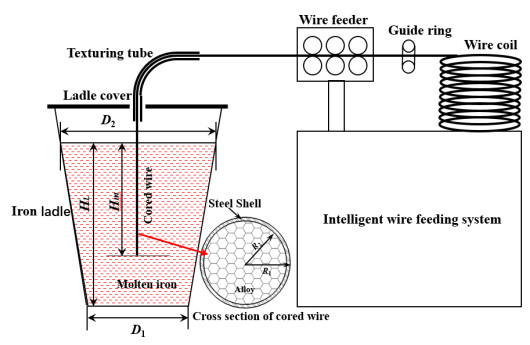
Many useful numerical algorithms of the numerical solution are proposed due to the increasing interest of the researchers in fractional calculus. A new discretization of the competition model for the real statistical data of banking finance for the years 2004–2014 is presented. We use a novel numerical method that is more reliable and accurate which is introduced recently for the solution of ordinary differential equations numerically. We apply this approach to solve our model for the case of Caputo derivative. We apply the Caputo derivative on the competition system and obtain its numerical results. For the numerical solution of the competition model, we use the Newton polynomial approach and present in detail a novel numerical procedure. We utilize the numerical procedure and present various numerical results in the form of graphics. A comparison of the present method versus the predictor corrector method is presented, which shows the same solution behavior to the Newton Polynomial approach. We also suggest that the real data versus model provide good fitting for both the data for the fractional-order parameter value ρ=0.7. Some more values of ρ are used to obtain graphical results. We also check the model in the stochastic version and show the model behaves well when fitting to the data.
Citation: Meihua Huang, Pongsakorn Sunthrayuth, Amjad Ali Pasha, Muhammad Altaf Khan. Numerical solution of stochastic and fractional competition model in Caputo derivative using Newton method[J]. AIMS Mathematics, 2022, 7(5): 8933-8952. doi: 10.3934/math.2022498
[1] | Yujia Chang, Yi Jiang, Rongliang Chen . A parallel domain decomposition algorithm for fluid-structure interaction simulations of the left ventricle with patient-specific shape. Electronic Research Archive, 2022, 30(9): 3377-3396. doi: 10.3934/era.2022172 |
[2] | Zhao Dong, Zhiyi Sai, Jinglin Zhang, Guangji Xu . Fatigue damage calculation of cold recycled asphalt pavement considering measured temperature field and traffic volume distribution. Electronic Research Archive, 2023, 31(7): 3722-3740. doi: 10.3934/era.2023189 |
[3] | Victor Ginting . An adjoint-based a posteriori analysis of numerical approximation of Richards equation. Electronic Research Archive, 2021, 29(5): 3405-3427. doi: 10.3934/era.2021045 |
[4] | Jiping Xing, Yunchi Wu, Di Huang, Xin Liu . Transfer learning for robust urban network-wide traffic volume estimation with uncertain detector deployment scheme. Electronic Research Archive, 2023, 31(1): 207-228. doi: 10.3934/era.2023011 |
[5] | Yao Yu, Guanyu Xue . A nonlinear correction finite volume scheme preserving maximum principle for diffusion equations with anisotropic and discontinuous coefficient. Electronic Research Archive, 2025, 33(3): 1589-1609. doi: 10.3934/era.2025075 |
[6] | Xiaojie Huang, Gaoke Liao . Identifying driving factors of urban digital financial network—based on machine learning methods. Electronic Research Archive, 2022, 30(12): 4716-4739. doi: 10.3934/era.2022239 |
[7] | E. A. Abdel-Rehim . The time evolution of the large exponential and power population growth and their relation to the discrete linear birth-death process. Electronic Research Archive, 2022, 30(7): 2487-2509. doi: 10.3934/era.2022127 |
[8] | Yun Ni, Jinqing Zhan, Min Liu . Topological design of continuum structures with global stress constraints considering self-weight loads. Electronic Research Archive, 2023, 31(8): 4708-4728. doi: 10.3934/era.2023241 |
[9] | Mingtao Cui, Min Pan, Jie Wang, Pengjie Li . A parameterized level set method for structural topology optimization based on reaction diffusion equation and fuzzy PID control algorithm. Electronic Research Archive, 2022, 30(7): 2568-2599. doi: 10.3934/era.2022132 |
[10] | Leilei Wei, Xiaojing Wei, Bo Tang . Numerical analysis of variable-order fractional KdV-Burgers-Kuramoto equation. Electronic Research Archive, 2022, 30(4): 1263-1281. doi: 10.3934/era.2022066 |
Many useful numerical algorithms of the numerical solution are proposed due to the increasing interest of the researchers in fractional calculus. A new discretization of the competition model for the real statistical data of banking finance for the years 2004–2014 is presented. We use a novel numerical method that is more reliable and accurate which is introduced recently for the solution of ordinary differential equations numerically. We apply this approach to solve our model for the case of Caputo derivative. We apply the Caputo derivative on the competition system and obtain its numerical results. For the numerical solution of the competition model, we use the Newton polynomial approach and present in detail a novel numerical procedure. We utilize the numerical procedure and present various numerical results in the form of graphics. A comparison of the present method versus the predictor corrector method is presented, which shows the same solution behavior to the Newton Polynomial approach. We also suggest that the real data versus model provide good fitting for both the data for the fractional-order parameter value ρ=0.7. Some more values of ρ are used to obtain graphical results. We also check the model in the stochastic version and show the model behaves well when fitting to the data.
In recent years, the rapid development of numerical simulation technology provides great convenience for solving complex problems in engineering [1,2]. Finite volume method (FVM) is an advanced high-precision simulation method developed based on finite element and finite difference methods [3,4,5], which combines the idea of finite element piecewise approximation and finite difference method. It is suitable for any type of element grid, and convenient to simulate the fluid motion with complex boundary shape [6,7]. By splitting and solving control equation, the heat and mass transfer processes of complex systems can be scientifically characterized. Therefore, the finite volume method is widely used in engineering field as an advanced numerical simulation method [8,9,10].
Cored wire feeding spheroidizing treatment of molten iron is a complex physical metallurgical process, which is characterized by continuous feeding cored wire into molten iron to a certain depth, so that the spheroidizing elements react with high temperature molten iron to realize spheroidization and modification. The advantages of this method are energy saving, environmental protection and low cost, which meet the development needs of modern industry. Therefore, in recent years, cored wire feeding spheroidization technology of molten iron has attracted much attention of cast iron metallurgists [11], and the application is increasing day by day, which shows the potential to replace the traditional flushing method. However, there are still some imperfections in the production practice. The absorption rate of magnesium is low, only 30–40%. The content of slag is large, and the mechanical properties of the material such as elongation and tensile strength are low. The uppermost problem is that the uniformity of chemical composition and microstructure are not ideal, and the impact absorbing energy at low temperature is significantly lower than that using of flushing method. To a certain extent, it limits the application in high-performance castings such as high-speed railway, wind power and nuclear power castings. There are reasons mainly related to the insufficient understanding of the dynamic heat transfer rule in the process of spheroidizing, so it is impossible to establish the internal relations among the temperature of molten iron, melt explosion depth and feeding speed of different structures cored wires. At the same time, due to the high temperature and opacity of molten iron, it is difficult to track and observe the change of variables. As a result, the selection of actual parameters is mainly based on trial and error, it is difficult to achieve effective control of the feeding spheroidization process in molten iron. Although in the past few years, some researchers have conducted theoretical studies on cored wire feeding process of molten steel by using numerical simulation technology, established relevant theoretical models, and explored the heat transfer characteristics between cored wire and molten steel. It lays a good foundation for optimizing cored wire feeding spheroidization process, provides theoretical support for controlling the heat transfer process between molten steel and molten slag [12,13,14]. However, because molten iron with high carbon liquid, the process of treatment has less slag, and the physical properties and temperature of treatment in molten iron are quite different from that of molten steel, applying the theoretical model of molten steel directly to the spheroidizing treatment process of molten iron will inevitably produce large errors. At the same time, due to the calculation and derivation process are complex, it is difficult to obtain ideal parameters control of spheroidizing process. G. W. Chang applied ANSYS software to simulate the heat transfer process, calculated the melting time of steel strip in molten iron [15]. However, the theoretical research on the model establishment and parameter optimization of feeding spheroidization in molten iron are still rare, and the systematic and in-depth study on the heat transfer behavior in molten iron have important theoretical significance and application value.
In this paper, taking single core and shell core structured cored wires as research objects, a three-dimensional dynamic model of cored wire feeding spheroidization is established based on FVM. By comparing the temperature field in molten iron of two different structured cored wires, the dynamic heat transfer behavior between molten iron and cored wire is explored. We also research the melt explosion characteristics of the top end of cored wire. Meanwhile, the correlations among the feeding speed, melt explosion depth and temperature of molten iron are revealed. In addition, the influence of magnesium absorption rate with different structured cored wires is further studied, it provides a theoretical basis for the optimization of parameters and intelligent control of cored wire feeding spheroidization in molten iron.
In order to comprehensively understand the physical process of melt explosion in molten iron, and realize the visualization control of cored wire feeding process, a three-dimensional heat transfer model is established.
The feeding spheroidization treatment system of molten iron is composed of iron ladle, intelligent wire feeder and cored wire, as shown in Figure 1. In the iron ladle, the dashed line is molten iron, in which the height is HL = 1000 mm, the diameters of the lower and upper ends are D1 = 500 mm, D2 = 700 mm, respectively. In addition, the mass of molten iron is 1.2 t. Driven by the wire feeder, cored wire enters the center of iron ladle vertically at a constant speed, and conduct unsteady heat transfer with molten iron in initial stage. When the cored wire reaches a certain depth of Hm, the heat transfer tends to be stable and then enters steady state. At this moment, the temperature of the top end of cored wire has reached explosion point, which means that the feeding speed is equal to the melting loss speed of cored wire, and the melt explosion depth tends to remain constant. The theoretical calculation area is shown in the dashed line area in Figure 1. In the figure, the cored wire of shell core structure is divided into two layers, the inner layer is alloy material, and the outer layer is sheet steel, with the outer diameter of cored wire is 2R1 = 13 mm, the inner diameter is 2R2 = 12.2 mm respectively, and the thickness of sheet steel is 0.4 mm. For the cored wire of single core structure, only the inner magnesium core, its diameter is 13 mm.
The inserted velocity v0 keep constant in the process of cored wire feeding spheroidization, and the energy equation can be expressed in cylindrical coordinate system [16]:
∂T∂t=α(1r∂∂r(r∂T∂r)+1r2∂∂θ(∂T∂θ)+∂∂z(∂T∂z))−v0∂T∂z | (1) |
In the formula, T is temperature, α is thermal diffusion coefficient, as α = λ/λρCpρCp, λ is heat conductivity, ρ is density, Cp is isobaric heat capacity, and r is radius of cored wire. The temperature field function of cylindrical coordinate system is T (r, θ, z; t). As cored wire and molten iron are both have axisymmetric structure, so the angle parameter θ has no function, and then simplification yields:
∂T∂t=α(1r∂∂r(r∂T∂r)+∂∂z(∂T∂z))−v0∂T∂z | (2) |
where, the temperature field function can be expressed as T (r, z; t).
To avoid being divided by dimensionless (when r is close to 0), both sides of equation are multiplied by r, thus can obtain:
r∂T∂t=α[∂∂r(r∂T∂r)+∂∂z(r∂T∂z)]−v0r∂T∂z | (3) |
The vector form can be expressed as:
r∂T∂t=α[∇⋅(r∇T)]−∇⋅(0,rv0T) | (4) |
A. Initial conditions
In the process of numerical calculation, the cored wire feeding speed v0 select as 20, 25, 30 and 35 m/min, set the temperature of molten iron T to 1440, 1460, 1480 and 1500 ℃, respectively. Meanwhile, the initial temperature of cored wire is set to 26 ℃. To make the calculation easy, it is assumed that the composition of molten iron is constant, and the physical parameters of molten iron and cored wire are isotropic. Ignoring the influence of stirring of molten iron and its influence on cored wire. Neglecting the convective heat transfer between iron ladle and molten iron. At the same time, the core material of cored wire is dense and uniform, there is no empty line and broken line. Ignore the radiation heat transfer between iron surface and air.
B. Boundary conditions
The boundary conditions corresponding to the different structured cored wires are described as follows:
(a) Single core structure
For single core magnesium wire, Boundary A1 is defined as symmetry axes of cored wire. Heat transfer surface Boundaries A2 and A3 are shown in Figure 2(a). Boundary A4 is contact surface between air and iron ladle. And the corresponding boundary conditions are:
① Axisymmetric boundary condition: (Boundary A1)
∂T∂n|Γ1=0 | (5) |
② Mg-core wire contact with molten iron: (Boundary A2)
−λ∂T∂n|Γ2=h1(T(Γ2;t)−TL) | (6) |
③ Mg-core wire contact with air and transfer heat by radiating outwards: (Boundary A3)
−λ∂T∂n|Γ3=εσ(T4(Γ3;t)−T4g) | (7) |
In which, TL is the temperature of molten iron, Tg is ambient temperature, σ is Stefan-Boltzmann constant, ε is radiation coefficient and n is the outward normal vector to the boundary Γi(i = 1, 2, 3). Meanwhile, h1 is the heat exchange coefficient between molten iron and cored wire.
(b) Shell core structure
For shell core structured cored wire, Boundary B1 is still the axisymmetric interface, and the heat transfer surfaces are Boundaries B2–B5, as shown in Figure 2(b). Boundary B6 is the molten iron/air interface, and Boundary B7 is the air/iron ladle interface. The corresponding boundary conditions are:
① Axisymmetric boundary condition: (Boundary B1)
∂T∂n|Γ1=0 | (8) |
② Mg-core contacts with sheet steel: (Boundary B2)
−λ∂T∂n|Γ′2=h2(T(Γ′2;t)−Ts) | (9) |
③ Sheet steel contacts with molten iron: (Boundary B3)
−λ∂T∂n|Γ′3=h3(T(Γ′3;t)−TL) | (10) |
④ Mg-core contacts with molten iron: (Boundary B4)
−λ∂T∂n|Γ4=h4(T(Γ4;t)−TL) | (11) |
⑤ Cored wire contacts with air and transfers heat by radiating outwards: (Boundary B5)
−λ∂T∂n|Γ5=εσ(T4(Γ5;t)−T4g) | (12) |
where, h2, h3, h4 are the heat exchange coefficient, Ts is the temperature of sheet steel.
In view of the irregular computational region and complex boundary conditions in our model, FVM is applied to solve the heat transfer problem numerically, the specific process is shown as follow [17]:
First, determine the position of the node in each subdomain and the control volume represented by the node, make sure that there is no repeat control volume around each grid point [18,19]. After obtaining control volumes covering the entire computational region, it is convenient to get the integral form of the control equation with each control volume, and then obtain a set of discrete equations. In order to ensure the stability of the calculation, implicit time integration is used and the calculation area is discretized. Figure 3(a) is grid division of the computational region mainly using quadrilateral and triangular grids. Figure 3(b) is the partial enlarged view of grid division. Dual subdivision is used to define the control units of triangular elements and the approximate points of grid nodes. As shown in Figure 4(a), (b), where Li is grid nodes, Mi is all the midpoints of the edges incident to vertex L0, Ni is the gravity centers of triangular units with vertex L0, and K∗L0 is control unit of node L0. Setting domain conditions, dynamic mesh, boundary conditions, etc., and considering appropriate initial load step length and total load steps for calculation.
In the framework of FVM, a critical step is to integrate the master equation on control volume, so as to generate discrete equations on the control volume nodes. The integration of Eq (4) can display as:
∫K∗L0r∂T∂tdV=α∫K∗L0(∇⋅(r∇T))dV−v0∫K∗L0∇⋅(0,rT)dV | (13) |
Apply Gauss's divergence theorem, the integral transformation form of heat transfer control equation is:
∫K∗L0r∂T∂tdV=α∫∂K∗L0n⋅(r∇T)ds−v0∫∂K∗L0n⋅(0,rT)ds | (14) |
A. Discretizing of transient term
Forward difference scheme is applied for discretizing transient term on the left of Eq (14):
∫K∗L0r∂T∂tdV = rL0Tn+1L0−TnL0τ⋅SK∗L0 | (15) |
where SK∗L0 is the area of control volume K∗L0, τ is the discrete time step, rL0 is the coordinate component along the raxis, Tn+1L0, TnL0 is the temperature of computational point L0 at n + 1, and n time layers, respectively.
B. Discretization of diffusion term
In this part, the discretization of diffusion term concluded area-weighted interpolation of temperature, discretization of gradient operator, integral of line unit and dual unit. To get more accurate valuation, the temperature T(r, z) at each node L(r, z) inside triangular element is evaluated by interpolating nodal temperatures Ti, Tj, Tk at the mesh nodes Li, Lj, Lk, and area-weighted values wi = Si/S, wj = Sj/S and wk = Sk/S.
T(r,z)=wiTi+wjTj+wkTk | (16) |
where, get the triangle areas S, Si, Sj and Sk through the determinant of the vertex coordinates:
{S=12|1rizi1rjzj1rkzk|,Si=12|1rz1rjzj1rkzk|Sj=12|1rizi1rz1rkzk|,Sk=12|1rizi1rjzj1rz| | (17) |
According to the interpolated temperature approximation in Eq (16) and area-weighted values wi, wj, and wk, the spatial derivative terms ∇T = (∂T∂r,∂T∂z) can be discretized as:
∂T∂r = 12S(zj−zk,zk−zi,zi−zj)(TiTjTk) | (18) |
∂T∂z = 12S(rk−rj, ri−rk, rj−ri) (TiTjTk) | (19) |
(a) For line unit integral
As shown in Figure 4(a), (b), for diffusion term integration on the boundary of control unit K∗L0, which is carried out over line elements, should be divided into boundary line unit lying on the region boundary and internal line unit inside the computational area. For internal line unit, taking M1N1M2 in Figure 4(a) as an example, it can get that
∫¯M1N1M2n⋅(r∇T) ds = ∫¯M1N1M2[r∂T∂rdz−r∂T∂zdr]=rL0+rL1+rL212S1[(zL2−zL1)(zL1−zL2,zL2−zL0,zL0−zL1)−(rL2−rL1)(rL2−rL1,rL0−rL2,rL1−rL0)](TL0TL1TL2) | (20) |
For boundary line unit, take L0M1 in Figure 4(b) as an example:
∫¯L0M1n⋅(r∇T) ds = ∫¯L0M1r(−hλ(Tl−TL))ds = 3rL0+rL14⋅[−hλ(3TL0+TL14−TL)]√(rL1−rL0)2+(zL1−zL0)22 | (21) |
∫¯L0M1n⋅(r∇T) ds = ∫¯L0M1r(−1kεσ(T4l−T4g))ds = 3rL0+rL14⋅[−1kεσ((3TL0+TL14)4−T4e)]√(rL1−rL0)2+(zL1−zL0)22 | (22) |
∫¯L0M1n⋅(r∇T) ds = ∫¯L0M1r∂T∂nds | (23) |
(b) For dual unit integral
For discretization of diffusion term, it should be considered at internal nodes and boundary nodes separately. At interior points, all boundary edges of control volume lie in the computational area as shown in Figure 4(a), so the right hand of Eq (14) can be expressed as an integral sum over all boundary edges of control volume.
∫∂K∗L0n⋅(r∇T) ds = m∑i=1∫¯MiNiMi+1[r∂T∂rdz−r∂T∂zdr] = m∑i=0ciTLi | (24) |
The node coefficient ci expressed:
c0=m∑i=1[rL0+rLi+rLi+1314Si{(zLi + 1−zLi)(zLi−zLi+1)+(rLi + 1−rLi)(rLi−rLi+1)}] | (25) |
ci=rL0+rLi+rLi+1314Si{(zLi + 1−zLi)(zLi + 1−zL0)+(rLi + 1−rLi)(rLi+1−rL0)}+ rL0+rLi−1+rLi314Si−1{(zLi−zLi−1)(zL0−zLi−1)+(rLi−rLi−1)(rL0−rLi−1)} (i=1,⋅⋅⋅, m) | (26) |
For boundary points in Figure 4(b), the dual unit boundary consists of both the boundary and internal line units. So the discretization of diffusion term at boundary point obtained according to Eqs (21)–(24) as below:
∫∂K∗L0n⋅(r∇T) ds = m−1∑i=1∫¯MiNiMi+1[r∂T∂rdz−r∂T∂zdr] + ∫¯L0M1r∂T∂nds+∫¯MmL0r∂T∂nds=m∑i=0ciTLi+fL0 | (27) |
where,
c0=m−1∑i=1[rL0+rLi+rLi+1314Si{(zLi + 1−zLi)(zLi−zLi+1)+(rLi + 1−rLi)(rLi−rLi+1)}] | (28) |
c1=rL0+rL1+rL2314S1{(zL2−zL1)(zL2−zL0)+(rL2−rL1)(rL2−rL0)} | (29) |
ci=rL0+rLi+rLi+1314Si{(zLi + 1−zLi)(zLi + 1−zL0)+(rLi + 1−rLi)(rLi+1−rL0)}+ rL0+rLi−1+rLi314Si−1{(zLi−zLi−1)(zL0−zLi−1)+(rLi−rLi−1)(rL0−rLi−1)} (i=2,⋅⋅⋅, m−1) | (30) |
cm=rL0+rLm−1+rLm314Sm−1{(zLm−zLm−1)(zL0−zLm−1)+(rLm−rLm−1)(rL0−rLm−1)} | (31) |
The form of boundary related coefficient fL0 is reference to the types of boundary conditions.
C. Discretization of convection term
Likewise, the discretization of convection term on the right end of integral Eq (14) should contain interior points and boundary points, which is similar to the discretization of diffusion term. It can be expressed as:
∫∂K∗L0n⋅(0,rT) ds = −m∑i=1∫¯MiNiMi+1rTdr = m∑i=0biTLi | (32) |
where, bi is the coefficient of node temperature TLi.
After obtaining the discretization forms of transient term, convection term and diffusion term, the discretized form of heat transfer Eq (14) deducing naturally. Here, the stable implicit scheme is applied for iteration. For internal node, the discrete equation as:
rL0Tn+1L0−TnL0τ⋅SK∗L0 = αm∑i=0ciTn + 1Li−v0m∑i=0biTn + 1Li | (33) |
rL0Tn+1L0−gL0m∑i=0ciTn + 1Li+hL0m∑i=0biTn + 1Li=rL0TnL0 | (34) |
rL0Tn+1L0+m∑i=0(hL0bi−gL0ci)Tn + 1Li=rL0TnL0 | (35) |
where, gL0=ατ/ατSK∗L0SK∗L0, hL0=v0τ/v0τSK∗L0SK∗L0.
Similarly, for boundary node, it follows:
rL0Tn+1L0−TnL0τ⋅SK∗L0 = α(m∑i=0ciTn + 1Li + fnL0)−v0m∑i=0biTn + 1Li | (36) |
rL0Tn+1L0−gL0m∑i=0ciTn + 1Li + hL0m∑i=0biTn + 1Li = rL0TnL0+gL0fnL0 | (37) |
rL0Tn+1L0+m∑i=0(hL0bi−gL0ci)Tn + 1Li=rL0TnL0+gL0fnL0 | (38) |
According to the discretization forms of governing equation, obtain the matrix system of equations:
ATn+1=Bn | (39) |
where, A is coefficient matrix satisfy the following rules: for each node L0 and its proximal point L1, L2, …, Lm, which are numbered as i0, i1, i2, … im, the elements on line i0 of matrix A can be obtained. Tn+1 is vector that involves the temperatures of all grid nodes at the n + 1 time layer.
A(i0,i0)=rL0+hL0b0−gL0c0, A(i0,i1) = hL0b1−gL0c1, | (40) |
A(i0,i2) = hL0b2−gL0c2,⋅⋅⋅, A(i0,im) = hL0bm−gL0cm. | (41) |
Moreover, the other elements of the i0-th row are zero. Therefore, the iterative matrix constituted by np nodes is Anp×np. The unknown term on the right end of (Bn)np×1 will be updated by every step. At last, the temperature field of the n + 1th time can be got according to temperature field in cored wire at the nth time. And the linear system of equation ATn+1=Bn can be solved through Gauss-Seidel iterative method or Gaussian elimination method directly.
The shell core spheroidized cored wire is made of 08AL low carbon steel, and its corresponding physical parameters are listed in Table 1. The chemical composition of the core material is listed in Table 2. The liquidus temperature of alloy core material is 1100 ℃, and the solidus temperature is 1070 ℃. The physical properties of core materials at different temperatures are listed in Table 3.
Temperature, T/℃ | 20 | 200 | 400 | 600 | 800 | 1450 |
Specific heat capacity, C/J·kg-1·K-1 | 481 | 544 | 595 | 960 | 970 | |
Thermal conductivity, λ/W·m-1·K-1 | 60.3 | 54.9 | 45.2 | 36.4 | 28.5 | 27.6 |
Density, ρ/g·cm-3 | 7.85 | |||||
Liquidus temperature, TL/℃ | 1420 | |||||
Solidus temperature, Ts/℃ | 1400 | |||||
Melting latent heat, L/kJ·kg-1 | 270 (1400℃) |
Si | Ca | Mg | Ba | La | Ce | Al |
43.5 | 2.92 | 30.14 | - | 1.14 | 2.05 | 0.7 |
T/℃ | 25 | 200 | 500 | 800 | 1100 | ρ | L | |||||
Mg/% | λc | Cc | λc | Cc | λc | Cc | λc | Cc | λc | Cc | ||
30 | 111 | 807.9 | 109 | 917.6 | 107.1 | 1044.6 | 106 | 1078.7 | 106 | 1137.7 | 2.63 | 1066 |
100 | 149 | 1030 | 146 | 1100 | - | 1260 | 145 | 1400 | - | - | 1.65 | 377 |
Figure 5(a) displays the temperature nephogram of unsteady heat transfer of cored wire with shell core structure when immersed in molten iron. In the figure, the cored wire moves at a constant speed v0 vertically downward from the center of the liquid pool. During the movement, there exist a strong heat exchange between cored wire and molten iron, which resulting in a large temperature gradient in the axial and radial directions of cored wire and along the axial direction is particularly significant. The reason is that as the top end of cored wire enter into molten iron first, the heat transfer lasts longer than other locations, so the heating speed is the fastest, and the temperature is the highest. Therefore, a large temperature gradient shaping in the vertical direction. It can be clearly seen from the nephogram that the temperature of the longitudinal section gradually transits from the bottom to the top and from the edge to the center of the cored wire, thus forming an upward-opening "U" type temperature field with axis symmetry.
In the temperature field, the "U" type isotherms is clearly visible due to the combined heat transfer of axial and radial. It presents a narrow and slender wedged geometric feature at the bottom, which runs through the whole longitudinal section of the cored wire. Its shape is particularly obvious at the top end of cored wire, as shown in the tip amplification diagram of temperature nephogram at different times in Figure 5(a). The "U" type isotherm visually display the unsteady dynamic heat transfer characteristics between molten iron and cored wire. As the distance increasing, the opening of "U" shaped line gradually increases and the isotherm becomes denser, which indicates that the heat transfer of radial dominates the process mainly. When the top end of cored wire reaches melting temperature of sheet steel (corresponding to the time of 1.68 s in nephogram), formed a small range of temperature about 5–10 cm, where most of the core materials are in melting or semi-melting state. At this moment, the top end of cored wire has the highest temperature and in the molten explosion state, accompanied by gasification, diffusion and metallurgical reactions of magnesium atoms. It marks the beginning of spheroidization reaction. When the melting loss speed is equal to wire feeding speed, the heat transfer entering steady state and the reaction continues until the spheroidization treatment is completed.
Without the protection of sheet steel, the thermal resistance at the interface between the single core structured cored wire and the molten iron is relatively small. Moreover, as the thermal conductivity of magnesium is relatively large, so the heat transfer between single core structured magnesium core and molten iron is faster, and it can reach the steady heat transfer stage in a short time about t = 1.0 s. It can be clearly seen in Figure 5(b), due to the rapidly heat transfer in the axial and radial directions, the isotherm at the bottom of the cored wire presents a typical "U" shaped distribution characteristic. This shows that the heat transfer law of single core structured cored wire is basically the same as those of the shell core structured cored wire.
The spheroidizing reaction of molten iron starts at the top end of cored wire, and the heating rate restricts the melt explosion process directly. Figure 6 shows the temperature curves of top end of two different structured cored wires varying with time in melt explosion zone, when the temperature of molten iron T = 1460 ℃ and the wire feeding speed v0 = 25 m/min. It can be seen that the heating rate of single core magnesium wire can reach 3.12 × 103 K/s due to its high thermal conductivity. When the temperature rises to about 650 ℃, the top end of magnesium core tend to melt, and represent an obvious inflection point. The appearance of inflection point is obviously the temperature arrest generated by the absorption of latent heat of fusion when magnesium melts, which indicates the beginning of melting.
As the temperature continuous rises, it enters the state of melt explosion reaction and gasification of liquid magnesium. For the shell core structured cored wire, since the melting point of sheet steel is higher and the thermal conductivity is lower than that of magnesium metal, the heating rate of core material is relatively slow, about 1.75 × 103 K/s. When the temperature rises to about 1108 ℃, the alloy core material tends to melt, a temperature platform on the heating curve presents due to the absorption of latent heat by the alloy, it followed by a rapid temperature rise in the liquid state, then entering into melt explosion reaction and gasification state of magnesium. It can be seen that the magnesium wire of single core structure has lower melting point, higher thermal conductivity, and faster heating rate, and it is difficult to reach a deeper melt explosion depth. While the shell core structured cored wire has a relatively slower heat transfer rate due to the protective effect of sheet steel, which lead a deeper melting depth. Therefore, the heat transfer capacity of cored wire is an important parameter that restricts the melt explosion depth of cored wire. Since the heat transfer capacity of cored wire with shell core structure is relatively weak, it has general adaptability to the molten iron.
During the spheroidizing process of molten iron, the ideal melt explosion depth should be located in the center of the pool about 10 cm away from the bottom of the ladle. The primary factors affecting the melt explosion depth are: temperature of molten iron, structure of cored wire, wire feeding speed, type and chemical composition of core material. Figure 7 shows the curves of melt explosion depth varying with the temperature of molten iron and cored wire feeding speed. It can be seen from the diagram that with the different structure of single core and shell core that the melt explosion depth is different too. Under the condition of a certain temperature of molten iron, with the increasing feeding speed, the melt explosion depth of the two structured cored wire increasing nonlinearly. Accordingly, when the feeding speed of cored wire is constant, the melt explosion depth of cored wire decreasing as the temperature of molten iron increasing. And the melt explosion depth of single core magnesium wire is much lower than that of shell core structure. The main reason is that the melting point of magnesium is lower, with the heat transfer speed is faster, it is difficult to enter a deeper depth, so the melt explosion depth is shallow. Owing to the protective effect of sheet steel, the heat transfer rate of cored wire with shell core structure is relatively slow, so it can reach a deeper melt explosion depth at the same wire feeding speed, which is very suitable for the spheroidization of large volume molten iron. There is no doubt, as the melt explosion depth is deeper, the diffusion path of free magnesium atoms overflow to the liquid surface will prolonged, which is conducive to improving the absorption rate of magnesium in molten iron. Since the single core structured magnesium wire cannot reach a deeper melt explosion depth even at a higher feeding speed, it is difficult to adapt the spheroidization treatment of molten iron with a capacity of more than 100 kg, and cannot meet the production requirements of modern ductile iron castings. It only can be used for the spheroidization treatment of molten iron with small volume, alloy preparation and new product development of ductile iron castings under laboratory conditions. In the actual production, melt explosion depth can effectively controlled by changing wire feeding speed and spheroidizing temperature, so that make the explosion point at a desired depth.
After spheroidization, carbon atoms in molten iron exist as spherical graphite, which can greatly improve the tensile strength, elongation and impact toughness of the alloy. The prerequisite for obtaining ideal ductile iron materials is that after spheroidization reaction, the molten iron still contains about 0.03–0.05% residual magnesium. Obviously, the residual magnesium increases with the amount of total magnesium added to the molten iron. However, since the solubility of magnesium in molten iron is very limited, increasing the total amount of magnesium will inevitably increase the burning loss of magnesium. In order to reduce the burning loss and energy consumption, improve the absorption rate of magnesium and obtain good spheroidization effect, the melt explosion depths of two different structured cored wires are calculated theoretically in this work. Meanwhile, the melt explosion depth and the absorption rate of magnesium of industrial ductile iron are tested. Using manual insertion method in the experiment to test the melt explosion depth of cored wire, and the chemical composition of molten iron is tested by directly reading spectrometer (wt%): 3.85%C, 1.25%Si, 0.028%P, 0.02%S, 0.18%Mn. The calculation formula of magnesium absorption rate can be expressed as:
εMg = ωMgR⋅WLWMg×100% | (42) |
In the formula, εMg is absorption rate of magnesium, %. ωMgR is residual magnesium content in molten iron after spheroidization, %. WMg is the amount of magnesium added to molten iron, kg. And WL is the mass of molten iron, kg.
Figure 8 shows the relationship among the absorption rate of magnesium, the melt explosion depth and the wire feeding speed when the temperature of molten iron is 1460 ℃. It revealed in the figure that the melt explosion depth obtained by theoretical calculation basically consistent with the date measured by experiment, which indicated that the developed mathematical model can be used to theoretically predict the spheroidization process and the melt explosion depth of molten iron. With the cored wire feeding speed increasing, the melt explosion depth of the two structured cored wires increasing rapidly at first and then tends to be gentle, which showing a monotonically increasing trend, but there is a peak. While the absorption rate of magnesium shows a trend of increasing rapidly first and then tended to be gentle. The reason is that the increasing depth of melt explosion lengthens the distance for the diffusion and overflow of magnesium vapor from the molten iron, which resulting in decreasing in the loss of magnesium. When the wire feeding speed is high, there is a limited space for the depth of melt explosion. As the melting loss speed becomes faster, intensifies the melt explosion reaction and the concentration of magnesium vapor increases sharply, which results in poor stability of molten iron and increased loss of magnesium. This leads to a decrease in the absorption rate of magnesium. It can also be seen from the figure that when using single core magnesium wire for spheroidization, the absorption rate of magnesium is only 10–20%, which is mainly due to the shallow explosion depth resulting from the fast heat transfer rate and the low melting point of pure magnesium. It follows that the passivated magnesium wire is not suitable for spheroidizing treatment of cored wire feeding in molten iron for industrial ductile iron.
In this paper, the mathematical model of cored wire feeding spheroidization in molten iron has established based on FVM. Comparative analysis are performed of the dynamic heat transfer characteristics of single core structure and shell core structure cored wire respectively. By using computer simulation, we studied the influence of feeding speed, cored wire structure and molten iron temperature on melt explosion depth of cored wire and absorption rate of magnesium. The main results are as follows:
1) When cored wire is inserted into molten iron at a constant speed, there is a fierce unsteady heat transfer between cored wire and molten iron, and a large temperature gradient is formed along the axial and radial directions of cored wire. Thus, a "U" shaped isotherm characterized by narrow, slender, wedge-shaped bottom, and running through the entire longitudinal section of the cored wire is formed.
2) When the temperature of molten iron and feeding speed are fixed, the heating rate of top end of single core magnesium wire is faster than that of cored wire with shell core structure, and the heating rates are 3.12 × 103 and 1.75 × 103 K/s respectively. Obviously, the shell core structure cored wire is easier to reach a deeper melt explosion depth.
3) Under the condition of a certain temperature of molten iron, the melt explosion depth of two kinds of cored wires increases with the increasing feeding speed, while the absorption rate of magnesium increases first and then tends to be gentle. Under the same conditions, the melt explosion depth and magnesium absorption rate of cored wire with shell core structure are always higher than that of single core magnesium wire.
4) The proposed theoretical model can predict the melt explosion depth and spheroidizing process of molten iron. Under the condition that the structure of core wire is determined, the top end of cored wire can reach an ideal melt explosion depth by adjusting the temperature of molten iron and feeding speed of cored wire, in order to obtain ideal spheroidization effect and realize the effective control of spheroidization process of molten iron.
This work was supported by the National Natural Science Foundation of China (Project Nos. 71571144 and 71401134), and the Natural Science Basic Research Program of Shaanxi (Project No. 2022JM-024).
The authors declare that they have no known competing financial interests or personal relationships that could have appeared to influence the work reported in this paper.
[1] |
X. P. Li, Y. Wang, M. A. Khan, M. Y. Alshahrani, T. Muhammad, A dynamical study of SARS-COV-2: A study of third wave, Res. Phys., 29 (2021), 1–6. https://doi.org/10.1016/j.rinp.2021.104705 doi: 10.1016/j.rinp.2021.104705
![]() |
[2] |
Z. H. Shen, Y. M. Chu, M. A. Khan, S. Muhammad, O. A. AlHartomy, M. Higazy, Mathematical modeling and optimal control of the COVID-19 dynamics, Res. Phy., 31 (2021), 1–9. https://doi.org/10.1016/j.rinp.2021.105028 doi: 10.1016/j.rinp.2021.105028
![]() |
[3] |
X. P. Li, N. Gul, M. A. Khan, R. Bilal, A. Ali, M. Y. Alshahrani, et al., A new Hepatitis B model in light of asymptomatic carriers and vaccination study through Atangana-Baleanu derivative, Res. Phys., 29 (2021), 104603. https://doi.org/10.1016/j.rinp.2021.104603 doi: 10.1016/j.rinp.2021.104603
![]() |
[4] | P. Y. Xiong, M. I. Khan, R. J. P. Gowda, R. N. Kumar, B. C. Prasannakumara, Y. M. Chu, Comparative analysis of (Zinc ferrite, Nickel Zinc ferrite) hybrid nanofluids slip flow with entropy generation, Mod. Phys. Lett. B, 35 (2021), 1–22. |
[5] |
P. Y. Xiong, A. Hamid, Y. M. Chu, M. I. Khan, R. J. P. Gowda, R. N. Kumar, et al., Dynamics of multiple solutions of Darcy-Forchheimer saturated flow of Cross nanofluid by a vertical thin needle point, Eur. Phys. J. Plus, 136 (2021), 1–22. https://doi.org/10.1140/epjp/s13360-021-01294-2 doi: 10.1140/epjp/s13360-021-01294-2
![]() |
[6] | Laws of the republic indonesia number 10 year 1998 about amendment to law number 7 of 1992 concerning banking. Available from: https://www.global-regulation.com/translation/indonesia/7224941/act-no.-10-of-1998.html. |
[7] | S. Arbi, Lembaga perbankan keuangan dan pembiayaan, Yogyakarta: BPFE, 2013. |
[8] | S. Iskandar, Bank dan lembaga keuangan lainnya, Jakarta: Penerbit, 2013. |
[9] | OJK, Statistik Perbankan Indonesia, 2004–2014. Available from: http://www.ojk.go.id/datastatistikperbankan-indonesia. |
[10] | A. Hastings, Population biology: Concepts and models, Springer Science & Business Media, 2013. |
[11] |
J. Kim, D. J. Lee, J. Ahn, A dynamic competition analysis on the korean mobile phone market using competitive diffusion model, Comput. Ind. Eng., 51 (2006), 174–182. https://doi.org/10.1016/j.cie.2006.07.009 doi: 10.1016/j.cie.2006.07.009
![]() |
[12] |
S. A. Morris, D. Pratt, Analysis of the lotka-volterra competition equations as a technological substitution model, Technol. Forecast. Soc., 70 (2003), 103–133. https://doi.org/10.1016/S0040-1625(01)00185-8 doi: 10.1016/S0040-1625(01)00185-8
![]() |
[13] |
S. J. Lee, D. J. Lee, H. S. Oh, Technological forecasting at the korean stock market: A dynamic competition analysis using lotka-volterra model, Technol. Forecast. Soc., 72 (2005), 1044–1057. https://doi.org/10.1016/j.techfore.2002.11.001 doi: 10.1016/j.techfore.2002.11.001
![]() |
[14] |
C. Michalakelis, C. Christodoulos, D. Varoutas, T. Sphicopoulos, Dynamic estimation of markets exhibiting a prey-predator behavior, Expert Syst. Appl., 39 (2012), 7690–7700. https://doi.org/10.1016/j.eswa.2012.01.049 doi: 10.1016/j.eswa.2012.01.049
![]() |
[15] |
S. Lakka, C. Michalakelis, D. Varoutas, D. Martakos, Competitive dynamics in the operating systems market: Modeling and policy implications, Technol. Forecast. Soc., 80 (2013), 88–105. https://doi.org/10.1016/j.techfore.2012.06.011 doi: 10.1016/j.techfore.2012.06.011
![]() |
[16] |
C. A. Comes, Banking system: Three level lotka-volterra model, Proc. Econ. Financ., 3 (2012), 251–255. https://doi.org/10.1016/S2212-5671(12)00148-7 doi: 10.1016/S2212-5671(12)00148-7
![]() |
[17] |
Fatmawati, M. A. Khan, M. Azizah, Windarto, S. Ullah, A fractional model for the dynamics of competition between commercial and rural banks in Indonesia, Chaos Soliton. Fract., 122 (2019), 32–46. https://doi.org/10.1016/j.chaos.2019.02.009 doi: 10.1016/j.chaos.2019.02.009
![]() |
[18] |
W. Wang, M. A. Khan, Fatmawati, P. Kumam, P. Thounthong, A comparison study of bank data in fractional calculus, Chaos Soliton. Fract., 126 (2019), 369–384. https://doi.org/10.1016/j.chaos.2019.07.025 doi: 10.1016/j.chaos.2019.07.025
![]() |
[19] |
Z. F. Li, Z. Liu, M. A. Khan, Fractional investigation of bank data with fractal-fractional Caputo derivative, Chaos Soliton. Fract., 131 (2020), 109528. https://doi.org/10.1016/j.chaos.2019.109528 doi: 10.1016/j.chaos.2019.109528
![]() |
[20] |
W. Wang, M. A. Khan, Analysis and numerical simulation of fractional model of bank data with fractal-fractional Atangana-Baleanu derivative, J. Comput. Appl. Math., 369 (2020), 112646. https://doi.org/10.1016/j.cam.2019.112646 doi: 10.1016/j.cam.2019.112646
![]() |
[21] |
M. A. Khan, M. Azizah, S. Ullah, A fractional model for the dynamics of competition between commercial and rural banks in indonesia, Chaos Soliton. Fract., 122 (2019), 32–46. https://doi.org/10.1016/j.chaos.2019.02.009 doi: 10.1016/j.chaos.2019.02.009
![]() |
[22] |
S. Ullah, M. A. Khan, M. Farooq, A fractional model for the dynamics of tb virus, Chaos Soliton. Fract., 116 (2018), 63–71. https://doi.org/10.1016/j.chaos.2018.09.001 doi: 10.1016/j.chaos.2018.09.001
![]() |
[23] |
M. A. Khan, Fatmawati, A. Atangana, E. Alzahrani, The dynamics of COVID-19 with quarantined and isolation, Adv. Differ. Equ., 2020 (2020), 425. https://doi.org/10.1186/s13662-020-02882-9 doi: 10.1186/s13662-020-02882-9
![]() |
[24] |
Fatmawati, M. A. Khan, H. P. Odinsyah, Fractional model of HIV transmission with awareness effect, Chaos Soliton. Fract., 138 (2020), 109967. https://doi.org/10.1016/j.chaos.2020.109967 doi: 10.1016/j.chaos.2020.109967
![]() |
[25] | A. Atangana, S. I. Araz, Atangana-Seda numerical scheme for Labyrinth attractor with new differential and integral operators, Fractals, 2020. https://doi.org/10.1142/S0218348X20400447 |
[26] | P. I, Fractional differential equations: An introduction to fractional derivatives, fractional differential equations, to methods of their solution and some of their applications, Academic Press, USA, 1998. |
[27] |
S. Das, P. Gupta, A mathematical model on fractional lotka-volterra equations, J. Theor. Biol., 277 (2011), 1–6. https://doi.org/10.1016/j.jtbi.2011.01.034 doi: 10.1016/j.jtbi.2011.01.034
![]() |
[28] |
M. A. Khan, Z. Hammouch, D. Baleanu, Modeling the dynamics of hepatitis E via the Caputo-Fabrizio derivative, Math. Model. Nat. Pheno., 14 (2019), 311. https://doi.org/10.1051/mmnp/2018074 doi: 10.1051/mmnp/2018074
![]() |
[29] |
M. A. Khan, S. Ullah, M. Farooq, A new fractional model for tuberculosis with relapse via atangana-baleanu derivative, Chaos Soliton. Fract., 116 (2018), 227–238. https://doi.org/10.1016/j.chaos.2018.09.039 doi: 10.1016/j.chaos.2018.09.039
![]() |
[30] | F. Fatmawati, E. Shaiful, M. Utoyo, A fractional-order model for hiv dynamics in a two-sex population, Int. J. Math. Math. Sci., 2018 (2018). https://doi.org/10.1155/2018/6801475 |
[31] | A. Atangana, J. J. Nieto, Numerical solution for the model of rlc circuit via the fractional derivative without singular kernel, Adv. Mech. Eng., 7 (2015). https://doi.org/10.1177/1687814015613758 |
[32] | Y. Che, M. Y. A. Keir, Study on the training model of football movement trajectory drop point based on fractional differential equation, Appl. Math. Nonlinear Sci., 2021, 1–6. https://doi.org/10.2478/amns.2021.2.00095 |
[33] | S. Man, R. Yang, Educational reform informatisation based on fractional differential equation, Appl. Math. Nonlinear Sci., 2021, 1–10. https://doi.org/10.2478/amns.2021.2.00079 |
[34] | J. Gao, F. S. Alotaibi, R. T. Ismail, The model of sugar metabolism and exercise energy expenditure based on fractional linear regression equation, Appl. Math. Nonlinear Sci., 2021, 1–9. https://doi.org/10.2478/amns.2021.2.00026 |
[35] | N. Zhao, F. Yao, A. O. Khadidos, B. M. Muwafak, The impact of financial repression on manufacturing upgrade based on fractional Fourier transform and probability, Appl. Math. Nonlinear Sci., 2021, 1–11. https://doi.org/10.2478/amns.2021.2.00060 |
[36] | C. Li, N. Alhebaishi, M. A. Alhamami, Calculating university education model based on finite element fractional differential equations and macro-control analysis, Appl. Math. Nonlinear Sci., 2021, 1–10. https://doi.org/10.2478/amns.2021.2.00069 |
[37] | A. Zeb, E. Alzahrani, V. S. Erturk, G. Zaman, Mathematical model for coronavirus disease 2019 (COVID-19) containing isolation class, Biomed Res. Int., 2020 (2020). https://doi.org/10.1155/2020/3452402 |
[38] |
Z. Zhang, A. Zeb, S. Hussain, E. Alzahrani, Dynamics of COVID-19 mathematical model with stochastic perturbation, Adv. Differ. Equ., 2020 (2020), 1–2. https://doi.org/10.1186/s13662-020-02909-1 doi: 10.1186/s13662-020-02909-1
![]() |
[39] |
S. Bushnaq, T. Saeed, D. F. Torres, A. Zeb, Control of COVID-19 dynamics through a fractional-order model, Alex. Eng. J., 60 (2021), 3587–3592. https://doi.org/10.1016/j.aej.2021.02.022 doi: 10.1016/j.aej.2021.02.022
![]() |
[40] |
Z. Zhang, A. Zeb, E. Alzahrani, S. Iqbal, Crowding effects on the dynamics of COVID-19 mathematical model, Adv. Differ. Equ., 2020 (2020), 1–3. https://doi.org/10.1186/s13662-020-03137-3 doi: 10.1186/s13662-020-03137-3
![]() |
[41] | A. Din, Y. Li, A. Yousaf, A. I. Ali, Caputo type fractional operator applied to Hepatitis B system, Fractals, 2021. https://doi.org/10.1142/S0218348X22400230 |
[42] | A. Din, Y. Li, F. M. Khan, Z. U. Khan, P. Liu, On Analysis of fractional order mathematical model of Hepatitis B using Atangana-Baleanu Caputo (ABC) derivative, Fractals, 2021. https://doi.org/10.1142/S0218348X22400175 |
[43] |
A. Din, A. Khan, A. Zeb, M. R. Sidi Ammi, M. Tilioua, D. F. Torres, Hybrid method for simulation of a fractional COVID-19 model with real case application, Axioms, 10 (2021), 290. https://doi.org/10.3390/axioms10040290 doi: 10.3390/axioms10040290
![]() |
[44] |
C. Xu, M. Liao, P. Li, S. Yuan, Impact of leakage delay on bifurcation in fractional-order complex-valued neural networks, Chaos Soliton. Fract., 142 (2021), 110535. https://doi.org/10.1016/j.chaos.2020.110535 doi: 10.1016/j.chaos.2020.110535
![]() |
[45] |
C. Xu, Z. Liu, L. Yao, C. Aouiti, Further exploration on bifurcation of fractional-order six-neuron bi-directional associative memory neural networks with multi-delays, Appl. Math. Comput., 410 (2021), 126458. https://doi.org/10.1016/j.amc.2021.126458 doi: 10.1016/j.amc.2021.126458
![]() |
[46] |
C. Xu, M. Liao, P. Li, Y. Guo, Q. Xiao, S. Yuan, Influence of multiple time delays on bifurcation of fractional-order neural networks, Appl. Math. Comput., 361 (2019), 565–582. https://doi.org/10.1016/j.amc.2019.05.057 doi: 10.1016/j.amc.2019.05.057
![]() |
[47] |
C. Xu, M. Liao, P. Li, Y. Guo, Z. Liu, Bifurcation properties for fractional order delayed BAM neural networks, Cogn. Comput., 13 (2021), 322–356. https://doi.org/10.1007/s12559-020-09782-w doi: 10.1007/s12559-020-09782-w
![]() |
[48] | C. J. Xu, W. Zhang, C. Aouiti, Z. X. Liu, M. X. Liao, P. L. Li, Further investigation on bifurcation and their control of fractional-order BAM neural networks involving four neurons and multiple delays, Math. Meth. Appl. Sci., 2021, 75. |
[49] | C. Xu, W. Zhang, Z. Liu, L. Yao, Delay-induced periodic oscillation for fractional-order neural networks with mixed delays, Neurocomputing, 2021. https://doi.org/10.1016/j.neucom.2021.11.079 |
[50] | OJK, Statistik Perbankan Indonesia 2004–2014. |
[51] |
A. Atangana, M. A. Khan, Modeling and analysis of competition model of bank data with fractal-fractional Caputo-Fabrizio operator, Alex. Eng. J., 159 (2020), 1985–1998. https://doi.org/10.1016/j.aej.2019.12.032 doi: 10.1016/j.aej.2019.12.032
![]() |
[52] | A. Din, Y. Li, T. Khan, G. Zaman, Mathematical analysis of spread and control of the novel corona virus (COVID-19) in China, Chaos Soliton Fract., 141 (2020). https://doi.org/10.1016/j.chaos.2020.110286 |
[53] |
A. Din, Y. Li, M. A. Shah, The complex dynamics of hepatitis B infected individuals with optimal control, J. Syst. Sci. Comput., 34 (2021), 1301–1323. https://doi.org/10.1007/s11424-021-0053-0 doi: 10.1007/s11424-021-0053-0
![]() |
[54] |
A. Din, T. Khan, Y. Li, H. Tahir, A. Khan, W. A. Khan, Mathematical analysis of dengue stochastic epidemic model, Result Phys., 20 (2021), 103719. https://doi.org/10.1016/j.rinp.2020.103719 doi: 10.1016/j.rinp.2020.103719
![]() |
[55] |
A. Din, Y. Li, The extinction and persistence of a stochastic model of drinking alcohol, Result Phys., 28 (2021), 104649. https://doi.org/10.1016/j.rinp.2021.104649 doi: 10.1016/j.rinp.2021.104649
![]() |
[56] | A. Din, Y. Li, Stochastic optimal control for norovirus transmission dynamics by contaminated food and water, Chinese Phys. B, 2021. https://doi.org/10.1088/1674-1056/ac2f32 |
[57] | A. Atangana, Mathematical model of survival of fractional calculus, critics and their impact: How singular is our world? Adv. Differ. Equ., 2021 (2021), 1–59. |
[58] |
A. Atangana, S. I. Araz, Modeling third waves of Covid-19 spread with piecewise differential and integral operators: Turkey, Spain and Czechia, Result Phys., 29 (2021), 104694. https://doi.org/10.1016/j.rinp.2021.104694 doi: 10.1016/j.rinp.2021.104694
![]() |
[59] | M. Caputo, Linear models of dissipation whose Q is almost frequency independent, part II, Geophys. J. Int., 13 (1967), 529–539. |
[60] | A. Atangana, S. I. Araz, New numerical scheme with newton polynomial: Theory, methods, and applications, Academic Press, 2021. |
Temperature, T/℃ | 20 | 200 | 400 | 600 | 800 | 1450 |
Specific heat capacity, C/J·kg-1·K-1 | 481 | 544 | 595 | 960 | 970 | |
Thermal conductivity, λ/W·m-1·K-1 | 60.3 | 54.9 | 45.2 | 36.4 | 28.5 | 27.6 |
Density, ρ/g·cm-3 | 7.85 | |||||
Liquidus temperature, TL/℃ | 1420 | |||||
Solidus temperature, Ts/℃ | 1400 | |||||
Melting latent heat, L/kJ·kg-1 | 270 (1400℃) |
Si | Ca | Mg | Ba | La | Ce | Al |
43.5 | 2.92 | 30.14 | - | 1.14 | 2.05 | 0.7 |
T/℃ | 25 | 200 | 500 | 800 | 1100 | ρ | L | |||||
Mg/% | λc | Cc | λc | Cc | λc | Cc | λc | Cc | λc | Cc | ||
30 | 111 | 807.9 | 109 | 917.6 | 107.1 | 1044.6 | 106 | 1078.7 | 106 | 1137.7 | 2.63 | 1066 |
100 | 149 | 1030 | 146 | 1100 | - | 1260 | 145 | 1400 | - | - | 1.65 | 377 |
Temperature, T/℃ | 20 | 200 | 400 | 600 | 800 | 1450 |
Specific heat capacity, C/J·kg-1·K-1 | 481 | 544 | 595 | 960 | 970 | |
Thermal conductivity, λ/W·m-1·K-1 | 60.3 | 54.9 | 45.2 | 36.4 | 28.5 | 27.6 |
Density, ρ/g·cm-3 | 7.85 | |||||
Liquidus temperature, TL/℃ | 1420 | |||||
Solidus temperature, Ts/℃ | 1400 | |||||
Melting latent heat, L/kJ·kg-1 | 270 (1400℃) |
Si | Ca | Mg | Ba | La | Ce | Al |
43.5 | 2.92 | 30.14 | - | 1.14 | 2.05 | 0.7 |
T/℃ | 25 | 200 | 500 | 800 | 1100 | ρ | L | |||||
Mg/% | λc | Cc | λc | Cc | λc | Cc | λc | Cc | λc | Cc | ||
30 | 111 | 807.9 | 109 | 917.6 | 107.1 | 1044.6 | 106 | 1078.7 | 106 | 1137.7 | 2.63 | 1066 |
100 | 149 | 1030 | 146 | 1100 | - | 1260 | 145 | 1400 | - | - | 1.65 | 377 |