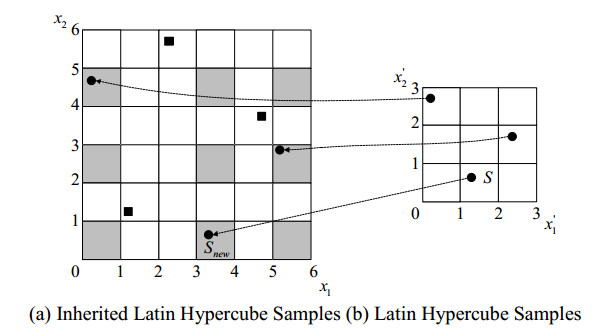
Citation: Ma Jun, Han Xinyu, Xu Qian, Chen Shiyou, Zhao Wenbo, Li Xiaoke. Reliability-based EDM process parameter optimization using kriging model and sequential sampling[J]. Mathematical Biosciences and Engineering, 2019, 16(6): 7421-7432. doi: 10.3934/mbe.2019371
[1] | Xiaoke Li, Fuhong Yan, Jun Ma, Zhenzhong Chen, Xiaoyu Wen, Yang Cao . RBF and NSGA-II based EDM process parameters optimization with multiple constraints. Mathematical Biosciences and Engineering, 2019, 16(5): 5788-5803. doi: 10.3934/mbe.2019289 |
[2] | Xiaoke Li, Qingyu Yang, Yang Wang, Xinyu Han, Yang Cao, Lei Fan, Jun Ma . Development of surrogate models in reliability-based design optimization: A review. Mathematical Biosciences and Engineering, 2021, 18(5): 6386-6409. doi: 10.3934/mbe.2021317 |
[3] | Z. Feng . Final and peak epidemic sizes for SEIR models with quarantine and isolation. Mathematical Biosciences and Engineering, 2007, 4(4): 675-686. doi: 10.3934/mbe.2007.4.675 |
[4] | Zulqurnain Sabir, Hafiz Abdul Wahab, Juan L.G. Guirao . A novel design of Gudermannian function as a neural network for the singular nonlinear delayed, prediction and pantograph differential models. Mathematical Biosciences and Engineering, 2022, 19(1): 663-687. doi: 10.3934/mbe.2022030 |
[5] | Xiaoye Zhao, Yinlan Gong, Lihua Xu, Ling Xia, Jucheng Zhang, Dingchang Zheng, Zongbi Yao, Xinjie Zhang, Haicheng Wei, Jun Jiang, Haipeng Liu, Jiandong Mao . Entropy-based reliable non-invasive detection of coronary microvascular dysfunction using machine learning algorithm. Mathematical Biosciences and Engineering, 2023, 20(7): 13061-13085. doi: 10.3934/mbe.2023582 |
[6] | Jiashuai Li, Xiuyan Peng, Bing Li, Victor Sreeram, Jiawei Wu, Ziang Chen, Mingze Li . Model predictive control for constrained robot manipulator visual servoing tuned by reinforcement learning. Mathematical Biosciences and Engineering, 2023, 20(6): 10495-10513. doi: 10.3934/mbe.2023463 |
[7] | Huiping Zang, Shengqiang Liu, Yi Lin . Evaluations of heterogeneous epidemic models with exponential and non-exponential distributions for latent period: the Case of COVID-19. Mathematical Biosciences and Engineering, 2023, 20(7): 12579-12598. doi: 10.3934/mbe.2023560 |
[8] | Dongning Chen, Jianchang Liu, Chengyu Yao, Ziwei Zhang, Xinwei Du . Multi-strategy improved salp swarm algorithm and its application in reliability optimization. Mathematical Biosciences and Engineering, 2022, 19(5): 5269-5292. doi: 10.3934/mbe.2022247 |
[9] | Martha Garlick, James Powell, David Eyre, Thomas Robbins . Mathematically modeling PCR: An asymptotic approximation with potential for optimization. Mathematical Biosciences and Engineering, 2010, 7(2): 363-384. doi: 10.3934/mbe.2010.7.363 |
[10] | Zulqurnain Sabir, Muhammad Asif Zahoor Raja, Aldawoud Kamal, Juan L.G. Guirao, Dac-Nhuong Le, Tareq Saeed, Mohamad Salama . Neuro-Swarm heuristic using interior-point algorithm to solve a third kind of multi-singular nonlinear system. Mathematical Biosciences and Engineering, 2021, 18(5): 5285-5308. doi: 10.3934/mbe.2021268 |
With high specific strength and good wear resistance, Al 7075 is widely used in die & mould, automobile and aerospace industries. To machine the micro-hole in Al 7075 plate, traditional drilling method can be used. However, due to the weak stiffnesses of drill, the machining precision cannot be guaranteed for some high demanding products. Electrical discharge machining (EDM) is a non-contacting special machining method, which can achieve high precision in processing various shapes in all electrically conductive materials regardless of the hardness [1,2]. Therefore, electrical discharge machining (EDM) becomes a promising method in micro-hole machining of Al 7075 plate. In EDM, the tool electrode is submerged in the dielectric fluid, where the rapid and repetitive spark discharges is conducted [3]. Finally, the workpiece material is removed and the finial surface is formed.
Due to the erosion when sparking occurs from the sides of the electrodes to the workpiece, a gap is observed between the tool electrode and the workpiece, which results in the dimension error of machined workpiece. Moreover, using the least possible tool electrode to machine the most possible workpiece is an effective strategy to reduce the machining cost. Therefore, many researches focus on the methods to improve the EDM machining accuracy and reduce the EDM machining cost. There are many factors affecting the machining performance of EDM, which can be divided into electrical parameters and non-electrical parameters. In literatures, pulse current, pulse on time, pulse off time, corner servo voltage, wire feed rate, wire tension, servo feed, spark gap voltage and dielectric flow rate are all found to have some influence on EDM machining performance such as machining efficiency, machining accuracy, surface integrity, surface roughness (SR), electrode wear rate (EWR) and material removal rate (MRR) [2,4,5,6,7,8,9]. To construct the relationship between EDM parameters and machining performance, many surrogate model and corresponding design of experiment (DOE) methods are introduced. Commonly used surrogate models in EDM are quadratic response surface model (RSM) [4,9], radial basis function (RBF) [10] and support vector regression (SVR) model [7], which are usually built by the central composite design (CCD) [4,9] and Taguchi method [3,6]. Furthermore, to obtain the optimal machining performance, various optimization methods are used in EDM, including particle swarm optimization (PSO) algorithm [5] and genetic algorithm (GA) [7,11].
Great achievements have been made on EDM parameters optimization, but most researches are limited to the multi-objective optimization fields, where Taguchi method is always used to conduct the design of experiment and the grey relational analysis is used to convert the multi-objective optimization problem into single-objective optimization problem [12]. Using Taguchi method to generate the orthogonal array is a viable method, but the sampling efficiency is not so high. Furthermore, possible lack of samples in important regions affects the approximation accuracy of surrogate model. Therefore, more efficient DOE method should be considered in EDM process parameter optimization. Moreover, the slight fluctuations of EDM parameters are unavoidable during the machining process, which are not considered in existing researches. To address this issue, a novel reliability-based EDM process parameter optimization method is proposed. In this paper, the modeling of relationship between EDM parameters and machining performances, the DOE strategy and sequential sampling strategy are considered.
The rest of this paper is framed in the following manner. Section 2 describes the Kriging-based RBDO methods and the sampling criterions used in this paper. Following this, the proposed method including the EDM experiment details and reliability-based EDM optimization flowchart is detailed in Section 3. The optimization process and experimental confirmation are performed in Section 4. Finally, a summary of this new EDM parameter optimization method is concluded.
Different from deterministic optimization methods, Reliability-based design optimization (RBDO) methods are defined as special optimization problems with probabilistic constraints [13]. Generally, RBDO can be formulated as Eq 1 [14]:
find:dmin:Cost(d)s.t.:P(gi(X)⩽0)−Φ(−βti)⩽0,i=1,2,⋯,NdL⩽d⩽dU,d=μ(X) | (1) |
To evaluate the probability of constraint gi(X)⩽0, reliability analysis is needed, where the analytical methods and simulation methods are generally used [15]. The analytical methods such as first order reliability analysis method (FORM) [16,17] are always very efficient, but the potential high error stemming from the performance function approximation make them inapplicable for practical engineering problems. The simulation methods such as MCS [18] and importance sampling (IS) method [19] are more accurate but the computational cost is unbearable if the performance function evaluations are directly called. However, if the surrogate model of implicit performance function is built first and then the simulation methods are conducted by calling the surrogate model, the computation cost can be significantly reduced.
On the other hand, the solution of Eq 1 involves reliability analysis phase and iterative design optimization phase. To handle the coupled relationship between these two phases, double-loop methods, single-loop methods and decoupling methods can be used [20]. Usually, the double-loop methods [21] and the single-loop methods [22] are confronted with efficiency or accuracy problem, thus decoupling methods [23] are preferred in various researches. Among all decoupling methods, SAP has a good performance when combining with surrogate model, thus it's selected in this paper.
Moreover, to reduce the high computational cost in performance function evaluation and iterative design point calculation, various surrogate models including RSM [24], ANN (artificial neural network) [20], SVR [25], RBF [26] and Kriging [27,28] are introduced to solve RBDO problems. Kriging is used in this paper because it can provide an indicator of a priori uncertainty prediction [14].
Kriging is composed of a regression model and stochastic process as Eq 2 [15]:
ˆg(x)=f(x)Tλ+Z(x) | (2) |
Where f(x) is the polynomial regression model with coefficient vector λ. The mean of Gaussion stochastic process Z(x) is zero and the covariance between two different points is expressed as follows [29]:
Cov[Z(x),Z(w)]=σ2ZR(θ,x,w) | (3) |
Where σ2Z is the process variance and R(θ,x,w) is the correlation function. Because the EDM parameters are of different natures, the anisotropic Gaussian model (squared-exponential function) is selected in this paper, which is formulated as Eq 4 [29]:
R(θ,x,w)=∏n1exp[−θi(xi−wi)2] | (4) |
Where xi and wi are the ith coordinate of vector x and w, θi denotes the multiplicative inverse of the correlation length [29].
Design of experiment and active learning strategy are very important for the Kriging-based RBDO [30]. To construct the Kriging model in RBDO, one-stage sampling based methods and sequential sampling based methods can be used [14]. Compared to one-stage sampling, the sampling process of sequential sampling can be controlled, which generally leads to a more accurate surrogate model with fewer samples [14]. There, the sequential sampling method is used in this paper.
In Kriging-based methods, expected feasibility function (EFF) [31] criterion is a promising sequential sampling method, which selects points on constraint boundaries and points with large uncertainty. Therefore, EFF is a viable method for improving the accuracy of Kriging model. Moreover, the selection of initial design point has substantial influence on the efficiency of reliability-based design optimization. In this paper, Inherited Latin Hypercube Sampling (ILHS) is used as the initial sampling method and Expected Feasibility Function (EFF) criterion is considered to add new samples in proposed method.
ILHS is a special DOE method which maintains the uniform distribution property of LHS [32] and contains the specified points [33,34]. To describe the sampling process of ILHS method, a 2-D example with 6 samples is shown in Figure 1. Firstly, every dimensionality (x1 and x2) is divided into 6 intervals, which is equal to the sample number. Then the position of the inherited samples (black squares) is determined and the design space containing samples is removed. After that, 3 LHS samples (black dots in Figure 1b) are generated in reduced design space. Finally, 3 new generated samples are mapped to the original design space, then the ILHS sample set is constructed using the inherited 3 samples (black squares) and the new mapped 3 samples (black dots).
After initial sampling, sequential samples are added to update the Kriging model. EFF sampling criterion has proved its effectiveness [14], thus it's selected in this paper. Moreover, to take the influence of samples on optimization process into consideration, the objective function value is applied to select sequential samples. Therefore, a new sequential sampling criterion is formulated as Eq 5:
OEFF=c(x)uG[2Φ(−uGσG)−Φ(−2σG−uGσG)−Φ(2σG−uGσG)]−c(x)σG[2ϕ(−uGσG)−ϕ(−2σG−uGσG)−ϕ(2σG−uGσG)]+2c(x)σG[Φ(2σG−uGσG)−Φ(−2σG−uGσG)] | (5) |
Where uG and σG are the performance function prediction value and prediction variance at x respectively. c(x) is the objective function prediction value of x. Because the objective function value is combined with the expected feasibility function, the proposed sampling method is termed as the OEFF criterion. Using OEFF, the samples with smaller objective function value, prediction error and distance to constraint boundary will be the priority to update the Kriging model.
According to the research of Gopalakannan [3] and Jia [35], peak current, pulse on time and pulse off time have statistical significance on material removal rete, electrode wear ratio and electrode zoom value (the dimension difference between the electrode and finished workpiece) [3,34]. Therefore, these processing parameters are selected as the design variables in this paper. The unites of these EDM parameters are A, μs and μs, respectively.
Dimension of the finished workpiece is greater than that of the electrode, the reason is that the erosion is caused by sparking from the sides of the electrodes to the workpiece [2]. But the dimension difference (aperture gap) must be controlled in a reasonable range to ensure the size accuracy of the finished hole. Therefore, the aperture gap is selected as the probabilistic constraint in this paper. The unit of the aperture gap is mm.
Besides aperture gap, electrode wear is also considered for evaluating the machining performance, which is termed as the optimization objective to reduce the machining cost as much as possible. As mentioned above, these two performance characteristics correlated with input machining parameters such as peak current, pulse on time and pulse off time. Electrode wear w is termed as the wear in electrode length, which can be calculated by the difference before and after processing. The unit of the electrode wear is μm. The aperture gap is calculated by δ=(dh−de)/2, where dh is the diameter of machined hole and de is the diameter of electrode.
The experiments were conducted on EDM-350 machine. A hollow red copper pipe with 0.6 mm in diameter was used as the electrode and Al 7075 plates with 10mm in depth were selected as the workpiece material. The chemical composition details of the aluminum alloy plate can be seen in Table 1.
Mg | Cr | Zn | Cu | Si | Mn | Fe | Ti |
2.1-2.9 | 0.18-0.28 | 5.1-6.1 | 1.2-2.0 | 0.4 | 0.3 | 0.5 | 0.2 |
Negative polarity processing is performed in this study, which means the workpiece is connected with the negative electrode and the tool electrode is connected with the positive electrode. Kerosene is selected as the working fluid.
As mentioned above, the aperture gap should be smaller than a given value to ensure the EDM processing quality. Moreover, the electrode wear should be as small as possible to reduce the machining cost and energy consumption. Therefore, aperture gap is defined as the optimization constraint and electrode wear is regarded as the optimization objective. To further take the slight uncertainties of the EDM process parameters into consideration, the optimization model is formulated using reliability based method. The detailed mathematical model is defined as Eq 6:
find:μI,μTon,μToffmin:w(μI,μTon,μToff)s.t.:p[δmax⩽δg]⩾Φ(βt)2⩽μI⩽10,10⩽μTon⩽30,10⩽μToff⩽50(μ0I,μ0Ton,μ0Toff)=[6,15,25]T | (6) |
Where, the peak current, pulse on time and pulse off time are considered as random parameters which are assumed to be statistically independent and follow a normal distribution with the mean μI, μTon and μToff. The standard deviation vector of all random variables is [0.2,0.5,0.5]T. The probabilistic constraint of aperture gap must not be less than 99.87% (βt=3). Aperture gap limitation of 0.03 is imposed on the finished small hole.
To optimize the electrode wear with probabilistic constraint of aperture gap less than a given value, reliability-based optimization method using Kriging model and sequential sampling is used in this paper. The flowchart of proposed method is described in Figure 2. d0 is the initial design point and s0 is the initial sample set.
The procedure of proposed method consists of the following five phases:
Initial Sampling. To ensure the accuracy and efficiency of reliability-based EDM parameter optimization, ILHD with the initial process parameter design as inherited point is used to generate 15 samples. Then EDM experiments are conducted to obtain the electrode wear and aperture gap.
Kriging construction. According to the initial samples and corresponding EDM experiment results, Kriging model used to approximate the relationship between the EDM parameters inputs and response outputs is constructed.
Sequential sampling. To ensure the global accuracy of Kriging model, OEFF criteria is used to select sequential samples. The detailed description of OEFF criteria is shown in Section 2.2. Then EDM experiments are conducted and the sample set used to construct Kriging model is updated using sequential samples.
Kriging update. Using the samples and their responses obtained in the last phase, Kriging model is updated.
Optimization Solution. In this step, the constructed electrode wear Kriging model is taken as the optimization target. By calling the aperture gap Kriging model, the failure probability and corresponding gradient of performance response at current EDM parameter combination are calculated using MCS with 106 samples. Then the optimization model in Section 3.2 is solved by SAP. SAP is selected here because its good performance in surrogate model-based design optimization [14].
To ensure the Kriging model accuracy around the initial EDM parameter design point, ILHD is used to generate 15 samples, as shown in Table 2. Then EDM experiments are conducted to obtain corresponding electrode wear and aperture gap. The initial samples are shown as follows:
No. | I | Ton | Toff | No. | I | Ton | Toff | No. | I | Ton | Toff |
1 | 6.0 | 15.0 | 25.0 | 6 | 5.5 | 20.0 | 17.2 | 11 | 2.3 | 24.0 | 46.5 |
2 | 8.5 | 22.0 | 30.6 | 7 | 6.6 | 18.4 | 11.4 | 12 | 7.6 | 10.9 | 27.1 |
3 | 2.9 | 17.4 | 33.4 | 8 | 9.8 | 28.4 | 35.9 | 13 | 4.4 | 27.3 | 22.4 |
4 | 4.9 | 14.5 | 49.6 | 9 | 3.8 | 26.0 | 15.0 | 14 | 8.1 | 13.5 | 43.0 |
5 | 9.2 | 12.1 | 40.1 | 10 | 3.2 | 29.8 | 18.0 | 15 | 7.0 | 22.6 | 37.5 |
In Table 2, I means the peak current, Ton is the pulse on time and Toff is the pulse off time.
After initial sampling, sequential samples are selected using OEFF criterion to update Kriging model, which is shown in Table 3.
No. | I | Ton | Toff | No. | I | Ton | Toff | No. | I | Ton | Toff |
16 | 2.0 | 10.0 | 10.0 | 20 | 2.1 | 20.0 | 12.2 | 24 | 2.1 | 28.9 | 12.2 |
17 | 2.1 | 10.4 | 49.3 | 21 | 2.1 | 11.1 | 30.0 | 25 | 2.1 | 13.3 | 12.2 |
18 | 2.4 | 29.6 | 47.8 | 22 | 3.3 | 10.4 | 12.2 | 26 | 2.1 | 13.3 | 47.8 |
19 | 9.9 | 11.1 | 12.2 | 23 | 2.1 | 28.9 | 12.2 | 27 | 2.1 | 15.6 | 12.2 |
After accurate Kriging approximations of the relationship between EDM parameters and machining performance are constructed, reliability-based EDM parameter optimization model is solved using MCS and SAP. The detailed iteration design points are shown in Table 4. w is the electrode wear value at current EDM design point and β is corresponding reliability index.
No. | I | Ton | Toff | w | β |
0 | 6.0 | 15.0 | 25.0 | 258.12 | Inf. |
1 | 6.8 | 13 | 21 | 221.33 | Inf. |
2 | 7.6 | 11 | 17 | 193.71 | 5.76 |
3 | 8.0 | 10 | 13 | 178.778 | 4.22 |
4 | 8.1 | 10 | 10 | 174.10 | 3.02 |
5 | 8.2 | 10 | 10 | 174.08 | 3.01 |
As can be seen from Table 4, with optimization iteration progressing, the objective function value decreases and optimal electrode wear is observed at [8.21010]. Though higher reliability indexes are observed at former five iterations, higher objective functions are also observed, which means waste of electrode material. Therefore, the proposed method has an economic electrode wear with acceptable aperture gap reliability requirement.
In order to further verify the feasibility of optimal EDM parameter combination, additional experiments are conducted. The comparative results of the confirmation experiments (CE) and the Kriging based method (KRG) are shown in Table 5. Where, Ew=|wCE−wKRG|/wCE and Eβ=|βCE−βKRG|/βCE. As can be seen in Table 5, the electrode wear is 174.2, and the reliability that the aperture gap smaller than the requirement is 3.02, which coincide with the Kriging based process parameter optimization results. Therefore, the Kriging model used to approximate the relationship between EDM parameters and machining performance is accurate and the proposed sequential sampling method is feasible. The proposed method is an effective method to conduct EDM parameter optimization, which leads to an economic electrode wear and a reasonable aperture gap.
wCE | wKRG | Ew | βCE | βKRG | Eβ |
174.08 | 174.2 | 0.07% | 3.01 | 3.02 | 0.33% |
To overcome the issues in machining accuracy and machining cost of Al 7075 plate, reliability-based EDM process parameters optimization method is developed to handle the uncertainties of process parameters in this paper. The effect of peak current, pulse on time and pulse off time on electrode wear, termed as the design objective, and on the aperture gap, termed as the performance function, is approximated using Kriging model. To build the Kriging model, ILHD with the initial EDM design as inherited point is applied to generate 15 process parameters combinations. Different from existing sequential methods, the OEFF criterion is developed to update the Kriging model, which leads to a high global accuracy for parameter optimization. EDM experiments with aforementioned process parameter combinations are performed to obtain corresponding electrode wear and aperture gap. The probability of aperture gap smaller than a given value, which is termed as the constraint function in reliability-based EDM process parameters optimization model, is calculated by MCS. Based on it, the optimal EDM parameter combination is obtained by SAP.
Using the optimal EDM parameters to perform Al 7075 verification experiments, the feasibility of proposed method is demonstrated, where smaller electrode wear as low as 174.2 μm is obtained with the reliability satisfaction (β=3.02) of aperture gap. Therefore, the Kriging model used to approximate the relationship between EDM parameters and machining performance is accurate and the sampling method is feasible. It's worth noting that, the proposed method is a prevalent method, which can be used in EDM of other materials. Besides EDM machining accuracy and machining cost, the machining efficiency and low carbon manufacturing will be considered in future study.
This project is supported by National Natural Science Foundation of China (Grant No. 11602230), Key Scientific and Technological Research Projects in Henan Province (Grant No. 192102210069), Henan Key scientific research projects in Colleges and Universities (Grant No. 19A460031), Innovative Research Team (in Science and Technology) in University of Henan Province (Grant No. 18IRTSTHN015).
The authors declare that there is no conflict of interests in this paper.
[1] | R. Ramakrishnan and L. Karunamoorthy, Multi response optimization of wire EDM operations using robust design of experiments, Int. J. Adv. Manuf. Tech., 29 (2006), 105–112. |
[2] | A. Mandal, A. R. Dixit, S. Chattopadhyaya, et al., Improvement of surface integrity of Nimonic C 263 super alloy produced by WEDM through various post processing techniques, Int. J. Adv. Manuf. Tech., 93 (2017), 433–443. |
[3] | G. Rajyalakshmi and P. V. Ramaiah, Multiple process parameter optimization of wire electrical discharge machining on inconel 825 using taguchi grey relational analysis, Int. J. Adv. Manuf. Tech., 69 (2013), 1249–1262. |
[4] | S. Gopalakannan, T. Senthilvelan, S. Ranganathan, et al., Modeling and optimization of EDM process parameters on machining of Al 7075-B4C MMC using RSM, Procedia Eng., 38 (2012), 685–690. |
[5] | A. Majumder, Process parameter optimization during EDM of AISI 316 LN stainless steel by using fuzzy based multi-objective PSO, J. Mech. Sci. Tech., 27 (2013), 2143–2151. |
[6] | A. Nikalje, A. Kumar and K. Srinadh, Influence of parameters and optimization of EDM performance measures on MDN 300 steel using taguchi method, Int. J. Adv. Manuf. Tech., 69 (2013), 41–49. |
[7] | L. Zhang, Z. Jia, F. Wang, et al., A hybrid model using supporting vector machine and multi-objective genetic algorithm for processing parameters optimization in micro-EDM, Int. J. Adv. Manuf. Tech., 51 (2010), 575–586. |
[8] | H. Lee and C. Liu, Optimizing the EDM hole-drilling strain gage method for the measurement of residual stress, J. Mater. Process. Tech., 209 (2009), 5626–5635. |
[9] | T. A. El-Taweel, Multi-response optimization of EDM with Al–Cu–Si–Tic P/M composite electrode, Int. J. Adv. Manuf. Tech., 44 (2009), 100–113. |
[10] | X. Li, F. Yan, J. Ma, et al., RBF and NSGA-II based EDM process parameters optimization with multiple constraints, Math. Biosci. Eng., 16 (5) (2019), 5788–5803. |
[11] | X. Li, L. Gao, Q. Pan, et al., An effective hybrid genetic algorithm and variable neighborhood search for integrated process planning and scheduling in a packaging machine workshop, IEEE T. Syst. Man. Cy. S., (2018), 1–13. |
[12] | Y. Lin, Y. Chen, D. Wang, et al., Optimization of machining parameters in magnetic force assisted EDM based on Taguchi method, J. Mater. Process. Tech., 209 (2009), 3374–3383. |
[13] | Z. Chen, H. Qiu, L. Gao, et al., An optimal shifting vector approach for efficient probabilistic design, Struct. Multidiscip. O., 47 (2013), 905–920. |
[14] | X. Li, H. Qiu, Z. Chen, et al., A local kriging approximation method using MPP for reliability-based design optimization, Comput. Struct., 162 (2016), 102–115. |
[15] | X. Li, H. Qiu, Z. Chen, et al., A local sampling method with variable radius for RBDO using Kriging, Eng. Comput., 32 (2015), 1908–1933. |
[16] | A. Chiralaksanakul and S. Mahadevan, First-order approximation methods in reliability-based design optimization, J. Mech. Design, 127 (2005), 851–857. |
[17] | B. Keshtegar and M. Zeng, A hybrid relaxed first-order reliability method for efficient structural reliability analysis, Struct. Saf., 66 (2017), 84–93. 18. G. Bird, Monte-carlo simulation in an engineering context, Prog. Astronaut. Aeronaut., 74 (1981), 239–255. |
[18] | 19. S. Au and J. L. Beck, A new adaptive importance sampling scheme for reliability calculations, Struct. Saf., 21 (1999), 135–158. |
[19] | 20. C. Jiang, H. Qiu, X. Li, et al., Iterative reliable design space approach for efficient reliability-based design optimization. Eng. Comput., (20, 1–19. |
[20] | 21. D. Lehký, O. Slowik and D. Novák, Reliability-based design: Artificial neural networks and double-loop reliability-based optimization approaches, Adv. Eng. Softw., 117 (8): 123–135. |
[21] | 22. C. Jiang, H. Qiu, L. Gao, et al., An adaptive hybrid single-loop method for reliability-based design optimization using iterative control strategy, Struct. Multidiscip. O., 56 (2017), 1271–1286. |
[22] | 23. X. Du, Saddlepoint approximation for sequential optimization and reliability analysis, J. Mech. Design, 130 (2008), 011011. |
[23] | 24. P. Zhang, P. Breitkopf, C. Vayssade, et al., XU-RSM: Diffuse Response surface model for reliability-based design optimization, IOP conference series: Materials Science and Engineering, 10 (2010), 012209. |
[24] | 25. A. Basudhar and S. Missoum, A sampling-based approach for probabilistic design with random fields, Comput. Meth. Appl. Mech. Eng., 198 (2009), 3647–3655. |
[25] | 26. G. Li and Z. Meng, Reliability-based design optimization with the RBF neural network model, Appl. Math. Mech. 35 (2014), 1271–1279. |
[26] | 27. N. Xiao, M. Zuo and C. Zhou, A new adaptive sequential sampling method to construct surrogate models for efficient reliability analysis, Reliab. Eng. Syst. Saf., 169 (2018), 330–338. |
[27] | 28. C. Jiang, H. Qiu, L. Gao, et al., Real-time estimation error-guided active learning Kriging method for time-dependent reliability analysis, Appl. Math. Model., 77 (2020), 82–98. |
[28] | 29. B. Echard, N. Gayton and M. Lemaire, AK-MCS: An active learning reliability method combining kriging and monte carlo simulation, Struct. Saf., 33 (2011), 145–154. |
[29] | 30. C. Jiang, H. Qiu, Z. Yang, et al., A general failure-pursuing sampling framework for surrogate-based reliability analysis, Reliab. Eng. Syst. Saf., 183 (2019), 47–59. |
[30] | 31. B. J. Bichon, M. S. Eldred, L. P. Swiler, et al., Efficient global reliability analysis for nonlinear implicit performance functions, AIAA J., 46 (2008), 2459–2468. |
[31] | 32. W. C. Yeh, J. C. P. Su, T. J. Hsieh, et al., Approximate reliability function based on wavelet latin hypercube sampling and bee recurrent neural network, IEEE T. Reliab., 60 (2011), 404–414. |
[32] | 33. G. Wang, Adaptive response surface method using inherited latin hypercube design points, transactions-american society of mechanical engineers, J. Mech. Design, 125 (2003), 210–220. |
[33] | 34. X. Li, J. Du, Z. Chen, et al., Reliability-based NC milling parameters optimization using ensemble metamodel. Int. J. Adv. Manuf. Tech., 97 (2018), 9–3369. |
[34] | 35. Z. Jia, F. Gu, F. Wang, et al., Parameter optimization of EDM micro-and-small holes based on signal-to-noise and grey relational grade, Chin. J. Mech. Eng., 43 (2007), 63–67. |
1. | Xiaoke Li, Xinyu Han, Zhenzhong Chen, Wuyi Ming, Yang Cao, Jun Ma, A multi-constraint failure-pursuing sampling method for reliability-based design optimization using adaptive Kriging, 2020, 0177-0667, 10.1007/s00366-020-01135-3 | |
2. | Xiaoke Li, Qingyu Yang, Yang Wang, Xinyu Han, Yang Cao, Lei Fan, Jun Ma, Development of surrogate models in reliability-based design optimization: A review, 2021, 18, 1551-0018, 6386, 10.3934/mbe.2021317 | |
3. | Jun Ma, Chunyang Yin, Xiaoke Li, Xinyu Han, Wuyi Ming, Shiyou Chen, Yang Cao, Kun Liu, Optimization of EDM process parameters based on variable-fidelity surrogate model, 2022, 122, 0268-3768, 2031, 10.1007/s00170-022-09963-x | |
4. | Dongdong You, Wenbin Pang, Dongqing Cai, Thermal Fatigue Life Prediction under Temperature Uncertainty for Shot Sleeve of Squeeze Casting Machine, 2021, 11, 2075-4701, 1126, 10.3390/met11071126 |
Mg | Cr | Zn | Cu | Si | Mn | Fe | Ti |
2.1-2.9 | 0.18-0.28 | 5.1-6.1 | 1.2-2.0 | 0.4 | 0.3 | 0.5 | 0.2 |
No. | I | Ton | Toff | No. | I | Ton | Toff | No. | I | Ton | Toff |
1 | 6.0 | 15.0 | 25.0 | 6 | 5.5 | 20.0 | 17.2 | 11 | 2.3 | 24.0 | 46.5 |
2 | 8.5 | 22.0 | 30.6 | 7 | 6.6 | 18.4 | 11.4 | 12 | 7.6 | 10.9 | 27.1 |
3 | 2.9 | 17.4 | 33.4 | 8 | 9.8 | 28.4 | 35.9 | 13 | 4.4 | 27.3 | 22.4 |
4 | 4.9 | 14.5 | 49.6 | 9 | 3.8 | 26.0 | 15.0 | 14 | 8.1 | 13.5 | 43.0 |
5 | 9.2 | 12.1 | 40.1 | 10 | 3.2 | 29.8 | 18.0 | 15 | 7.0 | 22.6 | 37.5 |
No. | I | Ton | Toff | No. | I | Ton | Toff | No. | I | Ton | Toff |
16 | 2.0 | 10.0 | 10.0 | 20 | 2.1 | 20.0 | 12.2 | 24 | 2.1 | 28.9 | 12.2 |
17 | 2.1 | 10.4 | 49.3 | 21 | 2.1 | 11.1 | 30.0 | 25 | 2.1 | 13.3 | 12.2 |
18 | 2.4 | 29.6 | 47.8 | 22 | 3.3 | 10.4 | 12.2 | 26 | 2.1 | 13.3 | 47.8 |
19 | 9.9 | 11.1 | 12.2 | 23 | 2.1 | 28.9 | 12.2 | 27 | 2.1 | 15.6 | 12.2 |
No. | I | Ton | Toff | w | β |
0 | 6.0 | 15.0 | 25.0 | 258.12 | Inf. |
1 | 6.8 | 13 | 21 | 221.33 | Inf. |
2 | 7.6 | 11 | 17 | 193.71 | 5.76 |
3 | 8.0 | 10 | 13 | 178.778 | 4.22 |
4 | 8.1 | 10 | 10 | 174.10 | 3.02 |
5 | 8.2 | 10 | 10 | 174.08 | 3.01 |
wCE | wKRG | Ew | βCE | βKRG | Eβ |
174.08 | 174.2 | 0.07% | 3.01 | 3.02 | 0.33% |
Mg | Cr | Zn | Cu | Si | Mn | Fe | Ti |
2.1-2.9 | 0.18-0.28 | 5.1-6.1 | 1.2-2.0 | 0.4 | 0.3 | 0.5 | 0.2 |
No. | I | Ton | Toff | No. | I | Ton | Toff | No. | I | Ton | Toff |
1 | 6.0 | 15.0 | 25.0 | 6 | 5.5 | 20.0 | 17.2 | 11 | 2.3 | 24.0 | 46.5 |
2 | 8.5 | 22.0 | 30.6 | 7 | 6.6 | 18.4 | 11.4 | 12 | 7.6 | 10.9 | 27.1 |
3 | 2.9 | 17.4 | 33.4 | 8 | 9.8 | 28.4 | 35.9 | 13 | 4.4 | 27.3 | 22.4 |
4 | 4.9 | 14.5 | 49.6 | 9 | 3.8 | 26.0 | 15.0 | 14 | 8.1 | 13.5 | 43.0 |
5 | 9.2 | 12.1 | 40.1 | 10 | 3.2 | 29.8 | 18.0 | 15 | 7.0 | 22.6 | 37.5 |
No. | I | Ton | Toff | No. | I | Ton | Toff | No. | I | Ton | Toff |
16 | 2.0 | 10.0 | 10.0 | 20 | 2.1 | 20.0 | 12.2 | 24 | 2.1 | 28.9 | 12.2 |
17 | 2.1 | 10.4 | 49.3 | 21 | 2.1 | 11.1 | 30.0 | 25 | 2.1 | 13.3 | 12.2 |
18 | 2.4 | 29.6 | 47.8 | 22 | 3.3 | 10.4 | 12.2 | 26 | 2.1 | 13.3 | 47.8 |
19 | 9.9 | 11.1 | 12.2 | 23 | 2.1 | 28.9 | 12.2 | 27 | 2.1 | 15.6 | 12.2 |
No. | I | Ton | Toff | w | β |
0 | 6.0 | 15.0 | 25.0 | 258.12 | Inf. |
1 | 6.8 | 13 | 21 | 221.33 | Inf. |
2 | 7.6 | 11 | 17 | 193.71 | 5.76 |
3 | 8.0 | 10 | 13 | 178.778 | 4.22 |
4 | 8.1 | 10 | 10 | 174.10 | 3.02 |
5 | 8.2 | 10 | 10 | 174.08 | 3.01 |
wCE | wKRG | Ew | βCE | βKRG | Eβ |
174.08 | 174.2 | 0.07% | 3.01 | 3.02 | 0.33% |