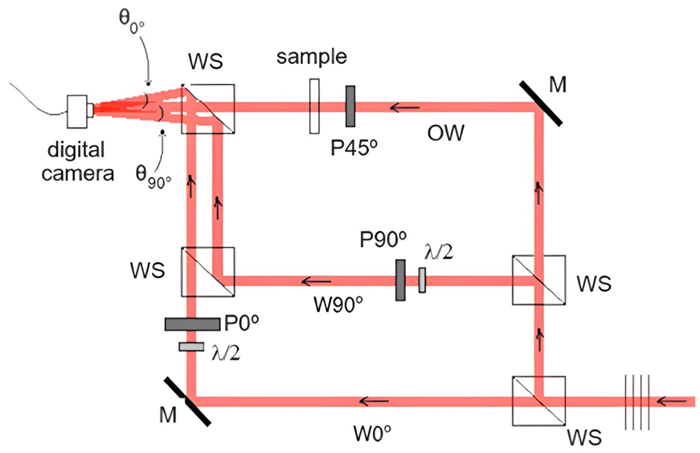
The remora optimization algorithm (ROA) is a newly proposed metaheuristic algorithm for solving global optimization problems. In ROA, each search agent searches new space according to the position of host, which makes the algorithm suffer from the drawbacks of slow convergence rate, poor solution accuracy, and local optima for some optimization problems. To tackle these problems, this study proposes an improved ROA (IROA) by introducing a new mechanism named autonomous foraging mechanism (AFM), which is inspired from the fact that remora can also find food on its own. In AFM, each remora has a small chance to search food randomly or according to the current food position. Thus the AFM can effectively expand the search space and improve the accuracy of the solution. To substantiate the efficacy of the proposed IROA, twenty-three classical benchmark functions and ten latest CEC 2021 test functions with various types and dimensions were employed to test the performance of IROA. Compared with seven metaheuristic and six modified algorithms, the results of test functions show that the IROA has superior performance in solving these optimization problems. Moreover, the results of five representative engineering design optimization problems also reveal that the IROA has the capability to obtain the optimal results for real-world optimization problems. To sum up, these test results confirm the effectiveness of the proposed mechanism.
Citation: Rong Zheng, Heming Jia, Laith Abualigah, Shuang Wang, Di Wu. An improved remora optimization algorithm with autonomous foraging mechanism for global optimization problems[J]. Mathematical Biosciences and Engineering, 2022, 19(4): 3994-4037. doi: 10.3934/mbe.2022184
[1] | Katsumasa Satoh, Yasuhide Tsuji . A study on photonic crystal slab waveguide with absolute photonic band gap. AIMS Materials Science, 2018, 5(1): 116-126. doi: 10.3934/matersci.2018.1.116 |
[2] | M.M. Reza Mousavi, Masoud D. Champiri, Mohammad S. Joshaghani, Shahin Sajjadi . A kinematic measurement for ductile and brittle failure of materials using digital image correlation. AIMS Materials Science, 2016, 3(4): 1759-1772. doi: 10.3934/matersci.2016.4.1759 |
[3] | Grujicic Mica, Galgalikar Rohan, Ramaswami S., Snipes Jennifer S. . Derivation, parameterization and validation of a creep deformation/rupture material constitutive model for SiC/SiC ceramic-matrix composites (CMCs). AIMS Materials Science, 2016, 3(2): 591-619. doi: 10.3934/matersci.2016.2.591 |
[4] | M.A.R. Loja, André Carvalho, Ines C.J. Barbosa . A study on the static behavior of functionally graded I-shaped beams. AIMS Materials Science, 2024, 11(1): 28-57. doi: 10.3934/matersci.2024002 |
[5] | Ahmed M. Abood, Haider Khazal, Abdulkareem F. Hassan . On the determination of first-mode stress intensity factors and T-stress in a continuous functionally graded beam using digital image correlation method. AIMS Materials Science, 2022, 9(1): 56-70. doi: 10.3934/matersci.2022004 |
[6] | G. Sri Harsha, P. Poluraju, Veerendrakumar C. Khed . Computation of shear strength equation for shear deformation of reinforced concrete deep beams using finite element method. AIMS Materials Science, 2021, 8(1): 42-61. doi: 10.3934/matersci.2021004 |
[7] | Mohammed Y. Abdellah, Hamzah Alharthi, Mohamed K. Hassan, Ahmed F. Mohamed . Effect of specimen size on natural vibration of open hole copper/glass-reinforced epoxy laminate composites. AIMS Materials Science, 2020, 7(4): 499-517. doi: 10.3934/matersci.2020.4.499 |
[8] | Ivan Jandrlić, Stoja Rešković, Dušan Ćurčija, Ladislav Lazić, Tin Brlić . Modeling of stress distribution on the basis of the measured values of strain and temperature changes. AIMS Materials Science, 2019, 6(4): 601-609. doi: 10.3934/matersci.2019.4.601 |
[9] | Sujith Bobba, Z. Leman, E.S. Zainudin, S.M. Sapuan . Hoop tensile strength behaviour between different thicknesses E-glass and S-glass FRP rings. AIMS Materials Science, 2019, 6(3): 315-327. doi: 10.3934/matersci.2019.3.315 |
[10] | Bandar Abdullah Aloyaydi, Subbarayan Sivasankaran, Hany Rizk Ammar . Influence of infill density on microstructure and flexural behavior of 3D printed PLA thermoplastic parts processed by fusion deposition modeling. AIMS Materials Science, 2019, 6(6): 1033-1048. doi: 10.3934/matersci.2019.6.1033 |
The remora optimization algorithm (ROA) is a newly proposed metaheuristic algorithm for solving global optimization problems. In ROA, each search agent searches new space according to the position of host, which makes the algorithm suffer from the drawbacks of slow convergence rate, poor solution accuracy, and local optima for some optimization problems. To tackle these problems, this study proposes an improved ROA (IROA) by introducing a new mechanism named autonomous foraging mechanism (AFM), which is inspired from the fact that remora can also find food on its own. In AFM, each remora has a small chance to search food randomly or according to the current food position. Thus the AFM can effectively expand the search space and improve the accuracy of the solution. To substantiate the efficacy of the proposed IROA, twenty-three classical benchmark functions and ten latest CEC 2021 test functions with various types and dimensions were employed to test the performance of IROA. Compared with seven metaheuristic and six modified algorithms, the results of test functions show that the IROA has superior performance in solving these optimization problems. Moreover, the results of five representative engineering design optimization problems also reveal that the IROA has the capability to obtain the optimal results for real-world optimization problems. To sum up, these test results confirm the effectiveness of the proposed mechanism.
Transparent photoelastic materials represent an exciting alternative to the experimental study of stress and strain distributions induced in solids by carges. When subjected to carges, these materials present the double refraction phenomenon, or birefringence, changing the polarization state of the transmitted light through the solids, which can be used to analyze the stress distribution [1]. The effect of double refraction, first described by Bartholinus [2,3,4] and related with the stress state by Brewster in the early 19th century [5], advanced throughout the 20th century with a non-destructive set of techniques and methods which associates the study of material stresses with optics, the photoelasticity [6,7,8]. Since the pioneering work of Coker and Filon [9,10,11], photoelasticity became a fundamental base for determining stress and strain distributions in photoelastic materials. Thus, great interest was generated in several fields, such as Engineering and Odontology [12,13,14], which validated and contributed to developing the theoretical method of finite elements [15,16].
Despite advances, most studies are qualitative or indirectly quantitative [13,14] due to the difficulties in obtaining direct optical information. Improvements in qualitative data and quantitative analysis methods are needed so that non-destructive, fast, and reliable optical methods become a reference for determining stress distribution in materials. Although holographic techniques have advanced significantly in recent years, the various works have invested very little in the stresses distribution analysis in photoelasticity using holography. The dynamics of holography allow the results to be more precise, as they are based on optical properties such as intensity, phase, refractive index, etc., which are provided directly or almost directly, thus offering a great perspective in the more quantitative treatment of problems involving elasticity mechanics [17].
We present an alternative approach to determine the stress distribution profile through a non-destructive procedure based on digital holography (DH) [18,19], allowing us to obtain quantitative intensity and phase information from light transmitted through a photoelastic material. The DH produces remarkably accurate results when combined with appropriate statistical processing of optical data, facilitating the quantitative treatment of the specific problem as outlined in the proposed methods [20]. An off-axis holographic setup was used to obtain two cross-holograms with two orthogonally polarized reference waves and a birefringent system with photoelastic samples under static loads [21,22,23,24,25]. After digitally reconstructed with DH, the received data generates the phase differences used to calculate the distributions of elastic stresses. The validation of the method was carried out with the methods finite elements and RGB (red, green, and blue) photoelasticity [14,16,26,27].
Four standard rectangular blocks, composed of mixtures of epoxy resin solutions, were prepared according to the traditional procedures [28] of the photoelastic technique, constituting the samples used in this work. The preparation of the samples involved two stages: making the silicone molds, from curing in a liquid solution and catalyst, and the photoelastic samples, from curing, in silicone molds, a liquid solution of epoxy resin and hardener. Details are presented in the work [17]. For the determinations of the mechanical and holographic parameters, two samples with different thicknesses were made, one more flexible and one less flexible. Two other samples with different thicknesses, one more and one less flexible, were also made to determine the stress distributions. Details of the procedures are presented in [17]. The more or less flexible samples were intended to help verify the order of magnitude of the stress-optical coefficient (C) and to provide a greater range of comparison with the photoelastic methodology.
The utilized holographic technique is shown in Figure 1.
A laser light source (1) was used to generate three independent waves: one object wave (OW), with the direction of polarization at 45º concerning two orthogonal reference waves, one with the direction of polarization at 0º (W0º), and another with the direction of polarization at 90º (W90º). Two distinct holograms were produced from the resulting interference patterns among OW, W0º, and W90º, propagating with different angles to the digital camera, as shown in Figure 1: θ(0º) between the OW and W0º, and θ (90º) between OW and W90º, as limited by the N-quest Theorem [29,30,31]. Two sets of holograms were recorded from each sample for compression and decompression in the birefringent system. The compression occurs by the progressive addition of load on the samples, and the decompression occurs by progressive removal of these loads.
The photoelastic images were obtained by blocking both reference waves, removing the wave splitter (WS), near the digital camera, and exchanging the polarizer, P45º, of the object wave for two polarizers with orthogonal polarizations, one before and another after the photoelastic sample. Figure 2 presents an experimental configuration scheme used in photoelasticity.
The optical information obtained through photoelasticity is related to the difference between the stresses considered in the components longitudinal (σ∥) and transverse (σ⊥) to the applied load, defined by Eq 1, as given by the stress-optic law [6,17,28]:
n∥−n⊥=C(σ∥−σ⊥) | (1) |
where C is the stress-optical coefficient, and (n∥−n⊥) is the difference between the refraction indexes in the components longitudinal (n∥) and transverse (n⊥) to the effort. For a material with thickness e, the refractive index difference is also associated with the phase difference Δϕ, so Eq 1 can be rewritten as Eq 2:
(σ∥−σ⊥)=fσNe | (2) |
where N=Δϕ2π is defined as the relative retardation, fσ=λC is the fringe value that indicates the degree of rigidity of the material, and λ is the wavelength of the light source. Using the matrix of stress-strain (σ−ε) of the material in the stress state plane [26], the difference between the stresses in the orthogonal components, defined by Eq 3, is [17]:
[σ⊥σ∥]=E1−ν2[1νν1][ε⊥ε∥]⇒(σ∥−σ⊥)=E1+ν(ε∥−ε⊥) | (3) |
E is the mechanical elasticity modulus, and ν is the Poisson's coefficient. Therefore, comparing Eqs 2 and 3, with N=(ε∥−ε⊥), the material fringes value can be determined by their intrinsic properties through Eq 4 [17]:
fσ=eE1+ν=λC(λ) | (4) |
The holographic method was empirically inferred and correlated with the stress-optic law. The stress difference (σ∥−σ⊥) occurs in the plane normal to the passage of light [26]. Due to angular displacements, the shear stresses were not considered to limit the boundary conditions and obtain the desired equation. In analogy with photoelasticity, the stress-strain matrix for the holographic parameters is given by Eq 5 [17]:
[σ⊥σ∥]=Ea(1−ν2)[1νν1][aεH⊥aεH∥]⇒(σ∥−σ⊥)holographic=E(1+ν)ℵ | (5) |
considering, by Eq 6, that
E=aE | (6) |
E is defined as the holographic elasticity modulus, and a is a dimensionless constant that relates the holography elasticity with the mechanical elasticity. εH=1aε is defined as the relative holographic deformation and ℵ=(ϕ∥−ϕ⊥)holographic2π=(εH∥−εH⊥) as the relative holographic retardation. Thus, the holographic dispersion can be written as the Eq 7 [17]:
H(λ)≡λfσ=a(1+ν)eEλ | (7) |
where, by Eq 8,
![]() |
(8) |
and fσ are the fringe values obtained in holography and photoelasticity, respectively. The photoelastic fringe value is related to the wavelength of light (λ) and the photoelastic stress-optical coefficient (C). Then, analogously to what occurs with photoelasticity, there comes the holographic dispersion term, H(λ), an intrinsic property of the material whose value depends on the light wavelength, resultant from the relation between the component differences in refractive indexes, (n∥−n⊥)holographic and the plane stresses (σ∥−σ⊥)holographic. For a given wavelength, the stress-holographic law is given by Eq 9 [17]:
(n∥−n⊥)holographic=H(σ∥−σ⊥)holographic | (9) |
We have experimentally confirmed these equations in [21,22].
The off-axis configuration separates the diffraction orders during the digital reconstruction performed with FTM's fresnel transform method [17,32,33]. The image field (ψmn) and phase (ϕmn) were calculated using Eqs 10 and 11, and the corresponding maps were reconstructed.
ψmn=eikz∙eikzλ2(n2N2Δξ2+m2M2Δη2)izλ∙F[Δkξ,Δkη] | (10) |
ϕmn=arctg{Im[ψmn]Re[ψmn]} | (11) |
where F[Δkξ,Δkη]=F[IH(ξ,η)∙ψR(ξ,η)∙eπizλ[(n∙Δξ)2+(m∙Δη)2]] is the Fourier Transform of the discretized field, Δkξ=−kλNΔξ, Δkη=−kλMΔη, Δξ=zλNΔh, Δη=zλMΔv, Δh and Δv are the horizontal and vertical pixel dimensions, respectively. All the phase maps were demodulated with the Volkov Method [34].
The calibration of the setup followed the work of Colomb et al. [24] and was carried out using a quarter-wave plate as a sample. Two-phase maps reconstructed by FTM, one for each polarization, were subtracted to obtain the maps of phase differences in the function of the angle of orientation of the quarter-wave plate. The general expression for the phase difference (Δφ) as a function of the orientation of the quarter-wave, by Eq 12:
Δϕ=arctan[sin(2δ)cos2(2δ)] | (12) |
The process to obtain the demodulated phase maps for compression and decompression. The area selected (the rectangle on the hologram) of the hologram was processed with the FTM to obtain the frequency spectrum [17]. The chosen area (the rectangle on the frequency spectrum) of the frequency spectrum was obtained from the modulated phase map, and the Volkov method [34] was obtained from the demodulated phase map. The mean phase was determined from the phases of the pixels in the area selected from the demodulated phase map. To reduce the noise, in each phase map, a region of the phase map with no object was chosen, and the mean phase value of this region was subtracted from the phase map [17].
From the vertical phase maps of each stress applied, the load, σi, was calculated in the vertical holographic deformations, εHv−i, in both processes: compression and decompression. In the same way, with the phase values of the horizontal phase maps, the horizontal holographic deformations, εHh−i, were calculated. The mean value ⟨E⟩ was calculated from various values E by fitting the linear function, by Eq 13:
σi=⟨E⟩εHv−i | (13) |
The mean value of the Poisson's coefficient, ⟨ν⟩, was calculated from various values ν by fitting the linear function, by Eq 14:
εHh−i=⟨ν⟩εHv−i | (14) |
In both cases, the Least Squares Method [34] was utilized.
For each horizontal line j, the phase differences, (ϕv−ϕh)j, were obtained and, from the result, the relative retardation, ℵj=(ϕv−ϕh)j/2π, was calculated between the dark fringes. These results, associated with the holographic parameters ⟨E⟩ and⟨ν⟩, allowed us to find the stress differences (σv−σh)j−holographic using Eq 5. The graphic (σv−σh)j−holographic as a function of the number of pixels produced the distributions of stress differences in the selected region.
A dimensionless constant parameter from Eq 6 gives the relation between holographic and mechanical elasticity. According to Eq 4, using the photoelastic images, mechanical parameters, ⟨E⟩ and⟨ν⟩, and the thicknesses, e, it is possible to calculate the photoelastic fringes, fσ, and the photoelastic dispersions, C(λ). Using Eq 8, the holographic parameters, E and ν, the thickness e, and the constant a, the holographic fringes, , can be calculated using the phase maps. Using Eq 7 and the wavelength, λ, the holographic dispersion, H(λ), can be calculated.
The mechanical parameters were measured with samples sized 4.15, 2.25, and 1.03 cm, and the stress distribution was tested in samples sized 4.15, 2.25, and 4.90 cm, both in holography and photoelasticity.
Each technique was applied to only one block from each pair of standard blocks, which were prepared with identical flexibilities and labeled as −F low flexibility and +F high flexibility. Stresses were applied to the top surface of the sample blocks via a loading device, as illustrated in Figure 1.
The modified Mach-Zehnder interferometer apparatus was built with a He-Ne laser (632.8 nm CW, 20 mW, model 1135PUniphase). The photoelastic images and hologram registers were captured with a Thorlabs digital camera, model DCC1240C-HQ color, CMOS sensor, 1280 × 1024 pixels, size pixel 5.3 μm (square).
The calibration process of the holographic system generated an experimental distribution that, when compared to a theoretical curve, Figure 3, showed the reliability of the system [24].
The continuous line represents the theoretical curve, Eq 12, and the circles of the experimental distribution. The distribution of the point around the curve indicates that the adjustment of the polarization of waves is correct.
Two sets of holograms were recorded for each sample for compression and decompression. The stresses, applied to the upper central phase of the sample, ranged from 0.3 to 1.5 MPa. In holography, the mean phases were obtained from the statistics of ten selected areas in each demodulated phase map. The final mean was calculated using the values of compression and decompression.
The photoelasticity RGB method, in transmission mode, was associated with the finite elements method to determine the distributions of the stress differences in the same selected regions as those used with the holographic method. These results were used to evaluate the proposed method by comparing holography and photoelasticity by stress-optic and stress-holographic law, given by Eqs 1 and 9, respectively.
All the fitted functions used the least square method [27]. A third-degree polynomial function was fitted to the points, but all the results showed that they were linear functions.
Figure 4 presents the graphics of the experimental values of the σ versus εv for the +F sample under compression and decompression. This graphic is used to determine the mechanical and holographic modulus of elasticity.
Figure 5 presents the graphics of the experimental values of σ versus εHv for the +F samples under compression and decompression, and they are used to obtain the Holographic and Mechanical modulus of elasticity.
Similar graphs were made for the −F samples. Table 1 summarizes the holographic and mechanical modules of elasticity. The values are similar for the samples with different flexibilities in analysis. However, the rate E/E differed for each method (holographic and mechanical). Considering the uncertainties, the values of ⟨E/E⟩ are practically equal for all samples in both flexibilities.
−F sample (modulus of elasticity) | +F sample (modulus of elasticity) | |
Holography (MPa) | 1.589 ± 0.032 | 1.320 ± 0.024 |
Mechanical elasticity (10 MPa) | 3.35 ± 0.16 | 2.86 ± 0.11 |
⟨a⟩=⟨E/E⟩(10−2) | 4.75 ± 0.26 | 4.62 ± 0.20 |
It was verified, in all graphics, using polynomials up to the third degree, that the best-fit function was a first-degree polynomial, related function, agreeing with Robert Hooke's theory of elasticity for the elastic regime.
Figure 6 presents the values of the εh(transverse) versus εv (longitudinal), used to calculate the mechanical Poisson's coefficient under the compression and decompression processes, using samples +F.
Figure 7 presents the values of the εHh(transverse)versus εHv(longitudinal) used to determine the holographic Poisson's coefficient under the compression and decompression processes, using samples +F to determine the stress distribution.
Similar graphs were made for the −F samples. Table 2 summarizes the Poisson's coefficients: holographic and mechanical. Considering the uncertainties, the Poisson's coefficients ν are practically equal for the sample with the same flexibility.
−F sample [Poisson's coefficient (10−1)] | +F sample [Poisson's coefficient (10−1)] | |
Holography | 3.723 ± 0.022 | 3.735 ± 0.025 |
Mechanical elasticity | 3.822 ± 0.095 | 3.90 ± 0.11 |
With these parameters, it was possible to determine the mean stress-optical coefficients in photoelasticity and holography, whose values are presented in Table 3.
−F sample [stress-optical coefficient (10−12 m2/N)] |
+F sample [stress-optical coefficient (10−12 m2/N)] |
|
Holography | 3.921 ± 0.08 | 4.442 ± 0.09 |
Mechanical elasticity | 3.95 ± 0.21 | 4.50 ± 0.22 |
The difference between the values of the samples with the same flexibility is due to the dependence of the stress-optical coefficient with sample thickness, e. However, for the same flexibility, the values agree both in holography and in photoelasticity. An important observation is that in holography, the precision of the results is better since the values are of the order of 10−6 N/m2.
The graphics in Figure 8 show the distribution of stress difference over the vertical lines between two dark fringes obtained using the holographic method (), photoelasticity RGB (+), and analytical method (
). The load, in mass, applied was 600 g for all samples.
The behavior of curves in graphics exhibits similarities, indicating that the theoretical model of the proposed method is correct. The +F samples are less rigid and suffer more significant vertical deformation, reducing the modulus of elasticity under the same load. This behavior is observed graphically due to the smaller and more scattered peaks about the −F sample distribution.
In photoelasticity, the intensity of the images of the fringes pattern depends on the characteristics of the experimental configuration: transmittance of the materials, anisotropic behavior level, spectral radiation distribution of the light source (white light), the conversion factor of the light-signal control and electric-signal control, and the temporary birefringence effect. In digital holography, these effects are less relevant due to the subtractions performed in the numerical reconstruction process, which eliminate much of this noise, and also due to the optical retardations obtained directly from the phase differences maps.
We present an alternative method to obtain the stress differences in photoelastic materials, as verified by the experiments. The similar results for the modulus of elasticity obtained through the different methods (photoelasticity, mechanical, and holographical) allowed the assumption of an analogy between Hooke's law and holography. The photoelastic and holographic dispersions are equal, allowing the establishment of the stress-holographic law in analogy with the stress-optic law. The experimental stress distributions in holography presented the same behavior as the analytic and photoelastic distributions. The results of stress distributions in holography were more accurate than in photoelasticity when compared to the theoretical results. Thus, the proposed method presents efficiency and independence in procedures since it uses only the extracted parameters obtained directly from the phase maps.
The authors declare they have not used Artificial Intelligence (AI) tools in the creation of this article.
The authors are grateful for the financial support from Fundação de Amparo à Pesquisa do Estado de São Paulo (2012/18162-4, 2019/23700-4, 2022/15276-0); the physical support from Faculdade de Tecnologia de Pompeia (Fatec Pompeia), Faculdade de Tecnologia de Itaquera (Fatec Itaquera), Instituto de Física da Universidade de São Paulo (IFUSP) and Instituto de Pesquisas Energéticas e Nucleares de São Paulo (IPEN-SP).
The lead author (Sidney Leal da Silva) contributed theory, data, and analysis from his doctoral work [17]. The other co-authors helped with the preparation and first revisions of the article.
The authors declare no conflict of interest.
[1] |
K. Hussain, M. N. Mohd Salleh, S. Cheng, Y. Shi, Metaheuristic research: a comprehensive survey, Artif. Intell. Rev., 52 (2019), 2191-2233. https://doi.org/10.1007/s10462-017-9605-z doi: 10.1007/s10462-017-9605-z
![]() |
[2] |
W. Qiao, H. Moayedi, L. K. Foong, Nature-inspired hybrid techniques of IWO, DA, ES, GA, and ICA, validated through a k-fold validation process predicting monthly natural gas consumption, Energy Build., 217 (2020), 110023. https://doi.org/10.1016/j.enbuild.2020.110023 doi: 10.1016/j.enbuild.2020.110023
![]() |
[3] |
M. Wang, H. Chen, Chaotic multi-swarm whale optimizer boosted support vector machine for medical diagnosis, Appl. Soft Comput., 88 (2020), 105946. https://doi.org/10.1016/j.asoc.2019.105946 doi: 10.1016/j.asoc.2019.105946
![]() |
[4] |
S. Wang, J. Xiang, Y. Zhong, Y. Zhou, Convolutional neural network-based hidden Markov models for rolling element bearing fault identification, Knowl.-Based Syst., 144 (2018), 65-76. https://doi.org/10.1016/j.knosys.2017.12.027 doi: 10.1016/j.knosys.2017.12.027
![]() |
[5] |
H. Chen, Y. Xu, M. Wang, X. Zhao, A balanced whale optimization algorithm for constrained engineering design problems, Appl. Math. Model., 71 (2019), 45-59. https://doi.org/10.1016/j.apm.2019.02.004 doi: 10.1016/j.apm.2019.02.004
![]() |
[6] | J. Kennedy, R. Eberhart, Particle swarm optimization, in Proceedings of ICNN'95 - International Conference on Neural Networks, 4 (1995), 1942-1948. https://doi.org/10.1109/ICNN.1995.488968 |
[7] | S. Mirjalili, A. Lewis, The whale optimization algorithm, Adv. Eng. Software, 95 (2016), 51-67. https://doi.org/10.1016/j.advengsoft.2016.01.008 |
[8] | S. Mirjalili, S. M. Mirjalili, A. Lewis, Grey wolf optimizer, Adv. Eng. Software, 69 (2014), 46-61. https://doi.org/10.1016/j.advengsoft.2013.12.007 |
[9] | G. Wang, S. Deb, Z. Cui, Monarch butterfly optimization, Neural Comput. Appl., 31 (2019), 1995-2014. https://doi.org/10.1007/s00521-015-1923-y |
[10] | L. Abualigah, A. Diabat, S. Mirjalili, M. A. Elaziz, A. H. Gandomi, The arithmetic optimization algorithm, Comput. Methods Appl. Mech. Eng., 376 (2021), 113609. https://doi.org/10.1016/j.cma.2020.113609 |
[11] |
S. Li, H. Chen, M. Wang, A. A. Heidari, S. Mirjalili, Slime mould algorithm: a new method for stochastic optimization, Future Gener. Comput. Syst., 111 (2020), 300-323. https://doi.org/10.1016/j.future.2020.03.055 doi: 10.1016/j.future.2020.03.055
![]() |
[12] | S. Mirjalili, The ant lion optimizer, Adv. Eng. Software, 83 (2015), 80-98. https://doi.org/10.1016/j.advengsoft.2015.01.010 |
[13] |
S. Mirjalili, A. H. Gandomi, S. Z. Mirjalili, S. Saremi, H. Faris, S. M. Mirjalili, Salp swarm algorithm: a bio-inspired optimizer for engineering design problems, Adv. Eng. Software, 114 (2017), 163-191. https://doi.org/10.1016/j.advengsoft.2017.07.002 doi: 10.1016/j.advengsoft.2017.07.002
![]() |
[14] |
S. Saremi, S. Mirjalili, A. Lewis, Grasshopper optimization algorithm: theory and application, Adv. Eng. Software, 105 (2017), 30-47. https://doi.org/10.1016/j.advengsoft.2017.01.004 doi: 10.1016/j.advengsoft.2017.01.004
![]() |
[15] |
A. A. Heidari, S. Mirjalili, H. Faris, I. Aljarah, M. Mafarja, H. Chen, Harris hawks optimization: algorithm and applications, Future Gener. Comput. Syst., 97 (2019), 849-872. https://doi.org/10.1016/j.future.2019.02.028 doi: 10.1016/j.future.2019.02.028
![]() |
[16] |
A. Faramarzi, M. Heidarinejad, S. Mirjalili, A. H. Gandomi, Marine predators algorithm: a nature-inspired metaheuristic, Expert Syst. Appl., 152 (2020), 113377. https://doi.org/10.1016/j.eswa.2020.113377 doi: 10.1016/j.eswa.2020.113377
![]() |
[17] |
L. Abualigah, D. Yousri, M. A. Elaziz, A. A. Ewees, M. A. A. Al-qaness, A. H. Gandomi, Aquila optimizer: a novel meta-heuristic optimization algorithm, Comput. Ind. Eng., 157 (2021), 107250. https://doi.org/10.1016/j.cie.2021.107250 doi: 10.1016/j.cie.2021.107250
![]() |
[18] |
B. Abdollahzadeh, F. S. Gharehchopogh, S. Mirjalili, Artificial gorilla troops optimizer: a new nature-inspired metaheuristic algorithm for global optimization problems, Int. J. Intell. Syst., 36 (2021), 5887-5958. https://doi.org/10.1002/int.22535 doi: 10.1002/int.22535
![]() |
[19] |
B. Abdollahzadeh, F. S. Gharehchopogh, S. Mirjalili, African vultures optimization algorithm: a new nature-inspired metaheuristic algorithm for global optimization problems, Comput. Ind. Eng., 158 (2021), 107408. https://doi.org/10.1016/j.cie.2021.107408 doi: 10.1016/j.cie.2021.107408
![]() |
[20] |
I. Naruei, F. Keynia, Wild horse optimizer: a new meta-heuristic algorithm for solving engineering optimization problems, Eng. Comput., 2021. https://doi.org/10.1007/s00366-021-01438-z doi: 10.1007/s00366-021-01438-z
![]() |
[21] | Y. Yang, H. Chen, A. A. Heidari, A. H. Gandomi, Hunger games search: visions, conception, implementation, deep analysis, perspectives, and towards performance shifts, Expert Syst. Appl., 177 (2021), 114864. https://doi.org/10.1016/j.eswa.2021.114864 |
[22] | J. Tu, H. Chen, M. Wang, A. H. Gandomi, The colony predation algorithm, J. Bionic Eng., 18 (2021), 674-710. https://doi.org/10.1007/s42235-021-0050-y |
[23] |
D. H. Wolpert, W. G. Macready, No free lunch theorems for optimization, IEEE Trans. Evol. Comput., 1 (1997), 67-82. https://doi.org/10.1109/4235.585893 doi: 10.1109/4235.585893
![]() |
[24] |
M. A. A. Al-qaness, A. A. Ewees, M. A. Elaziz, Modified whale optimization algorithm for solving unrelated parallel machine scheduling problems, Soft Comput., 25 (2021), 9545-9557. https://doi.org/10.1007/s00500-021-05889-w doi: 10.1007/s00500-021-05889-w
![]() |
[25] |
A. A. Ewees, M. A.A. Al-qaness, M. A. Elaziz, Enhanced salp swarm algorithm based on firefly algorithm for unrelated parallel machine scheduling with setup times, Appl. Math. Model., 94 (2021), 285-305. https://doi.org/10.1016/j.apm.2021.01.017 doi: 10.1016/j.apm.2021.01.017
![]() |
[26] |
F. K. Onay, S. B. Aydemir, Chaotic hunger games search optimization algorithm for global optimization and engineering problems, Math. Comput. Simul., 192 (2021), 514-536. https://doi.org/10.1016/j.matcom.2021.09.014 doi: 10.1016/j.matcom.2021.09.014
![]() |
[27] | H. Jia, X. Peng, C. Lang, Remora optimization algorithm, Expert Syst. Appl., 185 (2021), 115665. https://doi.org/10.1016/j.eswa.2021.115665 |
[28] |
S. Shadravan, H. R. Naji, V. K. Bardsiri, The sailfish optimizer: a novel nature-inspired metaheuristic algorithm for solving constrained engineering optimization problems, Eng. Appl. Artif. Intell., 80 (2019), 20-34. https://doi.org/10.1016/j.engappai.2019.01.001 doi: 10.1016/j.engappai.2019.01.001
![]() |
[29] |
A. A. Heidari, P. Pahlavani, An efficient modified grey wolf optimizer with Lévy Flight for Optimization Tasks, Appl. Soft Comput., 60 (2017), 115-134. https://doi.org/10.1016/j.asoc.2017.06.044 doi: 10.1016/j.asoc.2017.06.044
![]() |
[30] | M. Molga, C. Smutnicki, Test functions for optimization needs, 2005. |
[31] |
R. Zheng, H. Jia, L. Abualigah, Q. Liu, S. Wang, Deep ensemble of slime mold algorithm and arithmetic optimization algorithm for global optimization, Process, 9 (2021), 1774. https://doi.org/10.3390/pr9101774 doi: 10.3390/pr9101774
![]() |
[32] |
L. Abualigah, M. A. Elaziz, P. Sumari, Z. W. Geem, A. H. Gandomi, Reptile Search Algorithm (RSA): a nature-inspired meta-heuristic optimizer, Expert Syst. Appl., 191 (2022), 116158. https://doi.org/10.1016/j.eswa.2021.116158 doi: 10.1016/j.eswa.2021.116158
![]() |
[33] |
E. H. Houssein, N. Neggaz, M. E. Hosney, W. M. Mohamed, M. Hassaballah, Enhanced Harris hawks optimization with genetic operators for selection chemical descriptors and compounds activities, Neural Comput. Appl., 33 (2021), 13601-13618. https://doi.org/10.1007/s00521-021-05991-y doi: 10.1007/s00521-021-05991-y
![]() |
[34] |
L. Rodríguez, O. Castillo, M. García, J. Soria, A new randomness approach based on sine waves to improve performance in metaheuristic algorithms, Soft. Comput., 24 (2020), 11989-12011. https://doi.org/10.1007/s00500-019-04641-9 doi: 10.1007/s00500-019-04641-9
![]() |
[35] |
W. Long, J. Jiao, X. Liang, S. Cai, M. Xu, A random opposition-based learning grey wolf optimizer, IEEE Access, 7 (2019), 113810-113825. https://doi.org/10.1109/ACCESS.2019.2934994 doi: 10.1109/ACCESS.2019.2934994
![]() |
[36] |
Y. Li, Y. Zhao, J. Liu, Dynamic sine cosine algorithm for large-scale global optimization problems, Expert Syst. Appl., 173 (2021), 114950. https://doi.org/10.1016/j.eswa.2021.114950 doi: 10.1016/j.eswa.2021.114950
![]() |
[37] |
S. Wang, K. Sun, W. Zhang, H. Jia, Multilevel thresholding using a modified ant lion optimizer with opposition-based learning for color image segmentation, Math. Biosci. Eng., 18 (2021), 3092-3143. https://doi.org/10.3934/mbe.2021155 doi: 10.3934/mbe.2021155
![]() |
[38] |
N. Singh, J. Kaur, Hybridizing sine-cosine algorithm with harmony search strategy for optimization design problems, Soft Comput., 25 (2021), 11053-11075. https://doi.org/10.1007/s00500-021-05841-y doi: 10.1007/s00500-021-05841-y
![]() |
[39] |
S. García, A. Fernández, J. Luengo, F. Herrera, Advanced nonparametric tests for multiple comparisons in the design of experiments in computational intelligence and data mining: experimental analysis of power, Inf. Sci., 180 (2010), 2044-2064. https://doi.org/10.1016/j.ins.2009.12.010 doi: 10.1016/j.ins.2009.12.010
![]() |
[40] |
E. Theodorsson-Norheim, Friedman and Quade tests: BASIC computer program to perform nonparametric two-way analysis of variance and multiple comparisons on ranks of several related samples, Comput. Biol. Med., 17 (1987), 85-99. https://doi.org/10.1016/0010-4825(87)90003-5 doi: 10.1016/0010-4825(87)90003-5
![]() |
[41] |
C. A. Coello, Use of a self-adaptive penalty approach for engineering optimization problems, Comput. Ind., 41 (2000), 113-127. https://doi.org/10.1016/S0166-3615(99)00046-9 doi: 10.1016/S0166-3615(99)00046-9
![]() |
[42] | E. Rashedi, H. Nezamabadi-pour, S. Saryazdi, GSA: a gravitational search algorithm, Inf. Sci., 179 (2009), 2232-2248. https://doi.org/10.1016/j.ins.2009.03.004 |
[43] |
F. Huang, L. Wang, Q. He, An effective co-evolutionary differential evolution for constrained optimization, Appl. Math. Comput., 186 (2007), 340-356. https://doi.org/10.1016/j.amc.2006.07.105 doi: 10.1016/j.amc.2006.07.105
![]() |
[44] |
Q. He, L. Wang, An effective co-evolutionary particle swarm optimization for constrained engineering design problems, Eng. Appl. Artif. Intell., 20 (2007), 89-99. https://doi.org/10.1016/j.engappai.2006.03.003 doi: 10.1016/j.engappai.2006.03.003
![]() |
[45] |
A. Baykasoğlu, S. Akpinar, Weighted superposition attraction (WSA): A swarm intelligence algorithm for optimization problems-part2: Constrained optimization, Appl. Soft Comput., 37 (2015), 396-415. https://doi.org/10.1016/j.asoc.2015.08.052 doi: 10.1016/j.asoc.2015.08.052
![]() |
[46] |
H. Yapici, N. Cetinkaya, A new meta-heuristic optimizer: pathfinder algorithm, Appl. Soft Comput., 78 (2019), 545-568. https://doi.org/10.1016/j.asoc.2019.03.012 doi: 10.1016/j.asoc.2019.03.012
![]() |
[47] | Q. Fan, H. Huang, Q. Chen, L. Yao, K. Yang, D. Huang, A modified self-adaptive marine predators algorithm: framework and engineering applications, Eng. Comput., (2021). https://doi.org/10.1007/s00366-021-01319-5 |
[48] |
W. Long, T. Wu, X. Liang, S. Xu, Solving high-dimensional global optimization problems using an improved sine cosine algorithm, Expert Syst. Appl., 123 (2019), 108-126. https://doi.org/10.1016/j.eswa.2018.11.032 doi: 10.1016/j.eswa.2018.11.032
![]() |
[49] |
Y. Li, X. Zhu, J. Liu, An improved moth-flame optimization algorithm for engineering problems, Symmetry, 12 (2020), 1234. https://doi.org/10.3390/sym12081234 doi: 10.3390/sym12081234
![]() |
[50] |
T. Ray, P. Saini, Engineering design optimization using a swarm with an intelligent information sharing among individuals, Eng. Optim., 33 (2001), 735-748. https://doi.org/10.1080/03052150108940941 doi: 10.1080/03052150108940941
![]() |
[51] |
S. Mirjalili, Moth-flame optimization algorithm: a novel nature-inspired heuristic paradigm, Knowl.-Based Syst., 89 (2015), 228-249. https://doi.org/10.1016/j.knosys.2015.07.006 doi: 10.1016/j.knosys.2015.07.006
![]() |
[52] |
H. Liu, Z. Cai, Y. Wang, Hybridizing particle swarm optimization with differential evolution for constrained numerical and engineering optimization, Appl. Soft Comput., 10 (2010), 629-640. https://doi.org/10.1016/j.asoc.2009.08.031 doi: 10.1016/j.asoc.2009.08.031
![]() |
[53] |
L. Gu, R. J. Yang, C. H. Tho, M. Makowskit, O. Faruquet, Y. Li, Optimisation and robustness for crashworthiness of side impact, Int. J. Veh. Des., 26 (2001), 348-360. https://doi.org/10.1504/IJVD.2001.005210 doi: 10.1504/IJVD.2001.005210
![]() |
[54] |
B. S. Yildiz, N. Pholdee, S. Bureerat, A. R. Yildiz, S. M. Sait, Enhanced grasshopper optimization algorithm using elite opposition-based learning for solving real-world engineering problems, Eng. Comput., 2021. https://doi.org/10.1007/s00366-021-01368-w doi: 10.1007/s00366-021-01368-w
![]() |
[55] | S. S. Rao, Engineering optimization: Theory and Practice, 3rd edn. John Wiley & Sons, Chichester, 1996. |
[56] |
A. H. Gandomi, X. S. Yang, A. H. Alavi, Cuckoo search algorithm: a metaheuristic approach to solve structural optimization problems, Eng. Comput., 29 (2013), 17-35. https://doi.org/10.1007/s00366-011-0241-y doi: 10.1007/s00366-011-0241-y
![]() |
1. | Francisco J. G. Silva, Rita C. M. Sales-Contini, Advances in laser materials and processing technologies: An overview, 2025, 12, 2372-0484, 23, 10.3934/matersci.2025002 |
−F sample (modulus of elasticity) | +F sample (modulus of elasticity) | |
Holography (MPa) | 1.589 ± 0.032 | 1.320 ± 0.024 |
Mechanical elasticity (10 MPa) | 3.35 ± 0.16 | 2.86 ± 0.11 |
⟨a⟩=⟨E/E⟩(10−2) | 4.75 ± 0.26 | 4.62 ± 0.20 |
−F sample [Poisson's coefficient (10−1)] | +F sample [Poisson's coefficient (10−1)] | |
Holography | 3.723 ± 0.022 | 3.735 ± 0.025 |
Mechanical elasticity | 3.822 ± 0.095 | 3.90 ± 0.11 |
−F sample [stress-optical coefficient (10−12 m2/N)] |
+F sample [stress-optical coefficient (10−12 m2/N)] |
|
Holography | 3.921 ± 0.08 | 4.442 ± 0.09 |
Mechanical elasticity | 3.95 ± 0.21 | 4.50 ± 0.22 |
−F sample (modulus of elasticity) | +F sample (modulus of elasticity) | |
Holography (MPa) | 1.589 ± 0.032 | 1.320 ± 0.024 |
Mechanical elasticity (10 MPa) | 3.35 ± 0.16 | 2.86 ± 0.11 |
⟨a⟩=⟨E/E⟩(10−2) | 4.75 ± 0.26 | 4.62 ± 0.20 |
−F sample [Poisson's coefficient (10−1)] | +F sample [Poisson's coefficient (10−1)] | |
Holography | 3.723 ± 0.022 | 3.735 ± 0.025 |
Mechanical elasticity | 3.822 ± 0.095 | 3.90 ± 0.11 |
−F sample [stress-optical coefficient (10−12 m2/N)] |
+F sample [stress-optical coefficient (10−12 m2/N)] |
|
Holography | 3.921 ± 0.08 | 4.442 ± 0.09 |
Mechanical elasticity | 3.95 ± 0.21 | 4.50 ± 0.22 |