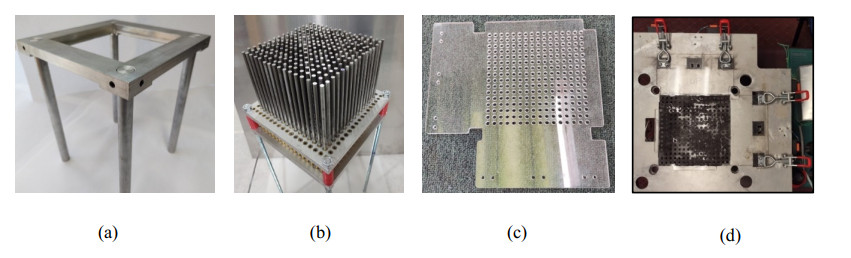
Pad printing is used in automotive, medical, electrical and other industries, employing diverse materials to transfer a 2D image onto a 3D object with different sizes and geometries. This work presents a universal fixation system for pad printing of plastic parts (UFSP4) in response to the needs of small companies that cannot afford to invest in the latest technological advances. The UFSP4 comprises two main subsystems: a mechanical support system (i.e., support structure, jig matrix and braking system) and a control system (i.e., an electronic system and an electric-hydraulic system). A relevant feature is the combination of a jig matrix and jig pins to fixate complex workpieces with different sizes. Using finite element analysis (FEA), in the mesh convergence, the total displacement converges to 0.00028781 m after 12,000 elements. The maximum equivalent stress value is 1.22 MPa for the polycarbonate plate in compliance with the safety factor. In a functionality test of the prototype performed in a production environment for one hour, the jigs fixed by the plate did not loosen, maintaining the satisfactory operation of the device. This is consistent with the displacement distribution of the creep analysis and shows the absence of the creep phenomenon. Based on FEA that underpinned the structural health computation of the braking system, the prototype was designed and built, seeking to ensure a reliable and safe device to fixate plastic parts, showing portability, low-cost maintenance and adaptability to the requirements of pad printing of automotive plastic parts.
Citation: José Alejandro Fernández Ramírez, Óscar Hernández-Uribe, Leonor Adriana Cárdenas-Robledo, Alfredo Chávez Luna. Universal fixation system for pad printing of plastic parts[J]. Mathematical Biosciences and Engineering, 2023, 20(12): 21032-21048. doi: 10.3934/mbe.2023930
[1] | Choonsung Shin, Sung-Hee Hong, Hieyoung Jeong, Hyoseok Yoon, Byoungsoo Koh . All-in-one encoder/decoder approach for non-destructive identification of 3D-printed objects. Mathematical Biosciences and Engineering, 2022, 19(12): 14102-14115. doi: 10.3934/mbe.2022657 |
[2] | Tianbao Liu, Yue Li, Xiwen Qin . A Pad$ \acute{e} $ approximation and intelligent population shrinkage chicken swarm optimization algorithm for solving global optimization and engineering problems. Mathematical Biosciences and Engineering, 2024, 21(1): 984-1016. doi: 10.3934/mbe.2024041 |
[3] | Hao Li, Xiaoyu Wen, Haoqi Wang, Guofu Luo, Steve Evans . A methodology for the modular structure planning of product-service systems. Mathematical Biosciences and Engineering, 2019, 16(3): 1489-1524. doi: 10.3934/mbe.2019072 |
[4] | Qiaokang Liang, Jianzhong Peng, Zhengwei Li, Daqi Xie, Wei Sun, Yaonan Wang, Dan Zhang . Robust table recognition for printed document images. Mathematical Biosciences and Engineering, 2020, 17(4): 3203-3223. doi: 10.3934/mbe.2020182 |
[5] | Jingchao Jiang, Chunling Yu, Xun Xu, Yongsheng Ma, Jikai Liu . Achieving better connections between deposited lines in additive manufacturing via machine learning. Mathematical Biosciences and Engineering, 2020, 17(4): 3382-3394. doi: 10.3934/mbe.2020191 |
[6] | Wenfa Qi, Wei Guo, Tong Zhang, Yuxin Liu, Zongming Guo, Xifeng Fang . Robust authentication for paper-based text documents based on text watermarking technology. Mathematical Biosciences and Engineering, 2019, 16(4): 2233-2249. doi: 10.3934/mbe.2019110 |
[7] | Lufeng Yao, Haiqing Wang, Feng Zhang, Liping Wang, Jianghui Dong . Minimally invasive treatment of calcaneal fractures via the sinus tarsi approach based on a 3D printing technique. Mathematical Biosciences and Engineering, 2019, 16(3): 1597-1610. doi: 10.3934/mbe.2019076 |
[8] | Zhan Cui, Jinjin Chu . Design and assessment of a vision computing-based multimedia interaction system for hybrid teaching. Mathematical Biosciences and Engineering, 2023, 20(8): 14718-14733. doi: 10.3934/mbe.2023658 |
[9] | Zulin Xu . An intelligent fault detection approach for digital integrated circuits through graph neural networks. Mathematical Biosciences and Engineering, 2023, 20(6): 9992-10006. doi: 10.3934/mbe.2023438 |
[10] | Tingting Yang, Yi He . Design of intelligent robots for tourism management service based on green computing. Mathematical Biosciences and Engineering, 2023, 20(3): 4798-4815. doi: 10.3934/mbe.2023222 |
Pad printing is used in automotive, medical, electrical and other industries, employing diverse materials to transfer a 2D image onto a 3D object with different sizes and geometries. This work presents a universal fixation system for pad printing of plastic parts (UFSP4) in response to the needs of small companies that cannot afford to invest in the latest technological advances. The UFSP4 comprises two main subsystems: a mechanical support system (i.e., support structure, jig matrix and braking system) and a control system (i.e., an electronic system and an electric-hydraulic system). A relevant feature is the combination of a jig matrix and jig pins to fixate complex workpieces with different sizes. Using finite element analysis (FEA), in the mesh convergence, the total displacement converges to 0.00028781 m after 12,000 elements. The maximum equivalent stress value is 1.22 MPa for the polycarbonate plate in compliance with the safety factor. In a functionality test of the prototype performed in a production environment for one hour, the jigs fixed by the plate did not loosen, maintaining the satisfactory operation of the device. This is consistent with the displacement distribution of the creep analysis and shows the absence of the creep phenomenon. Based on FEA that underpinned the structural health computation of the braking system, the prototype was designed and built, seeking to ensure a reliable and safe device to fixate plastic parts, showing portability, low-cost maintenance and adaptability to the requirements of pad printing of automotive plastic parts.
In small and medium enterprises (SMEs), process technology capabilities include skilled plant personnel and manufacturing processes [1]. Thus, small companies should concentrate on designing and manufacturing products compatible with their technological process capability. Commonly, they use established tools or processes for a more extended period than large companies, for instance, in fixing methods to manufacture or machine a workpiece, where its precision depends on the efficiency of the fixing process [2] as well as the success of the human operator skills [3]. Facing the need to support the design and flexible manufacturing of products in SMEs, industry 4.0 (I4.0) emerges as an ally to reduce manufacturing time and costs, as well as to promote the increment in the quality of the finished part [4] supported by cyber-physical systems (CPS), the Internet of Things (IoT) [5] and additive manufacturing or 3D printing [6].
Pad printing is a technique that transfers a 2D image onto a 3D object. Its base principle is the color taking through the pad made of elastic silicone (etched with a print motif) and can thus adapt to curved surfaces [7]. This process is practical for printing motifs on complex shapes products for diverse industries such as automotive, medical, electrical, textile and others, employing different kinds of material (e.g., plastics, metal, glass, paper and wood) in a cost-efficient manner [8]. In industry, it is necessary to securely fixate and hold the workpiece to avoid displacement during the pad printing task without compromising the output cycle time [9] and achieving the quality and productivity specifications of the workpiece.
Fixtures are fundamental tooling to secure the position and orientation of the workpiece as needed, of either a large or small volume piece or the subtlest and most delicate piece [10]. The fixing procedure strongly affects the final quality of the work, especially when employing traditional fixing methods (e.g., welding, mechanical fasteners, or riveted joints and screws) [11]. Conventional fixtures are not flexible enough to adjust workpieces during machining operations, and their rigidity often reduces the accuracy of the finished surface, increasing production time and cost. Hence, reconfigurations are required to enhance the quick, automatic location and adjustment of a workpiece with high flexibility, greater accuracy and interchangeability [12].
A modular fixture (MF) consists of a series of interlocking construction components such as frames, modular base plates, locators and fastening elements (e.g., clamps, screws and accessories) [13], meaning that it uses a set of parts to fix a wide range of different types of elements during manufacturing operations, leading to some advantages and drawbacks [14]. With this in mind, to support advanced designs of fixtures for flexible manufacturing systems, MF becomes relevant for holding an accurate position of the workpiece to achieve repeatability [15] and as an enabler for adaptable or changeable manufacturing [16].
In this context, the adoption of advanced manufacturing technology gains relevance from improving the efficiency of the processes to accomplish higher productivity and sustainability in the business [17], such as 3D printing for rapid prototyping of complex designs with minimal waste [18]. In this vain, in a manufacturing line, the fixture is changed on each workpiece variant, performing a manual process that results in a more time-consuming task and affects performance indicators in the industry [19]. The motivation of this work is to contribute to the construction of a low-cost fastening or supporting device for the pad printing process that enables the handling of workpieces of different sizes and shapes. In addition, it seeks to offer a CPS device ready for seamless and flexible integration in the pad printing process of SMEs, assisting with a soft transition toward I4.0 adoption.
This work proposes a prototype design and development of a universal fixation system for pad printing of plastic parts (UFSP4). Such a prototype allows a proper and flexible fixation of pieces that could support and improve the quality and efficiency of the pad printing process, and SMEs could benefit by saving time and cost due to no mold use in comparison with traditional methods. The organization of the paper is as follows: Section 2 introduces the core concepts for this study; Section 3 describes materials and methods useful for this work; Section 4 outlines the numerical definition and setup for finite element analysis (FEA); Section 5 discusses a preliminary test and operation of the prototype; and Section 6 presents the conclusions and future work.
In assembly systems, jigs and fixtures are fundamental to holding parts and sub-assemblies in place, directly affecting cost, quality and time [16]. Moreover, structural or adaptive changes impact the equipment design, the joining technology and the number of robots used [20]. Jigs and fixtures hold and locate the workpiece during a machining operation. The former also guides the device in its location, whereas the latter serves as support. For instance, Radhwan et al. [21] analyze the design concept of jigs and fixtures in a semi-auto insertion of an e-ring, considering parameters such as maximums of the deformation, shear stress and holding force and number of contact faces. In the same context, Ma et al. [22] led a study of the jig constraint position and pitch effect on welding deformation. They employ a 3D coordinate measuring device and compare it to numerical simulation analysis.
Clamps are the mechanism that exerts a force on jigs and fixtures, securing the parts [23]. There are different clamping solutions for machining low-volume and high-variability pieces. However, these are expensive or deliver insufficient flexibility [24]. Ju et al. [25] denote the importance of analyzing the clamping deformation of parts under the clamping load with complex boundary conditions for a reliable fixture design and workpiece quality. Moreover, Moussavi et al. [26] study the influence of clamping in the mechanical modeling of dynamics of typical fixture configuration in terms of vibratory characteristics for machining automotive pieces.
Modular fixtures offer universality since the jig pins can be rearranged to fix a variety of object geometries by providing support reactions for parts and preventing slippage and shaking during machining processes [27]. Matejic et al. [28] describe a multi-purpose design consisting of a mounting frame with a larger surface, allowing access to cutting tools to enhance the accessibility, flexibility and stiffness of modular fixtures. Additionally, the importance of flexibility in a fixture system relies on adjusting mechanisms and the capability of the control system to compute, realize locating adjustments and clamping parts, as is the case for automotive body roofs described by Yu et al. [29]. Extra works were found concerning topics such as intelligent reconfigurable fixtures for the rail industry [30], convolutional neural networks for automating the task of fixture layout in automotive parts [31], as well as the visualization of automotive fixture design via virtual reality [32] and the use of case-based reasoning for stamping tooling design [33].
The need for approximate solutions to the behavior of the physical prototype and the nature of the mathematical models, laws, physical principles and operating conditions demands the use of computational techniques such as the finite element method (FEM) [34]. For instance, the work developed by Croppi et al. [35] introduces a methodology for fixture optimization and clamping configuration to guarantee tolerance and stable cutting conditions of thin wall components, using a FEM approach to predict static and dynamic behavior.
Further, Zhu et al. [36] apply a control clamping strategy on the floating fixtures, utilizing FEM to analyze strain energy evolution. Rezaei et al. [37] focus on part tolerance and fixture layout for sheet metal assembly to determine the deviations of the assemblage and genetic algorithms to optimize the locating points for the fixture. Chen et al. [38] use FEA to localize failures of composite sandwich panels with carbon fiber. Another example addresses multi-objective optimization to minimize workpiece deflections due to clamping forces, conducting an FEA with ANSYS software [39]. Veiga et al. [40] study the mechanical behavior in additive manufacturing designs using FEM simulations with MSC Nastran software to manufacture a turret for the clamping parts in the aeronautical industry.
Regarding pad printing, Xu et al. study the factors that affect the quality of images, analyze the effect of cell depth on the transfer process of ink, and conclude that controlling the cell depth at the solid plate of the printed matter is a means of printing quality control [41]. Likewise, Arredondo-Soto et al. [42] implement a plan-do-check-act process for quality improvement in a production line that involves box stamping using a hot stamp machine versus a pad printing machine and find that pad printing is a viable low-cost solution. Lastly, Al Aboud et al. [43] optimize the geometry of silicone rubber for pad printing applications employing FEM.
The I4.0 adoption in SMEs is a progressive and complex transition that implies a digital transformation and challenges involving financial resource constraints, technology awareness and knowledge [44,45]. It enables the connection between machines and human beings through cyber-physical systems [46], the IoT [47] and artificial intelligence [48]. For instance, Li et al. [49] employ an event-based camera to monitor fault diagnosis using a deep neural network and solve situations where sensors do not adjust to a fixing method and space constraints.
This section describes the proposed fully functional prototype, UFSP4, as a comprehensive and tangible artifact close to a final product [50]. The manufacturing process of the UFSP4 comprises two main subsystems: a mechanical support system and a control system. The first includes three components: support structure, jig matrix and braking system, while the second contains two major components: an electronic system and an electric-hydraulic system. Finally, a unit cover protects the main components of the UFSP4 from liquids and dust.
Mechanical support system. In the UFSP4 design, the factors considered for holding a piece on a jig matrix structure for pad printing are the function of the modular element, the geometries and the size of the workpieces [51]. Moreover, the constant parameters include drilled plates, spacer bushings, retainer rods and clamp plates; as for the variable parameters, the height of the clamping rods, the pressure force of the clamping lever and the sliding capability of the clamping rods inside the offset bushing. The first component is a support structure, an aluminum plate of 30 cm × 30 cm × 2.5 cm with a perforation of 2.54 cm on each corner, adapted to accommodate the jig's matrix to give sliding space for the braking plate on the jigs frontally and transversely. An aluminum bar of 37 cm in length and 2.54 cm in diameter passes through each perforation, acting as support legs of the prototype, fixed to the support plate by eight oppressing screws, as observed in Figure 1(a). The second component is the jig matrix, which comprises two aluminum plates of 20 cm × 20 cm with an array of 16 × 16 holes with a total of 256 symmetrical perforations (5.9 mm in diameter) in each plate joined by bronze bushings of 5 cm in length. In addition, stainless-steel jig pins of 18 cm in length and 5.85 mm in diameter traverse each perforation, as seen in Figure 1(b).
The third component is the braking system, which includes a transparent polycarbonate plate and a brake support plate. Figure 1(c) shows the braking polycarbonate plate 6 mm thick and with precision laser-cut to size, matching the perforations on the polycarbonate with the jig matrix and the bushings. The brake support is an aluminum plate with a thickness of 1.5 cm. Its conformation adapts to the structure of the jig matrix and the polycarbonate plate, illustrated in Figure 1(d). The support plate keeps four clamping levers fixed, two in front and two on the right side of the fixture, each lever with a servomotor activating and deactivating it automatically. The braking of the jig pins in a fixed position occurs when the polycarbonate plate pulls to the front and the right side of the device, forcing the polycarbonate and aluminum plates to press against the jig pins. Such plates rub simultaneously with all 256 jig pins, using equal force to retain their downward or upward movement. The necessary tolerance for this effect is due to the minimal difference (a few tenths of millimeters) between the jig pins' diameter and each plate's bushings' diameter.
Control system. The open-loop control system regulates the behavior of the UFSP4 with user intervention for the jig pins to adjust to the workpiece shape and handle the interconnection between the electronic and electro-hydraulic systems. The electronic system, utilizing a microprocessor and a screen, controls the movement of the hydraulic system to position the jig pins at a certain height according to the piece to be pad printed. The block diagram depicted in Figure 2 illustrates the general function of the control system. The core element is the microcontroller, supported by two linear encoders to control the hydraulic motor for positioning the jig pins; an H-bridge card enables bidirectional motor driving, and the servomotors exert pressure over the clamping levers to activate the braking system.
The electronic system of the UFSP4 employs the microcontroller Pic18F46K22, which drives an LCD screen to display data. The system uses a power supply system from a direct voltage source of 12 volts. The 40-pin microcontroller has nanoWatt XLP technology, working with low power consumption and high performance in data processing. Figure 3(a) shows the electronic schematic of the board (through-hole type) created in Protel PCB [52] design software that was printed and immersed in an iron perchloride solution. In addition, Figure 3(b) depicts the spots for electronic components that were inserted and welded with the H bridge and the switched source. The user interface of the electronic system includes a control keypad with a power button on the upper side, three command buttons and a SOC1602D screen series OLED display of 16 × 2 characters, as shown in Figure 3(c). The green button performs as an accept command, the blue button cancels the operation and the red button resets the UFSP4 system.
The electric-hydraulic system of the UFSP4 works for 12 volts DC at 15 amperes. It is responsible for placing the 256 jig pins at the same height on the jig matrix when starting a new clamping for pad printing in conjunction with the electronic system. The speed of the hydraulic system is 0.2 cm/s, both upward and downward, and the stop control works with up and down microswitches. As for the operation, when the hydraulic system plate complies with locating the jig pins at the set point, it will lower to the required level to allow the imprint of the part under the pad printing process shown in Figure 3(d). The tolerance limit at this point is critical but manageable with tolerance analysis tools [53].
Unit's cover. A structural coverage protects the UFSP4 components, comprising four 29 × 30 cm metal sheets with their respective adaptations, molded according to the structure of the prototype and held in place by jack-type screws to ensure its fixation. When the brake support plate and the unit cover pass through its four support legs, the structure becomes more rigid, giving greater solidity and firmness to the entire unit, and aesthetic appearance. Regarding the electronic system, the metal cover includes an inner box with four polycarbonate plates attached to the electronic card structure to avoid damage to the components. Finally, Figure 3(e) illustrates the UFSP4 prototype ready to be used. This solution provides universality since the jig pins can be effortlessly adapted to workpieces, even with irregular geometries, obtaining sufficient support for the piece during the pad printing task, thus avoiding slipping and shaking.
This section presents the material and geometry used in the simulation, the numerical definition and setup of the polycarbonate plate with the element details and parameters used in FEA and the mesh convergence. At the end of this section, the state of plane stress and the stress concentration for the fixture's base and creep behavior are introduced.
Material. The mechanical properties and stress-strain curve profiles of polycarbonate were identified in literature [54,55]. The properties of the polycarbonate used in the numerical simulation are a density of 1197 kg/m3, modulus of elasticity of 2.59 GPa, tensile strength of 30 MPa and Poisson's ratio of 0.3. It is worth mentioning as a limitation of the study that no further mechanical studies and experimental procedures were addressed to obtain stress-strain curve profiles and property values of the material used.
Geometry. The clamping mechanism made with a perforated plate with a matrix of 16 × 16 holes of 5.9 mm diameter can be approximated by plane stress, as shown in Figure 4(a). Therefore, a finite element model was developed for the extrapolation of the stresses of the piece through the nodal displacements of its elements to convert the system of differential equations into a system of algebraic equations for each node that composes the discretization. For the calibration, Figure 4(b) considers a simplified geometry of the polycarbonate plate divided into three regions. Each one was analyzed using purely biaxial loads applied to the edges marked in red, representing the reaction forces to the stress generated by the servomotors when they pull the plate for fixing the workpiece.
The embedded plate (the deflection W = 0) is applied at y = 0 and x = 0.2 m, restricting the piece to produce an elastic deformation that holds the jig pins, and the system triggers the clamps for the mechanical fixation of the part. Since there are no significant variations in time for stresses and deformations, the analysis is static and concentrated on the biaxial load in plane stress, developing an analytical approach in contrast with FEA. Therefore, a continuous isotropic modeled plate of 0.263 m × 0.179 m × 0.006 m was subjected to a linear distributed load with a value of p = 14710 N/m that corresponds to the sum of forces of two servomotors (7355 N/m each one). The force is applied in the holes shown with the black arrows, representing the force of the servomotors (Fs) or anchor force pointed by the red and blue lines, which are pressure one (P1) and pressure two (P2) exerted by the internal forces of the material, as depicted in Figure 4(c).
Element and mesh convergence. FEA was used to predict stresses, displacements, deformations and the safety factor. The FEA employed a mesh of 12,558 solid185 type elements of first order with average dimensions of 6 × 10-3 m using ANSYS 2023 software. Because the used element has 6 degrees of freedom for nodal displacements in x, y and z, it was ideal for extrapolating nodal deformation in stresses (e.g., the von Mises stress) employing Hooke's Law. The computer program allows modeling hyperelasticity, long deflections, creep and plasticity, to name a few. However, the analysis is limited to the domain of an isotropic material with an elastic behavior.
The process of mesh convergence involves the analysis of the impact on the accuracy and computational efficiency of the solution [56]. Figure 5 plots the convergence of calculated displacement (Y-axis) against the number of elements (X-axis). By increasing the number of nodes, the total displacement remains convergent to 0.00028781, as shown by the asymptotic convergence line. Consequently, after 12,000 elements, the numerical solution is convergent.
State of plane stress. The polycarbonate plate is a component with constant thickness. Its operating condition consists of blocking the movement of the jig pins by applying load without such a plate presenting any plastic deformation. Therefore, the mechanical behavior of the piece's material only considers the elastic range (i.e., flexible system). The geometric characteristics of the polycarbonate plate and the boundary conditions of the workpiece allow modeling as a flat element with a constant thickness. As validation, approximations of known geometries were solved and verified with the plane stress state to verify the results' reliability obtained with the finite element numerical simulation. The stress distribution in the surface of the plate induced by the uniformly distributed load is called the biaxial state of stress, and the induced displacement on a flat plate with uniformly distributed loads is applied to its contours [57]. The directional stress within the plate obtained with Hooke's Law and the relationships that associate deformation and displacement are induced by a load.
The values of the in-plane principal stresses are obtained by Eq (1). Thus, σx1,σx2 are the stresses in the directions x1 and x2, and τx1x2 is the maximum in-plane shear stress. Safety factor (SF) is the ratio between the yield strength Sy of the component material and the maximum stress induced on the component by the loads applied.
σ1,2=σx1+σx22±√(σx1−σx22)2+τ2x1x2 | (1) |
Stress concentration. For a given perforations and holes, a variation in the stress of the isotropic solid is due to the reduction of its material, where the stress concentration factor (K) represents this change. Consequently, the direct axial load is unfeasible in the region where the material was removed, causing changes in the stress distribution of the continuous body. The concentration factors are calculated according to the load condition and the stress distribution described by Hibbeler [57] for a rounded piece and a holed piece.
Creep behavior. The fixation or blocking of the jigs for a relatively long period with a polymeric plate can present the phenomenon known as creep. This phenomenon is associated with the viscoelastic deformation in a polymeric component subjected to a load for a while. For the case of the braking plate, this phenomenon could induce the loosening or loss of fixation of the jig pins after a period and, therefore, the loss of the position of the jig pins. The creep model that represents the viscoelastic process that the polycarbonate plate can present is the Bailey-Norton model. It describes the increase in the deformation of the material due to the stress resulting from the mechanical load for a period, expressed in Eq (2), where C1,C2, and C3 are constants that define the material's behavior under specific load conditions obtained from the experimental approach presented by Jazouli et al. [58].
˙ε=C1σC2tC3 | (2) |
In this section, the mechanical characterization of the polycarbonate plate is described through the simulation of the plane stress state for flat plates, where a priority is to guarantee its structural health, followed by an experimental test that exhibits a pad printing case with the UFSP4 using automotive plastic parts. The last part of the section presents the simulation outcomes and device tests.
Structural analysis. Regarding the FEA, the mechanical braking plate modeling includes all the details of its geometry, as shown in Figure 6(a). The maximum equivalent stress value is 1.22 MPa, shown in Figure 6(b). The tensile strength of polycarbonate is 30 MPa, so the piece can work in compliance with an SF > 20, maintaining its structural health. The force that induces each servomotor in the polymeric plate is 7355 N/m, applied in a standard way to the upper-right surface of the perimeter of the fixing plate section. Each of the jigs operates as a restraint of displacement in the plane.
Creep analysis. The structural behavior of the polycarbonate plate with different conditions is obtained with the restriction of 32, 64 and 128 jig pins, as illustrated in Figure 7(a)–(c). A configuration of 60 jig pins corresponding to the perimeter of the plate is also considered for deformation analysis. It is worth mentioning that a smaller number of restricted jigs was not analyzed because the device design would not fulfill the job's purpose.
Figure 8(a)–(d) illustrates the total displacement of the polycarbonate plate after the period of 3600 s in the four evaluated cases (32, 64,128, and 60), where the maximum total deformation increases as the number of fixed jigs reduces. It is due to the load induced by the servomotors on the plate being distributed more evenly with a high number of jigs and concentrated with a smaller number of fixed jigs. The simulations show that the total displacement of the plate remains constant for the case of 1 s, 1800 s and 3600 s, depicted in Table 1. It is assumed that the effort generated by the load during the period evaluated does not present the creep phenomenon. Hence, the jigs fixed by the plate will not loosen and maintain the satisfactory operation of the device.
Jig pins setup | Time (s) | Maximum (m) |
32 jigs | 1, 1800, 3600 | 9.012e-005 |
64 jigs | 1, 1800, 3600 | 7.144e-005 |
128 jigs | 1, 1800, 3600 | 2.737e-005 |
60 jigs | 1, 1800, 3600 | 2.727e-005 |
As part of the verification and validation process, a record of the activities of a sample of pieces for the pad printing process was conducted, identifying challenges and opportunities in the UFSP4 functionality presented in Figure 9 related to the fixation task. The pad printing test with the UFSP4 employed plastic parts of automotive interiors. For instance, Figure 10(a) shows the piece placed in the jig matrix, where the fixture holds it firmly and prevents it from slipping. It exhibits the adaptability of the fixation system according to the geometry of the workpiece. Figure 10(b) illustrates the pad printing process of the piece, and Figure 10(c) depicts a printed motif on the workpiece. Moreover, the plate's behavior evaluation considered a load application period of 1 s, 1800 s and 3600 s (the maximum period for blocking jigs).
The UFSP4 design and building meet the needs of a pad printing SME in Hidalgo, México. In the experimental test, the prototype exhibited adaptability for diverse geometries of pieces. The entire operation of the device showed its full integration of activities in the plant, being functional, efficient and safe. The FEA indicates that the braking plate was not structurally compromised (not exhibiting red dots in the simulation), demonstrating that the whole braking system is safe. Further, during the evaluated period of the simulation, we do not see the creep phenomenon. In the company environment, the UFSP4 integration into the production line presented difficulties, handled by adapting the height and proximity of the jig matrix to the pad printing system. Regarding the UFSP4's operability, the company's workers safely employed the fixturing of plastic pieces to be pad printed.
For the correct use of the device, the worker must know the basic operations of each element and the relationships, observing features such as tensions, displacements, deformations and the security factor. It is worth mentioning that the prototype works with plastic workpieces that do not exceed the dimensions of the jig matrix, which seems a spatial limitation of the full capabilities of the fastening device presented. Nevertheless, the company's goal of pad printing for small pieces was achieved. The use of USFP4 contributes to the efficiency of the pad printing process since it does not require molds. Thus, there are time and cost savings in mold creation, considering that plastic pieces can have different sizes and complex shapes.
This research proposes a UFSP4 prototype that responds to a specific need of an SME devoted to pad printing of plastic parts. The UFSP4 was firmly built and capable of adapting to the workspace of the company's pad printing area. In addition, the device is consistent, solid and easy to operate, not compromising the maintenance budget of the business. The FEA underpins the prototype design by supporting the structural health computation of the braking system. Relevant features of the device are the electronic system that provides precision to operation, the hydraulic system that supplies enough power for uninterrupted work and the system is mobile and portable.
In addition, it generates low waste or contaminants by eliminating the use of molds. As an added value, USFP4 is ready to support the company with a soft transition toward I4.0 adoption. Finally, future work will include the incorporation of enhancements into the USFP4, such as a system based on artificial vision cameras for the pad printing process, enlarging the jig matrix surface for larger dimension pieces, increasing the jig pins number per square centimeter for a finer fixation and real-time control and monitoring to support the task fixation activity.
The authors declare they have not used Artificial Intelligence (AI) tools in the creation of this article.
To the company Plásticos Decorados and Centro de Tecnología Avanzada (CIATEQ A.C.) for the facilities and support to carry out this work. To the Consejo Nacional de Humanidades, Ciencias y Tecnologías (CONAHCYT) for a Ph.D. scholarship support number 500839 and CONAHCYT SNI.
The authors declare there are no conflicts of interest.
[1] |
R. Müller, M. Vette, A. Geenen, Skill-based dynamic task allocation in human-robot-cooperation with the example of welding application, Procedia Manuf., 11 (2017), 13–21. https://doi.org/10.1016/j.promfg.2017.07.113 doi: 10.1016/j.promfg.2017.07.113
![]() |
[2] |
E. Olaiz, J. Zulaika, F. Veiga, M. Puerto, A. Gorrotxategi, Adaptive fixturing system for the smart and flexible positioning of large volume workpieces in the wind-power sector, Procedia CIRP, 21 (2014), 183–188. https://doi.org/10.1016/j.procir.2014.03.193 doi: 10.1016/j.procir.2014.03.193
![]() |
[3] | L. Joyanes, Industria 4.0: La Cuarta Revolución Industrial, 1st edition, Alfaomega Grupo Editor, 2017. |
[4] |
V. Ivanov, F. Botko, I. Dehtiarov, M. Kočiško, A. Evtuhov, I. Pavlenko, et al., Development of flexible fixtures with incomplete locating, Machines, 10 (2022), 493. https://doi.org/10.3390/machines10070493 doi: 10.3390/machines10070493
![]() |
[5] | M. Jones, L. Zarzycki, G. Murray, Does industry 4.0 pose a challenge for the SME machine builder? A case study and reflection of readiness for a UK SME, in Precision Assembly in the Digital Age, Springer, (2019), 183–197. https://doi.org/10.1007/978-3-030-05931-6_17 |
[6] |
Y. Chen, A. Klingler, K. Fu, L. Ye, 3D printing and modelling of continuous carbon fibre reinforced composite grids with enhanced shear modulus, Eng. Struct., 286 (2023), 116165. https://doi.org/10.1016/j.engstruct.2023.116165 doi: 10.1016/j.engstruct.2023.116165
![]() |
[7] | C. Bodenstein, H. M. Sauer, F. Fernandes, E. Dörsam, Assessing and improving edge roughness in pad-printing by using outlines in a one-step exposure process for the printing form, J. Print Media Technol. Res., 8 (2019), 19–27. |
[8] |
T. S. S. Saikumar, Bhanumurthysoppari, C. R. Bandaru, Design and simulation of automated pad printing machine using automation studio, Mater. Today Proc., 45 (2021), 2871–2877. https://doi.org/10.1016/j.matpr.2020.11.813 doi: 10.1016/j.matpr.2020.11.813
![]() |
[9] |
E. Hrušková, M. Matúšová, Š. Václav, Design of construction and controlling of automation technics in order to improve skills of students, Multidiscip. Aspects Prod. Eng., 4 (2021), 120–131. https://doi.org/10.2478/mape-2021-0011 doi: 10.2478/mape-2021-0011
![]() |
[10] | H. Hashemi, A. M. Shaharoun, S. Izman, B. Ganji, Z. Namazian, S. Shojaei, Fixture design automation and optimization techniques: Review and future trends, Int. J. Eng. Trans. B, 27 (2014), 1787–1794. |
[11] |
A. F. Casas Pulido, O. Bohórquez, O. A. González-Estrada, J. Quiroga, A. Pertuz, Adhesive joints for composite materials produced by additive manufacturing, J. Phys. Conf. Ser., 1386 (2019), 012005. https://doi.org/10.1088/1742-6596/1386/1/012005 doi: 10.1088/1742-6596/1386/1/012005
![]() |
[12] |
I. A. Daniyan, A. O. Adeodu, B. I. Oladapo, O. L. Daniyan, O. R. Ajetomobi, Development of a reconfigurable fixture for low weight machining operations, Cogent Eng., 6 (2019), 1579455. https://doi.org/10.1080/23311916.2019.1579455 doi: 10.1080/23311916.2019.1579455
![]() |
[13] |
A. Gameros, S. Lowth, D. Axinte, A. Nagy-Sochacki, O. Craig, H. R. Siller, State of the art in fixture systems for the manufacture and assembly of rigid components: A review, Int. J. Mach. Tools Manuf., 123 (2017), 1–21. https://doi.org/10.1016/j.ijmachtools.2017.07.004 doi: 10.1016/j.ijmachtools.2017.07.004
![]() |
[14] | Y. Kılıçarslan, Modular Fixture Design for CNC Machining Centers, Master thesis, Middle East Technical University in Ankara, Turkey, 2019. |
[15] | P. Raval, N. P. Maniar, S. Thaker, P. Thanki, Industry 4.0 technology: Design and manufacturing of modular fixture, in Recent Advances in Mechanical Infrastructure, Springer, (2021), 411–417. https://doi.org/10.1007/978-981-33-4176-0_35 |
[16] |
H. Tohidi, T. AlGeddawy, Change management in modular assembly systems to correspond to product geometry change, Int. J. Prod. Res., 57 (2019), 6048–6060. https://doi.org/10.1080/00207543.2018.1559374 doi: 10.1080/00207543.2018.1559374
![]() |
[17] |
A. Stornelli, S. Ozcan, C. Simms, Advanced manufacturing technology adoption and innovation: A systematic literature review on barriers, enablers, and innovation types, Res. Policy, 50 (2021), 104229. https://doi.org/10.1016/j.respol.2021.104229 doi: 10.1016/j.respol.2021.104229
![]() |
[18] | A. Sachdeva, R. Agrawal, C. Chaudhary, D. Siddhpuria, D. Kashyap, S. Timung, Sustainability of 3D printing in industry 4.0: A brief review, in 3D Printing Technology for Water Treatment Applications, Elsevier, (2023), 229–251. https://doi.org/10.1016/B978-0-323-99861-1.00010-2 |
[19] |
D. R. Harish, T. Gowtham, A. Arunachalam, M. S. Narassima, D. Lamy, M. Thenarasu, Productivity improvement by application of simulation and lean approaches in an multimodel assembly line, Proc. Inst. Mech. Eng. Part B: J. Eng. Manuf., 2023. https://doi.org/10.1177/09544054231182264 doi: 10.1177/09544054231182264
![]() |
[20] | G. Schuh, G. Bergweiler, F. Fiedler, V. Slawik, C. Ahues, A review of data-based methods for the development of an adaptive engineering change system for automotive body shop, in Proceedings of the Conference on Production Systems and Logistics, Hannover: publish-Ing., (2021), 359–369. https://doi.org/10.15488/11295 |
[21] |
H. Radhwan, M. S. M. Effendi, M. F. Rosli, Z. Shayfull, K. N. Nadia, Design and analysis of jigs and fixtures for manufacturing process, IOP Conf. Ser.: Mater. Sci. Eng., 551 (2019), 012028. https://doi.org/10.1088/1757-899X/551/1/012028 doi: 10.1088/1757-899X/551/1/012028
![]() |
[22] |
N. Ma, H. Huang, H. Murakawa, Effect of jig constraint position and pitch on welding deformation, J. Mater. Process. Technol., 221 (2015), 154–162. https://doi.org/10.1016/j.jmatprotec.2015.02.022 doi: 10.1016/j.jmatprotec.2015.02.022
![]() |
[23] | H. C. Pandit, Jigs and fixtures in manufacturing, Int. J. Eng. Res. Appl., 12 (2022), 50–55. |
[24] |
S. Weckx, S. Robyns, J. Baake, E. Kikken, R. De Geest, M. Birem, et al., A cloud-based digital twin for monitoring of an adaptive clamping mechanism used for high performance composite machining, Procedia Comput. Sci., 200 (2022), 227–236. https://doi.org/10.1016/j.procs.2022.01.221 doi: 10.1016/j.procs.2022.01.221
![]() |
[25] |
K. Ju, C. Duan, J. Kong, Y. Chen, Y. Sun, Clamping deformation of thin circular workpiece with complex boundary in vacuum fixture system, Thin-Walled Struct., 171 (2022), 108777. https://doi.org/10.1016/j.tws.2021.108777 doi: 10.1016/j.tws.2021.108777
![]() |
[26] |
S. Mousavi, M. Guskov, J. Duchemin, P. Lorong, Clamping modeling in automotive flexible workpieces machining, Procedia CIRP, 101 (2021), 134–137. https://doi.org/10.1016/j.procir.2021.04.004 doi: 10.1016/j.procir.2021.04.004
![]() |
[27] |
H. Tohidi, T. AlGeddawy, Planning of modular fixtures in a robotic assembly system, Procedia CIRP, 41 (2016), 252–257. https://doi.org/10.1016/j.procir.2015.12.090 doi: 10.1016/j.procir.2015.12.090
![]() |
[28] |
M. Matejic, B. Tadic, M. Lazarevic, M. Misic, D. Vukelic, Modelling and simulation of a novel modular fixture for a flexible manufacturing system, Int. J. Simul. Model., 17 (2018), 18–29. https://doi.org/10.2507/IJSIMM17(1)407 doi: 10.2507/IJSIMM17(1)407
![]() |
[29] |
K. Yu, S. Wang, Y. Wang, Z. Yang, A flexible fixture design method research for similar automotive body parts of different automobiles, Adv. Mech. Eng., 10 (2018). https://doi.org/10.1177/1687814018761272 doi: 10.1177/1687814018761272
![]() |
[30] |
W. T. Seloane, K. Mpofu, B. I. Ramatsetse, D. Modungwa, Conceptual design of intelligent reconfigurable welding fixture for rail car manufacturing industry, Procedia CIRP, 91 (2020), 583–593. https://doi.org/10.1016/j.procir.2020.02.217 doi: 10.1016/j.procir.2020.02.217
![]() |
[31] |
J. Villena Toro, A. Wiberg, M. Tarkian, Application of optimized convolutional neural network to fixture layout in automotive parts, Int. J. Adv. Manuf. Technol., 126 (2023), 339–353. https://doi.org/10.1007/s00170-023-10995-0 doi: 10.1007/s00170-023-10995-0
![]() |
[32] |
L. Gong, H. Söderlund, L. Bogojevic, X. Chen, A. Berce, Å. Fast-Berglund, et al., Interaction design for multi-user virtual reality systems: An automotive case study, Procedia CIRP, 93 (2020), 1259–1264. https://doi.org/10.1016/j.procir.2020.04.036 doi: 10.1016/j.procir.2020.04.036
![]() |
[33] |
K. J. Jonsson, R. Stolt, F. Elgh, A case-based reasoning method including tooling function for case retrieval and reuse in stamping tooling design, Comput. Aided Des. Appl., 20 (2023), 839–855. https://doi.org/10.14733/cadaps.2023.839-855 doi: 10.14733/cadaps.2023.839-855
![]() |
[34] |
J. P. Cardona, J. J. Leal, J. U. Castellanos, J. E. Ustariz, Soluciones analíticas y numéricas de esfuerzos mecánicos en placas rectangulares isotrópicas, Inf. Tecnol., 32 (2021), 13–24. http://doi.org/10.4067/S0718-07642021000600013 doi: 10.4067/S0718-07642021000600013
![]() |
[35] |
L. Croppi, N. Grossi, A. Scippa, G. Campatelli, Fixture optimization in turning thin-wall components, Machines, 7 (2019), 68. https://doi.org/10.3390/machines7040068 doi: 10.3390/machines7040068
![]() |
[36] |
B. Zhu, Z. Mu, W. He, L. Fan, G. Zhao, Y. Yang, Research on clamping action control technology for floating fixtures, Materials, 15 (2022), 5571. https://doi.org/10.3390/ma15165571 doi: 10.3390/ma15165571
![]() |
[37] |
A. R. Aderiani, M. Hallmann, K. Wärmefjord, B. Schleich, R. Söderberg, S. Wartzack, Integrated tolerance and fixture layout design for compliant sheet metal assemblies, Appl. Sci., 11 (2021), 1646. https://doi.org/10.3390/app11041646 doi: 10.3390/app11041646
![]() |
[38] |
Y. Chen, K. Fu, B. Jiang, Modelling localised progressive failure of composite sandwich panels under in-plane compression, Thin-Walled Struct., 184 (2023), 110552. https://doi.org/10.1016/j.tws.2023.110552 doi: 10.1016/j.tws.2023.110552
![]() |
[39] |
M. M. Rashid, A. A. Khan, M. Usman, M. Ayub, B. Rustam, Optimization of modular fixture layout by minimizing work-piece deformation, Pak. J. Eng. Technol., 4 (2021), 43–51. https://doi.org/10.51846/vol4iss1pp43-51 doi: 10.51846/vol4iss1pp43-51
![]() |
[40] |
F. Veiga, T. Bhujangrao, A. Suárez, E. Aldalur, I. Goenaga, D. Gil-Hernandez, Validation of the mechanical behavior of an aeronautical fixing turret produced by a design for additive manufacturing (DfAM), Polymers, 14 (2022), 2177. https://doi.org/10.3390/polym14112177 doi: 10.3390/polym14112177
![]() |
[41] | Y. Xu, W. Zhang, X. Wei, B. Huang, Research on image quality control technology of pad printing, in China Academic Conference on Printing and Packaging, Springer, (2023), 163–169. https://doi.org/10.1007/978-981-19-9024-3_22 |
[42] |
K. C. Arredondo-Soto, J. Blanco-Fernández, M. A. Miranda-Ackerman, M. M. Solís-Quinteros, A. Realyvásquez-Vargas, J. L. García-Alcaraz, A plan-do-check-act based process improvement intervention for quality improvement, IEEE Access, 9 (2021), 132779–132790. https://doi.org/10.1109/ACCESS.2021.3112948 doi: 10.1109/ACCESS.2021.3112948
![]() |
[43] | A. Al Aboud, E. Dörsam, D. Spiehl, Investigation of printing pad geometry by using FEM simulation, J. Print Media Technol. Res., 9 (2020), 81–93. |
[44] |
E. Pessot, A. Zangiacomi, C. Battistella, V. Rocchi, A. Sala, M. Sacco, What matters in implementing the factory of the future: Insights from a survey in European manufacturing regions, J. Manuf. Technol. Manag., 32 (2021), 795–819. https://doi.org/10.1108/JMTM-05-2019-0169 doi: 10.1108/JMTM-05-2019-0169
![]() |
[45] |
T. Masood, P. Sonntag, Industry 4.0: Adoption challenges and benefits for SMEs, Comput. Ind., 121 (2020), 103261. https://doi.org/10.1016/j.compind.2020.103261 doi: 10.1016/j.compind.2020.103261
![]() |
[46] |
M. Sanchez, E. Exposito, J. Aguilar, Industry 4.0: Survey from a system integration perspective, Int. J. Comput. Integr. Manuf., 33 (2020), 1017–1041. https://doi.org/10.1080/0951192X.2020.1775295 doi: 10.1080/0951192X.2020.1775295
![]() |
[47] | S. H. Moon, Industry 4.0 for advanced manufacturing and its implementation, Eurasian J. Anal. Chem., 13 (2018), 491–497. |
[48] |
B. Tjahjono, C. Esplugues, E. Ares, G. Pelaez, What does industry 4.0 mean to supply chain, Procedia Manuf., 13 (2017), 1175–1182. https://doi.org/10.1016/j.promfg.2017.09.191 doi: 10.1016/j.promfg.2017.09.191
![]() |
[49] |
X. Li, S. Yu, Y. Lei, N. Li, B. Yang, Intelligent machinery fault diagnosis with event-based camera, IEEE Trans. Ind. Inform., 2023. https://doi.org/10.1109/TII.2023.3262854 doi: 10.1109/TII.2023.3262854
![]() |
[50] | K. T. Ulrich, S. D. Eppinger, M. C. Yang, Product Design and Development, 7th edition, McGraw-Hill, 2019. |
[51] | V. Balachandran, Design of Jigs, Fixtures and Press Tools, Notion Press, 2015. |
[52] | Protel 99 SE Training Manual, PCB Design, 2001. Available from: https://www.mikrocontroller.net/attachment/17909/Protel_99_SE_Traning_Manual_PCB_Design.pdf. |
[53] |
A. Corrado, W. Polini, Tolerance analysis tools for fixture design: A comparison, Procedia CIRP, 92 (2020), 112–117. https://doi.org/10.1016/j.procir.2020.05.174 doi: 10.1016/j.procir.2020.05.174
![]() |
[54] | MatWeb, Materials Information Resource, 2023. Available from: https://matweb.com/. |
[55] |
M. Dixit, V. Mathur, S. Gupta, M. Baboo, K. Sharma, N. S. Saxena, Morphology, miscibility and mechanical properties of PMMA/PC blends, Phase Transitions, 82 (2009), 866–878. https://doi.org/10.1080/01411590903478304 doi: 10.1080/01411590903478304
![]() |
[56] |
Y. Chen, L. Ye, H. Dong, Lightweight 3D carbon fibre reinforced composite lattice structures of high thermal-dimensional stability, Compos. Struct., 304 (2023), 116471. https://doi.org/10.1016/j.compstruct.2022.116471 doi: 10.1016/j.compstruct.2022.116471
![]() |
[57] | R. C. Hibbeler, Mechanics of Materials, 11th edition, Pearson, 2022. |
[58] |
S. Jazouli, W. Luo, F. Brémand, T. Vu-Khanh, Nonlinear creep behavior of viscoelastic polycarbonate, J. Mater. Sci., 41 (2006), 531–536. https://doi.org/10.1007/s10853-005-2276-1 doi: 10.1007/s10853-005-2276-1
![]() |
Jig pins setup | Time (s) | Maximum (m) |
32 jigs | 1, 1800, 3600 | 9.012e-005 |
64 jigs | 1, 1800, 3600 | 7.144e-005 |
128 jigs | 1, 1800, 3600 | 2.737e-005 |
60 jigs | 1, 1800, 3600 | 2.727e-005 |