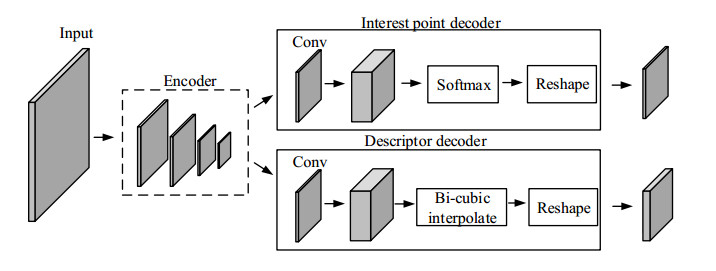
This review article provided a thorough examination of porous ceramic materials, concentrating on production, characteristics, and the involvement of pore-forming agents. The primary objective of this research was to evaluate the effects of various ceramic materials and pore-forming agents on the structure, porosity, and mechanical characteristics of porous ceramics. The study's scope included a thorough investigation of key sources of literature, such as academic publications, review articles, and industry reports, to provide a comprehensive understanding of porous ceramic technology. According to the literature review, the selection of ceramic material and pore-forming agents has a significant influence on the pore size distribution, porosity, and mechanical strength of porous ceramics. Various manufacturing methods, including foaming, sintering, and sol-gel procedures, were explored in terms of their influence on porous ceramic microstructure and characteristics. Furthermore, the study emphasized the need to optimize processing settings and select pore-forming agents to obtain the necessary qualities in porous ceramic materials. Overall, this review is useful for researchers, engineers, and practitioners who desire to learn more about porous ceramic manufacturing, characteristics, and applications.
Citation: Mohamed Lokman Jalaluddin, Umar Al-Amani Azlan, Mohd Warikh Abd Rashid, Norfauzi Tamin, Mohamad Najmi Masri. A review of pore-forming agents on the structures, porosities, and mechanical properties of porous ceramics[J]. AIMS Materials Science, 2024, 11(4): 634-665. doi: 10.3934/matersci.2024033
[1] | Yongli Yan, Tiansheng Sun, Teng Ren, Li Ding . Enhanced grip force estimation in robotic surgery: A sparrow search algorithm-optimized backpropagation neural network approach. Mathematical Biosciences and Engineering, 2024, 21(3): 3519-3539. doi: 10.3934/mbe.2024155 |
[2] | Xiaoming Liu, Zhonghan Liu, Yaqin Pan, Yufeng Huang, Desheng Wu, Zhaoyu Ba . Full-endoscopic transforaminal procedure to treat the single-level adjacent segment disease after posterior lumbar spine fusion: 1–2 years follow-up. Mathematical Biosciences and Engineering, 2019, 16(6): 7829-7838. doi: 10.3934/mbe.2019393 |
[3] | Lufeng Yao, Haiqing Wang, Feng Zhang, Liping Wang, Jianghui Dong . Minimally invasive treatment of calcaneal fractures via the sinus tarsi approach based on a 3D printing technique. Mathematical Biosciences and Engineering, 2019, 16(3): 1597-1610. doi: 10.3934/mbe.2019076 |
[4] | Xuefei Deng, Yu Liu, Hao Chen . Three-dimensional image reconstruction based on improved U-net network for anatomy of pulmonary segmentectomy. Mathematical Biosciences and Engineering, 2021, 18(4): 3313-3322. doi: 10.3934/mbe.2021165 |
[5] | Akim Kapsalyamov, Shahid Hussain, Prashant K. Jamwal . A novel compliant surgical robot: Preliminary design analysis. Mathematical Biosciences and Engineering, 2020, 17(3): 1944-1958. doi: 10.3934/mbe.2020103 |
[6] | Hafiz Muhammad Muzzammil, Yong-De Zhang, Hassan Ejaz, Qihang Yuan, Muhammad Muddassir . A review on tissue-needle interaction and path planning models for bevel tip type flexible needle minimal intervention. Mathematical Biosciences and Engineering, 2024, 21(1): 523-561. doi: 10.3934/mbe.2024023 |
[7] | Wenlu Zhang, Ziyue Ma, Hong Wang, Juan Deng, Pengfei Li, Yu Jia, Yabin Dong, Hong Sha, Feng Yan, Wenjun Tu . Study on automatic ultrasound scanning of lumbar spine and visualization system for path planning in lumbar puncture surgery. Mathematical Biosciences and Engineering, 2023, 20(1): 613-623. doi: 10.3934/mbe.2023028 |
[8] | Maher Alwuthaynani, Raluca Eftimie, Dumitru Trucu . Inverse problem approaches for mutation laws in heterogeneous tumours with local and nonlocal dynamics. Mathematical Biosciences and Engineering, 2022, 19(4): 3720-3747. doi: 10.3934/mbe.2022171 |
[9] | Tianran Yuan, Hongsheng Zhang, Hao Liu, Juan Du, Huiming Yu, Yimin Wang, Yabin Xu . Watertight 2-manifold 3D bone surface model reconstruction from CT images based on visual hyper-spherical mapping. Mathematical Biosciences and Engineering, 2021, 18(2): 1280-1313. doi: 10.3934/mbe.2021068 |
[10] | Tian Ma, Boyang Meng, Jiayi Yang, Nana Gou, Weilu Shi . A half jaw panoramic stitching method of intraoral endoscopy images based on dental arch arrangement. Mathematical Biosciences and Engineering, 2024, 21(1): 494-522. doi: 10.3934/mbe.2024022 |
This review article provided a thorough examination of porous ceramic materials, concentrating on production, characteristics, and the involvement of pore-forming agents. The primary objective of this research was to evaluate the effects of various ceramic materials and pore-forming agents on the structure, porosity, and mechanical characteristics of porous ceramics. The study's scope included a thorough investigation of key sources of literature, such as academic publications, review articles, and industry reports, to provide a comprehensive understanding of porous ceramic technology. According to the literature review, the selection of ceramic material and pore-forming agents has a significant influence on the pore size distribution, porosity, and mechanical strength of porous ceramics. Various manufacturing methods, including foaming, sintering, and sol-gel procedures, were explored in terms of their influence on porous ceramic microstructure and characteristics. Furthermore, the study emphasized the need to optimize processing settings and select pore-forming agents to obtain the necessary qualities in porous ceramic materials. Overall, this review is useful for researchers, engineers, and practitioners who desire to learn more about porous ceramic manufacturing, characteristics, and applications.
Compared to traditional surgery, the advantages of minimally invasive surgery are minor trauma, minor infection, and minor pain [1], a trend of surgical treatment in modern medicine. In modern minimally invasive surgery technology, the endoscope and specialist instruments are inserted into the internal cavity through a small incision in the surgical site. The images captured by the endoscope are displayed on the screen in real-time [2]. The surgeon can monitor the patient's entire operation through the endoscopic transmission of images and can determine the patient's surgical condition [3]. For traditional minimally invasive surgery, there are still limitations in obtaining image information from the endoscope, such as the narrow field of view, uneven illumination and high reflection intensity, and the difficulty in obtaining depth information of the target area and locating the endoscope accurately. Under such complex environmental conditions, higher requirements are put forward for computer vision processing systems. Therefore, SLAM system is innovatively applied to the field of minimally invasive surgery to solve the bottleneck faced by modern minimally invasive surgery [4]. The endoscope acts as a robot in the field of minimally invasive surgery. It moves through the cavity of the human body, measures spatial information of the visible area of the cavity, completes the reconstruction of soft tissue, and displays it to the doctor. Minimally invasive surgery can help doctors make the right decisions by combining SLAM with better positioning of the endoscope and depth of the target area. It has crucial research significance and application value [5].
The concept of minimally invasive surgery and the issue of visual SLAM were first proposed in 1983 and 1986, respectively. The use of vision technology based on endoscope images in minimally invasive surgery has obvious advantages without introducing additional equipment to the already very complex surgical device [6]. SLAM is most frequently used in minimally invasive surgery in the abdomen, where deformation and tissue movement are minimal. At the initial stage of application, SLAM was added to the algorithm as an auxiliary means for positioning [7]. In 2009, Grasa et al. used monocular laparoscopy to generate a sparse map of the environment from SLAM and then estimated the three-dimensional information of the scene through sequential images. In 2009 and 2010, the Mountney P team respectively proposed the application of an SLAM system based on the monocular endoscope and binocular endoscope in minimally invasive surgery for endoscope positioning and 3D modeling, and the monocular system based on the framework of SLAM to establish a motion model to estimate the motion of the camera and soft tissue effectively [8]. The binocular system constructs a 3D texture model of a minimally invasive surgery environment, a method model of dynamic view expansion [9]. In recent years, there have been more and more studies on the application of visual SLAM in minimally invasive surgery [10,11,12], most of which are devoted to solving the bottleneck of minimally invasive surgery. Vision-based techniques are good at restoring 3D structures and estimating endoscope motion. However, this research has a long way to go to solve the problems of accuracy [13].
This paper mainly studies visual SLAM in minimally invasive surgery. For the deficiencies of traditional minimally invasive surgery, visual SLAM technology is used to complete the positioning and 3D mapping of the endoscope [14,15]. In combination with the K-means algorithm and the Super point algorithm, the feature information of the image in the inner cavity is extracted. It solves the problem that it is difficult to obtain the depth information of the target area and accurately locate the endoscope position in the environment with narrow vision, uneven illumination and high reflection intensity of minimally invasive surgical endoscope. Then, the iterative nearest point method was used to estimate the position and attitude of the endoscope. Finally, the stereo matching method was used to reconstruct the lumen image, and the point cloud image of the surgical area was recovered. Improve surgical accuracy and shorten the surgical time, thus optimizing the operation of the entire system [16].
The structure of this paper is as follows. Section 2 discusses the visual SLAM and the method of extracting image features through Superpoint algorithm, as well as the method of extracting image feature points based on Superpoint algorithm and k-means algorithm. In Section 3, experiments are carried out to verify the effectiveness of our proposed method. Section 4 summarizes the whole article.
The final output of the Super point (self supervised interest point detection and description) algorithm is the feature point algorithm with descriptors [17]. The network diagram is shown in Figure 1.
In this network, the initial feature detector is obtained by training the basic graph with undisputed feature points in a self-supervised way, and the image feature information is further extracted by the neural network. The stability of feature extraction is improved while the sensitivity of the feature extraction algorithm to illumination is reduced. The network is divided into two parts [18], the network for detecting basic graph corners and the network for extracting image features and outputting descriptors. The specific steps are as follows:
(1) Feature point detector pre-training. For an image, it is difficult to define which points are the real feature points, but if it is a simple graph with defined corner positions, it is easy to determine the truth. Therefore, the pre-training is carried out by extracting undisputed feature points from an unlabelled virtual simple image, obtaining pseudo-truths, and using the resulting pseudo-truths to determine the true feature points. Then, the pseudo-true values are combined with the true values to retrain the feature detector to obtain the extracted feature. The resulting pseudo-truths are combined with the true values to retrain the feature detector to obtain the extracted feature point model.
(2) The feature point detection network is divided into two parts: encoding and decoding. Image coding is to input the image to be processed into the shared coding network and reduce the dimension of the image to reduce the computation of the network. After dimensionality reduction, the image size is 1/8 of the original image. The main function of the encoder in the network is to map the input image to the spatial tensor, which has a smaller spatial dimension and larger channel depth. A probability is calculated for each pixel, which represents the probability that this pixel is a feature point. When decoding feature points, subpixel convolution is adopted to avoid the possibility of network overload caused by excessive computation in the process of extracting feature points. The input dimension of the decoder is
(3) Description sub detection network. Extracting the descriptor is a decoding operation. The descriptors are obtained from feature points. First, the image size and feature point position are normalized.
K-Means clustering algorithm will use all the data as a whole, the initial clustering center is
After the Super point algorithm extracts the feature points and descriptors of the image, the heatmap of the feature map can be obtained. Each feature point in the heatmap has an index value, and the K-means method is used to cluster these index values. When feature points are matched, a confidence probability of a correct match is set for each index value. According to this probability, whether this point is the correct match of the points to be matched is determined. Set the maximum number of matching point pairs and match according to the index of feature points. When all feature points are matched, or the maximum number of matching points is reached, the matching graph is output. The K-means clustering algorithm is applied to avoid the successful matching between the reflective spot and the strong light point in the inner cavity and reduce the probability of mismatching. Because the k-means algorithm is very simple, very fast, time complexity is nearly linear, and it is suitable for mining large-scale datasets, combining it with the super point algorithm not only improves the matching degree, but also shortens the time it takes to compute the k-means algorithm.
The pose estimation process is actually to find the corresponding point between the 2D image and the 3D spatial position. When representing an object's 3D spatial position and orientation, a coordinate system rotating with the object is usually established with the object as the coordinate origin. The transformation relationship between the rotating coordinate system and the reference coordinate system can determine the spatial position of the object. That is, the solution of pose estimation discusses the transformation relationship between coordinate systems.
In visual SLAM, there are usually two methods to estimate the pose of the sensor. One is to use a linear method to estimate the pose information of the visual sensor. After obtaining the initial pose, the pose information is further optimized by constructing and solving the least square problem. The other is to directly integrate the position of the space point and the position of the sensor to solve the pose information. In the estimation of the pose information of the endoscope, since the position of the endoscope is not continuous and uniform, the first method is selected to solve the pose information of the endoscope. The initial pose is estimated first, and then the results are optimized to increase the accuracy and robustness of the SLAM system.
The iterative closest point (ICP) is a standard algorithm that estimates pose between completed 3D Point pairs. Suppose there are a pair of 3D point pairs matched and their centroids:
P={p1,…,pn},P′={p′1,…,p′n}p=1nn∑i=1(pi),p′=1nn∑i=1(p′i) | (1) |
where:
To perform pose estimation is actually to find a Euclidean transform that satisfies:
∀i,pi=Rp′i+t | (2) |
The result of the above formula is solved through the algebraic method of singular value decomposition, and the error term of the point
ei=pi−(Rpi′+t) | (3) |
Constructing the least-squares problem:
minR,tJ=12n∑i=1‖pi−(Rp′i+t)‖22=12n∑i=1‖pi−p−R(p′i−p′)‖22+‖p−Rp′−t‖22 | (4) |
Solve the above equation and get
qi=pi−p, q′i=p′i−p′ | (5) |
The rotation matrix and translation vector are calculated according to the following formula:
{R∗=argminR12n∑i=1‖qi−Rq′i‖22t∗=p−Rp′ | (6) |
Define matrix:
W=n∑i=1qiqi′T | (7) |
R=UVT | (8) |
Substitute the solved rotation matrix into Eq (8) to solve the translation vector.
Firstly, the disparity value of the target region is obtained and optimized by the SGBM stereo matching method; Secondly, the depth value is calculated by using the parallax value to form the depth image; Finally, the 3D point cloud data are obtained by further calculation.
Parallax refers to that when binocular stereo vision obtains two frames of images at the same time through the left and right cameras, the corresponding relationship between features is established at the imaging points on the left and right imaging planes of the camera through the corresponding three-dimensional space points so that the human eye can feel the depth. Observe the imaging difference of the image on the camera plane. This difference is called parallax. In short, parallax describes the horizontal pixel difference between the corresponding imaging points of the left and right eyes [21].
There is a point
The parallax values in the parallax map can be calculated to obtain the corresponding depth values. The depth map shows the form of the image by integrating these depth values. The depth map contains the depth information of each pixel value, and the pixel value in the depth map is the depth value. According to the geometric relation of parallel binocular vision, the relation between parallax value and object depth information is as follows:
bdep=(b+xr)−xldep−f | (9) |
where:
dep=b×fxl−xr=f×bd | (10) |
where,
According to the coordinate transformation relation, the transformation relation between the world coordinate system and the pixel coordinate system can be obtained as follows:
zp[uv1]=[fx0cx0fycy001][R,t][XYZ1] | (11) |
where: The first matrix on the right of the equation is the endoscope internal parameter; matrix
{z=zpx=(u−cx)×zp/fxy=(v−cy)×zp/fy | (12) |
The calculated data can be saved in the created point cloud data, and the point cloud image can be displayed by using some libraries. The depth image of point cloud data can be calculated through the reverse calculation of the above operations.
In order to verify whether the improved algorithm has better feature extraction and matching effect in the strong reflection environment in minimally invasive surgery, the feature extraction results of the improved algorithm and the improved algorithm in the lumen environment are compared, and the simulation results are compared and analyzed. The original image pairs for feature extraction are shown in a) and b) Figure 5. By comparing the feature extraction results of various methods on the image pairs, the effectiveness of the improved extraction network is shown [22].
The results of image feature extraction using the original Super point algorithm are shown in c) in Figure 5, and the results of feature extraction using the improved Super point algorithm are shown in d) in Figure 5. As can be seen from the figure, the number of feature points extracted by the Super point algorithm in the inner cavity environment under a strong reflection environment is more and more uniform than that extracted by the traditional algorithm, but there are too many failed matching points and many invalid points. These matching failed points and invalid points are caused by the narrow field of vision, uneven lighting and high reflection intensity of minimally invasive surgical endoscope, The numerical value of the depth map physically means the distance from the camera. A lot of black and a lot of white are similar distances from you. The feature points are difficult to extract, and the resolution of the depth map is low, which reduces the number of feature points that can be extracted. False matching situations are reasonable. However, the distribution of feature points extracted by the improved Super point algorithm is more uniform, and effective features can be extracted from the edge part of the insufficient light. e) in Figure 5 is the matching result of feature points extracted by the original Super point algorithm, and f) in Figure 5 is the matching result of feature points extracted by the improved Super point algorithm. It can be easily seen from the figure that the improved algorithm has a better matching effect on feature points, and the number of invalid feature points is 0, which is better than the original algorithm and the traditional algorithm. As can be seen from Figure 5 and Table 1, after the Super point algorithm and clustering algorithm are combined and improved, the number of feature extraction effects of the inner cavity image increases and is evenly distributed, without any redundant points that fail to be matched successfully, and the percentage of successfully matched points in the total number of extractions is the highest and the false matching rate is the lowest. Although the proportion of effective points extracted by SIFT, SURF and ORB algorithms can reach 100%, their speed is very slow when there are too many matching points, and there are many wrong matching point pairs. The original Superpoint algorithm can not only ensure the number of feature points, but also ensure the speed, but it has a very low proportion of effective points. Compared with the traditional feature extraction algorithm and the original Super point algorithm, it shows the best effect.
SIFT | SURF | ORB | Superpoint | Improving Superpoint | |
Extracting time /s | 1.282 | 0.182 | 0.125 | 0.103 | 0.101 |
Match time /s | 0.187 | 0.078 | 0.031 | 0.018 | 0.021 |
Extract point pairs/pairs | 334 | 121 | 268 | 352 | 349 |
Match point pairs/pairs | 334 | 121 | 268 | 263 | 349 |
False match point pair/pair | 79 | 25 | 31 | 13 | 15 |
Effective point proportion /% | 100.00 | 100.00 | 100.00 | 74.72 | 100.00 |
False match rate /% | 23.65 | 20.66 | 11.57 | 4.94 | 4.30 |
Table 1 shows the numerical results of each algorithm. From the two indicators of Extracting time and Match time in the table, the time of the improved algorithm is significantly shorter than that of other algorithms, which also proves that the improved algorithm has the minimum time consumption, the maximum number of matching success points and the minimum mismatch rate, and the effective point ratio is significantly improved compared with that before the improvement.
Different from large-scale scenarios, when the endoscope is in the special environment of minimally invasive surgery, the estimation of the position information of the endoscope only needs numerical values. Since the movement process of the endoscope is irregular, it is not meant to form the map of its position information [23]. In this topic, will the SLAM system of camera pose estimation algorithm used in endoscopic minimally invasive surgery, using the image information of the real environment of minimally invasive surgery for endoscopic frame only when the estimate judgment in endoscopic movement between rotation and translation in the process of calculation is accurate, lumen mapping results of image feature points as shown in Figure 6.
The blue point in Figure 6 is the feature point of the current frame, and the green point is the feature point of the next frame. The current frame is directly processed without any operation. The position difference between blue and green is why the camera moves when shooting different frames, and the red point is the position of the green point after the rotation matrix and the motion vector move left. The distance between blue dots and red dots is smaller than that between green dots, with an average error of 5.43 pixels.
The disparity image and depth image before and after optimization are obtained by using the algorithm in this chapter as follows:
Figure 7 shows the point cloud before and after optimization of the lumen image in the actual scene, which is displayed in the gray form, and the cavity area is more obvious. The image information with too dark illumination in the original image has the condition that the visual difference has not been calculated, so the depth value cannot be calculated, which is reflected as the whole area in the point cloud image. The point cloud image before optimization has obvious segmentation lines. After optimization, this phenomenon is weakened, and most of the information is effectively restored. The details of the main areas are more delicate, and some smaller blood vessels that are not easy to extract can also be restored [24].
Figure 8 is a pure point cloud image without adding mesh and texture. The color depth in the figure indicates the distance between the point and the endoscope. Although the edge results of the disparity map and depth map are not satisfactory, it can be seen from b) of Figures 7 and 8 that the reconstruction method adopted can have a good effect on the restoration of images in the lumen environment.
As can be seen from a) and b) in Figure 9, except for the empty part with extremely weak light, the image has a filling effect, and the edge is partially optimized. Although the "boundary" between the core area and the fat part of the image does not have an excellent restoration result, the edge is smoothed. c) is a pure point cloud image without mesh and texture, and the depth of color in the figure represents the distance between the point and the endoscope. d) is the point cloud diagram of the inner cavity image in the real scene. In the case of the image information with a too-dark light in the original image, the parallax value is not calculated, so the depth value cannot be calculated, which is reflected in the point cloud image as the empty area in the figure. Most of the information in the image can be effectively restored. The details of the main areas are delicate, and some small vessels that are not easy to be extracted can also be recovered. The reconstruction method used in this paper can restore the image in the inner cavity with good effect.
In view of the problem that it is difficult to obtain depth information on the target area and accurately locate the position of the endoscope in the environment of the narrow field of vision, uneven illumination, and high reflection intensity of minimally invasive surgery endoscope, the method based on the combination of K-means and Super point algorithm is first used to extract image feature points and match. Compared with the traditional algorithm, the simulation results are more accurate and stable. Compared with the Super point, the logarithm of successful matching points is increased by 32.69%, the proportion of effective points is increased by 25.28%, the false matching rate is reduced by 0.64%, and the extraction time is reduced by 1.98%. In the real minimally invasive surgery scene, the feature points in the endovascular image were mapped to verify the accuracy of the calculated rotation and translation, with an average error of 5 pixels. Finally, the stereo matching algorithm is used to calculate the disparity map of the original image, and then the disparity map is used to calculate the depth information so as to calculate the point cloud image with depth information, which can well reconstruct the small features such as blood vessels in the image, and also have a good reconstruction effect on the edge part of the insufficient light [25].
Funding: This research was supported by the Natural Science Foundation of Heilongjiang Province (LH2019F024), China, 2019–2022, and Key R & D Program Guidance Projects of Heilongjiang Province (Grant No. GZ20210065), 2021–2024
The authors declare there is no conflict of interest.
[1] | Sudha PN, Sangeetha K, Vijayalakshmi K, et al. (2018) Nanomaterials history, classification, unique properties, production and market, In: Barhoum A, Makhlouf ASH, Emerging Applications of Nanoparticles and Architecture Nanostructures, Amsterdam: Elsevier, 341–384. https://doi.org/10.1016/B978-0-323-51254-1.00012-9 |
[2] | Al-Naib UMB (2018) Introductory chapter: A brief introduction to porous ceramic, In: Al-Naib UMB, Recent Advances in Porous Ceramics, Rijeka: IntechOpen. https://doi.org/10.5772/intechopen.74747 |
[3] |
Yin D, Chen C, Saito M, et al. (2019) Ceramic phases with one-dimensional long-range order. Nature Mater 18: 19–23. https://doi.org/10.1038/s41563-018-0240-0 doi: 10.1038/s41563-018-0240-0
![]() |
[4] |
Mitchell AL, Perea DE, Wirth MG, et al. (2021) Nanoscale microstructure and chemistry of transparent gahnite glass-ceramics revealed by atom probe tomography. Scripta Mater 203: 114110. https://doi.org/10.1016/j.scriptamat.2021.114110 doi: 10.1016/j.scriptamat.2021.114110
![]() |
[5] |
Liu X, Wang H, Lu H, et al. (2023) Grain-interior planar defects induced by heteroatom monolayer. APM 2: 100130. https://doi.org/10.1016/j.apmate.2023.100130 doi: 10.1016/j.apmate.2023.100130
![]() |
[6] |
Xiong H, Shui A, Shan Q, et al. (2021) Fabrication of foamed ceramics with enhanced compressive strength and low thermal conductivity via a simple route. Mater Chem Phys 267: 124699. https://doi.org/10.1016/j.matchemphys.2021.124699 doi: 10.1016/j.matchemphys.2021.124699
![]() |
[7] |
Chen A, Li L, Wang C, et al. (2022) Novel porous ceramic with high strength and thermal performance using MA hollow spheres. Prog Nat Sci 32: 732–738. https://doi.org/10.1016/j.pnsc.2022.09.015 doi: 10.1016/j.pnsc.2022.09.015
![]() |
[8] |
Lou J, He C, Shui A, et al. (2023) Enhanced sound absorption performance of porous ceramics with closed-pore structure. Ceram Int 49: 38103–38114. https://doi.org/10.1016/j.ceramint.2023.09.140 doi: 10.1016/j.ceramint.2023.09.140
![]() |
[9] |
Zhou G, Gu Q, Sun H, et al. (2024) High-temperature self-healing behavior of reaction-bonded silicon carbide porous ceramic membrane supports. J Eur Ceram Soc 44: 1959–1971. https://doi.org/10.1016/j.jeurceramsoc.2023.11.065 doi: 10.1016/j.jeurceramsoc.2023.11.065
![]() |
[10] |
Liao M, De Guzman MR, Shen G, et al. (2024) Preparation of compact ZrC-SiC ceramic matrix from thermoset precursors for C/C-ZrC-SiC composites with high mechanical properties. J Eur Ceram Soc 44: 1983–1999. https://doi.org/10.1016/j.jeurceramsoc.2023.11.076 doi: 10.1016/j.jeurceramsoc.2023.11.076
![]() |
[11] |
Li B, Xu G, Wang B, et al. (2021) Fabrication and characterization of bioactive zirconia-based nanocrystalline glass-ceramics for dental abutment. Ceram Int 47: 26877–26890. https://doi.org/10.1016/j.ceramint.2021.06.097 doi: 10.1016/j.ceramint.2021.06.097
![]() |
[12] |
Sobczak-Kupiec A, Tomala AM, Domínguez López C, et al. (2022) Polymer–ceramic biocomposites based on PVP/histidine/hydroxyapatite for hard tissue engineering applications. Int J Polym Mater Polym Biomater 71: 1380–1392. http://dx.doi.org/10.1080/00914037.2021.1963725 doi: 10.1080/00914037.2021.1963725
![]() |
[13] |
Thanigachalam M, Muthusamy Subramanian AV (2022) Evaluation of PEEK-TiO2-SiO2 nanocomposite as biomedical implants with regard to in-vitro biocompatibility and material characterization. J Biomater Sci Polym Ed 33: 727–746. https://doi.org/10.1080/09205063.2021.2014028 doi: 10.1080/09205063.2021.2014028
![]() |
[14] |
Nasedkin A, Nassar ME (2022) Comprehensive numerical characterization of a piezoelectric composite with hollow metallic inclusions using an adaptable random representative volume. Comput Struct 267: 106799. https://doi.org/10.1016/j.compstruc.2022.106799 doi: 10.1016/j.compstruc.2022.106799
![]() |
[15] |
Nasedkin A, Nassar ME (2021) About anomalous properties of porous piezoceramic materials with metalized or rigid surfaces of pores. Mech Mater 162: 104040. https://doi.org/10.1016/j.mechmat.2021.104040 doi: 10.1016/j.mechmat.2021.104040
![]() |
[16] |
Shakirzyanov RI, Volodina NO, Kozlovskiy AL, et al. (2023) Study of the structural, electrical, and mechanical properties and morphological features of Y-doped CeO2 ceramics with porous structure. J Compos Sci 7: 411. https://doi.org/10.3390/jcs7100411 doi: 10.3390/jcs7100411
![]() |
[17] |
Michalak J (2021) Ceramic tile adhesives from the producer's perspective: A literature review. Ceramics 4: 378–390. https://doi.org/10.3390/ceramics4030027 doi: 10.3390/ceramics4030027
![]() |
[18] |
Sadineni SB, Madala S, Boehm RF (2011) Passive building energy savings: A review of building envelope components. Renew Sust Energ Rev 15: 3617–3631. https://doi.org/10.1016/j.rser.2011.07.014 doi: 10.1016/j.rser.2011.07.014
![]() |
[19] |
Pacheco R, Ordóñez J, Martínez G (2012) Energy efficient design of building: A review. Renew Sust Energ Rev 16: 3559–3573. https://doi.org/10.1016/j.rser.2012.03.045 doi: 10.1016/j.rser.2012.03.045
![]() |
[20] |
Mirrahimi S, Mohamed MF, Haw LC, et al. (2016) The effect of building envelope on the thermal comfort and energy saving for high-rise buildings in hot–humid climate. Renew Sust Energ Rev 53: 1508–1519. https://doi.org/10.1016/j.rser.2015.09.055 doi: 10.1016/j.rser.2015.09.055
![]() |
[21] |
Frankel GS, Vienna JD, Lian J, et al. (2018) A comparative review of the aqueous corrosion of glasses, crystalline ceramics, and metals. npj Mater Degrad 2: 15. https://doi.org/10.1038/s41529-018-0037-2 doi: 10.1038/s41529-018-0037-2
![]() |
[22] |
Liu Y, Ma H, Hsiao BS, et al. (2016) Improvement of meltdown temperature of lithium-ion battery separator using electrospun polyethersulfone membranes. Polymer 107: 163–169. https://doi.org/10.1016/j.polymer.2016.11.020 doi: 10.1016/j.polymer.2016.11.020
![]() |
[23] |
Wen Q, Yu Z, Riedel R (2020) The fate and role of in situ formed carbon in polymer-derived ceramics. Prog Mater Sci 109: 100623. https://doi.org/10.1016/j.pmatsci.2019.100623 doi: 10.1016/j.pmatsci.2019.100623
![]() |
[24] |
Chen Y, Wang N, Ola O, et al. (2021) Porous ceramics: Light in weight but heavy in energy and environment technologies. Mater Sci Eng R 143: 100589. https://doi.org/10.1016/j.mser.2020.100589 doi: 10.1016/j.mser.2020.100589
![]() |
[25] |
Al-Shaeli M, Orhun Teber O, Al-Juboori RA, et al. (2024) Inorganic layered polymeric membranes: Highly-ordered porous ceramics for surface engineering of polymeric membranes. Sep Purif Technol 350: 127925. https://doi.org/10.1016/j.seppur.2024.127925 doi: 10.1016/j.seppur.2024.127925
![]() |
[26] |
Fukushima M (2013) Microstructural control of macroporous silicon carbide. J Ceram Soc Jpn 121: 162–168. https://doi.org/10.2109/jcersj2.121.162 doi: 10.2109/jcersj2.121.162
![]() |
[27] |
Youness RA, Tag El-deen DM, Taha MA (2023) A review on calcium silicate ceramics: Properties, limitations, and solutions for their use in biomedical applications. Silicon 15: 2493–2505. https://doi.org/10.1007/s12633-022-02207-3 doi: 10.1007/s12633-022-02207-3
![]() |
[28] |
Tulyaganov DU, Dimitriadis K, Agathopoulos S, et al. (2023) Glasses and glass-ceramics in the CaO–MgO–SiO2 system: Diopside containing compositions—A brief review. J Non Cryst Solids 612: 122351. https://doi.org/10.1016/j.jnoncrysol.2023.122351 doi: 10.1016/j.jnoncrysol.2023.122351
![]() |
[29] | Zhao X (2011) Bioactive materials in orthopaedics, In: Zhao X, Courtney JM, Qian H, Bioactive Materials in Medicine, Amsterdam: Elsevier, 124–154. https://doi.org/10.1533/9780857092939.2.124 |
[30] | Zahir A, Mahmood U, Nazir A, et al. (2022) Biomaterials for medical and healthcare products, In: Mondal MIH, Medical Textiles from Natural Resources, Amsterdam: Elsevier, 43–86. https://doi.org/10.1016/B978-0-323-90479-7.00013-0 |
[31] |
Merlet RB, Pizzoccaro-Zilamy MA, Nijmeijer A, et al. (2020) Hybrid ceramic membranes for organic solvent nanofiltration: State-of-the-art and challenges. J Memb Sci 599: 117839. https://doi.org/10.1016/j.memsci.2020.117839 doi: 10.1016/j.memsci.2020.117839
![]() |
[32] |
Li C, Sun W, Lu Z, et al. (2020) Ceramic nanocomposite membranes and membrane fouling: A review. Water Res 175: 115674. https://doi.org/10.1016/j.watres.2020.115674 doi: 10.1016/j.watres.2020.115674
![]() |
[33] |
Alonso-De la Garza DA, Guzmán AM, Gómez-Rodríguez C, et al. (2022) Influence of Al2O3 and SiO2 nanoparticles addition on the microstructure and mechano-physical properties of ceramic tiles. Ceram Int 48: 12712–12720. https://doi.org/10.1016/j.ceramint.2022.01.140 doi: 10.1016/j.ceramint.2022.01.140
![]() |
[34] |
Maletsky AV, Belichko DR, Konstantinova TE, et al. (2021) Structure formation and properties of corundum ceramics based on metastable aluminium oxide doped with stabilized zirconium dioxide. Ceram Int 47: 19489–19495. https://doi.org/10.1016/j.ceramint.2021.03.286 doi: 10.1016/j.ceramint.2021.03.286
![]() |
[35] |
Besisa DHA, Ewais EMM, Ahmed YMZ (2021) A comparative study of thermal conductivity and thermal emissivity of high temperature solar absorber of ZrO2/Fe2O3 and Al2O3/CuO ceramics. Ceram Int 47: 28252–28259. https://doi.org/10.1016/j.ceramint.2021.06.240 doi: 10.1016/j.ceramint.2021.06.240
![]() |
[36] |
Zheng W, Li C, Yuan J, et al. (2022) The crystallization and fracture toughness of transparent glass-ceramics with various Al2O3 additions for mobile devices. J Wuhan Univ Technol Mater Sci Ed 37: 378–384. https://doi.org/10.1007/s11595-022-2542-y doi: 10.1007/s11595-022-2542-y
![]() |
[37] |
Jõgiaas T, Zabels R, Tarre A, et al. (2020) Hardness and modulus of elasticity of atomic layer deposited Al2O3-ZrO2 nanolaminates and mixtures. Mater Chem Phys 240: 122270. https://doi.org/10.1016/j.matchemphys.2019.122270 doi: 10.1016/j.matchemphys.2019.122270
![]() |
[38] |
Tang H, Rogov AB, Soutis C, et al. (2023) Fabrication, interfacial and flexural properties of a polymer composite reinforced by γ-Al2O3/Al fibres. Compos Part A Appl Sci Manuf 169: 107502. https://doi.org/10.1016/j.compositesa.2023.107502 doi: 10.1016/j.compositesa.2023.107502
![]() |
[39] |
Lin L, Wu H, Li Y, et al. (2024) Effect of particle size on rheology, curing kinetics, and corresponding mechanical and thermal properties of aluminum nitride (AlN) ceramic by digital light processing (DLP)-based vat photopolymerization. J Eur Ceram Soc 44: 184–192. https://doi.org/10.1016/j.jeurceramsoc.2023.08.048 doi: 10.1016/j.jeurceramsoc.2023.08.048
![]() |
[40] |
Yang X, Bi J, Liang G, et al. (2022) The effect of boron nitride nanosheets on the mechanical and thermal properties of aluminum nitride ceramics. Int J Appl Ceram Technol 19: 2817–2825. https://doi.org/10.1111/ijac.14069 doi: 10.1111/ijac.14069
![]() |
[41] |
Duan W, Li S, Wang G, et al. (2020) Thermal conductivities and mechanical properties of AlN ceramics fabricated by three dimensional printing. J Eur Ceram Soc 40: 3535–3540. https://doi.org/10.1016/j.jeurceramsoc.2020.04.004 doi: 10.1016/j.jeurceramsoc.2020.04.004
![]() |
[42] |
Yaşar ZA, Haber RA (2020) Effect of carbon addition and mixture method on the microstructure and mechanical properties of silicon carbide. Materials 13: 3768. https://doi.org/10.3390/ma13173768 doi: 10.3390/ma13173768
![]() |
[43] |
Li C, Li S, An D, et al. (2020) Microstructure and mechanical properties of spark plasma sintered SiC ceramics aided by B4C. Ceram Int 46: 10142–10146. https://doi.org/10.1016/j.ceramint.2020.01.005 doi: 10.1016/j.ceramint.2020.01.005
![]() |
[44] |
Kultayeva S, Kim Y (2023) Electrical, thermal, and mechanical properties of porous silicon carbide ceramics with a boron carbide additive. Int J Appl Ceram Technol 20: 1114–1128. https://doi.org/10.1111/ijac.14113 doi: 10.1111/ijac.14113
![]() |
[45] |
Kim GD, Kim YW, Song IH, et al. (2020) Effects of carbon and silicon on electrical, thermal, and mechanical properties of porous silicon carbide ceramics. Ceram Int 46: 15594–15603. https://doi.org/10.1016/j.ceramint.2020.03.106 doi: 10.1016/j.ceramint.2020.03.106
![]() |
[46] |
Vivekananthan M, Ahilan C, Sakthivelu S, et al. (2020) A primary study of density and compressive strength of the silicon nitride and titanium nitride ceramic composite. Mater Today Proc 33: 2741–2745. https://doi.org/10.1016/j.matpr.2020.01.570 doi: 10.1016/j.matpr.2020.01.570
![]() |
[47] |
Lv X, Huang J, Dong X, et al. (2023) Influence of α-Si3N4 coarse powder on densification, microstructure, mechanical properties, and thermal behavior of silicon nitride ceramics. Ceram Int 49: 21815–21824. https://doi.org/10.1016/j.ceramint.2023.04.003 doi: 10.1016/j.ceramint.2023.04.003
![]() |
[48] |
Ye CC, Ma K, Chen HM, et al. (2024) Effect of texture on the thermal conductivity and mechanical properties of silicon nitride ceramic. Ceram Int 50: 4014–4021. https://doi.org/10.1016/j.ceramint.2023.11.170 doi: 10.1016/j.ceramint.2023.11.170
![]() |
[49] |
Duan Y, Liu N, Zhang J, et al. (2020) Cost effective preparation of Si3N4 ceramics with improved thermal conductivity and mechanical properties. J Eur Ceram Soc 40: 298–304. https://doi.org/10.1016/j.jeurceramsoc.2019.10.003 doi: 10.1016/j.jeurceramsoc.2019.10.003
![]() |
[50] |
Li S, Wei C, Wang P, et al. (2020) Fabrication of ZrO2 whisker modified ZrO2 ceramics by oscillatory pressure sintering. Ceram Int 46: 17684–17690. https://doi.org/10.1016/j.ceramint.2020.04.071 doi: 10.1016/j.ceramint.2020.04.071
![]() |
[51] |
Oguntuyi SD, Johnson OT, Shongwe MB, et al. (2021) The effects of sintering additives on the ceramic matrix composite of ZrO2: Microstructure, densification, and mechanical properties—A review. Adv Appl Ceram 120: 319–335. https://doi.org/10.1080/17436753.2021.1953845 doi: 10.1080/17436753.2021.1953845
![]() |
[52] |
Lian W, Liu Z, Zhu R, et al. (2021) Effects of zirconium source and content on zirconia crystal form, microstructure and mechanical properties of ZTM ceramics. Ceram Int 47: 19914–19922. https://doi.org/10.1016/j.ceramint.2021.03.327 doi: 10.1016/j.ceramint.2021.03.327
![]() |
[53] |
Chen G, Ling Y, Li Q, et al. (2020) Stability properties and structural characteristics of CaO-partially stabilized zirconia ceramics synthesized from fused ZrO2 by microwave sintering. Ceram Int 46: 16842–16848. https://doi.org/10.1016/j.ceramint.2020.03.261 doi: 10.1016/j.ceramint.2020.03.261
![]() |
[54] |
Mhadhbi M, Driss M (2020) Titanium carbide: Synthesis, properties and applications. BEN 2: 1–11. https://doi.org/10.36937/ben.2021.002.001 doi: 10.36937/ben.2021.002.001
![]() |
[55] |
Alonso-De la Garza DA, Guzmán AM, Gómez-Rodríguez C, et al. (2022) Influence of Al2O3 and SiO2 nanoparticles addition on the microstructure and mechano-physical properties of ceramic tiles. Ceram Int 48: 12712–12720. https://doi.org/10.1016/j.ceramint.2022.01.140 doi: 10.1016/j.ceramint.2022.01.140
![]() |
[56] |
Ye K, Li F, Zhang J, et al. (2021) Effect of SiO2 on microstructure and mechanical properties of composite ceramic coatings prepared by centrifugal-SHS process. Ceram Int 47: 12833–12842. https://doi.org/10.1016/j.ceramint.2021.01.144 doi: 10.1016/j.ceramint.2021.01.144
![]() |
[57] |
Rahimi S, SharifianJazi F, Esmaeilkhanian A, et al. (2020) Effect of SiO2 content on Y-TZP/Al2O3 ceramic-nanocomposite properties as potential dental applications. Ceram Int 46: 10910–10916. https://doi.org/10.1016/j.ceramint.2020.01.105 doi: 10.1016/j.ceramint.2020.01.105
![]() |
[58] |
Kang ES, Kim YW, Nam WH (2021) Multiple thermal resistance induced extremely low thermal conductivity in porous SiC-SiO2 ceramics with hierarchical porosity. J Eur Ceram Soc 41: 1171–1180. https://doi.org/10.1016/j.jeurceramsoc.2020.10.004 doi: 10.1016/j.jeurceramsoc.2020.10.004
![]() |
[59] |
Keziz A, Rasheed M, Heraiz M, et al. (2023) Structural, morphological, dielectric properties, impedance spectroscopy and electrical modulus of sintered Al6Si2O13–Mg2Al4Si5O18 composite for electronic applications. Ceram Int 49: 37423–37434. https://doi.org/10.1016/j.ceramint.2023.09.068 doi: 10.1016/j.ceramint.2023.09.068
![]() |
[60] |
Ren Y, Zhang B, Zhong Z, et al. (2024) A simple and efficient hydratable alumina gel‐casting method for the fabrication of high‐porosity mullite ceramics. J Am Ceram Soc 107: 2067–2080. https://doi.org/10.1111/jace.19550 doi: 10.1111/jace.19550
![]() |
[61] |
Huang J, Yao M, Lin J, et al. (2022) Enhanced mechanical properties and excellent electrical properties of PZT piezoelectric ceramics modified by YSZ. Mater Lett 307: 131006. https://doi.org/10.1016/j.matlet.2021.131006 doi: 10.1016/j.matlet.2021.131006
![]() |
[62] |
Coleman K, Ritter M, Bermejo R, et al. (2021) Mechanical failure dependence on the electrical history of lead zirconate titanate thin films. J Eur Ceram Soc 41: 2465–2471. https://doi.org/10.1016/j.jeurceramsoc.2020.11.002 doi: 10.1016/j.jeurceramsoc.2020.11.002
![]() |
[63] |
Tiwari B, Babu T, Choudhary RNP (2021) Piezoelectric lead zirconate titanate as an energy material: A review study. Mater Today Proc 43: 407–412. https://doi.org/10.1016/j.matpr.2020.11.692 doi: 10.1016/j.matpr.2020.11.692
![]() |
[64] |
Okayasu M, Okawa M (2021) Piezoelectric properties of lead zirconate titanate ceramics at low and high temperatures. Adv Appl Ceram 120: 127–133. https://doi.org/10.1080/17436753.2021.1904765 doi: 10.1080/17436753.2021.1904765
![]() |
[65] |
Thakur VN, Yadav S, Kumar A (2021) Effect of bismuth substitution on piezoelectric coefficients and temperature and pressure-dependent dielectric and impedance properties of lead zirconate titanate ceramics. Mater Today Commun 26: 101846. https://doi.org/10.1016/j.mtcomm.2020.101846 doi: 10.1016/j.mtcomm.2020.101846
![]() |
[66] |
Khorashadizade F, Abazari S, Rajabi M, et al. (2021) Overview of magnesium-ceramic composites: Mechanical, corrosion and biological properties. J Mater Res Technol 15: 6034–6066. https://doi.org/10.1016/j.jmrt.2021.10.141 doi: 10.1016/j.jmrt.2021.10.141
![]() |
[67] |
Ma B, Zan W, Liu K, et al. (2023) Preparation and properties of porous MgO based ceramics from magnesite tailings and fused magnesia. Ceram Int 49: 19072–19082. https://doi.org/10.1016/j.ceramint.2023.03.034 doi: 10.1016/j.ceramint.2023.03.034
![]() |
[68] |
Wei Y, Gu S, Fang H, et al. (2020) Properties of MgO transparent ceramics prepared at low temperature using high sintering activity MgO powders. J Am Ceram Soc 103: 5382–5391. https://doi.org/10.1111/jace.17267 doi: 10.1111/jace.17267
![]() |
[69] |
Xie YZ, Peng CQ, Wang XF, et al. (2017) Porous alumina ceramic prepared by HEMA-TBA gelcasting system. J Inorg Mater 32: 731. http://dx.doi.org/10.15541/jim20160550 doi: 10.15541/jim20160550
![]() |
[70] |
Yu J, Wang H, Zhang J, et al. (2010) Gelcasting preparation of porous silicon nitride ceramics by adjusting the content of monomers. J Solgel Sci Technol 53: 515–523. https://doi.org/10.1007/s10971-009-2125-9 doi: 10.1007/s10971-009-2125-9
![]() |
[71] |
Yang J, Yu J, Huang Y (2011) Recent developments in gelcasting of ceramics. J Eur Ceram Soc 31: 2569–2591. https://doi.org/10.1016/j.jeurceramsoc.2010.12.035 doi: 10.1016/j.jeurceramsoc.2010.12.035
![]() |
[72] |
Belrhiti Y, Kerth P, McGilvray M, et al. (2023) Gel-casting for manufacturing porous alumina ceramics with complex shapes for transpiration cooling. Adv Appl Ceram 122: 375–380. https://doi.org/10.1080/17436753.2023.2265204 doi: 10.1080/17436753.2023.2265204
![]() |
[73] |
Han L, Deng X, Li F, et al. (2018) Preparation of high strength porous mullite ceramics via combined foam-gelcasting and microwave heating. Ceram Int 44: 14728–14733. https://doi.org/10.1016/j.ceramint.2018.05.101 doi: 10.1016/j.ceramint.2018.05.101
![]() |
[74] |
Deng X, Ran S, Han L, et al. (2017) Foam-gelcasting preparation of high-strength self-reinforced porous mullite ceramics. J Eur Ceram Soc 37: 4059–4066. https://doi.org/10.1016/j.jeurceramsoc.2017.05.009 doi: 10.1016/j.jeurceramsoc.2017.05.009
![]() |
[75] |
Ge S, Lin L, Zhang H, et al. (2018) Synthesis of hierarchically porous mullite ceramics with improved thermal insulation via foam-gelcasting combined with pore former addition. Adv Appl Ceram 117: 493–499. https://doi.org/10.1080/17436753.2018.1502065 doi: 10.1080/17436753.2018.1502065
![]() |
[76] |
Saidi R, Fathi M, Salimijazi H, et al. (2017) Fabrication and characterization nanostructured forsterite foams with high compressive strength, desired porosity and suitable bioactivity for biomedical applications. J Solgel Sci Technol 81: 734–740. https://doi.org/10.1007/s10971-016-4240-8 doi: 10.1007/s10971-016-4240-8
![]() |
[77] |
Zhou W, Yan W, Li N, et al. (2019) Fabrication of mullite-corundum foamed ceramics for thermal insulation and effect of micro-pore-foaming agent on their properties. J Alloys Compd 785: 1030–1037. https://doi.org/10.1016/j.jallcom.2019.01.212 doi: 10.1016/j.jallcom.2019.01.212
![]() |
[78] |
Zhou M, Ge X, Wang H, et al. (2017) Effect of the CaO content and decomposition of calcium-containing minerals on properties and microstructure of ceramic foams from fly ash. Ceram Int 43: 9451–9457. https://doi.org/10.1016/j.ceramint.2017.04.122 doi: 10.1016/j.ceramint.2017.04.122
![]() |
[79] |
Liu T, Tang Y, Li Z, et al. (2016) Red mud and fly ash incorporation for lightweight foamed ceramics using lead-zinc mine tailings as foaming agent. Mater Lett 183: 362–364. https://doi.org/10.1016/j.matlet.2016.07.041 doi: 10.1016/j.matlet.2016.07.041
![]() |
[80] |
Li Z, Mao H, Korzhavyi PA, et al. (2016) Thermodynamic re-assessment of the Co–Cr system supported by first-principles calculations. Calphad 52: 1–7. https://doi.org/10.1016/j.calphad.2015.10.013 doi: 10.1016/j.calphad.2015.10.013
![]() |
[81] |
Scialla S, Carella F, Dapporto M, et al. (2020) Mussel shell-derived macroporous 3D scaffold: Characterization and optimization study of a bioceramic from the circular economy. Mar Drugs 18: 309. https://doi.org/10.3390/md18060309 doi: 10.3390/md18060309
![]() |
[82] |
Liu R, Xu T, Wang C (2016) A review of fabrication strategies and applications of porous ceramics prepared by freeze-casting method. Ceram Int 42: 2907–2925. https://doi.org/10.1016/j.ceramint.2015.10.148 doi: 10.1016/j.ceramint.2015.10.148
![]() |
[83] |
Mocciaro A, Lombardi MB, Scian AN (2017) Ceramic material porous structure prepared using pore-forming additives. Refract Ind Ceram 58: 65–68. https://doi.org/10.1007/s11148-017-0055-6 doi: 10.1007/s11148-017-0055-6
![]() |
[84] |
Yu J, Yang Z, Song Z, et al. (2018) Preparation of porous Al2O3 ceramics with in situ formed C-nanowires derived form silicone resin. Mater Lett 212: 271–274. https://doi.org/10.1016/j.matlet.2017.10.054 doi: 10.1016/j.matlet.2017.10.054
![]() |
[85] |
Zhang Y, Wu Y, Yang X, et al. (2020) High-strength thermal insulating mullite nanofibrous porous ceramics. J Eur Ceram Soc 40: 2090–2096. https://doi.org/10.1016/j.jeurceramsoc.2020.01.011 doi: 10.1016/j.jeurceramsoc.2020.01.011
![]() |
[86] |
Yang J, Xu L, Wu H, et al. (2021) Preparation and properties of porous ceramics from spodumene flotation tailings by low-temperature sintering. T Nonferr Metal Soc 31: 2797–2811. https://doi.org/10.1016/S1003-6326(21)65694-7 doi: 10.1016/S1003-6326(21)65694-7
![]() |
[87] |
Dang W, Wang W, Wu P, et al. (2022) Freeze-cast porous Al2O3 ceramics strengthened by up to 80% ceramics fibers. Ceram Int 48: 9835–9841. https://doi.org/10.1016/j.ceramint.2021.12.185 doi: 10.1016/j.ceramint.2021.12.185
![]() |
[88] |
Studart AR, Gonzenbach UT, Tervoort E, et al. (2006) Processing routes to macroporous ceramics: A review. J Am Ceram Soc 89: 1771–1789. https://doi.org/10.1111/j.1551-2916.2006.01044.x doi: 10.1111/j.1551-2916.2006.01044.x
![]() |
[89] |
Xu H, Liu J, Guo A, et al. (2012) Porous silica ceramics with relatively high strength and novel bi-modal pore structure prepared by a TBA-based gel-casting method. Ceram Int 38: 1725–1729. https://doi.org/10.1016/j.ceramint.2011.09.013 doi: 10.1016/j.ceramint.2011.09.013
![]() |
[90] |
Novais RM, Seabra MP, Labrincha JA (2014) Ceramic tiles with controlled porosity and low thermal conductivity by using pore-forming agents. Ceram Int 40: 11637–11648. https://doi.org/10.1016/j.ceramint.2014.03.163 doi: 10.1016/j.ceramint.2014.03.163
![]() |
[91] |
Kultayeva S, Kim YW, Song IH (2021) Effects of dopants on electrical, thermal, and mechanical properties of porous SiC ceramics. J Eur Ceram Soc 41: 4006–4015. https://doi.org/10.1016/j.jeurceramsoc.2021.01.049 doi: 10.1016/j.jeurceramsoc.2021.01.049
![]() |
[92] |
Wei Z, Li S, Li Y, et al. (2018) Porous alumina ceramics with enhanced mechanical and thermal insulation properties based on sol-treated rice husk. Ceram Int 44: 22616–22621. https://doi.org/10.1016/j.ceramint.2018.09.036 doi: 10.1016/j.ceramint.2018.09.036
![]() |
[93] |
Liu J, Ren B, Wang Y, et al. (2019) Hierarchical porous ceramics with 3D reticular architecture and efficient flow-through filtration towards high-temperature particulate matter capture. Chem Eng J 362: 504–512. https://doi.org/10.1016/j.cej.2019.01.065 doi: 10.1016/j.cej.2019.01.065
![]() |
[94] |
Guzman IY (2003) Certain principles of formation of porous ceramic structures. Properties and applications (a review). Glass Ceram 60: 280–283. https://doi.org/10.1023/B:GLAC.0000008227.85944.64 doi: 10.1023/B:GLAC.0000008227.85944.64
![]() |
[95] |
Vogt UF, Györfy L, Herzog A, et al. (2007) Macroporous silicon carbide foams for porous burner applications and catalyst supports. J Phys Chem Solids 68: 1234–1238. https://doi.org/10.1016/j.jpcs.2006.12.008 doi: 10.1016/j.jpcs.2006.12.008
![]() |
[96] |
Hammel EC, Ighodaro OLR, Okoli OI (2014) Processing and properties of advanced porous ceramics: An application based review. Ceram Int 40: 15351–15370. https://doi.org/10.1016/j.ceramint.2014.06.095 doi: 10.1016/j.ceramint.2014.06.095
![]() |
[97] |
Zuo KH, Zeng YP, Jiang D (2010) Effect of polyvinyl alcohol additive on the pore structure and morphology of the freeze-cast hydroxyapatite ceramics. Mater Sci Eng C 30: 283–287. https://doi.org/10.1016/j.msec.2009.11.003 doi: 10.1016/j.msec.2009.11.003
![]() |
[98] |
Chen F, Ma L, Shen Q, et al. (2011) Pore structure control of starch processed silicon nitride porous ceramics with near-zero shrinkage. Mater Lett 65: 1410–1412. https://doi.org/10.1016/j.matlet.2011.02.016 doi: 10.1016/j.matlet.2011.02.016
![]() |
[99] |
Liu J, Ren B, Zhu T, et al. (2018) Enhanced mechanical properties and decreased thermal conductivity of porous alumina ceramics by optimizing pore structure. Ceram Int 44: 13240–13246. https://doi.org/10.1016/j.ceramint.2018.04.151 doi: 10.1016/j.ceramint.2018.04.151
![]() |
[100] |
DiReda N, D'Orazio G, Sobhani S (2024) Thermal and structural performance of additively manufactured ceramic porous media burners. J Eur Ceram Soc 44: 2271–2279. https://doi.org/10.1016/j.jeurceramsoc.2023.11.001 doi: 10.1016/j.jeurceramsoc.2023.11.001
![]() |
[101] |
Roy S (2024) Recent developments in processing techniques and morphologies of bulk macroporous ceramics for multifunctional applications. Mater Today Commun 38: 107752. https://doi.org/10.1016/j.mtcomm.2023.107752 doi: 10.1016/j.mtcomm.2023.107752
![]() |
[102] |
Rathee G, Bartwal G, Rathee J, et al. (2021) Emerging multimodel zirconia nanosystems for high‐performance biomedical applications. Adv NanoBiomed Res 1: 2100039. https://doi.org/10.1002/anbr.202100039 doi: 10.1002/anbr.202100039
![]() |
[103] |
Pandey V, Yadav MK, Gupta A, et al. (2022) Synthesis, morphological and thermomechanical characterization of light weight silica foam via reaction generated thermo-foaming process. J Eur Ceram Soc 42: 6671–6683. https://doi.org/10.1016/j.jeurceramsoc.2022.07.034 doi: 10.1016/j.jeurceramsoc.2022.07.034
![]() |
[104] |
Park HY, Lee HJ, Seo H, et al. (2023) Improvement of mechanical properties of ceramic green body and fired body by aging of inorganic binder in ceramic slurry for 3D printing. J Eur Ceram Soc 44: 3400–3409. https://doi.org/10.1016/j.jeurceramsoc.2023.12.066 doi: 10.1016/j.jeurceramsoc.2023.12.066
![]() |
[105] |
Adukadukkam AK, Pillai R, Puthiyathara Kanakamma M (2024) Offshore high‐grade limemud resources of west coast of India: Economic potential and industrial applications. Deep Undergr Sci Eng 3: 163–170. https://doi.org/10.1002/dug2.12064 doi: 10.1002/dug2.12064
![]() |
[106] |
Ma Y, He B, Wang J, et al. (2021) Porous/dense bilayer BaZr0.8Y0.2O3-δ electrolyte matrix fabricated by tape casting combined with solid-state reactive sintering for protonic ceramic fuel cells. Int J Hydrogen Energy 46: 9918–9926. https://doi.org/10.1016/j.ijhydene.2020.04.282 doi: 10.1016/j.ijhydene.2020.04.282
![]() |
[107] |
Long K, Zhong Y, Wang B, et al. (2023) A novel strategy in micomechanics modeling of silica fibrous ceramics considering morphology-related sintering effects. Compos Part A Appl Sci Manuf 175: 107751. https://doi.org/10.1016/j.compositesa.2023.107751 doi: 10.1016/j.compositesa.2023.107751
![]() |
[108] |
Chen Y, Tian X, Su K, et al. (2023) Preparation and properties of porous mullite-based ceramics fabricated by solid state reaction. Ceram Int 49: 31846–31854. https://doi.org/10.1016/j.ceramint.2023.07.144 doi: 10.1016/j.ceramint.2023.07.144
![]() |
[109] |
Nicoara AI, Alecu AE, Balaceanu GC, et al. (2023) Fabrication and characterization of porous diopside/akermanite ceramics with prospective tissue engineering applications. Materials 16: 5548. https://doi.org/10.3390/ma16165548 doi: 10.3390/ma16165548
![]() |
[110] |
Xiang R, Cheng LC, Qi HY, et al. (2023) Electromagnetic wave absorption properties of Ca1-xCexFe0.5Mn0.5O3–δ ceramics prepared by a sol–gel combustion method. Ceram Int 49: 8350–8360. https://doi.org/10.1016/j.ceramint.2022.10.367 doi: 10.1016/j.ceramint.2022.10.367
![]() |
[111] |
Fiume E, Massera J, D'Ambrosio D, et al. (2022) Robocasting of multicomponent sol-gel–derived silicate bioactive glass scaffolds for bone tissue engineering. Ceram Int 48: 35209–35216. https://doi.org/10.1016/j.ceramint.2022.08.121 doi: 10.1016/j.ceramint.2022.08.121
![]() |
[112] |
Li S, Cui H, Ma Q, et al. (2021) The one-step pyrolysis process of rattan-based silicon carbide multiphase ceramics prepared by sol–gel method. J Wood Sci 67: 58. https://doi.org/10.1186/s10086-021-01991-7 doi: 10.1186/s10086-021-01991-7
![]() |
[113] |
Xu X, Liu X, Wu J, et al. (2021) Fabrication and characterization of porous mullite ceramics with ultra-low shrinkage and high porosity via sol-gel and solid state reaction methods. Ceram Int 47: 20141–20150. https://doi.org/10.1016/j.ceramint.2021.04.020 doi: 10.1016/j.ceramint.2021.04.020
![]() |
[114] |
Lin L, Wang H, Xia C, et al. (2023) Low sintering shrinkage porous mullite ceramics with high strength and low thermal conductivity via foam‐gelcasting. J Am Ceram Soc 106: 3800–3811. https://doi.org/10.1111/jace.19035 doi: 10.1111/jace.19035
![]() |
[115] |
Zhong Z, Zhang B, Tian Z, et al. (2022) Highly porous LAS-SiC ceramic with near-zero thermal expansion prepared via aqueous gel-casting combined with adding pore-forming agents. Mater Charact 187: 111829. https://doi.org/10.1016/j.matchar.2022.111829 doi: 10.1016/j.matchar.2022.111829
![]() |
[116] |
Dong B, Wang L, Min Z, et al. (2022) Fabrication of novel porous Al2O3 substrates by combining emulsion templating and gel-tape-casting methods. Ceram Int 48: 7320–7324. https://doi.org/10.1016/j.ceramint.2021.11.205 doi: 10.1016/j.ceramint.2021.11.205
![]() |
[117] | Yüzbasi NS, Graule T (2021) Colloid casting processes: slip casting, centrifugal casting, and gel casting, In: Pomeroy M, Encyclopedia of Materials: Technical Ceramics and Glasses, Amsterdam: Elsevier, 146–153. https://doi.org/10.1016/b978-0-12-803581-8.11767-9 |
[118] |
Ricceri F, Malaguti M, Derossi C, et al. (2022) Microalgae biomass concentration and reuse of water as new cultivation medium using ceramic membrane filtration. Chemosphere 307: 135724. https://doi.org/10.1016/j.chemosphere.2022.135724 doi: 10.1016/j.chemosphere.2022.135724
![]() |
[119] |
Echakouri M, Salama A, Henni A (2022) Experimental investigation of the novel periodic feed pressure technique in minimizing fouling during the filtration of oily water systems using ceramic membranes. Membranes 12: 868. https://doi.org/10.3390/membranes12090868 doi: 10.3390/membranes12090868
![]() |
[120] |
Wu C, Wan B, Entezari A, et al. (2024) Machine learning-based design for additive manufacturing in biomedical engineering. Int J Mech Sci 266: 108828. https://doi.org/10.1016/j.ijmecsci.2023.108828 doi: 10.1016/j.ijmecsci.2023.108828
![]() |
[121] |
Youness RA, Al-Ashkar E, Taha MA (2023) Role of porosity in the strength, dielectric properties, and bioactivity of hardystonite ceramic material for use in bone tissue engineering applications. Ceram Int 49: 40520–40531. https://doi.org/10.1016/j.ceramint.2023.10.029 doi: 10.1016/j.ceramint.2023.10.029
![]() |
[122] |
Khan MUA, Aslam MA, Bin Abdullah MF, et al. (2023) Recent perspective of polymeric biomaterial in tissue engineering—A review. Mater Today Chem 34: 101818. https://doi.org/10.1016/j.mtchem.2023.101818 doi: 10.1016/j.mtchem.2023.101818
![]() |
[123] |
Dobriţa CI, Bădănoiu AI, Voicu G, et al. (2023) Porous bioceramic scaffolds based on akermanite obtained by 3D printing for bone tissue engineering. Ceram Int 49: 35898–35906. https://doi.org/10.1016/j.ceramint.2023.08.270 doi: 10.1016/j.ceramint.2023.08.270
![]() |
[124] |
Raymond Y, Johansson L, Thorel E, et al. (2022) Translation of three-dimensional printing of ceramics in bone tissue engineering and drug delivery. MRS Bull 47: 59–69. https://doi.org/10.1557/s43577-021-00259-1 doi: 10.1557/s43577-021-00259-1
![]() |
[125] |
Arai Y, Saito M, Samizo A, et al. (2024) Material design using calculation phase diagram for refractory high‐entropy ceramic matrix composites. Int J Appl Ceram Technol 21: 2702–2711. https://doi.org/10.1111/ijac.14688 doi: 10.1111/ijac.14688
![]() |
[126] |
Schönfeld K, Klemm H (2019) Interaction of fiber matrix bonding in SiC/SiC ceramic matrix composites. J Eur Ceram Soc 39: 3557–3565. https://doi.org/10.1016/j.jeurceramsoc.2019.05.025 doi: 10.1016/j.jeurceramsoc.2019.05.025
![]() |
[127] |
Kütemeyer M, Schomer L, Helmreich T, et al. (2016) Fabrication of ultra high temperature ceramic matrix composites using a reactive melt infiltration process. J Eur Ceram Soc 36: 3647–3655. https://doi.org/10.1016/j.jeurceramsoc.2016.04.039 doi: 10.1016/j.jeurceramsoc.2016.04.039
![]() |
[128] |
Dele-Afolabi T, Azmah Hanim M, Jung D, et al. (2022) Rice husk as a pore-forming agent: Impact of particle size on the porosity and diametral tensile strength of porous alumina ceramics. Coatings 12: 1259. https://doi.org/10.3390/coatings12091259 doi: 10.3390/coatings12091259
![]() |
[129] |
Wan Y, Li X, Ma J (2023) Mullite porous ceramics with high strength for high-temperature thermal insulation. J Mater Res Technol 27: 5692–5700. https://doi.org/10.1016/j.jmrt.2023.10.288 doi: 10.1016/j.jmrt.2023.10.288
![]() |
[130] |
Guo T, Liu Z, Yu C, et al. (2023) Effect of pore structure evolution on mechanical properties and thermal conductivity of porous SiC-Mullite ceramics. Ceram Int 49: 33618–33627. https://doi.org/10.1016/j.ceramint.2023.08.040 doi: 10.1016/j.ceramint.2023.08.040
![]() |
[131] |
Chen Y, Tian X, Su K, et al. (2023) Preparation and properties of porous mullite-based ceramics fabricated by solid state reaction. Ceram Int 49: 31846–31854. https://doi.org/10.1016/j.ceramint.2023.07.144 doi: 10.1016/j.ceramint.2023.07.144
![]() |
[132] |
Qin Z, Xu X, Xu T, et al. (2022) High-strength thermal insulating porous mullite fiber-based ceramics. J Eur Ceram Soc 42: 7209–7218. https://doi.org/10.1016/j.jeurceramsoc.2022.08.050 doi: 10.1016/j.jeurceramsoc.2022.08.050
![]() |
[133] |
Deng X, Zhang W, Yin J, et al. (2020) Microstructure and mechanical performance of porous mullite ceramics added with TiO2. Ceram Int 46: 8438–8443. https://doi.org/10.1016/j.ceramint.2019.12.078 doi: 10.1016/j.ceramint.2019.12.078
![]() |
[134] |
Choo TF, Mohd Salleh MA, Kok KY, et al. (2019) Modified cenospheres as non-sacrificial pore-forming agent for porous mullite ceramics. Ceram Int 45: 21827–21834. https://doi.org/10.1016/j.ceramint.2019.07.189 doi: 10.1016/j.ceramint.2019.07.189
![]() |
[135] |
Mohammadi M, Pascaud-Mathieu P, Allizond V, et al. (2020) Robocasting of single and multi-functional calcium phosphate scaffolds and its hybridization with conventional techniques: Design, fabrication and characterization. Appl Sci 10: 8677. https://doi.org/10.3390/app10238677 doi: 10.3390/app10238677
![]() |
[136] |
Das D, Lucio MDS, Kultayeva S, et al. (2024) Effect of pore size on the flexural strength of porous silicon carbide ceramics. Open Ceram 17: 100521. https://doi.org/10.1016/j.oceram.2023.100521 doi: 10.1016/j.oceram.2023.100521
![]() |
[137] |
Das D, Lucio MDS, Kultayeva S, et al. (2023) Effects of pore size on electrical and thermal properties of porous SiC ceramics. Int J Appl Ceram Technol 21: 2651–2662. https://doi.org/10.1111/ijac.14620 doi: 10.1111/ijac.14620
![]() |
[138] |
Chen G, Yang F, Zhao S, et al. (2022) Preparation of high-strength porous mullite ceramics and the effect of hollow sphere particle size on microstructure and properties. Ceram Int 48: 19367–19374. https://doi.org/10.1016/j.ceramint.2022.03.231 doi: 10.1016/j.ceramint.2022.03.231
![]() |
[139] | Farid SBH (2019) Bioceramics: For Materials Science and Engineering, Amsterdam: Elsevier, 1–37. https://doi.org/10.1016/C2016-0-04604-1 |
[140] |
Ohji T, Fukushima M (2012) Macro-porous ceramics: Processing and properties. Int Mater Rev 57: 115–131. https://doi.org/10.1179/1743280411Y.0000000006 doi: 10.1179/1743280411Y.0000000006
![]() |
[141] |
Schlumberger C, Thommes M (2021) Characterization of hierarchically ordered porous materials by physisorption and mercury porosimetry—A tutorial review. Adv Mater Interfaces 8: 2002181. https://doi.org/10.1002/admi.202002181 doi: 10.1002/admi.202002181
![]() |
[142] |
Colombo P (2006) Conventional and novel processing methods for cellular ceramics. Philos Trans R Soc A 364: 109–124. https://doi.org/10.1098/rsta.2005.1683 doi: 10.1098/rsta.2005.1683
![]() |
[143] |
Eom JH, Kim YW, Raju S (2013) Processing and properties of macroporous silicon carbide ceramics: A review. J Asian Ceram Soc 1: 220–242. https://doi.org/10.1016/j.jascer.2013.07.003 doi: 10.1016/j.jascer.2013.07.003
![]() |
[144] |
Khattab RM, Wahsh MMS, Khalil NM (2012) Preparation and characterization of porous alumina ceramics through starch consolidation casting technique. Ceram Int 38: 4723–4728. https://doi.org/10.1016/j.ceramint.2012.02.057 doi: 10.1016/j.ceramint.2012.02.057
![]() |
[145] |
He R, Qu Z, Cheng X (2016) Effects of starch addition amount on microstructure, mechanical properties and room temperature thermal conductivity of porous Y2SiO5 ceramics. Ceram Int 42: 2257–2262. https://doi.org/10.1016/j.ceramint.2015.10.019 doi: 10.1016/j.ceramint.2015.10.019
![]() |
[146] |
Li Y, Cao W, Gong L, et al. (2016) Effect of starch on sintering behavior for fabricating porous cordierite ceramic. High Temp Mater Processes 35: 955–961. https://doi.org/10.1515/htmp-2015-0074 doi: 10.1515/htmp-2015-0074
![]() |
[147] |
Khattab RM, EL-Rafei AM, Zawrah MF (2018) Fabrication of porous TiO2 ceramics using corn starch and graphite as pore forming agents. Interceram-Int Ceram Rev 67: 30–35. https://doi.org/10.1007/s42411-018-0024-1 doi: 10.1007/s42411-018-0024-1
![]() |
[148] |
Mastalska-Popławska J, Sikora M, Izak P, et al. (2019) Applications of starch and its derivatives in bioceramics. J Biomater Appl 34: 12–24. https://doi.org/10.1177/0885328219844972 doi: 10.1177/0885328219844972
![]() |
[149] |
Ishii K, Shimizu M, Sameshima H, et al. (2020) Fabrication of porous (Ba, Sr)(Co, Fe)O3-δ (BSCF) ceramics using gelatinization and retrogradation phenomena of starch as pore-forming agent. Ceram Int 46: 13047–13053. https://doi.org/10.1016/j.ceramint.2020.02.075 doi: 10.1016/j.ceramint.2020.02.075
![]() |
[150] |
Cui Z, Hao T, Yao S, et al. (2023) Preparation of porous mullite ceramic supports from high alumina fly ash. J Mater Cycles Waste Manag 25: 1120–1129. https://doi.org/10.1007/s10163-023-01598-8 doi: 10.1007/s10163-023-01598-8
![]() |
[151] |
Pinheiro ED, Thenmuhil D (2021) Effect of different pore formers on the performance of lead free piezoelectric ceramics. Ferroelectrics 583: 162–176. https://doi.org/10.1080/00150193.2021.1980343 doi: 10.1080/00150193.2021.1980343
![]() |
[152] |
Wang W, Chen W, Liu H (2019) Recycling of waste red mud for fabrication of SiC/mullite composite porous ceramics. Ceram Int 45: 9852–9857. https://doi.org/10.1016/j.ceramint.2019.02.024 doi: 10.1016/j.ceramint.2019.02.024
![]() |
[153] |
Wan P, Wang J (2018) Highly porous nano-SiC with very low thermal conductivity and excellent high temperature behavior. J Eur Ceram Soc 38: 463–467. https://doi.org/10.1016/j.jeurceramsoc.2017.09.037 doi: 10.1016/j.jeurceramsoc.2017.09.037
![]() |
[154] |
Sarikaya A, Dogan F (2013) Effect of various pore formers on the microstructural development of tape-cast porous ceramics. Ceram Int 39: 403–413. https://doi.org/10.1016/j.ceramint.2012.06.041 doi: 10.1016/j.ceramint.2012.06.041
![]() |
[155] |
Živcová Z, Gregorová E, Pabst W (2007) Porous alumina ceramics produced with lycopodium spores as pore-forming agents. J Mater Sci 42: 8760–8764. https://doi.org/10.1007/s10853-007-1852-y doi: 10.1007/s10853-007-1852-y
![]() |
[156] |
Abhinay S, Dixit P, Mazumder R (2020) Effect of pore former sucrose on microstructure and electrical properties of porous BZT-0.5BCT ceramics. Ferroelectrics 557: 18–27. https://doi.org/10.1080/00150193.2020.1713359 doi: 10.1080/00150193.2020.1713359
![]() |
[157] |
Mohanta K, Kumar A, Parkash O, et al. (2014) Processing and properties of low cost macroporous alumina ceramics with tailored porosity and pore size fabricated using rice husk and sucrose. J Eur Ceram Soc 34: 2401–2412. https://doi.org/10.1016/j.jeurceramsoc.2014.01.024 doi: 10.1016/j.jeurceramsoc.2014.01.024
![]() |
[158] |
Le Ray AM, Gautier H, Bouler JM, et al. (2010) A new technological procedure using sucrose as porogen compound to manufacture porous biphasic calcium phosphate ceramics of appropriate micro- and macrostructure. Ceram Int 36: 93–101. https://doi.org/10.1016/j.ceramint.2009.07.001 doi: 10.1016/j.ceramint.2009.07.001
![]() |
[159] |
Wu Q, Yang C, Zhang H, et al. (2013) Fabrication and characterization of reaction-bonded silicon carbide with poly(methyl methacrylate) as pore-forming agent. Ceram Int 39: 5295–5302. https://doi.org/10.1016/j.ceramint.2012.12.032 doi: 10.1016/j.ceramint.2012.12.032
![]() |
[160] |
Novais RM, Seabra MP, Labrincha JA (2014) Ceramic tiles with controlled porosity and low thermal conductivity by using pore-forming agents. Ceram Int 40: 11637–11648. https://doi.org/10.1016/j.ceramint.2014.03.163 doi: 10.1016/j.ceramint.2014.03.163
![]() |
[161] |
Mahnicka-Goremikina L, Svinka R, Svinka V, et al. (2023) Porous mullite ceramic modification with nano-WO3. Materials 16: 4631. https://doi.org/10.3390/ma1613463 doi: 10.3390/ma1613463
![]() |
[162] |
Obradović N, Filipović S, Marković S, et al. (2017) Influence of different pore-forming agents on wollastonite microstructures and adsorption capacities. Ceram Int 43: 7461–7468. https://doi.org/10.1016/j.ceramint.2017.03.021 doi: 10.1016/j.ceramint.2017.03.021
![]() |
[163] |
Yang H, Li Y, Li Q, et al. (2020) Preparation and properties of porous silicon nitride ceramics with polymethyl methacrylate as pore-forming agent. Ceram Int 46: 17122–17129. https://doi.org/10.1016/j.ceramint.2020.03.204 doi: 10.1016/j.ceramint.2020.03.204
![]() |
[164] |
Wang S, Yang Z, Luo X, et al. (2022) Preparation of calcium hexaluminate porous ceramics by gel-casting method with polymethyl methacrylate as pore-forming agent. Ceram Int 48: 30356–30366. https://doi.org/10.1016/j.ceramint.2022.06.309 doi: 10.1016/j.ceramint.2022.06.309
![]() |
[165] |
Pia G, Casnedi L, Sanna U (2015) Porous ceramic materials by pore-forming agent method: An intermingled fractal units analysis and procedure to predict thermal conductivity. Ceram Int 41: 6350–6357. https://doi.org/10.1016/j.ceramint.2015.01.069 doi: 10.1016/j.ceramint.2015.01.069
![]() |
[166] |
Fang L, Chen C, Wang Y (2022) Carbon fibers and graphite as pore-forming agents for the obtention of porous alumina: Correlating physical and fractal characteristics. Fractal Fract 6: 501. https://doi.org/10.3390/fractalfract6090501 doi: 10.3390/fractalfract6090501
![]() |
[167] |
Mercadelli E, Sanson A, Pinasco P, et al. (2011) Influence of carbon black on slurry compositions for tape cast porous piezoelectric ceramics. Ceram Int 37: 2143–2149. https://doi.org/10.1016/j.ceramint.2011.03.058 doi: 10.1016/j.ceramint.2011.03.058
![]() |
[168] |
Liu J, Li Y, Li Y, et al. (2016) Effects of pore structure on thermal conductivity and strength of alumina porous ceramics using carbon black as pore-forming agent. Ceram Int 42: 8221–8228. https://doi.org/10.1016/j.ceramint.2016.02.032 doi: 10.1016/j.ceramint.2016.02.032
![]() |
[169] |
Çelik A, Çağlar G, Çelik Y (2022) Fabrication of porous Al2O3 ceramics using carbon black as a pore forming agent by spark plasma sintering. Ceram Int 48: 28181–28190. https://doi.org/10.1016/j.ceramint.2022.06.121 doi: 10.1016/j.ceramint.2022.06.121
![]() |
[170] |
Wang S, Liu M, Liu X, et al. (2022) Carbothermal reduction synthesis of high porosity and low thermal conductivity ZrC-SiC ceramics via an one-step sintering technique. J Eur Ceram Soc 42: 4465–4471. https://doi.org/10.1016/j.jeurceramsoc.2022.04.044 doi: 10.1016/j.jeurceramsoc.2022.04.044
![]() |
[171] |
Fu F, Hu N, Ye Y, et al. (2023) The foaming mechanism and properties of SiO2–Al2O3–CaO-based foamed ceramics with varied foaming agents. Ceram Int 49: 32448–32457. https://doi.org/10.1016/j.ceramint.2023.07.192 doi: 10.1016/j.ceramint.2023.07.192
![]() |
[172] |
Jalaluddin ML, Azlan UAA, Rashid MWA (2023) A preliminary study of porous ceramics with carbon black contents. AIMS Mater Sci 10: 741–754. https://doi.org/10.3934/matersci.2023041 doi: 10.3934/matersci.2023041
![]() |
[173] |
Wu C, Li Z, Li Y, et al. (2023) Effect of starch on pore structure and thermal conductivity of diatomite-based porous ceramics. Ceram Int 49: 383–391. https://doi.org/10.1016/j.ceramint.2022.08.352 doi: 10.1016/j.ceramint.2022.08.352
![]() |
[174] |
Parku GK, Collard FX, Görgens JF (2020) Pyrolysis of waste polypropylene plastics for energy recovery: Influence of heating rate and vacuum conditions on composition of fuel product. Fuel Process Technol 209: 106522. https://doi.org/10.1016/j.fuproc.2020.106522 doi: 10.1016/j.fuproc.2020.106522
![]() |
[175] |
Singh RK, Ruj B, Sadhukhan AK, et al. (2020) A TG-FTIR investigation on the co-pyrolysis of the waste HDPE, PP, PS and PET under high heating conditions. J Energy Inst 93: 1020–1035. https://doi.org/10.1016/j.joei.2019.09.003 doi: 10.1016/j.joei.2019.09.003
![]() |
[176] |
Harussani MM, Sapuan SM, Rashid U, et al. (2022) Pyrolysis of polypropylene plastic waste into carbonaceous char: Priority of plastic waste management amidst COVID-19 pandemic. Sci Total Environ 803: 149911. https://doi.org/10.1016/j.scitotenv.2021.149911 doi: 10.1016/j.scitotenv.2021.149911
![]() |
[177] |
Lomonaco T, Manco E, Corti A, et al. (2020) Release of harmful volatile organic compounds (VOCs) from photo-degraded plastic debris: A neglected source of environmental pollution. J Hazard Mater 394: 122596. https://doi.org/10.1016/j.jhazmat.2020.122596 doi: 10.1016/j.jhazmat.2020.122596
![]() |
[178] |
Shen M, Song B, Zeng G, et al. (2020) Are biodegradable plastics a promising solution to solve the global plastic pollution? Environ Pollut 263: 114469. https://doi.org/10.1016/j.envpol.2020.114469 doi: 10.1016/j.envpol.2020.114469
![]() |
[179] |
Evode N, Qamar SA, Bilal M, et al. (2021) Plastic waste and its management strategies for environmental sustainability. Case Stud Chem Environ Eng 4: 100142. https://doi.org/10.1016/j.cscee.2021.100142 doi: 10.1016/j.cscee.2021.100142
![]() |
[180] |
Hou Y, Qiu J, Wang W, et al. (2023) Controllable preparation and thermal properties of SiC spherical high temperature shape-stable composite phase change materials based on gel-casting. J Alloys Compd 960: 170966. https://doi.org/10.1016/j.jallcom.2023.170966 doi: 10.1016/j.jallcom.2023.170966
![]() |
[181] |
Moens E, De Smit K, Marien Y, et al. (2020) Progress in reaction mechanisms and reactor technologies for thermochemical recycling of poly(methyl methacrylate). Polymers 12: 1667. https://doi.org/10.3390/polym12081667 doi: 10.3390/polym12081667
![]() |
[182] |
Mohammed MI, Khafagy RM, Hussien MSA, et al. (2022) Enhancing the structural, optical, electrical, properties and photocatalytic applications of ZnO/PMMA nanocomposite membranes: Towards multifunctional membranes. J Mater Sci Mater Electron 33: 1977–2002. https://doi.org/10.1007/s10854-021-07402-3 doi: 10.1007/s10854-021-07402-3
![]() |
[183] |
Gao X, Zheng X, Liu J, et al. (2019) Effects of carbon black content on the microstructure and properties of carbon/ceramic conductive composites. Mater Tehnol 53: 245–250. http://dx.doi.org/10.17222/mit.2018.078 doi: 10.17222/mit.2018.078
![]() |
[184] |
Hu L, Benitez R, Basu S, et al. (2012) Processing and characterization of porous Ti2AlC with controlled porosity and pore size. Acta Mater 60: 6266–6277. https://doi.org/10.1016/j.actamat.2012.07.052 doi: 10.1016/j.actamat.2012.07.052
![]() |
[185] |
Huang K, Wang L, Li M, et al. (2023) Mechanism of porous ceramic fabrication using second aluminum dross assisted by corn stalk as pore-forming agent. Environ Technol Inno 31: 103195. https://doi.org/10.1016/j.eti.2023.103195 doi: 10.1016/j.eti.2023.103195
![]() |
[186] |
Nikolopoulos N, Parker LA, Wickramasinghe A, et al. (2023) Addition of pore-forming agents and their effect on the pore architecture and catalytic behavior of shaped zeolite-based catalyst bodies. Chem Biomed Imaging 1: 40–48. http://dx.doi.org/10.1021/cbmi.2c00009 doi: 10.1021/cbmi.2c00009
![]() |
[187] |
Ulusoy U (2023) A review of particle shape effects on material properties for various engineering applications: From macro to nanoscale. Minerals 13: 91. https://doi.org/10.3390/min13010091 doi: 10.3390/min13010091
![]() |
[188] |
Wu Y, Chen F, Han W, et al. (2020) Synthesis and pyrolysis of non-oxide precursors for ZrC/SiC and HfC/SiC composite ceramics. Ceram Int 46: 22102–22107. https://doi.org/10.1016/j.ceramint.2020.05.260 doi: 10.1016/j.ceramint.2020.05.260
![]() |
[189] |
Chen Y, Wang N, Ola O, et al. (2021) Porous ceramics: Light in weight but heavy in energy and environment technologies. Mater Sci Eng R 143: 100589. https://doi.org/10.1016/j.mser.2020.100589 doi: 10.1016/j.mser.2020.100589
![]() |
[190] |
Alqutaibi AY, Ghulam O, Krsoum M, et al. (2022) Revolution of current dental zirconia: A comprehensive review. Molecules 27: 1699. https://doi.org/10.3390/molecules27051699 doi: 10.3390/molecules27051699
![]() |
[191] |
Kim JY, Yoon SH, Kim YH, et al. (2011) Thermal shock behavior of porous nozzles with various pore sizes for continuous casting process. J Korean Ceram Soc 48: 617–620. http://dx.doi.org/10.4191/kcers.2011.48.6.617 doi: 10.4191/kcers.2011.48.6.617
![]() |
[192] |
Liu R, Wang C (2013) Effects of mono-dispersed PMMA micro-balls as pore-forming agent on the properties of porous YSZ ceramics. J Eur Ceram Soc 33: 1859–1865. https://doi.org/10.1016/j.jeurceramsoc.2013.01.036 doi: 10.1016/j.jeurceramsoc.2013.01.036
![]() |
[193] |
Chen A, Li L, Ren W, et al. (2023) Influence of MgO-Al2O3 hollow sphere content on the microstructure and mechanical properties of calcium hexaluminate porous ceramics. J Asian Ceram Soc 12: 59–70. https://doi.org/10.1080/21870764.2023.2292874 doi: 10.1080/21870764.2023.2292874
![]() |
[194] |
Novais RM, Ascensão G, Seabra MP, et al. (2015) Lightweight dense/porous PCM-ceramic tiles for indoor temperature control. Energies Buildings 108: 205–214. https://doi.org/10.1016/j.enbuild.2015.09.019 doi: 10.1016/j.enbuild.2015.09.019
![]() |
[195] |
Coulon A, Cohen M, Pillet G (2024) Light-weighing traditional ceramics by porosity control and consequences on mechanical strength. Ceram Int 50: 6001–6008. https://doi.org/10.1016/j.ceramint.2023.11.269 doi: 10.1016/j.ceramint.2023.11.269
![]() |
[196] |
Lou J, He C, Shui A, et al. (2023) Enhanced sound absorption performance of porous ceramics with closed-pore structure. Ceram Int 49: 38103–38114. https://doi.org/10.1016/j.ceramint.2023.09.140 doi: 10.1016/j.ceramint.2023.09.140
![]() |
[197] |
Ma B, Zan W, Liu K, et al. (2023) Preparation and properties of porous MgO based ceramics from magnesite tailings and fused magnesia. Ceram Int 49: 19072–19082. https://doi.org/10.1016/j.ceramint.2023.03.034 doi: 10.1016/j.ceramint.2023.03.034
![]() |
[198] |
Gu J, Zou J, Liu J, et al. (2020) Sintering highly dense ultra-high temperature ceramics with suppressed grain growth. J Eur Ceram Soc 40: 1086–1092. https://doi.org/10.1016/j.jeurceramsoc.2019.11.056 doi: 10.1016/j.jeurceramsoc.2019.11.056
![]() |
[199] |
Qin Z, Xu X, Xu T, et al. (2022) High-strength thermal insulating porous mullite fiber-based ceramics. J Eur Ceram Soc 42: 7209–7218. https://doi.org/10.1016/j.jeurceramsoc.2022.08.050 doi: 10.1016/j.jeurceramsoc.2022.08.050
![]() |
[200] |
Son S, Kang S, Kim K (2021) Thermal properties of porous ceramics manufactured by direct foaming using silicon sludge and silica fume. J Asian Ceram Soc 9: 1364–1375. https://doi.org/10.1080/21870764.2021.1978651 doi: 10.1080/21870764.2021.1978651
![]() |
[201] |
Živcová Z, Gregorová E, Pabst W, et al. (2009) Thermal conductivity of porous alumina ceramics prepared using starch as a pore-forming agent. J Eur Ceram Soc 29: 347–353. https://doi.org/10.1016/j.jeurceramsoc.2008.06.018 doi: 10.1016/j.jeurceramsoc.2008.06.018
![]() |
[202] |
Wu Z, Sun L, Pan J, et al. (2018) Fiber reinforced highly porous γ-Y2Si2O7 ceramic fabricated by foam-gelcasting-freeze drying method. Scripta Mater 146: 331–334. https://doi.org/10.1016/j.scriptamat.2017.12.017 doi: 10.1016/j.scriptamat.2017.12.017
![]() |
[203] |
Malik N, Bulasara VK, Basu S (2020) Preparation of novel porous ceramic microfiltration membranes from fly ash, kaolin and dolomite mixtures. Ceram Int 46: 6889–6898. https://doi.org/10.1016/j.ceramint.2019.11.184 doi: 10.1016/j.ceramint.2019.11.184
![]() |
[204] |
Chen A, Li L, Wang C, et al. (2022) Novel porous ceramic with high strength and thermal performance using MA hollow spheres. Prog Nat Sci: Mater Int 32: 732–738. https://doi.org/10.1016/j.pnsc.2022.09.015 doi: 10.1016/j.pnsc.2022.09.015
![]() |
[205] |
Wu C, Li Z, Li Y, et al. (2023) Effect of starch on pore structure and thermal conductivity of diatomite-based porous ceramics. Ceram Int 49: 383–391. https://doi.org/10.1016/j.ceramint.2022.08.352 doi: 10.1016/j.ceramint.2022.08.352
![]() |
[206] |
Li M, Tang H, Li J, et al. (2024) Preparation of ZrP2O7-CePO4 composite porous ceramics and their excellent thermal insulation and wave-transmission performance for supersonic aircraft. J Eur Ceram Soc 44: 4232–4242. https://doi.org/10.1016/j.jeurceramsoc.2024.01.008 doi: 10.1016/j.jeurceramsoc.2024.01.008
![]() |
[207] |
Das D, Lucio MDS, Oh Y, et al. (2024) Tuning the electrical, thermal, and mechanical properties of porous SiC ceramics using metal carbides. J Eur Ceram Soc 44: 3020–3030. https://doi.org/10.1016/j.jeurceramsoc.2023.12.017 doi: 10.1016/j.jeurceramsoc.2023.12.017
![]() |
1. | Le Ren, Peng Yang, Rongchuan Sun, Shumei Yu, Gang Wang, Lining Sun, 2024, Semi-dense Map Reconstruction of Bronchus Based on Prior Feature Correlation, 979-8-3503-6479-8, 263, 10.1109/ISoIRS63136.2024.00058 | |
2. | Bowen Deng, 2024, 3144, 0094-243X, 030008, 10.1063/5.0215489 | |
3. | Hao Qu, 2024, 3194, 0094-243X, 020017, 10.1063/5.0222938 | |
4. | Hao Qu, 2024, 3194, 0094-243X, 020006, 10.1063/5.0222939 |
SIFT | SURF | ORB | Superpoint | Improving Superpoint | |
Extracting time /s | 1.282 | 0.182 | 0.125 | 0.103 | 0.101 |
Match time /s | 0.187 | 0.078 | 0.031 | 0.018 | 0.021 |
Extract point pairs/pairs | 334 | 121 | 268 | 352 | 349 |
Match point pairs/pairs | 334 | 121 | 268 | 263 | 349 |
False match point pair/pair | 79 | 25 | 31 | 13 | 15 |
Effective point proportion /% | 100.00 | 100.00 | 100.00 | 74.72 | 100.00 |
False match rate /% | 23.65 | 20.66 | 11.57 | 4.94 | 4.30 |
SIFT | SURF | ORB | Superpoint | Improving Superpoint | |
Extracting time /s | 1.282 | 0.182 | 0.125 | 0.103 | 0.101 |
Match time /s | 0.187 | 0.078 | 0.031 | 0.018 | 0.021 |
Extract point pairs/pairs | 334 | 121 | 268 | 352 | 349 |
Match point pairs/pairs | 334 | 121 | 268 | 263 | 349 |
False match point pair/pair | 79 | 25 | 31 | 13 | 15 |
Effective point proportion /% | 100.00 | 100.00 | 100.00 | 74.72 | 100.00 |
False match rate /% | 23.65 | 20.66 | 11.57 | 4.94 | 4.30 |