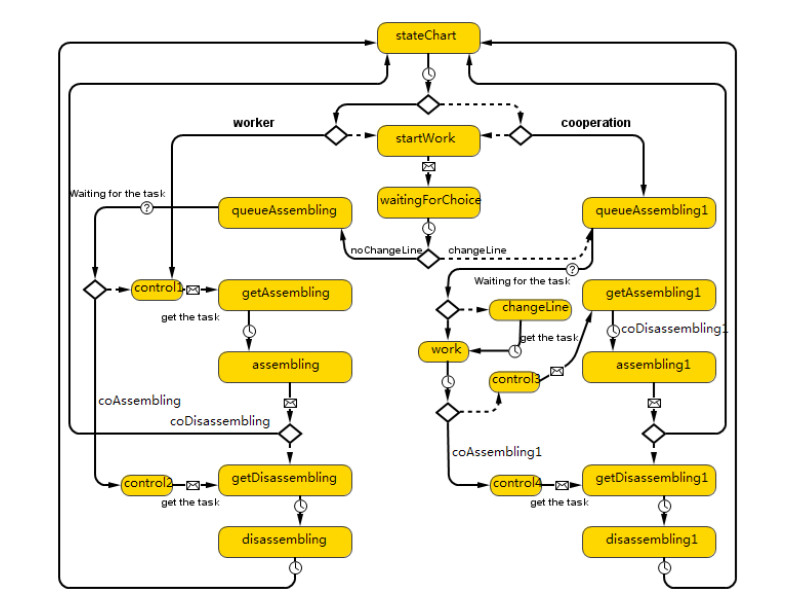
Citation: Dawei Ren, Xiaodong Zhang, Shaojuan Lei, Zehua Bi. Research on flexibility of production system based on hybrid modeling and simulation[J]. Mathematical Biosciences and Engineering, 2021, 18(1): 933-949. doi: 10.3934/mbe.2021049
[1] | YoungSu Yun, Mitsuo Gen, Tserengotov Nomin Erdene . Applying GA-PSO-TLBO approach to engineering optimization problems. Mathematical Biosciences and Engineering, 2023, 20(1): 552-571. doi: 10.3934/mbe.2023025 |
[2] | Raj Kumar Bachar, Shaktipada Bhuniya, Santanu Kumar Ghosh, Ali AlArjani, Elawady Attia, Md. Sharif Uddin, Biswajit Sarkar . Product outsourcing policy for a sustainable flexible manufacturing system with reworking and green investment. Mathematical Biosciences and Engineering, 2023, 20(1): 1376-1401. doi: 10.3934/mbe.2023062 |
[3] | Xiaodong Zhang, Dawei Ren . Modeling and simulation of task rescheduling strategy with resource substitution in cloud manufacturing. Mathematical Biosciences and Engineering, 2023, 20(2): 3120-3145. doi: 10.3934/mbe.2023147 |
[4] | M. E. Bakr, Abdulhakim A. Al-Babtain, Zafar Mahmood, R. A. Aldallal, Saima Khan Khosa, M. M. Abd El-Raouf, Eslam Hussam, Ahmed M. Gemeay . Statistical modelling for a new family of generalized distributions with real data applications. Mathematical Biosciences and Engineering, 2022, 19(9): 8705-8740. doi: 10.3934/mbe.2022404 |
[5] | Tongyu Wang, Yadong Chen . Event-triggered control of flexible manipulator constraint system modeled by PDE. Mathematical Biosciences and Engineering, 2023, 20(6): 10043-10062. doi: 10.3934/mbe.2023441 |
[6] | Qingyun Zhang, Xinhua Zhao, Liang Liu, Tengda Dai . Dynamics analysis of spatial parallel robot with rigid and flexible links. Mathematical Biosciences and Engineering, 2020, 17(6): 7101-7129. doi: 10.3934/mbe.2020365 |
[7] | Mitali Sarkar, Yong Won Seo . Biodegradable waste to renewable energy conversion under a sustainable energy supply chain management. Mathematical Biosciences and Engineering, 2023, 20(4): 6993-7019. doi: 10.3934/mbe.2023302 |
[8] | Walid Emam, Ghadah Alomani . Predictive modeling of reliability engineering data using a new version of the flexible Weibull model. Mathematical Biosciences and Engineering, 2023, 20(6): 9948-9964. doi: 10.3934/mbe.2023436 |
[9] | Guohui Zhang, Jinghe Sun, Xing Liu, Guodong Wang, Yangyang Yang . Solving flexible job shop scheduling problems with transportation time based on improved genetic algorithm. Mathematical Biosciences and Engineering, 2019, 16(3): 1334-1347. doi: 10.3934/mbe.2019065 |
[10] | Christopher DuBois, Jesse Farnham, Eric Aaron, Ami Radunskaya . A multiple time-scale computational model of a tumor and its micro environment. Mathematical Biosciences and Engineering, 2013, 10(1): 121-150. doi: 10.3934/mbe.2013.10.121 |
In recent years, with the diversification of product demand and the intensification of global market competition, various advanced manufacturing models have been continuously updated. A large number of production experiments and practices show that personnel flexibility has an important impact on the efficiency and flexibility of the production system. Therefore, the evaluation and optimization of the flexibility of the production system and personnel factors, as well as the problems related to the deployment of personnel with multiple skill levels are gradually becoming a hot spot in the operation and management of the current production system [1].
Personnel flexibility. With the continuous attention of production enterprises to the flexibility of the production system, scholars have conducted extensive research from the perspectives on the mechanism of action, internal elements, and personnel skills. Qin et al. [2], Yu et al. [3] and Gürsel et al. [4] show that system's flexibility usually refers to the multi-skill level and stability of system. In an unrestricted model (no restrictions on the number of personnel and settings), using diverse and decentralized settings to reduce the number of personnel could reduce system fluctuations and improve system efficiency. Gokhan et al. [5] presented a method of hierarchical approach allowing decision makers to perform manpower level determination, cell loading and individual worker assignment with respect to the desired risk level. Evans [6] presented a developed conceptual framework, which integrates the temporal and intentional dimensions of flexibility. This theory has been supported by studies such as Xu et al. [7], Metin [8] and Omogbai et al. [9], who used hybrid model which employs analytic network process together. This model was proposed for the personnel selection problem. Malhotra et al. [10] and Denkena et al. [11] argued that the greatest benefits could be achieved when inter‐departmental worker flexibility is incrementally introduced into the system. The study of worker flexibility has sparked interest among scholars, such as Darwin et al. [12], Cyrille et al. [13] and Aicha et al. [14]. In recent years, scholars have found that more extensive worker cross training significantly enhanced the shop performance and solved this dynamic multi-skilled workers assignment problem using a new methodology. In the real-life production process, the external environment and internal configuration such as order arrival order, interval, original quality defects, personnel skills, personnel allocation etc. have been dynamically changed. Although the above researches discuss the impact of human factors on production performance, it ignored the fluctuations in the external environment of the production system and did not consider the influence of personnel flexibility on the flexibility of the production system. According to the characteristics of personnel flexibility and the real-life production situation, this paper studies the influence of personnel flexibility on the flexibility of the production system in the case of fluctuations in the external environment and changes in internal factors.
Evaluation index. Based on the understanding of the flexibility of the production system, many studies have tried to quantitatively analyze the flexibility of the system, and believed there is no global accepted, operational and useful measures of organizational flexibility. Phillips et al. [15] showed that there was no accepted, operational, and useful measures of organizational flexibility. Discussion indicated how a flexibility model could complement DEA studies to round out the characterization of performance. More recently, Rao [16], Yue et al. [17] and Nembhard et al. [18] also found support for this flexibility model. The selected flexibility measures could quantify flexibility and eventually integrated it into the change management processes of manufacturing organizations. This theory has been supported by studies such as Georgoulias et al. [19], Singh et al. [20] and Naderi et al. [21], who used flexible manufacturing system selection index and flexibility measures defined and indicators generally associated respectively. Factors like partly mix, layout type, batching condition, the system performance in terms of productivity, system utilization rate, and cycle time was analyzed [22]. While the processing capability was represented as the number of operations that the machines could perform, the manufacturing capacity was modelled as the efficiency of different machines [23]. Wahab et al. [24] found support for this method using time and cost to measure the flexible of machines. Kemmoe et al. [25], Mishra [26], F. Long et al. [27] and Mishra et al. [28] also reported evidences for this conclusion employing different methodologies such as two-step Mix Integer, analytical hierarchy process (AHP) and ideal solution (TOPSIS). Analyzing the availability of flexible production systems in Industry 4.0 aims to reduce the risks of unexpected machine failure and thus resulting losses, and subsequently to support the optimization of production systems [27]. The above researches all measured the flexibility index value of the production system from various indicators with a variety of mathematical methods, such as integer programming, linear programming, etc. But the measurement dimensions and angles are not enough, the programming issues are mainly considered instead.
However, the human factor is not taken as the initiative factors that leading to the idealization of the experimental results. This paper quantitatively evaluates the flexibility index value of the production system by the machine utilization, personnel utilization, production and personnel production efficiency. The experimental results are more in line with the real-life production situation.
Simulation model. Combining with the real-life production process, more and more researches regarde internal factors as the main factor affecting the flexibility of the production system and built production simulation models to simulate real-life production. The discrete event simulation model permits one to take into account all the working constraints: the maximal number of jobs simultaneously allowed in the system [29]. Many authors have supported this theory including Kia et al. [30], Lennartson et al. [31] and more recently Antonelli et al. [32] and Ehsan et al. [33], who used RMS and real data to obtain approaches respectively. The structure of the production system was simulated by discrete events, this mothed was also supported in the short run [34]. In a dynamic environment, the product mix and part demands are varying during a multi-period planning horizon. To address these limitations, a modular hybrid simulation framework for complex manufacturing system design was presented. Many authors have supported this theory including Lin et al. [35] and Pawel et al. [36]. Barenji et al. [37], who proposed an indirect coordination mechanism based on ant colony intelligence aiming to improve the self-organization and processing time of the system. Zhang et al. [38] proposed a multi-agent-based collaborative virtual manufacturing environment (VME) to save energy consumption and improve efficiency in the manufacturing process. In order to achieve the high autonomy of the manufacturing system, a multi-agent system (MAS) is designed to build a collaborative VME. The problem with most discrete event modeling methods currently used is that people are regarded as a manufacturing resource with relatively simple attributes and cannot fully support the modeling of human behavior. Based on the above problems, this paper establishes a hybrid model of human-machine cooperation in a fluctuating environment, which simulates the production process of the production system more reasonably.
This paper takes the production system of a certain motorcycle engine parts as the research target and studies the influence of personnel flexibility, which is the main factor of the production system flexibility. First of all, the four dimensions of production system, machine utilization, personnel utilization, production and personnel efficiency, are used as the evaluation indexes of the flexibility of the production system and a method for calculating the comprehensive flexibility index of the production system is proposed. Secondly, a hybrid modeling method is proposed, which can not only realize the description and operation of the manufacturing process, but also define and model the attributes and behavior of personnel more abundantly. Finally, based on Anylogic software, the construction and operation of the simulation model are realized, the multi-programme comparative study of personnel flexibility is carried out and the influence mechanism of personnel flexibility on the overall flexibility of the production system is analyzed.
The research innovations of this article are as follows. From the perspective of research methods, this article describes the production process by constructing a hybrid model. From the perspective of research issues, this paper innovatively applies the man-machine collaborative hybrid modeling method to the production of motorcycle engine parts. This not only enriches the research methods of intelligent manufacturing, but also studies the influence law of personnel and system flexibility, which provides guidance for intelligent manufacturing.
The content of this paper is arranged as follows. Section 2 gives the calculation method of production system flexibility; Section 3 proposes the construction method and implementation process of the hybrid model of production system; Section4 gives the parameters design and running results of the multi-programme comparison simulation experiment and discusses the results in detail; Section5 gives the conclusions and recommendations of this paper.
This paper defines the production system flexibility [39] as "the adaptability of the production system under fluctuations in the manufacturing environment". The fluctuations in the manufacturing environment are defined as the degree of change in the internal and external conditions of the production environment. Facing fluctuations in the manufacturing environment, if the personnel elements of the production system can adapt to environmental fluctuations and reduce the impact caused by changes in the manufacturing environment, the flexibility of the production system will be higher, and vice versa. In the production system, personnel flexibility is the main factor of system flexibility fluctuations. Based on the above definition of the flexibility of production system, the connotations of personnel elements, environmental fluctuations and flexibility measurement are given below.
1) Personnel elements
The internal elements of the production system are listed as organizational structure, personnel division, and personnel behavior. These three aspects affect system flexibility respectively. Organizational structure refers to the settings among the various production levels in the production system. The division of labor refers to the allocation of personnel according to the types of production and operating machines. The personnel behavior refers to the control, training, collaboration, and decision-making mechanisms among personnel. Internal factors are the basic factors that affect the flexibility of the system, and they are also important issues that need to be studied in the production system.
2) Environmental fluctuations
The diversity of production order types, time changes in order requirements and production material defects reflect the external fluctuations of the production system caused by changes in external conditions. Machine failures, production abnormalities, personnel errors, etc. reflect internal fluctuations in the production system caused by changes in internal factors. In the production, external and internal fluctuations will directly affect the performance of system production.
3) Flexible measurement
For a production system, the lower the impact of environmental fluctuations on the performance of the production system is, the higher the flexible of the production system is. In most production systems, system performance includes machine utilization, personnel utilization, production and personnel production efficiency. Therefore, the flexibility of the production system can be measured by the changes in production performance under different fluctuating environments.
Based on the above definition, all environmental fluctuations are divided into three levels in order to measure system flexibility indicators: small fluctuations, medium fluctuations and large fluctuations. The fluctuation value of each performance indicators can be calculated by the standard deviation of each performance indicator in three fluctuation environments, and the performance fluctuation indicator value of the system (the sum of fluctuations in the system) is calculated by the weight of the standard deviation of each indicator. The following describes the specific calculation process of system flexibility.
1) This paper uses the number of failures, the rate of human error, the rate of material defect and the total number of line changes to describe environmental fluctuations and makes random process statistics on the production results. Record the probability of environmental fluctuation as a_k, and the fluctuation level of the manufacturing environment is represented by an integer k (k = 1, 2, 3). When k = 1, the degree of fluctuation in the manufacturing environment is small, that is small fluctuations; When k = 2, the degree of fluctuation in the manufacturing environment is too large, that is medium fluctuations; When k = 3, the degree of fluctuation in the manufacturing environment is the most, that is large fluctuations.
2) Calculate machine utilization fluctuations, personnel utilization fluctuations production fluctuations and personnel production efficiency fluctuations of the production system under three fluctuation environments respectively. The calculation process is as follows:
Ykjs=Ykj∑nj=1Ykj,j=1, 2,…,n, | (1) |
where Ykj is standardize the sum of production of the j-th production batch in fluctuating environment of k, n is the production batch of the production system during the evaluation period, and the standard deviation of ykjs (the standardized sum of ykj) is used to express the fluctuation of production σky.
① Production fluctuations σkY:
σkY=√∑nj=1(Ykjs−1n∑nj=1Ykjs)2n−1, | (2) |
When the fluctuation environment is k, where ykjs is the production index value of the standardized sum of production ykj under a fluctuating environment of k. Calculate the Production fluctuations index value σky by the standard deviation of ykjs.
Ujs=TkjvTkjt,j=1, 2,…,N, | (3) |
where N is the number of machines, Tkjv is the effective running time of the j-th machine and Tkjt is the total running time of the j-th machine in fluctuating environment of k.
② Fluctuations in machine utilization σkU:
σkU=√∑Nj=1(Ukjs−1N∑Nj=1Ukjs)2N−1, | (4) |
where Ukjs is the utilization rate of the j-th machine in fluctuating environment of k. The machine utilization fluctuation index value σkU is calculated by the standard deviation of Ujs.
Pkjs=TkjpTkjh, | (5) |
where Pkjs is the utilization rate of the j-th person in fluctuating environment of k.
③ Staff utilization fluctuation σkP:
σkP=√∑Wj=1(Pkjs−1W∑Wj=1Pkjs)2W−1, | (6) |
where W is the number of personnel, TkjP is the effective working time of the j-th person and Tkjh is the total working time of the j-th person in fluctuating environment of k. Calculate the personnel utilization fluctuation index value σkP by the standard deviation of Pkjs.
CkijP=TkijpQkijP,Ckijs=∑Pi=1Tkijp∑Pi=1QkijP,i=1, 2,…,P, | (7) |
where P is the number of personnel, TkijP is the total working time of the i-th person, Qkijp is the total production number of the first person in fluctuating environment of k.
④ Staff productivity fluctuation σkT:
σkT=√∑Mj=1[∑Pi=1(1Ckijs−1CkijP)2]P(M−1),j=1, 2,…,M, | (8) |
where M is the production batch of the production system during the evaluation period, CkijP is the production cycle of the i-th person in a fluctuating environment of k and Ckijs is the production cycle of the production system in fluctuating environment of k.
3) Combine the above four performance index values, take the weight coefficients of the four fluctuation index values as ω1,ω2,ω3 and ω4 respectively and calculate the comprehensive performance value:
FLk=ω1σkY+ω2σkU+ω3σkP+ω4σkT, | (9) |
4) Count the probability of k-level fluctuations and calculate the comprehensive fluctuation index of the fluctuation value of the performance indicator respectively:
FL=P1FL1+P2FL2+P3FL3, | (10) |
where P1, P2 and P3 are the probability of fluctuation.
5) According to the production system flexibility defined in section 2.1, it can be seen that under the fluctuating environment of production, the higher the performance index of the system fluctuation is, the worse the stability and flexibility of production system are. The comprehensive flexibility calculation index is defined as follows:
OF=1−FL, | (11) |
In order to realize dynamic configuration and organizational optimization of personnel flexibility, this paper adopts hybrid modeling method to simulate all possible fluctuations in real-life production according to different orders and machines as well as different personnel skills. In addition, this paper evaluates and calculates the index value of system flexibility by collecting and analyzing simulation data.
As shown in Figure 1, in the hybrid modeling simulation model, discrete events are used to simulate the manufacturing process in the production system, and multi-agent simulation is used to simulate the behavior of operators in the production system. Then the two models are integrated into a human-machine collaboration hybrid model. The operation process of the hybrid modeling simulation model of human-machine interaction is as follows: The information of the production states in the discrete production simulation model is transmitted to the receiver of the agent model, and the agent model makes corresponding behaviors based on the agent modeling settings, such as coordinated assembling, changing line, detection and other agent behaviors. Then transfer the information to the discrete production model through the connector so as to realize the production process of man-machine coordinated interconnection.
Construction method of personnel agent model: The personnel agent model is constructed using a statechart-based method. Since Anylogic supports a mixed method of discrete events and agents for modeling and has built-in a wealth of plug-in libraries as well as agent communication and movement methods, this paper chooses Anylogic to build production process model and uses java language for secondary development. The internal personnel model is shown in worker of Figure 1.
Construction method of machine agent model: The machine detects the processing status of the workpiece and the process of co-production with the personnel who can be regarded as being driven by discrete events. This paper uses the built-in process modeling library in Anylogic software to complete the construction of the machine agent model. The internal discrete event model is shown in machine of Figure 1. Thus, the hybrid simulation of production system with man-machine interconnection is realized.
In order to verify the proposed simulation evaluation method for the manufacturing system flexibility, this paper takes the manufacturing of XT, GT and K40, the key components of motorcycle engine, as the research background and conducts a case study of the influence of personnel flexibility on the flexibility of the production system.
The production system has multi-frequency production product type switching, order diversity, machine failure rate and personnel error rate fluctuations. It is a typical multi-variety small-batch production system model in a multi-variable environment. The production system consists of 8 processing machines (the number M1–M8) and 6 operators (the numberOP1–OP6), the processing route of part type XT is M1→M2→M3→M4→M5, the processing route of part type GT is M6→M7→M8, the processing route of part type K40 is M2→M4 or independent processing by M7.
In the production system, the skill distribution of personnel operating machine is 0–10. However, 0 indicates that the operator does not master the operational skills of the machine, 10 indicates that the operator masters the personnel skills of the machine and can operate it skillfully. Operators can operate the machine independently with skills of 6 or above. The skill level of [6,7] indicates that the personnel basically master the operation of the machine. The skill level [8,9] indicates that the personnel completely have mastery of the operation of the machine. The skills below 6 indicate that the operator is in a learning state and cannot operate the machine independently, but can cooperate with other operators to complete relevant operations of the machine. According to the real-life situation of the production system, the skills of the operators can be divided into 5 levels. The higher the skill levels of operators are, the greater the proficiency of operating the machine is; the higher the work efficiency is and the shorter the processing time will be. The distribution of operators-machine skills is shown in Table 1.
Machine | Programme A operators Distribution of machine skill | Programme B operators Distribution of machine skil | ||||||||||
Op1 | Op2 | Op3 | Op4 | Op5 | Op6 | Op1 | Op2 | Op3 | Op4 | Op5 | Op6 | |
M1 | 8 | 0 | 0 | 0 | 0 | 10 | 8 | 3 | 0 | 0 | 0 | 10 |
M2 | 9 | 0 | 0 | 0 | 0 | 7 | 9 | 5 | 0 | 9 | 0 | 7 |
M3 | 0 | 8 | 0 | 0 | 0 | 9 | 6 | 8 | 6 | 3 | 0 | 9 |
M4 | 0 | 8 | 0 | 0 | 0 | 7 | 5 | 8 | 6 | 7 | 4 | 7 |
M5 | 0 | 0 | 8 | 0 | 0 | 9 | 0 | 7 | 9 | 0 | 5 | 9 |
M6 | 0 | 0 | 0 | 8 | 0 | 9 | 0 | 7 | 7 | 8 | 5 | 9 |
M7 | 0 | 0 | 0 | 7 | 0 | 10 | 6 | 0 | 4 | 8 | 9 | 10 |
M8 | 0 | 0 | 0 | 0 | 8 | 8 | 0 | 0 | 4 | 7 | 8 | 8 |
In the above table, the production system in programme A experiment adopts team specialization, operator OP1 is responsible for operating machine M1 and M2; OP2 is responsible for operating machine M3 and M4; OP3 is responsible for operating machine M5; OP4 is responsible for operating machine M6 and M7, OP5 is responsible for operating machine M8. As a multi-functional worker, OP6 has the skills to operate all machines, cooperates with other operators to the procedure of assembling, changing line, processing and other operations. Although the personnel in project A are highly skilled and can operate the relevant machines independently, the operation of the machines and the manufacturing of the production are single.
In the above table, the operators of production system in programme B experiment are all multi-functional workers, and the operator OP1 is responsible for operating 5 machines (M1–M4, M7); OP2 is responsible for operating 6 machines (M1–M6); OP3 is responsible for operating 6 machines (M3–M8); OP4 is responsible for operating 6 machines (M2–M4, M6–M8); OP5 is responsible for operating 5 machines (M4–M8). As a multi-functional worker, OP6 has the skills to operate all machines. Although the personnel of programme B are less skilled, they can operate more machines. In other words, they can operate some related machines independently and flexibly complete the collaborative works such as assembling, changing line and disassembling. According to the order of tasks and emergency situations, work can be effectively configured, with high personnel flexibility.
Through the real-life investigation and statistical analysis, the environmental fluctuation of the production system is mainly from four aspects: the number of machine failures, the quality defect rate of raw materials, the operation error rate of personnel and the number of changing line. These four types of fluctuations are set as follows in the simulation model of hybrid modeling:
1) Machine failure: The initial time of machine failure obeys uniform distribution, and the interval of failure time obeys exponential distribution. In the simulation model of hybrid modeling, the uniform (0, a, 0) and exponential (0, b, 0) are used to simulate the initial time and time interval of machine failure respectively, the variation of machine fault fluctuation is controlled by adjusting the numerical values of a and b.
2) Material defect: According to the real-life production situation, the occurrence of material defects is tested with a certain probability. If the occurrence of material defects increases the inspection time, the material is returned for repair and reproduction.
3) Personnel error: The personnel error in the production system is mainly reflected in the reliability of the operating machine. The error rate of personnel is set through the parameters of the agent model. The occurrence of personnel errors will increase additional production time and failure numbers.
4) Change line: Due to the characteristics of small batch and many types of products, the production system needs to change lines many times. When the XT product type is switched to K40 or GT is switched to K40 production, the production of related machines must be temporarily suspended, the processing tools of the machine (M2, M4 or M7) can be replaced before the beginning of production again.
The simulation model of hybrid modeling sets the number of changing lines by the variation frequency of the order type. The environment fluctuation in the simulation model is listed as three levels according to the statistics of real-life production, as shown in Table 2.
Fluctuating environment | Failure number/n | Error rate of worker/% | Defect rate of material/% | Change line number/n | Fluctuating probability/% |
Light fluctuation | 1–10 | 1 | 1 | 1–10 | 15 |
Medium fluctuation | 10–30 | 2 | 4 | 10–25 | 50 |
Huge fluctuation | 30–60 | 4 | 7 | 25–50 | 35 |
The statistical analysis of the data generated in the production system shows that the probabilities of small fluctuation, medium fluctuation and large fluctuation are 15, 50, and 35% respectively. Therefore, in the simulation experiment, the probability of environmental fluctuation is set to a1 = 0.15, a2 = 0.5 and a3 = 0.35 respectively, the weights(ω1, ω2, ω3, ω4) of flexible performance index of production system are set to 0.25.
Each simulation experiment is set to run for 3 months, with operators working for 8 hours a day. The real-life working time of the model in each cycle is 720 hours, the simulation is carried out for 30 times.
From Table 3, when the environmental fluctuations of programme A are small fluctuations, the changes in the fluctuation index values are small: especially the fluctuation range of the production fluctuation index values is the smallest. When the environmental fluctuation range increases, the comprehensive fluctuation index value increases from 0.043 with small fluctuations to 0.094 with medium fluctuations, and then to 0.302 with large fluctuations.
Period | Light fluctuation (a1=0.5) | Medium fluctuation (a2=0.5) | Huge fluctuation (a3=0.5) | |||||||||||||
Programme A/B | Fluctuating utilization of machine ω1=0.25 | Fluctuating utilization of worker ω2=0.25 | Fluctuating production ω3=0.25 | Fluctuating efficiency of worker ω4=0.25 | Performance indicator (FL1) | Fluctuating utilization of machine ω1=0.25 | Fluctuating utilization of worker ω2=0.25 | Fluctuating production ω3=0.25 | Fluctuating efficiency of worker ω4=0.25 | Performance indicator (FL2) | Fluctuating utilization of machine ω1=0.25 | Fluctuating utilization of worker ω2=0.25 | Fluctuating production ω3=0.25 | Fluctuating efficiency of worker ω4=0.25 | Performance indicator (FL3) | |
A | 1 | 0.058 0.053 0.054 0.05 0.059 0.057 0.053 0.057 0.054 0.056 0.055 |
0.079 0.085 0.08 0.079 0.08 0.074 0.082 0.078 0.081 0.077 0.08 |
0.027 0.032 0.029 0.025 0.029 0.03 0.032 0.033 0.027 0.029 0.029 |
0.005 0.005 0.007 0.003 0.007 0.005 0.007 0.007 0.005 0.005 0.006 |
0.042 0.044 0.043 0.039 0.044 0.042 0.044 0.044 0.042 0.042 0.043 |
0.125 0.136 0.137 0.105 0.123 0.125 0.102 0.104 0.106 0.138 0.12 |
0.135 0.126 0.159 0.118 0.151 0.115 0.157 0.146 0.155 0.138 0.14 |
0.087 0.119 0.11 0.069 0.108 0.082 0.094 0.098 0.12 0.081 0.097 |
0.02 0.018 0.021 0.019 0.018 0.019 0.016 0.021 0.018 0.019 0.019 |
0.092 0.1 0.107 0.078 0.1 0.085 0.092 0.092 0.1 0.094 0.094 |
0.377 0.483 0.458 0.546 0.232 0.611 0.462 0.507 0.407 0.557 0.464 |
0.337 0.568 0.447 0.242 0.437 0.411 0.461 0.262 0.237 0.367 0.377 |
0.461 0.316 0.454 0.371 0.267 0.334 0.232 0.272 0.403 0.361 0.347 |
0.021 0.022 0.019 0.019 0.023 0.023 0.021 0.023 0.021 0.022 0.021 |
0.299 0.347 0.345 0.295 0.24 0.345 0.294 0.266 0.267 0.327 0.302 |
2 | ||||||||||||||||
3 | ||||||||||||||||
4 | ||||||||||||||||
5 | ||||||||||||||||
6 | ||||||||||||||||
7 | ||||||||||||||||
8 | ||||||||||||||||
9 | ||||||||||||||||
10 | ||||||||||||||||
Average | ||||||||||||||||
B | 1 | 0.034 0.036 0.036 0.031 0.032 0.034 0.03 0.033 0.035 0.036 0.034 |
0.024 0.028 0.027 0.021 0.03 0.028 0.026 0.022 0.025 0.026 0.026 |
0.017 0.015 0.016 0.022 0.014 0.014 0.011 0.016 0.019 0.014 0.016 |
0.005 0.003 0.006 0.004 0.003 0.004 0.001 0.006 0.004 0.002 0.004 |
0.02 0.021 0.021 0.02 0.02 0.02 0.017 0.019 0.021 0.02 0.02 |
0.077 0.07 0.074 0.086 0.068 0.058 0.069 0.074 0.071 0.082 0.073 |
0.062 0.063 0.055 0.064 0.071 0.052 0.062 0.052 0.067 0.051 0.06 |
0.048 0.047 0.036 0.039 0.056 0.054 0.04 0.047 0.044 0.041 0.045 |
0.004 0.004 0.006 0.002 0.006 0.006 0.004 0.006 0.004 0.006 0.005 |
0.048 0.046 0.043 0.048 0.05 0.043 0.044 0.045 0.047 0.045 0.046 |
0.251 0.352 0.302 0.314 0.253 0.303 0.38 0.39 0.405 0.299 0.325 |
0.208 0.281 0.397 0.279 0.302 0.3 0.217 0.258 0.221 0.258 0.272 |
0.309 0.19 0.239 0.301 0.282 0.123 0.333 0.221 0.302 0.229 0.253 |
0.009 0.011 0.011 0.002 0.003 0.017 0.011 0.012 0.013 0.017 0.011 |
0.194 0.209 0.237 0.224 0.21 0.186 0.235 0.22 0.235 0.201 0.215 |
2 | ||||||||||||||||
3 | ||||||||||||||||
4 | ||||||||||||||||
5 | ||||||||||||||||
6 | ||||||||||||||||
7 | ||||||||||||||||
8 | ||||||||||||||||
9 | ||||||||||||||||
10 | ||||||||||||||||
Average | ||||||||||||||||
Fluctuating indicator(ProgrammeA)=0.159 | Calculation index of organizational flexibility(ProgrammeA)=0.841 | |||||||||||||||
Fluctuating indicator(ProgrammeB)=0.101 | Calculation index of organizational flexibility(ProgrammeB)=0.899 |
The reason why the fluctuation index value increases significantly is due to the professional division of programme A where the large number of operators operate single machine. When the environment fluctuation is high, the personnel flexibility will be greatly affected, the adaptability of production system will be poor and the flexibility will be low. Combining the fluctuation value of each environmental fluctuation level, the flexibility index value of programme A is calculated by Eq (11) to be 0.841.
Under the condition that the fluctuation level of the production environment is constant, the simulation model is run repeatedly. The performance index value of programme B can be obtained from 0.02 with small fluctuations to 0.046 with medium fluctuations and then to 0.215 with large fluctuations. Combining the fluctuation value of each environmental fluctuation level, the flexibility index value of programme B is calculated by Eq (11) to be 0.899.
The operators of programme B are all multi-functional workers who can process a variety of products and operate multiple machines. Compared with programme A, the fluctuation index value of programme B has a smaller increase, the production system is more flexible and the flexibility index of 5.8% is improved overall.
In order to further study the law of the influence of two internal factor configurations on the production system's flexibility, the average value of each fluctuating performance index is compared. This paper uses paired T-test to detect the difference of each index value and obtains the flexible comparison result of programme A and programme B.
Based on the analysis of the results in Figure 2 and Table 4, when the environmental fluctuations in production are medium and large fluctuations, the fluctuation index values of programme B are all smaller than those of programme A. It shows that the production system under programme B is more stable and flexible at this time. Only when the environmental fluctuations are small fluctuations will there be no obvious difference among the fluctuations in machine utilization, personnel utilization, production and personnel efficiency under the two programmes. But there are still differences in personnel utilization fluctuations, which indicate that the production flexibility of multi-skilled workers is much higher than that of professional skilled workers.
Evaluation index | Null hypothesis | Programme | Average (standard deviation) | Simulation number | Student's test | Test result | Conclusion | |
k=1 | Fluctuating utilization of machine | σ1AU=σ1BU | A | 0.055(0.003) | 10 | 19.823(df=9) | Reject | σ1AU>σ1BU |
B | 0.034(0.002) | |||||||
Fluctuating utilization of worker | σ1AP=σ1BP | A | 0.08(0.003) | 10 | 42.865(df=9) | Reject | σ1AP>σ1BP | |
B | 0.026(0.003) | |||||||
Fluctuating production | σ1AY=σ1BY | A | 0.029(0.002) | 10 | 7.77(df=9) | Reject | σ1AY>σ1BY | |
B | 0.016(0.002) | |||||||
Fluctuating efficiency of worker | σ1AT=σ1BT | A | 0.006(0.001) | 10 | 0.654(df=9) | Not reject | Uncertain | |
B | 0.004(0.001) | |||||||
k=2 | Fluctuating utilization of machine | σ2AU=σ2BU | A | 0.12(0.014) | 10 | 8.37(df=9) | Reject | σ2AU>σ2BU |
B | 0.073(0.007) | |||||||
Fluctuating utilization of worker | σ2AP=σ2BP | A | 0.14(0.015) | 10 | 14.676(df=9) | Reject | σ2AP>σ2BP | |
B | 0.06(0.007) | |||||||
Fluctuating production | σ2AY=σ2BY | A | 0.097(0.016) | 10 | 8.72(df=9) | Reject | σ2AY>σ2BY | |
B | 0.045(0.006) | |||||||
Fluctuating efficiency of worker | σ2AT=σ2BT | A | 0.019(0.002) | 10 | 25.431(df=9) | Reject | σ2AT>σ2BT | |
B | 0.005(0.001) | |||||||
k=3 | Fluctuating utilization of machine | σ3AU=σ3BU | A | 0.464(0.102) | 10 | 3.959(df=9) | Reject | σ3AU>σ3BU |
B | 0.325(0.052) | |||||||
Fluctuating utilization of worker | σ3AP=σ3BP | A | 0.377(0.103) | 10 | 3.056(df=9) | Reject | σ3AP>σ3BP | |
B | 0.272(0.053) | |||||||
Fluctuating production | σ3AY=σ3BY | A | 0.347(0.074) | 10 | 2.882(df=9) | Reject | σ3AY>σ3BY | |
B | 0.253(0.061) | |||||||
Fluctuating efficiency of worker | σ3AT=σ3BT | A | 0.021(0.001) | 10 | 6.915(df=9) | Reject | σ3AT>σ3BT | |
B | 0.011(0.001) |
From Figure 3, when the environmental fluctuation increases, all the fluctuation index values under the two programmes show an increasing trend, but the variation range of all the fluctuation index values under programme A is obviously greater than that under programme B.
Comprehensive experimental results show that when the environment of the production system fluctuates slightly, there is no need to reconfigure the specialized production system. If the environment fluctuates greatly, the production system should be configured and reorganized in time to better adapt to the changing production environment.
In order to study the influence of the personnel flexibility on production system flexibility in fluctuating manufacturing environment, this paper investigates the definition and calculation method of the production system flexibility, and puts forward a simulation research method based on mixed modeling. In the production process of the key parts of a motorcycle engine, the simulation experiment of production flexibility under three kinds of environment fluctuation and two kinds of personnel flexibility scheme is designed and completed.
The study showed that the hybrid modeling simulation method can not only reflect the discrete characteristics of the production process, but also reflect the attributes and behaviors of the personnel in the production system. In addition, this method can effectively support the research on the influence of personnel flexibility, which is on the flexibility of the production system. The simulation results show that with the improvement of the diversity of personnel skills, the flexibility of the production system is significantly improved, and the ability of the system to deal with environmental fluctuations is obviously enhanced. However, when the dynamic manufacturing environment is controlled within a small fluctuation range, the change of production system flexibility brought by different personnel flexibility is not obvious. This shows that the production team is not always necessary. In the case of small fluctuations in the manufacturing environment, specialized teams also have better system flexibility.
Although the system flexibility is quantitatively evaluated in this study, the cost factor is not considered. While multi-skilled workers can bring flexibility, need to invest a certain cost of training. Therefore, in the subsequent research, we can consider adding cost factors to the simulation in order to further explore the balance between economic benefits and input costs brought by flexible upgrading.
This research was supported by the National Natural Science Foundation of China (No. 71871018).
The authors gratefully acknowledge the anonymous reviewers for insightful comments that helped us improve the quality of this paper.
The authors declare that they have no conflict of interests.
[1] | R. Laughery, Modeling human performance in systems, in Proceedings of the Human Factors and Ergonomics Society Annual Meeting, Sage Publications Ltd., 1 (2000), 2254–2254. |
[2] | R. Qin, D. A. Nembhard, W. L. Barnes II, Workforce flexibility in operations management, Surv. Oper. Res. Manage. Sci., 20 (2015), 19–33. |
[3] |
Y. Yang, J. Tang, W. Sun, Y. Yin, I. Kaku, Reducing worker(s) by converting assembly line into a pure cell system, Int. J. Prod. Econ., 145 (2013), 799–806. doi: 10.1016/j.ijpe.2013.06.009
![]() |
[4] |
G. A. Süer, K. Kamat, E. Mese, J. Huang, Minimizing total tardiness subject to manpower restriction in labor–intensive manufacturing cells, Math. Comput. Modell., 57 (2013), 741–753. doi: 10.1016/j.mcm.2012.08.013
![]() |
[5] | G. Egilmez, B. Erenay, G. A. Süer, Stochastic skill-based manpower allocation in a cellular manufacturing system, J. Manuf. Syst., 33 (2014), 578–588. |
[6] |
J. S. Evans, Strategic flexibility for high technology manoeuvres: a conceptual framework, J. Manage. Stud., 28 (1991), 69–89. doi: 10.1111/j.1467-6486.1991.tb00271.x
![]() |
[7] | R. Xu, Q. Qin, Impact of Entrepreneurial Orientation and Organizational Flexibility on Technological Innovation, in 2010 3rd International Conference on Information Management, Innovation Management and Industrial Engineering, 2 (2010), 421–425. |
[8] |
M. Dağdeviren, A hybrid multi-criteria decision-making model for personnel selection in manufacturing systems, J. Intell. Manuf., 21 (2010), 451–460. doi: 10.1007/s10845-008-0200-7
![]() |
[9] |
O. Oleghe, K. Salonitis, Hybrid simulation modelling of the human-production process interface in lean manufacturing systems, Int. J. Lean Six Sigma, 10 (2019), 665–690. doi: 10.1108/IJLSS-01-2018-0004
![]() |
[10] |
M. K. Malhotra, T. D. Fry, H. V. Kher, J. M. Donohue, The impact of learning and labor attrition on worker flexibility in dual resource constrained job shops, Decis. Sci., 24 (1993), 641–664. doi: 10.1111/j.1540-5915.1993.tb01296.x
![]() |
[11] |
B. Denkena, M. A. Dittrich, F. Winter, C. Wagener, Simulation-based planning and evaluation of personnel scheduling in knowledge-intensive production systems, Prod. Eng., 10 (2016), 489–496. doi: 10.1007/s11740-016-0693-4
![]() |
[12] |
D. J. Davis, H. V. Kher, B. J. Wagner, Influence of workload imbalances on the need for worker flexibility, Comput. Ind. Eng., 57 (2009), 319–329. doi: 10.1016/j.cie.2008.11.029
![]() |
[13] |
C. Pach, T. Berger, Y. Sallez, T. Bonte, E. Adam, D. Trentesaux, Reactive and energy-aware scheduling of flexible manufacturing systems using potential fields, Comput. Ind., 65 (2014), 434–448. doi: 10.1016/j.compind.2013.11.008
![]() |
[14] |
A. Ferjani, A. Ammar, H. Pierreval, S. Elkosantini, A simulation-optimization based heuristic for the online assignment of multi–skilled workers subjected to fatigue in manufacturing systems, Comput. Ind. Eng., 112 (2017), 663–674. doi: 10.1016/j.cie.2017.02.008
![]() |
[15] |
F. Phillips, S. D. Tuladhar, Measuring organizational flexibility: an exploration and general model, Technol. Forecasting Soc. Change, 64 (2000), 23–38. doi: 10.1016/S0040-1625(99)00077-3
![]() |
[16] |
R. V. Rao, A decision-making framework model for evaluating flexible manufacturing systems using digraph and matrix methods, Int. J. Adv. Manuf. Technol., 30 (2006), 1101–1110. doi: 10.1007/s00170-005-0150-6
![]() |
[17] | H. Yue, J. Slomp, E. Molleman, D. J. Van Der Zee, Worker flexibility in a parallel dual resource constrained job shop, Int. J. Prod. Res., 46 (2008), 451–467. |
[18] |
D. Nembhard, K. Prichanont, Cross training in serial production with process characteristics and operational factors, IEEE Trans. Eng. Manage., 54 (2007), 565–575. doi: 10.1109/TEM.2007.900793
![]() |
[19] |
K. Georgoulias, N. Papakostas, G. Chryssolouris, S. Stanev, H. Krappe, J. Ovtcharova, Evaluation of flexibility for the effective change management of manufacturing organizations, Rob. Comput. Integr. Manuf., 25 (2009), 888–893. doi: 10.1016/j.rcim.2009.04.010
![]() |
[20] |
S. K. Singh, M. K. Singh, Evaluation of productivity, quality and flexibility of an advanced manufacturing system, J. Inst. Eng. (India): Ser. C, 93 (2012), 93–101. doi: 10.1007/s40032-011-0002-0
![]() |
[21] |
M. Naderi, E. Ares, G. Peláez, D. Prieto, A. Fernández, L. P. Ferreira, The sustainable evaluation of manufacturing systems based on simulation using an economic index function: A case study, Procedia Manuf., 13 (2017), 1043–1050. doi: 10.1016/j.promfg.2017.09.128
![]() |
[22] |
A. Yadav, S. C. Jayswal, Evaluation of batching and layout on the performance of flexible manufacturing system, Int. J. Adv. Manuf. Technol., 101 (2019), 1435–1449. doi: 10.1007/s00170-018-2999-1
![]() |
[23] |
N. V. Hop, Approach to measure the mix response flexibility of manufacturing systems, In. J. Prod. Res., 42 (2004), 1407–1418. doi: 10.1080/00207540310001638064
![]() |
[24] |
M. I. M. Wahab, D. Wu, C. Lee, A generic approach to measuring the machine flexibility of manufacturing systems, Eur. J. Oper. Res., 186 (2008), 137–149. doi: 10.1016/j.ejor.2007.01.052
![]() |
[25] |
S. Kemmoe, P. Pernot, N. Tchernev, Model for flexibility evaluation in manufacturing network strategic planning, Int. J. Prod. Res., 52 (2014), 4396–4411. doi: 10.1080/00207543.2013.845703
![]() |
[26] |
R. Mishra, A comparative evaluation of manufacturing flexibility adoption in SMEs and large firms in India, J. Manuf. Technol. Manage., 27 (2016), 730–762. doi: 10.1108/JMTM-11-2015-0105
![]() |
[27] | F. Long, P. Zeiler, B. Bertsche, Modelling the flexibility of production systems in Industry 4.0 for analysing their productivity and availability with high-level Petri nets, IFAC-PapersOnLine, 50 (2017), 5680–5687. |
[28] |
R. Mishra, A. K. Pundir, L. Ganapathy, Evaluation and prioritisation of manufacturing flexibility alternatives using integrated AHP and TOPSIS method, Benchmarking: Int. J., 24 (2017), 1437–1465. doi: 10.1108/BIJ-07-2015-0077
![]() |
[29] | M. Mohun, Modelling of fuzzy discrete event dynamic systems, in Proceedings of 2005 International Conference on Intelligent Sensing and Information Processing, (2005), 278–283. |
[30] |
R. Kia, A. Baboli, N. Javadian, R. Tavakkoli-Moghaddam, M. Kazemi, J. Khorrami, Solving a group layout design model of a dynamic cellular manufacturing system with alternative process routings, lot splitting and flexible reconfiguration by simulated annealing, Comput. Oper. Res., 39 (2012), 2642–2658. doi: 10.1016/j.cor.2012.01.012
![]() |
[31] | B. Lennartson, O. Wigstrom, M. Fabian, F. Basile, Unified model for synthesis and optimization of discrete event and hybrid systems, IFAC Proc. Vol., 47 (2014), 86–92. |
[32] |
D. Antonelli, P. Litwin, D. Stadnicka, Multiple system dynamics and discrete event simulation for manufacturing system performance evaluation, Procedia CIRP, 78 (2018), 178–183. doi: 10.1016/j.procir.2018.08.312
![]() |
[33] |
S. E. H. Petroodi, A. B. D. Eynaud, N. Klement, R. Tavakkoli-Moghaddam, Simulation–based optimization approach with scenario–based product sequence in a reconfigurable manufacturing system (RMS): A case study, IFAC-PapersOnLine, 52 (2019), 2638–2643. doi: 10.1016/j.ifacol.2019.11.605
![]() |
[34] | D. Xu, C. Lu, W. Zhou, S. Liu, Hybrid model of multi-agent and DEDS for steelmaking-continuous casting-hot rolling manufacturing process simulation, in The 26th Chinese Control and Decision Conference (2014 CCDC), (2014), 1936–1940. |
[35] |
Z. Lin, A. Matta, J. G. Shanthikumar, Combining simulation experiments and analytical models with area–based accuracy for performance evaluation of manufacturing systems, IISE Trans., 51 (2019), 266–283. doi: 10.1080/24725854.2018.1490046
![]() |
[36] |
P. Pawlewski, M. Anholcer, Relational database template in the simulation modeling of manufacturing systems, IFAC PapersOnLine, 52 (2019), 1744–1748. doi: 10.1016/j.ifacol.2019.11.453
![]() |
[37] | A. V. Barenji, R. V. Barenji, Improving multi-agent manufacturing control system by indirect communication based on ant agents, Proc. Inst. Mech. Eng., Part I: J. Syst. Control Eng., 231 (2017), 447–458. |
[38] |
X. Zhang, S. Tang, X. Liu, R. Malekian, Z. Li, A novel multi-agent-based collaborative virtual manufacturing environment integrated with edge computing technique, Energies, 12 (2019), 2815. doi: 10.3390/en12142815
![]() |
[39] |
X. Zhang, J. Qiu, D. Zhao, C. M. Schlick, A Human-Oriented Simulation Approach for Labor Assignment Flexibility in Changeover Processes of Manufacturing Cells, Hum. Factors Ergon. Manuf. Serv. Ind., 25 (2015), 740–757. doi: 10.1002/hfm.20589
![]() |
1. | Xiaodong Zhang, Dawei Ren, Modeling and simulation of task rescheduling strategy with resource substitution in cloud manufacturing, 2022, 20, 1551-0018, 3120, 10.3934/mbe.2023147 | |
2. | Tong YiFei, Hu Jichuan, Zhang Xu, Srikanta Patnaik, Tao Shen, 2023, Flexible evaluation of complex equipment assembly cell, 9781510668072, 34, 10.1117/12.2688848 | |
3. | Noor Yusuf, Tareq Al-Ansari, Current and Future Role of Natural Gas Supply Chains in the Transition to a Low-Carbon Hydrogen Economy: A Comprehensive Review on Integrated Natural Gas Supply Chain Optimisation Models, 2023, 16, 1996-1073, 7672, 10.3390/en16227672 |
Machine | Programme A operators Distribution of machine skill | Programme B operators Distribution of machine skil | ||||||||||
Op1 | Op2 | Op3 | Op4 | Op5 | Op6 | Op1 | Op2 | Op3 | Op4 | Op5 | Op6 | |
M1 | 8 | 0 | 0 | 0 | 0 | 10 | 8 | 3 | 0 | 0 | 0 | 10 |
M2 | 9 | 0 | 0 | 0 | 0 | 7 | 9 | 5 | 0 | 9 | 0 | 7 |
M3 | 0 | 8 | 0 | 0 | 0 | 9 | 6 | 8 | 6 | 3 | 0 | 9 |
M4 | 0 | 8 | 0 | 0 | 0 | 7 | 5 | 8 | 6 | 7 | 4 | 7 |
M5 | 0 | 0 | 8 | 0 | 0 | 9 | 0 | 7 | 9 | 0 | 5 | 9 |
M6 | 0 | 0 | 0 | 8 | 0 | 9 | 0 | 7 | 7 | 8 | 5 | 9 |
M7 | 0 | 0 | 0 | 7 | 0 | 10 | 6 | 0 | 4 | 8 | 9 | 10 |
M8 | 0 | 0 | 0 | 0 | 8 | 8 | 0 | 0 | 4 | 7 | 8 | 8 |
Fluctuating environment | Failure number/n | Error rate of worker/% | Defect rate of material/% | Change line number/n | Fluctuating probability/% |
Light fluctuation | 1–10 | 1 | 1 | 1–10 | 15 |
Medium fluctuation | 10–30 | 2 | 4 | 10–25 | 50 |
Huge fluctuation | 30–60 | 4 | 7 | 25–50 | 35 |
Period | Light fluctuation (a1=0.5) | Medium fluctuation (a2=0.5) | Huge fluctuation (a3=0.5) | |||||||||||||
Programme A/B | Fluctuating utilization of machine ω1=0.25 | Fluctuating utilization of worker ω2=0.25 | Fluctuating production ω3=0.25 | Fluctuating efficiency of worker ω4=0.25 | Performance indicator (FL1) | Fluctuating utilization of machine ω1=0.25 | Fluctuating utilization of worker ω2=0.25 | Fluctuating production ω3=0.25 | Fluctuating efficiency of worker ω4=0.25 | Performance indicator (FL2) | Fluctuating utilization of machine ω1=0.25 | Fluctuating utilization of worker ω2=0.25 | Fluctuating production ω3=0.25 | Fluctuating efficiency of worker ω4=0.25 | Performance indicator (FL3) | |
A | 1 | 0.058 0.053 0.054 0.05 0.059 0.057 0.053 0.057 0.054 0.056 0.055 |
0.079 0.085 0.08 0.079 0.08 0.074 0.082 0.078 0.081 0.077 0.08 |
0.027 0.032 0.029 0.025 0.029 0.03 0.032 0.033 0.027 0.029 0.029 |
0.005 0.005 0.007 0.003 0.007 0.005 0.007 0.007 0.005 0.005 0.006 |
0.042 0.044 0.043 0.039 0.044 0.042 0.044 0.044 0.042 0.042 0.043 |
0.125 0.136 0.137 0.105 0.123 0.125 0.102 0.104 0.106 0.138 0.12 |
0.135 0.126 0.159 0.118 0.151 0.115 0.157 0.146 0.155 0.138 0.14 |
0.087 0.119 0.11 0.069 0.108 0.082 0.094 0.098 0.12 0.081 0.097 |
0.02 0.018 0.021 0.019 0.018 0.019 0.016 0.021 0.018 0.019 0.019 |
0.092 0.1 0.107 0.078 0.1 0.085 0.092 0.092 0.1 0.094 0.094 |
0.377 0.483 0.458 0.546 0.232 0.611 0.462 0.507 0.407 0.557 0.464 |
0.337 0.568 0.447 0.242 0.437 0.411 0.461 0.262 0.237 0.367 0.377 |
0.461 0.316 0.454 0.371 0.267 0.334 0.232 0.272 0.403 0.361 0.347 |
0.021 0.022 0.019 0.019 0.023 0.023 0.021 0.023 0.021 0.022 0.021 |
0.299 0.347 0.345 0.295 0.24 0.345 0.294 0.266 0.267 0.327 0.302 |
2 | ||||||||||||||||
3 | ||||||||||||||||
4 | ||||||||||||||||
5 | ||||||||||||||||
6 | ||||||||||||||||
7 | ||||||||||||||||
8 | ||||||||||||||||
9 | ||||||||||||||||
10 | ||||||||||||||||
Average | ||||||||||||||||
B | 1 | 0.034 0.036 0.036 0.031 0.032 0.034 0.03 0.033 0.035 0.036 0.034 |
0.024 0.028 0.027 0.021 0.03 0.028 0.026 0.022 0.025 0.026 0.026 |
0.017 0.015 0.016 0.022 0.014 0.014 0.011 0.016 0.019 0.014 0.016 |
0.005 0.003 0.006 0.004 0.003 0.004 0.001 0.006 0.004 0.002 0.004 |
0.02 0.021 0.021 0.02 0.02 0.02 0.017 0.019 0.021 0.02 0.02 |
0.077 0.07 0.074 0.086 0.068 0.058 0.069 0.074 0.071 0.082 0.073 |
0.062 0.063 0.055 0.064 0.071 0.052 0.062 0.052 0.067 0.051 0.06 |
0.048 0.047 0.036 0.039 0.056 0.054 0.04 0.047 0.044 0.041 0.045 |
0.004 0.004 0.006 0.002 0.006 0.006 0.004 0.006 0.004 0.006 0.005 |
0.048 0.046 0.043 0.048 0.05 0.043 0.044 0.045 0.047 0.045 0.046 |
0.251 0.352 0.302 0.314 0.253 0.303 0.38 0.39 0.405 0.299 0.325 |
0.208 0.281 0.397 0.279 0.302 0.3 0.217 0.258 0.221 0.258 0.272 |
0.309 0.19 0.239 0.301 0.282 0.123 0.333 0.221 0.302 0.229 0.253 |
0.009 0.011 0.011 0.002 0.003 0.017 0.011 0.012 0.013 0.017 0.011 |
0.194 0.209 0.237 0.224 0.21 0.186 0.235 0.22 0.235 0.201 0.215 |
2 | ||||||||||||||||
3 | ||||||||||||||||
4 | ||||||||||||||||
5 | ||||||||||||||||
6 | ||||||||||||||||
7 | ||||||||||||||||
8 | ||||||||||||||||
9 | ||||||||||||||||
10 | ||||||||||||||||
Average | ||||||||||||||||
Fluctuating indicator(ProgrammeA)=0.159 | Calculation index of organizational flexibility(ProgrammeA)=0.841 | |||||||||||||||
Fluctuating indicator(ProgrammeB)=0.101 | Calculation index of organizational flexibility(ProgrammeB)=0.899 |
Evaluation index | Null hypothesis | Programme | Average (standard deviation) | Simulation number | Student's test | Test result | Conclusion | |
k=1 | Fluctuating utilization of machine | σ1AU=σ1BU | A | 0.055(0.003) | 10 | 19.823(df=9) | Reject | σ1AU>σ1BU |
B | 0.034(0.002) | |||||||
Fluctuating utilization of worker | σ1AP=σ1BP | A | 0.08(0.003) | 10 | 42.865(df=9) | Reject | σ1AP>σ1BP | |
B | 0.026(0.003) | |||||||
Fluctuating production | σ1AY=σ1BY | A | 0.029(0.002) | 10 | 7.77(df=9) | Reject | σ1AY>σ1BY | |
B | 0.016(0.002) | |||||||
Fluctuating efficiency of worker | σ1AT=σ1BT | A | 0.006(0.001) | 10 | 0.654(df=9) | Not reject | Uncertain | |
B | 0.004(0.001) | |||||||
k=2 | Fluctuating utilization of machine | σ2AU=σ2BU | A | 0.12(0.014) | 10 | 8.37(df=9) | Reject | σ2AU>σ2BU |
B | 0.073(0.007) | |||||||
Fluctuating utilization of worker | σ2AP=σ2BP | A | 0.14(0.015) | 10 | 14.676(df=9) | Reject | σ2AP>σ2BP | |
B | 0.06(0.007) | |||||||
Fluctuating production | σ2AY=σ2BY | A | 0.097(0.016) | 10 | 8.72(df=9) | Reject | σ2AY>σ2BY | |
B | 0.045(0.006) | |||||||
Fluctuating efficiency of worker | σ2AT=σ2BT | A | 0.019(0.002) | 10 | 25.431(df=9) | Reject | σ2AT>σ2BT | |
B | 0.005(0.001) | |||||||
k=3 | Fluctuating utilization of machine | σ3AU=σ3BU | A | 0.464(0.102) | 10 | 3.959(df=9) | Reject | σ3AU>σ3BU |
B | 0.325(0.052) | |||||||
Fluctuating utilization of worker | σ3AP=σ3BP | A | 0.377(0.103) | 10 | 3.056(df=9) | Reject | σ3AP>σ3BP | |
B | 0.272(0.053) | |||||||
Fluctuating production | σ3AY=σ3BY | A | 0.347(0.074) | 10 | 2.882(df=9) | Reject | σ3AY>σ3BY | |
B | 0.253(0.061) | |||||||
Fluctuating efficiency of worker | σ3AT=σ3BT | A | 0.021(0.001) | 10 | 6.915(df=9) | Reject | σ3AT>σ3BT | |
B | 0.011(0.001) |
Machine | Programme A operators Distribution of machine skill | Programme B operators Distribution of machine skil | ||||||||||
Op1 | Op2 | Op3 | Op4 | Op5 | Op6 | Op1 | Op2 | Op3 | Op4 | Op5 | Op6 | |
M1 | 8 | 0 | 0 | 0 | 0 | 10 | 8 | 3 | 0 | 0 | 0 | 10 |
M2 | 9 | 0 | 0 | 0 | 0 | 7 | 9 | 5 | 0 | 9 | 0 | 7 |
M3 | 0 | 8 | 0 | 0 | 0 | 9 | 6 | 8 | 6 | 3 | 0 | 9 |
M4 | 0 | 8 | 0 | 0 | 0 | 7 | 5 | 8 | 6 | 7 | 4 | 7 |
M5 | 0 | 0 | 8 | 0 | 0 | 9 | 0 | 7 | 9 | 0 | 5 | 9 |
M6 | 0 | 0 | 0 | 8 | 0 | 9 | 0 | 7 | 7 | 8 | 5 | 9 |
M7 | 0 | 0 | 0 | 7 | 0 | 10 | 6 | 0 | 4 | 8 | 9 | 10 |
M8 | 0 | 0 | 0 | 0 | 8 | 8 | 0 | 0 | 4 | 7 | 8 | 8 |
Fluctuating environment | Failure number/n | Error rate of worker/% | Defect rate of material/% | Change line number/n | Fluctuating probability/% |
Light fluctuation | 1–10 | 1 | 1 | 1–10 | 15 |
Medium fluctuation | 10–30 | 2 | 4 | 10–25 | 50 |
Huge fluctuation | 30–60 | 4 | 7 | 25–50 | 35 |
Period | Light fluctuation (a1=0.5) | Medium fluctuation (a2=0.5) | Huge fluctuation (a3=0.5) | |||||||||||||
Programme A/B | Fluctuating utilization of machine ω1=0.25 | Fluctuating utilization of worker ω2=0.25 | Fluctuating production ω3=0.25 | Fluctuating efficiency of worker ω4=0.25 | Performance indicator (FL1) | Fluctuating utilization of machine ω1=0.25 | Fluctuating utilization of worker ω2=0.25 | Fluctuating production ω3=0.25 | Fluctuating efficiency of worker ω4=0.25 | Performance indicator (FL2) | Fluctuating utilization of machine ω1=0.25 | Fluctuating utilization of worker ω2=0.25 | Fluctuating production ω3=0.25 | Fluctuating efficiency of worker ω4=0.25 | Performance indicator (FL3) | |
A | 1 | 0.058 0.053 0.054 0.05 0.059 0.057 0.053 0.057 0.054 0.056 0.055 |
0.079 0.085 0.08 0.079 0.08 0.074 0.082 0.078 0.081 0.077 0.08 |
0.027 0.032 0.029 0.025 0.029 0.03 0.032 0.033 0.027 0.029 0.029 |
0.005 0.005 0.007 0.003 0.007 0.005 0.007 0.007 0.005 0.005 0.006 |
0.042 0.044 0.043 0.039 0.044 0.042 0.044 0.044 0.042 0.042 0.043 |
0.125 0.136 0.137 0.105 0.123 0.125 0.102 0.104 0.106 0.138 0.12 |
0.135 0.126 0.159 0.118 0.151 0.115 0.157 0.146 0.155 0.138 0.14 |
0.087 0.119 0.11 0.069 0.108 0.082 0.094 0.098 0.12 0.081 0.097 |
0.02 0.018 0.021 0.019 0.018 0.019 0.016 0.021 0.018 0.019 0.019 |
0.092 0.1 0.107 0.078 0.1 0.085 0.092 0.092 0.1 0.094 0.094 |
0.377 0.483 0.458 0.546 0.232 0.611 0.462 0.507 0.407 0.557 0.464 |
0.337 0.568 0.447 0.242 0.437 0.411 0.461 0.262 0.237 0.367 0.377 |
0.461 0.316 0.454 0.371 0.267 0.334 0.232 0.272 0.403 0.361 0.347 |
0.021 0.022 0.019 0.019 0.023 0.023 0.021 0.023 0.021 0.022 0.021 |
0.299 0.347 0.345 0.295 0.24 0.345 0.294 0.266 0.267 0.327 0.302 |
2 | ||||||||||||||||
3 | ||||||||||||||||
4 | ||||||||||||||||
5 | ||||||||||||||||
6 | ||||||||||||||||
7 | ||||||||||||||||
8 | ||||||||||||||||
9 | ||||||||||||||||
10 | ||||||||||||||||
Average | ||||||||||||||||
B | 1 | 0.034 0.036 0.036 0.031 0.032 0.034 0.03 0.033 0.035 0.036 0.034 |
0.024 0.028 0.027 0.021 0.03 0.028 0.026 0.022 0.025 0.026 0.026 |
0.017 0.015 0.016 0.022 0.014 0.014 0.011 0.016 0.019 0.014 0.016 |
0.005 0.003 0.006 0.004 0.003 0.004 0.001 0.006 0.004 0.002 0.004 |
0.02 0.021 0.021 0.02 0.02 0.02 0.017 0.019 0.021 0.02 0.02 |
0.077 0.07 0.074 0.086 0.068 0.058 0.069 0.074 0.071 0.082 0.073 |
0.062 0.063 0.055 0.064 0.071 0.052 0.062 0.052 0.067 0.051 0.06 |
0.048 0.047 0.036 0.039 0.056 0.054 0.04 0.047 0.044 0.041 0.045 |
0.004 0.004 0.006 0.002 0.006 0.006 0.004 0.006 0.004 0.006 0.005 |
0.048 0.046 0.043 0.048 0.05 0.043 0.044 0.045 0.047 0.045 0.046 |
0.251 0.352 0.302 0.314 0.253 0.303 0.38 0.39 0.405 0.299 0.325 |
0.208 0.281 0.397 0.279 0.302 0.3 0.217 0.258 0.221 0.258 0.272 |
0.309 0.19 0.239 0.301 0.282 0.123 0.333 0.221 0.302 0.229 0.253 |
0.009 0.011 0.011 0.002 0.003 0.017 0.011 0.012 0.013 0.017 0.011 |
0.194 0.209 0.237 0.224 0.21 0.186 0.235 0.22 0.235 0.201 0.215 |
2 | ||||||||||||||||
3 | ||||||||||||||||
4 | ||||||||||||||||
5 | ||||||||||||||||
6 | ||||||||||||||||
7 | ||||||||||||||||
8 | ||||||||||||||||
9 | ||||||||||||||||
10 | ||||||||||||||||
Average | ||||||||||||||||
Fluctuating indicator(ProgrammeA)=0.159 | Calculation index of organizational flexibility(ProgrammeA)=0.841 | |||||||||||||||
Fluctuating indicator(ProgrammeB)=0.101 | Calculation index of organizational flexibility(ProgrammeB)=0.899 |
Evaluation index | Null hypothesis | Programme | Average (standard deviation) | Simulation number | Student's test | Test result | Conclusion | |
k=1 | Fluctuating utilization of machine | σ1AU=σ1BU | A | 0.055(0.003) | 10 | 19.823(df=9) | Reject | σ1AU>σ1BU |
B | 0.034(0.002) | |||||||
Fluctuating utilization of worker | σ1AP=σ1BP | A | 0.08(0.003) | 10 | 42.865(df=9) | Reject | σ1AP>σ1BP | |
B | 0.026(0.003) | |||||||
Fluctuating production | σ1AY=σ1BY | A | 0.029(0.002) | 10 | 7.77(df=9) | Reject | σ1AY>σ1BY | |
B | 0.016(0.002) | |||||||
Fluctuating efficiency of worker | σ1AT=σ1BT | A | 0.006(0.001) | 10 | 0.654(df=9) | Not reject | Uncertain | |
B | 0.004(0.001) | |||||||
k=2 | Fluctuating utilization of machine | σ2AU=σ2BU | A | 0.12(0.014) | 10 | 8.37(df=9) | Reject | σ2AU>σ2BU |
B | 0.073(0.007) | |||||||
Fluctuating utilization of worker | σ2AP=σ2BP | A | 0.14(0.015) | 10 | 14.676(df=9) | Reject | σ2AP>σ2BP | |
B | 0.06(0.007) | |||||||
Fluctuating production | σ2AY=σ2BY | A | 0.097(0.016) | 10 | 8.72(df=9) | Reject | σ2AY>σ2BY | |
B | 0.045(0.006) | |||||||
Fluctuating efficiency of worker | σ2AT=σ2BT | A | 0.019(0.002) | 10 | 25.431(df=9) | Reject | σ2AT>σ2BT | |
B | 0.005(0.001) | |||||||
k=3 | Fluctuating utilization of machine | σ3AU=σ3BU | A | 0.464(0.102) | 10 | 3.959(df=9) | Reject | σ3AU>σ3BU |
B | 0.325(0.052) | |||||||
Fluctuating utilization of worker | σ3AP=σ3BP | A | 0.377(0.103) | 10 | 3.056(df=9) | Reject | σ3AP>σ3BP | |
B | 0.272(0.053) | |||||||
Fluctuating production | σ3AY=σ3BY | A | 0.347(0.074) | 10 | 2.882(df=9) | Reject | σ3AY>σ3BY | |
B | 0.253(0.061) | |||||||
Fluctuating efficiency of worker | σ3AT=σ3BT | A | 0.021(0.001) | 10 | 6.915(df=9) | Reject | σ3AT>σ3BT | |
B | 0.011(0.001) |