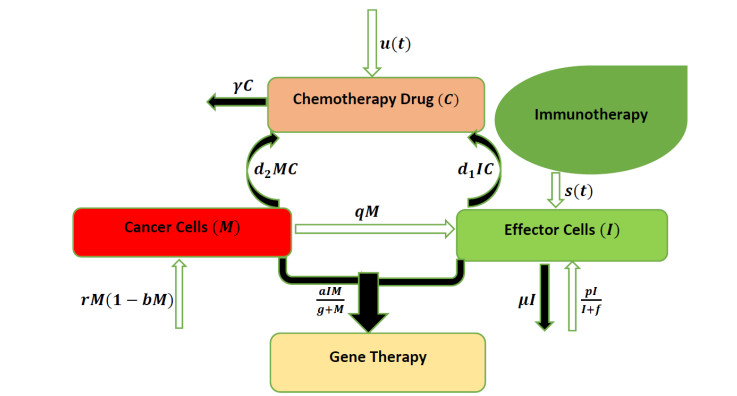
Characterization of new innovative natural seed fibers from seedpods or fruits of various plants has increased popularly in textile, automotive, and construction industries due to various aspects, availability, and biodegradability. In addition, these fibers provide sustainable solutions to support technological innovation in numerous industrial applications. The current research aims to investigate the new lignocellulose fibers extracted from Wrightia tinctoria seedpods. The obtained Wrightia tinctoria seed fibers (WTSFs) were characterized via Scanning electron microscope (SEM), Fourier Transform Infrared-ray (FTIR), X-ray diffraction (XRD), Thermogravimetric analysis (TGA), and Differential scanning calorimetry (DSC) to understand the fibers physicochemical properties. Complete experimental study of natural seed fibers of Wrightia tinctoria found to be a lignocellulose fiber and contains unique characteristics. Surface morphological studies reveal that, WTSFs contain smoother surface which is beneficial to develop a good bond with matrix while making composites. It does not get wet quickly with water due to fatty, wax, mineral matters, and higher lignin content on the fiber surface which means the fiber is soft compared with other natural seed fibers. These unique properties of WTSFs ascertain as a suitable material for polymer fabrication process, which would be favourable to develop good bonding with the matrix for making composites and also useful for insulating composite materials.
Citation: SYED HABIBUNNISA, Ruben Nerella, Srirama Chand Madduru, RajaGopal Reddy S. Physicochemical characterization of lignocellulose fibers obtained from seedpods of Wrightia tinctoria plant[J]. AIMS Materials Science, 2022, 9(1): 135-149. doi: 10.3934/matersci.2022009
[1] | Ahmed J. Abougarair, Mohsen Bakouri, Abdulrahman Alduraywish, Omar G. Mrehel, Abdulrahman Alqahtani, Tariq Alqahtani, Yousef Alharbi, Md Samsuzzaman . Optimizing cancer treatment using optimal control theory. AIMS Mathematics, 2024, 9(11): 31740-31769. doi: 10.3934/math.20241526 |
[2] | Monica Conti, Stefania Gatti, Alain Miranville . Mathematical analysis of a phase-field model of brain cancers with chemotherapy and antiangiogenic therapy effects. AIMS Mathematics, 2022, 7(1): 1536-1561. doi: 10.3934/math.2022090 |
[3] | Anusmita Das, Kaushik Dehingia, Hemanta Kumar Sharmah, Choonkil Park, Jung Rye Lee, Khadijeh Sadri, Kamyar Hosseini, Soheil Salahshour . Optimal control of effector-tumor-normal cells dynamics in presence of adoptive immunotherapy. AIMS Mathematics, 2021, 6(9): 9813-9834. doi: 10.3934/math.2021570 |
[4] | Hussein Raad, Cyrille Allery, Laurence Cherfils, Carole Guillevin, Alain Miranville, Thomas Sookiew, Luc Pellerin, Rémy Guillevin . Simulation of tumor density evolution upon chemotherapy alone or combined with a treatment to reduce lactate levels. AIMS Mathematics, 2024, 9(3): 5250-5268. doi: 10.3934/math.2024254 |
[5] | Xingxiao Wu, Lidong Huang, Shan Zhang, Wenjie Qin . Dynamics analysis and optimal control of a fractional-order lung cancer model. AIMS Mathematics, 2024, 9(12): 35759-35799. doi: 10.3934/math.20241697 |
[6] | Noufe H. Aljahdaly, Nouf A. Almushaity . A diffusive cancer model with virotherapy: Studying the immune response and its analytical simulation. AIMS Mathematics, 2023, 8(5): 10905-10928. doi: 10.3934/math.2023553 |
[7] | Zholaman Bektemessov, Laurence Cherfils, Cyrille Allery, Julien Berger, Elisa Serafini, Eleonora Dondossola, Stefano Casarin . On a data-driven mathematical model for prostate cancer bone metastasis. AIMS Mathematics, 2024, 9(12): 34785-34805. doi: 10.3934/math.20241656 |
[8] | Hsiu-Chuan Wei . Mathematical modeling of ER-positive breast cancer treatment with AZD9496 and palbociclib. AIMS Mathematics, 2020, 5(4): 3446-3455. doi: 10.3934/math.2020223 |
[9] | Eminugroho Ratna Sari, Lina Aryati, Fajar Adi-Kusumo . An age-structured SIPC model of cervical cancer with immunotherapy. AIMS Mathematics, 2024, 9(6): 14075-14105. doi: 10.3934/math.2024685 |
[10] | Hengjie Peng, Changcheng Xiang . A Filippov tumor-immune system with antigenicity. AIMS Mathematics, 2023, 8(8): 19699-19718. doi: 10.3934/math.20231004 |
Characterization of new innovative natural seed fibers from seedpods or fruits of various plants has increased popularly in textile, automotive, and construction industries due to various aspects, availability, and biodegradability. In addition, these fibers provide sustainable solutions to support technological innovation in numerous industrial applications. The current research aims to investigate the new lignocellulose fibers extracted from Wrightia tinctoria seedpods. The obtained Wrightia tinctoria seed fibers (WTSFs) were characterized via Scanning electron microscope (SEM), Fourier Transform Infrared-ray (FTIR), X-ray diffraction (XRD), Thermogravimetric analysis (TGA), and Differential scanning calorimetry (DSC) to understand the fibers physicochemical properties. Complete experimental study of natural seed fibers of Wrightia tinctoria found to be a lignocellulose fiber and contains unique characteristics. Surface morphological studies reveal that, WTSFs contain smoother surface which is beneficial to develop a good bond with matrix while making composites. It does not get wet quickly with water due to fatty, wax, mineral matters, and higher lignin content on the fiber surface which means the fiber is soft compared with other natural seed fibers. These unique properties of WTSFs ascertain as a suitable material for polymer fabrication process, which would be favourable to develop good bonding with the matrix for making composites and also useful for insulating composite materials.
Cancer, the disease that triggers the unregulated development of irregular cells in the human body, is one of the leading mortality factors among humankind. As the disorder causes the disease to go to the tissue level, precise detection at an early stage becomes challenging. Another obstacle faced at the treatment level is to decide the therapeutic effectiveness of the drugs to be administered. Therefore, many researchers worldwide are carrying out their research work to find out the cause of the origin of the disease and impart a patient-friendly, effective, and successful treatment method.
In cancer treatment, immunotherapies are used to enhance the host anti-tumour immune response by perturbing the tumor microenvironment. Over the past few years, different types of immunotherapies have been developed, spanning from Immune-Checkpoint Blockade (ICB) to strategies that boost the T cell activity [1,2]. But, a high dose of immunotherapy to a patient can induce negative responses such as fever, chills, weakness, nausea, etc. [3,4].
Chemotherapy is an effective method to fight against cancer [5]. However, it has a substantial adverse effect as induction of chemotherapeutic drugs depletes the immune system and makes the patients vulnerable to harmful infections. Thus, after the immune-depleting phase of chemotherapy, it becomes an absolute necessity to improve the patient's immune system. Therefore, it is a difficult challenge during the chemotherapy process to preserve a stable immune system and combat cancer successfully [6]. Cancer chemotherapy is usually administered on a cyclic basis. When an anti-cancer medicine is injected into the body, all harmless cells also get destroyed along with malignant cells. As a result, white blood cell counts decline to low rates, and life-threatening fever may occur [5]. Thus, control of the chemotherapy dosage becomes a very critical aspect in cancer chemotherapy design [7,8].
At the molecular level, cancer can be characterized as a genetic defect in the cell cycle. Gene therapy is a common form of immunotherapy that strengthens the body's immunity and aims to cure genetic conditions. By inserting a well-designed gene into the cells of the patients, correction can be carried out in the inborn inaccuracy of metabolism, inherited hereditary abnormality, etc.[9].
Ongoing research of clinical studies is now developing in cancer eradication policies by incorporating two or more drugs [10]. The application of chemotherapy and gene therapy is now in operation, which has demonstrated that this type of treatment reduces the primary tumor, avoids intra-peritoneal metastases, and restricts harmful side effects [11]. The application of TRAIL gene therapy and chemotherapy is also successful in the diagnosis of metastatic diseases [12]. Anti-cancer gene therapy under review is generally conducted in a two-phase cycle. The first step is a successful search for chemo-resistant cells during chemotherapy which results in an increased proportion of transfected cells. The population of the transfected cells must surpass that of the mutant cells to maintain the optimum relationship between the species necessary for the bystander effect. The second step consists of a negative selection step accomplished by ganciclovir injection. Such cells that are vulnerable to antiviral drug treatment through transfection or bystander effect will undergo activated apoptosis [13].
Mathematical modeling since a long time back has been used as a tool for finding out some solutions to the problems related to cancer and other dreaded diseases faced by the human population [14,15]. Kuznetsov et al. [16] proposed a model showing the reaction of the cytotoxic T lymphocyte to the development of the immunogenic tumor. Kirschner and Panetta [17] proposed a model to explore the effects of IL-2 therapy and ACI therapy on tumor-immune dynamics. Kolev et al. [18] presented a model that identified the early phases of a solid tumor or all phases of leukemia. A variety of clinical trials have been performed to investigate the impact of the immune system on the destruction of tumor cells in the body by inducing the host's immune response to destroy cancer cells [19,20]. As the tumor grows in the human body, the immune system seeks to recognize and destroy the tumor cells as soon as possible. In [21], Rihan et al. examined the interactions among tumor cells, immune-induced cells, and interleukin-2 (IL-2) cytokines. Very recently, in COVID-19 pandemic situation, Musa et al. [22] examined the dynamical feature of a deterministic COVID-19 model based on the data of Nigeria and also investigated the imapcts of awarness program and different hospitalization strategies in the society to effectively mitigate the epidemic. In the work [23], the authors formulated a model based on the data of Pakistan to investigate the role of quarantine and isolation in controlling the COVID-19 disease. Optimal control strategies have been proposed for a model in [24] to minimize the population number of infected and asymptotically infected people.
In the present day, researchers are interested in a combination of two or more therapies in the chemotherapeutic treatment protocols. Until now, several significant works have been carried out in the field of cancer chemotherapeutic modeling. De Pillis et al. [25] updated their previously proposed model [6] with the inclusion of NK cells, CD8+T cells, and IL-2 therapy. Their results revealed that while eliminating cancerous tissue in the presence of chemotherapy, immunotherapy is helpful for low immune efficacy patients. The effect of anti-angiogenic agents in controlling cancer with chemotherapy has been demonstrated in [26]. An appropriate optimal combination treatment of vaccine therapy and chemotherapy for controlling cancer dynamics has been presented in [27]. In consideration of radiotherapy as a treatment of cancer followed by chemotherapy, a periodic mathematical model has been proposed by Liu and Yang [28]. Guiraldello et al. [29] presented a mathematical model involving partial differential equations to show the behavior of tumor development in the presence of two chemotherapy protocols; Maximum Tolerated Dose (MTD) and metronomic, as well as two methods of drug delivery. They have also evaluated the effectiveness of both protocols. Pang et al. [30] explored the effect of a combination of immunotherapy and chemotherapy, single chemo, and single immunotherapy in their work. Rodrigues et al. [31] explored a model by considering chemo-immunotherapy as a treatment to reduce unwanted cytotoxic effects on immune cells of a cancer patient. In [32], the authors presented a model for the growth of the immune system during chemotherapy. Alqudah [33] introduced a new mathematical model for the treatment of cancer as a combination of chemotherapy and stem cell therapy. In 2013, Tsygvinsev et al. [34] proposed a mathematical model of gene therapy for cancer treatment by modifying an already investigated model [17]. We have considered a modified version of the model proposed by Tsygvintsev et al. [34] in which the authors studied the effects of gene therapy and immunotherapy. In contrast, in this paper we have introduced chemotherapy together with gene and immunotherapy as the treatment protocol.
Controlling drugs in the treatment of cancer patients is a big problem for researchers. Many researchers are working on optimal drug control for cancer treatment. Khajanchi and Ghosh [7] designed a model based on Kuznetsov et al. model [16] with two types of external treatments, one is ACI therapy for anti-tumor activity and another is IL-2 therapy for boosting the immune system to fight against tumor. Moreover, they have found the optimal combination treatment for tumor reduction. Sharma and Samanta [8] have carried out another optimal chemotherapeutic strategy for a tumor growth model and addressed that the administration of chemotherapy drug as control reduces the spread of the disease. Rihan et al. [35] established from their model that the performance of the combination therapy protocol of immuno-chemotherapy is better than the standard protocol of chemotherapy alone. d'Onofrio et al. [36] formulated a model for the optimal scheduling of angiogenic inhibitors in combination with a chemotherapeutic agent. In the work [37], the author explored the dynamical behavior of the glioma-immune interaction in conjunction with an optimally controlled immunotherapeutic drug ACI. By considering an abstract mathematical model of cancer chemotherapy, Leszczynski et al. [38] investigated an optimal control problem for a single drug remove and when various pharmacodynamic (PD) and pharmacokinetic (PK) models are included in the modeling. Recently, the authors of [39] designed an optimal model for chemotherapy treatment to find the best rate of drug injection during treatment. Najafi et al. [40] introduced an optimal control homotopy perturbation method to find better outcomes in drug controlling for therapeutic cancer model. Rihan et al. [41] studied an extended work of [17] to a delayed model of tumor-immune interactions and then find the optimal protocol of immuno-chemotherapy, which reduces the tumor load in a few months of therapy. In the work [42], the author performed a detailed analysis to find the optimal regimens of combined chemo-immunotherapy for a PKPD cancer evolution model. Das et al. [43] analyzed an optimal control problem of immuno-chemotherapeutic drugs for a delayed tumor-immune model. In this article, we propose a modified cancer gene therapy model following [34] in the presence of immunotherapy and chemotherapy. To control the immuno-chemo-drug toxicity effect on the patient, we also construct an optimal control problem for the proposed model which was not discussed in [34].
In section 2, we have described the model about which we have investigated in the subsequent sections.
We already mentioned several research works to understand the effectiveness and side effects of chemotherapy and immunotherapy in cancer treatment. In work [34], the authors showed that high levels of immunotherapy and 'cancer clearance term' of gene therapy would be able to clear cancer optimally from patients' body. Lestari et al. [44] studied the local stability analysis of the proposed model in [34]. In [45], the authors estimated the external parameters of the model in [34] for which the growth of tumor cells remains under control. For further study on the applications of gene therapy in cancer treatment models, the authors would like to refer to the works [34,44] to the reader. In this work, we reconstruct the earlier proposed model [34] in combination with immuno-chemo-gene-therapy. The model is built based on interactions among tumor cells, effector immune cells, gene therapy, immunotherapy, and chemotherapeutic drugs. The assumptions imposed on the model are:
A1: Gene therapy detects how tumor cells are different from normal cells, and this can be described by the term qM with a fixed antigenicity q.
A2: Effector immune cells can proliferate themselves with proliferation rate p. However, effector immune cells also have a natural death rate μ.
A3: External source of immunotherapy s(t) (TIL-therapy) boosts the immune system, which is time-dependent.
A4: Cancer cells can grow logistically in the absence of immune cells and treatments.
A5: The interaction of effector cells and cancer cells during gene therapy is considered according to the Michaelis-Menten form −aIMg+M which is usually used for describing anti-tumor immune responses [17]. The term a represents the constant rate of cancer clearance during gene therapy.
A6: Chemotherapy can kill both the cell populations viz. cancer and effector immune cells with different constant rates.
The flowchart of the model is depicted in Figure 1.
Considering above mentioned assumptions and the flowchart, the model [34] can be reformulated as:
dIdt=qM+pII+f−μI+s(t)−d1IC,dMdt=rM(1−bM)−aIMg+M−d2MC,dCdt=u(t)−γC, | (2.1) |
with initial conditions
I(0)≥0,M(0)≥0,C(0)≥0. | (2.2) |
The first equation represents the dynamics of the effector immune cells I(t). qM represents the cancer antigenicity during gene therapy, giving strong immunity to cancer. As the effector cells proliferate themselves, so it can be represented by the term pII+f. −μ represents the half-life of effector cells. The term s(t) is used for describing the dose of immunotherapy drug given, which boosts the immune system. −d1IC is the degradation of effector cells that get killed during chemotherapy.
The second equation describes the variability of the cancerous tumor cells M(t). The term rM(1−bM) represents the logistic growth of cancer cells. −aIMg+M describes the interaction between effector cells and cancer cells during gene therapy. The term −d2MC indicates the degradation of cancerous cells by chemotherapy.
The last equation is the continuous drug administration of chemotherapy, where u(t) represents the dose of the chemotherapeutic drug given, and γ is the per capita decay rate of the chemotherapeutic drug.
Due to bilogical meaning, all values of three state variables must be non-negative. In the following section, we will discuss the positiveness and boundedness of the solutions of the system (2.1).
In order to check the behavior of the solutions of the system (2.1), we have considered the dose of chemotherapeutic drug given u(t) as a constant with value u(t)=u0 and s(t)=s.
Theorem 3.1. Every solution of the system (2.1) with the non-neagtive initial conditions (2.2) are exists in IR3+, and are non-negative for all t≥0.
Proof. It is clear that the uniform continuity and locally Lipschitzian conditions hold for R.H.S of the system (2.1) on its domain. Hence, there exists an unique solution (I(t),M(t),C(t)) of (2.1) with initial conditions I(0)≥0, M(0)≥0, and C(0)≥0 on IR3+. Also, this unique solution is non-neagtive and it will be proved as follows:
We can write the system (2.1) as
dIdt=qM+pII+f−μI+s−d1IC≥pII+f−μI−d1IC,dMdt=rM(1−bM)−aIMg+M−d2MC,dCdt=u0−γC≥−γC. | (3.1) |
Solving (3.1), we get
I(t)≥I(0)e∫t0{pI(t)+f−μ−d1C(t)}dt≥0,M(t)=M(0)e∫t0{r(1−bM(t))−aI(t)g+M(t)−d2C(t)}dt≥0,C(t)≥e−γC≥0. | (3.2) |
Therefore, the solution (I(t), M(t), C(t)) will be non-negative in IR3+ for all t≥0. This completes the proof.
Theorem 3.2. There exists bounded solutions for the model (2.1) subject to initial conditions I(0)≥0, M(0)≥0, and C(0)≥0.
Proof. From the second equation of system ({2.1}) and using the standard Kamke comparison theory [8] to it, we have
dMdt≤rM(1−bM),⟹limt→∞supM(t)≤1b. | (3.3) |
The third equation implies that
C(t)=u0γ+[C(0)−u0γ]e−γt,⟹limt→∞supC(t)≤u0γ. | (3.4) |
Now, using the bounds of M(t) (suppose supM(t)=Ms), the first equation implies that
dIdt≤qMs+pII+f−μI+s,⟹dIdt≤κ+pII+f,where qMs+s=κ(by assumption this is constant)⟹I(t)≤I(0)+∫t0(κ+pI(s)I(s)+f)ds,⟹I(t)≤I(0)+κt+∫t0(pI(s)I(s)+f)ds. | (3.5) |
By using the generalized Gronwall Lemma [35], we get
I(t)<A, | (3.6) |
where, A is uniformly bounded. This completes the proof.
In this section, we will study the existence and stability behaviour of the system (2.1) at various equilibrium points. In order to investigate the dynamics of the system (2.1), we set u(t)=u0, s(t)=s, dIdt=0, dMdt=0, and dCdt=0. The equilibrium points of the system (2.1) are:
(1) The two equilibria E1(I1,0,u0γ) and E2(I2,0,u0γ), where cancerous tumor cells are not present, are termed as healthy equilibria. Here, I1 and I2 are the roots of the equation:
(μ+d1u0γ)I2−(p+s−μf−d1fu0γ)I−sf=0. |
Solving above equation, we get the roots I1 and I2 as,
I1=A+√B2(μ+d1u0γ),I2=A−√B2(μ+d1u0γ), |
where
A=p+s−μf−d1fu0γ,B=(p+s−μf−d1fu0γ)2+4fs(μ+d1u0γ). |
(2) The system exhibits the disease persistent equilibrium at E∗(I∗,M∗,u0γ), where both immune-effector cells and cancerous tumor cells will present. Here,
I∗=(g+M∗){r(1−bM∗)−d2u0γ}a, |
and
M∗=μI∗+d1I∗u0γ−s−pI∗f+I∗q. |
Now, let us study the existence and stability of two equilibria E1 and E2.
E1(I1,0,u0γ) exists only when I1>0 i.e., p+s+√(p+s−μf−d1fu0γ)2+4fs(μ+d1u0γ)>μf+d1fu0γ.
The variational matrix of system (2.1) at E1(I1,0,u0γ) is given by
V(E1)=(pf(I1+f)2−μ−d1u0γq−d1I10r−aI1g−d2u0γ000−γ). |
The eigenvalues of V(E1) are: λ1,1=pf(I1+f)2−μ−d1u0γ, λ2,1=r−aI1g−d2u0γ, and λ3,1=−γ. Clearly, λ3,1<0. Now, E1 is stable if λ1,1<0 and λ2,1<0; this implies pf(I1+f)2−μ−d1u0γ<0 and r−aI1g−d2u0γ<0; which gives u0>γd1[pf(I1+f)2−μ] and r<aI1g+d2u0γ.
E2(I2,0,u0γ) exists only when I2>0 i.e., p+s>√(p+s−μf−d1fu0γ)2+4fs(μ+d1u0γ)+μf+d1fu0γ.
The variational matrix of the system (2.1) at E2(I2,0,u0γ) is given by
V(E2)=(pf(I2+f)2−μ−d1u0γq−d1I20r−aI2g−d2u0γ000−γ). |
The eigenvalues of V(E2) are: λ1,2=pf(I2+f)2−μ−d1u0γ, λ2,2=r−aI2g−d2u0γ, and λ3,2=−γ. Clearly, λ3,2<0. Now, E2 is stable if λ1,2<0 and λ2,2<0; this implies pf(I2+f)2−μ−d1u0γ<0 and r−aI2g−d2u0γ<0; which gives u0>γd1[pf(I2+f)2−μ] and r<aI2g+d2u0γ. Thus, we have the following result.
Theorem 4.1. The healthy equilibrium E1 exists if
p+s+√(p+s−μf−d1fu0γ)2+4fs(μ+d1u0γ)>μf+d1fu0γ, |
and it is locally asymptotically stable if
u0>γd1[pf(I1+f)2−μ] and r<aI1g+d2u0γ. |
Other healthy equilibrium E2 exists if
p+s>√(p+s−μf−d1fu0γ)2+4fs(μ+d1u0γ)+μf+d1fu0γ, |
and it is locally asymptotically stable if
u0>γd1[pf(I2+f)2−μ] and r<aI2g+d2u0γ. |
Next, we will also study the existence and stability behaviour at the disease persistent equilibria E∗.
E∗(I∗,M∗,u0γ) exists only when I∗>0 and M∗>0 i.e, r(1−bM)>d2u0γ and μI∗+d1I∗u0γ>s+pI∗f+I∗.
The variational matrix of the system (2.1) at E∗(I∗,M∗,u0γ) is given by
V(E∗)=(pf(I∗+f)2−μ−d1u0γq−d1I∗−aM∗g+M∗r−2rbM∗−agI∗(M∗+g)2−d2u0γ−d2M∗00−γ). |
One eigenvalue of V(E∗) is −γ and the other two eigenvalues of the matrix can be calculated from the follwing equation
λ2+D1λ+D2=0, | (4.1) |
where
{D1=μ−pf(I∗+f)2+d1u0γ−r+2rbM∗+agI∗(M∗+g)2+d2u0γ,D2=(r−2rbM∗−agI∗(M∗+g)2−d2u0γ)(−μ+pf(I∗+f)2−d1u0γ)+qaM∗g+M∗. |
Since −γ<0, hence, the equilibrium E∗ will be asymptotically stable if D1>0 and D2>0. Hence, we get the following result.
Theorem 4.2. The disease persistent equilibrium E∗ exists if
r(1−bM)>d2u0γ and μI∗+d1I∗u0γ>s+pI∗f+I∗, |
and it is locally asymptotically stable if
{μ−pf(I∗+f)2+d1u0γ−r+2rbM∗+agI∗(M∗+g)2+d2u0γ>0,(r−2rbM∗−agI∗(M∗+g)2−d2u0γ)(−μ+pf(I∗+f)2−d1u0γ)+qaM∗g+M∗>0. |
This section is related to the study of the control problem related to our proposed model (2.1), when we administer immunotherapy and chemotherapy treatments over a fixed period. For the biomedical perspective, we use the concept of optimal control for the model. This addresses how the combination of chemo-gene-immunotherapy may be an efficient treatment to assist the patient fighting against cancer.
To construct and analyze the optimal control problem for our proposed model, we follow the previous works [7,8,43]. As a higher dose of immunotherapy and chemotherapy causes many side effects, the total amount of immuno-chemotherapy agents must be minimized to minimize the tumor size. For that, we assume the immunotherapy and chemotherapeutic drugs are given as the functions s(t) and u(t), which are time-dependent. For the control variables s(t) and u(t), we consider quadratic controls to reflect the extremity of the imposed immunotherapy and chemotherapeutic drugs' side effects. Therefore, the objective functional which is to be minimized is defined as:
Π(s(t),u(t))=∫tf0[ξ1M(t)+12ξ2s2(t)+12ξ3u2(t)]dt, | (5.1) |
where the constants ξ1,ξ2, and ξ3 represent the weight factors of the respective terms which are used for balancing the size of the terms. The first term of the integrand signifies the number of cancerous cells while the second and third reflect the effectiveness of the drugs. Here, we establish an optimal control (s∗,u∗) such that
Π(s∗,u∗)=min{Π(s,t):(s,u)∈Ω}, | (5.2) |
where Ω={(s,u):sanduare measurable, 50≤s≤100,0≤u≤1,andt∈[0,tf]} is the admissible control set. Hence, the problem with the control (s(t),u(t)) becomes
dIdt=qM+pII+f−μI+s(t)−d1IC,dMdt=rM(1−bM)−aIMg+M−d2MC,dCdt=u(t)−γC, | (5.3) |
with initial conditions,
I(0)=I0,M(0)=M0,C(0)=C0, | (5.4) |
and the objective functional
Π(s(t),u(t))=∫tf0[ξ1M+12ξ2s2+12ξ3u2]dt. | (5.5) |
In this subsection, we will discuss the existence of the optimal control of our system (5.3). The solutions of the system (5.3) are bounded in a finite time interval. For proving this, we assume that
→g(t,→W,s,u)=(p000r000−γ)(IMC)+(s0u), | (5.6) |
where →W=(IMC)T. Using the boundedness of the solutions, we get
|→g(t,→W,s,u)|≤|(p000r000−γ)(IMC)|+|(s0u)|. | (5.7) |
As the above system is linear having bounded coefficients in a finite time interval, hence, we conclude that the solutions of the system (5.3) are bounded. Using the theorem proposed by Lukes [46], we get the admissible control class and the corresponding state equations with initial conditions (5.4) are found to be non-empty. Moreover, by deffinition of the set Ω, it is clear that the control set Ω is convex and closed. Since the state solutions are bounded, hence, the continuity of R.H.S of the state system (5.3) holds and is bounded above by a sum of the bounded control and state.
If π(s,u) denotes the integrand of Π(s,u), to prove the convexity of π(s,u) on Ω, we need to show
π[(1−ϕ)v+ϕw]≤[(1−ϕ)π(v)+ϕπ(w)], | (5.8) |
where v=(s1,u1) and w=(s2,u2) are two distinct elements of Ω and 0≤ϕ≤1. Now
π[(1−ϕ)v+ϕw]−[(1−ϕ)π(v)+ϕπ(w)]=ξ1M+ξ22((1−ϕ)s1+ϕs2)2+ξ32((1−ϕ)u1+ϕu2)2−(1−ϕ)(ξ1M+ξ22s21+ξ32u21)−ϕ(ξ1M+ξ22s22+ξ32u22)=ξ22ϕ(ϕ−1)(s1−s2)2+ξ32ϕ(ϕ−1)(u1−u2)2≤0,[sinceϕ∈[0,1],(s1−s2)2,(u1−u2)2>0] |
which implies that the integrand of π(s,u) is convex on Ω. Again,
ξ1M(t)+12ξ2s2(t)+12ξ3u2(t)≥12ξ2s2(t)+12ξ3u2(t)≥η1(s2(t)+u2(t))≥η1(s2(t)+u2(t))−η2, | (5.9) |
where η1=min{ξ22,ξ32}. Therefore, the integrand Π(s,u) is bounded below by η1(s2(t)+u2(t))−η2. Hence, there exists an optimal control (s∗,u∗) for which Π(s,u) is minimized. From the above analysis, we established the following theorem.
Theorem 5.1. There exists an optimal control (s∗,u∗) for a given objective functional
Π(s(t),u(t))=∫tf0[ξ1M+12ξ2s2+12ξ3u2]dt, | (5.10) |
such that Π(s∗,u∗)=min{Π(s,u):(s,u)∈Ω}, where Ω={(s,u):s and uare measurable,50≤s(t)≤100,0≤u(t)≤1, and t∈[0,tf]} subject to the system (5.3) with initial conditions (5.4).
Pontryagins Maximum Principle [47] is invoked on the system (5.3) to derive the conditions for optimal control. For the system (5.3) the Hamiltonian is defined as follows:
H=ξ1M+12ξ2s2+12ξ3u2+θ1[qM+pII+f−μI+s−d1IC]+θ2[rM(1−bM)−aIMg+M−d2MC]+θ3[u−γC], | (5.11) |
where θ1,θ2, and θ3 are the adjoint functions which are to be determined.
Using Pontryagins Maximum Principle [47], the adjoint system and the transversality conditions can be obtained as follows:
dθ1dt=−∂H∂I=θ1[μ+d1C−pf(I+f)2]+θ2aMM+g,dθ2dt=−∂H∂M=θ2[2rbM+agI(g+M)2+d2C−r]−θ1q−ξ1,dθ3dt=−∂H∂C=θ1d1I+θ2d2M+θ3γ. | (5.12) |
The transversality conditions are
θi(tf)=0,i=1,2,3. | (5.13) |
From the optimality conditions of sandu, we have
∂H∂s=ξ2s∗+θ1=0⟹s∗(t)=−θ1(t)ξ2,∂H∂u=ξ3u∗+θ3=0⟹u∗(t)=−θ3(t)ξ3. | (5.14) |
Using the bounds of control s(t)andu(t), we get
s∗={−θ1(t)ξ2,if50<−θ1(t)ξ2<100,50,if−θ1(t)ξ2≤50,100,if−θ1(t)ξ2≥100, | (5.15) |
u∗={−θ3(t)ξ3,if0<−θ3(t)ξ3<1,0,if−θ3(t)ξ3≤0,1,if−θ3(t)ξ3≥1. | (5.16) |
Hence, from the above discussion, we get the following result:
Theorem 5.2. For a given optimal control (s∗,u∗) with the corresponding state variables (I∗(t),M∗(t),C∗(t)), there exist co-states or adjoint variables θ1, θ2, and θ3 satisfying the following system:
dθ1dt=θ1[μ+d1C−pf(I+f)2]+θ2aMM+g,dθ2dt=θ2[2rbM+agI(g+M)2+d2C−r]−θ1q−ξ1,dθ3dt=θ1d1I+θ2d2M+θ3γ, | (5.17) |
with transversality conditions
θi(tf)=0,i=1,2,3. | (5.18) |
Moreover,
s∗=min{max{50,−θ1(t)ξ2},100},u∗=min{max{0,−θ3(t)ξ3},1}. | (5.19) |
In the next section, we have solved our uncontrolled system (2.1) by setting s(t)=s and u(t)=u0, and controlled system (5.3) alongwith adjoint system (5.17) both numerically and graphically.
The following simulations have been done using the parameters of Table 1. For checking local behaviour of the system (2.1), we set the external immunotherapy s(t) as the key parameter and u(t)=u0. The time series diagrams of effector cells, tumor cells, and without control of drug administration for different values of s(t) but with the same cancer clearance term a have been presented in Figures 2–4. In Figure 2, it is seen that while the cancer clearance term is a=5 (1/time) during gene therapy with external immunotherapy s(t)=1 (cells/time), both effector and tumor cells go in tandem in the presence of chemotherapy. In this situation, there are two biologically feasible solutions E1(37.48,0,1.65) and E∗(965.34,556.72,1.65) (assuming u0=0.01650) having unstable behavior. In our second observation in Figure 3 with a=5 (1/time) and immunotherapy s(t)=25 (cells/time), the system has two feasible equilibrium points E2(837.483,0,1.65) and E∗(960.709,73.935,1.65) (assuming u0=0.01650) which are again found to be unstable. In Figure 4, we have observed that with external immunity strength s(t)=53 (cells/time), the cancer clearance term of gene therapy a=5 (1/time), and in the presence of chemo-drug, the tumor cell goes to zero rather than oscillating about zero in time around t=120 and the effector cells converge to a stable position. This scenario implies that there are only one biologically valid equilibrium E2(1770.82,0,1.65) (assuming u0=0.01650), which is locally stable in nature.
Parameter | Definition | Value | Range | Source |
q | Cancer antigenicity | 0.05 (1/time) | [10−3,0.5] | [34] |
s(t) | Immunotherapy term | [10−2,102] (cells/time) | [10−2,102] | [34] |
p | Proliferation rate of I | 0.1245 (1/time) | 0.1245 | [34] |
f | Half saturation for I proliferation term | 10−3 (cells) | [10−5,1] | [34] |
μ | Half life of effector cells I | 0.03 (1/time) | 0.03 | [34] |
r | Cancer growth rate | 0.18 (1/time) | [10−1,2] | [34] |
b | Cancer cell capacity | 10−9 (1/cells) | 10−9 | [34] |
a | Cancer clearance term | 5 (1/time) | [10−2,102] | [34] |
g | Half saturation for cancer clearance | 105 (cells) | 105 | [34] |
d1 | Response Coefficients of Chemotherapy drugs to I | 2×10−11/day | 2×10−11/day | [8] |
d2 | Response Coefficients of Chemotherapy drugs to M | 0.08/day | 0.08/day | [8] |
γ | Decay rate of Chemotherapy drug | 0.01/day | 0.01/day | [8] |
The optimal system (5.3) associated with the adjoint system (5.17) and the separated boundary conditions at time t=0 and t=tf are solved. Forward method is used to solve the original optimal system (5.3) and the backward method for the respective adjoint system (5.17) with tf=200. Here, we consider the treatment parameter a=5 and the drug administration s(t) and u(t) which will be controlled. As the variables associated with the optimal system (5.3) and in the objective functional (5.1) have different scales, hence, to balance the objective functional, we have chosen the weight constants ξ1=5, ξ2=10, and ξ3=10 in (5.1). In Figure 5(a), (b), we have presented the time series plots of effector cells and tumor cells with drug control. We have seen that the tumor cells vanish around time 15<tf<20. From Figure 6(a), it can be observed that the optimal drug dose for immunotherapy is s(t)=53 (cells/time) for which immune cell population becomes stable at a sufficient level and tumor cell vanishes. Figure 6(b) shows that the chemo-drug concentration reduces gradually depending upon the size of the tumor and hence it also goes to zero as the tumor vanishes from the body.
We have developed an ODE mathematical model for tumor growth under the action of effector immune cells in the presence of gene therapy, immunotherapy and chemotherapy. We established the basic characteristics of the dependent variables of the model. We presented the stability analysis of the system, revealing the conditions that must hold well for the cure equilibrium to be attained. For the numerical solution, we set up s(t) as the key parameter. We investigated the dynamics of the model for the values (i) s(t)=1 (cells/time), (ii) s(t)=25 (cells/time), and (iii) s(t)=53 (cells/time), respectively. From the numerical simulation, it can be concluded that for the value of immunotherapy term s(t)=53 (cells/time), in the presence of gene and chemotherapy, tumor cells may eradicate from the body. In [34], the authors found the values of treatment term for the two cases:
Case (i): s(t)=100 and a(t)=2 for tumor clearence at a slower rate (where global stability conditions of the tumor-free state are not satisified).
Case (ii): s(t)=764.5072 and a(t)=38.0040 for tumor clearence at a faster rate (where global stability conditions of the tumor-free state are satisified).
However, our results reveal that when chemotherapy is applied, the patient requires less amount of external source of immunotherapy to fight against cancer. This conclusion can be drawn by comparing our results with those of [34].
We also have constructed an optimal control problem associated with the system to minimize the tumor cell population, immunotherapy and the chemotherapeutic drug within a finite time interval [0,200]. According to our results, the tumor cells can be eliminated from the body in a shorter period in the presence of chemo-immuno-gene therapy with the control of immuno-chemotherapy drug parameter s(t) and u(t). From optimal control problem, it can be also verified that the optimum amount of immunotherapy for which tumor is eradicated is 53 (cells/time). Our model is probably one of the very few models in which gene therapy is combined with chemo-immunotherapy for finding optimal cancer treatment. Also, our discussion and results are on the basis of a modified mathematical model and hence it is a theoretical one. The results of the work can be a guiding factor for clinicians and the usefulness of our theoretical prediction will depend on the practical results found by the experiment of the clinicians.
Numerical results of our paper are dervied using the inbuilt functions of MATLAB as we are more interested in discussing the qualitative dynamical behaviours of the considered model rather than the precision, rate of convergence etc. of the derived numerical solutions. Researchers who are interested in those issues are reffered to [48,49,50]. Qureshi and Yusuf [48] proposed a third order convergence numerical solver for continuous dynamical systems. The authors performed the error analysis of the proposed solver and found to contain the smallest errors when it is compared with two well-known solvers (Heun and RK3HM) having the same order of convergence. Odibat and Baleanu [49] derived a generalized Caputo-type fractional derivative. In addition to generalised Caputo-type fractional derivatives, they successfully implemented the adaptive P-C algorithm for finding numerical solution of some fractional order dynamical systems. In the work [50], the authors applied Mohand integral transform for finding the exact solutions of fractional-order ordinary differential equations under the Caputo type operator. Upon comparison, the obtained results were in agreement with results produced by other existing well-known integral transforms. Our future work is to see the more realistic scenarios using the fractional derivative to the model and investigate the related control problem. Interested reader may also see the references [1,2] for finding various treatment combinations along with optimal immunotherapy.
The authors declare that they have no competing interests.
[1] |
Eltahir HA, Xu W, Lu X, et al. (2020) Prospect and potential of adansonia digitata L.(baobab) bast fiber in composite materials reinforced with natural fibers. Part 1: fiber characterization. J Nat Fibers 18: 2197-2207. https://doi.org/10.1080/15440478.2020.172423. doi: 10.1080/15440478.2020.172423
![]() |
[2] |
Gurukarthik BB, Prince WD, SenthamaraiKannan P, et al. (2019) Study on characterization and physicochemical properties of new natural fiber from Phaseolus vulgaris. J Nat Fibers 16: 1035-1042. https://doi.org/10.1080/15440478.2018.144831. doi: 10.1080/15440478.2018.144831
![]() |
[3] |
Asim M, Jawaid M, Abdan K, et al. (2016) Effect of alkali and silane treatments on mechanical and fibre-matrix bond strength of kenaf and pineapple leaf fibres. J Bionic Eng 13: 426-435. https://doi.org/10.1016/S1672-6529(16)60315-3 doi: 10.1016/S1672-6529(16)60315-3
![]() |
[4] |
Baskaran PG, Kathiresan M, Senthamaraikannan P, et al. (2018) Characterization of new natural cellulosic fiber from the bark of Dichrostachys Cinerea. J Nat Fibers 15: 62-68. https://doi.org/10.1080/15440478.2017.1304314 doi: 10.1080/15440478.2017.1304314
![]() |
[5] |
Sanjay MR, Arpitha GR, Naik LL, et al. (2016) Applications of natural fibers and its composites: An overview. Nat Resour 7: 108-114. http://dx.doi.org/10.4236/nr.2016.73011 doi: 10.4236/nr.2016.73011
![]() |
[6] |
Habert G, Roussel N (2009) Study of two concrete mix-design strategies to reach carbon mitigation objectives. Cement Concrete Comp 31: 397-402. https://doi.org/10.1016/j.cemconcomp.2009.04.001 doi: 10.1016/j.cemconcomp.2009.04.001
![]() |
[7] |
Hasan KMF, Horváth PG, Alpár T (2021) Lignocellulosic fiber cement compatibility: A state of the art review. J Nat Fibers 18: 1-26. https://doi.org/10.1080/15440478.2021.1875380 doi: 10.1080/15440478.2021.1875380
![]() |
[8] |
Pividal P, Rocha AM (2020) Thermal behavior of bi-layered needle-punched nonwovens produced from 100% raw kapok fibers. J Text Inst 112: 928-935. https://doi.org/10.1080/00405000.2020.1786209 doi: 10.1080/00405000.2020.1786209
![]() |
[9] |
Oduor EO, Ciera L, Adolkar V, et al. (2021) Physical characterization of eri silk fibers produced in Kenya. J Nat Fibers 18: 59-70. https://doi.org/10.1080/15440478.2019.1612306 doi: 10.1080/15440478.2019.1612306
![]() |
[10] |
Madhu P, Sanjay MR, Senthamaraikannan P, et al. (2019) A review on synthesis and characterization of commercially available natural fibers: Part II. J Nat Fibers 16: 25-36. https://doi.org/10.1080/15440478.2017.1379045 doi: 10.1080/15440478.2017.1379045
![]() |
[11] |
Fiore V, Di Bella G, Valenza A (2019) Effect of sheep wool fibers on thermal insulation and mechanical properties of cement-based composites. J Nat Fibers 17: 1532-1543. https://doi.org/10.1080/15440478.2019.1584075 doi: 10.1080/15440478.2019.1584075
![]() |
[12] |
Alothman OY, Kian LK, Saba N, et al. (2021) Cellulose nanocrystal extracted from date palm fibre: Morphological, structural and thermal properties. Ind Crops Prod 159: 113075. https://doi.org/10.1016/j.indcrop.2020.113075 doi: 10.1016/j.indcrop.2020.113075
![]() |
[13] |
Jawaid M, Kian LK, Fouad H, et al. (2021) Morphological, structural, and thermal analysis of three part of Conocarpus cellulosic fibres. J Mater Res Technol 10: 24-33. https://doi.org/10.1016/j.jmrt.2020.11.108 doi: 10.1016/j.jmrt.2020.11.108
![]() |
[14] |
Asim M, Abdan K, Jawaid M, et al. (2015) A review on pineapple leaves fibre and its composites. Int J Polym Sci 2015:1-16. http://dx.doi.org/10.1155/2015/950567 doi: 10.1155/2015/950567
![]() |
[15] |
Hamdaoui O, Limam O, Ibos L, et al. (2021) Thermal and mechanical properties of hardened cement paste reinforced with Posidonia-Oceanica natural fibers. Constr Build Mater 269: 121339. https://doi.org/10.1016/j.conbuildmat.2020.121339 doi: 10.1016/j.conbuildmat.2020.121339
![]() |
[16] |
Nadlene R, Sapuan SM, Jawaid M, et al. (2016) A review on roselle fiber and its composites. J Nat Fibers 13: 10-41. https://doi.org/10.1080/15440478.2014.984052 doi: 10.1080/15440478.2014.984052
![]() |
[17] |
Loganathan TM, Sultan MTH, Ahsan Q, et al. (2021) Comparative study of mechanical properties of chemically treated and untreated cyrtostachys renda fibers. J Nat Fibers 19: 1-16. https://doi.org/10.1080/15440478.2021.1902900 doi: 10.1080/15440478.2021.1902900
![]() |
[18] | Petroudy SRD (2017) Physical and mechanical properties of natural fiber, In: Fan Mizi, Feng Fu, Advanced High Strength Natural Fibre Composites in Construction, London: Woodhead Publishing, 59-83. https://doi.org/10.1016/B978-0-08-100411-1.00003-0 |
[19] |
Kumar R, Hynes NRJ, Senthamaraikannan P, et al. (2018) Physicochemical and thermal properties of ceiba pentandra bark fiber. J Nat Fibers 15: 822-829. https://doi.org/10.1080/15440478.2017.1369208 doi: 10.1080/15440478.2017.1369208
![]() |
[20] |
Subramanian K, Kumar PS, Jeyapal P, et al. (2005) Characterization of ligno-cellulosic seed fibre from Wrightia Tinctoria plant for textile applications-an exploratory investigation. Eur Polym J 41: 853-861. https://doi.org/10.1016/j.eurpolymj.2004.10.037 doi: 10.1016/j.eurpolymj.2004.10.037
![]() |
[21] |
Mothilal B, Prakash C, Ramakrishnan G (2019) Design and development of non-woven medical product from Wrightia tinctoria fiber. J Nat Fibers 16: 576-588. https://doi.org/10.1080/15440478.2018.1430649 doi: 10.1080/15440478.2018.1430649
![]() |
[22] | Grace Annapoorani S, Divya S (2017) Investigating the characterization of fiber extracted from Wrightia tinctoria (Roxb.) R. BR. Int J Appl Res 3: 731-736. |
[23] | Bureau of Indian Standards (1980) Methods of test for soils, Part 3: Determination of specific gravity, New Delhi: India Government. IS 2720-3-1 |
[24] | Bureau of Indian Standards (1973) Methods of test for soils-Part 2: Determination of water content, New Delhi: India Government. IS 2720-2 |
[25] | Segal L, Creely JJ, Martin Jr AE, et al. (1959) An empirical method for estimating the degree of crystallinity of native cellulose using the X-ray diffractometer. Text Res J 29: 786-794. https://doi.org/10.1177%2F004051755902901003 |
[26] |
Manimaran P, Senthamaraikannan P, Murugananthan K, et al.(2018) Physicochemical properties of new cellulosic fibers from Azadirachta indica plant. J Nat Fibers 15: 29-38. https://doi.org/10.1080/15440478.2017.1302388 doi: 10.1080/15440478.2017.1302388
![]() |
[27] |
Purnawati R, Febrianto F, Wistara I, et al. (2018) Physical and chemical properties of kapok (Ceiba Pentandra) and balsa (Ochroma Pyramidale) fibers. J Korean Wood Sci Technol 46: 393-401. https://doi.org/10.5658/WOOD.2018.46.4.393 doi: 10.5658/WOOD.2018.46.4.393
![]() |
[28] |
Sathishkumar TP, Navaneethakrishnan P, Shankar S, et al. (2013) Characterization of new cellulose sansevieria ehrenbergii fibers for polymer composites. Compos Interfac 20: 575-593. https://doi.org/10.1080/15685543.2013.816652 doi: 10.1080/15685543.2013.816652
![]() |
[29] |
Saravanakumar SS, Kumaravel A, Nagarajan T, et al. (2013) Characterization of a novel natural cellulosic fiber from Prosopis juliflora bark. Carbohydr Polym 92: 1928-1933. https://doi.org/10.1016/j.carbpol.2012.11.064 doi: 10.1016/j.carbpol.2012.11.064
![]() |
[30] |
Rashid B, Leman Z, Jawaid M, et al. (2016) Physicochemical and thermal properties of lignocellulosic fiber from sugar palm fibers: Effect of treatment. Cellulose 23: 2905-2916. https://doi.org/10.1007/s10570-016-1005-z doi: 10.1007/s10570-016-1005-z
![]() |
[31] |
Prithiviraj M, Muralikannan R, Senthamaraikannan P, et al. (2016) Characterization of new natural cellulosic fiber from the Perotis indica plant. Int J Polym Anal Ch 21: 669-674. https://doi.org/10.1080/1023666X.2016.1202466 doi: 10.1080/1023666X.2016.1202466
![]() |
[32] | Jawaid M, Kian LK, Fouad H, et al. (2021) New cellulosic fibers from Washingtonia tree agro-wastes: Structural, morphological, and thermal properties. 2021: 1-11. https://doi.org/10.1080/15440478.2021.1875374 |
1. | Xiang Wu, Yuzhou Hou, Kanjian Zhang, Optimal feedback control for a class of fed-batch fermentation processes using switched dynamical system approach, 2022, 7, 2473-6988, 9206, 10.3934/math.2022510 | |
2. | Fazal Subhan, Muhammad Adnan Aziz, Jawad Ali Shah, Kushsairy Abdul Kadir, Ijaz Mansoor Qureshi, Tumor Treatment Protocol by Using Genetic Algorithm Based Bernstein Polynomials and Sliding Mode Controller, 2021, 9, 2169-3536, 152503, 10.1109/ACCESS.2021.3126491 | |
3. | Fazal Subhan, Muhammad Adnan Aziz, Inam Ullah Khan, Muhammad Fayaz, Marcin Wozniak, Jana Shafi, Muhammad Fazal Ijaz, Cancerous Tumor Controlled Treatment Using Search Heuristic (GA)-Based Sliding Mode and Synergetic Controller, 2022, 14, 2072-6694, 4191, 10.3390/cancers14174191 | |
4. | H. J. Alsakaji, F. A. Rihan, K. Udhayakumar, F. El Ktaibi, Stochastic tumor-immune interaction model with external treatments and time delays: An optimal control problem, 2023, 20, 1551-0018, 19270, 10.3934/mbe.2023852 | |
5. | M. M. Abou Hasan, S. M. AL-Mekhlafi, K. Udhayakumar, F. A. Rihan, Hybrid fractional-order optimal control problem for immuno-chemotherapy with gene therapy and time-delay: numerical treatments, 2023, 0228-6203, 1, 10.1080/02286203.2023.2216621 | |
6. | Rui Zhou, Ping Zhou, Yi-Feng Yu, Qin Lin, San-Gang Wu, A Pilot Study of Anlotinib as a Combination Treatment in Advanced Nasopharyngeal Carcinoma, 2024, 24, 15680096, 319, 10.2174/1568009623666230810121918 | |
7. | G. Rigatos, Nonlinear optimal control for the multi-variable tumor-growth dynamics, 2024, 1025-5842, 1, 10.1080/10255842.2023.2297660 | |
8. | Kaushik Dehingia, Yamen Alharbi, Vikas Pandey, A mathematical tumor growth model for exploring saturated response of M2 macrophages, 2024, 5, 27724425, 100306, 10.1016/j.health.2024.100306 | |
9. | Ye Zhang, Hai-jiao Yan, Jun Wu, The Tumor Immune Microenvironment plays a Key Role in Driving the Progression of Cholangiocarcinoma, 2024, 24, 15680096, 681, 10.2174/0115680096267791231115101107 | |
10. | A. M. D. Clotilda, G. V. R. K. Vithanage, D. D. Lakshika, A Mathematical Model to Treat for a Cancer Using Chemotherapy and Immunotherapy under Mass Action Kinetics for Immunotherapy, 2024, 4, 2732-9992, 150, 10.37394/232023.2024.4.15 | |
11. | Muner. M. Abou Hasan, Seham. M. AL‐Mekhlafi, Fathala. A. Rihan, Hannah. A. Al‐Ali, Modeling Hybrid Crossover Dynamics of Immuno‐Chemotherapy and Gene Therapy: A Numerical Approach, 2025, 0170-4214, 10.1002/mma.10765 | |
12. | Kaushik Dehingia, Sana Abdulkream Alharbi, Awatif Jahman Alqarni, Mounirah Areshi, Mona Alsulami, Reima Daher Alsemiry, Reem Allogmany, Homan Emadifar, Mati ur Rahman, Kavikumar Jacob, Exploring the combined effect of optimally controlled chemo-stem cell therapy on a fractional-order cancer model, 2025, 20, 1932-6203, e0311822, 10.1371/journal.pone.0311822 | |
13. | Muhammad Zubair, Daniela Iacoviello, Sheraz Ahmad Babar, Barrier Function and Terminal Synergetic-Based Controllers for the Chemotherapy of Brain Tumor, 2025, 13, 2169-3536, 36201, 10.1109/ACCESS.2025.3544757 |
Parameter | Definition | Value | Range | Source |
q | Cancer antigenicity | 0.05 (1/time) | [10−3,0.5] | [34] |
s(t) | Immunotherapy term | [10−2,102] (cells/time) | [10−2,102] | [34] |
p | Proliferation rate of I | 0.1245 (1/time) | 0.1245 | [34] |
f | Half saturation for I proliferation term | 10−3 (cells) | [10−5,1] | [34] |
μ | Half life of effector cells I | 0.03 (1/time) | 0.03 | [34] |
r | Cancer growth rate | 0.18 (1/time) | [10−1,2] | [34] |
b | Cancer cell capacity | 10−9 (1/cells) | 10−9 | [34] |
a | Cancer clearance term | 5 (1/time) | [10−2,102] | [34] |
g | Half saturation for cancer clearance | 105 (cells) | 105 | [34] |
d1 | Response Coefficients of Chemotherapy drugs to I | 2×10−11/day | 2×10−11/day | [8] |
d2 | Response Coefficients of Chemotherapy drugs to M | 0.08/day | 0.08/day | [8] |
γ | Decay rate of Chemotherapy drug | 0.01/day | 0.01/day | [8] |
Parameter | Definition | Value | Range | Source |
q | Cancer antigenicity | 0.05 (1/time) | [10−3,0.5] | [34] |
s(t) | Immunotherapy term | [10−2,102] (cells/time) | [10−2,102] | [34] |
p | Proliferation rate of I | 0.1245 (1/time) | 0.1245 | [34] |
f | Half saturation for I proliferation term | 10−3 (cells) | [10−5,1] | [34] |
μ | Half life of effector cells I | 0.03 (1/time) | 0.03 | [34] |
r | Cancer growth rate | 0.18 (1/time) | [10−1,2] | [34] |
b | Cancer cell capacity | 10−9 (1/cells) | 10−9 | [34] |
a | Cancer clearance term | 5 (1/time) | [10−2,102] | [34] |
g | Half saturation for cancer clearance | 105 (cells) | 105 | [34] |
d1 | Response Coefficients of Chemotherapy drugs to I | 2×10−11/day | 2×10−11/day | [8] |
d2 | Response Coefficients of Chemotherapy drugs to M | 0.08/day | 0.08/day | [8] |
γ | Decay rate of Chemotherapy drug | 0.01/day | 0.01/day | [8] |