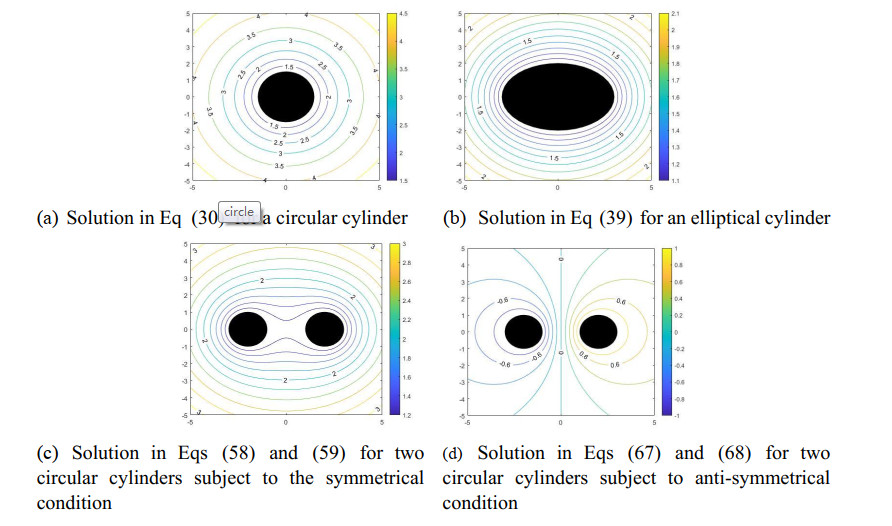
Epoxy composites were prepared by doping nano Zirconia Toughened Alumina (ZTA) which were synthesized by solution combustion method into epoxy resin and hardener. Initially ZTA nanopowder was characterized to check its purity, morphology and to confirm its metal-oxide bonding using XRD, SEM and FTIR respectively. The thermal properties such as TGA and DTG were also analysed. The polymer composites were obtained by uniformly dispersing ZTA nanopowder into epoxy using an ultrasonicator. Polymer composites of various concentrations viz, 0.5, 1, 1.5, 2 and 2.5 wt% were synthesized, all concentrations were prepared on weight basis. All the polymer composites were tested for compression properties, flexural properties and tensile properties. Best results for all the mechanical properties were obtained for epoxy with 1.5 wt% ZTA composites. Electrical properties such as breakdown voltage and breakdown strength were analysed and outstanding results were observed for epoxy with 2.5 wt% ZTA composite.
Citation: Chaitra Srikanth, G.M. Madhu, Shreyas J. Kashyap. Enhanced structural, thermal, mechanical and electrical properties of nano ZTA/epoxy composites[J]. AIMS Materials Science, 2022, 9(2): 214-235. doi: 10.3934/matersci.2022013
[1] | Xiao-Min Huang, Xiang-ShengWang . Traveling waves of di usive disease models with time delay and degeneracy. Mathematical Biosciences and Engineering, 2019, 16(4): 2391-2410. doi: 10.3934/mbe.2019120 |
[2] | Kang Wu, Yibin Lu . Numerical computation of preimage domains for spiral slit regions and simulation of flow around bodies. Mathematical Biosciences and Engineering, 2023, 20(1): 720-736. doi: 10.3934/mbe.2023033 |
[3] | Bing Hu, Minbo Xu, Zhizhi Wang, Jiahui Lin, Luyao Zhu, Dingjiang Wang . Existence of solutions of an impulsive integro-differential equation with a general boundary value condition. Mathematical Biosciences and Engineering, 2022, 19(4): 4166-4177. doi: 10.3934/mbe.2022192 |
[4] | Meng Zhao, Wan-Tong Li, Yang Zhang . Dynamics of an epidemic model with advection and free boundaries. Mathematical Biosciences and Engineering, 2019, 16(5): 5991-6014. doi: 10.3934/mbe.2019300 |
[5] | Huy Tuan Nguyen, Nguyen Van Tien, Chao Yang . On an initial boundary value problem for fractional pseudo-parabolic equation with conformable derivative. Mathematical Biosciences and Engineering, 2022, 19(11): 11232-11259. doi: 10.3934/mbe.2022524 |
[6] | Sai Zhang, Li Tang, Yan-Jun Liu . Formation deployment control of multi-agent systems modeled with PDE. Mathematical Biosciences and Engineering, 2022, 19(12): 13541-13559. doi: 10.3934/mbe.2022632 |
[7] | P. Vafeas, A. Skarlatos, P. K. Papadopoulos, P. Svarnas, N. Sarmas . A boundary value problem of heat transfer within DBD-based plasma jet setups. Mathematical Biosciences and Engineering, 2023, 20(10): 18345-18367. doi: 10.3934/mbe.2023815 |
[8] | Zhenwu Xiang, Qi Mao, Jintao Wang, Yi Tian, Yan Zhang, Wenfeng Wang . Dmbg-Net: Dilated multiresidual boundary guidance network for COVID-19 infection segmentation. Mathematical Biosciences and Engineering, 2023, 20(11): 20135-20154. doi: 10.3934/mbe.2023892 |
[9] | Fugeng Zeng, Yao Huang, Peng Shi . Initial boundary value problem for a class of p-Laplacian equations with logarithmic nonlinearity. Mathematical Biosciences and Engineering, 2021, 18(4): 3957-3976. doi: 10.3934/mbe.2021198 |
[10] | M. B. A. Mansour . Computation of traveling wave fronts for a nonlinear diffusion-advection model. Mathematical Biosciences and Engineering, 2009, 6(1): 83-91. doi: 10.3934/mbe.2009.6.83 |
Epoxy composites were prepared by doping nano Zirconia Toughened Alumina (ZTA) which were synthesized by solution combustion method into epoxy resin and hardener. Initially ZTA nanopowder was characterized to check its purity, morphology and to confirm its metal-oxide bonding using XRD, SEM and FTIR respectively. The thermal properties such as TGA and DTG were also analysed. The polymer composites were obtained by uniformly dispersing ZTA nanopowder into epoxy using an ultrasonicator. Polymer composites of various concentrations viz, 0.5, 1, 1.5, 2 and 2.5 wt% were synthesized, all concentrations were prepared on weight basis. All the polymer composites were tested for compression properties, flexural properties and tensile properties. Best results for all the mechanical properties were obtained for epoxy with 1.5 wt% ZTA composites. Electrical properties such as breakdown voltage and breakdown strength were analysed and outstanding results were observed for epoxy with 2.5 wt% ZTA composite.
Five basic quantities (voltage, charge, current, capacitance, and resistance) in electrostatics are involved in almost all applications. Electrostatics generally plays an important role in improving the performance of microelectro/mechanical systems (MEMS) and electron devices in the design stage. Many numerical methods (e.g., the finite difference method, the variational method, the moment method, the finite element method, and the boundary element method) were popularly used for engineering problems. Among diverse numerical techniques, the finite element method (FEM) and the boundary integral equation method (BIEM), as well as the boundary element method (BEM) become acceptable tools for engineers due to the increasing development of digital computing power. Here, we may focus on the mathematical study of the BIEM for electrostatics of two identical cylinders. Researchers have paid attention to the dual BEM paper of IEEE in 2003 [1], which has received nearly 5000 views in the Research Gate.
For a pair of two conducting cylinders, there is a large amount of literature on charged cylinders [2,3,4]. Different solutions existed to the electrostatic problem of two identical parallel cylinders held at the same (symmetric) potential [2,3]. A note was given to show their equivalence, and the identities were confirmed [4]. Four distinct solutions for the potential distribution around two equal circular parallel conducting cylinders by [2,3,5,6] were demonstrated to be equivalent by Lekner [7] by ways of several identities. Here, we may try an alternative way of BIEM using degenerate kernels to revisit this problem. A degenerate kernel is based on the method of separation variables, but it separates the variables in the two-point kernel function. Although the BIE in conjunction with the available degenerate kernel can only solve simple geometries and the results may be obtained more directly by using the method of separation variables for the solution instead of the fundamental solution, the tool can explain the rank-deficiency mechanism in the BIE/BEM such as degenerate scale, degenerate boundary, spurious eigenvalues and fictitious frequency, which is meaningful to the BEM community. Besides, symmetric and anti-symmetric cases are both considered. Regarding the anti-symmetric electrostatic potential, Lebedev et al. [8] have provided a closed-form solution by using the bipolar coordinates. The solution is interestingly found to be the simplest method of fundamental solution (MFS) of two opposite strengths of sources at the two foci. It is not trivial to check the asymptotic behavior at infinity of the two cases, symmetric and anti-symmetric. Besides, whether the equilibrium of the boundary flux along the two cylinders is satisfied or not is also our main concern.
Regarding the potential problem of a two-dimensional plane containing two circular boundaries, Chen and Shen [9] studied the multiply-connected Laplace problem. They found that a degenerate scale depends on the outer boundary. Chen et al. [10] solved the Laplace problem by using the BIEM in conjunction with the degenerate kernel to derive an analytical solution. It is found that a degenerate scale may occur due to the introduction of the logarithmic kernel for the two-dimensional case. Efficient techniques for the rank-deficiency of the BEM in electrostatic problems were proposed by Chyuan et al. [11]. Later, it was found that the special (degenerate) geometry happened to be the shape of unit logarithmic capacity. Kuo et al. [12] studied the degenerate scale for regular N-gon domains by using complex variables. Numerical implementation was also done by using the BEM. Kuo et al. [13] revisited the degenerate scale for an infinite plane problem containing two circular holes using the conformal mapping. Chen et al. [14] linked the logarithmic capacity in the potential theory and the degenerate scale in the BEM for two tangent discs. The logarithmic capacity of the line segment as well as the double degeneracy in the BIEM/BEM was studied by Chen et al. [15]. Due to the use of the two-dimensional fundamental solution in the BIEM, the solution space is expanded, and sometimes the corresponding matrix is rank deficient in the BEM. In other words, the integral operator of the logarithmic kernel is range deficient. A corresponding chart to show the rank deficiency and the null space of the integral operator of single, double layer potentials and their derivatives was given in [16,17,18], while the original one was provided in the face cover of the Strang book [19]. Fikioris et al. [20] solved rectangularly shielded lines by using the Carleman-Vekua method. In the mentioned paper [20], it is interesting to find that its formulation also needs a constraint [21] to ensure a unique solution. This outcome is similar to the paper of Chen et al. [22] using the Fichera's approach, where an additional constraint is also required.
In this paper, we revisit two cylinders of electrostatics by using the BIE with the degenerate kernel of the bipolar coordinates. Both the symmetric and anti-symmetric specified potentials are considered. Besides, the logarithmic capacity is also discussed. The boundary potential and flux are expanded by using the Fourier series, while the fundamental solution is represented by using the degenerate kernel. The equilibrium of boundary flux and the asymptotic behavior at infinity are also examined. The solution space expanded using the BIEM is compared with the true solution space. After summarizing the single (circle and ellipse) and two cylinders, a conclusion for constructing the solution space can be made.
First, we consider a conducting cylinder. The governing equation and the Dirichlet boundary condition are shown below:
∇2u(x)=0, x∈D,u(x)=ˉu(x), x∈B,u(x)= ln |x|+O(1), x→∞, | (1) |
where ∇2, D and B are the Laplace operator, the domain of interest and the boundary, respectively. Furthermore, x is the position vector of a field point and ˉu(x) is the specified B.C. The integral formulation for the Laplace problem is derived from Green's third identity. The representation of the conventional integral equation for the domain point is written as
2πu(x)=∫BT(s,x)ˉu(s)dB(s)−∫BU(s,x)t(s)dB(s),x∈D, | (2) |
where s is the position vector of a source point, U(s,x)= ln |x−s| is the fundamental solution, T(s,x)=∂U(s,x)∂ns, and t(x) is the unknown boundary flux. By moving the field point to the smooth boundary, Eq (2) becomes:
πˉu(x)=C.P.V.∫BT(s,x)ˉu(s)dB(s)−∫BU(s,x)t(s)dB(s),x∈B, | (3) |
where the C.P.V. denotes the Cauchy principal value, and T(s,x)=∂U(s,x)/∂ns is the closed-form kernel. Once the field point x locates outside the domain, we obtain the null-field integral equation as shown below:
0=∫BT(s,x)ˉu(s)dB(s)−∫BU(s,x)t(s)dB(s),x∈Dc. | (4) |
where Dc is the complementary domain. By employing the proper degenerate kernel (U(s,x)) to represent the closed-form fundamental solution, the collocation point can be exactly located on the real boundary free of facing the singular integral. Equations (2) and (4) can be rewritten as:
2πu(x)=∫BTdk(s,x)ˉu(s)dB(s)−∫BUdk(s,x)t(s)dB(s),x∈D∪B | (5) |
and
0=∫BTdk(s,x)ˉu(s)dB(s)−∫BUdk(s,x)t(s)dB(s),x∈Dc∪B. | (6) |
where Tdk(s,x) and Udk(s,x) are the corresponding degenerate kernels to represent T(s,x) and U(s,x), respectively. By setting the field point x=(ρ,ϕ) and the source point s=(R,θ) in the polar coordinates for a circular domain, the closed-form fundamental solution in Eqs (5) and (6) can be expressed by using the degenerate kernel form as shown below:
Udk(s,x)={Ui(R,θ;ρ,ϕ)= ln R−∑∞m=11m(ρR)m cos m(θ−ϕ), R≥ρ, (a)Ue(R,θ;ρ,ϕ)= ln ρ−∑∞m=11m(Rρ)m cos m(θ−ϕ), ρ>R, (b). | (7) |
and
Tdk(s,x)={Ti(R,θ;ρ,ϕ)=−(1R+∑∞m=1(ρmRm+1) cos m(θ−ϕ)), R>ρ, (a)Te(R,θ;ρ,ϕ)=∑∞m=1(Rm−1ρm) cos m(θ−ϕ), ρ>R. (b). | (8) |
The unknown boundary flux t(s) is expanded in terms of Fourier series as shown below:
t(s)=1Js(a0+∑∞n=1an cos (nθ)+∑∞n=1bn sin (nθ)), 0≤θ≤2π, | (9) |
where Js=1 is the Jacobian term, a0, an and bn are unknown coefficients. The given boundary condition is
ˉu(x)=v. | (10) |
where v is a constant. By considering R=a in Eqs (6)–(8), the coefficient of the Fourier constant base is
−a ln a a0=v, | (11) |
where a is the radius of the circular cylinder. Equation (11) indicates that the occurring mechanism of a degenerate scale is
ln a=0. | (12) |
When a=1, the coefficient of a0 cannot be determined. It results in a non-unique solution. This critical size is called a degenerate scale. In Rumely's book [23], the logarithmic capacity, cL, of a circle is equal to its radius. It is easily found that the special (degenerate) geometry happens to be the shape of unit logarithmic capacity. The discriminant Dp(a) of the degenerate scale in the BEM/BIEM for a circular boundary is written as
Dp(a)= ln a. | (13) |
If Dp(a)≠0, this size is an ordinary scale and there exists a unique solution. Otherwise, according to the Fredholm alternative theorem, there is no solution or infinite solutions. For an ordinary scale, the boundary flux, of the electrostatic field along the boundary, is obtained as
t(x)=−va ln a,x∈B. | (14) |
The unique solution of electrostatic potential is obtained by
u(x)=v ln ρ ln a, | (15) |
as shown in Figure 1(a). Even though the electrostatic field along the boundary in Eq (14) is not in equilibrium, i.e. ∫Bt(x)dB(x)≠0, the electrostatic field at infinity, Γ∞, would exist and satisfy the equilibrium condition together in total, ∫B+Γ∞t(x)dB(x)=0. If we normalize the potential on the cylinder to the unity, and let λ be the dimensionless ratio, the potential becomes
u(x)=v+λud(x), | (16) |
where
ud(x)= ln ρ− ln a. | (17) |
The solution by using the direct BIE of Eq (15) is the special case of Eq (16) by setting λ=vDp(a). When the size of the boundary is a degenerate scale, i.e., a=1 and Dp(a)= ln a=0, it has no solution if v≠0. If v=0, then the constant term in Eq (9), a0, is a free constant. The electrostatic potential yields
u(x)=a0 ln ρ, | (18) |
and Eq (16) would reduce to
u(x)=λud(x), | (19) |
and ud(x) in Eq (19) reduces to ln ρ since ln a=0. It is easy to find that a0 and λ are equivalent.
For an elliptical case, we naturally utilize the elliptic coordinates to solve the problem in the BIE. The relation between the Cartesian coordinates and the elliptic coordinates is given below:
x=c cosh ξ cos η,y=c sinh ξ sin η. | (20) |
where c is the focal length. By separating the source point and the field point in the elliptic coordinates [24] to represent the closed-form fundamental solution, we have
Udk(s,x)= ln |x−s|={Ui(ξs,ηs;ξx,ηx)=ξs+ ln c2−∑∞m=12me−mξs cosh m ξx cos m ηx cos m ηs −∑∞m=12me−mξs sinh m ξx sin m ηx sin m ηs, ξs≥ξx, (a)Ue(ξs,ηs;ξx,ηx)=ξx+ ln c2−∑∞m=12me−mξx cosh m ξs cos m ηx cos m ηs −∑∞m=12me−mξx sinh m ξs sin m ηx sin m ηs, ξs<ξx, (b) | (21) |
Tdk(s,x)=∂U(s,x)∂ns={Ti(ξs,ηs;ξx,ηx)=−1Js(1+2∑∞m=1e−mξs cosh m ξx cos m ηx cos m ηs +2∑∞m=1e−mξs sinh m ξx sin m ηx sin m ηs), ξs>ξx, (a)Te(ξs,ηs;ξx,ηx)=1Js(2∑∞m=1e−mξx sinh m ξs cos m ηx cos m ξs+2∑∞m=1e−mξx cosh m ξs sin m ηx sin m ηs), ξs<ξx. (b) | (22) |
where Js=c√ cosh 2ξs sin 2ηs+ sinh 2ξs cos 2ηs. The unknown boundary flux t(s) is expanded in terms of generalized Fourier series. We have
t(s)=1Js(a0+∑∞n=1an cos (nηs)+∑∞n=1bn sin (nηs)), 0≤ηs≤2π, | (23) |
where a0, an and bn are unknown coefficients. The given boundary condition is
ˉu(x)=v. | (24) |
By substituting Eqs (21a), (22a), (23) and (24) into Eq (6), the coefficient of the Fourier constant base is
−(ξ0+ ln c2)a0=v, | (25) |
Equation (25) indicates that the occurring mechanism of a degenerate scale is
ξ0+ ln c2=0. | (26) |
Equation (26) yields the degenerate scale of a+b2=1, where a and b are the semi-major and semi-minor axes of an ellipse, respectively. According to Eq (25), the discriminant of a degenerate scale in the BEM/BIEM is obtained
De(c,ξ0)=ξ0+ ln c2= ln (a+b2). | (27) |
In Rumely's book [23], the logarithmic capacity of an ellipse is equal to a+b2. According to Eqs (13) and (27), the logarithmic capacity, cL, and the discriminant, De(⋅), satisfy the relation,
cL=eDe(⋅). | (28) |
The relationship of the discriminant, logarithmic capacity, and degenerate scale are summarized in Table 1. If De(c,ξ0) is not equal to zero, this size is an ordinary scale with a unique solution. Otherwise, according to the Fredholm alternative theorem, it has no solution or infinite solution. For an ordinary scale, the boundary flux is obtained by
t(x)=−vDe(c,ξ0),x∈B. | (29) |
![]() |
The unique solution of electrostatic potential is
u(x)=(ξx+ ln c2)(vDe(c,ξ0)), | (30) |
as shown in Figure 1(b). Even though the boundary flux in Eq (29) is not in equilibrium, i.e., ∫Bt(x)dB(x)≠0, the electrostatic field at infinity, Γ∞, would exist and satisfy the equilibrium condition together in total, i.e., ∫B+Γ∞t(x)dB(x)=0. If we normalize the potential on the cylinder to the unity, and let λ be the dimensionless ratio, the potential becomes
u(x)=v+λud(x), | (31) |
where
ud(x)=(ξx+ ln c2)−(ξ0+ ln c2)=ξx−ξ0. | (32) |
A neat formula of ud(x) could be defined as ud(x)=De(ξx)−De(ξ0). The solution by using the direct BIE of Eq (30) is the special case of Eq (31), if λ=vDe(c,ξ0).
When the size of the boundary is a degenerate scale, De(c,ξ0)=ξ0+lnc2=0, it is no solution if v≠0. If v=0, the constant term in Eq (23), a0, is a free constant. The electrostatic potential yields
u(x)=(ξx+ ln c2)a0, | (33) |
and Eq (16) reduces to
u(x)=λud(x), | (34) |
where ud(x) in Eq (32) reduces to ξx+ ln c2 since De(ξ0) is equal to zero. It is easy to find that a0 and λ are equivalent. In addition, the degenerate scale in the BEM/BIEM is due to the logarithmic kernel.
For the single elliptical cylinder, the degenerate kernel is expanded in terms of the generalized form as
Udk(s,x)= ln |x−s|={Ui(ξs,ηs;ξx,ηx)=De(ξs)−∑∞m=1αm(ξs,ηs;ξx,ηx), ξs≥ξx, (a)Ue(ξs,ηs;ξx,ηx)=De(ξx)−∑∞m=1αm(ξx,ηx;ξs,ηs), ξs<ξx, (b) | (35) |
Tdk(s,x)=∂U(s,x)∂ns={Ti(ξs,ηs;ξx,ηx)=−1Js(D'eξs)−∑∞m=1βm(ξs,ηs;ξx,ηx)), ξs>ξx, (a)Te(ξs,ηs;ξx,ηx)=1Js∑∞m=1βm(ξs,ηs;ξx,ηx), ξs<ξx, (b) | (36) |
where ξ and η are the radial and angular directions, respectively, De(⋅) is the constant function for ηs and other term is α(⋅). The unknown boundary flux t(s) is expanded in terms of the generalized Fourier series as shown below:
t(s)=1Js(a0+∑∞n=1an cos (nηs)+∑∞n=1bn sin (nηs)), 0≤ηs≤2π, | (37) |
where a0, an and bn are unknown coefficients. By substituting Eqs (35a), (36a), (37) and the boundary condition (Eq (10)) into Eq (6), the coefficient of the Fourier constant base is
De(ξ0)a0=−vD'e(ξ0), | (38) |
If D(ξ0)≠0, then the unique solution of electrostatic potential is
u(x)=vDe(ξ0)De(ξx), | (39) |
and
ud(x)=De(ξx)−De(ξ0). | (40) |
When the size of the boundary is a degenerate scale, De(ξ0)=0, there is no solution if v≠0. If v=0, the constant term in Eq (37), a0, is a free constant. The electrostatic potential yields
u(x)=(De(ξx)−De(ξ0))a0, | (41) |
and Eq (40) reduces to
u(x)=λud(x), | (42) |
where ud(x) in Eq (40) is reduced to De(ξx), since De(ξ0) is equal to zero. By using the generalized form of Eqs (35) and (36), the analytical and neat form of ud(x) for the single elliptical cylinder is derived. It is easy to find that a0 and λ are equivalent. The generalized potential and the solution by using the BIEM are compared in Table 2.
![]() |
In this section, we consider two circular cylinders of electrostatics. The Dirichlet boundary conditions of two circular cylinders are given by
ul(x)=v1 and ur(x)=v2,x∈B, | (43) |
where ul(x) and ur(x) are potentials of the left and right circular boundaries, respectively, x is the position vector of the field point, B is the boundary, and v1 and v2 are specified constant potentials. The original problem can be decomposed into a symmetric problem and an anti-symmetric problem as shown below:
ul(x)=ur(x)=v,x∈B, symmetry BC, | (44) |
and
ul(x)=−ur(x)=v,x∈B. anti-symmetry BC. | (45) |
Since the problem contains two circular boundaries, we naturally employ the bipolar coordinates to express the closed-form fundamental solution. The relation between the Cartesian coordinates and the bipolar coordinates is shown below:
x=c sinh η cosh η− cos ξ,y=c sin ξ cosh η− cos ξ. | (46) |
where η and ξ are the radial and angular coordinates, respectively, c is the half distance between the two foci of the bipolar coordinates. By separating the source point and the field point in the bipolar coordinates [9] for the closed-form fundamental solution, we have
Udk(s,x)= ln |x−s|= |
{ ln (2c)+ηs−∑∞m=11m{e−m(ηs−ηx) cos [m(ξx−ξs)]−emηx cos (mξx)−emηs cos (mξs)},0>ηs≥ηx ln (2c)+ηx−∑∞m=11m{e−m(ηx−ηs) cos [m(ξx−ξs)]−emηx cos (mξx)−emηs cos (mξs)},0>ηx>ηs ln (2c)−∑∞m=11m{e−m(ηx−ηs) cos [m(ξx−ξs)]−e−mηx cos (mξx)−emηs cos (mξs)},ηx>0>ηs ln (2c)−ηs−∑∞m=11m{e−m(ηx−ηs) cos [m(ξx−ξs)]−e−mηx cos (mξx)−e−mηs cos (mξs)},ηx≥ηs>0 ln (2c)−ηx−∑∞m=11m{e−m(ηs−ηx) cos [m(ξx−ξs)]−e−mηx cos (mξx)−e−mηs cos (mξs)},ηs>ηx>0 ln (2c)−∑∞m=11m{e−m(ηs−ηx) cos [m(ξx−ξs)]−emηx cos (mξx)−e−mηs cos (mξs)},ηs>0>ηx | (47) |
Tdk(s,x)=∂U(s,x)∂ns= |
{1Js{−1+∑∞m=1[−e−m(ηs−ηx) cos [m(ξx−ξs)]−emηs cos (mξs)]},0>ηs≥ηx1Js∑∞m=1{e−m(ηx−ηs) cos [m(ξx−ξs)]−emηs cos (mξs)},0>ηx>ηs1Js∑∞m=1{e−m(ηx−ηs) cos [m(ξx−ξs)]−emηs cos (mξs)},ηx>0>ηs1Js{−1+∑∞m=1[e−m(ηx−ηs) cos [m(ξx−ξs)]−e−mηs cos (mξs)]},ηx≥ηs>01Js∑∞m=1{e−m(ηs−ηx) cos [m(ξx−ξs)]−e−mηs cos (mξs)},ηs>ηx>0 1Js∑∞m=1{e−m(ηs−ηx) cos [m(ξx−ξs)]−e−mηs cos (mξs)},ηs>0>ηx | (48) |
where x=(ηx,ξx), s=(ηs,ξs) and Js=c/[cosh(ηs)−cos(ξs)].
The boundary condition of the symmetry problem is shown in Eq (44). The unknown boundary densities on the two circular cylinders can be expanded by using the generalized Fourier series as shown below:
tM(s)={1Js(al0+∑∞n=1aln cos n ξs+∑∞n=1bln sin n ξs), ηs < 0,s∈Bl,1Js(ar0+∑∞n=1arn cos n ξs+∑∞n=1brn sin n ξs), ηs≥0,s∈Br, | (49) |
where al0,aln,bln,ar0,arn and brn are unknown coefficients of the generalized Fourier series. By substituting Eqs (47a), (47f), (48a), (48f), (44) and (49) into Eq (6), and collocating the null-field point on the left boundary, Bl, we have
−2πv−π{2( ln (2c)−η0)al0+∑∞n=11ne−nη0aln−∑∞n=11n(−2e−nη0al0+aln) cos n ξx−∑∞n=11nbln sin n ξx}−π{2 ln (2c)ar0+∑∞n=11ne−nη0arn+∑∞n=11n[(2e−nη0ar0−e−2nη0arn) cos n ξx−e−2nη0brn sin n ξx]}=0. | (50) |
Similarly, substituting Eqs (47c), (47d), (48c), (48d), (44) and (49) into Eq (6), and collocating the null-field point on the right boundary, Br, we have
−π{2 ln (2c)al0+∑∞n=11ne−nη0aln+∑∞n=11n[(−e−2nη0aln+2e−nη0al0) cos n ξx−e−2nη0bln sin n ξx]}−2πv−π{2( ln (2c)−η0)ar0+∑∞n=11ne−nη0arn+∑∞n=11n[(2e−nη0ar0−arn) cos n ξx−brn sin n ξx]}=0. | (51) |
By adding Eqs (50) and (51) together, we obtain
(4 ln (2c)−2η0)(al0+ar0)+2∑∞n=11ne−nη0(aln+arn)+∑∞n=11n[−(1+e−2nη0)(aln+arn)+4e−nη0(al0+ar0)] cos n ξx−∑∞n=11n[(1+e−2nη0)(bln+brn)] sin n ξx=−4v | (52) |
After comparing the coefficient of generalized Fourier bases, we have
{(4ln(2c)−2η0)(al0+ar0)+2∑∞n=11ne−nη0(aln+arn)=−4v,n=1, 2, 3...1n(1+e−2nη0)(aln+arn)+4e−nη0(al0+ar0)=0,n=1, 2, 3...1n(1+e−2nη0)(bln+brn)=0,n=1, 2, 3... | (53) |
By similarly subtracting Eq (50) from Eq (51), we have
π{−2η0al0+∑∞n=11n[(−1+e−2nη0)aln cos n ξx+(−1+e−2nη0)bln sin n ξx]}+π{2η0ar0+∑∞n=11n[(1−e−2nη0)arn cos n ξx+(1−e−2nη0)brn sin n ξx]}=0 | (54) |
After comparing the coefficient of generalized Fourier bases, we have
{2η0(al0−ar0)=0,n=1, 2, 3...1n(−1+e−2nη0)(aln−arn)=0, n=1, 2, 3...1n(−1+e−2nη0)(bln−brn)=0, n=1, 2, 3... | (55) |
In order to solve the coefficients al0 and ar0, we need to define a discriminant as shown below:
Db(c,η0)=2 ln (2c)−η0+∑∞n=11n4e−2nη0(1+e−2nη0). | (56) |
For the case of two cylinders, Rumely [23] employed the complex variable to derive the logarithmic capacity, as shown in Table 1. Since the logarithmic capacity is not a closed-form or an exact formula, the postulate in Eq (28) for the case of two cylinders could not be analytically verified at present. If Db≠0, the geometry of the problem is an ordinary scale, Eqs (53) and (55) yield the coefficients as shown below:
al0=ar0=vDb(c,η0)aln=arn=2e−nη0(1+e−2nη0)al0,n=1,2,3...bln=brn=0,n=1,2,3... | (57) |
Substituting Eqs (47b), (47f), (48b), (48f), (44) and the obtained unknown boundary densities into Eq (5) for the field solution of ηx<0, we have the unique solution
u(x)=vDb(c,η0)((2 ln (2c)+ηx+∑∞n=14ne−2nη01+e−2nη0)−∑∞n=12n(e−nη0enηx+e−nηxenη0+e−nη0−enηx) cos (nξx)),−η0≤ηx<0. | (58) |
Similar substitution of Eqs (47c), (47e), (48c), (48e), (44) and the obtained unknown densities into Eq (5), the field solution for ηx≥0 yields
u(x)=vDb(c,η0)((2 ln (2c)−ηx+∑∞n=14ne−2nη01+e−2nη0)−∑∞n=12n(e−nη0enηx+e−nηxenη0+e−nη0−e−nηx) cos (nξx)),η0≥ηx≥0. | (59) |
It is found that Eqs (58) and (59) show the symmetry solution. All potentials are shown in Figure 1(c). This solution will be compared and discussed with that of Darevski [2] later.
If Db(c,η0)=0, a degenerate scale occurs. When the constant potential v≠0, it yields no solution. When the constant potential v=0, it yields infinite solutions. Equations (53) and (55) yield the coefficients as shown below:
ar0=al0=k,aln=arn=4e−nη0(1+e−2nη0)k,n=1,2,3...bln=brn=0,n=1,2,3... | (60) |
where k is an arbitrary constant. In case of a degenerate scale, η0 becomes
η0=2 ln (2c)+∞∑n=11n4e−2nη0(1+e−2nη0) | (61) |
Substituting Eqs (47b), (47f), (48b), (48f), (44) and the obtained boundary unknown densities into Eq (5) for the field solution of ηx<0, we have the infinite solution,
u(x)=((η0+ ηx)−∞∑n=12n(e−nη0enηx+e−nηxenη0+e−nη0−enηx) cos (nξx))k, −η0≤ηx<0. | (62) |
Similar substitution of Eqs (47c), (47e), (48c), (48e), (44) and the obtained boundary unknown densities into Eq (5), the field solution for ηx≥0 yields the infinite solution,
u(x)=((η0−ηx)−∞∑n=12n(e−nη0enηx+e−nηxenη0+e−nη0−e−nηx) cos (nξx))k, η0≥ηx≥0. | (63) |
Equations (62) and (63) also indicate symmetry.
Similarly, we consider the anti-symmetry problem. The coefficient of generalized Fourier bases in Eqs (45) and (49) satisfy
{−(2 ln (2c)−η0+4∑∞n=1e−2nη0n(1+e−2nη0))(al0+ar0)=0,1n(1+e−2nη0)(aln+arn)+4e−nη0(al0+ar0)=0, n=1, 2, 3...1n(1+e−2nη0)(bln+brn)=0, n=1, 2, 3... | (64) |
and
{2η0(al0−ar0)=4v,1n(−1+e−2nη0)(aln−arn)=0, n=1, 2, 3...,1n(−1+e−2nη0)(bln−brn)=0, n=1, 2, 3... | (65) |
We also find the discriminant, Db(c,η0) in Eq (64). If Db(c,η0)≠0, the geometry of the problem is an ordinary scale. Equations (64) and (65) yield the coefficients as shown below:
al0=−ar0=vη0aln=arn=0,n=1,2,3...bln=brn=0,n=1,2,3... | (66) |
Substituting Eqs (47b), (47f), (48b), (48f), (45) and the obtained boundary unknown densities into Eq (5) for the field solution of ηx<0, we have
u(x)=vηxη0, ηx < 0. | (67) |
Substituting Eqs (47c), (47e), (48c), (48e), (45) and the obtained unknown densities into Eq (5) for the field solution of ηx≥0, we also have
u(x)=vηxη0, ηx≥0. | (68) |
All potentials are shown in Figure 1(d). The solution in Eq (68) matches well with that of Lebedev et al. [8]. From the viewpoint of the MFS, this solution is the simplest one since only two sources with opposite strengths are required to locate the two foci.
If Db(c,η0)=0, a degenerate scale occurs. Fortunately, it doesn't result in no solution whether v is equal to zero or not as shown in the boundary condition of Eq (45). Equations (64) and (65) yield the coefficients as shown below:
al0+ar0=2k,aln=arn=4e−nη0(1+e−2nη0)k,n=1,2,3...bln=brn=0,n=1,2,3... | (69) |
where k is an arbitrary constant. For a degenerate scale case, η0 satisfies Db(c,η0)=0, i.e.
η0=2 ln (2c)+∑∞n=11n4e−2nη0(1+e−2nη0) | (70) |
Substituting Eqs (47b), (47f), (48b), (48f), (45) and the obtained boundary unknown densities into Eq (5) for the field solution of ηx<0, we have
u(x)=vη0ηx+k( ln (2 cosh ηx−2 cos ξx)−η0+2∑∞n=11ne−nη0 cosh (nηx) cosh (nη0) cos (nξx)), −η0≤ηx≤0. | (71) |
Similarly substituting Eqs (47c), (47e), (48c), (48e), (45) and the obtained unknown densities into Eq (5), we obtain the field solution
u(x)=vη0ηx+k(ln(2 cosh ηx−2 cos ξx)−η0+2∑∞n=11ne−nη0 cosh (nη0) cosh (nηx) cos (nξx)), η0≥ηx > 0. | (72) |
Equations (71) and (72) destroy the anti-symmetry due to the second part of k. To obey the anti-symmetry solution, k should be zero. In other words, this k part in the solution of Eqs (71) and (72) also disobey the bounded potential at infinity. This solution for a free constant, k, will be compared with that of Lekner [4] later.
According to the solution of Lekner [4], the general solution space of the symmetry problem in Eq (44) is expressed as follows:
u(x)=v+λud(x) | (73) |
where
ud(x)= ln (2 cosh ηx−2 cos ξx)−η0+∑∞n=12ne−nη0 cosh (nηx) cosh (nη0) cos (nξx). | (74) |
By using the identity equation,
ln ( cosh ηx− cos ξx)=ηx−∑∞m=12me−mηx cos m ξx− ln 2, | (75) |
the solution by using the direct BIE of Eq (59) is rewritten as
u(x)=vDb(c,η0)( ln (2 cosh ηx−2 cos ξx)+∑∞n=12ne−nη0 cosh (nηx) cosh (nη0) cos (nξx)−(2 ln (2c)+∑∞n=11n4e−2nη01+e−2nη0)),η0≥ηx > 0. | (76) |
Equation (59) is the special case of Eq (73), if λ=−vDb(c,η0). When the size of the boundary is a degenerate scale, i.e., Db(c,η0)=0, the BIE solution does not exist if v≠0. If v=0, the constant term in Eq (57), ar0, is a free constant. The electrostatic potential is obtained by
u(x) =−( ln (2 cosh ηx−2 cos ξx)−η0+∑∞n=12ne−nη0 cosh (nηx) cosh (nη0) cos (nξx))ar0, η0≥ηx > 0, | (77) |
and Eq (73) can be reduced to
u(x)=λud(x), | (78) |
since v is zero. It is easy to find that ar0 and λ are equivalent.
Similarly, the general solution space of the anti-symmetry problem in Eq (45) is expressed as follows:
u(x)=vηxη0+λud(x) | (79) |
where
ud(x)= ln (2 cosh ηx−2 cos ξx)−η0+∑∞n=12ne−nη0 cosh (nηx) cosh (nη0) cos (nξx). | (80) |
Lebedev et al. [8] considered the condition at the infinity, u(x)=0,x→∞, the solution of Eq (79) would reduce to only
u(x)=vηxη0. | (81) |
It is the reason why the solution of Eq (68) by using the BIEM is a special case of Eq (79) for λ=0. When the size of the boundary is a degenerate scale, i.e., Db(c,η0)=0, it yields infinite solutions. Since the sum of constant terms, ar0 and al0, in Eq (69) is a free constant, k, the electrostatic potential yields
u(x)=vηxη0−( ln (2 cosh ηx−2 cos ξx)−η0+2∑∞n=11ne−nη0 cosh (nη0) cosh (nηx) cos (nξx))k, η0≥ηx > 0. | (82) |
It is easy to find that k and λ are equivalent. To sum up, the free constant, λ and ud(x) in the general solution by Lekner [4] are similar to the constant term in the boundary potential and the obtained BIE solution for the degenerate scale by Chen et al. [9], respectively. The obtained BIE solution for the degenerate case yields nontrivial boundary flux even though the boundary potential is trivial. The generalized potential and the available solutions by using the BIEM for the problem containing two cylinders are compared with each other in Table 3.
![]() |
This paper investigates the solution space for the electrostatics of two cylinders using the BIEM. Both the symmetric and anti-symmetric cases are considered. Flux equilibrium on the cylindrical boundaries and the asymptotic behavior at infinity is also examined. Moreover, on the base of the Fredholm alternative theorem, the relation of unique solution and the degenerate scale in the BIEM is linked. The logarithmic capacity and the discriminant are also linked by using an exponential relation. Besides, the degenerate scale is also related. Not only two cylinders but also a single one (circle or ellipse) are considered. Finally, the results are compared with those derived by other researchers. Linkage and agreement are made.
The authors wish to thank the financial supports from the National Science and Technology Council, Taiwan under Grant No. MOST 111-2221-E-019-009-MY3 for National Taiwan Ocean University.
The authors declare there is no conflict of interest.
[1] |
Wetzel B, Haupert F, Zhang MQ (2003) Epoxy nanocomposites with high mechanical and tribological performance. Compos Sci Technol 63: 2055-2067. https://doi.org/10.1016/S0266-3538(03)00115-5 doi: 10.1016/S0266-3538(03)00115-5
![]() |
[2] |
Carolan D, Ivankovic A, Kinloch AJ, et al. (2017) Toughened carbon fibre-reinforced polymer composites with nanoparticle-modified epoxy matrices. J Mater Sci 52: 1767-1788. https://doi.org/10.1007/s10853-016-0468-5 doi: 10.1007/s10853-016-0468-5
![]() |
[3] |
Dorigato A, Pegoretti A, Bondioli F, et al. (2010) Improving epoxy adhesives with zirconia nanoparticles. Compos Interface 17: 873-892. https://doi.org/10.1163/092764410X539253 doi: 10.1163/092764410X539253
![]() |
[4] |
Bondioli F, Cannillo V, Fabbri E, et al. (2006) Preparation and characterization of epoxy resins filled with submicron spherical zirconia particles. Polimery 51: 794-798. https://doi.org/10.14314/polimery.2006.794 doi: 10.14314/polimery.2006.794
![]() |
[5] |
Dorigato A, Pegoretti A (2011) The role of alumina nanoparticles in epoxy adhesives. J Nanopart Res 13: 2429-2441. https://doi.org/10.1007/s11051-010-0130-0 doi: 10.1007/s11051-010-0130-0
![]() |
[6] |
Yu ZQ, You SL, Yang ZG, et al. (2011) Effect of surface functional modification of nano-alumina particles on thermal and mechanical properties of epoxy nanocomposites. Adv Compos Mater 20: 487-502. https://doi.org/10.1163/092430411X579104 doi: 10.1163/092430411X579104
![]() |
[7] |
Reyes-Rojas A, Dominguez-Rios C, Garcia-Reyes A, et al. (2018) Sintering of carbon nanotube-reinforced zirconia-toughened alumina composites prepared by uniaxial pressing and cold isostatic pressing. Mater Res Express 5: 105602. https://doi.org/10.1088/2053-1591/aada35 doi: 10.1088/2053-1591/aada35
![]() |
[8] | Chuankrerkkul N, Somton K, Wonglom T, et al. (2016) Physical and mechanical properties of zirconia toughened alumina (ZTA) composites fabricated by powder injection moulding. Chiang Mai J Sci 43: 375-380. |
[9] |
Ponnilavan V, Kannan S (2019) Structural, optical tuning, and mechanical behavior of zirconia toughened alumina through europium substitutions. J Biomed Mater Res Part B 107: 1170-1179. https://doi.org/10.1002/jbm.b.34210 doi: 10.1002/jbm.b.34210
![]() |
[10] |
Srikanth C, Madhu GM (2020) Effect of ZTA concentration on structural, thermal, mechanical and dielectric behavior of novel ZTA-PVA nanocomposite films. SN Appl Sci 2: 1-12. https://doi.org/10.1007/s42452-020-2232-3 doi: 10.1007/s42452-020-2232-3
![]() |
[11] |
Zhang J, Ge L, Chen ZG, et al. (2019) Cracking behavior and mechanism of gibbsite crystallites during calcination. Cryst Res Technol 54: 1800201. https://doi.org/10.1002/crat.201800201 doi: 10.1002/crat.201800201
![]() |
[12] |
Bhaduri S, Bhaduri SB, Zhou E (1998) Auto ignition synthesis and consolidation of Al2O3-ZrO2 nano/nano composite powders. J Mater Res 13: 156-165. https://doi.org/10.1557/JMR.1998.0021 doi: 10.1557/JMR.1998.0021
![]() |
[13] |
Vasylkiv O, Sakka Y, Skorokhod VV (2003) Low-temperature processing and mechanical properties of zirconia and zirconia-alumina nanoceramics. J Am Ceram Soc 86: 299-304. https://doi.org/10.1111/j.1151-2916.2003.tb00015.x doi: 10.1111/j.1151-2916.2003.tb00015.x
![]() |
[14] |
Sagar JS, Kashyap SJ, Madhu GM, et al. (2020) Investigation of mechanical, thermal and electrical parameters of gel combustion-derived cubic zirconia/epoxy resin composites for high-voltage insulation. Cerâmica 66: 186-196. https://doi.org/10.1590/0366-69132020663782887 doi: 10.1590/0366-69132020663782887
![]() |
[15] |
Ho MW, Lam CK, Lau K, et al. (2006) Mechanical properties of epoxy-based composites using nanoclays. Compos Struct 75: 415-421. https://doi.org/10.1016/j.compstruct.2006.04.051 doi: 10.1016/j.compstruct.2006.04.051
![]() |
[16] |
Uhl FM, Davuluri SP, Wong SC, et al. (2004) Organically modified montmorillonites in UV curable urethane acrylate films. Polymer 45: 6175-6187. https://doi.org/10.1016/j.polymer.2004.07.001 doi: 10.1016/j.polymer.2004.07.001
![]() |
[17] |
Nguyen TA, Nguyen TV, Thai H, et al. (2016) Effect of nanoparticles on the thermal and mechanical properties of epoxy coatings. J Nanosci Nanotechnol 16: 9874-9881. https://doi.org/10.1166/jnn.2016.12162 doi: 10.1166/jnn.2016.12162
![]() |
[18] |
Baiquni M, Soegijono B, Hakim AN (2019) Thermal and mechanical properties of hybrid organoclay/rockwool fiber reinforced epoxy composites. J Phys Conf Ser 1191: 012056. https://doi.org/10.1088/1742-6596/1191/1/012056 doi: 10.1088/1742-6596/1191/1/012056
![]() |
[19] |
Zhang X, Alloul O, He Q, et al. (2013) Strengthened magnetic epoxy nanocomposites with protruding nanoparticles on the graphene nanosheets. Polymer 54: 3594-3604. https://doi.org/10.1016/j.polymer.2013.04.062 doi: 10.1016/j.polymer.2013.04.062
![]() |
[20] |
Nazarenko OB, Melnikova TV, Visakh PM (2016) Thermal and mechanical characteristics of polymer composites based on epoxy resin, aluminium nanopowders and boric acid. J Phys Conf Ser 671: 012040. https://doi.org/10.1088/1742-6596/671/1/012040 doi: 10.1088/1742-6596/671/1/012040
![]() |
[21] |
Sand Chee S, Jawaid M (2019) The effect of Bi-functionalized MMT on morphology, thermal stability, dynamic mechanical, and tensile properties of epoxy/organoclay nanocomposites. Polymers 11: 2012. https://doi.org/10.3390/polym11122012 doi: 10.3390/polym11122012
![]() |
[22] |
Bikiaris D (2011) Can nanoparticles really enhance thermal stability of polymers? Part Ⅱ: An overview on thermal decomposition of polycondensation polymers. Thermochim Acta 523: 25-45. https://doi.org/10.1016/j.tca.2011.06.012 doi: 10.1016/j.tca.2011.06.012
![]() |
[23] |
Xue Y, Shen M, Zeng S, et al. (2019) A novel strategy for enhancing the flame resistance, dynamic mechanical and the thermal degradation properties of epoxy nanocomposites. Mater Res Express 6: 125003. https://doi.org/10.1088/2053-1591/ab537f doi: 10.1088/2053-1591/ab537f
![]() |
[24] |
Colomban P (1989) Structure of oxide gels and glasses by infrared and Raman scattering. J Mater Sci 24: 3011-3020. https://doi.org/10.1007/BF02385660 doi: 10.1007/BF02385660
![]() |
[25] |
Taavoni-Gilan A, Taheri-Nassaj E, Naghizadeh R, et al. (2010) Properties of sol-gel derived Al2O3-15 wt% ZrO2 (3 mol% Y2O3) nanopowders using two different precursors. Ceram Int 36: 1147-1153. https://doi.org/10.1016/j.ceramint.2009.11.011 doi: 10.1016/j.ceramint.2009.11.011
![]() |
[26] |
Noma T, Sawaoka A (1984) Fracture toughness of high pressure sintered Al2O3-ZrO2 ceramics. J Mater Sci Lett 3: 533-535. https://doi.org/10.1007/BF00720992 doi: 10.1007/BF00720992
![]() |
[27] |
Shukla DK, Kasisomayajula SV, Parameswaran V (2008) Epoxy composites using functionalized alumina platelets as reinforcements. Compos Sci Technol 68: 3055-3063. https://doi.org/10.1016/j.compscitech.2008.06.025 doi: 10.1016/j.compscitech.2008.06.025
![]() |
[28] |
Abbate M, Martuscelli E, Musto P, et al. (1994) Toughening of a highly cross-linked epoxy resin by reactive blending with bisphenol A polycarbonate. I. FTIR spectroscopy. J Polym Sci Pol Phys 32: 395-408. https://doi.org/10.1002/polb.1994.090320301 doi: 10.1002/polb.1994.090320301
![]() |
[29] |
Katon JE, Bentley FF (1963) New spectra-structure correlations of ketones in the 700-750 cm-1 region. Spectrochim Acta 19: 639-653. https://doi.org/10.1016/0371-1951(63)80127-7 doi: 10.1016/0371-1951(63)80127-7
![]() |
[30] |
Magnani G, Brillante A (2005) Effect of the composition and sintering process on mechanical properties and residual stresses in zirconia-alumina composites. J Eur Ceram Soc 25: 3383-3392. https://doi.org/10.1016/j.jeurceramsoc.2004.09.025 doi: 10.1016/j.jeurceramsoc.2004.09.025
![]() |
[31] |
Ashamol A, Priyambika VS, Avadhani GS, et al. (2013) Nanocomposites of crosslinked starch phthalate and silane modified nanoclay: Study of mechanical, thermal, morphological, and biodegradable characteristics. Starch-Stärke 65: 443-452. https://doi.org/10.1002/star.201200145 doi: 10.1002/star.201200145
![]() |
[32] |
Jumahat A, Soutis C, Mahmud J, et al. (2012) Compressive properties of nanoclay/epoxy nanocomposites. Procedia Eng 41: 1607-1613. https://doi.org/10.1016/j.proeng.2012.07.361 doi: 10.1016/j.proeng.2012.07.361
![]() |
[33] |
Abbass A, Abid S, Özakça M (2019) Experimental investigation on the effect of steel fibers on the flexural behavior and ductility of high-strength concrete hollow beams. Adv Civ Eng 2019: 8390345. https://doi.org/10.1155/2019/8390345 doi: 10.1155/2019/8390345
![]() |
[34] |
Konnola R, Deeraj BDS, Sampath S, et al. (2019) Fabrication and characterization of toughened nanocomposites based on TiO2 nanowire-epoxy system. Polym Compos 40: 2629-2638. https://doi.org/10.1002/pc.25058 doi: 10.1002/pc.25058
![]() |
[35] |
Zhao S, Schadler LS, Duncan R, et al. (2008) Mechanisms leading to improved mechanical performance in nanoscale alumina filled epoxy. Compos Sci Technol 68: 2965-2975. https://doi.org/10.1016/j.compscitech.2008.01.009 doi: 10.1016/j.compscitech.2008.01.009
![]() |
[36] |
Goyat MS, Rana S, Halder S, et al. (2018) Facile fabrication of epoxy-TiO2 nanocomposites: a critical analysis of TiO2 impact on mechanical properties and toughening mechanisms. Ultrason Sonochem 40: 861-873. https://doi.org/10.1016/j.ultsonch.2017.07.040 doi: 10.1016/j.ultsonch.2017.07.040
![]() |
[37] |
Johnsen BB, Kinloch AJ, Mohammed RD, et al. (2007) Toughening mechanisms of nanoparticle-modified epoxy polymers. Polymer 48: 530-541. https://doi.org/10.1016/j.polymer.2006.11.038 doi: 10.1016/j.polymer.2006.11.038
![]() |
[38] |
Johnsen BB, Kinloch AJ, Taylor AC (2005) Toughness of syndiotactic polystyrene/epoxy polymer blends: microstructure and toughening mechanisms. Polymer 46: 7352-7369. https://doi.org/10.1016/j.polymer.2005.05.151 doi: 10.1016/j.polymer.2005.05.151
![]() |
[39] |
Mohanty A, Srivastava VK (2013) Dielectric breakdown performance of alumina/epoxy resin nanocomposites under high voltage application. Mater Design 47: 711-716. https://doi.org/10.1016/j.matdes.2012.12.052 doi: 10.1016/j.matdes.2012.12.052
![]() |
![]() |
![]() |
1. | Jeng-Tzong Chen, Wei-Chen Tai, Ying-Te Lee, Shing-Kai Kao, An analytical Green’s function for Laplace operator in an infinite plane with two circular holes using degenerate kernels, 2023, 146, 08939659, 108774, 10.1016/j.aml.2023.108774 |
![]() |
![]() |
![]() |