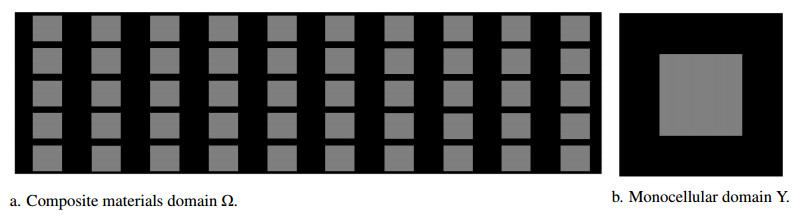
In this paper, a topology optimization algorithm for the mechanical-electrical coupling problem of periodic composite materials is studied. Firstly, the homogenization problem of the mechanical-electrical coupling topology optimization problem of periodic composite materials is established by the multi-scale asymptotic expansion method. Secondly, the topology optimization algorithm for the mechanical-electrical coupling problem of periodic composite materials is constructed by finite element method, solid isotropic material with penalisation method and homogenization method. Finally, numerical results show that the proposed algorithm is effective to calculate the optimal structure of the periodic composite cantilever beam under the influence of the mechanical-electrical coupling.
Citation: Ziqiang Wang, Chunyu Cen, Junying Cao. Topological optimization algorithm for mechanical-electrical coupling of periodic composite materials[J]. Electronic Research Archive, 2023, 31(5): 2689-2707. doi: 10.3934/era.2023136
[1] | Mingtao Cui, Wennan Cui, Wang Li, Xiaobo Wang . A polygonal topology optimization method based on the alternating active-phase algorithm. Electronic Research Archive, 2024, 32(2): 1191-1226. doi: 10.3934/era.2024057 |
[2] | Wen Li, Jian Wang, Zhanpeng Du, Hongfeng Ma, Lijie Zhang, Libin Duan . Lightweight design method and application of MEWP bracket based on multi-level optimization. Electronic Research Archive, 2022, 30(12): 4416-4435. doi: 10.3934/era.2022224 |
[3] | Moutian Liu, Lixia Duan . In-phase and anti-phase spikes synchronization within mixed Bursters of the pre-Bözinger complex. Electronic Research Archive, 2022, 30(3): 961-977. doi: 10.3934/era.2022050 |
[4] | Furong Xie, Yunkai Gao, Ting Pan, De Gao, Lei Wang, Yanan Xu, Chi Wu . Novel lightweight connecting bracket design with multiple performance constraints based on optimization and verification process. Electronic Research Archive, 2023, 31(4): 2019-2047. doi: 10.3934/era.2023104 |
[5] | Mingtao Cui, Wang Li, Guang Li, Xiaobo Wang . The asymptotic concentration approach combined with isogeometric analysis for topology optimization of two-dimensional linear elasticity structures. Electronic Research Archive, 2023, 31(7): 3848-3878. doi: 10.3934/era.2023196 |
[6] | Yun Ni, Jinqing Zhan, Min Liu . Topological design of continuum structures with global stress constraints considering self-weight loads. Electronic Research Archive, 2023, 31(8): 4708-4728. doi: 10.3934/era.2023241 |
[7] | Mingtao Cui, Min Pan, Jie Wang, Pengjie Li . A parameterized level set method for structural topology optimization based on reaction diffusion equation and fuzzy PID control algorithm. Electronic Research Archive, 2022, 30(7): 2568-2599. doi: 10.3934/era.2022132 |
[8] | Yuanfei Li . A study on continuous dependence of layered composite materials in binary mixtures on basic data. Electronic Research Archive, 2024, 32(10): 5577-5591. doi: 10.3934/era.2024258 |
[9] | Haolei Wang, Lei Zhang . Energy minimization and preconditioning in the simulation of athermal granular materials in two dimensions. Electronic Research Archive, 2020, 28(1): 405-421. doi: 10.3934/era.2020023 |
[10] | Ibrahim M. Hezam, Aref M. Al-Syadi, Abdelaziz Foul, Ahmad Alshamrani, Jeonghwan Gwak . Evaluation of nanostructured electrode materials for high-performance supercapacitors using multiple-criteria decision-making approach. Electronic Research Archive, 2023, 31(4): 2286-2314. doi: 10.3934/era.2023117 |
In this paper, a topology optimization algorithm for the mechanical-electrical coupling problem of periodic composite materials is studied. Firstly, the homogenization problem of the mechanical-electrical coupling topology optimization problem of periodic composite materials is established by the multi-scale asymptotic expansion method. Secondly, the topology optimization algorithm for the mechanical-electrical coupling problem of periodic composite materials is constructed by finite element method, solid isotropic material with penalisation method and homogenization method. Finally, numerical results show that the proposed algorithm is effective to calculate the optimal structure of the periodic composite cantilever beam under the influence of the mechanical-electrical coupling.
Structural optimization of piezoelectric composites is one of the hot issues in structural design of materials. Piezoelectric composites are widely used in aircraft structure, electronic information technology and semiconductor materials [1,2]. Composite materials generally have some small periodicity, which makes it difficult to solve the differential equations that describe piezoelectric problems theoretically. For piezoelectric phenomena of composite structures, a simple and effective algorithm is developed based on the idea of homogenization[3,4]. In [5], the homogenization method is used to establish a numerical algorithm for calculating the optimal design of composite structures. In [6], mainly presented a multi-scale and multi-material topology optimization algorithm for designing cellular structure. The reference [7] proposed a topology optimization method for structural heat transfer and load carrying capabilities. The optimal structure and microstructure topology optimization methods of materials are presented in [8]. In [9], a piezoelectric plate energy harvester of in-plane harmonic energy is studied, and proposed a topology optimization algorithm of two-dimensional piezoelectric material model, which minimizes the numerical instability. A topology optimization algorithm is proposed based on probabilistic reliability for piezoelectric uncertainty, and established a nested double-loop optimization algorithm to satisfy the displacement performance in [10]. For multi-scale structural topology optimization, in [11], mainly studies a two-scale concurrent topology optimization design of multi-micro heterogeneous materials. The two-scale design optimization problem of minimizing structural compliance under the constraints of seepage flow rate and material void is studied in [12]. In [13], a hierarchical topology optimization design method applied to single scale microstructure of mechanical materials is proposed. The finite element method is introduced through the homogenization method of composite materials, and the homogenization constant of composite materials is realized by the program [14,15,16]. A structure-material design two-scale optimization methods in the framework of level set method presented in [17]. In reference [18,19] proposed a topology optimization design method for solids and fluids periodicity and microstructure of porous materials. In [20], based on the multi-material topology optimization, some materials with fully combined bi-functions are developed and proposed a method for selecting reasonable parameters. A topology optimization algorithm to improve the alternating active phase and object of multiple materials and a new formula to overcome convergent oscillations are presented in [21]. A two-scale parallel optimization method is proposed and applied to the macroscopic and microscopic structures, finally, compared the optimized gradient and uniform graded lattice structures in [22]. In [23], mainly proposed a multi-material topology optimization algorithm and candidate material selection criteria, and applied the topology optimization algorithm to the compliance minimization problem. In [24], this paper mainly studies the bending behavior of three-dimensional periodic composite plates and designs a two-scale computing method, which is used to solve the effective parameters and displacement strains of the composite plates. A method of constructing a higher order scheme for numerical solutions of the fractional ordinary differential equations is proposed in [25]. The high-order numerical scheme of caputo time fractional differential equation with uniform accuracy is constructed by constructing high-order finite difference method and local truncation error in [26]. An effective topology optimization method for macrostructure and their corresponding parameterized microstructure is presented in [27]. In [28], a topology optimization algorithm based on level set composites is proposed, and the algorithm is applied to the compliance minimization of linear elastic problems. It established a two-scale coupling relationship between potential and displacement and analyzed some improved asymptotic error estimates in [29]. The structure optimization algorithm of piezoelectric material plate is established by moving asymptote method, and the program experiment is given by Matlab in [30]. For more practical applications, see [31,32].
According to the current literature research, there are few mechanical-electrical coupling topology optimization algorithms for piezoelectric composites. This paper constructs a structural optimization algorithm for the electro-mechanical coupling problem of composite materials based on the two-scale asymptotic expansion method. The algorithm is used to calculate the optimization problem of cantilever beam structure. This paper is arranged as follows: construction and analysis of topological optimization method for electro-mechanical coupling problems of periodic composite materials in Section 2. In Section 3, establish a topological optimization algorithm for the electro-mechanical coupling problem of periodic composite materials, and the topology optimization structure of fine mesh and homogenized solution were compared. Finally, some conclusions are given in Section 4.
Nomenclature | |||
List of Symbols | |||
Eε | Young's modulus(N/m2) | ρ | Density(kg/m3) |
Eε0 | Young's modulus for void materials(N/m2) | λε,με | Lame constants |
Eε1 | Young's modulus for solid materials(N/m2) | fi | Body forces(N) |
Cθ,εijhk | Elastic constant(N/m2) | uεk | Displacement field(m) |
Cθ,εijhk(0) | Elastic constant for void materials(N/m2) | ti | Surface load(N) |
Cθ,εijhk(1) | Elastic constant for solid materials(N/m2) | θ | Design variable |
eθ,εijk | Piezoelectric constant(C/m2) | ν | Poisson's ratio |
eθ,εijk(0) | Piezoelectric constant for void materials(C/m2) | G | Original sensitivity |
eθ,εijk(1) | Piezoelectric constant for solid materials(C/m2) | Gr | Smoothed sensitivity |
bθ,εij | Dielectric constant(F/m) | δGr | The variation of Gr |
bθ,εij(0) | Dielectric constant for void materials (F/m) | γi | Positive constant |
bθ,εij(1) | Dielectric constant for solid materials(F/m) | χk,ˉλ,ϕ | Lagrange multiplier |
Φε | Electric potential field(V) | move | Density change |
p | Penalization factor | η | Damping coefficient |
q | Concentrated electric loads(C) | ϑ | Volume constraint |
Kh0(Y) | Finite element spaces | Kh1(Y) | Finite element spaces |
Suppose a cantilever beams with length W and width L were considered in the simulations. As shown in Figure 1, let Ω be a bounded domain with Lipschitz boundary. In what follows, Latin indices take numbers in 1, 2, 3, while Greek ones only run over 1, 2. In addition, we shall constantly use the Einstein summation convention.
The famous material interpolation schemes is the density-based method. For non-isotropic piezoelectric material, the interpolation function is the extension of solid isotropic microstructure with penalization (SIMP) scheme which can be written as follows:
Eε(x)=Eε0(x)+(Eε1(x)−Eε0(x))θp(x),Cθ,εijhk(x)=Cθ,εijhk(0)(x)+(Cθ,εijhk(1)(x)−Cθ,εijhk(0)(x))θp(x),eθ,εkij(x)=eθ,εkij(0)(x)+(eθ,εkij(1)(x)−eθ,εkij(0)(x))θp(x),bθ,εij(x)=bθ,εij(0)(x)+(bθ,εij(1)(x)−bθ,εij(0)(x))θp(x). | (2.1) |
It is noted that the parameter θ(x) is a design variable. Similarly, the Lame parameters describing the mechanical properties of a solid can be expressed as follows:
λε(x)=νEε(x)(1+ν)(1−2ν), με(x)=Eε(x)2(1+ν). | (2.2) |
Consider the following minimization of mechanical-electrical coupling problem for two-dimensional periodic composite materials, the objective function is described as:
minθJ(θ)=∫Ωfi(x)uεi(x)θ(x)dx+∫Btti(x)uεi(x)ds−∫Ωρ(x)Φε(x)θ(x)dx−∫Bϕq(x)Φε(x)ds, | (2.3) |
subject to
{−∂∂xj(Cθ,εijkl(x)∂uεk(x)∂xl+eθ,εkij(x)∂Φε(x)∂xk)=fi(x)θ(x), inΩ,−∂∂xi(bθ,εij(x)∂Φε(x)∂xj−eθ,εijk(x)∂uεk(x)∂xj)=ρ(x)θ(x), inΩ,uεk(x)=0, onBu,(∂uεk(x)∂xlCθ,εijkl(x)+eθ,εkij(x)∂Φε(x)∂xk)nj=ti(x), onBt,(∂Φε(x)∂xjbθ,εij(x)−eθ,εijk(x)∂uεk(x)∂xj)ni=q(x), onBϕ,Φε(x)=0, onBq,∫Ωθ(x)dx/|Ω|≤ϑ,0≤θ(x)≤1, | (2.4) |
where fi(x) is the body force, ρ(x) is the density of charge, ϑ is volume constraint, n is a normal vector, uεk(x) is the displacement vector, Φε(x) is the scalar electric potential field, ti(x) is surface traction force, q(x) denotes the electric body charge, and the boundary ∂Ω of Ω is composed of the traction boundary Bt and the displacement boundary Bu with Bu∩Bt=0 and Bu∪Bt=∂Ω. Similarly, the electrical boundary Ω is divided into two parts, the electric potential boundary Bϕ and the electric loads boundary Bq with Bϕ∩Bq=0 and Bϕ∪Bq=∂Ω.
Assume that all coefficients satisfy the following conditions
(I) Cθ,εijhk(x)=Cθijhk(ξ),eθ,εijk(x)=eθijk(ξ),bθ,εij(x)=bθij(ξ) is periodic Y and ξ=x/ε;
(II) Cθ,εijhk(x) satisfies the following coercive condition Ξ(k1,k2), s.t.,
{Cθ,εijhk(x)=Cθ,εjikh(x)=Cθ,εijkh(x),k1ζihζih≤Cθ,εijhk(x)ζihζjk≤k2ζjkζjk, |
where {ζih} is real elements with arbitrary symmetric matrix, k1 and k2 are positive constants independent of ε;
(III) bθ,εij(x) satisfies the following positive definite condition:
bθ,εij(x)=bθ,εji(x), τ1ζiζi≤bθ,εij(x)ζiζj≤τ2ζjζj, |
where {ζi} is an arbitrary vector with real element, τ1 and τ2 are constants greater than zero independent of ε;
(IV) For tensor eθ,εijk(x), we assume that eθ,εijk(x)=eθ,εikj(x).
Theorem 2.1. Assume that the homogenization coefficients ˆCθijhk,ˆeθijk and ˆbθij satisfy the conditions (I)–(IV), then the homogenization problem of Eq (2.3) is as follows:
minθJ(θ)=∫Ωfi(x)u0i(x)θ(x)dx+∫Btti(x)u0i(x)ds−∫Ωρ(x)Φ0(x)θ(x)dx−∫Bϕq(x)Φ0(x)ds, |
and satisfy the following equations
{−∂∂xj(ˆCθijkl∂u0k(x)∂xl+ˆeθkij∂Φ0(x)∂xk)=fi(x)θ(x),inΩ,−∂∂xi(ˆbθij∂Φ0(x)∂xj−ˆeθijk∂u0k(x)∂xj)=ρ(x)θ(x),inΩ,u0k(x)=0,onBu,(ˆCθijkl∂u0k(x)∂xl+ˆeθkij∂Φ0(x)∂xk)nj=ti(x),on Bt,(ˆbθij∂Φ0(x)∂xj−ˆeθijk∂u0k(x)∂xj)ni=q(x),onBϕ,Φ0(x)=0,onBq,∫Ωθ(x)dx/|Ω|≤ϑ,0≤θ(x)≤1. | (2.5) |
Let's define the coefficients of homogenization ˆCθijhk,ˆeθijk and ˆbθij as follows:
ˆCθijhk=1|Y|∫Y[Cθijhk(ξ)+Cθijlm(ξ)∂(Nhk(ξ))l∂ξm+eθlij(ξ)∂Ghk(ξ)∂ξl]dξ, | (2.6) |
ˆeθijk=1|Y|∫Y[eθijk(ξ)+Cθijlm(ξ)∂(Mk(ξ))l∂ξm+eθlij(ξ)∂Hk(ξ)∂ξl]dξ, | (2.7) |
ˆbθij=1|Y|∫Y[bθij(ξ)−eθilm(ξ)∂(Mj(ξ))l∂ξm+bθik(ξ)∂Hj(ξ)∂ξk]dξ, | (2.8) |
where H(ξ),G(ξ),M(ξ),N(ξ) are Y-periodic in ξ and defined by as follows
{∂∂ξj(eθkij(ξ)∂Hα1(ξ)∂ξk)+∂∂ξj(Cθijhk(ξ)∂(Mα1(ξ))h∂ξk)+∂∂ξj(eθα1ij(ξ))=0,in Ω, ∂∂ξi(−bθij(ξ)∂Hα1(ξ)∂ξj)+∂∂ξi(eθikj(ξ)∂(Mα1(ξ))k∂ξj)−∂∂ξi(bθα1i(ξ))=0, in Ω,∫ΩMα1(ξ)dξ=0,∫ΩHα1(ξ)dξ=0, | (2.9) |
and
{∂∂ξj(Cθijhk(ξ)∂(Nα1m(ξ))h∂ξk)+∂∂ξj(Cθijα1m(ξ))+∂∂ξj(eθkij(ξ)∂Gα1m(ξ)∂ξk)=0,in Ω,∂∂ξi(−bθij(ξ)∂Gα1m(ξ)∂ξj)+∂∂ξi(eθikj(ξ)∂(Nα1m(ξ))k∂ξj)+∂∂ξi(eθimα1(ξ))=0, in Ω,∫ΩNα1m(ξ)dξ=0,∫ΩGα1m(ξ)dξ=0. | (2.10) |
Proof. For a detailed proof, see Appendix A.
The sensitivity analysis is derived by the Lagrange multiplier L, for the optimization problem of mechanical-electrical coupling of the discussed composite materials, the Lagrange multiplier can be defined as:
L(ˉu0(x),ˉΦ0(x),θ(x),ˉχ(x),ˉϕ(x))=J(θ)−∫Ωfi(x)ˉχi(x)θ(x)dx−∫Btti(x)ˉχi(x)ds +∫Ωρ(x)ˉϕ(x)θ(x)dx+∫Ω(ˆeθkij(ξ)∂ˉΦ0(x)∂xi)∂ˉχk(x)∂xjdx+∫Ω(ˆeθijk(ξ)∂ˉu0k(x)∂xj)∂ˉϕ(x)∂xidx +∫Ω(ˆCθijkl(ξ)∂ˉu0k(x)∂xl)∂ˉχi(x)∂xjdx+∫Bϕq(x)ˉϕ(x)ds−∫Ω(ˆbθij(ξ)∂ˉΦ0(x)∂xj)∂ˉϕ(x)∂xidx, | (2.11) |
where (ˉu0(x),ˉχ(x))∈U is a vector-valued function, ˉχ(x) is the Lagrange multiplier of the governing equation and the Neumann boundary condition on Bt, (ˉΦ0(x),ˉϕ(x))∈Z is a quantity-valued function, ˉϕ(x) is the Lagrange multiplier of the governing equation and the Neumann boundary condition on Bϕ. The dual spaces of U and Z are U′ and Z′, respectively.
Theorem 2.2. Suppose ˉu0k(x)∈U and ˉΦ0(x)∈Z are locally optimal solutions of (2.5), then there are χk(x)∈U′ and ϕ(x)∈Z′, both of which satisfied the following conditions:
{∂∂xj(ˆCθijkl∂χk(x)∂xl+ˆeθijk∂ϕ(x)∂xk)=fi(x)θ(x),inΩ,∂∂xi(ˆbθij∂ϕ(x)∂xj−ˆeθkij∂χk(x)∂xj)=ρ(x)θ(x), in Ω,χk(x)=0,onBu,−(ˆCθijkl∂χk(x)∂xl+ˆeθijk∂ϕ(x)∂xk)nj=ti(x), onBt,−(ˆbθij∂ϕ(x)∂xj−ˆeθkij∂χk(x)∂xj)ni=q(x),onBϕ,ϕ(x)=0,onBq. | (2.12) |
Proof. The partial derivative of Eq (2.11) with respect to ˉu0k(x) in the direction δˉu0k(x) at a stationary point (u0k(x),χk(x))∈U leads to
⟨∂L∂ˉu0k(x)(u0(x),Φ0(x),θ(x),χ(x),ϕ(x)),δˉu0k(x)⟩=∫Bttk(x)δˉu0k(x)ds+∫Ωfk(x)δˉu0k(x)θ(x)dx+∫Ω(ˆCθijkl(ξ)∂∂xlδˉu0k(x))∂χi(x)∂xjdx+∫Ω(ˆeθijk(ξ)∂∂xjδˉu0k(x))∂ϕ(x)∂xidx=0. | (2.13) |
Similarly, taking the derivative of Eq (2.11) with respect to ˉΦ0(x) in the direction δˉΦ0(x) at a stationary point (Φ0(x),ϕ(x))∈Z leads to
⟨∂L∂ˉΦ0(x)(u0(x),Φ0(x),θ(x),χ(x),ϕ(x)),δˉΦ0(x)⟩=−∫Ωρ(x)δˉΦ0(x)θ(x)dx−∫Bϕq(x)δˉΦ0(x)ds −∫Ω(ˆbθij(ξ)∂∂xjδˉΦ0(x))∂ϕ(x)∂xidx+∫Ω(ˆeθkij(ξ)∂∂xiδˉΦ0(x))∂χk(x)∂xjdx=0. | (2.14) |
In the third term on the right hand side of (2.13) and (2.14), δˉu0k(x) can commute with χk(x) and δˉΦ0 commute with ϕ(x) due to the symmetric property of the bilinear form, i.e.,
(ˆCθijkl(ξ)∂δˉu0k(x)∂xl)∂χi(x)∂xj=(ˆCθijkl(ξ)∂χi(x)∂xj)∂δˉu0k(x)∂xl, | (2.15) |
(ˆbθij(ξ)∂δˉΦ0(x)∂xj)∂ϕ(x)∂xi=(ˆbθij(ξ)∂ϕ(x)∂xi)∂δˉΦ0(x)∂xj. | (2.16) |
Substituting (2.15) into (2.13) and (2.16) into (2.14) and taking integration by parts lead to the following equation
⟨∂L∂ˉu0k(u0(x),Φ0(x),θ(x),χ(x),ϕ(x)),δˉu0k(x)⟩=∫Ωfk(x)θ(x)δˉu0k(x)dx+∫Bttk(x)δˉu0k(x)ds +∫Btnj(ˆCθijkl(ξ)∂χi(x)∂xj)δˉu0k(x)ds+∫Btnj(ˆeθijk(ξ)∂ϕ(x)∂xi)δˉu0k(x)ds −∫Ω∂∂xl(ˆCθijkl(ξ)∂χi(x)∂xj)δˉu0k(x)dx−∫Ω∂∂xj(ˆeθijk(ξ)∂ϕ(x)∂xi)δˉu0k(x)dx=0, | (2.17) |
and
⟨∂L∂ˉΦ0(x)(u0(x),Φ0(x),θ(x),χ(x),ϕ(x)),δˉΦ0(x)⟩=−∫Ωρ(x)θ(x)δˉΦ0(x)dx−∫Bϕq(x)δˉΦ0(x)ds +∫Ω∂∂xi(bθij(ξ)∂ϕ(x)∂xj)δˉΦ0(x)dx−∫Ω∂∂xi(ˆeθkij(ξ)∂χk(x)∂xj)δˉΦ0(x)dx −∫Bϕnj(ˆbθij(ξ)∂ϕ(x)∂xi)δˉΦ0(x)ds+∫Bϕni(ˆeθkij(ξ)∂χk(x)∂xj)δˉΦ0(x)ds=0. | (2.18) |
For arbitrarily function ˉu0k(x)∈U and ˉΦ0(x)∈Z are locally optimal solutions of (2.5). Theorem 2.2 has been proved.
The finite element method is used to solve the adjoint Eq (2.12) to obtain χk(x) and ϕ(x), which are substituted into J(θ). The sensitivity of the objective function is obtained by taking the derivative of
J(θ)=L(u0(x),Φ0(x),θ(x),χ(x),ϕ(x)). | (2.19) |
With take the derivative of the design variable θ:
⟨∂J∂θ,δθ⟩=∫Ω[fi(x)u0i(x)+(∂ˆCθijkl(ξ)∂θ∂u0k(x)∂xl)∂χi(x)∂xj−ρ(x)Φ0(x)+(∂ˆeθkij(ξ)∂θ∂Φ0(x)∂xi)∂χk(x)∂xj−(∂ˆbθij(ξ)∂θ∂Φ0(x)∂xj)∂ϕ(x)∂xi+ρ(x)ϕ(x)+(∂ˆeθijk(ξ)∂θ∂u0k(x)∂xj)∂ϕ(x)∂xi−fi(x)χi(x)]δθdx=∫Ω∂J∂θδθdx. |
Then the objective function of the sensitivity analysis is following as:
∂J∂θ=fi(x)u0i(x)−ρ(x)Φ0(x)+(∂ˆCθijkl(ξ)∂θ∂u0k(x)∂xl)∂χi(x)∂xj−fi(x)χi(x)+ρ(x)ϕ(x)+(∂ˆbθij(ξ)∂θ∂Φ0(x)∂xj)∂ϕ(x)∂xi−(∂ˆeθkij(ξ)∂θ∂Φ0(x)∂xi)∂χk(x)∂xj+(∂ˆeθijk(ξ)∂θ∂u0k(x)∂xj)∂ϕ(x)∂xi. | (2.20) |
In order to ensure that checkerboard patterns are avoided in the solution of topology optimization problems, some design constraints must be limited. This situation can be eliminated by smoothing sensitivity of objective function J(θ) and material volume V is given by the following equation:
∫Ω(γi∂Gr∂xi∂∂xr(δGr)+Gr(δGr))dx=∫ΩG(δGr)dx, | (2.21) |
where Gr and G are the smoothed and original densities, respectively. δGr is the variation of Gr, γi is a positive constant. Considering only the volume constraint, the structural optimization problem of Eq (2.19) can be expressed as:
minθJ(θ)s.t. ∫Ωθdx/|Ω|≤ϑ,θmin≤θ≤1. | (2.22) |
For the constraint conditions of Eq (2.22), the necessary condition for θ to be optimal is satisfying that a subset of the stability condition of the Lagrange function, so we use the Lagrange multiplier Λ,λ1 and λ2. Then, we have:
˜L(θ,Λ,ˉλ1,ˉλ2)=Λ(∫Ωθdx/|Ω|−ϑ)+∫Ωˉλ1(θmin−1)dx+∫Ωˉλ2(θmin−θ)dx+J(θ). | (2.23) |
Similar references [33], to solve the optimization problem, the Optimality Criteria algorithm is used here which can be written as:
θm+1={max(0,θ−move),if θβb≤max(0,θ−move),min(1,θ+move),if θβb≥min(1,θ−move),θβb, otherwise , | (2.24) |
and β=−∂J∂θ(ˉλ∂V∂θ)−1, where θm+1 represents the value of the density variable in the iterative step m=1,2,...,n, move parameter is the maximum amount of density change, the value of move is considered to be 0.2, b is a damping coefficient and takes the value 0.3, ˉλ is the Lagrange multiplier to augment the volume constrain.
Next, we introduce the optimization algorithm for the mechanical-electrical coupling problem of periodic composites as follows:
1). The geometric structure Y=[0,1]2 and homogenization domain Ω of the reference cell and the material parameters of each material were determined, the two domains are divided into finite element spaces Kh1(Y) and Kh0(Y), where h1 and h2 represent the mesh size of the monocellular domain and finite element respectively;
2). Equations (2.9) and (2.10) of first-order unicellular functions are solved on the finite element domain Kh1(Y), and obtain the first order monocellular solutions Mα1(ξ),Hα1(ξ),Nα1m(ξ) and Gα1m(ξ), and the coefficients of homogenization ˆCθijhk,ˆeθijk and ˆbθij. Interpolation is performed using the calculated homogenization coefficients at these mesh points, finally, we can obtain the homogenization coefficients of domain Kh0(Ω);
3). Substituting the homogenization coefficients ˆCθijhk,ˆeθijk and ˆbθij into Eq (2.5) to find Φ0(x) and u0k(x);
4). By solving the adjoint Eq (2.12) of mechanical-electric coupling by finite element method, we can obtain χk(x) and ϕ(x);
5). Substituting Φ0(x), u0(x), χ(x) and ϕ(x) into J(θ) and take the derivative of θ to obtain the sensitivity analysis (2.20);
6). In order to eliminate checkerboard and other problems, smoothing sensitivity (2.21) is used;
7). In order to obtain the optimal solution of the structure, it is necessary to continuously iterate and update the element density value, modify design variables using update scheme (2.23), here we use dichotomy to update the intermediate variable:
(a) Calculate the Lagrange multiplier Λ=(Λmin+Λmax)/2, where Λmin and Λmax represent the upper limit and lower limit of the initial Kuhn-Tucker condition respectively, and substitute into (2.24) to update the design variable θ;
(b) The structural volume ∫Ωθm+1dx is calculated, if ∫Ωθm+1dx−∫Ωϑdx>0, output Λ=Λmin, otherwise print Λ=Λmax;
(c) Repeat (a) and (b) until Λmax>10−40 and (Λmax−Λmin)/(Λmin+Λmax)>10−40, if true, output θm+1=θ, otherwise, go back to step (a).
8). Equations (2.1) and (2.2) were used to update the design variables for each material and calculate the average compliance and volume fraction as well as the variation of the variables;
9). Optimization convergence |θm+1−θm|<10−3, whether the number of iterations is greater than or equal to the maximum number of iterations, if so, output the result, otherwise return step (b).
In this section, we give some numerical results show that the proposed algorithm is effective to calculate the optimal structure of the periodic composite cantilever beam under the influence of the electromechanical coupling. Suppose a cantilever beams Ω with length W=2(m) and width L=0.5(m) were considered in the simulations. As shown in Figure 1, let Ω be a bounded domain with Lipschitz boundary. The boundary ∂Ω of Ω is composed of the traction boundary Bt={x=−0.96∗l+1.04,y=0.625,l∈(0,1)} and the displacement boundary Bu={x=0.04∗l+1.96,y=0,l∈(0,1)}, which do not overlap each other so that Bu∩Bt=0 and Bu∪Bt=∂Ω, a surface traction force ti(x)=−107(N) is applied to the border of Bt. Also consider the electrical boundary Ω is divided into two parts, the electric potential boundary Bϕ={x=0.08∗l+0.96,y=0,l∈(0,1)} and the electric loads boundary Bq, there are Bϕ∩Bq=0 and Bϕ∪Bq=∂Ω. q(x)=10−2(C) denotes the electric body charge applied to the border Bϕ of the design domain. Assume that γi=0.002,λ=0.4,r=0.1,θmin=0.001,Λmin=0,Λmax=100,000,ϑ=0.4(m3), the maximum number of iterations n=300. And the Table 1 shows two different periodic composite material parameters.
PZT5A(Y1) | PZT4A (Y2) | Homogenize material properties |
E1=72×109(N/m2) | E1=76×109(N/m2) | E1=72×109(N/m2) |
E0=E110−9(N/m2) | E0=E110−9(N/m2) | E0=E110−9(N/m2) |
e31=−5.4(C/m2) | e31=−6.98(C/m2) | e31=−6.635(C/m2) |
e310=e3110−9(C/m2) | e310=e3110−9(C/m2) | e310=e3110−9(C/m2) |
e33=15.8(C/m2) | e33=13.84(C/m2) | e33=14.292(C/m2) |
e330=e3310−9(C/m2) | e330=e3310−9(C/m2) | e330=e3310−9(C/m2) |
e15=12.3(C/m2) | e15=13.44(C/m2) | e15=13.217(C/m2) |
e150=e1510−9(C/m2) | e150=e1510−9(C/m2) | e150=e1510−9(C/m2) |
b11=916(F/m) | b11=677(F/m) | b11=743.557(F/m) |
b110=b3310−9(F/m) | b110=b1110−9(F/m) | b110=b1110−9(F/m) |
b33=830(F/m) | b33=618(F/m) | b33=676.708(F/m) |
b330=b3310−9(F/m) | b330=b3310−9(F/m) | b330=b3310−9(F/m) |
In order to illustrate the effectiveness of topology optimization algorithms using solid isotropic material penalization method and homogenization method, some numerical results of periodic composite topology optimization are presented. In other words, the comparison of the mechanical-electrical coupling topology optimization between the composite cantilever in fine mesh which is the reference solution of this problem and the homogeneous cantilever in coarse mesh is shown in Figure 2. It can be seen from a3 and a4 in Figure 2 that the topology optimization results of composite structures are almost unchanged after 200 and 300 iterations. Similarly, it can also be seen from b3 and b4 in Figure 2 that the topology optimization results of homogeneous cantilever are almost unchanged after 200 and 300 iterations. Therefore, this shows that the topology optimization algorithm of material structure is convergent after 300 iterations. It can be seen from a4 and b4 in Figure 2 that the topology optimization result of composite cantilever is consistent with the topology optimization result of homogeneous cantilever. Therefore, it is concluded that the homogeneity method can effectively obtain the topological optimization of the composite.
In the following Figure 3, it shows the convergence curve of the objective function. It can be seen from the curve change that the objective function value is decreasing fast in the first 100 iterations and almost unchanged after 200 iterations. In this paper, we take the topology optimization result of the structure at 300 iterations as the final result of the material structure design. This is consistent with the conclusion in Figure 2.
Table 2 shows the grid information of composite material and homogenization structure respectively. It can be seen from the table 2 that the number of triangles or vertices of the composite material is much greater than that of the homogenization structure. So it can be known that the calculation cost of the fine mesh method is much higher than that of the homogenization method. Therefore the topology optimization algorithm of piezoelectric composite structure based on homogenization theory is very effective.
Macro periodic complex solution | Homogenized solution | |
Triangles | 1,207,779 | 191,601 |
vertices | 606,690 | 96,851 |
In this paper, the topological optimization algorithm and numerical simulation for electro-mechanical coupling problems of composites are discussed. Using the two scale asymptotic method, we prove the homogenization problem of topological optimization electro-mechanical coupling problems of composites. By solving the homogenization problem of the topology optimization problem of the piezoelectric composite structure, we obtained the topology optimization algorithm of the topology optimization problem of the piezoelectric composite structure. The numerical results of the paper show that the results of equivalent homogenized materials are close to the results of calculating composite materials in fine mesh. Therefore the topology optimization algorithm of piezoelectric composite structure based on homogenization theory is effective. The structural optimization of piezoelectric materials has a broad application prospect, which can be used in intelligent sensors, intelligent control, intelligent robots, intelligent home, intelligent transportation and other fields. In addition, structural optimization of piezoelectric materials can also be used to improve the performance, reliability and energy efficiency of electronic components.
In the future work, we will use the topological optimization algorithm to establish the topology optimization algorithm of structural optimization of composite plates of electro-mechanical coupling problems.
Ziqiang Wang was supported by National Natural Science Foundation of China (Grant No. 11961009). Junying Cao was supported by National Natural Science Foundation of China (Grant No. 11901135), Foundation of Guizhou Science and Technology Department, China (Grant No. [2020]1Y015). Ziqiang Wang and Junying Cao were supported by Natural Science Research Project of Department of Education of Guizhou Province (Grant Nos. QJJ2022015 and QJJ2022047).
The authors declare there is no conflicts of interest.
Appendix A: the proof of Theorem 2.1.
Proof. The asymptotic expansion of Φε(x) and uεk(x) is as follows:
Φε(x)=Φ(x,x/ε)=Φ(x,ξ)=Φ0(x,ξ)+εΦ1(x,ξ)+ε2Φ2(x,ξ)+o(ε2), | (A.1) |
uεk(x)=uk(x,x/ε)=uk(x,ξ)=u0k(x,ξ)+εu1k(x,ξ)+ε2u2k(x,ξ)+o(ε2), | (A.2) |
in which x and ξ are two independent variables, and the partial derivative operation is:
∂∂xi→∂∂xi+ε−1∂∂ξi. | (A.3) |
Suppose Φj(x,ξ) and uj(x,ξ)(j=0,1,2),x∈Ω,ξ∈Y are Y-periodic with respect to ξ. Define the operators Hε,Fε,Aε and Wε as follows:
Hε=−∂∂xj(Cθijkl(ξ)∂∂xl), Fε=−∂∂xj(eθkij(ξ)∂∂xk),Aε=−∂∂xi(bθij(ξ)∂∂xj), Wε=∂∂xi(eθkij(ξ)∂∂xj). |
Form (2.4), the mechanical-electrical coupling equations can be written as:
fk(x)θ(x)=Hεuεk+FεΦε=(ε−2H0+ε−1H1+H2)(u0k+εu1k+ε2u2k+o(ε2))(x,x/ε) +(ε−2F0+ε−1F1+F2)(Φ0+εΦ1+ε2Φ2+o(ε2))(x,x/ε), | (A.4) |
ρ(x)θ(x)=Wεuεk+AεΦε=(ε−2W0+ε−1W1+W2)(u0k+εu1k+ε2u2k+o(ε2))(x,x/ε) +(ε−2A0+ε−1A1+A2)(Φ0+εΦ1+ε2Φ2+o(ε2))(x,x/ε), | (A.5) |
where
{H0=−∂∂ξj(Cθijkl(ξ)∂∂ξl), H1=−∂∂ξj(Cθijkl(ξ)∂∂xl)−∂∂xj(Cθijkl(ξ)∂∂ξl),H2=−∂∂xj(Cθijkl(ξ)∂∂xl), F0=−∂∂ξj(eθkij(ξ)∂∂ξk),F1=−∂∂ξj(eθkij(ξ)∂∂xk)−∂∂xj(eθkij(ξ)∂∂ξk), F2=−∂∂xj(eθkij(ξ)∂∂xk),A0=−∂∂ξi(bθij(ξ)∂∂ξj), A1=−∂∂ξi(bθij(ξ)∂∂xj)−∂∂xi(bθij(ξ)∂∂ξj),A2=−∂∂xi(bθij(ξ)∂∂xj), W0=∂∂ξi(eθijk(ξ)∂∂ξj),W1=∂∂ξi(eθijk(ξ)∂∂xj)+∂∂xi(eθijk(ξ)∂∂ξj), W2=∂∂xi(eθijk(ξ)∂∂xj). | (A.6) |
By comparing the ε power coefficients at both ends of Eqs (A.4) and (A.5), (A.1) and (A.2), we can obtain the following equations:
{H0u0k=−F0Φ0,A0Φ0=−W0u0k, in Y,u0k andΦ0 forξ is the period Y. | (A.7) |
{H0u1k=−F0Φ1−F1Φ0−H1u0k, in Y,A0Φ1=−A1Φ0−W0u1k−W1u0k, in Y,u1k andΦ1 forξ is the period Y. | (A.8) |
{H0u2k=fk(x)θ(x)−H1u1k−H2u0k−F0Φ2−F1Φ1−F2Φ0, in Y,A0Φ2=ρ(x)θ(x)−A1Φ1−A2Φ0−W0u2k−W1u1k−W2u0k, in Y,u2k andΦ2 forξ is the period Y. | (A.9) |
For Eq (A.7), we can be further expressed is:
∂∂ξj(eθkij(ξ)∂Φ0∂ξk)+∂∂ξj(Cθijkl(ξ)∂u0k∂ξl)=0, | (A.10) |
∂∂ξi(eθijk(ξ)∂u0k∂ξj)−∂∂ξi(bθij(ξ)∂Φ0∂ξj)=0. | (A.11) |
According to the theory of partial differential equation, both Φ0(x,ξ) and u0k(x,ξ) are independent of microscopic variable ξ, i.e.,
Φ0(x,ξ)=Φ0(x),u0k(x,ξ)=u0k(x). | (A.12) |
Substituting (A.12) into (A.8) yields:
{−(∂∂ξj(Cθijkl(ξ)∂u1k∂ξl)+∂∂ξj(eθkij(ξ)∂Φ1∂ξk))=∂Cθijkl∂ξj(ξ)∂u0k∂xl+∂eθkij∂ξj(ξ)∂Φ0∂xk, −(∂∂ξi(bθij(ξ)∂Φ1∂ξj)−∂∂ξi(eθijk(ξ)∂u1k∂ξj))=∂bθij∂ξi(ξ)∂Φ0∂xj−∂eθijk∂ξi(ξ)∂u0k∂xj,Φ1 and u1k forξ is the period Y. | (A.13) |
By the linear property of (A.12), the operators H0,F0,W0 and A0 refer only to the variable ξ, and the partial derivative operations ∂Φ0∂xj and ∂u0k∂xj are independent of ξ, so it can be solved in the following form
{Φ1(x,ξ)=Hα(ξ)∂Φ0(x)∂xα+Gαm(ξ)∂u0m(x)∂xα,u1(x,ξ)=Nα(ξ)∂u0(x)∂xα+Mα(ξ)∂Φ0(x)∂xα. | (A.14) |
Substituting (A.14) into (A.13), which leads to
{∂∂ξj(eθkij(ξ)∂Hα1(ξ)∂ξk)+∂∂ξj(Cθijhk(ξ)∂(Mα1(ξ))h∂ξk)=−∂∂ξj(eθα1ij(ξ)),in Ω,∂∂ξi(−bθij(ξ)∂Hα1(ξ)∂ξj)+∂∂ξi(eθijk(ξ)∂(Mα1(ξ))k∂ξj)=∂∂ξi(bθα1i(ξ)), in Ω,∫ΩMα1(ξ)dξ=0,∫ΩHα1(ξ)dξ=0, Mα1(ξ),Hα1(ξ) is Y-periodic inξ, | (A.15) |
and
{∂∂ξj(eθkij(ξ)∂Gα1m(ξ)∂ξk)+∂∂ξj(Cθijhk(ξ)∂(Nα1m(ξ))h∂ξk)=−∂∂ξj(Cθijα1m(ξ)),in Ω,∂∂ξi(−bθij(ξ)∂Gα1m(ξ)∂ξj)+∂∂ξi(eθijk(ξ)∂(Nα1m(ξ))k∂ξj)=−∂∂ξi(eθimα1(ξ)), in Ω,∫ΩNα1m(ξ)dξ=0,∫ΩGα1m(ξ)dξ=0, Nα1m(ξ),Gα1m(ξ) is Y-periodic inξ. | (A.16) |
Suppose these three the homogenization coefficients ˆCθijhk, ˆeθijk and ˆbθij satisfy conditions (I)-(IV), Φε(x)∈Z={Φ(x)∈H1(Ω)∣Φ(x)=0 on Bt}, uεk(x)∈U={uk(x)∈[H1(Ω)]2|uk(x)=0 on Bu}, so the monocellular problems (A.15) and (A.16) have unique solutions Mα1(ξ),Hα1(ξ),Nα1m(ξ) and Gα1m(ξ)∈Wper(Y), where Wper(Y)={θ(ξ)∣θ(ξ)∈H1(Ω)}, and θ(ξ) is periodic Y.
All operators of formula (A.9) are expanded as follows:
−∂∂ξj(Cθijkl(ξ)∂u2k∂ξl+eθkij(ξ)∂Φ2∂ξk)=∂∂ξj(Cθijkl(ξ)∂u1k∂xl+eθkij(ξ)∂Φ1∂xk) +∂∂xj(Cθijkl(ξ)∂u1k∂ξl+Cθijkl(ξ)∂u0k∂xl)+∂∂xj(eθkij(ξ)∂Φ1∂ξk+eθkij(ξ)∂Φ0∂xk)+fi(x)θ(x), | (A.17) |
−∂∂ξibθij(ξ)∂Φ2∂ξj+∂∂ξieθijk(ξ)∂u2k∂ξj=∂∂ξi(bθij(ξ)∂Φ1∂xj−eθijk(ξ)∂u1k∂xj) +∂∂xi(bθij(ξ)∂Φ1∂ξj+bθij(ξ)∂Φ0∂xj)−∂∂xi(eθijk(ξ)∂u1k∂ξj−eθijk(ξ)∂u0k∂xj)+ρ(x)θ(x). | (A.18) |
For Eqs (A.17) and (A.18), you average the integral over Y, according to the definition (A.14) of Φ1(x) and u1k(x), and the Y periodicity of Φ2(x) and u2k(x) on ξ, Eqs (A.17) and (A.18) can still be written as:
−∂∂xj{1|Y|∫Y(Cθijlm(ξ)∂(Nhk(ξ))l∂ξm+Cθijhk(ξ)+eθlij(ξ)∂Ghk(ξ)∂ξl)dξ∂u0k(x)∂xh+1|Y|∫Y(Cθijlm(ξ)∂(Mk(ξ))l∂ξm+eθlij(ξ)∂Hk(ξ)∂ξl+eθijk(ξ))dξ∂Φ0(x)∂xk}=fi(x)θ(x), inΩ, | (A.19) |
−∂∂xi{1|Y|∫Y(bθij(ξ)+bθik(ξ)∂Hj(ξ)∂ξk−eθilm(ξ)∂(Mj(ξ))m∂ξl)dξ∂Φ0(x)∂xj−1|Y|∫Y(eθijk(ξ)+eθilm(ξ)∂(Nkj(ξ))m∂ξl−bθil(ξ)∂Gkj(ξ)∂ξl)dξ∂u0k(x)∂xj}=ρ(x)θ(x), inΩ. | (A.20) |
Therefore, the homogenization equations are defined as:
−∂∂xj(ˆCθijkl∂u0k(x)∂xl+ˆeθkij∂Φ0(x)∂xk)=fi(x)θ(x), −∂∂xi(ˆbθij∂Φ0(x)∂xj−ˆeθijk∂u0k(x)∂xj)=ρ(x)θ(x),inΩ, |
where ˆCθijkl,ˆeθkij and ˆbθij are homogenization coefficients, which can be expressed as:
{ˆCθijhk=1|Y|∫Y[Cθijhk(ξ)+Cθijlm(ξ)∂(Nhk(ξ))m∂ξl+eθlij(ξ)∂Ghk(ξ)∂ξl]dξ,ˆeθijk=1|Y|∫Y[eθijk(ξ)+Cθijlm(ξ)∂(Mk(ξ))m∂ξl+eθlij(ξ)∂Hk(ξ)∂ξl]dξ,ˆbθij=1|Y|∫Y[bθij(ξ)−eθilm(ξ)∂(Mj(ξ))m∂ξl+bθik(ξ)∂Hj(ξ)∂ξk]dξ. | (A.21) |
Substituting (A.1) and (A.2) into (2.3) of the objective function, the minimization of mechanical-electrical coupling problem (2.3) can be rewritten as:
minθJ(θ)=∫Ωfi(x)[u0i(x,ξ)+εu1i(x,ξ)+ε2u2i(x,ξ)+o(ε2)]θ(x)dx+∫Btti(x)[u0i(x,ξ)+εu1i(x,ξ)+ε2u2i(x,ξ)+o(ε2)]ds−∫Ωρ(x)[Φ0(x,ξ)+εΦ1(x,ξ)+ε2Φ2(x,ξ)+o(ε2)]θ(x)dx−∫Bϕq(x)[Φ0(x,ξ)+εΦ1(x,ξ)+ε2Φ2(x,ξ)+o(ε2)]ds. |
Assume that ε→0, because of u0k(x,ξ) and Φ0(x,ξ) are independent of ξ, the objective function of homogenization can be defined as:
minθJ(θ)=∫Ωfi(x)u0i(x)θ(x)dx+∫Btti(x)u0i(x)ds−∫Ωρ(x)Φ0(x)θ(x)dx−∫Bϕq(x)Φ0(x)ds. |
The homogenization solution of Φ0(x) and u0k(x) satisfies the homogenization problem (2.5), so Theorem 2.1 is proved.
[1] |
A. C. Eringen, Theory of nonlocal piezoelectricity, J. Math. Phys., 25 (1984), 717–727. https://doi.org/10.1063/1.526180 doi: 10.1063/1.526180
![]() |
[2] |
J. S. Yang, R. C. Batra, Conservation laws in linear piezoelectricity, Eng. Fract. Mech., 51 (1995), 1041–1047. https://doi.org/10.1016/0013-7944(94)00271-I doi: 10.1016/0013-7944(94)00271-I
![]() |
[3] |
M. Deng, Y. Feng, Two-scale finite element for piezoelectric problem in periodic structure, Appl. Math. Mech., 32 (2011), 1525–1540. https://doi.org/10.1007/s10483-011-1521-7 doi: 10.1007/s10483-011-1521-7
![]() |
[4] |
J. Telega, S. Bytner, Piezoelectricity with polarization gradient: homogenization, Mech. Res. Commun., 29 (2002), 53–59. https://doi.org/10.1016/S0093-6413(02)00228-8 doi: 10.1016/S0093-6413(02)00228-8
![]() |
[5] |
G. Allaire, E. Bonnetier, G. Francfort, F. Jouve, Shape optimization by the homogenization method, Numer. Math., 76 (1997), 27–68. https://doi.org/10.1007/s002110050253 doi: 10.1007/s002110050253
![]() |
[6] |
M. Zhou, D. Geng, Multi-scale and multi-material topology optimization of channel-cooling cellular structures for thermomechanical behaviors, Comput. Methods Appl. Mech. Eng., 383 (2021), 113896. https://doi.org/10.1016/j.cma.2021.113896 doi: 10.1016/j.cma.2021.113896
![]() |
[7] |
X. Zhao, M. Zhou, Y. Liu, M. Ding, P. Hu, P. Zhu, Topology optimization of channel cooling structures considering thermomechanical behavior, Struct. Multidiscip. Optim., 59 (2019), 613–632. https://doi.org/10.1007/s00158-018-2087-z doi: 10.1007/s00158-018-2087-z
![]() |
[8] |
L. Ling, J. Yan, G. Cheng, Optimum structure with homogeneous optimum truss-like material, Comput. Struct., 86 (2008), 1417–1425. https://doi.org/10.1016/j.compstruc.2007.04.030 doi: 10.1016/j.compstruc.2007.04.030
![]() |
[9] |
A. Homayouni-Amlashi, A. Mohand-Ousaid, M. Rakotondrabe, Topology optimization of 2DOF piezoelectric plate energy harvester under external in-plane force, J. Micro-Bio Rob., 16 (2020), 65–77. https://doi.org/10.1007/s12213-020-00129-0 doi: 10.1007/s12213-020-00129-0
![]() |
[10] |
B. Yang, C. Cheng, X. Wang, Z. Meng, A. Homayouni-Amlashi, Reliability-based topology optimization of piezoelectric smart structures with voltage uncertainty, J. Intell. Mater. Syst. Struct., 33 (2022), 1975–1989. https://doi.org/10.1177/1045389X211072197 doi: 10.1177/1045389X211072197
![]() |
[11] |
L. Xu, G. Cheng, Two-scale concurrent topology optimization with multiple micro materials based on principal stress orientation, Struct. Multidiscip. Optim., 57 (2018), 2093–2107. https://doi.org/10.1007/s00158-018-1916-4 doi: 10.1007/s00158-018-1916-4
![]() |
[12] |
S. Xu, G. Cheng, Optimum material design of minimum structural compliance under seepage constraint, Struct. Multidiscip. Optim., 41 (2010), 575–587. https://doi.org/10.1007/s00158-009-0438-5 doi: 10.1007/s00158-009-0438-5
![]() |
[13] |
H. Rodrigues, J. Guedes, M. Bendsoe, Hierarchical optimization of material and structure, Struct. Multidiscip. Optim., 24 (2002), 1–10. https://doi.org/10.1007/s00158-002-0209-z doi: 10.1007/s00158-002-0209-z
![]() |
[14] |
J. Guedes, N. Kikuchi, Preprocessing and postprocessing for materials based on the homogenization method with adaptive finite element methods, Comput. Methods Appl. Mech. Eng., 83 (1990), 143–198. https://doi.org/10.1016/0045-7825(90)90148-F doi: 10.1016/0045-7825(90)90148-F
![]() |
[15] |
E. Andreassen, C. Andreasen, How to determine composite material properties using numerical homogenization, Comput. Mater. Sci., 83 (2014), 488–495. https://doi.org/10.1016/j.commatsci.2013.09.006 doi: 10.1016/j.commatsci.2013.09.006
![]() |
[16] |
G. Cheng, Y. Cai, L. Xu, Novel implementation of homogenization method to predict effective properties of periodic materials, Acta Mech. Sin., 29 (2013), 550–556. https://doi.org/10.1007/s10409-013-0043-0 doi: 10.1007/s10409-013-0043-0
![]() |
[17] |
Y. Wang, M. Wang, F. Chen, Structure-material integrated design by level sets, Struct. Multidiscip. Optim., 54 (2016), 1145–1156. https://doi.org/10.1007/s00158-016-1430-5 doi: 10.1007/s00158-016-1430-5
![]() |
[18] |
J. Guest, J. Prvost, Optimizing multifunctional materials: design of microstructures for maximized stiffness and fluid permeability, Int. J. Solids Struct., 43 (2006), 7028–7047. https://doi.org/10.1016/j.ijsolstr.2006.03.001 doi: 10.1016/j.ijsolstr.2006.03.001
![]() |
[19] |
J. Guest, J. Prvost, Design of maximum permeability material structures, Comput. Methods Appl. Mech. Eng., 196 (2007), 1006–1017. https://doi.org/10.1016/j.cma.2006.08.006 doi: 10.1016/j.cma.2006.08.006
![]() |
[20] |
Z. Han, Z. Wang, K. Wei, Shape morphing structures inspired by multi-material topology optimized bi-functional metamaterials, Compos. Struct., 300 (2022), 116135. https://doi.org/10.1016/j.compstruct.2022.116135 doi: 10.1016/j.compstruct.2022.116135
![]() |
[21] |
Z. Han, K. Wei, Multi-material topology optimization and additive manufacturing for metamaterials incorporating double negative indexes of Poissons ratio and thermal expansion, Addit. Manuf., 54 (2022), 102742. https://doi.org/10.1016/j.addma.2022.102742 doi: 10.1016/j.addma.2022.102742
![]() |
[22] |
M. Costa, A. Sohouli, A. Suleman, Multi-scale and multi-material topology optimization of gradient lattice structures using surrogate models, Compos. Struct., 289 (2022), 115402. https://doi.org/10.1016/j.compstruct.2022.115402 doi: 10.1016/j.compstruct.2022.115402
![]() |
[23] |
X. Huangy, W. Li, A new multi-material topology optimization algorithm and selection of candidate materials, Comput. Methods Appl. Mech. Eng., 386 (2021), 114114. https://doi.org/10.1016/J.CMA.2021.114114 doi: 10.1016/J.CMA.2021.114114
![]() |
[24] |
Z. Wang, J. Cui, Second-order two-scale method for bending behavior analysis of composite plate with 3-D periodic configuration and its approximation, Sci. China Math., 57 (2014), 1713–1732. https://doi.org/10.1007/s11425-014-4831-1 doi: 10.1007/s11425-014-4831-1
![]() |
[25] |
J. Cao, C. Xu, A high order schema for the numerical solution of the fractional ordinary differential equations, J. Comput. Phys., 238 (2013), 154–168. https://doi.org/10.1016/j.jcp.2012.12.013 doi: 10.1016/j.jcp.2012.12.013
![]() |
[26] |
L. Tian, Z. Wang, J. Cao, A high-order numerical scheme for right Caputo fractional differential equations with uniform accuracy, Electron. Res. Arch., 30 (2022), 3825–3854. https://doi:10.3934/era.2022195 doi: 10.3934/era.2022195
![]() |
[27] |
C. Wang, J. Zhu, W. Zhang, S. Li, J. Kong, Concurrent topology optimization design of structures and non-uniform parameterized lattice microstructures, Struct. Multidiscip. Optim., 58 (2018), 35–50. https://doi.org/10.1007/s00158-018-2009-0 doi: 10.1007/s00158-018-2009-0
![]() |
[28] |
P. Gangl, A multi-material topology optimization algorithm based on the topological derivative, Comput. Methods Appl. Mech. Eng., 366 (2020), 113090. https://doi.org/10.1016/j.cma.2020.113090 doi: 10.1016/j.cma.2020.113090
![]() |
[29] |
Y. Feng, M. Deng, X. Guan, The twoscale asymptotic error analysis for piezoelectric problems in the quasi-periodic structure, Sci. China Phys., Mech. Astron., 56 (2013), 1844–1853. https://doi.org/10.1007/s11433-013-5304-1 doi: 10.1007/s11433-013-5304-1
![]() |
[30] |
A. Homayouni-Amlashi, T. Schlinquer, A. Mohand-Ousaid, M. Rakotondrabe, 2D topology optimization MATLAB codes for piezoelectric actuators and energy harvester, Struct. Multidiscip. Optim., 63 (2021), 983–1014. https://doi.org/10.1007/s00158-020-02726-w doi: 10.1007/s00158-020-02726-w
![]() |
[31] |
M. Wang, S. Feng, A. Incecik, G. Krolczyk, Z. Li, Structural fatigue life prediction considering model uncertainties through a novel digital twin-driven approach, Comput. Methods Appl. Mech. Eng., 391 (2022), 114512. https://doi.org/10.1016/j.cma.2021.114512 doi: 10.1016/j.cma.2021.114512
![]() |
[32] |
S. Feng, X. Han, Z. Li, A. Incecik, Ensemble learning for remaining fatigue life prediction of structures with stochastic parameters: a data-driven approach, Appl. Math. Modell., 101 (2022), 420–431. https://doi.org/10.1016/j.apm.2021.08.033 doi: 10.1016/j.apm.2021.08.033
![]() |
[33] |
W. Mason, H. Baerwald, Piezoelectric crystals and their applications to ultrasonics, Phys. Today, 4 (1951), 23–24. https://doi.org/10.1063/1.3067231 doi: 10.1063/1.3067231
![]() |
1. | Zhao Li, Hongyu Xu, Shuai Zhang, Jintao Cui, Xiaofeng Liu, Multi-Material Structures Topology Optimization for Thin-Walled Tube Used by Vehicles Under Static Load: A Review, 2025, 1134-3060, 10.1007/s11831-025-10285-w |
PZT5A(Y1) | PZT4A (Y2) | Homogenize material properties |
E1=72×109(N/m2) | E1=76×109(N/m2) | E1=72×109(N/m2) |
E0=E110−9(N/m2) | E0=E110−9(N/m2) | E0=E110−9(N/m2) |
e31=−5.4(C/m2) | e31=−6.98(C/m2) | e31=−6.635(C/m2) |
e310=e3110−9(C/m2) | e310=e3110−9(C/m2) | e310=e3110−9(C/m2) |
e33=15.8(C/m2) | e33=13.84(C/m2) | e33=14.292(C/m2) |
e330=e3310−9(C/m2) | e330=e3310−9(C/m2) | e330=e3310−9(C/m2) |
e15=12.3(C/m2) | e15=13.44(C/m2) | e15=13.217(C/m2) |
e150=e1510−9(C/m2) | e150=e1510−9(C/m2) | e150=e1510−9(C/m2) |
b11=916(F/m) | b11=677(F/m) | b11=743.557(F/m) |
b110=b3310−9(F/m) | b110=b1110−9(F/m) | b110=b1110−9(F/m) |
b33=830(F/m) | b33=618(F/m) | b33=676.708(F/m) |
b330=b3310−9(F/m) | b330=b3310−9(F/m) | b330=b3310−9(F/m) |
Macro periodic complex solution | Homogenized solution | |
Triangles | 1,207,779 | 191,601 |
vertices | 606,690 | 96,851 |
PZT5A(Y1) | PZT4A (Y2) | Homogenize material properties |
E1=72×109(N/m2) | E1=76×109(N/m2) | E1=72×109(N/m2) |
E0=E110−9(N/m2) | E0=E110−9(N/m2) | E0=E110−9(N/m2) |
e31=−5.4(C/m2) | e31=−6.98(C/m2) | e31=−6.635(C/m2) |
e310=e3110−9(C/m2) | e310=e3110−9(C/m2) | e310=e3110−9(C/m2) |
e33=15.8(C/m2) | e33=13.84(C/m2) | e33=14.292(C/m2) |
e330=e3310−9(C/m2) | e330=e3310−9(C/m2) | e330=e3310−9(C/m2) |
e15=12.3(C/m2) | e15=13.44(C/m2) | e15=13.217(C/m2) |
e150=e1510−9(C/m2) | e150=e1510−9(C/m2) | e150=e1510−9(C/m2) |
b11=916(F/m) | b11=677(F/m) | b11=743.557(F/m) |
b110=b3310−9(F/m) | b110=b1110−9(F/m) | b110=b1110−9(F/m) |
b33=830(F/m) | b33=618(F/m) | b33=676.708(F/m) |
b330=b3310−9(F/m) | b330=b3310−9(F/m) | b330=b3310−9(F/m) |
Macro periodic complex solution | Homogenized solution | |
Triangles | 1,207,779 | 191,601 |
vertices | 606,690 | 96,851 |