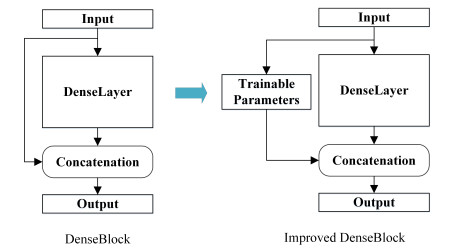
In batch operation, most industries require engineers to maintain low hardness on the welded parts, particularly for low carbon steel. This article focuses on tungsten inert gas (TIG) welding performed on 0.90 mm of a C67 grade sheet by varying different welding parameters such as current, velocity, and temperature. Samples were collected from the tool side, mid-wall, and operator side for metallographic and micro-hardness examinations considering various parameters. Without post welding heat treatment (PWHT), the welded parts were quenched at room temperature, while with PWHT the welded parts were kept at 710 ℃ for 99 s after welding, and subsequently, the samples were cooled slowly by air at ambient temperature. An increase in hardness was registered in either the fusion zone or melted zone, with decrements in the heat affected zone (HAZ) for both procedures. When the the welding was performed without PWHT, a martensitic and bainitic microstructure was noticed in the melting zone (MZ) and HAZ, respectively. In contrast, a bainitic microstructure was observed in either the melting or heat affected zone in the welding with PWHT. Metallographic images revealed crack propagation when welding was performed without PWHT. A larger HAZ was noted in the welding sample with PWHT, and hardness was also relatively lower compared the samples without PWHT. There was no significant difference in hardness among the samples taken from tool side, mid-wall, and operator side for both procedures. Finally, the lowest microhardness (265 HV) was found in the MZ when the welding was carried out with PWHT employing a 90 A current and 10 mm/s velocity.
Citation: Utpal K. Dhar, Md. Farabi Rahman, Mustafa Oguzhan Ayanoglu, Ahammad Abdullah. Welding on C67 steel grade sheet: Influence of the parameters and post welding heat treatment[J]. AIMS Materials Science, 2023, 10(3): 453-464. doi: 10.3934/matersci.2023025
[1] | Eleonora Amoroso, Angela Sciammetta, Patrick Winkert . Anisotropic (→p,→q)-Laplacian problems with superlinear nonlinearities. Communications in Analysis and Mechanics, 2024, 16(1): 1-23. doi: 10.3934/cam.2024001 |
[2] | Dan Li, Yuhua Long . On periodic solutions of second-order partial difference equations involving p-Laplacian. Communications in Analysis and Mechanics, 2025, 17(1): 128-144. doi: 10.3934/cam.2025006 |
[3] | Chunming Ju, Giovanni Molica Bisci, Binlin Zhang . On sequences of homoclinic solutions for fractional discrete p-Laplacian equations. Communications in Analysis and Mechanics, 2023, 15(4): 586-597. doi: 10.3934/cam.2023029 |
[4] | Leandro Tavares . Solutions for a class of problems driven by an anisotropic (p,q)-Laplacian type operator. Communications in Analysis and Mechanics, 2023, 15(3): 533-550. doi: 10.3934/cam.2023026 |
[5] | Xiulan Wu, Yaxin Zhao, Xiaoxin Yang . On a singular parabolic p-Laplacian equation with logarithmic nonlinearity. Communications in Analysis and Mechanics, 2024, 16(3): 528-553. doi: 10.3934/cam.2024025 |
[6] | Efstratios Stratoglou, Alexandre Anahory Simoes, Leonardo J. Colombo . Reduction in optimal control with broken symmetry for collision and obstacle avoidance of multi-agent system on Lie groups. Communications in Analysis and Mechanics, 2023, 15(2): 1-23. doi: 10.3934/cam.2023001 |
[7] | Lovelesh Sharma . Brezis Nirenberg type results for local non-local problems under mixed boundary conditions. Communications in Analysis and Mechanics, 2024, 16(4): 872-895. doi: 10.3934/cam.2024038 |
[8] | Xiaotian Hao, Lingzhong Zeng . Eigenvalues of the bi-Xin-Laplacian on complete Riemannian manifolds. Communications in Analysis and Mechanics, 2023, 15(2): 162-176. doi: 10.3934/cam.2023009 |
[9] | Hongying Jiao, Shuhai Zhu, Jinguo Zhang . Existence of infinitely many solutions for critical sub-elliptic systems via genus theory. Communications in Analysis and Mechanics, 2024, 16(2): 237-261. doi: 10.3934/cam.2024011 |
[10] | Mohamed Karim Hamdani, Lamine Mbarki, Mostafa Allaoui . A new class of multiple nonlocal problems with two parameters and variable-order fractional p(⋅)-Laplacian. Communications in Analysis and Mechanics, 2023, 15(3): 551-574. doi: 10.3934/cam.2023027 |
In batch operation, most industries require engineers to maintain low hardness on the welded parts, particularly for low carbon steel. This article focuses on tungsten inert gas (TIG) welding performed on 0.90 mm of a C67 grade sheet by varying different welding parameters such as current, velocity, and temperature. Samples were collected from the tool side, mid-wall, and operator side for metallographic and micro-hardness examinations considering various parameters. Without post welding heat treatment (PWHT), the welded parts were quenched at room temperature, while with PWHT the welded parts were kept at 710 ℃ for 99 s after welding, and subsequently, the samples were cooled slowly by air at ambient temperature. An increase in hardness was registered in either the fusion zone or melted zone, with decrements in the heat affected zone (HAZ) for both procedures. When the the welding was performed without PWHT, a martensitic and bainitic microstructure was noticed in the melting zone (MZ) and HAZ, respectively. In contrast, a bainitic microstructure was observed in either the melting or heat affected zone in the welding with PWHT. Metallographic images revealed crack propagation when welding was performed without PWHT. A larger HAZ was noted in the welding sample with PWHT, and hardness was also relatively lower compared the samples without PWHT. There was no significant difference in hardness among the samples taken from tool side, mid-wall, and operator side for both procedures. Finally, the lowest microhardness (265 HV) was found in the MZ when the welding was carried out with PWHT employing a 90 A current and 10 mm/s velocity.
In recent years, with the development of computer hardware and information technology, unmanned surface vehicles (USV) has made rapid progress and development, and it is the development trend of future ships. For example, USV can replace persons to perform a task that is dangerous or requiring long-term attendance, thereby reducing casualties and costs. In the future, USV will be widely used in marine tasks, such as environmental monitoring, search and rescue, hydrological mapping, maritime supervision and so on [1,2].
As a highly intelligent system, USV must have a stable and reliable autonomous navigation system to finish tasks. Obviously, only with the ability of environment perception, USV can deal with the complex environment. The environmental perception of USV is to obtain environmental information through multi-sensor fusion. The USV uses the highly effective computer vision method to simulate the human vision intelligent behaviour, extract the information from the complex environment to carry on the analysis and the processing, and enhances the environment perception ability. Obstacle avoidance is one of the key technologies for USV. The research on the recognition and detection of obstacle is mainly based on radar, infrared and visual images [3,4,5]. Compared with radar and infrared method, visible light vision system can obtain obstacle target information, such as texture, shape and so on, so as to improve the obstacle detection ability greatly. This paper studies the obstacle detection and classification method based on visible light for USV.
The early existing methods of detecting marine targets are mostly based on simple image processing and traditional machine learning [3,4,5,6]. These methods mainly use image pre-processing to extract edge, shape, texture and other features for target detection, or select target sample on a given image, then extract feature on the sample for training, and finally target detection by classifier. The digital image processing method is simple in operation, but limited in function, easy to be interfered by external factors, it is more suitable for the target detection of simple scene, and the detection accuracy is low in the complex environment. The traditional target detection method based on machine learning needs prior knowledge, manual extraction of features and other processes, its procedures are cumbersome, real-time and not very suitable for complex and multi-target detection tasks. Background subtraction methods were evaluated for object detection in a maritime environment is discussed in [7]. An agglomerative clustering of temporally stable features is applied for object detection in highly dynamic maritime environment in [8]. Adaptive hysteresis threshold method was applied to saliency map for boat detection in [9]. A graphical model is developed for segmentation obstacle in USV [10]. A stereo model instead of single view model is proposed for obstacles extraction in [11]. A more comprehensive review of vision-based maritime object detection and tracking can be found in reference [12].
In recent years, the target detection method based on convolutional neural network (CNN) has emerged as a cutting-edge technology [13,14,15,16,17]. This kind of target detection algorithm based on deep learning has strong intelligence ability and high detection efficiency [18]. For example, dual path network (DPN) is developed to provide better performance for object detection in [19], a modified VGG16 network architecture is proposed for visual object detection of marine surface objects in [20]. CNN was used for surface vehicle detection and tracking in [21], in which Faster R-CNN and YOLO method were employed. Semantic segmentation networks including SegNet, ENet and ESPNet were evaluated for maritime survellance in [22]. An improved Faster R-CNN method is developed for maritime target detection, in which Resnet is used to extract feature and bacth normalization layer is employed to optimize for Faster R-CNN [23]. An object detection method is proposed with fusing region based recognition and regression based location is reported in [24]. Another maritime target detection method based on hierarchical and multi-scale convolutional neural network is proposed in [25]. It used multi-scale strategy to expand region proposal to multi convolutional layers of ResNet. It also extracted target on the fourth layer instead of the last convolutional layer of R-CNN, and added deconvolution operation with bilinear interpolation for small target perception.
Recently, a USV is developed by Harbin Institute of Technology and visual camera is installed on USV for automatic obstacle avoidance [26]. Due to the obstacles are small in image and blurred in contour, it is the key to improve the accuracy of obstacles for USV. In this paper, the obstacle detection algorithm based on convolutional neural network for USV is developed. A feature pyramid method of hybrid network combining ResNet and DenseNet is proposed, which is more efficient for the obstacle detection by using the underlying multi-detail features and high-level strong semantic features in the network architecture. Experimental results show that this method has the highest detection and classification performance than other CNN based methods and is more suitable for USV.
As one of the most popular networks in the deep neural network, convolutional neural network is widely used in many fields, especially in the field of image classification and detection [27,28,29,30]. The traditional neural networks are all connected networks, the upper and lower neurons are fully connected. With the increase of the network level, the number of parameters expands, and the computational volume not only makes the network easy to fit, but also easily falls into the local optimum. Convolution networks usually include input layer, convolution layer, pooling layer and fully connected layer. The most important characteristics of convolution networks are weight sharing and sparse connection, which can greatly reduce the number of parameters of training networks and reduce the computational complexity.
Convolution kernel is the core of feature extraction in convolution network. The output pixels xlj of convolution layer are calculated as
xlj=f(ulj), | (2.1) |
ulj=∑i∈Mjxl−1i∗Wlij+blj, | (2.2) |
where f is the activation function, xl−1i is an pixel in the upper feature image layer, Wlij is the convolution kernel, the symbol ∗ is the convolution operation, blj is the bias item, Mj is the subset feature image of upper layer, l is the layer number. This convolution process is to perform convolution operation of convolution kernel to input layer image, and then the new feature image is obtained by data conversion from activation function. And ReLU function as following is selected as the activation function
max(0,x)={0,ifx≤0x,ifx>0 | (2.3) |
Pooling layer samples each input feature map through the following formula and outputs the eigenvalue
xlj=f(ulj), | (2.4) |
ulj=βljdown(xl−1j)+blj, | (2.5) |
where ulj is the j-th channel activation of l-th down-sample layer, it is obtained from down-sampling and the weighted calculation of the output feature map xl−1j from the previous layer, β is the weights. The down symbol represents the down-sample function, it divides the input feature map into several non-overlapping image blocks with size of n×n by sliding window, and then sums the pixels within each image block to find the mean or maximum value, so that the output image is reduced to 1/n by two dimensions.
The convolution kernel parameters can be trained through the following optimization loss function
C=12m∑x||y(x)−a(x)||2, | (2.6) |
where C is loss function, m is the sample number, x is samples, y is actual output, a is the network output. The goal of network training learning is to minimize the objective function, which can be accomplished by the reverse gradient descent method.
The most effective methods to improve convolutional neural networks are to improve the performance of models by deepening the network hierarchy. However, when the network layer is increased to a certain extent, the optimization function will fall into the local optimal, deviating from the global optimal, and the deepening of the network accelerates the disappearance of the gradient. In order to solve this problem, the deep residual network ResNet [31] and the densely connected network DenseNet [32] are proposed to mitigate the effect of gradient disappearance. With the deepening of the network, there are a lot of parameters to be trained in the network model. It is difficult to learn better effect from the sample of small dataset, however, large-scale dataset can not get more labeled samples by hand in some tasks. In this paper, transfer learning is used to improve the learning efficiency for the problem of small sample data.
Transfer learning is to apply the knowledge learned in one mode to another related domain for problem solving. The use of transfer learning in image detection means that the feature extraction part of convolutional neural network is trained in another large-scale data set, the corresponding training weight parameter is obtained, and then the training fine tuning of network model is carried out on the basis of the weight of the training in the small scale dataset. Therefore, in order to improve the learning efficiency of the deep neural network, we use the transfer learning in the application of the deep learning neural network for the requirement of large data and the time consuming of training. In this paper, ImageNet dataset is employed for transfer learning.
Region convolutional neural network (R-CNN) uses deep learning for object recognition and detection employing region search. Fatser R-CNN uses region proposal network (RPN) instead of selective search to speed up the object recognition and detection [13]. RPN reduces the amount of suggested box calculations by sharing the convolution layer and parallel computing. At the same time, the target border is roughly corrected by the border regression in the RPN network, and then corrected again in the final border return of the network, and the two fixes make the target more accurate. The loss function of faster R-CNN is defined as
L({pi},{ti})=1Ncls∑iLcls(pi,p∗i)+λ1Nreg∑iLreg(ti,t∗i) | (2.7) |
Lcls(pi,p∗i)=−log[p∗ipi+(1−p∗i)(1−pi)] | (2.8) |
Lreg(ti,t∗i)=R(ti−t∗i) | (2.9) |
R(x)={0.5x2,if|x|<1|x|−0.5,otherwise | (2.10) |
where i is the anchor index of batch, pi is the target prediction probability of the anchor i, if anchor is positive, the true lable probability p∗i is 1, otherwise 0. ti is a vector which represents 4 parameters coordinate, t∗i is the true boundary coordinate, Lcls(pi,p∗i) is the classification loss, and Lreg(ti,t∗i) is regression loss. Ncls and Nreg are normalized, λ is balanced weights. The 4 coordinates are as follows
{tx=(x−xa)/wa,ty=(y−ya)/ha,tw=log(w/wa),th=log(h/ha). | (2.11) |
{t∗x=(x∗−xa)/wa,t∗y=(y∗−ya)/ha,t∗w=log(w∗/wa),t∗h=log(h∗/ha), | (2.12) |
where the centre of the boundary is (x,y), w and h is width and height. Faster R-CNN detection is very accurate, but the detection speed is slow. In our USV application test, it can be performed about 5 frames per second, it cannot meet the real-time requirements of obstacle detection for USV.
Most deep learning recognition and detection algorithms use the top-level feature map for prediction, but the actual bottom level feature map contains more detailed information and more precise target location. Some other algorithms use multi-scale feature maps for prediction respectively, but mainly use high-level feature map information, such as single shot multi-box detector algorithm [33]. And network feature of feature pyramid networks (FPN) has the advantages of independent forecasts on the feature map, it is due to the fact that different depth corresponds to the different feature information [34].
The underlying high-resolution feature figure contains more details while the high-level low-resolution feature figure contains more semantic information. By fusing feature information of different layers, the efficiency of small target detection and recognition can be improved effectively. It can be seen from the structure that the main network forms different scale and different layers of pyramid feature map when propagating forward [34]. FPN propagates the multi-scale feature map from the side to the back, and the feature map of each layer fuses with the lower layer by upper sampling, and then the fused feature map of each layer is predicted separately. In the forward propagation path of the main network, the scale of feature map decreases gradually, but the semantic feature increases gradually. The reverse top-down path of FPN enhances the underlying semantic features by fused with the underlying feature map through horizontal connection, and at the same time makes better use of the underlying multi-details information. So CNN combined with FPN can further improve the detection accuracy of small targets by using multi-scale feature information. And in this paper, FPN is employed for obstacle detection and recogniton for USV.
The gradient descent technique is employed in CNN. When input information and gradient information are transferred layer by layer, the problem of gradient vanishment becomes more and more serious as the number of layers increases. This will lead to the training failure of deep neural network. The most effective way to avoid the disappearance of gradients is to establish direct connections between layers that are not adjacent to each other. DenseNet adopts this approach and achieves great success. In DenseNet, the input for each layer comes from the output of all the preceding layers. Due to each layer is connected to input and loss, it can make gradient vanishment weaken. DenseNet uses dense block to make the transmission of features and gradients more efficient, this network architecture transmit and use features more effectively.
In DenseNet, the output of the l-th layer is
yl=Fl([x0,x1,...,xl−1],Wl), | (2.13) |
where yl is the output of the l-th layer, Fl is a non-linear transformation function, xi is the input of the l-th layer (i=0,1,...,l−1.), [x0,x1,...,xl−1] refers to the concatenation of the features produced in layer 0,1,...,l−1, Wl is the parameters of Fl in the l-th layer.
In DenseNet, features of the previous layers are concatenated with the same weight, but not all these previous features are useful. An improved architecture is proposed by adding the trainable weight parameters to each skip connection [27,28]. This is shown in Figure 1.
The output of the l-th layer in this improved architecture is modified as
yl=Fl([x0kl,0,x1kl,1,...,xl−1kl,l−1],Wl), | (2.14) |
where kl,0,kl,1,...,kl,l−1 is the parameters which determinate weights of [x0,x1,...,xl−1] when they concatenate to the l−th layer. The improved dense block is efficient for image classification, and it is employed in this paper for obstacle detection of USV.
By analyzing the algorithm structure combining Faster R-CNN and FPN network, it can be seen that the network uses the fusion of the feature map of each layer and that of the previous features layer to enhance the predicted feature information. To a certain extent improve the accuracy of the small target detection and recognition, but it still has improvement space for network structure design. At present, the improvement of deep learning target detection algorithm is mainly considered from two aspects. On one hand, it can attain more detailed information by improving structure of the network. On the other hand, it can assist recogntion of small target using the peripheral object information by combining image context information and algorithm. Being combined with the context information, just like human visual identification, when information such as appearance and color cannot be attained due to far distance, small size and fuzzy contour, it can be conjectured through surrounding large target object information. This idea is similar to the language prediction of recurrent neuron network (RNN) used to establish data sequence and sequence data before and after have relatively stronger correlation. Bidirectional RNN using both front and back information when makes sentence prediction. The bidirectional RNN is shown in Figure 2.
Therefore, the idea of improvement in this paper is getting inspiration from the structure of bidirectional RNN, adding a bottom-up path to the top down path in the FPN structure, in order to improve accuracy of marine obstacle detection and recogntion for USV. The structure design is shown in Figure 3.
First, Resnet and DenseNet are used to construct a hybrid network combined with FPN, the output feature map of each layer is improved according to bidirectional architecture. The proposed bidirectional FPN architecture makes the features map of each layer not only be with the aid of the upper high semantic features, but also use the lower level detail features to assist small target classification and recognition of the current layer. Architecture in Figure 3 use the improved DenseNet described before in the hybrid network. The output feature map of each layer in the proposed bidirectional FPN is the sum of P2, P3, P4 and P5 of ResNet and DenseNet.
After reducing and enlarging, the shortest side of the input image is not less than 600 pixels and the largest edge is not more than 1024 pixels, because size setting of image clipping does affect the result of detection. Parameter limitation of 600 and 1024 has a relatively good effect. In RPN network, non-maximum suppression (NMS) is used for border selection. The judgment threshold of RPN target positive sample is set to 0.7 and negative sample is 0.3. In RPN, the proportion of border of foreground target is set to 0.5. That is, the ratio of positive and negative samples of anchor is maintained at 1:1 after selection. There are 256 anchors that are selected here, with 128 positive samples and 128 negative samples.
The training process uses subsection training method. Namely in every 10,000 times iteration training, every 1,000 times save weight value once time. The maximum primary weight of mAP (mean average precision) in the test results is found as the initial weight of the new training and repeat the replacement of the optimal initial weight. Such segmented training can prevent network over-fitting, speed up network convergence, improve the network performance of training quickly. Replace the weight several times until the detection accuracy is no longer improved. Then the final optimal training weight can be obtained.
To estimate the proposed recognition method, some other methods are employed for test. Standard Faster R-CNN [13] with VGG16 as backbone and Mask R-CNN [15], using ResNet101 as backbone with FPN are employed to compare with the method proposed in this paper. Three state-of-the-art object recognition methods reported in references are selected for comparison, they are improved Faster R-CNN [23], fusion based method which fuses region based recognition and regression based location [24], and CNN method based on multi-scale [25]. So five methods are used to compare with our proposed method, they are Faster R-CNN, Mask R-CNN, improved Faster R-CNN, fusion, and multi-scale method.
We collect 2,800 images using our own USV. As our images are collected by USV on a lake, the content of the images are not rich enough. Some sample images are illustrated in Figure 4. We also collect 9,300 marine images through the network. We select 8,400 images as training set, 2,100 as validation set and 1,600 as test set. As the purpose of our obstacle detection method is to support the autonomous navigation of USV for the obstacle avoidance, we divide the target into four categories. These four categories are aircraft, bird, ship and people. Then the prepared dataset is labeled with the border and category name of the target object in each image through the image annotation software LabelImg, and the labeling information is saved and transformed into the text format. Python program is written to read text files and convert them into XML files in PASCAL VOC format. Finally, all the labeled dataset is named USVD2018, and it is employed in our test experiments. Some sample images in USVD2018 are illustrated in Figure 5.
According to whether the classification results are correct, TP, TN, FP, and FN can be determined. TP means that the classification result is true and positive. Similarly, TN means true negative, and so on.
Recall, precision, accuracy, specificity and F1-score are employed as classification performance indicators to evaluate different methods. They are defined as follows.
Recall=TPTP+FN. | (3.1) |
Precision=TPTP+FP. | (3.2) |
Accuracy=TP+TNTP+TN+FP+FN. | (3.3) |
F1-score=2TP2TP+FP+FN. | (3.4) |
Recall measures the proportion of actual positives that are correctly identified as such. Accuracy is defined as the proportion of all samples that have been successfully classified. Precision is the ratio of samples correctly classified as positive to all the samples which are classified. F1-score is the harmonic mean of precision and sensitivity. When the above performance index is greater, the classification performance is better.
Our proposed method and other methods are tested in our experiments using USVD2018 data set. The performance indicators of each class are listed in Tables 1– 4. These data are also plotted in Figure 6. It is clear that our proposed method obtains the best values in all the evaluation indicators of four categories. It can be seen from Tables 1 to 4 that the detection accuracy of aircraft is the highest in the 4 categories, since the large number of aircraft samples are used in data training. Correspondingly, the detection rate of other categories is relatively low. Thus, it can be seen that the number and quality of samples are the key factors in the training and learning process. It also shows that the performance of our proposed method is the best, even if the number of samples varies.
Method | Faster RCNN | Mask RCNN | Improved Faster RCNN | Fusion | Multi-Scale | Proposed |
Recall | 0.8029 | 0.8743 | 0.8257 | 0.8886 | 0.8629 | 0.9257 |
Precision | 0.7337 | 0.7927 | 0.7707 | 0.8141 | 0.8436 | 0.8594 |
Accuracy | 0.8931 | 0.9225 | 0.9081 | 0.9313 | 0.9350 | 0.9506 |
F1 Score | 0.7667 | 0.8315 | 0.7972 | 0.8497 | 0.8531 | 0.8913 |
Method | Faster RCNN | Mask RCNN | Improved Faster RCNN | Fusion | Multi-Scale | Proposed |
Recall | 0.7629 | 0.8114 | 0.7886 | 0.8229 | 0.8514 | 0.8629 |
Precision | 0.7216 | 0.8068 | 0.7340 | 0.8205 | 0.8076 | 0.8603 |
Accuracy | 0.8838 | 0.9163 | 0.8913 | 0.9219 | 0.9231 | 0.9393 |
F1 Score | 0.7417 | 0.8091 | 0.7603 | 0.8217 | 0.8289 | 0.8616 |
Method | Faster RCNN | Mask RCNN | Improved Faster RCNN | Fusion | Multi-Scale | Proposed |
Recall | 0.7620 | 0.8220 | 0.7840 | 0.8440 | 0.8660 | 0.8920 |
Precision | 0.8355 | 0.8726 | 0.8340 | 0.8884 | 0.8819 | 0.9065 |
Accuracy | 0.8788 | 0.9069 | 0.8838 | 0.9181 | 0.9219 | 0.9375 |
F1 Score | 0.7970 | 0.8466 | 0.8082 | 0.8656 | 0.8739 | 0.8992 |
Method | Faster RCNN | Mask RCNN | Improved Faster RCNN | Fusion | Multi-Scale | Proposed |
Recall | 0.7800 | 0.8150 | 0.7575 | 0.8300 | 0.7975 | 0.8400 |
Precision | 0.7980 | 0.8338 | 0.7995 | 0.8469 | 0.8351 | 0.8842 |
Accuracy | 0.8956 | 0.9131 | 0.8919 | 0.9200 | 0.9100 | 0.9325 |
F1 Score | 0.7889 | 0.8243 | 0.7779 | 0.8384 | 0.8159 | 0.8615 |
Figure 7 shows ship target detection samples. In the image on the left, there are four boats in the relatively blurry background. Other methods do not correctly detect the smallest boat, while the proposed method in this paper correctly detects all the boats. Similarly, in the image on the right, other methods miss two small boats in a clear background, as well as one not obvious hinder ship in a complex background. However, all the boats are correctly recognized by our proposed method.
In order to verify the effectiveness of each part of the proposed method in this paper, ablation experiments are used in this study.
Firstly, to verify the effectiveness of the proposed biderectional RNN network architecture, experiments are performed without improved dense block. This experiment is performed with the same condition as in above section. mAP (Mean Average Precison) is used to evaluate the obstacle detection performance, and IOU = 0.5 is set as threshold. The results are listed in Table 5. It reveals that the proposed method without improved dense block still has the best performance with the highest mAP value.
Faster | Mask | Improved | Proposed without | |||
Method | RCNN | RCNN | Faster RCNN | Fusion | Multi-Scale | improved dense block |
mAP | 0.8636 | 0.8926 | 0.8780 | 0.8948 | 0.9040 | 0.9380 |
To verify the effectiveness of the proposed improved dense block, the improved dense block is applied to Faster R-CNN and Mask R-CNN respectively. The backbone network of these methods are DenseNet101. Whether improved dense block is used in the proposed method is also shown in Table 6. When the improved dense block is applied to these methods, all the performances is improved. It can be seen that the proposed improved dense block has the ability to improve the obstacle detection performance.
Method | Without improved dense block | With improved dense block |
Faster RCNN | 0.8761 | 0.8869 |
Mask RCNN | 0.9002 | 0.9248 |
Proposed | 0.9380 | 0.9463 |
In order to further compare the accuracy of different methods, they are also trained and tested on a large-scale open source data set COCO. After 100 cycles and 1000 iterations per cycle, the test results on COCO data are shown in Table 7. The threshold setting of IOU = 0.5 is selected by mAP corresponding to different methods for comparison.
Method | Faster RCNN | Mask RCNN | Improved Faster RCNN | Fusion | Multi-Scale | Proposed |
mAP | 0.3742 | 0.4169 | 0.3804 | 0.4248 | 0.3740 | 0.4452 |
The experimental results show that the proposed algorithm performs better than other methods in COCO data sets with 80 categories. COCO data sets have many kinds of objects to be recognized. The average accuracy of 80 different types is calculated. The overall mAP is low when the training time is limited, but the actual detection effect of this method is very good. Some test results are shown in Figure 8. It can be seen that the detection effect of this method is better.
The obstacle detection method based on CNN for autonomous navigation of USV is discussed. A feature pyramid method of bidirectional feature pyramid networks is developed combining hybrid network architecture of ResNet and improved DenseNet. The results show that the proposed method has the highest performance for obstacle detection and is more suitable for the application of USV.
This paper mainly discusses the detection of water surface obstacles for SUV applications. The number of categories is very limited. The main problem of this method is that it can not detect untrained categories. Therefore, obstacle classification of training is very important for this method. When more classification types are trained, more types of obstacle can be detected and recognized. And more samples are required for training. In the future, we will collect more samples and carry out more detection research.
First of all, we would like to thank the reviewers for their valuable comments on this paper, which is very helpful to improve this paper. Secondly, this work was supported by Shandong Provincial Natural Science Foundation of China (ZR2018MF026), Shandong Province Key R & D Program (2019GGX101054, 2019GSF111062, 2018GGX101034), University Co-construction Project at Weihai (ITDAZMZ001708), and the Discipline Construction Foundation in Harbin Institute of Technology, Weihai (WH20160103).
All authors declare no conflicts of interest in this paper.
[1] |
Ayanoglu MO, Tauhiduzzaman M, Carlsson LA (2022) In-plane compression modulus and strength of Nomex honeycomb cores. J Sandw Struct Mater 24: 627–642. https://doi.org/10.1177/10996362211021888 doi: 10.1177/10996362211021888
![]() |
[2] |
Tauhiduzzaman M, Carlsson LA, Ayanoglu MO (2021) Design analysis of end notch flexure sandwich specimen with honeycomb core. J Compos Mater 55: 1295–1308. https://doi.org/10.1177/0021998320967050 doi: 10.1177/0021998320967050
![]() |
[3] |
İrsel G (2022) Study of the microstructure and mechanical property relationships of shielded metal arc and TIG welded S235JR steel joints. Mater Sci Eng A-Struct 830: 142320. https://doi.org/10.1016/j.msea.2021.142320 doi: 10.1016/j.msea.2021.142320
![]() |
[4] |
Wu X, Zhao X, Chen J, et al. (2022) Simulation of the influence of welding parameters on weld pool behavior during a TIG-MIG hybrid welding process. J Manuf Process 79:460–475. https://doi.org/10.1016/j.jmapro.2022.05.007 doi: 10.1016/j.jmapro.2022.05.007
![]() |
[5] |
Pang S, Cao B (2021) Low current arc ignition stability in micro-TIG welding. J Manuf Process 69: 12–20. https://doi.org/10.1016/j.jmapro.2021.07.022 doi: 10.1016/j.jmapro.2021.07.022
![]() |
[6] |
Zala AB, Jamnapara NI, Sasmal CS, et al. (2022) Study of microstructure & mechanical properties of TIG welded aluminized 9Cr-1Mo steel. Fusion Eng Design 176: 113038. https://doi.org/10.1016/j.fusengdes.2022.113038 doi: 10.1016/j.fusengdes.2022.113038
![]() |
[7] |
Li T, Bi X, Li R (2022) A strategy for bonding immiscible Mg/steel by laser-TIG butt fusion welding and lattice distortion on the Fe/Mg interface matching. Mater Design 219:110763. https://doi.org/10.1016/j.matdes.2022.110763 doi: 10.1016/j.matdes.2022.110763
![]() |
[8] |
Pydi HP, Pasupulla AP, Vijayakumar S, et al. (2021) Study on microstructure, behavior and Al2O3 content flux A-TIG weldment of SS-316L steel. Mater Today Proc 51: 728–734. https://doi.org/10.1016/j.matpr.2021.06.218 doi: 10.1016/j.matpr.2021.06.218
![]() |
[9] |
Panda SS (2021) Characterisation of Cu–Al alloy lap joint using TIG Welding. CIRP J Manuf Sci Technol 35: 454–459. https://doi.org/10.1016/j.cirpj.2021.07.009 doi: 10.1016/j.cirpj.2021.07.009
![]() |
[10] |
Mahajan A, Singh H, Kumar S, et al. (2022) Mechanical properties assessment of TIG welded SS 304 joints. Mater Today Proc 56:3073–3077. https://doi.org/10.1016/j.matpr.2021.12.133 doi: 10.1016/j.matpr.2021.12.133
![]() |
[11] |
Nguyen VN, Nguyen QM, Huang SC (2018) Microstructure and mechanical properties of butt joints between stainless steel sus304l and aluminum alloy A6061-T6 by TIG welding. Materials 11: 1136. https://doi.org/10.3390/ma11071136 doi: 10.3390/ma11071136
![]() |
[12] |
Anwar S, Rehman AU, Usmani Y, et al. (2021) Influence of post weld heat treatment on the grain size, and mechanical properties of the alloy-800h rotary friction weld joints. Materials 14: 4366. https://doi.org/10.3390/ma14164366 doi: 10.3390/ma14164366
![]() |
[13] |
Li D, Lu S, Dong W, et al. (2012) Study of the law between the weld pool shape variations with the welding parameters under two TIG processes. J Mater Process Technol 212: 128–136. https://doi.org/10.1016/j.jmatprotec.2011.08.015 doi: 10.1016/j.jmatprotec.2011.08.015
![]() |
[14] |
Zmitrowicz P, Kawiak M, Kochmański P, et al. (2021) Microstructure and mechanical properties of welded joints of 1.4462 duplex steel made by the k-tig method. Materials 14: 7868. https://doi.org/10.3390/ma14247868 doi: 10.3390/ma14247868
![]() |
[15] |
Li M, Yao D, Guan Y, et al. (2020) Effect of welding speed and post quenching on the microstructure and mechanical properties of laser-welded B1500HS joints. Materials 13: 4645. https://doi.org/10.3390/ma13204645 doi: 10.3390/ma13204645
![]() |
[16] |
Fei Z, Pan Z, Cuiuri D, et al. (2019) Microstructural characterization and mechanical properties of K-TIG welded SAF2205/AISI316L dissimilar joint. J Manuf Process 45: 340–355. https://doi.org/10.1016/j.jmapro.2019.07.017 doi: 10.1016/j.jmapro.2019.07.017
![]() |
[17] |
Konat Ł (2021) Technological, microstructural and strength aspects of welding and post-weld heat treatment of martensitic, wear-resistant hardox 600 steel. Materials 14: 4541. https://doi.org/10.3390/ma14164541 doi: 10.3390/ma14164541
![]() |
[18] |
Alipooramirabad H, Paradowska A, Nafisi S, et al. (2020) Post-weld heat treatment of api 5l x70 high strength low alloy steel welds. Materials 13: 5801. https://doi.org/10.3390/ma13245801 doi: 10.3390/ma13245801
![]() |
[19] |
Królicka A, Radwański K, Janik A, et al. (2020) Metallurgical characterization of welded joint of nanostructured bainite: Regeneration technique versus post welding heat treatment. Materials 13: 4841. https://doi.org/10.3390/ma13214841 doi: 10.3390/ma13214841
![]() |
[20] |
Chaudry UM, Ahmad HW, Tariq MR, et al. (2020) Effect of post weld heat treatment on the microstructure and electrochemical characteristics of dissimilar material welded by butter method. Materials 13: 4512. https://doi.org/10.3390/ma13204512 doi: 10.3390/ma13204512
![]() |
[21] |
Tian S, Xu F, Zhang G, et al. (2021) Influence of post-weld heat treatment on microstructure and toughness properties of 13MnNiMoR high strength low alloy steel weld joint. Materials 14: 5336. https://doi.org/10.3390/ma14185336 doi: 10.3390/ma14185336
![]() |
[22] |
Brykov MN, Petryshynets I, Džupon M, et al. (2020) Microstructure and properties of heat affected zone in high-carbon steel after welding with fast cooling in water. Materials 13: 5059. https://doi.org/10.3390/ma13225059 doi: 10.3390/ma13225059
![]() |
[23] |
Smith M, Bichler L, Gholipour J, et al. (2017) Mechanical properties and microstructural evolution of in-service Inconel 718 superalloy repaired by linear friction welding. Int J Adv Manuf Tech 90: 1931–1946. https://doi.org/10.1007/s00170-016-9515-2 doi: 10.1007/s00170-016-9515-2
![]() |
[24] | Drabble DJ, Bishop CM, Kral M (2011) A microstructural study of grain boundary engineered alloy 800H. In: Metallurgical and Materials Transactions A: Physical Metallurgy and Materials Science. pp 763–772 |
[25] |
Wang H, Ikeuchi K, Aritoshi M, et al. (2009) Microstructures forming in friction welding of Inconel 718 alloy—joint performance and its controlling factors in friction welding of Inconel 718 alloy. Weld Int 23: 670–678. https://doi.org/10.1080/09507110902842869 doi: 10.1080/09507110902842869
![]() |
[26] |
Szczucka-Lasota B, Węgrzyn T, Szymczak T, et al. (2021) High martensitic steel after welding with micro-jet cooling in microstructural and mechanical investigations. Materials 14: 936. https://doi.org/10.3390/ma14040936 doi: 10.3390/ma14040936
![]() |
[27] |
Lan L, Shao G (2020) Morphological evolution of HAZ microstructures in low carbon steel during simulated welding thermal cycle. Micron 131: 102828. https://doi.org/10.1016/j.micron.2020.102828 doi: 10.1016/j.micron.2020.102828
![]() |
[28] |
Sehgal AK (2020) An investigation of variable welding current on impact strength of metal inert gas welded specimen. Mater Today Proc 37: 3679–3682. https://doi.org/10.1016/j.matpr.2020.10.151 doi: 10.1016/j.matpr.2020.10.151
![]() |
[29] |
Pham CH, Trinh HN, Proust G (2021) Effect of manufacturing process on microstructures and mechanical properties, and design of cold-formed G450 steel channels. Thin Wall Struct 162: 107620. https://doi.org/10.1016/j.tws.2021.107620 doi: 10.1016/j.tws.2021.107620
![]() |
[30] |
Bodude MA, Momohjimoh I (2015) Studies on effects of welding parameters on the mechanical properties of welded low-carbon steel. J Miner Mater Char Eng 3: 142–153. https://doi.org/10.4236/jmmce.2015.33017 doi: 10.4236/jmmce.2015.33017
![]() |
[31] |
Bansal A, Kumar MS, Shekhar I, et al. (2021) Effect of welding parameter on mechanical properties of TIG welded AA6061. Mater Today Proc 37: 2126–2131. https://doi.org/10.1016/j.matpr.2020.07.567 doi: 10.1016/j.matpr.2020.07.567
![]() |
[32] |
Boumerzoug Z, Derfouf C, Baudin T (2010) Effect of welding on microstructure and mechanical properties of an industrial low carbon steel. Engineering 2: 502–506. https://doi.org/10.4236/eng.2010.27066 doi: 10.4236/eng.2010.27066
![]() |
[33] |
Shrivas SP, Vaidya SK, Khandelwal AK, et al. (2019) Investigation of TIG welding parameters to improve strength. Mater Today Proc 26: 1897–1902. https://doi.org/10.1016/j.matpr.2020.02.416 doi: 10.1016/j.matpr.2020.02.416
![]() |
[34] |
Su L, Fei Z, Davis B, et al. (2021) Digital image correlation study on tensile properties of high strength quenched and tempered steel weld joints prepared by K-TIG and GMAW. Mater Sci Eng A-Struct 827: 142033. https://doi.org/10.1016/j.msea.2021.142033 doi: 10.1016/j.msea.2021.142033
![]() |
[35] |
Fei Z, Pan Z, Cuiuri D, et al. (2019) Improving the weld microstructure and material properties of K TIG welded armour steel joint using filler material. Int J Adv Manuf Technol 100: 1931–1944. https://doi.org/10.1007/s00170-018-2787-y doi: 10.1007/s00170-018-2787-y
![]() |
[36] |
Fei Z, Pan Z, Cuiuri D, et al. (2019) Effect of heat input on weld formation and tensile properties in keyhole mode TIG welding process. Metals 9: 1327. https://doi.org/10.3390/met9121327 doi: 10.3390/met9121327
![]() |
[37] |
Kumar K, Kumar CS, Masanta M, et al. (2021) A review on TIG welding technology variants and its effect on weld geometry. Mater Today Proc 50: 999–1004. https://doi.org/10.1016/j.matpr.2021.07.308 doi: 10.1016/j.matpr.2021.07.308
![]() |
[38] |
Li Y, Guan Q, He B (2023) Improving the strength and ductility of medium Mn steel by depleting the stress-assisted martensite. Scr Mater 226: 115267. https://doi.org/10.1016/j.scriptamat.2022.115267 doi: 10.1016/j.scriptamat.2022.115267
![]() |
[39] |
Cui S, Pang S, Pang D, et al. (2021) Influence of welding speeds on the morphology, mechanical properties, and microstructure of 2205 DSS welded joint by k-tigwelding. Materials 14: 3426. https://doi.org/10.3390/ma14123426 doi: 10.3390/ma14123426
![]() |
1. | Renqiang Wang, Donglou Li, Keyin Miao, Optimized Radial Basis Function Neural Network Based Intelligent Control Algorithm of Unmanned Surface Vehicles, 2020, 8, 2077-1312, 210, 10.3390/jmse8030210 | |
2. | Tey Wee Teng, Prabakaran Veerajagadheswar, Balakrishnan Ramalingam, Jia Yin, Rajesh Elara Mohan, Braulio Félix Gómez, Vision Based Wall Following Framework: A Case Study With HSR Robot for Cleaning Application, 2020, 20, 1424-8220, 3298, 10.3390/s20113298 | |
3. | Cristiano Rafael Steffens, Lucas Ricardo Vieira Messias, Paulo Jorge Lilles Drews-Jr, Silvia Silva da Costa Botelho, On Robustness of Robotic and Autonomous Systems Perception, 2021, 101, 0921-0296, 10.1007/s10846-021-01334-0 | |
4. | Borja Bovcon, Jon Muhovic, Dusko Vranac, Dean Mozetic, Janez Pers, Matej Kristan, MODS—A USV-Oriented Object Detection and Obstacle Segmentation Benchmark, 2022, 23, 1524-9050, 13403, 10.1109/TITS.2021.3124192 | |
5. | Borja Bovcon, Matej Kristan, WaSR—A Water Segmentation and Refinement Maritime Obstacle Detection Network, 2022, 52, 2168-2267, 12661, 10.1109/TCYB.2021.3085856 | |
6. | Ivan Porres, Sepinoud Azimi, Sebastien Lafond, Johan Lilius, Johanna Salokannel, Mirva Salokorpi, 2020, On the Verification and Validation of AI Navigation Algorithms, 978-1-7281-5446-6, 1, 10.1109/IEEECONF38699.2020.9389133 | |
7. | Longfei Ma, Hsiucheng Wang, Fenghua Liu, Kaiyuan Li, 2021, Remote Monitoring Algorithm for Unmanned Surface Vessel: A System Based on Classification and Learning, 978-9-8815-6380-4, 5117, 10.23919/CCC52363.2021.9549604 | |
8. | Lifa Fang, Yanqiang Wu, Yuhua Li, Hongen Guo, Hua Zhang, Xiaoyu Wang, Rui Xi, Jialin Hou, Ginger Seeding Detection and Shoot Orientation Discrimination Using an Improved YOLOv4-LITE Network, 2021, 11, 2073-4395, 2328, 10.3390/agronomy11112328 | |
9. | Chong Qu, Zhiguo Zhou, Zhiwen Liu, Shuli Jia, Liyong Ma, Mary Immaculate Sheela L, K. Raja, A Multisensor Data Fusion Based Anomaly Detection (Ammonia Nitrogen) Approach for Ensuring Green Coastal Environment, 2022, 2022, 1687-8442, 1, 10.1155/2022/4632137 | |
10. | Lulu Shen, Kun Li, Lin Zhu, Xuewei Liu, Liyong Ma, 2021, Radar Point Cloud Clustering Method Based on Optimization, 978-1-6654-3890-2, 158, 10.1109/CCET52649.2021.9544261 | |
11. | Hongguang Lyu, Zeyuan Shao, Tao Cheng, Yong Yin, Xiaowei Gao, Sea-Surface Object Detection Based on Electro-Optical Sensors: A Review, 2023, 15, 1939-1390, 190, 10.1109/MITS.2022.3198334 | |
12. | Lojze Žust, Matej Kristan, Learning with Weak Annotations for Robust Maritime Obstacle Detection, 2022, 22, 1424-8220, 9139, 10.3390/s22239139 | |
13. | Hua Yang, Jinchao Xiao, Junfeng Xiong, Jinqing Liu, 2023, Chapter 69, 978-981-99-0478-5, 753, 10.1007/978-981-99-0479-2_69 | |
14. | Renqiang Wang, Qinrong Li, Shengze Miao, Keyin Miao, Hua Deng, Design of Intelligent Controller for Ship Motion with Input Saturation Based on Optimized Radial Basis Function Neural Network, 2021, 14, 22127976, 105, 10.2174/2212797613999200730211514 | |
15. | Yuxue Liu, Shuli Jia, Yuan Yu, Liyong Ma, Prediction with coastal environments and marine diesel engine data based on ship intelligent platform, 2023, 13, 2190-5509, 1437, 10.1007/s13204-021-02042-9 | |
16. | Lojze Zust, Matej Kristan, 2022, Learning Maritime Obstacle Detection from Weak Annotations by Scaffolding, 978-1-6654-0915-5, 1888, 10.1109/WACV51458.2022.00195 | |
17. | Hongteng Wang, Lianfang Wang, Liyong Ma, 2021, Anomaly Detection of Hydropower Bearing Based on Convolutional Neural Network Autoencoder, 978-1-6654-3890-2, 430, 10.1109/CCET52649.2021.9544462 | |
18. | Liyong Ma, Xuewei Liu, Yong Zhang, Shuli Jia, Visual target detection for energy consumption optimization of unmanned surface vehicle, 2022, 8, 23524847, 363, 10.1016/j.egyr.2022.01.204 | |
19. | Carlos Barrera, Mustapha Maarouf, Francisco Campuzano, Octavio Llinas, Graciliano Nicolas Marichal, A Comparison of Intelligent Models for Collision Avoidance Path Planning on Environmentally Propelled Unmanned Surface Vehicles, 2023, 11, 2077-1312, 692, 10.3390/jmse11040692 | |
20. | Shuaiwen Sun, Zhijing Xu, Large kernel convolution YOLO for ship detection in surveillance video, 2023, 20, 1551-0018, 15018, 10.3934/mbe.2023673 | |
21. | Ivana Jovanović, Maja Perčić, Ahmad BahooToroody, Ailong Fan, Nikola Vladimir, Review of research progress of autonomous and unmanned shipping and identification of future research directions, 2024, 23, 2046-4177, 82, 10.1080/20464177.2024.2302249 | |
22. | Marcos A. Fleck, Elisa G. Pereira, Jonas F. Gava, Henrique B. Silva, Fernando G. Moraes, Ney L.V. Calazans, Felipe Meneguzzi, Rodrigo P. Bastos, Ricardo A. L. Reis, Luciano Ost, Rafael Garibotti, Assessment of Radiation-Induced Soft Error on Unmanned Surface Vehicles, 2024, 71, 0018-9499, 1589, 10.1109/TNS.2024.3378807 | |
23. | Kasper Foss Hansen, Linghong Yao, Kang Ren, Sen Wang, Wenwen Liu, Yuanchang Liu, Image segmentation in marine environments using convolutional LSTM for temporal context, 2023, 139, 01411187, 103709, 10.1016/j.apor.2023.103709 | |
24. | Lojze Žust, Janez Perš, Matej Kristan, 2023, LaRS: A Diverse Panoptic Maritime Obstacle Detection Dataset and Benchmark, 979-8-3503-0718-4, 20247, 10.1109/ICCV51070.2023.01857 | |
25. | Tilen Cvenkel, Marija Ivanovska, Jon Muhovič, Janez Perš, 2023, Chapter 18, 978-3-031-45381-6, 209, 10.1007/978-3-031-45382-3_18 | |
26. | Peng Wu, Jiaju Zhang, Shaojing Su, Zhen Zuo, Bei Sun, 2023, Sea Surface Target Detection System and Ship Detection Dataset Based on Unmanned Surface Vessel, 979-8-3503-3603-0, 232, 10.1109/ICMSP58539.2023.10171072 | |
27. | Matija Teršek, Lojze Žust, Matej Kristan, eWaSR—An Embedded-Compute-Ready Maritime Obstacle Detection Network, 2023, 23, 1424-8220, 5386, 10.3390/s23125386 | |
28. | Joshua H X Lim, Swee King Phang, Classification and Detection of Obstacles for Rover Navigation, 2023, 2523, 1742-6588, 012030, 10.1088/1742-6596/2523/1/012030 | |
29. | Helmi Abrougui, Samir Nejim, Autopilot Design for an Unmanned Surface Vehicle Based on Backstepping Integral Technique with Experimental Results, 2023, 22, 1671-9433, 614, 10.1007/s11804-023-00356-4 | |
30. | Luca Tarasi, Francesco Wanderlingh, Nicoletta Noceti, Giovanni Indiveri, Enrico Simetti, 2024, LiDAR and RGB Camera Performance for Obstacle Detection in Marine Environment, 979-8-3315-4008-1, 1, 10.1109/OCEANS55160.2024.10753999 |
Method | Faster RCNN | Mask RCNN | Improved Faster RCNN | Fusion | Multi-Scale | Proposed |
Recall | 0.8029 | 0.8743 | 0.8257 | 0.8886 | 0.8629 | 0.9257 |
Precision | 0.7337 | 0.7927 | 0.7707 | 0.8141 | 0.8436 | 0.8594 |
Accuracy | 0.8931 | 0.9225 | 0.9081 | 0.9313 | 0.9350 | 0.9506 |
F1 Score | 0.7667 | 0.8315 | 0.7972 | 0.8497 | 0.8531 | 0.8913 |
Method | Faster RCNN | Mask RCNN | Improved Faster RCNN | Fusion | Multi-Scale | Proposed |
Recall | 0.7629 | 0.8114 | 0.7886 | 0.8229 | 0.8514 | 0.8629 |
Precision | 0.7216 | 0.8068 | 0.7340 | 0.8205 | 0.8076 | 0.8603 |
Accuracy | 0.8838 | 0.9163 | 0.8913 | 0.9219 | 0.9231 | 0.9393 |
F1 Score | 0.7417 | 0.8091 | 0.7603 | 0.8217 | 0.8289 | 0.8616 |
Method | Faster RCNN | Mask RCNN | Improved Faster RCNN | Fusion | Multi-Scale | Proposed |
Recall | 0.7620 | 0.8220 | 0.7840 | 0.8440 | 0.8660 | 0.8920 |
Precision | 0.8355 | 0.8726 | 0.8340 | 0.8884 | 0.8819 | 0.9065 |
Accuracy | 0.8788 | 0.9069 | 0.8838 | 0.9181 | 0.9219 | 0.9375 |
F1 Score | 0.7970 | 0.8466 | 0.8082 | 0.8656 | 0.8739 | 0.8992 |
Method | Faster RCNN | Mask RCNN | Improved Faster RCNN | Fusion | Multi-Scale | Proposed |
Recall | 0.7800 | 0.8150 | 0.7575 | 0.8300 | 0.7975 | 0.8400 |
Precision | 0.7980 | 0.8338 | 0.7995 | 0.8469 | 0.8351 | 0.8842 |
Accuracy | 0.8956 | 0.9131 | 0.8919 | 0.9200 | 0.9100 | 0.9325 |
F1 Score | 0.7889 | 0.8243 | 0.7779 | 0.8384 | 0.8159 | 0.8615 |
Faster | Mask | Improved | Proposed without | |||
Method | RCNN | RCNN | Faster RCNN | Fusion | Multi-Scale | improved dense block |
mAP | 0.8636 | 0.8926 | 0.8780 | 0.8948 | 0.9040 | 0.9380 |
Method | Without improved dense block | With improved dense block |
Faster RCNN | 0.8761 | 0.8869 |
Mask RCNN | 0.9002 | 0.9248 |
Proposed | 0.9380 | 0.9463 |
Method | Faster RCNN | Mask RCNN | Improved Faster RCNN | Fusion | Multi-Scale | Proposed |
mAP | 0.3742 | 0.4169 | 0.3804 | 0.4248 | 0.3740 | 0.4452 |
Method | Faster RCNN | Mask RCNN | Improved Faster RCNN | Fusion | Multi-Scale | Proposed |
Recall | 0.8029 | 0.8743 | 0.8257 | 0.8886 | 0.8629 | 0.9257 |
Precision | 0.7337 | 0.7927 | 0.7707 | 0.8141 | 0.8436 | 0.8594 |
Accuracy | 0.8931 | 0.9225 | 0.9081 | 0.9313 | 0.9350 | 0.9506 |
F1 Score | 0.7667 | 0.8315 | 0.7972 | 0.8497 | 0.8531 | 0.8913 |
Method | Faster RCNN | Mask RCNN | Improved Faster RCNN | Fusion | Multi-Scale | Proposed |
Recall | 0.7629 | 0.8114 | 0.7886 | 0.8229 | 0.8514 | 0.8629 |
Precision | 0.7216 | 0.8068 | 0.7340 | 0.8205 | 0.8076 | 0.8603 |
Accuracy | 0.8838 | 0.9163 | 0.8913 | 0.9219 | 0.9231 | 0.9393 |
F1 Score | 0.7417 | 0.8091 | 0.7603 | 0.8217 | 0.8289 | 0.8616 |
Method | Faster RCNN | Mask RCNN | Improved Faster RCNN | Fusion | Multi-Scale | Proposed |
Recall | 0.7620 | 0.8220 | 0.7840 | 0.8440 | 0.8660 | 0.8920 |
Precision | 0.8355 | 0.8726 | 0.8340 | 0.8884 | 0.8819 | 0.9065 |
Accuracy | 0.8788 | 0.9069 | 0.8838 | 0.9181 | 0.9219 | 0.9375 |
F1 Score | 0.7970 | 0.8466 | 0.8082 | 0.8656 | 0.8739 | 0.8992 |
Method | Faster RCNN | Mask RCNN | Improved Faster RCNN | Fusion | Multi-Scale | Proposed |
Recall | 0.7800 | 0.8150 | 0.7575 | 0.8300 | 0.7975 | 0.8400 |
Precision | 0.7980 | 0.8338 | 0.7995 | 0.8469 | 0.8351 | 0.8842 |
Accuracy | 0.8956 | 0.9131 | 0.8919 | 0.9200 | 0.9100 | 0.9325 |
F1 Score | 0.7889 | 0.8243 | 0.7779 | 0.8384 | 0.8159 | 0.8615 |
Faster | Mask | Improved | Proposed without | |||
Method | RCNN | RCNN | Faster RCNN | Fusion | Multi-Scale | improved dense block |
mAP | 0.8636 | 0.8926 | 0.8780 | 0.8948 | 0.9040 | 0.9380 |
Method | Without improved dense block | With improved dense block |
Faster RCNN | 0.8761 | 0.8869 |
Mask RCNN | 0.9002 | 0.9248 |
Proposed | 0.9380 | 0.9463 |
Method | Faster RCNN | Mask RCNN | Improved Faster RCNN | Fusion | Multi-Scale | Proposed |
mAP | 0.3742 | 0.4169 | 0.3804 | 0.4248 | 0.3740 | 0.4452 |