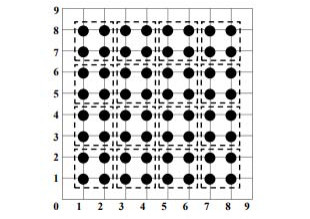
Ultrahigh molecular weight polyethene (UHMWPE) is employed as a bearing material in a range of applications due to its improved elasticity, compatibility, and impact resistance, processing conditions for a suitable surface texture are necessary. Surface texture processing on microchannels using lasers is always associated with the effect of heat damage on the polymer specimen surface. This study aims to explore the use of polydimethylsiloxane (PDMS) and polyacrylic acid (PAA) in the form of liquid gel coatings in order to reduce heat damage to surfaces during the laser processing of ultrahigh molecular weight polyethene (UHMWPE). First, PDMS and PAA were coated on the surface of the UHMWPE material specimen, and then texturing was performed using a laser diode and cleaned using the ultrasonic method. Second, the dimensions and texture profiles of all the samples from this study were measured using a confocal microscope and open source software. In addition, the effect of adding liquid gel on the surface at 150 µm thickness and laser power parameters was determined. The results show that the PDMS and PAA liquid gel layers help regulate the dimensional bulge of the fabricated microchannels at laser powers below 6 watts, compared to those produced without the coating.
Citation: Eko Sasmito Hadi, Ojo Kurdi, Ari Wibawa BS, Rifky Ismail, Mohammad Tauviqirrahman. Influence of laser processing conditions for the manufacture of microchannels on ultrahigh molecular weight polyethylene coated with PDMS and PAA[J]. AIMS Materials Science, 2022, 9(4): 554-571. doi: 10.3934/matersci.2022033
[1] | Emadidin Gahalla Mohmed Elmahdi, Jianfei Huang . Two linearized finite difference schemes for time fractional nonlinear diffusion-wave equations with fourth order derivative. AIMS Mathematics, 2021, 6(6): 6356-6376. doi: 10.3934/math.2021373 |
[2] | Fouad Mohammad Salama, Faisal Fairag . On numerical solution of two-dimensional variable-order fractional diffusion equation arising in transport phenomena. AIMS Mathematics, 2024, 9(1): 340-370. doi: 10.3934/math.2024020 |
[3] | Ajmal Ali, Tayyaba Akram, Azhar Iqbal, Poom Kumam, Thana Sutthibutpong . A numerical approach for 2D time-fractional diffusion damped wave model. AIMS Mathematics, 2023, 8(4): 8249-8273. doi: 10.3934/math.2023416 |
[4] | Junying Cao, Zhongqing Wang, Ziqiang Wang . Stability and convergence analysis for a uniform temporal high accuracy of the time-fractional diffusion equation with 1D and 2D spatial compact finite difference method. AIMS Mathematics, 2024, 9(6): 14697-14730. doi: 10.3934/math.2024715 |
[5] | Abdul-Majeed Ayebire, Saroj Sahani, Priyanka, Shelly Arora . Numerical study of soliton behavior of generalised Kuramoto-Sivashinsky type equations with Hermite splines. AIMS Mathematics, 2025, 10(2): 2098-2130. doi: 10.3934/math.2025099 |
[6] | Yanjie Zhou, Xianxiang Leng, Yuejie Li, Qiuxiang Deng, Zhendong Luo . A novel two-grid Crank-Nicolson mixed finite element method for nonlinear fourth-order sin-Gordon equation. AIMS Mathematics, 2024, 9(11): 31470-31494. doi: 10.3934/math.20241515 |
[7] | Fouad Mohammad Salama, Nur Nadiah Abd Hamid, Norhashidah Hj. Mohd Ali, Umair Ali . An efficient modified hybrid explicit group iterative method for the time-fractional diffusion equation in two space dimensions. AIMS Mathematics, 2022, 7(2): 2370-2392. doi: 10.3934/math.2022134 |
[8] | Ailing Zhu, Yixin Wang, Qiang Xu . A weak Galerkin finite element approximation of two-dimensional sub-diffusion equation with time-fractional derivative. AIMS Mathematics, 2020, 5(5): 4297-4310. doi: 10.3934/math.2020274 |
[9] | Din Prathumwan, Thipsuda Khonwai, Narisara Phoochalong, Inthira Chaiya, Kamonchat Trachoo . An improved approximate method for solving two-dimensional time-fractional-order Black-Scholes model: a finite difference approach. AIMS Mathematics, 2024, 9(7): 17205-17233. doi: 10.3934/math.2024836 |
[10] | Fouad Mohammad Salama, Nur Nadiah Abd Hamid, Umair Ali, Norhashidah Hj. Mohd Ali . Fast hybrid explicit group methods for solving 2D fractional advection-diffusion equation. AIMS Mathematics, 2022, 7(9): 15854-15880. doi: 10.3934/math.2022868 |
Ultrahigh molecular weight polyethene (UHMWPE) is employed as a bearing material in a range of applications due to its improved elasticity, compatibility, and impact resistance, processing conditions for a suitable surface texture are necessary. Surface texture processing on microchannels using lasers is always associated with the effect of heat damage on the polymer specimen surface. This study aims to explore the use of polydimethylsiloxane (PDMS) and polyacrylic acid (PAA) in the form of liquid gel coatings in order to reduce heat damage to surfaces during the laser processing of ultrahigh molecular weight polyethene (UHMWPE). First, PDMS and PAA were coated on the surface of the UHMWPE material specimen, and then texturing was performed using a laser diode and cleaned using the ultrasonic method. Second, the dimensions and texture profiles of all the samples from this study were measured using a confocal microscope and open source software. In addition, the effect of adding liquid gel on the surface at 150 µm thickness and laser power parameters was determined. The results show that the PDMS and PAA liquid gel layers help regulate the dimensional bulge of the fabricated microchannels at laser powers below 6 watts, compared to those produced without the coating.
Fractional-order differential equations (FDM) have many applications in various fields of engineering and science, such as chemical and physical phenomena [2,3,4,5]. For instance, the fractional-order diffusion equation is used to describe anomalous diffusion phenomena in the transport process through disordered and complex systems including fractal media, fractional kinetic equations regarding slow diffusion, and movement of small molecular along the concentration space [6].
In this article, the two-dimensional (2-D) time-fractional sub-diffusion equation (FSDE) with the weak singularity at initial time t=0 is considered as follows:
∂αV∂tα=∂2V∂x2+∂2V∂y2+G(x,y,t), | (1.1) |
with subject to conditions
V(x,y,0)=ζ0(x,y), |
and
V(0,y,t)=ζ1(x,y,t),V(L,y,t)=ζ2(x,y,t),V(x,0,t)=ζ3(x,y,t),V(x,L,t)=ζ4(x,y,t),0≤x,y≤M,0≤t≤N, |
where ζ0, ζ1, ζ2, ζ3, ζ4 are known functions and α∈(0,1).
The FSDE can be obtained from the anomalous diffusion system by replacing the time derivative with a fractional derivative α where 0<α<1. The FSDE is an important class of fractional partial differential equations (PDEs), which is mainly used in the modeling of fractional random walk, the phenomenon of wave propagation, diffusion unification, etc. [7,8].
The Caputo derivative of order α is
C0Dαtf(x)=1Γ(1−α)∫t0f′(x)(t−x)αdx. | (1.2) |
The Caputo derivative approximated using the L1 gives the accuracy 2−α [9,10], but the presence of kernel (t−x)α produces solutions for Eq (1.1) with the weak-singularity at initial time t=0, which increases the computation cost and give low convergence rate for the approximate methods on uniform meshes [11]. Therefore, to increase the convergence rate many researchers solved the FSDE using different high-order numerical methods. Based on the chronology, several numerical methods are proposed for the solution of 2-D time FSDE (1.1), for example, Cui [12] proposed high-order alternating direction implicit (ADI) method, and it is unconditionally stable and convergent with convergence order O(να+h40). Zhuang and Liu [13] proposed an unconditionally stable and convergent implicit difference scheme. Zhang et al. [14] used the Crank-Nicolson-type compact ADI scheme and proved the unconditional stability and convergence having convergence order O(νmin[2−α2,2α]+h014+h024) in H10 norm. Ji and Sun [15] used a high-order numerical scheme to solve (1.1), and proved convergence in L1(L∞)-norm and unconditional stability by the energy method. Wang et al. [16] solved 2-D FSDE using C-N alternating direction implicit finite difference method (FDM), where the fractional derivative is discretized using Riemann-Liouville fractional definition and to improve its temporal accuracy they used the Richardson extrapolation algorithm. Also, they proved its unique solvability, unconditional stability, and convergence O(ν2γ+h0x4+h0y4) of the scheme. Zhai and Feng [17] presented three different compact schemes for a 2-D time-fractional diffusion equation. The Caputo fractional definition is used for fractional derivative. All the schemes are fourth-order accurate for space and second-order accurate for the time variable. The stability of all the schemes is analyzed using Fourier analysis, which shows that two schemes are unconditionally stable, and the third one is conditionally stable.
The advantage of high-order schemes is that it produces more accurate results but at the same time increase the execution timings because of the escalated computational complexity of the scheme. Similarly, the advantage of explicit group methods over the standard point methods that the it considered quarter grid points of the solution domain and the points are considered as iterative points in the iterative process which reduces the computational complexity of the proposed method and hence reduce the execution time per iteration. Since, the computational complexity is greatly reduced using the explicit group method the 2-D time-fractional advection-diffusion, hyperbolic telegraph fractional differential, and fractional diffusion equations etc. [18,19,20,21,22] with second-order accuracy, therefore, we proposed the grouping strategy with uniform grids for the solution of the 2-D time FSDE with fourth-order accuracy. The purpose of this paper is to solve 2-D time FSDE with the fourth-order explicit group method (FEGM).
The paper is organized as follows: In Section 2, the derivation of the group explicit method from the finite difference method is presented. Section 3 discussed the stability of the proposed scheme, and the convergence of the proposed scheme is presented in Section 4. To show the efficiency of the proposed method, some numerical examples with discussion are presented in Section 5, and finally, Section 6 consists of the conclusion.
First, let us define some notations:
δ2xVki,j=Vki+1,j−2Vki,j+Vki−1,j,Vk+12i,j=Vk+1i,j+Vki,j2,xi=ih0,yj=jh0,i,j=0,1,2,3...,M,tk=kν,k=0,1,2,3...,N, |
where h0=Δx=Δy=LM represents the space step and ν=TN time step.
Since, the Taylor series expansion with respect to x is
Vki+1,j=Vki,j+h01!Vx|ki,j+h202!Vxx|ki,j+h303!V|ki,j+..., | (2.1) |
Vki−1,j=Vki,j−h01!Vx|ki,j+h202!Vxx|ki,j−h303!Vxxx|ki,j+... | (2.2) |
By adding Eqs (2.1) and (2.2) and after rearranging, we get
∂2Vki,j∂x2=Vki+1,j−2uki,j+Vki−1,jh20+2h204!∂4Vki,j∂x4+...=Vki+1,j−2Vki,j+Vki−1,jh20+O(h20). | (2.3) |
Therefore, the Taylor series expansions at points uki+1,j and uki,j+1 are
δ2xh20Vki,j=∂2V∂x2|ki,j−h2012∂4V∂x4|ki,j−h40360∂6V∂x6|ki,j+O(h60), | (2.4) |
δ2yh20Vki,j=∂2V∂y2|ki,j−h2012∂4V∂y4|ki,j+h40360∂6V∂y6|ki,j+O(h60). | (2.5) |
The difference operator δ2x, which maintain the three-point stencil is given by []
δ2xh20(1+112δ2x)Vki,j=∂2V∂x2|ki,j−h40240∂4V∂x4|ki,j+O(h60), | (2.6) |
and
δ2yh20(1+112δ2y)Vki,j=∂2V∂y2|ki,j−h40240∂4V∂y4|ki,j+O(h60). | (2.7) |
The fractional derivative is approximated using the Central difference formula as [24]
∂α∂tαV(x,y,t)|k+12i,j=1Γ(1−α)∫tk+120Vt(x,y,ε)(tk+12−ε)−α∂ε=1Γ(1−α)[∫tk+120Vt(x,y,ε)((k+12)ν−ε)−α∂ε+∫ttk+12tk(Vk+1i,j−Vki,jν+O(ν))((k+12)ν−ε)−α∂ε]=1Γ(1−α)k∑s0=1[∫sν(s0−1)νVs0i,j−Vs0−1i,jν+(ε−ts0−12)Vtt(xi,yj,cs0)×((k+12ν−ε)−α∂ε)]+∫(k+12)νkν(Vk+1i,j−Vki,jν+O(ν))((k+12)ν−ε)−α∂ε=1Γ(1−α)k∑s0=1Vs0i,j−Vs0−1i,jν∫sν(s0−1)ν((k+12)ν−ε)−α∂ε+1Γ(1−α)k∑s0=1∫sν(s−1)ν(ε−ts0−12)Vtt(xi,yj,cs0)((k+12)ν−ε)−α∂ε+1Γ(1−α)[Vk+1i,j−Vki,jν+O(ν)]∫(k+12)νkν[((k+12)ν−ε)−α−ε]∂ε=1να(1−α)Γ(1−α)k∑s0=1[Vs0i,j−Vs0−1i,j][(k−s0+32)1−α−(k−s0+12)1−α]+1να(1−α)Γ(1−α)(Vk+1i,j−Vki,j)121−α+1Γ(1−α)k∑s0=1∫sν(s−1)ν(ε−ts0−12)Vtt(xi,yj,cs0)((k+12)ν−ε)−α∂ε+1Γ(1−α)(1−α)21−αO(ν)2−α. |
Therefore, after some simplifications, the Crank-Nicolson (C-N) Caputo fractional derivative
∂α∂tαV(x,y,t)|k+12i,j=a1V|ki,j+k−1∑s=1(ak−s+1−ak−s)V|si,j−akV|0i,j+σVk+1i,j+Vki,j21−α+O(ν2−α),σ=1ναΓ(2−α),as=σ((s+12)1−α−(s−12)1−α),s=0,1,2,...,k. | (2.8) |
Now using Eqs (2.6)–(2.8) and C-N or standard point (SP) scheme at V(xi,yj,tk+12), the standard fourth-order finite difference scheme for Eq (1.1) is as follows:
a1Vki,j+k−1∑s=1(ak−s+1−ak−s)Vsi,j−akV0i,j+σVk+1i,j+Vki,j21−α=(1+112δ2x)−1×δ2xh20Vk+12i,j+(1+112δ2y)−1δ2yh20Vk+12i,j+fk+12i,j+O(ν2−α+h40). | (2.9) |
Substituting the values of δ2x, δ2y and Vk+12i,j into Eq (2.9), and after rearranging we get the standard point SP compact scheme:
λ1Vk+1i,j=λ2(Vk+1i+1,j+Vk+1i−1,j+Vk+1i,j+1+Vk+1i,j−1)+λ3(Vk+1i+1,j+1+Vk+1i−1,j+1+Vk+1i+1,j−1+Vk+1i−1,j−1)+λ4Vki,j+λ5(Vki+1,j+Vki−1,j+Vki,j+1+Vki,j−1)+λ6(Vki+1,j+1+Vki−1,j+1+Vki+1,j−1+Vki−1,j−1)+2518h20fk+12i,j+536h20(fk+1ti+1,j+fk+1ti−1,j+fk+1ti,j+1+fk+1ti,j−1)+h2072(fk+12i+1,j+1+fk+12i−1,j+1+fk+12i+1,j−1+fk+12i−1,j−1)−k−1∑s=1(ak−s+1−ak−s)(2518h20Vsi,j+536h20(Vsi+1,j+Vsi−1,j+Vsi,j+1+Vsi,j−1)+h2072(Vsi+1,j+1+Vsi−1,j+1+Vsi+1,j−1+Vsi−1,j−1))+O(ν2−α+h40), | (2.10) |
where
g0=σ21−α,g1=a1−g0,λ1=172(240+100h20g0),λ2=172(48−10h20g0),λ3=172(12−h20g0),λ4=−172(240+100h20g1),λ5=172(48−10h20g1),λ6=172(12−h20g1). |
Now, using Eq (2.10) will give the following system for the group of four points:
[λ1−λ2−λ3−λ2−λ2λ1−λ2−λ3−λ3−λ2λ1−λ2−λ2−λ3−λ2λ1][Vk+1i,jVk+1i+1,jVk+1i+1,j+1Vk+1i,j+1]=[rhsi,jrhsi+1,jrhsi+1,j+1rhsi,j+1], | (2.11) |
where
rhsi,j=λ2(Vk+1i−1,j+Vk+1i,j−1)+λ3(Vk+1i−1,j+1+Vk+1i+1,j−1+Vk+1i−1,j−1)+λ4Vki,j+λ5(Vki+1,j+Vki−1,j+Vki,j+1+Vki,j−1)+λ6(Vki+1,j+1+Vki−1,j+1+Vki+1,j−1+Vki−1,j−1)+2518h20fk+12i,j+536h20(fk+12i+1,j+fk+12i−1,j+fk+12i,j+1+fk+12i,j−1)+h2072(fk+12i+1,j+1+fk+12i−1,j+1+fk+12i+1,j−1+fk+12i−1,j−1)−Fi,j, |
rhsi+1,j=λ2(Vk+1i+2,j+Vk+1i+1,j−1)+λ3(Vk+1i+2,j+1+Vk+1i+2,j−1+Vk+1i,j−1)+λ4Vki+1,j+λ5(Vki+2,j+Vki,j+Vki+1,j+1+Vki+1,j−1)+λ6(Vki+2,j+1+Vki,j+1+Vki+2,j−1+Vki,j−1)+2518h20fk+12i+1,j+536h20(fk+12i+2,j+fk+12i,j+fk+12i+1,j+1+fk+12i+1,j−1)+h2072(fk+12i+2,j+1+fk+12i,j+1+fk+12i+2,j−1+fk+12i,j−1)−Fi+1,j, |
rhsi+1,j+1=λ2(Vk+1i+2,j+1+Vk+1i+1,j+2)+λ3(Vk+1i+2,j+2+Vk+1i,j+2+Vk+1i+2,j)+λ4Vki+1,j+1+λ5(Vki+2,j+1+Vki,j+1+Vki+1,j+2+Vki+1,j)+λ6(Vki+2,j+2+Vki,j+2+Vki+2,j+Vki,j)+2518h20fk+12i+1,j+1+536h20(fk+12i+2,j+1+fk+12i,j+1+fk+12i+1,j+2+fk+12i+1,j)+h2072(fk+12i+2,j+2+fk+12i,j+2+fk+12i+2,j+fk+12i,j)−Fi+1,j+1, |
rhsi,j+1=λ2(Vk+1i−1,j+1+Vk+1i,j+2)+λ3(Vk+1i+1,j+2+Vk+1i−1,j+2+Vk+1i−1,j)+λ4Vki,j+1+λ5(Vki+1,j+1+Vki−1,j+1+Vki,j+2+Vki,j)+λ6(Vki+1,j+2+Vki−1,j+2+Vki+1,j+Vki−1,j)+2518h20fk+12i,j+1+536h20(fk+12i+1,j+1+fk+12i−1,j+1+fk+12i,j+2+fk+12i,j)+h2072(fk+12i+1,j+2+fk+12i−1,j+2+fk+12i+1,j+fk+12i−1,j)−Fi,j+1, |
and
Fi,j=k−1∑s=1(ak−s+1−ak−s)(2518h20Vsi,j+536h20(Vsi+1,j+Vsi−1,j+Vsi,j+1+Vsi,j−1)+h2072(Vsi+1,j+1+Vsi−1,j+1+Vsi+1,j−1+Vsi−1,j−1)). |
Similarly, the inverted matrix equation (2.11) will give explicit group equation
[Vk+1i,jVk+1i+1,jVk+1i+1,j+1Vk+1i,j+1]=1d[ϕ1ϕ2ϕ3ϕ2ϕ2ϕ1ϕ2ϕ3ϕ3ϕ2ϕ1ϕ2ϕ2ϕ3ϕ2ϕ1][rhsi,jrhsi+1,jrhsi+1,j+1rhsi,j+1], | (2.12) |
where
ϕ1=λ31−2λ1λ22−2λ22λ3−λ1λ23,ϕ2=λ21λ2+2λ1λ2λ3+λ2λ23,ϕ3=2λ1λ22+λ21λ3+2λ22λ3−λ33,d=(−4λ22+(λ1−λ3)2)(λ1+λ3)2. |
In the proposed method, firstly, group of four points are computed for the different iterations using Eq (2.12) till the required convergence is attained. After the required convergence, the SP compact scheme Eq (2.10) is used directly once for computing of reaming points. Figures 1 and 2 show the grid points on the x-y plane for FDM and FEGM at various time levels when m=9 respectively.
In this section, the stability of the proposed method is discussed.
The Eq (2.12) can also be written as
AV1=BV0+f12,k=0,AVk+1=BVk−h20k−1∑s=1(ak−s+1−ak−s)CVs+h20fk+12,k>0, | (3.1) |
where
A=[R1R30R2R1R3R2R1⋱R30R2R1],B=[P1P30P2P1P3P2P1⋱P30P2P1], |
R1=[G1G3G2G1G3G2G1⋱G3G2G1],C=[Q1Q30Q2Q1Q3Q2Q1⋱Q30Q2Q1],f=[K1K1⋮K1K1], |
R2=[G6G4G8G6G4G8G6⋱G4G8G6],R3=[G7G9G5G7G9G5G7⋱G9G5G7], |
P1=[H1H3H2H1H3H2H1⋱H3H2H1],P2=[H6H4H8H6H4H8H6⋱H4H8H6], |
P3=[H7H9H5H7H9H5H7⋱H9H5H7],Q1=[L1L3L2L1L3L2L1⋱L3L2L1], |
Q2=[L6L4L8L6L4L8L6⋱L4L8L6],Q3=[L7L9L5L7L9L5L7⋱L9L5L7],K1=[W1W1⋮W1W1], |
G1=[λ1−λ2−λ3−λ2−λ2λ1−λ2−λ3−λ3−λ2λ1−λ2−λ2−λ3−λ2λ1],G2=[00−λ3−λ200−λ2−λ300000000],G3=[00000000−λ3−λ200−λ2−λ300], |
G4=[0000000000000−λ300],G5=[0000000−λ300000000],G6=[0−λ2−λ30000000000−λ3−λ20], |
G7=[0000−λ200−λ3−λ300−λ20000],G8=[00−λ30000000000000],G9=[00000000−λ30000000], |
H1=[λ4λ5λ6λ5λ5λ4λ5λ6λ6λ5λ4λ5λ5λ6λ5λ4],H2=[00λ6λ500λ5λ600000000],H3=[00000000λ6λ500λ5λ600], |
H4=[0000000000000λ600],H5=[0000000λ600000000],H6=[0λ5λ60000000000λ6λ50], |
H7=[0000λ500λ6λ600λ50000],H8=[00λ60000000000000],H9=[00000000λ60000000], |
L1=118[25521454522552141452255252145225],L2=118[00145400521400000000],L3=118[00000000145400541400], |
L4=[000000000000017200],L5=[000000017200000000],L6=118[05214000000000014520], |
L7=118[00005200141400520000],L8=[001720000000000000],L9=[000000001720000000],W1=[fi,jfi+1,jfi+1,j+1fi,j+1]. |
It can observe that Eq (3.1) form the particular structure as
[A(N−2)2×(N−2)2]Vk+1=[B(N−2)2×(N−2)2]Vk−h20k−1∑s=1(ak−s+1−ak−s)[C(N−2)2×(N−2)2]Vs+h20fk+12. |
Proposition 3.1. The proposed scheme Eq (2.12) is unconditionally stable.
Proof. Let Vki,j represents approximate and vki,j represents exact solutions for the time FSDE respectively, then the error is defined as ϵki,j=vki,j−Vki,j. So, from Eq (3.1),
AE1=BE0,k=0,AEk+1=BEk−h20k−1∑s=1(ak−s+1−ak−s)CEs,k>0, | (3.2) |
where
Ek+1=[Ek+11Ek+12⋮Ek+1m−2Ek+1m−1],Ek+1i=[ϵk+11ϵk+12⋮ϵk+1m−2ϵk+1m−1],ϵk+1i=[ϵk+1i,jϵk+1i+1,jϵk+1i+1,j+1ϵk+1i,j+1],i,j=1,2,...,m−1. |
From Eq (3.1) we know
A=G1I+(G2+G3)Q+G6I+(G4+G8)Q+G7I+(G5+G9)Q, | (3.3) |
B=H1I+(H2+H3)Q+H6I+(H4+H8)Q+H7I+(H5+H9)Q, | (3.4) |
C=L1I+(L2+L3)Q+L6I+(L4+L8)Q+L7I+(L5+L9)Q, | (3.5) |
where I and Q are two matrices, I represents identity matrix and Q represents unity values having each diagonal forthwith above and below the main diagonal, and elsewhere zero.
Suppose maximum eigenvalues are represented with ψ, χ and η for the matrices A, B and C respectively, then using Mathematica software, we get
ψ=98(g1h20+4),χ=(296+7972h20g0),η=12172. | (3.6) |
From Eq (3.2), when k = 0,
E1=A−1BE0,‖E1‖≤‖A−1B‖‖E0‖=132+121h2g1348+79h2g0‖E0‖. |
But since a1=σ((32)1−α−(12)1−α)=g0(31−α−1) and g1=a1−g0=g0(31−α−2). Also we know that 31−α<3, so,
31−α−2<1,g0(31−α−2)<g0,∵g0>0,g1<g0. |
Hence,
‖E1‖≤‖E0‖,∵g0>g1. |
Suppose
‖Er‖≤‖E0‖,r=2,3,...,k, | (3.7) |
and for r=k+1,
‖Ek+1‖=‖A−1(BEk−h20k−1∑s=1(ak−s+1−ak−s)CEs))‖≤‖A−1B‖‖Ek‖+h20k−1∑s=1(ak−s+1−ak−s)‖A−1C‖‖Es‖≤(‖A−1B‖+h20k−1∑s=1(ak−s+1−ak−s)‖A−1C‖)‖E0‖by using Eq. (3.7)=(324+81h20g1348+h20g0+121h20(ak−a1)72(348+79h20g0))‖E0‖=(324+81h20g1+1.68h20(ak−a1)348+79h20g0)‖E0‖=(132+(72.02)h2(g1+(ak−a1))348+79h20g0)‖E0‖. |
‖Ek+1‖≤‖E0‖,∵(ak−a1)<0. |
So, by mathematical induction, we prove that FEGM is unconditionally stable.
Suppose ek+12i,j,ek+12i+1,j,ek+12i+1,j+1 and ek+12i,j+1 represent different truncation errors, then,
Rk+12={Rk+121,1,Rk+121,2,...,Rk+121,M2−14,Rk+122,1,Rk+122,2,...,Rk+12M1−14,M2−14}, |
where
Rk+12i,j={ek+12i,j,ek+12i+1,j,ek+12i+1,j+1,ek+12i,j+1},i,j={1,2,...,M−14}, |
so from Eq (2.10) we have
‖Rk+12‖≤φ0(ν2−γ+h40), | (4.1) |
where φ0 is a constant.
Proposition 4.1. The FEGS equation (2.12) is unconditionally convergent with the order of convergence O(ν2−α+h4).
Proof. Since from Eq (4.1),
‖R(k−1)+12‖≤φ0(ν2−α+h40), | (4.2) |
then,
‖R(k−1)+12‖−‖Rk+12‖≤0,‖R(k−1)+12‖≤‖Rk+12‖. | (4.3) |
Since E0=0, then from Eq (2.10), we have
AE1=R12,k=0,AEk+1=BEk−h20k−1∑s=1(ak−s+1−ak−s)CEs+Rk+12,k>0. | (4.4) |
When k=0,
AE1=R12,‖E1‖≤‖A−1‖‖R12‖=1λ1+2λ2+λ3‖R12‖=1348+79h20g0‖R12‖,‖E1‖≤μ0‖R12‖,whereμ0=1348+79h20g0andμ0∈(0,1),‖E1‖≤‖R12‖. |
Assume that
‖Es‖≤‖R(s−1)+12‖,s=2,3,...,k, | (4.5) |
and now from Eq (4.4),
AEk+1=BEk−h20k−1∑s=1(ak−s+1−ak−s)CEs+Rk+12. | (4.6) |
By taking norm function on both sides of Eq (4.6),
‖Ek+1‖≤‖A−1B‖‖Ek‖−h20k−1∑s=1(ak−s+1−ak−s)‖A−1C‖‖Es‖+‖A−1‖‖Rk+12‖≤(324+81h20g1348+79h20g0+1.68h20(ak−a1)348+79h20g0+1348+79h20g0)‖Rk+12‖(by using Eqs (4.3) and (4.5))=(325+81h20g1+1.68h20(ak−a1)348+79h20g0)‖Rk+12‖=γ‖Rk+12‖, |
where γ=133+121h2g1+1.68h20(ak−a1)348+79h20g0, but since h∈(0,1), g0>g1, and (a1−ak)<0, then γ∈(0,1), therefore,
‖Ek+1‖≤‖Rk+12‖≤φ0(ν2−α+h40). |
Therefore, we get
‖Ek+1‖≤φ0(ν2−α+h40),∀k=0,1,2...,N−1. |
Thus the proposed scheme is conditionally stable.
The proposed scheme can be written in matrix form:
G1V1=G2V0+G3Υ12,k=0,G1Vk+1=G2Vk+G3Υk+12−k−1∑s=1(ak−s+1−ak−s)G3Vs,k≥1,V0i,j=b0(xi,yj),1≤i≤M,1≤j≤M,Vk0,j=b1(0,yj),1≤j≤M,0≤k≤N,VkL,j=b2(L,yj),1≤j≤M,0≤k≤N,Vki,0=b3(xi,0),1≤i≤M,0≤k≤N,Vki,L=b4(xi,L),1≤i≤M,0≤k≤N, | (5.1) |
where
G1=[λ1−λ2⋯−λ2−λ3⋯0−λ2λ1−λ2−λ3−λ2−λ3⋮−λ2λ1−λ2⋯−λ3−λ2−λ3⋮⋯−λ2λ1−λ2−λ3−λ2−λ3−λ2λ1−λ2−λ3−λ2⋮⋯−λ2λ1−λ2−λ2λ1−λ2−λ2λ1−λ20⋯⋯−λ2λ1], |
G2=[λ4λ5⋯λ5λ6⋯0λ5λ4λ5λ6λ5λ6⋮λ5λ4λ5⋯λ6λ5λ6⋮⋯λ5λ4λ5λ6λ5λ6λ5λ4λ5λ6λ5⋮⋯λ5λ4λ5λ5λ4λ5λ5λ4λ50⋯⋯λ5λ4], |
G3=[ρ1ρ2⋯ρ2ρ3⋯0ρ2ρ1ρ2ρ3ρ2ρ3⋮ρ2ρ1ρ2⋯ρ3ρ2ρ3⋮⋯ρ2ρ1ρ2ρ3ρ2ρ3ρ2ρ1ρ2ρ3ρ2⋮⋯ρ2ρ1ρ2ρ2ρ1ρ2ρ2ρ1ρ20⋯⋯ρ2ρ1], |
Υk=[Υk0,Υk1,Υk2,...,Υkn]T,Υk+12=f(xi,yj,tk+12),ρ1=25h2018,ρ2=5h2036andρ3=h2072. |
Proposition 5.1. The difference equation (2.12) is uniquely solvable.
Proof. Since λ1=172(240+100h20g0), λ2=172(48−10h20g0), λ3=172(12−h20g0), and h0,g0>0, then,
|λ1|=103+25h20g018 |
and
3|λ2|+2|λ3|≤73+49h20g0<103+2518h20g0=|λ1|. |
Hence, |λ1|>3|λ2|+2|λ1|, which shows that matrix G1 is strictly diagonally dominant and G1 is non-singular. This completes the proof.
The proposed method is simulated using the Intel Core i-7, 2.40GHz GHz, 6GB of RAM with Windows 8 using Mathematica software, and the experiments were done using the proposed method with SOR iterative technique as an acceleration factor (ω=1.8) with different mesh sizes (n=10,14,18,22,30) and different time steps. Furthermore, throughout the experiments, the L∞-norm convergence criteria ζ=10−5 is used. Also, the C2-order and C1-order of convergence are used for the computational order of spatial and temporal convergence using [25]
C2−order=log2(‖L∞(16ν,2h0)‖‖L∞(ν,h0)‖), | (6.1) |
C1−order=log2(∥L∞(2ν,h0)∥∥L∞(ν,h0)∥), | (6.2) |
where L∞ is the maximum error.
Some examples are presented below to show the efficiency of FEGM.
Problem 1. [26]
∂αV∂tα=∂2V∂x2+∂2V∂y2+(2Γ(3−α)t2−α+2t2)sin(x)sin(y),0<x, y<1,0<t≤1, |
with initial and Dirichlet boundary conditions.
The analytic solution for Problem 1 is
V(x,y,t)=t2sin(x)sin(y). |
Problem 2. [12]
∂2V∂t2=∂2V∂x1+∂2V∂y2+(Γ(2+α)−2t1+α)ex+y,0<x, y<1,0<t≤1, |
with initial and Dirichlet boundary conditions.
The analytic solution for Problem 2 is
V(x,y,t)=ex+yt1+α. |
The number of iterations, error analysis, and execution times are shown for the comparison between FEGM and SP methods from Tables 1–5. The execution times in FEGM are decreased by (4.7−28.49)%, (2−23)%, (9.16−28.13)%, (8.9−25.39)% and (6.98−27.79)% compared to SP method in Tables 1–5 respectively. Similarly, in Table 6, the comparison between the proposed method and high-order standard point method[27] is presented, which shows the proposed method gives better results. Figures 3 and 4 represent the exact and approximate solution for Problem 1, respectively, which depicts the effectiveness of the FEGM. Likewise, In Figure 5, the compression of execution times between the SP and proposed methods are shown, which shows the proposed method is efficient in terms of execution timings. Table 7 shows the computational complexity per iteration, while the computational effort is shown in Tables 8 and 9, which depict that the FEGM requires less number of operations during computations as compared to the standard SP method. Tables 10 and 11 represent the spatial convergence order for Problems 1 and 2, respectively. Similarly, Tables 12 and 13 represent the temporal convergence order for the first and second Problem respectively, which depict the experimental and theoretical convergence orders in agreement.
h0/ν | No. of iteration | Execution time | Maximum-error | Average-error | ||||
FEGM | SP | FEGM | SP | FEGM | SP | FEGM | SP | |
h0=ν=110 | 43 | 49 | 7.39 | 7.76 | 1.6404×10−4 | 1.653 ×10−4 | 7.9408 ×10−5 | 7.3891 ×10−5 |
h0=ν=118 | 41 | 48 | 66.19 | 79.82 | 6.6571 ×10−5 | 6.5544×10−5 | 2.8320 ×10−5 | 2.9081 ×10−5 |
h0=ν=122 | 42 | 54 | 148.1 | 207.1 | 4.5739 ×10−5 | 4.6717 ×10−5 | 1.9997 ×10−5 | 2.085 ×10−5 |
h0=ν=130 | 43 | 56 | 530.45 | 658.68 | 3.0559 ×10−5 | 3.2268 ×10−5 | 1.1887 ×10−5 | 1.2180 ×10−5 |
h0/ν | No. of iteration | Execution time | Maximum-error | Average-error | ||||
FEGM | SP | FEGM | SP | FEGM | SP | FEGM | SP | |
h0=ν=110 | 44 | 50 | 7.75 | 7.94 | 2.1534 ×10−4 | 2.2065 ×10−4 | 1.0469 ×10−4 | 1.0634 ×10−4 |
h0=ν=114 | 44 | 43 | 27.36 | 27.28 | 1.2736 ×10−4 | 1.2786×10−4 | 5.9175 ×10−5 | 6.0624 ×10−5 |
h0=ν=118 | 42 | 48 | 68.29 | 80.18 | 8.0887 ×10−5 | 8.5709 ×10−5 | 3.0710 ×10−5 | 3.9889×10−5 |
h0=ν=122 | 41 | 55 | 150.40 | 197.87 | 6.1207 ×10−5 | 6.2773 ×10−5 | 2.8554 ×10−5 | 2.8809 ×10−5 |
h0=ν=130 | 42 | 56 | 523.25 | 648.55 | 3.7373×10−5 | 4.4510 ×10−5 | 1.6460 ×10−5 | 1.7874 ×10−5 |
h0/ν | No. of iteration | Execution time | Maximum-error | Average-error | ||||
FEGM | SP | FEGM | SP | FEGM | SP | FEGM | SP | |
h0=ν=110 | 44 | 50 | 7.75 | 7.94 | 2.1534 ×10−4 | 2.2065 ×10−4 | 1.0469 ×10−4 | 1.0634 ×10−4 |
h0=ν=114 | 44 | 43 | 27.36 | 27.28 | 1.2736 ×10−4 | 1.2786×10−4 | 5.9175 ×10−5 | 6.0624 ×10−5 |
h0=ν=118 | 42 | 48 | 68.29 | 80.18 | 8.0887 ×10−5 | 8.5709 ×10−5 | 3.0710 ×10−5 | 3.9889×10−5 |
h0=ν=122 | 41 | 55 | 150.40 | 197.87 | 6.1207 ×10−5 | 6.2773 ×10−5 | 2.8554 ×10−5 | 2.8809 ×10−5 |
h0=ν=130 | 42 | 56 | 523.25 | 648.55 | 3.7373×10−5 | 4.4510 ×10−5 | 1.6460 ×10−5 | 1.7874 ×10−5 |
ν/h0 | No. of iteration | Execution time | Maximum-error | Average-error | ||||
FEGM | SP | FEGM | SP | FEGM | SP | FEGM | SP | |
h0=ν=110 | 46 | 52 | 7.65 | 8.72 | 2.9442 ×10−4 | 2.8915 ×10−4 | 1.3091 ×10−4 | 1.2849 ×10−4 |
h0=ν=114 | 48 | 47 | 30.93 | 29.53 | 1.3893 ×10−4 | 1.4377 ×10−4 | 3.7322 ×10−5 | 3.9455 ×10−5 |
h0=ν=118 | 48 | 52 | 77.2 | 84.75 | 8.5499 ×10−5 | 8.5075 ×10−5 | 2.4058 ×10−5 | 2.4340 ×10−5 |
h0=ν=122 | 47 | 57 | 172.53 | 203.76 | 5.5120 ×10−5 | 5.5018 ×10−5 | 1.9837 ×10−5 | 1.7813 ×10−5 |
h0=ν=130 | 47 | 65 | 588.74 | 789.14 | 2.9259 ×10−5 | 2.9669 ×10−5 | 1.2478 ×10−5 | 1.2549 ×10−5 |
h0/ν | No. of iteration | Execution time | Maximum-error | Average-error | ||||
FEGM | SP | FEGM | SP | FEGM | SP | FEGM | SP | |
h0=ν=110 | 47 | 53 | 7.92 | 8.82 | 2.2868 ×10−4 | 2.2917 ×10−4 | 1.0194 ×10−4 | 1.0189 ×10−4 |
h0=ν=114 | 48 | 48 | 31.23 | 30.46 | 2.3640 ×10−4 | 2.3848 ×10−4 | 1.1941 ×10−4 | 1.2003 ×10−4 |
h0=ν=118 | 49 | 52 | 78.34 | 85.3 | 2.1361 ×10−4 | 2.1290 ×10−4 | 1.0621 ×10−4 | 1.0863 ×10−4 |
h0=ν=122 | 48 | 57 | 169.15 | 207.6 | 1.9686 ×10−4 | 1.8908 ×10−4 | 9.5981 ×10−5 | 9.5644 ×10−5 |
h0=ν=130 | 48 | 65 | 599.97 | 775.49 | 1.5244 ×10−4 | 1.4938 ×10−4 | 7.3782 ×10−5 | 7.3922 ×10−5 |
h0/ν | No. of iteration | Maximum-error | Average-error | |||
FEGM | [27] | FEGM | [27] | FEGM | [27] | |
h0=ν=110 | 43 | 53 | 1.6404 ×10−4 | 1.2428 ×10−2 | 7.9408 ×10−5 | 8.8490 ×10−3 |
h0=ν=118 | 41 | 52 | 6.6571 ×10−5 | 7.1213 ×10−3 | 2.8320 ×10−5 | 3.6917 ×10−3 |
h0=ν=122 | 42 | 55 | 4.7739 ×10−5 | 2.6959 ×10−3 | 1.9997 ×10−5 | 1.3580 ×10−3 |
h0=165,ν=135 | 41 | 58 | 2.5368 ×10−5 | 2.0605 ×10−3 | 5.0090 ×10−6 | 1.0285 ×10−3 |
Technique | operations per iteration | |
+/- | */ ÷ | |
SP | (26+8(k−1))m2 | (8+4(k−1))m2 |
FEGM | (28+8(k−1))(m−1)2 + (26+8(k−1))(2m−1) | (12+4(k−1))(m−1)2 + (8+4(k−1))(2m−1) |
h0/ν | SP method | FEGM | ||
Number of iteration | Total operations | Number of iteration | Total operations | |
h0=ν=110 | 49 | 695800 | 43 | 631498 |
h0=ν=118 | 48 | 3701376 | 41 | 3232686 |
h0=ν=122 | 54 | 7474896 | 42 | 5924940 |
h0=ν=130 | 56 | 19252800 | 43 | 15000378 |
k/m | SP method | FEGM | ||
Number of iteration | Total operations | Number of iteration | Total operations | |
h0=ν=110 | 53 | 752600 | 47 | 690242 |
h0=ν=118 | 52 | 4009824 | 49 | 3863454 |
h0=ν=122 | 57 | 7890168 | 48 | 6771360 |
h0=ν=130 | 65 | 22347000 | 48 | 16744608 |
α=0.4 | α=0.5 | ||||
ν/h0 | Maximum error | C2-order | ν/h0 | Maximum error | C2-order |
ν=h0=0.5 | 1.4394 ×10−4 | — | ν=h0=0.5 | 3.1088 ×10−4 | — |
ν=0.031, h0=0.25 | 1.0910 ×10−5 | 3.72 | ν=0.031, h0=0.25 | 2.2509 ×10−5 | 3.78 |
ν=h0=0.25 | 2.1929 ×10−4 | — | ν=h0=0.25 | 3.546 ×10−4 | — |
ν=0.016, h0=0.12 | 9.1371 ×10−6 | 4.58 | ν=0.016, h0=0.12 | 2.1414 ×10−5 | 4.04 |
α=0.6 | α=0.8 | ||||
ν/h0 | Maximum error | C2-order | ν/h0 | Maximum error | C2-order |
ν=h0=0.5 | 5.2435 ×10−4 | — | ν=h0=0.5 | 9.9004 ×10−4 | — |
ν=0.031, h0=0.25 | 2.7191 ×10−5 | 4.26 | ν=0.031, h0=0.25 | 9.9004 ×10−5 | 4.13 |
ν=h0=0.25 | 5.0421 ×10−4 | — | ν=h0=0.25 | 7.2673 ×10−4 | — |
ν=0.016, h0=0.12 | 3.1980 ×10−5 | 3.97 | ν=0.016, h0=0.12 | 3.7243 ×10−5 | 4.28 |
α=0.7 | α=0.8 | ||||
ν/h0 | Maximum error | C2-order | ν/h0 | Maximum error | C2-order |
ν=h0=0.5 | 1.6072 ×10−3 | — | ν=h0=0.5 | 3.4202 ×10−3 | — |
ν=0.031, h0=0.25 | 1.0543 ×10−4 | 3.93 | ν=0.031, h0=0.25 | 1.7636 ×10−4 | 4.27 |
ν=h0=0.25 | 1.3545 ×10−3 | — | ν=h0=0.25 | 1.6955 ×10−3 | — |
ν=0.016, h0=0.12 | 5.9784 ×10−5 | 4.50 | ν=0.016, h0=0.12 | 8.2806 ×10−5 | 4.35 |
α=0.3 | α=0.5 | ||||
ν/h0 | Maximum error | C2-order | ν/h0 | Maximum error | C2-order |
ν=h0=0.5 | 3.832 ×10−3 | — | ν=h0=0.5 | 8.6771 ×10−4 | — |
ν=0.031, h0=0.25 | 3.2105 ×10−4 | 3.57 | ν=0.031, h0=0.25 | 4.8772 ×10−5 | 4.15 |
ν=h0=0.25 | 4.5916 ×10−4 | — | ν=h0=0.25 | 4.1734 ×10−4 | — |
ν=0.016, h0=0.12 | 2.5978 ×10−5 | 4.14 | ν=0.016, h0=0.12 | 2.3009 ×10−5 | 4.18 |
ν | α=0.3 | α=0.8 | ||
L∞ | C1− Order | L∞ | C1− Order | |
ν=110 | 7.8675×10−4 | — | 2.1609×10−4 | — |
ν=120 | 3.2208 ×10−5 | 1.28 | 7.1112 ×10−5 | 1.60 |
ν= 140 | 1.7253 ×10−5 | 1.29 | 2.6203 ×10−5 | 1.44 |
ν=180 | 6.2057×10−6 | 1.72 | 8.3392×10−6 | 1.65 |
ν | α=0.1 | α=0.8 | ||
L∞ | C1− Order | L∞ | C1− Order | |
ν=110 | 4.7691×10−4 | — | 2.1429×10−4 | — |
ν=120 | 1.6086 ×10−4 | 1.56 | 8.2679 ×10−5 | 1.37 |
ν= 140 | 5.1170 ×10−5 | 1.65 | 3.2827 ×10−5 | 1.33 |
ν=180 | 1.7848×10−5 | 1.51 | 1.3010×10−5 | 1.51 |
In this article, the 2-D fractional sub-diffusion equation is solved using the fractional explicit group method with weak singularity at initial time t=0, where the standard point finite difference scheme is used for the development of the fourth-order grouping scheme. The fractional explicit group method reduces the computational complexity and execution time by comparing it with the standard point fourth-order method without deteriorating the accuracy of the solutions. Furthermore, the unconditional stability and convergence of the proposed scheme are proved using the matrix analysis via mathematical induction, which confirms the feasibility and reliability of the new formulation.
This work was supported by the Ministry of Higher Education under Fundamental Research Grant Scheme (FRGS/1/2019/STG06/UTM/02/13, FRGS/1/2020/STG05/UTM/02/12).
We declare no conflicts of interest in this paper.
[1] |
Drakopoulos SX, Psarras GC, Forte G, et al. (2018) Entanglement dynamics in ultra-high molecular weight polyethylene as revealed by dielectric spectroscopy. Polymer 150: 35–43. https://doi.org/10.1016/j.polymer.2018.07.021. doi: 10.1016/j.polymer.2018.07.021
![]() |
[2] |
Golchin A, Simmons GF, Glavatskih S, et al. (2013) Tribological behaviour of polymeric materials in water-lubricated contacts. P I Mech Eng J-J Eng 227: 811–825. https://doi.org/10.1177/1350650113476441. doi: 10.1177/1350650113476441
![]() |
[3] |
Chang T, Yuan C, Guo Z (2019) Tribological behavior of aged UHMWPE under water-lubricated condition. Tribol Int 133: 1–11. https://doi.org/10.1016/j.triboint.2018.12.038. doi: 10.1016/j.triboint.2018.12.038
![]() |
[4] |
Chen S, Li J, Wei L, et al. (2017) Tribological properties of polyimide-modified UHMWPE for bushing materials of seawater lubricated sliding bearings. Tribol Int 115: 470–476. https://doi.org/10.1016/j.triboint.2017.06.011. doi: 10.1016/j.triboint.2017.06.011
![]() |
[5] |
Cho MH, Bahadur S, Pogosian AK (2005) Friction and wear studies using Taguchi method on polyphenylene sulfide filled with a complex mixture of MoS2, Al2O3, and other compounds. Wear 258: 1825–1835. https://doi.org/10.1016/j.wear.2004.12.017. doi: 10.1016/j.wear.2004.12.017
![]() |
[6] |
Ramadan MA (2018) Friction and wear of sand-contaminated lubricated sliding. Friction 6: 457–463. https://doi.org/10.1007/s40544-017-0192-4. doi: 10.1007/s40544-017-0192-4
![]() |
[7] |
Golchin A, Villain A, Emami N (2017) Tribological behaviour of nanodiamond reinforced UHMWPE in water-lubricated contacts. Tribol Int 110: 195–200. https://doi.org/10.1016/j.triboint.2017.01.016. doi: 10.1016/j.triboint.2017.01.016
![]() |
[8] |
Bruck AL, Karuppiah KS, Sundararajan S, et al. (2010) Friction and wear behavior of ultrahigh molecular weight polyethylene as a function of crystallinity in the presence of the phospholipid dipalmitoyl phosphatidylcholine. J Biomed Mater Res B 93: 351–358. https://doi.org/10.1002/jbm.b.31587. doi: 10.1002/jbm.b.31587
![]() |
[9] |
Atwood SA, Van Citters DW, Patten EW, et al. (2011) Tradeoffs amongst fatigue, wear, and oxidation resistance of cross-linked ultra-high molecular weight polyethylene. J Mech Behav Biomed Mater 4: 1033–1045. https://doi.org/10.1016/j.jmbbm.2011.03.012. doi: 10.1016/j.jmbbm.2011.03.012
![]() |
[10] |
Dougherty PSM, Srivastava G, Onler R, et al. (2015) Lubrication enhancement for UHMWPE sliding contacts through surface texturing. Tribol Trans 58: 79–86. https://doi.org/10.1080/10402004.2014.933935. doi: 10.1080/10402004.2014.933935
![]() |
[11] |
Kustandi TS, Choo JH, Low HY, et al. (2009) Texturing of UHMWPE surface via NIL for low friction and wear properties. J Phys D Appl Phys 43: 015301. https://doi.org/10.1088/0022-3727/43/1/015301. doi: 10.1088/0022-3727/43/1/015301
![]() |
[12] |
Nakatsuji T, Mori A (2001) The tribological effect of mechanically produced micro-dents by a micro diamond pyramid on medium carbon steel surfaces in rolling-sliding contact. Meccanica 36: 663–674. https://doi.org/10.1023/A:1016348803781. doi: 10.1023/A:1016348803781
![]() |
[13] |
Wang X, Adachi K, Otsuka K, et al. (2006) Optimization of the surface texture for silicon carbide sliding in water. Appl Surf Sci 253: 1282–1286. https://doi.org/10.1016/j.apsusc.2006.01.076. doi: 10.1016/j.apsusc.2006.01.076
![]() |
[14] |
Etsion I (2004) Improving tribological performance of mechanical components by laser surface texturing. Tribol Lett 17: 733–737. https://doi.org/10.1007/s11249-004-8081-1. doi: 10.1007/s11249-004-8081-1
![]() |
[15] |
Etsion I (2005) State of the art in laser surface texturing. J Tribol 127: 248–253. https://doi.org/10.1115/1.1828070. doi: 10.1115/1.1828070
![]() |
[16] |
Zhang YL, Zhang XG, Matsoukas G (2015) Numerical study of surface texturing for improving tribological properties of ultra-high molecular weight polyethylene. Biosurface Biotribology 1: 270–277. https://doi.org/10.1016/j.bsbt.2015.11.003. doi: 10.1016/j.bsbt.2015.11.003
![]() |
[17] |
Riveiro A, Soto R, Del Val J, et al. (2014) Laser surface modification of ultra-high-molecular-weight polyethylene (UHMWPE) for biomedical applications. Appl Surf Sci 302: 236–242. https://doi.org/10.1016/j.apsusc.2014.02.130. doi: 10.1016/j.apsusc.2014.02.130
![]() |
[18] |
Hussain M, Sufyan M, Abbas N, et al. (2019) Influence of laser processing conditions for texturing on ultra-high-molecular-weight-polyethylene (UHMWPE) surface. Case Studies in Thermal Engineering 14: 100491. https://doi.org/10.1016/j.csite.2019.100491. doi: 10.1016/j.csite.2019.100491
![]() |
[19] |
Tangwarodomnukun V, Chen HY (2015) Laser ablation of PMMA in air, water, and ethanol environments. Mater Manuf Process 30: 685–691. https://doi.org/10.1080/10426914.2014.994774. doi: 10.1080/10426914.2014.994774
![]() |
[20] |
Gao K, Liu J, Fan Y, et al. (2019) Ultra-low-cost fabrication of polymer-based microfluidic devices with diode laser ablation. Biomed Microdevices 21: 83. https://doi.org/10.1007/s10544-019-0433-6. doi: 10.1007/s10544-019-0433-6
![]() |
[21] |
Katayama S, Kubo Y, Yamada N (2002) Characterization and mechanical properties of flexible dimethylsiloxane‐based inorganic/organic hybrid sheets. J Am Ceram Soc 85: 1157–1163. https://doi.org/10.1111/j.1151-2916.2002.tb00238.x. doi: 10.1111/j.1151-2916.2002.tb00238.x
![]() |
[22] |
Aoki Y (2012) Electrical treeing characteristics in polydimethylsiloxane-based organic-inorganic hybrid materials. Mol Cryst Liq Cryst 568: 186–191. https://doi.org/10.1080/15421406.2012.708841. doi: 10.1080/15421406.2012.708841
![]() |
[23] |
Aoki Y (2016) Heat-resistant, thermally conductive coating of alumina on metal via electrophoretic deposition with added polydimethylsiloxane-based organic–inorganic hybrid materials. Polym Bull 73: 2605–2614. https://doi.org/10.1007/s00289-016-1700-9. doi: 10.1007/s00289-016-1700-9
![]() |
[24] |
Mata A, Fleischman AJ, Roy S (2005) Characterization of polydimethylsiloxane (PDMS) properties for biomedical micro/nanosystems. Biomed Microdevices 7: 281–293. https://doi.org/10.1007/s10544-005-6070-2. doi: 10.1007/s10544-005-6070-2
![]() |
[25] |
Torrisi L, Cutroneo M, Torrisi A, et al. (2020) IR ns pulsed laser irradiation of Polydimethylsiloxane in vacuum. Vacuum 177: 109361. https://doi.org/10.1016/j.vacuum.2020.109361. doi: 10.1016/j.vacuum.2020.109361
![]() |
[26] | Kurtz SM (2016) A primer on UHMWPE, UHMWPE Biomaterials Handbook, Amsterdam, Netherlands: William Andrew Publishing, 1–6. |
[27] | Material Property Database (polydimethylsiloxane). Available from: https://www.mit.edu/~6.777/matprops/pdms.htm. |
[28] |
Price EJ, Covello J, Tuchler A, et al. (2020) Intumescent, epoxy-based flame-retardant coatings based on poly(acrylic acid) compositions. ACS Appl Mater Interfaces 12: 18997–19005. https://doi.org/10.1021/acsami.0c00567. doi: 10.1021/acsami.0c00567
![]() |
[29] |
Sonnier R, Otazaghine B, Iftene F, et al. (2016) Predicting the flammability of polymers from their chemical structure: an improved model based on group contributions. Polymer 86: 42–55. https://doi.org/10.1016/j.polymer.2016.01.046. doi: 10.1016/j.polymer.2016.01.046
![]() |
[30] |
Xie X, Li D, Tsai TH, et al. (2016) Thermal conductivity, heat capacity, and elastic constants of water-soluble polymers and polymer blends. Macromolecules 49: 972–978. https://doi.org/10.1021/acs.macromol.5b02477. doi: 10.1021/acs.macromol.5b02477
![]() |
[31] | ChemSrc. Polyacrylic Acid. CAS#: 9003-01-4. Available from: https://www.chemsrc.com/en/cas/9003-01-4_453957.html#wuHuaDiv. |
[32] |
Wang Y, Li P, Sun Z, et al. (2018) A model of screen reaction force for the 3D additive screen printing. The Journal of The Textile Institute 109: 1000–1007. https://doi.org/10.1080/00405000.2017.1397834. doi: 10.1080/00405000.2017.1397834
![]() |
[33] | ASTM International (2013) Standard test methods for measurement of wet film thickness of organic coatings. ASTM D1212-91. Available from: https://www.astm.org/Standards/D1212.htm. |
[34] |
Nečas D, Klapetek P (2012) Gwyddion: an open-source software for SPM data analysis. Cent Eur J Phys 10: 181–188. https://doi.org/10.2478/s11534-011-0096-2. doi: 10.2478/s11534-011-0096-2
![]() |
[35] | Mahmoudzadeh R, Salabati M, Hsu J, et al. (2021) Agreement of optical coherence tomography thickness measurements between Heidelberg Eye Explorer and ImageJ software. CJO (In press). https://doi.org/10.1016/j.jcjo.2021.05.018. |
[36] |
Duangwas S, Tangwarodomnukun V, Dumkum C (2014) Development of an overflow-assisted underwater laser ablation. Mater Manuf Process 29: 1226–1231. https://doi.org/10.1080/10426914.2014.930896. doi: 10.1080/10426914.2014.930896
![]() |
[37] |
Mannion PT, Magee J, Coyne E, et al. (2004) The effect of damage accumulation behaviour on ablation thresholds and damage morphology in ultrafast laser micro-machining of common metals in air. Appl Surf Sci 233: 275–287. https://doi.org/10.1016/j.apsusc.2004.03.229. doi: 10.1016/j.apsusc.2004.03.229
![]() |
[38] |
Furzikov N (1990) Approximate theory of highly absorbing polymer ablation by nanosecond laser pulses. Appl Phys Lett 56: 1638–1640. https://doi.org/10.1063/1.103150. doi: 10.1063/1.103150
![]() |
[39] |
Kamal A, Bashir M, Firdous S, et al. (2016) Optical properties of ultra-high molecular weight polyethylene (UHMWPE): a material of choice for total joint applications. Radiat Phys Chem 118: 102–106. https://doi.org/10.1016/j.radphyschem.2015.03.012. doi: 10.1016/j.radphyschem.2015.03.012
![]() |
[40] |
Nunes dos Santos W, Mummery P, Wallwork A (2005) Thermal diffusivity of polymers by the laser flash technique. Polym Test 24: 628–634. https://doi.org/10.1016/j.polymertesting.2005.03.007. doi: 10.1016/j.polymertesting.2005.03.007
![]() |
[41] | Brown MS, Arnold CB (2010) Fundamentals of laser-material interaction and application to multiscale surface modification, In: Sugioka K, Meunier M, Piqué A, Laser Precision Microfabrication, Berlin, Heidelberg: Springer Berlin Heidelberg, 91–120. |
[42] |
Ahmed N, Darwish S, Alahmari AM (2016) Laser ablation and laser-hybrid ablation processes: a review. Mater Manuf Process 31: 1121–1142. https://doi.org/10.1080/10426914.2015.1048359. doi: 10.1080/10426914.2015.1048359
![]() |
[43] |
Von der Linde D, Sokolowski-Tinten K (2000) The physical mechanisms of short-pulse laser ablation. Appl Surf Sci 154: 1–10. https://doi.org/10.1016/S0169-4332(99)00440-7. doi: 10.1016/S0169-4332(99)00440-7
![]() |
[44] |
Hoffman J (2015) The effect of recoil pressure in the ablation of polycrystalline graphite by a nanosecond laser pulse. J Phys D Appl Phys 48: 235201. https://doi.org/10.1088/0022-3727/48/23/235201. doi: 10.1088/0022-3727/48/23/235201
![]() |
[45] |
Tangwarodomnukun V, Likhitangsuwat P, Tevinpibanphan O, et al. (2015) Laser ablation of titanium alloy under a thin and flowing water layer. Int J Mach Tool Manu 89: 14–28. https://doi.org/10.1016/j.ijmachtools.2014.10.013. doi: 10.1016/j.ijmachtools.2014.10.013
![]() |
[46] |
Singh S, Argument M, Tsui Y, et al. (2005) Effect of ambient air pressure on debris redeposition during laser ablation of glass. J Appl Phys 98: 113520. https://doi.org/10.1063/1.2138800. doi: 10.1063/1.2138800
![]() |
[47] |
Miotello A, Kelly R (1999) Laser-induced phase explosion: new physical problems when a condensed phase approaches the thermodynamic critical temperature. Appl Phys A 69: S67–S73. https://doi.org/10.1007/s003399900296. doi: 10.1007/s003399900296
![]() |
[48] |
Bulgakova N, Bulgakov A (2001) Pulsed laser ablation of solids: transition from normal vaporization to phase explosion. Appl Phys A 73: 199–208. https://doi.org/10.1007/s003390000686. doi: 10.1007/s003390000686
![]() |
[49] |
Sarma U, Joshi SN (2020) Numerical modelling and simulation of microchannel fabrication on polycarbonate using Laser-Induced Plasma Assisted Ablation (LIPAA). Optik 223: 165379. https://doi.org/10.1016/j.ijleo.2020.165379. doi: 10.1016/j.ijleo.2020.165379
![]() |
[50] |
Aoki Y, Yoshioka K (2014) Preparation and characterization of highly heat-resistant organic–inorganic hybrid materials made from two-component polydimethylsiloxane. Mol Cryst Liq Cryst 597: 59–64. https://doi.org/10.1080/15421406.2014.932224. doi: 10.1080/15421406.2014.932224
![]() |
[51] |
Samant AN, Dahotre NB (2008) Computational predictions in single-dimensional laser machining of alumina. Int J Mach Tool Manu 48: 1345–1353. https://doi.org/10.1016/j.ijmachtools.2008.05.004. doi: 10.1016/j.ijmachtools.2008.05.004
![]() |
[52] |
Zhou J, Shen H, Pan Y, et al. (2016) Experimental study on laser microstructures using long pulse. Opt Laser Eng 78: 113–120. https://doi.org/10.1016/j.optlaseng.2015.10.009. doi: 10.1016/j.optlaseng.2015.10.009
![]() |
1. | Rasel Islam, M. Abul Kawser, M. Sohel Rana, M. Nurul Islam, Mathematical analysis of soliton solutions in space-time fractional Klein-Gordon model with generalized exponential rational function method, 2024, 12, 26668181, 100942, 10.1016/j.padiff.2024.100942 | |
2. | Fouad Mohammad Salama, Faisal Fairag, On numerical solution of two-dimensional variable-order fractional diffusion equation arising in transport phenomena, 2024, 9, 2473-6988, 340, 10.3934/math.2024020 | |
3. | Jalu A. Prakosa, Norma Alias, Chifayah Astuti, 2023, Performance comparison of applying integer and fractional order calculus to DC motor speed control experiments, 979-8-3503-4389-2, 79, 10.1109/ICRAMET60171.2023.10366595 | |
4. | Nasir Ali, Muhammad Waseem, Maimoona Safdar, Ali Akgül, Fikadu Tesgera Tolasa, Iterative solutions for nonlinear equations via fractional derivatives: adaptations and advances, 2024, 32, 2769-0911, 10.1080/27690911.2024.2333816 | |
5. | Waleed Hamali, Abdulah A. Alghamdi, Exact solutions to the fractional nonlinear phenomena in fluid dynamics via the Riccati-Bernoulli sub-ODE method, 2024, 9, 2473-6988, 31142, 10.3934/math.20241501 |
h0/ν | No. of iteration | Execution time | Maximum-error | Average-error | ||||
FEGM | SP | FEGM | SP | FEGM | SP | FEGM | SP | |
h0=ν=110 | 43 | 49 | 7.39 | 7.76 | 1.6404×10−4 | 1.653 ×10−4 | 7.9408 ×10−5 | 7.3891 ×10−5 |
h0=ν=118 | 41 | 48 | 66.19 | 79.82 | 6.6571 ×10−5 | 6.5544×10−5 | 2.8320 ×10−5 | 2.9081 ×10−5 |
h0=ν=122 | 42 | 54 | 148.1 | 207.1 | 4.5739 ×10−5 | 4.6717 ×10−5 | 1.9997 ×10−5 | 2.085 ×10−5 |
h0=ν=130 | 43 | 56 | 530.45 | 658.68 | 3.0559 ×10−5 | 3.2268 ×10−5 | 1.1887 ×10−5 | 1.2180 ×10−5 |
h0/ν | No. of iteration | Execution time | Maximum-error | Average-error | ||||
FEGM | SP | FEGM | SP | FEGM | SP | FEGM | SP | |
h0=ν=110 | 44 | 50 | 7.75 | 7.94 | 2.1534 ×10−4 | 2.2065 ×10−4 | 1.0469 ×10−4 | 1.0634 ×10−4 |
h0=ν=114 | 44 | 43 | 27.36 | 27.28 | 1.2736 ×10−4 | 1.2786×10−4 | 5.9175 ×10−5 | 6.0624 ×10−5 |
h0=ν=118 | 42 | 48 | 68.29 | 80.18 | 8.0887 ×10−5 | 8.5709 ×10−5 | 3.0710 ×10−5 | 3.9889×10−5 |
h0=ν=122 | 41 | 55 | 150.40 | 197.87 | 6.1207 ×10−5 | 6.2773 ×10−5 | 2.8554 ×10−5 | 2.8809 ×10−5 |
h0=ν=130 | 42 | 56 | 523.25 | 648.55 | 3.7373×10−5 | 4.4510 ×10−5 | 1.6460 ×10−5 | 1.7874 ×10−5 |
h0/ν | No. of iteration | Execution time | Maximum-error | Average-error | ||||
FEGM | SP | FEGM | SP | FEGM | SP | FEGM | SP | |
h0=ν=110 | 44 | 50 | 7.75 | 7.94 | 2.1534 ×10−4 | 2.2065 ×10−4 | 1.0469 ×10−4 | 1.0634 ×10−4 |
h0=ν=114 | 44 | 43 | 27.36 | 27.28 | 1.2736 ×10−4 | 1.2786×10−4 | 5.9175 ×10−5 | 6.0624 ×10−5 |
h0=ν=118 | 42 | 48 | 68.29 | 80.18 | 8.0887 ×10−5 | 8.5709 ×10−5 | 3.0710 ×10−5 | 3.9889×10−5 |
h0=ν=122 | 41 | 55 | 150.40 | 197.87 | 6.1207 ×10−5 | 6.2773 ×10−5 | 2.8554 ×10−5 | 2.8809 ×10−5 |
h0=ν=130 | 42 | 56 | 523.25 | 648.55 | 3.7373×10−5 | 4.4510 ×10−5 | 1.6460 ×10−5 | 1.7874 ×10−5 |
ν/h0 | No. of iteration | Execution time | Maximum-error | Average-error | ||||
FEGM | SP | FEGM | SP | FEGM | SP | FEGM | SP | |
h0=ν=110 | 46 | 52 | 7.65 | 8.72 | 2.9442 ×10−4 | 2.8915 ×10−4 | 1.3091 ×10−4 | 1.2849 ×10−4 |
h0=ν=114 | 48 | 47 | 30.93 | 29.53 | 1.3893 ×10−4 | 1.4377 ×10−4 | 3.7322 ×10−5 | 3.9455 ×10−5 |
h0=ν=118 | 48 | 52 | 77.2 | 84.75 | 8.5499 ×10−5 | 8.5075 ×10−5 | 2.4058 ×10−5 | 2.4340 ×10−5 |
h0=ν=122 | 47 | 57 | 172.53 | 203.76 | 5.5120 ×10−5 | 5.5018 ×10−5 | 1.9837 ×10−5 | 1.7813 ×10−5 |
h0=ν=130 | 47 | 65 | 588.74 | 789.14 | 2.9259 ×10−5 | 2.9669 ×10−5 | 1.2478 ×10−5 | 1.2549 ×10−5 |
h0/ν | No. of iteration | Execution time | Maximum-error | Average-error | ||||
FEGM | SP | FEGM | SP | FEGM | SP | FEGM | SP | |
h0=ν=110 | 47 | 53 | 7.92 | 8.82 | 2.2868 ×10−4 | 2.2917 ×10−4 | 1.0194 ×10−4 | 1.0189 ×10−4 |
h0=ν=114 | 48 | 48 | 31.23 | 30.46 | 2.3640 ×10−4 | 2.3848 ×10−4 | 1.1941 ×10−4 | 1.2003 ×10−4 |
h0=ν=118 | 49 | 52 | 78.34 | 85.3 | 2.1361 ×10−4 | 2.1290 ×10−4 | 1.0621 ×10−4 | 1.0863 ×10−4 |
h0=ν=122 | 48 | 57 | 169.15 | 207.6 | 1.9686 ×10−4 | 1.8908 ×10−4 | 9.5981 ×10−5 | 9.5644 ×10−5 |
h0=ν=130 | 48 | 65 | 599.97 | 775.49 | 1.5244 ×10−4 | 1.4938 ×10−4 | 7.3782 ×10−5 | 7.3922 ×10−5 |
h0/ν | No. of iteration | Maximum-error | Average-error | |||
FEGM | [27] | FEGM | [27] | FEGM | [27] | |
h0=ν=110 | 43 | 53 | 1.6404 ×10−4 | 1.2428 ×10−2 | 7.9408 ×10−5 | 8.8490 ×10−3 |
h0=ν=118 | 41 | 52 | 6.6571 ×10−5 | 7.1213 ×10−3 | 2.8320 ×10−5 | 3.6917 ×10−3 |
h0=ν=122 | 42 | 55 | 4.7739 ×10−5 | 2.6959 ×10−3 | 1.9997 ×10−5 | 1.3580 ×10−3 |
h0=165,ν=135 | 41 | 58 | 2.5368 ×10−5 | 2.0605 ×10−3 | 5.0090 ×10−6 | 1.0285 ×10−3 |
Technique | operations per iteration | |
+/- | */ ÷ | |
SP | (26+8(k−1))m2 | (8+4(k−1))m2 |
FEGM | (28+8(k−1))(m−1)2 + (26+8(k−1))(2m−1) | (12+4(k−1))(m−1)2 + (8+4(k−1))(2m−1) |
h0/ν | SP method | FEGM | ||
Number of iteration | Total operations | Number of iteration | Total operations | |
h0=ν=110 | 49 | 695800 | 43 | 631498 |
h0=ν=118 | 48 | 3701376 | 41 | 3232686 |
h0=ν=122 | 54 | 7474896 | 42 | 5924940 |
h0=ν=130 | 56 | 19252800 | 43 | 15000378 |
k/m | SP method | FEGM | ||
Number of iteration | Total operations | Number of iteration | Total operations | |
h0=ν=110 | 53 | 752600 | 47 | 690242 |
h0=ν=118 | 52 | 4009824 | 49 | 3863454 |
h0=ν=122 | 57 | 7890168 | 48 | 6771360 |
h0=ν=130 | 65 | 22347000 | 48 | 16744608 |
α=0.4 | α=0.5 | ||||
ν/h0 | Maximum error | C2-order | ν/h0 | Maximum error | C2-order |
ν=h0=0.5 | 1.4394 ×10−4 | — | ν=h0=0.5 | 3.1088 ×10−4 | — |
ν=0.031, h0=0.25 | 1.0910 ×10−5 | 3.72 | ν=0.031, h0=0.25 | 2.2509 ×10−5 | 3.78 |
ν=h0=0.25 | 2.1929 ×10−4 | — | ν=h0=0.25 | 3.546 ×10−4 | — |
ν=0.016, h0=0.12 | 9.1371 ×10−6 | 4.58 | ν=0.016, h0=0.12 | 2.1414 ×10−5 | 4.04 |
α=0.6 | α=0.8 | ||||
ν/h0 | Maximum error | C2-order | ν/h0 | Maximum error | C2-order |
ν=h0=0.5 | 5.2435 ×10−4 | — | ν=h0=0.5 | 9.9004 ×10−4 | — |
ν=0.031, h0=0.25 | 2.7191 ×10−5 | 4.26 | ν=0.031, h0=0.25 | 9.9004 ×10−5 | 4.13 |
ν=h0=0.25 | 5.0421 ×10−4 | — | ν=h0=0.25 | 7.2673 ×10−4 | — |
ν=0.016, h0=0.12 | 3.1980 ×10−5 | 3.97 | ν=0.016, h0=0.12 | 3.7243 ×10−5 | 4.28 |
α=0.7 | α=0.8 | ||||
ν/h0 | Maximum error | C2-order | ν/h0 | Maximum error | C2-order |
ν=h0=0.5 | 1.6072 ×10−3 | — | ν=h0=0.5 | 3.4202 ×10−3 | — |
ν=0.031, h0=0.25 | 1.0543 ×10−4 | 3.93 | ν=0.031, h0=0.25 | 1.7636 ×10−4 | 4.27 |
ν=h0=0.25 | 1.3545 ×10−3 | — | ν=h0=0.25 | 1.6955 ×10−3 | — |
ν=0.016, h0=0.12 | 5.9784 ×10−5 | 4.50 | ν=0.016, h0=0.12 | 8.2806 ×10−5 | 4.35 |
α=0.3 | α=0.5 | ||||
ν/h0 | Maximum error | C2-order | ν/h0 | Maximum error | C2-order |
ν=h0=0.5 | 3.832 ×10−3 | — | ν=h0=0.5 | 8.6771 ×10−4 | — |
ν=0.031, h0=0.25 | 3.2105 ×10−4 | 3.57 | ν=0.031, h0=0.25 | 4.8772 ×10−5 | 4.15 |
ν=h0=0.25 | 4.5916 ×10−4 | — | ν=h0=0.25 | 4.1734 ×10−4 | — |
ν=0.016, h0=0.12 | 2.5978 ×10−5 | 4.14 | ν=0.016, h0=0.12 | 2.3009 ×10−5 | 4.18 |
ν | α=0.3 | α=0.8 | ||
L∞ | C1− Order | L∞ | C1− Order | |
ν=110 | 7.8675×10−4 | — | 2.1609×10−4 | — |
ν=120 | 3.2208 ×10−5 | 1.28 | 7.1112 ×10−5 | 1.60 |
ν= 140 | 1.7253 ×10−5 | 1.29 | 2.6203 ×10−5 | 1.44 |
ν=180 | 6.2057×10−6 | 1.72 | 8.3392×10−6 | 1.65 |
ν | α=0.1 | α=0.8 | ||
L∞ | C1− Order | L∞ | C1− Order | |
ν=110 | 4.7691×10−4 | — | 2.1429×10−4 | — |
ν=120 | 1.6086 ×10−4 | 1.56 | 8.2679 ×10−5 | 1.37 |
ν= 140 | 5.1170 ×10−5 | 1.65 | 3.2827 ×10−5 | 1.33 |
ν=180 | 1.7848×10−5 | 1.51 | 1.3010×10−5 | 1.51 |
h0/ν | No. of iteration | Execution time | Maximum-error | Average-error | ||||
FEGM | SP | FEGM | SP | FEGM | SP | FEGM | SP | |
h0=ν=110 | 43 | 49 | 7.39 | 7.76 | 1.6404×10−4 | 1.653 ×10−4 | 7.9408 ×10−5 | 7.3891 ×10−5 |
h0=ν=118 | 41 | 48 | 66.19 | 79.82 | 6.6571 ×10−5 | 6.5544×10−5 | 2.8320 ×10−5 | 2.9081 ×10−5 |
h0=ν=122 | 42 | 54 | 148.1 | 207.1 | 4.5739 ×10−5 | 4.6717 ×10−5 | 1.9997 ×10−5 | 2.085 ×10−5 |
h0=ν=130 | 43 | 56 | 530.45 | 658.68 | 3.0559 ×10−5 | 3.2268 ×10−5 | 1.1887 ×10−5 | 1.2180 ×10−5 |
h0/ν | No. of iteration | Execution time | Maximum-error | Average-error | ||||
FEGM | SP | FEGM | SP | FEGM | SP | FEGM | SP | |
h0=ν=110 | 44 | 50 | 7.75 | 7.94 | 2.1534 ×10−4 | 2.2065 ×10−4 | 1.0469 ×10−4 | 1.0634 ×10−4 |
h0=ν=114 | 44 | 43 | 27.36 | 27.28 | 1.2736 ×10−4 | 1.2786×10−4 | 5.9175 ×10−5 | 6.0624 ×10−5 |
h0=ν=118 | 42 | 48 | 68.29 | 80.18 | 8.0887 ×10−5 | 8.5709 ×10−5 | 3.0710 ×10−5 | 3.9889×10−5 |
h0=ν=122 | 41 | 55 | 150.40 | 197.87 | 6.1207 ×10−5 | 6.2773 ×10−5 | 2.8554 ×10−5 | 2.8809 ×10−5 |
h0=ν=130 | 42 | 56 | 523.25 | 648.55 | 3.7373×10−5 | 4.4510 ×10−5 | 1.6460 ×10−5 | 1.7874 ×10−5 |
h0/ν | No. of iteration | Execution time | Maximum-error | Average-error | ||||
FEGM | SP | FEGM | SP | FEGM | SP | FEGM | SP | |
h0=ν=110 | 44 | 50 | 7.75 | 7.94 | 2.1534 ×10−4 | 2.2065 ×10−4 | 1.0469 ×10−4 | 1.0634 ×10−4 |
h0=ν=114 | 44 | 43 | 27.36 | 27.28 | 1.2736 ×10−4 | 1.2786×10−4 | 5.9175 ×10−5 | 6.0624 ×10−5 |
h0=ν=118 | 42 | 48 | 68.29 | 80.18 | 8.0887 ×10−5 | 8.5709 ×10−5 | 3.0710 ×10−5 | 3.9889×10−5 |
h0=ν=122 | 41 | 55 | 150.40 | 197.87 | 6.1207 ×10−5 | 6.2773 ×10−5 | 2.8554 ×10−5 | 2.8809 ×10−5 |
h0=ν=130 | 42 | 56 | 523.25 | 648.55 | 3.7373×10−5 | 4.4510 ×10−5 | 1.6460 ×10−5 | 1.7874 ×10−5 |
ν/h0 | No. of iteration | Execution time | Maximum-error | Average-error | ||||
FEGM | SP | FEGM | SP | FEGM | SP | FEGM | SP | |
h0=ν=110 | 46 | 52 | 7.65 | 8.72 | 2.9442 ×10−4 | 2.8915 ×10−4 | 1.3091 ×10−4 | 1.2849 ×10−4 |
h0=ν=114 | 48 | 47 | 30.93 | 29.53 | 1.3893 ×10−4 | 1.4377 ×10−4 | 3.7322 ×10−5 | 3.9455 ×10−5 |
h0=ν=118 | 48 | 52 | 77.2 | 84.75 | 8.5499 ×10−5 | 8.5075 ×10−5 | 2.4058 ×10−5 | 2.4340 ×10−5 |
h0=ν=122 | 47 | 57 | 172.53 | 203.76 | 5.5120 ×10−5 | 5.5018 ×10−5 | 1.9837 ×10−5 | 1.7813 ×10−5 |
h0=ν=130 | 47 | 65 | 588.74 | 789.14 | 2.9259 ×10−5 | 2.9669 ×10−5 | 1.2478 ×10−5 | 1.2549 ×10−5 |
h0/ν | No. of iteration | Execution time | Maximum-error | Average-error | ||||
FEGM | SP | FEGM | SP | FEGM | SP | FEGM | SP | |
h0=ν=110 | 47 | 53 | 7.92 | 8.82 | 2.2868 ×10−4 | 2.2917 ×10−4 | 1.0194 ×10−4 | 1.0189 ×10−4 |
h0=ν=114 | 48 | 48 | 31.23 | 30.46 | 2.3640 ×10−4 | 2.3848 ×10−4 | 1.1941 ×10−4 | 1.2003 ×10−4 |
h0=ν=118 | 49 | 52 | 78.34 | 85.3 | 2.1361 ×10−4 | 2.1290 ×10−4 | 1.0621 ×10−4 | 1.0863 ×10−4 |
h0=ν=122 | 48 | 57 | 169.15 | 207.6 | 1.9686 ×10−4 | 1.8908 ×10−4 | 9.5981 ×10−5 | 9.5644 ×10−5 |
h0=ν=130 | 48 | 65 | 599.97 | 775.49 | 1.5244 ×10−4 | 1.4938 ×10−4 | 7.3782 ×10−5 | 7.3922 ×10−5 |
h0/ν | No. of iteration | Maximum-error | Average-error | |||
FEGM | [27] | FEGM | [27] | FEGM | [27] | |
h0=ν=110 | 43 | 53 | 1.6404 ×10−4 | 1.2428 ×10−2 | 7.9408 ×10−5 | 8.8490 ×10−3 |
h0=ν=118 | 41 | 52 | 6.6571 ×10−5 | 7.1213 ×10−3 | 2.8320 ×10−5 | 3.6917 ×10−3 |
h0=ν=122 | 42 | 55 | 4.7739 ×10−5 | 2.6959 ×10−3 | 1.9997 ×10−5 | 1.3580 ×10−3 |
h0=165,ν=135 | 41 | 58 | 2.5368 ×10−5 | 2.0605 ×10−3 | 5.0090 ×10−6 | 1.0285 ×10−3 |
Technique | operations per iteration | |
+/- | */ ÷ | |
SP | (26+8(k−1))m2 | (8+4(k−1))m2 |
FEGM | (28+8(k−1))(m−1)2 + (26+8(k−1))(2m−1) | (12+4(k−1))(m−1)2 + (8+4(k−1))(2m−1) |
h0/ν | SP method | FEGM | ||
Number of iteration | Total operations | Number of iteration | Total operations | |
h0=ν=110 | 49 | 695800 | 43 | 631498 |
h0=ν=118 | 48 | 3701376 | 41 | 3232686 |
h0=ν=122 | 54 | 7474896 | 42 | 5924940 |
h0=ν=130 | 56 | 19252800 | 43 | 15000378 |
k/m | SP method | FEGM | ||
Number of iteration | Total operations | Number of iteration | Total operations | |
h0=ν=110 | 53 | 752600 | 47 | 690242 |
h0=ν=118 | 52 | 4009824 | 49 | 3863454 |
h0=ν=122 | 57 | 7890168 | 48 | 6771360 |
h0=ν=130 | 65 | 22347000 | 48 | 16744608 |
α=0.4 | α=0.5 | ||||
ν/h0 | Maximum error | C2-order | ν/h0 | Maximum error | C2-order |
ν=h0=0.5 | 1.4394 ×10−4 | — | ν=h0=0.5 | 3.1088 ×10−4 | — |
ν=0.031, h0=0.25 | 1.0910 ×10−5 | 3.72 | ν=0.031, h0=0.25 | 2.2509 ×10−5 | 3.78 |
ν=h0=0.25 | 2.1929 ×10−4 | — | ν=h0=0.25 | 3.546 ×10−4 | — |
ν=0.016, h0=0.12 | 9.1371 ×10−6 | 4.58 | ν=0.016, h0=0.12 | 2.1414 ×10−5 | 4.04 |
α=0.6 | α=0.8 | ||||
ν/h0 | Maximum error | C2-order | ν/h0 | Maximum error | C2-order |
ν=h0=0.5 | 5.2435 ×10−4 | — | ν=h0=0.5 | 9.9004 ×10−4 | — |
ν=0.031, h0=0.25 | 2.7191 ×10−5 | 4.26 | ν=0.031, h0=0.25 | 9.9004 ×10−5 | 4.13 |
ν=h0=0.25 | 5.0421 ×10−4 | — | ν=h0=0.25 | 7.2673 ×10−4 | — |
ν=0.016, h0=0.12 | 3.1980 ×10−5 | 3.97 | ν=0.016, h0=0.12 | 3.7243 ×10−5 | 4.28 |
α=0.7 | α=0.8 | ||||
ν/h0 | Maximum error | C2-order | ν/h0 | Maximum error | C2-order |
ν=h0=0.5 | 1.6072 ×10−3 | — | ν=h0=0.5 | 3.4202 ×10−3 | — |
ν=0.031, h0=0.25 | 1.0543 ×10−4 | 3.93 | ν=0.031, h0=0.25 | 1.7636 ×10−4 | 4.27 |
ν=h0=0.25 | 1.3545 ×10−3 | — | ν=h0=0.25 | 1.6955 ×10−3 | — |
ν=0.016, h0=0.12 | 5.9784 ×10−5 | 4.50 | ν=0.016, h0=0.12 | 8.2806 ×10−5 | 4.35 |
α=0.3 | α=0.5 | ||||
ν/h0 | Maximum error | C2-order | ν/h0 | Maximum error | C2-order |
ν=h0=0.5 | 3.832 ×10−3 | — | ν=h0=0.5 | 8.6771 ×10−4 | — |
ν=0.031, h0=0.25 | 3.2105 ×10−4 | 3.57 | ν=0.031, h0=0.25 | 4.8772 ×10−5 | 4.15 |
ν=h0=0.25 | 4.5916 ×10−4 | — | ν=h0=0.25 | 4.1734 ×10−4 | — |
ν=0.016, h0=0.12 | 2.5978 ×10−5 | 4.14 | ν=0.016, h0=0.12 | 2.3009 ×10−5 | 4.18 |
ν | α=0.3 | α=0.8 | ||
L∞ | C1− Order | L∞ | C1− Order | |
ν=110 | 7.8675×10−4 | — | 2.1609×10−4 | — |
ν=120 | 3.2208 ×10−5 | 1.28 | 7.1112 ×10−5 | 1.60 |
ν= 140 | 1.7253 ×10−5 | 1.29 | 2.6203 ×10−5 | 1.44 |
ν=180 | 6.2057×10−6 | 1.72 | 8.3392×10−6 | 1.65 |
ν | α=0.1 | α=0.8 | ||
L∞ | C1− Order | L∞ | C1− Order | |
ν=110 | 4.7691×10−4 | — | 2.1429×10−4 | — |
ν=120 | 1.6086 ×10−4 | 1.56 | 8.2679 ×10−5 | 1.37 |
ν= 140 | 5.1170 ×10−5 | 1.65 | 3.2827 ×10−5 | 1.33 |
ν=180 | 1.7848×10−5 | 1.51 | 1.3010×10−5 | 1.51 |