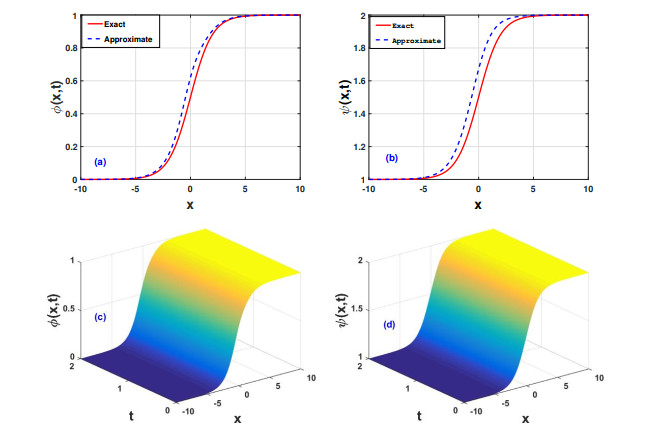
The most essential cause of the fracture of the dropper is the effect of alternating stress for a long time. Therefore, in order to ensure the safe operation of high-speed railways, the influence of moving loads on the stress of a dropper was investigated in this study. Due to a high-voltage catenary system, it is very difficult to measure the moving load. Thus, the uplift displacement measured by some software and hardware devices has been applied to the contact wire instead of the moving load. The response equation for the contact wire has been derived so as to determine the initial and boundary conditions of each dropper. Then it was combined with the equation for vibration analysis of the dropper and the stress of each dropper was calculated by using the finite-difference method based on a written MATLAB program. The results show that the dropper stress, during a certain period goes through two stages of immediate rebound and bending compression when the uplift displacement is large. After the pantograph passes, the vibration of the dropper tends to be smooth; also, dropper stress variation with timecan be described by three stages: immediate rebound, vibration attenuation, and bending compression. In addition, the maximum tensile stress of dropper Ⅳ was the highest. It indicates that dropper Ⅳ was more prone to fracture than other droppers.
Citation: Caizhi Yang, Xinxin Shen, Like Pan, Liming Chen, Fan He. Numerical analysis of dropper stress under a moving load based on the uplift displacement for a high-speed railway[J]. AIMS Mathematics, 2024, 9(3): 6568-6585. doi: 10.3934/math.2024320
[1] | M. Mossa Al-Sawalha, Rasool Shah, Adnan Khan, Osama Y. Ababneh, Thongchai Botmart . Fractional view analysis of Kersten-Krasil'shchik coupled KdV-mKdV systems with non-singular kernel derivatives. AIMS Mathematics, 2022, 7(10): 18334-18359. doi: 10.3934/math.20221010 |
[2] | Asif Khan, Tayyaba Akram, Arshad Khan, Shabir Ahmad, Kamsing Nonlaopon . Investigation of time fractional nonlinear KdV-Burgers equation under fractional operators with nonsingular kernels. AIMS Mathematics, 2023, 8(1): 1251-1268. doi: 10.3934/math.2023063 |
[3] | Khalid Khan, Amir Ali, Muhammad Irfan, Zareen A. Khan . Solitary wave solutions in time-fractional Korteweg-de Vries equations with power law kernel. AIMS Mathematics, 2023, 8(1): 792-814. doi: 10.3934/math.2023039 |
[4] | Hayman Thabet, Subhash Kendre, James Peters . Travelling wave solutions for fractional Korteweg-de Vries equations via an approximate-analytical method. AIMS Mathematics, 2019, 4(4): 1203-1222. doi: 10.3934/math.2019.4.1203 |
[5] | Ihsan Ullah, Aman Ullah, Shabir Ahmad, Hijaz Ahmad, Taher A. Nofal . A survey of KdV-CDG equations via nonsingular fractional operators. AIMS Mathematics, 2023, 8(8): 18964-18981. doi: 10.3934/math.2023966 |
[6] | Muath Awadalla, Abdul Hamid Ganie, Dowlath Fathima, Adnan Khan, Jihan Alahmadi . A mathematical fractional model of waves on Shallow water surfaces: The Korteweg-de Vries equation. AIMS Mathematics, 2024, 9(5): 10561-10579. doi: 10.3934/math.2024516 |
[7] | Aslı Alkan, Halil Anaç . The novel numerical solutions for time-fractional Fornberg-Whitham equation by using fractional natural transform decomposition method. AIMS Mathematics, 2024, 9(9): 25333-25359. doi: 10.3934/math.20241237 |
[8] | Gulalai, Shabir Ahmad, Fathalla Ali Rihan, Aman Ullah, Qasem M. Al-Mdallal, Ali Akgül . Nonlinear analysis of a nonlinear modified KdV equation under Atangana Baleanu Caputo derivative. AIMS Mathematics, 2022, 7(5): 7847-7865. doi: 10.3934/math.2022439 |
[9] | Musawa Yahya Almusawa, Hassan Almusawa . Numerical analysis of the fractional nonlinear waves of fifth-order KdV and Kawahara equations under Caputo operator. AIMS Mathematics, 2024, 9(11): 31898-31925. doi: 10.3934/math.20241533 |
[10] | Ritu Agarwal, Mahaveer Prasad Yadav, Dumitru Baleanu, S. D. Purohit . Existence and uniqueness of miscible flow equation through porous media with a non singular fractional derivative. AIMS Mathematics, 2020, 5(2): 1062-1073. doi: 10.3934/math.2020074 |
The most essential cause of the fracture of the dropper is the effect of alternating stress for a long time. Therefore, in order to ensure the safe operation of high-speed railways, the influence of moving loads on the stress of a dropper was investigated in this study. Due to a high-voltage catenary system, it is very difficult to measure the moving load. Thus, the uplift displacement measured by some software and hardware devices has been applied to the contact wire instead of the moving load. The response equation for the contact wire has been derived so as to determine the initial and boundary conditions of each dropper. Then it was combined with the equation for vibration analysis of the dropper and the stress of each dropper was calculated by using the finite-difference method based on a written MATLAB program. The results show that the dropper stress, during a certain period goes through two stages of immediate rebound and bending compression when the uplift displacement is large. After the pantograph passes, the vibration of the dropper tends to be smooth; also, dropper stress variation with timecan be described by three stages: immediate rebound, vibration attenuation, and bending compression. In addition, the maximum tensile stress of dropper Ⅳ was the highest. It indicates that dropper Ⅳ was more prone to fracture than other droppers.
The time-fractional singular and non-singular operator are widely used in modern sciences and technology to study the behavior and applications of nonlinear ordinary and partial differential equations [1,2,3,4]. Fractional-order models are useful to study numerous real-world problems for longtime memory, and chaotic behaviour [5]. Due to these characteristics, the nonlinear models having fractional-order derivatives have been widely attracted in many areas of fractional calculus including image processing and signal, mechanics, biophysics and bioengineering, electrical engineering, biology, viscoelasticity, rheology, and control theory [6,7,8].
The Korteweg-de Vries (KdV) equation has extensively studied for nonlinear models describing the evaluation in time of long, unidirectional shallow water waves [9]. It was mainly presented by Boussinesq in 1877 and then retrieved by Diederik Korteweg and Gustav-de Vries in 1895 [10]. The existence solution to the a KdV equation can be seen in [11,12]. The KdV system having time-fractional derivatives attained remarkable attention in plasma physics especially in electrons acoustic waves (EAWs) propagation, due to its important role in studying diverse forms of mutual developments experimentally [13,14]. It has observed that the time-fractional operators in the system dramatically change the soliton amplitudes of the electron-acoustic solitary waves. This effects have been particularly equated with the structures of the broadband electrostatic noise experienced in the dayside auroral zone [15]. The system of coupled KdV system plays a leading part in various areas of sciences and engineering, particularly in water waves, quantum field theory, hydrodynamics and plasma physics [16,17]. It also represents the relations in extended waves with altered dispersion relations and describes iterations of water waves [18,19].
Here, we consider the mCKdV in the form [20]
∂αϕ∂tα+3ϕ2∂ϕ∂x−32∂2ψ∂x2−3ϕ∂ψ∂x−3ψ∂ϕ∂x+3λ∂ϕ∂x−12∂3ϕ∂x3=0,∂αψ∂tα−3ϕ2∂ψ∂x+3ψ∂ψ∂x+3∂ϕ∂x∂ψ∂x−3λ∂ψ∂x+∂3ψ∂x3=0,0<α≤1,t>0 | (1.1) |
with subsidiary conditions
ϕ(x,0)=f(x),ψ(x,0)=g(x), |
where λ is a real number to be chosen accordingly.
The proposed mCKdV Eq (1.1) has more interesting features than classical, because the operators will be defined by an integral which play a vital role in modern technology, engineering, plasma physics, hydrodynamics and quantum theory [21]. The nonlinear differential equations contain numerous fractional differential singular and non-singular operators such as Hilfer, Caputo, Caputo-Fabrizio, Riemann-Liouville, Antagana-Balenau in Caputo's sense [22,23,24]. These operators can be reduced in Caputo's form after some parametric addition. One can assume that the fractional operator could provide a power-law estimate of the local conduct of non-differentiable functions [25]. The Caputo operator possesses a power-law kernel and has restrictions to apply in modeling physical phenomena.
A modified laplace decomposition method (MLDM) is applied to Schrodinger-KdV equation in the sense of Atangana-Baleanu derivative in[26]. To deal successfully in such a situation, an alternative fractional operator possess a kernel with exponential decay has been introduced [27]. This novel operator is called the Caputo-Fabrizio (CF) operator which has a non-singular kernel. This operator is broadly applicable for modeling particular type of physical problems which follows the exponential decay law. Currently, mathematical and physical models having the CF operator have a remarkable development. The characteristics and applications of the above derivatives has been extensively studied (see [28,29,30,31,32,33,34,35] and the reference therein).
There are many analytical methods that offer approximate solutions to nonlinear models, for example, perturbation methods [36,37,38], homotopy perturbation [39,40,41,42], the Adomian decomposition methods (ADM) [43,44] and Laplace Adomian decomposition methods (LADM) [45,46,47]. The modified coupled KdV model has been analyzed numerically by applying the q-homotopy approach with Caputo operator by using Petrov-Galerkin method and product approximation technique [20,48]. We will study the mCKdV equations with Caputo and CF derivatives by applying the modified double Laplace transform decomposing method (MDLDM) [49]. The decomposition method has extensively applied for many fractional models in physics and applied mathematics [50,51,52].
Some resent contribution of the time fractional order KdV equations have been studied by using different techniques [53,54,55,56,57]. The proposed method is an essential and effective approach to finding approximate solutions of the nonlinear models having time-fractional derivatives. In the non-linear model (1.1), the time fractional derivative has been taken in the form of Caputo's and Caputo-Fabrizio operator form which have a remarkable advantages in such physical models. The model is solved by using an affective method called modified double Laplace decomposition method (MDLDM) to obtain an approximate solution. The numerical solution of the model has been discuss in the form tables follow by its plots.
The rest of the paper is organized as follows: In Section 2, some main definitions, remarks, important results and a brief discussion of the proposed method is included. The convergence and uniqueness of the proposed method with the help of Banach contraction principle theorems are also studied in Section 3. In Section 4, the problem is discussed in Caputo's and Fabrizio forms and its solutions are obtained in a series form. We consider two numerical examples in Caputo's and Fabrizio form with the application of the proposed method, approximate solutions are obtained in the same section. This section also includes numerical discussion and figures for both the examples. Section 5 concludes the article followed by the Section 6 contain the future work in the manuscript, and Appendix contains the numerical values of the examples in the form of tables and also includes some parameters values.
In this section, we provide some basic definitions, lemmas and remarks regarding to the proposed method. Here also given some basics rules and definition related to double Laplace transform and decomposition method.
Definition 1. [5,35,58] Caputo's fractional derivative of positive real order α>0 of a function ϕ(x,t) is given by function ϕ:(0,∞)→IR is defined by
cDαϕ(x,t)=1Γ(n−α)∫t0(t−s)n−α−1ϕ(x,t)n(x,s)ds,n−1<α≤n, | (2.11) |
where n=[α]+1, [α] denotes the integer part of a real number α, provided the right-hand side is point-wise defined on (0,∞).
Definition 2. [35,59] Let ϕ(x,t)∈H1(a,b), with b>a and α∈(0,1], then the fractional order in sense of Caputo-Fabrizio is define as
CFDαϕ(x,t)=M(α)(2−α)1−α)∫t0ϕ(x,t)n(x,s)exp(−αt−s1−α)ds, | (2.12) |
where CFDαϕ(x,t) is a fractional operator with Mittage-Leffler kernel in Caputo sense. M(α) is called normalization function with properties M(0)=M(1)=1.
Definition 3. [60] For a ϕ(x,t), where x,t>0 lies in xt-plane, the double Laplace transform of the function ϕ(x,t) is defined by
LxLt[ϕ(x,t)]=∫∞0e−px∫∞0e−stϕ(x,t)dtdx, | (2.13) |
where p and s are complex numbers.
Definition 4. [61,62] Applying the definition of double Laplace transform on fractional order derivative with respect t and x in Caputo sense is given by
LxLt{CDαxϕ(x,t)}=pαˉϕ(p,s)−n−1∑k=0pα−1−kLt{∂ku(0,t)∂xk}, | (2.14) |
LxLt{CDβtϕ(x,t)}=sβˉϕ(p,s)−m−1∑k=0sβ−1−kLx{∂kϕ(x,0)∂tk}, | (2.15) |
where n=[α]+1, m=[β]+1.
Definition 5. [61,62] Applying the definition of double Laplace transform on fractional order derivative with respect t and x in Caputo-Fabrizio sense is given by
LxLt{CFDα+rxϕ(x,t)}=M(α)P+α(1−p)[pr+1LxLtϕ(p,s)−n∑k=1pr−kLt{∂kϕ(0,t)∂xk}], | (2.16) |
LxLt{CFDβ+rtϕ(x,t)}=M(β)s+β(1−s)[sr+1LxLtϕ(p,s)−m∑k=1sr−kLx{∂kϕ(x,0)∂tk}], | (2.17) |
where n=[α]+1, m=[β]+1 for r=0,1. For Eq (2.17), with normalization property hold, we can write
LxLt{CFDαtϕ(x,t)}=1s+α(1−s)[sLxLtϕ(x,t)−Lxϕ(x,0)], |
LxLt{CFDβtϕ(x,t)}=1s+β(1−s)[sLxLtϕ(x,t)−sLtϕ(x,0)−Lx∂∂tϕ(x,0)]. |
From the above definitions, we can conclude that
LxLtϕ(x,t)ψ(x,t)=ˉϕ(p,s)ˉψ(p,s)=Lxϕ(x,t)Ltψ(x,t). | (2.18) |
The inverse double Laplace transform L−1xL−1t{ˉϕ(x,t)}=ϕ(x,t), is represented by a complex double integral formula
L−1xL−1t{ˉϕ(x,t)}=12πic+i∞∫c−i∞estd+i∞∫d−i∞epxˉϕ(p,s)dpds, | (2.19) |
where ˉϕ(p,s) is an analytic function ∀p and s defined in the region by the inequalities Re (p)≥c and Re (s)≥d, where c,d∈R to be considered accordingly.
The proposed method MDLDM is hybrid method used widely for non-linear ordinary or partial differential equations. It is the combination of double Laplace and Adomian decomposition method to obtain an approximate solution for problems in hand. To discuss the analysis of the proposed method, we consider the following coupled non-linear problems:
Lϕ(x,t)+Rϕ(x,t))+N1(ϕ,ψ))=f1(x,t),Lψ(x,t)+Rψ(x,t))+N1(ϕ,ψ))=f2(x,t),∀t∈R, | (2.21) |
where L=cDαt(.) is the fractional-time derivative in Caputo's form, R1, R2 are the operators contains the linear terms of Eq (1.1), N1, N2 are the non-linear operators and f1(x,t), f2(x,t) are some external functions. Applying double Laplace on both sides to Eq (2.21), we obtain
LxLt{cDαtϕ}+LxLt{R1ϕ}+LxLt{N1(ϕ,ψ)}=LxLt{f1(x,t)},LxLt{cDαtψ)}+LxLt{R2ψ)}+LxLt{N2(ϕ,ψ)}=LxLt{f2(x,t)}. | (2.22) |
Using the scheme defined above of double Laplace on the nth-derivative in Caputo's form, we obtain
LxLt{ϕ(x,t))}=G1(p,s)−1sαLxLt{R1ϕ(x,t))}−1sαLxLt{N1(ϕ,ψ)},LxLt{ψ(x,t))}=G2(p,s)−1sαLxLt{R1ψ(x,t))}−1sαLxLt{N2(ϕ,ψ)}, | (2.23) |
where
G1(p,s)=sαLxLt{ϕ(x,t))}−n−1∑k=0sα−1−kLx{∂kϕ(x,0)∂tk}+f1(x,t),G2(p,s)=sαLxLt{ψ(x,t))})−n−1∑k=0sα−1−kLx{∂kψ(x,0)∂tk}+f2(x,t). | (2.24) |
Consider the series solution of the form
ϕ(x,t))=∞∑n=0ϕn(x,t),ψ(x,t))=∞∑n=0ψn(x,t), | (2.25) |
let N1 and N2 be the non-linear operators in the model are defined by
N1(ϕ,ψ)=∞∑n=0An,N2(ϕ,ψ)=∞∑n=0Bn, | (2.26) |
where An and Bn are well known Adomian polynomials [50] of the functions ϕ0,ϕ1,ϕ2,… and ψ0,ψ1,ψ2,… respectively. For convince consider An can be described by the following formula:
An(ϕ0,…,ψ0,…)=1n!dndλn[N1n∑k=0λkϕk(x,t)n∑k=0λkψk(x,t)]λ=0. | (2.27) |
Applying an inverse double Laplace on both sides to Eq (2.3):
∞∑n=0ϕn(x,t)=L−1xL−1tG1(p,s)−L−1xL−1t{1sαLxLt{R1ϕ(x,t))}}−L−1xL−1t{1sαLxLt∞∑n=0An},∞∑n=0ψn(x,t)=L−1xL−1tG2(p,s)−L−1xL−1t{1sαLxLt{R2ψ(x,t))}}−L−1xL−1t{1sαLxLt∞∑n=0Bn}, |
equating terms on both sides, we obtain
ϕ0=L−1xL−1t[G1(p,s)],ψ0=L−1xL−1t[G2(p,s)],ϕ1=−L−1xL−1t{1sαLxLt{R1ϕ0}}−L−1xL−1t{1sαLxLt∞∑n=0A0},ψ1=−L−1xL−1t{1sαLxLt{R1ψ0}}−L−1xL−1t{1sαLxLt∞∑n=0B0},ϕ2=−L−1xL−1t{1sαLxLt{R1ϕ1}}−L−1xL−1t{1sαLxLt∞∑n=0A1},ψ2=−L−1xL−1t{1sαLxLt{R1ψ1}}−L−1xL−1t{1sαLxLt∞∑n=0B1},ϕ3=−L−1xL−1t{1sαLxLt{R1ϕ2}}−L−1xL−1t{1sαLxLt∞∑n=0A2},ψ2=−L−1xL−1t{1sαLxLt{R1ψ2}}−L−1xL−1t{1sαLxLt∞∑n=0B2}. |
In general, the following recursive formulas can be obtained, the final solutions can be obtained as
ϕn+1=ϕ(x,0)−L−1xL−1t{1sαLxLt{R1ϕn}}−L−1xL−1t{1sαLxLt∞∑n=0An}, | (2.29) |
ψn+1=ψ(x,0)−L−1xL−1t{1sαLxLt{R1ψn}}−L−1xL−1t{1sαLxLt∞∑n=0Bn}, | (2.30) |
for numerical purposes we take α=1, the exact solution can be obtained as
limn→∞(ϕn,ψn)=(ϕ,ψ). | (2.31) |
Similar procedures can be used to a problem having Caputo-Fabrizio fractional-time derivative to obtain a recursive relation.
In this section, we are discussing the existence and uniqueness of the solutions (2.29) and (2.30) of the general coupled time fractional non-linear partial differential equation (2.21). The following theorems are taken from [63].
Theorem 1. (Uniqueness theorem) For 0<σ<1, the solution (2.29) of Eq (2.21) is a unique solution, where σ=(κ1+κ2+κ3)tα+1Γ(α).
Proof. We create a mapping T : B→ B where B=(C[J],‖.‖) is the Banach space of all continuous functions on J=[0,T] with the norm ‖.‖. We can write Eq (2.29) in the following form:
ϕn+1=ϕ(x,0)+L−1xL−1t{1sαLxLt(Lϕn+Mϕn+Nϕn)}, |
where L=−32∂2ψ∂x2+3λ∂2ϕ∂x2, M=−∂3ϕ∂x3 and N=3ϕ2∂2ψ∂x2−3ψ∂ϕ∂x−3ϕ∂ψ∂x. Let Lϕ, Mϕ and Nϕ are also Lipschitzian with |Lϕ−Lˉϕ|<κ1|ϕ−ˉϕ|, |Mϕ−Mˉϕ|<κ2|ϕ−ˉϕ| and |Nϕ−Nˉϕ|<κ3|ϕ−ˉϕ| where κ1, κ2 and κ3 are Lipschitz constants, ϕ and ˉϕ are the function's distinct values. Now we proceed as follow:
‖Tϕ−Tˉϕ‖=maxt∈J|L−1xL−1t{1sαLxLt(Lϕ+Mϕ+Nϕ)}−L−1xL−1t{1sαLxLt(Lˉϕ+Mˉϕ+Nˉϕ)}|≤maxt∈J|N−1{1sαLxLt(Lϕ−Lˉϕ)}+LxL−1t{1sαLxLt(Mϕ−Mˉϕ)}+LxL−1t{1sαLxLt(Nϕ−Nˉϕ)}|≤maxt∈J|κ1L−1xL−1t{1sαLxLt(ϕ−ˉϕ)}+κ2L−1xL−1t{1sαLxLt(ϕ−ˉϕ)}+κ3L−1xL−1t{1sαLxLt(Nϕ−ˉϕ)}|≤maxt∈J(κ1+κ2+κ3)|L−1xL−1t{1sαLxLt(ϕ−ˉϕ)}|=(κ1+κ2+κ3)t(α−1)Γ(α)‖ϕ−ˉϕ‖. |
The mapping is contraction under the condition 0<σ<1. As a result of the Banach fixed point theorem for contraction, Eq (2.21) has a unique solution. This marks the end of the proof.
Next we discuss convergence analysis of the problem.
Theorem 2. (Convergence theorem) The solution of Eq (2.21) in general forum will be convergence.
Proof. The Banach space of all continuous functions on the interval J with the norm ‖ϕ‖ = maxt∈J‖ϕ‖ is denoted as (C[J],‖.‖). Define the {Sn} sequence of partial sums i.e Sn=∑nj=0. With n≥m, let Sn and Sm be arbitrary partial sums. In this Banach space, we will show that Sn is a Cauchy sequence. We obtain by employing a new formulation of Adomian polynomials.
P(Sn)=ˉAn+n−1∑r1=0ˉAr1,Q(Sn)=ˉAn+n−1∑r2=0ˉAr2, |
now
‖Sn−Sm‖=|n∑j=0ϕj−m∑k=0ϕk|=maxt∈J|n∑j=m+1ϕj|≤maxt∈J|L−1xL−1t{1sαLxLt(n∑j=m+1Lϕj−1)}+L−1xL−1t{1sαLxLt(n∑j=m+1Mϕj−1)}+L−1xL−1t{1sαLxLt(n∑j=m+1Aj−1)}|=maxt∈J|L−1xL−1t{1sαLxLt(n−1∑j=mLϕj)}+L−1xL−1t{1sαLxLt(n−1∑j=mMϕj)}+L−1xL−1t{1sαLxLt(n−1∑j=m(Aj))}|≤maxt∈J|L−1xL−1t{1sαLxLt(n−1∑j=mLSn−1−LSm−1)}+L−1xL−1t{1sαLxLt(n−1∑j=mMSn−1−MSm−1)}+L−1xL−1t{1sαLxLt(n−1∑j=mNSn−1−NSm−1)}|≤κ1maxt∈J|L−1xL−1t{1sαLxLt(Sn−1−Sm−1)}|+κ2maxt∈J|L−1xL−1t{1sαLxLt(Sn−1−Sm−1)}|+κ3maxt∈J|L−1xL−1t{1sαLxLt(Sn−1−Sm−1)}|=(κ1+κ2+κ3)tα−1Γ(α)‖Sn−1−Sm−1‖. |
Choosing n=m+1, then
‖Sm+1−Sm‖≤σ‖Sm−Sm−1‖≤σ2‖Sm−1−Sm−2‖≤⋯⋯≤σm‖S1−S0‖, |
with σ=(κ1+κ2+κ3)tα−1Γ(α), by using the following triangular inequality
‖Sn−Sm‖≤‖Sm−Sm+1‖≤‖Sm+1−Sm+2‖≤⋯⋯≤σm‖S1−S0‖≤(σm+σm+1+⋯+σn)‖S1−S0‖≤σm(1+σ+σ2+⋯+σn−m−1)‖S1−S0‖≤σm(1−σn−m1−σ)‖ϕ1‖. |
Now by definition 0<σ<1, we have 1−σn−m<1, thus we have
‖Sn−Sm‖≤σm1−σmaxt∈J‖ϕ1‖, | (3.1) |
and also as |ϕ|<∞ (ϕis bounded), therefore, ‖Sn−Sm‖→0, hence Sn is a Cauchy sequence in the Banach space B, so the series ∑nj=0ϕj is convergent.
Remark 1. Theorems 1 and 2 can also be applicable to the solution (2.30) for its uniqueness and convergent.
In this section, we illustrate some examples on Eq (1.1) with time-fractional derivatives in the form of Caputo and Caputo-Fabrizio operators in each case, and apply the proposed method discussed in this section with (f1,f2)=0.
Example 1. Consider the following (mCKdV)[20] in Caputo's form
cDαtϕ+3ϕ2∂ϕ∂x−32∂2ψ∂x2−3ϕ∂ψ∂x−3ψ∂ϕ∂x+3λ∂ϕ∂x−12∂3ϕ∂x3=0,cDαtψ+3ψ∂ψ∂x+3∂ϕ∂x∂ψ∂x−3ϕ2∂ψ∂x−3λ∂ψ∂x+∂3ψ∂x3=0,0<α≤1,t>0, | (4.1) |
with initial conditions
ϕ(x,0)=r12k+ktanh(kx),ψ(x,0)=λ(r1+k)2r1+r1tanh(kx). | (4.2) |
The exact solution of Eq (4.1) for α=1 is [20]
ϕ(x,t)=r12k+ktanh(ξ),ψ(x,t)=λ(r1+k2r1+r1tanh(ξ), | (4.3) |
where
ξ=kx+k4(−6λ−4k2−kλr1+3r21k2)t. |
Apply the modified double Laplace transform decomposition (MDLDM) scheme discussed in this section to Eq (4.1) and single Laplace transform to Eq (4.2), we obtain the following recurrence relations:
ϕ0=G1(p,s),ϕn+1=t(n+1)αΓ((n+1)α+1)[−3An+32ψnxx+3Bn+3Cn−3λϕnx+12ϕnxxx],ψ0=G2(p,s),ψn+1=t(n+1)αΓ((n+1)α+1)[−3Dn−3En+3Fn+3λψnx−ψnxxx], | (4.4) |
for n≥0. The Adomian polynomials An,⋯Fn,n=1,2,3, for nonlinearity appears in Eq (4.4) are calculated by using the general rules shown in Eq (2.27)
A0=ϕ20ϕ0x,A1=2ϕ0ϕ1ϕ0x+ϕ20ϕ1x,A2=2ϕ0ϕ2ϕ0x+ϕ21ϕ0x+2ϕ0ϕ1ϕ1x+ϕ20ϕ2x,B0=ϕ0ψ0x,B1=ϕ1ψ0x+ϕ0ψ1x,B2=ϕ2ψ0x+ϕ1ψ1x+ϕ0ψ2x,C0=ψ0ϕ0x,C1=ψ1ϕ0x+ψ0ϕ1x,C2=ψ2ϕ0x+ψ1ϕ1x+ψ0ϕ2x,D0=ψ0ψ0x,D1=ψ1ψ0x+ψ0ψ1x,D2=ψ2ψ0x+ψ1ψ1x+ψ0ψ2x,E0=ϕ0xψ0x,E1=ϕ1xψ0x+ϕ0xψ1x,E2=ϕ2xψ0x+ϕ1xψ1x+ϕ0xψ2x,F0=ϕ20ψ0x,F1=2ϕ0ϕ1ψ0x+ϕ20ψ1x,F2=2ϕ0ϕ2ψox+ϕ21ψ0x+2ϕ0ϕ1ψ1x+ϕ20ψ2x. | (4.5) |
For more details, one can see [51,52,64]. Plugging Eq (4.5) in Eq (4.4), we obtain
ϕ0=r12k+ktanh(kx),ψ0=λ(r1+k)2r1+r1tanh(kx),ϕ1=tα4r1Γ(α+1)[(3r31−4r1k4−6r1λk2+6λk3)sech2(kx)],ψ1=tα4kΓ(α+1)[(−4k4r1−6λk3+6λk2r1+3r31)sech2(kx)],ϕ2=−t2α(8r21k)Γ(2α+1)[η1tanh(kx)sech2(kx)],ψ2=t2α(16r1k2)Γ(2α+1)[(a1tanh(kx)(a2cosh(2kx))+a3tanh(kx)))sech4(kx)],ϕ3=t3α(32r31k)Γ(3α+1)[(2b0+3sech2(kx)(2r1tanh(kx)(b3sech2(kx))+b2sech2(kx)))sech2(kx)],ψ3=t3α(32r21k3)Γ(3α+1)[3c1c2tanh(kx)sech4(kx)(2c0+3sech2(kx))(c3sech2(kx)−sech2(kx))], |
where the coefficients given above can be seen in Appendix. It should be noted that, other terms can be calculated in the similar way. The final solutions can be obtained
ϕ(x,t)=∞∑n=0ϕ(x,t),ψ(x,t)=∞∑n=0ψn(x,t). | (4.6) |
For numerical purposes we take α=1, the exact solution can be obtained as
limn→∞(ϕn,ψn)=(ϕ,ψ). |
For the numerical illustrations, Figure 1 depicts obtained solutions ϕ and ψ in Eq (4.6) associated with the modified coupled Korteweg-de Vries (mCKdV) Eq (4.1). Thus the waves solutions ϕ(x,t) and ψ(x,t) in Figure 1(a), (b) reveals the evolution of the shock excitations. The three-dimensional profiles of ϕ(x,t) and ψ(x,t) in Figure 1(c), (d) manifest sudden changes in the potential fields for the spatial variables −10≤x≤10. We observe that the mCKdV equations describe nonlinear evolution of the waves, suffered by weak dispersion effect in an inviscid fluid. Thus the nonlinear steeping attributed to temporal evolution excites the shocks. For the impact of the time fraction coefficient α on the waves characteristics, we have displayed solutions (4.6) versus x at α=0.1,0.2,0.4,1, see Figure 2(a), (b). Notice that a degree enhancement in α modifies the steeping effect and therefore rise the waves amplitudes. Similarly Figure 2(c), (d) show the nature of the MDLDM method in Caputo's sense for different values of α and time when spatial variable x is kept constant of the Eq (4.6) in Example 1. The wave solutions are revealing the propagation of monotonic shocks. Figure 3(a), (b) show the error plots of the Table 1 (see Appendix).
Example 2. Consider the following example having time fractional derivative in Caputo-Fabrizio (CF) form
CFDαtϕ+3ϕ2∂ϕ∂x−32∂2ψ∂x2−3ϕ∂ψ∂x−3ψ∂ϕ∂x+3λ∂ϕ∂x−12∂3ϕ∂x3=0,CFDαtψ+3ψ∂ψ∂x+3∂ϕ∂x∂ψ∂x−3ϕ2∂ψ∂x−3λ∂ψ∂x+∂3ψ∂x3=0,0<α≤1,t>0. | (4.7) |
With the help of Eq (2.17) and the procedure used in Example 1, we can obtain the following series solutions in Caputo-Fabrizio form
ϕ0=r12k+ktanh(kx),ψ0=λ(r1+k)2r1+r1tanh(kx),ϕ1=1+α(t−1)4r1[(3r31−4r1k4−6r1λk2+6λk3)sech2(kx)],ψ1=1+α(t−1)4k[(−4k4r1−6λk3+6λk2r1+3r31)sech2(kx)],ϕ2=−h1(t)8r21k[η1tanh(kx)sech2(kx)],ψ2=h1(t)(16r1k2)[(a1tanh(kx)(a2cosh(2kx))+a3tanh(kx)))sech4(kx)],ϕ3=h2(t)(32r31k)[(2b0+3sech2(kx)(2r1tanh(kx)(b3sech2(kx))+b2sech2(kx)))sech2(kx)],ψ3=h2(t)(32r21k3)[(2c0+3sech2(kx)(c1tanh(kx)(c3sech2(kx)−sech2(kx)(3c2sech2(kx)))))sech2(kx)], |
where
h1(t)=1/2α2t2+α2−2α+1−2α2t+2αt,h2(t)=3/2α3t2−3/2α2t2+α3−3α2+3α−1−3α3t+6α2t−3αt−1/6α3t3. |
Other terms can be calculated in the similar way. The general solutions can be obtained in the form
ϕ(x,t)=∞∑n=0ϕn(x,t),ψ(x,t)=∞∑n=0ψn(x,t). | (4.8) |
For numerical purposes we take α=1, the exact solution can be obtained as
limn→∞(ϕn,ψn)=(ϕ,ψ). |
The shock wave solutions ϕ(x,t) and ψ(x,t) in Eq (4.8) for the modified coupled Korteweg-de Vries (mCKdV) Eq 4.1 with Caputo's Fabrizio operators (CF) are depicted in Figure 4(a), (b) against x. Obviously, the approximate Fabrizio solution (red stared dotted and blue dashed, black dotted curves) in both the plots (a) and (b) by MDLDM method is approaching to the exact solution (black solid curve) of the Eq (4.8) in Example 2, the corresponding plots in three dimension are shown in Figure 4(c), (d).
Figure 5(a), (b) show the nature of the MDLDM method in Fabrizio's sense for different values of α and time when spatial variable x is kept constant of the Eq (4.6) in Example 2. For the purpose of error analysis, we have depicted the absolute of the difference of exact and approximate solutions |Exact−(ϕ(x,t)ψ(x,t))| and for mCKdV equation, see Figure 6(a), (b). Notice that the difference of the wave solutions from the exact solutions is much small. It signifies the importance of the MDLDM for the approximate solutions. The observed errors are inserted in Table 2 (see Appendix) and their related plots are shown in Figure 6(a), (b) which shows the effectiveness of our proposed method to such non-linear modified coupled Korteweg-de Vries (mCKdV) equations. A comparative analysing of the problem in Tables 3–6 (see Appendix) between the two methods (MDLDM and q-HATM[20]) are shown. By analysing these tables, one can conclude easily the validation and accuracy of the proposed method over the q-HATM. Figure 7(a)–(d) are also show a remarkable results for the presented method.
We have studied analytically the mCKdV with Caputo's and Caputo-Fabrizio (CF) derivatives using MDLDM. The proposed method is applied to the mCKdV system and approximate results are obtained in the form of series solutions by considering examples. The error analysis of the proposed method is also discussed. It is observed that the suggested scheme is one of the vigorous tools to investigate nonlinear problems. The main advantage of the suggested method is to analyze analytical solutions of the considered problem without using linearization and discretization. For validation, two examples in Caputo's and CF form are studied numerically and the results are compared with the numerical results with a physical interpretation. When non-integer order was employed in models including non-integer order derivatives, many scientists were less interested. For non-integer order fractional time derivative with singular and non-singular kernels of the mKdV equations, the MDLDM can be used. The MDLDM approach for handling nonlinear evolutionary equations was shown to have a broader applicability in this work. Physical meaning was given to the parameters in the resulting travelling wave solution. For varied values of the parameters, a three-dimensional simulation of wave behaviour is built, which alters the wave profile of the equation.The wave dynamics are discussed with the help of simulation. The results show that this strategy worked. The new wave solution presented in this work can open up new avenues for future research.
A modified coupled time fractional KdV equation with Caputo's and Caputo-Fabrizio operators is considered in this manuscript. The characteristics wave profiles of the solution to the equation show some interesting behaviour especially when altering in the parameters. These interesting behaviours may be more interesting to transform the modified coupled time fractional KdV to modified coupled Schrodinger and sine-Gordon equations with Caputo's and Caputo-Fabrizio operators.
The authors are grateful to the Spanish Government for its support through grant RTI2018-094336-B-100 (MCIU/AEI/FEDER, UE) and to the Basque Government for its support through Grant IT1207-19.
It is declared that all the authors have no conflict of interest regarding this manuscript.
η1=(9r61+r41(36k2λ−24k4)−36r31k3λ+4r21k4(2k2+3λ)2−24r1k5λ(2k2+3λ)+36k6λ2),a1=−(3r31−4r1k4+6r1λk2−6λk3)),a2=((3r31−4r1k4+6r1λk2−6λk3)+3r31+4r1k4+6r1λk2−6λk3),a3=8r1k4((3r31−4r1k4−66r1λk2+66λk3)+18r1λ(k−r1)),b0=(3r31−4r1k4)3−216r1λ2k4(r1−k)2(r21+4k4)+36r21λk2(r1−k)(3r41−24r21k4−16k8)−432λ3k6(r1−k)3,b2=36r1λ2k4(r1−k)2(3r21+14k4)−6r21λk2(r1−k)(9r41−60r21k4−64k8)−3r31(r21−2k4)(3r21−4k4)2+216λ3k6(r1−k)3,b3=2r1g((3r31−4r1k4)2+60r1λk2(r1−k)(3r21−20k4)+2592r1λk6(r1−k)+180λ2k4(r1−k)2g),c0=(3r31−4r1k4+6r1λk2−6λk3)3,c1=−36r1λ2k4(r1−k)2(9r21−124k4)−18r21λk2(r1−k)(9r41−152r21k4+1296k8)−r31(3r21−4k4)2(3r21−20k4)−216λ3k6(r1−k)3+6r1k4,c2=(3r31−4r1k4)2−4r1λk2(r1−k)(105r21−3692k4)−11520r1λk6(r1−k)−780λ2k4(r1−k)2,c3=8r1r1−kλ(9r31+216r1k4−116r1k4+18λk2(r1−k)). |
Error analysis tables:
Please notes that, for error analysis, we consider α=1, b=k=0.5, λ=1.5, n = 3 and h = -1.
t | x | Exact | ϕ | ∣ Exact−ϕ∣ | Exact | ψ | ∣ Exact−ψ∣ |
0.01 | -10 | 4.7725E(-05) | 4.7720E(-05) | 1.1932E(-11) | 1.0000E(-01) | 1.0000E(-01) | 2.5353E(-05) |
0.02 | . | 5.0172E(-05) | 5.0172E(-05) | 1.9286E(-10) | 1.0019E(-01) | 1.0001E(-01) | 5.0706E(-05) |
0.03 | . | 5.2744E(-05) | 5.2743E(-05) | 9.8635E(-10) | 1.0001E(-01) | 1.0015E(-01) | 7.6059E(-05) |
0.01 | -5 | 7.0336E(-03) | 7.0336E(-03) | 1.4449E(-09) | 1.0070E(-01) | 1.0107E(-01) | 3.7126E(-03) |
0.02 | . | 7.3915E(-03) | 7.3915E(-03) | 1.3553E(-09) | 1.0074E(-01) | 1.0148E(-01) | 7.4247E(-03) |
0.03 | . | 7.7676E(-03) | 7.7675E(-03) | 4.8942E(-08) | 1.0078E(-01) | 1.0189E(-01) | 1.1136E(-02) |
0.01 | 0 | 5.1250E(-01) | 5.1266E(-01) | 1.6117E(-04) | 1.5125E(-01) | 1.6518E(-01) | 1.3931E(-01) |
0.02 | . | 2.4980E(-01) | 5.2627E(-01) | 1.2893E(-04) | 1.5250E(-01) | 1.8030E(-01) | 2.7798E(-01) |
0.03 | . | 5.3740E(-01) | 5.4178E(-01) | 4.3515E(-03) | 1.5374E(-01) | 1.9549E(-01) | 4.1601E(-01) |
0.01 | 5 | 9.9360E(-01) | 9.9363E(-01) | 4.5887E(-09) | 1.9936E(-01) | 1.9973E(-01) | 3.7128E(-03) |
0.02 | . | 9.9394E(-01) | 9.9394E(-01) | 4.8954E(-08) | 1.9939E(-01) | 2.0014E(-01) | 7.4254E(-03) |
0.03 | . | 9.9423E(-01) | 9.9423E(-01) | 2.0582E(-07) | 1.9942E(-01) | 2.0054E(-01) | 1.1138E(-02) |
0.01 | 10 | 9.9996E(-01) | 9.9996E(-01) | 1.1698E(-11) | 2.0000 E(-01) | 2.0000E(-01) | 2.5353E(-05) |
0.02 | . | 9.9996E(-01) | 9.9996E(-01) | 1.8532E(-10) | 2.0000E(-01) | 2.0000E(-01) | 5.0707E(-05) |
0.03 | . | 9.9996E(-01) | 9.9996E(-01) | 9.2900E(-10) | 2.0000E(-01) | 2.0000E(-01) | 7.6061E(-05) |
t | x | Exact | ϕ | ∣ Exact−ϕ∣ | Exact | ψ | ∣ Exact−ψ∣ |
0.01 | -10 | 6.7725E(-04) | 4.7520E(-05) | 1.4932E(-11) | 1.0004E(-01) | 1.0040E(-01) | 2.5356E(-05) |
0.02 | . | 4.3172E(-04) | 5.0152E(-05) | 1.9276E(-10) | 1.0019E(-01) | 1.0001E(-01) | 5.0706E(-05) |
0.03 | . | 6.7440E(-04) | 5.2543E(-05) | 9.8637E(-10) | 1.0001E(-01) | 1.0015E(-01) | 7.6056E(-05) |
0.01 | -5 | 7.0346E(-04) | 7.5336E(-03) | 1.4479E(-09) | 1.0070E(-01) | 1.0107E(-01) | 3.7126E(-03) |
0.02 | . | 7.3945E(-03) | 7.3515E(-03) | 1.3557E(-09) | 1.0743E(-01) | 1.0148E(-01) | 7.4246E(-03) |
0.03 | . | 7.7655E(-03) | 7.7575E(-03) | 4.8946E(-08) | 1.0078E(-01) | 1.0189E(-01) | 1.1166E(-02) |
0.01 | 0 | 5.1550E(-01) | 5.5266E(-01) | 1.6116E(-04) | 1.5125E(-01) | 1.6518E(-01) | 1.6931E(-01) |
0.02 | . | 2.4980E(-01) | 5.2527E(-01) | 1.2896E(-04) | 1.5260E(-01) | 1.8030E(-01) | 2.7768E(-01) |
0.03 | . | 5.3740E(-01) | 5.4678E(-01) | 4.3516E(-03) | 1.5374E(-01) | 1.9534E(-01) | 4.1606E(-01) |
0.01 | 5 | 9.9360E(-01) | 9.6363E(-01) | 4.5867E(-09) | 1.9936E(-01) | 1.9973E(-01) | 3.6128E(-03) |
0.02 | . | 9.9394E(-01) | 9.6394E(-01) | 4.8964E(-08) | 1.9939E(-01) | 2.0014E(-01) | 7.4654E(-03) |
0.03 | . | 9.9423E(-01) | 9.6423E(-01) | 2.0586E(-07) | 1.9942E(-01) | 2.0054E(-01) | 1.1136E(-02) |
0.01 | 10 | 9.9996E(-01) | 9.6996E(-01) | 1.1696E(-11) | 2.0000 E(-01) | 2.0000E(-01) | 2.5653E(-05) |
0.02 | . | 9.9996E(-01) | 9.6996E(-01) | 1.8562E(-10) | 2.0000E(-01) | 2.0000E(-01) | 4.0707E(-05) |
0.03 | . | 9.9996E(-01) | 9.96996E(-01) | 9.2906E(-10) | 2.0000E(-01) | 2.0000E(-01) | 7.6555E(-05) |
t | x | Exact [18] | q-HATM[20] | |Exact−q−HATM| | Exactϕ | MDLDM | |Exact−ϕ| |
0.1 | 5.0 | 0.99360 | 0.98290 | 1.0700 ×10−03 | 1.00000 | 1.00000 | 4.6000×10−09 |
0.2 | 0.99390 | 0.97230 | 2.1600 ×10−02 | 1.00000 | 1.000000 | 4.9600×10−09 | |
0.3 | 0.99420 | 0.96160 | 4.0000 ×10−03 | 1.00000 | 1.00000 | 2.0580×10−09 | |
0.1 | 6.0 | 0.99760 | 0.99370 | 8.0000×10−03 | 0.99760 | 0.99760 | 1.0970×10−08 |
0.2 | 0.99780 | 0.98970 | 1.2100×10−02 | 0.99780 | 0.99780 | 5.3000×10−08 | |
0.3 | 0.99790 | 0.98580 | 3.3660×10−05 | 0.99790 | 0.99790 | 7.7000×10−10 | |
0.1 | 7.0 | 0.99910 | 0.99770 | 1.5000×10−03 | 0.99910 | 0.99910 | 2.4000×10−10 |
0.2 | 0.99920 | 0.99620 | 3.0000 ×10−03 | 0.99920 | 0.99920 | 3.7300×10−09 | |
0.3 | 0.99920 | 0.99470 | 4.5000×10−03 | 0.99920 | 0.99920 | 1.8620×10−08 | |
0.1 | 8.0 | 0.99970 | 0.9991 | 5.0000 ×10−04 | 0.99970 | 0.99970 | 8.6000×10−11 |
0.2 | 0.99970 | 0.99860 | 1.1000 ×10−03 | 0.99970 | 0.99970 | 1.3660 ×10−09 | |
0.3 | 0.99970 | 0.99810 | 1.6000×10−03 | 0.99990 | 0.99970 | 6.8440×10−09 | |
0.1 | 9.0 | 0.99990 | 9.99700 | 1.9900 ×10−04 | 0.99990 | 0.99990 | 3.2000×10−11 |
0.2 | 0.99990 | 9.99500 | 4.0100 ×10−04 | 0.99990 | 0.99990 | 5.0300×10−10 | |
0.3 | 0.99990 | 0.999300 | 6.06200×10−04 | 0.99990 | 0.99990 | 2.5230×10−09 | |
0.1 | 10 | 1.00000 | 0.99990 | 7.3200 ×10−05 | 1.00000 | 1.00000 | 1.1700×10−11 |
0.2 | 1.00000 | 0.99980 | 1.4760×10−04 | 1.00000 | 1.00000 | 1.8530×10−10 | |
0.3 | 1.00000 | 0.99980 | 2.2310×10−04 | 1.00000 | 1.00000 | 9.2900×10−09 |
t | x | Exact [20] | q−HATM [20] | ∣ Exact−q-HATM∣ | Exactϕ | MDLDM | ∣ Exact−ϕ∣ |
0.1 | 5.0 | 1.99360 | 1.98290 | 1.0700 ×10−03 | 1.99360 | 1.99730 | 3.7000×10−03 |
0.2 | 0.99390 | 1.97230 | 2.1600 ×10−02 | 1.99390 | 2.00140 | 7.4000×10−03 | |
0.3 | 1.99420 | 1.96160 | 3.2700×10−02 | 1.99420 | 2.00540 | 1.1100×10−02 | |
0.1 | 6.0 | 1.99760 | 1.99370 | 4.0000×10−03 | 1.99760 | 1.99900 | 1.4000 ×10−03 |
0.2 | 1.99780 | 1.98970 | 8.0000 ×10−02 | 1.99780 | 2.00050 | 2.8000×10−03 | |
0.3 | 1.99790 | 1.98580 | 1.2100×10−02 | 1.99790 | 2.00200 | 4.1000×10−03 | |
0.1 | 7.0 | 1.99910 | 1.99770 | 1.5000×10−03 | 1.99910 | 1.99960 | 5.0000×10−04 |
0.2 | 1.99920 | 1.99620 | 3.0000 ×10−03 | 1.99920 | 2.00020 | 1.0000×10−03 | |
0.3 | 1.99920 | 1.99470 | 4.5000×10−03 | 1.99920 | 2.00070 | 1.5000×10−03 | |
0.1 | 8.0 | 1.99970 | 1.99910 | 5.0000 ×10−04 | 1.99970 | 1.99990 | 1.8720×10−04 |
0.2 | 1.99970 | 1.99860 | 1.1000 ×10−03 | 1.99970 | 2.00010 | 3.7450×10−04 | |
0.3 | 1.99970 | 1.99810 | 1.6000×10−03 | 1.99990 | 2.00030 | 5.6170×10−04 | |
0.1 | 9.0 | 1.99990 | 9.99700 | 1.9900 ×10−04 | 1.99990 | 2.00000 | 6.8900×10−05 |
0.2 | 1.99990 | 9.99500 | 4.0100 ×10−04 | 1.99990 | 2.00000 | 1.3780×10−04 | |
0.3 | 1.99990 | 1.99930 | 6.0620×10−04 | 1.99990 | 2.00000 | 2.0670×10−04 | |
0.1 | 10 | 2.00000 | 1.99990 | 7.3200 ×10−05 | 2.00000 | 2.00000 | 2.5350×10−05 |
0.2 | 2.00000 | 1.99980 | 1.4760×10−04 | 2.00000 | 2.00000 | 5.0710×10−05 | |
0.3 | 2.00000 | 1.99980 | 2.2310×10−04 | 2.00000 | 2.00000 | 7.6060×10−05 |
t | x | Exact [18] | q-HATM[20] | ∣ Exact−q-HATM∣ | Exactϕ | MDLDM | ∣ Exact−ϕ∣ |
0.1 | 5.0 | 0.99363 | 0.995590 | 1.9616 ×10−03 | 0.99363 | 0.99363 | 2.6743×10−07 |
0.2 | 0.99394 | 0.99780 | 3.8576 ×10−03 | 0.99394 | 0.99394 | 2.1272×10−06 | |
0.3 | 0.99423 | 0.99992 | 5.6881×10−03 | 1.00000 | 0.99423 | 7.1386×10−06 | |
0.1 | 6.0 | 0.99765 | 0.99838 | 7.2768×10−04 | 0.99765 | 0.99765 | 1.0070×10−07 |
0.2 | 0.99776 | 0.99919 | 4.3080×10−03 | 0.99776 | 0.99776 | 8.0150×10−07 | |
0.3 | 0.99787 | 0.99998 | 2.1094×10−04 | 0.99787 | 0.99787 | 2.6891×10−07 | |
0.1 | 7.0 | 0.99913 | 0.99940 | 2.6852 ×10−04 | 0.99913 | 0.99913 | 3.7495×10−08 |
0.2 | 0.99918 | 0.9997 | 5.2796 ×10−04 | 0.99910 | 0.99910 | 2.9814×10−07 | |
0.3 | 0.99922 | 0.99999 | 7.7833×10−04 | 0.99922 | 0.99922 | 1.0002×10−06 | |
0.1 | 8.0 | 0.99980 | 0.99940 | 5.0000 ×10−04 | 0.99970 | 0.99970 | 8.6000×10−08 |
0.2 | 0.99980 | 0.99864 | 1.1000 ×10−03 | 0.99970 | 0.99970 | 1.3660 ×10−07 | |
0.3 | 0.99980 | 0.99840 | 1.6000×10−04 | 0.99990 | 0.99970 | 6.8440×10−06 | |
0.1 | 9.0 | 0.99988 | 0.99992 | 3.6397 ×10−05 | 0.99988 | 0.99988 | 5.1053×10−08 |
0.2 | 0.99989 | 0.99996 | 7.1561×10−05 | 0.99989 | 0.99989 | 4.0593×10−08 | |
0.3 | 0.99989 | 0.999900 | 1.0549×10−05 | 0.99989 | 00.99989 | 1.3618×10−07 | |
0.1 | 10 | 0.99996 | 0.99996 | 1.3392 ×10−05 | 0.99996 | 0.99996 | 1.8793×10−09 |
0.2 | 0.99997 | 0.99996 | 2.633×10−05 | 0.99996 | 0.99996 | 1.4943×10−08 | |
0.3 | 0.99996 | 1.00000 | 3.8815×10−05 | 0.99996 | 0.99996 | 5.0127×10−08 |
t | x | ExactH | q−HATM [18] | ∣ Exact−q-HATM∣ | Exactϕ | MDLDM | ∣ Exact−ϕ∣ |
0.1 | 5.0 | 1.99360 | 1.99560 | 1.9616 ×10−03 | 1.99360 | 1.99730 | 3.7125×10−03 |
0.2 | 0.99390 | 1.99780 | 3.8577×10−03 | 1.99390 | 2.00140 | 7.4231×10−03 | |
0.3 | 1.99420 | 1.99990 | 5.6882×10−03 | 1.99420 | 2.00540 | 1.1213×10−02 | |
0.1 | 6.0 | 1.99760 | 1.99840 | 7.2768×10−04 | 1.99760 | 1.99900 | 1.3774×10−03 |
0.2 | 1.99780 | 1.99920 | 1.4308×10−04 | 1.99780 | 2.00050 | 2.7542×10−03 | |
0.3 | 1.99790 | 2.00000 | 2.1095×10−04 | 1.99790 | 2.00200 | 41.2970×10−03 | |
0.1 | 7.0 | 1.99910 | 1.99940 | 2.6852×10−04 | 1.99910 | 1.99960 | 5.0831×10−04 |
0.2 | 1.99920 | 1.99970 | 5.2797×10−04 | 1.99920 | 2.00020 | 1.0164×10−03 | |
0.3 | 1.99920 | 2.00000 | 7.7833×10−04 | 1.99920 | 2.00070 | 1.5240×10−03 | |
0.1 | 8.0 | 1.99970 | 1.99980 | 9.8896×10−05 | 1.99970 | 1.99990 | 1.8721×10−04 |
0.2 | 1.99970 | 1.99990 | 1.9444 ×10−04 | 1.99970 | 2.00010 | 3.7435×10−04 | |
0.3 | 1.99970 | 2.00000 | 2.8665×10−03 | 1.99990 | 2.00030 | 5.6130×10−04 | |
0.1 | 9.0 | 1.99990 | 1.99990 | 3.6397 ×10−05 | 1.99990 | 2.00000 | 6.8902×10−05 |
0.2 | 1.99990 | 2.00000 | 7.1561×10−05 | 1.99990 | 2.00000 | 1.3777×10−04 | |
0.3 | 1.99990 | 2.00000 | 1.0549×10−04 | 1.99990 | 2.00001 | 2.0658×10−04 | |
0.1 | 10 | 2.00000 | 2.00000 | 1.3392 ×10−05 | 2.00000 | 2.00000 | 2.5350×10−05 |
0.2 | 2.00000 | 2.00000 | 2.6330×10−04 | 2.00000 | 2.00000 | 5.0692×10−05 | |
0.3 | 2.00000 | 2.00000 | 3.8815×10−05 | 2.00000 | 2.00000 | 7.7.6010×10−05 |
[1] |
J. Ruan, H. B. Yuan, H. M. Li, H. Y. Xu, Design and application of vibratory fatigue test rig for high speed railway OCS dropper, China Railway, 2020 (2020), 117–122. https://doi.org/10.19549/j.issn.1001-683x.2020.08.117 doi: 10.19549/j.issn.1001-683x.2020.08.117
![]() |
[2] |
L. K. Pan, L. M. Chen, H. B. Zhang, C. Xu, C. Z. Yang, T. Xing, Research on vibration fatigue test method and device of integrated dropper, Electr. Railway, 31 (2020), 73–76. https://doi.org/10.19587/j.cnki.1007-936x.2020z2.017 doi: 10.19587/j.cnki.1007-936x.2020z2.017
![]() |
[3] |
P. H. Peng, L. M. Chen, W. Wang, F. He, The effect of frequency and amplitude of dropper on its fatigue life, J. Railway Sci. Eng., 16 (2019), 471–477. https://doi.org/10.19713/j.cnki.43-1423/u.2019.02.025 doi: 10.19713/j.cnki.43-1423/u.2019.02.025
![]() |
[4] |
X. Li, W. Z. Liu, C. Sun, J. H. Yi, M. Xu, Study on current collection characteristics of catenary based on new type of dropper, Railway Stand. Design, 65 (2021), 128–131. https://doi.org/10.13238/j.issn.1004-2954.202001060004 doi: 10.13238/j.issn.1004-2954.202001060004
![]() |
[5] |
W. H. Zhang, G. M. Mei, X. J. Wu, L. Q. Chen, A study on dynamic behaviour of pantographs by using hybrid simulation method, Proc. I. Mech. Eng. Part F, 219 (2005), 189–199. https://doi.org/10.1243/095440905X8880 doi: 10.1243/095440905X8880
![]() |
[6] |
H. Zhao, X. H. Xiao, G. F. Qi, H. Y. Xu, H. M. Li, Analysis of fatigue life of catenary dropper for high-speed railway, Eng. J. Wuhan Univ., 52 (2019), 351–357. https://doi.org/10.14188/j.1671-8844.2019-04-011 doi: 10.14188/j.1671-8844.2019-04-011
![]() |
[7] | Q. Zhang, Research on fatigue characteristics of catenary droppers of high-speed railway, Shijiazhuang: Shijiazhuang Tiedao University, 2023. https://doi.org/10.27334/d.cnki.gstdy.2022.000442 |
[8] | D. F. Chen, Analysis on the operation characteristics of the integral dropper of high-speed rail catenary and discussion on countermeasures, Beijing: China Academy of Railway Sciences, 2020. https://doi.org/10.27369/d.cnki.gtdky.2020.000049 |
[9] |
L. M. Chen, J. Sun, L. K. Pan, F. He, Analysis of dropper stress in a catenary system for a high-speed railway, Math. Probl. Eng., 2022 (2022), 1–7. https://doi.org/10.1155/2022/9663767 doi: 10.1155/2022/9663767
![]() |
[10] |
F. He, D. D. Guo, The effects of load location on dropper stress in a catenary system for a high-speed railway, Math. Probl. Eng., 2020 (2020), 1–10. https://doi.org/10.1155/2020/7986141 doi: 10.1155/2020/7986141
![]() |
[11] |
L. M. Chen, P. H. Peng, F. He, Fatigue life analysis of dropper used in pantograph-catenary system of high-speed railway, Adv. Mech. Eng., 10 (2018), 1–10. https://doi.org/10.1177/1687814018776135 doi: 10.1177/1687814018776135
![]() |
[12] | Y. Zhong, A new approach to desired contact force between pantograph and overhead contact line system based on sliding electrical contact fundamental mechanism, Cheng Du: Southwest Jiaotong University, 2020. https://doi.org/10.27414/d.cnki.gxnju.2020.002536 |
[13] |
J. B. Guo, S. P. Yang, G. S. Gao, Study on active control of high-speed-train pantographs, J. China Railway Soc., 26 (2004), 41–45. https://doi.org/10.3321/j.issn:1001-8360.2004.04.009 doi: 10.3321/j.issn:1001-8360.2004.04.009
![]() |
[14] |
L. M. Chen, Study on dynamic force of integral dropper of catenary under action of high-speed pantograph, China Railway Sci., 39 (2018), 86–92. https://doi.org/10.3969/j.issn.1001-4632.2018.03.12 doi: 10.3969/j.issn.1001-4632.2018.03.12
![]() |
[15] |
S. G. Zhang, A finite difference method for second order ordinary differential equation of initial-value problem, J. Chongqing Univ. Tech., 26 (2012), 110–112. https://doi.org/10.3969/j.issn.1674-8425-B.2012.08.023 doi: 10.3969/j.issn.1674-8425-B.2012.08.023
![]() |
[16] | A. G. Costello, Theory of wire rope, New York: Springer, 1997. https://doi.org/10.1007/978-1-4612-1970-5 |
[17] |
Z. G. Yu, Z. R. Ge, Z. S. Niu, Z. Y. Zhu, Discussion on causes of failures and optimized schemes for OCS integrated droppers for high speed railway, Electr. Railway, 31 (2020), 10–14. https://doi.org/10.19587/j.cnki.1007-936x.2020.01.003 doi: 10.19587/j.cnki.1007-936x.2020.01.003
![]() |
[18] | H. Li, M. Yazdi, Advanced decision-making methods and applications in system safety and reliability problems, Switzerland: Springer, 2022. https://doi.org/10.1007/978-3-031-07430-1 |
1. | Sayed Saifullah, Amir Ali, Kamal Shah, Chanon Promsakon, Investigation of Fractal Fractional nonlinear Drinfeld–Sokolov–Wilson system with Non-singular Operators, 2022, 33, 22113797, 105145, 10.1016/j.rinp.2021.105145 | |
2. | Sadia Arshad, Iram Saleem, Ali Akgül, Jianfei Huang, Yifa Tang, Sayed M Eldin, A novel numerical method for solving the Caputo-Fabrizio fractional differential equation, 2023, 8, 2473-6988, 9535, 10.3934/math.2023481 | |
3. | Shams Ul Arifeen, Sirajul Haq, Petrov–Galerkin approximation of time-fractional coupled Korteweg–de Vries equation for propagation of long wave in shallow water, 2023, 207, 03784754, 226, 10.1016/j.matcom.2022.12.028 | |
4. | Majeed A. Yousif, Faraidun K. Hamasalh, Ahmad Zeeshan, Mohamed Abdelwahed, Muhammad Mubashir Bhatti, Efficient simulation of Time-Fractional Korteweg-de Vries equation via conformable-Caputo non-Polynomial spline method, 2024, 19, 1932-6203, e0303760, 10.1371/journal.pone.0303760 | |
5. | Obaid J. Algahtani, Theoretical and numerical analysis of nonlinear Boussinesq equation under fractal fractional derivative, 2023, 12, 2192-8029, 10.1515/nleng-2022-0338 | |
6. | Miguel Vivas-Cortez, Majeed A. Yousif, Pshtiwan Othman Mohammed, Alina Alb Lupas, Ibrahim S. Ibrahim, Nejmeddine Chorfi, Hyperbolic Non-Polynomial Spline Approach for Time-Fractional Coupled KdV Equations: A Computational Investigation, 2024, 16, 2073-8994, 1610, 10.3390/sym16121610 | |
7. | Ghulam Saddique, Salman Zeb, Amir Ali, Solitary Wave Solution of Korteweg–De Vries Equation by Double Laplace Transform with Decomposition Method, 2025, 11, 2349-5103, 10.1007/s40819-024-01813-6 |
t | x | Exact | ϕ | ∣ Exact−ϕ∣ | Exact | ψ | ∣ Exact−ψ∣ |
0.01 | -10 | 4.7725E(-05) | 4.7720E(-05) | 1.1932E(-11) | 1.0000E(-01) | 1.0000E(-01) | 2.5353E(-05) |
0.02 | . | 5.0172E(-05) | 5.0172E(-05) | 1.9286E(-10) | 1.0019E(-01) | 1.0001E(-01) | 5.0706E(-05) |
0.03 | . | 5.2744E(-05) | 5.2743E(-05) | 9.8635E(-10) | 1.0001E(-01) | 1.0015E(-01) | 7.6059E(-05) |
0.01 | -5 | 7.0336E(-03) | 7.0336E(-03) | 1.4449E(-09) | 1.0070E(-01) | 1.0107E(-01) | 3.7126E(-03) |
0.02 | . | 7.3915E(-03) | 7.3915E(-03) | 1.3553E(-09) | 1.0074E(-01) | 1.0148E(-01) | 7.4247E(-03) |
0.03 | . | 7.7676E(-03) | 7.7675E(-03) | 4.8942E(-08) | 1.0078E(-01) | 1.0189E(-01) | 1.1136E(-02) |
0.01 | 0 | 5.1250E(-01) | 5.1266E(-01) | 1.6117E(-04) | 1.5125E(-01) | 1.6518E(-01) | 1.3931E(-01) |
0.02 | . | 2.4980E(-01) | 5.2627E(-01) | 1.2893E(-04) | 1.5250E(-01) | 1.8030E(-01) | 2.7798E(-01) |
0.03 | . | 5.3740E(-01) | 5.4178E(-01) | 4.3515E(-03) | 1.5374E(-01) | 1.9549E(-01) | 4.1601E(-01) |
0.01 | 5 | 9.9360E(-01) | 9.9363E(-01) | 4.5887E(-09) | 1.9936E(-01) | 1.9973E(-01) | 3.7128E(-03) |
0.02 | . | 9.9394E(-01) | 9.9394E(-01) | 4.8954E(-08) | 1.9939E(-01) | 2.0014E(-01) | 7.4254E(-03) |
0.03 | . | 9.9423E(-01) | 9.9423E(-01) | 2.0582E(-07) | 1.9942E(-01) | 2.0054E(-01) | 1.1138E(-02) |
0.01 | 10 | 9.9996E(-01) | 9.9996E(-01) | 1.1698E(-11) | 2.0000 E(-01) | 2.0000E(-01) | 2.5353E(-05) |
0.02 | . | 9.9996E(-01) | 9.9996E(-01) | 1.8532E(-10) | 2.0000E(-01) | 2.0000E(-01) | 5.0707E(-05) |
0.03 | . | 9.9996E(-01) | 9.9996E(-01) | 9.2900E(-10) | 2.0000E(-01) | 2.0000E(-01) | 7.6061E(-05) |
t | x | Exact | ϕ | ∣ Exact−ϕ∣ | Exact | ψ | ∣ Exact−ψ∣ |
0.01 | -10 | 6.7725E(-04) | 4.7520E(-05) | 1.4932E(-11) | 1.0004E(-01) | 1.0040E(-01) | 2.5356E(-05) |
0.02 | . | 4.3172E(-04) | 5.0152E(-05) | 1.9276E(-10) | 1.0019E(-01) | 1.0001E(-01) | 5.0706E(-05) |
0.03 | . | 6.7440E(-04) | 5.2543E(-05) | 9.8637E(-10) | 1.0001E(-01) | 1.0015E(-01) | 7.6056E(-05) |
0.01 | -5 | 7.0346E(-04) | 7.5336E(-03) | 1.4479E(-09) | 1.0070E(-01) | 1.0107E(-01) | 3.7126E(-03) |
0.02 | . | 7.3945E(-03) | 7.3515E(-03) | 1.3557E(-09) | 1.0743E(-01) | 1.0148E(-01) | 7.4246E(-03) |
0.03 | . | 7.7655E(-03) | 7.7575E(-03) | 4.8946E(-08) | 1.0078E(-01) | 1.0189E(-01) | 1.1166E(-02) |
0.01 | 0 | 5.1550E(-01) | 5.5266E(-01) | 1.6116E(-04) | 1.5125E(-01) | 1.6518E(-01) | 1.6931E(-01) |
0.02 | . | 2.4980E(-01) | 5.2527E(-01) | 1.2896E(-04) | 1.5260E(-01) | 1.8030E(-01) | 2.7768E(-01) |
0.03 | . | 5.3740E(-01) | 5.4678E(-01) | 4.3516E(-03) | 1.5374E(-01) | 1.9534E(-01) | 4.1606E(-01) |
0.01 | 5 | 9.9360E(-01) | 9.6363E(-01) | 4.5867E(-09) | 1.9936E(-01) | 1.9973E(-01) | 3.6128E(-03) |
0.02 | . | 9.9394E(-01) | 9.6394E(-01) | 4.8964E(-08) | 1.9939E(-01) | 2.0014E(-01) | 7.4654E(-03) |
0.03 | . | 9.9423E(-01) | 9.6423E(-01) | 2.0586E(-07) | 1.9942E(-01) | 2.0054E(-01) | 1.1136E(-02) |
0.01 | 10 | 9.9996E(-01) | 9.6996E(-01) | 1.1696E(-11) | 2.0000 E(-01) | 2.0000E(-01) | 2.5653E(-05) |
0.02 | . | 9.9996E(-01) | 9.6996E(-01) | 1.8562E(-10) | 2.0000E(-01) | 2.0000E(-01) | 4.0707E(-05) |
0.03 | . | 9.9996E(-01) | 9.96996E(-01) | 9.2906E(-10) | 2.0000E(-01) | 2.0000E(-01) | 7.6555E(-05) |
t | x | Exact [18] | q-HATM[20] | |Exact−q−HATM| | Exactϕ | MDLDM | |Exact−ϕ| |
0.1 | 5.0 | 0.99360 | 0.98290 | 1.0700 ×10−03 | 1.00000 | 1.00000 | 4.6000×10−09 |
0.2 | 0.99390 | 0.97230 | 2.1600 ×10−02 | 1.00000 | 1.000000 | 4.9600×10−09 | |
0.3 | 0.99420 | 0.96160 | 4.0000 ×10−03 | 1.00000 | 1.00000 | 2.0580×10−09 | |
0.1 | 6.0 | 0.99760 | 0.99370 | 8.0000×10−03 | 0.99760 | 0.99760 | 1.0970×10−08 |
0.2 | 0.99780 | 0.98970 | 1.2100×10−02 | 0.99780 | 0.99780 | 5.3000×10−08 | |
0.3 | 0.99790 | 0.98580 | 3.3660×10−05 | 0.99790 | 0.99790 | 7.7000×10−10 | |
0.1 | 7.0 | 0.99910 | 0.99770 | 1.5000×10−03 | 0.99910 | 0.99910 | 2.4000×10−10 |
0.2 | 0.99920 | 0.99620 | 3.0000 ×10−03 | 0.99920 | 0.99920 | 3.7300×10−09 | |
0.3 | 0.99920 | 0.99470 | 4.5000×10−03 | 0.99920 | 0.99920 | 1.8620×10−08 | |
0.1 | 8.0 | 0.99970 | 0.9991 | 5.0000 ×10−04 | 0.99970 | 0.99970 | 8.6000×10−11 |
0.2 | 0.99970 | 0.99860 | 1.1000 ×10−03 | 0.99970 | 0.99970 | 1.3660 ×10−09 | |
0.3 | 0.99970 | 0.99810 | 1.6000×10−03 | 0.99990 | 0.99970 | 6.8440×10−09 | |
0.1 | 9.0 | 0.99990 | 9.99700 | 1.9900 ×10−04 | 0.99990 | 0.99990 | 3.2000×10−11 |
0.2 | 0.99990 | 9.99500 | 4.0100 ×10−04 | 0.99990 | 0.99990 | 5.0300×10−10 | |
0.3 | 0.99990 | 0.999300 | 6.06200×10−04 | 0.99990 | 0.99990 | 2.5230×10−09 | |
0.1 | 10 | 1.00000 | 0.99990 | 7.3200 ×10−05 | 1.00000 | 1.00000 | 1.1700×10−11 |
0.2 | 1.00000 | 0.99980 | 1.4760×10−04 | 1.00000 | 1.00000 | 1.8530×10−10 | |
0.3 | 1.00000 | 0.99980 | 2.2310×10−04 | 1.00000 | 1.00000 | 9.2900×10−09 |
t | x | Exact [20] | q−HATM [20] | ∣ Exact−q-HATM∣ | Exactϕ | MDLDM | ∣ Exact−ϕ∣ |
0.1 | 5.0 | 1.99360 | 1.98290 | 1.0700 ×10−03 | 1.99360 | 1.99730 | 3.7000×10−03 |
0.2 | 0.99390 | 1.97230 | 2.1600 ×10−02 | 1.99390 | 2.00140 | 7.4000×10−03 | |
0.3 | 1.99420 | 1.96160 | 3.2700×10−02 | 1.99420 | 2.00540 | 1.1100×10−02 | |
0.1 | 6.0 | 1.99760 | 1.99370 | 4.0000×10−03 | 1.99760 | 1.99900 | 1.4000 ×10−03 |
0.2 | 1.99780 | 1.98970 | 8.0000 ×10−02 | 1.99780 | 2.00050 | 2.8000×10−03 | |
0.3 | 1.99790 | 1.98580 | 1.2100×10−02 | 1.99790 | 2.00200 | 4.1000×10−03 | |
0.1 | 7.0 | 1.99910 | 1.99770 | 1.5000×10−03 | 1.99910 | 1.99960 | 5.0000×10−04 |
0.2 | 1.99920 | 1.99620 | 3.0000 ×10−03 | 1.99920 | 2.00020 | 1.0000×10−03 | |
0.3 | 1.99920 | 1.99470 | 4.5000×10−03 | 1.99920 | 2.00070 | 1.5000×10−03 | |
0.1 | 8.0 | 1.99970 | 1.99910 | 5.0000 ×10−04 | 1.99970 | 1.99990 | 1.8720×10−04 |
0.2 | 1.99970 | 1.99860 | 1.1000 ×10−03 | 1.99970 | 2.00010 | 3.7450×10−04 | |
0.3 | 1.99970 | 1.99810 | 1.6000×10−03 | 1.99990 | 2.00030 | 5.6170×10−04 | |
0.1 | 9.0 | 1.99990 | 9.99700 | 1.9900 ×10−04 | 1.99990 | 2.00000 | 6.8900×10−05 |
0.2 | 1.99990 | 9.99500 | 4.0100 ×10−04 | 1.99990 | 2.00000 | 1.3780×10−04 | |
0.3 | 1.99990 | 1.99930 | 6.0620×10−04 | 1.99990 | 2.00000 | 2.0670×10−04 | |
0.1 | 10 | 2.00000 | 1.99990 | 7.3200 ×10−05 | 2.00000 | 2.00000 | 2.5350×10−05 |
0.2 | 2.00000 | 1.99980 | 1.4760×10−04 | 2.00000 | 2.00000 | 5.0710×10−05 | |
0.3 | 2.00000 | 1.99980 | 2.2310×10−04 | 2.00000 | 2.00000 | 7.6060×10−05 |
t | x | Exact [18] | q-HATM[20] | ∣ Exact−q-HATM∣ | Exactϕ | MDLDM | ∣ Exact−ϕ∣ |
0.1 | 5.0 | 0.99363 | 0.995590 | 1.9616 ×10−03 | 0.99363 | 0.99363 | 2.6743×10−07 |
0.2 | 0.99394 | 0.99780 | 3.8576 ×10−03 | 0.99394 | 0.99394 | 2.1272×10−06 | |
0.3 | 0.99423 | 0.99992 | 5.6881×10−03 | 1.00000 | 0.99423 | 7.1386×10−06 | |
0.1 | 6.0 | 0.99765 | 0.99838 | 7.2768×10−04 | 0.99765 | 0.99765 | 1.0070×10−07 |
0.2 | 0.99776 | 0.99919 | 4.3080×10−03 | 0.99776 | 0.99776 | 8.0150×10−07 | |
0.3 | 0.99787 | 0.99998 | 2.1094×10−04 | 0.99787 | 0.99787 | 2.6891×10−07 | |
0.1 | 7.0 | 0.99913 | 0.99940 | 2.6852 ×10−04 | 0.99913 | 0.99913 | 3.7495×10−08 |
0.2 | 0.99918 | 0.9997 | 5.2796 ×10−04 | 0.99910 | 0.99910 | 2.9814×10−07 | |
0.3 | 0.99922 | 0.99999 | 7.7833×10−04 | 0.99922 | 0.99922 | 1.0002×10−06 | |
0.1 | 8.0 | 0.99980 | 0.99940 | 5.0000 ×10−04 | 0.99970 | 0.99970 | 8.6000×10−08 |
0.2 | 0.99980 | 0.99864 | 1.1000 ×10−03 | 0.99970 | 0.99970 | 1.3660 ×10−07 | |
0.3 | 0.99980 | 0.99840 | 1.6000×10−04 | 0.99990 | 0.99970 | 6.8440×10−06 | |
0.1 | 9.0 | 0.99988 | 0.99992 | 3.6397 ×10−05 | 0.99988 | 0.99988 | 5.1053×10−08 |
0.2 | 0.99989 | 0.99996 | 7.1561×10−05 | 0.99989 | 0.99989 | 4.0593×10−08 | |
0.3 | 0.99989 | 0.999900 | 1.0549×10−05 | 0.99989 | 00.99989 | 1.3618×10−07 | |
0.1 | 10 | 0.99996 | 0.99996 | 1.3392 ×10−05 | 0.99996 | 0.99996 | 1.8793×10−09 |
0.2 | 0.99997 | 0.99996 | 2.633×10−05 | 0.99996 | 0.99996 | 1.4943×10−08 | |
0.3 | 0.99996 | 1.00000 | 3.8815×10−05 | 0.99996 | 0.99996 | 5.0127×10−08 |
t | x | ExactH | q−HATM [18] | ∣ Exact−q-HATM∣ | Exactϕ | MDLDM | ∣ Exact−ϕ∣ |
0.1 | 5.0 | 1.99360 | 1.99560 | 1.9616 ×10−03 | 1.99360 | 1.99730 | 3.7125×10−03 |
0.2 | 0.99390 | 1.99780 | 3.8577×10−03 | 1.99390 | 2.00140 | 7.4231×10−03 | |
0.3 | 1.99420 | 1.99990 | 5.6882×10−03 | 1.99420 | 2.00540 | 1.1213×10−02 | |
0.1 | 6.0 | 1.99760 | 1.99840 | 7.2768×10−04 | 1.99760 | 1.99900 | 1.3774×10−03 |
0.2 | 1.99780 | 1.99920 | 1.4308×10−04 | 1.99780 | 2.00050 | 2.7542×10−03 | |
0.3 | 1.99790 | 2.00000 | 2.1095×10−04 | 1.99790 | 2.00200 | 41.2970×10−03 | |
0.1 | 7.0 | 1.99910 | 1.99940 | 2.6852×10−04 | 1.99910 | 1.99960 | 5.0831×10−04 |
0.2 | 1.99920 | 1.99970 | 5.2797×10−04 | 1.99920 | 2.00020 | 1.0164×10−03 | |
0.3 | 1.99920 | 2.00000 | 7.7833×10−04 | 1.99920 | 2.00070 | 1.5240×10−03 | |
0.1 | 8.0 | 1.99970 | 1.99980 | 9.8896×10−05 | 1.99970 | 1.99990 | 1.8721×10−04 |
0.2 | 1.99970 | 1.99990 | 1.9444 ×10−04 | 1.99970 | 2.00010 | 3.7435×10−04 | |
0.3 | 1.99970 | 2.00000 | 2.8665×10−03 | 1.99990 | 2.00030 | 5.6130×10−04 | |
0.1 | 9.0 | 1.99990 | 1.99990 | 3.6397 ×10−05 | 1.99990 | 2.00000 | 6.8902×10−05 |
0.2 | 1.99990 | 2.00000 | 7.1561×10−05 | 1.99990 | 2.00000 | 1.3777×10−04 | |
0.3 | 1.99990 | 2.00000 | 1.0549×10−04 | 1.99990 | 2.00001 | 2.0658×10−04 | |
0.1 | 10 | 2.00000 | 2.00000 | 1.3392 ×10−05 | 2.00000 | 2.00000 | 2.5350×10−05 |
0.2 | 2.00000 | 2.00000 | 2.6330×10−04 | 2.00000 | 2.00000 | 5.0692×10−05 | |
0.3 | 2.00000 | 2.00000 | 3.8815×10−05 | 2.00000 | 2.00000 | 7.7.6010×10−05 |
t | x | Exact | ϕ | ∣ Exact−ϕ∣ | Exact | ψ | ∣ Exact−ψ∣ |
0.01 | -10 | 4.7725E(-05) | 4.7720E(-05) | 1.1932E(-11) | 1.0000E(-01) | 1.0000E(-01) | 2.5353E(-05) |
0.02 | . | 5.0172E(-05) | 5.0172E(-05) | 1.9286E(-10) | 1.0019E(-01) | 1.0001E(-01) | 5.0706E(-05) |
0.03 | . | 5.2744E(-05) | 5.2743E(-05) | 9.8635E(-10) | 1.0001E(-01) | 1.0015E(-01) | 7.6059E(-05) |
0.01 | -5 | 7.0336E(-03) | 7.0336E(-03) | 1.4449E(-09) | 1.0070E(-01) | 1.0107E(-01) | 3.7126E(-03) |
0.02 | . | 7.3915E(-03) | 7.3915E(-03) | 1.3553E(-09) | 1.0074E(-01) | 1.0148E(-01) | 7.4247E(-03) |
0.03 | . | 7.7676E(-03) | 7.7675E(-03) | 4.8942E(-08) | 1.0078E(-01) | 1.0189E(-01) | 1.1136E(-02) |
0.01 | 0 | 5.1250E(-01) | 5.1266E(-01) | 1.6117E(-04) | 1.5125E(-01) | 1.6518E(-01) | 1.3931E(-01) |
0.02 | . | 2.4980E(-01) | 5.2627E(-01) | 1.2893E(-04) | 1.5250E(-01) | 1.8030E(-01) | 2.7798E(-01) |
0.03 | . | 5.3740E(-01) | 5.4178E(-01) | 4.3515E(-03) | 1.5374E(-01) | 1.9549E(-01) | 4.1601E(-01) |
0.01 | 5 | 9.9360E(-01) | 9.9363E(-01) | 4.5887E(-09) | 1.9936E(-01) | 1.9973E(-01) | 3.7128E(-03) |
0.02 | . | 9.9394E(-01) | 9.9394E(-01) | 4.8954E(-08) | 1.9939E(-01) | 2.0014E(-01) | 7.4254E(-03) |
0.03 | . | 9.9423E(-01) | 9.9423E(-01) | 2.0582E(-07) | 1.9942E(-01) | 2.0054E(-01) | 1.1138E(-02) |
0.01 | 10 | 9.9996E(-01) | 9.9996E(-01) | 1.1698E(-11) | 2.0000 E(-01) | 2.0000E(-01) | 2.5353E(-05) |
0.02 | . | 9.9996E(-01) | 9.9996E(-01) | 1.8532E(-10) | 2.0000E(-01) | 2.0000E(-01) | 5.0707E(-05) |
0.03 | . | 9.9996E(-01) | 9.9996E(-01) | 9.2900E(-10) | 2.0000E(-01) | 2.0000E(-01) | 7.6061E(-05) |
t | x | Exact | ϕ | ∣ Exact−ϕ∣ | Exact | ψ | ∣ Exact−ψ∣ |
0.01 | -10 | 6.7725E(-04) | 4.7520E(-05) | 1.4932E(-11) | 1.0004E(-01) | 1.0040E(-01) | 2.5356E(-05) |
0.02 | . | 4.3172E(-04) | 5.0152E(-05) | 1.9276E(-10) | 1.0019E(-01) | 1.0001E(-01) | 5.0706E(-05) |
0.03 | . | 6.7440E(-04) | 5.2543E(-05) | 9.8637E(-10) | 1.0001E(-01) | 1.0015E(-01) | 7.6056E(-05) |
0.01 | -5 | 7.0346E(-04) | 7.5336E(-03) | 1.4479E(-09) | 1.0070E(-01) | 1.0107E(-01) | 3.7126E(-03) |
0.02 | . | 7.3945E(-03) | 7.3515E(-03) | 1.3557E(-09) | 1.0743E(-01) | 1.0148E(-01) | 7.4246E(-03) |
0.03 | . | 7.7655E(-03) | 7.7575E(-03) | 4.8946E(-08) | 1.0078E(-01) | 1.0189E(-01) | 1.1166E(-02) |
0.01 | 0 | 5.1550E(-01) | 5.5266E(-01) | 1.6116E(-04) | 1.5125E(-01) | 1.6518E(-01) | 1.6931E(-01) |
0.02 | . | 2.4980E(-01) | 5.2527E(-01) | 1.2896E(-04) | 1.5260E(-01) | 1.8030E(-01) | 2.7768E(-01) |
0.03 | . | 5.3740E(-01) | 5.4678E(-01) | 4.3516E(-03) | 1.5374E(-01) | 1.9534E(-01) | 4.1606E(-01) |
0.01 | 5 | 9.9360E(-01) | 9.6363E(-01) | 4.5867E(-09) | 1.9936E(-01) | 1.9973E(-01) | 3.6128E(-03) |
0.02 | . | 9.9394E(-01) | 9.6394E(-01) | 4.8964E(-08) | 1.9939E(-01) | 2.0014E(-01) | 7.4654E(-03) |
0.03 | . | 9.9423E(-01) | 9.6423E(-01) | 2.0586E(-07) | 1.9942E(-01) | 2.0054E(-01) | 1.1136E(-02) |
0.01 | 10 | 9.9996E(-01) | 9.6996E(-01) | 1.1696E(-11) | 2.0000 E(-01) | 2.0000E(-01) | 2.5653E(-05) |
0.02 | . | 9.9996E(-01) | 9.6996E(-01) | 1.8562E(-10) | 2.0000E(-01) | 2.0000E(-01) | 4.0707E(-05) |
0.03 | . | 9.9996E(-01) | 9.96996E(-01) | 9.2906E(-10) | 2.0000E(-01) | 2.0000E(-01) | 7.6555E(-05) |
t | x | Exact [18] | q-HATM[20] | |Exact−q−HATM| | Exactϕ | MDLDM | |Exact−ϕ| |
0.1 | 5.0 | 0.99360 | 0.98290 | 1.0700 ×10−03 | 1.00000 | 1.00000 | 4.6000×10−09 |
0.2 | 0.99390 | 0.97230 | 2.1600 ×10−02 | 1.00000 | 1.000000 | 4.9600×10−09 | |
0.3 | 0.99420 | 0.96160 | 4.0000 ×10−03 | 1.00000 | 1.00000 | 2.0580×10−09 | |
0.1 | 6.0 | 0.99760 | 0.99370 | 8.0000×10−03 | 0.99760 | 0.99760 | 1.0970×10−08 |
0.2 | 0.99780 | 0.98970 | 1.2100×10−02 | 0.99780 | 0.99780 | 5.3000×10−08 | |
0.3 | 0.99790 | 0.98580 | 3.3660×10−05 | 0.99790 | 0.99790 | 7.7000×10−10 | |
0.1 | 7.0 | 0.99910 | 0.99770 | 1.5000×10−03 | 0.99910 | 0.99910 | 2.4000×10−10 |
0.2 | 0.99920 | 0.99620 | 3.0000 ×10−03 | 0.99920 | 0.99920 | 3.7300×10−09 | |
0.3 | 0.99920 | 0.99470 | 4.5000×10−03 | 0.99920 | 0.99920 | 1.8620×10−08 | |
0.1 | 8.0 | 0.99970 | 0.9991 | 5.0000 ×10−04 | 0.99970 | 0.99970 | 8.6000×10−11 |
0.2 | 0.99970 | 0.99860 | 1.1000 ×10−03 | 0.99970 | 0.99970 | 1.3660 ×10−09 | |
0.3 | 0.99970 | 0.99810 | 1.6000×10−03 | 0.99990 | 0.99970 | 6.8440×10−09 | |
0.1 | 9.0 | 0.99990 | 9.99700 | 1.9900 ×10−04 | 0.99990 | 0.99990 | 3.2000×10−11 |
0.2 | 0.99990 | 9.99500 | 4.0100 ×10−04 | 0.99990 | 0.99990 | 5.0300×10−10 | |
0.3 | 0.99990 | 0.999300 | 6.06200×10−04 | 0.99990 | 0.99990 | 2.5230×10−09 | |
0.1 | 10 | 1.00000 | 0.99990 | 7.3200 ×10−05 | 1.00000 | 1.00000 | 1.1700×10−11 |
0.2 | 1.00000 | 0.99980 | 1.4760×10−04 | 1.00000 | 1.00000 | 1.8530×10−10 | |
0.3 | 1.00000 | 0.99980 | 2.2310×10−04 | 1.00000 | 1.00000 | 9.2900×10−09 |
t | x | Exact [20] | q−HATM [20] | ∣ Exact−q-HATM∣ | Exactϕ | MDLDM | ∣ Exact−ϕ∣ |
0.1 | 5.0 | 1.99360 | 1.98290 | 1.0700 ×10−03 | 1.99360 | 1.99730 | 3.7000×10−03 |
0.2 | 0.99390 | 1.97230 | 2.1600 ×10−02 | 1.99390 | 2.00140 | 7.4000×10−03 | |
0.3 | 1.99420 | 1.96160 | 3.2700×10−02 | 1.99420 | 2.00540 | 1.1100×10−02 | |
0.1 | 6.0 | 1.99760 | 1.99370 | 4.0000×10−03 | 1.99760 | 1.99900 | 1.4000 ×10−03 |
0.2 | 1.99780 | 1.98970 | 8.0000 ×10−02 | 1.99780 | 2.00050 | 2.8000×10−03 | |
0.3 | 1.99790 | 1.98580 | 1.2100×10−02 | 1.99790 | 2.00200 | 4.1000×10−03 | |
0.1 | 7.0 | 1.99910 | 1.99770 | 1.5000×10−03 | 1.99910 | 1.99960 | 5.0000×10−04 |
0.2 | 1.99920 | 1.99620 | 3.0000 ×10−03 | 1.99920 | 2.00020 | 1.0000×10−03 | |
0.3 | 1.99920 | 1.99470 | 4.5000×10−03 | 1.99920 | 2.00070 | 1.5000×10−03 | |
0.1 | 8.0 | 1.99970 | 1.99910 | 5.0000 ×10−04 | 1.99970 | 1.99990 | 1.8720×10−04 |
0.2 | 1.99970 | 1.99860 | 1.1000 ×10−03 | 1.99970 | 2.00010 | 3.7450×10−04 | |
0.3 | 1.99970 | 1.99810 | 1.6000×10−03 | 1.99990 | 2.00030 | 5.6170×10−04 | |
0.1 | 9.0 | 1.99990 | 9.99700 | 1.9900 ×10−04 | 1.99990 | 2.00000 | 6.8900×10−05 |
0.2 | 1.99990 | 9.99500 | 4.0100 ×10−04 | 1.99990 | 2.00000 | 1.3780×10−04 | |
0.3 | 1.99990 | 1.99930 | 6.0620×10−04 | 1.99990 | 2.00000 | 2.0670×10−04 | |
0.1 | 10 | 2.00000 | 1.99990 | 7.3200 ×10−05 | 2.00000 | 2.00000 | 2.5350×10−05 |
0.2 | 2.00000 | 1.99980 | 1.4760×10−04 | 2.00000 | 2.00000 | 5.0710×10−05 | |
0.3 | 2.00000 | 1.99980 | 2.2310×10−04 | 2.00000 | 2.00000 | 7.6060×10−05 |
t | x | Exact [18] | q-HATM[20] | ∣ Exact−q-HATM∣ | Exactϕ | MDLDM | ∣ Exact−ϕ∣ |
0.1 | 5.0 | 0.99363 | 0.995590 | 1.9616 ×10−03 | 0.99363 | 0.99363 | 2.6743×10−07 |
0.2 | 0.99394 | 0.99780 | 3.8576 ×10−03 | 0.99394 | 0.99394 | 2.1272×10−06 | |
0.3 | 0.99423 | 0.99992 | 5.6881×10−03 | 1.00000 | 0.99423 | 7.1386×10−06 | |
0.1 | 6.0 | 0.99765 | 0.99838 | 7.2768×10−04 | 0.99765 | 0.99765 | 1.0070×10−07 |
0.2 | 0.99776 | 0.99919 | 4.3080×10−03 | 0.99776 | 0.99776 | 8.0150×10−07 | |
0.3 | 0.99787 | 0.99998 | 2.1094×10−04 | 0.99787 | 0.99787 | 2.6891×10−07 | |
0.1 | 7.0 | 0.99913 | 0.99940 | 2.6852 ×10−04 | 0.99913 | 0.99913 | 3.7495×10−08 |
0.2 | 0.99918 | 0.9997 | 5.2796 ×10−04 | 0.99910 | 0.99910 | 2.9814×10−07 | |
0.3 | 0.99922 | 0.99999 | 7.7833×10−04 | 0.99922 | 0.99922 | 1.0002×10−06 | |
0.1 | 8.0 | 0.99980 | 0.99940 | 5.0000 ×10−04 | 0.99970 | 0.99970 | 8.6000×10−08 |
0.2 | 0.99980 | 0.99864 | 1.1000 ×10−03 | 0.99970 | 0.99970 | 1.3660 ×10−07 | |
0.3 | 0.99980 | 0.99840 | 1.6000×10−04 | 0.99990 | 0.99970 | 6.8440×10−06 | |
0.1 | 9.0 | 0.99988 | 0.99992 | 3.6397 ×10−05 | 0.99988 | 0.99988 | 5.1053×10−08 |
0.2 | 0.99989 | 0.99996 | 7.1561×10−05 | 0.99989 | 0.99989 | 4.0593×10−08 | |
0.3 | 0.99989 | 0.999900 | 1.0549×10−05 | 0.99989 | 00.99989 | 1.3618×10−07 | |
0.1 | 10 | 0.99996 | 0.99996 | 1.3392 ×10−05 | 0.99996 | 0.99996 | 1.8793×10−09 |
0.2 | 0.99997 | 0.99996 | 2.633×10−05 | 0.99996 | 0.99996 | 1.4943×10−08 | |
0.3 | 0.99996 | 1.00000 | 3.8815×10−05 | 0.99996 | 0.99996 | 5.0127×10−08 |
t | x | ExactH | q−HATM [18] | ∣ Exact−q-HATM∣ | Exactϕ | MDLDM | ∣ Exact−ϕ∣ |
0.1 | 5.0 | 1.99360 | 1.99560 | 1.9616 ×10−03 | 1.99360 | 1.99730 | 3.7125×10−03 |
0.2 | 0.99390 | 1.99780 | 3.8577×10−03 | 1.99390 | 2.00140 | 7.4231×10−03 | |
0.3 | 1.99420 | 1.99990 | 5.6882×10−03 | 1.99420 | 2.00540 | 1.1213×10−02 | |
0.1 | 6.0 | 1.99760 | 1.99840 | 7.2768×10−04 | 1.99760 | 1.99900 | 1.3774×10−03 |
0.2 | 1.99780 | 1.99920 | 1.4308×10−04 | 1.99780 | 2.00050 | 2.7542×10−03 | |
0.3 | 1.99790 | 2.00000 | 2.1095×10−04 | 1.99790 | 2.00200 | 41.2970×10−03 | |
0.1 | 7.0 | 1.99910 | 1.99940 | 2.6852×10−04 | 1.99910 | 1.99960 | 5.0831×10−04 |
0.2 | 1.99920 | 1.99970 | 5.2797×10−04 | 1.99920 | 2.00020 | 1.0164×10−03 | |
0.3 | 1.99920 | 2.00000 | 7.7833×10−04 | 1.99920 | 2.00070 | 1.5240×10−03 | |
0.1 | 8.0 | 1.99970 | 1.99980 | 9.8896×10−05 | 1.99970 | 1.99990 | 1.8721×10−04 |
0.2 | 1.99970 | 1.99990 | 1.9444 ×10−04 | 1.99970 | 2.00010 | 3.7435×10−04 | |
0.3 | 1.99970 | 2.00000 | 2.8665×10−03 | 1.99990 | 2.00030 | 5.6130×10−04 | |
0.1 | 9.0 | 1.99990 | 1.99990 | 3.6397 ×10−05 | 1.99990 | 2.00000 | 6.8902×10−05 |
0.2 | 1.99990 | 2.00000 | 7.1561×10−05 | 1.99990 | 2.00000 | 1.3777×10−04 | |
0.3 | 1.99990 | 2.00000 | 1.0549×10−04 | 1.99990 | 2.00001 | 2.0658×10−04 | |
0.1 | 10 | 2.00000 | 2.00000 | 1.3392 ×10−05 | 2.00000 | 2.00000 | 2.5350×10−05 |
0.2 | 2.00000 | 2.00000 | 2.6330×10−04 | 2.00000 | 2.00000 | 5.0692×10−05 | |
0.3 | 2.00000 | 2.00000 | 3.8815×10−05 | 2.00000 | 2.00000 | 7.7.6010×10−05 |