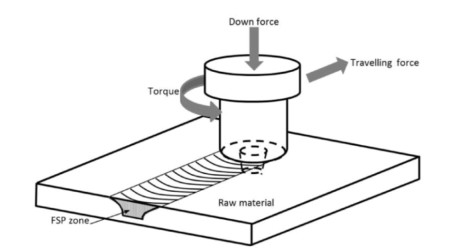
Citation: P. Sagar, A. Handa. A comprehensive review of recent progress in fabrication of magnesium base composites by friction stir processing technique—A review[J]. AIMS Materials Science, 2020, 7(5): 684-704. doi: 10.3934/matersci.2020.5.684
[1] | Carlos A. Sánchez, Yamile Cardona-Maya, Andrés D. Morales, Juan S. Rudas, Cesar A. Isaza . Development and evaluation of polyvinyl alcohol films reinforced with carbon nanotubes and alumina for manufacturing hybrid metal matrix composites by the sandwich technique. AIMS Materials Science, 2021, 8(2): 149-165. doi: 10.3934/matersci.2021011 |
[2] | Mateo Duarte, Andrés Benítez, Katiuska Gómez, Benjamín Zuluaga D, Juan Meza, Yamile Cardona-Maya, Juan S. Rudas, César Isaza . Nanomechanical characterization of a metal matrix composite reinforced with carbon nanotubes. AIMS Materials Science, 2020, 7(1): 33-45. doi: 10.3934/matersci.2020.1.33 |
[3] | Afsaneh Dorri Moghadam, J.B. Ferguson, Benjamin F. Schultz, Pradeep K. Rohatgi . In-situ reactions in hybrid aluminum alloy composites during incorporating silica sand in aluminum alloy melts. AIMS Materials Science, 2016, 3(3): 954-964. doi: 10.3934/matersci.2016.3.954 |
[4] | Shashi Bahl, Tarunpreet Singh, Virinder Kumar, Shankar Sehgal, Ashok Kumar Bagha . A systematic review on recent progress in advanced joining techniques of the lightweight materials. AIMS Materials Science, 2021, 8(1): 62-81. doi: 10.3934/matersci.2021005 |
[5] | Abdulkader A. Annaz, Saif S. Irhayyim, Mohanad L. Hamada, Hashim Sh. Hammood . Comparative study of mechanical performance between Al–Graphite and Cu–Graphite self-lubricating composites reinforced by nano-Ag particles. AIMS Materials Science, 2020, 7(5): 534-551. doi: 10.3934/matersci.2020.5.534 |
[6] | Marek Konieczny . Mechanical properties and failure analysis of laminated magnesium-intermetallic composites. AIMS Materials Science, 2022, 9(4): 572-583. doi: 10.3934/matersci.2022034 |
[7] | Reginald Umunakwe, Ifeoma Janefrances Umunakwe, Uzoma Samuel Nwigwe, Wilson Uzochukwu Eze, Akinlabi Oyetunji . Review on properties of hybrid aluminum–ceramics/fly ash composites. AIMS Materials Science, 2020, 7(6): 859-870. doi: 10.3934/matersci.2020.6.859 |
[8] | Robiul Islam Rubel, Md. Hasan Ali, Md. Abu Jafor, Md. Mahmodul Alam . Carbon nanotubes agglomeration in reinforced composites: A review. AIMS Materials Science, 2019, 6(5): 756-780. doi: 10.3934/matersci.2019.5.756 |
[9] | Marek Konieczny . Mechanical properties and wear characterization of Al-Mg composites synthesized at different temperatures. AIMS Materials Science, 2024, 11(2): 309-322. doi: 10.3934/matersci.2024017 |
[10] | Md. Hasan Ali, Robiul Islam Rubel . A comparative review of Mg/CNTs and Al/CNTs composite to explore the prospect of bimetallic Mg-Al/CNTs composites. AIMS Materials Science, 2020, 7(3): 217-243. doi: 10.3934/matersci.2020.3.217 |
Metal matrix composite (MMC), widely known as the cluster of smartly developed engineered materials, synthesized by adding secondary phase reinforced micro, macro or nano particulates with parent materials of different chemical composition [1]. Continuous phase of metal is called matrix, and depending upon the chemical composition of matrix, composites are classified as metal matrix composites (MMCs), ceramic matrix composite (CMC) and polymer matrix composite (PMC) [2]. MMC’s recently are drawing interests of the researchers for not only they demonstrate firm bond with reinforced particles also develops no chemical alteration in terms of composition but also exhibits superior properties. MMC’s clearly proven themselves as a promising candidate with their wide application in various fields [3,4]. Copper, magnesium, aluminum and titanium are commonly used matrix materials and TiC, MWCNTs, SiO2, B4C and Al2O3 few types of reinforced particles. Various manufacturing techniques like diffusion bonding [5], powder metallurgy, in situ fabrication [9], spray deposition [10], stir and squeeze casting [11,12,13,14] and vapor deposition been adopted by researchers to fabricate bulk MMCs [15,16]. All these manufacturing process of developing composites transform material from solid to liquid phase. On the flip side, techniques which do not have phase change process like solid state processing comparatively shows many merits over conventional phase change techniques. Friction stir processing (FSP) is a newly developed technique based on the principle of friction stir welding (FSW) [17]. And the principles along with recent progresses on friction stir welding and processing reported in [18]. Stirring action of FSP been successfully used to disperse secondary phase particles in the parent metal and producing next generation materials as MMCs [19]. Till now FSP is widely used to fabricate aluminum based composites [20,21,22,23,24,25,26,27,28]. Presently the world is more concerned about ecofriendly low-emission transportation vehicles with light-weight and maximum-performance. Magnesium been adopted by researchers and scientists over aluminum not for having density two-thirds that of aluminum also for its high strength-to-weight ratio [29]. Magnesium itself or its alloy doesn’t meet the today need. For full filling this purpose few percentage of particulates need to be added in magnesium or its alloys. Addition of these particulates not only increases the microstructure of the composite but also enhanced it mechanical properties. Recently, Sunil et al. [30] summarized all work related to magnesium based composites. This paper present extended study of literature survey and review all recent development in the area of magnesium based composites fabrication by FSP. The demanding situations and future bearing of FSP are summed up.
FSP in its least difficult structure comprises of a rotating tool that is non-consumable, which is dove into the work piece and afterward moved toward intrigue. The schematic outline of FSP is appeared in Figure 1.
FSP serves two essential capacities: (a) development of thermal energy thus deforming work piece material (b) mixing of secondary phase particles and form substrate. Intense rubbing of tool with material develop high frictional energy which results in producing enormous thermal energy. This thermal energy converts the metal into semi solid phase and makes it softer, while the turning of pin mixes and makes it flow around the pin. It then settle the soft metal depression at the back of the rotating tool. The material that flows around the tool is exposed to serious plastic deformation and heating, which prompts significant dynamic recrystallization thus refinement of microstructure in the stir zone (SZ) initiated [31].
FSP machine process variables are classified into five categories. All these are the significant components that direct the successful achievement of the composite manufacture by FSP [32,33,34,35,36,37,38,39,40]. Variables are further divided into other various parameters. Figure 2 illustrates a schematic diagram of classification of the variables involved in the manufacture of the composite as well detalied by Rathee et al. [41].
Prior investigations reveal that formation of composite materials was mainly via ceramic slurry layer for FSP process. Now a day’s most common approaches for doping secondary phase particles into parent metal for composite manufacturing through FSP are shown schematically in Figure 3. Varity of secondary phase particles may considered, as reported by literature, i.e., TiC, SiC, MWCNT, Al2O3, B4C and SiO2, etc.
● Hole drilling approach: Holes filling is a common strategy where required blind holes usually in straight/zig-zag pattern bored on top of the work piece and loaded up with reinforce particles. However, before final experimentation a pin less FSP tool is employed after loading of reinforced particles to avoid scattering of these particles.
● Groove filling approach: Groove filling is another common strategy in which a section is created on work piece and loaded up with reinforced particles. However, before final experimentation a pin less FSP tool is employed after loading of reinforced particles to avoid scattering of these particles.
● Sandwich approach: In this approach a layer of reinforced particles is prepared between parent material plates like a sandwich. High Thermal energy generated by tool breaks the particles and help in fabricating composite. However, uniform distribution may require increased number of passes.
Tool geometry is a vital processing parameter which generates heat and guide material flow. The shoulder diameter affect heat generation at SZ and it is usually taken as, D/d = 3 (where D is shoulder diameter, d is pin diameter) [43]. Common types of tools used in FSP of magnesium based alloys are presented in Figure 4.
Most common magnesium alloys comprised of aluminum, zinc, thorium and uncommon earth. Using the ASTM alphanumeric designation system encourages grouping magnesium alloys by principal alloy composition like Mg–Al–Mn (AM), Mg–Al–Zn–Mn (AZ), Mg–Zr (K), Mg–Zn–Zr (ZK) with rare earth (ZE), Mg–Y–rare earth metal–Zr (WE). Initial two letters demonstrate the chief code for major alloying components followed by their concentration respectively. Last alphabet suggests alloy modification [45]. Studies considering major magnesium alloy for composite fabrication via FSP, as reported by the literature, are presented here.
Asadi et al. [46] fabricate AZ91/SiC magnesium base composite considering square tool pin profile with three tool penetration depth (PD) 0.1, 0.2 and 0.3 mm and a tool tilt angle of 3°. They observed complete cracked processing zone for PD 0.1 mm, hole and tunneling cavity for PD 0.2 mm and sound surface quality for PD 0.3. They also studied the effect of tool rotational and tool transverse speed on grain size and micro hardness by considering groove filling approach for fabricating magnesium base AZ91 alloy with 5 µm SiC particles. They consider two 900 and 1400 rpm tool rotational speed and five 12.5, 25, 40, 50 and 63 mm/min tool transverse speeds. Finding of their research work suggests that best result for grain size and micro hardness were achieved at tool rotational speed of 900 rpm with transverse speed of 63 mm/min, i.e., 7.16 µm and 94 Hv. Asadi et al. [47] further extended their research for AZ91/SiC composite and suggests grain size increases with increase in rotational speed and lowers the micro hardness. Also it was noted that increasing transverse speed reduced the grain size, while the micro hardness increases. It was also added that changing the tool rotation speed resulting in fine grains and uniform distribution of particles. Faraji et al. [48] synthesized AZ91/Al2O3 composite by using friction stir processing, Their work included three different size nano particles ranging from nanometer to micrometer scale, i.e., 3000,300 and 30 nm and two different tool geometries along with varying number of passes and also studies their effect on performance measures like grain size, cluster size, micro structure and mechanical properties. Findings of their work suggests that grain size in triangular tool is less than square tool but follows opposite trend in case of hardness. Finally the conclusion drawn from their work suggests that decrease in size of nanoparticle increases hardness of the composite. Khayyamin et al. [49] studied the effect of process parameters on micro structural characteristics of AZ91/SiO2 composite fabricated by FSP. They fix tool rotation speed to 1250 rpm, tilt angle to 3° and number of passes to 4 passes with varying transverse speed to 20, 40 and 63 mm/min. They also examine metallurgical and mechanical properties by Optical Microscopy (OM), Scanning Electron Microscopy (SEM) and Vickers hardness tester. All optical microscopy and scanning electron microscopy tests were conducted on composites having all different passes and different transverse speed. Outline of the work concluded that grain size decreases and strength and hardness increase with increase in transverse speed. Increase number of pass increase hardness and reduce grain size. Faraji et al. [50] consider tool geometry of two types square and circular to examine the influence of process parameters on AZ91 with and without Al2O3 nano particles. It can be understood from the work that at tool rotation speed 900 rpm and transverse speed of 80 mm/min for square tool provides the best result with grain size 6 µm and microhardness 103 Hv as compared to 7.27 µm and 98.52 Hv without particles. Ahmadkhaniha et al. [51] analyzed wear resistance on AZ91/Al2O3 as produced by FSP adopting groove filling approach with circular tool. They further consider different tool rotation speed, transverse speed and a fixed tool tilt angle of 3° to investigate mechanical and metallurgical properties. Finally outcome of the study suggests that tool rotation speed of 800 rpm and transverse speed 40 mm/min gives optimum results for grain refinement and wear behavior. Dadashpour et al. [52] introduced 10–15 nm SiO2 particulates to study the fracture behavior AZ91C composite fabricated by FSP. H13 tool material was considered along with square pin geometry with a fixed tool rotational speed of 1250 rpm and feed rate 40 mm/min. Extreme refined grain from starting size of 140 to 4 µm was observed along with the hardness of 130 Hv and ultimate tensile stress of 239.6 MP for three FSP passes. Chen [53] mixes SiC particles and prepared a layer of surface composite on thixoformed AZ91 using FSP. Wear behavior of thixoformed AZ91/SiC was compared with thixoformed AZ91 alloy without composite surface. The authors concluded that found that increasing number of passes can minimize the agglomeration and maximize the SiC particles distribution. Further they reported reduced coefficient of friction and enhanced wear resistance of surface composite layer when compared with parent alloy. Very recently, Singh [54] developed AZ91/B4C nano composite using drill hole approach with cylindrical tool rotating with 900 rpm and having feed of 45 mm/min. Three different sizes nano particles were considered for examine microhardness and wear behavior. Finally study concluded that average hardness, wear resistance increases and wear rate decreases as the reinforce particle size increases.
Morisada et al. [55] fabricate AZ31 magnesium alloy with SiC via using friction stir processing. They used SiC powder of mean diameter 1 µm into a groove of 1 × 2 mm of a 6 mm thick plate. A tool of columnar shape of material SKD61 with diameter 12 mm along with a probe of diameter 4 mm and length of 1.8 mm was used, also they fix the value of parameters like tool rotation 1500 rpm, tool tilt angle 3° and travel speed of range 25–200 mm/min for processing. OM, SEM and Transmission Electron Microscopy (TEM) tests were conducted to study the micro structural properties of the composite. Findings of the test reported a fine grain size, i.e., 6 µm in the developed AZ31/SiC as compared to the mean grain size, i.e., 79.1, 12.9 of as-received AZ31 and FSPed AZ31 respectively for the travel speed of 50 mm/min. Further they reported that as travel speed increase grain size of the composite decreases. Micro-vickers hardness tester with a load of 200 g was used to measure micro hardness and it shows a maximum value of 69.3 Hv for FSPed AZ31 with SiC particles and 48.1 Hv and 60.0 Hv for as-received AZ31 and FSPed AZ31 respectively. Morisada et al. [56] studied the influence of addition of multi walled carbon nano tubes on grain size and hardness of AZ31 magnesium composite prepared through friction stir processing. AZ31 rolled plate of 6 mm thickness with a groove of 1 × 2 mm, filled with multi walled carbon nanotubes of outer diameter 20–50 nm and of 250 nm length was used. A tool of columnar shape of material SKD61 with diameter 12 mm along with a probe of diameter 4 mm and length of 1.8 mm was used for fabrication. Good dispersion of nanoparticles was observed at 25 mm/min transverse speed and 1500 rpm tool rotation speed respectively. Hardness of 78 Hv was observed for AZ31/MWCNT as compared with hardness of 41 Hv of as received AZ31. Azizieh et al. [57] examine the effect of process parameters like tool profile, rotational speed and number of passes on micro structural and mechanical properties of FSPed fabricated AZ31/Al2O3.They used three kinds of Al2O3 particles with mean diameters of 35,350 and 1000 nm respectively. Rectangular shape of 60 × 100 × 10 mm as cast AZ31 was used along with a groove of 1.2 mm width and 5 mm depth with a grain size of 70 µm. Varying geometry of tools, i.e., tool with a columnar probe without threads, a tool with a columnar probe with threads and a tool with columnar probe with threads and three flutes heat treated till 53HRC hardness along a fixed tool transverse speed of 45 mm/min, tool rotational speed of 800, 1000, 1200 rpm and tool tilt angle of 2° and FSP 2–4 times passes was adopted. OM, SEM and micro hardness tests was conducted to examine the etched sample. Finally cavity formation was noticed when non-threaded tool was used also they reported that use of threaded pin leads to good grain size along with uniform distribution of nano particles. In case of threaded pin with flute they observed low homogeneity along with tunneling effect. Azizieh et al. [58] synthesized AZ31/Al2O3 composite by using friction stir processing. They considered parameters like rotational speed and number of passes to find out their effect on particle distribution, grain refinement, hardness and temperature changes in the magnesium metal composite. A constant travel speed of 45 mm/min, tool rotational speed of 800, 1000, 1200 rpm, tool tilt angle of 2° and FSP 2–4 times passes was adopted. Temperature in the stir zone was measured by the K-type thermocouple immersed in the stir region. Findings suggest that with increase in tool rotational speed average grain size, peak temperature and particle distribution increases. Also if number of passes increases nanoparticle agglomeration decreases and hardness increases which is good. Finally work concludes that at 800 rpm hardness is higher as compared to 1000 and 1200 rpm. Srinivasan et al. [59] developed AZ31B/Al2O3 magnesium metal matrix nanocomposites through rotational friction welding. Authors, further examine the influence on mechanical and microstructure for the various controllable parameters like upsetting and friction time, upsetting and friction pressure. Cumulative effect of machine parameters and thermo mechanical stresses results in typical grain refinement in the SZ. Authors reported increase in friction time decrease joint efficiency. Microhardness variation is attributed due to distribution of heat produces by friction pressure and time. Chang et al. [60] synthesized metal matrix magnesium based composite AZ31/nano-ZrO2 and nano-SiO2 via FSP and examined both the microstructure and mechanical properties of. A tool with cylindrical probe with shoulder diameter 18 mm and pin length and diameter of 6 mm with 2° tilt angle along with pin rotation of 800 rpm and advancing speed of 45 min/min was used. Two grooves each 6 mm in depth and 1.25 mm in width were cut, in which 10–20 vol% of nano-sized ZrO2 and 5–10 vol% nano-sized SiO2 particles was filled. Mechanical properties like vickers hardness was checked using a 200 gf load for 10 s along with optical microscopy, scanning and energy dispersive spectrometer was conducted to examine mechanical and metallurgical properties. Average grain size of composite produced 4P FSP resulted to be refined upto to 2–4 µm. Balakrishnan et al. [61] used magnesium alloy AZ31 with particulates like TiC to fabricate a magnesium matrix composite. They operate or execute or demonstrate the FSP by taking fixed tool rotational speed, transverse speed, and axial force on a 6 mm AZ31 plate by single pass. They engraved four different width (0, 0.4, 0.8, 1.2) and of equal depth 4.5 mm in the plate to introduced varying different fraction of the given (0, 6, 12, 18). Macrostructure and microstructure was studied by digital optical scanner and scanning electron microscope and it suggested TiC were properly distributed. Jiang et al. [62] dispersed nano SiO2 reinforced by FSP into AZ31 Mg alloy. The main result reflects uniform grain refinement up to less than 1 µm and increase in hardness up to 1.83 times higher than that of the as-received AZ31 can be achieved. Sharma et al. [63] fabricated a novel hybrid nanocomposite AZ31/MWCNT–Graphene using multi-pass FSP with constant other parameters. Uniform, refined and more localized grains of average size of 4.0 μm with lesser tensile twin fraction were reported for hybrid nano composites as shown in Figure 5.
Also uniform dispersion of hybridized reinforce particles leads to significant enhancement of elastic modulus, tensile failure strains along with the improved mechanical properties like microhardness, i.e., 90.6 Hv and superior ultimate tensile strength as 49.23% as shown in Figure 6 with yield strength as 32.31%.
Huang et al. [64] executes the process of synthesized AZ31/SiC composite with a special FSP tool unlike other FSP tool. In this novel tool reinforce particles introduced via a hole prepared within this new direct friction stir process tool (DFSP). More than four times lesser grain was formed as compared to as cast magnesium alloy grain size of 16.57 µm. Authors further suggested groove or hole filling step can completely be eliminated with new tool also better hardness can be achieved as compared to conventional FSP. Soltani et al. [65] synthesized AZ31B/CNT surface composite using FSP. For this research work author provides a suitable combination of transverse speed of 24 mm/min and rotational speed of 870 rpm for significant increase in hardness of 60 vickers and reduced grain size of less than 5 µm. Navazani and Dehghani [66] introduced 5 µm TiC particles for the fabrication of AZ31 magnesium base composite. Microstructural and hardness of the produced composite was examined. Authors suggested that three vital factors are responsible for dislocation of grain in composite i.e. dissimilar deformation behavior between particle and matrix, grain boundaries and thermal expansion. Finally, work suggests that defect free zone can be achieved at 1250 rpm and 50 mm/min with declined grain size. Sunil et al. [67] loaded nanohydroxypatite reinforced particles into the groove of base AZ31 magnesium alloy in order to produce composite material. Authors mainly investigate the composite for biomedical applications and degradation of material. Wettabilty, cytotoxicity and vitro bioactivity in super saturated simulated field is been checked. Grain refinement upto 2 µm been the main reason of enhanced surface energy. Further authors concluded that dissolution of iron at FSP zone was within tolerance limit and hence its effect on corrosion is negligible. Newly, Sharma et al. [68] examined the influence of tool rotation speeds on mechanical and microstructure properties of fabricated a novel hybrid nanocomposite AZ31/MWCNT–Graphene using FSP. Optimum ratio of 1.6 and 0.3 vol% of MWCNT and grapheme was used. Author obtained various values of microhardness at different tool rotation speeds and presented them into a graph form as shown in Figure 7.
Das et al. [69] prepared a metal matrix composite WE43/B4C/6 vol% via friction stir processing. For the experimentation work they used 30 × 5 × 1.6 cm3 of WE43 plate, B4C of 6 µm along with stepped tool. They drilled a set of holes into the plate for the friction processing and observe the microstructural and mechanical properties through scanning electron microscopy and tensile, hardness tests. Finally they analyze reduction in grain size and increase in micro hardness for four passes as compare to single pass. Further they concluded that post treatment of composite at 210 ºС for 48 h not only increase yield strength from 189–281 but also increase the ultimate tensile strength and elastic modulus with reduction in ductility and elongation to failure. Recently, Vedabouriswaran and Aravindan [70] introduced boron carbide (B4C), MWCNT and a mixture of ZrO2 + Al2O3 secondary phase particulates for production of magnesium rare earth alloy—RZ 5 based composite of by single pass FSP. Pinning effect cause by the reinforce particles produces refined grains of range 0.8 to 1.87 μm. Microhardness from 125 to 403 Hv was reached with increased ultimate tensile strength with range of 250–320 MPa.
Valle et al. [71] like Chang et al. [60] used backing plates as of cooper to speed up heat transfer rate between tool and work piece. They studied the effect of FSP on AZ61 via examining mechanical and micro structural properties. Grain refinement was achieved with maximum size 45 to 1.8 µm. Further authors reported that the surface created during FSP favors basal slip during the tensile test, leading to increase of ductility, a decrease in yield stress and a decrease in strain rate sensitivity in comparison with rolled AZ61 alloy. Lee et al. [72] created AZ61 based nanocomposite by mixing 5–10 vol% nanosized SiO2 via FSP. Fix parameters with tool rotation 800 rpm and tool transverse 45 mm/min was employed. A back plate for cooling purpose for the whole procedure was deployed beneath. Succeeded FSP, authors declared that as number of passes increases nano-SiO2 particles turns into a cluster of size going from 0.1 to 3 µm and the degree of grouping decreases. TEM contemplates that nano-SiO2 particles stayed as shapeless and opposes change to crystalline stage during whole procedure. Du and Wu [73] processed magnesium base AZ61 alloy with rapid heat sink via FSP and achieved fine-microstructure at the processed zone with enhanced mechanical properties. Authors, observed average grain size less than 300 nm with mean micro hardness of 120−130 Hv, two times higher than that of AZ61 substrate. They further declares that one pass FSP under a high cooling rate may produces ultra-fine structure in AZ61 alloy with superior mechanical properties.
Literature survey concludes that various magnesium based composites were developed in past decade. All these composite materials shows improved microstrurtural and mechanical properties. Tribological performance, however, is by far the most commonly encountered industrial problem where the material is mainly influenced by speed, environmental conditions, and workload. Wear is a gradual and progressive material loss that is continuously subjected to rubbing action. Wear resistance of the composite metal matrix depends primarily on different microstructural features, such as particle size, volume fraction, reinforcement material distribution, and shape.
Tribological performance of magnesium based composites is an other parameter which have been succesfully studied and improved by the various researchers. Table 1 provides the brief summary of the work carried out so far pretaning to tribological performance of magnesuim based composites.
Composite | Tool geometry | Grain size improvement | Machine parameters | Wear test specifications | Significant outcome | References |
ZM21/SiC/B4C | Straight cylindrical | 40 µm refined up to 20 µm | 1200 rpm, 50 mm/min | Pin on disc, load 0.5 kg, sliding speed 640 rpm for 6 km | Wear rate of composite decreases seventy six times to the base metal | Reddy et al. [74] |
AZ91/Al2O3/SiC | Straight cylindrical | More refined grains as number of passes increases | 730–1800 rpm, 14–80 mm/min with 1–4 passes | Tri pin on disc, load 50 N, sliding speed 1 mm/s for 500 m | Wear rate decreases as number of pass increases AZ91/ AZ91/Al2O3 & AZ91/SiC gives almost same wear rate | Abbasi et al. [75] |
AZ91/TiC | Straight cylindrical | More refined grains | 900 rpm, 40 mm/min with PD = 0.3 mm | Pin on disc, load 5–10 N, sliding speed 1 m/s for 2000 m | Wear rate of composite decreases half to the base metal | Singh et al. [76] |
AZ31/TiC | Straight cylindrical | More refined grains | 800 rpm, 40 mm/min | Pin on disc, load 5–20 N, sliding speed 1 m/s for 1.5 km | At 20 N higher wear resistance was noticed | H. S. Arora et al. [77] |
AE42 as cast and FSPed AE42 | Straight cylindrical | 40% reduction in grain size and reached upto 1.5 µm | 700 rpm, 60 mm/min | Pin on disc, load 5–20 N, sliding speed 0.3–3 m/s for 2500 m | Higher co-efficient of friction attended at low sliding velocities | Arora et al. [78] |
As cast Mg/SiC | Threaded cyllindrical | Grain size reduced from 170 to 3 µm | 1300 rpm, 50 mm/min | Pin on disc, load 1–5 Kg, sliding speed 1 m/s for 600 m | 20% and 47% wear loss was noticed at 1 and 5 Kg | Ram et al. [79] |
AZ31/Al2O3 | Threaded cyllindrical | With development of refined grains hardness increases from 50 to 90 Hv | 800, 1000, 1200 and 1400 rpm, 45 mm/min and 2° tilt angle | Pin on disc, load 10, 50 and 90 N, sliding velocity 0.12m/s for 600 m | Wear rate at 1000 and 1200 rpm is higher as compared to 800 rpm | Azizieh et al. [80] |
AZ31/Fly ash | Straight cylindrical | Upto 4 µm grain size achevied | 1200 rpm and 40mm/min | Pin on disc, load 20 N, sliding velocity 1.0 m/s for 3000 m | FSP exhibhits 33% lower wear rate as compared to stir cast | Dinaharan et al. [81] |
AZ91/Al2O3 | Circular and square tool | Average grain size 5–10 µm was obtained | 900–1200 rpm, 40–80 mm/min with 3° tilt angle | Pin on disc, load 50 N, sliding velocity 1.0 mm/min for 500 m | Wear rate decreases more than three times to the base metal | Faraji and Asadi [82] |
AZ31/MWCNT/ Al2O3 | Cone shape | Much small size grains with microhardness 1.4 times higher than those of AZ31 | 1050 rpm, 33.4 mm/min | Pin on disc, disc rotation 200 rpm, load 0.65, 1.30, 1.95, 2.60 and 3.25 MPa | For load more to 1.95 MPa, the wear and friction coefficient of hybrid AZ31 composite is low and it only follows in case of 0.1% A12O3 and 0.2% CNTs composites | Lu et al. [83] |
Considering the development of magnesium based metal matrix composites via FSP as reported in literature only selective strengthening mechanism hold good. Grain boundary and secondary phase mechanism are the two strengthening mechanism and both of them are Hall–Petch relationship, and Orowan strengthening.
Hall–Petch strengthening mechanism have a vital role in the upgradation of major properties like strength of a composites, and it’s contribution is directly depend on refined grains existing in metal matrix zone. And the pinning action exerted by the secondary phase particles give rise to the concept of grain boundary and grain size which is further expresses by Zener equation as shown in Eq 1 where the grain size of the matrix dm that can be achieved [70].
dm=4αdp/3vp | (1) |
Here dp shows particle size, volume fraction of particles is vp and α is a constant of proportionality. It may be concluded that newly developed grain size is highly influenced by the size of the reinforcement particles and its volume fraction. Hall–Petch relationship states that hardness is inversely proportional to grain size in other words any reduction in the grain size attributes to increase the yield strength. According to Hall–Petch Eqs 2 and 3 [84,85,86,87].
ΔσHall−Petch=Ky(d−1/2composites−d−1/2matrix) | (2) |
where dcomposites and dmatrix are the average grain size of the composite and matrix and Ky is the strengthening coefficient.
σy=σo+Ky/√d | (3) |
where σy is the yield stress, σo is a materials constant for the starting stress for dislocation movement (or yield strength before FSP), ky is the strengthening coefficient (a constant specific to each material), and d is the average grain diameter. Based on similar theory [46,47] reported that increases the tool transverse speed, grain size reduces in SZ which further increases hardness at SZ. The influence of grain size on yield strength of magnesium alloys has also been reported in number of studies [59,60,64,69]. Azizieh et al. [81] and Huang et al. [64] based on average grain size uses further simplified Hall–Petch relationship and uses Eqs 4 and 5 for calculating microhardness of the samples.
Hv=43+78d−1/2 | (4) |
Hv=40+72d−1/2 | (5) |
where d is the average grain size. Rather Hung [88] established a generalized equation (Eq 6) for AZ series magnesium alloys. As reported in literature Figure 8 shows the ultra-refinement in grain size of magnesium composites as compared to base metal and Figure 9 shows the corresponding values of microhardness for magnesium composites when compared to base metal.
Hv=56+348d−1/2 | (6) |
Zhang and Chen [89] well explained the contribution of Orowan strengthening mechanism in reinforced metal matrix composites. Furthermore, Sanaty-Zadeh [90] studies different strengthening mechanisms and it is worth maintaining that Hall–Petch strengthening mechanism is the most important factor, which should not be neglected even in micro-scale grain. Dadashpour et al. [52] concluded that in fabricating AZ/SiC magnesium based composite Orowan strengthening mechanism influence dislocation of grains, Vedabouriswaran and Aravindan [70] studies the effect of Orowan strengthening mechanism for fabricating magnesium based composite and concluded insignificant contribution of Orowan strengthening mechanism for their work. Sharma et al. [68] calculated as 58.65 MPa as the total contribution of Orowan strengthening by using Orowan equation as mention below in Eq 7.
ΔσOrowan=(0.8×Gm×M×b)/Lp | (7) |
where Gm is the shear modulus of alloy matrix, b is the magnitude of Burger’s vector of the alloy matrix and M is Taylors factor. Lp is the inter-particle distance of the composites and can be calculated by equation mentioned below in Eq 8.
Lp=√(πdef2)/(2Vref) | (8) |
where, Vref is the volume fraction of the hybrid reinforcements and dref is the average grain sizes of nano composites used.
Above studies of literature clearly concludes that new materials especially composite manufacturing could be effectively achieved via FSP. Various reinforcements have been successfully incorporated in metallic matrix by FSP. The grain refinement accomplished by FSP along with high hardness, expanded wear and erosion opposition is the one of a kind point of interest of this procedure. MMCs manufactured by FSP are typically a kind of defect free composites with homogeneous distribution of particles. FSP has indicated promising outcomes in different investigations. Copper, titanium, aluminum, and magnesium materials are the most commonly accepted materials used to supply FSP surface MMCs. Magnesium based components are among them a category of tough to process materials. It has been unmistakably reported in literature and in reality there is a lot of improvement for as long as decade that distinctive magnesium based surface composites can be effectively delivered by FSP. Very recently Huang [91] suggested that singly dispersed CNTs formed compact bonding with the matrix, which contributed to the grain refinement and the mechanical properties enhancement of the Mg–6Zn matrix. In addition, they explanied about strengthening mechanism contributions to grain refinement, load transfer and Orowan looping mechanisms. Finally they acheived 144%, 156% and 87% higher values of yield strength, ultimate tensile strength and elongation of the FSPed CNTs/Mg–6Zn composites than those of the as-cast pristine Mg–6Zn alloy.
Apart from various applications of MMCs prepared by FSP yet production engineers are still wondering for the best outcome of the FSP process. Compound and articulate surfaces are hard to produce by FSP. More FSP passes could only have a homogeneous mixture of the reinforce particles into metal matrix, thereby increasing the cost of output. Tool wear is a significant issue in FSP particularly at high temperature. Basically this wear is due to prolonged contact between reinforce particles and tool pin. Literature also shows that various machine parameters affect the tool wear such as tool rotaion speed, transverse speed and axial force [92]. In addition, it was observed that considering tool wear, shear phenomenon is more dominating than drag, as demostrated by Bist [92]. The development of wear-resistant tools is necessary for repetable solid-state joining. Hence tungsten base and high carbon high chromium based tools are highly recommended for FSP processes.
Also high thermal energy generation and its controlled is an major issue [93].These constraints confine the utilization of FSP to process hard surface composites. Flow of reinforce particles into the matrix is still wide area which need to be explore. Optimizing the FSP parameters and developing a model is still an area of future scope. Few recent developments such as fed friction stir technology reported in [94,95] may be considered for further improvement.
Literature study clearly summed up that even hard to processed material such as magnesium can be easily processed via FSP. Mainly two holes filling approach and groove filling approach been adapted for doping reinforce particles into the metal matrix. Every technique holds its advantages and limitations. Grain refinement, improved hardness, wear opposition, mechanical conduct, improved bioactivity and erosion obstruction are the normal perceptions in the entirety of the magnesium based composites produced by FSP. The relative contribution of Orowan strengthening effect increases with decreasing size of nanoparticles and Hall–Petch strengthening mechanisms increases with decreasing size of grains.
Also due to the stochastic nature of FSP machine parameters, an optimum combination of these parameters need to be established for producing defect free composite materials.
Dominant part of the work has been done utilizing AZ arrangement magnesium compounds. It is foreseen that composites of other magnesium combinations likewise will be created by FSP in future for a wide scope of uses.
All authors declare no conflicts of interest in this paper.
[1] | Smith W, Hashemi J, Prakash R (2008) Materials Science and Engineering (SIE), 4 Eds., New York: McGraw Hill Education. |
[2] | Clyne TW, Hull D (2019) An Introduction to Composite Materials, 3 Eds., Cambridge: Cambridge University Press. |
[3] | Van Suchtelen J (1972) Product properties: a new application of composite materials. Philips Res Rep 27: 28-37. |
[4] | Chung DDL (2010) Composite Materials Science and Applications, 2 Eds., New York: Springer. |
[5] | Mukhin I, Perevezentsev E, Palashov O (2014) Fabrication of composite laser elements by a new thermal diffusion bonding method. Opt Mater Express 4: 266-271. |
[6] | Bodukuri AK, Eswaraiah K, Rajendar K, et al. (2016) Fabrication of Al-SiC-B4C metal matrix composite by powder metallurgy technique and evaluating mechanical properties. Perspect Sci 8: 428-431. |
[7] | Jiang QC, Wang HY, Ma BX, et al. (2005) Fabrication of B4C particulate reinforced magnesium matrix composite by powder metallurgy. J Alloy Compd 386: 177-181. |
[8] | Schubert T, Trindade B, Weißgärber T, et al. (2008) Interfacial design of Cu-based composites prepared by powder metallurgy for heat sink applications. Mat Sci Eng A-Struct 475: 39-44. |
[9] | Wang X, Jha A, Brydson R (2004) In situ fabrication of Al3Ti particle reinforced aluminium alloy metal-matrix composites. Mat Sci Eng A-Struct 364: 339-345. |
[10] | Yang B, Wang F, Zhang JS (2003) Microstructural characterization of in situ TiC/Al and TiC/Al-20Si-5Fe-3Cu-1Mg composites prepared by spray deposition. Acta Mater 51: 4977-4989. |
[11] | Hashim J, Looney L, Hashmi MSJ (1999) Metal matrix composites: production by the stir casting method. J Mater Process Tech 92: 1-7. |
[12] | Uozumi H, Kobayashi K, Nakanishi K, et al. (2008) Fabrication process of carbon nanotube/light metal matrix composites by squeeze casting. Mat Sci Eng A-Struct 495: 282-287. |
[13] | Hu H (1998) Squeeze casting of magnesium alloys and their composites. J Mater Sci 33: 1579-1586. |
[14] | Dhanashekar M, Kumar VSS (2014) Squeeze casting of aluminium metal matrix composites—An overview. Procedia Eng 97: 412-420. |
[15] | He CN, Zhao NQ, Shi CS, et al. (2009) Mechanical properties and microstructures of carbon nanotube-reinforced Al matrix composite fabricated by in situ chemical vapor deposition. J Alloys Compd 487: 258-262. |
[16] | Delhaes P (2002) Chemical vapor deposition and infiltration processes of carbon materials. Carbon 40: 641-657. |
[17] | Mishra RS, Ma ZY (2005) Friction stir welding and processing. Mat Sci Eng R 50: 1-78. |
[18] | Meng X, Huang Y, Cao J, et al. (2020) Recent progress on control strategies for inherent issues in friction stir welding. Prog Mater Sci 115: 100706. |
[19] | Sharma V, Prakash U, Kumar BVM (2018) Surface composites by friction stir processing: A review. J Mater Process Tech 224: 117-134. |
[20] | Ni DR, Wang JJ, Zhou ZN, et al. (2014) Fabrication and mechanical properties of bulk NiTip/Al composites prepared by friction stir processing. J Alloys Compd 586: 368-374. |
[21] | Thangarasu A, Murugan N, Dinaharan I, et al. (2015) Synthesis and characterization of titanium carbide particulate reinforced AA6082 aluminium alloy composites via friction stir processing. Arch Civ Mech Eng 15: 324-334. |
[22] | Salehi M, Farnoush H, Mohandesi JA (2014) Fabrication and characterization of functionally graded Al-SiC nanocomposite by using a novel multistep friction stir processing. Mater Design 63: 419-426. |
[23] | Byung-Wook AHN, Don-Hyun C, Yong-Hwan KIM, et al. (2012) Fabrication of SiCp/AA5083 composite via friction stir welding. T Nonferr Metal Soc 22: s634-s638. |
[24] | Sagar P, Handa A (2020) Selection of tool transverse speed considering trial run experimentations for AZ61/Tic composite developed via friction stir processing using triangular tool. Mater Today Proc In press. |
[25] | Guo J, Amira S, Gougeon P, et al. (2011) Effect of the surface preparation techniques on the EBSD analysis of a friction stir welded AA1100-B4C metal matrix composite. Mater Charact 62: 865-877. |
[26] | Yang M, Xu C, Wu C, et al. (2010) Fabrication of AA6061/Al2O3 nano ceramic particle reinforced composite coating by using friction stir processing. J Mater Sci 45: 4431-4438. |
[27] | Feng AH, Ma ZY (2007) Formation of Cu2FeAl7 phase in friction-stir-welded SiCp/Al-Cu-Mg composite. Scripta Mater 57: 1113-1116. |
[28] | Lim DK, Shibayanagi T, Gerlich AP (2009) Synthesis of multi-walled CNT reinforced aluminium alloy composite via friction stir processing. Mat Sci Eng A-Struct 507: 194-199. |
[29] | Gupta M, Ling MN (2011) Magnesium, Magnesium Alloys and Magnesium Composites, 1 Ed., Hoboken: John Wiley and Sons. |
[30] | Sunil BR, Reddy GPK, Patle H, et al. (2016) Magnesium based surface metal matrix composites by friction stir processing. J Magnes Alloy 4: 52-61. |
[31] | Mishra RS, Mahoney MW, McFadden SX, et al. (1999) High strain rate superplasticity in a friction stir processed 7075Al alloy. Scripta Mater 42: 163-168. |
[32] | Dinaharan I, Murugan N, Parameswaran S (2012) Developing an empirical relationship to predict the influence of process parameters on tensile strength of friction stir welded AA6061/0-10 wt% ZrB2 in situ composite. Trans Indian Inst Met 65: 159-170. |
[33] | Dolatkhah A, Golbabaei P, Givi MKB, et al. (2012) Investigating effects of process parameters on microstructural and mechanical properties of Al5052/SiC metal matrix composite fabricated via friction stir processing. Mater Design 37: 458-464. |
[34] | Zohoor M, Givi MKB, Salami P (2012) Effect of processing parameters on fabrication of Al-Mg/Cu composites via friction stir processing. Mater Design 39: 358-365. |
[35] | Thangarasu A, Murugan N, Dinaharan I, et al. (2014) Influence of traverse speed on microstructure and mechanical properties of AA6082-TiC surface composite fabricated by friction stir processing. Procedia Mater Sci 5: 2115-2121. |
[36] | Bauri R, Janaki Ram GD, Yadav D, et al. (2015) Effect of process parameters and tool geometry on fabrication of Ni particles reinforced 5083 Al composite by friction stir processing. Mater Today Proc 2: 3203-3211. |
[37] | Patel VV, Badheka V, Kumar A (2016) Influence of friction stir processed parameters on superplasticity of Al-Zn-Mg-Cu alloy. Mater Manuf Process 31: 1573-1582. |
[38] | Salehi M, Farnoush H, Mohandesi JA (2014) Fabrication and characterization of functionally graded Al-SiC nanocomposite by using a novel multistep friction stir processing. Mater Design 63: 419-426. |
[39] | Hoda MDN, Singari RM, Arulmoni VJ (2016) Friction stir processing (FSP) of copper and enhancement of its mechanical properties using graphite powder. IJRSI 3: 58-65. |
[40] | Sathiskumar R, Murugan N, Dinaharan I, et al. (2013) Prediction of mechanical and wear properties of copper surface composites fabricated using friction stir processing. Mater Design 55: 224-234. |
[41] | Rathee S, Maheshwari S, Siddiquee AN, et al. (2018) A review of recent progress in solid state fabrication of composites and functionally graded systems via friction stir processing. Crit Rev Solid State 43: 334-366. |
[42] | Li K, Liu X, Zhao Y (2019) Research status and prospect of friction stir processing technology. Coatings 9: 129. |
[43] | Vijay SJ, Murugan N (2010) Influence of tool pin profile on the metallurgical and mechanical properties of friction stir welded Al-10 wt% TiB2 metal matrix composite. Mater Design 31: 3585-3589. |
[44] | Zhang YN, Cao X, Larose S, et al. (2012) Review of tools for friction stir welding and processing. Can Metall Quart 51: 250-261. |
[45] | Kirkland NT, Birbilis N (2014) Introduction to magnesium biomaterials, Magnesium Biomaterials, 1 Ed., Cham: Springer, 1-12. |
[46] | Asadi P, Faraji G, Besharati MK (2010) Producing of AZ91/SiC composite by friction stir processing (FSP). Int J Adv Manuf Tech 51: 247-260. |
[47] | Asadi P, Givi MKB, Faraji G (2010) Producing ultrafine-grained AZ91 from as-cast AZ91 by FSP. Mater Manuf Process 25: 1219-1226. |
[48] | Faraji G, Dastani O, Asghar SA, et al. (2011) Effect of process parameters on microstructure and micro-hardness of AZ91/Al2O3 surface composite produced by FSP. J Mater Eng Perform 20: 1583-1590. |
[49] | Khayyamin D, Mostafapour A, Keshmiri R (2013) The effect of process parameters on microstructural characteristics of AZ91/SiO2 composite fabricated by FSP. Mat Sci Eng A-Struct 559: 217-221. |
[50] | Faraji G, Dastani O, Mousavi SAAA (2011) Microstructures and mechanical properties of Al2O3/AZ91 surface nanocomposite layer produced by friction stir processing. P I Mech Eng B-J Eng 225: 1331-1345. |
[51] | Ahmadkhaniha D, Heydarzadeh Sohi M, Salehi A, et al. (2016) Formations of AZ91/Al2O3 nano-composite layer by friction stir processing. J Magnes Alloy 4: 314-318. |
[52] | Dadashpour M, Mostafapour A, Yeşildal R, et al. (2016) Effect of process parameter on mechanical properties and fracture behavior of AZ91C/SiO2 composite fabricated by FSP. Mat Sci Eng A-Struct 655: 379-387. |
[53] | Chen T, Zhu Z, Ma Y, et al. (2010) Friction stir processing of thixoformed AZ91D magnesium alloy and fabrication of surface composite reinforced by SiCps. J Wuhan Univ Technol 25: 223-227. |
[54] | Singh N, Singh J, Singh B, et al. (2018) Wear behavior of B4C reinforced AZ91 matrix composite fabricated by FSP. Mater Today Proc 5: 19976-19984. |
[55] | Morisada Y, Fujii H, Nagaoka T, et al. (2006) Effect of friction stir processing with SiC particles on microstructure and hardness of AZ31. Mat Sci Eng A-Struct 433: 50-54. |
[56] | Morisada Y, Fujii H, Nagaoka T, et al. (2006) MWCNTs/AZ31 surface composites fabricated by friction stir processing. Mat Sci Eng A-Struct 419: 344-348. |
[57] | Azizieh M, Kokabi AH, Abachi P (2011) Effect of rotational speed and probe profile on microstructure and hardness of AZ31/Al2O3 nanocomposites fabricated by friction stir processing. Mater Design 32: 2034-2041. |
[58] | Azizieh M, Kim HS, Kokabi AH, et al. (2011) Fabrication of AZ31/Al2O3 nanocomposites by friction STIR processing. Rev Adv Mater Sci 28: 85-89. |
[59] | Srinivasan M, Loganathan C, Balasubramanian V, et al. (2011) Feasibility of joining AZ31B magnesium metal matrix composite by friction welding. Mater Design 32: 1672-1676. |
[60] | Chang CI, Wang YN, Pei HR, et al. (2007) Microstructure and mechanical properties of nano-ZrO2 and nano-SiO2 particulate reinforced AZ31-Mg based composites fabricated by friction stir processing. Key Eng Mater 351: 114-119. |
[61] | Balakrishnan M, Dinaharan I, Palanivel R, et al. (2015) Synthesize of AZ31/TiC magnesium matrix composites using friction stir processing. J Magnes Alloy 3: 76-78. |
[62] | Jiang Y, Yang X, Miura H, et al. (2013) Particles reinforced magnesium alloy produced by friction stir processing. Rev Adv Mater Sci 33: 29-32. |
[63] | Sharma S, Handa A, Singh SS, et al. (2019) Synthesis of a novel hybrid nanocomposite of AZ31Mg-Graphene-MWCNT by multi-pass friction stir processing and evaluation of mechanical properties. Mater Res Express 6: 126531. |
[64] | Huang Y, Wang T, Guo W, et al. (2014) Microstructure and surface mechanical property of AZ31 Mg/SiCp surface composite fabricated by direct friction stir processing. Mater Design 59: 274-278. |
[65] | Soltani M, Shamanian M, Niroumand B (2015) Surface characteristics improvement of AZ31B magnesium by surface compositing with carbon nano-tubes through friction stir processing. Int J Adv Des Manuf Technol 8: 85-95. |
[66] | Navazani M, Dehghani K (2015) Investigation of microstructure and hardness of Mg/TiC surface composite fabricated by friction stir processing (FSP). Procedia Mater Sci 11: 509-514. |
[67] | Sunil BR, Kumar TSS, Chakkingal U, et al. (2014) Nano-hydroxyapatite reinforced AZ31 magnesium alloy by friction stir processing: A solid state processing for biodegradable metal matrix composites. J Mater Sci Mater Med 25: 975-988. |
[68] | Sharma S, Handa A, Singh SS, et al. (2019) Influence of tool rotation speeds on mechanical and morphological properties of friction stir processed nano hybrid composite of MWCNT-Graphene-AZ31 magnesium. J Magnes Alloy 7: 487-500. |
[69] | Das S, Mishra RS, Doherty KJ, et al. (2016) Magnesium based composite via friction stir processing, In: Mishra R, Mahoney MW, Sato Y, et al., Frict Stir Weld Process VII, Cham: Springer, 245-252. |
[70] | Vedabouriswaran G, Aravindan S (2018) Development and characterization studies on magnesium alloy (RZ 5) surface metal matrix composites through friction stir processing. J Magnes Alloy 6: 145-163. |
[71] | Del Valle JA, Rey P, Gesto D, et al. (2012) Friction stir processing of the magnesium alloy AZ61: Grain size refinement and mechanical properties. Mater Sci Forum 706: 1823-1828. |
[72] | Lee CJ, Huang JC, Hsieh PJ (2006) Mg based nano-composites fabricated by friction stir processing. Scripta Mater 54: 1415-1420. |
[73] | Du X, Wu B (2009) Using two-pass friction stir processing to produce nanocrystalline microstructure in AZ61 magnesium alloy. Sci China Technol Sci 52: 1751-1755. |
[74] | Madhusudhan Reddy G, Sambasiva Rao A, Srinivasa Rao K (2013) Friction stir processing for enhancement of wear resistance of ZM21 magnesium alloy. Trans Indian Inst Met 66: 13-24. |
[75] | Abbasi M, Bagheri B, Dadaei M, et al. (2015) The effect of FSP on mechanical, tribological, and corrosion behavior of composite layer developed on magnesium AZ91 alloy surface. Int J Adv Manuf Tech 77: 2051-2058. |
[76] | Singh J, Lal H, Bala N (2013) Investigations on the wear behavior of friction stir processed magnesium based AZ91 alloy. Int J Mech Eng Robot Res 2: 271-274. |
[77] | Arora HS, Singh H, Dhindaw BK, et al. (2012) Improving the tribological properties of mg based AZ31 alloy using friction stir processing. Adv Mater Res 585: 579-583. |
[78] | Arora HS, Singh H, Dhindaw BK (2013) Wear behaviour of a Mg alloy subjected to friction stir processing. Wear 303: 65-77. |
[79] | Ram B, Deepak D, Bala N (2019) Role of friction stir processing in improving wear behavior of Mg/SiC composites produced by stir casting route. Mater Res Express 6: 026577. |
[80] | Azizieh M, Larki AN, Tahmasebi M, et al. (2018) Wear behavior of AZ31/Al2O3 magnesium matrix surface nanocomposite fabricated via friction stir processing. J Mater Eng Perform 27: 2010-2017. |
[81] | Dinaharan I, Vettivel SC, Balakrishnan M, et al. (2019) Influence of processing route on microstructure and wear resistance of fly ash reinforced AZ31 magnesium matrix composites. J Magnes Alloy 7: 155-165. |
[82] | Faraji G, Asadi P (2011) Characterization of AZ91/alumina nanocomposite produced by FSP. Mat Sci Eng A-Struct 528: 2431-2440. |
[83] | Lu D, Jiang Y, Zhou R (2013) Wear performance of nano-Al2O3 particles and CNTs reinforced magnesium matrix composites by friction stir processing. Wear 305: 286-290. |
[84] | Whang S (2011) Nanostructured metals and alloys, Woodhead Publishing Series in Metals and Surface Engineering, 1 Ed., Cambridge: Woodhead Publishing, 15-19. |
[85] | Pande CS, Cooper KP (2009) Nanomechanics of Hall-Petch relationship in nanocrystalline materials. Prog Mater Sci 54: 689-706. |
[86] | Sato YS, Urata M, Kokawa H, et al. (2003) Hall-Petch relationship in friction stir welds of equal channel angular-pressed aluminum alloys. Mat Sci Eng A-Struct 354: 298-305. |
[87] | Xiao P, Gao Y, Yang C, et al. (2018) Microstructure, mechanical properties and strengthening mechanisms of Mg matrix composites reinforced with in situ nanosized TiB2 particles. Mat Sci Eng A-Struct 710: 251-259. |
[88] | Hung YP, Huang JC, Wu KJ, et al. (2006) Strengthening and toughness of AZ61 Mg with nano SiO2 particles. Mater Trans 47: 1985-1993. |
[89] | Zhang Z, Chen DL (2008) Contribution of Orowan strengthening effect in particulate-reinforced metal matrix nanocomposites. Mat Sci Eng A-Struct 483: 148-152. |
[90] | Sanaty-Zadeh A (2012) Comparison between current models for the strength of particulate-reinforced metal matrix nanocomposites with emphasis on consideration of Hall-Petch effect. Mat Sci Eng A-Struct 531: 112-118. |
[91] | Huang Y, Li J, Wan L, et al. (2018) Strengthening and toughening mechanisms of CNTs/Mg-6Zn composites via friction stir processing. Mat Sci Eng A-Struct 732: 205-211. |
[92] | Bist A, Saini JS, Sharma B (2018) A review of tool wear prediction during friction stir welding of aluminium matrix composite. T Nonferr Metal Soc 26: 2003-2018. |
[93] | Chen G, Zhang S, Zhu Y, et al. (2020) Thermo-mechanical analysis of friction stir welding: A review on recent advances. Acta Metall Sin Engl Lett 33: 3-12. |
[94] | Kosturek R, Śnieżek L, Torzewski J, et al. (2019) Research on the friction stir welding of sc-modified AA2519 extrusion. Metals 9: 1024-1038. |
[95] | Derazkola HA, Khodabakhshi F (2020) A novel fed friction-stir (FFS) technology for nanocomposite joining. Sci Technol Weld Joi 25: 89-100. |
1. | Packia Antony Amalan A, N. M. Sivaram, A state-of-the-art review on magnesium-based composite materials, 2022, 2374-068X, 1, 10.1080/2374068X.2022.2096835 | |
2. | Prem Sagar, Amit Handa, Gitesh Kumar, Metallurgical, mechanical and tribological behavior of Reinforced magnesium-based composite developed Via Friction stir processing, 2022, 236, 0954-4089, 1440, 10.1177/09544089211063099 | |
3. | Vadym Shalomeev, Galyna Tabunshchyk, Viktor Greshta, Kinga Korniejenko, Martin Duarte Guigou, Sławomir Parzych, Casting Welding from Magnesium Alloy Using Filler Materials That Contain Scandium, 2022, 15, 1996-1944, 4213, 10.3390/ma15124213 | |
4. | Bo Wu, M.Z. Ibrahim, Sufian Raja, Farazila Yusof, Bushroa binti Abdul Razak, Mohd Ridha Bin Muhamad, Rongxue Huang, Yun Zhang, Irfan Anjum Badruddin, Mohamed Hussien, Sarfaraz Kamangar, The influence of reinforcement particles friction stir processing on microstructure, mechanical properties, tribological and corrosion behaviors: a review, 2022, 20, 22387854, 1940, 10.1016/j.jmrt.2022.07.172 | |
5. | Prem Sagar, Gitesh Kumar, Amit Handa, Progressive use of nanocomposite hydrogels materials for regeneration of damaged cartilage and their tribological mechanical properties, 2023, 2397-7914, 239779142311514, 10.1177/23977914231151487 | |
6. | Shivali Singla, Prem Sagar, Amit Handa, Magnesium-based nanocomposites synthesized using friction stir processing: an experimental study, 2023, 1042-6914, 1, 10.1080/10426914.2023.2195909 | |
7. | P. Sagar, A. Handa, Sushma Sangwan, Magnesium‐based nanocomposites developed through multi‐pass friction stir processing and strengthening mechanisms exploration, 2024, 55, 0933-5137, 758, 10.1002/mawe.202300291 | |
8. | Prem Sagar, Mukesh Kumar, Sanjeev Khanna, Yi Huang, 2024, chapter 10, 9798369339930, 180, 10.4018/979-8-3693-3993-0.ch010 | |
9. | Kunal Chauhan, Jimmy Karloopia, R. S. Walia, Mandeep Dhanda, Recent advances in magnesium alloys and its composites for bioimplant applications: Processing, matrix, reinforcement, and corrosion perspectives, 2024, 49, 1040-8436, 1202, 10.1080/10408436.2024.2323010 | |
10. | Shivali Singla, Prem Sagar, Amit Handa, Amardeep Singh Kang, Recent Advances in Magnesium-Based Metal Matrix Surface Composites Developed via Friction Stir Processing Route—An Overview, 2023, 12, 2192-9262, 385, 10.1007/s13632-023-00969-9 | |
11. | Prem Sagar, Amit Handa, Enhanced strength ductility and wear resistance in a friction stir processing engineered AZ31B/TiC magnesium-based nanocomposites, 2024, 63, 0008-4433, 1150, 10.1080/00084433.2023.2289800 | |
12. | Prem Sagar, Amit Handa, Exploring the mechanical, metallurgical, and fracture characteristics of hybrid-reinforced magnesium metal matrix composite synthesized via friction stir processing route, 2024, 238, 1464-4207, 829, 10.1177/14644207231200640 | |
13. | Prem Sagar, Sanjeev K Khanna, Rade Vignjevic, Amit Handa, Synergistic effect of hybrid reinforcement on magnesium-based composites for enriching mechanical and tribological characteristics, 2024, 0954-4089, 10.1177/09544089231221683 | |
14. | Yu-Xin Luo, Bai-Xin Dong, Hong-Yu Yang, Feng Qiu, Bai-Chuan Yan, Shi-Li Shu, Qi-Chuan Jiang, Feng-Jian Shi, Research progress on nanoparticles reinforced magnesium alloys, 2024, 30, 22387854, 5166, 10.1016/j.jmrt.2024.04.129 | |
15. | Prem Sagar, Sushma Sangwan, 2024, chapter 2, 9798369312612, 37, 10.4018/979-8-3693-1261-2.ch002 | |
16. | Roshan Vijay Marode, Tamiru Alemu Lemma, Nabihah Sallih, Srinivasa Rao Pedapati, Mokhtar Awang, Adeel Hassan, Research progress in friction stir processing of magnesium alloys and their metal matrix surface composites: Evolution in the 21st century, 2024, 12, 22139567, 2091, 10.1016/j.jma.2024.06.007 | |
17. | Prem Sagar, Sushma Sangwan, Amit Handa, Investigation on Mechanical and Fracture Behavior of Magnesium Composite Reinforced With Hybrid Fly Ash Particulates Synthesized via Friction Stir Processing Route, 2024, 146, 0094-4289, 10.1115/1.4064658 | |
18. | Bo Wu, Farazila Yusof, Fuguo Li, Huan Miao, A.R. Bushroa, Mohd Ridha Bin Muhamad, Irfan Anjum Badruddin, Mahmoud Z. Ibrahim, Effects of friction stir processing and nano-hydroxyapatite on the microstructure, hardness, degradation rate and in-vitro bioactivity of WE43 alloy for biomedical applications, 2024, 12, 22139567, 209, 10.1016/j.jma.2023.10.010 | |
19. | Vipul K. Patel, Harikrishna Rana, D. K. Patel, Study on AZ31 magnesium alloy-based surface composite through friction stir processing: a review, 2025, 0950-7116, 1, 10.1080/09507116.2025.2458043 | |
20. | Prem Sagar, Hybrid GA-ANN and GA-ANFIS soft computing approaches for optimizing tensile strength in magnesium-based composites fabricated via friction stir processing, 2025, 44, 23524928, 112083, 10.1016/j.mtcomm.2025.112083 |
Composite | Tool geometry | Grain size improvement | Machine parameters | Wear test specifications | Significant outcome | References |
ZM21/SiC/B4C | Straight cylindrical | 40 µm refined up to 20 µm | 1200 rpm, 50 mm/min | Pin on disc, load 0.5 kg, sliding speed 640 rpm for 6 km | Wear rate of composite decreases seventy six times to the base metal | Reddy et al. [74] |
AZ91/Al2O3/SiC | Straight cylindrical | More refined grains as number of passes increases | 730–1800 rpm, 14–80 mm/min with 1–4 passes | Tri pin on disc, load 50 N, sliding speed 1 mm/s for 500 m | Wear rate decreases as number of pass increases AZ91/ AZ91/Al2O3 & AZ91/SiC gives almost same wear rate | Abbasi et al. [75] |
AZ91/TiC | Straight cylindrical | More refined grains | 900 rpm, 40 mm/min with PD = 0.3 mm | Pin on disc, load 5–10 N, sliding speed 1 m/s for 2000 m | Wear rate of composite decreases half to the base metal | Singh et al. [76] |
AZ31/TiC | Straight cylindrical | More refined grains | 800 rpm, 40 mm/min | Pin on disc, load 5–20 N, sliding speed 1 m/s for 1.5 km | At 20 N higher wear resistance was noticed | H. S. Arora et al. [77] |
AE42 as cast and FSPed AE42 | Straight cylindrical | 40% reduction in grain size and reached upto 1.5 µm | 700 rpm, 60 mm/min | Pin on disc, load 5–20 N, sliding speed 0.3–3 m/s for 2500 m | Higher co-efficient of friction attended at low sliding velocities | Arora et al. [78] |
As cast Mg/SiC | Threaded cyllindrical | Grain size reduced from 170 to 3 µm | 1300 rpm, 50 mm/min | Pin on disc, load 1–5 Kg, sliding speed 1 m/s for 600 m | 20% and 47% wear loss was noticed at 1 and 5 Kg | Ram et al. [79] |
AZ31/Al2O3 | Threaded cyllindrical | With development of refined grains hardness increases from 50 to 90 Hv | 800, 1000, 1200 and 1400 rpm, 45 mm/min and 2° tilt angle | Pin on disc, load 10, 50 and 90 N, sliding velocity 0.12m/s for 600 m | Wear rate at 1000 and 1200 rpm is higher as compared to 800 rpm | Azizieh et al. [80] |
AZ31/Fly ash | Straight cylindrical | Upto 4 µm grain size achevied | 1200 rpm and 40mm/min | Pin on disc, load 20 N, sliding velocity 1.0 m/s for 3000 m | FSP exhibhits 33% lower wear rate as compared to stir cast | Dinaharan et al. [81] |
AZ91/Al2O3 | Circular and square tool | Average grain size 5–10 µm was obtained | 900–1200 rpm, 40–80 mm/min with 3° tilt angle | Pin on disc, load 50 N, sliding velocity 1.0 mm/min for 500 m | Wear rate decreases more than three times to the base metal | Faraji and Asadi [82] |
AZ31/MWCNT/ Al2O3 | Cone shape | Much small size grains with microhardness 1.4 times higher than those of AZ31 | 1050 rpm, 33.4 mm/min | Pin on disc, disc rotation 200 rpm, load 0.65, 1.30, 1.95, 2.60 and 3.25 MPa | For load more to 1.95 MPa, the wear and friction coefficient of hybrid AZ31 composite is low and it only follows in case of 0.1% A12O3 and 0.2% CNTs composites | Lu et al. [83] |
Composite | Tool geometry | Grain size improvement | Machine parameters | Wear test specifications | Significant outcome | References |
ZM21/SiC/B4C | Straight cylindrical | 40 µm refined up to 20 µm | 1200 rpm, 50 mm/min | Pin on disc, load 0.5 kg, sliding speed 640 rpm for 6 km | Wear rate of composite decreases seventy six times to the base metal | Reddy et al. [74] |
AZ91/Al2O3/SiC | Straight cylindrical | More refined grains as number of passes increases | 730–1800 rpm, 14–80 mm/min with 1–4 passes | Tri pin on disc, load 50 N, sliding speed 1 mm/s for 500 m | Wear rate decreases as number of pass increases AZ91/ AZ91/Al2O3 & AZ91/SiC gives almost same wear rate | Abbasi et al. [75] |
AZ91/TiC | Straight cylindrical | More refined grains | 900 rpm, 40 mm/min with PD = 0.3 mm | Pin on disc, load 5–10 N, sliding speed 1 m/s for 2000 m | Wear rate of composite decreases half to the base metal | Singh et al. [76] |
AZ31/TiC | Straight cylindrical | More refined grains | 800 rpm, 40 mm/min | Pin on disc, load 5–20 N, sliding speed 1 m/s for 1.5 km | At 20 N higher wear resistance was noticed | H. S. Arora et al. [77] |
AE42 as cast and FSPed AE42 | Straight cylindrical | 40% reduction in grain size and reached upto 1.5 µm | 700 rpm, 60 mm/min | Pin on disc, load 5–20 N, sliding speed 0.3–3 m/s for 2500 m | Higher co-efficient of friction attended at low sliding velocities | Arora et al. [78] |
As cast Mg/SiC | Threaded cyllindrical | Grain size reduced from 170 to 3 µm | 1300 rpm, 50 mm/min | Pin on disc, load 1–5 Kg, sliding speed 1 m/s for 600 m | 20% and 47% wear loss was noticed at 1 and 5 Kg | Ram et al. [79] |
AZ31/Al2O3 | Threaded cyllindrical | With development of refined grains hardness increases from 50 to 90 Hv | 800, 1000, 1200 and 1400 rpm, 45 mm/min and 2° tilt angle | Pin on disc, load 10, 50 and 90 N, sliding velocity 0.12m/s for 600 m | Wear rate at 1000 and 1200 rpm is higher as compared to 800 rpm | Azizieh et al. [80] |
AZ31/Fly ash | Straight cylindrical | Upto 4 µm grain size achevied | 1200 rpm and 40mm/min | Pin on disc, load 20 N, sliding velocity 1.0 m/s for 3000 m | FSP exhibhits 33% lower wear rate as compared to stir cast | Dinaharan et al. [81] |
AZ91/Al2O3 | Circular and square tool | Average grain size 5–10 µm was obtained | 900–1200 rpm, 40–80 mm/min with 3° tilt angle | Pin on disc, load 50 N, sliding velocity 1.0 mm/min for 500 m | Wear rate decreases more than three times to the base metal | Faraji and Asadi [82] |
AZ31/MWCNT/ Al2O3 | Cone shape | Much small size grains with microhardness 1.4 times higher than those of AZ31 | 1050 rpm, 33.4 mm/min | Pin on disc, disc rotation 200 rpm, load 0.65, 1.30, 1.95, 2.60 and 3.25 MPa | For load more to 1.95 MPa, the wear and friction coefficient of hybrid AZ31 composite is low and it only follows in case of 0.1% A12O3 and 0.2% CNTs composites | Lu et al. [83] |