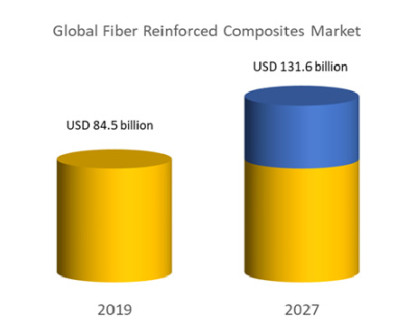
The composites industry is present in practically all industrial sectors with an annual growth rate of 5%. Its contribution to the priority "light-weighting" driver in the transport sector is key. The efficiency of the industry is made possible by the evolution of manufacturing processes that also improve the performance of the products obtained. For example, out-of-autoclave (OOA) processes can obtain high-performance composites such as those obtained by the autoclave process at lower costs. A key aspect in the development of this type of process is the preforming of continuous fibre reinforcements, which can achieve high fibre percentages while facilitating processing. Manufacturing these preforms currently requires multiple steps, equipment and tooling. TECNALIA's work developing the ADDICOMP technology, an alternative preform manufacturing method using an additive process based on Fused Deposition Modelling (FDM) is detailed in this article. This development is patented by Tecnalia and was conducted in 2 phases: (a) development of continuous fibre filaments coated with polymeric material and printable by FDM and (b) fine-tuning of FDM technology to print filaments with a very high content of continuous fibre.
Citation: M. A. Mendizabal, Maitane Garcia, Luis Palenzuela, Enrique Hernández. Obtaining preforms by additive fused deposition modelling (FDM) extrusion technology for the manufacture of high-performance composites[J]. AIMS Materials Science, 2022, 9(3): 481-497. doi: 10.3934/matersci.2022028
[1] | Mnvrl Kumar, R. Ramakrishnan, Alnura Omarbekova, Santhosh Kumar. R . Experimental characterization of mechanical properties and microstructure study of polycarbonate (PC) reinforced acrylonitrile-butadiene-styrene (ABS) composite with varying PC loadings. AIMS Materials Science, 2021, 8(1): 18-28. doi: 10.3934/matersci.2021002 |
[2] | Mahdi Rafiee, Roozbeh Abidnejad, Anton Ranta, Krishna Ojha, Alp Karakoç, Jouni Paltakari . Exploring the possibilities of FDM filaments comprising natural fiber-reinforced biocomposites for additive manufacturing. AIMS Materials Science, 2021, 8(4): 524-537. doi: 10.3934/matersci.2021032 |
[3] | Mohammad S. Alsoufi, Mohammed W. Alhazmi, Dhia K. Suker, Mohammed Yunus, Rashad O. Malibari . From 3D models to FDM 3D prints: experimental study of chemical treatment to reduce stairs-stepping of semi-sphere profile. AIMS Materials Science, 2019, 6(6): 1086-1106. doi: 10.3934/matersci.2019.6.1086 |
[4] | Azhar Equbal, Ramesh Murmu, Veenit Kumar, Md. Asif Equbal . A recent review on advancements in dimensional accuracy in fused deposition modeling (FDM) 3D printing. AIMS Materials Science, 2024, 11(5): 950-990. doi: 10.3934/matersci.2024046 |
[5] | Stelladriana Volpe, Andrea Petrella, Valentino Sangiorgio, Michele Notarnicola, Francesco Fiorito . Preparation and characterization of novel environmentally sustainable mortars based on magnesium potassium phosphate cement for additive manufacturing. AIMS Materials Science, 2021, 8(4): 640-658. doi: 10.3934/matersci.2021039 |
[6] | Francisco J. G. Silva, Rita C. M. Sales-Contini . Advances in laser materials and processing technologies: An overview. AIMS Materials Science, 2025, 12(1): 23-27. doi: 10.3934/matersci.2025002 |
[7] | Yong X. Gan . A review of electrohydrodynamic casting energy conversion polymer composites. AIMS Materials Science, 2018, 5(2): 206-225. doi: 10.3934/matersci.2018.2.206 |
[8] | Carlos A. Sánchez, Yamile Cardona-Maya, Andrés D. Morales, Juan S. Rudas, Cesar A. Isaza . Development and evaluation of polyvinyl alcohol films reinforced with carbon nanotubes and alumina for manufacturing hybrid metal matrix composites by the sandwich technique. AIMS Materials Science, 2021, 8(2): 149-165. doi: 10.3934/matersci.2021011 |
[9] | Bandar Abdullah Aloyaydi, Subbarayan Sivasankaran, Hany Rizk Ammar . Influence of infill density on microstructure and flexural behavior of 3D printed PLA thermoplastic parts processed by fusion deposition modeling. AIMS Materials Science, 2019, 6(6): 1033-1048. doi: 10.3934/matersci.2019.6.1033 |
[10] | Alejandro Sandá, Rocío Ruiz, Miguel Ángel Mafé, Jon Ander Sarasua, Antonio González-Jiménez . Scrapping of PEKK-based thermoplastic composites retaining long fibers and their use for compression molded recycled parts. AIMS Materials Science, 2023, 10(5): 819-834. doi: 10.3934/matersci.2023044 |
The composites industry is present in practically all industrial sectors with an annual growth rate of 5%. Its contribution to the priority "light-weighting" driver in the transport sector is key. The efficiency of the industry is made possible by the evolution of manufacturing processes that also improve the performance of the products obtained. For example, out-of-autoclave (OOA) processes can obtain high-performance composites such as those obtained by the autoclave process at lower costs. A key aspect in the development of this type of process is the preforming of continuous fibre reinforcements, which can achieve high fibre percentages while facilitating processing. Manufacturing these preforms currently requires multiple steps, equipment and tooling. TECNALIA's work developing the ADDICOMP technology, an alternative preform manufacturing method using an additive process based on Fused Deposition Modelling (FDM) is detailed in this article. This development is patented by Tecnalia and was conducted in 2 phases: (a) development of continuous fibre filaments coated with polymeric material and printable by FDM and (b) fine-tuning of FDM technology to print filaments with a very high content of continuous fibre.
An analysis of the scope of the composites industry from a global point of view shows that composites are present in practically all industrial sectors. Frédérique Mutel, President and CEO (Chief Executive Officer) of JEC Group (Journées Européennes des Composites Group) stated in his opening speech of the XXIII Technical conference, organized by the Spanish Plastics Center (CEP: Centro Español de plasicos) as part of the Automobile Barcelona show in 2018 that "composites are growing continuously (around 5% per year) and in very heterogeneous industries, in fact, at JEC Group we have positioned our offer in 40 sectors" [1]. This statement points mainly to transport, aeronautics, wind power, energy and construction, which account for 75% of the market for these materials. This growth is expected to continue in the coming years, as supported by several market studies and highlighted in Figure 1.
Each industrial sector consumes composite materials in different ways, but what these sectors share is that their use is driven by the excellent specific mechanical, stiffness, durability, and undoubtedly light weight properties of these materials, making them indispensable in numerous applications. While the materials, processes and costs of aerospace manufacturing have little in common with the materials, processes and costs in recreational boat building or the automotive sector, the wide variety of available reinforcement types, matrices, processing technologies, and post-processing means solutions can be found to satisfy each user.
Despite the enormous diversity, there are some general trends shaping today's composites industry that should be considered: process automation aimed at increasing production volumes and reducing costs; the development of out-of-autoclave (OOA) processes such as resin infusion, resin transfer moulding (RTM) and thermoplastic processing as a competitive alternative for the production of high-performance composites; the increased consumption of thermoplastics arising from the use of OOA processes, and given their ease of handling and storage, automation capability, and recyclability; industry 4.0 for composites: the complete digitization of the manufacturing process from design to simulation, manufacturing simulation, troubleshooting, part tracking, and more. All these trends are leading to the development of thinking machines in the next-generation composites manufacturing environment. Lastly, the irruption of additive manufacturing, or rapid prototyping as it was initially called, is also impacting today's composite industry [3]. Additive manufacturing has been around for almost 40 years, beginning with the development of stereolithography technology used mainly for prototyping. Since then, it has evolved dramatically, resulting in the emergence of a wide variety of techniques using different materials [4]. Some of the advantages offered by additive manufacturing compared to traditional manufacturing processes are truly ground-breaking, such as the broad freedom of design, the possibility of manufacturing parts with complex shapes used to produce components that would be impossible to obtain through other manufacturing processes, and the feasibility of manufacturing parts without the need for a mould. Its disadvantages also differentiate it from other manufacturing processes [5]. The layer-by-layer deposition of the material prevents high mechanical properties from being obtained, generally creating structures that are not very compact and highly porous. Post-processes or the combination of traditional manufacturing processes with additive manufacturing are required to obtain components and final parts with satisfactory mechanical properties. This is the case of high-performance composites [6].
Several technologies such as Selective Laser Sintering (SLS), Stereolithography (SLA), and Fused Deposition modelling (FDM) have been used to address the additive manufacturing of plastic or reinforced plastic parts for years. Among these technologies, FDM technology is the most widely used in this materials field. In addition to printing polymeric materials and loaded polymeric materials, FDM is capable of printing polymers loaded with short reinforcement fibres, generally carbon. While this improves the properties of the final part, it cannot compete in the composite world [7]. The great challenge faced by this technology is to be able to print polymer/long continuous fibre in such a way that components with properties like those obtained by traditional composite manufacturing processes can be obtained. It would be impossible to tackle this challenge exclusively with additive manufacturing due to the lack of compaction inherent in the technology itself and the difficulty of incorporating adequate compaction pressure into the processes.
There have been continuous developments in these technologies since Markforged introduced the first 3D printer capable of printing polymer-based structures with continuous long fibre to the market in 2013, and the ways to accomplish the required integration and printing are varied [8,9].
These technologies offer the possibility of manufacturing complex shapes, generate savings as the use of moulds is not required and do not generate waste. However, despite the enormous possibilities, none of them can be used to obtain components with good mechanical properties because the content of fibre obtained directly inside of the Additve Process is low (≤30%) and the content of voids is high. Post-processing or hybrid processing techniques (i.e., processing techniques that combine additive manufacturing with conventional composite manufacturing processes) are required to obtain final parts with such propertieswhere the fibre content is high (60%–70%) and the voids content is low (<1%), similar to the traditional composites manufacturing processes [9].
The most important characteristic of high-performance composites is their high fibre content. For example, a high-performance carbon fibre-based composite applicable to sectors such as aerospace contains a fibre percentage of around 65% by volume. This very high percentage is easily achievable by processes such as autoclave, using the applicable pressure and optimized materials.
In alternative processes, such as liquid processes (resin infusion, Resin Transfer Moulding (RTM), High Pressure Resin Transfer Moulding (HPRTM), this high percentage of fibre is achievable using preforms as an intermediate state, prior to the final manufacturing process. These liquid processes consist of placing the reinforcement inside a closed mould, followed by the introduction of liquid resin that properly impregnates the fabric. The use of preforms allows the number of reinforcement layers and their placement in the mould to be such that the desired high percentages can be obtained. The preform is an intermediate configuration of the same shape as the final part, formed by layers of fabric compacted under pressure to form the shape, facilitating its subsequent placement in the mould and ensuring that the desired percentage is possible [10].
The sequence of a liquid composite manufacturing process using a preform as an intermediate stage in the manufacturing process is shown in the following images (Figure 2): (a) and (b) perform manufacturing by hot forming and stitching; (c) preform manufacturing by joining ribs and skin; (d); placement of preform and inserts in the mold; (e) closed mold ready for RTM process (f) finished part.
In this context, TECNALIA has been immersed in the composite world for 40 years and has been working with Additive Manufacturing in this field of materials for the last 5 years. Its knowledge of materials and manufacturing processes is extremely broad, covering both thermosetting and thermoplastic composites technology. TECNALIA is therefore capable of approaching Additive Manufacturing in this field from a privileged position, knowing how to introduce it in areas where clear benefits are truly provided. One of these areas is preforming.
This article details the work developed by TECNALIA on the manufacture of preforms using the FDM additive process. TECNALIA has patented ADDICOMP technology, which consists on preforms manufacturing by printing filaments formed by continuous carbon or glass fibre roving, coated with thermoplastic polymer. These filaments are manufactured using the cable extrusion process, where the copper wire has been replaced by the carbon or glass roving.
The key advantage and the innovation of this technology is that this new filament contains a very high percentage of fibre by volume (around 90%) and offers the advantage of printing preforms, that subjected to subsequent liquid composite manufacturing processes, allows obtaining composite final parts with a fiber content between 65 and 75% in volume.
This development has three phases which are described below, following an introduction to the technology: development of continuous fibre filaments by extrusion (Section 2.1); setting up the FDM additive technology for these continuous fibre filaments (Section 2.2); and selecting the thermostable matrix-thermoplastic binder blend (Section 2.3). Once the thermoplastics binder has definitely been selected, the manufacturing and characterization of composite parts produced from preforms made by FDM printing will be done. Until now, only some manufacturing tests without testing were carried out. This work is currently being carried out and publications will be made as results are obtained.
TECNALIA has patented the manufacture of preforms (ADDICOMP) by printing filaments formed by continuous reinforcement fibre roving (CF or GF) coated with thermoplastic polymer, using FDM additive technology. This technology is based on extruding the material through a nozzle and subsequently depositing it in successive layers, so the extrusion of these filaments will allow this type of preform to be manufactured [12]. This preform will later be used as a reinforcement material in liquid composite manufacturing processes.
The continuous fibre additive preforming technology (ADDICOMP) focusses on obtaining structural composites of geometrical complexity (see Figure 3) with mechanical performances similar to those obtainable through composite infusion moulding or RTM processes. To do so, an essential step is to ensure the absence of the porosity typical of additive technologies that do not apply consolidation pressure at the same time the material is deposited.
To eliminate the risk of porosity in the final part, the preform is printing without pressure to be subsequently impregnated by a liquid resin in a conventional composites liquid processes (Infusion or RTM) or consolidated with pressure and temperature in a compression process of thermoplastics The main technical challenge of this technology has been to develop printable filaments using a modified FDM process. The development of these filaments has involved: (1) minimizing the percentage of binder or plastic coating that enables printing; (2) configuring the reinforcement to ensure its subsequent wettability with the resin; (3) selecting binder-resin combinations that do not impair the mechanical properties of the composite obtained; (4) adapt the equipment and software to the new requirements of filaments consisting mainly of continuous fibre.
Figure 4 represents the different filament and nozzle configurations that FDM technology presents and that determine the printing process. The first figure represents the printing of a polymer filament. The second figure is the printing of a filament of continuous fibre roving with polymer to obtain a composite final part. The fiber content in this filament and in the final part is around 30% in volume. And the third figure represents the filament of ADDICOMP technology to obtain preforms, no final parts, where the fiber content in the filament is around 90%.
Printing impregnable preforms requires significant software and hardware modifications. The post-processing (impregnation) requirements of infusion or RTM processes are also critical to obtain a composite final part with a fiber content of 65%–75% in volume.
Figure 5 shows the advantages of manufacturing preforms using ADDICOMP technology, as an alternative to the conventional compression process, based on a comparative cost estimate of the two manufacturing processes. The manufacturing of preforms in the conventional compression process requires of expensive materials, fabrics of carbon or glass fibre, and their placement and adaptation to the mold (fabric cutting, stacking and compression) (Figure 2) while ADDICOMP technology only requires the continuous fiber roving filament coated with thermoplastic polymer and the FDM printer.
Furthermore, ADDICOMP technology allows complex shapes such as hollow or deep parts to be printed, which would be impossible to do using conventional methods. Topological optimization can be applied to the part design and therefore reduce thicknesses, surfaces, etc., and it does not generate excess material. This optimization means an important saving in material costs and labour.
The manufacture of preforms using FDM technology has meant two major technological challenges. The first one is the development of this type of filaments using conventional extrusion processes, and the second is the development of the FDM technology itself for printing these filaments.
ADDICOMP has required the development and set-up of 3 technological lines: (1) development of continuous fibre filaments by extrusion; (2) setting up the FDM additive technology of the continuous fibre filaments; (3) selecting the thermostable matrix-thermoplastic binder blend and printing impregnable preforms.
The methods and materials used to develop continuous carbon fibre filaments coated by thermoplastic polymer are Carbon Fibre Tenax-E HTS40 24K 1600TEX as filament reinforcement, and Polycarbonate MAKROLON ET3137 and Polyurethane DESMOPAN® 3660DU as filament coating. A conventional extrusion process is used to manufacture the continuous carbon fibre filaments.
FDM technology is used as the additive manufacturing method to print the continuous carbon fibre filaments and a Dynamical 3D DT Lite model printer is used.
In the test carried out in the task of Selecting the thermostable matrix-thermoplastic binder blend, the epoxy resin used is RESOLTECH 1800/1805 and the different binders used were: Styrene-Acrylonitrile (SAN KIBISAN® PN-127 L100 FG), polycarbonate (PC TARFLON™ #1900), styrene-butadiene-styrene (SB Dynasol C-540S), styrene-ethylene-butadiene-styrene (SEBS Kraton™ G), low molecular weight polycaprolactone (PCL6250), high molecular weight polycaprolactone (PCL6800), polyoxyethylene (POE), polycaprolactone-based polyurethane (TPUPCL), polyamide (PA6), ether-based polyurethane (TPU3660) and ester-based polyurethane (TPU5996). All these resins are commercial except for TPUPCL, which has been synthesized by TECNALIA ad-hoc for our process.
The methods used in this selection task are based on the determination of Hansen solubility parameters, based on Hansen and Van Krevelen's theory of intermolecular forces based on the surface tension energy.
Conventional extrusion processes, optimized for the electrical wiring industry, have been used to develop this type of filament, in which the copper wires are replaced by carbon or glass wires, and the coating is selected according to the matrix to be used to manufacture the composite component. The objective is that the matrix, generally epoxy resin, dissolves the filament coating, leaving the carbon or glass reinforcement bare. Subsequently, it can be properly impregnated by the resin through processes such as Infusion, RTM, etc., thus obtaining the final part with an appropriate percentage of fibre.
The developed filaments have a total diameter of 1.75 mm. They are formed by a carbon or glass core coated with a thermoplastic polymer, where the percentage of reinforcement reaches 90% (Figure 6). The function of this coating is exclusively that of a vehicle to be able to print the reinforcement threads, and therefore an adequate amount should be used for this purpose. The materials used as coating materials included polycarbonate and thermoplastic polyurethanes given their solubility in epoxy resin.
The FDM printer used to set up the printing process of these filaments was a Dynamical 3D DT Lite model (Figure 7) modified to reach a higher temperature, with a printing volume of 600 mm × 450 mm × 450 mm. This printer was selected due to the possibility of working with Gcode files generated in slicer programs such as Simplify3D, which is essential when conducting R and D activities as it provides control over practically all printing parameters. Another advantage of this type of slicer is that the Gcode generated can be read later and modified to include cutting points or other functions required for continuous fibre printing that are not available in current slicers. The easy access to elements such as extruders and hotends has also been decisive when choosing this printer since modifications have been made to both to adapt them to this filament.
This printer offers technical specifications such as the maximum temperature that the material can reach in the extruder is 300 ℃, the chamber reaches a temperature of up to 50 ℃ and the printing bed 120 ℃, there is a wide range of available nozzle diameters for the extruder (0.2/0.4/0.6/0.8/1/1.2 mm), and it has two independent extruders capable of printing in single, dual, twin and reflex modes.
Numerous impediments were faced when adjusting the printing process. These included the type and thickness of the coating which are not common among printable materials using this technology, and multiple equipment software parameters needed to be modified. Other issues faced included the difficulty of the continuous fibre to cross the nozzle and be deposited, the excessive pressure exerted by the extruder gears on the filament, coating cracking, exposed filaments, the difficulty of turning the filament during printing, and the need to introduce a cutting tool in the printing process.
The following image (Figure 8) shows the appearance of the printed carbon filament. This filament is constituted by a core of carbon yarn coated with polycarbonate. The image clearly shows how the filament has a very high percentage of carbon compared to that of the polymer that covers it.
This section is a brief introduction to the study of the molecular interactions of the matrix-binder blend to select an appropriate binder for each thermosetting matrix. This is a complex process that is widely documented in the literature [13,14] but never in the framework of additive manufacturing of preforms. Moreover, these studies consider previous mixing through mechanical stirring, temperature and/or dissolution [15]. Due to the characteristics of our post-processing (infusion) of the preform, the matrix-binder interaction is governed by conditions that hinder the diffusion of the preform through the matrix-binder. Thus, we believe that this study presents an innovative and particularly useful approach within the framework of the additive manufacturing of continuous carbon fibre preforms. On the one hand, some limitations have been found in this context, and some assumptions have also been made which are imposed by the patented filament technology. For example, the amount of binder should be less than 10%, which limits the field of visibility in experimental trials when working with such small proportions. On the other hand, it must be considered that the binder must not only have good miscibility with the matrix but must also be printable. An example of a binder that has been pre-selected is polycarbonate (PC), as it is similar in structure to DGBA.
It should be noted that it is not a matter of reinforcing the matrix. Our interest lies in obtaining a final part with as little binder as possible in which the binder dissolves in the matrix in the base case scenario. The pre-selected set of thermoplastic binders was as follows: Styrene-Acrylonitrile (SAN), PC, styrene-butadiene-styrene (SBS), styrene-ethylene-butadiene-styrene (SEBS), low molecular weight polycaprolactone (PCL6250), high molecular weight polycaprolactone (PCL6800), polyoxyethylene (POE), polycaprolactone-based polyurethane (TPUPCL), polyamide (PA6), ether-based polyurethane (TPU3660) and ester-based polyurethane (TPU5996). As noted, these binders are commercial except for TPUPCL, which has been synthesized by TECNALIA ad-hoc for our process.
Some of the tests to carry out the selection have been based on determining the following experimental parameters: (1) dissolution test of the binders in the matrix-in the experimental test, the binders that dissolve best (transparent vial) in the resin are identified; (2) Hansen solubility parameters, based on Hansen and Van Krevelen's theory of intermolecular forces based on the surface tension energy [16,17]; (3) optical microscopic analysis of TP-EPOXY compatibility under conditions of our vacuum resin infusion.
This test consists of mixing each of the thermoplastics with the resin prior to catalysation for solubility analysis. Figure 9a shows different vials after mixing. The amount of thermoplastic comprises a range of 1–10% by weight of the total mixture. An example of incompatibility is shown in Figure 9b, where the SBS thermoplastic has been mixed with epoxy resin. It can be seen how the rubber particles float on the surface of the resin indicating that this mixture is not soluble.
Hansen divides the solubility parameter (HSP) into three contributions: (1) nonpolar or dispersion bonds δd, (2) polar or dipole-dipole bonds δp and (3) hydrogen bridge bonds δh, as Eq 1:
δ2=δd2+δp2+δh2 | (1) |
Each of these contributions determines an axis in a three-dimensional (3D) space called Hansen space. To compare TP_EPOXY compatibility, another parameter R0 is required, which is the radius of the solubility sphere of the resin and can be calculated empirically. An approximation of the 3D Hansen space has been graphically depicted in Figure 10, where the solubility sphere of EPOXY is shown in purple color. According to the theory, any TP within the sphere is expected to be soluble in EPOXY.
To obtain these parameters, an attempt is made to dissolve each thermoplastic polymer in various solvents of a different chemical nature, after which the optimization problem proposed by de los Ríos et al. [18] is solved. For the interpretation of the results, the thermosetting matrix (epoxy resin) has been considered as a solvent and the different thermoplastic binders as solutes. In Figure 10, the theoretical Hansen parameters found in [16] have been plotted. It can be seen how some binders (PC, POE, etc.) fall within the reactivity radius of the "epoxy" matrix. PA6 is a clear example of intermolecular incompatibility between the solvent-solute pair.
In order to observe if the TP's are miscible in EPOXY, an optical microscopic analysis has been carried out. In this work, we have focused on the EPOXY-PC pair. Here, the experimental protocol has been determined by the conditions of the resin vacuum infusion process, which is the key moment when is important the dissolution of the binder in the resin. For this purpose, PC powder was mixed at 10% by weight with the resin, without hardener, at room temperature. Then, a drop was taken with a pipette, making sure that it incorporated binder, and placed on the Microscope slide. From there, the sample was subjected to a heating sweep, always under the conditions of the process. Frist, it was heated for two minutes at 60 degrees to simulate vacuum infusion and then ninety minutes at 90 degrees, simulating the curing of the composite in the oven.
In Figure 11, images of three-time instants, each corresponding to one step of the experiment are shown. As the temperature increases over time, the PC disappears in the resin, indicating a certain miscibility.
The preforms obtained from the carbon continuous filament printing are showed in this section. These results are preliminary and qualitative. The optimization of preforms printing and the composites parts manufacturing from these preforms are now in progress.
The main goal of this section is to introduce a brief description of the printing process of impregnable preforms to use in liquid composite manufacturing process for composites manufacturing. Here, the type of preforms that have been printed respond to structures that are difficult or impossible to manufacture by the conventional process currently used. The following images are examples of this: Figure 12 shows ribbed structures that are also called isogrids. These are optimized geometries to provide stiffness and reduce weight. It has been possible to manufacture this preform by FDM printing the carbon filament. Once impregnated with resin, by means of either infusion or RTM processes, this preform will produce a rigid and light structure, an alternative to current isogrid structures that are generally manufactured in aluminium and by machining.
Figure 13 shows two preforms, the smaller of which represents the shape of a test tube. In this specimen the different printed layers arranged in perpendicular directions can be distinguished. A cut needs to be made in the filament to move from one layer to the other. The larger piece represents the preform of an automotive component. Its complex geometry and hollow nature prevent it from being manufactured by the conventional process, but it is feasible to do so using FDM.
Multi-material and multi-functional structures can be printed as more than one extrusion nozzle is available on the same equipment. An example is the structures shown in the image below (Figure 13).
The parts shown in Figure 14 represent structures that could be called "self-tooling". The outside is made of a pure polymer filament, acting as a mould. The inside corresponds to a preform consisting of 90% carbon filaments. Resin could be injected into the polymer cavity in such a way that it impregnates the inner preform. Once the resin has cured, the outer polymer layer would be removed, and the composite part would be obtained. This development is currently in the optimization phase. From the point of view of materials, we are working mainly on the selection of the most suitable coating material for the continuous carbon fibre, based on solubility studies of the coating/epoxy resin and on the polymer/carbon ratio suitable for further processing. From the process point of view, the first composite moulding tests are being conducted using the infusion process to determine the percentages of carbon fibre and percentage of voids that could be obtained.
From the development approached so far it can be concluded that: (i) filaments formed by continuous fibre coated with polymeric material with a high fibre content (90%), printable using FDM technology, can be obtained using an adapted conventional extrusion process. This method is novel in the field of additive manufacturing of continuous fibre and adds another option to the technologies already identified; (ii) FDM printing of these continuous fibre/polymer filaments makes it possible to manufacture "performs" that will allow composite components with complex shapes to be manufactured, which cannot be obtained by other processes; (iii) this printing process could be scaled by replacing the printing equipment used (Dynamical Tools) with a robot to which an extrusion head could be implemented. This would allow large components to be manufactured, in addition to manufacturing complex components; (iv) the manufacturing process of preforms using FDM technology offers an economic advantage compared to the conventional compression process.
The future development of this additive preform manufacturing process is oriented to: (I) Optimizing filament manufacturing by identifying the most compatible coating with further processed resin and adjusting the continuous carbon fibre/polymer ratio to ensure the best possible wettability and least possible interference in the subsequent composite moulding process. These achievements would benefit the properties of the final component. (II) Developing tools (software and hardware) capable of designing, improving and controlling the printing process. (III) Establishing the appropriate parameters and processing conditions in the moulding of composites via liquid processes (RTM or infusion), using preforms manufactured by FDM additive processes to obtain a composite component that meets the required conditions of reinforcement and porosity percentage. (IV) Extending this additive technology of continuous fibre filament extrusion coated with thermoplastic material to the manufacture of 3D thermoplastic preforms processable by thermoforming technologies typical of thermoplastic composite materials.
The authors declare no conflict of interest.
[1] | Mutel F (2017) Trends and opportunities in the Composites industry. XXIII Technical Conference CEP Composites. Available from: https://www.interempresas.net/Plastico/Articulos/189333-Los-composites-ganan-terreno-en-sectores-industriales-muy-diversos.html. |
[2] | The World's Largest Market Research Store, Fiber reinforced composites market by fiber type, resin type and end-user industry: Global opportunity analysis and industry forecast, 2020-2027, 2021. Available from: https://www.researchandmarkets.com/reports/5321542/fiber-reinforced-composites-market-by-fiber-type. |
[3] |
Ngo TD, Kashani A, Imbalzano G, et al. (2018) Additive manufacturing (3D printing): A review of materials, methods, applications and challenges. Compos Part B-Eng 143: 172-196. https://doi.org/10.1016/j.compositesb.2018.02.012 doi: 10.1016/j.compositesb.2018.02.012
![]() |
[4] | Mafel A (2021) Introduction to the additive manufacturing of fibre-reinforced composite. JEC Compos Mag, 6-13. |
[5] | Gardiner G, The evolution of additive composites, CompositesWord, 2021. Available from: https://www.compositesworld.com/articles/the-evolution-of-additive-composites. |
[6] |
Roan Eagle IN, Yodo N (2021) A review on filament materials for fused filament fabrication. JMMP 5: 69. https://doi.org/10.3390/jmmp5030069 doi: 10.3390/jmmp5030069
![]() |
[7] | Gardiner G, Mason H, 3D printing with continuous fiber: A landscape, CompositesWord, 2020. Available from: https://www.compositesworld.com/articles/3d-printing-with-continuous-fiber-a-landscape. |
[8] | Gardiner G, The evolution of additive composites, CompositesWord, 2021. Available from: https://www.compositesworld.com/articles/the-evolution-of-additive-composites. |
[9] | Gardiner G, Compression RTM for production of future aerostructures, CompositesWord, 2020. Available from: https://www.compositesworld.com/articles/compression-rtm-for-production-of-future-aerostructures. |
[10] | Maitane G, Mendizabal M, Ollo EO, et al. (2019) Method for additive manufacturing of a preform. European Patent 3827967A1. Available from: https://www.patentguru.com/EP3827967A1. |
[11] | Gayoso J, Harysmendi I, Mezzacasa R, et al. (2017) Development of preforming and RTM processes for highly integrated structures. Mater Comp 2: 69-74. Available from: https://revista.aemac.org/materiales-compuestos/article/view/149. |
[12] | Deng S, Djukic L, Paton R, et al. (2015). Thermoplastic-epoxy interactions and their potential applications in joining composite structures-A review. Compos Part A-Appl S 68: 121-132. https://doi.org/10.1016/j.compositesa.2014.09.027 |
[13] |
Launay H, Hansen CM, Almdal, K (2007) Hansen solubility parameters for a carbon fiber/epoxy composite. Carbon 45: 2859-2865. https://doi.org/10.1016/j.carbon.2007.10.011 doi: 10.1016/j.carbon.2007.10.011
![]() |
[14] |
Naffakh M, Dumon M, Gérard JF (2006) Study of a reactive epoxy-amine resin enabling in situ dissolution of thermoplastic films during resin transfer moulding for toughening composites. Compos Sci Technol 66: 1376-1384. https://doi.org/10.1016/j.compscitech.2005.09.007 doi: 10.1016/j.compscitech.2005.09.007
![]() |
[15] | Hansen CM (2007) Hansen Solubility Parameters: a User's Handbook, CRC press. https://doi.org/10.1201/9781420006834 |
[16] | Van Krevelen DW, Te Nijenhuis K (2009) Properties of Polymers: Their Correlation with Chemical Structure; Their Numerical Estimation and Prediction from Additive Group Contributions, Elsevier. |
[17] |
de los Ríos MD, Ramos EH (2020) Determination of the Hansen solubility parameters and the Hansen sphere radius with the aid of the solver add-in of Microsoft Excel. SN Appl Sci 2: 1-7. https://doi.org/10.1007/s42452-020-2512-y doi: 10.1007/s42452-020-2512-y
![]() |
[18] |
Zanjani JSM, Baran I, Akkerman R (2020) Characterization of interdiffusion mechanisms during co-bonding of unsaturated polyester resin to thermoplastics with different thermodynamic affinities. Polymer 209: 122991. DOI:10.1016/j.polymer.2020.122991 doi: 10.1016/j.polymer.2020.122991
![]() |
1. | John Kechagias, Dimitrios Chaidas, Fused filament fabrication parameter adjustments for sustainable 3D printing, 2023, 1042-6914, 1, 10.1080/10426914.2023.2176872 | |
2. | John D. Kechagias, Materials for Additive Manufacturing, 2022, 9, 2372-0484, 785, 10.3934/matersci.2022048 | |
3. | Jing Li, Qing Huang, Yajun Yin, Jigang Xu, Yimin Jiang, Wenjie Du, The technology and current applications of continuous fiber‐reinforced thermoplastic composites, 2024, 45, 0272-8397, 13480, 10.1002/pc.28764 | |
4. | John D. Kechagias, Effects of thermomechanical parameters on surface texture in filament materials extrusion: outlook and trends, 2024, 13, 2046-1402, 1039, 10.12688/f1000research.144965.1 | |
5. | Zhaosong Zhang, Chao Hu, Qing-Hua Qin, The improvement of void and interface characteristics in fused filament fabrication-based polymers and continuous carbon fiber-reinforced polymer composites: a comprehensive review, 2025, 0268-3768, 10.1007/s00170-025-15240-4 | |
6. | Enrique Hernández‐Murillo, Itziar Otaegi, Itxaso Calafel, Luis Palenzuela, Ricardo Mezzacasa, Cristina Elizetxea, Gonzalo Guerrica‐Echevarría, Nora Aranburu, Robert Aguirresarobe, Continuous carbon fiber Additive Preforming and its application for the fabrication of epoxy composites, 2025, 0272-8397, 10.1002/pc.29683 |