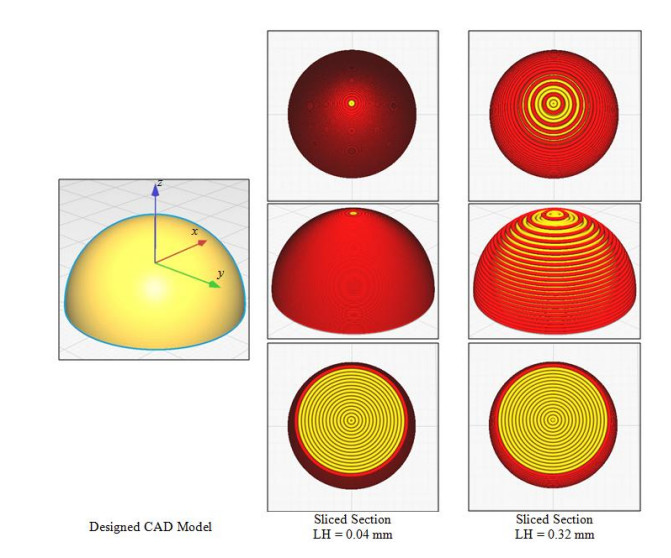
Citation: Mohammad S. Alsoufi, Mohammed W. Alhazmi, Dhia K. Suker, Mohammed Yunus, Rashad O. Malibari. From 3D models to FDM 3D prints: experimental study of chemical treatment to reduce stairs-stepping of semi-sphere profile[J]. AIMS Materials Science, 2019, 6(6): 1086-1106. doi: 10.3934/matersci.2019.6.1086
[1] | Mnvrl Kumar, R. Ramakrishnan, Alnura Omarbekova, Santhosh Kumar. R . Experimental characterization of mechanical properties and microstructure study of polycarbonate (PC) reinforced acrylonitrile-butadiene-styrene (ABS) composite with varying PC loadings. AIMS Materials Science, 2021, 8(1): 18-28. doi: 10.3934/matersci.2021002 |
[2] | Azhar Equbal, Ramesh Murmu, Veenit Kumar, Md. Asif Equbal . A recent review on advancements in dimensional accuracy in fused deposition modeling (FDM) 3D printing. AIMS Materials Science, 2024, 11(5): 950-990. doi: 10.3934/matersci.2024046 |
[3] | Bandar Abdullah Aloyaydi, Subbarayan Sivasankaran, Hany Rizk Ammar . Influence of infill density on microstructure and flexural behavior of 3D printed PLA thermoplastic parts processed by fusion deposition modeling. AIMS Materials Science, 2019, 6(6): 1033-1048. doi: 10.3934/matersci.2019.6.1033 |
[4] | M. A. Mendizabal, Maitane Garcia, Luis Palenzuela, Enrique Hernández . Obtaining preforms by additive fused deposition modelling (FDM) extrusion technology for the manufacture of high-performance composites. AIMS Materials Science, 2022, 9(3): 481-497. doi: 10.3934/matersci.2022028 |
[5] | Stelladriana Volpe, Andrea Petrella, Valentino Sangiorgio, Michele Notarnicola, Francesco Fiorito . Preparation and characterization of novel environmentally sustainable mortars based on magnesium potassium phosphate cement for additive manufacturing. AIMS Materials Science, 2021, 8(4): 640-658. doi: 10.3934/matersci.2021039 |
[6] | Mahdi Rafiee, Roozbeh Abidnejad, Anton Ranta, Krishna Ojha, Alp Karakoç, Jouni Paltakari . Exploring the possibilities of FDM filaments comprising natural fiber-reinforced biocomposites for additive manufacturing. AIMS Materials Science, 2021, 8(4): 524-537. doi: 10.3934/matersci.2021032 |
[7] | Subbarayan Sivasankaran . Influence of TiC addition on the surface roughness during turning of AA 7075 alloy processed through stir-casting. AIMS Materials Science, 2018, 5(4): 699-710. doi: 10.3934/matersci.2018.4.699 |
[8] | Leonid A. Kaledin, Fred Tepper, Yuly Vesga, Tatiana G. Kaledin . The effect of the surface roughness and ageing characteristics of boehmite on the removal of biological particles from aqueous solution. AIMS Materials Science, 2019, 6(4): 498-508. doi: 10.3934/matersci.2019.4.498 |
[9] | Huazhuo Liang, Jiabin Lu, Qiusheng Yan . Catalysts based on Fenton reaction for SiC wafer in chemical magnetorheological finishing. AIMS Materials Science, 2018, 5(6): 1112-1123. doi: 10.3934/matersci.2018.6.1112 |
[10] | Tomasz Blachowicz, Kamila Pająk, Przemysław Recha, Andrea Ehrmann . 3D printing for microsatellites-material requirements and recent developments. AIMS Materials Science, 2020, 7(6): 926-938. doi: 10.3934/matersci.2020.6.926 |
Rapid prototyping (RP) is a group of different technologies used to quickly fabricate a physical 3D model, functional testing prototypes and small batch size tools of printed samples directly from a 3D computer aided design (CAD) data file without tooling, machining, time consuming or involving considerable expenses [1,2,3,4]. The rapid growth of desktop/personal/end-user 3D printer is generally based on Stratasys’s Fused Deposition Modeling (FDM) technology [5]. It is an economically beneficial technology as it has a great potential to make a substantial reduction in the manufacturability time of the printed samples from 30 to 50% even if the sample is relatively having a high-level approximation of complexity [6]. The RP can be used for visualization, design verification, form and fit checking as well as to produce a tooling (or master) pattern for molding or casting [7]. Each printing process begins by slicing the 3D CAD file to compute the horizontal cross-sections at small increments of layer height (LH) of the object to be manufactured [8]. The layers are built vertically only one at a time from the bottom to the top layer. With RP machines, the lesser the LH, the better the surface roughness finishing quality, which is also affected by the angle between 0° to 180°, defining 0° to 90° as upward and 90° to 180° as downward direction to surface. The differences between the CAD file and fabricated sample occurs commonly known as the “stairs-stepping effect”, which is remarkable on an inclined printed surface. It is a non-horizontal or non-vertical surface approximated by stacked layers, causing deviations between model-surface and print-surface, especially at shallow angles. Furthermore, since the 3D solid model is estimated by a series of triangles (Standard Triangulation Language, STL format), this results are clearly in a chordal estimation error or defect that will affect negatively the smoothness of the surface profile. As a result, customers will occasionally request hand finishing for even the most basic levels of printed sample quality, with the result that the prototype’s geometrical features are strongly dependent on the operator’s talent [9]. In the literature review, a wide variety of approaches have addressed the problem of analysing, improving the dimensional accuracy and the surface roughness of RP parts [10,11].
In this research paper, the authors examine the relationship between the FDM 3D printing process parameters and the surface aspects of printed samples by applying a chemical treatment technique to enhance the surface finish quality of the printed samples. This technique performs better if compared to that reported in [9,12] as it needs average skilled man, cost-effective and short curing time. The trials were carried out at two phases, focusing on the main independent variables in both the FDM 3D printing process and the chemical finishing treatment. First phase is before and second phase after the chemical treatment. Finally, the authors use the developed decision support system for helping end-users and the designers in selecting the optimal printing process parameters such that FDM process overcomes the stairs-stepping effect of the semi-sphere problem.
In this section, the thermoplastic filament materials, equipment technology, printing process and procedures used in the production of the FDM 3D printed samples are described in detail.
The filament materials chosen are of the greatest significant and dominant for each Additive Manufacturing (AM) process. FDM with modeling materials [5] such as polylactic acid (PLA+ and PLA) and acrylonitrile butadiene styrene (ABS+) whose properties are described in [3]. They are known as thermoplastic filament materials. The filaments were purchased from eSUN (around $25 for one kilogram of the spool) which was initially founded in Shenzhen, China [13], with the outer diameter of 1.75 mm and tolerance of ±0.02 mm and used as received. The main advantage of this material is that it is easy to use in 3D printing and deliver the good results. In this study, investigations are to be made on PLA+, PLA and ABS+ over other thermoplastic filament materials as these filament materials worked with FDM 3D printer very well as well to explore the more significant approach to the knowledge of their behavior and material performance under the several printing process parameters. The best print temperature is from 205 to 225 ℃ for PLA+ and PLA, and from 220 to 260 ℃ for ABS+ which is based on the data sheet available in [13]. So, the maximum extrusion temperature point was chosen for all thermoplastic filament materials viz. 225 ℃ (for PLA+ and PLA) and 260 ℃ (for ABS+).
At the printer device level, the low-cost and end-user desktop FDM 3D printer used was a single spool of filament Original Prusa I3 MK3, PRUSA RESEARCH, Prague, Czech Republic. The printing method is based on FDM technology, which was developed by S. Scott Crump in the late 1980s [14]. The maximum printing size was 25 × 21 × 21 cm (length, width and height, respectively) with a great build volume of 11, 025 cm3. The FDM 3D system was used with a 0.4 mm nozzle diameter (E3D V6 brass nozzle) able to produce a minimum LH of 40 μm and a maximum LH of 320 μm, precisely driven by a computer-controlled platform system in Cartesian coordinates. The FDM 3D printer was equipped with an automatic mesh bed levelling (MBL), a heat bed and a cold corners compensation for warp less FDM 3D printing from PLA+, PLA and ABS+ filament materials. The power consumption was set at 80 W for both PLA+ and PLA and 120 W for ABS+. The printer has a calibration system of automatic 9 points XYZ/skew axes compensation. The FDM 3D printer was calibrated for this new fabrication technology and used to manufacture the samples.
At the computer level, two professional forms of software were used in this study (Autodesk® Inventor Professional 2019 and Ultimaker Cura® 2019). The CAD file were drawn and visualized in Autodesk® Inventor Professional 2019 software with four groups. 3D semi-sphere shape with 15 mm dia. × 7.5 mm ht. (group A), 20 mm dia. × 10 mm ht. (group B), 25 mm dia. × 12.5 mm ht. (group C) and 30 mm dia. × 15 mm ht. (group D) and transferred to the 3D printable format using the Cura® software (open-source software). The Ultimaker Cura® 3.6 edition (www.ultimaker.com) was used to generate the machine source code for the end-user FDM 3D printer from the 3D CAD model. Twenty-four printed samples were chosen for the final assessment. Figure 1 shows the standard test semi-sphere modeled in Autodesk® Inventor Professional 2019 and the Ultimaker Cura® 2019 software. Hence, the geometric differences occur commonly between the CAD file and the fabricated sample are known as the “stairs-stepping effect” present remarkable behavior on an inclined surface profile as appear clearly on a semi-sphere printed sample. The stairs-stepping effect can be reduced significantly by minimizing the LH, but this increases the printing time necessary to accomplish the fabrication printing process. The stairs-stepping effect has a significant influence on the overall surface quality finish of RP processed parts. The average surface roughness steadily changes as the angle of the inclined surface profile increases. Since the value of the surface roughness (Ra) is a dependent variable on the surface profile angle, the actual characteristics of the Ra distribution with different surface diameters (15, 20, 25 and 30 mm) must be investigated in advance.
Several printing sample runs were first accomplished to find out the optimal printing process parameters with PLA+, PLA, and ABS+. So, the printing process parameters were adopted by experimental values. All of the selected parameters were ranked as the most influential printing process parameter in the cited research papers. Table 1 shows the comprehensive outlines of the FDM 3D printing process parameters used throughout the experiment. The unaffected parameters are fixed at default settings of software. The independent printing temperature, T, was set at 225 ℃ for both PLA+ and PLA, and 260 ℃ for ABS+ as recommended by the FDM 3D printer manufacturer. The independent LH was set at 0.04 and 0.32 mm for all groups shown graphically in Figure 2. The build plate temperature was set at 60 ℃ to help the printed samples to stick on and later cooled to 10 ℃. All FDM 3D samples were printed on a raft. Certain parameters such as wall thickness, infill density, infill pattern and printing direction were fixed for all the printed samples to focus on the influence of the previous process parameters. The infill pattern takes discrete string values. The Cura software is capable of implementing more than twelve different infill pattern types but, only the concentric circle pattern was used for the optimization. The concentric circle patterns are circles with a common center follow the entire semi-sphere pattern. The infill density for FDM 3D printed samples are chosen at the highest responsible level (100% infill density). It is noted that, various manufacturing process parameters set by Cura software along with configuration related have unaffected the printed part properties. The printing process parameter levels are carefully chosen based on the scholarly papers, experience, their implication and significance according to the initial pilot investigations allowing the high and low levels recommended by the equipment manufacturer. In this research paper, the LH is the independent build parameter also known as layer thickness or slice height. It is the height of the extruded layer by an extrusion head. The values of LH are based on the model filament material, and the nozzle diameter used. Higher values of LH produce faster prints with lower resolution and vice versa (refer Figure 2). LH can affect the top and bottom layers, minimum skin width for expansion, regular fan speed and support infill layer, raft top and raft middle layer as noticed near horizontal surface profiles introduced more error than near vertical one [15,16].
Setting | Parameters | Unit | Values | |||
Quality | Layer height | mm | 0.04 | 0.32 | ||
Shell | Wall thickness | mm | 0.4 | |||
Wall line count | - | 1 | ||||
Top/Bottom thickness (mm) | mm | 0 | ||||
Top thickness | mm | |||||
Top layer | - | |||||
Bottom thickness | mm | |||||
Bottom layer | - | |||||
Infill | Infill density | % | 100 | |||
Infill pattern | - | Concentric | ||||
Infill line direction | ° | - | ||||
Infill overlap percentage | % | 25 | ||||
Infill layer thickness | mm | 0.1 | ||||
Nozzle | Nozzle size | mm | 0.4 | |||
Compatible material diameter | mm | 1.75 | ||||
Nozzle offset x-axis | mm | 0 | ||||
Nozzle offset y-axis | mm | |||||
Material | Filament type | - | PLA+ | PLA | ABS+ | |
Filament colour | - | Dark blue | Light blue | Black | ||
AM process | - | FDM (fused deposition modeling) | ||||
Printing direction | - | Flat on platform (on printing table) | ||||
Printing temperature | ℃ | 225 | 260 | |||
Printing temperature initial layer | ℃ | |||||
Material | Initial printing temperature | ℃ | ||||
Final printing temperature | ℃ | |||||
Build plate temperature | ℃ | 60 | ||||
Build plate temperature initial layer | ℃ | |||||
Flow | % | 100 | ||||
Initial layer flow | % | |||||
Retraction distance | mm | 0.8 | ||||
Retraction speed | mm/s | 35 | ||||
Speed | Print speed | mm/s | 30 | |||
Infill speed | mm/s | |||||
Wall speed | mm/s | 15 | ||||
Outer wall speed | mm/s | |||||
Inner wall speed | mm/s | 30 | ||||
Top/Bottom Speed | mm/s | 15 | ||||
Initial Layer Sped | mm/s | |||||
Cooling | Fan speed (%) | % | 100 | |||
Build Plate Adhesion | Build plate adhesion type | - | Skirt | |||
Skirt lin count | - | 1 | ||||
Skirt distance | mm | 3 | ||||
Skirt/Brim minimum length | mm | 250 | ||||
Environmental Condition | Room temperature | ℃ | 23 ± 2 | |||
Relative humidity | % RH | 50 ± 10 |
Twenty four FDM 3D printed samples (refer Figure 3) were manufactured with independent printing process parameters to compare the Ra aspect and density. In the current study, all semi-sphere printed parts were tested for each group A to group D. Each group was printed with a LH of 0.04 and 0.32 mm. Moreover, PLA+ and PLA were printed at an independent printing temperature of 225 ℃ and for ABS+ at 260 ℃ and constant printing speeds of 30 mm/s. During the printing processes, there were no issues with clogged nozzles or material jams. Figure 4 shows the sample details of printed parts for the LH of 0.04 and 0.32 mm with a printing process time. At both LH values, the increased in number of layers almost doubled while the printing time was increased by 85% and 88% respectively for each LH value as depicted in Table 2. The overall printing process time is highly dependent on many process parameters. Two vital manufacturing process parameters are the nozzle diameter (0.4 mm) and the infill density (100%).
No. | LH (mm) | Number of layers | Printing time (min) | Change in diameter (mm) | Increase in layer | Increase in printing time |
1 | 0.04 | 183 | 23 | 15 | Doubled | 85% |
371 | 183 | 30 | ||||
2 | 0.32 | 24 | 3 | 15 | Doubled | 88% |
47 | 24 | 30 |
All FDM 3D printed samples were subjected to a chemical treatment process. The chemical bath was selected according to the following considerations like PLA+, PLA and ABS+ as thermoplastic filament materials, a low reticulation degree, nitrile functionality having weak interaction and polar solvents such as dimethylketone (acetone). In this study, dimethylketone (Sigma-Aldrich, St. Louis, MO) was selected due to its cost-effectiveness, very high diffusion, and very low toxicity.
Difficult to control the process using pure dimethylketone requires deionized water to be added into the bath (18.2 MΩ cm, Milli-Q system, Millipore, MA) due to its high mixability with acetone. A highly accurate trial and error procedure was performed to notice suitable values of the independent variables (i.e., concentration and immersion). The process consisted of immersion of dry fabricated PLA+, PLA and ABS+ into a glass jar at a volume of 80% pure dimethylketone (acetone) and 20% deionized water for 5 min, as shown in Figure 5. Following the immersion procedure, the prototypes were removed using tweezers and allowed to dry at room temperature for 24 h. All FDM 3D printed samples sizes were measured before and after the chemical treatment to evaluate the variations in terms of the stairs-stepping effect. The Ra and the density of all printed samples were also measured to evaluate the improvements.
In the profile inspection(raw and modified), a declared precision of almost 0.7 mN low contact force, 50 nm high sensitivity displacement and a small stainless steel tip radius of a 2 μm stylus being used on FDM 3D printed samples. The distribution of Ra for potential irregularities of the 100% infill density FDM 3D printed samples were assessed by a conventional contact-type Taly-Surf® surface roughness profilometer from Taylor Hobson Precision, Inc. to measure FDM 3D samples affected by stairs-stepping effect and characterized by a wide peak to valley height. The inspections were completed under the fundamental friction and wear-free, high-precision, and high-accuracy measurement. It provided high spatial resolution downcast to 0.8 nm, an exploratory measuring instrument range (x-axis) of 12.5 mm, and linear mode speed up to 0.5 mm/s or higher. The traces were auto-leveled in terms of direction and set-up to a linear least-squares (LLS) fitting technique (single scan mode). After this, it is filtered with a standard low-pass filter (LPF) of 0.8 mm effective cut-off wavelength. Full details of the measurement procedure have been reported in [1,2,3,4,17]. The calibration results are measured after a series of trials under various working and eco-friendly issues with an absolute value of each uncertainty at less than 1% using a standard ball of 22.0161 mm dia. The results obtained for one-end cantilever beam system having a linear mass-spring system showing regression, R2 > 0.99 and displacement resolution at worst performance of 50 nm.
For proper positioning of specimens, a simple specimen holder was designed and built on a 3D printer using a PLA+ thermoplastic filament material (refer Figure 6a and the measurements were conducted in steps of 10 mm over the printed samples (refer Figure 6b). The measuring direction was vertical to the stairs-stepping. The assessment was conducted at least three times at different locations. The average of three measured values was taken as Ra, Rq, Rsk, Rku and Rq/Ra for each output.
All FDM 3D printed samples were tested for different printing process parameter settings. The Ra results obtained at different locations and the calculated average of it.
Many significant variables can be used to evaluate the quality of finishing of printed part. In this research, Ra, Rq, Rsk, Rku and Rq/Ra and density (weight and volume) parameters are evaluated. After printing the Original Prusa I3 MK3 model, the test specimens were conditioned at normal room temperature of 23 ± 2 ℃ and relative humidity of 50 ± 10%. Then measurement carried using the digital Vernier gauge after the three days of manufacturing and removing from the build platform surface. Every dimension was measured at least three times at a different location, and the average value was considered. The standard deviation (±SD) for each dimension of the printed samples was calculated statistically and presented in the form of the mean and standard deviation (mean ± SD). Also, the surface chemical treatments increases model printing time and lead to a degradation of the geometrical definition of the model. The geometrical differences gap occurs between the original CAD data model and the fabricated semi-sphere samples because of the stair-stepping effect. It may be another potential cause of dimensional inaccuracy. Explanations of the investigations are discussed in greater detail in the following sub-section.
Figures 7 and 8 show the raw and modified profile of the semi-sphere FDM 3D printed sample before and after chemical treatment over a 10 mm measuring distance using a contact-type measurement procedure. Figures 7a and 8a show clearly the stairs-stepping effect behaviour at LH = 40 and 320 μm respectively for profiles before and after chemical treatment. Each stair is ~50 μm height and ~300 μm respectively. As the printing system reached the top layer, the stairs-stepping becomes more evident and nozzle diameter (0.4 mm) plays a very significant role in determining the Ra aspects. Particularly, the last layer of printing at LH of 0.04 mm cannot follow pattern because of the differences in the dimensions. It is also self-evident that the depositions of layers are close to an elliptic curve once get completed. This fact has been reported in [18,19].
Figures 7b and 8b show the modified profile of semi-sphere FDM 3D printed sample before and after chemical treatment with frequent narrower peaks to valleys distribution. It also shows a sinusoidal pattern. This pattern suggests that the LH may be one of the significant features in the prototype surface. Also, a similar trend was observed on other inclined surfaces at different diameters (15, 20, 25 and 30 mm) and with different materials (PLA+, PLA, and ABS+). Based on the frequency values, it is hypothesized that the main root cause is attributed to the LH. In general, the Ra improved by ~20% when the surface profile was exposed to chemical treatment (acetone) for 5 min. The frequent peaks to valleys variation were minor and relatively very small. The data generated from Figures 7b and 8b revealed that the Ra at different LH is in the range as shown in Table 3. However, as a 3D FMD sample is fabricated by depositing extruded filaments, therefore, it seems that the surface profile of the printed samples is different from that of the STL sample. Since the cross-sectional shape of the thermoplastic filament material resembles a curve (an ellipse or a parabola), surface profile variation along the surface angle would not be following that of another RP. With this, the shrinkage phenomenon is quite visible on the printed samples. This happens due to the rough temperature difference of the deposited material (225 and 260 ℃) and the deposition platform has temperature of 25 ℃. In general, the Ra improved by ~40% when the surface profile was exposed to chemical treatment having LH = 300 μm, which is twice when compared with ~20% at LH = 40 μm. This proves that the chemical treatment procedure has an impact on the stairs-stepping effect. Moreover, a wider peaks-to-valley indicates that there is a gap (or positive gap) between deposited layers. The thick layer (LH = 0.32 mm) had produced a rougher surface than the thin layer (LH = 0.04 mm) whether measured vertically or horizontally.
No. | LH (mm) | Chemical treatment | Raw surface profile (μm) | Modified surface profile (μm) | Ra improvements |
1 | 0.04 | Before | Ra = 8.3762 | -17.28 < Ra < +17.06 | ~20% |
After | Ra = 33.1254 | -15.94 < Ra < +16.96 | ~20% | ||
2 | 0.32 | Before | Ra = 6.6530 | -126.01 < Ra < +89.97 | ~40% |
After | Ra = 18.5529 | -98.75 < Ra < +85.13 | ~40% |
Thus, this result indicates that at LH = 0.32 mm, every horizontal surface (side face) is better than the vertical surface (top face). This is due to the formation of elliptical curves or fillet on the down-facing surface during layer-bonding.
Figures 9 and 10 show the Ra of semi-sphere profile at same processing parameters before and after the chemical bath treatment and its roughness was measured on a single contact-scan mode (gauge length of 10 mm). At LH = 40 μm, many thin layers (183, 246, 308 and 371 layers w.r.t their diameters) are required to manufacture the samples for increasing the non-uniform temperature in it as more thermal cycles are needed. This causes some voids and pinholes in the interior part, resulting in weaker parts and more brittle structure. At LH = 320 μm, few thick layers (24, 32, 39 and 47 w.r.t their diameters) will reduce the number of layers and hence a least number of thermal cycles are required to build the samples subjecting to minimum part distortion. The Ra was seen decreasing with 300 s acetone treatment for all filaments (PLA+, PLA, and ABS+) indicating that the stairs-stepping effects were almost removed from the surface, especially for ABS+. Also, PLA+ and PLA follow the same pattern where 20 and 25 mm diameter of semi-sphere represents the highest while 15 and 30 mm diameter represents the lowest Ra in case of LH = 320 μm. Whereas in case of LH = 40 μm, 15 mm diameter represents the highest while 30 mm diameter represents the lowest Ra. Printing will take much longer to print the semi-sphere and more thermoplastic filament material, which increases the cost of the printed samples. The 20 and 25 mm diameter of semi-sphere showed fluctuated surface roughness behavior. The total mean and standard deviation value (mean ± SD) of each filament before and after treatment are shown in Figure 9a–c with ~35%, ~11% and ~39% reduction in Ra values at LH = 40 μm respectively. Figure 10a–c show ~30%, ~22% and ~42% reduction in Ra values for each filament respectively at LH = 320 μm (refer Table 4). Although PLA showed low Ra behavior before and after chemical treatment, the total reduction was very low, indicating that the stairs-stepping effects are more likely to be significant. The remaining peaks-to-valleys are more visible on the surface profile in comparison to PLA+ and ABS+. It can be concluded that ABS+ reached the lowest Ra value of ~3.9092 μm after being exposed to chemical treatment at the lowest extrusion speed (30 mm/s) and LH = 0.04 mm. This produced finer grooves between each layer and layer interface with the total reduction in surface profile was around 36%. Each Ra distribution had its own characteristics such as several irregular steps and micro-sized burrs.
No. | LH (mm) | Chemical treatment | Mean and standard deviation (mean ± SD) μm | ||
PLA+ | PLA | ABS+ | |||
1 | 0.04 | Before | 10.2315 ± 1.1134 μm | 6.8746 ± 0.4603 μm | 8.0217 ± 1.0389 μm |
After | 6.6474 ± 0.4437 μm | 6.1273 ± 0.7169 μm | 4.9086 ± 0.9108 μm | ||
2 | 0.32 | Before | 43.8942 ± 10.7897 μm | 37.6168 ± 5.2260 μm | 45.4202 ± 7.9432 μm |
After | 30.8442 ± 9.8090 μm | 29.4950 ± 3.7771 μm | 26.3328 ± 3.6647 μm |
After chemical treatment, the stairs-stepping effect was almost removed by ~45% at LH of 320 μm and by ~5% more than at a LH of 40 μm. The total reduction in all filaments before and after chemical treatment was clearly indicating that the stairs-stepping effects more likely to be large and the remaining peaks-to-valleys more visible on the surface profile. These results confirmed that a LH of 320 μm (takes less building time) has a significant effect on the smoothing process using acetone treatment compared to 40 μm. As it can be understood (refer Figure 10) that by increasing the exposure time to chemical treatment more than 300 s, smoother Ra is obtained. But the total geometry (height and diameter) will decrease as chemical etching takes place more on as-polished 3D FDM printed sample.
Therefore, an increase in LH results is a significant rise in the stair-stepping effect. Thus, the surface finish increased with increase in LH and decrease in build time. So, it can be concluded that the stairs-stepping effect at LH = 0.32 mm is more substantial, and the remaining peaks and valleys are more visible on the surface in comparison to LH = 0.04 mm. This result confirms that LH has a significant effect on the result of the smoothing process by chemical treatment (i.e., acetone). It is indeed more evident at LH = 0.32 mm, particularly at the top surface of the semi-sphere printed sample due to the altered width of the thermoplastic filament material.
The author of this research paper has verified that even with chemical treatment (acetone) in the process, the Ra behavior for LH of 0.04 mm (Ra = 3.9092 μm) cannot reach the Ra behavior at LH of 0.32 mm (Ra = 18.5529 μm). This fact is in contradiction to the results obtained in the paper [20], where the authors state that, a higher LH takes lesser building time gives the final Ra is close to the lower LH.
In current case, the difference cannot be negligible even when the build time is of great importance, and the goal is to minimize it by giving up surface roughness. Furthermore, it has been reported that the typical values for Ra of an inclined surface that does suffer from a stairs-stepping effect at LH of 40 μm [21].
Figure 11 shows the Rq/Ra ratio performance of three filaments at LH = 40 μm. Particularly, the Rq/Ra ratio is satisfactory when its empirical value of ~1.22 (for a 2D geometric model) with a slight deviation. Leads to admirable surface profile ratio as the Rq parameter is much more sensitive to irregular high peaks and deep valleys of the assessed roughness profile than the Ra parameter because of the fact that the amplitudes of Rq are squared.
Geometrically, for PLA+, PLA, and ABS+, the maximum and minimum ratio Rq/Ra at different diameters listed in Table 5 with a total standard deviation (±SD) of ±0.12 and ±0.04 (PLA+), ±0.04 and ±0.03 (for PLA) and ±0.12 and ±0.04 (for ABS+) respectively.
No. | LH (mm) | Chemical treatment | PLA+ | PLA | ABS+ | |||
Maximum Rq/Ra (mm) | Minimum Rq/Ra (mm) | Maximum Rq/Ra (mm) | Minimum Rq/Ra (mm) | Maximum Rq/Ra (mm) | Minimum Rq/Ra (mm) | |||
1 | 0.04 | Before | ~1.51 at Φ25 | ~1.22 at Φ30 | ~1.27 at Φ15 | ~1.18 at Φ30 | ~1.52 at Φ15 | ~1.26 at Φ30 |
After | ~1.27 at Φ15 | ~1.19 at Φ25 | ~1.29 at Φ30 | ~1.21 at Φ20 | ~1.27 at Φ30 | ~1.17 at Φ15 | ||
2 | 0.32 | Before | ~1.3 at Φ30 | ~1.23 at Φ25 | ~1.28 at Φ25 | ~1.19 at Φ15 | ~1.36 at Φ30 | ~1.24 at Φ15 |
After | ~1.54 at Φ30 | ~1.18 at Φ20 | ~1.19 at Φ15 | ~1.23 at Φ25 | ~1.34 at Φ 20 | ~1.20 at Φ30 |
Figure 12 shows the Rq/Ra ratio performance of PLA+, PLA, and ABS+ at LH = 320 μm with an SD of ±0.03 and ±0.17, ±0.10 and ±0.04 and ±0.05 and ±0.06, respectively are tabulated in Table 5.
The values of Rq/Ra using data collected from the contact-type machine are reasonably close to the value of ~1.22 predicted by the theory, especially after chemical treatment with PLA (~1.21) at LH = 0.04mm and PLA+ (~1.23) at LH = 0.32mm. This result proved significant as it indicates that the asperity height distribution of these surfaces is approximately Gaussian and that the statistical relationships for Ra are applicable. For asperity height Gaussian distribution, the statistical theory (estimation and hypothesis testing) shows that the Rq/Ra should be ~1.22. The author in [22] mentions that the conditional height Gaussian distribution of most engineering surfaces (tribology) might be approximated by a Gaussian distribution with Rq/Ra of ~1.31.
The third-order central moment (measure for the degree of symmetry, positive or negative) and fourth-order central moment (measure for the degree of peakedness/flatness, tall or flat) in the variable distribution are skewness (Rsk) and kurtosis (Rku) respectively. Both provide instrumental data on the real surface distribution profile of the FDM 3D printed part, which includes skewness, Rsk, and kurtosis, Rku and discussed here in more detail.
Skewness, Rsk, is well-defined by ISO 4287 (1997) as it evaluates the degree of asymmetry distribution [23] and is categorized as positively skewed distribution (Rsk > 0 when surfaces are ‘empty’ of material) or negatively skewed distribution (Rsk < 0 when printed part surface profile is “full” of filament material). It is an essential parameter for micro and nano-tribological applications involving friction, wear, and lubrication. Normal distribution (Gaussian distribution) presents Rsk = 0 (symmetrical). Kurtosis, Rku, is also defined by ISO 4287 for evaluating the distribution sharpness with Rku = 3 (mesokurtic distribution) for the normal distribution. The surface profile is influenced by sharp peaks (spiky) surface when Rku > 3 (a leptokurtic distribution with a high degree of peakedness). While the surface profile is influenced by bumpy peaks surface when Rku < 3 (a platykurtic distribution with a low degree of peakedness). In this regard, Rku is a critical assessment parameter as regards to providing beneficial information on the real contact area of thermoplastic filament material and friction/wear resistance. Also, it is more likely to distinguish the periodicity of the surface profile assessment (Rku < 3).
Thermoplastic filament material showed both positive for steep peaks and flat valleys and negative skewed distribution for flat peaks and steep valleys before exposure to chemical treatment at minimum LH of 0.04 mm are as shown in Figure 13a. The distribution of positive and negative values indicates the existence of protruding grains. After exposure to chemical treatment as seen from Figure 13b, PLA+ and PLA showed the same kind of distribution except ABS+ which changed completely to negative skewed distribution indicates more resistance to friction and wear behavior, while a positive skewed profile indicates less resistance to tribological behavior. Moreover, negative values of the skewness indicate that the valleys are dominant over the scanned area. Continued negative values would indicate cracks, representative of valleys.
In contrast, thermoplastic filament materials (PLA+ and ABS+) show completely negative skewed distribution (-Rsk), while PLA showed both positive and negative skewed distribution before exposure to chemical treatment at maximum LH of 0.32 mm (see Figure 14a). After chemical treatment, almost all the surfaces behavior (for PLA+ and ABS+) fluctuated between positive to negative skewed distribution except PLA (refer Figure 14b).
The maximum and minimum approximate trend distribution of skewness range various filaments are shown in Figures 13 at LH = 0.04mm and Figures 14 at LH = 0.320 mm before and after the chemical treatment. After the chemical treatment, the majority of these values were close to zero in magnitude (refer Table 6), which will be beneficial for a large number of applications.
No. | LH (mm) | Chemical treatment | PLA+ | PLA | ABS+ |
Max ≤ Rsk ≤ min | Max ≤ Rsk ≤ min | Max ≤ Rsk ≤ min | |||
1 | 0.04 | Before | -1.4563 ≤ Rsk ≤ 0.8077 | -0.7599 ≤ Rsk ≤ 0.1017 | -0.7347 ≤ Rsk ≤ 0.4729 |
After | -0.8570 ≤ Rsk ≤ -0.0445 | -0.7095 ≤ Rsk ≤ 0.3942 | -0.5170 ≤ Rsk ≤ -0.3175 | ||
2 | 0.32 | Before | -0.9626 ≤ Rsk ≤ -0.3427 | -0.9322 ≤ Rsk ≤ 0.2144 | -0.8740 ≤ Rsk ≤ -0.3786 |
After | -0.0559 ≤ Rsk ≤ 0.5009 | -0.0068 ≤ Rsk ≤ 0.3887 | -0.2350 ≤ Rsk ≤ 0.2077 |
Figures 15 and 16, the kurtosis measurement showed both leptokurtic distribution (fat-tailed if Rku > 3) with a high degree of peakedness. Platykurtic distribution (thin-tailed, rough profile distribution if Rku < 3) with a low degree of frequent peakedness, as Rku records both lower and higher.
In this last section, the influence of the different diameters (15, 20, 25 and 30 mm) and layer heights (0.04 and 0.32 mm) on the density performance (weight and volume) is studied. All the FDM 3D printed samples were weighed with laboratory high precision on an electronic balance (0.1 mg accuracy). The density (g/cm3) of the thermoplastic filament material is measured merely using weight (g) divided by the volume (cm3) of the thermoplastic filament material. The stairs-stepping effect of the semi-sphere printed samples leads to volumetric loss, especially at high LH. The FDM 3D printed samples shrink as well as the average weight of all samples was increased by less than 1%. Initial average weight of 1.0078, 2.3860, 4.6478 and 8.0346 g were considered for the samples of 15 to 30 mm diameter respectively.
The density of the filaments (PLA+, PLA, and ABS+) was slightly decreased when FDM 3D printed part increased from 15 to 30 mm in diameter. Besides, all filament densities were increased after exposure to chemical treatment (acetone) due to the absorption of the chemical solution.
Figure 17 shows the relationship between the FDM 3D printed sample diameter and its corresponding filament’s density at LH = 0.04 mm before and after chemical treatment. The mean and standard deviation (mean ± SD) of PLA+, PLA and BAS+ densities (refer Table 7) before and after chemical treatment are as shown in Figure 17a–c respectively. This could possibly be due to pinholes, incomplete filling, or interfacial void. The similar trend of results is found at LH = 0.32 mm were given in Table 7 and are plotted in Figure 18a–c, respectively. After exposure to chemical treatment, ~6% increase in density is seen in both the cases and ABS+ shows the low-density structure due to pinholes or incomplete filling etc.
No. | LH (mm) | Chemical treatment | Mean and standard deviation (mean ± SD) g/cm3 | ||
PLA+ | PLA | ABS+ | |||
1 | 0.04 | Before | 1.1709 ± 0.0109 g/cm3 | 1.2397 ± 0.0045 g/cm3 | 1.0195 ± 0.0078 g/cm3 |
After | 1.2652 ± 0.0323 g/cm3 | 1.3188 ± 0.0.251 g/cm3 | 1.0955 ± 0.0274 g/cm3 | ||
2 | 0.32 | Before | 1.1893 ± 0.0082 g/cm3 | 1.2377 ± 0.0070 g/cm3 | 1.0263 ± 0.0146 g/cm3 |
After | 1.2722 ± 0.0243 g/cm3 | 1.3170 ± 0.0235 g/cm3 | 1.1008 ± 0.0334 g/cm3 |
By changing the LH from 0.04 to 0.32 mm, the increased in the density of the all printed parts remains almost the same might be due to there being few particles from the chemical remains on the asperities of the FDM 3D printed surface (refer Figure 18). The improvement is remarkable in both cases. However, at both LH, ABS+ shows low density which is ~1.02 to ~1.1 g/cm3 while PLA+ and PAL indicates almost the same value of density around ~1.2 to ~1.3 g/cm3.
It can be concluded that found data is very consistent with the available data in the literature review (~1.24 g/cm3 for PLA and PLA+ and ~1.06 g/cm3 for ABS+) [13].
The semi-sphere 3D physical model is manufactured for surface roughness aspect and density analysis of FDM 3D prototypes considering different LHs (0.04 nm, 0.32 mm) and filament types (PLA+, PLA, ABS+). In this research, acetone vapour bath as a chemical treatment for smoothing the surface is employed for improving the surface roughness aspects of the FDM 3D semi-sphere printed samples as well the density performance. Study led us to the following main conclusions and insights:
LH proved to be the important printing process parameters in determining the surface finish quality of the printed samples. The thin layer (0.04 mm) produces a smoother surface than the thick layer (0.32 mm), whether it is measured horizontally or vertically.
At LH = 0.04 mm, the surface roughness (Ra) of FDM 3D semi-sphere printed samples was in the range of 6.3167 to 10.9565 μm before and 3.9092 to 7.1952 μm after exposure to the chemical treatment. At LH = 0.32 mm, the Ra value was found lying in the range of 31.1908 to 53.2628 μm before and 40.0284 to 18.5529 μm after the chemical treatment.
The density of the filaments was moderately decreased when the FDM 3D printed part’s diameter increased from 15 to 30 mm. All filament densities were increased after exposure to chemical treatment (acetone) due to the absorption of the chemical solution.
The authors declare no conflict of interests.
[1] | Alsoufi MS, Elsayed AE (2017) How surface roughness performance of printed parts manufactured by desktop FDM 3D printer with PLA+ is influenced by measuring direction. Am J Mech Eng 5: 211-222. |
[2] | Alsoufi MS, Elsayed AE (2018) Quantitative analysis of 0% infill density surface profile of printed part fabricated by personal FDM 3D printer. Int J Eng Technol 7: 44-52. |
[3] | Alsoufi MS, Elsayed AE (2018) Surface roughness quality and dimensional accuracy-a comprehensive analysis of 100% infill printed parts fabricated by a personal/desktop cost-effective FDM 3D printer. Mater Sci Appl 9: 11-40. |
[4] | Alsoufi MS, Elsayed AE (2017) Warping deformation of desktop 3D printed parts manufactured by open source fused deposition modeling (FDM) system. Int J Mech Mech Eng 17: 7-16. |
[5] |
Li Y, Linke BS, Voet H, et al. (2017) Cost, sustainability and surface roughness quality-A comprehensive analysis of products made with personal 3D printers. CIRP J Manuf Sci Tec 16: 1-11. doi: 10.1016/j.cirpj.2016.10.001
![]() |
[6] |
Thrimurthulu K, Pandey PM, Reddy NV, et al. (2004) Optimum part deposition orientation in fused deposition modeling. Int J Mach Tool Manu 44: 585-594. doi: 10.1016/j.ijmachtools.2003.12.004
![]() |
[7] | Byun, HS, Lee KH (2006) Determination of the optimal build direction for different rapid prototyping processes using multi-criterion decision making. Robot Cim-Int Manuf 22: 69-80. |
[8] | Mostafa MAG, Alsoufi MS, Tayeb BA (2015) CAD/CAM integration based on machining features for prismatic parts. Int J Emerging Trends Technol Com Sci 4: 106-110. |
[9] |
Galantucci LM, Lavecchia F, Percoco G (2009) Experimental study aiming to enhance the surface finish of fused deposition modeled parts. CIRP Annals 58: 189-192. doi: 10.1016/j.cirp.2009.03.071
![]() |
[10] |
Ippolito R, Iuliano L, Gatto A (1995) Benchmarking of rapid prototyping techniques in terms of dimensional accuracy and surface finish. CIRP Annals 44: 157-160. doi: 10.1016/S0007-8506(07)62296-3
![]() |
[11] |
Armillotta A (2006) Assessment of surface quality on textured FDM prototypes. Rapid Prototyping J 12: 35-41. doi: 10.1108/13552540610637255
![]() |
[12] |
Singh R, Singh S, Singh IP, et al. (2017) Investigation for surface finish improvement of FDM parts by vapor smoothing process. Compos Part B-Eng 111: 228-234. doi: 10.1016/j.compositesb.2016.11.062
![]() |
[13] | Esun suppliers from China for purchasing 3D filaments, resins for 3D FDM printer, 2019. Available from: http://www.esunchina.net/Products/Filament. |
[14] |
Jiang C, Zhao GF (2015) A preliminary study of 3D printing on rock mechanics. Rock Mech Rock Eng 48: 1041-1050. doi: 10.1007/s00603-014-0612-y
![]() |
[15] |
Mohamed OA, Masood SH, Bhowmik JL (2016) Optimization of fused deposition modeling process parameters for dimensional accuracy using I-optimality criterion. Measurement 81: 174-196. doi: 10.1016/j.measurement.2015.12.011
![]() |
[16] |
Mohamed OA, Masood SH, Bhowmik JL (2015) Optimization of fused deposition modeling process parameters: a review of current research and future prospects. Adv Manuf 3: 42-53. doi: 10.1007/s40436-014-0097-7
![]() |
[17] |
Alsoufi MS, Alhazmi MW, Suker DK, et al. (2019) Experimental characterization of the influence of nozzle temperature in FDM 3D printed pure PLA and advanced PLA+. Am J Mech Eng 7: 45-60. doi: 10.12691/ajme-7-2-1
![]() |
[18] |
Sun Q, Rizvi GM, Bellehumeur CT, et al. (2008) Effect of processing conditions on the bonding quality of FDM polymer filaments. Rapid Prototyping J 14: 72-80. doi: 10.1108/13552540810862028
![]() |
[19] | Ahn S H, Montero M, Odell D, et al. (2002) Anisotropic material properties of fused deposition modeling ABS. Rapid Prototyping J 8: 248-257. |
[20] | Lalehpour A, Barari A (2016) Post processing for fused deposition modeling parts with acetone vapour bath. IFAC-Papers OnLine 49: 42-48. |
[21] |
Galantucci LM, Lavecchia F, Percoco G (2010) Quantitative analysis of a chemical treatment to reduce roughness of parts fabricated using fused deposition modeling. CIRP Annals 59: 247-250. doi: 10.1016/j.cirp.2010.03.074
![]() |
[22] | Kumar BR, Rao TS (2012) AFM studies on surface morphology, topography and texture of nanostructured zinc aluminum oxide thin films. Dig J Nanomater Bios 7: 1881-1889. |
[23] | ISO 4287 (1997). Geometrical product specifications (GPS)-surface texture: profile method-terms, definitions and surface texture parameters, ISO. |
1. | Sachini Wickramasinghe, Truong Do, Phuong Tran, FDM-Based 3D Printing of Polymer and Associated Composite: A Review on Mechanical Properties, Defects and Treatments, 2020, 12, 2073-4360, 1529, 10.3390/polym12071529 | |
2. | Izabela Rojek, Dariusz Mikołajewski, Ewa Dostatni, Marek Macko, AI-Optimized Technological Aspects of the Material Used in 3D Printing Processes for Selected Medical Applications, 2020, 13, 1996-1944, 5437, 10.3390/ma13235437 | |
3. | Daniel Castro-Casado, Chemical treatments to enhance surface quality of FFF manufactured parts: a systematic review, 2021, 2363-9512, 10.1007/s40964-020-00163-1 | |
4. | Jianhua Sun, Hai Gu, Jie Zhang, Yuanyuan Xu, Guoqing Wu, Weiwei Wu, Generalized Newtonian flow analysis in the microchannel manufactured by SLA considering nano-scale stair effect, 2022, 14, 1687-8140, 168781402110704, 10.1177/16878140211070448 | |
5. | Abishek Kafle, Eric Luis, Raman Silwal, Houwen Matthew Pan, Pratisthit Lal Shrestha, Anil Kumar Bastola, 3D/4D Printing of Polymers: Fused Deposition Modelling (FDM), Selective Laser Sintering (SLS), and Stereolithography (SLA), 2021, 13, 2073-4360, 3101, 10.3390/polym13183101 | |
6. | Ahmad Kholil, Eko Arif Syaefuddin, Agung Premono, Farhan Nugraha, The Effect of Orientation Angle and Layer Thickness on Surface Roughness of ABS Material on FDM, 2022, 1057, 1662-9752, 3, 10.4028/p-m37s90 | |
7. | Mahsa Karimi, Mitra Asadi‐Eydivand, Nabiollah Abolfathi, Yalda Chehrehsaz, Mehran Solati‐Hashjin, The effect of pore size and layout on mechanical and biological properties of 3D ‐printed bone scaffolds with gradient porosity , 2023, 44, 0272-8397, 1343, 10.1002/pc.27174 | |
8. | Leon R.S. Rosseau, Merlijn A.M.R. Schinkel, Ivo Roghair, Martin van Sint Annaland, Experimental Quantification of Gas Dispersion in 3D-Printed Logpile Structures Using a Noninvasive Infrared Transmission Technique, 2022, 2, 2694-2488, 236, 10.1021/acsengineeringau.1c00040 | |
9. | Xiaochen Sun, Maciej Mazur, Chi-Tsun Cheng, A review of void reduction strategies in material extrusion-based additive manufacturing, 2023, 67, 22148604, 103463, 10.1016/j.addma.2023.103463 | |
10. | Mohamed Benamira, Naamane Benhassine, Amar Ayad, Azzeddine Dekhane, Investigation of printing parameters effects on mechanical and failure properties of 3D Printed PLA, 2023, 13506307, 107218, 10.1016/j.engfailanal.2023.107218 | |
11. | A. A. Potapov, V. M. Volgin, A. P. Malakho, I. V. Gnidina, Supplementary treatment of FDM printed parts. Review, 2024, 93, 0036-021X, RCR5127, 10.59761/RCR5127 | |
12. | Gianluca Cicala, Claudio Tosto, 2024, 9780443159176, 37, 10.1016/B978-0-443-15917-6.00002-5 | |
13. | Mohammad Heidari-Rarani, Mohsen Ahmadi Jebeli, 2024, 9780443184628, 235, 10.1016/B978-0-443-18462-8.00009-X | |
14. | M. Girija, T. Sampath Kumar, State of art on evaluation of three- to six-dimensional novel additive manufacturing technology for biomedical applications, 2024, 0954-4089, 10.1177/09544089241281985 | |
15. | John Kechagias, Stephanos Zaoutsos, Effects of 3D-printing processing parameters on FFF parts’ porosity: outlook and trends, 2024, 39, 1042-6914, 804, 10.1080/10426914.2024.2304843 | |
16. | Philipp Zimmermann, Christoph Schammel, Jürgen Nagel, Additive Manufacturing of Watertight ABS Parts and Its Use for Chemical Metal Plating, 2024, 1438-7492, 10.1002/mame.202400367 | |
17. | John D. Kechagias, Nikolaos A. Fountas, Ioannis Papantoniou, Nikolaos M. Vaxevanidis, Interlaminar bonding assessment in vertical-oriented filament material extrusion bending specimens, 2025, 0268-3768, 10.1007/s00170-025-15124-7 |
Setting | Parameters | Unit | Values | |||
Quality | Layer height | mm | 0.04 | 0.32 | ||
Shell | Wall thickness | mm | 0.4 | |||
Wall line count | - | 1 | ||||
Top/Bottom thickness (mm) | mm | 0 | ||||
Top thickness | mm | |||||
Top layer | - | |||||
Bottom thickness | mm | |||||
Bottom layer | - | |||||
Infill | Infill density | % | 100 | |||
Infill pattern | - | Concentric | ||||
Infill line direction | ° | - | ||||
Infill overlap percentage | % | 25 | ||||
Infill layer thickness | mm | 0.1 | ||||
Nozzle | Nozzle size | mm | 0.4 | |||
Compatible material diameter | mm | 1.75 | ||||
Nozzle offset x-axis | mm | 0 | ||||
Nozzle offset y-axis | mm | |||||
Material | Filament type | - | PLA+ | PLA | ABS+ | |
Filament colour | - | Dark blue | Light blue | Black | ||
AM process | - | FDM (fused deposition modeling) | ||||
Printing direction | - | Flat on platform (on printing table) | ||||
Printing temperature | ℃ | 225 | 260 | |||
Printing temperature initial layer | ℃ | |||||
Material | Initial printing temperature | ℃ | ||||
Final printing temperature | ℃ | |||||
Build plate temperature | ℃ | 60 | ||||
Build plate temperature initial layer | ℃ | |||||
Flow | % | 100 | ||||
Initial layer flow | % | |||||
Retraction distance | mm | 0.8 | ||||
Retraction speed | mm/s | 35 | ||||
Speed | Print speed | mm/s | 30 | |||
Infill speed | mm/s | |||||
Wall speed | mm/s | 15 | ||||
Outer wall speed | mm/s | |||||
Inner wall speed | mm/s | 30 | ||||
Top/Bottom Speed | mm/s | 15 | ||||
Initial Layer Sped | mm/s | |||||
Cooling | Fan speed (%) | % | 100 | |||
Build Plate Adhesion | Build plate adhesion type | - | Skirt | |||
Skirt lin count | - | 1 | ||||
Skirt distance | mm | 3 | ||||
Skirt/Brim minimum length | mm | 250 | ||||
Environmental Condition | Room temperature | ℃ | 23 ± 2 | |||
Relative humidity | % RH | 50 ± 10 |
No. | LH (mm) | Number of layers | Printing time (min) | Change in diameter (mm) | Increase in layer | Increase in printing time |
1 | 0.04 | 183 | 23 | 15 | Doubled | 85% |
371 | 183 | 30 | ||||
2 | 0.32 | 24 | 3 | 15 | Doubled | 88% |
47 | 24 | 30 |
No. | LH (mm) | Chemical treatment | Raw surface profile (μm) | Modified surface profile (μm) | Ra improvements |
1 | 0.04 | Before | Ra = 8.3762 | -17.28 < Ra < +17.06 | ~20% |
After | Ra = 33.1254 | -15.94 < Ra < +16.96 | ~20% | ||
2 | 0.32 | Before | Ra = 6.6530 | -126.01 < Ra < +89.97 | ~40% |
After | Ra = 18.5529 | -98.75 < Ra < +85.13 | ~40% |
No. | LH (mm) | Chemical treatment | Mean and standard deviation (mean ± SD) μm | ||
PLA+ | PLA | ABS+ | |||
1 | 0.04 | Before | 10.2315 ± 1.1134 μm | 6.8746 ± 0.4603 μm | 8.0217 ± 1.0389 μm |
After | 6.6474 ± 0.4437 μm | 6.1273 ± 0.7169 μm | 4.9086 ± 0.9108 μm | ||
2 | 0.32 | Before | 43.8942 ± 10.7897 μm | 37.6168 ± 5.2260 μm | 45.4202 ± 7.9432 μm |
After | 30.8442 ± 9.8090 μm | 29.4950 ± 3.7771 μm | 26.3328 ± 3.6647 μm |
No. | LH (mm) | Chemical treatment | PLA+ | PLA | ABS+ | |||
Maximum Rq/Ra (mm) | Minimum Rq/Ra (mm) | Maximum Rq/Ra (mm) | Minimum Rq/Ra (mm) | Maximum Rq/Ra (mm) | Minimum Rq/Ra (mm) | |||
1 | 0.04 | Before | ~1.51 at Φ25 | ~1.22 at Φ30 | ~1.27 at Φ15 | ~1.18 at Φ30 | ~1.52 at Φ15 | ~1.26 at Φ30 |
After | ~1.27 at Φ15 | ~1.19 at Φ25 | ~1.29 at Φ30 | ~1.21 at Φ20 | ~1.27 at Φ30 | ~1.17 at Φ15 | ||
2 | 0.32 | Before | ~1.3 at Φ30 | ~1.23 at Φ25 | ~1.28 at Φ25 | ~1.19 at Φ15 | ~1.36 at Φ30 | ~1.24 at Φ15 |
After | ~1.54 at Φ30 | ~1.18 at Φ20 | ~1.19 at Φ15 | ~1.23 at Φ25 | ~1.34 at Φ 20 | ~1.20 at Φ30 |
No. | LH (mm) | Chemical treatment | PLA+ | PLA | ABS+ |
Max ≤ Rsk ≤ min | Max ≤ Rsk ≤ min | Max ≤ Rsk ≤ min | |||
1 | 0.04 | Before | -1.4563 ≤ Rsk ≤ 0.8077 | -0.7599 ≤ Rsk ≤ 0.1017 | -0.7347 ≤ Rsk ≤ 0.4729 |
After | -0.8570 ≤ Rsk ≤ -0.0445 | -0.7095 ≤ Rsk ≤ 0.3942 | -0.5170 ≤ Rsk ≤ -0.3175 | ||
2 | 0.32 | Before | -0.9626 ≤ Rsk ≤ -0.3427 | -0.9322 ≤ Rsk ≤ 0.2144 | -0.8740 ≤ Rsk ≤ -0.3786 |
After | -0.0559 ≤ Rsk ≤ 0.5009 | -0.0068 ≤ Rsk ≤ 0.3887 | -0.2350 ≤ Rsk ≤ 0.2077 |
No. | LH (mm) | Chemical treatment | Mean and standard deviation (mean ± SD) g/cm3 | ||
PLA+ | PLA | ABS+ | |||
1 | 0.04 | Before | 1.1709 ± 0.0109 g/cm3 | 1.2397 ± 0.0045 g/cm3 | 1.0195 ± 0.0078 g/cm3 |
After | 1.2652 ± 0.0323 g/cm3 | 1.3188 ± 0.0.251 g/cm3 | 1.0955 ± 0.0274 g/cm3 | ||
2 | 0.32 | Before | 1.1893 ± 0.0082 g/cm3 | 1.2377 ± 0.0070 g/cm3 | 1.0263 ± 0.0146 g/cm3 |
After | 1.2722 ± 0.0243 g/cm3 | 1.3170 ± 0.0235 g/cm3 | 1.1008 ± 0.0334 g/cm3 |
Setting | Parameters | Unit | Values | |||
Quality | Layer height | mm | 0.04 | 0.32 | ||
Shell | Wall thickness | mm | 0.4 | |||
Wall line count | - | 1 | ||||
Top/Bottom thickness (mm) | mm | 0 | ||||
Top thickness | mm | |||||
Top layer | - | |||||
Bottom thickness | mm | |||||
Bottom layer | - | |||||
Infill | Infill density | % | 100 | |||
Infill pattern | - | Concentric | ||||
Infill line direction | ° | - | ||||
Infill overlap percentage | % | 25 | ||||
Infill layer thickness | mm | 0.1 | ||||
Nozzle | Nozzle size | mm | 0.4 | |||
Compatible material diameter | mm | 1.75 | ||||
Nozzle offset x-axis | mm | 0 | ||||
Nozzle offset y-axis | mm | |||||
Material | Filament type | - | PLA+ | PLA | ABS+ | |
Filament colour | - | Dark blue | Light blue | Black | ||
AM process | - | FDM (fused deposition modeling) | ||||
Printing direction | - | Flat on platform (on printing table) | ||||
Printing temperature | ℃ | 225 | 260 | |||
Printing temperature initial layer | ℃ | |||||
Material | Initial printing temperature | ℃ | ||||
Final printing temperature | ℃ | |||||
Build plate temperature | ℃ | 60 | ||||
Build plate temperature initial layer | ℃ | |||||
Flow | % | 100 | ||||
Initial layer flow | % | |||||
Retraction distance | mm | 0.8 | ||||
Retraction speed | mm/s | 35 | ||||
Speed | Print speed | mm/s | 30 | |||
Infill speed | mm/s | |||||
Wall speed | mm/s | 15 | ||||
Outer wall speed | mm/s | |||||
Inner wall speed | mm/s | 30 | ||||
Top/Bottom Speed | mm/s | 15 | ||||
Initial Layer Sped | mm/s | |||||
Cooling | Fan speed (%) | % | 100 | |||
Build Plate Adhesion | Build plate adhesion type | - | Skirt | |||
Skirt lin count | - | 1 | ||||
Skirt distance | mm | 3 | ||||
Skirt/Brim minimum length | mm | 250 | ||||
Environmental Condition | Room temperature | ℃ | 23 ± 2 | |||
Relative humidity | % RH | 50 ± 10 |
No. | LH (mm) | Number of layers | Printing time (min) | Change in diameter (mm) | Increase in layer | Increase in printing time |
1 | 0.04 | 183 | 23 | 15 | Doubled | 85% |
371 | 183 | 30 | ||||
2 | 0.32 | 24 | 3 | 15 | Doubled | 88% |
47 | 24 | 30 |
No. | LH (mm) | Chemical treatment | Raw surface profile (μm) | Modified surface profile (μm) | Ra improvements |
1 | 0.04 | Before | Ra = 8.3762 | -17.28 < Ra < +17.06 | ~20% |
After | Ra = 33.1254 | -15.94 < Ra < +16.96 | ~20% | ||
2 | 0.32 | Before | Ra = 6.6530 | -126.01 < Ra < +89.97 | ~40% |
After | Ra = 18.5529 | -98.75 < Ra < +85.13 | ~40% |
No. | LH (mm) | Chemical treatment | Mean and standard deviation (mean ± SD) μm | ||
PLA+ | PLA | ABS+ | |||
1 | 0.04 | Before | 10.2315 ± 1.1134 μm | 6.8746 ± 0.4603 μm | 8.0217 ± 1.0389 μm |
After | 6.6474 ± 0.4437 μm | 6.1273 ± 0.7169 μm | 4.9086 ± 0.9108 μm | ||
2 | 0.32 | Before | 43.8942 ± 10.7897 μm | 37.6168 ± 5.2260 μm | 45.4202 ± 7.9432 μm |
After | 30.8442 ± 9.8090 μm | 29.4950 ± 3.7771 μm | 26.3328 ± 3.6647 μm |
No. | LH (mm) | Chemical treatment | PLA+ | PLA | ABS+ | |||
Maximum Rq/Ra (mm) | Minimum Rq/Ra (mm) | Maximum Rq/Ra (mm) | Minimum Rq/Ra (mm) | Maximum Rq/Ra (mm) | Minimum Rq/Ra (mm) | |||
1 | 0.04 | Before | ~1.51 at Φ25 | ~1.22 at Φ30 | ~1.27 at Φ15 | ~1.18 at Φ30 | ~1.52 at Φ15 | ~1.26 at Φ30 |
After | ~1.27 at Φ15 | ~1.19 at Φ25 | ~1.29 at Φ30 | ~1.21 at Φ20 | ~1.27 at Φ30 | ~1.17 at Φ15 | ||
2 | 0.32 | Before | ~1.3 at Φ30 | ~1.23 at Φ25 | ~1.28 at Φ25 | ~1.19 at Φ15 | ~1.36 at Φ30 | ~1.24 at Φ15 |
After | ~1.54 at Φ30 | ~1.18 at Φ20 | ~1.19 at Φ15 | ~1.23 at Φ25 | ~1.34 at Φ 20 | ~1.20 at Φ30 |
No. | LH (mm) | Chemical treatment | PLA+ | PLA | ABS+ |
Max ≤ Rsk ≤ min | Max ≤ Rsk ≤ min | Max ≤ Rsk ≤ min | |||
1 | 0.04 | Before | -1.4563 ≤ Rsk ≤ 0.8077 | -0.7599 ≤ Rsk ≤ 0.1017 | -0.7347 ≤ Rsk ≤ 0.4729 |
After | -0.8570 ≤ Rsk ≤ -0.0445 | -0.7095 ≤ Rsk ≤ 0.3942 | -0.5170 ≤ Rsk ≤ -0.3175 | ||
2 | 0.32 | Before | -0.9626 ≤ Rsk ≤ -0.3427 | -0.9322 ≤ Rsk ≤ 0.2144 | -0.8740 ≤ Rsk ≤ -0.3786 |
After | -0.0559 ≤ Rsk ≤ 0.5009 | -0.0068 ≤ Rsk ≤ 0.3887 | -0.2350 ≤ Rsk ≤ 0.2077 |
No. | LH (mm) | Chemical treatment | Mean and standard deviation (mean ± SD) g/cm3 | ||
PLA+ | PLA | ABS+ | |||
1 | 0.04 | Before | 1.1709 ± 0.0109 g/cm3 | 1.2397 ± 0.0045 g/cm3 | 1.0195 ± 0.0078 g/cm3 |
After | 1.2652 ± 0.0323 g/cm3 | 1.3188 ± 0.0.251 g/cm3 | 1.0955 ± 0.0274 g/cm3 | ||
2 | 0.32 | Before | 1.1893 ± 0.0082 g/cm3 | 1.2377 ± 0.0070 g/cm3 | 1.0263 ± 0.0146 g/cm3 |
After | 1.2722 ± 0.0243 g/cm3 | 1.3170 ± 0.0235 g/cm3 | 1.1008 ± 0.0334 g/cm3 |