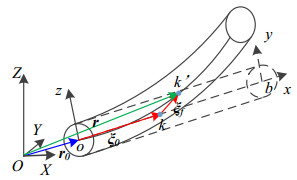
Citation: Qingyun Zhang, Xinhua Zhao, Liang Liu, Tengda Dai. Dynamics analysis of spatial parallel robot with rigid and flexible links[J]. Mathematical Biosciences and Engineering, 2020, 17(6): 7101-7129. doi: 10.3934/mbe.2020365
[1] | Zhen Liu, Song Yang, Tao Ding, Ruimin Chai . Dynamic modeling and performance analysis of a lower-mobility parallel robot with a rotatable platform. Mathematical Biosciences and Engineering, 2023, 20(2): 3918-3943. doi: 10.3934/mbe.2023183 |
[2] | Zhen Liu, Song Yang, Chen Cheng, Tao Ding, Ruimin Chai . Study on modeling and dynamic performance of a planar flexible parallel manipulator based on finite element method. Mathematical Biosciences and Engineering, 2023, 20(1): 807-836. doi: 10.3934/mbe.2023037 |
[3] | Dawei Ren, Xiaodong Zhang, Shaojuan Lei, Zehua Bi . Research on flexibility of production system based on hybrid modeling and simulation. Mathematical Biosciences and Engineering, 2021, 18(1): 933-949. doi: 10.3934/mbe.2021049 |
[4] | Dan Yang, Zhiqiang Xie, Chunting Zhang . Multi-flexible integrated scheduling algorithm for multi-flexible integrated scheduling problem with setup times. Mathematical Biosciences and Engineering, 2023, 20(6): 9781-9817. doi: 10.3934/mbe.2023429 |
[5] | Lingling Wei, Haiyi Liu, Lifeng Wu . Spatial distribution of floating population in Beijing, Tianjin and Hebei Region and its correlations with synergistic development. Mathematical Biosciences and Engineering, 2023, 20(3): 5949-5965. doi: 10.3934/mbe.2023257 |
[6] | Yun Kang, Sourav Kumar Sasmal, Komi Messan . A two-patch prey-predator model with predator dispersal driven by the predation strength. Mathematical Biosciences and Engineering, 2017, 14(4): 843-880. doi: 10.3934/mbe.2017046 |
[7] | T. J. Newman . Modeling Multicellular Systems Using Subcellular Elements. Mathematical Biosciences and Engineering, 2005, 2(3): 613-624. doi: 10.3934/mbe.2005.2.613 |
[8] | Bo Kou, Jinde Cao, Wei Huang, Tao Ma . The rutting model of semi-rigid asphalt pavement based on RIOHTRACK full-scale track. Mathematical Biosciences and Engineering, 2023, 20(5): 8124-8145. doi: 10.3934/mbe.2023353 |
[9] | Mette S. Olufsen, Ali Nadim . On deriving lumped models for blood flow and pressure in the systemic arteries. Mathematical Biosciences and Engineering, 2004, 1(1): 61-80. doi: 10.3934/mbe.2004.1.61 |
[10] | Zhen Yang, Junli Li, Liwei Yang, Qian Wang, Ping Li, Guofeng Xia . Path planning and collision avoidance methods for distributed multi-robot systems in complex dynamic environments. Mathematical Biosciences and Engineering, 2023, 20(1): 145-178. doi: 10.3934/mbe.2023008 |
In multibody systems, the demand for lightweight designs requires researchers and designers to account for the impact of the link flexibility of the mechanisms. However, research on link flexibility has mainly focused on planar mechanisms and robotic arms, whereas there have been fewer studies focused on rigid flexible spatial parallel mechanisms with non-linear coupling effects. The parallel mechanism with rigid links and flexible spatial links is widely used in aerospace, industrial production, and other practical engineering fields. In particular, in the field of industrial production, robots with fewer degrees of freedom have been widely used [1,2,3,4,5]. Ideally, all the components should be set as rigid links for dynamics analysis, but at high speeds, the slender links will be elastically deformed, and the flexible deformation of the links and the coupling effects with the rigid links will have an important impact on the dynamic performance of the system. Therefore, it is of great significance to derive a reasonable dynamics model [6,7,8,9] of the rigid–flexible spatial parallel mechanisms with nonlinear coupling effects for analyzing the forces acting on a system and ensuring the trajectory accuracy of the end-effector.
The absolute nodal coordinate formulation (ANCF) [10,11,12,13] and the floating frame of reference (FFR) formulation [14,15] are widely used methods for establishing dynamics models of flexible multibody systems. The advantages of the former include the mass matrix being constant and the centrifugal and Coriolis forces being zero. However, the stiffness matrix is highly complicated and inefficient for use in calculating the dynamics solutions. In the FFR formulation, the coupling effects between the rigid and flexible coordinates are included in the dynamics [1,16,17,18], which can be applied with modal reduction techniques. There are two sets of coordinate systems in the FFR formulation. The first set is used to define the configuration of the local coordinate system, whereas the second set is applied to describe the configuration of the deformed body. Lugrís et al. [19,20,21,22] provide detailed derivations for the inertia terms, shape integrals, and elastic forces of planar mechanisms based on the FFR formulation. For instance, the dynamic performance of the rigid–flexible coupling of a hub-beam was considered in Liu and Liu [23]. Long et al. [24] presented a new method for determining the dynamics of a parallel robot with a flexible platform. In Zhang et al. [25,26], flexible multibody dynamics models of planar parallel robots were established, and the coupling effects were analyzed. Liu et al. [27] verified the importance of thermoplastic coupling using a rigid–flexible–thermal coupling model and a simulation verification. In Liu et al. [28], Lagrange's equations were applied to analyze the dynamic characteristics of a spatial parallel manipulator with a rigid end-effector and three flexible kinematic chains. Han et al. [29] implemented dynamics analysis and a simulation of a flexible beam element using the ANCF and FFR methods.
This paper makes six new contributions:
1) By setting the local coordinate system of the flexible spatial links as a non-centroid coordinate system, the influence of the coupling term in the inertia tensor on the dynamic performance of the system is considered.
2) Unlike previous models, this model uses the FFR method to determine the dynamics while accounting for the coupling effects between the rigid and flexible coordinates and the micro-displacement of the end effector. This allows the elastic vibrations and motion errors of the system to be more accurate.
3) Since the coupling term in the inertia tensor has an important influence on the dynamic performance of the system, it is considered in this analysis by setting the local coordinate system of the flexible spatial link as a non-centroid coordinate system. This coupling term was not taken into account in previous studies.
4) Three typical models were compared. The FFR model was established using the FFR formulation and Lagrange's equations, and simulation code was written in MATLAB. The FEA model was implemented using a co-simulation of SOLIDWORKS, ANSYS, and ADAMS. The ideal rigid–body model, which was established based on Lagrange's equations of the first kind, and an analytical solution were obtained.
5) The dynamics equation of the FFR model is a highly coupled, highly nonlinear, high-index differential-algebraic equation. The mass matrix is no longer a symmetric matrix, and the stiffness matrix is no longer a constant matrix. Converting the dynamics equation into a pure differential equation to obtain a numerical solution avoids the problem of numerical divergence caused by the inaccurate estimation of the initial value of the Lagrange multiplier and the new solution problem caused by the expansion of the model.
6) The results indicate that the FFR model is more accurate for calculating the influence of the flexible deformation on the dynamic performance of the spatial parallel robot. The recursive formulas are also applicable to other flexible spatial links.
As depicted in Figure 1, the O-XYZ system is a global coordinate system that defines the large rigid-body displacement, and the o-xyz system is a local coordinate system that defines the small deformation body displacement.
By using the FFR formulation, the absolute position vector of point k on the flexible link can be written as
rk=r0+Rξ=r0+R(ξ0+ξf), | (1) |
where r0 is the origin vector of the o−xyz system, ξ0(x,y,z) defines the vector of the point k in o−xyz in the undeformed state, and ξf represents the vector of point k relative to the o−xyz system in the deformed state. o and b are the two nodes of the spatial beam element. The rotation matrix R from the o−xyz system to the O−XYZ system is given by Eq (2). In particular, when the flexible link is a spatial link, matrix R includes more than one transformation angle θi(i=1,…n) as follows
R=Rθ1Rθ2...Rθn. | (2) |
The finite element method was employed to discretize the deformation field of the flexible spatial link. The displacement vector of any point k on the flexible spatial link caused by the deformation can be expressed as
ξf=Nqf, | (3) |
where qf represents the node displacement vector of the spatial beam element in the local coordinate system, and N represents the shape function. The specific expression of qf is follows
qf=[xoyozoθoxθoyθozxbybzbθbxθbyθbz], | (4) |
where xo, yo, zo, xb, yb, and zb represent deformation displacement vectors along the three coordinate axes at the nodes. θox, θoy, θoz, θbx, θby, and θbz represent the rotational displacement vectors around the three coordinate axes at the nodes.
It is assumed that the deformation displacement along the axis is described using a first-order polynomial, and a cubic polynomial interpolation function is used to describe the elastic angular deformation.
1) Axial interpolation function
Assuming that the axial interpolation function is a linear function, it can be written as
v(x,t)=b0+b1x | (5) |
According to the boundary conditions
{v(0,t)=xo=b0v(L,t)=xb=b0+b1L | (6) |
2) Horizontal interpolation function
Assuming that the axial interpolation function is a linear function, it can be written as
N(x,t)=c0+c1⋅x+c2⋅x2+c3⋅x3 | (7) |
According to the boundary conditions
{N(0,t)=yo=zo˙N(0,t)=θoy=θozN(L,t)=yb=zb˙N(L,t)=θby=θbz | (8) |
The axial and horizontal displacements corresponding to nodes o and b can be obtained by solving Eq (6) and Eq (8), therefore, the shape function N can be expressed as
N=[NANBNC]=[xo00000xb000000yo000θoz0yb000θbz00zo0θoy000zb0θby0], | (9) |
where e=x/L, xo=e, yo=zo=1−3e2+2e3, θby=−θbz=L(−e2+e3), yb=zb=3e2−2e3, θoy=−θoz=L(e−2e2+e3), xb=1−e.
Lagrange's equations are typically used to derive the dynamics equations as follows [30]
ddt(∂(T−V)∂˙q)−∂(T−V)∂q+∂CT∂qλ=Q, | (10) |
where the T is the kinetic energy, V represents the potential energy, C represents constraint equations, vectors q and Q are the generalized coordinates of the generalized external forces, and λ is a Lagrange multiplier vector.
For the spatial flexible links, translational and rotational kinetic energy must be included.
1) Translational kinetic energy of flexible spatial link
The translational kinetic energy of the flexible spatial link based on the energy principle is as follows
Tf−T=12∫Vρ(˙rk)T(˙rk)dV, | (11) |
where ρ is the density of the material. The global position vector rk is equal to
rk=r0+Rθ1Rθ2...Rθnξ. | (12) |
The velocity vector of the flexible spatial link is computed from Eq (12), yielding the following equation
˙rk=˙r0+∂(Rθ1Rθ2⋯Rθn)∂tξ+Rθ1Rθ2…RθnN˙qf=H˙q. | (13) |
The matrix H and generalized velocity vector ˙q can be expressed as
{H=[I00I11I22...InIn+11]˙q=d[r00θ11θ22...θnqf]dt, | (14) |
where I0 is a 3 × 3 identity matrix, and I1,I2,...,In+1 can be expressed as follows:
{I1=˙Rθ1Rθ2…RθnI2=Rθ1˙Rθ2…RθnξIn=Rθ1Rθ2…˙RθnξIn+1=Rθ1Rθ2…RθnN. | (15) |
By means of Eq (11), the translational kinetic energy of the flexible spatial link may be written as
Tf−T=12˙qT(ρA∫L0HTHdx)˙q=12˙qTMf−T˙q, | (16) |
where A represents the cross-sectional area of the flexible spatial link. The mass matrix Mf−T of the translational kinetic energy is expressed in the following compact form
Mf−T=ρA∫L0HTHdx=[MttMtθ1Mtθ2...MtθnMtfMθ1θ1Mθ1θ2...Mθ1θnMθ1fMθ2θ2...Mθ2θnMθ2f.........MθnθnMθnfsymmetricMff], | (17) |
where Mtt represents the purely translational inertia terms, Mff is the purely flexible component, Mtθn(n=1,2,…j) is the coupling term containing the translational and rotational coordinates, Mtf represents the coupling term between translational coordinates and flexible coordinates, Mθnθn(n=1,2,…j) is the purely rotational component, and Mθnf(n=1,2,…j) is the coupling term between rotational coordinates and flexible coordinates.
The matrix Mtt is a constant matrix, and Mff,Mtθn,Mθnθn,Mtf,Mθnf can be written as
{Mtθn=ρA∫L0IT0IndxMtf=ρA∫L0IT0In+1dxMθnθn=ρA∫L0ITnIndxMθnf=ρA∫L0ITnIn+1dxMff=ρA∫L0ITn+1In+1dx=ρA∫L0NTNdx. | (18) |
When the flexible spatial link degenerates into a rigid spatial link, the deformation coordinates of the flexible link are zero (qf=0). Hence, the translational kinetic energy of the rigid spatial link can be further written as
Tf−T→r−T=12˙qT(Mtt+…+Mθjθj)˙q. | (19) |
2) Rotational kinetic energy of flexible spatial link
The rotational kinetic energy of the flexible spatial link is defined as
Tf−R=12∫L0˙θ2dJc, | (20) |
where θ(x,t) is the absolute rotation angle of the micro-segment with a distance x and a width dx from the local coordinate system origin in actual motion, and dJc=ρJdx is the area moment of inertia around the center of mass.
The link area moment of inertia in the O-XYZ system can be expressed as
J=Rθ1Rθ2…Rθn−1¯J(Rθ1Rθ2…Rθn)T, | (21) |
where ˉJ=[IxIyIz], Ix, Iy, and Iz represent the respective area moments of inertia of the flexible spatial link with respect to the local coordinate axes x, y and z the rotational kinetic energy of the flexible spatial link can be written as
Tf−R=12˙qTMf−R˙q, | (22) |
where Mf−R is the mass matrix corresponding to the rotational kinetic energy and is expressed as follows
Mf−R=[mrrmrθ1mrθ2...mrθnmrfmθ1θ1mθ1θ2...mθ1θnmθ1fmθ2θ2...mθ2θnmθ2f.........mθnθnmθnfsymmetricmff]. | (23) |
The matrices mrr,mff,mrθn,mrf,mθnθn, and mθnf can be written as
{mrr=003×3mrθ1=mrθ2=mrθn=003×1mrf=001×12mff=ρ∫L0(dNCdx)TJ(dNCdx)dxmθnθn=ρ∫L0[010]J[010]Tdxmθnf=dqfdtρ∫L0[001](dNCdx)dx. | (24) |
When the flexible spatial link degenerates into a rigid spatial link, the deformation coordinates of the flexible link are zero (qf=0). Hence, the rotational kinetic energy of the rigid spatial link can be further written as
Tf−R→r−R=12˙qT(mrr+...+mθjθj)˙q. | (25) |
3) Total kinetic energy of flexible spatial link
The total kinetic energy of the flexible spatial link is calculated as follows:
Tf=Tf−T+Tf−R. | (26) |
The total kinetic energy of the rigid spatial link is calculated as follows:
Tr=Tr−T+Tr−R. | (27) |
However, the generalized coordinates of the flexible spatial link are expressed in the o−xyz system, and they must be expressed in the O−XYZ system. Therefore, the transformation relationships from qf to um are expressed as follows
{qf=Bum˙qf=˙Bum+B˙um, | (28) |
where B is given by
B=R−θnR−θn−1...R−θ1. | (29) |
Substituting Eqs (28) and (29) into Eq (26), the total kinetic energy of the flexible spatial link in the O−XYZ system is
TO−f=12˙ˉqiTMO−f˙ˉqi. | (30) |
The specific forms of ˙ˉqi and MO−f are shown in Appendix 1. Since the mass matrix in the o−xyzsystem is a symmetric matrix, but the total mass matrix of the system must be converted to the O−XYZ system for representation, so it needs to be multiplied by the transform matrix B, and because the matrix B is a asymmetry matrix. Therefore, the system mass matrix is no longer a symmetric matrix.
By assembling the differential equations of the rigid and flexible links, the kinetic energy of each kinematic chain can be expressed as
TiO=TiO−f+TiO−r=12˙ˉqiTMi˙ˉqiTiO, | (31) |
where ˉq represents the generalized coordinates of the kinematic chain, and Mi represents the mass matrix of the kinematic chain.
According to the virtual work principle, the elastic force virtual work of any beam element in the flexible spatial link can be written as
δW=−∫VσTδεεdV, | (32) |
where σ and ε represent stress and strain vectors, respectively. For linear isotropic materials, σ=Eεε, and the strain–displacement relationship is εε=DNqf. Substituting σ=Eεε and εε=DNqf into Eq (32), the beam element stiffness matrix can be written as
kf=∫V(DN)TEDNdV, | (33) |
where E and D represent the partial differential operator of the strain–displacement and the shear modulus of the flexible spatial link, respectively. The specific expression of kf is shown in Appendix 1.
Because the rigid links cannot produce generalized elastic forces, the stiffness matrix of the kinematic chain in the o−xyz system can be expressed as
ki=[0000...kf]. | (34) |
Since kf is a constant matrix, ki is also a constant matrix, but the total stiffness matrix of the system must be converted to the O−XYZ system for representation, so it needs to be multiplied by the transform matrix B, and because the matrix B is a time-varying related to generalized coordinates. Therefore, the system stiffness matrix is no longer a constant matrix, and its specific form Ki is shown in Appendix 1.
The generalized elastic forces of the kinematic chain may be expressed by deriving the elastic potential energy relative to the elastic coordinates
Fielastic=∂Vie∂¯qi=Ki¯qi. | (35) |
where Vie represent the elastic potential energy of the kinematic chain i.
Based upon the aforementioned generalized forces, the generalized forces of the kinematic chain due to gravity of the spatial parallel robot can be written as
Fig=∂Vig∂¯qi. | (36) |
The virtual work of the robotic actuated force (torque) can be written as
δW=Fix∂x∂qj+Fiy∂y∂qj+Fiz∂z∂qj. | (37) |
The robotic actuated force (torque) of the kinematic chain can be derived by differentiation as
QiF=δWiFδ¯qi. | (38) |
By means of Eq (10), the matrix form of the dynamics equations of the kinematic chain can be obtained as follows
Mi¨¯qi+Ki¯qi+Fig=QiF+QiV, | (39) |
where QiV includes the Coriolis and centrifugal force matrices of the kinematic chain, which can be written as
QiV=−˙Mi˙¯qi+∂∂¯qi(12˙¯qTiMi˙¯qi). | (40) |
The dynamics equations of the spatial rigid–flexible coupling model can be expressed by assembling the dynamics equations of the kinematic chain and the constraint equations as follows
M¨ˆq+Kˆq+ˆFg+ˆCTˆqˆλ=ˆQF+ˆQV, | (41) |
where M and K are the mass and stiffness matrices of the spatial rigid–flexible coupling model, respectively, ˆFg and ˆQF are the generalized gravitational and robotic actuated force (torque), respectively, ˆQV represents the Coriolis and centrifugal forces, ˆq and ˆCTˆq are generalized coordinates and constraint Jacobian matrix of the spatial rigid–flexible coupling model, respectively. Among them, the constrained Jacobian matrix ˆCTˆq can be obtained by deriving the generalized coordinates from the constrained equations.
The matrices M, Kand ˆq can be expressed as
M=[M1M2...Mi], K=[K1K2...Ki], |
ˆq=[r01θ11θ12...θ1nu11...1mr02θ21...um1...mm], | (42) |
where n and m represent the number of the rigid and flexible coordinates of the spatial parallel robot, respectively.
A typical 3-RRRU spatial parallel robot with rigid links and flexible spatial links is shown in Figure 2.
This robot has three triangular symmetric kinematic chains. It is composed of ten parts, a driving link AiBi (i = 1, 2, 3), an intermediate link BiCi (i = 1, 2, 3), a passive link CiPi (i = 1, 2, 3), and the end-effector P1P2P3. The fixed base and driving links are connected by a revolute pair Ai (i = 1, 2, 3), whereas joints Bi (i = 1, 2, 3) and Ci (i = 1, 2, 3) are passive revolute pairs. The end-effector and passive links are connected by universal joints. Among these ten parts, the passive link CiPi (i = 1, 2, 3) is a slender link that will be elastically deformed under high-speed motion. Therefore, it is treated as a flexible-body, and the other parts are treated as a rigid body. The link CiPi (i = 1, 2, 3) can perform arbitrary movements in space. However, the component connected to it is a rigid component, so the end-effector can only perform translational movement along three coordinate axes.
The joint variables of the robotic kinematic chain with rigid links and flexible spatial links is illustrated in Figure 3.
The global coordinate system O-XYZ is attached to the geometric center of the fixed base. The Z-axis is perpendicular to the fixed base, and the X-axis is opposite to the undeformed neutral axis of each link. The local coordinate is fixed at the upper joint of each link. The driving link AiBi (i = 1, 2, 3) and intermediate link BiCi (i = 1, 2, 3) are in the same plane, the rotating axis in the global coordinate system is the Y-axis, but the rotation axis of passive link CiPi (i = 1, 2, 3) is the Z-axis. Therefore, the passive link CiPi (i = 1, 2, 3) is a spatial link.
The lengths of components AiBi, BiCi, and CiPi (i = 1, 2, 3) are L1, L2, and L3, respectively.θi1, θi2 and θi3 are the angles between the rotation axis and links AiBi, BiCi, and CiPi (i = 1, 2, 3) in the local coordinate system, respectively. φi (i = 1, 2, 3) denotes the angle between the coordinate system O−XYZ and Ai−XAiYAiZAi(i=1,2,3) in the Z direction, and ZAi is parallel to Z.
To ensure the correctness of the derived dynamic equations, it is necessary to verify the influence of the flexible deformation on the system by comparing the end-effector motion trajectories in the FFR and the ideal rigid-body models and to verify the accuracy of the derived formula by comparing the motion trajectory deviations of the FFR and FEA models relative to that of the ideal rigid-body model. The dynamics equations of the three models were established using Lagrange's equations of the first kind and solved by numerical integration.
1) Dynamic equations of the spatial flexible link
Dynamics models can be established using the dynamics equations derived in section 2 and 3. First, by means of Eq (12), the vector rk is described as follows:
rk=r0+R1R2ξ, | (43) |
where ξ0=[xyz]T, ξf=Nqf.
The absolute rotation angle vector can be written as
θ=Rθi[00θi3+dNCdx]+[0θi20]. | (44) |
Figures 4 and 5 show the flexible coordinates in the o−xyz and O−XYZ systems, respectively.
By means of Eq (28), the relationship between the generalized coordinates qf and ui can be obtained.
Finally, the translational and rotational kinetic energies of the flexible spatial link of the 3-RRRU spatial parallel robot can be obtained by substituting Eqs (43) and (44) into Eqs (11) and (20), respectively, and the total kinetic energy of the flexible spatial link in the global coordinate system can be obtained according to Eq (30), as follows:
TO−f=12˙¯qTiMO−f˙¯qi, | (45) |
where ˙¯qi=d([θi1θi2θi3um])dt.
2) Dynamic equations of rigid components
Because the driving link AiBi (i = 1, 2, 3) is purely rotated, its rotational kinetic energy is
TAiBi=16m1L21˙θ2i1=12˙¯qTiMAiBi˙¯qi. | (46) |
The intermediate link BiCi (i = 1, 2, 3) has both translational and rotational kinetic energy, and its kinetic energy is expressed as follows
TBiCi=16m2L21˙θ2i1+12m2L1L2˙θi1˙θi2cosθi2+16m2L21˙θ2i1=12˙¯qTiMBiCi˙¯qi. | (47) |
The kinetic energy of each kinematic chain can be obtained by substituting Eqs (45)–(47) into Eq (31).
The potential energy of rigid component of the kinematic chain can be written as
{VAiBi=12m1gL1sin(θi1)VBiCi=12m2gL2sin(θi2). | (48) |
The generalized gravitational force Fig of the kinematic chain can be obtained by substituting Eq (48) into Eq (36).
The generalized coordinates and the driving force of the CiPi (i = 1, 2, 3) can be expressed as
{AB=[−L1cos(θi1)0−L1sin(θi1)]F=[Fsin(θi1)0−Fcos(θi1)]. | (49) |
The actuated torque QiF of the robotic system can be obtained by substituting Eq (49) into Eq (38).
However, the elastic deformation of the flexible links will cause positional errors in the kinetic trajectory of the end-effector, Therefore, the micro-displacement and micro-rotation generalized coordinates of the end-effector can be assumed to be ΔP=[ΔPxΔPyΔPzΔPθxΔPθyΔPθz], the actual kinetic trajectory P′=[Px′Py′Pz′Pθx′Pθy′Pθz′], the ideal motion trajectory P=[PxPyPzPθxPθyPθz], and the relationship between P′, ΔP andP can be expressed as
P′=P+UPΔP, | (50) |
where UP=[10Pz−Py1−Pz0Px1Py−Px0].UP represents geometrical constraint relationship [31] between the actual kinetic trajectory and ideal kinetic trajectory of the end-effector. Thus, the kinetic and potential energy of the end-effector can be written as
{Tend−effector=12˙P′TmP˙P′+12JωTPVend−effector=mpg[001000]˙P′. | (51) |
3) Constraint relationship
The constraint equations are defined as follows.
(1) Constraint equation of the length of link BiCi (i = 1, 2, 3)
C1−i=(rCi−x−L2cos(θi2))2+(rCi−z+L2sin(θi2))2−L22=0. | (52) |
(2) Constraint equation for the distance between point Pi (i = 1, 2, 3) and P
C2−i=(Px−Pix)2+(Py−Piy)2+(Pz−Piz)2−r2=0. | (53) |
(3) Constraint equation for joint Ci (i = 1, 2, 3) can be expressed by the position vector of the rigid joint Ci (i = 1, 2, 3) equal to the position vector of the flexible joint Ci (i = 1, 2, 3)
C3−i=rC1−f−rC1−r=002×1. | (54) |
(4) Constraint equation for joint Pi (i = 1, 2, 3) can be expressed by the position vector of the rigid joint Pi (i = 1, 2, 3) equal to the position vector of the flexible joint Pi (i = 1, 2, 3)
C4−i=rP1−f−rP1−r=003×1, | (55) |
The constraint equations can be written as
ˆC=[C1−1C1−2C1−3C2−1C2−2C2−3CT3−1CT3−2CT3−3CT4−1CT4−2CT4−3] | (56) |
The velocity constraint matrix and the angular velocity constraint matrix can be obtained by calculating the first and second derivative of the position constraint matrix ˆCwith respect to time t, the specific expression are as follows
ˆCˆq˙ˆq+ˆCt=00 | (57) |
ˆCˆq¨ˆq=−(ˆCˆq˙ˆq)ˆq˙ˆq−2ˆCqt˙ˆq−ˆCtt | (58) |
The Eq (56), TiO,QiF,Fig and Eq (51) are substituted into Eq (41) to obtain the matrix form of the system dynamics equations of the spatial rigid–flexible coupling model.
4) Numerical solution
The FFR model of the spatial parallel robot with rigid links and flexible spatial links was established using the FFR formulation. The number of generalized coordinates for the FFR model was 42, which included 12 rigid and 30 flexible coordinates. By means of Eq (41), the dynamics equations can be rewritten as
M¨ˆq+ˆCTˆqˆλ=ˆQ, | (59) |
where ˆQ=ˆQF+ˆQV−Kˆq−ˆFg.
Since the Eq (59) in this study were differential algebraic equations with a high index of 3, and numerical divergence occurred readily. Therefore, to obtain the solution, they were combined with the acceleration Eq (58) to solve.
Because the dynamics solution was obtained at the acceleration level, as the number of iterations increased, it was possible to calculate the position and velocity constraint equation errors. Therefore, positional and velocity violations were eliminated using the Baumgarte stabilization method, which can be expressed as follows
ˆCˆq¨ˆq=−(ˆCˆq˙ˆq)ˆq˙ˆq−2ˆCˆqt˙ˆq−ˆCtt−2αε2−β2ε1, | (60) |
where α and β are system feedback control parameters, εε1 and εε2 represent the displacement and velocity constraint stabilization parameters, respectively, expressed as follows
{εε1=ˆCεε2=ˆCˆq˙ˆq+ˆCt. | (61) |
It is necessary to estimate the initial values of the generalized position coordinate vector ˆq and the Lagrange multiplier vector ˆλ. ˆq can be estimated based on the initial position of the rigid-body dynamics, but it is much more difficult for ˆλ. Therefore, the numerical calculation was performed by reducing the index to 1. Equation (59) can be rewritten in the following form
¨ˆq=ˆM−1ˆQ−ˆM−1ˆCTˆqˆλ. | (62) |
Multiplying both sides of Eq (62) by ˆCˆq yields the following
ˆCˆq¨ˆq=ˆCˆqˆM−1ˆQ−ˆCˆqˆM−1ˆCTˆqˆλ. | (63) |
Vector ˆλ can be obtained by combining Eqs (60) and (63). Vector d2ˆq/dt2 can be obtained by substituting ˆλ into Eq (62). Vectors ˆq and dˆq/dt were obtained by utilizing the Newmark β method.
{˙ˆqi+11=˙ˆqi+(1−α)h¨ˆqi+αh¨ˆqi+1ˆqi+11=ˆqi+11+h˙ˆqi+(1/2−β)h2¨ˆqi+βh2¨ˆqi+1, | (64) |
where h is the step size. Computational programs were written in MATLAB to perform dynamic simulation of the FFR model.
5) Frequency solution
By means of Eq (41), the free vibration equations of the 3-RRRU spatial parallel robot with rigid links and flexible spatial links can be written as
M¨ˆq+Kˆq=00 | (65) |
According to the modal analysis theory [32], the natural frequency and modal expressions of the system can be obtained as
|−λM+K|=00 | (66) |
When the mass matrix is a non-singular matrix, let S=M−1K, then Eq (66) can be rewritten as
{|−λI+S|=00λ=ω2mωm=2πfm | (67) |
where ωm is the natural angular frequency of the system, and fm is the natural frequency of the system.
Ideally, the spatial links CiPi (i = 1, 2, 3) of the spatial parallel robot can be treated as a rigid body, and the kinetic energy TCiPi can be directly calculated using Eq (27). The specific expression is
TCiPi=−m3gL1sin(θi1)−m3gL2sin(θi2)−12m3L3sin(θi2)cos(θi3). | (68) |
The potential energy of the spatial link CiPi (i = 1, 2, 3) can be obtained by the work–energy theorem, and its expression is as follows:
VCiPi=−m3gL1sin(θi1)−m3gL2sin(θi2)−12m3L3sin(θi2)cos(θi3). | (69) |
The kinetic and potential energies of the end-effector can be calculated as
{Tend−effector=12mp(˙Px2+˙Py2+˙Pz2)Vend−effector=mpgPz. | (70) |
Therefore, the dynamic model of the ideal rigid-body can be established by introducing the kinetic and potential energy of each rigid link into the Lagrange equations of the first kind, which can be solved by numerical methods.
To compare and verify with the FFR model, the structural features and numerical solution methods of the FEA model are the same as the FFR model. When the spatial parallel mechanism is simulated by finite element software, there are many factors affecting its dynamic characteristics. Therefore, the following assumptions must be made before establishing a FEA model of a spatial rigid–flexible coupled parallel robot.
1) The elastic deformation of the spatial slender link during system operation will have an important impact on the dynamic performance of the system. Therefore, in the FEA model, the spatial link is considered to be a flexible body, and the other links are considered to be rigid bodies for analysis.
2) Each pair of components are connected by a rigid motion pair.
3) There is negligible friction between pairs.
The FEA model was implemented using a co-simulation of three software packages: ANSYS, SOLIDWORKS, and ADAMS. The workflow of the co-simulation using these three software packages is shown in Figure 6.
First, the 3D model was established in SOLIDWORKS and imported into finite element analysis software in the STP file format. Second, the deformation of the flexible spatial link CiPi(i=1,2,3) is described by the FEA method. The bodies of the flexible spatial links were meshed with SOLID 185 units and contained 48,598 elements and 63,659 nodes. The model was saved as a flexible neutral file (.mnf) and imported into ADAMS through the ADAMS connection module in ANSYS. Finally, the constraint relationship of the FEA model was defined based on the actual physical prototype in ADAMS, and the material properties are shown in Table 1. The dynamics equations were deduced using Lagrange's equations, and an integral solver (SI2, GSTIFF) was used for the simulation analysis in ADAMS, and the solution accuracy is 10-4.
Link | AiBi | BiCi | CiPi | End-effector | Fixed base |
Young's modulus (MPa) | 2.07 × 105 | 2.07 × 105 | 7.17 × 104 | 2.07 × 105 | — |
Density (kg/m3) | 7.8 × 103 | 7.8 × 103 | 2.7 × 103 | 7.8 × 103 | — |
Poisson's ratio | 0.3 | 0.3 | 0.3 | 0.3 | — |
The simulation time was set to 5 s, and the step size was 0.001 s. To verify the correctness of the rigid–flexible coupled model, the results of the fully rigid inverse dynamics model were loaded into the rigid–flexible coupled model based on the same driver. The validity of the model was determined by examining the movement trends and trajectory errors of the two types of models.
To validate the presented method, a circular trajectory of the geometric center point of the end-effector was used to carry out the simulation. The circle defined in the plane Pz=−0.7m with a radius of 0.1 m can be written as
{Px=0.1cos(ω⋅t)Py=0.1sin(ω⋅t)Pz=−0.7, | (71) |
where ω represents the angular velocity of the end-effector, which was set to 2 rad/s. The shearing modulus G = 8 × 104 MPa. The geometric properties of all the parts are shown in Table 2, and the solution accuracy is 10-4. When the dynamic analysis was performed on an ideal rigid-body model, the material properties of all parts were steel.
Link | AiBi | BiCi | CiPi | End-effect | Fixed base |
Length (m) | 0.4 | 0.1 | 0.8 | — | — |
Mass (kg) | 2 | 0.3 | — | 1.5 | — |
Radius (m) | 0.01 | 0.01 | 0.01 | 0.1 | 0.4 |
Thickness (m) | — | — | — | 0.02 | 0.15 |
The relationship of the natural frequency of the spatial parallel robot with rigid links and flexible spatial links with time can be solved by MATLAB software programming, and the result is shown in Figure 7.
In order to verify the correctness of natural frequency by using the derived dynamics model, based on the FEA simulation model, the natural frequency of the system is analyzed through the ADAMS/Vibration module. The results are shown in Table 3.
Order | 1~6 | 7 | 8 | 9 | 10 | 11 | 12 |
Frequencies /Hz | 0 | 2.21E-05 | 0.002 | 1.496 | 2.484 | 12.276 | 17.799 |
It can be seen from Table 3 that the first 6 natural frequencies in the vibration simulation model are all 0, that is, the rigid body mode corresponding to the system. Therefore, the minimum natural frequency of the system appears at the 7th order, and the corresponding natural frequency is 2.21E-005Hz. The minimum natural frequency of the derived dynamics model calculated by Eq (67) is 3.72E-005Hz. Due to the large number of elements of the flexible spatial link and the system's assembly errors, the minimum natural frequency of the simulation model is smaller than the derived dynamics model, but the two values are basically the same, thus verifying the correctness of the establishment of the dynamics model.
A comparison of the displacement of the end-effector between the ideal rigid-body and FFR models is shown in the figures below. The displacement trajectories of the geometric center point of the end-effector in the X and Y directions with time are shown in Figures 8 and 9, respectively.
As shown in Figures 7 and 8, the trajectory trends of the end-effector of the ideal rigid-body and FFR models were basically the same, but the FFR model predictions yielded certain range of fluctuations relative to the ideal rigid-body model trajectory. The maximum deviations of the fluctuations are shown in Table 4. The fluctuations reached a maximum at the peak point of the motion trajectory.
Axis | Displacement/m | Maximum error/m | |
FFR model | Ideal rigid-body model | ||
X | −0.09623 | −0.08955 | 0.00668 |
Y | −0.00841 | −0.00552 | 0.00289 |
Z | −0.70083 | −0.6981 | 0.00273 |
The displacement of the geometric center of the end-effector in the Z direction is shown in Figure 9.
As shown in Figure 10, when the end-effector was moving in a plane, the Z-direction displacement of the rigid system did not change, and the rigid flexible coupling system floated between −0.70083 and −0.6993 m.
The circular motion trajectories of the end-effector of the ideal rigid-body and FFR models on the three planes are shown in Figure 11.
Figure 11 shows that the motion trajectory of the ideal rigid-body model was an ideal circular curve, but the FFR model was no longer an ideal circular curve. This was because the elastic deformation of the flexible spatial links in the FFR model affected the dynamic performance of the system. Therefore, the elastic deformation of the flexible spatial links cannot be ignored, and it is necessary to establish a dynamic model that follows rigid–flexible coupling dynamics.
Figures 12 and 13 show the displacement differences of the end-effector between the FFR and FEA models in the X and Y directions, respectively.
As shown in Figures 12 and 13, the FFR and FEA models exhibited the same trends and fluctuated within a certain range. This was because the FFR and FEA models considered the elastic deformation of the flexible spatial links. The maximum fluctuations of both models in the X and Y directions mainly appeared at the peaks of the trajectories. However, compared to the FEA model, the ranges of the FFR model's values in the X and Y directions were −0.008942 to 0.0022 m and −0.00471 to 0.000805 m, respectively.
The displacements of the end-effector for the FFR and FEA models in the Z direction are shown in Figure 14.
As shown in Figure 14, the motion trajectories of the FFR and the ideal rigid-body models both fluctuated within a certain range, and the range of the FFR model was larger than that of the ideal rigid-body model. The floating values in the Z direction were −0.00099 to 0.00125 m.
The comparison of the deviations of the end-effector of the FFR model relative to the FEA model in the X, Y, and Z directions is shown in Figure 15.
As shown in Figure 15, the deviations of the end-effector in the X, Y, and Z directions showed periodic variations. The error fluctuations in the X direction were the largest, followed by those in the Y direction, and the error changes in the Z axis were the smallest. This was related to the relative position of the geometric center of the end-effector and the global coordinate system.
The comparison of the maximum deviations of the motion trajectories of the end-effector of the FFR and FEA models in the X, Y, and Z directions relative to the ideal rigid-body model are shown in Figure 16.
As shown in Figure 16, the maximum deviations of the motion trajectory of the end-effector of the FFR model relative to the ideal rigid-body in the X, Y, and Z direction were larger than those of the FEA model. The deviations of the trajectories between the FFR and FEA models relative to the ideal rigid-body in the X, Y, and Z directions were 0.00372, 0.00015, and 0.000066 m, respectively. This was because the FFR model accounted for the micro-displacement of the end-effector in the dynamic modeling process and strengthened the influence of the flexible spatial link deformation on the dynamic performance of the system by ignoring damping. In addition, the FFR model further considered the nonlinear coupling effects of the rigid links and flexible spatial links. Therefore, the FFR model could more accurately describe the nonlinear deformation of the flexible links and the robotic rigid–flexible coupling effects during the motion, resulting in fluctuations in the trajectory compared to the trajectories of the other two methods.
Compared with an ideal rigid-body model, the FFR and FEA models exhibited a range of fluctuations in the X, Y, and Z directions because they considered flexible deformation of the spatial links, and the results were consistent with actual observations. The peak values of the end-effector were larger for the FFR than those obtained using the FEA model. This occurred because the FFR model considered not only the deformation of the spatial flexible links, but also the nonlinear coupling effects between the rigid and flexible spatial links and the micro-displacement of the end-effector. The FFR model could more accurately describe the influence of the flexible links on the spatial parallel robot. Because the effectiveness of the dynamics equations was verified, this method can be used for the dynamics modeling of other flexible spatial links where the nonlinear coupling effects cannot be neglected.
The work described in this paper was supported by the National Key Research and Development Project (No. 2017YFB1303502), the Tianjin Research Program of Application Foundation and Advanced Technology (No.17JCYBJC18300, No.18JCYBJC87900, and No.17JCQNJC04200), the Tianjin Municipal Education Commission Research Project (Grant No. 2017KJ259 and 2017KJ260), and the National Undergraduate Training Programs for Innovation and Entrepreneurship (No.20181006 0013).
The author(s) declared no potential conflicts of interest with respect to the research, authorship, and/or publication of this article.
Natation
A cross-sectional area
B transformation matrix to convert from local coordinate system to global coordinate system
C constraint equations
E elastic modulus
Fielastic elastic force of flexible link of kinetic chain
Fig elastic force of kinematic chain
G shearing modulus
Ix, Iy, Iz area moments of inertia of spatial flexible link with respect to the local coordinate x, y, and z axes
kf stiffness matrix of flexible spatial link
K stiffness matrix of system
L length
M mass matrix
N shape function
P trajectory of the geometric center point of the end-effector
qf generalized elastic coordinate
q generalized coordinate of kinematic chain in reference system
ˉq generalized coordinate of kinematic chain in global system
ˆq generalized coordinate of system in global system
˙ˆq generalized velocity vector of system in global system
¨ˆq generalized acceleration vector of system in global system
Q generalized external vector
QiF robotic actuated force (torque) of kinetic chain
QiV Coriolis and centrifugal forces
rk position vector of an arbitrary point
r0 position vector of the reference
R transformation matrix
T kinetic energy
um elastic generalized coordinate in global coordinate system
V potential energy
α,β system feedback control parameters
ξ0 undeformed state in the reference system
ξf deformed state in the reference system
θ absolute angle
ε1 displacement constraint stabilization parameters
ε2 velocity constraint parameters
ω angular velocity vector defined in global coordinates
kf=[EAL00000−EAL0000012EIzzL30006EIzzL20−12EIzzL30006EIzzL212EIyyL30−6EIyyL2000−12EIyyL30−6EIyyL20GIPL00000−GIPL004EIyyL0006EIyyL202EIyyL04EIzzL0−6EIzzL20002EIzzLEAL0000012EIzzL3000−6EIzzL212EIyyL306EIyyL20GIPL004EIyyL0Symmetric4EIzzL], |
where G represents the shear modulus of the flexible spatial link, Ip=∫A(y2+z2)dA, Iy=∫Az2dA and Iz=∫Ay2dA
˙ˉq=d([r0θ1θ2...θnum])dt;dqdt=˙ˉq[101010...0100dBθ1dtumdBθ2dtum...dBθndtumB]; |
MO−f=[101010...0100uTm(dBθ1dt)TuTm(dBθ2dt)T...uTm(dBθndt)TBT](Mf−T+Mf−R)⋅ |
[101010...0100(dBθ1dt)um(dBθ2dt)um...(dBθndt)umB]; Ki=[101010...010000...0BT]ki[101010...010000...0B]. |
[1] | S. K. Dwivedy, P. Eberhard, Dynamic analysis of flexible manipulators, a literature review, Mech. Mach. Theory, 41 (2006), 749-777. |
[2] |
S. Yang, Y. Li, Classification and analysis of constraint singularities for parallel mechanisms using differential manifolds, Appl. Math. Model, 77 (2020), 469-477. doi: 10.1016/j.apm.2019.07.040
![]() |
[3] |
B. Lian, T. Sun, Y. Song, Y. Jin, M. Price, Stiffness analysis and experiment of a novel 5-DoF parallel kinematic machine considering gravitational effects, Int. J. Mach. Tools Manuf., 95 (2015), 82-96. doi: 10.1016/j.ijmachtools.2015.04.012
![]() |
[4] |
T. Sun, B. Lian, Y. Song, L. Feng, Elasto-dynamic Optimization of A 5-DoF Parallel Kinematic Machine Considering Parameter Uncertainty, IEEE ASME Trans. Mechatron., 24 (2019), 315-325. doi: 10.1109/TMECH.2019.2891355
![]() |
[5] | T. Sun, S. Yang, B. Lian. Finite and Instantaneous Screw Theory in Robotic Mechanism, Singapore: Springer, 2020. |
[6] |
S. Lu, Y. Li, B. Ding, Kinematics and dynamics analysis of the 3PUS-PRU parallel mechanism module designed for a novel 6-DOF gantry hybrid machine tool, J. Mech. Sci. Technol., 34 (2020), 345-357. doi: 10.1007/s12206-019-1234-9
![]() |
[7] |
T. Sun, B. Lian, Stiffness and mass optimization of parallel kinematic machine, Mech. Mach. Theory, 120 (2018), 73-88. doi: 10.1016/j.mechmachtheory.2017.09.014
![]() |
[8] |
T. Sun, S. Yang, An Approach to Formulate the Hessian Matrix for Dynamic Control of Parallel Robots, IEEE ASME Trans. Mechatron., 24 (2019), 271-281. doi: 10.1109/TMECH.2019.2891297
![]() |
[9] |
T. Sun, B. Lian, S. Yang, Y. Song, Kinematic Calibration of Serial and Parallel Robots Based on Finite and Instantaneous Screw Theory, IEEE Trans. Robot., 36 (2020), 816-834. doi: 10.1109/TRO.2020.2969028
![]() |
[10] |
A. A. Shabana, Finite element incremental approach and exact rigid body inertia, J. Mech. Des., 118 (1996), 171-178. doi: 10.1115/1.2826866
![]() |
[11] |
A. A. Shabana, Definition of the slopes and the finite element absolute nodal coordinate formulation, Multibody Syst. Dyn., 1 (1997), 339-348. doi: 10.1023/A:1009740800463
![]() |
[12] | A. A. Shabana, H. A. Hussien, J. L. Escalona, Application of the absolute nodal coordinate formulation to large rotation and large deformation problems, J. Mech. Des., 120 (1998), 185-195. |
[13] |
A. A. Shabana, R. Y. Yakoub, Three dimensional absolute nodal coordinate formulation for beam elements: theory, J. Mech. Des., 123 (2001), 606-613. doi: 10.1115/1.1410100
![]() |
[14] | A. A. Shabana, G. Wang, Durability analysis and implementation of the floating frame of reference formulation, Proc. Inst. Mech. Eng. Pt. K J. Multi-Body Dyn., 232 (2018), 295-313. |
[15] | A. A. Shabana, Dynamics of multibody systems, 4th ed. New York: Cambridge University Press, 2013. |
[16] | M. Dibold, J. Gerstmayr, H. Irschik, A detailed comparison of the absolute nodal coordinate and the floating frame of reference formulation in deformable multibody systems, J. Comput. Nonlinear Dyn., 4 (2009), 021006. |
[17] |
A. A. Shabana, R. Schwertassek, Equivalence of the floating frame of reference approach and finite element formulations, Int. J. Non Linear Mech., 33 (1998), 417-432. doi: 10.1016/S0020-7462(97)00024-3
![]() |
[18] |
A. A. Shabana, G. Wang, S. Kulkarni, Further investigation on the coupling between the reference and elastic displacements in flexible body dynamics, J. Sound Vib., 427 (2018), 159-177. doi: 10.1016/j.jsv.2018.02.054
![]() |
[19] | U. Lugrís, M. A. Naya, A. Luaces, J. Cuadrado, Efficient calculation of the inertia terms in floating frame of reference formulations for flexible multibody dynamics, Proc. Inst. Mech. Eng. Pt. K J. Multi-Body Dyn., 223 (2009), 147-157. |
[20] |
G. Orzechowski, M. K. Matikainen, A. M. Mikkola, Inertia forces and shape integrals in the floating frame of reference formulation, Nonlinear Dyn., 88 (2017), 1953-1968. doi: 10.1007/s11071-017-3355-y
![]() |
[21] |
M. Berzeri, M. Campanelli, A. A. Shabana, Definition of the elastic forces in the finite-element absolute nodal coordinate formulation and the floating frame of reference formulation, Multibody Syst. Dyn., 5 (2001), 21-54. doi: 10.1023/A:1026465001946
![]() |
[22] | H. Luo, J. Fu, L. Jiao, N. Chen, T. Wu, Rigid-flexible coupled dynamics analysis of 3-revolute-prismatic-spherical parallel robot based on multi-software platform, Adv. Mech. Eng., 11 (2019), 1-12. |
[23] |
Z. Liu, J. Liu, Experimental validation of rigid-flexible coupling dynamic formulation for hub-beam system, Multibody Syst. Dyn., 40 (2017), 303-326. doi: 10.1007/s11044-016-9539-2
![]() |
[24] |
P. Long, W. Khalil, P. Martinet, Dynamic modeling of parallel robots with flexible platforms, Mech. Mach. Theory, 81 (2014), 21-35. doi: 10.1016/j.mechmachtheory.2014.06.009
![]() |
[25] | Q. Zhang, X. Zhang, J. Liang, Dynamic analysis of planar 3-RRR flexible parallel robot, IEEE International Conference on Robotics and Biomimetics, 2012,154-159. |
[26] | L. Sheng, W. Li, Y. Wang, X. Yang, M. Fan, Rigid-flexible coupling dynamic model of a flexible planar parallel robot for modal characteristics research, Adv. Mech. Eng., 11 (2019), 1-10. |
[27] |
J. Liu, K. Pan, Rigid-flexible-thermal coupling dynamic formulation for satellite and plate multibody system, Aerosp. Sci. Technol., 52 (2016), 102-114. doi: 10.1016/j.ast.2016.02.025
![]() |
[28] | S. Z. Liu, J. S. Dai, G. Shen, A. M. Li, G. H. Cao, S. Z. Feng, et al., Dynamic analysis of spatial parallel manipulator with rigid and flexible couplings, J. Cent. South Univ., 24 (2017), 840-853. |
[29] | L. Han, Y. Liu, B. Yang, Y. Q. Zhang, Dynamic modeling and simulation of flexible beam finite rotation with ANCF method and FFR method, Mechanics, 24 (2018), 715-724. |
[30] |
D. Liang, Y. Song, T. Sun, X. Jin, Rigid-flexible coupling dynamic modeling and investigation of a redundantly actuated parallel manipulator with multiple actuation modes, J. Sound Vib., 403 (2017), 129-151. doi: 10.1016/j.jsv.2017.05.022
![]() |
[31] | J. Hu, X. Zhang, D. Zhu, Q. Chen, Dynamic modeling of flexible parallel robot, Trans. Chin. Soc. Agric. Mach., 11 (2011), 208-213. |
[32] | W. Bao, Q. Bai, H. Lu, Vibration Mechanics Foundation and Application of MATLAB, Beijing: Tsinghua University Press, 2015,157-170. |
1. | Zhangping You, Wenhui Zhang, Jinmiao Shen, Yangfan Ye, Xiaoping Ye, Shuhua Zhou, Adaptive neural network vibration suppression control of flexible joints space manipulator based on H∞ theory, 2023, 1392-8716, 10.21595/jve.2022.22797 | |
2. | Xiaozong Song, Xiaorong Wang, Jidong Wang, Haitao Fu, Design and Analysis of an Inverted XY-3RPS Hybrid Mechanism for Polishing of Complex Surface, 2022, 15, 22127976, 422, 10.2174/2212797615666220606094601 | |
3. | Qingyun Zhang, Xinhua Zhao, Inverse Dynamics Modeling and Simulation Analysis of Multi-Flexible-Body Spatial Parallel Manipulators, 2023, 12, 2079-9292, 2038, 10.3390/electronics12092038 | |
4. | Yunxia Wei, Yuanfei Zhang, Bin Hang, Construction and management of smart campus: Anti-disturbance control of flexible manipulator based on PDE modeling, 2023, 20, 1551-0018, 14327, 10.3934/mbe.2023641 | |
5. | Zhang Wenhui, Ma Jing, Ding Shuaibo, Wu Maojun, Yi Dajian, Huang Xiaochen, Chen Rui, 2023, Improved Sliding Mode Variable Structure Control of Robot Manipulators with Flexible Joints based on Singular Perturbation, 979-8-3503-4296-3, 288, 10.1109/ICTEI60496.2023.00084 |
Link | AiBi | BiCi | CiPi | End-effector | Fixed base |
Young's modulus (MPa) | 2.07 × 105 | 2.07 × 105 | 7.17 × 104 | 2.07 × 105 | — |
Density (kg/m3) | 7.8 × 103 | 7.8 × 103 | 2.7 × 103 | 7.8 × 103 | — |
Poisson's ratio | 0.3 | 0.3 | 0.3 | 0.3 | — |
Link | AiBi | BiCi | CiPi | End-effect | Fixed base |
Length (m) | 0.4 | 0.1 | 0.8 | — | — |
Mass (kg) | 2 | 0.3 | — | 1.5 | — |
Radius (m) | 0.01 | 0.01 | 0.01 | 0.1 | 0.4 |
Thickness (m) | — | — | — | 0.02 | 0.15 |
Order | 1~6 | 7 | 8 | 9 | 10 | 11 | 12 |
Frequencies /Hz | 0 | 2.21E-05 | 0.002 | 1.496 | 2.484 | 12.276 | 17.799 |
Axis | Displacement/m | Maximum error/m | |
FFR model | Ideal rigid-body model | ||
X | −0.09623 | −0.08955 | 0.00668 |
Y | −0.00841 | −0.00552 | 0.00289 |
Z | −0.70083 | −0.6981 | 0.00273 |
Link | AiBi | BiCi | CiPi | End-effector | Fixed base |
Young's modulus (MPa) | 2.07 × 105 | 2.07 × 105 | 7.17 × 104 | 2.07 × 105 | — |
Density (kg/m3) | 7.8 × 103 | 7.8 × 103 | 2.7 × 103 | 7.8 × 103 | — |
Poisson's ratio | 0.3 | 0.3 | 0.3 | 0.3 | — |
Link | AiBi | BiCi | CiPi | End-effect | Fixed base |
Length (m) | 0.4 | 0.1 | 0.8 | — | — |
Mass (kg) | 2 | 0.3 | — | 1.5 | — |
Radius (m) | 0.01 | 0.01 | 0.01 | 0.1 | 0.4 |
Thickness (m) | — | — | — | 0.02 | 0.15 |
Order | 1~6 | 7 | 8 | 9 | 10 | 11 | 12 |
Frequencies /Hz | 0 | 2.21E-05 | 0.002 | 1.496 | 2.484 | 12.276 | 17.799 |
Axis | Displacement/m | Maximum error/m | |
FFR model | Ideal rigid-body model | ||
X | −0.09623 | −0.08955 | 0.00668 |
Y | −0.00841 | −0.00552 | 0.00289 |
Z | −0.70083 | −0.6981 | 0.00273 |