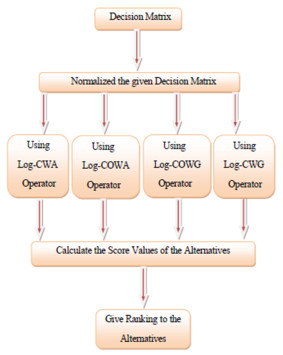
The heat and mass transfer within non-Newtonian fluid flow results in complex mathematical equations and solution in this regard remains a challenging task for researchers. The present paper offers a numerical solution for the non-Newtonian flow field by using Artificial neural networking (ANN) model with the Levenberg Marquardt training technique. To be more specific, we considered thermally magnetized non-Newtonian flow headed for inclined heated surfaces. The flow is carried with viscous dissipation, stagnation point, heat generation, mixed convection, and thermal radiation effects. The concentration aspects are entertained by the owing concentration equation. The shooting method is used to solve the mathematical flow equations. The quantity of interest includes the temperature and heat transfer coefficient. Two different artificial neural networking models have been built. The training of networks is done by use of the Levenberg Marquardt technique. The values of the coefficient of determination suggest artificial neural networks as the best method for predicting the Nusselt number at both surfaces. The thermal radiation parameter and Prandtl number admit a direct relationship to the Nusselt number while the differing is the case for variable thermal conductivity and Casson parameters. Further, by using Nusselt number (NN)-ANN models, we found that for cylindrical surface, the strength of the NN is greater than the flat surface.
Citation: Khalil Ur Rehman, Wasfi Shatanawi, Zeeshan Asghar, Haitham M. S. Bahaidarah. Neural networking analysis for MHD mixed convection Casson flow past a multiple surfaces: A numerical solution[J]. AIMS Mathematics, 2023, 8(7): 15805-15823. doi: 10.3934/math.2023807
[1] | Esmail Hassan Abdullatif Al-Sabri, Muhammad Rahim, Fazli Amin, Rashad Ismail, Salma Khan, Agaeb Mahal Alanzi, Hamiden Abd El-Wahed Khalifa . Multi-criteria decision-making based on Pythagorean cubic fuzzy Einstein aggregation operators for investment management. AIMS Mathematics, 2023, 8(7): 16961-16988. doi: 10.3934/math.2023866 |
[2] | Saleem Abdullah, Muhammad Qiyas, Muhammad Naeem, Mamona, Yi Liu . Pythagorean Cubic fuzzy Hamacher aggregation operators and their application in green supply selection problem. AIMS Mathematics, 2022, 7(3): 4735-4766. doi: 10.3934/math.2022263 |
[3] | Khulud Fahad Bin Muhaya, Kholood Mohammad Alsager . Extending neutrosophic set theory: Cubic bipolar neutrosophic soft sets for decision making. AIMS Mathematics, 2024, 9(10): 27739-27769. doi: 10.3934/math.20241347 |
[4] | Hifza, Muhammad Gulistan, Zahid Khan, Mohammed M. Al-Shamiri, Muhammad Azhar, Asad Ali, Joseph David Madasi . A new fuzzy decision support system approach; analysis and applications. AIMS Mathematics, 2022, 7(8): 14785-14825. doi: 10.3934/math.2022812 |
[5] | Anam Habib, Zareen A. Khan, Nimra Jamil, Muhammad Riaz . A decision-making strategy to combat CO2 emissions using sine trigonometric aggregation operators with cubic bipolar fuzzy input. AIMS Mathematics, 2023, 8(7): 15092-15128. doi: 10.3934/math.2023771 |
[6] | Muhammad Danish Zia, Esmail Hassan Abdullatif Al-Sabri, Faisal Yousafzai, Murad-ul-Islam Khan, Rashad Ismail, Mohammed M. Khalaf . A study of quadratic Diophantine fuzzy sets with structural properties and their application in face mask detection during COVID-19. AIMS Mathematics, 2023, 8(6): 14449-14474. doi: 10.3934/math.2023738 |
[7] | Sohail Ahmad, Ponam Basharat, Saleem Abdullah, Thongchai Botmart, Anuwat Jirawattanapanit . MABAC under non-linear diophantine fuzzy numbers: A new approach for emergency decision support systems. AIMS Mathematics, 2022, 7(10): 17699-17736. doi: 10.3934/math.2022975 |
[8] | Muhammad Riaz, Khadija Akmal, Yahya Almalki, S. A. Alblowi . Cubic m-polar fuzzy topology with multi-criteria group decision-making. AIMS Mathematics, 2022, 7(7): 13019-13052. doi: 10.3934/math.2022721 |
[9] | Ashraf Al-Quran, Nimra Jamil, Syeda Tayyba Tehrim, Muhammad Riaz . Cubic bipolar fuzzy VIKOR and ELECTRE-II algorithms for efficient freight transportation in Industry 4.0. AIMS Mathematics, 2023, 8(10): 24484-24514. doi: 10.3934/math.20231249 |
[10] | Attaullah, Shahzaib Ashraf, Noor Rehman, Asghar Khan, Muhammad Naeem, Choonkil Park . Improved VIKOR methodology based on q-rung orthopair hesitant fuzzy rough aggregation information: application in multi expert decision making. AIMS Mathematics, 2022, 7(5): 9524-9548. doi: 10.3934/math.2022530 |
The heat and mass transfer within non-Newtonian fluid flow results in complex mathematical equations and solution in this regard remains a challenging task for researchers. The present paper offers a numerical solution for the non-Newtonian flow field by using Artificial neural networking (ANN) model with the Levenberg Marquardt training technique. To be more specific, we considered thermally magnetized non-Newtonian flow headed for inclined heated surfaces. The flow is carried with viscous dissipation, stagnation point, heat generation, mixed convection, and thermal radiation effects. The concentration aspects are entertained by the owing concentration equation. The shooting method is used to solve the mathematical flow equations. The quantity of interest includes the temperature and heat transfer coefficient. Two different artificial neural networking models have been built. The training of networks is done by use of the Levenberg Marquardt technique. The values of the coefficient of determination suggest artificial neural networks as the best method for predicting the Nusselt number at both surfaces. The thermal radiation parameter and Prandtl number admit a direct relationship to the Nusselt number while the differing is the case for variable thermal conductivity and Casson parameters. Further, by using Nusselt number (NN)-ANN models, we found that for cylindrical surface, the strength of the NN is greater than the flat surface.
Multi attribute group decision making (MAGDM) is quite an interesting and eminent field of research attempting to produce arguments and techniques that determine the most favorable alternative from a set of alternatives. It is challenging for decision makers to give accurate information about options due to the complexity of the socioeconomic environment and their lack of expertise and judgment. Classical set theory deals with the information of type yes or no, that is, whether an element belongs to a set or not. On the other hand, real life situations may be imprecise or unclear, and there may be possibility other than yes or no. To tackle vague or imprecise information, in 1965, Zadeh [36] extended the concept of classical sets in the form of fuzzy sets. Fuzzy set theory permits a membership function valued in the interval [0,1]. After that, Atanassov [1] presented the intuitionistic fuzzy set (IFS) as a generalization of the fuzzy set. The IFS has both a positive and a negative membership degree, and that the sum of both these degrees is less than or equal to one.
Analysis of clusters [6], medical diagnosis problems with decision-making (DM) [14] and pattern recognition [8] are some of the fields that have used IFSs. In the success of IFSs, numerous researchers have contributed. Chen et al. [7] defined a method for the use of intuitionistic fuzzy numbers (IFNs) and interval valued intuitionistic fuzzy (IVIF) numbers in aggregation processes and to address DM challenges. The intuitionistic fuzzy Hamacher aggregation procedures were cited by Huang as being advantageous in instances involving decision-making. Khan et al. [22] defined a solution of linear and quadratic equations based on triangular linear Diophantine fuzzy numbers. Alaoui et al. [5] defined a novel analysis of fuzzy physical models by generalized fractional fuzzy operators.
In order to combine intuitionistic fuzzy data and make decisions, a variety of intuitionistic fuzzy aggregation operators have been proposed for combining different options [20]. The cumulative positive and negative membership degrees of the decision-maker may occasionally exceed one. For example, if a decision-maker assigns a positive membership degree of 0.3 and a negative membership degree of 0.9,0.3+0.9=1.2>1. Intuitionistic fuzzy sets are unable to handle this situation. Yager [34] developed the Pythagorean fuzzy set (PyFS), which includes both positive and negative membership degrees but whose square sum is equal to or less than one, to address this issue. 0.32+0.92=0.9 corresponds to the above-mentioned example. PyFS is a generalization of IFS. PyFS resolves inaccurate and uncertain information in actual MADM problems better than IFS. Since the development of PyFS, many aggregation operators have been established for Pythagorean fuzzy Dombi aggregation operators and their application in Pythagorean fuzzy multiple criteria group decision making and decision support systems [20,37]. In multiple attribute group decision-making, some generalized Pythagorean fuzzy Bonferroni mean aggregation operations are used [38]. Ren et al. [31] defined the Pythagorean fuzzy TODIM approach to multi-criteria decision making. Gou et al. [12] proposed some properties of continuous Pythagorean fuzzy information.
Zeng et al. [39] introduced the exponential intuitionistic divergence measure, envelopment analysis, preference fusion and membership improvement of intuitionistic fuzzy numbers and discussed its potential application in multi-criteria decision making in 2019. Garg et al. [13] discussed the correlation measures for cubic m-polar fuzzy sets with applications. Ayub et al. [3] proposed cubic Heronian mean Dombi aggregation operators and their application on the MADM problem. Qiyas et al. [30] presented a novel approach of linguistic intuitionistic cubic hesitant variables and their application in decision making.
In multi-attribute decision making, Hussain et al. [15] applied averaging operators based on spherical cubic fuzzy numbers. Decision support systems use cubic picture fuzzy aggregation operators [28]. Decision-making including distance measure and induced aggregation operators, as well as decision-making involving distance measures and linguistic aggregation operators are discussed in [24]. Fuzzy generalized hybrid aggregation operators and their application in fuzzy decision making, and fuzzy induced generalized aggregation operators and its application in multi-criteria decision making are discussed in [25,27]. For comparison, the author studied the cubic fuzzy Einstein aggregation operations and their application to decision-making [10]. Multi-attribute decision-making problems were solved under a cubic intuitionistic fuzzy set environment, based on Bonferroni mean operators [18], and cubic intuitionistic fuzzy aggregation operators [19]. Multi-attribute decision-making problems are solved under cubic hesitant fuzzy sets and an assessment method of prostate cancer risk classes utilizing cubic hesitant fuzzy sets similarity measure was presented by different authors [2,9,35]. The expected values of aggregation operators on cubic triangular fuzzy numbers and their use in problems involving multi-criteria are described in [32,33]. Abdullah et al. [4] defined Pythagorean cubic fuzzy Hamacher aggregation operators and their application in a green supply selection problem.
The main motivation is the extension of aggregation operators characteristics to consider a wider range of complex problems. To deal with the aggregate uncertainty expressed in the form of cubic sets, a variety of aggregation operators have been created based on the algebraic t-norm and t-conorm. Important mathematical processes called logarithmic operational rules can be used to conveniently aggregate uncertain and erroneous data. These concepts served as inspiration for us to create a cubic MAGDM approach to solve the problem within cubic sets (CSs). This method is built on the logarithmic aggregation operators and the logarithmic operations of cubic sets.
The contributions of our method are as follows:
(1) To overcome the limitations of algebraic operations and represent the interactions between various cubic sets, we developed a variety of distinct logarithmic operations for cubic sets.
(2) We developed aggregation operators for cubic information that overcome the limitations of algebraic operators. These operators are logarithmic cubic weighted averaging (log-CWA), logarithmic cubic ordered weighted averaging (log-COWA), logarithmic cubic weighted geometric (log -CWG) and logarithmic cubic ordered weighted geometric (log-COWG) operators.
(3) Using cubic information, we developed a method to handle multi-attribute decision-making scenarios.
(4) To illustrate the efficiency and dependability of the recommended cubic logarithmic aggregation operators, we used a circulation center evaluation problem.
(5) According to the data, the suggested strategy performs better and yields more accurate results when compared to the current approaches.
The remainder of the paper is organized as follows: Section 2 introduces numerous key terms, including IFS, PyFS, CS, score, and accuracy function. Section 3 discusses the logarithmic operation rules and characteristics of cubic numbers (CNs). In Section 4, logarithmic cubic averaging aggregation operators are defined. In Section 5, logarithmic cubic geometric aggregation operators are defined. The MAGDM approach is given in Section 6 based on the logarithmic cubic aggregation operators. An example is solved in Section 7 based on the logarithmic aggregation operator. In Section 8, we demonstrate the sensitivity analysis and comparison of the proposed method to other existing methods. Finally, the study's conclusion is reached in Section 8.
This part recaps the basic definitions of current fuzzy set extensions, which served as the study's foundation.
Definition 2.1. [1] Let ˆG≠ϕ be a universal set. Then, the set
ˇZ={ˆs.(ˆWˇZ(ˆs),˘UˇZ(ˆs)|ˆs∈ˆG)}, | (2.1) |
is an IFS, where ˆWˇZ(ˆs),˘UˇZ(ˆs)∈[0,1] are the element's positive and negative membership degrees ˆs∈ˆG in ˇZ, respectively. ˆWˇZ(ˆs),˘UˇZ(ˆs) satisfy the condition, for all ˆs∈ˆG,
0≤ˆWˇZ(ˆs)+˘UˇZ(ˆs)≤1. | (2.2) |
Definition 2.2.[29] Let ˇZ=(ˆWˇZ(ˆs),˘UˇZ(ˆs)|ˆs∈ˆG) be an IFN. Then, the score function of ˇZ is defined as;
S(ˇZ)=ˆWˇZ(ˆs)−˘UˇZ(ˆs),S(ˇZ)∈[−1,1]. | (2.3) |
The accuracy function of ˇZ is defined as;
ˆS(ˇZ)=ˆWˇZ(ˆs)+˘UˇZ(ˆs),ˆS(ˇZ)∈[−1,1]. | (2.4) |
Definition 2.3. [39] Let ˇZ1=((ˆWˇZ1(ˆs),˘UˇZ1(ˆs)) and ˇZ2=((ˆWˇZ2(ˆs),˘UˇZ2(ˆs)) be any two IFNs. Then, the comparison rules are defined as follows:
(1) If S(ˇZ1)>S(ˇZ2), then ˇZ1>ˇZ2.
(2) If S(ˇZ1)=S(ˇZ2) and ˆS(ˇZ1)>ˆS(ˇZ2), then ˇZ1>ˇZ2.
(3) If S(ˇZ1)=S(ˇZ2) and ˆS(ˇZ1)=ˆS(ˇZ2), then ˇZ1=ˇZ2.
Definition 2.4.[1] Let ˇZ1,ˇZ2 and ˇZ3 be a fuzzy sets. Then, the following properties of fuzzy sets are as follows:
Identity
ˇZ1∩U=ˇZ1,whereUisauniversalset.ˇZ1∪ϕ=ˇZ1,whereϕistheemptyset. |
Absorption by ϕ and U
ˇZ1∩ϕ=ϕˇZ1∪U=U. |
Idempotent
ˇZ1∩ˇZ1=ˇZ1ˇZ1∪ˇZ1=ˇZ1. |
De Morgan laws
(ˇZ1∩ˇZ2)′=ˇZ′1∪ˇZ′2(ˇZ1∪ˇZ2)′=ˇZ′1∩ˇZ′2. |
Involution
(ˇZ′1)′=ˇZ1. |
Absorption
ˇZ1∩(ˇZ2∪ˇZ3)=ˇZ1ˇZ1∪(ˇZ2∩ˇZ3)=ˇZ1. |
The cubic set is an appropriate way to deal with fuzziness. The cubic set has been extensively applied to the decision making problems. It can be defined as follows:
Definition 2.5.[10] Let ˆG≠ϕ, be a fixed set. Then, the set
ˇZ={ˆs,([ˆWˇZ(ˆs),˘UˇZ(ˆs)],ˆYˇZ(ˆs)|ˆs∈ˆG)}, | (2.5) |
is called CS, where [ˆWˇZ(ˆs),˘UˇZ(ˆs)],ˆYˇZ(ˆs) are known as the element's positive and negative membership degrees ˆs∈ˆG in ˇZ respectively, with the condition that 0≤[ˆWˇZ(ˆs),˘UˇZ(ˆs)],ˆYˇZ(ˆs)≤1.
Definition 2.6.[10] Let ˇZ=([ˆWˇZ(ˆs),˘UˇZ(ˆs)],ˆYˇZ(ˆs)|ˆs∈ˆG),ˇZ1=([ˆWˇZ1(ˆs),˘UˇZ1(ˆs)],ˆYˇZ1(ˆs)|ˆs∈ˆG) and ˇZ2=([ˆWˇZ2(ˆs),˘UˇZ2(ˆs)],ˆYˇZ2(ˆs)|ˆs∈ˆG) are any two IFSs. Then the following operations are defined:
(1) ˇZc={ˆYˇZ(ˆs),[˘UˇZ(ˆs),ˆWˇZ(ˆs)]}.
(2) ˇZ1∧ˇZ2={[min(ˆWˇZ1(ˆs),ˆWˇZ2(ˆs)),min(˘UˇZ1(ˆs),˘UˇZ2(ˆs))],max(ˆYˇZ1(ˆs),ˆYˇZ2(ˆs))}.
(3) ˇZ1∧ˇZ2={[max(ˆWˇZ1(ˆs),ˆWˇZ2(ˆs)),max(˘UˇZ1(ˆs),˘UˇZ2(ˆs))],min(ˆYˇZ1(ˆs),ˆYˇZ2(ˆs))}.
(4) υ⋅ˇZ={[1−(1−ˆWˇZ)υ,(˘UˇZ)υ],(ˆYˇZ)υ}.
(5) ˇZυ={[(ˆWˇZ)υ,1−(1−˘UˇZ)υ],1−(1−ˆYˇZ)υ}.
In this section, we define the basic operation laws, and some properties of logarithmic cubic numbers.
In this section, we will introduce and investigate the characteristics of certain novel logarithmic operating rules for cubic numbers. It is noted that log˘e0 in the real number system, has no meaning, and log˘e1 is not defined. As a result, we assume ˇZ≠0, where ˇZ is a CN. Also, the base of a logarithm, i.e., ˘e≠1, is in the open interval (0,1) and always a positive-real number.
Definition 3.1. Let ˆG≠ϕ be a fixed set and ˇZ=([ˆWˇZ(ˆs),˘UˇZ(ˆs)],ˆYˇZ(ˆs)) be a cubic number. Then, the logarithmic cubic number is defined as,
log˘eˇZ={([1−log˘eˆWˇZ(ˆs−log˘e˘UˇZ),1(ˆs)],log˘e(1−ˆYˇZ(ˆs))|ˆs∈ˆG)},0<˘e≤[ˆW,˘U]≤1,˘e≠1, | (3.1) |
where, [ˆWˇZ(ˆs),˘UˇZ(ˆs)],ˆYˇZ(ˆs) are identified as positive and negative membership degrees of the element ˆs∈ˆG in ˇZ respectively, with the condition that 0≤[ˆWˇZ(ˆs),˘UˇZ(ˆs)],ˆYˇZ(ˆs)≤1. The logarithmic operational law's positive membership is thus defined as follows:
[1−log˘eˆWˇZ(ˆs),1−log˘e˘UˇZ(ˆs)]:ˆG→[0,1],suchthat[1−log˘eˆWˇZ(ˆs),1−log˘e˘UˇZ(ˆs)]∈[0,1],forall˚u∈ˆG, |
Negative membership is defined as
log˘e(1−ˆYˇZ(ˆs)):ˆG→[0,1],suchthatlog˘e(1−ˆYˇZ(ˆs))∈[0,1],∀ˆs∈ˆG, | (3.2) |
and the refusal degree is defined as
1−([(1−log˘eˆWˇZ(ˆs))+1−log˘e˘UˇZ(ˆs)]+log˘e(1−ˆYˇZ(ˆs))),forallˆs∈ˆG. | (3.3) |
The operational law of log-CNs is defined next.
Definition 3.2. Let ˇZ=([ˆWˇZ(ˆs),˘UˇZ(ˆs)],ˆYˇZ(ˆs)), ˇZ1=([ˆWˇZ1(ˆs),˘UˇZ1(ˆs)],ˆYˇZ1(ˆs)) and ˇZ2=([ˆWˇZ2(ˆs),˘UˇZ2(ˆs)],ˆYˇZ2(ˆs)) be any three CNs, let υ be any scalar greater than 0. Then, the logarithmic cubic operational law is defined as follows;
logˇeˇZ1⊕logˇeˇZ2=([1−logˇeˆW1.logˇeˆW2,1−logˇe˘U1.logˇe˘U2],logˇe(1−ˆY1).logˇe(1−ˆY2))logˇeˇZ1⊗logˇeˇZ2=([(1−logˇeˆW1).(1−logˇeˆW2),1−(1−(1−logˇe˘U1)).(1−(1−logˇe˘U2))],1−(1−logˇe(1−ˆY1)).(1−logˇe(1−ˆY2)))υ.logˇeˇZ=([1−(logˇeˆW)υ,(1−(logˇe˘U))υ],(logˇe(1−ˆY)υ))logˇeˇZυ=([(1−logˇeˆW)υ,1−(1−(1−logˇe˘U))υ],1−(1−logˇe(1−ˆY))υ). |
We discuss the attributes of CNs based on the logarithmic operational law in this section of the article.
Theorem 3.1. Let ˇZ=([ˆWˇZ,˘UˇZ],ˆYˇZ) be any cubic number with condition 0<˘e≤[ˆW,˘U]≤1,˘e≠1. Then, prove that
ˇelogˇeˇZ=ˇZ. |
Proof. For proof, see Appendix A.
Theorem 3.2.Let ˇZ=([ˆWˇZ,˘UˇZ],ˆYˇZ) be any cubic numbers with condition 0<˘e≤[ˆW,˘U]≤1,˘e≠1, Then, prove that
logˇeˇeˇZ=ˇZ. | (3.4) |
Proof. As we know,
logˇeˇeˇZ=logˇe([ˇe(1−ˆWˇZ),ˇe(1−˘UˇZ)],1−ˇeˆYˇZ)=([1−logˇeˇe(1−ˆWˇZ),1−logˇeˇe(1−˘UˇZ)],logˇe(1−(1−ˇeˆYˇZ))=([ˆWˇZ,˘UˇZ],ˆYˇZ)=ˇZ. |
Theorem 3.3. Let the collection of two cubic numbers is ˇZ1=([ˆW1,˘U1],ˆY1) and ˇZ2=([ˆW2,˘U2],ˆY2) with conditions 0<ˇe≤min([ˆW1,˘U1],[ˆW2,˘U2]) and ˇe≠1. Then, show that
(a)logˇeˇZ1⊕logˇeˇZ2=logˇeˇZ2⊕logˇeˇZ1.(b)logˇeˇZ1⊗logˇeˇZ2=logˇeˇZ2⊗logˇeˇZ1. |
Proof. For proof, see Appendix B.
Theorem 3.4. Let the collection of three cubic numbers is ˇZ1=([ˆW1,˘U1],ˆY1),ˇZ2=([ˆW2,˘U2],ˆY2) and ˇZ3=([ˆW3,˘U3],ˆY3) with conditions 0<ˇe≤min([ˆW1,˘U1],[ˆW2,˘U2]) and ˇe≠1. Then, we shows that
(logˇeˇZ1⊕logˇeˇZ2)⊕logˇeˇZ3=logˇeˇZ1⊕(logˇeˇZ2⊕logˇeˇZ3). | (3.5) |
Proof. For proof, see Appendix C.
Theorem 3.5. Let the collection of three cubic numbers is ˇZ1=([ˆW1,˘U1],ˆY1),ˇZ2=([ˆW2,˘U2],ˆY2) and ˇZ3=([ˆW3,˘U3],ˆY3) with conditions 0<ˇe≤min([ˆW1,˘U1],[ˆW2,˘U2]) and ˇe≠1. Then, we shows that
(logˇeˇZ1⊗logˇeˇZ2)⊗logˇeˇZ3=logˇeˇZ1⊗(logˇeˇZ2⊗logˇeˇZ3). | (3.6) |
Proof. For proof, see Appendix D.
Theorem 3.6.Let two CNs is ˇZ1=([ˆW1,˘U1],ˆY1) and ˇZ2=([ˆW2,˘U2],ˆY2) with conditions satisfy, 0<ˇe≤min([ˆW1,˘U1],[ˆW2,˘U2]) and ˇe≠1, and also let υ be any positive real number. Then,
(logˇeˇZ1⊗logˇeˇZ2)υ=(logˇeˇZ1)υ⊗(logˇeˇZ2)υ. | (3.7) |
Proof. The procedure in this case is eliminated because the proof is comparable to Theorem 3.2.
Theorem 3.7. Let ˇZ=([ˆW,˘U],ˆY) be a CN, 0<ˇe≤ˆW≤1, ˇe≠1, and υ1,υ2>0. Then, we show that
υ1.logˇeˇZ⊕υ2.logˇeˇZ=(υ1⊕υ2)logˇeˇZ(logˇeˇZ)υ1⊗(logˇeˇZ)υ2=(logˇeˇZ)υ1⊕υ2((logˇeˇZ)υ1)υ2=(logˇeˇZ)υ1υ2. | (3.8) |
Proof. For proof, see Appendix E.
We defined some logarithmic cubic fuzzy averaging aggregation operators, namely, log-CWA and log-COWA, and study their features in depth in this section.
Definition 4.1.Let ˇZp=([ˆWˇZp,˘UˇZp],ˆYˇZp)(p=1,2,⋯,n) be a collection of cubic numbers with 0<˘ep≤[ˆWp,˘Up]≤1, and ˘ep≠1. Then, the mapping log−CWA:ˇRn⟶ˇR, is defined,
log−CWA(ˇZ1,⋯,ˇZn)=n⨁p=1ϖp.log˘epˇZp. | (4.1) |
The function log-CWA is called the logarithmic cubic weighted averaging operator, where ϖ=(ϖ1,ϖ2,⋯,ϖn)T denotes the weighed vector of log˘epˇZp(p=1,2,⋯,n), such that ϖp∈[0,1], and ∑np=1ϖp=1.
Theorem 4.1. Let ˇZp=([ˆWp,˘Up],ˆYp)(p=1,2,⋯,n) be a collection of CNs with condition 0<ˇep≤[ˆWp,˘Up]≤1, and ˇep≠1. Then, using Definitions 3.1 and 3.2, we have
log−CWA(ˇZ1,...,ˇZn)=([1−n∏p=1(log˘ep(ˆWp))ϖP,1−n∏p=1(log˘ep(˘Up))ϖP],n∏p=1(log˘ep(1−ˆYp))ϖP). | (4.2) |
Proof. For proof, see Appendix F.
(1) Idempotency:Let ˇZp=([ˆWp,˘Up],ˆYp)(p=1,2,⋯,n) be a collection of cubic numbers that are equal, i.e., ˇZp=ˇZ,(p=1,2,⋯,n). Then,
log−CWA(ˇZ1,...,ˇZn)=log˘eˇZ, | (4.3) |
where ˘e1=˘e2=...=˘en=˘e.
Proof. We have
log−CWA(ˇZ1,...,ˇZn)=([1−n∏p=1(log˘ep(ˆWp))ϖP,1−n∏p=1(log˘ep(˘Up))ϖP],n∏p=1(log˘ep(1−ˆYp))ϖP) |
log−CWA(ˇZ1,...,ˇZn)=([1−n∏p=1(log˘ep(ˆW))ϖP,1−n∏p=1(log˘ep(˘U))ϖP],n∏p=1(log˘ep(1−ˆY))ϖP) |
=([1−log˘eˆWˇZ(ˆs−log˘e˘UˇZ),1(ˆs)],log˘e(1−ˆYˇZ(ˆs)))=log˘eˇZ. |
(2) Boundedness:If ˇZp=([ˆWp,˘Up],ˆYp)(p=1,2,⋯,n) is a collection of CNs, let ˇZ−=min(ˇZ1,⋯,ˇZn) and ˇZ+=max(ˇZ1,ˇZ2,⋯,ˇZn). Then,
ˇZ−≤log−CWA(ˇZ1,ˇZ2,⋯,ˇZn)≤ˇZ+ | (4.4) |
where ˘e1=˘e2=⋯=˘en=˘e.
Proof. Let, ˇZp=([ˆWp,˘Up],ˆYp),(p=1,2,⋯,n) be a collection of CNs and ˇZ−=min(ˇZ1,⋯,ˇZn), ˇZ+=max(ˇZ1,ˇZ2,⋯,ˇZn). We have the following inequalities.
minp{[ˆWp,˘Up]}≤[ˆWp,˘Up]≤maxp{[ˆWp,˘Up]}minp{ˆYp}≤ˆYp≤maxp{ˆYp}. |
It follows that
[1−n∏p=1(log˘ep(ˆWp))ϖP,1−n∏p=1(log˘ep(˘Up))ϖP]≥[1−n∏p=1(log˘ep(minp{ˆWp}))ϖP,1−n∏p=1(log˘ep(minp{˘Up}))ϖP]=[1−(log˘ep(minp{ˆWp}))n∑p=1ϖP,1−(log˘ep(minp{˘Up}))n∑p=1ϖP]=[1−(log˘ep(minp{ˆWp})),1−(log˘ep(minp{˘Up}))]n∏p=1(log˘ep(1−ˆYp))ϖP≥n∏p=1(log˘ep(1−minp{ˆYp}))ϖP=(log˘ep(1−minp{ˆYp}))n∑p=1ϖP=(log˘ep(1−minp{ˆYp})) |
[1−n∏p=1(log˘ep(ˆWp))ϖP,1−n∏p=1(log˘ep(˘Up))ϖP]≤[1−n∏p=1(log˘ep(maxp{ˆWp}))ϖP,1−n∏p=1(log˘ep(maxp{˘Up}))ϖP]=[1−n∏p=1(log˘ep(maxp{ˆWp}))n∑p=1ϖP,1−n∏p=1(log˘ep(maxp{˘Up}))n∑p=1ϖP]=[1−n∏p=1(log˘ep(maxp{ˆWp})),1−n∏p=1(log˘ep(maxp{˘Up}))]n∏p=1(log˘ep(1−ˆYp))ϖP≤n∏p=1(log˘ep(1−maxp{ˆYp}))ϖP=(log˘ep(1−maxp{ˆYp}))n∑p=1ϖP=(log˘ep(1−maxp{ˆYp})). |
Therefore, we have
ˇZ−≤log−CFWA(ˇZ1,ˇZ2,...,ˇZn)≤ˇZ+. |
(3) Monotonicity: Let ˇZp=([ˆWp,˘Up],ˆYp) and ˇZ∗p=([ˆW∗p,˘U∗p],ˆY∗p),(p=1,2,⋯,n) be a collections of CNs, if [ˆWp,˘Up]≤[ˆW∗p,˘U∗p] and ˆYp≥ˆY∗p, with 0<˘ep≤min([ˆWp,˘Up],[ˆW∗p,˘U∗p])≤1, hold for any p, then
log−CWA(ˇZ1,⋯,ˇZn)=log−CFWG(ˇZ∗1,⋯,ˇZ∗n) | (4.5) |
where ˘e1=˘e2=...=˘en=˘e.
Proof. Let
ˇZp=log−CWA(ˇZ1,...,ˇZn)=([1−n∏p=1(log˘ep(ˆWp))ϖP,1−n∏p=1(log˘ep(˘Up))ϖP],n∏p=1(log˘ep(1−ˆYp))ϖP) |
and
ˇZ∗p=log−CWA(ˇZ∗1,...,ˇZ∗n)=([1−n∏p=1(log˘ep(ˆW∗p))ϖP,1−n∏p=1(log˘ep(˘U∗p))ϖP],n∏p=1(log˘ep(1−ˆY∗p))ϖP) |
altough [ˆWˇZp,˘UˇZp]≤[ˆW∗ˇZp,˘U∗ˇZp] and ˆYˇZp≥ˆY∗ˇZp for any p, giving
[1−n∏p=1(log˘ep(ˆWp))ϖP,1−n∏p=1(log˘ep(˘Up))ϖP]≤[1−n∏p=1(log˘ep(ˆW∗p))ϖP,1−n∏p=1(log˘ep(˘U∗p))ϖP]n∏p=1(log˘ep(1−ˆYp))ϖP≥n∏p=1(log˘ep(1−ˆYp))ϖP. |
Therefore, by using the score function and accuracy function, we can conclude that
log−CWA(ˇZ1,...,ˇZn)=log−CWG(ˇZ∗1,...,ˇZ∗n). |
Definition 4.2.Let ˇZp=([ˆWˇZp,˘UˇZp],ˆYˇZp) where (p=1,2,...,n) be a collection of cubic numbers with 0<˘ep≤[ˆWp,˘Up]≤1, and ˘ep≠1. Then, the mapping log−CWA:ˇRn⟶ˇR, is defined as
log−COWA(ˇZ1,...,ˇZn)=n⨁p=1ϖp.log˘epˇZp. | (4.6) |
Thus, the function log-CWA is known as the logarithmic cubic ordered weighted averaging operator, where the weighed vectors are denoted by ϖ=(ϖ1,ϖ2,...,ϖn)T of log˘epˇZp(p=1,2,...,n), subject to ϖp∈[0,1], and their sum is always equal to 1.
Theorem 4.2. Let ˇZp=([ˆWp,˘Up],ˆYp)(p=1,...,n) be a collections of CNs with 0<˘ep≤[ˆWp,˘Up]≤1, and ˘ep≠1, that is, p=1,2,...,n. Then, utilized Definition 4.2, we have
log−COWA(ˇZ1,...,ˇZn)=([1−n∏p=1(log˘ep(ˆWp))ϖP,1−n∏p=1(log˘ep(˘Up))ϖP],n∏p=1(log˘ep(1−ˆYp))ϖP). | (4.7) |
Proof. For proof, see Appendix G.
(1) Idempotency:Let ˇZp=([ˆWp,˘Up],ˆYp),(p=1,2,..,n) be a collection of CNs are equal, i.e., ˇZp=ˇZ,(p=1,2,...,n). Then,
log−COWA(ˇZ1,...,ˇZn)=log˘eˇZ | (4.8) |
where ˘e1=˘e2=...=˘en=˘e.
(2) Boundedness:If ˇZp=([ˆWp,˘Up],ˆYp)(p=1,2,⋯,n) be a collection of CNs. Let ˇZ−=min(ˇZ1,...,ˇZn) and ˇZ+=max(ˇZ1,ˇZ2,...,ˇZn). Then,
ˇZ−≤log−COWA(ˇZ1,ˇZ2,⋯,ˇZn)≤ˇZ+ | (4.9) |
where ˘e1=˘e2=⋯=˘en=˘e.
(3) Monotonicity: Let ˇZp=([ˆWp,˘Up],ˆYp) and ˇZ∗p=([ˆW∗p,˘U∗p],ˆY∗p),(p=1,2,⋯,n) be a family of cubic numbers, if [ˆWp,˘Up]≤[ˆW∗p,˘U∗p] and ˆYp≥ˆY∗p, also 0<˘ep≤min([ˆWp,˘Up],[ˆW∗p,˘U∗p])≤1, holds for any p, then
log−COWA(ˇZ1,⋯,ˇZn)≤log−CWG(ˇZ∗1,⋯,ˇZ∗n) | (23) |
where˘e1=˘e2=⋯=˘en=˘e.
The logarithmic cubic weighted geometric and log-CFOWG aggregation operators, as well as their properties, are defined and explained in this portion of the paper.
Definition 5.1.Let ˇZp=([ˆWp,˘Up],ˆYp) (p=1,2,⋯,n) be a collection of cubic numbers with condition 0<˘ep≤[ˆWp,˘Up]≤1, and ˘ep≠1. Then, the mapping log−CWG:ˇRn⟶ˇR, defined as
log−CWG(ˇZ1,⋯,ˇZn)=n⨂p=1(log˘epˇZp)ϖp, | (5.1) |
is called the logarithmic cubic weighted geometric operator of dimension n. Where ϖ=(ϖ1,⋯,ϖn)T are the weight vector of log˘epˇZp (p=1,2,⋯,n), such that ϖp∈[0,1],∑np=1ϖp=1. And also we have take ˘e1=˘e2=⋯=˘en=˘e.
Theorem 5.1. Let there be a collection of cubic numbers ˇZp=((ˆWp,˘Up),ˆYp),(p=1,2,⋯,n) with condition 0<ˇep≤[ˆWp,˘Up]≤1, and ˇep≠1. Then, utilizing the log-CWG operator the aggregated value is also a logarithmic cubic number. Hence,
log−CWG(ˇZ1,...,ˇZn)=([n∏p=1(1−log˘ep(ˆWp))ϖP,n∏p=1(1−log˘ep(˘Up))ϖP],1−n∏p=1(1−log˘ep(1−ˆYp))ϖP). | (5.2) |
Proof. For proof, see Appendix H.
(1) Idempotency:Let ˇZp=([ˆWp,˘Up],ˆYp)(p=1,2,...,n) be a collection of cubic numbers and all the CNs are equal, i.e., ˇZp=ˇZ,(p=1,2,...,n). Then,
log−CWG(ˇZ1,...,ˇZn)=log˘eˇZ | (5.3) |
where ˘e1=˘e2=...=˘en=˘e.
(2) Boundedness:If ˇZp=([ˆWp,˘Up],ˆYp),(p=1,2,...,n) is a family of CNs, let ˇZ−=min(ˇZ1,...,ˇZn) and ˇZ+=max(ˇZ1,ˇZ2,...,ˇZn). Then,
ˇZ−≤log−CWG(ˇZ1,ˇZ2,⋯,ˇZn)≤ˇZ+ | (5.4) |
where ˘e1=˘e2=⋯=˘en=˘e.
(3) Monotonicity: Let ˇZp=([ˆWp,˘Up],ˆYp) and ˇZ∗p=([ˆW∗p,˘U∗p],ˆY∗p), (p=1,2,...,n) be a collections of cubic numbers. If [ˆWp,˘Up]≤[ˆW∗p,˘U∗p] and ˆYp≥ˆY∗p, with 0<˘ep≤min([ˆWp,˘Up],[ˆW∗p,˘U∗p])≤1, holds for any p, then
log−CWG(ˇZ1,...,ˇZn)≤log−CWG(ˇZ∗1,...,ˇZ∗n) | (5.5) |
where ˘e1=˘e2=...=˘en=˘e.
Definition 5.2.Let the collection of the cubic numbers are ˇZp=([ˆWp,˘Up],ˆYp)(p=1,2,...,n) with condition 0<˘ep≤[ˆWp,˘Up]≤1, and ˘ep≠1. Then, the mapping log−COWG:ˇRn⟶ˇR, defined as
log−COWG(ˇZ1,...,ˇZn)=n⨂p=1(log˘eˇZˇz(p))ϖp, | (5.6) |
is called the logarithmic cubic ordered weighted geometric operator of dimension n. The permutations are denoted by (ˇz(1),ˇz(2),...,ˇz(n)) of (p=1,2,...,n), such that ˇZˇz(p−1)≥ˇZˇz(p), for all p=1,2,...,n. Also the weighted vectors are denoted by ϖ=(ϖ1,ϖ2,⋯,ϖn)T of log˘eˇZ(p),(p=1,2,...,n), subject to ϖp∈[0,1], and their sum is always equal to one. And, we have ˘e1=˘e2=...=˘en=˘e.
Theorem 5.2. Let the collection of cubic numbers are ˇZp=([ˆWp,˘Up],ˆYp),(p=1,2,...,n) with the condition 0<˘ep≤[ˆWp,˘Up]≤1, and ˘ep≠1. Then, by utilizing the log-COWG operator the aggregated value is also a logarithmic CNs. Hence,
log−COWG(ˇZ1,...,ˇZn)=([n∏p=1(1−log˘ep(ˆWp))ϖP,n∏p=1(1−log˘ep(˘Up))ϖP],1−n∏p=1(1−log˘ep(1−ˆYp))ϖP). | (5.7) |
Proof. For proof, see Appendix I.
(1) Idempotency:Let there be a collection of cubic numbers are ˇZp=([ˆWp,˘Up],ˆYp) (p=1,2,...,n) with ˇZp=ˇZ. Then, we show that
log−COWG(ˇZ1,...,ˇZn)=logˇeˇZ | (5.8) |
where ˇe1=ˇe2=...=ˇen=ˇe.
(2) Boundedness:Let there be a collection of cubic numbers are ˇZp=([ˆWp,˘Up],ˆYp)(p=1,2,...,n). ˇZ−=min(ˇZ1,ˇZ2,...,ˇZn) and ˇZ+=max(ˇZ1,ˇZ2,...,ˇZn). Then,
ˇZ−≤log−COWG(ˇZ1,⋯,ˇZn)≤ˇZ+, | (5.9) |
where ˇe1=ˇe2=⋯=ˇen=ˇe.
(3) Monotonicity: Let ˇZp=([ˆWp,˘Up],ˆYp) and ˇZ∗p=([ˆW∗p,˘U∗p],ˆY∗p)(p=1,2,...,n) be a collections of cubic numbers. If [ˆWp,˘Up]≤[ˆW∗p,˘U∗p] and ˆYp≥ˆY∗p, with 0<ˇep≤min([ˆWp,˘Up],[ˆW∗p,˘U∗p])≤1, holds for any p, then,
log−COWG(ˇZ1,...,ˇZn)≤log−PFOWG(ˇZ∗1,...,ˇZ∗n). | (5.10) |
Definition 5.3. Let there be a collection of cubic numbers are logˇeˇZ=([1−logˇe˘U,logˇe(1−˘U)],logˇe(1−ˆY)).
Then, S is the score function of log˘eˇZ, which is defined as follows:
S(log˘eˇZ)=[(1−log˘eˆWˇZ)−log˘e(1−˘UˇZ)]−log˘e(1−ˆYˇZ),S(log˘eˇZ)∈[−1,1]. |
ˆS be the accuracy degree of log˘eˇZ and is defined as follows:
ˆS(log˘eˇZ)=[(1−log˘eˆWˇZ)+log˘e(1−˘UˇZ)]+log˘e(1−ˆYˇZ),ˆS(log˘eˇZ)∈[0,1] |
(1) If S(log˘eˇZ1)>S(log˘eˇZ2), then log˘eˇZ1>log˘eˇZ2.
(2) If S(log˘eˇZ1)=S(log˘eˇZ2), then if ˆS(log˘eˇZ1)>ˆS(log˘eˇZ2), then log˘eˇZ1>log˘eˇZ2.
(3) If ˆS(log˘eˇZ1)=ˆS(log˘eˇZ2), then log˘eˇZ1=log˘eˇZ2.
This part tackles the MAGDM problem using the previously mentioned aggregation operations. An example is given to demonstrate the superiority as well as the validity of the introduced operators in a real-life scenario. Let the finite set of m alternatives be ˘U={u1,u2,...,um}, and the finite set of n attribute is ˇZ={z1,z2,...,zn}. The weight vector of attributes is ϖ=(ϖ1,ϖ2,⋯,ϖn)T, such that ϖp∈[0,1], ∑np=1ϖp=1. Let the decision matrices (DMs) as follows:
![]() |
By using the log-CWA, log-COWA, log-CWG, and log-CWG operators, we intend to solve the MAGDM issue using cubic fuzzy information using the following algorithm.
Step 1.Make the decision matrices (DMs).
Step 2.Normalize the given decision matrices (DMs).
Step 3. Use the introduced operators to combine the preferences of the DMs of various types.
Step 4.Use the Definition of the score function to calculate the score value.
Step 5.On the basis of the score function, rank all of the possibilities and choose the best one.
Figure 1 shows the algorithm of the proposed method.
Education plays a vital role in the development of society and individual behavior. For that purpose, the role of teachers is the most important in delivering and transferring of knowledge and experience to students in a healthy and effective environment with smoothness and easy way. The relationship of teacher to student in this sense is like a backbone in the body. If there is more effective ways and suitable environment for sharing knowledge there will be the best outcomes of it. The flow of knowledge between teacher and student plays a key role in that scenario. We have studied and observed the difference between the flow and gaining of knowledge between students and teacher before and after the Covid-19 pandemic. We have found very vivid clues of teacher teaching effect before Covid-19, and the effects on students today has a clear difference.
Knowledge flow between Students and teacher before and after Covid-19 in colleges:
R1: Face to face interaction
Teacher student interaction in the classroom before Covid was face to face interaction. The teacher was teaching everything in a friendly environment with direct student interaction. However this effective way of teaching with face to face interaction has vanished because of Covid-19, which creates hurdles in the way of transferring knowledge from teacher to students.
R2: Attention
Face to face interaction was interrupted by the arrival of Covid-19. Before Covid, the relationship between teacher and student was so closed which was showing their strong connection whenever students lost their attention during class from their particular topic, teachers were always there to help them pay their attention again. However now, using virtual classrooms, that strong bonding between teacher and students has lost and students lose their attention. Such teaching method includes not powerful visual presentations because the teacher didn't see whether students are attentive or not. Finally, we come to the conclusion that taking classes from home fuels a disturbing environment that leads to losing attention, etc.
R3: Performance
Performances of students are getting worse because of the lack of face to face interaction in the classroom between teacher and student and the lack of full attention. This badly effects students performance. They lose their vocabulary skills, fluency, sharpness, and obedience, etc. Informal environment of class at home leads to disturbed patterns of gaining knowledge that directly affects student performance.
R4: Interest
Interest is something really important for achieving goals. Online classes create a situation in which students cannot hold their interest in studies. When the students pick up a cell phone and get on the internet, a lot of unwanted notifications start coming, which attract students toward unproductive things. Especially immature students can easily lose their attention to other things than studies and taking classes.
Step 1.Decision matrices given by three experts are given in Tables 1–4.
C1 | C2 | C3 C4 C5 | |
R1 | ([.11,.15],.23) | ([.13,.18],.32) | ([.11,.21],.20) ([.26,.27],.12) ([.16,.18],.23) |
R2 | ([.19,.20],.25) | ([.17,.18],.29) | ([.25,.26],.19) ([.17,.18],.25) ([.21,.22],.15) |
R3 | ([.12,.14],.20) | ([.14,.16],.26) | ([.15,.16],.23) ([.21,.22],.16) ([.17,.18],.22) |
R4 | ([.16,.17],.40) | ([.20,.21],.21) | ([.24,.25],.21) ([.31,.32],.23) ([.30,.31],.25) |
Step 2.We do not need to normalize the data because all the criteria are of the same type.
Step 3.Use the methods that have been introduced, which are listed below.
First, we utilized the log-CWA operator, and we obtained Table 5.
R1 | ([0.381,0.466],0.055) |
R2 | ([0.449,0.494],0.050) |
R3 | ([0.307,0.367],0.051) |
R4 | ([0.449,0.486],0.055) |
Second, we utilized the log-CWG operator, and we get Table 6.
R1 | ([0.419,0.497],0.053) |
R2 | ([0.456,0.499],0.049) |
R3 | ([0.347,0.402],0.051) |
R4 | ([0.453,0.489],0.053) |
Third, we utilized the log-COWA operator, and we get Table 7.
R1 | ([0.275,0.430],0.060) |
R2 | ([0.368,0.456],0.055) |
R3 | ([0.244,0.327],0.052) |
R4 | ([0.372,0.443],0.059) |
Fourth, we utilized the log-COWG operator, and we get Table 8.
R1 | ([0.312,0.463],0.059) |
R_{2} | \left(\left[ 0.386, 0.465\right], 0.055\right) |
R_{3} | \left(\left[ 0.272, 0.361\right], 0.051\right) |
R_{4} | \left(\left[ 0.376, 0.447\right], 0.059\right) |
Step 4.The following score values are obtained by using the score function (see Table 9).
Proposed Operators | Score value | |||
S\left(R_{1}\right) | S\left(R_{2}\right) | S\left(R_{3}\right) | S\left(R_{4}\right) | |
\log -CWA | 0.264 | 0.297 | 0.207 | 0.293 |
\log -COWA | 0.287 | 0.302 | 0.232 | 0.296 |
\log -CWG | 0.215 | 0.256 | 0.173 | 0.252 |
\log -COWG | 0.238 | 0.265 | 0.194 | 0.254 |
Step 5.Thus, from the obtained score values, we get the ranking of the attributes, as shown in Table 10.
Proposed operators | Ranking |
\log -CWA | R_{2} > R_{4} > R_{1} > R_{3} |
\log -COWA | R_{2} > R_{4} > R_{1} > R_{3} |
\log -CWG | R_{2} > R_{4} > R_{1} > R_{3} |
\log -COWG | R_{2} > R_{4} > R_{1} > R_{3} |
Hence, R_{2} is our best choice.
In Figure 2, we show the ranking of the alternative graphically.
Uncertain outcomes are a result of the fact that, when applied to the same decision making problem, several MAGDM methods provide different assessments (rankings). In order to assess the validity and reliability of the MAGDM method, we consider the following.
Test criteria on 1:The MAGDM method works well when the best alternative is kept as the default, and the non-optimal alternative is changed to a worse alternative without altering the relative importance of any decision attribute.
Test criteria on 2:Transitive qualities should be followed by an effective MAGDM strategy.
Test criteria on 3:When the MAGDM problem is divided into smaller problems and these smaller problems, are subjected to the proposed MAGDM approach for the ranking of alternatives, the MAGDM approach is effective. The cumulative rating of the options maintains consistency with the ranking of the original problem.
The following attributes are used to evaluate the suggested solution's validity.
In order to assess the viability of the established technique using criteria on 1, the worst alternative R_{4}^{/} is substituted for the non-optimal alternative R_{4}^{/} for each expert in the original decision matrix, and the rating values are provided in Table 11.
\ \ \ \ \ \ \ \ \ C_{1} | \ \ \ \ \ \ \ \ \ C_{2} | \ \ \ \ \ \ \ \ \ \ C_{3} \ \ \ \ \ \ \ \ \ \ C_{4} \ \ \ \ \ \ \ \ \ \ C_{5} | |
E^{1} | \left(\left[.14, .15\right], .26\right) | \left(\left[.11, .14\right], .31\right) | \left(\left[.18, .20\right], .23\right) \left([.16, .17, .40\right) \left(\left[.16, .17\right], .23\right) |
E^{2} | \left([.26, .27], .12\right) | \left(\left[.14, .15\right], .26\right) | \left(\left[.20, .21\right], .31\right) \left(\left[.20, .22\right], .21\right) \left(\left[.12, .15\right], .20\right) |
E^{3} | \left(\left[.24, .25\right], .21\right) | \left(\left[.11, .13\right], .20\right) | \left(\left[.31, .32\right], .13\right) \left(\left[.17, .18\right], .22\right) \left(\left[.13, .15\right], .32\right) |
E^{4} | \left(\left[.17, .18\right], .25\right) | \left(\left[.16, .17\right], .40\right) | \left(\left[.21, .22\right], .16\right) \left(\left[.21, .22\right], .25\right) \left(\left[.17, .18\right], .29\right) |
Now, utilizing the \log -CWA operator in Step 3 on transferring alternative, we get the computed scores of the alternatives are S(R_{1}) = 0.234, S(R_{2}) = 0.265, S(R_{3}) = 0.223, S(R_{4}) = 0.245 . As a result, the final ranking of the options points to R_{2} as the best alternative, and the approach developed satisfies test criteria on 1.
We divided the initial decision-making problem into smaller decision making problems \left(R_{1}, R_{2}, R_{3}\right), \left(R_{2}, R_{3}, R_{4}\right) and \left(R_{1}, R_{3}, R_{4}\right) using these possibilities in order to test the defined MAGDM approach with criteria 2 and 3. When we use the provided MAGDM approach to solve these subproblems, the rating of the alternatives will be R_{2} > R_{1} > R_{3}, R_{2} > R_{4} > R_{3} and R_{4} > R_{1} > R_{3} . We achieve the ultimate ranking order as R_{2} > R_{4} > R_{1} > R_{3} by adding a ranking of alternatives to the smaller problems. This shows a transitive property and is equivalent to a non-decomposed problem. As a result, the criteria 2 and 3 have same best alternative as the defined MAGDM approach.
In this part, the comparing of our suggested aggregation operators to previous information aggregation operators is expressed using [10,11,18,21] aggregation operators. The STOLs for the MAGDM problem are defined for MAGDM problems with CFNs. The results and rankings are shown in Table 12. For comparison, we have solved the same numerical example present in Section 7.1 by the existing aggregation operators in [10,11,18,21]. The results are shown in Table 12. It is determined that the best option is still the same. Consequently, the new strategy is more logical than the existing one.
{\rm{Proposed\ operators}} | S\left(R_{1}\right) | S\left(R_{2}\right) | S\left(R_{3}\right) | S\left(R_{4}\right) | {\rm{Ranking}} |
Khoshaim et al. [21] | 0.139 | 0.163 | 0.109 | 0.156 | R_{2} > R_{4} > R_{1} > R_{3} |
Fahmi et al. [11] | 0.363 | 0.440 | 0.395 | 0.414 | R_{2} > R_{4} > R_{3} > R_{1} |
Fahmi et al. [10] | 0.207 | 0.224 | 0.180 | 0.195 | R_{2} > R_{1} > R_{4} > R_{3} |
Kaur et al. [18] | 0.541 | 0.563 | 0.538 | 0.551 | R_{2} > R_{4} > R_{1} > R_{3} |
We have observed the logarithmic aggregation operators, and we have suggested proposed results that are broader, are more accurate and represent a novel approach to aggregating the cubic fuzzy data. In Figure 3, we show the ranking of the alternatives using different methods.
In this study, we presented the CNs logarithmic operating laws, which are a useful addition to the currently used cubic aggregation methods. Based on logarithmic operational principles, we derived valuable operational laws under cubic information. Then, based on the developed logarithmic operational laws, a number of cubic aggregation operators were defined, including \log -CWA, \log -CWG, \log -COWA, and \log -COWG aggregation operators. We have examined a number of prerequisites for these logarithmic aggregation operations. To show the effectiveness and consistency of the suggested cubic logarithmic aggregation operators, we developed a method to handle MAGDM problems with uncertainty in the form of cubic fuzzy information. A real life example of Online study effect during Covid-19 was given in order to assess and show the applicability of our suggested technique. In order to demonstrate the superiority and the validity of the recommended aggregation methods, we employed certain existing tools. The research shows that our proposed aggregation operator outperforms the existing method in terms of reliability and accuracy. Thus, our suggested technique, logarithmic aggregation operator, provides a novel way to identify the best option in the MAGDM decision-making problem. The theory of logarithmic aggregation operators based on the CS is a very effective and dominant idea, which can be used for aggregating the collection of information into a single set. The proposed theory can easily resolve many real-life problems: for instance, artificial intelligence in education, in Health care, in business, in manufacturing, roads, machine learning, game theory, computer science and many more. Thus, our suggested technique, logarithmic aggregation operator, provides a novel way to identify the best option in the MAGDM decision-making problem.
In the future, we extended our work to other disciplines for further research, including pattern recognition, symmetric operators, power operators, Hamacher operators, Dombi operators, Einstein operator, etc.
The authors would like to thank the Deanship of Scientific Research at Umm Al-Qura University for supporting this work under grant code 22UQU4310396DSR45.
The authors declare that they have no conflicts of interest.
[1] |
M. A. Dweib, C. M. ÓBrádaigh, Extensional and shearing flow of a glass-mat-reinforced thermoplastics (GMT) material as a non-Newtonian viscous fluid, Compos. Sci. Technol., 59 (1999), 1399–1410. https://doi.org/10.1016/S0266-3538(98)00182-1 doi: 10.1016/S0266-3538(98)00182-1
![]() |
[2] |
K. A. Fisher, R. J. Wakeman, T. W. Chiu, O. F. J. Meuric. Numerical modelling of cake formation and fluid loss from non-Newtonian muds during drilling using eccentric/concentric drill strings with/without rotation, Chem. Eng. Res. Design, 78 (2000), 707–714. https://doi.org/10.1205/026387600527888 doi: 10.1205/026387600527888
![]() |
[3] |
Y. A. Berezin, V. A. Chugunov, K. Hutter, Hydraulic jumps on shallow layers of non-Newtonian fluids, J. Non-newtonian Fluid Mech., 101 (2001), 139–148. https://doi.org/10.1016/S0377-0257(01)00154-9 doi: 10.1016/S0377-0257(01)00154-9
![]() |
[4] |
H. Z. Li, Y. Mouline, N. Midoux, Modelling the bubble formation dynamics in non-Newtonian fluids, Chem. Eng. Sci., 57 (2002), 339–346. https://doi.org/10.1016/S0009-2509(01)00394-3 doi: 10.1016/S0009-2509(01)00394-3
![]() |
[5] | M. Anand, K. R. Rajagopal, A shear-thinning viscoelastic fluid model for describing the flow of blood, Int. J. Cardiovascular Medicine Sci., 4 (2004), 59–68. http://www.cs.cmu.edu/afs/cs.cmu.edu/project/taos-10/publications/MAKRR2004.pdf |
[6] |
Z. Yu, A. Wachs, Y. Peysson, Numerical simulation of particle sedimentation in shear-thinning fluids with a fictitious domain method, J. Non-Newtonian Fluid Mech., 136 (2006), 126–139. https://doi.org/10.1016/j.jnnfm.2006.03.015 doi: 10.1016/j.jnnfm.2006.03.015
![]() |
[7] |
J. Marn, P. Ternik, Laminar flow of a shear-thickening fluid in a 90 pipe bend, Fluid Dyn. Res.., 38 (2006), 295. https://doi.org/10.1016/j.fluiddyn.2006.01.003 doi: 10.1016/j.fluiddyn.2006.01.003
![]() |
[8] |
S. Guillou, R. Makhloufi, Effect of a shear-thickening rheological behaviour on the friction coefficient in a plane channel flow: A study by direct numerical simulation, J. Non-Newtonian Fluid Mech., 144 (2007), 73–86. https://doi.org/10.1016/j.jnnfm.2007.03.008 doi: 10.1016/j.jnnfm.2007.03.008
![]() |
[9] |
S. U. Siddiqui, S. Mishra, A study of modified Casson's fluid in modelled normal and stenotic capillary-tissue diffusion phenomena, Appl. Math. Comp., 189 (2007), 1048–1057. https://doi.org/10.1016/j.amc.2006.11.151 doi: 10.1016/j.amc.2006.11.151
![]() |
[10] |
M. H. Abolbashari, N. Freidoonimehr, F. Nazari, M. M. Rashidi, Analytical modeling of entropy generation for Casson nano-fluid flow induced by a stretching surface, Adv. Powder Tech., 26 (2015), 542–552. https://doi.org/10.1016/j.apt.2015.01.003 doi: 10.1016/j.apt.2015.01.003
![]() |
[11] |
K. Bhattacharyya, M. S. Uddin, G. C. Layek, Exact solution for thermal boundary layer in Casson fluid flow over permeable shrinking sheet with variable wall temperature and thermal radiation, Alex. Eng. J., 55 (2016), 1703–1712. https://doi.org/10.1016/j.aej.2016.03.010 doi: 10.1016/j.aej.2016.03.010
![]() |
[12] |
M. Abd El-Aziz, A. S. Yahya, Perturbation analysis of unsteady boundary layer slip flow and heat transfer of Casson fluid past a vertical permeable plate with Hall current, Appl. Math. Comput., 307 (2017), 146–164. https://doi.org/10.1016/j.amc.2017.02.034 doi: 10.1016/j.amc.2017.02.034
![]() |
[13] |
M. Nawaz, R. Naz, M. Awais, Magnetohydrodynamic axisymmetric flow of Casson fluid with variable thermal conductivity and free stream, Alex. Eng. J., 57 (2018), 2043–2050 https://doi.org/10.1016/j.aej.2017.05.016 doi: 10.1016/j.aej.2017.05.016
![]() |
[14] |
M. Usman, F. A. Soomro, R. Ul Haq, W. Wang, O. Defterli, Thermal and velocity slip effects on Casson nanofluid flow over an inclined permeable stretching cylinder via collocation method, Inter. J. Heat Mass Trans., 122 (2018), 1255–1263 https://doi.org/10.1016/j.ijheatmasstransfer.2018.02.045 doi: 10.1016/j.ijheatmasstransfer.2018.02.045
![]() |
[15] |
A. Tassaddiq, I. Khan, K. S. Nisar, J. Singh, MHD flow of a generalized Casson fluid with Newtonian heating: A fractional model with Mittag–Leffler memory, Alex. Eng. J., 59 (2020), 3049–3059. https://doi.org/10.1016/j.aej.2020.05.033 doi: 10.1016/j.aej.2020.05.033
![]() |
[16] |
F. Hussain, M. Nazeer, M. Altanji, A. Saleem, M. M. Ghafar, Thermal analysis of Casson rheological fluid with gold nanoparticles under the impact of gravitational and magnetic forces, Case Stud. Thermal Eng., 28 (2021), 101433. https://doi.org/10.1016/j.aej.2020.05.033 doi: 10.1016/j.aej.2020.05.033
![]() |
[17] |
M. T. Akolade, Y. O. Tijani, A comparative study of three dimensional flow of Casson–Williamson nanofluids past a riga plate: Spectral quasi-linearization approach, Part. Diff. Eqs. Appl. Math., 4 (2021), 100108. https://doi.org/10.1016/j.padiff.2021.100108 doi: 10.1016/j.padiff.2021.100108
![]() |
[18] |
B. K. Siddiqui, S. Batool, M. Y. Malik, Q. Mahmood ul Hassan, Ali S. Alqahtani, Darcy Forchheimer bioconvection flow of Casson nanofluid due to a rotating and stretching disk together with thermal radiation and entropy generation, Case Studies Thermal Eng., 27 (2021), 101201. https://doi.org/10.1016/j.csite.2021.101201 doi: 10.1016/j.csite.2021.101201
![]() |
[19] |
S. G. Bejawada, Y. D. Reddy, W. Jamshed, K. Sooppy Nisar, A. N. Alharbi, R. Chouikh. Radiation effect on MHD Casson fluid flow over an inclined non-linear surface with chemical reaction in a Forchheimer porous medium, Alex. Eng. J., 61 (2022), 8207–8220. https://doi.org/10.1016/j.aej.2022.01.043 doi: 10.1016/j.aej.2022.01.043
![]() |
[20] |
M. R. Khan, A. S. Al-Johani, A. MA Elsiddieg, T. Saeed, A. Mousa Abd Allah, The computational study of heat transfer and friction drag in an unsteady MHD radiated Casson fluid flow across a stretching/shrinking surface, Int. Comm. Heat Mass Trans., 130 (2022), 105832. https://doi.org/10.1016/j.icheatmasstransfer.2021.105832 doi: 10.1016/j.icheatmasstransfer.2021.105832
![]() |
[21] |
A. C. Venkata Ramudu, K. Anantha Kumar, V. Sugunamma, N. Sandeep, Impact of Soret and Dufour on MHD Casson fluid flow past a stretching surface with convective–diffusive conditions, J. Therm. Anal. Calorim., 147 (2022), 1–11. https://doi.org/10.1007/s10973-021-10569-w doi: 10.1007/s10973-021-10569-w
![]() |
[22] |
T. Hayat, S. A. Khan, S. Momani, Finite difference analysis for entropy optimized flow of Casson fluid with thermo diffusion and diffusion-thermo effects, Inter. J. Hydrogen Ener., 47 (2022), 8048–8059. https://doi.org/10.1016/j.ijhydene.2021.12.093 doi: 10.1016/j.ijhydene.2021.12.093
![]() |
[23] |
M. Afrand, N. Sina, H. Teimouri, A. Mazaheri, M. R. Safaei, M. H. Esfe, et al., Effect of magnetic field on free convection in inclined cylindrical annulus containing molten potassium, Inter. J. Appl. Mech., 7 (2015), 1550052. https://doi.org/10.1142/S1758825115500520 doi: 10.1142/S1758825115500520
![]() |
[24] |
M. S. Dehghani, D. Toghraie, B. Mehmandoust, Effect of MHD on the flow and heat transfer characteristics of nanofluid in a grooved channel with internal heat generation, Inter. J. Num. Methods. Heat Fluid Flow., 29 (2018), 1403–1431. https://doi.org/10.1108/HFF-05-2018-0235 doi: 10.1108/HFF-05-2018-0235
![]() |
[25] |
K. Ur, Rehman, M. Awais, A. Hussain, N. Kousar, M. Y. Malik, Mathematical analysis on MHD Prandtl‐Eyring nanofluid new mass flux conditions, Math. Method. Appl. Sci., 42 (2019), 24–38. https://doi.org/10.1002/mma.5319 doi: 10.1002/mma.5319
![]() |
[26] |
K. Ur. Rehman, W. Shatanawi, S. Yaseen, A comparative numerical study of heat and mass transfer individualities in Casson stagnation point fluid flow past a flat and cylindrical surfaces, Mathematics., 11 (2023), 470. https://doi.org/10.3390/math11020470 doi: 10.3390/math11020470
![]() |
[27] |
K. Ur. Rehman, W. Shatanawi, U. Firdous, A comparative thermal case study on thermophysical aspects in thermally magnetized flow regime with variable thermal conductivity, Case Stud. Therm. Eng., 44 (2023), 102839. https://doi.org/10.1016/j.csite.2023.102839 doi: 10.1016/j.csite.2023.102839
![]() |
[28] |
G. Tunc, Y. Bayazitoglu, Heat transfer in microtubes with viscous dissipation, Inter. J. Heat Mass Trans., 44 (2001), 2395–2403. https://doi.org/10.1016/S0017-9310(00)00298-2 doi: 10.1016/S0017-9310(00)00298-2
![]() |
[29] |
K. Ur. Rehman, Q. M. Al-Mdallal, M. Y. Malik, Symmetry analysis on thermally magnetized fluid flow regime with heat source/sink, Case Stud. Therm. Eng., 14 (2019), 100452. https://doi.org/10.1016/j.csite.2019.100452 doi: 10.1016/j.csite.2019.100452
![]() |
[30] |
P. Barnoon, D. Toghraie, R. B. Dehkordi, H. Abed, MHD mixed convection and entropy generation in a lid-driven cavity with rotating cylinders filled by a nanofluid using two phase mixture model, J. Magnet. Magnet. Material, 483 (2019), 224–248. https://doi.org/10.1016/j.jmmm.2019.03.108 doi: 10.1016/j.jmmm.2019.03.108
![]() |
[31] |
D. Toghraie, Numerical simulation on MHD mixed convection of Cu-water nanofluid in a trapezoidal lid-driven cavity, Inter. J. Appl. Electrom., 62 (2020), 683–710. https://doi.org/10.3233/JAE-190123 doi: 10.3233/JAE-190123
![]() |
[32] |
H. Sadaf, Z. Asghar, N. Iftikhar, Cilia-driven flow analysis of cross fluid model in a horizontal channel, Comp. Part. Mech., (2022), 1–8. https://doi.org/10.1007/s40571-022-00539-w doi: 10.1007/s40571-022-00539-w
![]() |
[33] |
A. Aabid, S. Afghan Khan, M. Baig, Numerical analysis of a microjet-based method for active flow control in convergent-divergent nozzles with a sudden expansion duct, Fluid Dynam. Mater. Process., 18 (2022), 1–24. https://doi.org/10.32604/fdmp.2022.021860 doi: 10.32604/fdmp.2022.021860
![]() |
[34] |
I. S. Hussain, D. Prakash, B. Abdalla, M. Muthtamilselvan, Analysis of Arrhenius activation energy and chemical reaction in nanofluid flow and heat transfer over a thin moving needle, Current Nanosci., 19 (2023), 39–48. https://doi.org/10.2174/1573413717666211117150656 doi: 10.2174/1573413717666211117150656
![]() |
[35] |
K. Ur Rehman, A. Batur Çolak, W. Shatanawi, Artificial neural networking (ANN) model for drag coefficient optimization for various obstacles, Mathematics, 10 (2022), 2450. https://doi.org/10.3390/math10142450 doi: 10.3390/math10142450
![]() |
[36] |
A. B. Çolak, An experimental study on the comparative analysis of the effect of the number of data on the error rates of artificial neural networks, Int. J. Ener. Resear., 45 (2021), 478–500. https://doi.org/10.1002/er.5680 doi: 10.1002/er.5680
![]() |
[37] |
A. Shafiq, A. Batur Çolak, T. Naz Sindhu, Designing artificial neural network of nanoparticle diameter and solid–fluid interfacial layer on single‐walled carbon nanotubes/ethylene glycol nanofluid flow on thin slendering needles, Int. J. Num. Methods Fluids, 93 (2021), 3384–3404. https://doi.org/10.1002/fld.5038 doi: 10.1002/fld.5038
![]() |
[38] |
A. Shafiq, A. Batur Çolak, T. Naz Sindhu, Q. M. Al-Mdallal, T. Abdeljawad, Estimation of unsteady hydromagnetic Williamson fluid flow in a radiative surface through numerical and artificial neural network modeling, Sci. Rep., 11 (2021), 14509. https://doi.org/10.1038/s41598-021-93790-9 doi: 10.1038/s41598-021-93790-9
![]() |
[39] |
A. B. Colak, Experimental study for thermal conductivity of water‐based zirconium oxide nanofluid: developing optimal artificial neural network and proposing new correlation, Int. J. Energy Res., 45 (2021), 2912–2930. https://doi.org/10.1002/er.5988 doi: 10.1002/er.5988
![]() |
[40] |
M. Adamu, A. Batur Çolak, Y. E. Ibrahim, S. I. Haruna, M. F. Hamza, Prediction of mechanical properties of rubberized concrete incorporating fly ash and nano silica by artificial neural network technique, Axiom., 12 (2023), 81. https://doi.org/10.3390/axioms12010081 doi: 10.3390/axioms12010081
![]() |
\ \ \ \ \ \ \ \ \ C_{1} | \ \ \ \ \ \ \ \ \ \ C_{2} | \ \ \ \ \ \ \ \ \ \ \ C_{3} \ \ \ \ \ \ \ \ \ \ \ C_{4} \ \ \ \ \ \ \ \ \ \ C_{5} | |
R_{1} | \left([.11, .15], .23\right) | \left([.13, .18], .32\right) | \left([.11, .21], .20\right) \left([.26, .27], .12\right) \left([.16, .18], .23\right) |
R_{2} | \left([.19, .20], .25\right) | \left([.17, .18], .29\right) | \left([.25, .26], .19\right) \left([.17, .18], .25\right) \left([.21, .22], .15\right) |
R_{3} | \left([.12, .14], .20\right) | \left([.14, .16], .26\right) | \left([.15, .16], .23\right) \left([.21, .22], .16\right) \left([.17, .18], .22\right) |
R_{4} | \left([.16, .17], .40\right) | \left([.20, .21], .21\right) | \left([.24, .25], .21\right) \left([.31, .32], .23\right) \left([.30, .31], .25\right) |
R_{1} | \left(\left[ 0.381, 0.466\right], 0.055\right) |
R_{2} | \left(\left[ 0.449, 0.494\right], 0.050\right) |
R_{3} | \left(\left[ 0.307, 0.367\right], 0.051\right) |
R_{4} | \left(\left[ 0.449, 0.486\right], 0.055\right) |
R_{1} | \left(\left[ 0.419, 0.497\right], 0.053\right) |
R_{2} | \left(\left[ 0.456, 0.499\right], 0.049\right) |
R_{3} | \left(\left[ 0.347, 0.402\right], 0.051\right) |
R_{4} | \left(\left[ 0.453, 0.489\right], 0.053\right) |
R_{1} | \left(\left[ 0.275, 0.430\right], 0.060\right) |
R_{2} | \left(\left[ 0.368, 0.456\right], 0.055\right) |
R_{3} | \left(\left[ 0.244, 0.327\right], 0.052\right) |
R_{4} | \left(\left[ 0.372, 0.443\right], 0.059\right) |
R_{1} | \left(\left[ 0.312, 0.463\right], 0.059\right) |
R_{2} | \left(\left[ 0.386, 0.465\right], 0.055\right) |
R_{3} | \left(\left[ 0.272, 0.361\right], 0.051\right) |
R_{4} | \left(\left[ 0.376, 0.447\right], 0.059\right) |
Proposed Operators | Score value | |||
S\left(R_{1}\right) | S\left(R_{2}\right) | S\left(R_{3}\right) | S\left(R_{4}\right) | |
\log -CWA | 0.264 | 0.297 | 0.207 | 0.293 |
\log -COWA | 0.287 | 0.302 | 0.232 | 0.296 |
\log -CWG | 0.215 | 0.256 | 0.173 | 0.252 |
\log -COWG | 0.238 | 0.265 | 0.194 | 0.254 |
Proposed operators | Ranking |
\log -CWA | R_{2} > R_{4} > R_{1} > R_{3} |
\log -COWA | R_{2} > R_{4} > R_{1} > R_{3} |
\log -CWG | R_{2} > R_{4} > R_{1} > R_{3} |
\log -COWG | R_{2} > R_{4} > R_{1} > R_{3} |
\ \ \ \ \ \ \ \ \ C_{1} | \ \ \ \ \ \ \ \ \ C_{2} | \ \ \ \ \ \ \ \ \ \ C_{3} \ \ \ \ \ \ \ \ \ \ C_{4} \ \ \ \ \ \ \ \ \ \ C_{5} | |
E^{1} | \left(\left[.14, .15\right], .26\right) | \left(\left[.11, .14\right], .31\right) | \left(\left[.18, .20\right], .23\right) \left([.16, .17, .40\right) \left(\left[.16, .17\right], .23\right) |
E^{2} | \left([.26, .27], .12\right) | \left(\left[.14, .15\right], .26\right) | \left(\left[.20, .21\right], .31\right) \left(\left[.20, .22\right], .21\right) \left(\left[.12, .15\right], .20\right) |
E^{3} | \left(\left[.24, .25\right], .21\right) | \left(\left[.11, .13\right], .20\right) | \left(\left[.31, .32\right], .13\right) \left(\left[.17, .18\right], .22\right) \left(\left[.13, .15\right], .32\right) |
E^{4} | \left(\left[.17, .18\right], .25\right) | \left(\left[.16, .17\right], .40\right) | \left(\left[.21, .22\right], .16\right) \left(\left[.21, .22\right], .25\right) \left(\left[.17, .18\right], .29\right) |
{\rm{Proposed\ operators}} | S\left(R_{1}\right) | S\left(R_{2}\right) | S\left(R_{3}\right) | S\left(R_{4}\right) | {\rm{Ranking}} |
Khoshaim et al. [21] | 0.139 | 0.163 | 0.109 | 0.156 | R_{2} > R_{4} > R_{1} > R_{3} |
Fahmi et al. [11] | 0.363 | 0.440 | 0.395 | 0.414 | R_{2} > R_{4} > R_{3} > R_{1} |
Fahmi et al. [10] | 0.207 | 0.224 | 0.180 | 0.195 | R_{2} > R_{1} > R_{4} > R_{3} |
Kaur et al. [18] | 0.541 | 0.563 | 0.538 | 0.551 | R_{2} > R_{4} > R_{1} > R_{3} |
\ \ \ \ \ \ \ \ \ C_{1} | \ \ \ \ \ \ \ \ \ \ C_{2} | \ \ \ \ \ \ \ \ \ \ \ C_{3} \ \ \ \ \ \ \ \ \ \ \ C_{4} \ \ \ \ \ \ \ \ \ \ C_{5} | |
R_{1} | \left([.11, .15], .23\right) | \left([.13, .18], .32\right) | \left([.11, .21], .20\right) \left([.26, .27], .12\right) \left([.16, .18], .23\right) |
R_{2} | \left([.19, .20], .25\right) | \left([.17, .18], .29\right) | \left([.25, .26], .19\right) \left([.17, .18], .25\right) \left([.21, .22], .15\right) |
R_{3} | \left([.12, .14], .20\right) | \left([.14, .16], .26\right) | \left([.15, .16], .23\right) \left([.21, .22], .16\right) \left([.17, .18], .22\right) |
R_{4} | \left([.16, .17], .40\right) | \left([.20, .21], .21\right) | \left([.24, .25], .21\right) \left([.31, .32], .23\right) \left([.30, .31], .25\right) |
R_{1} | \left(\left[ 0.381, 0.466\right], 0.055\right) |
R_{2} | \left(\left[ 0.449, 0.494\right], 0.050\right) |
R_{3} | \left(\left[ 0.307, 0.367\right], 0.051\right) |
R_{4} | \left(\left[ 0.449, 0.486\right], 0.055\right) |
R_{1} | \left(\left[ 0.419, 0.497\right], 0.053\right) |
R_{2} | \left(\left[ 0.456, 0.499\right], 0.049\right) |
R_{3} | \left(\left[ 0.347, 0.402\right], 0.051\right) |
R_{4} | \left(\left[ 0.453, 0.489\right], 0.053\right) |
R_{1} | \left(\left[ 0.275, 0.430\right], 0.060\right) |
R_{2} | \left(\left[ 0.368, 0.456\right], 0.055\right) |
R_{3} | \left(\left[ 0.244, 0.327\right], 0.052\right) |
R_{4} | \left(\left[ 0.372, 0.443\right], 0.059\right) |
R_{1} | \left(\left[ 0.312, 0.463\right], 0.059\right) |
R_{2} | \left(\left[ 0.386, 0.465\right], 0.055\right) |
R_{3} | \left(\left[ 0.272, 0.361\right], 0.051\right) |
R_{4} | \left(\left[ 0.376, 0.447\right], 0.059\right) |
Proposed Operators | Score value | |||
S\left(R_{1}\right) | S\left(R_{2}\right) | S\left(R_{3}\right) | S\left(R_{4}\right) | |
\log -CWA | 0.264 | 0.297 | 0.207 | 0.293 |
\log -COWA | 0.287 | 0.302 | 0.232 | 0.296 |
\log -CWG | 0.215 | 0.256 | 0.173 | 0.252 |
\log -COWG | 0.238 | 0.265 | 0.194 | 0.254 |
Proposed operators | Ranking |
\log -CWA | R_{2} > R_{4} > R_{1} > R_{3} |
\log -COWA | R_{2} > R_{4} > R_{1} > R_{3} |
\log -CWG | R_{2} > R_{4} > R_{1} > R_{3} |
\log -COWG | R_{2} > R_{4} > R_{1} > R_{3} |
\ \ \ \ \ \ \ \ \ C_{1} | \ \ \ \ \ \ \ \ \ C_{2} | \ \ \ \ \ \ \ \ \ \ C_{3} \ \ \ \ \ \ \ \ \ \ C_{4} \ \ \ \ \ \ \ \ \ \ C_{5} | |
E^{1} | \left(\left[.14, .15\right], .26\right) | \left(\left[.11, .14\right], .31\right) | \left(\left[.18, .20\right], .23\right) \left([.16, .17, .40\right) \left(\left[.16, .17\right], .23\right) |
E^{2} | \left([.26, .27], .12\right) | \left(\left[.14, .15\right], .26\right) | \left(\left[.20, .21\right], .31\right) \left(\left[.20, .22\right], .21\right) \left(\left[.12, .15\right], .20\right) |
E^{3} | \left(\left[.24, .25\right], .21\right) | \left(\left[.11, .13\right], .20\right) | \left(\left[.31, .32\right], .13\right) \left(\left[.17, .18\right], .22\right) \left(\left[.13, .15\right], .32\right) |
E^{4} | \left(\left[.17, .18\right], .25\right) | \left(\left[.16, .17\right], .40\right) | \left(\left[.21, .22\right], .16\right) \left(\left[.21, .22\right], .25\right) \left(\left[.17, .18\right], .29\right) |
{\rm{Proposed\ operators}} | S\left(R_{1}\right) | S\left(R_{2}\right) | S\left(R_{3}\right) | S\left(R_{4}\right) | {\rm{Ranking}} |
Khoshaim et al. [21] | 0.139 | 0.163 | 0.109 | 0.156 | R_{2} > R_{4} > R_{1} > R_{3} |
Fahmi et al. [11] | 0.363 | 0.440 | 0.395 | 0.414 | R_{2} > R_{4} > R_{3} > R_{1} |
Fahmi et al. [10] | 0.207 | 0.224 | 0.180 | 0.195 | R_{2} > R_{1} > R_{4} > R_{3} |
Kaur et al. [18] | 0.541 | 0.563 | 0.538 | 0.551 | R_{2} > R_{4} > R_{1} > R_{3} |