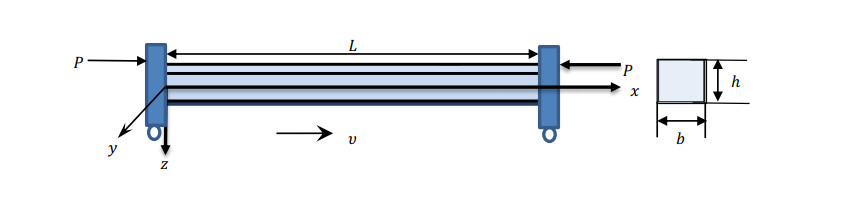
This paper gives a mathematical formulation for the transverse resonance of thermoelastic nanobeams that are simply supported and compressed with an initial axial force. The nonlocal elasticity concept is used to analyze the influence of length scale with the dual-phase-lag (DPL) heat transfer theory. The nanobeam is due to a changing thermal load and moves in one direction at a constant speed. The governing motion equation for the nonlocal Euler-Bernoulli (EB) beam hypothesis can also be derived with the help of Hamilton's principle and then solved by means of the Laplace transform technique. The impacts of nonlocal nanoscale and axial velocity on the different responses of the moving beam are investigated. The results reveal that phase delays, as well as the nonlocal parameter and external excitation load, have a substantial impact on the system's behavior.
Citation: Osama Moaaz, Ahmed E. Abouelregal, Fahad Alsharari. Lateral vibration of an axially moving thermoelastic nanobeam subjected to an external transverse excitation[J]. AIMS Mathematics, 2023, 8(1): 2272-2295. doi: 10.3934/math.2023118
[1] | Ahmed E. Abouelregal, Khalil M. Khalil, Wael W. Mohammed, Doaa Atta . Thermal vibration in rotating nanobeams with temperature-dependent due to exposure to laser irradiation. AIMS Mathematics, 2022, 7(4): 6128-6152. doi: 10.3934/math.2022341 |
[2] | Mofareh Alhazmi, Ahmed E. Abouelregal . Nonlocal fractional MGT-non-Fourier photothermal model with spatial and temporal nonlocality for controlling the behavior of semiconductor materials with spherical cavities. AIMS Mathematics, 2025, 10(3): 7559-7590. doi: 10.3934/math.2025348 |
[3] | Said Mesloub, Hassan Altayeb Gadain, Lotfi Kasmi . On the well posedness of a mathematical model for a singular nonlinear fractional pseudo-hyperbolic system with nonlocal boundary conditions and frictional damping terms. AIMS Mathematics, 2024, 9(2): 2964-2992. doi: 10.3934/math.2024146 |
[4] | Caizhi Yang, Xinxin Shen, Like Pan, Liming Chen, Fan He . Numerical analysis of dropper stress under a moving load based on the uplift displacement for a high-speed railway. AIMS Mathematics, 2024, 9(3): 6568-6585. doi: 10.3934/math.2024320 |
[5] | Chander Bhan, Ravi Karwasra, Sandeep Malik, Sachin Kumar, Ahmed H. Arnous, Nehad Ali Shah, Jae Dong Chung . Bifurcation, chaotic behavior and soliton solutions to the KP-BBM equation through new Kudryashov and generalized Arnous methods. AIMS Mathematics, 2024, 9(4): 8749-8767. doi: 10.3934/math.2024424 |
[6] | Zhoujin Cui, Xiaorong Zhang, Tao Lu . Resonance analysis and time-delay feedback controllability for a fractional horizontal nonlinear roller system. AIMS Mathematics, 2024, 9(9): 24832-24853. doi: 10.3934/math.20241209 |
[7] | Tijani A. Apalara, Aminat O. Ige, Cyril D. Enyi, Mcsylvester E. Omaba . Uniform stability result of laminated beams with thermoelasticity of type Ⅲ. AIMS Mathematics, 2023, 8(1): 1090-1101. doi: 10.3934/math.2023054 |
[8] | Mohammed Alkinidri, Rab Nawaz, Hani Alahmadi . Analytical and numerical investigation of beam-spring systems with varying stiffness: a comparison of consistent and lumped mass matrices considerations. AIMS Mathematics, 2024, 9(8): 20887-20904. doi: 10.3934/math.20241016 |
[9] | Pierluigi Colli, Gianni Gilardi, Jürgen Sprekels . Distributed optimal control of a nonstandard nonlocal phase field system. AIMS Mathematics, 2016, 1(3): 225-260. doi: 10.3934/Math.2016.3.225 |
[10] | Osama Moaaz, Ahmed E. Abouelregal . Multi-fractional-differential operators for a thermo-elastic magnetic response in an unbounded solid with a spherical hole via the DPL model. AIMS Mathematics, 2023, 8(3): 5588-5615. doi: 10.3934/math.2023282 |
This paper gives a mathematical formulation for the transverse resonance of thermoelastic nanobeams that are simply supported and compressed with an initial axial force. The nonlocal elasticity concept is used to analyze the influence of length scale with the dual-phase-lag (DPL) heat transfer theory. The nanobeam is due to a changing thermal load and moves in one direction at a constant speed. The governing motion equation for the nonlocal Euler-Bernoulli (EB) beam hypothesis can also be derived with the help of Hamilton's principle and then solved by means of the Laplace transform technique. The impacts of nonlocal nanoscale and axial velocity on the different responses of the moving beam are investigated. The results reveal that phase delays, as well as the nonlocal parameter and external excitation load, have a substantial impact on the system's behavior.
In recent decades, nano-electromechanical systems (NEMS) technology has significantly progressed [1]. Nanoscale structural materials used in NEMS, like nanobeams, nanoplates, and nanoshells, have better properties, so researchers in this field pay a lot of attention to studying their mechanical and physical properties [2]. Vibration at nanoscales, which is highly size-dependent, is still a mystery despite the existence of well-established classical theories of linear and nonlinear vibration of strings and beams. The resonance of a nanobeam is examined here using nonlocal elastic stress theories in an effort to expand the classical theory of size-dependent nanomechanics [3].
Microstructural engineering problems can be addressed using the standard local theories of continuum mechanics and flexibility from civil, mechanical, and bioengineering engineering fields. The classical-local continuum framework is predicated on the idea that stress and strain are correlated at every point in space and time. Elastic wave spreading, crack propagation, and dislocations are extensively studied in the traditional theory of elasticity. Conventional elastic models, on the other hand, are useless for studying these processes in real-time at the atomic and subatomic scales [4].
The distance between atoms has little effect on classical continuum theory; nonetheless, it becomes significant when the model size is reduced. Several investigators have thus constructed classical continuum mechanics to represent the size effect. These advancements have been dubbed non-classical (higher-order) elasticity theories. So-called nonlocal beams are a subcategory of beam structures that are distinguished by applying the nonlocal elasticity constitutive equation to take into account the small-scale effects. Because of the nanoscale dimensions of their formations, nonlocal beams of this kind are typically referred to as nanobeams in the scientific literature [5]. Several theories that emphasize small-scale influences have been created, including the strain gradient concept [6,7], modified couple stress theory [8,9], couple stress elasticity model [10,11], and nonlocal elasticity theory [12,13,14].
The nonlocal theories are often based on Eringen's nonlocal elasticity theory [12,13,14], which is the most widely used. Based on Eringen's hypothesis of nonlocal elasticity, stress at any situation point affects the entire body. It depends not only on strains at this point but also on strains throughout the body. The formulation of nonlocal Eringen elasticity focuses on the atomic theory of lattice dynamics and some experimental evidence for phonon scattering. As a result, the object's size affects the results of the nonlocal theory, which considers long-range interactions between atoms [12,13,14].
The nonlocal elasticity model has been used to investigate many applications in nano-mechanics, such as lattice propagation of transverse waves, vibration in nanomaterials, deformation mechanics, fracture mechanics, compressive fluids, and others [15]. Due to their mechanical properties, the greatest attention has been paid to nanotubes and nanobeams. Peddiesion et al. [16] initially constructed the nonlocal Euler-Bernoulli (EB) beam equations in order to analyze the static behavior of MEMS cantilever actuators utilizing Eringen's nonlocal differential form. Simultaneously, Wang [17] outlined the conditions under which a Carbon nanotube (CNT) may be described as a beam based on its dimensions. These studies prompted nonlocal differential beam theories on CNTs and nanobeams to analyze their stationary, dynamic, and buckled attitudes and behaviors. Abouelregal and Marin [18] presented a nonlocal thermal model that shows how the nanobeams move and change shape. Eringen's theory of nonlocal elasticity as well as generalized thermoelastic theory is used to derive the equations governing the nonlocal nanobeams. In this paper, the structure of the nanobeam is affected by external harmonic forces and temperature changes caused by the heating of a modified sine wave. A generalized kernel function for memory-based derivatives with two-time lags was proposed by Abouelregal et al. [19,20] as a theoretical model for analyzing the nonlocal heat conduction model. The thermomechanical reaction of spinning size-dependent nanobeams is the focus of the new model. The nonlocal elasticity theories and the extended heat transfer model with phase lags are used in the mathematical formulation. Bian and Qing [21] have created a new framework for the Finite Element Method (FEM) in order to simulate the mechanical interactions of an Euler-Bernoulli beam using a nonlocal and nonlocal two-phase mixed model at the same time. In this work, a fifth-degree polynomial was used for the model function, and the constitutive boundary conditions (CBCs) were treated the same way as the external loads. Scorza et al. [22] introduced a study that aims to extend the two-phase local/nonlocal stress-driven integral system (SDM) to the situation of nanobeams with internal discontinuities. In point of fact, the initial formulation attempts to avoid the existence of any discontinuities in the structure. The thermal buckling of an anisotropic flexible composite beam with a dielectric core and two thin semiconducting surface layers was recently modeled by Zhang et al. [23]. From the kinematic relations for a Timoshenko beam and the concepts of piezoelectricity, flexoelectricity, strain gradient elasticity, and semiconductors, we derive the system of equations and boundary conditions for the beam.
Many researchers have come up with the term "axially moving nanostructures" to describe how axially moving continuums work in many structural applications, such as band saws, printing mechanisms, tubes carrying fluids, etc. [24,25] Since the 1950s, scientists have been studying how materials vibrate when they move in one direction. Through many efforts, the first papers were presented on the vibration of the thread moving along it [26,27]. In recent decades, many research articles have been published about beams, plates, and shells that move in one direction [28,29,30].
The temperature of the body changes as a result of the body's deformation. The temperature of the body changes, and the body deforms when a heat source is applied from outside. Consequently, deformation and temperature affect the body's inner energy. Thermoelasticity looks at how stress, stain, and deformation are linked to heat source and time. The goal is to find a formula that describes how stress, stain, and deformation change over time. According to research, this theory can be applied to various engineering fields and advanced technologies, from acoustics to aeronautical engineering to chemical engineering. It can also be used to check the strength, stiffness, and stability of a structure or system parts and the elastic limit of a structure or machine [31].
The linear theory of linked thermoelasticity was first satisfactorily derived by Biot [32]. Later, Chadwick [33] published both linear and nonlinear formulations of the concept and solved several significant linear dynamic system issues. Coupled thermoelasticity has been expanded to include more types of materials, such as micro elastic materials, electromechanical solids, and viscoelastic solid particles, among others. The conventional uncorrelated thermoelasticity hypothesis predicts two events that are incompatible with physical phenomena. First, this heat transfer theory equation does not include any elastic factors, even though elastic changes create thermal effects. Second, the equation for thermal conductivity is of the parabolic type, which indicates that heat waves will propagate at an infinite rate within the medium. To address this dilemma, several efforts have been made to change the coupled concept of thermal elasticity in order to obtain a wave-type heat transfer formula. Some of the most well-known generalized thermoelastic concepts and theories include the Lord and Shulman (LS) model [34], the Green and Lindsey theory (G-L) [35], as well as the Green and Naghdi (GN) [36,37] theories, which were developed with the help of the energy equation. Also, the dual-phase lag (DPL) model [38,39] was introduced by Tzou.
Non-Fourier transient heat transport in a two-dimensional sub-100 nm metal-oxide-semiconductor field-effect transistor was the subject of research by Ghazanfarian and Shomali [40], who used numerical simulation to examine the phenomenon (MOSFET). Zhou et al. [41] constructed one/two-dimensional (1D/2D) TED models of rings by using the nonlocal dual-phase-lag (DPL) framework and the modified-couple-stress (MCS) concept. In order to represent heat transfer on the nanoscale, the dual-phase-lag (DPL) model is presented together with a tailored normalizing approach. Zhang and He [42] studied the dynamic behavior of a limited thermoelastic rod fixed at both ends and exposed to a moving heat source within the context of the extended thermoelasticity with nonlocal influence and memory-dependent derivative. Laplace transformation and numerical inversion are used to develop and solve the associated governing equations. In [43], Zhang et al. used a two-phase local/nonlocal mixture theory of strain- and stress-driven types to propose predictive models of the free vibration of Euler-Bernoulli beams in a uniformly heated environment. With the help of Hamilton's principle, we are able to derive the equation of motion and the conventional boundary conditions, and the constitutive equation is written in local/nonlocal mixed integral form using a bi-Helmholtz kernel.
Considering the effects of size and heat variations on softening hardness and elastic strengthening patterns in moving nano and nanostructures, the investigation into continuous size-dependent concepts, generalized heat conduction, and mass mechanisms of thermoelastic responses is still lacking, according to the aforementioned overview. To the author's knowledge, no one has ever investigated the thermoelastic resonances in nanobeams under external transversal excitation, non-localization, and thermomechanical influences using the generalized theory of thermoelasticity. The research aims to investigate how the nanoscale and longitudinal speed influence the various beam behaviors.
This work aims to present a governing system of equations that describe nonlocal thermoelastic moving Euler-Bernoulli beams that are excited from the outside in a transverse direction. When considering the nonlocal scale implications in the nanobeam resonances, the novel size-dependent thermoelastic model is based on Eringen's hypothesis of nonlocal elasticity and the DPL heat transfer model. Differential motion equations were also derived from the Euler-Bernoulli nanobeam theory, based on the generalized Hamiltonian concept. The Laplace transform and its inversion are used in the deductive process. The effects of nonlocal phase lags, moving speed, and external excitation will be studied and graphically depicted.
Consider an Euler-Bernoulli nanobeam of length L that has an initial axial tension P at either end. In Figure 1, we have a schematic diagram of a nanobeam moving at a constant horizontal velocity υ. Initially, the body is in equilibrium such that the beam is not restricted in any way, is not subject to any pressure, and maintains the same temperature T0. When the beam is bent around the x -axis, small-amplitude vibrations occur, which allow the deflection to be described using the linear Euler-Bernoulli hypothesis of mechanics. During bending, any plane cross-section initially parallel to the beam axis stays parallel to the reference plane and perpendicular to the plane. This means that the displacements can be expressed as
u=−z∂w∂x, v=0, w(x,y,z,t)=w(x,t), | (2.1) |
where w denotes the transverse displacement.
It is possible to establish the governing equation for nanobeam transverse vibration by employing Hamilton's principle. By applying Newton's second law of motion and the condition of moment equilibrium, one can derive the dynamic equation of motion for the element that is subject to an axial dynamic load P. This equation of motion may be written as [44,45]
∂2M∂x2+m(∂2w∂t2+2υ∂2w∂x∂t+υ2∂2w∂x2)+P∂2w∂x2=0, | (2.2) |
M(x,t) represents the bending moment, m=ρA is mass per unit length, ρ is the density, and A represents the cross-sectional area.
The components of the local stress and strain tensors are given by
τkl=λεmmδkl+μεkl−γδklθ, | (2.3) |
2εkl=∂uk∂xl+∂ul∂xk, | (2.4) |
where uk are the displacement vector components, τkl are the local stress tensor components. Also, θ=T−T0 is the of temperature change, T is the temperature distribution, T0 is the environmental temperature, εkl are the classical Cauchy relations, λ and μ are Lamé's constants, γ=αt(3λ+2μ)=Eαt/(1−2ν), αt is the coefficient of thermal expansion, E denotes Young modulus, ν is Poisson's ratio and δkl is Kronecker delta function. The Lamé constants λ and μ can be expressed as λ=Eν/(1+ν)(1−2ν) and μ=E/2(1+ν).
The dynamic study of the nanostructure is done using a nonlocal stress model. The basic equations of Eringen's nonlocal elasticity theory [12,13,14] incorporate spatial integrals that reflect the weighted averages of the contributions of associated strain tensors at the corresponding location in the body. As a result, the theory employs a spatial integral constitutive correlation to incorporate the small-size scale effect. The integral form of the nonlocal constitutive relation can be represented as follows in nonlocal elasticity theory:
σkl(x)=∫τkl(x′)Kξ(|x−x′|,ξ)dV(x′),∀x∈V, | (2.5) |
where σkl are the nonlocal stress tensor components at any point x, Kξ(|x−x′|,ξ) represents the attenuation function (kernel) which includes nonlocal influences into the constitutive relations, |x−x′| is a distance in Euclidean norm and ξ=(e0a)2 is the nonlocal parameter where a is the intrinsic property length (characteristic internal length) and e0 is a material constant that can be determined from molecular dynamics simulations or by using the dispersive curve of the Born-Karman model of lattice dynamics. Eringen [12,13,14] provided a differential form of constitutive equations by using an appropriate kernel function Kξ in the preceding integral form of the equation can be derived as [46]
σkl−ξ∂2σkl∂x2=τkl. | (2.6) |
According to Eringen's nonlocal elasticity theory, the one-dimensional nonlocal constitutive relation can be written as [47,48]
σx−ξ∂2σx∂x2=−E(z∂2w∂x2+αTθ), | (2.7) |
where σx represents the nonlocal axial stress, E is Young's modulus, αT=αt/(1−2ν) and θ=T−T0 indicates the over-temperature distribution.
The bending moment may be calculated using the Euler-Bernoulli beam theory as follows:
M(x,t)=b∫h/2−h/2σxzdz. | (2.8) |
When the of the axial stress σx is multiplied by z and integrated across the cross-section area of the nanobeam, the flexure moment satisfies the following equation:
M(x,t)−ξ∂2M∂x2=−EI(∂2w∂x2+αTMT), | (2.9) |
where I=bh3/12 is the moment of inertia and MT denotes the thermal moment which is obtained by
MT=12h3∫h/2−h/2θ(x,z,t)zdz. | (2.10) |
Equation (2.2) may be substituted into Eq (2.9), yielding the following equation of the flexure moment:
M(x,t)=−ξm(∂2w∂t2+2υ∂2w∂x∂t+υ2∂2w∂x2+Pm∂2w∂x2)−EI(∂2w∂x2+αTMT). | (2.11) |
Equation (2.2) can be represented as a nonlocal partial differential equation with a constant coefficient of the lateral displacement w(x,t) by substituting Eq (2.11) into Eq (2.2):
(1+ξmυ2EI)∂4w∂x4+[(mEI∂2∂t2+2υmEI∂2∂x∂t+PEI∂2∂x2)(ξ∂2∂x2−1)]w−mυ2EI∂2w∂x2+αT∂2MT∂x2=0. | (2.12) |
When ξ=0 is used in the preceding equations, the relevant local equation of motion for moving the Euler-Bernoulli beam is restored.
Tzou [38,39] suggested a dual-phase-lag (DPL) model that ignores the instantaneous interaction of temperature and energy. The DPL model, in particular, provides a straightforward and realistic representation of heat transmission in skin tissues. The DPL model has also been applied to describethe thermal response to laser transmission, thermal shock, and photothermal excitement. Also, this theory is built logically to generate a coherent theory that can logically contain thermal pulse excitation. Tzou's theory is a modified version of the conventional thermoelasticity model in which the Fourier law is substituted with an approximation of the following equation [38]:
→q(x,t+τq)=−K∇θ(x,t+τθ), | (2.13) |
where →q denotes the heat flux vector, and K symbolizes the thermal conductivity. The phase lag of the heat flow is τq, while the temperature gradient's phase lag is τθ.
The modified heat conduction equation for the DPL model may be expressed by using the first-order approximation of the previous equation as
(1+τq∂∂t)→q=−K∇(1+τθ∂∂t)θ. | (2.14) |
The equation for the conservation of energy is written as follows:
CE∂θ∂t+γT0∂e∂t=−∇·→q+Q, | (2.15) |
where CE denotes the specific heat per unit mass at constant strain, e=∇·→u represent the cubical dilatation, →u is the displacement vector, and Q signifies the internal energy generation (heat source).
When Eqs (2.14) and (2.15) are combined, we get the DPL heat conduction model as
(1+τq∂∂t)(ρCE∂θ∂t+γT0∂e∂t−Q)=K(1+τθ∂∂t)∇2θ. | (2.16) |
One can use Eq (2.1) to get the DPL heat equation for the current situation in the absence of a heat generation (Q=0) as
(1+τθ∂∂t)∂2θ∂x2+(1+τθ∂∂t)∂2θ∂z2=(1+τq∂∂t)[ρCEK∂θ∂t−γT0Kz∂∂t(∂2w∂x2)]. | (2.17) |
The DPL model simplifies the traditional Fourier's law when τq=0=τθ. Also, the Lord and Shulman thermoelastic model can be obtained when τθ and τq>0.
Assume that the temperature increment θ(x,z,t) increases sinusoidally (sin(πz/h)) along the thickness direction for an extremely nanobeam. Furthermore, there is no heat movement along the upper and bottom surfaces of the nanobeam, resulting in ∂θ∂z=0 at z=±h2. In this case,
MT=12h3∫h/2−h/2θzdz=12hπ2[θ|h/2−h/2−z∂θ∂z|h/2−h/2]=−12hπ2∫h2−h2∂2θ∂z2zdz. | (2.18) |
Substituting Eq (2.18) into (2.17) leads to
(1+τθ∂∂t)[∂2MT∂x2−π2h2MT]=(1+τq∂∂t)[ρCEK∂MT∂t−βT0π2h24K∂∂t(∂2w∂x2)]. | (2.19) |
To help with the solution, the dimensionless variables listed below are used:
(x′,L′,u′,w′,z′)=ηc(x,L,u,w,z),Θ′=ΘT0,σ′x=σxE,M′T=MTEAh,υ′=υc,M′=−MηcEI,(t′,t′0,τ′q,τ′θ)=ηc2(t,t0,τq,τθ),η=ρCEK,c=√Eρ. | (2.20) |
Applying the dimensionless values from (2.20) to Eqs (2.11)-(2.12) and (2.19), and then suppressing the primes for convenience, we obtain
M(x,t)=ξ(∂2w∂t2+2υ∂2w∂x∂t+υ2∂2w∂x2+P∂2w∂x2)+∂2w∂x2+24T0αThπ2MT. | (2.21) |
(1+ξυ2)∂4w∂x4+12h2[(∂2∂t2+2υ∂2∂x∂t+P∂2∂x2)(ξ∂2∂x2−1)]w−12υ2h2∂2w∂x2+24T0αThπ2∂2MT∂x2=0. | (2.22) |
(1+τθ∂∂t)[∂2MT∂x2−π2h2MT]=(1+τq∂∂t)[∂MT∂t−EαTπ2h24ηK∂3w∂t∂x2]. | (2.23) |
When the two ends of the microbeams are simply supported and kept at a sinusoidal temperature with a pulse width t0 at the first end (x=0) while the second end (x=L) is insulated, the boundary conditions are given by the expression:
w(x,t)=0,M(x,t)=0 at x=0,L, | (2.24) |
θ=θ(z,t)=θ0z sin(πt0t),0≤t≤t0 on x=0, | (2.25) |
∂θ∂x=0 at x=0,L | (2.26) |
Inserting Eqs (2.25) and (2.26) into Eq (2.10) leads to
MT=M0 sin(πt0t), 0≤t≤t0 on x=0, | (2.27) |
∂MT∂x=0 at x=0,L | (2.28) |
Most earlier investigations assumed that the transverse excitation axial force was either non-existent or fixed. Actually, the axial force can change over time. It is supposed that the dimensionless transverse excitation axial tension is a time-dependent function as [1]
P=Ps+PD cos(ωt). | (2.29) |
This equation uses ω to represent the frequency of the load and the terms " Ps " and " PD "to express the static and dynamic components of axial force.
Nonlinear differential equations are notoriously difficult to solve analytically, especially in their closed-form form. Many different numerical and approximation methods have been used in the literature to solve this problem. One can consider the following as initial conditions:
w(x,t)|t=0=0=∂w(x,t)∂t|t=0, MT(x,t)|t=0=0=∂MT(x,t)∂t|t=0. | (3.1) |
When the Laplace transform technique is applied to Eqs (2.7)-(2.13), one obtains the transformed differential equations that are shown below:
−M=(1+ξυ2+ξ−P)d2−wdx2+2υsξd−wdx+ξs2−w+24T0αThπ2−MT, | (3.2) |
d4−wdx4+A3d3−wdx3+A2d2−wdx2+A1d−wdx+A0−w=−B1d2−MTdx2, | (3.3) |
−A4d2−wdx2=(d2dx2−B2)−MT, | (3.4) |
where
A0=12s2h2(1+ξυ2+ξ−P),A1=2υA0s,A2=A0(s2ξ−υ2−−P),A3=2υξA0s,B1=24T0αTπ2h(1+ξυ2+ξ−P),B2=π2h2+s(1+τqs)1+τθs,A4=sγπ2h(1+τqs)24Kη(1+τθs),−P=Pss+sPDs2+ω2. | (3.5) |
By eliminating −w or −Θ from Eqs (3.3) and (3.4), the differential equation governing the functions −w and −Θ may be found.
[a6d6dx6+a5d5dx5+a3d4dx4+a3d3dx3+a2d2dx2+a1ddx+a0]{−w,−Θ}, | (3.6) |
where
a5=A3,a4=A2−B1A4, a3=A1−B2A3,a2=A0−B2A2,a1=−B2A1,a0=−B2A0. | (3.7) |
The solution to the Eq (3.6) may be written as
{−w,−MT}=∑6i=1{Ci,C′i}emix, | (3.8) |
where Ci and C′i are the integral constants and the parameters mi(i=1,2,...,6) are the roots of the equation
m6+a5m5+a4m4+a3m3+a2m2+a2m+a0=0. | (3.9) |
The compatibility between Eqs (3.8) and (3.4) gives
C′i=βiCi, βi=−A4m2im2i−B2. | (3.10) |
Substituting Eq (3.8) into Eq (2.1) after applying the Laplace transform, we get the displacement ˉu as follows:
ˉu=∑6i=1miCiemix. | (3.11) |
The bending moment −M given in Eq (3.2) with the help of Eq (3.8), takes the form
−M(x,t)=∑6i=1(υ2ξm2i+m2i+2υsξmi+ξs2+24T0αThπ2βi)Ciemix. | (3.12) |
The boundary conditions (2.24), (2.27) and (2.28) are as follows when the Laplace transformation
−w(x,s)|x=0,L=0,d−w(x,s)dx|x=0,L=0,−Θ(x,s)|x=0=πt0π2+t20s2=ˉG(s),d−Θ(x,s)dx|x=L=0. | (3.13) |
Substituting Eq (3.8) into the boundary mentioned above conditions yields six linear equations in matrix form as
∑6i=1emiLCi=0,∑6i=1miCi=0,∑6i=1miemiLCi=0,∑6i=1Ci=0,∑6i=1βiCi=ˉG(s),∑6i=1βimiemiLCi=0. | (3.14) |
The unknown parameters Ci(i=1,2,...,6) are obtained from the solution of the preceding system of linear equations. This concludes the solution to the issue in the domain of the Laplace transform.
To calculate the studied physical domains such as bending moment distributions, temperature, displacement, and pressure in the beam, the Laplace domains must be reversed to the time domain. However, these solutions are too complex to be directly inverted; therefore, no direct analytic solutions can be obtained. Consequently, the Riemann-sum approximation approach is employed to generate numerical results. In this approach, any function −f(x,t) in the Laplace domain may be inverted into the time domain as [38]
f(x,t)=eωtt[12Re[ˉF(x,ω)]+Re∑Nφ=0(ˉF(x,ω+iφπt)(−1)n)]. | (4.1) |
The influence of many elements, including the nanobeam's flexural stiffness, axial speed, phase delays, the static and dynamic parts of its axial force, and its vibration properties, was investigated using numerical computations. The non-dimensional investigated variables in the nanobeam are obtained by computational Laplace inversion using the Riemann-sum approximation stated in Eq (4.1). This study uses a silicon beam to examine the thermoelastic interaction behavior. The following are the physical values related to silicon [18,20]:
E=169GPa,ρ=2330kg/m3,CE=713J/(kgK),T0=293K, |
αT=2.59×10−6K−1,ν=0.22,K=156W/(mK). |
The numerical values of the studied non-dimensional domains were calculated, and graphs were generated using the dimensional physical values mentioned above. Based on the dimensionless values of the physical quantities, the beam lengths of L=10h=1, b=h/2, z=h/6, and t=0.12 are considered. The distributions of the thermal moment MT, Lateral vibration w, bending moment M, and axial displacement u domains are graphically represented for the x, and z directions by inverting Laplace transforms using Eq (4.1). The following three cases are numerically calculated and discussed.
Calculations were made to determine the numeric data of the non-dimensional research fields under investigation, and graphs were constructed based on the previous physical values. The dimensions of the nanobeam are considered to be L=10h=1, b=h/2, and t=0.12. By transposing the Laplace transforms with the help of Eq (4.1), the patterns of the thermal moment MT, lateral vibration w, bending moment M, and axial deformation u domains have been graphically displayed for the x axis at z=h/6. The following important situations are analyzed using figures and then highlighted.
The so-called nonlocal beams are a subcategory of beam structures characterized by applying the constitutive equation of nonlocal elasticity in order to account for small-scale influences. In published studies, these types of nonlocal beams are often called "nanobeams" because their structures lie on nanoscale dimensions. Due to its inherent length-free construction, the conventional continuum mechanics technique is not applicable at the nano-length scale. The small-scale effects and long-distance behavior in nanomechanical systems cannot be ignored the way they can be ignored in macroscopic mechanical systems.
Experiments on their mechanical characteristics have indicated a size effect that is not observable at the macroscale. This impact becomes more pronounced when the dimensions of the nanoscale structure approach those of the microstructure. Therefore, studying the size influence on the dynamic responses of axially moving nanoscale beams employing suitable models is essential to designing such structural systems.
In this section, a nonlocal continuum model will be used to figure out how nanobeams behave differently depending on their size. The effect of the dimensionless nonlocal factor ξ on the lateral vibration w amplitude, the thermal moment of inertia MT, displacement u, and bending moment M for a range of different values will be examined. These different effects are illustrated by introducing Figures (2)-(6). It can be seen that the local thermoelastic model is represented by the value ξ=0, while the other values (ξ=0.001 and 0.003) are represented by the nonlocal thermoelastic theory. In this case, it is assumed that the pulse width parameter (t0=0.1) and the delay phase coefficients τq=0.2 and τθ=0.15 remain constant. Also, the dimensionless transfer velocity of the nanobeam is also assumed to be constant (υ=1.2).
Figure 2 depicts the variations in thermal deflection w. The graphic depicts the lateral deflection pattern w, which always begins at zero (i.e., vanishes) and satisfies the problem's boundary condition at the edges x=0 and L. We also discovered that the deflection w reaches its maximum value at a specific distance from the nanobeam edge and then decreases as the distance x increases. As depicted, increasing the value of the nonlocal factor decreases the wave propagation rate of the lateral deflection w and causes it to vanish more rapidly. Compared with the results produced by standard vibration theory, the nonlocal effect results in more intense vibration signals.
In Figure 3, we can see the effect of changing the nonlocal factor ξ on the thermal moment MT of a moving nanobeam while it is subjected to a time-varying external axial force. The thermal moment MT is shown to be relatively insensitive to variations in the nonlocal parameter (see Figure 3). Observably, the nonlocal parameter appears to have minimal effect on the nanobeam's thermal moment. Moreover, moving away from the heat source in the direction of the spread of the heat wave causes the thermal moment MT to drop significantly as the distance x grows (see Figure 4).
Contrary to the expectations of standard continuum models, actual findings have shown that size effects have a major impact on the physical properties and mechanical responses of NEMS at the nanoscale [49,50]. The influence of the small scale on lattice dynamics depends on the crystal structure and the sort of material science being examined [51]. Unlike discrete microscopic or molecular dynamical simulations, which require much computer work, this continuum theory can be used to model submicron or nanoscale structures [52].
Figure 4 shows the variations in axial displacement u over the interval x∈[0,1] at a very short time t=0.12, for nonlocal moduli ξ=0, 0.001, and 0.003. As can be seen in the graph, the displacement u begins with negative values and grows in amplitude as the beam length increases. It is clear that as the nonlocal factor ξ is increased, the displacement u grows in the interval x∈[0,0.4] and shrinks in the region x∈[0.4,1]. Additionally, the graph clearly shows that the split between local and nonlocal thermoelastic concepts persists.
Figure 5 depicts how the bending moment changes as a function of the nonlocal component, which is dimensionless. Figure 5 shows that the nanobeam's bending moment varies as a function of distance from its ends, starting at zero at, and increasing steadily to a maximum some distance from the beam's ends before decreasing back to zeroat. As seen in Figure 5, the bending moment is highly sensitive to variations in the nonlocal constant.
Figure 6 depicts how the temperature changes θ along the longitudinal direction as a function of the nonlocal factor ξ. As can be seen, the non-dimensional temperature θ increases to its highest value at x=0 fluctuate along the longitudinal axis, then declines to zero at the end of the nanobeam resonator. The postulated thermal boundary conditions are consistent with this pattern. The non-dimensional temperature increases when the nonlocal factor's value increases.
Once again, it is clear that Eringen's nonlocal theory of elasticity predicts a larger bending moment than the local theory of elasticity. In other words, the nonlocal effects soften the structures, making them more adaptable. Mechanical qualities at the micro and nanoscale should be considered during the construction and design of MEMS and NEMS devices.
The results shown in Figures 2-6 demonstrate that the elastic field is more significantly affected by changes in the small-scale parameter value than the temperature profile. Minor changes in the lateral deflection, coupled with temperature field changes in the extended coupled thermoelasticity of the DPL theory, cause the temperature field's small alterations.
High-velocity cars and trucks, spacecraft antennas, and advanced robotic manipulators can benefit from axially-moving nanoscale beams exceptional mechanical and physical features. Recently, researchers have explored the subject of studying the resonance of an axially moving beam under the influence of an external force. Researchers have examined various practical applications, such as a transmission system, medical nanorobots, power cutting tools, tape cutting tools, and magnetic disks.
In the second scenario, the effects of the vibrational heat pulse on the distribution of the thermal bending moment of the nanobeam are studied. As well as deformation caused by turbulence and bending moment change in addition to stress when changing the axial velocities of the beam. In this case, three different velocity values (υ=1.2, 1.3 and 1.4) will be taken into account if the values of the nonlocal index and the values of the phase lag factors τq and τθ are held constant. In Figures 7-11, the effect of the axial velocity of the beam on the longitudinal vibration response of the fine beams is shown. It is also shown that the different field curves inside the beam are very sensitive to the axial velocity. It can be revealed by looking at the field curves that the amplitudes of thermal and mechanical waves increase with the increase in the axial speed with which the bite is moving. In addition, it is observed in the period x∈[0,0.4], the amounts of distortion decrease with increasing rate while increasing in the region x∈[0.4,1]. With the axial speed of the nanobeam impact, the thermal bending moment is less than it would be without it. As a result, it is clear that the beam's axial velocity significantly impacts the safety design of nanobeams. It is found that the velocity parameter does not have a significant effect on the temperature change.
The axially moving continuum types are paper sheets, drive shafts, fiber textile products, oil and gas pipelines, and various wire and structural steel processing technologies such as straightening lines. Excitations caused by continuously moving materials are what ultimately lead to failure and poor quality. As a consequence of this, the investigation of these vibrations is of utmost significance in the system design. Additionally, good agreement is found between the present results and the documented literature when analyzing the local results of the traveling Euler-Bernoulli nanobeam described in references [53,54]. That being said, the validity of the present findings can be independently confirmed. Thermomechanical disturbances can arise in the nanobeam if it experiences a considerable transverse deformation in the orthogonal direction to the rate [55]. In this way, noise that isn't expected might be introduced, which can reduce the structure's usefulness in some contexts, cause wear and tear on the system, and lower quality overall. During production, these things must be considered to ensure that the nanostructure is not overworked and loses its performance.
Engineers must ensure that axially moving nano-systems do not become unstable and that excessive vibrations are eliminated. System velocity is key in determining axial motion continuation's dynamic response and stability. Different instability mechanisms, such as divergence and flutter, manifest at different system velocities.
When studying and making new NEMS or MEMS systems, it is very important to study the thermodynamic stability of micro or nanostructures when exposed to time-dependent transverse external excitation. In this subsection, we will explore the effect of static (Ps), dynamic (PDcos(ωt)), and amplitude external transverse excitation (P=Ps+PDcos(ωt)) on the responses of the domains considered. The impact of various kinds of external transverse stimulation on all investigated physical fields is depicted in Figures 12-16.
In this case, the values of components of axial force, Ps=0.8 and PD=0.6 are considered, while the angular frequency ω of the employed transverse excitement remains constant (ω=0.3). It is assumed that the nonlocal factor ξ=0.001, the speed of axial motion υ=1.2, the pulse width t0=0.1 and also the parameters τq and τθ stay unchanged in this scenario. The figures show that the behavior of different domains inside the nanobeam is very sensitive to the strength of the axial tension. This effect also depends on the type of this external induction, whether it is static, dynamic, or both. In different cases, the curves of the studied fields exhibit the same behavior with different amounts. From these curves, it is also clear that the static axial external transverse excitation increases the magnitudes of various fields while the dynamic transverse excitation decreases the size of these fields.
This work investigated thermoelastic vibrations in a nanobeam moving axially at a constant speed and subjected to an axial transverse dynamic force. We obtain the linear motion equations by applying Hamilton's principle to the Euler-Bernoulli beam hypothesis. In addition, the thermal part of the problem was addressed by including a two-phase delay in the modified thermoelastic framework (DPL model). An effective method for finding solutions was provided, and it involved using the Laplace transform and a numerical inversion strategy. The influence of several factors, including phase delays, axial translation velocity, nonlocal parameters, statics, and dynamics of the transverse excitation, on the system's response, was examined. The following are the most important conclusions that can be drawn from this investigation:
1) The nonlocal parameter significantly influences all the minimum and maximum values of the different domains. Larger nonlocal parameter values result in an undamped system. In other words, nonlocal effects "soften" the structures, making them more adaptable.
2) Mechanical and thermal vibration studies on such nano-systems are critical to ensuring system integrity and stability. It can also be used to simulate the mechanical properties of basic elements in AMEMS and ANEMS.
3) The presence of a constant motion velocity of the nanobeam leads to large phase shifts in the transverse dynamic profiles, but the effect of the thermal change is negligible. Also, if the velocity increases, the phase gap between the variables of deformation and bending torque should decrease.
4) Unlike conventional models, the two-phase thermoelastic model predicts that waves can only move at a specific speed. This means that the theory of thermal expansion proposed in this article is more in line with how matter works as well as physical phenomena.
5) The behavior of different domains inside the nanobeam is very sensitive to the strength of the axial tension. This effect also depends on the type of this external induction, whether it is static, dynamic, or both.
The current work with axially moving nanobeams has many uses in many areas of science and engineering, such as making and designing some moving structures, civil, structural, and aerospace engineering, and systems engineering. Also, the current study covers systems like belt conveyors, clinical nanorobots, control saws, tape cutting tools, magnetic media, and many others.
The authors extend their appreciation to the Deputyship for Research & Innovation, Ministry of Education, Saudi Arabia for funding this research work through the project number (QU-IF-05-03-26925). The authors also thank to Qassim University for technical support.
The authors declare no conflicts of interest.
[1] |
M. Arda, M. Aydogdu, Dynamic stability of harmonically excited nanobeams including axial inertia, J. Vib. Control, 25 (2019), 820–833. https://doi.org/10.1177/1077546318802430 doi: 10.1177/1077546318802430
![]() |
[2] |
A. Apuzzo, R. Barretta, R. Luciano, F. M. de Sciarra, R. Penna, Free vibrations of Bernoulli-Euler nano-beams by the stress-driven nonlocal integral model, Compos. Part B-Eng., 123 (2017), 105–111. https://doi.org/10.1016/j.compositesb.2017.03.057 doi: 10.1016/j.compositesb.2017.03.057
![]() |
[3] |
C. Li, C.W. Lim, J. L. Yu, Q. C. Zeng, Analytical solutions for vibration of simply supported nonlocal nanobeams with an axial force, Int. J. Struct. Stab. Dyn., 11 (2011), 257–271. https://doi.org/10.1142/s0219455411004087 doi: 10.1142/s0219455411004087
![]() |
[4] |
Y. Huang, J. Fu, A. Liu, Dynamic instability of Euler-Bernoulli nanobeams subject to parametric excitation, Compos. Part B-Eng., 164 (2019), 226–234. https://doi.org/10.1016/j.compositesb.2018.11.088 doi: 10.1016/j.compositesb.2018.11.088
![]() |
[5] |
N. Nešić, M. Cajić, D. Karličić, G. Janevski, Nonlinear superharmonic resonance analysis of a nonlocal beam on a fractional visco-Pasternak foundation, P. I. Mech. Eng. C-J. Mech., 235 (2021), 4594–4611. https://doi.org/10.1177/0954406220936322 doi: 10.1177/0954406220936322
![]() |
[6] |
N. A. Fleck, J. W. Hutchinson, Strain gradient plasticity, Adv. Appl. Mech., 33 (1997), 296–361. https://doi.org/10.1016/S0065-2156(08)70388-0 doi: 10.1016/S0065-2156(08)70388-0
![]() |
[7] |
A. R. Hadjesfandiari, G. F. Dargush, Couple stress theory for solids, Int. J. Solids. Struct., 48 (2011), 2496–2510. https://doi.org/10.1016/j.ijsolstr.2011.05.002 doi: 10.1016/j.ijsolstr.2011.05.002
![]() |
[8] |
F. Yang, A. C. M. Chong, D. C. C. Lam, P. Tong, Couple stress based strain gradient theory for elasticity, Int. J. Solids. Struct., 39 (2002), 2731–2743. https://doi.org/10.1016/s0020-7683(02)00152-x doi: 10.1016/s0020-7683(02)00152-x
![]() |
[9] |
H. M. Ma, X. L. Gao, J. N. Reddy, A microstructure-dependent Timoshenko beam model based on a modified couple stress theory, J. Mech. Phys. Solids, 56 (2008), 3379–3391. https://doi.org/10.1016/j.jmps.2008.09.007 doi: 10.1016/j.jmps.2008.09.007
![]() |
[10] |
B. Akgöz, Ö. Civalek, Longitudinal vibration analysis for microbars based on strain gradient elasticity theory, J. Vib. Control, 20 (2012), 606–616. https://doi.org/10.1177/1077546312463752 doi: 10.1177/1077546312463752
![]() |
[11] |
B. Akgöz, Ö. Civalek, Buckling analysis of cantilever carbon nanotubes using the strain gradient elasticity and modified couple stress theories, J. Comput. Theor. Nanosci., 8 (2011), 1821–1827. https://doi.org/10.1166/jctn.2011.1888 doi: 10.1166/jctn.2011.1888
![]() |
[12] |
A. C. Eringen, On differential equations of nonlocal elasticity and solutions of screw dislocation and surface waves, J. Appl. Phys., 54 (1983), 4703–4710. https://doi.org/10.1063/1.332803 doi: 10.1063/1.332803
![]() |
[13] |
A. C. Eringen, A unified theory of thermomechanical materials, Int. J. Eng. Sci., 4 (1966), 179–202. https://doi.org/10.1016/0020-7225(66)90022-x doi: 10.1016/0020-7225(66)90022-x
![]() |
[14] | A. C. Eringen, Nonlocal continuum field theories, Springer, 2002. |
[15] |
Y. G. Hu, K. M. Liew, Q. Wang, X. Q. He, B. I. Yakobson, Nonlocal shell model for elastic wave propagation in single- and double-walled carbon nanotubes, J. Mech. Phys. Solids, 56 (2008), 3475–3485. https://doi.org/10.1016/j.jmps.2008.08.010 doi: 10.1016/j.jmps.2008.08.010
![]() |
[16] |
J. Peddieson, G. R. Buchanan, R. P. McNitt, Application of nonlocal continuum models to nanotechnology, Int. J. Eng. Sci., 41 (2003), 305–312. https://doi.org/10.1016/s0020-7225(02)00210-0 doi: 10.1016/s0020-7225(02)00210-0
![]() |
[17] |
Q. Wang, Wave propagation in carbon nanotubes via nonlocal continuum mechanics, J. Appl. Phys., 98 (2005), 124301. https://doi.org/10.1063/1.2141648 doi: 10.1063/1.2141648
![]() |
[18] |
A. E. Abouelregal, M. Marin, The size-dependent thermoelastic vibrations of nanobeams subjected to harmonic excitation and rectified sine wave heating, Mathematics, 8 (2020), 1128. https://doi.org/10.3390/math8071128 doi: 10.3390/math8071128
![]() |
[19] |
A. E. Abouelregal, D. Atta, H. M. Sedighi, Vibrational behavior of thermoelastic rotating nanobeams with variable thermal properties based on memory-dependent derivative of heat conduction model, Arch. Appl. Mech., 2022. https://doi.org/10.1007/s00419-022-02110-8 doi: 10.1007/s00419-022-02110-8
![]() |
[20] |
A. E. Abouelregal, K. M. Khalil, W. W. Mohammed, D. Atta, Thermal vibration in rotating nanobeams with temperature-dependent due to exposure to laser irradiation, AIMS Mathematics, 7 (2022), 6128–6152. https://doi.org/10.3934/math.2022341 doi: 10.3934/math.2022341
![]() |
[21] |
P. L. Bian, H. Qing, Structural analysis of nonlocal nanobeam via FEM using equivalent nonlocal differential model, Eng. Comput., 2022. https://doi.org/10.1007/s00366-021-01575-5 doi: 10.1007/s00366-021-01575-5
![]() |
[22] |
D. Scorza, S. Vantadori, R. Luciano, Nanobeams with internal discontinuities: a local/nonlocal approach, Nanomaterials-Basel, 11 (2021), 2651. https://doi.org/10.3390/nano11102651 doi: 10.3390/nano11102651
![]() |
[23] |
G. Y. Zhang, Z. W. Guo, Y. L. Qu, X. L. Gao, F. Jin, A new model for thermal buckling of an anisotropic elastic composite beam incorporating piezoelectric, flexoelectric and semiconducting effects, Acta Mech., 233 (2022), 1719–1738. https://doi.org/10.1007/s00707-022-03186-7 doi: 10.1007/s00707-022-03186-7
![]() |
[24] |
C. D. Mote, Stability of systems transporting accelerating axially moving materials, J. Dyn. Syst., 97 (1975), 96–98. https://doi.org/10.1115/1.3426880 doi: 10.1115/1.3426880
![]() |
[25] |
X. Zhao, C. F. Wang, W. D. Zhu, Y. H. Li, X. S. Wan, Coupled thermoelastic nonlocal forced vibration of an axially moving micro/nanobeam, Int. J. Mech. Sci., 206 (2021), 106600. https://doi.org/10.1016/j.ijmecsci.2021.106600 doi: 10.1016/j.ijmecsci.2021.106600
![]() |
[26] |
Y. Q. Wang, X. B. Huang, J. Li, Hydroelastic dynamic analysis of axially moving plates in continuous hot-dip galvanizing process, Int. J. Mech. Sci., 110 (2016), 201–216. https://doi.org/10.1016/j.ijmecsci.2016.03.010 doi: 10.1016/j.ijmecsci.2016.03.010
![]() |
[27] |
Y. W. Zhang, B. Yuan, B. Fang, L. Q. Chen, Reducing thermal shock-induced vibration of an axially moving beam via a nonlinear energy sink, Nonlinear Dynam., 87 (2017), 1159–1167. https://doi.org/10.1007/s11071-016-3107-4 doi: 10.1007/s11071-016-3107-4
![]() |
[28] |
I. Esen, A. A. Daikh, M. A. Eltaher, Dynamic response of nonlocal strain gradient FG nanobeam reinforced by carbon nanotubes under moving point load, Eur. Phys. J. Plus, 458 (2021), 136. https://doi.org/10.1140/epjp/s13360-021-01419-7 doi: 10.1140/epjp/s13360-021-01419-7
![]() |
[29] |
A. Shariati, D. W. Jung, H. Mohammad-Sedighi, K. K. Żur, M. Habibi, M. Safa, On the vibrations and stability of moving viscoelastic axially functionally graded nanobeams, Materials, 13 (2020), 1707. https://doi.org/10.3390/ma13071707 doi: 10.3390/ma13071707
![]() |
[30] |
B. A. Hamidi, S. A. Hosseini, H. Hayati, R. Hassannejad, Forced axial vibration of micro and nanobeam under axial harmonic moving and constant distributed forces via nonlocal strain gradient theory, Mech. Based Des. Struct., 50 (2022), 1491–1505. https://doi.org/10.1080/15397734.2020.1744003 doi: 10.1080/15397734.2020.1744003
![]() |
[31] | M. B. Bera, M. K. Mondal, B. S. Mahapatra, G. Roymahapatra, P. P. Acharjya, Generalized theory of thermoelasticity in isotropic and homogenious thermoelastic solids, Turk. J. Comput. Math. Ed., 11 (2020), 1877–1885. |
[32] |
M. A. Biot, Thermoelasticity and irreversible thermodynamics, J. Appl. Phys., 27 (1956) 240–253. https://doi.org/10.1063/1.1722351 doi: 10.1063/1.1722351
![]() |
[33] |
P. Chadwick, I. N. Sneddon, Plane waves in an elastic solid conducting heat, J. Mech. Phys. Solids, 6 (1958), 223–230. https://doi.org/10.1016/0022-5096(58)90027-9 doi: 10.1016/0022-5096(58)90027-9
![]() |
[34] |
H. W. Lord, Y. Shulman, A generalized dynamical theory of thermoelasticity, J. Mech. Phys. Solids, 15 (1967), 299–309. https://doi.org/10.1016/0022-5096(67)90024-5 doi: 10.1016/0022-5096(67)90024-5
![]() |
[35] |
A. E. Green, K. A. Lindsay, Thermoelasticity, J. Elasticity, 2 (1972), 1–7. https://doi.org/10.1007/BF00045689 doi: 10.1007/BF00045689
![]() |
[36] |
A. E. Green, P. M. Naghdi, On undamped heat waves in an elastic solid, J. Therm. Stresses, 15 (1992), 253–264. https://doi.org/10.1080/01495739208946136 doi: 10.1080/01495739208946136
![]() |
[37] |
A. E. Green, P. M. Naghdi, Thermoelasticity without energy dissipation, J. Elasticity, 31 (1993), 189–208. https://doi:10.1007/bf00044969 doi: 10.1007/bf00044969
![]() |
[38] |
D. Y. Tzou, A unified field approach for heat conduction from macro- to micro-scales, J. Heat Trans., 117 (1995), 8–16. https://doi.org/10.1115/1.2822329 doi: 10.1115/1.2822329
![]() |
[39] | D. Y. Tzou, Macro-to microscale heat transfer: the lagging behavior, John Wiley & Sons, 2014. https://doi.org/10.1002/9781118818275 |
[40] |
J. Ghazanfarian, Z. Shomali, Investigation of dual-phase-lag heat conduction model in a nanoscale metal-oxide-semiconductor field-effect transistor, Int. J. Heat. Mass Trans., 55 (2012), 6231–6237. https://doi.org/10.1016/j.ijheatmasstransfer.2012.06.052 doi: 10.1016/j.ijheatmasstransfer.2012.06.052
![]() |
[41] |
H. Zhou, P. Li, H. Jiang, H. Xue, B. Bo, Nonlocal dual-phase-lag thermoelastic dissipation of size-dependent micro/nano-ring resonators, Int. J. Mech. Sci., 219 (2022), 107080. https://doi.org/10.1016/j.ijmecsci.2022.107080 doi: 10.1016/j.ijmecsci.2022.107080
![]() |
[42] |
P. Zhang, T. He, A generalized thermoelastic problem with nonlocal effect and memory-dependent derivative when subjected to a moving heat source, Wave. Random. Complex., 30 (2020), 142–156. https://doi.org/10.1080/17455030.2018.1490043 doi: 10.1080/17455030.2018.1490043
![]() |
[43] |
P. Zhang, P. Schiavone, H. Qing, Local/nonlocal mixture integral models with bi-Helmholtz kernel for free vibration of Euler-Bernoulli beams under thermal effect, J. Sound. Vib., 525 (2022), 116798. https://doi.org/10.1016/j.jsv.2022.116798 doi: 10.1016/j.jsv.2022.116798
![]() |
[44] | N. Liu, G. Yang, B. Chen, Transverse vibration analysis of an axially moving beam with lumped mass, J. Vibroeng., 16 (2014), 3209–3217. |
[45] |
L. Q. Chen, Analysis and control of transverse vibrations of axially moving strings, Appl. Mech. Rev., 58 (2005), 91–116. https://doi.org/10.1115/1.1849169 doi: 10.1115/1.1849169
![]() |
[46] |
K. Rajabi, L. Li, S. Hosseini-Hashemi, A. Nezamabadi, Size-dependent nonlinear vibration analysis of Euler-Bernoulli nanobeams acted upon by moving loads with variable speeds, Mater. Res. Express, 5 (2018), 015058. https://doi.org/10.1088/2053-1591/aaa6e9 doi: 10.1088/2053-1591/aaa6e9
![]() |
[47] |
A. E. Abouelregal, H. E. Dargail, Memory and dynamic response of a thermoelastic functionally graded nanobeams due to a periodic heat flux, Mech. Based Des. Struct., 2021. https://doi.org/10.1080/15397734.2021.1890616 doi: 10.1080/15397734.2021.1890616
![]() |
[48] |
A. E. Abouelregal, M. Marin, The response of nanobeams with temperature-dependent properties using state-space method via modified couple stress theory, Symmetry, 12 (2020), 1276. https://doi.org/10.3390/sym12081276 doi: 10.3390/sym12081276
![]() |
[49] |
A. E. Abouelregal, H. Ersoy, Ö. Civalek, Solution of Moore–Gibson–Thompson equation of an unbounded medium with a cylindrical hole, Mathematics, 9 (2021), 1536. https://doi.org/10.3390/math9131536 doi: 10.3390/math9131536
![]() |
[50] |
M. Şimşek, Vibration analysis of a single-walled carbon nanotube under action of a moving harmonic load based on nonlocal elasticity theory, Physica. E., 43 (2010), 182–191. https://doi.org/10.1016/j.physe.2010.07.003 doi: 10.1016/j.physe.2010.07.003
![]() |
[51] |
S. K. Jena, S. Chakraverty, Free vibration analysis of Euler-Bernoulli nanobeam using differential transform method, Int. J. Comput. Mat. Sci., 07 (2018), 1850020. https://doi.org/10.1142/S2047684118500203 doi: 10.1142/S2047684118500203
![]() |
[52] |
P. Lu, P. Q. Zhang, H. P. Lee, C. M. Wang, J. N. Reddy, Nonlocal elastic plate theories. P. Roy. Soc. A-Math. Phys., 463 (2007), 3225–3240. https://doi.org/10.1098/rspa.2007.1903 doi: 10.1098/rspa.2007.1903
![]() |
[53] |
C. W. Lim, C. Li, J. L. Yu, Dynamic behaviour of axially moving nanobeams based on nonlocal elasticity approach, Acta Mech. Sinica, 26 (2010), 755–765. https://doi:10.1007/s10409-010-0374-z doi: 10.1007/s10409-010-0374-z
![]() |
[54] |
A. E. Abouelregal, H. Ahmad, S. -W. Yao, Functionally graded piezoelectric medium exposed to a movable heat flow based on a heat equation with a memory-dependent derivative, Materials, 13 (2020), 3953. https://doi:10.3390/ma13183953 doi: 10.3390/ma13183953
![]() |
[55] |
J. Wang, H. Shen, Nonlinear vibrations of axially moving simply supported viscoelastic nanobeams based on nonlocal strain gradient theory, J. Phys-Condens. Mat., 31 (2019), 485403. https://doi.org/10.1088/1361-648X/ab3bf7 doi: 10.1088/1361-648X/ab3bf7
![]() |
1. | Yifei Gui, Rujun Wu, Buckling analysis of embedded thermo-magneto-electro-elastic nano cylindrical shell subjected to axial load with nonlocal strain gradient theory, 2023, 128, 00936413, 104043, 10.1016/j.mechrescom.2023.104043 | |
2. | Sajid Ali, Muhammad A. Hawwa, Dynamic Characteristics of a Small-Size Beam Mounted on an Accelerating Structure, 2023, 14, 2072-666X, 780, 10.3390/mi14040780 | |
3. | Ahmed E. Abouelregal, S. S. Askar, Marin Marin, An Axially Compressed Moving Nanobeam Based on the Nonlocal Couple Stress Theory and the Thermoelastic DPL Model, 2023, 11, 2227-7390, 2155, 10.3390/math11092155 | |
4. | Mohammed Alkinidri, Rab Nawaz, Hani Alahmadi, Analytical and numerical investigation of beam-spring systems with varying stiffness: a comparison of consistent and lumped mass matrices considerations, 2024, 9, 2473-6988, 20887, 10.3934/math.20241016 | |
5. | Ahmed E. Abouelregal, Effect of non‐local modified couple stress theory on the responses of axially moving thermoelastic nano‐beams, 2024, 104, 0044-2267, 10.1002/zamm.202200233 |