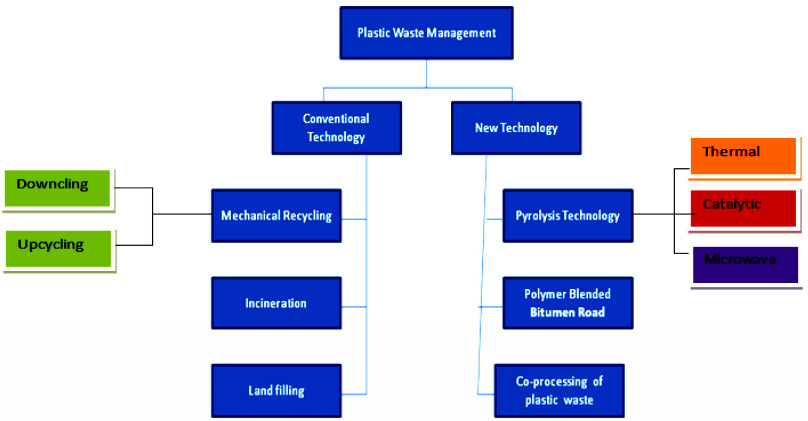
The world is today faced with the problem of plastic waste pollution more than ever before. Global plastic production continues to accelerate, despite the fact that recycling rates are comparatively low, with only about 15% of the 400 million tonnes of plastic currently produced annually being recycled. Although recycling rates have been steadily growing over the last 30 years, the rate of global plastic production far outweighs this, meaning that more and more plastic is ending up in dump sites, landfills and finally into the environment, where it damages the ecosystem. Better end-of-life options for plastic waste are needed to help support current recycling efforts and turn the tide on plastic waste. A promising emerging technology is plastic pyrolysis; a chemical process that breaks plastics down into their raw materials. Key products are liquid resembling crude oil, which can be burned as fuel and other feedstock which can be used for so many new chemical processes, enabling a closed-loop process. The experimental results on the pyrolysis of thermoplastic polymers are discussed in this review with emphasis on single and mixed waste plastics pyrolysis liquid fuel.
Citation: Wilson Uzochukwu Eze, Reginald Umunakwe, Henry Chinedu Obasi, Michael Ifeanyichukwu Ugbaja, Cosmas Chinedu Uche, Innocent Chimezie Madufor. Plastics waste management: A review of pyrolysis technology[J]. Clean Technologies and Recycling, 2021, 1(1): 50-69. doi: 10.3934/ctr.2021003
[1] | Wilson Uzochukwu Eze, Reginald Umunakwe, Michael Ifeanyichukwu Ugbaja, Mohammed Kabiru Yakubu, Narcillina Nkechi Adegboro, Amina Hassan Bayero, Maryann Ifeoma Uzochukwu . Utilization of commodity plastic wastes in flexible pavement: A review. Clean Technologies and Recycling, 2023, 3(1): 71-91. doi: 10.3934/ctr.2023005 |
[2] | Kyle Pender, Liu Yang . Glass fibre composites recycling using the fluidised bed: A study into the economic viability in the UK. Clean Technologies and Recycling, 2023, 3(3): 221-240. doi: 10.3934/ctr.2023014 |
[3] | Tanay Kuclourya, Roberto Monroy, Miguel Castillo, David Baca, Rafiq Ahmad . Design of a hybrid high-throughput fused deposition modeling system for circular economy applications. Clean Technologies and Recycling, 2022, 2(4): 170-198. doi: 10.3934/ctr.2022010 |
[4] | Wilson U. Eze, Toyese Oyegoke, Jonathan D. Gaiya, Reginald Umunakwe, David I. Onyemachi . Review of personal protective equipment and their associated wastes, life-cycle and effective management during the Covid-19 pandemic in developing nations. Clean Technologies and Recycling, 2022, 2(1): 1-31. doi: 10.3934/ctr.2022001 |
[5] | Chukwuebuka C. Okafor, Chinelo A. Nzekwe, Nixon N. Nduji, Charles C. Ajaero, Juliet C. Ibekwe . Energy and material recovery potential from municipal solid wastes (MSW) in Nigeria: Challenges and opportunities. Clean Technologies and Recycling, 2022, 2(4): 282-307. doi: 10.3934/ctr.2022015 |
[6] | Shuwen Zhang, Noah Kirumira . Techniques of recycling end-of-life wind turbine blades in the pavement industry: A literature review. Clean Technologies and Recycling, 2024, 4(1): 89-107. doi: 10.3934/ctr.2024005 |
[7] | Suman Kunwar . MWaste: An app that uses deep learning to manage household waste. Clean Technologies and Recycling, 2023, 3(3): 119-133. doi: 10.3934/ctr.2023008 |
[8] | Congying Wang, Fu Zhao, Carol Handwerker . Transforming and integrating informal sectors into formal e-waste management system: A case study in Guiyu, China. Clean Technologies and Recycling, 2022, 2(4): 225-246. doi: 10.3934/ctr.2022012 |
[9] | Glenn Baxter . Towards sustainable airport waste management through the adoption of a "green" airport strategy: The case of Incheon International Airport. Clean Technologies and Recycling, 2022, 2(4): 247-278. doi: 10.3934/ctr.2022013 |
[10] | Dmitry Baturkin, Ousmane A. Hisseine, Radhouane Masmoudi, Arezki Tagnit-Hamou, Slimane Metiche, Luc Massicotte . Compressive behavior of FRP-tube-confined concrete short columns using recycled FRP materials from wind turbine blades: Experimental investigation and analytical modelling. Clean Technologies and Recycling, 2022, 2(3): 136-164. doi: 10.3934/ctr.2022008 |
The world is today faced with the problem of plastic waste pollution more than ever before. Global plastic production continues to accelerate, despite the fact that recycling rates are comparatively low, with only about 15% of the 400 million tonnes of plastic currently produced annually being recycled. Although recycling rates have been steadily growing over the last 30 years, the rate of global plastic production far outweighs this, meaning that more and more plastic is ending up in dump sites, landfills and finally into the environment, where it damages the ecosystem. Better end-of-life options for plastic waste are needed to help support current recycling efforts and turn the tide on plastic waste. A promising emerging technology is plastic pyrolysis; a chemical process that breaks plastics down into their raw materials. Key products are liquid resembling crude oil, which can be burned as fuel and other feedstock which can be used for so many new chemical processes, enabling a closed-loop process. The experimental results on the pyrolysis of thermoplastic polymers are discussed in this review with emphasis on single and mixed waste plastics pyrolysis liquid fuel.
The discovery of synthetic plastics in 1907 and it(s) rapid commercialization in the early 1950's [1] has brought about advances in technology cutting across all facets of human endeavours. For instance, plastics have contributed extensively to the development of computers, cell phones, light weight automobile parts, roofing and ceiling materials as well as most of the lifesaving advances of modern medicine among many other areas of application. Even the current fight against COVID 19 pandemic will be impossible without personal protective gears made largely from plastics [2,3]. Furthermore, plastics have shown excellent insulating and dielectric properties and as such are widely employed in the fields of electrical and electronics [4,5].
Owing to the increasing these applications and more, we have become increasingly addicted to this modern material most of which are single-use articles.
In recent decades, the production and consumption of plastics have increased. Between 1950 and 2015, about 8,300 million tonnes (Mt) of virgin plastics were produced across the globe, generating approximately 6,300 Mt of plastic wastes, of which about 9% have been recycled, 12% incinerated, and 79% accumulated in landfills [6]. Consequently, the volumes of post-consumer plastic waste (PCPW) are steadily on the increase in the environment [7,8]. Global plastic production was estimated at around 300 million tons per year and is continuously increasing every year [9,10]. Waste generated from indiscriminate disposal of used plastics represents a considerable proportion of the total waste stream in many countries today [11,12]. Even more worrisome is the marine plastic litters which have been found to disintegrate into microplastics and nanoplastics, and are consumed by aquatic animals [13,14,15,16]. Research has shown that this poses serious negative impact on population and mortality of zooplankton which is an important source of energy for marine environment [15].
Presently, plastic wastes pose danger to global economy, human, animal and environment, especially for under developed and developing countries, which lack modern recycling facilities and weak policies on plastics production, usage and regulation [17].
Depending on type, application and service condition, plastic may contain some if not all of the following additives; plasticizers, fire retardants, antioxidants, light stabilisers, lubricants, pigments, antistatic agents and thermal stabilisers. Research has shown that many of these additives find their ways into human and animal systems and has the ability to mimic, block, or interfere with hormones in the body's endocrine system as such, are classified as endocrine disrupting chemicals (EDCs) [18]. Many have also been listed as Persistent organic pollutants (POPs), sometimes known as "forever chemicals". They are organic compounds that are resistant to environmental degradation through chemical, biological, and photolytic processes. Most flame retardants; polychlorinated biphenyls (PCBs), hexachlorobenzene, polybrominated diphenyl ethers (PBDs), hexabromobiphenyls (HBB), hexabromocyclododecane (HBCD), short-chain chlorinated paraffins (SCCPs) and the fluorinated tensides like perfluorooctanoic acid (PFOA) are all in this class [19].
While plastics have demonstrated excellent properties and uses towards advances in modern technology, inappropriate use, disposal of its waste and weak regulation on addition of additives in plastics meant for food packaging may result in the release of toxic substances, which is fueled by open burning of domestic and industrial plastics [20]. In this regard authorities around the world have resorted to non-scientific approach, such as waste plastic buyback, partial to outright ban of some categories of plastic articles in a bid to circumvent pollution from used discarded plastics [21,22]. However, these policies have not yielded substantial positive impact because of both; negative economic, legislative, political, technical and operational limitations [23,24].
To keep-up with the technological advances brought about by the use of plastics and its sustainable economic growth, it will require more than the mechanical recycling techniques; where used plastics are down cycled or up-cycled to a more holistic close loop approach. Mechanical recycling only delays the time taken for used plastics to get to the dumpsites and marine environment. The only way to permanently eliminate plastic waste is by destructive thermal treatment, such as controlled combustion or pyrolysis. Pyrolysis of plastic wastes is a holistic close-loop approach; a technique used to convert plastic waste into energy, in the form of solid, liquid and gaseous fuels [25,26,27].
Unlike mechanical recycling, Pyrolysis seems to be a suitable way to recover materials and energy from wastes plastic without selectivity of plastic type (thermoplastic or thermosetting) [28], component separation or sorting into various plastic type [27], provided an efficient method for reducing toxic compounds is applied.
In this reviews, we present conventional approach for plastics waste management with emphasis on their drawbacks and critical review on pyrolysis techniques as an effective depolymerisation approach for energy and resource recovery from waste plastics.
The conventional and new technologies for plastic waste management are shown in Figure 1. The conventional methods include:
Landfilling is the most common conventional approach for waste management in many countries, however, due to increasing human population and consequential urbanization has lead to scarcity of space for landfills. Plastic waste landfilling is the least favoured waste management option today because of growing environmental and public health concern. The types and quantities of toxic chemicals and their potential for leaching at landfill sites into groundwater is a huge public health issue [29].
Open burning of plastics fraction in municipal solid waste (MSW) is an old practice that is still prevalent in most communities around the world especially in underdeveloped and developing countries. Incineration of plastic waste in open fields is a major source of air pollution. About 12 percent of most municipal solid waste is made up of plastics of different kind, and 40 percent of the world's garbage is burned [30].
The burning of plastics releases toxic gases like dioxins, furans, mercury and polychlorinated biphenyls (better known as BCPs) into the atmosphere, and poses a threat to vegetation, and human and animal health [20]. Disposal of waste into landfills implies an irreversible loss of valuable raw materials and energy. The incomplete combustion of Polyethylene (PE), Polypropylene (PP) and Polystyrene (PS) during open burning can cause high concentrations of carbon monoxide (CO) and noxious emissions, while PVC generates dioxins, carbon black and aromatics like pyrene and chrysene.
Furthermore, the by-products of plastic combustion are airborne particulate emission (soot) and solid residue ash (black carbonaceous colour). Many studies have reported that soot and solid residue ash possess a high potential of causing health and environmental concerns, especially Volatile organic compounds (VOCs), semi-VOCs, smoke (particulate matter), particulate bound heavy metals, polycyclic aromatic hydrocarbons (PAH's), polychlorinated dibenzofurans (PCDF's) and dioxins [20,31].
Currently, landfills and dumpsites pose threat in most cities around the world as plastic fraction in MSW is burnt along with other wastes, a concerted and deliberate effort is needed to communicate information about danger of this practice, its health and environmental consequences in the long and short time.
Mechanical recycling of plastics refers to the processing of plastics waste into secondary raw material or products without significantly changing the chemical structure of the material. In principle, all types of thermoplastics can be mechanically recycled with little quality impairment which depends on the number of time the article is recycled. Additions of additive and blending with virgin plastic could help improve the quality of the new article. It is currently the almost, if not, the sole form of recycling in most countries, representing more than 99% of the recycled quantities.
The burden from collection, sorting, transport and recycling operations tends to render the process cost ineffective; as such most plastic processing companies tends to prefer the use of virgin material to the detriment of the environment.
Mechanical recycling of plastic wastes can be classified into: downcycling and upcycling.
Downcycling, is the recycling of plastic waste where the recycled material is of lower quality and functionality than the original material. However, unlike other materials like glass and metal, recycled plastics are not able to continually serve the same purpose after recycling. This is usually so because plastics tend to lose certain qualities like, mechanical integrity, optical clarity and other inherent properties, as such renders it unfit for its initial application. For example, a plastic water bottle may be downcycled to become artificial turf or plastic furniture. Generally, mechanical recycling of plastics by heating and rmoulding operations leads to downcycling in the long run; this is because the material overtime is no longer suitable for articles with stringent engineering requirements.
Upcycling, also known as creative reuse, is the process of transforming waste plastic materials into new materials or products perceived to be of greater quality, such as artistic value or environmental value. For example, Plastic bottles can be upcycled into flower pots, bird feeders, garden sprinklers, green parking canopy, chandeliers, Christmas trees, kid's toys, and more. However, as stated earlier in 2.3.1 above, if heating and remoulding is involved in the repurposing process of waste plastics articles is not able to serve in most stringent engineering application over time, hence are downcycled. Upcycling of waste single and mixed plastics have been achieved through thermo-chemical processes. pyrolysis is one of such thermo-chemical processes techniques that is gaining much attention today.
Pyrolysis is the thermal degradation of plastic waste at different temperatures (300–900℃), in the absence of oxygen, to produced liquid and gaseous fuel [9]. In pyrolysis, feedstock such as waste plastic is heated in the absence of oxygen or low-oxygen environment and, instead of burning, breaks down into mixture of simpler hydrocarbons. This process is simply thermal depolymerisation, plastics are made from small building blocks (monomers) through a process known as polymerization. Pyrolysis is a process that revert used, discarded plastics into valuable resource in the form of monomers, fuel and other useful resources.
Pyrolysis presents a several advantages over other conventional waste plastic management approaches. For instance most waste plastics during recycling are down cycled; plastics are used in producing articles of lower quality and application. This is because the plastic tends to lose properties such as clarity, strength and flexibility as they are recycled again and again.
Secondly, the cost associated with sorting, washing and blending before waste plastics are recycled mechanically is completely non-existing in pyrolysis technique.
Furthermore, mechanical recycling involves melting and remolding of used or discarded plastics into new articles. This implies that only wastes from thermoplastic articles are suitable for this technique, therefore thermoset fraction will persist in the dumpsites since they cannot be remolded. On the other hand, in pyrolysis techniques, both thermoset and thermoplastic can be used as feedstock [26]. Pyrolysis technique can also be used to treat waste of many novel materials, such as composites [32], especially in the emerging technology were polymer composites are replacing traditional materials in most engineered application.
Finally, depending on the feedstock composition, process condition (temperature, heating rate, reaction gas) and presence of catalyst (catalytic pyrolysis) or absence of catalyst (thermal pyrolysis), the product and yield composition can be varied.
Slow pyrolysis is the slow heating of the feedstock in absence of oxygen. Instead of combusting, the volatiles from the organic material evaporate partly, and a product (char) remains, consisting for a large part (normally 80%) of carbon. Slow pyrolysis is also called carbonisation, and emphasises the solid char as main product, instead of fast pyrolysis which emphasises the liquid product. Heating rates is kept at 10℃/s.
Fast pyrolysis involves rapidly heating the feedstock to moderate temperatures (400–600℃) at short residence time (few seconds) to yield high amount of pyrolysis liquid fuel. Fast pyrolysis provides a condition to maximize the production of the liquid, the reactor is considered to operate isothermally. It is the most common of the methods, both in research and in practical use in pyrolysis of plastics. Heating rates is kept at 100℃/s.
Ultra-fast, or flash pyrolysis is an extremely rapid thermal decomposition pyrolysis, with a high heating rate, the main products are gases and bio-oil. Heating rates can vary from 100–10,000℃/s and residence times are short in duration.
Thermal cracking or pyrolysis involves the depolymerisation or cracking of the plastics materials by heating them to a very high temperature in the absence or low oxygen environment. The temperature ranges between 350 and 900℃. The products formed include; gaseous, liquid and carbonized char (solid residues). The liquid fuel is usually recovered from the condensable fraction of the volatile product, while the remaining is a noncondensable high calorific value gas.
Thermal pyrolysis is a thermochemical treatment (TCT) its liquid product is a mixture of paraffins, isoparaffins, olefins, naphthenes, and aromatics. Because of chain scission, breaking of bonds, the intermolecular and intramolecular forces, elevated temperatures of up to 900℃ are required [33]. Scott et al. [34] reported in their work that at temperatures lower than 700℃ the major part of the product yielded was solid, whereas at higher temperatures the main product was a gas. Thermal pyrolysis of most single plastics has been widely reported in literature. The physical properties of the liquid fuel obtained by this process largely vary with the plastic type [35]. Table 1, Gave a summary of some of the properties of liquid fuel from the pyrolysis of different single plastics as reported in literatures.
Plastic fuel | Density 40℃ (g/cm3) | Viscosity at 40℃ (cSt) | Flash point (℃) | Calorific value (MJ/kg) | Appearance | References |
HDPE | 0.800–0.920 | 2.420–2.52 | 40–48 | 45.4 | Light oil, Brown | Kunwar, et al. [36] |
LDPE | 0.768–0.8020 | 1.650–1.801 | 50 | 39.1 | Light oil, Brown | Shah, et al. [37] |
PP | 0.767–0.80 | 2.72 | 31–36 | 40 | Light oil, Yellow | Yohandri, et al. [38] |
PET | 0.087–0.90 | NA | NA | 28.2 | Light oil, Brown | Honus, et al. [39] |
PS | 0.85–0.86 | 1.4 at 50℃ | 28 | 43.0 | Light oil, deep brown | Miandad, et al. [40] |
Note: NA: not available in literature. |
Furthermore, analysis of chemical properties on the produced liquid fuel by thermal pyrolysis technique has shown that it is a mixture of various hydrocarbons Table 2. The chemical properties of the liquid product vary from the other depending on plastic type. The comparative study of chemical structures HDPE, LDPE, PP, PS and PET shows that in HDPE and LDPE similar –CH2– and –CH3– group appear in their polymer chain. However, PS and PET in mixed feed contain aromatic benzene compound [41] which are completely not found in HDPE, LDPE products.
Plastic | Temperature (℃) | Liquid yield (%) | Elemental composition (%) | Carbon number distribution | References | |||
C | H | N | O | |||||
HDPE | 460 | 86 | 85.3 | 14.2 | 0.5 | 0.00 | C3–C28 | Kunwar et al. [36], Olufemi, et al. [41] |
LDPE | 430 | 75.6 | 85.3 | 14.2 | 0.5 | 0.00 | C5–C28 | Olufemi, et al. [41], |
PP | 350 250 | 70 45 | 85.61 | 14.38 | 0.00 | C3–C25 | Yohandri et al. [38], Olufemi et al. [41] | |
PS | 92.32 | 7.73 | 0.00 | 0.00 | NA | Honus, et al. [39] | ||
PET | 450 600 | 59.50 67.70 | 62.10 | 4.21 | - | 33.69 | NA | Honus, et al. [39] |
Note: NA: not available. |
Microwave pyrolysis (also known as microwave-assisted pyrolysis) is pyrolysis that involves microwave dielectric heating. Microwaves interact in three ways with different materials; it is reflected by conductors, transmitted by perfect insulators, or absorbed and decayed on the way inside materials depending on their dielectric properties. The heat is generated in dielectric materials due to agitation of molecules by the alternating electromagnetic fields. The mechanism of plastic microwave pyrolysis is based on absorbing the microwave energy via absorbent and subsequently transferring thermal heat to the plastic via conduction. The physical properties and the volume ratio of the absorbent affect the uniformity of heating distribution. Furthermore, different microwave power gives completely different product distribution.
It has been established that microwave induced pyrolysis can be used to get value added chemicals and fuels through its numerous noted advantages in contrast to thermal and catalytic pyrolysis [42]. The process has the potential for fast, volumetric and selective heating of plastics for the recovery of energy. However, plastics cannot absorb microwave energy, as it has a very low dielectric loss factor. Therefore, an absorbent must be mixed with the plastic to aid in heating the plastic in pyrolysis. Materials with high dielectric loss factor are good candidates as absorbents for plastic pyrolysis e.g. tyre shredded and silicon carbide [43], carbon [44], iron mesh [45].
Microwave pyrolysis of most single plastic types has been reported in literature. Some of these plastics are; polyethylene (PE), polypropylene (PP), polystyrene (PS), poly(ethylene terephthalate) (PET) and polyvinylchloride (PVC). None of these plastics is able to absorb microwave without the use of microwave absorbent. Table 3 below summarizes the yield (solid, liquid and gaseous), absorbent to polymer ratio, run time and microwave power of the above mentioned five plastic types using Tires instead of coal as microwave absorber.
Plastic | Microwave power range (KW) | Time (min) | Absorbent-plastic ratio | Solid (wt%) | Liquid (wt%) | Gas (wt%) |
HDPE | 3 | 75 | 1:2 | 0.40 | 83.92 | 15.68 |
PP | 3 | 68 | 1:2 | 15.89 | 70.82 | 13.29 |
PVC | 3 | 21 | 1:2 | 14.69 | 3.44 | 81.87 |
PET | 1.8–3 | 40 | 2.51 | 38.20 | 35.32 | 26.48 |
PS | 3–6 | 59 | 1:2 | 6.83 | 89.25 | 8.92 |
Note: Source: Undri et al. [46]. |
Catalytic pyrolysis involves the degradation of the polymeric materials by heating them in the absence of oxygen and in the presence of a catalyst. Catalysts are employed in plastic pyrolysis primarily to lower the energy requirement, influence the composition of the product through cracking and reduce the process time. The most commonly used catalysts reported in the literature for plastic waste pyrolysis includes silica alumina [47], zeolites [48], fluid catalytic cracking (FCC) [49] and mobil classification of materials (MCM-41) [10]. Higher conversion is usually achieved with zeolite-based catalysts due to their high acid strength compared to nonzeolitic catalysts, as such tends to give more gaseous product.
The conversion of polyethylene into gasoline-range fuels by two-stage catalytic degradation using silica-alumina and HZSM-5 zeolite was studied by Uemichi et al. [50]. They reported that two-stage method provides some advantages compared with the one-stage degradation over each catalyst. There was an improved gasoline yield and a high octane number despite low aromatics content. Significant results were obtained when silica-alumina and HZSM-5 were used in a weight ratio of 9:1 as upper and lower catalysts, respectively, in a flow reactor. The reverse sequence of catalysts showed no advantage. It was suggested that large pores and moderate acidity of the silica-alumina loaded in the upper layer operated favorably to catalyze the degradation of polyethylene into liquid hydrocarbons. The resulting oils showed low quality, and they were transformed into high-quality gasoline on the strongly acidic sites of the HZSM-5 loaded in the lower layer at the expense of oil yield.
Ratnasari et al. [10] reported a study on catalytic pyrolysis of waste plastics using staged catalysis for production of gasoline range hydrocarbon oils. The catalytic process involved staged catalysis, where a mesoporous catalyst was layered on top of a microporous catalyst with the aim of maximising the conversion of the waste plastic to gasoline range hydrocarbons. The catalysts used were mesoporous MCM-41 followed by microporous ZSM-5, and different MCM-41: zeolite ZSM-5 catalyst ratios were investigated. The MCM-41 and zeolite ZSM-5 were also used alone for comparison. The results showed that using the staged catalysis a high yield of oil product (83.15 wt%) was obtained from high density polyethylene at a MCM-41: ZSM-5 ratio of 1:1 in the staged pyrolysis-catalysis process. The main gases produced were C2 (mainly ethene), C3 (mainly propene), and C4 (mainly butene and butadiene) gases. In addition, the oil product was highly aromatic (95.85 wt% of oil) consisting of 97.72 wt% of gasoline range hydrocarbons.
Furthermore, Uddim et al. [51] studied the degradation of four different types of polyethylene (PE) namely high density PE (HDPE), low density PE (LDPE), linear low density PE (LLDPE), and cross-linked PE (XLPE) was carried out at 430℃ by batch operation using silica-alumina as a solid acid catalyst and thermally without any catalyst. For thermal degradation, both HDPE and XLPE produced a significant amount of wax-like compounds and the yields of liquid products (58–63 wt%) were lower than that of LDPE and LLDPE (76–77 wt%). LDPE and LLDPE produced a very small amount of wax-like compounds. Thus the structure of the degrading polymers influenced the product yields. The liquid products from thermal degradation were broadly distributed in the carbon fraction of n-C5 to n-C25 (boiling point range, 36–405℃). With silica-alumina, all of the polyethylenes were converted to liquid products with high yields (77–83 wt%) and without any wax production. The liquid products were distributed in the range of n-C5 to n-C20 (mostly C5–C12). A solid acid catalyst indiscriminately degraded the various types of polyethylene into light fuel oil with an improved rate [52,53] in separate studies on the effect of nonacidic catalysts for the pyrolysis of plastics using BaCO3 and MgCO3, observed that the % oil yield for MgCO3 and BaCO3 is 33.60% and 29.60% respectively when used as catalyst at 450℃ pyrolysis of High-density polyethylene. In addition, when CaCO3 was used as a catalyst under the same reaction conditions, the obtained % oil yield was 32.20%.
Recently, many researchers have focused on the use of clay as catalyst for plastic pyrolysis [26,27,42]. Hakeem et al. [54] carried out research on catalytic pyrolysis of waste polypropylene using Ahoko kaolin from Nigeria. They reported that in the absence of Ahoko kaolin, the process gave yields of liquid, gaseous, and solid products of 67.48, 8.85, and 23.67 wt%, respectively, but with the kaolin clay in catalytic pyrolysis of the same feedstock for catalyst-to-plastic ratio of 1:1, 1:2, 1:3, and 1:4 at the same operating parameters as in thermal cracking. Optimum yield was obtained at a catalyst-to-plastic ratio of 1:3 with a yield of 79.85, 1.48, and 18.67 wt% for liquid, gaseous, and solid products, respectively.
Catalytic Cracking of Polyethylene over Clay Catalysts and Comparison with an Ultrastable Y Zeolite was conducted by Manos et al. [48], they reported that the clays were found to be less active than US-Y zeolite around 600K, at slightly higher process temperatures, they were able to completely decompose polyethylene. Their yields to liquid products were around 70%, compared to less than 50% over US-Y zeolite. They also observed that the liquid products obtained over the clay catalysts were heavier. These they attribute to the milder acidity of clays.
(1) Effect of Catalyst Contact Mode
There are two basic modes by which catalyst can be used in the pyrolysis of plastics in a reactor: liquid phase contact (in-situ) and vapor phase contact (ex-situ). In the former, the catalyst and polymer are mixed together, and then they are placed in the reactor and heated to appropriate reaction temperature (Figure 2a). However, in the later, the polymer is first subjected to thermolysis to produce the volatile fraction. The catalyst is introduced in the path of the moving vapour, and as the vapour passes through the catalyst, the hydrocarbon vapour is cracked to get the required product distribution (Figure 2b). Xue et al. [55] studied the effects of feedstock-catalyst contact mode for polyethylene (PE), polypropylene (PP), polystyrene (PS) and polyethylene terephthalate (PET). It was found that in-situ catalytic pyrolysis produces higher yields of aromatics than ex-situ catalytic pyrolysis for PET, PE and PP. For PS, ex-situ catalytic pyrolysis produced more aromatics than in-situ catalytic pyrolysis because of a high yield of styrene in the products. They concluded that the variations in the product composition from the two modes suggest that the depolymerization of the plastics occur at different reaction mechanisms.
(2) Effect of polymer to catalyst ratio
Several studies have reported that polymer to catalyst ratio has significant effect on both the yield and composition of plastic pyrolysis products. However, it can be concluded that with the increase in the amount of catalyst, a direct proportionality in terms of increase in conversion or general effectiveness is not obtained. The increase in catalyst amount increases the conversion up to particular limit, but a further increase in the catalyst percentage does not give any appreciable increase in the conversion rate. Nnamso et al. [56] studied the effect of polymer to catalyst ratio in the degradation of polyethylene over ultrastable Y zeolite catalysts. An initial sharp increase was observed at lower catalyst to polymer ratio, afterwards a negative correlation was observed with further increase in catalyst composition, showing a maximum at a value around 7% of pure US-Y.
(3) Effect of temperature
Temperature has a strong effect on the pyrolysis process, if the catalytic pyrolysis is taking place at higher operating temperature or at high heating rates, it enhances bond breaking as such tends to favour the production of smaller molecules [57,58]. As the extent of conversion increases with increase in temperature, formation of gaseous product is improved with resulting decrease in liquid products. The effect of different catalysts on the liquid yield and the product distribution becomes less significant with increasing temperature this is because the reaction taking place becomes similar to thermal degradation. Basically, catalytic pyrolysis of plastics proceeds at much lower temperature compared with thermal pyrolysis under the same process condition [59,60]. Increase in the cracking rate at lower temperatures was observed under catalytic conditions [61].
(4) Effect of flow rate of nitrogen Gas
Nitrogen is an inert gas, as such does not interfere with the pyrolysis reaction going on inside the reactor. However, it enhances the movement of volatiles into the condenser thereby leading to availability of gases for condensing into liquid fuel. Usually the nitrogen flow rate is kept at about 10 mL/s for most plastic pyrolysis reported in literature [62].
Nowadays, pyrolysis technology is more and more widely used in the waste plastic management instead of landfill or recovery through secondary recycling, since it can convert various kinds of waste plastics to liquid fuel, which can not only effectively manage waste plastic but also bring very good economic benefit.
The liquid fuel from plastic waste is usually heavier compared to conventional commercial grade fuel, consequently has higher heating value slightly lower or greater than 10,000 kcal/L [63,64]. This property is an advantage for fuel used in boilers, cement factory, steel mill and glass factories.
Pyrolysis technology is suitable for almost all kinds of waste plastic, clean or unwashed and unsorted. For a batch waste plastic pyrolysis plant, no need to do the shredding works. All the processes from plastic to fuel are carried out inside the waste pyrolysis reactor together with its accessory system, very convenient and man-power saving. Co-pyrolysis of plastics with waste paper [65], biomass [66] and even plastics from medical wastes [67] has also been reported.
A major advantage of pyrolysis technology for plastic waste management is its ability to use various types and class of plastics as a single feedstock without the need for disassembling and sorting. Unlike recycling, pyrolysis does not require a careful sorting of different plastics. Most plastics are not compatible with each other consequently, cannot be processed together during recycling. For example, a little fraction of PVC in PET recycle stream will degrade the whole PET resin by becoming yellowish and brittle [68].
Demirbas [69] on polyolefin and PS mixture collected from landfill which was approximately 46.6 wt% of total plastic waste yielded 35 wt% of solid and of 2.2 wt% of gas. Baiden [67] carried out pyrolysis of mixed waste plastics comprising HDPE, LDPE, PP and Thermoplastic Polyurathane, TPU. They reported that the highest liquid product yield was obtained using 80 V for 55 min and was 89.5 wt% of the initial weight of the plastic waste sample pyrolyzed. The recorded maximum reaction temperature recorded for this yield was 497–500℃.
Donaj et al. [70] conducted a study on pyrolysis of polyolefin mixed plastics. The mixed plastics consist of 75 wt% LDPE, 30 wt% HDPE and 24 wt% PP. They conducted two sets of experiments at 650 and 730℃ by thermal pyrolysis and at 500 and 650℃ using Z–N catalyst in fluidized quartz-bed reactor. The ratios of gas/liquid/solid mass fractions via thermal pyrolysis were: 36.9/48.4/15.7 wt%. and 42.4/44.7/13.9 wt% at 650 and 730℃ while via catalytic pyrolysis were: 6.5/89.0/4.5 wt% and 54.3/41.9/3.8 wt% at 500 and 650℃, respectively.
Pratama and Saptoadi [71] studied the pyrolysis of mixed waste plastics in two stages batch reactors: pyrolysis and catalytic reforming reactor, at maximum temperature 500℃ and 450℃ respectively. They used Waste Polyethylene (PE), Polypropylene (PP), Polystyrene (PS), Polyethylene Terepthalate (PET) were used as raw material. They reported that the highest weight percentage of liquid fuel derived from mixture of PE waste (50 wt%), PP waste (40 wt%) and PS waste (10 wt%) is 45.13 wt%.
Eze et al. [26] conducted a study on thermal and catalytic pyrolysis using five different types of plastics that dominates in municipal solid wastes stream, mimicking the proportion in which they are found. Figure 3 shows the composition of the feedstock and yield.
The catalyzed liquid sample with the optimum yield of 46.7wt% was obtained using 10.49 wt%, 32.42 wt%, 27.09 wt% and 30 wt%, of Zeolite-Y, metakaolin, aluminun hydroxide and sodium silicate respectively as catalyst, while the thermal pyrolysis gave a liquid yield of 66.9 wt% (Figure 3).
The use of the zeolite-Y base catalyst led to reduction of pyrolysis temperature from 490℃ to 350℃, this is a huge energy reduction for the overall process. Some of the physical properties reported in this study include; density at 23℃ (0.8945 g/cm3), dynamic viscosity at 32℃ (2.03 mPa.s), fire point (90℃) and calorific value (14,751 J/g) for thermal pyrolysis. The corresponding values for catalytic pyrolysis were density at 23℃ (0.8336 g/cm3), dynamic viscosity at 32℃ (1.03 mPa.s), fire point (84℃) and calorific value (24,919 J/g) respectively.
Gas Chromatography and Mass Spectrometer (GC/MS) analysis of most studies on mixed waste plastics (MWPs) liquid fuel reveals that catalysed liquid fuel contain light liquid product with carbon range C6–C13 and absence of long chain alkanes and alkenes such as Eicosane, nonadecane, heptadecane, octadecene, pentadecane, tetradecane and undecene compared to the thermal pyrolysis liquid product with carbon range of C7–C20 [26,54,67,72].
Wathakit et al. [72] studied the chemical compositions and physicochemical properties of distilled waste plastic oil (WPO) and crude waste plastic oil (CWPO).The experimental results show that CWPO contains the highest percentage of carbon atoms in the C4–C11 group, while WPO contains the highest percentage of carbon atoms in the C12–C20 group, similar to the main compositions of diesel fuel.
Similarly, Eze et al. [26] studied the effect of zeolite-y based catalyst on pyrolysis fuel from mixed waste plastics comprising HDPE, LDPE, PP and PS in the ratio shown in Figure 3. The result of the study revealed that catalysed liquid sample consist of predominantly gasoline (93%) and 7% diesel range of fuel compared to the thermal pyrolysis liquid sample with 59%, 36% and 5% of gasoline, diesel and fuel oil respectively Table 4. The organic elemental analysis (CHNS) result of the MWPs for both thermal and catalysed sample with optimum yield is shown in Table 5. Sulphur content of the catalysed pyrolysis fuel was slightly lower than that of the thermal pyrolysis product; this can be attributed to the activities of the catalyst. Lower sulphur content is necessary to reduce possibility of formation of sulfur oxides (SOx) when fuel is burn in internal combustion engines [73]. The sulphur content of MWPs for both thermal and catalysed samples are significantly higher than gasoline (0.014%), diesel (0.15%), and other types of fuel oil because waste plastic contains some contamination [63]. However, plastic pyrolysis fuel can be subjected to desulphurization to bring its sulphur content to acceptable limit.
Gasoline (wt%) (C6–C12) | Diesel (wt%) (C13–C18) | Fuel oil (wt%) (C19–C23) | Residual fuel (wt%) (C24) | |
Thermal pyrolysis | 59 | 36 | 5 | - |
Catalysed pyrolysis | 93 | 7 | - | - |
Note: Source: Eze et al. [27]. |
Wt% | Thermal pyrolysis | Catalysed pyrolysis |
C | 94.24 | 97.11 |
H | 11.73 | 10.12 |
N | 0.61 | 0.28 |
S | 4.8 | 4.36 |
Note: Source: Eze et al. [27]. |
Liquid fuel from plastic waste has higher sulfur content than conventional fuel, even though many industries are equipped with environment protection devices to scrubber the smoke produced in the heating process, this becomes a huge concern for automobile and transportation fuel. The presence of sulphur in vehicle fuels causes emissions of oxides of sulphur into the atmosphere which is a major contributor of acid rain.
Liquid fuel from pyrolysis of different plastic types has been reported to have sulphur content significantly higher than conventional gasoline, kerosene and commercial grade diesel. Khan et al. [63] carried out pyrolysis of High density polyethylene, HDPE, to obtain waste plastic pyrolysis oil (WPPO). They reported sulphur content of 0.246% for the WPPO which is significantly higher than 0.15% for diesel and 0.014% for gasoline Figure 4. Furthermore, Eze et al. [27] reported that the sulphur content of both thermal (4.8%) and catalytic (4.36%) pyrolysis liquid fuel obtained from mixed waste plastics Table 3, are higher than the desired acceptable standard for low sulphur and ultra low sulfur fuel [74].
The flash point of liquid fuel from plastic waste is < 40 degrees, though it may vary depending on the plastic type used as feed. For single feed plasticlike polyethylene it could be as low as 10 degrees. The flash point of conventional diesel is about 50 degrees. A low flash point indicates the presence of highly volatile materials in the fuel that is a serious safety concern in handling and transporting [63].
Authorities around the world are intensifying their call for ban of certain catigories of plastics; this is because the conventional approaches have not impacted the environment positively. Furthermore, mechanical recycling of plastics is being considered as one of the most widely accepted remedies to the threat of growing volume of plastic waste by both the public and scientists. In practice, the approach is associated with many difficulties, such as problems related to separation, sorting and cleaning operations, high transport and electricity costs, coupled with feed stock selectivity.
Instead of combustion and incineration, pyrolysis can be another alternative method which is known to produce less toxic substances provided the process conditions are appropriate; fuel and several other useful raw materials are recovered in the process. Furthermore, the increasing amounts of plastic waste and the increasing fraction of thermosetting plastics highlight the importance of pyrolysis as a holistic approach. However, there are understandable issues surrounding the toxic byproducts generated by the pyrolysis of certain plastics like polyvinyl chloride, this can be negated through proper feedstock selection. Finally, liquid fuel from plastic pyrolysis may not be suitable for most engineered application due to high sulphur content. However, by further treatment and blending with commercial grade fuel, this can be circumvented.
The authors declare no conflict of interest.
[1] | Philippe C (2019) The history of plastics: from the capitol to the Tarpeian Rock. Field Actions Sci Rep 19: 6-11. |
[2] |
Livingston E, Desai A, Berkwits M (2020) Sourcing personal protective equipment during the COVID-19 pandemic. JAMA 323: 1912-1914. doi: 10.1001/jama.2020.5317
![]() |
[3] |
Czigány T, Ronkay F (2020) The coronavirus and plastics. Express Polym Lett 14: 510-511. doi: 10.3144/expresspolymlett.2020.41
![]() |
[4] | Gaiya JD, Eze WU, Ekpenyong SA, et al. (2018) Effect of carbon particles on electrical conductivity of unsaturated polyester resin composite national engineering conference, 142-144. |
[5] | Gaiya JD, Eze WU, Oyegoke T, et al. (2021) Assessment of the dielectric properties of polyester/metakaolin composite. Eur J Mater Sci Eng 6: 19-29. |
[6] |
Babayemi JO, Nnorom IC, Osibanjo O, et al. (2019) Ensuring sustainability in plastics use in Africa: consumption, waste generation, and projections. Environ Sci Eur 31: 60. doi: 10.1186/s12302-019-0254-5
![]() |
[7] | Li WC, Tse HF, Fok L (2016) Plastic waste in the marine environment: a review of sources, occurrence and effects. Sci Total Environ 567: 333-349. |
[8] |
Geyer R, Jambeck JR, Law KL (2017) Production, use, and fate of all plastics ever made. Sci Adv 3: 1-5. doi: 10.1126/sciadv.1700782
![]() |
[9] |
Miandad R, Barakat MA, Aburiazaiza AS, et al. (2016) Catalytic pyrolysis of plastic waste: a review. Process Safety Environ Protect 102: 822-838. doi: 10.1016/j.psep.2016.06.022
![]() |
[10] |
Ratnasari DK, Nahil MA, Williams PT (2016) Catalytic pyrolysis of waste plastics using staged catalysis for production of gasoline range hydrocarbon oils. J Anal Appl Pyrolysis 124: 631-637. doi: 10.1016/j.jaap.2016.12.027
![]() |
[11] |
Kawai K, Tasaki T (2016) Revisiting estimates of municipal solid waste generation per capita and their reliability. J Mater Cycles Waste Manage 18: 1-13. doi: 10.1007/s10163-015-0355-1
![]() |
[12] | ESI Africa (2018) S. Africa: 1.144 m tonnes of recyclable plastic dumped in landfills. Available from: https://www.esi-africa.com/top-stories/s-africa-1-144m-tonnes-of-recyclable-plastic-dumped-in-landfills/. |
[13] |
Wagner M, Scherer C, Alvarez-Munoz D, et al (2014) Microplastics in freshwater ecosystems: what we know and what we need to know. Environ Sci Eur 26: 9. doi: 10.1186/2190-4715-26-9
![]() |
[14] |
Wrighta SL, Thompson RC, Galloway TS (2013) The physical impacts of microplastics on marine organisms: a review. Environ Pollut 178: 483-492. doi: 10.1016/j.envpol.2013.02.031
![]() |
[15] | Werner S, Budziak A, van Franeker J, et al. (2016) Harm caused by marine litter. MSFD GES TG marine litter—Thematic Report; JRC Technical report; EUR 28317 EN. |
[16] |
Anderson JC, Park BJ, Palace VP (2016) Microplastics in aquatic environments: implications for Canadian ecosystems. Environ Pollut 218: 269-280. doi: 10.1016/j.envpol.2016.06.074
![]() |
[17] |
Srivastava V, Ismail SA, Singh P, et al. (2015) Urban solid waste management in the developing world with emphasis on India: Challenges and opportunities. Rev Environ Sci Bio-Technol 14: 317-337. doi: 10.1007/s11157-014-9352-4
![]() |
[18] |
Schuga TT, Janesickb A, Blumbergb B, et al. (2011) Endocrine disrupting chemicals and disease susceptibility. J Steroid Biochem Mol Biol 127: 204-215. doi: 10.1016/j.jsbmb.2011.08.007
![]() |
[19] | Willner SA, Blumberg B (2019) Encyclopedia of endocrine diseases (second edition). |
[20] |
Verma R, Vinoda KS, Papireddy M, et al. (2016) Toxic pollutants from plastic waste-a review. Procedia Environ Sci 35: 701-708. doi: 10.1016/j.proenv.2016.07.069
![]() |
[21] | Conlon K (2021) A social systems approach to sustainable waste management: leverage points for plastic reduction in Colombo, Sri Lanka. Int J Sustainable Dev World Ecol 1-19. |
[22] |
Clapp J, Swanston L (2009) Doing away with plastic shopping bags: international patterns of norm emergence and policy implementation. Environ Polit 18: 315-332. doi: 10.1080/09644010902823717
![]() |
[23] |
Imam A, Mohammed B, Wilson DC, et al. (2008) Solid waste management in Abuja, Nigeria. Waste Manage 28: 468-472. doi: 10.1016/j.wasman.2007.01.006
![]() |
[24] |
Chida M (2011) Sustainability in retail: The failed debate around plastic shopping bags. Fashion Pract 3: 175-196. doi: 10.2752/175693811X13080607764773
![]() |
[25] | Devy K, Nahil MA, Williams PT (2016) Catalytic pyrolysis of waste plastics using staged catalysis for production of gasoline range hydrocarbon oils. J Anal Appl Pyrolysis 124: 631-637. |
[26] |
Eze WU, Madufor IC, Onyeagoro GN, et al. (2020) The effect of Kankara zeolite-Y-based catalyst on some physical properties of liquid fuel from mixed waste plastics (MWPs) pyrolysis. Polym Bull 77: 1399-1415. doi: 10.1007/s00289-019-02806-y
![]() |
[27] |
Eze WU, Madufor IC, Onyeagoro GN, et al. (2021) Study on the effect of Kankara zeolite-Y-based catalyst on the chemical properties of liquid fuel from mixed waste plastics (MWPs) pyrolysis. Polym Bull 78: 377. doi: 10.1007/s00289-020-03116-4
![]() |
[28] |
Vasile C, Brebu M, Karayildirim T, et al. (2006) Feedstock recycling from plastic and thermoset fractions of used computers (I): pyrolysis. J Mater Cycles Waste Manage 8: 99-108. doi: 10.1007/s10163-006-0151-z
![]() |
[29] |
Teuten EL, Saquin JM, Knappe DR, et al. (2009) Transport and release of chemicals from plastics to the environment and to wildlife. Philos Trans R Soc Lond B Biol Sci 364: 2027-2045. doi: 10.1098/rstb.2008.0284
![]() |
[30] |
Hopewell J, Dvorak R, Kosior E (2009) Plastics recycling: challenges and opportunities. Philos Trans R Soc B 364: 2115-2126. doi: 10.1098/rstb.2008.0311
![]() |
[31] |
Valavanidid A, Iliopoulos N, Gotsis G, et al. (2008) Persistent free radicals, heavy metals and PAHs generated in particulate soot emissions and residual ash from controlled combustion of common type of plastics. J Hazard Mater 156: 277-284. doi: 10.1016/j.jhazmat.2007.12.019
![]() |
[32] |
Qureshi MS, Oasmaa A, Pihkola H, et al (2020) Pyrolysis of plastic waste: Opportunities and challenges. J Anal Appl Pyrolysis 152: 104804. doi: 10.1016/j.jaap.2020.104804
![]() |
[33] |
López A, de Marco I, Caballero BM, et al. (2011) Influence of time and temperature on pyrolysis of plastic wastes in a semi-batch reactor. Chem Eng J 173: 62-71. doi: 10.1016/j.cej.2011.07.037
![]() |
[34] |
Scott DS, Czernik SR, Piskorz J, et al. (1990) Fast pyrolysis of plastic wastes. Energy Fuels 4: 407-411. doi: 10.1021/ef00022a013
![]() |
[35] |
Santaweesuk C, Janyalertadun A (2017) The production of fuel oil by conventional slow pyrolysis using plastic waste from a municipal landfill. Int J Environ Sci Dev 8: 168-173. doi: 10.18178/ijesd.2017.8.3.941
![]() |
[36] |
Kunwar B, Moser BR, Chandrasekaran SR, et al. (2016) Catalytic and thermal depolymerization of low value post-consumer high density polyethylene plastic. Energy 111: 884-892. doi: 10.1016/j.energy.2016.06.024
![]() |
[37] |
Shah J, Jan MR, Mabood F, et al. (2010) Catalytic pyrolysis of LDPE leads to valuable resource recovery and reduction of waste problems. Energy Convers Manage 51: 2791-2801. doi: 10.1016/j.enconman.2010.06.016
![]() |
[38] |
Bow Y, Rusdianasari, Pujiastuti LS (2019) Pyrolysis of polypropylene plastic waste into liquid fuel. IOP Conf Ser: Earth Environ Sci 347: 012128. doi: 10.1088/1755-1315/347/1/012128
![]() |
[39] |
Honus S, Kumagai S, Fedorko G, et al. (2018) Pyrolysis gases produced from individual and mixed PE, PP, PS, PVC, and PET—Part I: Production and physical properties. Fuel 221: 346-360. doi: 10.1016/j.fuel.2018.02.074
![]() |
[40] |
Miandad R, Rehan M, Barakat MA, et al. (2019) Catalytic pyrolysis of plastic waste: Moving Toward Pyrolysis Based Biorefineries. Front Energy Res 7: 27. doi: 10.3389/fenrg.2019.00027
![]() |
[41] |
Olufemi AS, Olagboye S (2017) Thermal conversion of waste plastics into fuel oil. Int J Petrochem Sci Eng 2: 252-257. doi: 10.15406/ipcse.2017.02.00064
![]() |
[42] | Kaminsky W (1992) Plastics, recycling, In: Ullmann's encyclopedia of industrial chemistry, 57 73, Wiley-VCH, 3-52730-385-5, Germany. |
[43] | Meredith R (1998) Engineers' handbook of industrial microwave heating, The Institution of Electrical Engineers, 0-85296-916-3, United Kindom. |
[44] |
Ludlow-Palafox C, Chase HA (2001) Microwave-induced pyrolysis of plastic wastes. Ind Eng Chem Res 40: 4749-4756. doi: 10.1021/ie010202j
![]() |
[45] |
Hussain Z, Khan KM, Hussain K (2010) Microwave-metal interaction pyrolysis of polystyrene. J Anal Appl Pyrolysis 89: 39-43. doi: 10.1016/j.jaap.2010.05.003
![]() |
[46] | Undri A, Rosi L, Frediani M, et al. (2011) Microwave pyrolysis of polymeric materials, Microwave Heating, Usha Chandra, IntechOpen, DOI: 10.5772/24008. Available from: https://www.intechopen.com/books/microwave-heating/microwave-pyrolysis-of-polymeric-materials. |
[47] |
Panda AK, Singh RK (2011) Catalytic performances of kaoline and silica alumina in the thermal degradation of polypropylene. J Fuel Chem Technol 39: 198-202. doi: 10.1016/S1872-5813(11)60017-0
![]() |
[48] | George M, Yusof IY, Papayannakos N, et al. (2001) Catalytic cracking of polyethylene over clay catalysts. Comparison with an Ultrastable Y Zeolite. Ind Eng Chem Res 40: 2220-2225. |
[49] |
Kumar KP, Srinivas S (2020) Catalytic Co-pyrolysis of Biomass and Plastics (Polypropylene and Polystyrene) Using Spent FCC Catalyst. Energy Fuels 34: 460-473. doi: 10.1021/acs.energyfuels.9b03135
![]() |
[50] |
Yoshio U, Nakamura J, Itoh T, et al. (1999) Conversion of polyethylene into gasoline-range fuels by two-stage catalytic degradation using Silica−Alumina and HZSM-5 Zeolite. Ind Eng Chem Res 38: 385-390. doi: 10.1021/ie980341+
![]() |
[51] |
Uddin MA, Koizumi K, Murata K, et al. (1997) Thermal and catalytic degradation of structurally different types of polyethylene into fuel oil. Polym Degrad Stab 56: 37-44. doi: 10.1016/S0141-3910(96)00191-7
![]() |
[52] |
Rasul JM, Shah J, Gulab H (2010) Catalytic degradation of waste high-density polyethylene into fuel products using BaCO3 as a catalyst. Fuel Process Technol 91: 1428-1437. doi: 10.1016/j.fuproc.2010.05.017
![]() |
[53] |
Rasul JM, Shah J, Gulab H (2010) Degradation of waste High-density polyethylene into fuel oil using basic catalyst. Fuel 89: 474-480. doi: 10.1016/j.fuel.2009.09.007
![]() |
[54] |
Hakeem IG, Aberuagba F, Musa U (2018) Catalytic pyrolysis of waste polypropylene using Ahoko kaolin from Nigeria. Appl Petrochem Res 8: 203-210. doi: 10.1007/s13203-018-0207-8
![]() |
[55] |
Xue Y, Johnston P, Bai X (2017) Effect of catalyst contact mode and gas atmosphere during catalytic pyrolysis of waste plastics. Energy Convers Manage 142: 441-451. doi: 10.1016/j.enconman.2017.03.071
![]() |
[56] |
Akpanudoh NS, Gobin K, Manos G (2005) Catalytic degradation of plastic waste to liquid fuel over commercial cracking catalysts: Effect of polymer to catalyst ratio/acidity content. J Mol Catal A: Chem 235: 67-73. doi: 10.1016/j.molcata.2005.03.009
![]() |
[57] |
Bridgewater AV (2012) Review of fast pyrolysis of biomass and product upgrading. Biomass Bioenergy 38: 68-94. doi: 10.1016/j.biombioe.2011.01.048
![]() |
[58] |
Miskolczi N, Angyal A, Bartha L, et al. (2009) Fuel by pyrolysis of waste plastics from agricultural and packaging sectors in a pilot scale reactor. Fuel Process Technol 90: 1032-1040. doi: 10.1016/j.fuproc.2009.04.019
![]() |
[59] |
Chen D, Yin L, Wang H, et al. (2014) Pyrolysis technologies for municipal solid waste: a review. Waste Manage 34: 2466-2486. doi: 10.1016/j.wasman.2014.08.004
![]() |
[60] |
Achilias DS, Roupakias C, Megalokonomos P, et al. (2007) Chemical recycling of plastic wastes made from polyethylene (LDPE and HDPE) and polypropylene (PP). J Hazard Mater 149: 536-542. doi: 10.1016/j.jhazmat.2007.06.076
![]() |
[61] |
Lee SY (2001) Catalytic degradation of polystyrene over natural clinoptilolite zeolite. Polym Degrad Stab 74: 297-305. doi: 10.1016/S0141-3910(01)00162-8
![]() |
[62] | Christine C, Thomas S, Varghese S (2013) Synthesis of petroleum-based fuel from waste plastics and performance analysis in a CI engine. J Energy 2013: 608797. |
[63] | Khan MZH, Sultana M, Al-Mamun MR, et al. (2016) Pyrolytic waste plastic oil and its diesel Blend: fuel characterization. J Environ Public Health 2016: 7869080. |
[64] |
Panda AK, Alotaibi A, Kozhevnikov IV, et al. (2020) Pyrolysis of plastics to liquid fuel using sulphated zirconium hydroxide catalyst. Waste Biomass Valor 11: 6337-6345. doi: 10.1007/s12649-019-00841-4
![]() |
[65] | Sophonrat N (2018) Pyrolysis of mixed plastics and paper to produce fuels and other chemicals. Doctoral Dissertation, KTH Royal Institute of Technology School of Industrial Engineering and Management Department of Materials Science and Engineering Unit of Processes, Sweden. |
[66] |
Supramono D, Nabil M, Setiadi A, et al. (2018) Effect of feed composition of co-pyrolysis of corncobs-polypropylene plastic on mass interaction between biomass particles and plastics. IOP Conf Ser: Earth Environ Sci 105: 012049 doi: 10.1088/1755-1315/105/1/012049
![]() |
[67] | Baiden (2018) Pyrolysis of plastic waste from medical services facilities into potential fuel and/or fuel additives. Master's Theses, 3696. Available from: https://scholarworks.wmich.edu/masters_theses/3696. |
[68] |
Hopewell J, Dvorak R, Kosior E (2009) Plastics recycling: challenges and opportunities. Philos Trans R Soc London B Biol Sci 364: 2115-2126. doi: 10.1098/rstb.2008.0311
![]() |
[69] |
Demirbas A (2004) Pyrolysis of municipal plastic wastes for recovery of gasoline range hydrocarbons. J Anal Appl Pyrol 72: 97-102. doi: 10.1016/j.jaap.2004.03.001
![]() |
[70] |
Donaj PJ, Kaminsky W, Buzeto F, et al. (2012) Pyrolysis of polyolefins for increasing the yield of monomers' recovery. Waste Manage 32: 840-846. doi: 10.1016/j.wasman.2011.10.009
![]() |
[71] | Pratama NN, Saptoadi H (2014) Characteristics of waste plastics pyrolytic oil and its applications as alternative fuel on four cylinder diesel engines. Int J Renewable Energy Dev 3: 13-20. |
[72] |
Wathakit K, Sukjit E, Kaewbuddee C, et al. (2021) Characterization and impact of waste plastic oil in a variable compression ratio diesel engine. Energies 14: 2230. doi: 10.3390/en14082230
![]() |
[73] |
Abnisa F, Wan Daud WMA, Arami-Niya A, et al. (2014) Recovery of liquid fuel from the aqueous phase of pyrolysis oil using catalytic conversion. Energy Fuels 28: 3074-3085. doi: 10.1021/ef5003952
![]() |
[74] | Alam M, Song J, Acharya R, et al. (2004) Combustion and emissions performance of low sulfur, ultra low sulfur and biodiesel blends in a DI diesel engine. SAE Trans 113: 1986-1997. |
1. | Augmentation of Municipal Solid Waste Management in Hyderabad City, 2022, 2581-9429, 410, 10.48175/IJARSCT-4612 | |
2. | Ufuk Vural, Saban Uysal, Abdullah Yinanc, The improved diesel-like fuel from upgraded tire pyrolytic oil, 2022, 87, 0352-5139, 1219, 10.2298/JSC211108048V | |
3. | Abdul Rafey, Kunwar Pal, Ashish Bohre, Arindam Modak, Kamal Kishore Pant, A State-of-the-Art Review on the Technological Advancements for the Sustainable Management of Plastic Waste in Consort with the Generation of Energy and Value-Added Chemicals, 2023, 13, 2073-4344, 420, 10.3390/catal13020420 | |
4. | Agnieszka Kijo-Kleczkowska, Adam Gnatowski, Recycling of Plastic Waste, with Particular Emphasis on Thermal Methods—Review, 2022, 15, 1996-1073, 2114, 10.3390/en15062114 | |
5. | Anna Matuszewska, Adam Hańderek, Maciej Paczuski, Krzysztof Biernat, Hydrocarbon Fractions from Thermolysis of Waste Plastics as Components of Engine Fuels, 2021, 14, 1996-1073, 7245, 10.3390/en14217245 | |
6. | Sahar Jannesarahmadi, Milad Aminzadeh, Roberto Raga, Nima Shokri, Effects of microplastics on evaporation dynamics in porous media, 2023, 311, 00456535, 137023, 10.1016/j.chemosphere.2022.137023 | |
7. | Wilson U. Eze, Toyese Oyegoke, Jonathan D. Gaiya, Reginald Umunakwe, David I. Onyemachi, Review of personal protective equipment and their associated wastes, life-cycle and effective management during the Covid-19 pandemic in developing nations, 2022, 2, 2770-4580, 1, 10.3934/ctr.2022001 | |
8. | Grzegorz Gałko, Marcin Sajdak, Trends for the Thermal Degradation of Polymeric Materials: Analysis of Available Techniques, Issues, and Opportunities, 2022, 12, 2076-3417, 9138, 10.3390/app12189138 | |
9. | Zheli Ding, Sanjeev Kumar Awasthi, Manish Kumar, Vinay Kumar, Andrei Mikhailovich Dregulo, Vivek Yadav, Raveendran Sindhu, Parameswaran Binod, Surendra Sarsaiya, Ashok Pandey, Mohammad J. Taherzadeh, Rashmi Rathour, Lal Singh, Zengqiang Zhang, Zihao Lian, Mukesh Kumar Awasthi, A thermo-chemical and biotechnological approaches for bamboo waste recycling and conversion to value added product: Towards a zero-waste biorefinery and circular bioeconomy, 2023, 333, 00162361, 126469, 10.1016/j.fuel.2022.126469 | |
10. | Nurul Fatin Syamimi Khairul Anuar, Fahrul Huyop, Ghani Ur-Rehman, Faizuan Abdullah, Yahaya M. Normi, Mohd Khalizan Sabullah, Roswanira Abdul Wahab, An Overview into Polyethylene Terephthalate (PET) Hydrolases and Efforts in Tailoring Enzymes for Improved Plastic Degradation, 2022, 23, 1422-0067, 12644, 10.3390/ijms232012644 | |
11. | Adriano da Silva Mateus, Arleth Prata Serafim Francisco, Paulo Francisco, Ngoma Manuel, António André Chivanga Barros, Thermocatalytic Cracking of Frying Oil and Plastic Waste for Production of Organic Liquid Products and Derivatives, 2022, 45, 0930-7516, 1835, 10.1002/ceat.202200171 | |
12. | Ranjan Parajuli, Marty D. Matlock, Greg Thoma, Environmental life cycle impact assessment of fresh California strawberries: A full supply chain perspective, 2022, 6, 26667843, 100073, 10.1016/j.clrc.2022.100073 | |
13. | Ijaz Hussain, Abdullah Aitani, Zuhair Malaibari, Hassan Alasiri, Muhammad Naseem Akhtar, Obaid Fahad Aldosari, Shakeel Ahmed, Chemical Upcycling of Waste Plastics to High Value‐Added Products via Pyrolysis: Current Trends, Future Perspectives, and Techno‐Feasibility Analysis, 2023, 1527-8999, 10.1002/tcr.202200294 | |
14. | Il-Ho Choi, Hye-Jin Lee, Geun-Bae Rhim, Dong-Hyun Chun, Kyong-Hwan Lee, Kyung-Ran Hwang, Catalytic hydrocracking of heavy wax from pyrolysis of plastic wastes using Pd/Hβ for naphtha-ranged hydrocarbon production, 2022, 161, 01652370, 105424, 10.1016/j.jaap.2021.105424 | |
15. | Lubna Yaqoob, Tayyaba Noor, Naseem Iqbal, Conversion of Plastic Waste to Carbon-Based Compounds and Application in Energy Storage Devices, 2022, 7, 2470-1343, 13403, 10.1021/acsomega.1c07291 | |
16. | Shuo Feng, Shirui Xu, Peng Yuan, Yuye Xing, Boxiong Shen, Zhaoming Li, Chenguang Zhang, Xiaoqi Wang, Zhuozhi Wang, Jiao Ma, Wenwen Kong, The Impact of Alternative Fuels on Ship Engine Emissions and Aftertreatment Systems: A Review, 2022, 12, 2073-4344, 138, 10.3390/catal12020138 | |
17. | Salih Çevikarslan, Carsten Gelhard, Jörg Henseler, Improving the Material and Financial Circularity of the Plastic Packaging Value Chain in The Netherlands: Challenges, Opportunities, and Implications, 2022, 14, 2071-1050, 7404, 10.3390/su14127404 | |
18. | Anastasia Zabaniotou, Ioannis Vaskalis, Economic Assessment of Polypropylene Waste (PP) Pyrolysis in Circular Economy and Industrial Symbiosis, 2023, 16, 1996-1073, 593, 10.3390/en16020593 | |
19. | Wen Xie, Jing Su, Xiangkun Zhang, Tan Li, Cong Wang, Xiangzhou Yuan, Kaige Wang, Investigating kinetic behavior and reaction mechanism on autothermal pyrolysis of polyethylene plastic, 2023, 269, 03605442, 126817, 10.1016/j.energy.2023.126817 | |
20. | Sahil Khan, Raj Malviya, Kanti Kumar Athankar, Optimization and simulation of heat loss in pyrolysis reactor, 2023, 72, 22147853, 2643, 10.1016/j.matpr.2022.08.285 | |
21. | L. V. Furda, D. E. Smalchenko, O. E. Lebedeva, Catalytic Conversion of Polyolefins in the Presence of MCM-41 Type Mesoporous Materials, 2022, 62, 0965-5441, 310, 10.1134/S0965544122030045 | |
22. | Brenda Madrid, Sam Wortman, Douglas G. Hayes, Jennifer M. DeBruyn, Carol Miles, Markus Flury, Thomas L. Marsh, Suzette P. Galinato, Karl Englund, Shinsuke Agehara, Lisa Wasko DeVetter, End-of-Life Management Options for Agricultural Mulch Films in the United States—A Review, 2022, 6, 2571-581X, 10.3389/fsufs.2022.921496 | |
23. | Mohammad Jawaid, Balbir Singh, Lau Kia Kian, Sheikh Ahmad Zaki, A.M. Radzi, Processing techniques on plastic waste materials for construction and building applications, 2023, 40, 24522236, 100761, 10.1016/j.cogsc.2023.100761 | |
24. | Wilson Uzochukwu Eze, Reginald Umunakwe, Michael Ifeanyichukwu Ugbaja, Mohammed Kabiru Yakubu, Narcillina Nkechi Adegboro, Amina Hassan Bayero, Maryann Ifeoma Uzochukwu, Utilization of commodity plastic wastes in flexible pavement: A review, 2023, 3, 2770-4580, 71, 10.3934/ctr.2023005 | |
25. | Aravind J, K E Reby Roy, Jesna Mohammed, Kannan S, Manu M., Kasthoori Nath, Kasthoori M. S, Numerical Analysis to optimise the Effective Thermal resistance of novel waste plastic/SiO2 composite roofing tiles for Residential buildings, 2022, 1556-5068, 10.2139/ssrn.4057924 | |
26. | Anna Trubetskaya, Alican Akgül, Tania Palmeiro-Sánchez, Heiko Lange, Duarte Magalhaes, Sean Moore, Alexandre Paiva, Feyza Kazanç, Categorization of Tars from Recycling of Pha Bioplastic and Synthetic Plastics Using Fast Pyrolysis, 2022, 1556-5068, 10.2139/ssrn.4122863 | |
27. | Wai Chin Li, Ho Man Leung, 2024, 9780443153327, 399, 10.1016/B978-0-443-15332-7.00002-8 | |
28. | Soham V. Kawale, Shrikant S. Mete, Debashis Kundu, Remediation of plastic waste generated during the COVID-19 pandemic: A conceptual process design of pyrolysis using polyethylene, polypropylene, polystyrene based polymers, 2024, 12, 22133437, 114042, 10.1016/j.jece.2024.114042 | |
29. | Sha Wang, Jinbiao Yan, Huarong Zhang, Lipei Qiu, Weijun Liu, Yun Guo, Jun Shen, Cong Shi, Xiang Ge, Review of waste plastics treatment and utilization: Efficient conversion and high value utilization, 2024, 183, 09575820, 378, 10.1016/j.psep.2024.01.024 | |
30. | Ufuk Vural, Abdullah Yinanc, Huseyin Sevindir, Two-stage thermocatalytic conversion of waste XLPE to diesel-like fuel, 2024, 89, 0352-5139, 921, 10.2298/JSC230828035V | |
31. | Christina Podara, Stefania Termine, Maria Modestou, Dionisis Semitekolos, Christos Tsirogiannis, Melpo Karamitrou, Aikaterini-Flora Trompeta, Tatjana Kosanovic Milickovic, Costas Charitidis, Recent Trends of Recycling and Upcycling of Polymers and Composites: A Comprehensive Review, 2024, 9, 2313-4321, 37, 10.3390/recycling9030037 | |
32. | Nara Shin, Su Hyun Kim, Jang Yeon Cho, Jeong Hyeon Hwang, Hyun Jin Kim, Suk Jin Oh, See-Hyoung Park, Kyungmoon Park, Shashi Kant Bhatia, Yung-Hun Yang, Fast Degradation of Polycaprolactone/Poly(butylene adipate-co-terephthalate) Blends by Novel Bacillus Strain NR4 with Broad Degrading Activity, 2024, 32, 1566-2543, 898, 10.1007/s10924-023-02984-x | |
33. | Gloria Musongwa, Egide Manirambona, Stephen M. Talai, Anthony M. Muliwa, Combustion and emission characteristics of distilled waste plastic pyrolysis oil-gasoline blends using single cylinder motorcycle petrol engine, 2024, 17, 1939-7038, 1, 10.1080/19397038.2024.2358908 | |
34. | Leilei Dai, Suman Lata, Kirk Cobb, Rongge Zou, Hanwu Lei, Paul Chen, Roger Ruan, Recent advances in polyolefinic plastic pyrolysis to produce fuels and chemicals, 2024, 180, 01652370, 106551, 10.1016/j.jaap.2024.106551 | |
35. | Manal G. Mohamed, Nahla A. Mansour, Dalia S. Fathy, Azza M. Mazrouaa, 2024, 9780443223372, 185, 10.1016/B978-0-443-22337-2.00014-2 | |
36. | Konstanze Kruta, Jörg Fischer, Peter Denifl, Christian Paulik, Effect of different washing conditions on the removal efficiency of selected compounds in biopolymers, 2023, 3, 2770-4580, 134, 10.3934/ctr.2023009 | |
37. | Man Vir Singh, Pyrolysis Processes and Physiochemical Properties of Liquid Hydrocarbon Fuel from Waste Plastics, 2023, 46, 0930-7516, 1411, 10.1002/ceat.202200519 | |
38. | Gabriela Berkowicz-Płatek, Witold Żukowski, Jan Wrona, Kinga Wencel, Thermal decomposition of polyolefins under different oxygen content. Composition of products and thermal effects, 2024, 295, 03605442, 130987, 10.1016/j.energy.2024.130987 | |
39. | Devanshu Sajwan, Anitya Sharma, Manisha Sharma, Venkata Krishnan, Upcycling of Plastic Waste Using Photo-, Electro-, and Photoelectrocatalytic Approaches: A Way toward Circular Economy, 2024, 14, 2155-5435, 4865, 10.1021/acscatal.4c00290 | |
40. | Adel Zrelli, Samir Ismaili, Qusay Alsalhy, Valorization of waste plastics and waste oases of Gabes-Tunisia to prepare polymeric membrane for oily wastewater treatment, 2023, 8, 2365-6433, 907, 10.1007/s41207-023-00418-7 | |
41. | Alexander Ahrens, Andreas Bonde, Hongwei Sun, Nina Kølln Wittig, Hans Christian D. Hammershøj, Gabriel Martins Ferreira Batista, Andreas Sommerfeldt, Simon Frølich, Henrik Birkedal, Troels Skrydstrup, Catalytic disconnection of C–O bonds in epoxy resins and composites, 2023, 617, 0028-0836, 730, 10.1038/s41586-023-05944-6 | |
42. | Kumari Anshu, Hilkka I. Kenttämaa, Sonal K. Thengane, A comprehensive review on co-pyrolysis of lignocellulosic biomass and polystyrene, 2024, 205, 13640321, 114832, 10.1016/j.rser.2024.114832 | |
43. | Nasrollah Majidian, Mahyar Saleh, Mohammad Samipourgiri, Kinetics study of catalytic pyrolysis of polystyrene polymer using response surface method, 2024, 33, 1026-1265, 1793, 10.1007/s13726-024-01362-1 | |
44. | Abiodun Oluwatosin Adeoye, Jibrin Muhammad Yelwa, Naziru Imam, Rukayat Oluwatobiloba Quadri, Olayide Samuel Lawal, Dosu Malomo, Samson Abiodun Aasa, Augustine Eyikwuojo Onakpa, Ruth Kooaka Dorgbaa, Busuyi Patrick Omoniyi, Nuhu Ahmad, Husaina Anchau Garba, 2024, Chapter 11, 978-981-97-0436-1, 215, 10.1007/978-981-97-0437-8_11 | |
45. | Santa Margarida Santos, Margarida Gonçalves, Paulo Brito, Catarina Nobre, Waste-Derived Chars: A Comprehensive Review, 2024, 2, 2813-0391, 218, 10.3390/waste2030013 | |
46. | Silvia Saikia, Ajay S. Kalamdhad, Assessment of pyrolysis potential of Indian municipal solid waste and legacy waste via physicochemical and thermochemical characterization, 2024, 394, 09608524, 130289, 10.1016/j.biortech.2023.130289 | |
47. | José Alfredo Torres Tovar, Hermelinda Servín-Campuzano, Mauricio González-Avilés, Hugo Sobral, Francisco Javier Sánchez-Ruiz, Degradation of Plastic Materials through Small-Scale Pyrolysis: Characterization of the Obtained Hydrocarbons and Life Cycle Analysis, 2024, 9, 2313-4321, 5, 10.3390/recycling9010005 | |
48. | Biswajit Saha, Sundaramurthy Vedachalam, Ajay K. Dalai, Saumitra Saxena, Bassam Dally, William L. Roberts, Review on production of liquid fuel from plastic wastes through thermal and catalytic degradation, 2024, 114, 17439671, 101661, 10.1016/j.joei.2024.101661 | |
49. | Amrita Ghosh Majumdar, Biswajit Pany, Sankha Subhra Parua, Satyabrata Si, Junpei Yamanaka, Priti S. Mohanty, 2024, Chapter 20, 978-3-031-58440-4, 579, 10.1007/978-3-031-58441-1_20 | |
50. | Fiyinfoluwa Joan Medaiyese, Hamid Reza Nasriani, Leila Khajenoori, Khalid Khan, Ali Badiei, From Waste to Energy: Enhancing Fuel and Hydrogen Production through Pyrolysis and In-Line Reforming of Plastic Wastes, 2024, 16, 2071-1050, 4973, 10.3390/su16124973 | |
51. | Andromachi Chasioti, Anastasia Zabaniotou, An Industrial Perspective for Sustainable Polypropylene Plastic Waste Management via Catalytic Pyrolysis—A Technical Report, 2024, 16, 2071-1050, 5852, 10.3390/su16145852 | |
52. | Tarhemba Tobias Nyam, Olusola Olaitan Ayeleru, Ishmael Matala Ramatsa, Peter Apata Olubambi, 2024, 9783527352142, 227, 10.1002/9783527842209.ch9 | |
53. | Moses Jeremiah Barasa Kabeyi, Oludolapo Akanni Olanrewaju, Johan E. Hustad, Review and Design Overview of Plastic Waste-to-Pyrolysis Oil Conversion with Implications on the Energy Transition, 2023, 2023, 2314-615X, 1, 10.1155/2023/1821129 | |
54. | Lukumon Salami, Regina J. Patinvoh, Mohammad J. Taherzadeh, Waste plastic char as adsorbent for removal of pollutants from landfill leachates–A critical review, 2024, 16, 26667657, 100522, 10.1016/j.envadv.2024.100522 | |
55. | F. C. Adizue, T. H. Fidel-Anekwe, A. C. Osuofia, 2024, A Review on Innovative Methods of Plastic Waste-To-Energy Conversion for Sustainable Development, 10.2118/221624-MS | |
56. | XinYi Wu, Wei Han Tu, Andrei Veksha, Wenqian Chen, Grzegorz Lisak, Polyolefin-derived substrate-grown carbon nanotubes as binder-free electrode for hydrogen evolution in alkaline media, 2024, 349, 00456535, 140769, 10.1016/j.chemosphere.2023.140769 | |
57. | P.G.C. Nayanathara Thathsarani Pilapitiya, Amila Sandaruwan Ratnayake, The world of plastic waste: A review, 2024, 11, 27723976, 100220, 10.1016/j.clema.2024.100220 | |
58. | Biswajeet Acharya, Amulyaratna Behera, Kalim Deshmukh, Srikanta Moharana, 2024, 9783527352142, 173, 10.1002/9783527842209.ch7 | |
59. | S. B. Arun, P. Harsha Vardhan, K. B. Nandan, N. S. Preetam, T. M. Rajath, Fabrication of a System to Convert Waste Plastic into Fuel, 2023, 0022-2755, 161, 10.18311/jmmf/2023/45546 | |
60. | Julia N. Hancock, Julie E. Rorrer, Hydrogen-free catalytic depolymerization of waste polyolefins at mild temperatures, 2023, 338, 09263373, 123071, 10.1016/j.apcatb.2023.123071 | |
61. | Tarhemba Tobias Nyam, Olusola Olaitan Ayeleru, Ishmael Matala Ramatsa,, Peter Apata Olubambi1, 2024, 9783527352142, 31, 10.1002/9783527842209.ch2 | |
62. | Don Dasun Attanayake, Fabian Sewerin, Shreyas Kulkarni, Andrea Dernbecher, Alba Dieguez-Alonso, Berend van Wachem, Review of Modelling of Pyrolysis Processes with CFD-DEM, 2023, 111, 1386-6184, 355, 10.1007/s10494-023-00436-z | |
63. | S. S. Alam, A. H. Khan, Microwave-assisted pyrolysis for waste plastic recycling: a review on critical parameters, benefits, challenges, and scalability perspectives, 2024, 21, 1735-1472, 5311, 10.1007/s13762-023-05352-3 | |
64. | Ali Ghasemkhani, Gholamreza Pircheraghi, Mohammadreza Shojaei, An innovative polymer composite prepared through the recycling of spent lead-acid battery separators, 2023, 38, 22149937, e00753, 10.1016/j.susmat.2023.e00753 | |
65. | Mohammad Abu Nasir Rakib, Jeremy Scidmore, Justin Ginsberg, Cesar Torres, 2023, Thermoplastic Kilnforms: Extending Glass Kilnforming Techniques to Thermoplastic Materials using Ontology-Driven Design, 9781450398930, 263, 10.1145/3563657.3596027 | |
66. | Dong-Hyun Seo, Yi-Rac Choi, Jin-Ho Lim, Ou-Sup Han, Fire and Explosion Hazards and Safety Management Measures of Waste Plastic-to-Pyrolysis Oil Conversion Process, 2023, 19, 1738-3935, 22, 10.7849/ksnre.2023.0011 | |
67. | Ekta Gupta, Virendra Kumar Mishra, Anju Patel, Pankaj Kumar Srivastava, A modified methodology for extraction and quantification of microplastics in soil, 2024, 35, 24520748, 100525, 10.1016/j.impact.2024.100525 | |
68. | Kumari Anshu, Sonal K. Thengane, Kinetic and thermodynamic analysis of co-pyrolysis of rice straw and polystyrene, 2024, 2190-6815, 10.1007/s13399-024-06047-6 | |
69. | Suresh Vellaiyan, Optimization of pyrolysis process parameters for a higher yield of plastic oil with enhanced physicochemical properties derived from medical plastic wastes, 2023, 36, 23525541, 101310, 10.1016/j.scp.2023.101310 | |
70. | Alaka Samal, Nigamananda Das, Mini-review on remediation of plastic pollution through photoreforming: progress, possibilities, and challenges, 2023, 30, 1614-7499, 83138, 10.1007/s11356-023-28253-x | |
71. | Alexander Schade, Marcel Melzer, Sven Zimmermann, Thomas Schwarz, Klaus Stoewe, Harald Kuhn, Plastic Waste Recycling─A Chemical Recycling Perspective, 2024, 12, 2168-0485, 12270, 10.1021/acssuschemeng.4c02551 | |
72. | Jiakai Sun, Jinhu Dong, Lijun Gao, Yu-Quan Zhao, Hyunjin Moon, Susannah L. Scott, Catalytic Upcycling of Polyolefins, 2024, 124, 0009-2665, 9457, 10.1021/acs.chemrev.3c00943 | |
73. | Ajay Tomer, Mazharul M. Islam, Mounib Bahri, Donald R. Inns, Troy D. Manning, John B. Claridge, Nigel D. Browning, C. Richard A. Catlow, Alberto Roldan, Alexandros P. Katsoulidis, Matthew J. Rosseinsky, Enhanced production and control of liquid alkanes in the hydrogenolysis of polypropylene over shaped Ru/CeO2 catalysts, 2023, 666, 0926860X, 119431, 10.1016/j.apcata.2023.119431 | |
74. | Balasubramaniam Prabha, Desikan Ramesh, Srinivasan Sriramajayam, Doraiswamy Uma, Optimization of Pyrolysis Process Parameters for Fuel Oil Production from the Thermal Recycling of Waste Polypropylene Grocery Bags Using the Box–Behnken Design, 2024, 9, 2313-4321, 15, 10.3390/recycling9010015 | |
75. | Amit Kumar, Harveer Singh Pali, Optimizing the conversion of waste plastic into suitable engine fuel through response surface methodology, 2024, 191, 09575820, 1089, 10.1016/j.psep.2024.08.127 | |
76. | Saumitra Saxena, Pyrolysis and Beyond: Sustainable Valorization of Plastic Waste, 2024, 2666352X, 100311, 10.1016/j.jaecs.2024.100311 | |
77. | Ashrumochan Gouda, Devendra Sharma, Sahil Kumar, Venkata Krishnan, 2024, 1490, 9780841296091, 63, 10.1021/bk-2024-1490.ch003 | |
78. | Sakshi Sharma, Aman Deep Acharya, Yugesh Singh Thakur, , Solvothermal synthesized mesoporous BiOCl nano-ellipsoids with oxygen vacancies for photocatalytic degradation of low density polyethylene (LDPE) plastic, 2024, 00255408, 113214, 10.1016/j.materresbull.2024.113214 | |
79. | Soshi Tsubota, Shinya Kokuryo, Koji Miyake, Yoshiaki Uchida, Atsushi Mizusawa, Tadashi Kubo, Norikazu Nishiyama, Understanding the Role of the Surface Acidity of MFI Zeolites during LDPE Cracking: Decomposition Temperature and Product Distribution, 2024, 2155-5435, 18145, 10.1021/acscatal.4c06190 | |
80. | Muhammad Kashif, Muhammad Ashraf Sabri, Michele Aresta, Angela Dibenedetto, Franck Dumeignil, Sustainable synergy: unleashing the potential of biomass in integrated biorefineries, 2025, 2398-4902, 10.1039/D4SE01293C | |
81. | Abdu Mohammed Seid, Solomon Alemneh Adimass, Waleligne Molla Salilew, Krishnan Vignesh, Velmurugan Paramasivam, Birhanu Adisie Fentaw, Hamouda M Mousa, Recent Progress on the Physical, Thermal, and Mechanical Properties of Expanded Polystyrene Waste–Based Composites, 2025, 2025, 1687-9422, 10.1155/ijps/9285040 | |
82. | Kishor Kalauni, Ajitanshu Vedrtnam, Sahendra P Sharma, Abhishek Sharma, Shashikant Chaturvedi, A comprehensive review of recycling and reusing methods for plastic waste focusing Indian scenario, 2025, 0734-242X, 10.1177/0734242X241308499 | |
83. | Nega Chanie Belay, Birhanu Adisie Fentaw, Ramesh Babu Nallamothu, Melese Shiferaw Kebede, Performance Evaluation of Liquid Fuel Derived from Waste Plastics for Diesel Engine Applications and Emissions Characteristics, 2025, 03605442, 134911, 10.1016/j.energy.2025.134911 | |
84. | Milad Aminzadeh, Tanmay Kokate, Nima Shokri, Microplastics in Sandy Soils: Alterations in Thermal Conductivity, Surface Albedo, and Temperature, 2025, 02697491, 125956, 10.1016/j.envpol.2025.125956 | |
85. | Milon Selvam Dennison, Sathish Kumar Paramasivam, Titus Wanazusi, Kirubanidhi Jebabalan Sundarrajan, Bubu Pius Erheyovwe, Abisha Meji Marshal Williams, Addressing Plastic Waste Challenges in Africa: The Potential of Pyrolysis for Waste-to-Energy Conversion, 2025, 7, 2571-8797, 20, 10.3390/cleantechnol7010020 | |
86. | Rabab M. Nasser, Reham I. El Shazly, Mohammed E. Haseeb, 2025, 1501, 9780841296008, 137, 10.1021/bk-2025-1501.ch007 |
Plastic fuel | Density 40℃ (g/cm3) | Viscosity at 40℃ (cSt) | Flash point (℃) | Calorific value (MJ/kg) | Appearance | References |
HDPE | 0.800–0.920 | 2.420–2.52 | 40–48 | 45.4 | Light oil, Brown | Kunwar, et al. [36] |
LDPE | 0.768–0.8020 | 1.650–1.801 | 50 | 39.1 | Light oil, Brown | Shah, et al. [37] |
PP | 0.767–0.80 | 2.72 | 31–36 | 40 | Light oil, Yellow | Yohandri, et al. [38] |
PET | 0.087–0.90 | NA | NA | 28.2 | Light oil, Brown | Honus, et al. [39] |
PS | 0.85–0.86 | 1.4 at 50℃ | 28 | 43.0 | Light oil, deep brown | Miandad, et al. [40] |
Note: NA: not available in literature. |
Plastic | Temperature (℃) | Liquid yield (%) | Elemental composition (%) | Carbon number distribution | References | |||
C | H | N | O | |||||
HDPE | 460 | 86 | 85.3 | 14.2 | 0.5 | 0.00 | C3–C28 | Kunwar et al. [36], Olufemi, et al. [41] |
LDPE | 430 | 75.6 | 85.3 | 14.2 | 0.5 | 0.00 | C5–C28 | Olufemi, et al. [41], |
PP | 350 250 | 70 45 | 85.61 | 14.38 | 0.00 | C3–C25 | Yohandri et al. [38], Olufemi et al. [41] | |
PS | 92.32 | 7.73 | 0.00 | 0.00 | NA | Honus, et al. [39] | ||
PET | 450 600 | 59.50 67.70 | 62.10 | 4.21 | - | 33.69 | NA | Honus, et al. [39] |
Note: NA: not available. |
Plastic | Microwave power range (KW) | Time (min) | Absorbent-plastic ratio | Solid (wt%) | Liquid (wt%) | Gas (wt%) |
HDPE | 3 | 75 | 1:2 | 0.40 | 83.92 | 15.68 |
PP | 3 | 68 | 1:2 | 15.89 | 70.82 | 13.29 |
PVC | 3 | 21 | 1:2 | 14.69 | 3.44 | 81.87 |
PET | 1.8–3 | 40 | 2.51 | 38.20 | 35.32 | 26.48 |
PS | 3–6 | 59 | 1:2 | 6.83 | 89.25 | 8.92 |
Note: Source: Undri et al. [46]. |
Gasoline (wt%) (C6–C12) | Diesel (wt%) (C13–C18) | Fuel oil (wt%) (C19–C23) | Residual fuel (wt%) (C24) | |
Thermal pyrolysis | 59 | 36 | 5 | - |
Catalysed pyrolysis | 93 | 7 | - | - |
Note: Source: Eze et al. [27]. |
Wt% | Thermal pyrolysis | Catalysed pyrolysis |
C | 94.24 | 97.11 |
H | 11.73 | 10.12 |
N | 0.61 | 0.28 |
S | 4.8 | 4.36 |
Note: Source: Eze et al. [27]. |
Plastic fuel | Density 40℃ (g/cm3) | Viscosity at 40℃ (cSt) | Flash point (℃) | Calorific value (MJ/kg) | Appearance | References |
HDPE | 0.800–0.920 | 2.420–2.52 | 40–48 | 45.4 | Light oil, Brown | Kunwar, et al. [36] |
LDPE | 0.768–0.8020 | 1.650–1.801 | 50 | 39.1 | Light oil, Brown | Shah, et al. [37] |
PP | 0.767–0.80 | 2.72 | 31–36 | 40 | Light oil, Yellow | Yohandri, et al. [38] |
PET | 0.087–0.90 | NA | NA | 28.2 | Light oil, Brown | Honus, et al. [39] |
PS | 0.85–0.86 | 1.4 at 50℃ | 28 | 43.0 | Light oil, deep brown | Miandad, et al. [40] |
Note: NA: not available in literature. |
Plastic | Temperature (℃) | Liquid yield (%) | Elemental composition (%) | Carbon number distribution | References | |||
C | H | N | O | |||||
HDPE | 460 | 86 | 85.3 | 14.2 | 0.5 | 0.00 | C3–C28 | Kunwar et al. [36], Olufemi, et al. [41] |
LDPE | 430 | 75.6 | 85.3 | 14.2 | 0.5 | 0.00 | C5–C28 | Olufemi, et al. [41], |
PP | 350 250 | 70 45 | 85.61 | 14.38 | 0.00 | C3–C25 | Yohandri et al. [38], Olufemi et al. [41] | |
PS | 92.32 | 7.73 | 0.00 | 0.00 | NA | Honus, et al. [39] | ||
PET | 450 600 | 59.50 67.70 | 62.10 | 4.21 | - | 33.69 | NA | Honus, et al. [39] |
Note: NA: not available. |
Plastic | Microwave power range (KW) | Time (min) | Absorbent-plastic ratio | Solid (wt%) | Liquid (wt%) | Gas (wt%) |
HDPE | 3 | 75 | 1:2 | 0.40 | 83.92 | 15.68 |
PP | 3 | 68 | 1:2 | 15.89 | 70.82 | 13.29 |
PVC | 3 | 21 | 1:2 | 14.69 | 3.44 | 81.87 |
PET | 1.8–3 | 40 | 2.51 | 38.20 | 35.32 | 26.48 |
PS | 3–6 | 59 | 1:2 | 6.83 | 89.25 | 8.92 |
Note: Source: Undri et al. [46]. |
Gasoline (wt%) (C6–C12) | Diesel (wt%) (C13–C18) | Fuel oil (wt%) (C19–C23) | Residual fuel (wt%) (C24) | |
Thermal pyrolysis | 59 | 36 | 5 | - |
Catalysed pyrolysis | 93 | 7 | - | - |
Note: Source: Eze et al. [27]. |
Wt% | Thermal pyrolysis | Catalysed pyrolysis |
C | 94.24 | 97.11 |
H | 11.73 | 10.12 |
N | 0.61 | 0.28 |
S | 4.8 | 4.36 |
Note: Source: Eze et al. [27]. |