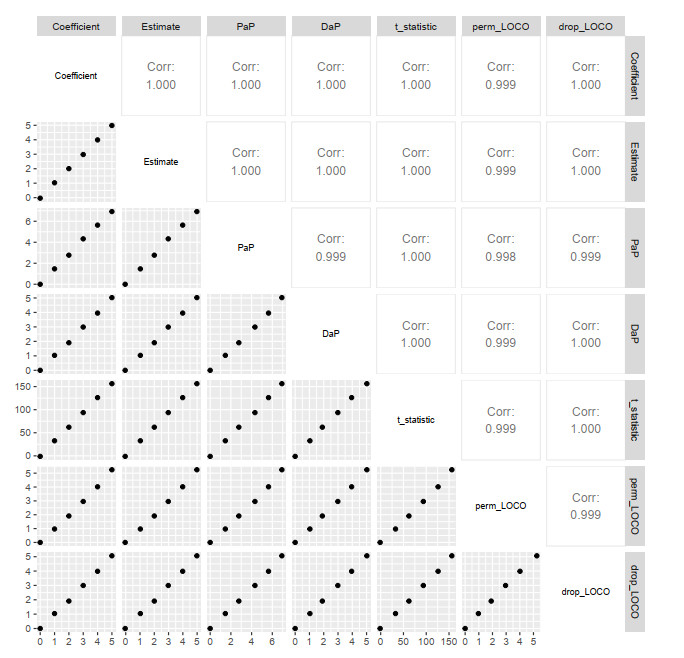
The machinability of hard brittle nanocrystalline cubic silicon carbide (3C-SiC) is strongly dependent on internal microstructure and its adapted machining response. Here, we conducted molecular dynamic simulations to explore the machinability of nanotwinned 3C-SiC with a large number of twin boundaries in diamond cutting. The effect of the introduction of twin boundaries on the diamond cutting of nanocrystalline 3C-SiC, particular for its contribution to suppressing brittle fracture and improving ductile-mode cutting, was investigated in-depth. Our simulation results revealed that twin boundaries exerted a significant impact on the deformation mechanism and subsequent surface integrity of nanocrystalline 3C-SiC. Specifically, intergranular fracture was significantly suppressed by the introduction of twin boundaries. In addition, various deformation behaviors such as phase transformation, crack propagation, dislocation activity, and twin boundary-associated deformation mechanisms were operated in cutting process of nanotwinned 3C-SiC. Furthermore, the influence of twin boundary spacing on the diamond cutting characteristics of nanotwinned 3C-SiC was also addressed.
Citation: Liang Zhao, Weimian Guan, Jiwen Xu, Zhiyuan Sun, Maoda Zhang, Junjie Zhang. Atomistic investigation of effect of twin boundary on machinability in diamond cutting of nanocrystalline 3C-SiC[J]. AIMS Materials Science, 2024, 11(6): 1149-1164. doi: 10.3934/matersci.2024056
[1] | Sandra Vaz, Delfim F. M. Torres . A dynamically-consistent nonstandard finite difference scheme for the SICA model. Mathematical Biosciences and Engineering, 2021, 18(4): 4552-4571. doi: 10.3934/mbe.2021231 |
[2] | A. M. Elaiw, Raghad S. Alsulami, A. D. Hobiny . Global dynamics of IAV/SARS-CoV-2 coinfection model with eclipse phase and antibody immunity. Mathematical Biosciences and Engineering, 2023, 20(2): 3873-3917. doi: 10.3934/mbe.2023182 |
[3] | Wenhan Guo, Yixin Xie, Alan E Lopez-Hernandez, Shengjie Sun, Lin Li . Electrostatic features for nucleocapsid proteins of SARS-CoV and SARS-CoV-2. Mathematical Biosciences and Engineering, 2021, 18(3): 2372-2383. doi: 10.3934/mbe.2021120 |
[4] | Maghnia Hamou Maamar, Matthias Ehrhardt, Louiza Tabharit . A nonstandard finite difference scheme for a time-fractional model of Zika virus transmission. Mathematical Biosciences and Engineering, 2024, 21(1): 924-962. doi: 10.3934/mbe.2024039 |
[5] | Anichur Rahman, Muaz Rahman, Dipanjali Kundu, Md Razaul Karim, Shahab S. Band, Mehdi Sookhak . Study on IoT for SARS-CoV-2 with healthcare: present and future perspective. Mathematical Biosciences and Engineering, 2021, 18(6): 9697-9726. doi: 10.3934/mbe.2021475 |
[6] | Sarafa A. Iyaniwura, Rabiu Musa, Jude D. Kong . A generalized distributed delay model of COVID-19: An endemic model with immunity waning. Mathematical Biosciences and Engineering, 2023, 20(3): 5379-5412. doi: 10.3934/mbe.2023249 |
[7] | Ahmed Alshehri, Saif Ullah . A numerical study of COVID-19 epidemic model with vaccination and diffusion. Mathematical Biosciences and Engineering, 2023, 20(3): 4643-4672. doi: 10.3934/mbe.2023215 |
[8] | Matthew Hayden, Bryce Morrow, Wesley Yang, Jin Wang . Quantifying the role of airborne transmission in the spread of COVID-19. Mathematical Biosciences and Engineering, 2023, 20(1): 587-612. doi: 10.3934/mbe.2023027 |
[9] | Fang Wang, Lianying Cao, Xiaoji Song . Mathematical modeling of mutated COVID-19 transmission with quarantine, isolation and vaccination. Mathematical Biosciences and Engineering, 2022, 19(8): 8035-8056. doi: 10.3934/mbe.2022376 |
[10] | Rahat Zarin, Usa Wannasingha Humphries, Amir Khan, Aeshah A. Raezah . Computational modeling of fractional COVID-19 model by Haar wavelet collocation Methods with real data. Mathematical Biosciences and Engineering, 2023, 20(6): 11281-11312. doi: 10.3934/mbe.2023500 |
The machinability of hard brittle nanocrystalline cubic silicon carbide (3C-SiC) is strongly dependent on internal microstructure and its adapted machining response. Here, we conducted molecular dynamic simulations to explore the machinability of nanotwinned 3C-SiC with a large number of twin boundaries in diamond cutting. The effect of the introduction of twin boundaries on the diamond cutting of nanocrystalline 3C-SiC, particular for its contribution to suppressing brittle fracture and improving ductile-mode cutting, was investigated in-depth. Our simulation results revealed that twin boundaries exerted a significant impact on the deformation mechanism and subsequent surface integrity of nanocrystalline 3C-SiC. Specifically, intergranular fracture was significantly suppressed by the introduction of twin boundaries. In addition, various deformation behaviors such as phase transformation, crack propagation, dislocation activity, and twin boundary-associated deformation mechanisms were operated in cutting process of nanotwinned 3C-SiC. Furthermore, the influence of twin boundary spacing on the diamond cutting characteristics of nanotwinned 3C-SiC was also addressed.
Variable importance and model selection are nuanced concepts that are relevant in statistics, data science, and many other areas of scientific literature (see Kruskal et al. [1]). Perhaps the simplest example of a metric for variable importance in regression may be found in introductory textbooks (see Achen [2]). When all variables have been standardized, the magnitude of the regression coefficients are considered measures of importance of the associated variables. A slew of variable importance measures have been developed over the years, including t-statistics and stepwise elimination of variables on the basis of statistical significance or measures like AIC. Most of these have been superseded by the LASSO [3] and variations, including the elastic net [4].
A different and axiomatic approach was taken by Pratt [5]. Starting with exchangeable, standardized predictor variables, Pratt showed that the importance of the jth predictor variable may be defined as:
VarImpj=ˆβj×ry,xj | (1.1) |
where ˆβj is the regression coefficient for the jth predictor variable and ry,xj is the marginal (Pearson) correlation between the response (y) and the jth predictor variable, xj.
In regression, the approach of using t-statistics for assessing variable importance may be shown to be equivalent to removing a variable and looking at the difference in mean squared errors for the models with and without the variable of interest. Complex machine learning methods, such as random forests, do not employ regression variable diagnostics such as estimated coefficients or t-statistics. Leo Breiman [6] introduced a variation of this idea for random forests in which the so-called out-of-bag (OOB) values on a variable of interest are permuted-and-predicted (PaP) so that change in accuracy can be observed and aggregated over all observations. This approach and related permutation methods have become a standard method in machine learning over the last 20 years; but see Strobl et al. [7] and Bladen [8] for a discussion of the impact of collinearity on permutation variable importance. Hooker et al. [9] pointed out that the variable permutation of Breiman's [6] original algorithm leads to a form of potentially problematic extrapolation and suggested that re-learning additional models is required to handle this problem. They pointed to the work done by Lei et al. [10] involving the technique of leave-one-covariate-out (LOCO) of the dataset and re-learning the model of interest. Barber et al. [11] and Candès et al. [12] chose to handle this via a technique they call knockoffs, which involves switching original variables for random replacements that are sampled conditionally on the remaining variables. Each of the LOCO and knockoff techniques involves fitting a new model after removing, permuting, or otherwise altering a training variable and comparing the new model to the original untainted model.
Variable importance assessments for random forests have been explored and furthered in various ways. In their work, Hooker et al. [9], expanded upon the LOCO technique and utilized a similar concept for work with random forests. Ye et al. [13] created the SOIL technique designed for sparse linear modeling and high-dimensional regression and showed the proficiency it has in model selection for random forests. Strobl et al. [7] attempted to navigate feature importance issues caused by collinearity via a conditional variable importance algorithm. Many researchers have developed plots relating changes in the predicted response to changes in a particular variable while holding other variables constant. Apley et al. [14] contibuted with the concept and visualization known as accumulated local effects (ALE) plots. Goldstein et al. [15] and Greenwell et al. [16] developed individual conditional expectation (ICE) plots and averaged partial dependence plots (PDPs), respectively. PDPs, in particular, have been used to assess the importance of a variable by taking the standard deviation of the response predictions from the PDP for the desired variable [16].
In this paper, we highlight how some variations of the PaP and LOCO methods for assessing variable importance in linear modeling and machine learning relate to regression metrics. By doing so, we hope to illustrate which variable importance methods should be employed to best approximate specific regression metrics of interest.
In the remainder of this section, we introduce, define, and provide notations for standard regression metrics and several machine learning variable importance computations. In Section 2, we outline our simulated data for comparing these importance values. In Section 3, we show comparative plots of our importance metrics and comment on observed results within them. Finally, in Section 4, we offer our conclusions about the different variable importance metrics we analyze.
In ordinary regression, there are three different metrics provided in standard summary tables: estimated coefficients, t-statistics, and p-values. If variables have been standardized, then higher magnitudes for coefficients are often interpreted to imply greater importance [2]. The same should be true for t-statistics, which are robust to standardization. While p-values communicate similar information to t-statistics, we recognize that p-values are rarely optimal for interpreting variable importance because they have an inverse and nonlinear relationship with t-statistics.
If variables are orthogonal, then t-statistics are proportional to the estimated coefficients. Let ˆβj be the estimate for the jth regression coefficient. These two metrics have the following relationship for the jth variable:
tj=ˆβjSE(ˆβj)∝ˆβj | (1.2) |
if the predictor variables have been standardized so that the standard error SE(ˆβj) is irrespective of which variable we are considering. However, these relationship conditions rarely hold true, which suggests a potential disconnect between the estimated coefficients and the t-statistics. A common issue occurs when variables are collinear. The standard errors of their estimated coefficients are then larger, which diminishes their t-statistics. Thus, the effect or relationship between a predictor and the response remains the same, but we are less certain of this relationship.
In more complex machine learning algorithms, a technique for assessing variable importance was introduced by Breiman [6]. Commonly called the permute-and-predict (PaP) method, it involves randomly scrambling the values of a chosen variable and accumulating predictions for the newly altered data. This method was originally conceived for random forests and was performed on out-of-bag (OOB) data, a type of validation dataset for individual trees. We will use the OOB PaP technique when assessing random forest importance metrics, but we will also perform the procedure manually on a separate validation set to compare to regression metrics and the OOB PaP.
Our research is motivated by earlier work we performed assessing how random forest variable importance metrics depend on collinearity and mtry, a tunable hyper-parameter of the number of randomly selected variables to consider for a given split for a tree in the forest [8]. In that work, we derived a heuristic suggesting a relationship between the regression t-statistics and random forest variable importance metrics. This heuristic submits that importancej∝t2j, which implies that a square root transformation is helpful for relating random forest importances back to regression metrics. In this paper, we will explore the relationship between regression metrics and PaP importances. We will also look at the relationships these metrics have with model refitting (LOCO importances) and with the true equation coefficients.
If the predictions using the raw data and the permuted data yield similar accuracies or errors, then that variable is not particularly important. Alternatively, if the original predictions clearly outperform the permutation predictions, then the variable is important.
Mathematically, our permutation variable importance may be expressed using syntax where the index indicates the validation data that we generate predictions for. Thus,
PaPj=√vMSE∼j−MSEMSE, | (1.3) |
where MSE is the validation mean squared error from the original model and vMSE∼j is the MSE generated from that same model when the validation values of the jth predictor have been permuted.
Alternatively, the variable importance can be assessed with a drop-and-predict (DaP) method. In our work, we accomplish this dropout by first rescaling each variable so that the center of the distribution is 0 and then setting all values of a given variable to the central value of 0. The structure is fundamentally equivalent to Eq (1.3), with one simple difference:
DaPj=√vMSE−j−MSEMSE, | (1.4) |
where vMSE−j is the MSE generated from the original model when the validation values of the jth predictor have all been set to the central value of 0.
These importance metrics are therefore equivalent if vMSE∼j=vMSE−j.
Another method for assessing variable importance is called re-learning (see Hooker et al. [9]) or LOCO (see Lei et al. [10]). When performing this technique, we randomly permute the values of a chosen variable in the training data rather than the validation data. We then build a new regression model using the training data containing the permuted feature. The difference of MSEs between the permuted data model and the original model is again computed. Just as before, if the original predictions clearly outperform the permutation predictions, then the variable is important.
The LOCO variable importance will be expressed in similar fashion to the PaP and DaP methods in Section 1.2. However, in this syntax, the index provides information about the model used to extract prediction and the training data that generated that model. Thus,
perm_LOCOj=√tMSE∼j−MSEMSE, | (1.5) |
where MSE is the validation mean squared error from the original model, just as in Section 1.2. The only difference between this and Eq (1.3) is the substitution of vMSE∼j with tMSE∼j. Here, tMSE∼j is the MSE generated with the original validation data but from a new regression model where training values of the jth predictor have been permuted.
Just like DaP techniques, LOCO variable importances can be assessed by rescaling each variable so the distribution center is 0 and then setting the values of the variable to 0. The structure is identical to Eq (1.5), with the exception of substituting notation for dropping a variable rather than permuting it:
drop_LOCOj=√tMSE−j−MSEMSE, | (1.6) |
where tMSE−j is the MSE generated with the original validation data but from a new regression model where training values of the jth predictor have all been set to the central value of 0.
Similar to Section 1.2, these importance metrics are equivalent if tMSE∼j=tMSE−j.
Using the standard regression metrics and the machine learning importance definitions listed above, we designed several simulations to assess the relationships among these metrics. The general architecture is to build both a training and validation dataset of identical sizes and structures with established coefficients and variable relations. In our subsequent methods and analyzes, we use only the training data for model creation, while we use the validation data to assess variable importance. We then collect regression metrics and compute PaP and LOCO metrics. Finally, we plot pairwise scatterplots and correlations amongst these importance values to assess the relationship between them. Higher correlations between metrics provide an empirical foundation for showing proportionality and agreement between variable importance assessments. We utilize the definitions in Sections 1.2 and 1.3 when computing permutation and dropout variable importance metrics [8].
For our first simulation, we let six predictor variables be independent and identically distributed (iid) from a N(0,1) distribution. Here, iid implies that all of the features are orthogonal to each other. We generated 1000 training observations and 1000 validation observations for each of these variables and then created the response variable values using the following equation:
y=5v1+4v2+3v3+2v4+1v5+0v6+ϵ. | (2.1) |
where initially ϵiid∼N(0,1) and then in a second iteration ϵiid∼N(0,10).
For our next simulation, we utilize a data structure from Strobl et al. [7] that allows for high collinearity among some of the predictor variables. In this architecture, we use a linear equation with twelve predictor variables and 1000 observations in the training and validation sets.
The regression coefficients for the predictor variables are chosen as follows:
y=5Cor1+5Cor2+2Cor3+0Cor4+5v5+5v6+2v7+0v8−12+ϵ, | (2.2) |
where initially ϵiid∼N(0,1) and then in a second iteration ϵiid∼N(0,10).
The predictor variables are sampled from a multivariate normal distribution:
Cor1,...,Cor4,v5,...,v12∼N(0,Σ). |
The covariance structure Σ is chosen such that all variables have unit variance σi,i=1 and the first four predictor variables are block-correlated with σi,j=0.95 for i≠j≤4, while the rest are orthogonal with σi,j=0.
We expand the previous simulation to create nonlinear datasets. We again use 12 predictor variables and 1000 observations. We initially sample the predictors from the exact multivariate normal distribution described in Section 2.2 to impose correlations. We then take the cumulative distribution function of each predictor to convert it to a standard uniform distribution, U(0,1). We multiply these values by 2 and subtract 1 from them to provide a new distribution of U(−1,1) for each predictor.
The regression equation matches the one found in Section 2.2, except we square each variable as follows:
y=5Cor21+5Cor22+2Cor23+0Cor24+5v25+5v26+2v27+0v28−12+ϵ, | (2.3) |
where ϵiid∼N(0,0.1).
Leaning heavily on the architecture in Section 2.3, we now create a response using cosine relations with the predictors. We sample the predictors from the same technique described in Section 2.3 to impose correlations and create standard uniform distributions, U(0,1). Instead of converting this to U(−1,1), we convert it to U(−4π,4π) by multiplying the values by 8π and subtracting 4π from them.
The regression equation matches that found in Section 2.2, except we remove the error term and take the cosine of each variable as follows:
y= 5cos(Cor1)+5cos(Cor2)+2cos(Cor3)+0cos(Cor4) + 5cos(v5)+5cos(v6)+2cos(v7)+0cos(v8−12). | (2.4) |
Finally, we generate interaction datasets of 1000 observations for 8 predictor variables and an error (ϵ) term. Each of the predictors is orthogonal and identically distributed from a N(0,1) distribution. We then create the response with this equation:
y=4v1v2+2v3v4+1v5v6+0v7v8+ϵ, | (2.5) |
where ϵiid∼N(0,0.1).
For each linear equation, we fit a linear regression model on the training data. The regression model summary provides estimates for the true equation coefficients and t-statistics. We collect and compare these to several machine learning assessments of importance and to the true coefficients.
For all datasets, except the orthogonal data, we fit a random forest regression model on the training data. In this case, we compare machine learning variable importances to the true coefficients, regression metrics (if the equation is linear), and the default random forest variable importance technique of OOB PaP discussed in Section 1.2.
The machine learning assessments that we will collect are the PaP, DaP, perm_LOCO, and drop_LOCO metrics discussed in Sections 1.2 and 1.3. For each metric, large values suggest higher variable importance, while small values indicate low variable importance.
We now provide pairwise scatterplots and correlations between each of the variable importance metrics calculated for our simulated datasets. We also show results relating to random forest models and compare their default importance metric to other PaP metrics as functions of the dominant hyper-parameter mtry.
We begin with our dataset where variables are all orthogonal. The importance values and their pairwise plots are provided in Figure 1. For this analysis, the regression R2≈0.98.
From Figure 1, we observe the following when variables are orthogonal:
● All variable importance metrics have a near perfect correlation with an average of 1.00.
● While this example is trivial, these results do not deviate from expectations and illustrate agreement between all importance metrics for orthogonal predictors such as principal components.
We will now use an identical regression structure but increase the standard deviation of the noise so that ϵ∼N(0,10). This yields a massive drop in the regression R2≈0.35. The plots of these results are in Figure 2.
From Figure 2, we observe the following when increasing the error for the response variable:
● All variable importance metrics have a strong association with an average correlation of 0.98.
● These results illustrate agreement between all importance metrics for orthogonal predictors.
We move to the dataset where some variables possess high collinearity. The pairwise plots of importance assessments for a linear regression model are provided in Figure 3. For this analysis, ϵ∼N(0,1) and the regression R2≈0.995.
From Figure 3, we observe the following when variables are highly collinear:
● Coefficients have perfect correlation with estimates but only moderate correlation with t-statistics.
● There are two blocks of high similarity metrics.
● The first block involving the true coefficients, the regression estimates, and PaP techniques has an average correlation of 1.00.
● The second block, involving t-statistics and LOCO techniques, has an average correlation of 1.00.
● In both blocks, the respective permute and drop methods have a perfect correlation of 1.00.
We now analyze this same dataset utilizing a random forest model. The pairwise plots of importance are provided in Figure 4. We keep the linear regression estimates and t-statistics from Figure 3, but now we perform the PaP and LOCO methods on the random forest model.
From Figure 4, we observe the following for high-collinearity data:
● The same two blocks of high-similarity metrics found in Figure 3 are observed here.
● The first block, the true coefficient and PaP techniques, has an average correlation of 0.99.
● The second block involving the regression t-statistics, the OOB PaP, and both LOCO techniques has an average correlation of 0.99.
● In both blocks, the permute and drop methods have a near perfect correlation of 1.00.
● The default importance method for random forests, OOB PaP, aligns with the t-statistics, while the other PaP methods align with the coefficients.
We now use an identical regression structure, but increase the error so ϵ∼N(0,10). This yields a large drop in the regression R2≈0.67. These results are plotted in Figure 5.
From Figure 5, we observe the following when increasing the error for the response variable:
● High and low correlation patterns align with those identified in Figure 3.
● The first block involving the true coefficients, the regression estimates, and both PaP techniques has an average correlation of 0.98.
● The second block, involving t-statistics and LOCO techniques, has an average correlation of 0.98.
● In each block, the permutation and dropout methods have nearly perfect correlations ≈ 0.99.
We now analyze this same dataset utilizing a random forest model. The pairwise plots of importance metrics are provided in Figure 6. We keep the linear regression estimates and t-statistics from Figure 5, but now we perform the PaP and LOCO methods on the random forest model.
From Figure 6, we observe the following for the high-collinearity data:
● The same blocks of high-similarity metrics are observed again.
● The first block involving the true coefficients, the regression estimates, and both PaP techniques has an average correlation of 0.95.
● The second block involving the t-statistics, the OOB PaP, and both LOCO techniques has an average correlation of 0.89, but it moves up to 0.98 when OOB PaP is removed.
● In both blocks, the respective permutation and dropout methods have a near perfect correlation of 0.98.
● The default importance method for random forests, OOB PaP, is the least stable metric in terms of alignment with other metrics.
We now offer results exclusively focused on our random forest models. In Section 1.2, we mention the hyper-parameter mtry and prior research assessing how variable importance fluctuates based on mtry [8]. Moving forward, we discuss plots that show how a few importance metrics change across mtry. These metrics include the default OOB PaP, the PaP and DaP metrics (Section 1.2), and a variation of PaP done on the training data instead of our validation data.
We start with our simulation from Section 2.2, with ϵ∼N(0,1). In Figure 4, we show importance metrics for a default random forest, where mtry = 4. Here, we utilize a Monte Carlo simulation of 20 replicates to build random forests for mtry = 1, 2, ..., 12.
From Figure 7, we observe the following:
● The OOB plot experiences a distinct shift or bias between the variables possessing coefficients of 5, for all mtry.
● The Train PaP experiences a distinct bias such that the importance of a pure noise variable, V8, is well above 0 for all mtry, especially for lower values of mtry.
● As mtry increases, the plots generally trend toward importances that are more proportional with the true coefficients.
● The Validation DaP spread is a bit smaller than the Validation PaP, suggesting slightly more variance in the PaP technique.
● The Validation DaP and PaP plots appear superior to the others due to their lack of bias and shifts in the importance values.
We repeat this assessment for our nonlinear datasets, beginning with the simulation where each feature has a quadratic relation with the response. The simulation is described in Section 2.3. We again utilize a Monte Carlo simulation of 20 replicates to build random forests for all values of mtry.
From Figure 8, we observe the following:
● Each plot experiences a shift between the variables possessing coefficients of 5, for all mtry.
● The OOB metrics contain a much stronger shift between the variables possessing coefficients of 5 than the other importance metrics.
● The Train PaP again experiences a distinct bias such that the pure noise variable, V8, is well above 0 for all mtry.
● The plots again trend toward importances that are more proportional with the true coefficients as mtry increases.
● The Validation DaP spread is again slightly smaller than the Validation PaP, suggesting slightly more variance in the PaP technique.
● The Validation DaP and PaP plots again appear superior to the others due to their reduced bias and shifts in the importance values.
We then expand to the structure where each feature has a cosine relation with the response, as described in Section 2.4.
From Figure 9, we observe the following:
● All plots experience a shift between the correlated variables and the orthogonal variables across mtry.
● The OOB metrics contain a much stronger shift between the correlated and orthogonal variables than the other importance metrics.
● The Train PaP experiences an enormous positive bias in the importance of V8.
● Each of the four importance metrics has at least a slight bias in the importance of V8, but the Validation DaP consistently has the lowest bias.
● The Validation DaP metric appears superior, especially when compared with the OOB and Train PaP.
Finally, we explore the situation where each variable relates to the response through an interaction. The data generation process is shown in Section 2.5.
From Figure 10, we observe the following:
● The OOB plot experiences the greatest spread in importance values.
● The Train PaP experiences a distinct positive bias in the importance values of V7 and V8.
● As mtry increases, each of the plots generally trends toward importances that are more proportional with the true coefficients.
● The gap between coefficients of 2 and 1 is much larger for the OOB plot than the other plots.
● The Validation DaP spread is just slightly smaller than the Validation PaP.
Our results highlight some powerful discoveries about permutation and variable deletion techniques. First and most notably, they provide valuable empirical evidence of a very high association between permuting a variable and dropping that variable if the structures are fundamentally equivalent.
This work suggests that t-statistics have high alignment with the LOCO technique for permutation and dropout. Mathematically, tj≈perm_LOCOj≈drop_LOCOj. If surrogate t-statistic importances are desired in machine learning, then utilizing a LOCO technique appears to be a reasonable approach to approximate them. However, it is noteworthy that this can often be computationally expensive, especially for large datasets.
Meanwhile, the true coefficients have strong alignment with the regression estimated coefficients and the PaP and DaP methods. This can be expressed as βj≈ˆβj≈PaPj≈DaPj. If interest is predominately in predictor relationships with the response rather than marginal predictive capacity, then these metrics would be preferred. Recognizing this relationship, PaP or DaP techniques could be employed to obtain meaningful surrogates to the functional equation coefficients. We especially note from our results that these should be calculated using validation data over training data due to biases in variables with lower importance. If no reasonable validation set is available, the same process might be done using a k-fold cross-validation technique.
Our work also suggests a clear difference between the random forest OOB importance and the validation PaP and DaP importances. This contradicts common intuition that they should be equal or proportional. Further consideration led us to realize that OOB importance assesses the variables in the individual trees and aggregates them, while Validation PaP and DaP assess the variables in the entire forest. If precision of estimating importance values matters, then the Validation PaP or DaP might be preferred over the OOB PaP.
In summary, we have shown that permutation techniques and dropout techniques are approximately equal. We also illustrate that manual PaP and DaP methods are not equal to the OOB PaP. Even more noteworthy, our work shows that equation coefficients and regression estimates have strong associations with manual PaP metrics, while t-statistics have strong associations with LOCO metrics. This implies that some excellent future theoretical work may be available to relate these approaches to mathematically well-defined regression metrics. Ultimately, if a machine learning project desires a certain regression metric, our work suggests which variable importance techniques should be used to obtain an appropriate surrogate.
The authors declare they have not used Artificial Intelligence (AI) tools in the creation of this article.
The authors declare there is no conflicts of interest.
The code used to generate the data and figures in this report can be found at:
[1] |
Huang XMH, Zorman CA, Mehregany M, et al. (2023) Nanodevice motion at microwave frequencies. Nature 421: 496–497. https://doi.org/10.1038/421496a doi: 10.1038/421496a
![]() |
[2] |
Yang X, Yang XZ, Sun RY, et al. (2019) Obtaining atomically smooth 4H-SiC (0001) surface by controlling balance between anodizing and polishing in electrochemical mechanical polishing. Nanomanuf Metrol 2: 140–147. https://doi.org/10.1007/s41871-019-00043-5 doi: 10.1007/s41871-019-00043-5
![]() |
[3] |
Mehregany M, Zorman CA, Rajan N, et al. (1998) Silicon carbide MEMS for harsh environments. P IEEE 86: 1594–1609. https://doi.org/10.1109/5.704265 doi: 10.1109/5.704265
![]() |
[4] |
Ekinci KL (2005) Electromechanical transducers at the nanoscale: actuation and sensing of motion in nanoelectromechanical systems (NEMS). Small 1: 786–97. https://doi.org/10.1002/smll.200500077 doi: 10.1002/smll.200500077
![]() |
[5] |
Yoon HS, Park B, Jun SC (2013) Surface roughness effects on the frequency tuning performance of a nanoelectromechanical resonator. Nanoscale Res Lett 8: 270. https://doi.org/10.1186/1556-276X-8-270 doi: 10.1186/1556-276X-8-270
![]() |
[6] |
Lee YJ, Wang H (2021) Characterizing crack morphology toward improving ductile material removal of calcium fluoride. Ceram Int 47: 28543–28556. https://doi.org/10.1016/j.ceramint.2021.07.012 doi: 10.1016/j.ceramint.2021.07.012
![]() |
[7] |
Luo XC, Goel S, Reuben RL (2012) A quantitative assessment of nanometric machinability of major polytypes of single crystal silicon carbide. J Eur Ceram Soc 32: 3423–3434. https://doi.org/10.1016/j.jeurceramsoc.2012.04.016 doi: 10.1016/j.jeurceramsoc.2012.04.016
![]() |
[8] |
Wu ZH, Liu WD, Zhang LC (2017) Revealing the deformation mechanisms of 6H-silicon carbide under nano-cutting. Comp Mater Sci 137: 282–288. https://doi.org/10.1016/j.commatsci.2017.05.048 doi: 10.1016/j.commatsci.2017.05.048
![]() |
[9] |
Tian Z, Chen X, Xu X (2020) Molecular dynamics simulation of the material removal in the scratching of 4H-SiC and 6H-SiC substrates. Int J Extreme Manuf 2: 045104. https://doi.org/10.1088/2631-7990/abc26c doi: 10.1088/2631-7990/abc26c
![]() |
[10] |
Chavoshi SZ, Luo XC (2016) Molecular dynamics simulation study of deformation mechanisms in 3C-SiC during nanometric cutting at elevated temperatures. Mat Sci Eng A-Struct 654: 400–417. https://doi.org/10.1016/j.msea.2015.11.100 doi: 10.1016/j.msea.2015.11.100
![]() |
[11] |
Wu Z, Liu W, Zhang L, et al. (2020) Amorphization and dislocation evolution mechanisms of single crystalline 6H-SiC. Acta Mater 182: 60–67. https://doi.org/10.1016/j.actamat.2019.10.037 doi: 10.1016/j.actamat.2019.10.037
![]() |
[12] |
Goel S, Stukowski A, Luo XC, et al. (2013) Anisotropy of single-crystal 3C-SiC during nanometric cutting. Modell Simul Mater Sci Eng 21: 065004. https://doi.org/10.1088/0965-0393/21/6/065004 doi: 10.1088/0965-0393/21/6/065004
![]() |
[13] |
Xiao GB, To S, Zhang GQ (2015) The mechanism of ductile deformation in ductile regime machining of 6H SiC. Comp Mater Sci 98: 178–188. https://doi.org/10.1016/j.commatsci.2014.10.045 doi: 10.1016/j.commatsci.2014.10.045
![]() |
[14] |
Tian D, Xu Z, Liu L, et al. (2021) In situ investigation of nanometric cutting of 3C-SiC using scanning electron microscope. Int J Adv Manuf Tech 115: 2299–2312. https://doi.org/10.1007/s00170-021-07278-x doi: 10.1007/s00170-021-07278-x
![]() |
[15] |
Zhang T, Jiang F, Huang H, et al. (2021) Towards understanding the brittle–ductile transition in the extreme manufacturing. Int J Extreme Manuf 3: 022001. https://doi.org/10.1088/2631-7990/abdfd7 doi: 10.1088/2631-7990/abdfd7
![]() |
[16] |
Mishra M, Tangpatjaroen C, Szlufarska I (2014) Plasticity-controlled friction and wear in nanocrystalline SiC. J Am Ceram Soc 97: 1194–1201. https://doi.org/10.1111/jace.12810 doi: 10.1111/jace.12810
![]() |
[17] |
Liu Y, Li B, Kong L (2018) Molecular dynamics simulation of silicon carbide nanoscale material removal behavior. Ceram Int 44: 11910–11913. https://doi.org/10.1016/j.ceramint.2018.03.195 doi: 10.1016/j.ceramint.2018.03.195
![]() |
[18] |
Liu Y, Li B, Kong L (2018) A molecular dynamics investigation into nanoscale scratching mechanism of polycrystalline silicon carbide. Comp Mater Sci 148: 76–86. https://doi.org/10.1016/j.commatsci.2018.02.038 doi: 10.1016/j.commatsci.2018.02.038
![]() |
[19] |
Zhao L. Hu WJ, Zhang Q, et al. (2021) Atomistic origin of brittle-to-ductile transition behavior of polycrystalline 3C-SiC in diamond cutting. Ceram Int 47: 23895–23904. https://doi.org/10.1016/j.ceramint.2021.05.098 doi: 10.1016/j.ceramint.2021.05.098
![]() |
[20] |
Zhao L, Zhang JG, Fu YF, et al. (2022) Thermal softening-suppressed inter-granular embrittlement of polycrystalline 3C-SiC under diamond cutting. Mater Design 223: 111250. https://doi.org/10.1016/j.matdes.2022.111250 doi: 10.1016/j.matdes.2022.111250
![]() |
[21] |
Zhao L, Zhang JJ, Zhang JG, et al. (2023) Numerical simulation of materials-oriented ultra-precision diamond cutting: review and outlook. Int J Extreme Manuf 5: 022001. https://doi.org/10.1088/2631-7990/acbb42 doi: 10.1088/2631-7990/acbb42
![]() |
[22] |
Chavoshi SZ, Tschopp MA, Branicio PS (2019) Transition of deformation mechanisms in nanotwinned single crystalline SiC. Philos Mag 99: 21. https://doi.org/10.1080/14786435.2019.1637033 doi: 10.1080/14786435.2019.1637033
![]() |
[23] |
Chavoshi SZ, Xu S (2018) Tension-compression asymmetry in plasticity of nanotwinned 3C-SiC nanocrystals. J Appl Phys 124: 095103. https://doi.org/10.1063/1.5046949 doi: 10.1063/1.5046949
![]() |
[24] |
Wang ZG, Li JB, Gao F, et al. (2010) Tensile and compressive mechanical behavior of twinned silicon carbide nanowires. Acta Mater 58: 1963–1971. https://doi.org/10.1016/j.actamat.2009.11.039 doi: 10.1016/j.actamat.2009.11.039
![]() |
[25] |
Lin ZJ, Wang L, Zhang J, et al. (2010) Nanoscale twinning-induced elastic strengthening in silicon carbide nanowires. Scripta Mater 63: 981–984. https://doi.org/10.1016/j.scriptamat.2010.07.023 doi: 10.1016/j.scriptamat.2010.07.023
![]() |
[26] |
Chavoshi SZ, Xu S (2018) Twinning effects in the single/nanocrystalline cubic silicon carbide subjected to nanoindentation loading. Materialia 3: 304–325. https://doi.org/10.1016/j.mtla.2018.09.003 doi: 10.1016/j.mtla.2018.09.003
![]() |
[27] |
Vashishta P, Kalia RK, Nakano A, et al. (2007) Interaction potential for silicon carbide: A molecular dynamics study of elastic constants and vibrational density of states for crystalline and amorphous silicon carbide. J Appl Phys 101: 103515. https://doi.org/10.1063/1.2724570 doi: 10.1063/1.2724570
![]() |
[28] |
Kikuchi H, Kalia RK, Nakano A, et al. (2005) Brittle dynamic fracture of crystalline cubic silicon carbide (3C-SiC) via molecular dynamics simulation. J Appl Phys 98: 103524. https://doi.org/10.1063/1.2135896 doi: 10.1063/1.2135896
![]() |
[29] |
Zhao L, Zhang JJ, Zhang JG, et al. (2021) Atomistic investigation of machinability of monocrystalline 3C-SiC in elliptical vibration-assisted diamond cutting. Ceram Int 47: 2358–2366. https://doi.org/10.1016/j.ceramint.2020.09.078 doi: 10.1016/j.ceramint.2020.09.078
![]() |
[30] |
Stukowski A, Bulatov VV, Arsenlis A (2012) Automated identification and indexing of dislocations in crystal interfaces. Modelling Simul Mater Sci Eng 20: 085007. https://doi.org/10.1088/0965-0393/20/8/085007 doi: 10.1088/0965-0393/20/8/085007
![]() |
[31] |
Plimpton S (1995) Fast parallel algorithms for short-range molecular dynamics. J Comput Phys 117: 1–19. https://doi.org/10.1006/jcph.1995.1039 doi: 10.1006/jcph.1995.1039
![]() |