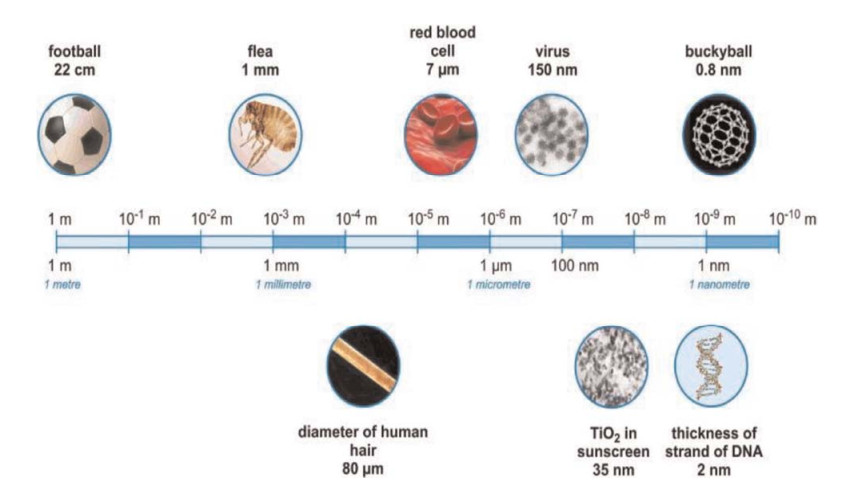
A stable colloid called ferrofluid is made up of tiny magnetic particles, often magnetite (Fe3O4), that have been bonded with an amphiphilic dispersion layer and are then suspended in a suitable liquid solvent carrier. Current industrial uses for ferrofluid include dynamic sealing, inertial and viscous damping, magnetic drug targeting, liquid microrobots, etc. In this article, we studied the heat transfer and MHD micropolar ferrofluid flow caused by non-linearly stretching surface. The results are presented for hybrid alumina- copper/ethylene glycol (Al2O3-Cu/EG) nanofluid. The governing non-linear equations describing flow are transformed into a system of ordinary differential equations using similarity transformations. Using the BVp4c method, the microstructure and inertial properties of a magnetite ferrofluid across a non-linear stretched sheet are studied. The influence of relevant parameters on stream function, velocity, micro-rotation velocity, and temperature are obtained and represented graphically. The computed results are original, and it has been observed that if we increase the magnetic parameter, the stream function and the velocity decrease, while the temperature and micro-rotation velocity increase. As the Prandtl number increases, the temperature profile decreases. It has been observed that the Nusselt number or heat transfer rate of hybrid nanofluid is better as compared to nanofluid flow.
Citation: Abdul Rauf, Nehad Ali Shah, Aqsa Mushtaq, Thongchai Botmart. Heat transport and magnetohydrodynamic hybrid micropolar ferrofluid flow over a non-linearly stretching sheet[J]. AIMS Mathematics, 2023, 8(1): 164-193. doi: 10.3934/math.2023008
[1] | Nadeem Abbas, Wasfi Shatanawi, Taqi A. M. Shatnawi . Innovation of prescribe conditions for radiative Casson micropolar hybrid nanofluid flow with inclined MHD over a stretching sheet/cylinder. AIMS Mathematics, 2025, 10(2): 3561-3580. doi: 10.3934/math.2025164 |
[2] | Umair Khan, Aurang Zaib, Sakhinah Abu Bakar, Anuar Ishak, Dumitru Baleanu, El-Sayed M Sherif . Computational simulation of cross-flow of Williamson fluid over a porous shrinking/stretching surface comprising hybrid nanofluid and thermal radiation. AIMS Mathematics, 2022, 7(4): 6489-6515. doi: 10.3934/math.2022362 |
[3] | Taqi A. M. Shatnawi, Nadeem Abbas, Wasfi Shatanawi . Comparative study of Casson hybrid nanofluid models with induced magnetic radiative flow over a vertical permeable exponentially stretching sheet. AIMS Mathematics, 2022, 7(12): 20545-20564. doi: 10.3934/math.20221126 |
[4] | Mir Sajjad Hashemi, Hadi Rezazadeh, Hassan Almusawa, Hijaz Ahmad . A Lie group integrator to solve the hydromagnetic stagnation point flow of a second grade fluid over a stretching sheet. AIMS Mathematics, 2021, 6(12): 13392-13406. doi: 10.3934/math.2021775 |
[5] | Madeeha Tahir, Ayesha Naz, Muhammad Imran, Hasan Waqas, Ali Akgül, Hussein Shanak, Rabab Jarrar, Jihad Asad . Activation energy impact on unsteady Bio-convection nanomaterial flow over porous surface. AIMS Mathematics, 2022, 7(11): 19822-19845. doi: 10.3934/math.20221086 |
[6] | Yasir Khan, Sohaib Abdal, Sajjad Hussain, Imran Siddique . Numerical simulation for thermal enhancement of $ H_2O $ + Ethyl Glycol base hybrid nanofluid comprising $ GO + (Ag, AA7072, MoS_2) $ nano entities due to a stretched sheet. AIMS Mathematics, 2023, 8(5): 11221-11237. doi: 10.3934/math.2023568 |
[7] | Imran Siddique, Yasir Khan, Muhammad Nadeem, Jan Awrejcewicz, Muhammad Bilal . Significance of heat transfer for second-grade fuzzy hybrid nanofluid flow over a stretching/shrinking Riga wedge. AIMS Mathematics, 2023, 8(1): 295-316. doi: 10.3934/math.2023014 |
[8] | Subhan Ullah, Hassan Ali Ghazwani, Dolat Khan, Zareen A. Khan . Heat transfer augmentation of Jeffery–Hamel hybrid nanofluid in a stretching convergent/divergent channel through porous medium. AIMS Mathematics, 2025, 10(1): 388-402. doi: 10.3934/math.2025018 |
[9] | Kottakkaran Sooppy Nisar, Muhammad Shoaib, Muhammad Asif Zahoor Raja, Yasmin Tariq, Ayesha Rafiq, Ahmed Morsy . Design of neural networks for second-order velocity slip of nanofluid flow in the presence of activation energy. AIMS Mathematics, 2023, 8(3): 6255-6277. doi: 10.3934/math.2023316 |
[10] | Umar Nazir, Kanit Mukdasai . Combine influence of Hall effects and viscous dissipation on the motion of ethylene glycol conveying alumina, silica and titania nanoparticles using the non-Newtonian Casson model. AIMS Mathematics, 2023, 8(2): 4682-4699. doi: 10.3934/math.2023231 |
A stable colloid called ferrofluid is made up of tiny magnetic particles, often magnetite (Fe3O4), that have been bonded with an amphiphilic dispersion layer and are then suspended in a suitable liquid solvent carrier. Current industrial uses for ferrofluid include dynamic sealing, inertial and viscous damping, magnetic drug targeting, liquid microrobots, etc. In this article, we studied the heat transfer and MHD micropolar ferrofluid flow caused by non-linearly stretching surface. The results are presented for hybrid alumina- copper/ethylene glycol (Al2O3-Cu/EG) nanofluid. The governing non-linear equations describing flow are transformed into a system of ordinary differential equations using similarity transformations. Using the BVp4c method, the microstructure and inertial properties of a magnetite ferrofluid across a non-linear stretched sheet are studied. The influence of relevant parameters on stream function, velocity, micro-rotation velocity, and temperature are obtained and represented graphically. The computed results are original, and it has been observed that if we increase the magnetic parameter, the stream function and the velocity decrease, while the temperature and micro-rotation velocity increase. As the Prandtl number increases, the temperature profile decreases. It has been observed that the Nusselt number or heat transfer rate of hybrid nanofluid is better as compared to nanofluid flow.
In order to meet industrial and technical requirements, a smart fluid with exceptional thermal capabilities is desired. A novel heat transfer fluid created using nanotechnology termed a nanofluid was first described by Choi [1] in 1955. A growing proportion of nanotechnology for heat transmission is called nanofluids, which are colloidal mixtures of nanoparticles (1–100 nm) and a base liquid (nanoparticle fluid suspensions) (see Buongiorno et al. [2]). Figure 1 shows a comparative sample of different sizes of materials from large scales to nanoscales. Polymers, metals, metal oxides, and other substances may all be found in nanofluids. The thermophysical properties of traditional thermal fluids are improved significantly by the inclusion of nanoparticles, improving the heat transfer coefficient. Nanofluids are currently widely used in a number of industries, including the electronics, automotive, solar energy, medicinal, and oil recovery industries, as a result of such a wider acceptance (see Singh et al. [3] and Suvardhan et al. [4]).
Researchers are presently drawn to hybrid and dihybrid nanofluid due to the advantages of nanofluid and the growing study into flow, heat, and mass transport phenomena. Hybrid nanofluid is the term used to describe a combination that contains several nanoparticles. It is referred to as a "dihybrid nanofluid" if the combination contains several nanoparticles and fluids [5]. According to Lou et al. [6], the key benefit of hybrid nanofluids is increased energy efficiency, conservation, and savings. In order to achieve uniform shear flow over a stretched sheet, Waini et al. [7] investigated the effects of transpiration on the hybrid nanofluid flow. They discovered that an improvement in copper nanoparticle volume fractions results in an improvement in heat transmission.
The heat conduction study of a stretching surface constantly moving along an ambient fluid has received a lot of attention and has been widely described in the literature. The composition of the ambient liquid and the pace of stretching determines the properties of products created through engineering procedures such as metallurgy and polymer extrusion. Because quick stretching or irregular temperature changes in the extrudate can compromise the intended qualities of the last product, the heat exchange rate must be exactly controlled. Nanofluids are mixtures of a base fluid and nanoparticles that are homogeneous. The particles in these suspensions can be metal or non-metal. Ferrofluid is a class of nanofluid in which the suspension of nanoparticles can be magnetized. Ferrofluids offer a lot of potential in these kinds of applications. Ferrofluids are fluids made artificially from extremely reduced mixture suspensions of tiny magnetic molecules suspended in a carrier fluid that is not conducting. This fluid acts normally except for the fact that it is subjected to a force owing to magnetization. Ferrohydrodynamics is the study of magnetic fluid motion mechanics that is transformed by strong magnetic polarization forces. The existence of an external magnetic source may affect significantly the dynamics of electrically conducting fluids flowing effectively in its spawned field [8]. The effects of magnetization on fluid flow with magnets were first described by Rosensweig [9]. In the last several years, for Newtonian and non-Newtonian fluids, as well as flat horizontal surfaces, flow and heat transfer have been extensively studied under various hydrodynamic and thermal boundary conditions [10,11,12]. Near the infinite plate, heat transport and magnetohydrodynamic (MHD) flow have been investigated. To make a ferrofluid flow, Andersson and Valnes [13] were the first to use a stretched surface with a magnetic dipole. Andersson [13,14] showed that the impact of an externally provided magnetic field on flow is similar to that of viscoelasticity.
The effects of nonlinear stretching or shrinking on MHD flow are discussed [15,16,17]. For flow past a stretching/shrinking sheet, two solutions were discovered in [18]. Furthermore, it's crucial to research boundary layer flow and heat transmission across a stretched surface, because it has a wide range of uses in industrial engineering and production processes, such as plastic sheet aerodynamic expulsion and paper manufacturing, manufacture of glass fiber. In the polymer sector, heat-treated materials are transported between feed and wind-up rolls, drawing using wires, whirling metal, and many others [19,20,21,22]. Hayat et al. [23] also came up with a solution based on an analysis of a second-grade fluid's slip flow and heat transfer through a planar stretching sheet. Martin and Boyd [24] looked at the steady wall temperature, heat transfer, and slide flow past a flat surface. Their findings show that boundary layer equations may be utilized to examine flow at the microelectromechanical systems (MEMS) scale and that they can be used to investigate rarefaction's impact on shear stress and flow structure. In chemical industries, such as the development of nuclear waste disposal canisters and the cooling systems for nuclear reactors, it's common to employ mixed convectional flow with heat transmission. These physical processes take place when the effects of buoyant forces become even more powerful. Ali [25] looked into the impact of viscosity that varies with temperature on heat transmission via laminar mixed convection along a surface that is constantly shifting. According to the literature study, there are just a few research on heat transmission from ferrofluids. Li and Xuan [26] explored the effects of an external magnetic field on convective heat transport using a ferrofluid flow through a thin wire. They discovered that the magnetic field from the outside affects the ferrofluids' heat transmission via convection performance. When Yamaguchi et al. [27] analyzed the convection naturally of the fluid with magnetic properties in a square hollow with partitions having a magnetic field imposed from the outside computationally, they discovered that a substantial magnetic field influences the convection flow. Motozawa et al. [28] explored the influence of heat transfer in a magnetic fluid flow with a magnetic field in a duct that is rectangular. They observed that the heat transfer coefficient rises locally in the presence of a magnetic field. The coefficient of heat transfer increases as the magnetic field increases. Characteristics of ferrofluid flow over a linearly stretching have already been discussed in previous work.
The thorough review of the literature demonstrates that, the study of heat transfer and MHD hybrid nano-fluid with micropolar ferrofluid flow over a non-linearly stretching sheet does not exist in literature. In this article, we considered this problem with two different nanoparticles (Al2O3 -Cu) suspended in the base fluid ethylene glycol (EG). Using the suitable similarity transformations, the governing equations are transformed into a set of nonlinear ordinary differential equations, which are then solved using the built-in MATLAB module BVP-4c.
The topic of micropolar and classical nanofluid across a stretched sheet has been studied by several researchers. The flow of a micropolar/classical ferrofluid on a stretched sheet in the y > 0 regions was presumed steady-state in this research. At x = 0, the surface is stretched in the x-direction and normal in the y-direction. The stretched sheet's surface velocity is uw(x) = a xm, where a is an optional constant that is positive. A magnetic field perpendicular to the surface is also present (See Figure 2). Here are the micropolar ferrofluid governing equations based on the preceding assumptions:
The continuity equation and momentum equations are [29],
ddt(ρhnfV)=∇·(ρhnfV) | (1) |
ρhnf(dVdt)=−∇p+(2μhnf+k)∇(∇·V)−(μhnf+k)∇×(∇×V)+k(∇×N)+J×B+ρhnf | (2) |
ρhnfj(dNdt)=(ϕ+λ+γhnf)∇·(ρhnf·N)−γhnf∇×(∇×N)+k(∇×v)−2kN+ρhnfI | (3) |
The thermophysical properties μhnf(β),ρhnf,Khnf,(ρβT)hnf,(ρβC)hnf,(ρCp)hnf and σhnf for hybrid nanofluid (Al2O3-Cu/EG) are defined as,
ρhnf=(1−ϕ2)[(1−ϕ1)ρf+ϕ1ρs1]+ϕ2ρs2, | (4) |
(ρCP)hnf=(1−ϕ2)[(1−ϕ1)(ρCP)f+ϕ1(ρCP)s1]+ϕ2(ρCP)s2, | (5) |
(ρβT)hnf=(1−ϕ2)[(1−ϕ1)(ρβT)f+ϕ1(ρβT)s1]+ϕ2(ρβT)s2, | (6) |
(ρβC)hnf=(1−ϕ2)[(1−ϕ1)(ρβC)f+ϕ1(ρβC)s1]+ϕ2(ρβC)s2, | (7) |
μhnfμf=1(1–ϕ1)2.5(1–ϕ2)2.5, | (8) |
khnfkbf=ks2+2kbf−2ϕ2(kbf−ks2)ks2+2kbf+ϕ2(kbf−ks2), | (9) |
where,
kbfkf=ks1+2kf−2ϕ1(kf−ks1)ks1+2kf+ϕ1(kf−ks1), | (10) |
σhnfσbf=σs2+2σbf−2ϕ2(σbf−σs2)σs2+2σbf+ϕ2(σbf−σs2), | (11) |
where,
σbfσf=σs1+2σf−2ϕ1(σf−σs1)σs1+2σf+ϕ1(σf−σs1), | (12) |
where ϕ1,ϕ2 are solid volume fraction of Alumina/Aluminium oxide, Cuprum/Copper, respectively, Cp is the specific heat, kf denotes the thermal conductivity of the regular fluid. The values for the thermophysical parameters for hybrid nanofluid (Al2O3-Cu/EG) is shown in Table 1.
Thermophysical property | Fluid (EG) | Alumina (Al2O3) | Cu |
ρ(kg/m3) | 1114.0 | 3970 | 8933 |
cp(j/kg.K) | 2415 | 765 | 385 |
k(w/m.K) | 0.2520 | 40 | 400 |
σ(s/smm) | 5.50×10−6 | 59.6×106 | 35×106 |
Also, flow is incompressible with no external forces, and the governing equations are:
ρhnf(dvdt+(v.∇)v)=(μhnf+k)∇2v+k(∇×N)+J×B, | (13) |
ρhnfj(dNdt+(N.∇)N)=γhnf∇2N+k(∇×v)−2kN. | (14) |
The body force proposed by Hussanan et al. is:
J×B=−σhnfB20v. | (15) |
The governing equations (momentum equations) take the form [30,31],
ρhnf(u∂u∂x+v∂u∂y)=(μhnf+k)∂2u∂y2+k∂N∂y−σhnfB20u, | (16) |
ρhnfj(u∂N∂x+v∂N∂y)=γhnf∂2N∂y2−k(2N+∂u∂y). | (17) |
The energy equation is
u∂T∂x+v∂T∂y=khnf(cp)nf∂2T∂y2−∂qr∂y, | (18) |
and, according to Rosseland's guess, it is
u∂T∂x+v∂T∂y=1(cp)hnf(khnf+16σ∗T3∞3k∗)∂2T∂y2. | (19) |
The problem's boundary conditions are
u=axm,v=0,T=Tw,N=−δ∂u∂y,aty=0, | (20) |
u=0,T=T∞,N=0,at y→∞. | (21) |
For a better understanding of these formulas, the velocity components in the x and y directions are assumed to be u and v, respectively. The angular velocity is denoted by N. μ is viscosity in a dynamic state, δ is a constant in the 0≤δ≤1 region. When δ=0, microelements close to the wall surface are not allowed to spin. If δ=12 demonstrated the insufficiency for the concentration of microelements. Furthermore, δ=1 when δ involve in the turbulent boundary layer flow. Micro inertia per unit mass is j, γ is the viscosity of a spinning gradient and k is the viscosity of the vortex. To solve these nonlinear differential equations quickly and easily, we made use of similarity transformations such as,
u=axmf',v=−√2νaxm−1(m+1)((m+1)2f+(m−1)2ηf'),η=√(m+1)axm−12νy,θ(η)=(T−T∞)(Tw−T∞), |
N=a32x(3m−1)2√(m+1)2G. | (22) |
By replacing the variables into the Eqs (16), (17), (19)–(21), we have
(e2+K)(m+1)2f″'+e1(m+1)2ff″−e1mf'2+KG'(m+1)2−M2e3f'=0, | (23) |
(e2+K2)(m+1)2G″+e1((m+1)2fG'−(3m−1)2f'G)−Kl(2G+f″)=0, | (24) |
1e5.Pr(e4+R)θ″+θ'f=0. | (25) |
And the boundary conditions are
f′=1,f=0,θ(η)=1,f′′=−G/Gδδ at η=0 | (26) |
f'→0,θ(η)→0,G→0 at η→∞. | (27) |
The non-dimensional variables are subsequently presented
M2=σfB20aρfx1−m,K=kμf,Kl=kμfx1−m,j=νfα,Pr=(ρcp)fυfkf,R=16σ∗T3∞3k∗·kf, | (28) |
and,
e1=ρhnfρf,e2=μhnfμf, e3=σhnfσf,e4=khnfkf and e5=(ρcp)hnf(ρcp)f, | (29) |
where K represents the Micro-rotation parameter, Kl is the local micro-rotation parameter, j is micro-inertia density, R is radiative parameter stretching and Pr is Prandtl number.
For this modeled flow problem, the skin friction coefficient and Nusselt, Sherwood number are defined as
Cf=τz/ρf,Nu=qwkf(Tw−T∞),Sh=xqm/DB, | (30) |
where qw represents surface heat flux, τz denotes surface shear stress, and qm defines surface mass flux for ferrofluid:
τz=[μhnf(∂u∂y)]y=0,qw=−K[∂T∂y]y=0,qm=−DB[∂N∂Y]y=0. | (31) |
Now apply the similarity transformation Eq (22) to both Eqs (30) and (31), and we get the results:
Cf(Rex)−(1/122)=f″(0),Nux(Rex)−(1/122)=−θ'(0),Shx(Rex)−(1/122)=−G'(0). | (32) |
In this article, a numerical approach is used to investigate and assess some of the physical parameters of the ferrofluid flow over a stretching sheet, such as stream function f(η), velocity f'(η), micro-rotation velocity G(η), and temperature θ(η). The numerical solution of nonlinear coupled differential equations is obtained by using the MATLAB software BVP4c method. Figures 3 and 4 depict that with the increase in the weakness of concentration of microelement δ, the stream function f(η) and the velocity f'(η) decreases. Whereas the effect of the weakness of concentration of micro-element δ on the micro-rotating velocity G(η) and temperature θ(η) is opposite as can be seen from Figures 5 and 6. Figures 7, 8, and 10 exhibit that with the increase in micro-rotation parameter K, the stream function f(η) and velocity f'(η) and micro-rotation velocity G(η) increase. While the effect of micro-rotation parameter K on temperature is converse as is visible in Figure 9. Figure 11 shows that the stream function f(η) increases with the increase of the local micro-rotation parameter K1. On the other hand, micro-rotation velocity G(η) decreases whenever the local micro-rotation parameter k1 increases as depicted in Figures 12–14 represent the effect of m on stream function f(η) and velocity f'(η). As m increases the stream function f(η) and velocity f'(η) increases. Even so with the increase of m temperature θ(η) and micro-rotation velocity G(η) decreases as disposed of in Figures 15 and 16.
Figures 17–20 are created to represent the effects of magnetic parameters on stream function f(η) and velocity f'(η), temperature θ(η) and micro-rotation velocity G(η) respectively, under the presumption that the other parameters have default values. When M increases then stream function f(η) and velocity f'(η) decrease display in Figures 17 and 18. The velocity field decreases as greater resistance to the flow phenomena is created by the application of the applied magnetic field. So, it is seen that the stream function f(η) and velocity curve f'(η) are reduced as a result of the Magnetic improvement. In contrast increases for temperature profile θ(η) and micro-rotation velocity G(η) as present in Figures 19 and 20. Magnetic materials experience a change in flux density as their temperature increases and decreases from an ambient temperature. Figure 21 illustrates the effect of shape factor n on temperature θ(η). When n = 3, 6.3698 and 16.1576 then its sphere, cylinder, and laminar respectively. Figures 22–24 exhibit the operation of ϕ1 on-stream function f(η), velocity f'(η) temperature θ(η) increase with the value ϕ1 increases. Unlike for micro-rotation velocity G(η) in Figure 25. Stream function f(η) and velocity f'(η) are decrease as well as increase the value of ϕ2 as present in Figures 26 and 27. Whereas in Figures 28 and 29 illustrate temperature θ(η) and micro-rotation velocity G(η) increase when increasing the value of ϕ2. Figures 22–29 show, the effects of the solid volume fractions of Alumina/Aluminum oxide and Copper/Copper on the thermal field. The volume fraction of Alumina/Aluminium oxide and Cuprum/Copper are boosting the thermal phenomena. However, as compared to ϕ1, the thermal profiles in case of ϕ2 are more obvious. Due to the nanoparticle volume fractions, the behaviour of these figures is consistent with the physical behaviour of the nanofluid. The thermal conductivity of the nanoparticles is greater than that of the base fluid, which increases the total thermal conductivity of the nanofluid and contributes to the rise in boundary layer temperature. Figure 30 display that as the Prandtl number increases the temperature θ(η) decrease. It is evident that the temperature distribution is a decreasing function of Prandtl number. This is because the thermal diffusivity of the fluid decreases due to higher values of Pr which further led the reduction in the thermal boundary layer thickness. The impact of radiation factors on temperature θ(η) are examined in Figure 31. More heat is introduced to the thermal phenomena as a result of changing the radiation parameter. More heat is introduced to the thermal phenomena as a result of changing the radiation parameter. As a result, the temperature curves are increased by the increasing radiation parameter value. Physically, by raising the value of the parameter R, we may enhance the radiative heat transfer.
The numerical outcomes of the Nusselt number, skin coefficient friction and Sherwood number are shown. The heat transfer factor is shown in Table 2 to see if the values of δ, Pr, ϕ1, ϕ2, Alpha, and M are inclined then heat transfer is also inclined. The effect of a different number of stretching parameters and other numbers on the skin coefficient friction is numerically shown in Table 2. When the quantities of δ, Pr, and M increase then skin coefficient friction expands, and if K1 expands, and the skin coefficient friction declines. The effect of M, Pr, K1, and δ, ϕ1, ϕ2, on the Sherwood number is shown in Table 3. If the value of K1 increases, then the mass transfer rate decreases. When the values M, m, K, and δ increase then the mass flow rate increase. The effect of various parameters δ, Pr, R, n, K1 and M on Nusselt number has been depicted in Table 4. It has been observed that when the values of parameters δ, M, R and N increase then the heat transfer expands, and if k, Pr and K1 expand, the Nusselt number decline.
Table 5 provides the comparative study of hybrid nanofluid and nanofluid under the effect of magnetic parameter M on Nusselt number, Skin friction, and Sherwood number. It is observed that the Nusselt number or heat transfer rate and shear stress or skin friction and Sherwood number or surface mass flux of hybrid nanofluid are better as compared to nanofluid flow.
Table 6 offers the proportional study of hybrid nanofluid and nanofluid under the effect of boundary parameter δ on Nusselt number, Skin friction, and Sherwood number. It is detected that the Nusselt number or heat transfer rate and shear stress or skin friction and Sherwood number or surface mass flux of hybrid nanofluid are better as compared to nanofluid flow. The values of other parameters in Tables 5 and 6 are taken as Rd=1.2, R=3, n=3, K=6, Pr=0.8, m=3, K1=2.5, δ=0.2, α=5, M=2.
In the comparison Tables 5 and 6, we have considered (a) ϕ1=0.2 and ϕ2=0 in the case of nanofluid (b) ϕ1=0.1 and ϕ2=0.1 in the case of hybrid nanofluid, where Al2O3→ϕ1 and Cu→ϕ2.
δ | R | N | K | Pr. | ϕ1 | ϕ2 | m | K1 | α | M | f″(η) |
0.5 | 5 | 3 | 0.3 | 0.6 | 0.5 | 0.03 | 2.5 | 5.5 | 2.5 | 1 | −0.000976 |
3.5 | −0.000699 | ||||||||||
8.5 | 0.000222 | ||||||||||
0.5 | 0.5 | 3 | 1 | 0.6 | 0.5 | 0.01 | 5 | 6.5 | 2.8 | 2 | 0.000165 |
3.5 | 0.000165 | ||||||||||
5.5 | 0.0001653 | ||||||||||
0.4 | 2 | 3 | 3 | 0.6 | 0.5 | 0.01 | 3.5 | 2 | 1 | 2 | 0.003354 |
6.3698 | 0.003354 | ||||||||||
16.1576 | 0.003354 | ||||||||||
0.5 | 5 | 3 | 1.5 | 0.6 | 0.5 | 0.02 | 5 | 5.5 | 2 | 1 | −0.001637 |
4.5 | −0.000945 | ||||||||||
9 | −0.000448 | ||||||||||
0.2 | 6 | 3 | 2 | 0.6 | 0.2 | 0.02 | 5 | 2.5 | 3 | 1 | −0.000035 |
0.8 | −0.000035 | ||||||||||
1 | −0.000035 | ||||||||||
0.2 | 6 | 2 | 1 | 0.6 | 0.1 | 0.02 | 5 | 2.5 | 3 | 2 | 0.000122 |
0.5 | 0.000610 | ||||||||||
0.6 | 0.000374 | ||||||||||
0.2 | 3 | 5 | 6 | 0.8 | 0.1 | 0.01 | 3 | 2.5 | 5 | 2 | 0.001575 |
0.09 | 0.001711 | ||||||||||
0.15 | 0.001724 | ||||||||||
0.3 | 1 | 3 | 5 | 0.8 | 0.5 | 0.05 | 1 | 1.5 | 2 | 1 | 0.000002 |
2 | −0.000330 | ||||||||||
3 | −0.001959 | ||||||||||
0.7 | 2.5 | 3 | 6 | 0.9 | 0.5 | 0.06 | 1.5 | 3 | 2 | 1 | 0.003838 |
4.5 | 0.001401 | ||||||||||
8 | −0.000379 | ||||||||||
0.4 | 2 | 1 | 3 | 0.6 | 0.5 | 0.01 | 3.5 | 2 | 1 | 1 | 0.000838 |
1.5 | 0.002978 | ||||||||||
2.5 | 0.003277 |
δ | R | N | K | Pr. | ϕ1 | ϕ2 | m | K1 | α | M | G'(η) |
0.5 | 5 | 3 | 0.3 | 0.6 | 0.5 | 0.03 | 2.5 | 5.5 | 2.5 | 1 | 0.000637 |
3.5 | 0.000821 | ||||||||||
8.5 | 0.001262 | ||||||||||
0.5 | 0.5 | 3 | 1 | 0.6 | 0.5 | 0.01 | 5 | 6.5 | 2.8 | 2 | 0.000525 |
3.5 | 0.000525 | ||||||||||
5.5 | 0.000525 | ||||||||||
0.4 | 2 | 3 | 3 | 0.6 | 0.5 | 0.01 | 3.5 | 2 | 1 | 2 | 0.003126 |
6.3698 | 0.003126 | ||||||||||
16.1576 | 0.003126 | ||||||||||
0.5 | 5 | 3 | 1.5 | 0.6 | 0.5 | 0.02 | 5 | 5.5 | 2 | 1 | 0.001389 |
4.5 | 0.001874 | ||||||||||
9 | 0.002749 | ||||||||||
0.2 | 6 | 3 | 2 | 0.6 | 0.2 | 0.02 | 5 | 2.5 | 3 | 1 | 0.000410 |
0.8 | 0.000410 | ||||||||||
1 | 0.000410 | ||||||||||
0.2 | 6 | 2 | 1 | 0.6 | 0.1 | 0.02 | 5 | 2.5 | 3 | 2 | 0.000037 |
0.5 | 0.001691 | ||||||||||
0.6 | 0.003608 | ||||||||||
0.2 | 3 | 5 | 6 | 0.8 | 0.1 | 0.01 | 3 | 2.5 | 5 | 2 | 0.000359 |
0.09 | 0.000304 | ||||||||||
0.15 | 0.000337 | ||||||||||
0.3 | 1 | 3 | 5 | 0.8 | 0.5 | 0.05 | 1 | 1.5 | 2 | 1 | −0.000000 |
2 | 0.000014 | ||||||||||
3 | 0.000023 | ||||||||||
0.7 | 2.5 | 3 | 6 | 0.9 | 0.5 | 0.06 | 1.5 | 3 | 2 | 1 | 0.001164 |
4.5 | 0.000586 | ||||||||||
8 | 0.000470 | ||||||||||
0.4 | 2 | 1 | 3 | 0.6 | 0.5 | 0.01 | 3.5 | 2 | 1 | 1 | 0.002425 |
1.5 | 0.002586 | ||||||||||
2.5 | 0.003882 |
δ | R | N | k | Pr. | ϕ1 | ϕ2 | m | K1 | α | M | θ'(η) |
0.5 | 5 | 3 | 0.3 | 0.6 | 0.5 | 0.03 | 2.5 | 5.5 | 2.5 | 1 | 0.239779 |
3.5 | 0.245450 | ||||||||||
8.5 | 0.258792 | ||||||||||
0.5 | 0.5 | 3 | 1 | 0.6 | 0.5 | 0.01 | 5 | 6.5 | 2.8 | 2 | 0.179407 |
3.5 | 0.229167 | ||||||||||
5.5 | 0.246877 | ||||||||||
0.4 | 2 | 3 | 3 | 0.6 | 0.5 | 0.01 | 3.5 | 2 | 1 | 2 | 0.211021 |
6.3698 | 0.246739 | ||||||||||
16.1576 | 0.282326 | ||||||||||
0.5 | 5 | 3 | 1.5 | 0.6 | 0.5 | 0.02 | 5 | 5.5 | 2 | 1 | 0.221892 |
4.5 | 0.214110 | ||||||||||
9 | 0.203964 | ||||||||||
0.2 | 6 | 3 | 2 | 0.6 | 0.2 | 0.02 | 5 | 2.5 | 3 | 1 | 0.067710 |
0.8 | 0.058471 | ||||||||||
1 | 0.050255 | ||||||||||
0.2 | 6 | 2 | 1 | 0.6 | 0.1 | 0.02 | 5 | 2.5 | 3 | 2 | 0.428781 |
0.5 | 0.433304 | ||||||||||
0.6 | 0.429139 | ||||||||||
0.2 | 3 | 5 | 6 | 0.8 | 0.1 | 0.01 | 3 | 2.5 | 5 | 2 | 0.040132 |
0.09 | 0.049593 | ||||||||||
0.15 | 0.055833 | ||||||||||
0.3 | 1 | 3 | 5 | 0.8 | 0.5 | 0.05 | 1 | 1.5 | 2 | 1 | 0.014491 |
2 | 0.012162 | ||||||||||
3 | 0.013738 | ||||||||||
0.7 | 2.5 | 3 | 6 | 0.9 | 0.5 | 0.06 | 1.5 | 3 | 2 | 1 | 0.180677 |
4.5 | 0.179365 | ||||||||||
8 | 0.177359 | ||||||||||
0.4 | 2 | 1 | 3 | 0.6 | 0.5 | 0.01 | 3.5 | 2 | 1 | 1 | 0.120237 |
1.5 | 0.144988 | ||||||||||
2.5 | 0.186923 |
Parameter | Skin Friction Cf | Nusselt Number Nu | Sherwood Number Sh | |||
M | Al2O3−EG | Al2O3−Cu/EG | Al2O3−EG | Al2O3−Cu/EG | Al2O3−EG | Al2O3−Cu/EG |
3 | −1.7899 | −2.3778 | −0.1511 | −0.1947 | 0.1326 | 0.1301 |
4 | −2.2672 | −2.9818 | −0.2240 | −0.2711 | 0.1132 | 0.1118 |
5 | −2.7581 | −3.6074 | −0.3036 | −0.3540 | 0.1001 | 0.0992 |
Parameter | Skin Friction Cf | Nusselt Number Nu | Sherwood Number Sh | |||
δ | Al2O3−EG | Al2O3−Cu/EG | Al2O3−EG | Al2O3−Cu/EG | Al2O3−EG | Al2O3−Cu/EG |
0.1 | −1.2860 | −1.7428 | 0.0829 | 0.0651 | 0.1660 | 0.1613 |
0.3 | −1.4054 | −1.9044 | −0.2762 | −0.3400 | 0.1563 | 0.1515 |
0.5 | −1.5478 | −2.0970 | −0.6996 | −0.8162 | 0.1437 | 0.1387 |
In this study, the microstructure and inertial characteristics of a magnetite ferrofluid over a non-linearly stretching sheet using the BVP4c method are examined. The effect of related parameters on stream function, velocity, micro-rotation velocity, and temperature are demonstrated graphically. Results revealed that:
(1) On the stream function subject, there is an inverse relation between magnetic and micro-rotation parameters.
(2) On the velocity subject, there is a reverse relation between boundary and micro-rotation parameters.
(3) On the micro-rotation velocity subject, in the deficiency of magnetic parameter, micro-rotation velocity is in the lowest form.
(4) On the temperature subject, the highest temperature is attained for the lowest value of the micro-rotation parameter.
The work done in this article can be extended for other non-Newtonian fluids, like, Maxwell fluid, Second grade fluid, and Oldroyd-B fluid, etc.
Nomenclature | σs Ferroparticles electric conductivity S/m |
I Body couple per unit mass | B0 Magnetic field intensity W/m2 |
u x-component of velocity m/s | F″ Coefficient of skin-friction |
ϕ,λ Spin gradient viscosity coefficients Pa.s | σnf Ferrofluid electric conductivity S/m |
j Micro-inertia density Kg/m3 | Cp,nf Ferrofluid heat capacity |
v y-component of velocity m/s | G Dimensionless micro-rotation velocity m/s |
μf Base fluid dynamic viscosity Pa.s | σ∗ Stefan-Boltzmann constant |
K Micro-rotation parameter | g Acceleration due to gravity |
V Velocity m/s | θ Dimensionless temperature |
μnf Ferrofluid dynamic viscosity Kg/ms | f Base fluid |
k∗ Mean absorption coefficient | p Pressure Kgm−1s−2 |
T The temperature of the fluid (℃) | ρf Base fluid density Kg/m3 |
ϕ Ferroparticles volume fraction | s Ferroparticle |
kf Base fluid thermal conductivity Wm−1K−1 | Pr Prandtl number m2/s |
Tw Wall temperature | ρs Ferroparticles density Kg/m3 |
δ Boundary parameter | hnf hybrid Ferrofluid |
ks Ferroparticle thermal conductivity Wm−1K−1 | qr Radiative heat flux |
T∞ Ambient temperature | ρhnf hybrid Ferrofluid density Kg/m3 |
κ Vortex viscosity | w Condition at wall |
knf Ferroparticle thermal conductivity Wm−1K−1 | R Radiative parameter α Stretching/shrinking parameter |
F Dimensionless stream function | ∞ Condition at infinity |
f Base fluid electric conductivity S/m | γnf Spin-gradient viscosity |
N Micro-rotation vector | F′ Dimensionless velocity m/s |
K1 local micro-rotation parameter |
This research received funding support from the NSRF via the Program Management Unit for Human Resources & Institutional Development, Research and Innovation, (grant number B05F650018).
The authors declare no conflict of interest.
[1] | S. U. S. Choi, J. Eastman, Enhancing thermal conductivity of fluids with nanoparticles, Asme Fed, 231 (1995), 99–103. |
[2] |
J. Buongiorno, D. C. Venerus, N. Prabhat, T. McKrell, J. Townsend, R. Christianson, et al., A benchmark study on the thermal conductivity of nanofluids, J. Appl. Phys., 106 (2009), 094312. https://doi.org/10.1063/1.3245330 doi: 10.1063/1.3245330
![]() |
[3] | K. R. Singh, P. R. Solanki, B. D. Malhotra, A. C. Pandey, R. P. Singh, Introduction to nanomaterials: An overview toward broad spectrum applications, nanomaterials in bionanotechnology, CRC Press: Boca Raton, FL, USA, 2021. https://doi.org/10.1201/9781003139744-1 |
[4] | K. Suvardhan, C. Rajasekhar, R. Mashallah, Smart nanodevices for point-of-care applications, CRC Press: Boca Raton, FL, USA, 2021. |
[5] |
S. Upadhya, S. V. Mamatha, S. R. Raju, C. S. R. Raju, N. A. Shah, J. D. Chung, Importance of entropy generation on Casson, Micropolar and Hybrid magneto-nanofluids in a suspension of cross diffusion, Chinese J. Phys., 77 (2022), 1080–1101. https://doi.org/10.1016/j.cjph.2021.10.016 doi: 10.1016/j.cjph.2021.10.016
![]() |
[6] |
Q. Lou, B. Ali, S. U. Rehman, D. Habib, S. Abdal, N. A. Shah, et al., Micropolar dusty fluid: Coriolis force effects on dynamics of MHD rotating fluid when Lorentz force is significant, Mathematics, 10 (2022), 2630. https://doi.org/10.3390/math10152630 doi: 10.3390/math10152630
![]() |
[7] |
Y. Li, M. Zhou, B. Cheng, Y. Shao, Recent advances in g-C3N4-based heterojunction photocatalysts, J. Mater. Sci. Technol., 56 (2020), 1–17. https://doi.org/10.1016/j.jmst.2020.04.028 doi: 10.1016/j.jmst.2020.04.028
![]() |
[8] |
N. A. Shah, A. Wakif, E. R. El-Zahar, S. Ahmad, S-J. Yook, Numerical simulation of a thermally enhanced EMHD flow of a heterogeneous micropolar mixture comprising (60%)-ethylene glycol (EG), (40%)-water (W), and copper oxide nanomaterials (CuO), Case Stud. Therm. Eng., 2022, 102046. https://doi.org/10.1016/j.csite.2022.102046 doi: 10.1016/j.csite.2022.102046
![]() |
[9] | R. E. Rosensweig, Ferrohydrodynamics, Cambridge University Press, Cambridge, England, 1985. |
[10] | S. U. S. Choi, D. A. Singer, H. P. Wang, Developments and applications of non-Newtonian flows, Asme Fed, 66 (1995), 99–105. |
[11] |
M. Hidetoshi, A. Ebata, K. Teramae, N. Hishiunma, Conductivity and viscosity of liquid by dispersed ultra-fine particles (dispersion of Al2O3, SiO2, and TiO2 ultra-fine particles), Netsu Bussei, 7 (1993). https://doi.org/10.2963/jjtp.7.227 doi: 10.2963/jjtp.7.227
![]() |
[12] |
M. Z. Ashraf, S. U. Rehman, S. Farid, A. K. Hussein, B. Ali, N. A. Shah, et al., Insight into significance of bioconvection on MHD tangent hyperbolic nanofluid flow of irregular thickness across a slender elastic surface, Mathematics, 10 (2022), 2592. https://doi.org/10.3390/math10152592 doi: 10.3390/math10152592
![]() |
[13] |
H. I. Andersson, O. A. Valnes, Flow of a heated ferrofluid over a stretching sheet in the presence of a magnetic dipole, Acta Mech., 128 (1998), 39–47. https://doi.org/10.1007/BF01463158 doi: 10.1007/BF01463158
![]() |
[14] |
H. I. Andersson, MHD flow of a viscoelastic fluid past a stretching surface, Acta Mech., 95 (1992), 227–230. https://doi.org/10.1007/BF01170814 doi: 10.1007/BF01170814
![]() |
[15] | B. Gabriella, On similarity solutions of MHD flow over a nonlinear stretching surface in non-Newtonian power-law fluid, Electron. J. Qual. Theo., 6 (2016), 1–12. |
[16] |
C. Fetecau, N. A. Shah, D. Vieru, General solutions for hydromagnetic free convection flow over an infinite plate with Newtonian heating, mass diffusion and chemical reaction, Commun. Theor. Phys., 68 (2017), 768–782. https://doi.org/10.1088/0253-6102/68/6/768 doi: 10.1088/0253-6102/68/6/768
![]() |
[17] |
A. S. Sabu, A. Wakif, S. Areekara, A. Mathew, N. A. Shah, Significance of nanoparticles' shape and thermo-hydrodynamic slip constraints on MHD alumina-water nanoliquid flows over a rotating heated disk: The passive control approach, Int. Commun. Heat Mass Tran., 129 (2021), 105711. https://doi.org/10.1016/j.icheatmasstransfer.2021.105711. doi: 10.1016/j.icheatmasstransfer.2021.105711
![]() |
[18] |
G. Bognár, K. Hriczó, Ferrofluid flow in the presence of magnetic dipole, Tech. Mech., 39 (2019), 3–15. https://doi.org/10.24874/ti.2019.41.03.12 doi: 10.24874/ti.2019.41.03.12
![]() |
[19] |
I. A. Abdallah, Analytic solution of heat and mass transfer over a permeable stretching plate affected by chemical reaction, internal heating, Dufour-Soret effect and Hall effect, Therm. Sci., 13 (2009), 183–197. https://doi.org/10.2298/TSCI0902183A doi: 10.2298/TSCI0902183A
![]() |
[20] |
A. Zeeshan, A. Majeed, R. Ellahi, Effect of magnetic dipole on viscous ferrofluid past a stretching surface with thermal radiation, J. Mol. Liq., 215 (2016), 549–554. https://doi.org/10.1016/j.molliq.2015.12.110 doi: 10.1016/j.molliq.2015.12.110
![]() |
[21] |
M. Nawaz, A. Zeeshan, R. Ellahi, S. Abbasbandy, S. Rashidi, Joules and Newtonian heating effects on stagnation point flow over a stretching surface by means of genetic algorithm and Nelder-Mead method, Int. J. Numer. Method. H., 25 (2015), 665–684. https://doi.org/10.1108/HFF-04-2014-0103 doi: 10.1108/HFF-04-2014-0103
![]() |
[22] |
K. Saeed, M. Shaban, S. Abbasbandy, Improved analytical solutions to a stagnation-point flow past a porous stretching sheet with heat generation, J. Franklin I., 348 (2011), 2044–2058. https://doi.org/10.1016/j.jfranklin.2011.05.020 doi: 10.1016/j.jfranklin.2011.05.020
![]() |
[23] |
T. Hayat, T. Javed, Z. Abbas, Slip flow and heat transfer of a second-grade fluid past a stretching sheet through a porous space, Int. J. Heat Mass Tran., 51 (2008), 4528–4534. https://doi.org/10.1016/j.ijheatmasstransfer.2007.12.022 doi: 10.1016/j.ijheatmasstransfer.2007.12.022
![]() |
[24] |
J. M. Martin, I. D. Boyd, Momentum and heat transfer in a laminar boundary layer with slip flow, J. Thermophysics Heat Tr., 20 (2006), 710–719. https://doi.org/10.2514/1.22968 doi: 10.2514/1.22968
![]() |
[25] |
M. E. Ali, The effect of variable viscosity on mixed convection heat transfer along a vertical moving surface, Int. J. Therm. Sci., 45 (2006), 60–69. https://doi.org/10.1016/j.ijthermalsci.2005.04.006 doi: 10.1016/j.ijthermalsci.2005.04.006
![]() |
[26] |
Q. Li, Y. Xuan, Experimental investigation on heat transfer characteristics of magnetic fluid flow around a fine wire under the influence of an external magnetic field, Exp. Therm. Fluid Sci., 33 (2009), 591–596. https://doi.org/10.1016/j.expthermflusci.2008.12.003 doi: 10.1016/j.expthermflusci.2008.12.003
![]() |
[27] |
H. Yamaguchi, Z. Zhang, S. Shuchi, K. Shimada, Heat transfer characteristics of magnetic fluid in a partitioned rectangular box, J. Magn. Magn. Mater., 252 (2002), 203–205. https://doi.org/10.1016/S0304-8853(02)00731-X doi: 10.1016/S0304-8853(02)00731-X
![]() |
[28] |
M. Motozawa, J. Chang, T. Sawada, Y. Kawaguchi, Effect of magnetic field on heat transfer in rectangular duct flow of a magnetic fluid, Phys. Procedia, 9 (2010) 190–193. https://doi.org/10.1016/j.phpro.2010.11.043 doi: 10.1016/j.phpro.2010.11.043
![]() |
[29] |
J. Bahram, S. Sadighi, P. Jalili, D. D. Ganji, Characteristics of ferrofluid flow over a stretching sheet with suction and injection, Case Stud. Therm. Eng., 14 (2019), 100470. https://doi.org/10.1016/j.csite.2019.100470 doi: 10.1016/j.csite.2019.100470
![]() |
[30] |
Z. Ziabakhsh, G. Domairry, H. Bararnia, Analytical solution of non-Newtonian micropolar fluid flow with uniform suction/blowing and heat generation, J. Taiwan Inst. Chem. E., 40 (2009), 443–451. https://doi.org/10.1016/j.jtice.2008.12.005 doi: 10.1016/j.jtice.2008.12.005
![]() |
[31] |
M. Ramzan, M. Farooq, T. Hayat, J. D. Chung, Radiative and Joule heating effects in the MHD flow of a micropolar fluid with partial slip and convective boundary condition, J. Mol. Liq., 221 (2016), 394–400. https://doi.org/10.1016/j.molliq.2016.05.091 doi: 10.1016/j.molliq.2016.05.091
![]() |
1. | Muhammad Tahir, Yasir Khan, Adeel Ahmad, Impact of pseudoplastic and dilatants behavior of Reiner-Philippoff nanofluid on peristaltic motion with heat and mass transfer analysis in a tapered channel, 2023, 8, 2473-6988, 7115, 10.3934/math.2023359 | |
2. | Muhammad Amin Sadiq Murad, Faraidun Kadir Hamasalh, Hajar F. Ismael, Numerical study of stagnation point flow of Casson-Carreau fluid over a continuous moving sheet, 2023, 8, 2473-6988, 7005, 10.3934/math.2023353 | |
3. | Rajeev Anandika, V. Puneeth, S. Manjunatha, The Darcy–Forechhiemer multilayer model of Casson nanofluid squeezed by Newtonian nanofluid under asymmetric slip conditions, 2022, 137, 2190-5444, 10.1140/epjp/s13360-022-03497-7 | |
4. | Yongzhuang Tang, Qidou Zhou, Xiaowei Wang, Zhiyong Xie, Ghulam Rasool, A Computational Method for Acoustic Interaction with Large Complicated Underwater Structures Based on the Physical Mechanism of Structural Acoustics, 2022, 2022, 1687-8442, 1, 10.1155/2022/3631241 | |
5. | Amjad Ali, Zainab Bukhari, Muhammad Amjad, Sohail Ahmad, Wasim Jamshed, Sayed M. El Din, Heat transfer analysis of the MHD stagnation-point flow of third-grade fluid over a porous sheet with thermal radiation effect: An algorithmic approach, 2023, 21, 2391-5471, 10.1515/phys-2022-0227 | |
6. | Yihao Shao, Huai Yang, Xiuya Guo, Huili Wang, Limei Zhu, Xuan Ma, Ruijuan Chen, Shufen Ruan, Lulu Ren, Qian Zheng, Thermal Conductivity Model of Porous Media Embedded with a Damaged Tree-like Branching Network Considering the Influence of Roughness, 2022, 7, 2504-3110, 5, 10.3390/fractalfract7010005 | |
7. | I. Rashid, T. Zubair, M. I. Asjad, S. Irshad, S. M. Eldin, The MHD graphene−CMC−water nanofluid past a stretchable wall with Joule heating and velocity slip impact: Coolant application, 2023, 10, 2296-424X, 10.3389/fphy.2022.1065982 | |
8. | Liaquat Ali Lund, Ubaidullah Yashkun, Nehad Ali Shah, Magnetohydrodynamics streamwise and cross flow of hybrid nanofluid along the viscous dissipation effect: Duality and stability, 2023, 35, 1070-6631, 023320, 10.1063/5.0135361 | |
9. | R. Padmavathi, B.S. Dhruvathara, K. Rashmi, K. Ganesh Kumar, Two-phase hydromagnetic Eyring-Powell fluid flow over a stretching sheet suspended to a dusty particle, 2023, 0228-6203, 1, 10.1080/02286203.2023.2185073 | |
10. | Wasfi Shatanawi, Nadeem Abbas, Taqi A.M. Shatnawi, Fady Hasan, Heat and mass transfer of generalized fourier and Fick's law for second-grade fluid flow at slendering vertical Riga sheet, 2023, 9, 24058440, e14250, 10.1016/j.heliyon.2023.e14250 | |
11. | Sunendra Shukla, Ram Prakash Sharma, R. J. Punith Gowda, B. C. Prasannakumara, Elastic deformation effect on carboxymethyl cellulose water-based (TiO2–Ti6Al4V) hybrid nanoliquid over a stretching sheet with an induced magnetic field, 2023, 1040-7782, 1, 10.1080/10407782.2023.2175750 | |
12. | M. Bilal, M. Safdar, S. Ahmed, R. Ahmad Khan, Analytic similarity solutions for fully resolved unsteady laminar boundary layer flow and heat transfer in the presence of radiation, 2023, 9, 24058440, e14765, 10.1016/j.heliyon.2023.e14765 | |
13. | Somayeh Davoodabadi Farahani, Amir Davoodabadi Farahani, Amirhossein Jazari mamoei, Hakan F. Öztop, Scrutiny of melting rate of phase change material in a four petals cavity with internal Branch fins under magnetic field, 2023, 03048853, 170727, 10.1016/j.jmmm.2023.170727 | |
14. | Nosheen Feroz, Brownian motions and thermophoresis effects in a vertically stretching sheet with micropolar nanofluid flow, 2024, 38, 0217-9849, 10.1142/S0217984924500593 | |
15. | Xiaomang Miao, Fahid Riaz, Badr Alotaibi, Manoj Kumar Agrawal, Mohammed Abuhussain, Theyab R. Alsenani, Mansoureh Alizadeh Balderlou, Qing Lin, Performance enhancement of latent heat thermal energy storage system by using spiral fins in phase change material solidification process, 2023, 176, 09575820, 568, 10.1016/j.psep.2023.05.102 | |
16. | H. Ashraf, Ayesha Siddiqa, Hamood Ur Rehman, A. M. Siddiqui, Jamshaid Ul Rahman, Lifting and drainage of Sisko fluid film with surface tension: A theoretical study on stationary points and thickness of uniform film, 2023, 37, 0217-9792, 10.1142/S0217979223503046 | |
17. | Supriya Devi, K. V. Nagaraja, Amit Verma, Pressure and flow transition over NACA airfoil with thrust optimized parabolic arcs, 2023, 37, 0217-9792, 10.1142/S0217979223502958 | |
18. | Samah Maatoug, Kamel Al-Khaled, Ali Raza, Taher Labidi, Lioua Kolsi, Wathek Chammam, Muqrin Almuqrin, Sami Ullah Khan, Fractional computations for free convective flow of Casson-hybrid nanofluid flow with sodium alginate and water as based materials, 2024, 38, 0217-9792, 10.1142/S0217979224502400 | |
19. | I. Sakthi, Raja Das, P. Bala Anki Reddy, Entropy generation on MHD flow of second-grade hybrid nanofluid flow over a converging/diverging channel: an application in hyperthermia therapeutic aspects, 2024, 233, 1951-6355, 1233, 10.1140/epjs/s11734-023-00947-w | |
20. | Fehmi Gamaoun, B. M. Shankaralingappa, K. Thanesh Kumar, B. Shanker, Raman Kumar, R. J. Punith Gowda, Consequence of the direction of uniform horizontal magnetic field on nanolubricant flow over a permeable rotating disk, 2024, 38, 0217-9849, 10.1142/S0217984924501732 | |
21. | Moh Yaseen, Sawan Kumar Rawat, Umair Khan, Ioannis E Sarris, Humera Khan, Anup Singh Negi, Arshad Khan, El-Sayed M Sherif, Ahmed M Hassan, Aurang Zaib, Numerical analysis of magnetohydrodynamics in an Eyring–Powell hybrid nanofluid flow on wall jet heat and mass transfer, 2023, 34, 0957-4484, 485405, 10.1088/1361-6528/acf3f6 | |
22. | Yasir Nawaz, Muhammad Shoaib Arif, Amna Nazeer, Javeria Nawaz Abbasi, Kamaleldin Abodayeh, A two‐stage reliable computational scheme for stochastic unsteady mixed convection flow of Casson nanofluid, 2024, 96, 0271-2091, 719, 10.1002/fld.5264 | |
23. | C. G. Pavithra, B. J. Gireesha, Impact of new similarity transformations on heat transfer analysis of Casson tri-hybrid nanofluid in blood with thermal radiation through a stretching sheet: a homotopy perturbation Sumudu transformation approach, 2024, 0228-6203, 1, 10.1080/02286203.2024.2327608 | |
24. | Pudhari Srilatha, R. J. Punith Gowda, J. Madhu, K. V. Nagaraja, Fehmi Gamaoun, R. S. Varun Kumar, K. Karthik, Designing a solid–fluid interface layer and artificial neural network in a nanofluid flow due to rotating rough and porous disk, 2024, 149, 1388-6150, 867, 10.1007/s10973-023-12706-z | |
25. | A. Sumithra, R. Sivaraj, V. Ramachandra Prasad, O. Anwar Bég, Ho-Hon Leung, Firuz Kamalov, S. Kuharat, B. Rushi Kumar, Computation of inclined magnetic field, thermophoresis and Brownian motion effects on mixed convective electroconductive nanofluid flow in a rectangular porous enclosure with adiabatic walls and hot slits, 2024, 38, 0217-9792, 10.1142/S0217979224503983 | |
26. | B.J. Gireesha, C.G. Pavithra, , Impact of new similarity transformation on analysis of nanoparticle shape effects on Casson nanofluid flow and heat transfer over a nonlinear stretching sheet with radiation, 2024, 0228-6203, 1, 10.1080/02286203.2024.2394776 | |
27. | Ikram Ullah, Saira Shukat, Ashwag Albakri, Hamid Khan, Ahmed M. Galal, Wasim Jamshed, Thermal performance of aqueous alumina–titania hybrid nanomaterials dispersed in rotating channel, 2023, 37, 0217-9792, 10.1142/S0217979223502375 | |
28. | Abdul Rauf, Fiaz Hussain, Aqsa Mushtaq, Nehad Ali Shah, Mohamed R. Ali, MHD mixed convection flow for Maxwell Hybrid nanofluid with Soret, Dufour and Morphology effects, 2023, 16, 18785352, 104965, 10.1016/j.arabjc.2023.104965 | |
29. | V. Jyothi, B. N. Hanumagowda, Raghawendra Mishra, Jagadish. V. Tawade, Raman Kumar, B. Shanker, R. S. Varun Kumar, Significance of slip velocity and couple-stress fluid lubrication on experiencing object sphere subject to Lorentz forces, 2024, 38, 0217-9849, 10.1142/S0217984924501276 | |
30. | V. Jyothi, B. N. Hanumagowda, Amit Verma, Analysis of pressure load-carrying capacity and squeezing time on magnetohydrodynamic couple stress fluid flow between sphere and flat plate with slip velocity, 2024, 38, 0217-9792, 10.1142/S0217979224503491 | |
31. | Qadeer Raza, Xiaodong Wang, Hussein A. H. Muhammed, M. Zubair Akbar Qureshi, Ali J. Chamkha, Hassan Ali Ghazwani, Bio-convection of ternary magnetized nanoparticles thermal conductivity in chemical reaction and activation energy flow with Darcy Forchheimer permeable across a double porous medium, 2024, 1040-7782, 1, 10.1080/10407782.2024.2316210 | |
32. | Shilpa B., Pudhari Srilatha, Umair Khan, Naveen Kumar R., Samia Ben Ahmed, Raman Kumar, Numerical study of thermal and solutal advancements in ZnO–SAE50 nanolubricant flow past a convergent/divergent channel with the effects of thermophoretic particle deposition, 2023, 5, 2516-0230, 6647, 10.1039/D3NA00816A | |
33. | Thimlapura Nagaraju Tanuja, Linganna Kavitha, Pudhari Srilatha, Umair Khan, Sibyala Vijaykumar Varma, Rangaswamy Naveen Kumar, Amal Abdulrahman, Mohammed Modather Mohammed Abdou, Effects of dissipation and radiation on the Jeffrey fluid flow in between nano and hybrid nanofluid subject to porous medium, 2024, 104, 0044-2267, 10.1002/zamm.202300852 | |
34. | J.K. Madhukesh, G.K. Ramesh, Krishna B. Chavaraddi, Emad H. Aly, Bander Almutairi, Nehad Ali Shah, Impact of active and passive control of nanoparticles in ternary nanofluids across a rotating sphere, 2023, 54, 22113797, 107069, 10.1016/j.rinp.2023.107069 | |
35. | Girish Sharma, B. N. Hanumagowda, S. V. K. Varma, R. Naveen Kumar, A. S. Alqahtani, M. Y. Malik, Impact of magnetic field and nonlinear radiation on the flow of Brinkmann-type chemically reactive hybrid nanofluid: a numerical study, 2024, 149, 1388-6150, 745, 10.1007/s10973-023-12720-1 | |
36. | B. Lavanya, J. Girish Kumar, M. Jayachandra Babu, C.S.K. Raju, Bander Almutairi, Nehad Ali Shah, Entropy generation minimization in the Carreau nanofluid flow over a convectively heated inclined plate with quadratic thermal radiation and chemical reaction: A Stefan blowing application, 2024, 13, 2212540X, 233, 10.1016/j.jppr.2024.04.004 | |
37. | Abdul Hamid Ganie, Ali M. Mahnashi, Ahmad Shafee, Rasool Shah, Dowlath Fathima, Peristaltic transport with multiple solutions of heat and mass transfer using modified Buongiorno nanofluid model over tapered channel with long wave‐length at small Reynolds number, 2024, 104, 0044-2267, 10.1002/zamm.202400110 | |
38. | Sun Yi, Azher M. Abed, Ahmed Deifalla, M. Riaz, Theyab R. Alsenani, Samia Elattar, Chun Yulei, Saleh Al Sulaie, Exergoeconomic evaluation of a novel multigeneration process using solar driven Kalina cycle integrated with gas turbine cycle, double-effect absorption chiller, and liquefied natural gas cold energy recovery, 2023, 176, 09575820, 271, 10.1016/j.psep.2023.05.077 | |
39. | M. B. Rekha, K. R. Raghunatha, K. Vinutha, Ankit Kedia, Jasgurpreet Singh Chohan, An analytical solution of MHD non-Newtonian fluid flow over a stretching surface with mixed convection and porous media, 2025, 8, 2520-8160, 10.1007/s41939-024-00614-0 | |
40. | Madhu J, Shreedevi Kalyan, Yamanappa Gudagi, Varun Kumar R S, Raman Kumar, S. Sureshkumar, Fluid sustainability by the effect of microrotational flow and chemical reactions in a vertical channel, 2024, 0228-6203, 1, 10.1080/02286203.2024.2319008 | |
41. | Kezheng Zhang, C.S.K. Raju, Kiran Sajjan, Bander Almutairi, Nehad Ali Shah, Sayed M. Eldin, Nonlinear free convective with longitudinal slits in the presence of super-hydrophobic and non-hydrophobic microchannels in a suspension of nanoparticles: Multi-Linear Regression Analysis, 2023, 49, 2214157X, 103138, 10.1016/j.csite.2023.103138 | |
42. | Muhammad Bilal, Aatif Ali, Samy Refahy Mahmoud, Elsayed Tag-Eldin, Mohammed Balubaid, Fractional analysis of unsteady radiative brinkman-type nanofluid flow comprised of CoFe2O3 nanoparticles across a vertical plate, 2023, 148, 1388-6150, 13869, 10.1007/s10973-023-12705-0 | |
43. | Tesymol Cyriac, B. N. Hanumagowda, M. Umeshaiah, Vijaya Kumar, Jasgurpreet Singh Chohan, R. Naveen Kumar, K. Karthik, Performance of rough secant slider bearing lubricated with couple stress fluid in the presence of magnetic field, 2024, 38, 0217-9849, 10.1142/S0217984924501409 | |
44. | Maha Alammari, Numerical framework of magnetized thermal Casson nanoliquid flow with time-dependent stretching channel enclosing chemical reaction effect and variable fluid properties: A Particle Swarm Optimization with stability, 2024, 38, 0217-9849, 10.1142/S0217984924501094 | |
45. | Temjennaro Jamir, Hemanta Konwar, Bendangwapang Tzudir, Soret and dufour effects on unsteady non-linear mixed convection flow past a stretching sheet influenced by non-linear thermal radiation, 2024, 1040-7782, 1, 10.1080/10407782.2024.2325675 | |
46. | Z. Abbas, T. Rahim, J. Hasnain, N. Abid, Z.M. Shah, Entropy generation analysis of multi-mass diffusion in a nanofluid-interfaced three-phase viscous fluid in an inclined channel, 2023, 49, 2214157X, 103368, 10.1016/j.csite.2023.103368 | |
47. | Sneha Gajbhiye, Arundhati Warke, Katta Ramesh, Mathematical modeling and analysis of immiscible metallic based nanofluid flow in a microchannel with non-spherical nanoparticles, 2023, 213, 03784754, 40, 10.1016/j.matcom.2023.05.022 | |
48. | Reshu Gupta, Susmay Nandi, Shyam Sundar Santra, Sandip Saha, Kuppalapalle Vajravelu, Numerical simulation of an unsteady ternary hybrid nanofluid along a convectively heated curved stretching sheet: A Tiwari-Das model, 2024, 2397-7914, 10.1177/23977914241286681 | |
49. | Heng Chen, Ibrahim B. Mansir, Bhupendra Singh Chauhan, Ahmed Al-Zahrani, Ahmed Deifalla, Yinhai Hua, Fan Peng, A comprehensive numerical study on the effectiveness of a rotational-based PTC collector integrated porous foam and PV module, 2023, 215, 09601481, 118869, 10.1016/j.renene.2023.05.127 | |
50. | Mahi Jaiswal, B. N. Hanumagowda, P V Ananth Subray, S. V. K. Varma, Umair Khan, Ioannis E. Sarris, El-Sayed M. Sherif, Thermal scrutinization of a triangular porous fin induced by linear and nonlinear temperature-dependent heat generation and magnetic field effect: the case of Darcy model, 2024, 1951-6355, 10.1140/epjs/s11734-024-01114-5 | |
51. | Se-Jin Yook, C.S.K. Raju, Bander Almutairi, S.U. Mamatha, Nehad Ali Shah, Sayed M. Eldin, Heat and momentum diffusion of ternary hybrid nanoparticles in a channel with dissimilar permeability's and moving porous walls: A Multi-linear regression, 2023, 47, 2214157X, 103133, 10.1016/j.csite.2023.103133 | |
52. | Hossam A. Nabwey, Zia Ullah, Asifa Ilyas, Muhammad Ashraf, Ahmed M. Rashad, Sumayyah I. Alshber, Miad Abu Hawsah, Qingkai Zhao, Reduced Gravity and Magnetohydrodynamic Effects on Transient Mixed Convection Flow Past a Magnetized Heated Cone Embedded in Porous Medium, 2023, 2023, 2314-4785, 1, 10.1155/2023/9618432 | |
53. | P. Priyadharshini, M. Vanitha Archana, Nehad Ali Shah, Mansoor H. Alshehri, Ternary Hybrid Nanofluid Flow Emerging on a Symmetrically Stretching Sheet Optimization with Machine Learning Prediction Scheme, 2023, 15, 2073-8994, 1225, 10.3390/sym15061225 | |
54. | M. Nagapavani, G. Venkata Ramana Reddy, Amit Verma, Raghawendra Mishra, Thanesh Kumar, Significance of Arrhenius activation energy and binary chemical reaction in ternary hybrid nanofluid flow over a convectively heated porous curved surface: A passive control strategy, 2023, 37, 0217-9792, 10.1142/S0217979223502910 | |
55. | Sameh A. Hussein, Anas A. M. Arafa, Abdelhafeez Elshekhipy, Nawal Hassan Almalki, Lulwah AL-Essa, Yasir Akbar, Radiative and dissipative MHD Eyring–Powell nanofluid bioconvective flow through peristaltic waves in the presence of bilateral chemical reaction with Arrhenius activation energy: Entropy optimization, 2023, 1040-7782, 1, 10.1080/10407782.2023.2292199 | |
56. | M. Nagapavani, G. Venkata Ramana Reddy, M. D. Alsulami, Cubic auto-catalysis chemical reaction in non-Newtonian nanolubricant flow over a convectively heated rotating porous disk, 2023, 37, 0217-9792, 10.1142/S0217979223503010 | |
57. | H. Ashraf, A. M. Siddiqui, A. Walait, Hamood Ur Rehman, M. Irfan, On the analysis of time-dependent drainage of Sisko fluid film slowly down a vertical belt, 2023, 37, 0217-9792, 10.1142/S021797922350306X | |
58. | Kanwal Jabeen, Bioconvective Carreau nanofluid flow with magnetic dipole, viscous, and ohmic dissipation effects subject to Arrhenius activation energy, 2024, 85, 1040-7782, 2341, 10.1080/10407782.2023.2221005 | |
59. | H. Ashraf, Sadia Sabir, A.M. Siddiqui, Hamood Ur Rehman, Bander Almutairi, Nehad Ali Shah, Heat transfer analysis of temperature dependent viscosity Johnson–Segalman fluid film flow on a vertical heated belt, 2023, 49, 2214157X, 103362, 10.1016/j.csite.2023.103362 | |
60. | Kezheng Zhang, Yang Li, Mansoor Alshehri, Nehad Ali Shah, B.C. Prasannakumara, Cross-diffusion and heat transfer effects on peristaltic flow of Reiner-Philippoff nanofluid with pseudoplastic and dilatant fluids over tapered channel: Multiple solutions and stability analysis, 2024, 59, 2214157X, 104548, 10.1016/j.csite.2024.104548 | |
61. | Maddina Dinesh Kumar, Gunisetty Ramasekhar, C. S. K. Raju, Bander Almutairi, Nehad Ali Shah, Enhanced heat transfer analysis on axisymmetric hydro-magnetic flow through a contracting or expanding Darcy porous channels, 2023, 138, 2190-5444, 10.1140/epjp/s13360-023-04543-8 | |
62. | P V Ananth Subray, B N Hanumagowda, S V K Varma, Jasgurpreet Singh Chouhan, K M Yogeesha, J Madhu, R Naveen Kumar, Impact of electromagnetic field on three-phase flow of dissipative and radiative Casson hybrid nanofluid with internal heat generation/absorption, 2024, 98, 0973-7111, 10.1007/s12043-023-02724-9 | |
63. | Abdullah Alhushaybari, Waris Khan, Aiedh Mrisi Alharthi, Fawziah M. Alotaibi, Hakim AL Garalleh, Stability analysis of Reiner–Philippoff nanofluid flow due to sinusoidal waves past a nonuniform channel with Brownian and thermophoretic diffusions, 2024, 1040-7790, 1, 10.1080/10407790.2024.2379004 | |
64. | Amjad Salamah M Aljaloud, Physical interference of magnetic dipole for retardation type nanofluid with bioconvection phenomenon, 2023, 37, 0217-9792, 10.1142/S0217979223503101 | |
65. | Ram Prakash Sharma, J. K. Madhukesh, Sunendra Shukla, Fehmi Gamaoun, B. C. Prasannakumara, Numerical study of the thermophoretic velocity of ternary hybrid nanofluid in a microchannel bounded by the two parallel permeable flat plates, 2023, 148, 1388-6150, 14069, 10.1007/s10973-023-12691-3 | |
66. | Ubaidullah Yashkun, Liaquat Ali Lund, Mustafa Abbas Fadhel, Nehad Ali Shah, Velocity slip effect on magnetized casson nanofluid over shrinking/stretching cylinder: duality and stability analysis, 2024, 99, 0031-8949, 025203, 10.1088/1402-4896/ad1795 | |
67. | Naveed Imran, Maryiam Javed, Muhammad Sohail, Mubashir Qayyum, Raja Mehmood Khan, Multi-objective study using entropy generation for Ellis fluid with slip conditions in a flexible channel, 2023, 37, 0217-9792, 10.1142/S0217979223503162 | |
68. | Humaira Yasmin, Azzh Saad Alshehry, Abdul Hamid Ghanie, Rasool Shah, Stability of non-Newtonian nanofluid movement with heat/mass transportation passed through a hydro magnetic elongating/contracting sheet: multiple branches solutions, 2023, 13, 2045-2322, 10.1038/s41598-023-44640-3 | |
69. | K. Sakkaravarthi, Bala Anki Reddy P, Entropy generation on MHD flow of Williamson hybrid nanofluid over a permeable curved stretching/shrinking sheet with various radiations, 2024, 85, 1040-7790, 231, 10.1080/10407790.2023.2231633 | |
70. | Sidra Afzal, Mubashir Qayyum, Ali Akgül, Ahmed M. Hassan, Heat transfer enhancement in engine oil based hybrid nanofluid through combustive engines: An entropy optimization approach, 2023, 52, 2214157X, 103803, 10.1016/j.csite.2023.103803 | |
71. | Puneet Rana, Vishal Gupta, Lokendra Kumar, Thermal instability analysis in magneto-hybrid nanofluid layer between rough surfaces with variable gravity and space-dependent heat source, 2024, 38, 0217-9792, 10.1142/S0217979224500516 | |
72. | J. Ait lahcen, Y. Ezaier, A. Hader, S. Moushi, R. Et Touizi, Y. Hariti, I. Tarras, F. Z. Krimech, A. Wakif, Numerical study of the nanoparticles effect on the desalination process, 2024, 38, 0217-9792, 10.1142/S0217979224501364 | |
73. | S. Sureshkumar, Krishna B. Chavaraddi, Priya M. Gouder, G. K. Ramesh, Praveen I. Chandaragi, Thermoconvective instability in a ferrofluid saturated porous layer, 2023, 37, 0217-9792, 10.1142/S0217979223503095 | |
74. | Liaquat Ali Lund, Ubaidullah Yashkun, Nehad Ali Shah, Multiple solutions of unsteady Darcy–Forchheimer porous medium flow of Cu–Al2O3/water based hybrid nanofluid with joule heating and viscous dissipation effect, 2024, 149, 1388-6150, 2303, 10.1007/s10973-023-12819-5 | |
75. | Nehad Ali Shah, Shahida Rehman, Dumitru Vieru, Se-Jin Yook, Unsteady flows of micropolar fluids parallel to the axis of an annular domain with a porous layer, 2023, 76, 11100168, 275, 10.1016/j.aej.2023.06.019 | |
76. | Umer Farooq, Musawara Safeer, Jifeng Cui, Muzamil Hussain, Nitasha Naheed, Forced convection analysis of Williamson-based magnetized hybrid nanofluid flow through a porous medium: Nonsimilar modeling, 2024, 1040-7790, 1, 10.1080/10407790.2023.2300704 | |
77. | Sana Ullah Saqib, Umar Farooq, Nahid Fatima, Yin-Tzer Shih, Ahmed Mir, Lioua Kolsi, Novel Recurrent Neural Networks for Efficient Heat Transfer Analysis in Radiative Moving Porous Triangular Fin with Heat Generation, 2024, 2214157X, 105516, 10.1016/j.csite.2024.105516 | |
78. | Ghaliah Alhamzi, Badr Saad T. Alkahtani, Ravi Shanker Dubey, Vinutha Kalleshachar, Neelima Nizampatnam, Impact of Pollutant Concentration and Particle Deposition on the Radiative Flow of Casson-Micropolar Fluid between Parallel Plates, 2025, 142, 1526-1506, 665, 10.32604/cmes.2024.055500 |
Thermophysical property | Fluid (EG) | Alumina (Al2O3) | Cu |
ρ(kg/m3) | 1114.0 | 3970 | 8933 |
cp(j/kg.K) | 2415 | 765 | 385 |
k(w/m.K) | 0.2520 | 40 | 400 |
σ(s/smm) | 5.50×10−6 | 59.6×106 | 35×106 |
δ | R | N | K | Pr. | ϕ1 | ϕ2 | m | K1 | α | M | f″(η) |
0.5 | 5 | 3 | 0.3 | 0.6 | 0.5 | 0.03 | 2.5 | 5.5 | 2.5 | 1 | −0.000976 |
3.5 | −0.000699 | ||||||||||
8.5 | 0.000222 | ||||||||||
0.5 | 0.5 | 3 | 1 | 0.6 | 0.5 | 0.01 | 5 | 6.5 | 2.8 | 2 | 0.000165 |
3.5 | 0.000165 | ||||||||||
5.5 | 0.0001653 | ||||||||||
0.4 | 2 | 3 | 3 | 0.6 | 0.5 | 0.01 | 3.5 | 2 | 1 | 2 | 0.003354 |
6.3698 | 0.003354 | ||||||||||
16.1576 | 0.003354 | ||||||||||
0.5 | 5 | 3 | 1.5 | 0.6 | 0.5 | 0.02 | 5 | 5.5 | 2 | 1 | −0.001637 |
4.5 | −0.000945 | ||||||||||
9 | −0.000448 | ||||||||||
0.2 | 6 | 3 | 2 | 0.6 | 0.2 | 0.02 | 5 | 2.5 | 3 | 1 | −0.000035 |
0.8 | −0.000035 | ||||||||||
1 | −0.000035 | ||||||||||
0.2 | 6 | 2 | 1 | 0.6 | 0.1 | 0.02 | 5 | 2.5 | 3 | 2 | 0.000122 |
0.5 | 0.000610 | ||||||||||
0.6 | 0.000374 | ||||||||||
0.2 | 3 | 5 | 6 | 0.8 | 0.1 | 0.01 | 3 | 2.5 | 5 | 2 | 0.001575 |
0.09 | 0.001711 | ||||||||||
0.15 | 0.001724 | ||||||||||
0.3 | 1 | 3 | 5 | 0.8 | 0.5 | 0.05 | 1 | 1.5 | 2 | 1 | 0.000002 |
2 | −0.000330 | ||||||||||
3 | −0.001959 | ||||||||||
0.7 | 2.5 | 3 | 6 | 0.9 | 0.5 | 0.06 | 1.5 | 3 | 2 | 1 | 0.003838 |
4.5 | 0.001401 | ||||||||||
8 | −0.000379 | ||||||||||
0.4 | 2 | 1 | 3 | 0.6 | 0.5 | 0.01 | 3.5 | 2 | 1 | 1 | 0.000838 |
1.5 | 0.002978 | ||||||||||
2.5 | 0.003277 |
δ | R | N | K | Pr. | ϕ1 | ϕ2 | m | K1 | α | M | G'(η) |
0.5 | 5 | 3 | 0.3 | 0.6 | 0.5 | 0.03 | 2.5 | 5.5 | 2.5 | 1 | 0.000637 |
3.5 | 0.000821 | ||||||||||
8.5 | 0.001262 | ||||||||||
0.5 | 0.5 | 3 | 1 | 0.6 | 0.5 | 0.01 | 5 | 6.5 | 2.8 | 2 | 0.000525 |
3.5 | 0.000525 | ||||||||||
5.5 | 0.000525 | ||||||||||
0.4 | 2 | 3 | 3 | 0.6 | 0.5 | 0.01 | 3.5 | 2 | 1 | 2 | 0.003126 |
6.3698 | 0.003126 | ||||||||||
16.1576 | 0.003126 | ||||||||||
0.5 | 5 | 3 | 1.5 | 0.6 | 0.5 | 0.02 | 5 | 5.5 | 2 | 1 | 0.001389 |
4.5 | 0.001874 | ||||||||||
9 | 0.002749 | ||||||||||
0.2 | 6 | 3 | 2 | 0.6 | 0.2 | 0.02 | 5 | 2.5 | 3 | 1 | 0.000410 |
0.8 | 0.000410 | ||||||||||
1 | 0.000410 | ||||||||||
0.2 | 6 | 2 | 1 | 0.6 | 0.1 | 0.02 | 5 | 2.5 | 3 | 2 | 0.000037 |
0.5 | 0.001691 | ||||||||||
0.6 | 0.003608 | ||||||||||
0.2 | 3 | 5 | 6 | 0.8 | 0.1 | 0.01 | 3 | 2.5 | 5 | 2 | 0.000359 |
0.09 | 0.000304 | ||||||||||
0.15 | 0.000337 | ||||||||||
0.3 | 1 | 3 | 5 | 0.8 | 0.5 | 0.05 | 1 | 1.5 | 2 | 1 | −0.000000 |
2 | 0.000014 | ||||||||||
3 | 0.000023 | ||||||||||
0.7 | 2.5 | 3 | 6 | 0.9 | 0.5 | 0.06 | 1.5 | 3 | 2 | 1 | 0.001164 |
4.5 | 0.000586 | ||||||||||
8 | 0.000470 | ||||||||||
0.4 | 2 | 1 | 3 | 0.6 | 0.5 | 0.01 | 3.5 | 2 | 1 | 1 | 0.002425 |
1.5 | 0.002586 | ||||||||||
2.5 | 0.003882 |
δ | R | N | k | Pr. | ϕ1 | ϕ2 | m | K1 | α | M | θ'(η) |
0.5 | 5 | 3 | 0.3 | 0.6 | 0.5 | 0.03 | 2.5 | 5.5 | 2.5 | 1 | 0.239779 |
3.5 | 0.245450 | ||||||||||
8.5 | 0.258792 | ||||||||||
0.5 | 0.5 | 3 | 1 | 0.6 | 0.5 | 0.01 | 5 | 6.5 | 2.8 | 2 | 0.179407 |
3.5 | 0.229167 | ||||||||||
5.5 | 0.246877 | ||||||||||
0.4 | 2 | 3 | 3 | 0.6 | 0.5 | 0.01 | 3.5 | 2 | 1 | 2 | 0.211021 |
6.3698 | 0.246739 | ||||||||||
16.1576 | 0.282326 | ||||||||||
0.5 | 5 | 3 | 1.5 | 0.6 | 0.5 | 0.02 | 5 | 5.5 | 2 | 1 | 0.221892 |
4.5 | 0.214110 | ||||||||||
9 | 0.203964 | ||||||||||
0.2 | 6 | 3 | 2 | 0.6 | 0.2 | 0.02 | 5 | 2.5 | 3 | 1 | 0.067710 |
0.8 | 0.058471 | ||||||||||
1 | 0.050255 | ||||||||||
0.2 | 6 | 2 | 1 | 0.6 | 0.1 | 0.02 | 5 | 2.5 | 3 | 2 | 0.428781 |
0.5 | 0.433304 | ||||||||||
0.6 | 0.429139 | ||||||||||
0.2 | 3 | 5 | 6 | 0.8 | 0.1 | 0.01 | 3 | 2.5 | 5 | 2 | 0.040132 |
0.09 | 0.049593 | ||||||||||
0.15 | 0.055833 | ||||||||||
0.3 | 1 | 3 | 5 | 0.8 | 0.5 | 0.05 | 1 | 1.5 | 2 | 1 | 0.014491 |
2 | 0.012162 | ||||||||||
3 | 0.013738 | ||||||||||
0.7 | 2.5 | 3 | 6 | 0.9 | 0.5 | 0.06 | 1.5 | 3 | 2 | 1 | 0.180677 |
4.5 | 0.179365 | ||||||||||
8 | 0.177359 | ||||||||||
0.4 | 2 | 1 | 3 | 0.6 | 0.5 | 0.01 | 3.5 | 2 | 1 | 1 | 0.120237 |
1.5 | 0.144988 | ||||||||||
2.5 | 0.186923 |
Parameter | Skin Friction Cf | Nusselt Number Nu | Sherwood Number Sh | |||
M | Al2O3−EG | Al2O3−Cu/EG | Al2O3−EG | Al2O3−Cu/EG | Al2O3−EG | Al2O3−Cu/EG |
3 | −1.7899 | −2.3778 | −0.1511 | −0.1947 | 0.1326 | 0.1301 |
4 | −2.2672 | −2.9818 | −0.2240 | −0.2711 | 0.1132 | 0.1118 |
5 | −2.7581 | −3.6074 | −0.3036 | −0.3540 | 0.1001 | 0.0992 |
Parameter | Skin Friction Cf | Nusselt Number Nu | Sherwood Number Sh | |||
δ | Al2O3−EG | Al2O3−Cu/EG | Al2O3−EG | Al2O3−Cu/EG | Al2O3−EG | Al2O3−Cu/EG |
0.1 | −1.2860 | −1.7428 | 0.0829 | 0.0651 | 0.1660 | 0.1613 |
0.3 | −1.4054 | −1.9044 | −0.2762 | −0.3400 | 0.1563 | 0.1515 |
0.5 | −1.5478 | −2.0970 | −0.6996 | −0.8162 | 0.1437 | 0.1387 |
Nomenclature | σs Ferroparticles electric conductivity S/m |
I Body couple per unit mass | B0 Magnetic field intensity W/m2 |
u x-component of velocity m/s | F″ Coefficient of skin-friction |
ϕ,λ Spin gradient viscosity coefficients Pa.s | σnf Ferrofluid electric conductivity S/m |
j Micro-inertia density Kg/m3 | Cp,nf Ferrofluid heat capacity |
v y-component of velocity m/s | G Dimensionless micro-rotation velocity m/s |
μf Base fluid dynamic viscosity Pa.s | σ∗ Stefan-Boltzmann constant |
K Micro-rotation parameter | g Acceleration due to gravity |
V Velocity m/s | θ Dimensionless temperature |
μnf Ferrofluid dynamic viscosity Kg/ms | f Base fluid |
k∗ Mean absorption coefficient | p Pressure Kgm−1s−2 |
T The temperature of the fluid (℃) | ρf Base fluid density Kg/m3 |
ϕ Ferroparticles volume fraction | s Ferroparticle |
kf Base fluid thermal conductivity Wm−1K−1 | Pr Prandtl number m2/s |
Tw Wall temperature | ρs Ferroparticles density Kg/m3 |
δ Boundary parameter | hnf hybrid Ferrofluid |
ks Ferroparticle thermal conductivity Wm−1K−1 | qr Radiative heat flux |
T∞ Ambient temperature | ρhnf hybrid Ferrofluid density Kg/m3 |
κ Vortex viscosity | w Condition at wall |
knf Ferroparticle thermal conductivity Wm−1K−1 | R Radiative parameter α Stretching/shrinking parameter |
F Dimensionless stream function | ∞ Condition at infinity |
f Base fluid electric conductivity S/m | γnf Spin-gradient viscosity |
N Micro-rotation vector | F′ Dimensionless velocity m/s |
K1 local micro-rotation parameter |
Thermophysical property | Fluid (EG) | Alumina (Al2O3) | Cu |
ρ(kg/m3) | 1114.0 | 3970 | 8933 |
cp(j/kg.K) | 2415 | 765 | 385 |
k(w/m.K) | 0.2520 | 40 | 400 |
σ(s/smm) | 5.50×10−6 | 59.6×106 | 35×106 |
δ | R | N | K | Pr. | ϕ1 | ϕ2 | m | K1 | α | M | f″(η) |
0.5 | 5 | 3 | 0.3 | 0.6 | 0.5 | 0.03 | 2.5 | 5.5 | 2.5 | 1 | −0.000976 |
3.5 | −0.000699 | ||||||||||
8.5 | 0.000222 | ||||||||||
0.5 | 0.5 | 3 | 1 | 0.6 | 0.5 | 0.01 | 5 | 6.5 | 2.8 | 2 | 0.000165 |
3.5 | 0.000165 | ||||||||||
5.5 | 0.0001653 | ||||||||||
0.4 | 2 | 3 | 3 | 0.6 | 0.5 | 0.01 | 3.5 | 2 | 1 | 2 | 0.003354 |
6.3698 | 0.003354 | ||||||||||
16.1576 | 0.003354 | ||||||||||
0.5 | 5 | 3 | 1.5 | 0.6 | 0.5 | 0.02 | 5 | 5.5 | 2 | 1 | −0.001637 |
4.5 | −0.000945 | ||||||||||
9 | −0.000448 | ||||||||||
0.2 | 6 | 3 | 2 | 0.6 | 0.2 | 0.02 | 5 | 2.5 | 3 | 1 | −0.000035 |
0.8 | −0.000035 | ||||||||||
1 | −0.000035 | ||||||||||
0.2 | 6 | 2 | 1 | 0.6 | 0.1 | 0.02 | 5 | 2.5 | 3 | 2 | 0.000122 |
0.5 | 0.000610 | ||||||||||
0.6 | 0.000374 | ||||||||||
0.2 | 3 | 5 | 6 | 0.8 | 0.1 | 0.01 | 3 | 2.5 | 5 | 2 | 0.001575 |
0.09 | 0.001711 | ||||||||||
0.15 | 0.001724 | ||||||||||
0.3 | 1 | 3 | 5 | 0.8 | 0.5 | 0.05 | 1 | 1.5 | 2 | 1 | 0.000002 |
2 | −0.000330 | ||||||||||
3 | −0.001959 | ||||||||||
0.7 | 2.5 | 3 | 6 | 0.9 | 0.5 | 0.06 | 1.5 | 3 | 2 | 1 | 0.003838 |
4.5 | 0.001401 | ||||||||||
8 | −0.000379 | ||||||||||
0.4 | 2 | 1 | 3 | 0.6 | 0.5 | 0.01 | 3.5 | 2 | 1 | 1 | 0.000838 |
1.5 | 0.002978 | ||||||||||
2.5 | 0.003277 |
δ | R | N | K | Pr. | ϕ1 | ϕ2 | m | K1 | α | M | G'(η) |
0.5 | 5 | 3 | 0.3 | 0.6 | 0.5 | 0.03 | 2.5 | 5.5 | 2.5 | 1 | 0.000637 |
3.5 | 0.000821 | ||||||||||
8.5 | 0.001262 | ||||||||||
0.5 | 0.5 | 3 | 1 | 0.6 | 0.5 | 0.01 | 5 | 6.5 | 2.8 | 2 | 0.000525 |
3.5 | 0.000525 | ||||||||||
5.5 | 0.000525 | ||||||||||
0.4 | 2 | 3 | 3 | 0.6 | 0.5 | 0.01 | 3.5 | 2 | 1 | 2 | 0.003126 |
6.3698 | 0.003126 | ||||||||||
16.1576 | 0.003126 | ||||||||||
0.5 | 5 | 3 | 1.5 | 0.6 | 0.5 | 0.02 | 5 | 5.5 | 2 | 1 | 0.001389 |
4.5 | 0.001874 | ||||||||||
9 | 0.002749 | ||||||||||
0.2 | 6 | 3 | 2 | 0.6 | 0.2 | 0.02 | 5 | 2.5 | 3 | 1 | 0.000410 |
0.8 | 0.000410 | ||||||||||
1 | 0.000410 | ||||||||||
0.2 | 6 | 2 | 1 | 0.6 | 0.1 | 0.02 | 5 | 2.5 | 3 | 2 | 0.000037 |
0.5 | 0.001691 | ||||||||||
0.6 | 0.003608 | ||||||||||
0.2 | 3 | 5 | 6 | 0.8 | 0.1 | 0.01 | 3 | 2.5 | 5 | 2 | 0.000359 |
0.09 | 0.000304 | ||||||||||
0.15 | 0.000337 | ||||||||||
0.3 | 1 | 3 | 5 | 0.8 | 0.5 | 0.05 | 1 | 1.5 | 2 | 1 | −0.000000 |
2 | 0.000014 | ||||||||||
3 | 0.000023 | ||||||||||
0.7 | 2.5 | 3 | 6 | 0.9 | 0.5 | 0.06 | 1.5 | 3 | 2 | 1 | 0.001164 |
4.5 | 0.000586 | ||||||||||
8 | 0.000470 | ||||||||||
0.4 | 2 | 1 | 3 | 0.6 | 0.5 | 0.01 | 3.5 | 2 | 1 | 1 | 0.002425 |
1.5 | 0.002586 | ||||||||||
2.5 | 0.003882 |
δ | R | N | k | Pr. | ϕ1 | ϕ2 | m | K1 | α | M | θ'(η) |
0.5 | 5 | 3 | 0.3 | 0.6 | 0.5 | 0.03 | 2.5 | 5.5 | 2.5 | 1 | 0.239779 |
3.5 | 0.245450 | ||||||||||
8.5 | 0.258792 | ||||||||||
0.5 | 0.5 | 3 | 1 | 0.6 | 0.5 | 0.01 | 5 | 6.5 | 2.8 | 2 | 0.179407 |
3.5 | 0.229167 | ||||||||||
5.5 | 0.246877 | ||||||||||
0.4 | 2 | 3 | 3 | 0.6 | 0.5 | 0.01 | 3.5 | 2 | 1 | 2 | 0.211021 |
6.3698 | 0.246739 | ||||||||||
16.1576 | 0.282326 | ||||||||||
0.5 | 5 | 3 | 1.5 | 0.6 | 0.5 | 0.02 | 5 | 5.5 | 2 | 1 | 0.221892 |
4.5 | 0.214110 | ||||||||||
9 | 0.203964 | ||||||||||
0.2 | 6 | 3 | 2 | 0.6 | 0.2 | 0.02 | 5 | 2.5 | 3 | 1 | 0.067710 |
0.8 | 0.058471 | ||||||||||
1 | 0.050255 | ||||||||||
0.2 | 6 | 2 | 1 | 0.6 | 0.1 | 0.02 | 5 | 2.5 | 3 | 2 | 0.428781 |
0.5 | 0.433304 | ||||||||||
0.6 | 0.429139 | ||||||||||
0.2 | 3 | 5 | 6 | 0.8 | 0.1 | 0.01 | 3 | 2.5 | 5 | 2 | 0.040132 |
0.09 | 0.049593 | ||||||||||
0.15 | 0.055833 | ||||||||||
0.3 | 1 | 3 | 5 | 0.8 | 0.5 | 0.05 | 1 | 1.5 | 2 | 1 | 0.014491 |
2 | 0.012162 | ||||||||||
3 | 0.013738 | ||||||||||
0.7 | 2.5 | 3 | 6 | 0.9 | 0.5 | 0.06 | 1.5 | 3 | 2 | 1 | 0.180677 |
4.5 | 0.179365 | ||||||||||
8 | 0.177359 | ||||||||||
0.4 | 2 | 1 | 3 | 0.6 | 0.5 | 0.01 | 3.5 | 2 | 1 | 1 | 0.120237 |
1.5 | 0.144988 | ||||||||||
2.5 | 0.186923 |
Parameter | Skin Friction Cf | Nusselt Number Nu | Sherwood Number Sh | |||
M | Al2O3−EG | Al2O3−Cu/EG | Al2O3−EG | Al2O3−Cu/EG | Al2O3−EG | Al2O3−Cu/EG |
3 | −1.7899 | −2.3778 | −0.1511 | −0.1947 | 0.1326 | 0.1301 |
4 | −2.2672 | −2.9818 | −0.2240 | −0.2711 | 0.1132 | 0.1118 |
5 | −2.7581 | −3.6074 | −0.3036 | −0.3540 | 0.1001 | 0.0992 |
Parameter | Skin Friction Cf | Nusselt Number Nu | Sherwood Number Sh | |||
δ | Al2O3−EG | Al2O3−Cu/EG | Al2O3−EG | Al2O3−Cu/EG | Al2O3−EG | Al2O3−Cu/EG |
0.1 | −1.2860 | −1.7428 | 0.0829 | 0.0651 | 0.1660 | 0.1613 |
0.3 | −1.4054 | −1.9044 | −0.2762 | −0.3400 | 0.1563 | 0.1515 |
0.5 | −1.5478 | −2.0970 | −0.6996 | −0.8162 | 0.1437 | 0.1387 |
Nomenclature | σs Ferroparticles electric conductivity S/m |
I Body couple per unit mass | B0 Magnetic field intensity W/m2 |
u x-component of velocity m/s | F″ Coefficient of skin-friction |
ϕ,λ Spin gradient viscosity coefficients Pa.s | σnf Ferrofluid electric conductivity S/m |
j Micro-inertia density Kg/m3 | Cp,nf Ferrofluid heat capacity |
v y-component of velocity m/s | G Dimensionless micro-rotation velocity m/s |
μf Base fluid dynamic viscosity Pa.s | σ∗ Stefan-Boltzmann constant |
K Micro-rotation parameter | g Acceleration due to gravity |
V Velocity m/s | θ Dimensionless temperature |
μnf Ferrofluid dynamic viscosity Kg/ms | f Base fluid |
k∗ Mean absorption coefficient | p Pressure Kgm−1s−2 |
T The temperature of the fluid (℃) | ρf Base fluid density Kg/m3 |
ϕ Ferroparticles volume fraction | s Ferroparticle |
kf Base fluid thermal conductivity Wm−1K−1 | Pr Prandtl number m2/s |
Tw Wall temperature | ρs Ferroparticles density Kg/m3 |
δ Boundary parameter | hnf hybrid Ferrofluid |
ks Ferroparticle thermal conductivity Wm−1K−1 | qr Radiative heat flux |
T∞ Ambient temperature | ρhnf hybrid Ferrofluid density Kg/m3 |
κ Vortex viscosity | w Condition at wall |
knf Ferroparticle thermal conductivity Wm−1K−1 | R Radiative parameter α Stretching/shrinking parameter |
F Dimensionless stream function | ∞ Condition at infinity |
f Base fluid electric conductivity S/m | γnf Spin-gradient viscosity |
N Micro-rotation vector | F′ Dimensionless velocity m/s |
K1 local micro-rotation parameter |