
The above derivation process manifests that Eq (19) must be true when the supporting forces provided by fulcrums are all equal. On the premise of the principle of minimum energy, if Eq (19) is true, then the supporting forces provided by all fulcrums must be equal.
Substituting Eq (19) into Eqs (16) and (17) achieves
dN+21−dN+22MyFz+dN+23MxFz=0, | (20) |
dN+31−dN+32MyFz+dN+33MxFz=0. | (21) |
Substituting Eqs (20) and (21) into Eqs (10) and (11) results in the following equation:
λ2=λ3=0. | (22) |
On the ground of Eq (8), the following equation can be deduced:
(Nλ1+λ2N∑i=1xi+λ3N∑i=1yi)=−Fzk. | (23) |
Substituting Eq (22) into Eq (23) acquires
λ1=−Fz/Nk. | (24) |
Substituting Eqs (22) and (24) into Eq (6) establishes Eq (18), that is, the supporting force provided by each fulcrum is equal.
The force translation theorem of statics [28,29] states that an additional torque is generated when a force transfers from one point to another in space. As depicted in Figure 2, a point o′ with a coordinate of (xo′,yo′) exists in the o-xy plane of the constructed Cartesian coordinate system o-xyz, so that the effect of external loads Fz, Mx, and My can be replaced by the external combined resistance Fz acting on this point called the force equivalent point (FEP). At this moment,
xo′=My/Fz, | (25) |
yo′=−Mx/Fz. | (26) |
Transforming Eq (19) obtains
¯x=My/Fz, | (27) |
¯y=−Mx/Fz, | (28) |
where ¯x=N∑i=1xi/N,¯y=N∑i=1yi/N, the point represented by the coordinate (¯x,¯y) is called the layout central point (LCP).
As demonstrated in Eqs (19), (25), and (26), when the FEP coincides with the LCP, namely xo′=¯x,yo′=¯y, the supporting forces provided by all fulcrums are equal, which prevents some supports from collapsing under excessive pressure and saves energy. In this study, the finding that all the supporting forces provided by the fulcrums are equal when the FEP coincides with the LCP is named as the law of uniform force characteristics of the multiple-fulcrum supporting platform.
In the Section 2.1, the optimal force transmission of the multiple-fulcrum supporting platform has been discussed. In the following part, the force transmission characteristics of the platform for constraint surfaces with three common shapes are discussed.
As shown in Figure 2, the distribution of the fulcrum (xi, yi, zα) on the constraint surfaceα: z = zα satisfies the following equation:
{|x|=p , (−q < y < q)|y| = q, (−p < x < p), | (29) |
where p and q respectively represent the length and width of the rectangle. When p is equal to q, they represent the side length of the square.
If the spatial distribution of the supporting force provided by each fulcrum can be solved, then the Cartesian coordinate system shown in Figure 3 needs to be established with variables Fi, x, and y as axes. Combining the plane Eq (6) and the rectangular cylindrical Eq (29) shows that the solution of Fi must be on the intersection line of the two space surfaces, and the spatial parallelogram plane formed by the intersection line is called the force distribution plane (FDP). The specific expression is as follows:
{Fik+λ1+λ2p+λ3yi=0 , (−q<yi<q)Fik+λ1−λ2p+λ3yi=0 , (−q<yi<q)Fik+λ1+λ2xi+λ3q=0 , (−p<xi<p)Fik+λ1+λ2xi−λ3q=0 , (−p<xi<p), | (30) |
where λc=(dN+i1Fz−dN+i2My+dN+i3Mx)/k,(c=1,2,3).
As shown in Figure 3, the maximum and minimum values of the supporting force must appear at the two diagonal vertices of the spatial parallelogram, and the coordinate of the central symmetric point about the force distribution plane of spatial parallelogram is (0,0,−kλ1). The geometric characteristics of the spatial force parallelogram can be completely determined by the above description. Under the condition of the external loads and the layout position of each fulcrum given, the supporting force provided by each fulcrum can be calculated by Eq (30).
The distribution of the fulcrum (xi, yi, zα) on the constraint surfaceα: z = zα satisfies the following equation:
x2i+y2i=r2. | (31) |
where r is the radius of the circle.
In the same way, the Cartesian coordinate system shown in Figure 4 is established with variables Fi, x, and y as axes. Combining the plane Eq (6) and cylinder Eq (31) shows that the solution of Fi must be on the intersection line of the two space surfaces.
On the basis of the analysis, the maximum and minimum values of the supporting force in this case are as follows:
Fmax=−kλ1+kr√λ22+λ23, | (32) |
Fmin=−kλ1−kr√λ22+λ23. | (33) |
On the basis of Eqs (32) and (33), three parameters of the spatial ellipse force distribution plane can be obtained as follows:
a=r√[(kλ2)2+(kλ3)2]+1, | (34) |
b=r, | (35) |
Fmax=−kλ1+kr√λ22+λ23, | (36) |
where a, b, and e are the long semi-axis, short semi-axis, and eccentricity of the spatial ellipse force distribution plane, respectively.
Transforming Eq (36) obtains
λ22+λ23=1k2e21−e2. | (37) |
Substituting Eqs (10) and (11) into Eq (37) achieves
(dN+21Fz−dN+22My+dN+23Mx)2+(dN+31Fz−dN+32My+dN+33Mx)2=e21−e2. | (38) |
Eq (38) indicates that in the Cartesian coordinate system with variables Fz, Mx, and My as the axes, an ellipse can be formed according to Eq (38) in the plane o-MxMy when the external resistance Fz and eccentricity e are given.
For different types of constrained surface, reconfiguration methods of the uniform force characteristics of the multiple-fulcrum supporting platform are different. Reconfiguration difficulty and energy consumption can be greatly reduced to achieve force uniformity effectively by reconfiguring as few layout positions of the fulcrums as possible and shortening the adjustment range of the fulcrum. The specific implementation method is described below.
Suppose the geometric center of the rectangular constraint surface is at the origin of the o-xy plane. The four vertices of the rectangular constraint surface are C, D, E, and F as shown in Figure 5. The expression of line lCD is y = q (q > 0), and the expression of line lDE is x = p (p > 0). Similarly, the expression of line lEF is y = −q, and the expression of line lCF is x = −p. If the direction of the external combined resistance moment M is depicted in Figure 5, then the straight line obtained by clockwise rotating π/2 along the direction of M is called the layout reconfiguration axis, and the angle between the positive direction of the x-axis and the layout reconfiguration axis is φ. Before adjustment, each fulcrum is in uniform distribution, and the following equation must be acquired:
{N∑i=1xi=0N∑i=1yi=0. | (39) |
In Figure 5 (a)–(d), when, the coordinate positions (xjs,√2q⋅cos[π/4+(s−1)⋅π/2]) and (√2p⋅sin[π/4+(s−1)⋅π/2],yks) of the two fulcrums are selected for adjustment, while the positions of other fulcrums remain unchanged. As depicted in Eqs (19) and (39), when the following equation is satisfied, the supporting force provided by each fulcrum is equal.
{x′js−xjs=−NMy/Fzy′ks−yks=NMx/Fz, | (40) |
where (x′js,√2q⋅cos[π/4+(s−1)⋅π/2]) and (√2p⋅sin[π/4+(s−1)⋅π/2],y′ks) are the adjusted coordinates of the two corresponding fulcrums (xjs,√2q⋅cos[π/4+(s−1)⋅π/2]) and (√2p⋅sin[π/4+(s−1)⋅π/2],yks), respectively.
When all fulcrums of the multiple-fulcrum supporting platform are uniformly distributed under the circular constraint surface, the layout phase angle of each fulcrum shown in Figure 6 satisfies the following equation:
N∑t=1rcosθt=0, | (41) |
N∑t=1rsinθt=0, | (42) |
where θt refers to the angle between the radius r of the circular constraint surface and the positive direction of the x-axis.
Transformation of Eqs (41) and (42) obtains
N∑t=1t≠m,nrcosθt+rcosθm+rcosθn=0, | (43) |
N∑t=1t≠m,nrsinθt+rsinθm+rsinθn=0, | (44) |
where θt (t = 1, 2, …, N and t ≠ m, n), θm and θn are the layout phase angles when all fulcrums are uniformly distributed.
When the multiple-fulcrum supporting platform is subjected to external loads shown in Figure 6, the positions of θm and θn are adjusted to θm' and θn', respectively, where θm and θn are the layout phase angles of adjacent fulcrums on both sides of the layout reconfiguration axis obtained by clockwise rotating 90° along the external combined resistance moment M shown in Figure 6, and the positions of other fulcrums are unchanged. The following equations can be established by combining Eqs (43) and (44). At this time, all the supporting forces provided by all fulcrums are equal.
cosθ′m−cosθm+cosθ′n−cosθn=−NMyrFz, | (45) |
sinθ′m−sinθm+sinθ′n−sinθn=NMxrFz. | (46) |
As shown in Figure 7, suppose N fulcrums are present in the multiple fulcrum supporting platform, among which the position of N-n fulcrums remains original, and the position of the jth (j = u, u+1, …, u+n-1) fulcrum changes from the original coordinate (xj,yj) to (x′j,y′j), so that the adjusted LCP of the structure coincides with the FEP. The specific elaboration is as follows:
After adjustment, the following formula can be established:
{N∑i=1xi+u+n−1∑j=ux′j=−NMy/Fz(i≠u,u+1,…,u+n−1)N∑i=1yi+u+n−1∑j=uy′j=NMx/Fz(i≠u,u+1,…,u+n−1). | (47) |
Through adjusting the position of some fulcrums, the supporting force provided by each fulcrum can be equal. This method does not increase the number of fulcrums in the structure. Thus, it is called "displacement reconfiguration method."
On the basis of the relationship between the number of equations and the unknowns, Eq (19) can solve two unknowns. Thus, the following formula can be established:
{N∑i=1i≠uxi+x′u=−NMy/FzN∑i=1i≠uyi+y′u=NMx/Fz. | (48) |
Eq (48) indicates that the supporting force provided by each fulcrum can also be equal by adjusting only the position of a certain fulcrum (xu,yu) to (x′u,y′u).
As shown in Figure 8, the original N fulcrums of the multiple-fulcrum supporting platform are assumed to remain unchanged. When fulcrums are added and reach the coordinate position (xv,yv) (v = N+1, N+2, …, N+n), the LCP of the structure only coincides with the FEP. The specific elaboration is as follows:
After adjustment, the following formula can be established:
{N∑i=1xi+N+n∑v=N+1xv=−(N+n)My/FzN∑i=1yi+N+n∑v=N+1yv=(N+n)Mx/Fz. | (49) |
In this method, the supporting force of each fulcrum is equal by adding some fulcrums and then adjusting the positions of the fulcrums. This reconfiguration method needs to adjust the position of the newly added fulcrums. Thus, it is called "reconfiguration method combined by number and displacement."
On the bases of the relationship between the number of equations and the unknowns, Eq (19) can solve two unknowns. Thus, the following formula can be established:
{N∑i=1xi+xv=−(N+1)My/FzN∑i=1yi+yv=(N+1)Mx/Fz. | (50) |
Eq (50) reveals that the supporting force provided by each fulcrum can also be equal by adding a fulcrum (xv,yv) and then adjusting the position of the fulcrum.
In section 2.3, layout reconfiguration methods are proposed for different types of constraint surfaces. However, in the engineering application, the above layout reconfiguration methods should be combined with the actual engineering background of the multiple-fulcrum supporting platform. The following is an illustration about the application of the layout reconfiguration methods to realize the uniform force characteristics of the multiple-fulcrum supporting platform.
The cartesian coordinate system o-xyz shown in Figure 9 is established. The acceleration of the truck in the y-axis direction is assumed to be zero, that is, the force on the y-axis is in static equilibrium, and the goods loaded by the truck are uniformly distributed in the tail-box, that is, the deviation of the barycenter of the whole truck on the x-axis is zero, and all tires of the truck have the same vertical stiffness. The tires cannot be moved in the direction of the x-axis because of the limitation of the truck structure. Therefore, the same supporting forces of all tires can be achieved by adjusting the tires along the z-axis in accordance with the engineering practice and the relevant theories in section 2.1. The four front wheels of the eight back wheels are regarded as an adjustable unit, known as group A adjustable support unit, and the four rear wheels of the eight back wheels are also regarded as an adjustable unit, known as group B adjustable support unit. With SolidWorks, the barycenter coordinate of the truck is (0 m, –0.418 m, –2.119 m) when the goods are not loaded and (0 m, 0.098 m, –3.254 m) when the goods are loaded. The barycenter is shifted backward, such that the group A adjustable support unit is moved along the negative direction of the z-axis, while the position of the group B adjustable support unit is unchanged. The supporting force of each tire is equal when Eq (19) is met. The original and adjusted positions of each tire in the z-axis direction are shown in Table 1.
State | Position of each tire in the o-zx plane (m) | ||||
Front wheel | A1 | A2 | B1 | B2 | |
Original position | (0.8, –0.798)(0.8, 0.798) | (–1.54, –0.798)(–1.54, 0.798) | (–2.46, –0.798)(–2.46, 0.798) | (–5.54, –0.798)(–5.54, 0.798) | (–6.46, –0.798)(–6.46, 0.798) |
Adjusted position | (0.8, –0.798)(0.8, 0.798) | (–2.075, –0.798)(–2.075, 0.798) | (–2.995, –0.798)(–2.995, 0.798) | (–5.54, –0.798)(–5.54, 0.798) | (–6.46, –0.798)(–6.46, 0.798) |
The original and adjusted truck models (Figure 10) are imported from SolidWorks into ADAMS for simulation [30,31], and the experimental results of simulation are shown in Figures 11 and 12. In the established Cartesian coordinate system o-zxFi, the original and adjusted spatial FDPs composed of the position of each tire in the o-zx plane and supporting force of the each tire as coordinate points are shown in Figures 13 and 14. As shown in Figures 13 and 14, the supporting force of the truck tires is distributed in a parallelogram in space before the adjustment, whereas the supporting force of the truck tires is distributed in a rectangular parallel to the o-zx plane in space after the adjustment.
Given the forces on the crane (Figure 15), the external loads Fz, Mx, and My acting on the crane are assumed to be 300, −30, and 30 KN·m, respectively, and the jacks and the tires of the crane have the same vertical stiffness. The adjusted layout position of the jacks and tires can be obtained using the displacement reconfiguration method in section 2.3.3, which is listed in Table 2 together with the original position. The number of corresponding jacks and tires in Table 2 is shown in Figure 15. The adjusted layout position of jacks and tires can also be obtained according to the reconfiguration method combined by number and displacement in section 2.3.3, which is listed in Table 3 together with the original position.
Num(i) | Layout position (m)(xi, yi) | Num(i) | Layout positon (m)(xi, yi) | ||
Original | Adjusted | Original | Adjusted | ||
H1 | (–4.982, 0) | (–4.982, 0) | T4 | (–2, –1) | (–2, –1) |
H2 | (–2.348, 3.350) | (–2.348, 3.350) | T5 | (0, 1) | (0, 1) |
H3 | (–2.348, –3.350) | (–2.348, –3.350) | T6 | (0, –1) | (0, –1) |
H4 | (5.202, 3.350) | (5.202, 3.350) | T7 | (2, 1) | (2, 1) |
H5 | (5.202, –3.350) | (5.976, –1.850) | T8 | (2, –1) | (2, –1) |
T1 | (–4, 1) | (–4, 1) | T9 | (4, 1) | (4, 1) |
T2 | (–4, –1) | (–4, –1) | T10 | (4, –1) | (4, –1) |
T3 | (–2, 1) | (–2, 1) |
Num(i) | Layout position (m)(xi, yi) | Num(i) | Layout positon (m)(xi, yi) | ||
Original | Adjusted | Original | Adjusted | ||
H1 | (–4.982, 0) | (–4.982, 0) | T3 | (–2, 1) | (–2, 1) |
H2 | (–2.348, 3.350) | (–2.348, 3.350) | T4 | (–2, –1) | (–2, –1) |
H3 | (–2.348, –3.350) | (–2.348, –3.350) | T5 | (0, 1) | (0, 1) |
H4 | (5.202, 3.350) | (5.202, 3.350) | T6 | (0, –1) | (0, –1) |
H5 | (5.202, –3.350) | (5.202, –3.350) | T7 | (2, 1) | (2, 1) |
H6 | – | (0.874, 1.600) | T8 | (2, –1) | (2, –1) |
T1 | (–4, 1) | (–4, 1) | T9 | (4, 1) | (4, 1) |
T2 | (–4, –1) | (–4, –1) | T10 | (4, –1) | (4, –1) |
As shown in Figures 16–18, the original and adjusted virtual prototype models of the crane established in SolidWorks are imported into ADAMS for simulation, and the specific simulation results of the original and adjusted supporting forces of five jacks and ten tires are obtained (Figures 19–21, respectively). Simulation results show that all jacks and tires do not have the same supporting force before the layout adjustment but obtain the same supporting force of 20 or 18.75 KN after the later adjustment.
The forces on the eight-legged spider robot are shown in Figure 22. The external loads Fz, Mx, and My acting on the eight-legged spider robot are assumed to be 100, 50, and 20 KN·m, respectively. The adjusted layout position of the fulcrum can be obtained using the displacement reconfiguration method in section 2.3.3. The results together with the original position are listed in Table 4. The number of corresponding fulcrums in Table 4 is shown in Figure 22. As listed in Table 4, selecting the position of the fourth fulcrum for adjustment not only achieves the uniform force characteristics of the structure but also avoids mutual interference of the supporting structure during adjustment. If the position of the fifth fulcrum is selected for adjustment, the coordinate of the adjusted position is (3.6, –1) according to the calculation of Eq (19), and interference occurs between this position and the position of the seventh fulcrum (4, –1). Selecting the position of one fulcrum for adjustment in practical engineering is theoretically feasible, but the interference effect of the supporting structure size and spatial position on the adjustment should also be considered.
Num(i) | Layout position of the fulcrum (m)(xi, yi) | Num(i) | Layout position of the fulcrum (m)(xi, yi) | ||
Original | Adjusted | Original | Adjusted | ||
S1 | (–4, –3) | (–4, –3) | S5 | (1, 1) | (1, 1) |
S2 | (–5, 2) | (–5, 2) | S6 | (5, 3) | (5, 3) |
S3 | (–3, 3) | (–3, 3) | S7 | (4, –1) | (4, –1) |
S4 | (–1, –3) | (1.6, –5) | S8 | (2, –4) | (2, –4) |
The original and adjusted virtual prototype models of the crane established in SolidWorks are imported into ADAMS for simulation, and the specific simulation results of the original and adjusted supporting forces provided by eight fulcrums are obtained (Figures 23 and 24, respectively). Simulation results show that all fulcrums do not have the same supporting force before the layout adjustment but obtain the same supporting force of 12.5 KN after the adjustment.
A model of the optimal force transmission of the multiple-fulcrum supporting platform and a model of the force transmission characteristics of the multiple-fulcrum supporting platform with rectangular and circular constrained surfaces are established, and the relationship between the two is demonstrated. Based on the above two models, layout reconfiguration methods for the uniform force characteristics of fulcrums under rectangular and circular constrained surfaces and unconstrained surfaces are proposed. Then, the application of these layout reconfiguration methods in practical engineering is discussed in detail. After studying the force transmission of the multiple-fulcrum supporting platform in the above aspects, the following conclusions can be drawn:
(1) In a multiple fulcrum supporting platform, no matter what the structural form of the support, as long as the stiffness of all supports in the vertical direction is equal, and when the LCP coincides with the FEP by adjusting the position of the fulcrum, the supporting force of all fulcrums in the multiple-fulcrum supporting platform becomes equal.
(2) The FDPs of the multiple-fulcrum supporting platform with rectangular and circular constrained surfaces are parallelograms and ellipses, respectively. If and only if the LCP coincides with the FEP, the FDPs of the multiple-fulcrum supporting platform with rectangular and circular constraint surfaces become rectangular and circular, respectively.
(3) For the multiple-fulcrum supporting platform with rectangular and circular constrained surfaces, only the position of the two fulcrums needs to be adjusted to achieve the uniform force characteristics of the fulcrum. For the multiple-fulcrum supporting platform with unconstrained surfaces, only the position of one fulcrum needs to be adjusted to achieve the uniform force characteristics of the fulcrum.
(4) With the layout reconfiguration methods, the uniform force characteristics of the fulcrum can be efficiently and quickly realized by selecting the fulcrum near the layout reconfiguration axis obtained by clockwise rotating 90° along the direction of external combined resistance moment M for layout adjustment.
This research is supported by the Key Laboratory of Road Construction Technology and Equipment (Chang'an University; No. 300102259509), Hunan Province Education Department Key Research Project (No. 18A181) and Hunan Provincial Natural Science Foundation China (No. 2018JJ2122). All authors thank the anonymous reviewers for constructive comments that helped improve this manuscript.
There is no conflict of interest for all the authors in this article.
[1] |
D. M. Gan, J. S. Dai, L. D. Seneviratne, Variable motion/force transmissibility of a metamorphic parallel mechanism with reconfigurable 3T and 3R motion, J. Mech. Rob., 8 (2016), 051001. doi: 10.1115/1.4032409
![]() |
[2] |
D. M. Gan, J. S. Dai, Q. Z. Liao, Mobility change in two types of metamorphic parallel mechanisms, J. Mech. Rob., 1 (2009), 041007. doi: 10.1115/1.3211023
![]() |
[3] |
D. Gan, J. S. Dai, J. Dias, L. Seneviratne, Joint force decomposition and variation in unified inverse dynamics analysis of a metamorphic parallel mechanism, Meccanica, 51 (2016), 1583-1593. doi: 10.1007/s11012-015-0216-y
![]() |
[4] |
J. S. Dai, Z. Huang, H. Lipkin, Mobility of overconstrained parallel mechanisms, J. Mech. Des., 128 (2006), 220-229. doi: 10.1115/1.1901708
![]() |
[5] | E. Rodriguez-Leal, J. S Dai, G. R. Pennock, Screw-system-based mobility analysis of a family of fully translational parallel manipulators, Math. Probl. Eng., 2013 (2013). |
[6] |
Q. A. John, M. L. Joyner, S. Edith, H. Nathaniel, L. Michael, T. C. Jones, An aggregate stochastic model incorporating individual dynamics for predation movements of anelosimus studiosus, Math. Biosci. Eng., 12 (2015), 585-607. doi: 10.3934/mbe.2015.12.585
![]() |
[7] |
K. S. Deng, X. Q. Tan, L. P Wang, X. Chen, Force transmission characteristics for the non-equidistant arrangement thrust systems of shield tunneling machines, Autom. Constr., 20 (2011), 588-595. doi: 10.1016/j.autcon.2010.11.025
![]() |
[8] |
K. Z. Zhang, H. D. Yu, Z. P. Liu, X. M. Lai, Dynamic characteristic analysis of TBM tunnelling in mixed-face conditions, Simul. Model Pract. Theory, 18 (2010), 1019-1031. doi: 10.1016/j.simpat.2010.03.005
![]() |
[9] |
S. Kim, K. Hirota, T. Nozaki, T. Murakami, Human motion analysis and its application to walking stabilization with Cog and ZMP, IEEE Trans. Ind. Inf., 14 (2018), 5178-5186. doi: 10.1109/TII.2018.2830341
![]() |
[10] | Z. Yu, Q. Zhou, X. Chen, Q. Li, L. Meng, W. Zhang, et al., Disturbance rejection for biped walking using zero-moment point variation based on body acceleration, IEEE Trans. Ind. Inf., 15 (2018), 2265-2276. |
[11] |
J. Or, A hybrid cpg-zmp controller for the real-time balance of a simulated flexible spine humanoid robot, IEEE Trans. Syst. Man Cybern., 39 (2009), 547-561. doi: 10.1109/TSMCC.2009.2020993
![]() |
[12] | D. A. Messuri, Optimization of the locomotion of a legged vehicle with respect to maneuverability, The Ohio State University, (1985). |
[13] |
Z. W. Zhu, M. Gu, Z. Q. Chen, Wind tunnel and CFD study on identification of flutter derivatives of a long-span self-anchored suspension bridge, Comput. Aided Civ. Inf. Eng., 22 (2007), 541-554. doi: 10.1111/j.1467-8667.2007.00509.x
![]() |
[14] |
R. Q. Wu, W. Zhang, M. H. Yao, Nonlinear dynamics near resonances of a rotor-active magnetic bearings system with 16-pole legs and time varying stiffness, Mech. Syst. Signal. Process., 100 (2018), 113-134. doi: 10.1016/j.ymssp.2017.07.033
![]() |
[15] |
A. Agudo, F. Moreno-Noguer, Combining local-physical and global-statistical models for sequential deformable shape from motion, Int. J. Comput. Vision, 122 (2017), 371-387. doi: 10.1007/s11263-016-0972-8
![]() |
[16] | J. T. Adams, Hamiltonian principles, Simon Publications, (2001). |
[17] | H. W. Zhang, W. X. Zhong, Y. P. Li, Stress singularity analysis at crack tip on bi-material interfaces based on hamiltonian principle, Acta. Mech. Solida Sin., 2 (1996), 124-138. |
[18] | K. S. Deng, B. L. Meng, C. Xiang, Adaptability to stratum characteristics for layout of thrust system in tunneling machines based on variation coefficient, Adv. Mech. Eng., 8 (2016), 1-9. |
[19] |
K. S. Deng, C. Xiang, B. L. Meng, H. G. Wang, A force transmission assessment method for thrust system in shield machines based on the relative coefficient in compound ground, Autom. Constr., 83 (2017), 354-359. doi: 10.1016/j.autcon.2017.07.002
![]() |
[20] | B. Cai, A three-story building bollapsed on xixia road in sheshan town, Min Dong Daily, 2016. Available from: http://115.236.76.50/mdrb_ty/html/2016-04/12/content_3_3.htm. |
[21] |
N. L. Nguyen, D. E. Meltzer, Visualization tool for 3-D relationships and the right-hand rule, Phys. Teach., 43 (2005), 155-157. doi: 10.1119/1.1869425
![]() |
[22] | X. Liang, On the crack evolution and failure form of concrete specimens based on minimum energy principle, Multimedia Tools Appl., 2019 (2019), 1-10. |
[23] | A. A. Tsonis, The principle of minimum energy consumption, in Randomnicity: Rules and Randomness in the Realm of the Infinite, World Scientific, 2008. |
[24] |
V. Cavina, A. Mari, V. Giovannetti, Slow dynamics and thermodynamics of open quantum systems, Phys. Rev. Lett., 119 (2017), 050601. doi: 10.1103/PhysRevLett.119.050601
![]() |
[25] | C. S. Li, Y. Zhang, Analysis on teaching of quasi-static process and related physics concepts, Phys. Bull., 3 (2016), 22-24. |
[26] |
Y. Wang, J. Wang, H. Lischka, Lagrange function method for energy optimization directly in the space of natural orbitals, Int. J. Quantum Chem., 117 (2017), e25376. doi: 10.1002/qua.25376
![]() |
[27] | Z. Dostál, Linear algebra, in Optimal Quadratic Programming Algorithms, Springer Science & Business Media, 2009. |
[28] | H. C. Xu, Vibration response of flexible spur ring gear with elastic foundation under internal excitation, J. Mech. Eng., 54 (2018), 161. |
[29] | X. M. Zhang, L. B. Zhu, A. W. Wang, S. H. Yang, M. Y. Hu, Superficial discussion on new framework of static equilibrium, Appl. Mech. Mater., 670 (2014), 691-695. |
[30] | Q. F. Cui, A dynamic simulation design of a ladder fire truck based on ADAMS, Appl. Mech. Mater., 670 (2014), 843-846. |
[31] |
K. Man, A. Damasio, Homeostasis and soft robotics in the design of feeling machines, Nature Mach. Intel., 1 (2019), 446-452. doi: 10.1038/s42256-019-0103-7
![]() |
State | Position of each tire in the o-zx plane (m) | ||||
Front wheel | A1 | A2 | B1 | B2 | |
Original position | (0.8, –0.798)(0.8, 0.798) | (–1.54, –0.798)(–1.54, 0.798) | (–2.46, –0.798)(–2.46, 0.798) | (–5.54, –0.798)(–5.54, 0.798) | (–6.46, –0.798)(–6.46, 0.798) |
Adjusted position | (0.8, –0.798)(0.8, 0.798) | (–2.075, –0.798)(–2.075, 0.798) | (–2.995, –0.798)(–2.995, 0.798) | (–5.54, –0.798)(–5.54, 0.798) | (–6.46, –0.798)(–6.46, 0.798) |
Num(i) | Layout position (m)(xi, yi) | Num(i) | Layout positon (m)(xi, yi) | ||
Original | Adjusted | Original | Adjusted | ||
H1 | (–4.982, 0) | (–4.982, 0) | T4 | (–2, –1) | (–2, –1) |
H2 | (–2.348, 3.350) | (–2.348, 3.350) | T5 | (0, 1) | (0, 1) |
H3 | (–2.348, –3.350) | (–2.348, –3.350) | T6 | (0, –1) | (0, –1) |
H4 | (5.202, 3.350) | (5.202, 3.350) | T7 | (2, 1) | (2, 1) |
H5 | (5.202, –3.350) | (5.976, –1.850) | T8 | (2, –1) | (2, –1) |
T1 | (–4, 1) | (–4, 1) | T9 | (4, 1) | (4, 1) |
T2 | (–4, –1) | (–4, –1) | T10 | (4, –1) | (4, –1) |
T3 | (–2, 1) | (–2, 1) |
Num(i) | Layout position (m)(xi, yi) | Num(i) | Layout positon (m)(xi, yi) | ||
Original | Adjusted | Original | Adjusted | ||
H1 | (–4.982, 0) | (–4.982, 0) | T3 | (–2, 1) | (–2, 1) |
H2 | (–2.348, 3.350) | (–2.348, 3.350) | T4 | (–2, –1) | (–2, –1) |
H3 | (–2.348, –3.350) | (–2.348, –3.350) | T5 | (0, 1) | (0, 1) |
H4 | (5.202, 3.350) | (5.202, 3.350) | T6 | (0, –1) | (0, –1) |
H5 | (5.202, –3.350) | (5.202, –3.350) | T7 | (2, 1) | (2, 1) |
H6 | – | (0.874, 1.600) | T8 | (2, –1) | (2, –1) |
T1 | (–4, 1) | (–4, 1) | T9 | (4, 1) | (4, 1) |
T2 | (–4, –1) | (–4, –1) | T10 | (4, –1) | (4, –1) |
Num(i) | Layout position of the fulcrum (m)(xi, yi) | Num(i) | Layout position of the fulcrum (m)(xi, yi) | ||
Original | Adjusted | Original | Adjusted | ||
S1 | (–4, –3) | (–4, –3) | S5 | (1, 1) | (1, 1) |
S2 | (–5, 2) | (–5, 2) | S6 | (5, 3) | (5, 3) |
S3 | (–3, 3) | (–3, 3) | S7 | (4, –1) | (4, –1) |
S4 | (–1, –3) | (1.6, –5) | S8 | (2, –4) | (2, –4) |
State | Position of each tire in the o-zx plane (m) | ||||
Front wheel | A1 | A2 | B1 | B2 | |
Original position | (0.8, –0.798)(0.8, 0.798) | (–1.54, –0.798)(–1.54, 0.798) | (–2.46, –0.798)(–2.46, 0.798) | (–5.54, –0.798)(–5.54, 0.798) | (–6.46, –0.798)(–6.46, 0.798) |
Adjusted position | (0.8, –0.798)(0.8, 0.798) | (–2.075, –0.798)(–2.075, 0.798) | (–2.995, –0.798)(–2.995, 0.798) | (–5.54, –0.798)(–5.54, 0.798) | (–6.46, –0.798)(–6.46, 0.798) |
Num(i) | Layout position (m)(xi, yi) | Num(i) | Layout positon (m)(xi, yi) | ||
Original | Adjusted | Original | Adjusted | ||
H1 | (–4.982, 0) | (–4.982, 0) | T4 | (–2, –1) | (–2, –1) |
H2 | (–2.348, 3.350) | (–2.348, 3.350) | T5 | (0, 1) | (0, 1) |
H3 | (–2.348, –3.350) | (–2.348, –3.350) | T6 | (0, –1) | (0, –1) |
H4 | (5.202, 3.350) | (5.202, 3.350) | T7 | (2, 1) | (2, 1) |
H5 | (5.202, –3.350) | (5.976, –1.850) | T8 | (2, –1) | (2, –1) |
T1 | (–4, 1) | (–4, 1) | T9 | (4, 1) | (4, 1) |
T2 | (–4, –1) | (–4, –1) | T10 | (4, –1) | (4, –1) |
T3 | (–2, 1) | (–2, 1) |
Num(i) | Layout position (m)(xi, yi) | Num(i) | Layout positon (m)(xi, yi) | ||
Original | Adjusted | Original | Adjusted | ||
H1 | (–4.982, 0) | (–4.982, 0) | T3 | (–2, 1) | (–2, 1) |
H2 | (–2.348, 3.350) | (–2.348, 3.350) | T4 | (–2, –1) | (–2, –1) |
H3 | (–2.348, –3.350) | (–2.348, –3.350) | T5 | (0, 1) | (0, 1) |
H4 | (5.202, 3.350) | (5.202, 3.350) | T6 | (0, –1) | (0, –1) |
H5 | (5.202, –3.350) | (5.202, –3.350) | T7 | (2, 1) | (2, 1) |
H6 | – | (0.874, 1.600) | T8 | (2, –1) | (2, –1) |
T1 | (–4, 1) | (–4, 1) | T9 | (4, 1) | (4, 1) |
T2 | (–4, –1) | (–4, –1) | T10 | (4, –1) | (4, –1) |
Num(i) | Layout position of the fulcrum (m)(xi, yi) | Num(i) | Layout position of the fulcrum (m)(xi, yi) | ||
Original | Adjusted | Original | Adjusted | ||
S1 | (–4, –3) | (–4, –3) | S5 | (1, 1) | (1, 1) |
S2 | (–5, 2) | (–5, 2) | S6 | (5, 3) | (5, 3) |
S3 | (–3, 3) | (–3, 3) | S7 | (4, –1) | (4, –1) |
S4 | (–1, –3) | (1.6, –5) | S8 | (2, –4) | (2, –4) |