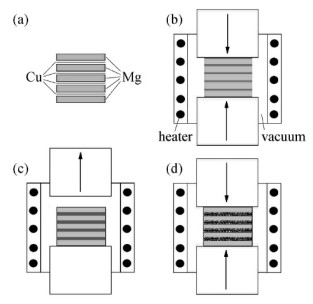
Laminated Mg-intermetallic composites were successfully fabricated by reaction synthesis in vacuum using 1 mm thick magnesium sheets and 0.25 mm thick copper foils. The final microstructure consisted of alternating layers of a hypoeutectic alloy containing crystals of CuMg2 and eutectic mixture of CuMg2 and solid solution of copper in magnesium and unreacted magnesium. The mechanical properties and fracture behavior of the fabricated composites were examined under different loading directions through compression, three-point bending and impact tests. The results indicated that the composites exhibited anisotropic features. The specimens compressed in the parallel direction failed by cracking along the layers of intermetallics and buckling of magnesium layers. The specimens compressed in the perpendicular direction failed by transverse cracking in the intermetallic layers and fallowing catastrophic cracking inclined about 45° to the interface of both intermetallic and magnesium layers. The flexural strength of the composites was higher in perpendicular than in parallel direction. When the load parallel to the layers was applied, the failure occurred by cleavage mode showing limited plastic deformation. When the load perpendicular to the layers was applied, the failure occurred by transverse cracking of the intermetallic layers and gradual cracking of the Mg layers. The Charpy-tested samples showed the same fracture behavior as the bend-tested specimens, which indicated that the same mechanisms operated at both high impact rate and low bending-test rate.
Citation: Marek Konieczny. Mechanical properties and failure analysis of laminated magnesium-intermetallic composites[J]. AIMS Materials Science, 2022, 9(4): 572-583. doi: 10.3934/matersci.2022034
[1] | Marek Konieczny . Transformation superplasticity of laminated CuAl10Fe3Mn2 bronze-intermetallics composites. AIMS Materials Science, 2020, 7(3): 312-322. doi: 10.3934/matersci.2020.3.312 |
[2] | Marek Konieczny . Mechanical properties and wear characterization of Al-Mg composites synthesized at different temperatures. AIMS Materials Science, 2024, 11(2): 309-322. doi: 10.3934/matersci.2024017 |
[3] | Mateo Duarte, Johan A. Oquendo, Sebastián Vallejo, Johnattan Vargas, Yamile Cardona-Maya, Cesar A. Isaza . Fabrication of FRP/CNT hybrid laminate composites and their effect on interlaminar and mechanical properties. AIMS Materials Science, 2024, 11(6): 1125-1144. doi: 10.3934/matersci.2024054 |
[4] | Venkatarajan Subbarayalu, Subbu Chinnaraman, Athijayamani Ayyanar, Jayaseelan Chinnapalanisamy . Mechanical properties of vinyl ester hybrid composite laminates reinforced with screw pine and glass fiber. AIMS Materials Science, 2024, 11(1): 114-128. doi: 10.3934/matersci.2024007 |
[5] | P. Sagar, A. Handa . A comprehensive review of recent progress in fabrication of magnesium base composites by friction stir processing technique—A review. AIMS Materials Science, 2020, 7(5): 684-704. doi: 10.3934/matersci.2020.5.684 |
[6] | Mica Grujicic, Jennifer S. Snipes, S. Ramaswami . Penetration resistance and ballistic-impact behavior of Ti/TiAl3 metal/intermetallic laminated composites (MILCs): A computational investigation. AIMS Materials Science, 2016, 3(3): 686-721. doi: 10.3934/matersci.2016.3.686 |
[7] | M. Rajanish, N. V. Nanjundaradhya, Ramesh S. Sharma, H. K. Shivananda, Alok Hegde . Directional Interlaminar Shear Strength (ILSS) of nano-modified epoxy/unidirectional glass fibre composite. AIMS Materials Science, 2018, 5(4): 603-613. doi: 10.3934/matersci.2018.4.603 |
[8] | Elisa Padovano, Francesco Trevisan, Sara Biamino, Claudio Badini . Processing of hybrid laminates integrating ZrB2/SiC and SiC layers. AIMS Materials Science, 2020, 7(5): 552-564. doi: 10.3934/matersci.2020.5.552 |
[9] | Saeid Saberi, Azam Abdollahi, Fawad Inam . Reliability analysis of bistable composite laminates. AIMS Materials Science, 2021, 8(1): 29-41. doi: 10.3934/matersci.2021003 |
[10] | Mohammed Y. Abdellah, Hamzah Alharthi, Mohamed K. Hassan, Ahmed F. Mohamed . Effect of specimen size on natural vibration of open hole copper/glass-reinforced epoxy laminate composites. AIMS Materials Science, 2020, 7(4): 499-517. doi: 10.3934/matersci.2020.4.499 |
Laminated Mg-intermetallic composites were successfully fabricated by reaction synthesis in vacuum using 1 mm thick magnesium sheets and 0.25 mm thick copper foils. The final microstructure consisted of alternating layers of a hypoeutectic alloy containing crystals of CuMg2 and eutectic mixture of CuMg2 and solid solution of copper in magnesium and unreacted magnesium. The mechanical properties and fracture behavior of the fabricated composites were examined under different loading directions through compression, three-point bending and impact tests. The results indicated that the composites exhibited anisotropic features. The specimens compressed in the parallel direction failed by cracking along the layers of intermetallics and buckling of magnesium layers. The specimens compressed in the perpendicular direction failed by transverse cracking in the intermetallic layers and fallowing catastrophic cracking inclined about 45° to the interface of both intermetallic and magnesium layers. The flexural strength of the composites was higher in perpendicular than in parallel direction. When the load parallel to the layers was applied, the failure occurred by cleavage mode showing limited plastic deformation. When the load perpendicular to the layers was applied, the failure occurred by transverse cracking of the intermetallic layers and gradual cracking of the Mg layers. The Charpy-tested samples showed the same fracture behavior as the bend-tested specimens, which indicated that the same mechanisms operated at both high impact rate and low bending-test rate.
Recently, magnesium and its alloys have attracted considerable attention, primarily because magnesium is one of the lightest structural metals. Low density magnesium alloys with excellent machinability and satisfactory recyclability are utilized in automotive, aerospace and electrical industries [1,2,3]. However, the quite low elastic modulus of the metal and its alloys has caused a limited use of these materials. A slightly higher modulus of elasticity can be obtained by introducing additional reinforcing phases into the magnesium matrix. The varied particulate-reinforced [4,5,6], fiber-reinforced [7,8,9] and laminated [10,11,12,13] magnesium composites have been fabricated. It is obvious that improvement of the composites properties depend strongly on the volume fraction, shape and morphology of reinforcement. It appears that significantly higher stiffness and generally higher mechanical properties e.g. improved fatigue behavior, fracture toughness, wear, and wear capacity, can be obtained for laminated composites [14]. Recently, metal-intermetallic laminated (MIL) composites have attracted considerable interest. They have the potential to fulfill various functions, such as thermal management, heat exchange, vibration damping, ballistic protection and blast mitigation [15]. Their production method is based on synthesis of intermetallics at the interface between two metals. To receive a laminated composite sheets of one metal are put alternately with foils of another metal into a packet. Subsequently the packet must be heated to a temperature that is high enough to start the reaction between the metals and the process should be continued till the thinner metal is fully consumed. This method has been used to produce various MIL composites [10,13,15,16,17,18,19,20]. Unfortunately, most intermetallics exhibit brittle fracture and low ductility at room temperature. Furthermore, during deformation the common crystal structure mismatch between the base metal and intermetallic layers makes almost impossible slip-bands slide through a metal/intermetallic interface. Numerous studies have illustrated the obvious benefits that can be achieved via the creation of a laminated structure. Improvements to the fracture resistance have been measured using many methods, including: tension testing, three-point bending testing, Charpy impact testing, ballistic testing etc. [14]. The main damage modes of laminated structures have been extensively investigated and modelled using stress-based criteria for damage initiation, fracture mechanics techniques, and the finite element method by Cao and Evans [21], Bruno et al. [22] and Shi et al. [23]. Generally, laminated composites can damage in the form of interlaminar delamination and intralaminar cracking in the direction transverse to the layers [22]. Toughening in laminated composites results from mechanisms that reduce the local stress intensity at the crack tip. In laminate systems the fallowing toughening mechanisms have been identified: crack deflection, crack blunting, crack bridging, stress redistribution, crack front convolution, and local plane stress deformation [14].
Improvement of the mechanical properties depends on the morphology and volume fraction of reinforcements and its shape. It was expected that substantially higher mechanical properties could be received for laminated composites with magnesium and copper-based intermetallic layers. This idea was the motivation of this work and it is a scientific novelty so far not studied by other researchers. The main aim of this work was to study the mechanical properties of the laminated magnesium-intermetallic composites under different loading conditions and to analyze their failure mechanisms.
In the work, 1 mm thick sheets of magnesium (99.79 at% Mg) and 0.25 mm thick foils of copper (99.99 at% Cu) were used to produce laminated magnesium-intermetallic composites. Sheets and foils were cut into 60 mm × 10 mm rectangular pieces. The joined surfaces were polished on 1200 grade abrasive paper just before bonding. After that sheets and foils were rinsed in water and then in ethanol. After drying they were stacked into laminates in an alternating sequence (6 pieces of magnesium and 5 pieces of copper). A pressure of 5 MPa was applied at room temperature in a specially constructed vacuum furnace to ensure good contact between the metals. After a series of attempts was found that a temperature of at least 480 ℃ was necessary for the start and rapid development of structural processes at the interface between magnesium and copper. During experiment the temperature was increased from 20 to 420 ℃ at a heating rate of 0.25 ℃/s. The samples were heated in vacuum of 10-3 Pa at 420 ℃ for 1 h under the applied 5 MPa pressure to allow diffusion bonding of the metals. After that the packets were heated to 490 ℃ and held at this temperature for 60 min. The pressure was removed during this processing sequence with the purpose of eliminating the possible expulsion of liquid phases. The temperature was then decreased slowly (cooling rate of 0.16 ℃/s) to 400 ℃ and the pressure of 5 MPa was applied again to final consolidation of the produced laminated magnesium-intermetallic composites. After that the samples were furnace-cooled to ambient temperature (Figure 1).
The microstructural observations were performed using a JMS 5400 (JEOL, Japan) scanning electron microscope and an ECLIPSE MA 200 (Nikon, Japan) optical microscope. Before the samples were examined with the optical microscope they had been etched to reveal the grains of copper-based compounds using solution of 40 g CrO3, 7.5 g NH4Cl, 8 mL H2SO4, 50 mL HNO3 and 1900 mL H2O. The chemical composition of the phases was determined by an energy dispersive spectroscopy (EDS) using a ISIS 300 (Oxford Instruments, UK). Composition of the phases was determined by comparing the results of the microprobe analysis with the data in the binary Cu-Mg phase diagram [24], which is shown in Figure 2.
An X-ray diffraction using a D/max RAPID2 diffractometer (Rigaku, Japan) was employed to confirm the presence of the intermetallic phases. The microstructures of the laminated magnesium-intermetallic composites were examined before and after mechanical testing. Especially, cracks location and cracks orientation were investigated carefully.
Compression and three-point bending tests were carried out on an Amsler (Zwick, Germany) screw machine. The compression tests were performed on cubic samples with dimension of 6 mm perpendicular and parallel to the laminate layers at a constant crosshead speed of 0.1 mm/min. The flexural strength measurements were performed using a three-point bending test on un-notched specimens with dimensions of 55 × 6 × 6 mm where the loading span was 45 mm. The tests were carried out under displacement control at a rate of 1.0 mm/min. The Charpy tests were conducted on a pendulum impact tester using identical rectangular samples as in the three-point bending test. The three-point bending and impact tests were performed in perpendicular and parallel directions to the magnesium-intermetallic interfaces. The reported data for all mechanical tests are average values of three tested specimens. In order to compare the properties of laminated composites and magnesium, samples of magnesium with identical dimensions were also made on which identical tests were carried out.
Reactions at 490 ℃ for 60 min between Mg sheets and Cu foils resulted in a laminated composite microstructure with alternating intermetallic layers and unreacted magnesium. The intermetallic layers were in fact layers of hypoeutectic alloy containing crystals of CuMg2 and eutectic mixture of CuMg2 and (Mg) solid solution of copper in magnesium (Figure 3).
The thickness of the Mg layers was between 0.56 and 0.72 mm and the thickness of the intermetallic layers was between 0.55 and 0.74 mm. The EDS examinations showed that only one intermetallic phase CuMg2 was formed in the samples and the XRD confirmed the results (Figure 4).
When the temperature reached 490 ℃ the reaction zone was a solid-liquid mixture. The existence of liquid is shown by the distribution of shrinkage voids (Figure 3). A solution to this problem is applying pressure during the cooling stage to achieve final consolidation of the produced laminated composites [15,16,17,18,19,20]. On the other hand, the existence of the solid-liquid mixture during formation of the intermetallic layers is very profitable. The presence of MgO inclusions in a continuous state in the formed layers could be a drawback. In solid-liquid mixture the MgO films changed into isolated harmless inclusions under the action of surface energy. The magnesium-intermetallic composite fabrication process has been studied in detail and described previously [13].
The tested specimens were investigated in order to understand damage evolution as a function of the compressive loading direction that was perpendicular or parallel to the layers. Figure 5 shows the quasi-static stress-strain curves for specimens tested during the compression test.
The compressive strength of the magnesium-intermetallic laminated composites as well as comparatively measured compressive strength of pure magnesium are given in Table 1.
Investigated material | Load direction | Compressive strength (MPa) | Flexural strength (MPa) | Impact toughness (J/cm2) |
Laminated magnesium-intermetallic composite | parallel to layers | 335 | 188 | 5 |
perpendicular to layers | 286 | 265 | 14 | |
Magnesium | - | 178 | 117 | 9 |
The quasi-static compression tests allowed characterizing the damage evolution operating during the tests. It is easily apparent from Figure 6 that different fracture mechanisms occurred in the investigated materials with respect to the loading direction.
The main feature during loading in perpendicular direction was the formation of transverse splitting cracks in the intermetallic layers and fallowing catastrophic cracking both of intermetallic layers and magnesium layers. Cracking that indicated the beginning of the deformation process in the intermetallic layers created stress concentration points at the magnesium-intermetallic interfaces, which formed shear bands that propagated from the crack tip through the magnesium layers into the next intermetallic layer. The observed serrations in the stress-strain curves in Figure 5 correspond to the formation of multiple cracks in the intermetallic layers. The main crack was inclined about 45° to the interface (Figure 6a). The energy absorption capability of the magnesium layers allowed numerous cracks to develop within each intermetallic layer before shear failure. With permanent increase of the crack number in the intermetallic layers the magnesium layers gradually undergone the total external load. As a result the plastic flow in the magnesium layers was restricted to the small regions between opposite cracks in the neighboring intermetallic layers. This fracture mechanism is consistent with the damage evolution model worked out by Li et al. [20] for metal-intermetallic laminated composites. The damage mechanisms of dissimilar laminated composites are alike because various intermetallics formed from the different constituent metals behave very similarly. They are ordinally brittle at room temperature due to the limited mobility of dislocations, have an insufficient number of slip or twinning systems, and very low surface energy resulting in little or no plastic deformation at crack tips. The contribution of sub-critical cracks was in particular discussed by Wu et al. [25], and they stated that the larger the crack density, the wider the crack distribution. The authors claimed that the mechanical performance is better, as long as the sub-critical crack is still in its "stable" domain and does not develop into unstably critical major crack causing catastrophic fracture. The compressive strength of the magnesium-intermetallic composites was about 17% higher in parallel than in perpendicular direction. The principal feature during loading in parallel direction was appearing of longitudinal cracks propagating along the layers of intermetallics (Figure 6b). When the intermetallic layers cracked in parallel direction, the Mg layers took the additional loading and had the tendency to buckle. This type of behavior was previously noticed when analyzing other types of metal-intermetallic phase composites [14,15,17,20]. The compressive strength of the magnesium-intermetallic composites was 88% higher in parallel and 60% higher in perpendicular direction than the compressive strength of pure magnesium.
The three-point bending tests allowed characterizing the damage evolution in two loading directions (Figure 7). The flexural strength of investigated laminated composites and magnesium is listed in Table 1. When the load direction was parallel to the layers, the load grew continuously up to the peak load, at which point a crack initiated at the surface. The crack grew gradually in the through-thickness direction and finally traveled across the specimens (Figure 7a). The failure occurred by cleavage mode showing limited plastic deformation and any delamination of layers was not observed. The similar failure mechanism for metal-intermetallic composites was reported previously [15,17].
When the load perpendicular to the layers was applied, the failure occurred in a different way. The composites failed by transverse cracking of the intermetallic layers and gradual cracking of the Mg layers. In this case the main crack did not travel across the specimen. It was arrested and deflected by intermetallic layers causing delamination (Figure 7b). Delamination made the main crack propagation difficult in the next layer, which had to deform plastically until a new dominant crack was nucleated. Similar crack progression in ductile/brittle laminates was previously reported by Cao et al. [21]. The flexural strength of the magnesium-intermetallic composites was about 40% higher in perpendicular than in parallel direction. Except that the flexural strength of the composites was 126% higher in perpendicular and 60% higher in parallel direction than the flexural strength of pure magnesium.
The Charpy-impact tests also allowed characterizing the damage evolution in two loading directions (Figure 8). The results of impact toughness measurements are listed in Table 1.
When the load direction was parallel to the layers, the failure occurred by cleavage mode shoving limited plastic deformation (Figure 8a). It was evident that there was solely one main crack that grew gradually in the through-thickness direction and travelled across the sample. The impact toughness of the magnesium-intermetallic composites was about 3 times smaller in parallel than in perpendicular direction. When the load direction was perpendicular to the layers, the composites displayed superior impact toughness that was 55% higher than for pure magnesium. In this case the main crack did not travel across the specimen, but was arrested and deflected by the subsequent layers. Charpy-impact tests confirmed the discussion regarding the bending test. The Charpy-tested samples showed the same fracture behavior as the bend-tested specimens, which indicated that the same mechanisms operated at both high impact rate and low bending-test rate.
From obtained results and discussions, the following conclusions can be drawn:
(1) The compressive strength of the magnesium-intermetallic composites is 88% higher in parallel and 60% higher in perpendicular direction than the compressive strength of magnesium. The specimens compressed in the parallel direction fail by cracking along the layers of intermetallics and buckling of magnesium layers. The specimens compressed in the perpendicular direction fail by transverse cracking in the intermetallic layers and fallowing catastrophic cracking inclined about 45° to the interface both intermetallic layers and magnesium layers.
(2) The flexural strength of the composites is 126% higher in perpendicular and 60% higher in parallel direction than the compressive strength of magnesium. When the load parallel to the layers is applied, the failure occurs by cleavage mode showing limited plastic deformation. When the load perpendicular to the layers is applied, the failure occurs by transverse cracking of the intermetallic layers and gradual cracking of the Mg layers.
(3) When the load direction is perpendicular to the layers, the composites displays superior impact toughness that is 55% higher than for magnesium.
The author declare no conflict of interests.
[1] |
Friedrich H, Schumann S (2001) Research for a "new age of magnesium" in the automotive industry. J Mater Process Tech 117: 276–281. https://doi.org/10.1016/S0924-0136(01)00780-4 doi: 10.1016/S0924-0136(01)00780-4
![]() |
[2] |
Mordike BL, Ebert T (2001) Magnesium: properties-applications-potential. Mater Sci Eng A-Struct 302: 37–45. https://doi.org/10.1016/S0921-5093(00)01351-4 doi: 10.1016/S0921-5093(00)01351-4
![]() |
[3] |
Luo AA (2013) Magnesium casting technology for structural applications. J Magnes Alloys 1: 2–22. https://doi.org/10.1016/j.jma.2013.02.002 doi: 10.1016/j.jma.2013.02.002
![]() |
[4] |
Vahid A, Hodgson P, Li Y (2017) Reinforced magnesium composites by metallic particles for biomedical applications. Mater Sci Eng A-Struct 685: 349–357. https://doi.org/10.1016/j.msea.2017.01.017 doi: 10.1016/j.msea.2017.01.017
![]() |
[5] |
Nie KB, Wang XJ, Deng KK, et al. (2021) Magnesium matrix composite reinforced by nanoparticles—A review. J Magnes Alloys 9: 57–77. https://doi.org/10.1016/j.jma.2020.08.018 doi: 10.1016/j.jma.2020.08.018
![]() |
[6] |
Matin A, Fereshteh Saniee F, Reza Abedi H (2015) Microstructure and mechanical properties of Mg/SiC and AZ80/SiC nano-composites fabricated through stir casting method. Mater Sci Eng A-Struct 625: 81–88. https://doi.org/10.1016/j.msea.2014.11.050 doi: 10.1016/j.msea.2014.11.050
![]() |
[7] |
Cortes P, Cantwell WJ (2004) Fracture properties of a fiber-metal laminates based on magnesium alloy. J Mater Sci 39: 1081–1083. https://doi.org/10.1023/B:JMSC.0000012949.94672.77 doi: 10.1023/B:JMSC.0000012949.94672.77
![]() |
[8] |
Qi L, Ju L, Zhou J, et al. (2017) Tensile and fatigue behavior of carbon fiber reinforced magnesium composite fabricated by liquid-solid extrusion following vacuum pressure infiltration. J Alloy Compd 721: 55–63. https://doi.org/10.1016/j.jallcom.2017.05.312 doi: 10.1016/j.jallcom.2017.05.312
![]() |
[9] |
Zhang X, Fang L, Xiong B, et al. (2015) Microstructure and tensile properties of Mg (AM60)/Al2O3 metal matrix composites with varying volume fractions of fiber reinforcement. J Mater Eng Perform 24: 4601–4611. https://doi.org/10.1007/s11665-015-1772-y doi: 10.1007/s11665-015-1772-y
![]() |
[10] |
Dziadoń A, Mola R, Błaż L (2011) Formation of layered Mg/eutectic composite using diffusional process at the Mg-Al interface. Arch Metall Mater 56: 677–684. https://doi.org/10.2478/v10172-011-0074-0 doi: 10.2478/v10172-011-0074-0
![]() |
[11] |
Takeichi N, Tanaka K, Tanaka H, et al. (2007) Hydrogen storage properties of Mg/Cu and Mg/Pd laminate composites and metallographic structure. J Alloy Compd 446–447: 543–548. https://doi.org/10.1016/j.jallcom.2007.04.220 doi: 10.1016/j.jallcom.2007.04.220
![]() |
[12] |
Wang P, Chen Z, Huang H, et al. (2021) Fabrication of Ti/Al/Mg laminated composites by hot roll bonding and their microstructures and mechanical properties. Chinese J Aeronaut 34: 192–201. https://doi.org/10.1016/j.cja.2020.08.044 doi: 10.1016/j.cja.2020.08.044
![]() |
[13] | Konieczny M (2022) Microstructure evolution of laminated magnesium-intermetallics composite, Proceedings of the conference METAL 2022—31st International Conference on Metallurgy and Materials, 67. |
[14] |
Wadsworth J, Lesuer DR (2000) Ancient and modern laminated composites—from the Great Pyramid of Gizeh to Y2K. Mater Charact 45: 289–313. https://doi.org/10.1016/S1044-5803(00)00077-2 doi: 10.1016/S1044-5803(00)00077-2
![]() |
[15] |
Vecchio KS (2005) Synthetic multifunctional metallic-intermetallic laminate composites. JOM 57: 25–31. https://doi.org/10.1007/s11837-005-0229-4 doi: 10.1007/s11837-005-0178-y
![]() |
[16] | Dziadoń A, Konieczny M (2004) Structural transformations at the Cu-Ti interface during synthesis of copper-intermetallics layered composite. Kov Mater 42: 42–50. |
[17] | Konieczny M, Dziadoń A (2007) Mechanical behaviour of multilayer metal-intermetallic laminate composite synthesised by reactive sintering of Cu/Ti foils. Arch Metall Mater 52: 555–562. |
[18] | Konieczny M, Mola R (2008) Fabrication, microstructure and properties of laminated iron-intermetallic composites. Steel Res Int 79: 499–505. |
[19] |
Wang H, Han J, Du S, et al. (2007) Effects of Ni foil thickness on the microstructure and tensile properties of reaction synthesized multilayer composites. Mater Sci Eng A-Struct 445–446: 517–525. https://doi.org/10.1016/j.msea.2006.09.082 doi: 10.1016/j.msea.2006.09.082
![]() |
[20] |
Li T, Olevsky EA, Meyers MA (2008) The development of residual stresses in Ti6Al4V-Al3Ti metal-intermetallic (MIL) composites. Mater Sci Eng A-Struct 473: 49–57. https://doi.org/10.1016/j.msea.2007.03.069 doi: 10.1016/j.msea.2007.03.069
![]() |
[21] |
Cao HC, Evans AG (1991) On crack extension in ductile/brittle laminates. Acta Metal Mater 39: 2997–3005. https://doi.org/10.1016/0956-7151(91)90032-V doi: 10.1016/0956-7151(91)90032-V
![]() |
[22] |
Bruno D, Greco F, Lonetti P (2005) Computation of energy release rate and mode separation in delaminated composite plates by using plate and interface variables. Mech Adv Mater Struc 12: 285–304. https://doi.org/10.1080/15376490590953563 doi: 10.1080/15376490590953563
![]() |
[23] |
Shi Y, Swait T, Soutis C (2012) Modelling damage evolution in composite laminates subjected to low velocity impact. Compos Struct 94: 2902–2913. https://doi.org/10.1016/j.compstruct.2012.03.039 doi: 10.1016/j.compstruct.2012.03.039
![]() |
[24] | Predel B (1994) Cu-Mg (Copper-Magnesium), In: Madelung O, Phase Equilibria, Crystallographic and Thermodynamic Data of Binary Alloys, Landolt-Börnstein-Group Ⅳ Physical Chemistry. https://doi.org/10.1007/b47753 |
[25] |
Wu H, Huang M, Li X, et al. (2021) Temperature-dependent reversed fracture behavior of multilayered TiBw/Ti–Ti(Al) composites. Int J Plast 141: 102998. https://doi.org/10.1016/j.ijplas.2021.102998 doi: 10.1016/j.ijplas.2021.102998
![]() |
1. | Sung-Jae Joo, JeongIn Jang, Ji-Hee Son, JongHo Park, Kim Kim, Bok-Ki Min, A Simple Solid-State Direct Bonding Process for Fabrication of Ohmic Contacts on n-type Mg3Sb2-xBix-based Thermoelectric Materials, 2025, 63, 1738-8228, 60, 10.3365/KJMM.2025.63.1.60 |
Investigated material | Load direction | Compressive strength (MPa) | Flexural strength (MPa) | Impact toughness (J/cm2) |
Laminated magnesium-intermetallic composite | parallel to layers | 335 | 188 | 5 |
perpendicular to layers | 286 | 265 | 14 | |
Magnesium | - | 178 | 117 | 9 |