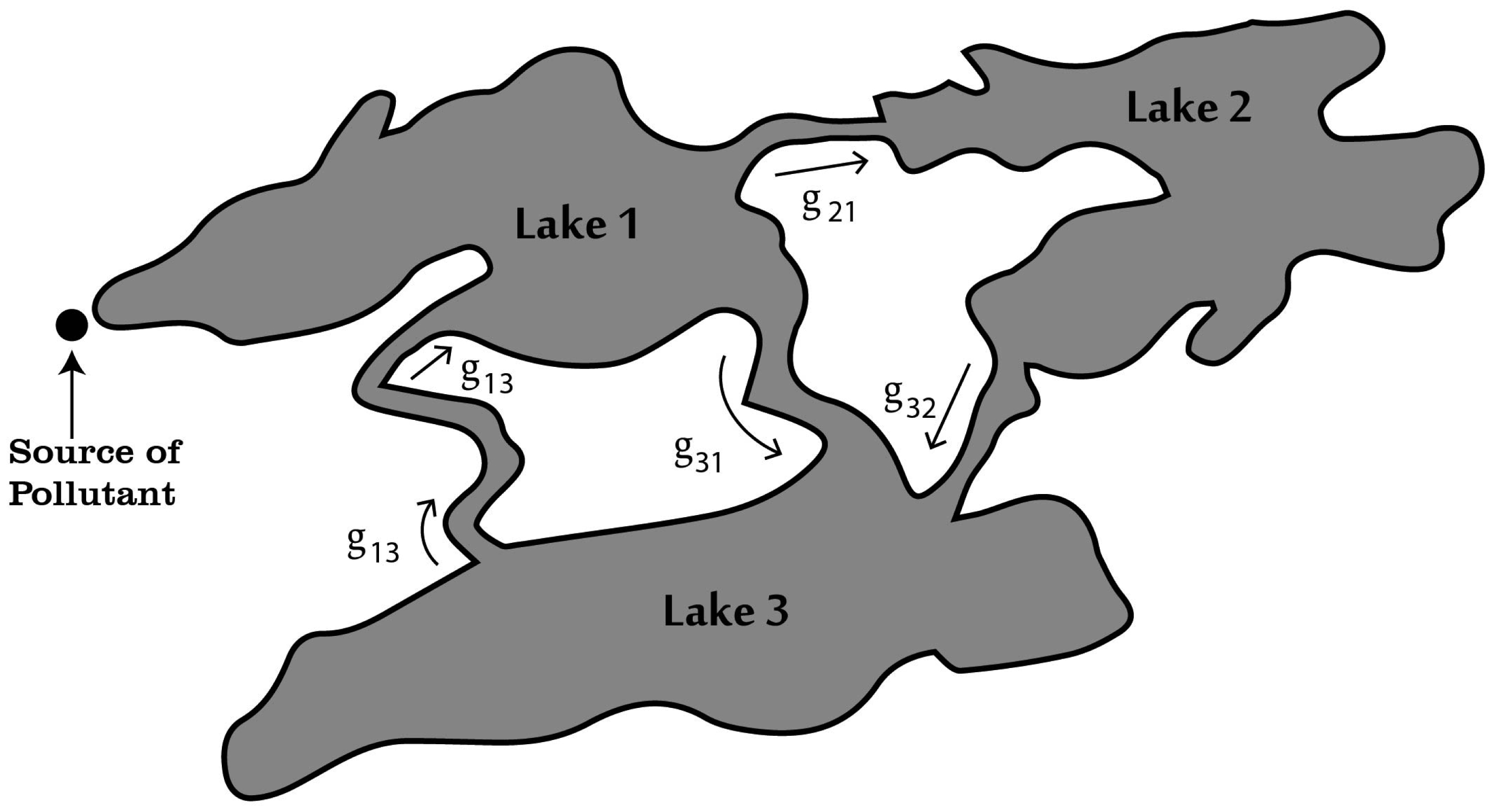
This article presents the results of research on the effects of electrolyte plasma hardening on the structure, phase composition, tribological, and mechanical properties of medium-carbon structural steel 45, which is widely used in the manufacturing of tools and machine parts. Hardening experiments were conducted using an electrolyte plasma hardening setup with electrolytes varying in sodium carbonate (Na2CO3) concentration in distilled water (15%, 20%, and 25%). With a consistent heating duration of 4 s during quenching, significant phase changes in the steel's microstructure were observed, enhancing hardness and wear resistance. The transformation of the initial structure of steel 45, which consists of ferrite and pearlite into martensite on the surface of the samples, led to an increase in microhardness up to 506–690 HV01. This value is 2.5–3.5 times higher compared to the untreated sample, and the thickness of the hardened layer reached up to 3.2 mm. Additionally, wear volume measurements showed that after electrolyte plasma hardening, the wear resistance of the samples increased by 1.3–1.5 times (2.01 × 10−4, 2.26 × 10−4 m3). The obtained results on the changes in microstructure and mechano-tribological properties of steel 45 confirm the potential of electrolyte plasma hardening technology for improving operational characteristics and extending the service life of heavily loaded and critical machine parts.
Citation: Bauyrzhan Rakhadilov, Rinat Kussainov, Aisulu Kalitova, Zarina Satbayeva, Aibek Shynarbek. The impact of technological parameters of electrolytic-plasma treatment on the changes in the mechano-tribological properties of steel 45[J]. AIMS Materials Science, 2024, 11(4): 666-683. doi: 10.3934/matersci.2024034
[1] | Mati ur Rahman, Mehmet Yavuz, Muhammad Arfan, Adnan Sami . Theoretical and numerical investigation of a modified ABC fractional operator for the spread of polio under the effect of vaccination. AIMS Biophysics, 2024, 11(1): 97-120. doi: 10.3934/biophy.2024007 |
[2] | Shaimaa A. M. Abdelmohsen, D. Sh. Mohamed, Haifa A. Alyousef, M. R. Gorji, Amr M. S. Mahdy . Mathematical modeling for solving fractional model cancer bosom malignant growth. AIMS Biophysics, 2023, 10(3): 263-280. doi: 10.3934/biophy.2023018 |
[3] | Mohammed Alabedalhadi, Mohammed Shqair, Ibrahim Saleh . Analysis and analytical simulation for a biophysical fractional diffusive cancer model with virotherapy using the Caputo operator. AIMS Biophysics, 2023, 10(4): 503-522. doi: 10.3934/biophy.2023028 |
[4] | Ken Takahashi, Takayuki Oda, Keiji Naruse . Coarse-grained molecular dynamics simulations of biomolecules. AIMS Biophysics, 2014, 1(1): 1-15. doi: 10.3934/biophy.2014.1.1 |
[5] | Nor Afiqah Mohd Aris, Siti Suhana Jamaian . Dynamical analysis of fractional-order chemostat model. AIMS Biophysics, 2021, 8(2): 182-197. doi: 10.3934/biophy.2021014 |
[6] | Alexander Galashev . Computer implementation of the method for electrolytic production of thin films for biomedical applications: short review. AIMS Biophysics, 2024, 11(1): 39-65. doi: 10.3934/biophy.2024004 |
[7] | Soumaya Eltifi-Ghanmi, Samiha Amara, Bessem Mkaouer . Kinetic and kinematic analysis of three kicks in Sanda Wushu. AIMS Biophysics, 2025, 12(2): 174-196. doi: 10.3934/biophy.2025011 |
[8] | Mehmet Yavuz, Fuat Usta . Importance of modelling and simulation in biophysical applications. AIMS Biophysics, 2023, 10(3): 258-262. doi: 10.3934/biophy.2023017 |
[9] | Carlo Bianca . Mathematical and computational modeling of biological systems: advances and perspectives. AIMS Biophysics, 2021, 8(4): 318-321. doi: 10.3934/biophy.2021025 |
[10] | Julia C. Arciero, Paola Causin, Francesca Malgaroli . Mathematical methods for modeling the microcirculation. AIMS Biophysics, 2017, 4(3): 362-399. doi: 10.3934/biophy.2017.3.362 |
This article presents the results of research on the effects of electrolyte plasma hardening on the structure, phase composition, tribological, and mechanical properties of medium-carbon structural steel 45, which is widely used in the manufacturing of tools and machine parts. Hardening experiments were conducted using an electrolyte plasma hardening setup with electrolytes varying in sodium carbonate (Na2CO3) concentration in distilled water (15%, 20%, and 25%). With a consistent heating duration of 4 s during quenching, significant phase changes in the steel's microstructure were observed, enhancing hardness and wear resistance. The transformation of the initial structure of steel 45, which consists of ferrite and pearlite into martensite on the surface of the samples, led to an increase in microhardness up to 506–690 HV01. This value is 2.5–3.5 times higher compared to the untreated sample, and the thickness of the hardened layer reached up to 3.2 mm. Additionally, wear volume measurements showed that after electrolyte plasma hardening, the wear resistance of the samples increased by 1.3–1.5 times (2.01 × 10−4, 2.26 × 10−4 m3). The obtained results on the changes in microstructure and mechano-tribological properties of steel 45 confirm the potential of electrolyte plasma hardening technology for improving operational characteristics and extending the service life of heavily loaded and critical machine parts.
In line with the Environmental Health Association of America's committee definition, the environment encompasses the habitats where humans reside, work, and engage in recreational activities. It includes the air we breathe, the food we consume, the water we drink, and the shelter we seek for protection against the elements. Additionally, it comprises harmful pollutants and other environmental factors that significantly impact our well-being and overall health. Our survival depends on access to nutritious food, clean air, and safe drinking water, which necessitates the promotion of a healthy atmosphere. The World Health Organization (WHO) emphasizes the importance of maintaining a clean environment that adheres to health standards. Regrettably, our water supply has become increasingly contaminated, with numerous pollutants affecting the quality of our drinking water sources. Thus, it is imperative that we develop a conscientious awareness of our surroundings. Environmental science encompasses scientific methodologies, economic considerations, and political interventions. Moreover, toxic substances introduced into lakes, streams, rivers, seas, and other bodies of water can dissolve, remain suspended, or settle at the bottom. Consequently, water contamination ensues, leading to a decline in groundwater quality and the deterioration of marine habitats [1].
Pollution can also seep into the groundwater and alter the sediment composition. Water pollution has various causes, with sewage and industrial waste being the most significant contributors that enter rivers. In many developed countries, the resources allocated for waste management are insufficient [2]. Currently, only around 10% of the generated wastewater is properly treated, while the rest is discharged and deposited into our water bodies. Consequently, impurities infiltrate groundwater, tributaries, and other water sources. The water that ultimately reaches our homes is often highly contaminated, carrying viruses that can harm microorganisms. Another major source of water pollution is agricultural runoff, which involves the drainage of water from fields containing pesticides and fertilizers. Domestic sewage, also known as sanitary sewage, refers to wastewater discharged from households. This type of water contains a wide array of dissolved and suspended contaminants.
Mathematical frameworks play a crucial role in predicting and addressing social issues, and they have been increasingly utilized in recent decades to mitigate the impact of these issues. By applying mathematical models, we can effectively control the spread of real-world problems. As many global challenges exhibit quasi-linear characteristics, relying solely on linear models can often lead to idealistic and unrealistic outcomes. Therefore, non-linear mathematical models provide a more accurate depiction of real-world issues. In the context of modeling lake contamination, a collocation approach has been proposed, which utilizes Bessel polynomials and collocation points to generate an updated matrix problem [3]. This approach allows for a more comprehensive understanding of the contamination dynamics within a lake system. Additionally, the homotopy perturbation approach has been employed to offer approximate and analytical solutions for nonlinear ordinary differential equation systems, such as those encountered in modeling lake contamination [4]. Furthermore, the differential transform method (DTM) has been utilized to analyze pollution models involving interconnected systems of three lakes connected by waterways [5]. These mathematical methods enhance our ability to study and address the complex dynamics of pollution in various environmental systems.
A fractional differential equation system has been investigated by Haq EU [6]. He designed the system to simulate the pollution of a group of lakes and assess the results using other well-known analytical approaches, such as iterative variation and Adomian decomposition. The Laplace Adomian decomposition method is widely applied to solve many real-life problems (see [7]–[9]). Several researchers have used the technique of LADM to investigate different types of problems. For example, in [10], the authors examined the free vibrations of a non-uniform Bernoulli beam using LADM. In [11], a fractional-order sterile insect technology model was studied with the help of LADM. Other studies include the investigation of MHD flow of incompressible fluid between two parallel plates [12], and the study of the effect of a magnetic field on the heat transfer of carbon nanotubes [13]. Different approaches have been used for disease models, studying them with various fractional operator techniques [14]–[23].
Aguirre and Tully [24] employed simple mixture problem methodologies to develop a differential equation that characterizes the pollution concentration in a lake. Prakasha and Veeresha [25] explored three alternative scenarios of the model and established an approximate analytical solution for the system of three fractional differential equations using the q-homotopy analysis transform technique (q-HATM). The results obtained demonstrated the high effectiveness and systematic nature of the proposed strategy. Khalid and Sultana [26] utilized the perturbation-iteration approach to estimate the solution of three input models: periodic, linear step, and exponentially decaying. As a reference, the analytical simulation of the lake system problem was conducted using the fourth-order Runge-Kutta technique (RK4). Biazar and Farrokhi [27] employed compartmental modeling to predict the contamination of a system of lakes through a set of mathematically-researched equations. Bazar and Shahbala [28] utilized the variational iteration method (VIM), and the results demonstrated that the variational iteration approach was easier to implement compared to the Adomian decomposition method for pollution monitoring in lakes. Three distinct types of input models were considered: sinusoidal, impulse, and step. Furthermore, Toufik and Atangana's novel numerical technique was applied [29] to examine the updated model of the contaminated lake system.
Fractional calculus, despite its name, deals with integrals and derivatives of any positive real order and can be considered a branch of mathematical modeling. It focuses on integrodifferential operators and equations with convolution-type integrals that involve weakly singular kernels of power-law form. It is closely related to the theory of pseudo-differential operators. In recent years, fractional calculus has garnered significant attention from researchers, and various aspects of this subject are being explored in research [30], [31]. This is because fractional derivatives serve as an important tool for describing the dynamic behavior of diverse physical systems [32]–[34]. The distinct characteristic of these differential operators lies in their non-local nature, which is absent in integer-order differential operators [35]. In fact, fractional order models are more accurate and practical than classical integer order models, and techniques such as the Legendre operational matrix can be extended to incorporate fractional calculus [36], [37]. The application of fractional differential equations in applied sciences is another area of interest [38], [39].
Fractional order derivatives offer increased flexibility in modeling various biomaterials and systems [40]. They provide powerful tools for characterizing the dynamic behavior of these systems. There are different types of fractional derivatives, such as Riemann and Liouville, and Caputo operators, which are commonly used in practice. Caputo [41] introduced a fractional derivative that allows for the incorporation of conventional initial and boundary conditions relevant to real-world problems. While these fractional derivatives offer improved accuracy in describing real phenomena compared to integer-order derivatives, their kernel functions may result in singularities that lead to computational challenges. To explore fractional mathematical models beyond the traditional Caputo derivative, various methodologies, including iterative and numerical methods, have been employed [42]–[44]. In this study, we focus on a system of three equations that describes lake contamination. The model represents the contamination of a three-lake system [27], as illustrated in Figure 1.
The arrows in the figure indicate the direction of flow in the channels or pipes. In this system, a contaminant is introduced into the first lake through a factory, and the rate of entrance of the pollutant into the lake per unit of time is represented by the function p(t). The function p(t) can be constant or vary over time. The goal is to determine the level of pollution in each lake at any given time. At time t ≥ 0, the contamination level ci(t) in Lake i is proportional to the volume of water vi and the concentration of pollutant yi(t) in the following manner:
In the lake system, it is assumed that each lake is initially free of any contaminants, so the concentration of pollutant in each lake at time t = 0 is given by yi(0) = 0 for i = 1, 2, 3. To simulate the dynamic behavior of the lake system, a constant gji is used to represent the flow rate from lake i to lake j. The flux of pollutant flowing from lake i into lake j at any time t is denoted by rji(t) and is defined as follows:
Thus, rji(t) represents the proportion at which the contamination level in lake i flows into lake j at time t. It is important to note this relationship.
Rate of change of pollutant = Input rate - Output rate.
Applying this principle to each lake, we obtain the following system of differential equations:
It is apparent from this that the incoming and outgoing flow rates in each lake are constant, and as a result, the water volume in each lake remains fixed. Therefore, we can establish the following conditions:
To evaluate the performance of the proposed model, we consider specific predicted values as listed in [27], which can be expressed as follows:
In this study, to obtain a more accurate qualitative and numerical iterative analysis of the proposed model, we consider the system (1.1) in terms of the Caputo fractional order differential operator. The system can be expressed as follows:
where α denotes the fractional order.
The objective of this study is to analyze a system of fractional differential equations that describe lake pollution and provide meaningful insights through a mathematical model that can explain real-world scenarios using a simple and efficient approach. It is important to highlight that the investigated model heavily relies on time and its history, which can be systematically incorporated and represented using the newly developed fractional operator. To obtain the solution of the model, we utilize the Laplace transform in conjunction with the Adomian decomposition method and the Homotopy perturbation method. These techniques enable us to obtain an approximate solution for the considered model. Additionally, we compare the results obtained from both techniques, demonstrating their identical nature. Furthermore, we employ MATLAB to facilitate the numerical solutions and depict the pollution levels in each lake graphically, considering arbitrary fractional orders. This visual representation aids in understanding the behavior of the lake system under different scenarios.
The structure of this paper is organized as follows: Section 2 provides fundamental results and definitions related to the topic. In Section 3, the general solutions of the suggested model are obtained using the Laplace Adomian decomposition technique. This section focuses on the qualitative analysis of the model. Section 4 presents the general solutions of the considered model using the Homotopy perturbation technique. This section discusses the application of the Homotopy perturbation method for obtaining the solutions. In Section 5, a graphical comparison of the numerical solutions obtained from both the Laplace Adomian decomposition technique and the Homotopy perturbation technique is presented. The numerical simulation results are briefly discussed in this section. Finally, in Section 6, the concluding remarks of the study are provided.
In this section, some essential preliminaries and fractional calculus results are presented in line with [45], [46].
Definition 2.1. For α > 0 with
such that the integral part on the right exists and n = [α] + 1, and the symbol Γ denotes the Gamma function which is described as
Definition 2.2. The Laplace transform of g(t) in the general framework of Caputo definition is described as follows:
Definition 2.3. The Homotopy perturbation method (HPM) is a semi-analytical technique used to solve linear and nonlinear ordinary and partial differential equations, as well as systems of equations. It is also applicable to systems consisting of both linear and nonlinear differential equations. One notable advantage of using the HPM over decomposition methods is that it can handle nonlinear problems without requiring the use of Adomian polynomials. The HPM was first proposed by the Chinese mathematician He
where L is used for the linear part, N for the nonlinear part, l ∈ Ω, Ω is a topological space and p ∈ [0,1] is the embedding parameter. Furthermore, u0 is an initial approximation that satisfies the boundary conditions.
In this section, we will discuss the general technique of the Laplace Adomian decomposition method (LADM) to construct the solution for the considered model (1.2), along with the initial conditions. We will also demonstrate how to integrate the LADM with the Caputo differential operator.
with subject to the initial conditions:
Now, taking the Laplace transform of (3.1) in the Caputo sense, one may get
using the initial conditions yields
Assuming the solution for y1(t), y2(t) and y3(t) in an infinite series is given below:
using the above series in (3.3), and comparing like terms on both sides, one can get
Further, utilizing the inverse Laplace transform to equation (3.4), we have
Additionally, the remaining terms can be derived in a similar fashion. The unknown values in the aforementioned equations are listed below:
We will now apply the Homotopy Perturbation Method (HPM) to derive the general solution of Model (1.2) as:
By substituting q = 0 into equation (4.1), we obtain the following system of fractional differential equations:
The solution to the above equation is straightforward. Next, setting q = 1 in equation (4.1) results in a similar model to equation (1.2). We assume the solution takes the form of an infinite series as:
Furthermore, the original system can be obtained by substituting q = 1 into equation (4.1). By substituting equation (4.3) into equation (4.1) and comparing the terms with respect to the powers of q, we obtain:
Similarly,
The approximate series solution is thus acquired. In the next section, we will do simulation for the aforementioned methods.
In this section, we conduct numerical simulations to complement the analytical findings of our proposed model. The simulations involve qualitative point analysis and consider the parameters from a biological feasibility perspective. By using the parametric values, we determine the following terms of the proposed model:
Furthermore, the solutions to the first few terms are given as:
Now, evaluating (5.2) for α = 0.97, one get
Similarly, for α = 0.98, the approximations are:
And for α = 0.99, one can obtain the approximate solutions are:
Furthermore, we have considered three different types of input functions to represent the duration of the contaminant in each lake. These input functions include periodic, exponentially decaying, and linear inputs.
Case 1: Periodic Input Model: In this scenario, the model is evaluated when pollution is periodically introduced into Lake 1. We have chosen the input function
Based on Figure 2, it is evident that the pollution concentration in the lakes increases over time. Moreover, for smaller fractional orders, the increase is more rapid. It is worth noting that the timescale in all the figures is measured in days. In the next step, we will provide a comparison of the lakes using both the Laplace Adomian decomposition method (LADM) and the Homotopy perturbation method (HPM). Specifically, we will focus on the first few terms of the simulations, which will demonstrate the similarities between the two methods.
Case 2: Exponentially Decaying Input Model: In this situation, the model is examined when pollutants with huge dumping. We chose
Figure 6 illustrates that the pollution concentration in the lakes initially increases, then decreases, and eventually stabilizes at a certain level over time. Similarly, we will proceed with the comparison of the lakes using both the Laplace Adomian decomposition method (LADM) and the Homotopy perturbation method (HPM). By examining the first few terms of the simulations, we will demonstrate the similarities between the two methods, thus validating their simulation results.
Case 3: Linear Input Model: In this scenario, the model considers the case where Lake 1 is initially contaminated with a pollutant with a linear proportion. We have chosen the input function p(t) = a, t, where a = 100. For this linear input, the pollutant starts flowing into the lake at time zero, and the amount of pollutant before time zero is assumed to be zero. In the case of a step input, the key characteristic is that the input abruptly increases at time zero and remains relatively constant thereafter. As an example, consider a manufacturing plant that starts its operations at time zero and immediately begins discharging untreated sewage at a consistent rate and intensity. This linear input represents the continuous influx of pollutants into the lake.
Figure 9 shows the concentration of pollution in lakes rising rapidly with passing time. Next, the comparison of these lakes using both proposed methods of LADM and HPM for the first few terms that demonstrate simulation similarities are presented.
In this research, we have analyzed the dynamic behavior of a lake pollution model using the Caputo differential operator and the utilities of fractional calculus. The model has been numerically explored using the Laplace transform with the Adomian decomposition method (LADM) and the Homotopy perturbation method (HPM). The numerical results obtained from both methods are highly similar and provide strong confirmation for the considered model in arbitrary order derivatives. The outcomes are influenced by various parameters used in the model, and both methods converge effectively for solving fractional-order differential equations. The graphical results, generated using MATLAB, demonstrate the dependency of the model on the fractional operator and the parameters utilized in the proposed methods. The present study highlights the significance of the fractional concept in understanding and analyzing the suggested lakes pollution model, which is highly dependent on time and its history. It also provides a foundation for future research in this field. For instance, the mathematical model can be further enhanced by considering various dynamic structures and investigating different types of derivatives. The advantages of the LADM and HPM methods, including simplicity, accuracy, flexibility, and efficiency, make them valuable tools for analyzing nonlinear problems in various scientific and engineering disciplines. These methods offer promising avenues for further exploration and application in fractional calculus and related fields.
[1] | Sharaya O, Vodolazskaya N (2019) Technological aspects of modification of surface layer of agricultural machines parts. Inn Agric Compl Probl Perspect 3: 82–92 (in Russian). Available from: https://www.bsaa.edu.ru/InfResource/library/Journal3(23)2019.pdf. |
[2] | Aulov V, Rozhkov Y (2016) On the issue of combining electrospark and thermodiffusion methods for hardening the machine parts surfaces in the agribusiness. Mach Equip Rural Area 2: 28–32 (in Russian). Available from: https://doi.org/10.33267/2072-9642-2022-2-28-32. |
[3] | Zobnev V, Markov A, Ivanov S, et al. (2014) Wear resistance of multicomponent diffusion boride coatings on working organs of agricultural machines. Mater Sci Mach Build 1: 435–439 (in Russian). Available from: https://elibrary.ru/download/elibrary_22610860_80996072.pdf. |
[4] |
Martínez-Vázquez J, Rodríguez-Ortiz G, Hortelano-Capetillo J, et al. (2021) Effect of induction heating on Vickers and Knoop hardness of 1045 steel heat treated. J Mech Eng 5: 8–15. https://doi.org/10.35429/JME.2021.15.5.8.15 doi: 10.35429/JME.2021.15.5.8.15
![]() |
[5] |
Dudnikov I (2011) Ensure the safety properties of parts that define security of agricultural machinery. Tech Audit Prod Res 1: 33–36 (in Russian). https://doi.org/10.15587/2312-8372.2011.4853 doi: 10.15587/2312-8372.2011.4853
![]() |
[6] |
Morshed-Behbahani K, Farhat Z, Nasiri A (2024) Effect of surface nanocrystallization on wear behavior of steels: A review. Materials 17: 1618. https://doi.org/10.3390/ma17071618 doi: 10.3390/ma17071618
![]() |
[7] |
Pour-Ali S, Kiani-Rashid A, Babakhani A, et al. (2018) Severe shot peening of AISI 321 with 1000% and 1300% coverages: A comparative study on the surface nanocrystallization, phase transformation, sub-surface microcracks, and microhardness. Int J Mater Res 109: 451–459. https://doi.org/10.3139/146.111622 doi: 10.3139/146.111622
![]() |
[8] |
Roy R, Ghosh S, Kaisar T, et al. (2022) Multi-response optimization of surface grinding process parameters of AISI 4140 alloy steel using response surface methodology and desirability function under dry and wet conditions. Coatings 12: 104. https://doi.org/10.3390/coatings12010104 doi: 10.3390/coatings12010104
![]() |
[9] | Stepanova T (2009) Technologies of Surface Hardening of Machine Parts, Ivanovo: Ivanovo State Chemical-Technological University, 64p (in Russian). Available from: https://www.isuct.ru/sites/default/files/department/ightu/ktmio/08.pdf. |
[10] | Ostromenskiy P, Aksenov V, Korotaev B, et al. (2001) Prospects for the use of high-energy technologies to increase the lateral wear resistance of rails. Curr Probl Transp Asian Part Russ 2001: 92–98 (in Russian). Available from: https://is.gd/dUCNDS. |
[11] | Maisuradze M (2022) Induction and Laser Thermal Treatment of Steel Products: A Textbook, Yekaterinburg: Ural University Publishing, 96p (in Russian). Available from: https://elar.urfu.ru/bitstream/10995/117127/1/978-5-7996-3544-2_2022.pdf. |
[12] |
Khisamutdinov R, Zvezdin V, Israfilov I, et al. (2016) Study of processes of steels surfaces modification with highly concentrated energy flows. J Phys Conf Ser 669: 012024. https://doi.org/10.1088/1742-6596/669/1/012024 doi: 10.1088/1742-6596/669/1/012024
![]() |
[13] | Barmin A, Rizakhanov R, Rudstein R (2012) Optimization of quenching regimes for carbon steels by electron beam treatment. Proc Interuniv Sci Sch Young Spec 1: 62–67 (in Russian). Available from: http://nuclphys.sinp.msu.ru/school/s12/12_15.pdf. |
[14] | Belinin D, Shchitsyn Y (2012) Features of structurization at plasma surface hardening on big depth of products from 40Cr13. Proc Samara Sci Cent Russ Acad Sci 4: 1200–1205 (in Russian). Available from: https://elar.urfu.ru/bitstream/10995/30926/1/sid_2014_04.pdf. |
[15] | Belinin D, Verkhorubov V, Kuchev P, et al. (2011) Plasma surface hardening of hard loading constructions made of steel 40Kh13. Bulletin Pnrpu 2: 12–18 (in Russian). Available from: https://cyberleninka.ru/article/n/plazmennaya-zakalka-tyazhelonagruzhennyh-detaley-iz-stali-40h13. |
[16] | Sidorov S (1998) Technical level and resource of working organs of agricultural machinery. Tract Agric Mach 3: 29 (in Russian). Available from: https://rusneb.ru/catalog/000200_000018_RU_NLR_PER_B_2381825_1998_3/. |
[17] | Kravchenko N (2013) Plasma Methods of Hardening and Restoration of Working Bodies Road-Building and Soil-Cultivating Machines, Moscow: Eco-Press, 328 p (in Russian). Available from: https://expo-books.ru/category/book?id = 12005. |
[18] | Kanayev A (2015) Modernization of the surface layer structure of structural steel. Herald Scin Seifullin Kaz Agro Tehn Univ 3: 78–86 (in Russian). Available from: https://bulletinofscience.kazatu.edu.kz/index.php/bulletinofscience/article/view/701. |
[19] |
Korotkov V (2011) Wear resistance of plasma-hardened materials. J Frict Wear 32: 17–22. https://doi.org/10.3103/S1068366611010077 doi: 10.3103/S1068366611010077
![]() |
[20] |
Jumbad V, Chel A, Verma U (2020) Application of electrolytic plasma process in surface improvement of metals: A review. Letters Appl NanoBioSci 9: 1249–1262. https://doi.org/10.33263/lianbs93.12491262 doi: 10.33263/lianbs93.12491262
![]() |
[21] |
Gupta P, Tenhundfeld G, Daigle E (2007) Electrolytic plasma technology: Science and engineering—An overview. Surf Coat Tech 201: 8746–8760. https://doi.org/10.1016/j.surfcoat.2006.11.023 doi: 10.1016/j.surfcoat.2006.11.023
![]() |
[22] |
Rakhadilov B, Bayatanova L, Kurbanbekov S, et al. (2023) Investigation on the effect of technological parameters of electrolyte-plasma cementation method on phase structure and mechanical properties of structural steel 20X. AIMS Mater Sci 10: 934–947. https://doi.org/10.3934/matersci.2023050 doi: 10.3934/matersci.2023050
![]() |
[23] |
Meletis E, Nie X, Wang F (2002) Electrolytic plasma processing for cleaning and metal-coating of steel surfaces. Surf Coat Tech 150: 246–256. https://doi.org/10.1016/S0257-8972(01)01521-3 doi: 10.1016/S0257-8972(01)01521-3
![]() |
[24] | Belkin P (2013) Electrolytic-plasma modification of metals and alloys. Bull Kostroma State Univ 5: 5–11 (in Russian). Available from: https://cyberleninka.ru/article/n/elektrolitno-plazmennaya-modifikatsiya-metallov-i-splavov-1. |
[25] |
Jiang Y, Bao Y, Wang M (2017) Kinetic analysis of additive on plasma electrolytic boriding. Coatings 7: 61. https://doi.org/10.3390/coatings7050061 doi: 10.3390/coatings7050061
![]() |
[26] |
Belkin V, Belkin P, Krit B, et al. (2019) Increasing wear resistance of low-carbon steel by anodic plasma-electrolytic nitroboriding. J Mater Eng Perform 29: 564–572. https://doi.org/10.1007/s11665-019-04521-1 doi: 10.1007/s11665-019-04521-1
![]() |
[27] |
Taheri P, Dehghanian C, Aliofkhazraei M, et al. (2007) Nanocrystalline structure produced by complex surface treatments: plasma electrolytic nitrocarburizing, boronitriding, borocarburizing, and borocarbonitriding. Plasma Process Polym 4: 721–727. https://doi.org/10.1002/ppap.200731805 doi: 10.1002/ppap.200731805
![]() |
[28] |
Skakov M, Rakhadilov B, Sheffler M (2013) Influence of electrolyte plasma treatment on structure, phase composition and microhardness of steel Р6М5. Key Eng Mater 531–532: 627–631. https://doi.org/10.4028/www.scientific.net/KEM.531-532.627 doi: 10.4028/www.scientific.net/KEM.531-532.627
![]() |
[29] |
Luk S, Leung T, Miu W (1999) A study of the effect of average preset voltage on effective case depth during electrolytic surface-hardening. Mater Charact 42: 65–71. https://doi.org/10.1016/S1044-5803(98)00044-8 doi: 10.1016/S1044-5803(98)00044-8
![]() |
[30] |
Tarakci M, Korkmaz K, Gencer Y (2005) Plasma electrolytic surface carburizing and hardening of pure iron. Surf Coat Tech 199: 205–212. https://doi.org/10.1016/j.surfcoat.2005.02.117 doi: 10.1016/j.surfcoat.2005.02.117
![]() |
[31] | Satbayeva Z (2022) Structure Formation in Alloyed Steels During Electrolytic-Plasma Surface Hardening, Oskemen: Sarsen Amanzholov East Kazakhstan University, 160p (in Russian). Available from: https://nabrk.kz/ru/e-catalog?catalog=4&language=rus&page=8&sphere=3&topic=0&publication_type=13. |
[32] | Suminov I (2011) Plasma Electrolytic Modification of the Surface of Metals and Alloys, Moscow: Tekhnosfera, 464 p (in Russian). Available from: https://f.eruditor.link/file/2686301/. |
[33] |
Cenk Kumruoğlu L, Özel A (2010) Surface modification of AISI 4140 steel using electrolytic plasma thermocyclic treatment. Mater Manuf Process 25: 923–931. https://doi.org/10.1080/10426911003720839 doi: 10.1080/10426911003720839
![]() |
[34] |
Sagdoldina Z, Zhurerova L, Tyurin Y, et al. (2022) Modification of the surface of 40Kh steel by electrolytic plasma hardening. Metals 12: 2071. https://doi.org/10.3390/met12122071 doi: 10.3390/met12122071
![]() |
[35] | Smirnov M (1999) Fundamentals of Heat Treatment of Steel, Yekaterinburg: Ural Branch of the Russian Academy of Sciences, 494p (in Russian). Available from: http://www.materialscience.ru/shared_folder/matved/books/Smirnov_Osnovy_TO_stali.djvu. |
[36] | Kartonova L (2020) Theory and Technology of Heat Treatment, Vladimir: Publishing house of Vladimir State University, 128p (in Russian). Available from: https://dspace.www1.vlsu.ru/bitstream/123456789/8725/1/02082.pdf. |
[37] |
Rasouli D, Khameneh Asl S, Akbarzadeh A, et al. (2008) Effect of cooling rate on the microstructure and mechanical properties of microalloyed forging steel. J Mater Process Technol 206: 92–98. https://doi.org/10.1016/j.jmatprotec.2007.12.006 doi: 10.1016/j.jmatprotec.2007.12.006
![]() |
[38] |
Sunardi S, Lusiani R, Listijorini E, et al. (2021) The effect of airflow speed as cooling media in the hardening process to the hardness, corrosion rate and fatigue life of medium carbon steel. Mater Sci Forum 1045: 40–49. https://doi.org/10.4028/www.scientific.net/msf.1045.40 doi: 10.4028/www.scientific.net/msf.1045.40
![]() |
[39] |
Jo H, Kang M, Park G, et al. (2020) Effects of cooling rate during quenching and tempering conditions on microstructures and mechanical properties of carbon steel flange. Materials 13: 4186. https://doi.org/10.3390/ma13184186 doi: 10.3390/ma13184186
![]() |
[40] |
Basori I, Pratiwi W, Dwiyati S (2019) Effect of salt quenching on the microstructures and mechanical properties of AISI 1045 steel. J Phys Conf Ser 5: 055102. https://doi.org/10.1088/1742-6596/1402/5/055102 doi: 10.1088/1742-6596/1402/5/055102
![]() |
[41] | Pérez R, Llano M, Ravagli R, et al. (2018) Effect of machining fluid like quenching media on the friction and wear behavior of AISI 1045 steel. Int J Mech Eng Technol 9: 146–154. Available from: https://iaeme.com/MasterAdmin/Journal_uploads/IJMET/VOLUME_9_ISSUE_7/IJMET_09_07_017.pdf. |
[42] |
Vieira E, Biehl L, Medeiros J, et al. (2021) Evaluation of the characteristics of an AISI 1045 steel quenched in different concentration of polymer solutions of polyvinylpyrrolidone. Sci Rep 11: 1313. https://doi.org/10.1038/s41598-020-79060-0 doi: 10.1038/s41598-020-79060-0
![]() |
[43] |
Dayanç A, Karaca B, Kumruoğlu L (2017) The cathodic electrolytic plasma hardening of steel and cast iron based automotive camshafts. Acta Phys Pol A 131: 374–378. https://doi.org/10.12693/APhysPolA.131.374 doi: 10.12693/APhysPolA.131.374
![]() |
[44] |
Belkin P, Kusmanov S (2016) Plasma electrolytic hardening of steels: review. Surf Engin Appl Electrochem 52: 531–546. https://doi.org/10.3103/S106837551606003X doi: 10.3103/S106837551606003X
![]() |
[45] |
Bayati M, Molaei R, Janghorban K (2011) Surface alloying of carbon steels from electrolytic plasma. Met Sci Heat Treat 53: 91–94. https://doi.org/10.1007/s11041-011-9347-5 doi: 10.1007/s11041-011-9347-5
![]() |
[46] | Rakhadilov B, Satbayeva Z, Bayatanova L, et al. (2019) Influence of electrolyte-plasma surface hardening on the structure and properties of steel 40KhN. J Phys Conf Ser 1393: 012119. https://doi.org/101088/1742-6596/1393/1/012119 |
[47] |
Ayday A, Durman M (2013) Surface hardening of ductile cast iron by electrolytic plasma technology. Acta Phys Pol A 123: 291–293. https://doi.org/10.12693/APhysPolA.123.291 doi: 10.12693/APhysPolA.123.291
![]() |
[48] | Gorelik S (2002) X-ray and Electron-optical Analysis, 4 Eds., Moscow: Publishing house MISIS, 360 p (in Russian). Available from: https://www.geokniga.org/bookfiles/geokniga-rentgenograficheskiy-analiz.pdf. |
[49] |
Rastkar A, Shokri B (2012) Surface modification and wear test of carbon steel by plasma electrolytic nitrocarburizing. Surf Interface Anal 44: 342–351. https://doi.org/10.1002/sia.3808 doi: 10.1002/sia.3808
![]() |
[50] |
Zhang L, Jin Y, Wang X, et al. (2019) Surface alloys of 0.45 C carbon steel produced by high current pulsed electron beam. High Temp Mater Process 38: 444–451. https://doi.org/10.1515/htmp-2018-0065 doi: 10.1515/htmp-2018-0065
![]() |
[51] |
Zheng B, Huang Z, Xing J, et al. (2016) Three-body abrasive behavior of cementite–iron composite with different cementite volume fractions. Tribol Lett 62: 1–11. https://doi.org/10.1007/s11249-016-0683-x doi: 10.1007/s11249-016-0683-x
![]() |
[52] |
Yaghmazadeh M, Dehghanian C (2009) Surface hardening of AISI H13 steel using pulsed plasma electrolytic carburizing (PPEC). Plasma Processes Polym 6: S168–S172. https://doi.org/10.1002/ppap.200930410 doi: 10.1002/ppap.200930410
![]() |
[53] |
Kurbanbekov S, Skakov M, Baklanov V, et al. (2017) Changes in mechanical properties and structure of electrolytic plasma treated×12 CrNi18 10 Ti stainless steel. Mater Test 59: 361–365. https://doi.org/10.3139/120.111014 doi: 10.3139/120.111014
![]() |
[54] |
Skakov M, Zhurerova L, Scheffler M (2013) Influence of regimes electrolytic-plasma processing on phase structure and hardening of steel 30CrMnSi. Adv Mat Res 601: 79–83. https://doi.org/10.4028/www.scientific.net/AMR.601.79 doi: 10.4028/www.scientific.net/AMR.601.79
![]() |
[55] |
Tabieva E, Zhurerova L, Baizhan D (2020) Influence of electrolyte-plasma hardening technological parameters on the structure and properties of banding steel 2. Key Eng Mater 839: 57–62. https://doi.org/10.4028/www.scientific.net/KEM.839.57 doi: 10.4028/www.scientific.net/KEM.839.57
![]() |
[56] |
Bayati M, Molaei R, Janghorban K (2010) Surface modification of AISI 1045 carbon steel by the electrolytic plasma process. Metall Mater Trans A 41: 906–911. https://doi.org/10.1007/s11661-009-0165-y doi: 10.1007/s11661-009-0165-y
![]() |
[57] |
Nunura C, Santos C, Spim J (2015) Numerical–experimental correlation of microstructures, cooling rates and mechanical properties of AISI 1045 steel during the Jominy end-quench test. Mater Des 76: 230–243. https://doi.org/10.1016/j.matdes.2015.03.031 doi: 10.1016/j.matdes.2015.03.031
![]() |
[58] |
Li Q, Xiao K, Lu Z, et al. (2024) Mechanism of laser carbonitriding enhancing the wear resistance of 45# steel. Mater Today Commun 38: 108327. https://doi.org/10.1016/j.mtcomm.2024.108327 doi: 10.1016/j.mtcomm.2024.108327
![]() |
[59] |
Korotkov V (2015) Wear resistance of carbon steel with different types of hardening. J Frict Wear 36: 149–152. https://doi.org/10.3103/S1068366615020105 doi: 10.3103/S1068366615020105
![]() |
[60] |
Algodi S, Salman A, Al-Helli A (2023) Microstructure and mechanical properties of AISI 1106/AISI 1045 steels drawn arc stud welded joints. Adv Sci Technol Res J 17: 48–55. https://doi.org/10.12913/22998624/171020 doi: 10.12913/22998624/171020
![]() |
1. | Hardik Joshi, Mehmet Yavuz, Numerical Analysis of Compound Biochemical Calcium Oscillations Process in Hepatocyte Cells, 2024, 8, 2701-0198, 10.1002/adbi.202300647 | |
2. | Yasir Nadeem Anjam, Rubayyi Turki Alqahtani, Nadiyah Hussain Alharthi, Saira Tabassum, Unveiling the Complexity of HIV Transmission: Integrating Multi-Level Infections via Fractal-Fractional Analysis, 2024, 8, 2504-3110, 299, 10.3390/fractalfract8050299 | |
3. | Yasir Nadeem Anjam, Asma Arshad, Rubayyi T. Alqahtani, Muhammad Arshad, Unveiling the dynamics of drug transmission: A fractal-fractional approach integrating criminal law perspectives, 2024, 9, 2473-6988, 13102, 10.3934/math.2024640 | |
4. | Mohamed EL-GAMEL, Nesreen MOHAMED, Waleed ADEL, Genocchi collocation method for accurate solution of nonlinear fractional differential equations with error analysis, 2023, 3, 2791-8564, 351, 10.53391/mmnsa.1373647 | |
5. | Twinkle R. Singh, Approximate‐analytical iterative approach to time‐fractional Bloch equation with Mittag–Leffler type kernel, 2024, 47, 0170-4214, 7028, 10.1002/mma.9955 | |
6. | M. L. Rupa, K. Aruna, K. Raghavendar, Insights into the time Fractional Belousov-Zhabotinsky System Arises in Thermodynamics, 2024, 63, 1572-9575, 10.1007/s10773-024-05770-0 | |
7. | Pushpendra Kumar, Vedat Suat Erturk, A variable-order fractional mathematical model for the strategy to combat the atmospheric level of carbon dioxide, 2024, 10, 2363-6203, 3529, 10.1007/s40808-024-01962-z | |
8. | Yasir Nadeem Anjam, Saira Tabassum, Muhammad Arshad, Mati ur Rahman, Muhammad Ateeq Tahir, Mathematical insights of social media addiction: fractal-fractional perspectives, 2024, 99, 0031-8949, 055230, 10.1088/1402-4896/ad348c | |
9. | Asiyeh Ebrahimzadeh, Amin Jajarmi, Dumitru Baleanu, Enhancing Water Pollution Management Through a Comprehensive Fractional Modeling Framework and Optimal Control Techniques, 2024, 31, 1776-0852, 10.1007/s44198-024-00215-y | |
10. | Ibtehal Alazman, Manvendra Narayan Mishra, Badr Saad Alkahtani, Pranay Goswami, Computational analysis of rabies and its solution by applying fractional operator, 2024, 32, 2769-0911, 10.1080/27690911.2024.2340607 | |
11. | Kottakkaran Sooppy Nisar, M. Sivashankar, S. Sabarinathan, C. Ravichandran, V. Sivaramakrishnan, Evaluating the stability and efficacy of fractal-fractional models in reproductive cancer apoptosis with ABT-737, 2025, 2025, 1029-242X, 10.1186/s13660-024-03249-4 | |
12. | Pasquini Fotsing Soh, Mathew Kinyanjui, David Malonza, Roy Kiogora, Non-local operator as a mathematical tool to improve the modeling of water pollution phenomena in environmental science: A spatio-temporal approach, 2025, 26668181, 101161, 10.1016/j.padiff.2025.101161 |