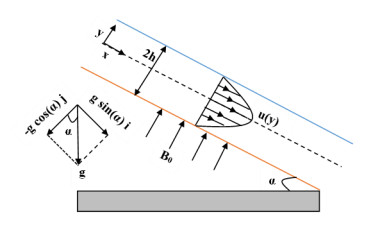
This study explores the flow properties of a couple stress fluid with the consideration of variable viscosity and a uniform transverse magnetic field. Under the effect of irreversible heat transfer, a steady fluid flow has taken place between two parallel inclined plates. The fluid flows due to gravity and the constant pressure gradient force. The plates are fixed and isothermal. The governing equations have been solved analytically for velocity and temperature fields. The total rate of heat flow and volume flow across the channel, skin friction, and Nusselt number at both plates are calculated and represent the impacts of relevant parameters through tables and graphs. The findings show that velocity, temperature, and the total rate of heat flow across the channel are enhanced by increasing the couple stress parameter and the viscosity variation parameter, while increasing the values of the Hartmann number reduces them.
Citation: Geetika Saini, B. N. Hanumagowda, S. V. K. Varma, Jasgurpreet Singh Chohan, Nehad Ali Shah, Yongseok Jeon. Impact of couple stress and variable viscosity on heat transfer and flow between two parallel plates in conducting field[J]. AIMS Mathematics, 2023, 8(7): 16773-16789. doi: 10.3934/math.2023858
[1] | Haifaa Alrihieli, Musaad S. Aldhabani, Ghadeer M. Surrati . Enhancing the characteristics of MHD squeezed Maxwell nanofluids via viscous dissipation impact. AIMS Mathematics, 2023, 8(8): 18948-18963. doi: 10.3934/math.2023965 |
[2] | W. Abbas, Ahmed M. Megahed, Osama M. Morsy, M. A. Ibrahim, Ahmed A. M. Said . Dissipative Williamson fluid flow with double diffusive Cattaneo-Christov model due to a slippery stretching sheet embedded in a porous medium. AIMS Mathematics, 2022, 7(12): 20781-20796. doi: 10.3934/math.20221139 |
[3] | Mohammed Alrehili . Managing heat transfer effectiveness in a Darcy medium with a vertically non-linear stretching surface through the flow of an electrically conductive non-Newtonian nanofluid. AIMS Mathematics, 2024, 9(4): 9195-9210. doi: 10.3934/math.2024448 |
[4] | S. R. Mishra, Subhajit Panda, Mansoor Alshehri, Nehad Ali Shah, Jae Dong Chung . Sensitivity analysis on optimizing heat transfer rate in hybrid nanofluid flow over a permeable surface for the power law heat flux model: Response surface methodology with ANOVA test. AIMS Mathematics, 2024, 9(5): 12700-12725. doi: 10.3934/math.2024621 |
[5] | Khalil Ur Rehman, Wasfi Shatanawi, Zeeshan Asghar, Haitham M. S. Bahaidarah . Neural networking analysis for MHD mixed convection Casson flow past a multiple surfaces: A numerical solution. AIMS Mathematics, 2023, 8(7): 15805-15823. doi: 10.3934/math.2023807 |
[6] | Nadeem Abbas, Wasfi Shatanawi, Taqi A. M. Shatnawi . Innovation of prescribe conditions for radiative Casson micropolar hybrid nanofluid flow with inclined MHD over a stretching sheet/cylinder. AIMS Mathematics, 2025, 10(2): 3561-3580. doi: 10.3934/math.2025164 |
[7] | Khalil Ur Rehman, Nosheen Fatima, Wasfi Shatanawi, Nabeela Kousar . Mathematical solutions for coupled nonlinear equations based on bioconvection in MHD Casson nanofluid flow. AIMS Mathematics, 2025, 10(1): 598-633. doi: 10.3934/math.2025027 |
[8] | Nadeem Abbas, Wasfi Shatanawi, Taqi A. M. Shatnawi, Fady Hasan . Theoretical analysis of induced MHD Sutterby fluid flow with variable thermal conductivity and thermal slip over a stretching cylinder. AIMS Mathematics, 2023, 8(5): 10146-10159. doi: 10.3934/math.2023513 |
[9] | Nadeem Abbas, Wasfi Shatanawi, Fady Hasan, Taqi A. M. Shatnawi . Numerical analysis of Darcy resistant Sutterby nanofluid flow with effect of radiation and chemical reaction over stretching cylinder: induced magnetic field. AIMS Mathematics, 2023, 8(5): 11202-11220. doi: 10.3934/math.2023567 |
[10] | Asifa, Poom Kumam, Talha Anwar, Zahir Shah, Wiboonsak Watthayu . Analysis and modeling of fractional electro-osmotic ramped flow of chemically reactive and heat absorptive/generative Walters'B fluid with ramped heat and mass transfer rates. AIMS Mathematics, 2021, 6(6): 5942-5976. doi: 10.3934/math.2021352 |
This study explores the flow properties of a couple stress fluid with the consideration of variable viscosity and a uniform transverse magnetic field. Under the effect of irreversible heat transfer, a steady fluid flow has taken place between two parallel inclined plates. The fluid flows due to gravity and the constant pressure gradient force. The plates are fixed and isothermal. The governing equations have been solved analytically for velocity and temperature fields. The total rate of heat flow and volume flow across the channel, skin friction, and Nusselt number at both plates are calculated and represent the impacts of relevant parameters through tables and graphs. The findings show that velocity, temperature, and the total rate of heat flow across the channel are enhanced by increasing the couple stress parameter and the viscosity variation parameter, while increasing the values of the Hartmann number reduces them.
In recent years, the major problem encountered by many researchers has been in the sector of magnetohydrodynamic (MHD) flows and heat transfer because of their significant applications in MHD pumps, MHD generators, aerodynamic heating, the petroleum industry, plasma studies, etc. [1,2,3]. The heat transfer in non-Newtonian fluids is necessary for the dismemberment of molten plastics, substantial oils and greases, synthetic fibers, and foodstuffs because non-Newtonian fluids have multiple applications in many areas of industry, biology, and engineering [4,5]. Stokes [6,7] proposed a couple stress fluid as one non-Newtonian fluid.
Falade et al. [8] and Farooq et al. [9] examined the heat transfer problem of couple stress fluid flow with variable viscosity between parallel plates. Srinivasacharya et al. [10] analyzed the Hall and Ion-slip effects with a variable heat source and MHD on couple stress fluid flow between two circular cylinders using the homotopy analysis method (HAM) and illustrated the impact of different appearing parameters on velocity and temperature fields. Numerous research studies [11,12,13,14,15,16] have expanded on the existing problems of couple stress fluid flow by including MHD with various effects and geometries. The impact of heat transfer and MHD on third-grade fluid flow between two parallel plates has been numerically investigated by [17,18,19] and examined in terms of the characteristics of velocity and temperature fields. Makinde et al. [20] showed how MHD and radiative heat transport work together to affect an optically thin fluid with a porous medium. Ahmed [21] looked into the steady MHD flow of an electrically conducting viscous fluid with heat and mass transfer in a porous medium and thermal diffusion. Umavathi et al. [22] examined the MHD Poiseuille-Couette flow of two non-mixable fluids, one of which conducts electricity and the other of which doesn't. They also looked at how new factors affect the speed and temperature distributions. Ahmed et al. [23] analysed the MHD flow of an electrically conducting viscous fluid with heat transfer across infinite annular vertical cylinders subjected to a time-dependent pressure gradient and thermal radiation. Ogunmola et al. [24] and Shah et al. [25] investigated the nature of velocity and temperature distributions by changing relevant factors and taking into account third-grade fluid flow and variable viscosity. Hassan et al. [26] studied the influence of varying viscosity and MHD on a heat-producing porous couple stress fluid with a convective cooling wall. Makinde et al. [27] investigated the MHD heat and mass transport effects on nanofluids using Poiseuille-Couette flow with the consideration of Hall effects and varying viscosity. Umavathi et al. [28] presented the variation in velocity and temperature domains by changing the physical characteristics of a couple stress fluid sandwiched between two viscous fluid layers. Imran et al. [29] investigated the applications of non-integer Caputo time fractional derivatives to natural convection flow subject to arbitrary velocity and Newtonian heating. Shah et. al. [30] presented the General solution for MHD-free convection flow over a vertical plate with ramped wall temperature and chemical reaction.
The innovative characteristics and aims of this work are noted by the fact that transportation heat couple stress model involves MHD, viscous dissipation, temperature-dependent viscosity, and inclination of the channel. This mathematical model is appropriate for the advantages of biological and lubrication systems. The behaviour of the fluid velocity, energy, skin friction and Nusselt number at the surfaces, total volume flow rate, and heat flow rate across the channel for various influential factors in the presence and absence of couple stress is discussed using graphs and tables.
To discard the induced magnetic field, assuming the magnetic Reynolds number is very small.
The current density is given by
→J=σ(→q×→B), | (1) |
The Lorentz force is defined as
→J×→B=−σB02→q, | (2) |
The dimensional version of the continuity, momentum, and energy equations is as follows:
→∇⋅→q=0, | (3) |
ρ[∂→q∂t+(→q⋅→∇)→q]=−→∇p+μ∇2→q−η∇4→q+→J×→B+ρ→g, | (4) |
ρCp[∂Θ∂t+(→q⋅→∇)Θ]=κ∇2Θ+φ. | (5) |
where →q is the vector velocity, φ is the viscous dissipation of energy, Cp is the specific heat, →J is the current density and B0 is the applied magnetic field.
It is considered the steady flow of a couple stress fluid passing through two infinitely long parallel plates separated by 2h, which are inclined from the surface at an angle of α. Plates are stable, and fluid flow is hydrodynamically and thermodynamically fully developed. The fluid is moving due to the axial pressure gradient and gravitational force. Θ0 and Θ1 are the temperatures at the bottom and top plates, respectively. A uniform magnetic field of intensity B0 is applied, which is in a perpendicular direction to the fluid flow. The viscosity is temperature dependent. We have chosen a cartesian coordinate system such that the x-axis is along the central line of the channel and the y-axis is in a direction perpendicular to it, as seen in Figure 1.
The channel is long enough so that all the physical quantities are functions of y alone, except the pressure. The velocity and temperature are as follows:
→q=(u(y),0,0)andΘ=Θ(y). | (6) |
Under the above assumptions, the Eqs (4) and (5) are transformed into
ηd4udy4−μd2udy2−(dμdy)(dudy)+∂p∂x−ρgsin(α)+σB02u=0, | (7) |
d2Θdy2+μκ(dudy)2+ηκ(d2udy2)2=0, | (8) |
The boundary conditions of the flow model are
Aty=−h,u(y)=0,u″(y)=0,Θ(y)=Θ0,Aty=h,u(y)=0,u″(y)=0,Θ(y)=Θ1.} | (9) |
The temperature-dependent viscosity by Reynold's model [16,31,32,33] is given by
μ(Θ)=μ0e−β(Θ−Θ0). | (10) |
Introducing the non-dimensional parameters [4,16] are as follows:
y∗=yh,x∗=xh,u∗=uU0,Θ∗=Θ−Θ0Θ1−Θ0,μ∗=μμ0,p∗=phμ0U0,m=β(Θ1−Θ0),Br=μ0U02κ(Θ1−Θ0),B2=μ0h2η,G=G1+G2sin(α),M2=σB02h2μ0. | (11) |
where G1=−∂p∂x is the pressure gradient parameter and G2=h2U0μ0ρg is the gravitational force parameter.
Equations (7) and (8) in the non-dimensional form (remove asterisks)
d4udy4−B2μd2udy2−B2dμdydudy−B2G+B2M2u=0, | (12) |
d2Θdy2+Brμ(dudy)2+BrB2(d2udy2)2=0, | (13) |
and the boundary conditions (9) reduced into
Aty=−1,u(y)=0,u″(y)=0,Θ(y)=0,Aty=1,u(y)=0,u″(y)=0,Θ(y)=1. | (14) |
The dimensionless form of Eq (10) is
μ(Θ)=e−mΘ. | (15) |
Use the Taylor's series, Eq (15) reduced into
μ(Θ)=1−mΘ,dμdy=−mdΘdy. | (16) |
Substitute Eq (16) in Eqs (12) and (13), then the equations are transformed in the form:
d4udy4−B2(1−mΘ)d2udy2+B2mdΘdydudy−B2G+B2M2u=0, | (17) |
d2Θdy2+Br(1−mΘ)(dudy)2+BrB2(d2udy2)2=0. | (18) |
Using the regular perturbation technique by taking the viscosity variation parameter m as a perturbation parameter where 0 < m < < 1, to solve the above non-linear coupled equations, and the velocity and temperature expressions are given by:
u=u0+mu1,Θ=Θ0+mΘ1. | (19) |
Substitute Eq (19) in Eqs (14), (17) and (18) and separating each order of approximation provides:
Zeroth order equations:
d4u0dy4−B2d2u0dy2−B2G+B2M2u0=0, | (20) |
d2Θ0dy2+Br(du0dy)2+BrB2(d2u0dy2)2=0, | (21) |
Aty=−1,u0(y)=0,u0″(y)=0,Θ0(y)=0,Aty=1,u0(y)=0,u0″(y)=0,Θ0(y)=1. | (22) |
First order equations:
d4u1dy4−B2d2u1dy2+B2Θ0d2u0dy2+B2(dΘ0dy)(du0dy)+B2M2u1=0, | (23) |
d2Θ1dy2+2Br(du0dy)(du1dy)−BrΘ0(du0dy)2+2BrB2(d2u0dy2)(d2u1dy2)=0, | (24) |
Aty=−1,u1(y)=0,u1″(y)=0,Θ1(y)=0,Aty=1,u1(y)=0,u1″(y)=0,Θ1(y)=0. | (25) |
Solve the zeroth and first order equations with their corresponding boundary conditions.
The solution for velocity and temperature distributions are obtained as:
u(y)=Ω0+Ω1cosh[Py]−Ω2cosh[Ry]+m{Ω3cosh[Py]+Ω4sinh[Py]+Ω5cosh[Ry]+Ω6sinh[Ry]+Ω7cosh[3Py]+Ω8cosh[3Ry]+Ω9cosh[(P+2R)y]+Ω10cosh[(P−2R)y]+Ω11cosh[(2P+R)y]+Ω12cosh[(2P−R)y]+y(Ω13sinh[Py]+Ω14cosh[Py]+Ω15sinh[Ry]+Ω16cosh[Ry])+y2(Ω17sinh[Py]+Ω18cosh[Py]+Ω19sinh[Ry]+Ω20cosh[Ry])+y3(Ω21sinh[Py]+Ω22sinh[Ry])}, | (26) |
Θ(y)=γ0+γ1y+γ2y2+γ3cosh[2Py]+γ4cosh[2Ry]+γ5cosh[(P+R)y]+γ6cosh[(P−R)y]+m{γ7+γ8sinh[2Py]+γ9cosh[2Py]+γ10cosh[4Py]+γ11sinh[2Ry]+γ12cosh[2Ry]+γ13cosh[4Ry]+γ14cosh[(P+R)y]+γ15cosh[(P−R)y]+γ16sinh[(P+R)y]+γ17sinh[(P−R)y]+γ18cosh[(P+3R)y]+γ19cosh[(P−3R)y]+γ20cosh[2(P+R)y]+γ21cosh[2(P−R)y]+γ22cosh[(3P+R)y]+γ23cosh[(3P−R)y]+y(γ24+γ25sinh[2Py]+γ26cosh[2Py]+γ27cosh[(P+R)y]+γ28cosh[(P−R)y]+γ29sinh[(P+R)y]+γ30sinh[(P−R)y]+γ31cosh[2Ry]+γ32sinh[2Ry])+y2(γ33+γ34sinh[2Py]+γ35cosh[2Py]+γ36cosh[(P+R)y]+γ37cosh[(P−R)y]+γ38sinh[(P+R)y]+γ39sinh[(P−R)y]+γ40sinh[2Ry]+γ41cosh[2Ry])+y3(γ42+γ43sinh[2Py]+γ44sinh[2Ry]+γ45sinh[(P+R)y]+γ46sinh[(P−R)y])+γ47y4}. | (27) |
where Ωi and γj, i = 1, 2……22 and j = 1, 2……47 are constants.
The volume flow rate across the channel
Q=∫1−1u(y)dy, | (28) |
By Eq (26),
Q=2{Ω0+1P4(P3Ω1+m(P3Ω3−P2Ω13+P(2+P2)Ω18−(6+3P2)Ω17))sinh[P]+1R4(−R3Ω2+m(R3Ω5−R2Ω15+R(2+R2)Ω20−(6+3R2)Ω22))sinh[R]+mP3(P2Ω13−2PΩ18+(6+P2)Ω21)cosh[P]+mR3(R2Ω15−2RΩ20+(6+R2)Ω22)cosh[R]+mΩ73Psinh[3P]+mΩ83Rsinh[3R]+mΩ9(P+2R)sinh[P+2R] +mΩ10(P−2R)sinh[P−2R]+mΩ11(2P+R)sinh[2P+R]+mΩ12(2P−R)sinh[2P−R]}. | (29) |
Total heat flow rate across the channel is given by
E=∫1−1u(y)Θ(y)dy | (30) |
At the lower plate, the skin friction coefficient Cf and Nusselt number Nu are given by
Cf=μdudy|y=−1,Nu=∂Θ∂y|y=−1, | (31) |
At the upper plate, Cf and Nu are given by
Cf=−μdudy|y=1,Nu=−∂Θ∂y|y=1. | (32) |
The negative sign is present because the top plate is positioned in the opposite direction of the fluid flow.
This section includes the variation of velocity and temperature profiles and a discussion of different values of the pressure gradient parameter G1, viscosity variation parameter m, the Brinkman number Br, the Hartmann number M, the angle of inclination α, and the couple stress parameter B. We also discussed the variation of volume flux, skin friction coefficient Cf, and the Nusselt number Nu on both plates through surface graphs.
Figure 2 shows that with the increase of m, the fluid viscosity decreases, and the viscous heating enhances, due to which the velocity increases.
Figure 3 depicts that the higher the pressure gradient, the faster the stream flows, and hence velocity increases.
According to Figure 4, a rise in B slows the motion of the fluid particles, providing them with enough force to pull off the frictional hindrance inboard the fluid and increase velocity in this manner.
Figure 5 shows that on increasing the values of Br, viscous dissipation dominates, due to which the velocity increases because the Brinkman number is the proportion of viscous heating to molecular conduction.
Figure 6 portrays that by raising the values of M, the Lorentz force gets stronger, which creates a resistive force in the fluid flow and causes the speed to slow down.
Figure 7 illustrates that as the angle of the inclined channel gets bigger, so does the velocity because fluid moves faster in a vertical channel than in a horizontal channel due to gravity.
According to Figures 8 and 9, raising the values of m and G1 increases the viscous dissipation due to velocity and gradient, which enhances the fluid temperature.
Figure 10 shows that when B increases, so does the temperature in the flow channel due to the viscous heating of the fluid particles.
Figure 11 displays that if Br increases, then heat production through viscous dissipation enhances, resulting in a temperature increase.
Figure 12 exhibits the variation in M. An increase in Hartmann's number strengthens the Lorentz force, which acts against the fluid flow and so lowers the fluid temperature.
Figure 13 represents that as raising the value of α, causing the channel to become vertical, due to which the frictional force in fluid flow increases and so does the temperature.
Figure 14 shows that when the Brinkman number and viscosity parameter rise, so does heat production from viscous dissipation. This makes the volume flow rate across the channel go up.
Figure 15(a) portrays the coefficient of skin friction Cf at the lower plate. It shows that when both Br and m grow at the same time, and when one of the parameters rises while the other remains unchanged, then the Cf increases. Figure 15(b) illustrates Cf at the upper plate. It shows that Cf grows with the increase of Br, whereas Cf initially increases for 0≤m≤0.3 and starts to decrease gradually for further increases in m.
Figure 16(a) and Figure 16(b) depict that when both Br and m increase in parallel time and if one of the parameters grows while the other stays constant, then the heat transfer irreversibility due to convection is more dominant and the temperature gradient rises, and hence the Nusselt number Nu at both the plates increases.
Table 1 represents the findings for the total rate of heat flow by varying the viscosity parameter, couple stress parameter, and the Hartmann number. The total heat flow rate increases as m and B increase, but higher Hartmann numbers lower the heat flow rate.
M | B | M | E |
0 | 1 | 1 | 0.0908 |
0.4 | 1 | 1 | 0.1145 |
0.8 | 1 | 1 | 0.1393 |
0.5 | 0.5 | 1 | 0.0356 |
0.5 | 1 | 1 | 0.1206 |
0.5 | 1.5 | 1 | 0.1929 |
0.5 | 1 | 1 | 0.1206 |
0.5 | 1 | 2 | 0.0713 |
0.5 | 1 | 3 | 0.0491 |
The current investigation in the absence of a magnetic field with the horizontal channel (α = 0) and the transformation y′=y+h2 validates the previously investigated work by Falade et al. [8].
The results are identical, which are represented in Figures 17 and 18 and Table 2 for the velocity profile by varying the Brinkman number, viscosity parameter, and couple stress parameter.
Br | Falade et al. [8] | Present study (M=α=0) |
1 | 0.1417 | 0.1417 |
50 | 0.1508 | 0.1508 |
100 | 0.1601 | 0.1601 |
The current study in the absence of a magnetic field and couple stress with the horizontal channel (α = 0) and the transformation y′=y+h2 validates the previously investigated work by O D Makinde [32].
For the velocity profile with variable viscosity parameter and Brinkman number, the findings shown in Figures 19 and 20 are equal.
The impact of MHD and temperature-dependent viscosity on couple stress fluid flow has been studied between two heated inclined parallel plates. The effects of relevant parameters on the fields of velocity, temperature, volume flow rate, total heat flow rate, coefficient of skin friction, and Nusselt number are concluded as follows:
● Velocity and temperature enhance with an increase in the pressure gradient, viscosity variation, couple stress parameters, Brinkman number, and angle of the inclined channel, whereas both reduce as the Hartmann number grows.
● The rate of volume flow across the channel increases as the viscosity variation parameter and Brinkman number increase.
● As the viscosity variation and couple stress parameters rise, the total rate of heat flow across the channel enhances, but it declines as the Hartmann number goes up.
● At the lower plate, skin friction increases as the viscosity variation parameter and Brinkman number increase. At the upper plate, it grows as the Brinkman number increases, whereas with the variation of the viscosity parameter, it initially increases and then gradually declines.
● The Nusselt number at both plates increases as the viscosity variation parameter and Brinkman number increase.
Geetika would like to express her heartfelt gratitude to CSIR-UGC for their financial support with grant no. 09/1313(0001)/2020-EMR-I. This study was supported by the National Research Foundation of Korea (NRF) funded by the Korean government (MSIT) [NRF-2021R1I1A3047845, NRF-2022R1A4A3023960] and BK21 Four program through the National Research Foundation of Korea (NRF) funded by the Ministry of Education of Korea (Center for Creative Leaders in Maritime Convergence).
The authors declare no conflict of interest.
[1] |
A. Bég, A. Y. Bakier, V. R. Prasad, J. Zueco, S. K. Ghosh, Nonsimilar, laminar, steady, electrically-conducting forced convection liquid metal boundary layer flow with induced magnetic field effects, Int. J. Therm. Sci., 48 (2009), 1596–1606. https://doi.org/10.1016/j.ijthermalsci.2008.12.007 doi: 10.1016/j.ijthermalsci.2008.12.007
![]() |
[2] |
A. Setayesh, V. Sahai, Heat transfer in developing magnetohydrodynamic Poiseuille flow and variable transport properties, Int. J. Heat Mass Tran., 33 (1990), 1711–1720. https://doi.org/10.1016/0017-9310(90)90026-Q doi: 10.1016/0017-9310(90)90026-Q
![]() |
[3] |
N. A. Shah, A. Ebaid, T. Oreyeni, S. J. Yook, MHD and porous effects on free convection flow of viscous fluid between vertical parallel plates: advance thermal analysis, Waves in Random and Complex Media, 2023. https://doi.org/10.1080/17455030.2023.2186717 doi: 10.1080/17455030.2023.2186717
![]() |
[4] |
M. Farooq, M. T. Rahim, S. Islam, A. M. Siddiqui, Steady Poiseuille flow and heat transfer of couple stress fluids between two parallel inclined plates with variable viscosity, J. Assoc. Arab Univ. Basic Appl. Sci., 14 (2013), 9–18. https://doi.org/10.1016/j.jaubas.2013.01.004 doi: 10.1016/j.jaubas.2013.01.004
![]() |
[5] |
A. Khan, M. Farooq, R. Nawaz, M. Ayza, H. Ahmad, H. Abu-Zinadah, et al., Analysis of couple stress fluid flow with variable viscosity using two homotopy-based methods, Open Phys., 19 (2021), 134–145. https://doi.org/10.1515/phys-2021-0015 doi: 10.1515/phys-2021-0015
![]() |
[6] |
V. K. Stokes, Couple stresses in fluids, Phys. Fluids, 9 (1996), 1709–1715. https://doi.org/10.1063/1.1761925 doi: 10.1063/1.1761925
![]() |
[7] | V. K. Stokes, Couple stresses in fluids, In: Theories of fluids with microstructure, Heidelberg: Springer, 1984. https://doi.org/10.1007/978-3-642-82351-0_4 |
[8] |
J. A. Falade, S. O. Adesanya, J. C. Ukaegbu, M. O. Osinowo, Entropy generation analysis for variable viscous couple stress fluid flow through a channel with non-uniform wall temperature, Alex. Eng. J., 55 (2016), 69–75. https://doi.org/10.1016/j.aej.2016.01.011 doi: 10.1016/j.aej.2016.01.011
![]() |
[9] |
M. Farooq, S. Islam, M. T. Rahim, T. Haroon, Heat transfer flow of steady couple stress fluids between two parallel plates with variable viscosity, Heat Transf. Res., 42 (2011), 737–780. https://doi.org/10.1615/HeatTransRes.2012000996 doi: 10.1615/HeatTransRes.2012000996
![]() |
[10] |
D. Srinivasacharya, K. Kaladhar, Analytical solution of MHD free convective flow of couple stress fluid in an annulus with Hall and ion-slip effects, Nonlinear Anal. Model. Control, 16 (2011), 477–487. https://doi.org/10.15388/NA.16.4.14090 doi: 10.15388/NA.16.4.14090
![]() |
[11] |
S. Jangili, S. O. Adesanya, H. A. Ogunseye, R. Lebelo, Couple stress fluid flow with variable properties: A second law analysis, Math. Method. Appl. Sci., 42 (2019), 85–98. https://doi.org/10.1002/mma.5325 doi: 10.1002/mma.5325
![]() |
[12] |
N. T. M. EL-Dabe, S. M. G. EL-Mohandis, Effect of couple stresses on pulsatile hydromagnetic poiseuille flow, Fluid Dyn. Res., 15 (1995), 313–324. https://doi.org/10.1016/0169-5983(94)00049-6 doi: 10.1016/0169-5983(94)00049-6
![]() |
[13] |
L. Jayaraman, G. Ramanaiah, Effect of couple stresses on transient MHD poiseuille flow, J. Comput. Phys., 60 (1985), 478–488. https://doi.org/10.1016/0021-9991(85)90032-4 doi: 10.1016/0021-9991(85)90032-4
![]() |
[14] |
K. Ramesh, Influence of heat and mass transfer on peristaltic flow of a couple stress fluid through porous medium in the presence of inclined magnetic field in an inclined asymmetric channel, J. Mol. Liq., 219 (2016), 256–271. https://doi.org/10.1016/j.molliq.2016.03.010 doi: 10.1016/j.molliq.2016.03.010
![]() |
[15] |
M. Dhlamini, H. Mondal, P. Sibanda, S. Motsa, Numerical analysis of couple stress nanofluid in temperature dependent viscosity and thermal conductivity, Int. J. Appl. Comput. Math., 7 (2021), 48. https://doi.org/10.1007/s40819-021-00983-x doi: 10.1007/s40819-021-00983-x
![]() |
[16] |
R. Ellahi, A. Zeeshan, F. Hussain, T. Abbas, Two-phase Couette flow of couple stress fluid with temperature dependent viscosity thermally affected by magnetized moving surface, Symmetry, 11 (2019), 647. https://doi.org/10.3390/sym11050647 doi: 10.3390/sym11050647
![]() |
[17] |
L. Wang, Y. Jian, Q. Liu, F. Li, L. Chang, Electromagnetohydrodynamic flow and heat transfer of third grade fluids between two micro-parallel plates, Colloid. Surface. A, 494 (2016), 87–94. https://doi.org/10.1016/j.colsurfa.2016.01.006 doi: 10.1016/j.colsurfa.2016.01.006
![]() |
[18] |
Y. M. Aiyesimi, G. T. Okedayo, O. W. Lawal, Unsteady magnetohydrodynamic (MHD) thin film flow of a third grade fluid with heat transfer and no slip boundary condition down an inclined plane, Int. J. Phys. Sci., 8 (2013), 946–955. https://doi.org/10.5897/IJPS2013.3891 doi: 10.5897/IJPS2013.3891
![]() |
[19] |
Z. Shao, N. A. Shah, I. Tlili, U. Afzal, S. Khan, Hydromagnetic free convection flow of viscous fluid between vertical parallel plates with damped thermal and mass fluxes, Alex. Eng. J., 58 (2019), 989–1000. https://doi.org/10.1016/j.aej.2019.09.001 doi: 10.1016/j.aej.2019.09.001
![]() |
[20] | O. Makinde, P. Y. Mhone, Heat transfer to MHD oscillatory flow in a channel Ölled with porous medium, Rom. J. Phys., 50 (2005), 931–938. |
[21] |
N. Ahmed, Heat and mass transfer in MHD Poiseuille flow with porous walls, J. Eng. Phys. Thermophys., 92 (2019), 122–131. https://doi.org/10.1007/s10891-019-01914-w doi: 10.1007/s10891-019-01914-w
![]() |
[22] |
J. Umavathi, I. C. Liu, P. Kumar, Magnetohydrodynamic Poiseuille-Couette flow and heat transfer in an inclined channel, J. Mech., 26 (2010), 525–532. https://doi.org/10.1017/S172771910000472X doi: 10.1017/S172771910000472X
![]() |
[23] |
N. Ahmed, M. Dutta, Heat transfer in an unsteady MHD flow through an infinite annulus with radiation, Bound. Value Probl., 2015 (2015), 11. https://doi.org/10.1186/s13661-014-0279-z doi: 10.1186/s13661-014-0279-z
![]() |
[24] |
B. Ogunmola, A. Akinshilo, G. Sobamowo, Perturbation solutions for Hagen-Poiseuille flow and heat transfer of third-grade fluid with temperature-dependent viscosities and internal heat generation, Int. J. Eng. Math., 2016 (2016), 8915745. https://doi.org/10.1155/2016/8915745 doi: 10.1155/2016/8915745
![]() |
[25] |
R. A. Shah, S. Islam, A. M. Siddiqui, T. Haroon, Heat transfer by laminar flow of a third grade fluid in wire coating analysis with temperature dependent and independent viscosity, Anal. Math. Phys., 1 (2011), 147–166. https://doi.org/10.1007/s13324-011-0011-4 doi: 10.1007/s13324-011-0011-4
![]() |
[26] |
A. R. Hassan, S. O. Salawu, A. B. Disu, The variable viscosity effects on hydromagnetic couple stress heat generating porous fluid flow with convective wall cooling, Sci. Afr., 9 (2020), e00495. https://doi.org/10.1016/j.sciaf.2020.e00495 doi: 10.1016/j.sciaf.2020.e00495
![]() |
[27] |
O. D. Makinde, T. Iskander, F. Mabood, W. A. Khan, M. S. Tshehla, MHD Couette-Poiseuille flow of variable viscosity nanofluids in a rotating permeable channel with Hall effects, J. Mol. Liq., 221 (2016), 778–787. https://doi.org/10.1016/j.molliq.2016.06.037 doi: 10.1016/j.molliq.2016.06.037
![]() |
[28] |
J. C. Umavathi, A. J. Chamkha, M. H. Manjula, A. Al-Mudhaf, Flow and heat transfer of a couple-stress fluid sandwiched between viscous fluid layers, Can. J. Phys., 83 (2005), 705–720. https://doi.org/10.1139/p05-032 doi: 10.1139/p05-032
![]() |
[29] |
M. A. Imran, N. A. Shah, I. Khan, M. Aleem, Applications of non-integer Caputo time fractional derivatives to natural convection flow subject to arbitrary velocity and Newtonian heating, Neural Comput. Appl., 30 (2018), 1589–1599. https://doi.org/10.1007/s00521-016-2741-6 doi: 10.1007/s00521-016-2741-6
![]() |
[30] |
N. A. Shah, A. A. Zafar, S. Akhtar, General solution for MHD-free convection flow over a vertical plate with ramped wall temperature and chemical reaction, Arab. J. Math., 7 (2018), 49–60. https://doi.org/10.1007/s40065-017-0187-z doi: 10.1007/s40065-017-0187-z
![]() |
[31] |
O. D. Makinde, Laminar falling liquid film with variable viscosity along an inclined heated plate, Appl. Math. Comput., 175 (2006), 80–88. https://doi.org/10.1016/j.amc.2005.07.021 doi: 10.1016/j.amc.2005.07.021
![]() |
[32] |
O. D. Makinde, Entropy-generation analysis for variable-viscosity channel flow with non-uniform wall temperature, Appl. Energy, 85 (2008), 384–393. https://doi.org/10.1016/j.apenergy.2007.07.008 doi: 10.1016/j.apenergy.2007.07.008
![]() |
[33] |
A. B. Disu, M. S. Dada, Reynold's model viscosity on radiative MHD flow in a porous medium between two vertical wavy walls, J. Taibah Univ. Sci., 11 (2017), 548–565. https://doi.org/10.1016/j.jtusci.2015.12.001 doi: 10.1016/j.jtusci.2015.12.001
![]() |
1. | Galal M. Moatimid, Mohamed F. E. Amer, Doaa A. Ibrahim, EHD instability of a cylindrical interface separating two couple-stress fluids, 2024, 14, 2045-2322, 10.1038/s41598-024-56143-w | |
2. | K. Venkateswara Raju, Ch. Maheswari, R. Mohana Ramana, S. Vijayakumar Varma, M. Changal Raju, Comparative numerical study between MHD Forchheimer nano and hybrid nanofluid flows over stretching sheet under aligned magnetic field in the presence of radiation absorption, 2024, 0228-6203, 1, 10.1080/02286203.2024.2393306 | |
3. | Nithya C Kumar, Hanumagowda B N, Girish Sharma, S.V.K. Varma, Jagadish V. Tawade, M. Ijaz Khan, Temperature-dependent thermal conductivity and viscosity effect on the pressure-gravity flow of an engine oil-based hybrid nanofluid in an inclined channel, 2024, 26668181, 101019, 10.1016/j.padiff.2024.101019 |
M | B | M | E |
0 | 1 | 1 | 0.0908 |
0.4 | 1 | 1 | 0.1145 |
0.8 | 1 | 1 | 0.1393 |
0.5 | 0.5 | 1 | 0.0356 |
0.5 | 1 | 1 | 0.1206 |
0.5 | 1.5 | 1 | 0.1929 |
0.5 | 1 | 1 | 0.1206 |
0.5 | 1 | 2 | 0.0713 |
0.5 | 1 | 3 | 0.0491 |
Br | Falade et al. [8] | Present study (M=α=0) |
1 | 0.1417 | 0.1417 |
50 | 0.1508 | 0.1508 |
100 | 0.1601 | 0.1601 |
M | B | M | E |
0 | 1 | 1 | 0.0908 |
0.4 | 1 | 1 | 0.1145 |
0.8 | 1 | 1 | 0.1393 |
0.5 | 0.5 | 1 | 0.0356 |
0.5 | 1 | 1 | 0.1206 |
0.5 | 1.5 | 1 | 0.1929 |
0.5 | 1 | 1 | 0.1206 |
0.5 | 1 | 2 | 0.0713 |
0.5 | 1 | 3 | 0.0491 |
Br | Falade et al. [8] | Present study (M=α=0) |
1 | 0.1417 | 0.1417 |
50 | 0.1508 | 0.1508 |
100 | 0.1601 | 0.1601 |