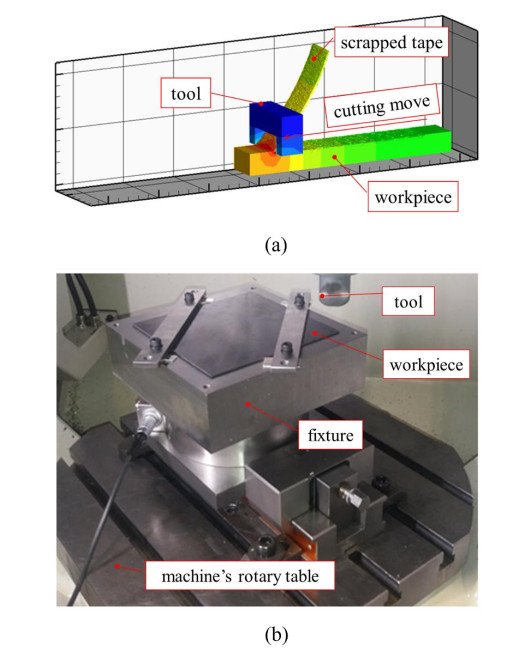
In this work, a novel method for a more sustainable recycling and cost-efficient manufacturing technique of polyether ketone ketone (PEKK) based thermoplastic composite materials is proposed to recover and reprocess waste and end-of-life materials in the aerospace industry. For the recycling of carbon fiber reinforced thermoplastics (CFrTP), an innovative scrapping process based on mechanical cutting was developed and the properties of the obtained scrap and the recycled panel were analyzed. Thus, a cutting tool was developed for the delamination of the input material so that long fibers can be retained in the resulting scrap. Different processing approaches of material scrapping were evaluated, aiming to obtain manageable scrap that can be subsequently used for a compression molding process. Additionally, an automatic process was evaluated to manage the scrap and perform the corresponding lay-up to manufacture high-quality thermoplastic composite products with recycled materials.
Citation: Alejandro Sandá, Rocío Ruiz, Miguel Ángel Mafé, Jon Ander Sarasua, Antonio González-Jiménez. Scrapping of PEKK-based thermoplastic composites retaining long fibers and their use for compression molded recycled parts[J]. AIMS Materials Science, 2023, 10(5): 819-834. doi: 10.3934/matersci.2023044
[1] | Kator Jeff Jomboh, Adele Dzikwi Garkida, Emmanuel Majiyebo Alemaka, Mohammed Kabir Yakubu, Vershima Cephas Alkali, Wilson Uzochukwu Eze, Nuhu Lawal . Properties and applications of natural, synthetic and hybrid fiber reinforced polymer composite: A review. AIMS Materials Science, 2024, 11(4): 774-801. doi: 10.3934/matersci.2024038 |
[2] | Wisawat Keaswejjareansuk, Xiang Wang, Richard D. Sisson, Jianyu Liang . Electrospinning process control for fiber-structured poly(Bisphenol A-co-Epichlorohydrin) membrane. AIMS Materials Science, 2020, 7(2): 130-143. doi: 10.3934/matersci.2020.2.130 |
[3] | Mahdi Rafiee, Roozbeh Abidnejad, Anton Ranta, Krishna Ojha, Alp Karakoç, Jouni Paltakari . Exploring the possibilities of FDM filaments comprising natural fiber-reinforced biocomposites for additive manufacturing. AIMS Materials Science, 2021, 8(4): 524-537. doi: 10.3934/matersci.2021032 |
[4] | Hendra Suherman, Yovial Mahyoedin, Afdal Zaky, Jarot Raharjo, Talitha Amalia Suherman, Irmayani Irmayani . Investigation of the mechanical properties of bio-composites based on loading kenaf fiber and molding process parameters. AIMS Materials Science, 2024, 11(6): 1165-1178. doi: 10.3934/matersci.2024057 |
[5] | Marta Perez, Anais Barasinski, Benoit Courtemanche, Chady Ghnatios, Francisco Chinesta . Sensitivity thermal analysis in the laser-assisted tape placement process. AIMS Materials Science, 2018, 5(6): 1053-1072. doi: 10.3934/matersci.2018.6.1053 |
[6] | Thomas J. Lee, Andrew H. Morgenstern, Thomas A. Höft, Brittany B. Nelson-Cheeseman . Dispersion of particulate in solvent cast magnetic thermoplastic polyurethane elastomer composites. AIMS Materials Science, 2019, 6(3): 354-362. doi: 10.3934/matersci.2019.3.354 |
[7] | Andrea San-Gil-León, Benito A. Stradi-Granados . Determination of thermal and mechanical properties of HDPE-based polymer blends for use in traffic signs. AIMS Materials Science, 2016, 3(3): 722-736. doi: 10.3934/matersci.2016.3.722 |
[8] | Rafael Resende Lucas, Rita de Cássia Mendonça Sales-Contini, Luis Felipe Barbosa Marques, Jonas Frank Reis, Ana Beatriz Ramos Moreira Abrahão, Edson Cocchieri Botelho, Rogério Pinto Mota . Characterization of the hybrid joint between AA2024-T3 alloy and thermoplastic composite obtained by oxy-fuel welding (OFW). AIMS Materials Science, 2024, 11(3): 585-601. doi: 10.3934/matersci.2024029 |
[9] | R. Daulath Banu, R. Karunanithi, S. Sivasankaran, B. Subramanian, Abdullah A. Alhomidan . Influence of graphene nanoplatelets (GNPs) and aluminum-carbon layered double hydroxides (Al-C LDH) in polypropylene matrix of hybrid composite structures on the microstructure and mechanical performances. AIMS Materials Science, 2024, 11(5): 882-917. doi: 10.3934/matersci.2024043 |
[10] | Madjid Haddad, Redouane Zitoune, Florent Eym, Bruno Castanié . The effect of rectification of composite materials on the mechanical behavior of long fiber composite materials. AIMS Materials Science, 2016, 3(2): 645-657. doi: 10.3934/matersci.2016.2.645 |
In this work, a novel method for a more sustainable recycling and cost-efficient manufacturing technique of polyether ketone ketone (PEKK) based thermoplastic composite materials is proposed to recover and reprocess waste and end-of-life materials in the aerospace industry. For the recycling of carbon fiber reinforced thermoplastics (CFrTP), an innovative scrapping process based on mechanical cutting was developed and the properties of the obtained scrap and the recycled panel were analyzed. Thus, a cutting tool was developed for the delamination of the input material so that long fibers can be retained in the resulting scrap. Different processing approaches of material scrapping were evaluated, aiming to obtain manageable scrap that can be subsequently used for a compression molding process. Additionally, an automatic process was evaluated to manage the scrap and perform the corresponding lay-up to manufacture high-quality thermoplastic composite products with recycled materials.
Due to the growing concerns about the environmental sustainability, there has been a widespread adoption of new lightweight materials such as polymer composites in the transport sector, crucial issues being performance, cost efficiency, multifunctionality and recyclability [1]. Carbon fibers reinforced plastic (CFRP) composites are high added value materials used in many manufactured products. For years, they have been used as a raw material by the aerospace sector to replace the aluminum of lightweight structures.
However, there are still some environmental aspects that have not been solved yet. New technologies should be developed in order to improve the handling and recycling of end-of-life aircrafts by increasing the circular economy, consequently reducing the environmental impact.
Composites are challenging to recycle, especially CFRP composites, due to their hardness and chemical stability. Nevertheless, finding ways to recover long, high modulus fibers is worth the effort, as opposed to the conventional way to handle composite waste, that is, either incineration or disposal in landfills [2], which are methods no longer preferred under the European Union's Waste Framework Directive 2008/98/EC [3].
The matrix phase of commercial fibers reinforced plastic (FRP) composites can be either thermoset or thermoplastic. Thermoset polymers, such as polyesters and vinyl esters resins, are primarily used in FRPs due to the good balance of low cost and mechanical properties. Epoxies are the most important resins in the market, particularly for structural aerospace applications, as they can perform under a wide range of temperatures and conditions. During polymerization, low shrinkage and good adhesion to most of fibers is shown. After curing, the cross-linking reaction creates a three-dimensional network with good mechanical properties under high service temperatures. Fiber reinforcements of either short (<1 mm) or long (>1 mm) fibers including glass fiber, carbon fiber or aramid fibers are the main type of materials useful for the reinforcement of FRPs.
For aerospace applications, the most used FRPs are those polymers or plastics reinforced with long and continuous filaments or fibers, allowing for an increase in the mechanical properties. Typically, they consist of an epoxy-based system and a large percentage of high-performance carbon fibers longer than 100 mm.
Thermoplastic matrix polymers, which exhibit minimal cross-linking, can be repeatedly heat-softened, melted and re-shaped. From a manufacturing point of view, compared to thermosets, the processing of thermoplastics is both easier and faster. In contrast to a CFRP with a thermoset matrix, thermoplastic composites (TPCs) have a better perspective for mechanical properties, notably in terms of impact and abrasion, unlimited shelf life of raw material, sustainable manufacturing and assembling; additionally, they can be recycled, remolded and repaired efficiently. The most recently used high-performance thermoplastics in aerospace applications are semicrystalline polymers such as polyether ether ketone (PEEK), PEKK and polyethylenimine (PEI), belonging to the polyarylether ketone (PAEK) family. E-glass, carbon (AS-4, T-300), aramid (Klevlar-49 Waron) and S- or R-glass, polypropylene (PP) and polyethylene (PE) are commonly used as reinforcements for structural thermoplastics [4].
Bearing the environmental benefits of thermoplastics in mind, TPCs are considered as the best material candidates to be used for the next generation of airplanes and commit the environmental challenges regarding the end-of-life (EoL) issues to employ the waste pre- and post-consuming scrap material and promote a circular economy, which is aligned with the European Directive 2000/53/EC for End-of-life Vehicles.
Recently, there has been a tremendous uptick in worldwide research on reclaiming high performance fibers, particularly aerospace-grade carbon fiber from end-of-life, cured thermoset composites. Fiber reclamation remains the main focus of such composite recycling efforts [3].
In the case of thermoset composites, traditional recycling techniques involve complex processes such as chemical or thermal processes where the plastic is removed and wasted through different processes, separate from the mechanical size reduction of the input material [2]. From the literature, it can be said that mechanical recycling is the most mature technology for processing great quantities of waste. Traditional mechanical recycling involves the use of crushing, grinding, milling and/or shredding techniques where the input material is reduced in size to particles below 10 mm [2]. Therefore, the fibers that give the mechanical properties to the material are in a relatively short format [5]. Additionally, pyrolysis and fluidized bed processes stand out among the thermal recycling techniques [2,6,7]. Finally, solvolysis used a chemical reaction to degrade the composite matrix [8].
In the case of thermoplastic composites, recycling has attracted considerable attention in recent years. Several recycling solutions specific to CFrTPs have been implemented to recover and reuse this production scrap, and mechanical recycling processes appear to be best alternative to efficiently recycle these composites. Some recent studies reported that, compared to landfilling, the mechanical recycling of thermoplastic composites could be the most economically and environmentally viable process if the mechanical properties of these recycled materials are further improved [9,10]. The main conventional mechanical recycling processes are shredding, electrodynamical fragmentation, conventional cutting (machining), laser cutting and abrasive waterjet cutting, although some of them are also energy intensive. In most of these processes, scrap material gives grains, which are used as reinforcement in thermoplastic injection processes.
Regarding the shredding process, Vincent et al. [11,12] chose multiple shaft shredding techniques for size reduction to understand its ability to produce large and uniform flakes unlike other technologies, such as hammer mills or cutting mills. Two and four shaft shredders manufactured by UNTHA shredding technology Gmbh (hereinafter UNTHA) were used for this purpose. This type of machine was designed to shear the input material rather than impact it, as in hammer mills, which is achieved by allowing the shafts to rotate at low speeds.
Practical experience of UNTHA and Nido Recycling Techniek had shown that these machines produce a small fraction of fine particles compared to single-shaft shredders or hammer mills. Here, fine particles are defined as being five to ten times smaller than the intended main output of a machine [13]. Therefore, this method allows to choose the particle size; however, there is no control over the internal fiber lay-up of the particles.
In electrodynamical fragmentation, the workpiece is immersed in an isolating liquid and, by means of high voltage discharges, a plasma channel is generated, and a crack is induced on the workpiece that ends in the fragmentation of the material through crack propagation [14].
Conventional cutting or machining can be used as an alternative to shredding, where control on the fiber content in the scrap can be achieved. The basic knowledge provided by studies regarding the simulation and orthogonal cutting of CFRP addresses that the main factors influencing the chip morphology are the depth of cut (DOC) and the fiber orientation (angle θ), in which the latter plays the dominant role [15].
Interestingly, the cutting mechanism observed under parallel fiber cutting conditions where interface layering separation occurs favors the separation of the fiber layer affected by the tool [16]. Therefore, it can be said that when θ = 0, the chip is formed by the debonding-bending mechanism, and the magnitude of the cutting force and thrust force slowly increases with the depth of cut, this is, low forces are needed to cut the material.
Other non-conventional cutting processes, such as laser cutting or abrasive waterjet cutting, have their drawbacks in the generation of tapered kerfs that depend on the depth of the cutting being performed [17,18]. Therefore, these cutting techniques are useful for cutting composites of low thickness but not for delaminating the material. Moreover, a lower recycling energy consumption is focused for searching more energy efficient processes.
In this work, a cutting process has been developed for the delamination of CFrTP retaining an effective length of reinforcement in the resulting thermoplastic scrap to improve the mechanical performance of the recycled composite parts compared to the one obtained by conventional mechanical recycling processes. Different processing approaches have been evaluated, aiming to obtain manageable scrap that can be subsequently used for a compression molding process. The goal pursued with this study is to use this scrap with aligned long carbon fibers distribution to manufacture high-quality thermoplastic composite products with recycled materials.
The use of thermoplastic composites has increased in recent years. This entails the processing of more production scrap today and more end-of-life parts tomorrow. Currently, there is no commercial solution for recovering and recycling the upcoming high volume of thermoplastic composite scrap in a cost-efficient way. De-Bruijn et al. [19] proposed a method to retain the maximum mechanical properties of long fiber-reinforced thermoplastic production scrap. They converted those flakes into a dough by melting and mixing them in a low shear mixer and placed the dough in the mold of a compression molding machine for a hot press. Although this process can result in recycled composite parts with mechanical properties superior to those of injection molded parts, they are still below the mechanical properties of the original composite material [20]. In recent years, extensive research has been carried out on the compression molding of sliced prepreg tapes in the bulk form [21,22]. Commercial thermoplastic chopped tapes in bulk form have normally between 25 and 50 mm in length. Compression molding of thermoplastic composites is an independent process that has the capacity of processing composite scraps chopped into relatively large bits to form a new composite. However, the composite parts obtained by this method are a random-fiber distribution performance, which mechanical properties are lower than the one manufactured with a controlled fiber distribution. A recycled composite with improved mechanical properties can be developed by controlling the fiber orientation in the laminate through optimizing the quality of the scrap unidirectional tapes obtained from the scrapping process. The present study investigates the influence of the geometrical parameters of the obtained scrap unidirectional tapes on the mechanical, thermal and morphological properties of the recycled composite panels.
A cutting process has been developed for the scrapping of CFrTP panels retaining long fibers in the scrap. A special cutter has been used as a tool in a milling machine (Goratu G-Dynamic) and cutting trials have been performed using the axes of the machine to move the cutter over the input material, thus removing the aimed scrapped tapes. The machine has the capacity to position the input material so that cuts can be done parallel to any carbon fiber layer (see Figure 1).
The material used for the experimentation has the following specifications:
● Material TenCate Cetex® TC1320 PEKK AS4 D 6.35 mm
● Panel thickness around 2.2 mm
● Panel dimensions around 200 × 200 mm2
The panels were manufactured using 6.35 mm wide tape of TenCate Cetex® TC1320, that is, a PEKK-based thermoplastic composite based on a semi crystalline thermoplastic matrix polymer. It has excellent resistance to chemicals and solvents, excellent service performance, good hot/wet strength, and excellent performance in flammability properties.
Three different lay-ups have been produced by the NLR-Netherlands Aerospace Centre to evaluate their performance under the developed scrapping process:
● 16 layer QI laminate ([0, +45, 90, −45]2s)
● 16 layer unidirectional laminate (16[0])
● 16 layer bidirectional laminate ([0, 90]4s)
The developed cutting process aims to get scrap tapes containing long fibres 12.3 mm wide and 200 mm long, this is, the same length of the panel. From the performed experimentation, different scrap tape thicknesses have been obtained, and, therefore, different internal fibre lay-ups.
From the input material lay-up already described in Section 2.1, ideally, one fibre layer should be expected every 0.14 mm. In a primary approach, the objective was to obtain unidirectional scrap tapes containing just one long fibre layer, this is, 0.14 mm thick scrap tapes. However, due to the panels' manufacturing accuracy and the scrapping process itself, this was very difficult, and resulted in bad quality scrap tapes, non-uniform shape and heterogenous thickness. Therefore, these issues make the scrapping process inefficient. Considering that the process aims to be scalable, a different approach has been undertaken, so that it is more robust and less dependent on panel manufacturing issues.
In order to obtain more uniform and better-quality scrap tapes, thicker tapes were cut, trying to obtain two fiber layers in each tape, this is, 0.28 mm. In this way, scrapped tapes with a layer of long fibers around 200 mm can be assured. Depending on the initial panel's lay-up, the second layer present in the scrap tapes can be as long as the first one (16[0] panels), as short as the width of the tape when the second layer is at 90º, this is, 12.3 mm ([0, 90]4s panels) or slightly longer than the tape's width when this second layer is at 45º ([0, +45, 90, −45]2s panels). It has been found that this approach gives the best quality scrap tapes and has a high potential to industrially scale the process.
A 200 × 200 mm shear-edge aluminum compression molding mold was used to manufacture composite panels from different scrap material obtained from the scrapping-step. Unidirectional scrap tapes from 16[0] and [0, 90]4s panel (200 mm length and 12.3 mm width) were selected for the fiber-orientated experiment, since the one from the quasi-isotropic (QI) [0, +45, 90, −45]2s panel had a curvature higher than 20º, which did not allow to accurately control the tape placement. For laminate fabrication, a commercial collaborative robot of Universal Robots was used for an automatic and controlled placement of the scrap tapes. A sheel tool was used for tapes positioning keeping an equidistant separation of 17.5 mm each other (Figuure 2a). Afterwards, the collaborative robot was programmed for the automatic pick and place of the scrap tapes. Grippers from the head of the collaborative robot were moved to the pick-up position at both sides of the scrap tape and were placed in an aligned way at the recorded position in the compression molding mold. The preform was made of plies orientated at a (0) direction to achieve the target thickness panel of 2.2 mm as the reference sample.
After finishing the scrap tapes lay-up over the mold, it was closed (Figure 2b), and the plates of the compression molding equipment were subject to a heated ramp of 5 ºC/min until a temperature of 370 ºC was reached; this temperature was maintained for 30 minutes to ensure a isothermal and stable condition in the mold cavity by heat convection of the compression molding press. After 10 minutes on the temperature plates, a consolidation pressure of 16 bar was applied for the thermo-compression process. Then, at the end of the dwell step, a cooling ramp of 5 ºC/min was applied to the plates until the mold temperature came down lower than 100 ºC. Demolding was performed at room temperature and the vertical flash around the contour of the recycled panel was trimmed off (Figure 2d).
To fully understand the influence of the scrapping process on the properties of the obtained scrap tapes and the final recycled CFrTP panels produced by compression molding means, mechanical, thermal and microstructural analyses of the samples were carried out. The goal is to evaluate the behavior of the recycled material in a new panel configuration.
The tensile properties of all composite samples, both single scrap tapes and recycled panels, were tested according to UNE EN ISO 527-4 standard test method. The evaluated properties were the modulus of elasticity, the ultimate tensile strength and the elongation at this point. The test specimens of the scrap tapes had a dimension of 200 mm (length) and 12.3 mm (width), while the one of the recycled panels were cut into 1B dumbbell-type test specimens according to standard ISO 527-4 using a CNC milling machine.
Tests were performed in a ZwickRoell Z250 universal testing machine with a MakroXtens extensometer. A constant speed of 2 mm/min with hydraulic grips and a 250 kN load cell were used to calculate tensile properties.
Thermogravimetric analysis (TGA) is a technique where the mass of a polymer is measured as a either function of temperature or time, while the sample is subjected to a controlled temperature program in a controlled atmosphere, air or nitrogen. The TGA analysis was determined using a TA Universal Analysis 2000 software according to the ASTM E1131 standard. The aim was to evaluate the influence of the scrapping process on the thermal history of the composite. The testing method was performed in a wide range of scrap tape and recycled panel samples. It was performed by exposing the specimens to a thermal degradation cycle that goes from room temperature to 900 ºC in 2 steps. First, there was a heating ramp from the room temperature to 900 ºC at N2 atmosphere; then, a cooling step until 400 ºC was performed to expose the sample to another heating cycle ramp up to 900 ºC, at air atmosphere. Results from a TGA analysis provided information in all the ranges and atmospheres.
Characterization of recycled panels were carried out in a Phenom ProX scanning electron microscope (SEM). The secondary electron images were taken under 15 KV acceleration voltages. The samples were obtained by cutting fragments of the test specimens from mechanical characterization. Those fragments were adhered to a sample holder, which was previously covered with a conductive self-adhesive base. Finally, the samples were covered with gold using the "sputter coating" technique to ensure electrical conductivity during electron bombardment. The surface and the cross section of the prepared samples were examined.
Following the ASTM D2734 standard, the density and the corresponding void content of the scrap tape samples obtained after the scrapping process was determined. Sample specimens of 15 × 15 mm were used. Through this test, it was possible to determine the amount of void content measuring the voids in the scrap tape samples. Determining this void content can be very useful since a high void content in samples can significantly reduce the strength of composite materials as far as we can determine, and thus, make a failure in the composite structure. The determination of the void content can be distinguished between the different levels of samples obtained from the different panels ([0, +45, 90, −45]2s, [0, 90]4s and 16[0]) considering that the fiber had a different orientation in the samples analyzed.
The process of delamination itself induces a plastic deformation on the input panel. In the case of non-unidirectional lay-ups, when the fiber orientation symmetry is broken, the material tends to deform. In the case of [0, +45, 90, −45]2s panels, the deformation gradually increases as different levels are removed from the panel. This impairs the process, making it impossible to process the last layers of material due to the high deformation of the workpiece that makes impossible its correct clamping. In the case of [0, 90]4s panels and 16[0] panels, the deformation is not an issue and a higher ratio of long fiber tapes can be obtained from the input panels.
Regarding the tapes' geometry, in the case of [0, +45, 90, −45]2s panels, the presence of a longitudinal fiber layer and another one at 45º results in a helical deformation of the scrap tape. This makes their manipulation for the compression molding process more difficult (see Figure 3a). In the case of [0, 90]4s panels, a curvature can also be observed due to the 90º fiber layer; however, in this case, it does not hinder their manipulation (see Figure 3b). Finally, when delaminating unidirectional panels (16[0] panels), the scrap tapes are flat without deformation or curvature (see Figure 3c). This is the ideal case where only long fibers are present in the scrap; additionally, they can be easily manipulated in a compression molding process.
The test was performed by removing the polymer matrix from scrap tape samples obtained from the [0, +45, 90, −45]2s, [0, 90]4s and 16[0] panel lay-ups. After exposing the sample to temperatures of 600 ºC during 1 h with an isolated atmosphere, the polymeric matrix was degraded but not the fibers. Figure 4 illustrates the fiber orientation and the number of layers of a single scrap tape after the polymer degradation. As was expected, Figure 4a shows the multidirectional orientation of fibers from [0, +45, 90, −45]2s panel, whereas the bidirectional orientation is shown in Figure 4b due to the [0, 90]4s panel and the unidirectional orientation in Figure 4c because of the 16[0] panel. At least two layers are contained in each single scrap tape samples.
The calculations of the void content were performed in accordance to the ASTM D2734 standard. The process adopted for carbon fiber samples was based on acid digestion. The samples' determination were made of the scrap tapes from the different panel configuration and ply level. The values obtained from the average measures of density and void content are collected in Table 1. The results indicate that samples have similar density values and that the fiber content depends on the panel configuration and the ply level where the scrap was obtained from.
Samples | Density (g/cm3) | Void content (%) | Fibre content (%) |
Scrap tape from [0, +45, 90, −45]2s panel | 1.59 | 1.32 | 71.25 |
Scrap tape from [0, 90]4s panel | 1.57 | < 1 | 76.35 |
Scrap tape from 16[0] panel | 1.57 | < 1 | 65.24 |
The tensile properties of the different panel configuration ([0, +45, 90, −45]2s, [0, 90]4s and 16[0]) were compared in Table 2. It is observed that scrap samples from 16[0] panel, where fiber samples match the orientation of the test method, have a higher resistance than samples from ([0, +45, 90, −45]2s and the [0, 90]4s panel. In this regard, scrap samples from 16[0] panel have a tensile strength loss around 23.5% in comparison to the virgin PEKK/AS4 sheet as a reference data.
Samples | Elasticity modulus (GPa) | Standard deviation (GPa) | Tensile strength (MPa) | Standard deviation (MPa) | Yield point at maximum tensile strength (%) | Standard deviation (%) |
Virgin sheet (PEKK/AS4) | 115 | 11.10 | 973.00 | 213.00 | 0.96 | 0.14 |
Scrap [0, +45, 90, −45]2s panel | 63.01 | 4.80 | 504.33 | 77.93 | 0.83 | 0.13 |
Scrap [0, 90]4s panel | 53 | 5.87 | 588.50 | 119 | 1.13 | 0.09 |
Scrap 16[0] panel | 89.07 | 7.54 | 743.50 | 107 | 0.86 | 0.07 |
Additionally, the modulus of elasticity was analyzed and the results are collected in Table 2. As in the case of the tensile properties, the best values were obtained from scrap tape samples of 16[0] panels. Compared to the virgin PEKK/AS4 sheet as a reference data, with 115 GPa, the scrap tape samples achieved 89 GPa, this is, 77% of the original value.
Similar values were found in scrap tape samples after the thermogravimetry analysis. Table 3 indicates the TGA values of the virgin sheet and the scrap tape samples, where the polymeric matrix decomposes under an N2 atmosphere in the first heating ramp and carbon fiber content is obtained after the second heating ramp to 900 ºC under oxidative (air) atmosphere. Results indicate a CF content of ~86.4 wt% and ~84.8 wt% for virgin sheet and the scrap tape samples, respectively. The organic residue in all samples is very low (<1%) (see TGA plots in Figure S1). It can be assumed that no inorganic loads are contained in the evaluated samples.
Samples | % of mass loss in N2 | Range of temperatures in N2 (ºC) | % of mass loss in air | Range of temperatures in air (ºC) |
Virgin sheet (PEKK/AS4) | 12.92 | 45–900 | 86.47 | 400–900 |
Scrap tape | 15.54 | 45–900 | 84.79 | 400–900 |
Concerning the recyclability, each panel type can be scrapped differently, achieving different long fiber scrapped tapes fractions. In the case of [0, +45, 90, −45]2s panels, 62% of the initial panel can be transformed into long fiber scraps. Around 74% of the [0, 90]4s panel can be scrapped into long fiber tapes. This fraction rises to 84% when scrapping 16[0] panels (see Figure 5). The low fraction of tapes obtained in [0, +45, 90, −45]2s panels comes from the deformation arisen during the delamination process both in the workpiece and in the tapes. This deformation facilitates the fragmentation of the scrapped tapes thus increasing the amount of short scrap lower than 200 mm. The [0, 90]4s panels do not have such a deformation problem; however, the lower scrap quality lowers the long tapes fraction due to increased fragmentation of the scrapped tapes during the scrapping process. In the case of the unidirectional panels, where no deformation is observed and the best quality of the scrapped tapes is obtained, the highest conversion into long tapes is achieved.
Through SEM, it could be verified that the structure of the fibers remains oriented and aligned in both materials (cross-section microstructure available in Figure S2).
Specimens were cut from the recycled panels by machining, and the mechanical properties were determined, as shown in Table 4. It is observed that those samples whose fiber orientation matched the test method (long sample) have an average tensile strength of 1160 MPa, having only 11% of mechanical loss compared to the virgin 16[0] panel (1310 MPa).
Samples | Elasticity modulus (GPa) | Standard deviation (GPa) | Tensile strength (MPa) | Standard deviation (MPa) | Yield point at maximum tensile strength (%) | Standard deviation (%) |
Virgin [0, +45, 90, −45]2s panel | 50.10 | 0.52 | 929 | 14 | 1.91 | 0.03 |
Virgin [0, 90]4s panel | 71.90 | 0.88 | 815 | 64 | 1.10 | 0.09 |
Virgin 16[0] panel | 136 | 6.41 | 1310 | 69 | 0.89 | 0.07 |
Recycled panel (long sample) | 118 | 6.44 | 1160 | 58 | 1 | 0.07 |
On the other hand, the average value of the modulus of elasticity of the recycled panel (long sample) is 118 GPa, which is 13% lower than the virgin 16[0] panel (136 GPa) taken as the most representative panel configuration for the case study.
The theoretical value of the percentage by weight for both virgin and recycled panels is approximately ~86–87 wt% carbon fiber (Table 5). Following the same behavior of the scrap tape samples, the organic residue after the observed mass loss in the examined panels has insignificant values (<1%) (see TGA plots in Figure S3).
Samples | % of mass loss in N2 | Range of temperatures in N2 (ºC) | % of mass loss in air | Range of temperatures in air (ºC) |
Virgin panel | 13.03 | 45–900 | 86.66 | 400–900 |
Scrap tape | 13.43 | 45–900 | 85.67 | 400–900 |
A mechanical scrapping process has been developed that delaminates the input material into scrap tapes containing long carbon fibers has been used in a compression molding process controlling the lay-up by means of a universal robot. The use of recycled long fibers together with a controlled lay-up ends in the manufacturing of recycled parts with good mechanical behavior compared to virgin composite panels.
The scrap tapes obtained with the developed mechanical process have a curvature that depends on the lay-up of the input material. Although it was seen that the three tried lay-ups could be managed in a compression mounding process, the unidirectional panels give the best quality scrapped tapes with no curvature. Additionally, the best rate in terms of material recovery from the input panels into scrap tapes containing long fibers was achieved for the 16[0] panel, 84%, decreasing to 74% and 62% for the [0, 90]4s and [0, +45, 90, −45]2s panels, respectively.
This study has shown that the scrapping process appears to recover greater useful scrap material rather than traditional mechanical recycling processes suitable to be used in a compression molding process. Mechanical, thermal and morphological properties of the obtained scrap tapes and the recycled panels were reported. For scrap tape samples from [0, +45, 90, −45]2s, [0, 90]4s and 16[0] panel, a median figure of 504,588 and 743 MPa for tensile strength, respectively, is reported compared with the virgin sheet of 973 MPa. Regarding the modulus of elasticity values of 63, 53 and 89 GPa for the [0, +45, 90, −45]2s, [0, 90]4s and 16[0] panels, respectively, being 115 GPa for the virgin sheet. Not drastic difference is reported in the fiber mass content (~85 wt% of single scrap tapes after scrapping process compared to the virgin sheet ~86 wt%). In recycled panels made of scrap tapes from 16[0] panels laid-up automatically in a aligned way by a collaborative robot, gave a longitudinal tensile strength and elasticity modulus of 1160 and 118 GPa respectively with a minimum mechanical loss of 11% in the strength and 13% in the modulus of elasticity, compared to the virgin 16[0] panel. The mass content values were similar to the virgin panel (around 86 wt%).
The mechanical properties figures compete well with those from the virgin 16[0] panel. Clearly, the scrapping recovery of a great amount of useful scrap tape for panel re-manufacturing with competitive mechanical properties is demonstrated. Fiber distribution in the recycled panel is another source of concern, randomly and orientated fiber of the scrapped tapes is the subject of on-going future work.
The authors declare they have not used Artificial Intelligence (AI) tools in the creation of this article.
Authors would like to thank the Topic Leader the NLR-Netherlands Aerospace Centre for panels supplying. This project has received funding from the European Union's Horizon 2020 research and innovation programme under grant agreement No 887073.
The authors declare no conflict of interest.
[1] |
Fontaine P, Weiss-Hortala E, Botaro V, et al. (2021) Impact of atmosphere on recovered carbon fibers from poly ether ether ketone (PEEK) based composites during thermoconversion. Waste Biomass Valor 12: 6389–6402. https://doi.org/10.1007/s12649-021-01445-7 doi: 10.1007/s12649-021-01445-7
![]() |
[2] |
Borjan D, Knez Ž, Knez M (2021) Recycling of carbon fibre-reinforced composites—difficulties and future perspectives. Materials 12: 4191–4204. https://doi.org/10.3390/ma14154191 doi: 10.3390/ma14154191
![]() |
[3] | Directive 2008/98/EC of the European Parliament and of the Council of 19 November 2008 on waste and repealing certain Directives. Available from: http://data.europa.eu/eli/dir/2008/98/2018-07-05. |
[4] | Chawla KK (2012) Composite Materials Science and Engineering, 3Eds., New York: Springer New York. |
[5] |
Howarth J, Mareddy SSR, Mativenga PT (2014) Energy intensity and environmental analysis of mechanical recycling of carbon fibre composite. J Clean Prod 81: 46–50. https://doi.org/10.1016/j.jclepro.2014.06.023 doi: 10.1016/j.jclepro.2014.06.023
![]() |
[6] | Pickering SJ, Yip H, Kennerley JR, et al. (2000) The recycling of carbon fibre composites using a fluidised bed process, In: Gibson AG, FRC 2000–Composites for the Millennium, Cambridge: Woodhead Publishing. |
[7] |
Lam KL, Oyedun AO, Cheung KY, et al. (2011) Modelling pyrolysis with dynamic heating. Chem Eng Sci 66: 6505–6514. https://doi.org/10.1016/j.ces.2011.09.013 doi: 10.1016/j.ces.2011.09.013
![]() |
[8] | Oliveux G, Dandy L, Leeke GA (2014) A step change in the recycling of composite materials. 16th European Conference on Composite Materials, ECCM 2014, 2–5. |
[9] |
Yang Y, Boom R, Irion B, et al. (2012) Recycling of composite materials. Chem Eng Process 51: 53–68. https://doi.org/10.1016/j.cep.2011.09.007 doi: 10.1016/j.cep.2011.09.007
![]() |
[10] |
Li X, Bai R, McKechnie J (2016) Environmental and financial performance of mechanical recycling of carbon fibre reinforced polymers and comparison with conventional disposal routes. J Clean Prod 127: 451–460. https://doi.org/10.1016/j.jclepro.2016.03.139 doi: 10.1016/j.jclepro.2016.03.139
![]() |
[11] |
Vincent GA (2019) Recycling of thermoplastic composite laminates: The role of processing. University of Twente. https://doi.org/10.3990/1.9789036548526 doi: 10.3990/1.9789036548526
![]() |
[12] |
Vincent GA, de Bruijn TA, Wijskamp S, et al. (2019) Shredding and sieving thermoplastic composite scrap: Method development and analyses of the fibre length distributions. Compos Part B-Eng 176: 107197. https://doi.org/10.1016/j.compositesb.2019.107197 doi: 10.1016/j.compositesb.2019.107197
![]() |
[13] |
Li H, Englund K (2017) Recycling of carbon fibre-reinforced thermoplastic composite wastes from the aerospace industry. J Compos Mater 51: 1265–1273. https://doi.org/10.1177/0021998316671796 doi: 10.1177/0021998316671796
![]() |
[14] |
Roux M, Eguémann N, Dransfeld C, et al. (2017) Thermoplastic carbon fibre-reinforced polymer recycling with electrodynamical fragmentation: From cradle to cradle. J Thermoplast Compos 30: 381–403. https://doi.org/10.1177/0892705715599431 doi: 10.1177/0892705715599431
![]() |
[15] |
Li H, Qin X, He G, et al. (2016) Investigation of chip formation and fracture toughness in orthogonal cutting of UD-CFRP. Int J Adv Manuf Technol 82: 1079–1088. https://doi.org/10.1007/s00170-015-7471-x doi: 10.1007/s00170-015-7471-x
![]() |
[16] |
An Q, Cai C, Cai X, et al. (2019) Experimental investigation on the cutting mechanism and surface generation in orthogonal cutting of UD-CFRP laminates. Compos Struct 230: 111441. https://doi.org/10.1016/j.compstruct.2019.111441 doi: 10.1016/j.compstruct.2019.111441
![]() |
[17] |
Herzog D, Schmidt-Lehr M, Oberlander M, et al. (2016) Laser cutting of carbon fibre reinforced plastics of high thickness. Mater Design 92: 742–749. https://doi.org/10.1016/j.matdes.2015.12.056 doi: 10.1016/j.matdes.2015.12.056
![]() |
[18] |
MM IW, Azmi A, Lee C, et al. (2018) Kerf taper and delamination damage minimization of FRP hybrid composites under abrasive water-jet machining. Int J Adv Manuf Technol 94: 1727–1744. https://doi.org/10.1007/s00170-016-9669-y doi: 10.1007/s00170-016-9669-y
![]() |
[19] | de Bruijn TA, Vincent GA, van Hattum F (2017) Recycling C/PPS laminates into long fibre thermoplastic composites by low shear mixing. 21st International Conference on Composite Materials 2017, 20–25. Available from: http://www.iccm-central.org/Proceedings/ICCM21proceedings/papers/4122.pdf. |
[20] |
Vincent GA, de Bruijn TA, Wijskamp S, et al. (2021) Characterisation and improvement of the quality of mixing of recycled thermoplastic composites. Compos Part C-Open 4: 100108. https://doi.org/10.1016/j.jcomc.2021.100108 doi: 10.1016/j.jcomc.2021.100108
![]() |
[21] |
Feraboli P, Cleveland T, Ciccu M, et al. (2010) Defect and damage analysis of advanced discontinuous carbon/epoxy composite materials. Compos Part A-Appl S 41: 888–901. https://doi.org/10.1016/j.compositesa.2010.03.002 doi: 10.1016/j.compositesa.2010.03.002
![]() |
[22] |
Landry B, Hubert P (2015) Experimental study of defect formation during processing of randomly-oriented strand carbon/PEEK composites. Compos Part A-Appl S 77: 301–309. https://doi.org/10.1016/j.compositesa.2015.05.020 doi: 10.1016/j.compositesa.2015.05.020
![]() |
![]() |
![]() |
1. | Yağız Özbek, Abdulrahman Al-Nadhari, Volkan Eskizeybek, Mehmet Yıldız, Hatice Sinem Şaş, Influence of Strand Size and Morphology on the Mechanical Performance of Recycled CF/PEKK Composites: Harnessing Waste for Aerospace Secondary Load-Bearing Applications, 2025, 13598368, 112232, 10.1016/j.compositesb.2025.112232 |
Samples | Density (g/cm3) | Void content (%) | Fibre content (%) |
Scrap tape from [0, +45, 90, −45]2s panel | 1.59 | 1.32 | 71.25 |
Scrap tape from [0, 90]4s panel | 1.57 | < 1 | 76.35 |
Scrap tape from 16[0] panel | 1.57 | < 1 | 65.24 |
Samples | Elasticity modulus (GPa) | Standard deviation (GPa) | Tensile strength (MPa) | Standard deviation (MPa) | Yield point at maximum tensile strength (%) | Standard deviation (%) |
Virgin sheet (PEKK/AS4) | 115 | 11.10 | 973.00 | 213.00 | 0.96 | 0.14 |
Scrap [0, +45, 90, −45]2s panel | 63.01 | 4.80 | 504.33 | 77.93 | 0.83 | 0.13 |
Scrap [0, 90]4s panel | 53 | 5.87 | 588.50 | 119 | 1.13 | 0.09 |
Scrap 16[0] panel | 89.07 | 7.54 | 743.50 | 107 | 0.86 | 0.07 |
Samples | % of mass loss in N2 | Range of temperatures in N2 (ºC) | % of mass loss in air | Range of temperatures in air (ºC) |
Virgin sheet (PEKK/AS4) | 12.92 | 45–900 | 86.47 | 400–900 |
Scrap tape | 15.54 | 45–900 | 84.79 | 400–900 |
Samples | Elasticity modulus (GPa) | Standard deviation (GPa) | Tensile strength (MPa) | Standard deviation (MPa) | Yield point at maximum tensile strength (%) | Standard deviation (%) |
Virgin [0, +45, 90, −45]2s panel | 50.10 | 0.52 | 929 | 14 | 1.91 | 0.03 |
Virgin [0, 90]4s panel | 71.90 | 0.88 | 815 | 64 | 1.10 | 0.09 |
Virgin 16[0] panel | 136 | 6.41 | 1310 | 69 | 0.89 | 0.07 |
Recycled panel (long sample) | 118 | 6.44 | 1160 | 58 | 1 | 0.07 |
Samples | % of mass loss in N2 | Range of temperatures in N2 (ºC) | % of mass loss in air | Range of temperatures in air (ºC) |
Virgin panel | 13.03 | 45–900 | 86.66 | 400–900 |
Scrap tape | 13.43 | 45–900 | 85.67 | 400–900 |
Samples | Density (g/cm3) | Void content (%) | Fibre content (%) |
Scrap tape from [0, +45, 90, −45]2s panel | 1.59 | 1.32 | 71.25 |
Scrap tape from [0, 90]4s panel | 1.57 | < 1 | 76.35 |
Scrap tape from 16[0] panel | 1.57 | < 1 | 65.24 |
Samples | Elasticity modulus (GPa) | Standard deviation (GPa) | Tensile strength (MPa) | Standard deviation (MPa) | Yield point at maximum tensile strength (%) | Standard deviation (%) |
Virgin sheet (PEKK/AS4) | 115 | 11.10 | 973.00 | 213.00 | 0.96 | 0.14 |
Scrap [0, +45, 90, −45]2s panel | 63.01 | 4.80 | 504.33 | 77.93 | 0.83 | 0.13 |
Scrap [0, 90]4s panel | 53 | 5.87 | 588.50 | 119 | 1.13 | 0.09 |
Scrap 16[0] panel | 89.07 | 7.54 | 743.50 | 107 | 0.86 | 0.07 |
Samples | % of mass loss in N2 | Range of temperatures in N2 (ºC) | % of mass loss in air | Range of temperatures in air (ºC) |
Virgin sheet (PEKK/AS4) | 12.92 | 45–900 | 86.47 | 400–900 |
Scrap tape | 15.54 | 45–900 | 84.79 | 400–900 |
Samples | Elasticity modulus (GPa) | Standard deviation (GPa) | Tensile strength (MPa) | Standard deviation (MPa) | Yield point at maximum tensile strength (%) | Standard deviation (%) |
Virgin [0, +45, 90, −45]2s panel | 50.10 | 0.52 | 929 | 14 | 1.91 | 0.03 |
Virgin [0, 90]4s panel | 71.90 | 0.88 | 815 | 64 | 1.10 | 0.09 |
Virgin 16[0] panel | 136 | 6.41 | 1310 | 69 | 0.89 | 0.07 |
Recycled panel (long sample) | 118 | 6.44 | 1160 | 58 | 1 | 0.07 |
Samples | % of mass loss in N2 | Range of temperatures in N2 (ºC) | % of mass loss in air | Range of temperatures in air (ºC) |
Virgin panel | 13.03 | 45–900 | 86.66 | 400–900 |
Scrap tape | 13.43 | 45–900 | 85.67 | 400–900 |