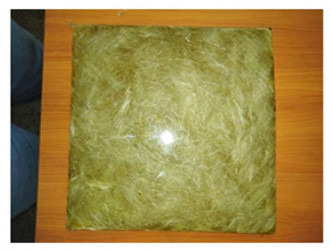
Machining natural fiber reinforced polymer composite materials is one of most challenging tasks due to the material's anisotropic property, non-homogeneous structure and abrasive nature of fibers. Commonly, conventional machining of composites leads to delamination, inter-laminar cracks, fiber pull out, poor surface finish and wear of cutting tool. However, these challenges can be significantly reduced by using proper machining conditions. Thus, this research aims at optimizing machining parameters in drilling hybrid sisal-cotton fibers reinforced polyester composite for better machining performance characteristics namely better hole roundness accuracy and surface finish using Taguchi method. The effect of machining parameters including spindle speed, feed rate and drill diameter on drill hole accuracy (roundness error) and surface-roughness of the hybrid composite are evaluated. Series of experiments based on Taguchi's L16 orthogonal array were performed using different ranges of machining parameters namely spindle speed (600,900, 1200, 1600 rpm), feed rate (10, 15, 20, 25 mm/min) and drill diameter (6, 7, 8, 10 mm). Hole roundness error and surface-roughness are determined using ABC digital caliper and Zeta 20 profilometer, respectively. Optimum machining condition for drilling hybrid composite material (speed: 1600 rpm, feed rate: 25 mm/min and drill diameter: 6 mm) is determined, and the results are verified by conducting confirmation test which proves that the results are reliable.
Citation: Nurhusien Hassen Mohammed, Desalegn Wogaso Wolla. Optimization of machining parameters in drilling hybrid sisal-cotton fiber reinforced polyester composites[J]. AIMS Materials Science, 2022, 9(1): 119-134. doi: 10.3934/matersci.2022008
[1] | Ravinder Kataria, Jatinder Kumar, B. S. Pabla . Experimental investigation of surface quality in ultrasonic machining of WC-Co composites through Taguchi method. AIMS Materials Science, 2016, 3(3): 1222-1235. doi: 10.3934/matersci.2016.3.1222 |
[2] | Madjid Haddad, Redouane Zitoune, Florent Eym, Bruno Castanié . The effect of rectification of composite materials on the mechanical behavior of long fiber composite materials. AIMS Materials Science, 2016, 3(2): 645-657. doi: 10.3934/matersci.2016.2.645 |
[3] | Araya Abera Betelie, Yonas Tsegaye Megera, Daniel Telahun Redda, Antony Sinclair . Experimental investigation of fracture toughness for treated sisal epoxy composite. AIMS Materials Science, 2018, 5(1): 93-104. doi: 10.3934/matersci.2018.1.93 |
[4] | Rasaq Kazeem, Tien-Chien Jen, Godwin Akande, Stephen Akinlabi, Esther Akinlabi . Performance evaluation of hybrid biodegradable oils as a lubricant during cylindrical turning of AISI 304 austenitic stainless steel. AIMS Materials Science, 2024, 11(2): 256-294. doi: 10.3934/matersci.2024015 |
[5] | Kator Jeff Jomboh, Adele Dzikwi Garkida, Emmanuel Majiyebo Alemaka, Mohammed Kabir Yakubu, Vershima Cephas Alkali, Wilson Uzochukwu Eze, Nuhu Lawal . Properties and applications of natural, synthetic and hybrid fiber reinforced polymer composite: A review. AIMS Materials Science, 2024, 11(4): 774-801. doi: 10.3934/matersci.2024038 |
[6] | Vo Thi Nhu Uyen, Nguyen Hong Son . Improving accuracy of surface roughness model while turning 9XC steel using a Titanium Nitride-coated cutting tool with Johnson and Box-Cox transformation. AIMS Materials Science, 2021, 8(1): 1-17. doi: 10.3934/matersci.2021001 |
[7] | Prashant Tripathi, Vivek Kumar Gupta, Anurag Dixit, Raghvendra Kumar Mishra, Satpal Sharma . Development and characterization of low cost jute, bagasse and glass fiber reinforced advanced hybrid epoxy composites. AIMS Materials Science, 2018, 5(2): 320-337. doi: 10.3934/matersci.2018.2.320 |
[8] | Nhu-Tung Nguyen, Do Duc Trung . A study on the surface grinding process of the SUJ2 steel using CBN slotted grinding wheel. AIMS Materials Science, 2020, 7(6): 871-886. doi: 10.3934/matersci.2020.6.871 |
[9] | Iketut Suarsana, Igpagus Suryawan, NPG Suardana, Suprapta Winaya, Rudy Soenoko, Budiarsa Suyasa, Wijaya Sunu, Made Rasta . Flexural strength of hybrid composite resin epoxy reinforced stinging nettle fiber with silane chemical treatment. AIMS Materials Science, 2021, 8(2): 185-199. doi: 10.3934/matersci.2021013 |
[10] | Ayumu Yasue, Keita Hayashi, Shogo Yamamoto, Toshitsugu Inukai, Shigeru Fujimori . Influence of concrete bleeding due to mix proportion on the drilling speed of hardened surface layer. AIMS Materials Science, 2021, 8(3): 486-500. doi: 10.3934/matersci.2021030 |
Machining natural fiber reinforced polymer composite materials is one of most challenging tasks due to the material's anisotropic property, non-homogeneous structure and abrasive nature of fibers. Commonly, conventional machining of composites leads to delamination, inter-laminar cracks, fiber pull out, poor surface finish and wear of cutting tool. However, these challenges can be significantly reduced by using proper machining conditions. Thus, this research aims at optimizing machining parameters in drilling hybrid sisal-cotton fibers reinforced polyester composite for better machining performance characteristics namely better hole roundness accuracy and surface finish using Taguchi method. The effect of machining parameters including spindle speed, feed rate and drill diameter on drill hole accuracy (roundness error) and surface-roughness of the hybrid composite are evaluated. Series of experiments based on Taguchi's L16 orthogonal array were performed using different ranges of machining parameters namely spindle speed (600,900, 1200, 1600 rpm), feed rate (10, 15, 20, 25 mm/min) and drill diameter (6, 7, 8, 10 mm). Hole roundness error and surface-roughness are determined using ABC digital caliper and Zeta 20 profilometer, respectively. Optimum machining condition for drilling hybrid composite material (speed: 1600 rpm, feed rate: 25 mm/min and drill diameter: 6 mm) is determined, and the results are verified by conducting confirmation test which proves that the results are reliable.
Composite materials have got very wide applications in replacing metals in various industrial sectors due to its better mechanical and structural functionalities [1]. Particularly, researchers [2,3] clearly showed in their work that fiber-reinforced polymers (FRPs) are the most commonly used composite material in aerospace structures due to their unique properties such as high performance, lightweight, higher stiffness and better corrosion resistance. In the recent times, their applications are now widely extended to marine industries [4]. Different products including boat hulls, sonar domes, marine buildings, the water front barriers, the offshore structures, propellers and hatch covers are made from these materials [5,6,7]. Among the composites, natural fiber reinforced polymer composites have better specific strength, light weight, non-corrosive, environmental friendly and low cost materials. Due to these attractive features, they have got imminent applications in automotive industries. Currently, these industries consume large amount of composite materials as they have proven potential to reduce weight (10%), save energy (80% efficiency) and reduce cost (5%) [8]. For example, hybrid sisal-cotton fiber reinforced polyester composites are widely used in making different automobile parts namely, the Mercedes Benz (C-Class) rear panel shelf is made of sisal-cotton fiber, and 95% recyclable vehicles (Daimler Chrysler or M-B Travego Coach) consist of several components made from sisal, flax, coir, hemp and cotton fiber reinforced composites [9]. Since natural fiber based composites have very low weld-ability, they can be joined with other materials using fastening techniques.
Drilling is the most common machining process performed on composite materials, and it's mainly used to create circular profiles for fitting, followed by fasteners [10,11]. It is commonly performed on composite laminates and considered as an essential operation to join composites with other materials [12]. Several challenges are observed in drilling fiber reinforced polymer composites materials including delamination, inter-laminar cracks and fiber pull out [13]. These challenges arise from their heterogeneous, anisotropic, highly abrasive and hard nature of fibers, which causes drilling induced damage issues such as delamination [14]. Such inconveniences are capable of affecting the operating performance of components fabricated from these materials and thereby reduce consistency. In addition, the quality of machined surface is usually poor due to abrasive nature of the fibers.
In tribology, rough surfaces generally wear at faster rate, and have higher coefficient of friction than smooth surfaces. Therefore, roughness can be considered as a good indicator for mechanical component's performance as irregularities in the surface can form nucleation sites for cracks or corrosion. In drilled holes, roughness is very important quality characteristic because crack propagation, creep, wear, fatigue and corrosion mechanisms are mainly depend on the level of the surface irregularities. Dinesh et al. [15] performed comparative research on three natural fibers reinforced composite materials namely sisal/cotton, cotton/coconut sheath and sisal/coconut sheath reinforced with polyester which were fabricated and examined for their mechanical properties: tensile strength, flexural strength and impact strength. They revealed that sisal/cotton polyester composite possess good performance characteristics as compared to the others. Kurt et al. [16] employed Taguchi method to optimize machining parameters for better surface roughness and hole diameter accuracy during dry drilling of composite material. They considered three cutting parameters namely insertion radius, feed rate and cutting depth in the analysis and they determined optimum set up for reduced surface roughness and better hole diameter accuracy. Davim and Reis [17] proposed effective methodology using the Taguchi method and ANOVA to evaluate the relation between cutting speed and feed rate with delamination in a composite laminate. Korkut et al. [18] also used Taguchi method to experimentally assess circularity deviation in the bored hole of composite materials. Similarly, a research work on evaluation of thrust force and surface roughness using Taguchi analysis and neural network in drilling composite material was presented by Tsao and Hocheng [19]. They showed that feed rate and the drill diameter are considered to be the most influential factors affecting the thrust force, while the feed rate and spindle speed are seen to make the greatest contribution to the surface roughness. Sahoo et al. [20] revealed that surface roughness of machined parts affects mechanical properties of the components such as fatigue behavior, corrosion resistance, creep life, etc. Other functional qualities of components such as friction, wear, light reflection, heat transfer, lubrication and electrical conductivity are also appreciably affected by surface conditions of machined parts. About the drilling of jute fiber reinforced polymer composites research, Hadi et al. [21] evaluating the effect of machining conditions on thrust force, delamination size, and surface roughness of jute fiber reinforced polymer composites using full factorial experimental design technique. And they suggested that the type of drill bit has a significant effect on both delamination factor and surface roughness in drilling FRP composites. High speed steel (HSS) twist drill results in a smaller delamination scale than that of Coro-Drill 854 and Coro-Drill 856.
Taguchi method was developed by Taguchi and Konishi [22] as a statistical tool, and it was initially designed to improve the quality of manufactured products, then its application was extended to many other engineering fields such as biotechnology [23]. Taguchi's efforts have been recognized by professional statisticians, especially in the creation of models for studying variations in a process. Progress in achieving the desired outcomes requires careful selection of process parameters and ascertaining them into factors of control and noise. The choice of control factors must be made in such a way that the influences of noise factors are nullified. In addition, to obtain the best result for the operation, Taguchi method requires identification of proper control factors and their levels. To perform a series of experiments, orthogonal arrays (OA) are designed to address the entire process parameters with small number of experiments [24]. In the current research, an attempt has been made to establish an approach in which Taguchi's method was adopted to optimize machining parameters for better drill hole accuracy and surface roughness. The challenges in drilling natural fiber reinforced composites were addressed and optimal machining parameters for drilling hybrid sisal-cotton fibers reinforced composites were determined. Meanwhile, mechanical properties of hybrid glass-sisal fiber reinforced composite are also evaluated.
The matrix material used to fabricate the composite specimens was polyester resin including catalyst (cobalt), accelerator (methyl ethyl ketone) and releasing agent (polyvinyl acetate) which was supplied by local paint and adhesive materials supplier. Hybrid sisal and cotton fibers were used to reinforce the composite material. The origin of sisal and cotton plants was from Dugda Woreda, Oromia Region, Ethiopia. Both fibers were extracted manually using decortication method from their plants. The fabricated composite has a composition of 30 wt% of fibers (with 15 wt% of sisal fiber and 15 wt% cotton fiber) and the remaining was polyester resin including the hardener. To remove the flesh and debris from the fiber surface, the extracted fibers were washed with distilled water and then sun dried for 72 h. In addition, chemical treatment of fibers using 10% NaOH solution was made with the purpose of improving surface adhesive characteristics by removing fatty impurities like lignin. Finally, treated fibers were washed again in distilled water, sun dried for 72 h and packed in the plastic bags to protect it from moisture contamination.
The sisal and cotton fibers were chopped into 30 mm length using scissors, and the weight of each fibers and matrix were determined using rule of mixture. Composite specimens were fabricated using hand lay-up technique followed by light compression load, and the image of composite during fabrication placed within the mold is shown in Figure 1.
Experimental plan was made using L16 OA of Taguchi method. Factors considered and their levels are given in Table 1. Three drilling parameters namely spindle speed, feed rate and drill diameter were considered and the response variables were hole roundness error and surface roughness. All specimens were drilled in a dry lubricating condition. The experimental values for each selected drilling parameters are depicted in Table 2 for all experimental runs.
Process parameters | Level 1 | Level 2 | Level 3 | Level 4 |
A: Spindle speed (rpm) | 600 | 900 | 1200 | 1600 |
B: Feed rate (mm/min) | 10 | 15 | 20 | 25 |
C: Drill diameter (mm) | 6 | 7 | 8 | 10 |
Experimental runs | Spindle speed (rpm) | Feed rate (mm/min) | Drill diameter (mm) |
1 | 600 | 10 | 6 |
2 | 600 | 15 | 7 |
3 | 600 | 20 | 8 |
4 | 600 | 25 | 10 |
5 | 900 | 10 | 7 |
6 | 900 | 15 | 6 |
7 | 900 | 20 | 10 |
8 | 900 | 25 | 8 |
9 | 1200 | 10 | 8 |
10 | 1200 | 15 | 10 |
11 | 1200 | 20 | 6 |
12 | 1200 | 25 | 7 |
13 | 1600 | 10 | 10 |
14 | 1600 | 15 | 8 |
15 | 1600 | 20 | 7 |
16 | 1600 | 25 | 6 |
Composite plates fabricated using hand lay-up technique have dimensions of 228 × 77 × 3 mm, and four HSS drill bits with helix angle of 30°, point angle of 135° and diameters as provided in Table 1 were utilized for creating holes. The selection of twist HSS drill bit was based on the fact that HSS drill is result in relatively smaller delamination scale than other tool materials [21]. In addition, HSS drill can capable to provide a lower trust force and better hole quality than carbide tools as revealed by Amirhossein et al. [25]. GSK computer numerical control (CNC) vertical milling machine was used to perform the drilling operation for the selected parameters, and the machine set up for drilling the composite is shown in Figure 2.
All drilling operations were carried out using part programs generated by Mastercam-X4 software. Drilled hole's geometry and its image after drilling operation are depicted in Figure 3a, b.
Hole accuracy described in terms of roundness error was measured, and for each hole circularity, the maximum and minimum diameters were determined by taking eight successive measurements in 22.5° variations. Precision ABS digital caliper with least count of 0.01 mm was used to measure the variance in diameter of all 16 individual holes of each composite specimen. From each measurement, the maximum and minimum values of diameter were used to compute roundness error using Eq 1 in a continuous manner, and then the roundness error values were utilized in Taguchi's L16 OA for further analysis. where Dmax is the maximum hole diameter and Dmin is the minimum hole diameter.
Roundnesserror=Dmax−Dmin2 | (1) |
Surface roughness of drilled hole on the composite specimens was measured using zeta 3D optical profilometer and the values are described using arithmetic mean roughness (Ra) as it is one of the most widely used surface roughness measures. All drilled composite specimens were cut into half section for ease of measurement and consistency, and measured surface roughness values were taken at 10× lens magnification for better precision. The setup adopted for surface roughness measurement using optical profilometer is shown in Figure 4. Surface roughness in Ra means that the value generated by using Eq 2 are described in micrometer (μm) when only the reference length of the roughness curve is taken in the location of the mean line, x-axis in the direction of the mean line and y-axis in the path of the longitudinal magnification of sample component. Ra parameter was determined using Eq 2 in which y = f(x) describes the roughness curve. Where lγ represents reference length of the roughness.
Ra=1lr∫lr0{f(x)}dx | (2) |
The effect of drilling parameters namely spindle speed, feed rate and drill diameter on hole accuracy (roundness error) and surface roughness were analyzed using statistical tool. The experimental results obtained for roundness error and surface roughness are depicted in Table 3.
Experimental runs | Spindle speed (rpm) |
Feed rate (mm/min) |
Drill diameter (mm) |
Roundness error (mm) |
Surface roughness (Ra) |
1 | 600 | 10 | 6 | 0.10 | 337.29 |
2 | 600 | 15 | 7 | 0.14 | 324.58 |
3 | 600 | 20 | 8 | 0.17 | 306.00 |
4 | 600 | 25 | 10 | 0.25 | 309.81 |
5 | 900 | 10 | 7 | 0.15 | 278.81 |
6 | 900 | 15 | 6 | 0.11 | 250.16 |
7 | 900 | 20 | 10 | 0.26 | 270.61 |
8 | 900 | 25 | 8 | 0.18 | 225.16 |
9 | 1200 | 10 | 8 | 0.19 | 230.40 |
10 | 1200 | 15 | 10 | 0.26 | 233.26 |
11 | 1200 | 20 | 6 | 0.11 | 162.48 |
12 | 1200 | 25 | 7 | 0.15 | 155.24 |
13 | 1600 | 10 | 10 | 0.28 | 175.22 |
14 | 1600 | 15 | 8 | 0.20 | 130.75 |
15 | 1600 | 20 | 7 | 0.16 | 98.40 |
16 | 1600 | 25 | 6 | 0.12 | 66.42 |
Based on the determined roundness errors, the linear polynomial model, Eq 3, was generated using commercially available MINITAB 19 software for different experimental conditions.
RE=−0.14180+0.000028S−0.000495F+0.38493D | (3) |
where, RE is roundness error in mm, S is spindle speed in rpm, F is feed rate in mm/min and D is drill diameter in mm. Experimental, predicted and mean error (%) values for hole accuracy were determined and summarized in Table 4, and pictorially represented in Figure 5.
Exp. runs | Experimental values (mm) | Predicted values (mm) | Mean error (%) |
1 | 0.10 | 0.101 | 1.00 |
2 | 0.14 | 0.137 | 2.14 |
3 | 0.17 | 0.174 | 2.35 |
4 | 0.25 | 0.247 | 1.20 |
5 | 0.15 | 0.147 | 2.00 |
6 | 0.11 | 0.107 | 3.10 |
7 | 0.26 | 0.258 | 0.60 |
8 | 0.18 | 0.179 | 0.61 |
9 | 0.19 | 0.195 | 2.53 |
10 | 0.26 | 0.269 | 3.58 |
11 | 0.11 | 0.113 | 2.72 |
12 | 0.15 | 0.149 | 0.73 |
13 | 0.28 | 0.283 | 1.07 |
14 | 0.20 | 0.204 | 1.75 |
15 | 0.16 | 0.163 | 1.63 |
16 | 0.12 | 0.122 | 1.66 |
In Taguchi approach, the term signal is the desirable value (mean) for the output characteristic and the term noise is the undesired value (standard deviation, SD). The signal to noise (S/N) ratio, therefore, is the ratio of desired value to undesired value. To evaluate the quality attribute that deviates from the target value, Taguchi used the S/N ratio. Depending on the type of characteristic, there are several S/N ratios available: smaller-is-better, nominal-is-best, and larger-is-better [26,27]. The S/N ratio for objective function of smaller-is-better is determined using Eq 4.
S/NL=−10log(1nn∑i=1y2i) | (4) |
where y is the observed data, and n is number of observations.
Using Eq 4, the results for S/N ratio for hole accuracy are given in Table 5, and it clearly indicates that drill diameter is the most significant factor influencing hole roundness error and ranked 1st.
Levels | Spindle speed (rpm) | Feed rate (mm/rev) | Drill diameter(mm) |
1 | 16.21 | 15.35 | 19.05 |
2 | 15.59 | 15.56 | 16.65 |
3 | 15.27 | 15.43 | 14.58 |
4 | 14.75 | 15.48 | 11.54 |
Delta | 1.46 | 0.21 | 7.51 |
Rank | 2 | 3 | 1 |
Figure 6 shows main effect plots of S/N ratio for hole roundness error from which optimum combination of drilling parameters are obtained as spindle speed of 600 rpm, feed rate of 15 mm/min and drill diameter of 6 mm.
Analysis of variance (ANOVA) determines the relative significance of factors in terms of their percentage contribution to the response [26,27]. For the estimation of variance of error for the effects and at confidence interval of 95%, ANOVA was determined and provided in Table 6. Drilling parameter's effect contribution (%) was found as 3.19%, 0.25% and 96.49% for spindle speed, feed rate and drill diameter, respectively.
Source | DF | Seq SS | Contribution | Adj SS | Adj MS | F-value | P-value |
Spindle speed | 3 | 0.001716 | 3.19% | 0.001716 | 0.000572 | 102.81 | 0.000 |
Feed rate | 3 | 0.000137 | 0.25% | 0.000137 | 0.000046 | 8.19 | 0.015 |
Drill diameter | 3 | 0.051877 | 96.49% | 0.051877 | 0.017292 | 3108.72 | 0.000 |
Error | 6 | 0.000033 | 0.06% | 0.000033 | 0.000006 | ||
Total | 15 | 0.053762 | 100.00% |
Based on the obtained surface roughness values for different experimental conditions, linear polynomial model, as given in Eq 5, was developed to relate it with the drilling parameters. Where, SR is hole surface roughness of drilled holes in Ra.
SR=−0.20213S−4.482F+10.779D+434.38 | (5) |
The experimental and predicted values of surface roughness are given in Table 7. In addition, the predicted values are compared with experimental values and depicted in Figure 7.
Exp. runs | Exp. results (Ra) | Predicted results (Ra) | Mean error (%) |
1 | 337.29 | 332.96 | 1.28 |
2 | 324.58 | 321.33 | 1.01 |
3 | 306.00 | 309.70 | 1.21 |
4 | 309.81 | 308.84 | 0.32 |
5 | 278.81 | 283.10 | 1.54 |
6 | 250.16 | 249.91 | 0.10 |
7 | 270.61 | 270.61 | 0.00 |
8 | 225.16 | 226.65 | 0.66 |
9 | 230.40 | 233.24 | 1.23 |
10 | 233.26 | 232.38 | 0.38 |
11 | 162.48 | 166.86 | 2.70 |
12 | 155.24 | 155.23 | 0.01 |
13 | 175.22 | 173.94 | 0.73 |
14 | 130.75 | 129.97 | 0.60 |
15 | 98.40 | 96.79 | 1.64 |
16 | 66.42 | 63.60 | 4.25 |
Using Eq 4, S/N ratio for surface roughness was determined and presented in Table 8. From the S/N ratio responses, it can be noted that spindle speed is the most significant factor influencing surface roughness and it is indicated with the 1st rank.
Level | Spindle speed (rpm) | Feed rate (mm/min) | Drill diameter (mm) |
1 | −50.09 | −47.90 | −44.79 |
2 | −48.14 | −46.95 | −45.69 |
3 | −45.66 | −45.61 | −46.58 |
4 | −40.85 | −44.28 | −47.68 |
Delta | 9.24 | 3.63 | 2.89 |
Rank | 1 | 2 | 3 |
Figure 8 shows the effect of drilling parameters on surface roughness and the optimum values based on their level of contribution. Based on the overall analysis and the main effect plots for S/N ratio, the optimum operating conditions for drilling holes on the composite material for reduced surface roughness are mainly 1600 rpm, 25 mm/min and 6 mm of spindle speed, feed rate and drill diameter, respectively.
A variance analysis determines the relative significance of the factors in terms of their percentage contribution to the response [26,27]. To obtain the percentage contribution for each of the drilling parameters, S/N ratio was determined at confidence interval of 95%.
From Table 9, it is observed that spindle speed has contribution of 86.33% and considered as most dominant factor affecting surface roughness whereas feed rate and drill diameter account for 9.7% and 3.94% contributions, respectively. Since the P-values are lower than 0.05 for all drilling parameters, the three parameters are significant and require close control.
Source | DF | Seq SS | Contribution | Adj SS | Adj MS | F-Value | P-Value |
Spindle Speed (rpm) | 3 | 89509 | 86.33% | 89508.5 | 29836.2 | 5698.72 | 0.000 |
Feed Rate (mm/min) | 3 | 10060 | 9.70% | 10059.5 | 3353.2 | 640.46 | 0.000 |
Drill diameter (mm) | 3 | 4083 | 3.94% | 4083.1 | 1361.0 | 259.96 | 0.000 |
Error | 6 | 31 | 0.03% | 31.4 | 5.2 | ||
Total | 15 | 103683 | 100.00% |
Verification of optimum machining parameters in reducing roundness error and surface roughness based on the analysis using Taguchi's method was conducted. In case of hole roundness error, the optimum values for better hole accuracy were 600 rpm, 15 mm/min and 6 mm in which drill diameter has most influence with the contribution of 96.49%. From this, we can deduce that spindle speed and feed rate effect to reduce roundness error are relatively less significant because these parameters are dominated by drill diameter. On the other hand, from the surface roughness analysis, the optimum values for reduced surface roughness were 1600 rpm, 25 mm/min and 6 mm in which spindle speed and feed rate accounts 86.33% and 9.7% contributions, respectively. This shows spindle speed and feed rate contribute 96% effect on the surface roughness and drill diameter has relatively smaller effect on the surface roughness according to the analysis. To reduce both roundness error and surface roughness based on the experimental analysis, the optimum machining parameters that have been selected and verified are 1600 rpm, 25 mm/min, and 6 mm. Roundness error measured for optimum drilling conditions were: 0.1, 0.11, 0.1 and 0.1 for four drilled holes which verifies the experimental result is reliable. Similarly, surface roughness values for the optimum conditions are obtained as Ra: 77.66, 51.88, 64.97 and 64.64 for the four drilled holes, respectively.
In general, the experimental verification was performed based on recommended optimum machining parameters which are 1600 rpm spindle speed, 25 mm/min feed rate and 6 mm drill diameter. The values of roundness error and surface roughness obtained are 0.1mm and 64.8 Ra respectively, which satisfies the objective of achieving reduced roundness error and surface roughness.
This paper presents optimization of machining parameters namely, spindle speed, feed rate and drill diameter for better machining performances (hole accuracy and surface roughness) in drilling hybrid sisal-cotton fiber reinforced polyester composite with 30 wt% of fibers in polyester resin. Taguchi's L16 OA and ANOVA were utilized for experimental design and analysis purpose. Based on the experimental results and analysis, the following conclusions are drawn.
(1) Using the L16 orthogonal array, statistically designed experiments are performed to examine the impact of drilling parameters on hole roundness error and surface roughness.
(2) Based on the ANOVA and S/N ratio, optimum machining condition for better hole accuracy was determined as 600 rpm, 15 mm/min and 6 mm of spindle speed, feed rate and drill diameter, respectively. Similarly, optimum drilling condition for reduced surface roughness was found as 1600 rpm, 25 mm/min and 6 mm of spindle speed, feed rate and drill diameter, respectively.
(3) Based on ANOVA, drill diameter (96.49% contribution) has greater influence on the hole roundness error compared to spindle speed (3.19% contribution) and feed rate (0.25% contribution), and spindle speed (86.33%) and feed rate (9.7%) have greater influence on the surface roughness compared to drill diameter (3.94%) of the drill bit.
(4) From observations, the optimum combination of the machining parameters and drill diameter for drilling hybrid sisal-cotton fiber reinforced polyester composite are determined as 1600 rpm of spindle speed, 25 mm/min of feed rate and 6 mm of drill diameter.
(5) Confirmation test was conducted to verify the experimental results and it showed that the experimental results are proven to be reliable.
(6) The results of current research can be directly applied for design and fabrication of natural fiber reinforced composite parts particularly in automotive industries including bumper covers, roof frames, door frames, door panels, engine valve covers, dashboards, and truck car mats [28,29].
(7) In our future research, the effect of drilling parameters on thrust force, tool life, assessment of appropriate lubricating conditions and other damages induced due to drilling on the composites will be extensively addressed.
The authors would like to thank Addis Ababa Institute of Technology for funding this research.
The authors decide to declare that we have no conflicts of interest in this work.
[1] | UD Din I, Hao P, Aamir M, et al. (2019) FEM implementation of the coupled elastoplastic/damage model: Failure prediction of fiber reinforced polymers FRPs composites. J Solid Mech 11: 842–853. |
[2] |
Aamir M, Tolouei-Rad M, Giasin K, et al. (2019) Recent advances in drilling of carbon fiber reinforced polymers for aerospace applications: A review. J Adv Manuf Technol 105: 2289–2308. https://doi.org/10.1007/s00170-019-04348-z doi: 10.1007/s00170-019-04348-z
![]() |
[3] | Davim PJ (2010) Machining Composites Materials, London: Wiley & Sons. https://doi.org/10.1002/9781118602713 |
[4] |
Hassan A, Khan R, Khan N, et al. (2021) Effect of seawater ageing on fracture toughness of stitched glass fiber/epoxy laminates for marine applications. J Mar Sci Eng 196: 1–9. https://doi.org/10.3390/jmse9020196 doi: 10.3390/jmse9020196
![]() |
[5] |
Guen-Geffroy L, Davies P, Le Gac PY, et al. (2020) Influence of seawater ageing on fracture of carbon fiber reinforced epoxy composites for ocean engineering. Oceans 1: 198–214. https://doi.org/10.3390/oceans1040015 doi: 10.3390/oceans1040015
![]() |
[6] |
Boscato G, Mottram JT, Russo S (2011) Dynamic response of a sheet pile of fiber-reinforced polymer for waterfront barriers. J Compos Constr 15: 974–984. https://doi.org/10.1061/(ASCE)CC.1943-5614.0000231 doi: 10.1061/(ASCE)CC.1943-5614.0000231
![]() |
[7] |
Rubino F, Nisticò A, Tucci F, et al. (2020) Marine application of fiber reinforced composites: A review. J Mar Sci Eng 8: 1–26. https://doi.org/10.3390/jmse8010026 doi: 10.3390/jmse8010026
![]() |
[8] |
Srinivasakumar P, Nandan MJ, Kiran CU, et al. (2013) Sisal and its potential for creating innovative employment opportunities and economic prospects. IOSR J Mech Civ Eng 8: 1–8. https://doi.org/10.9790/1684-0860108 doi: 10.9790/1684-0860108
![]() |
[9] | Kalia S, Kaith BS, Kaur I (2011). Cellulose Fibers: Bio-and Nano-Polymer Composites: Green Chemistry and Technology, Berlin: Springer. https://doi.org/10.1007/978-3-642-17370-7 |
[10] | Hufenbach W, Dobrzański LA, Gude M, et al. (2007) Optimization of the rivet joints of the CFRP composite material and aluminium alloy. J Achiev Mater Manuf Eng 20: 119–122. |
[11] |
Teti R (2002) Machining of composite materials. Cirp Ann Manuf Techn 51: 611–634. https://doi.org/10.1016/S0007-8506(07)61703-X doi: 10.1016/S0007-8506(07)61703-X
![]() |
[12] |
Mirsha R, Malik J, Singh I, et al. (2010) Neural network approach for estimate the residual tensile strength after drilling in unidirectional glass fiber reinforced plastic laminates. Mater Design 31: 2790–2795. https://doi.org/10.1016/j.matdes.2010.01.011 doi: 10.1016/j.matdes.2010.01.011
![]() |
[13] |
Abrão AM, Faria PE, Campos Rubio JC, et al. (2007) Drilling of fiber reinforced plastics: A review. J Mater Process Tech 186: 1–7. https://doi.org/10.1016/j.jmatprotec.2006.11.146 doi: 10.1016/j.jmatprotec.2006.11.146
![]() |
[14] |
Liu D, Tang Y, Cong W (2012) A review of mechanical drilling for composite laminates. Compos Struct 94: 1265–1279. https://doi.org/10.1016/j.compstruct.2011.11.024 doi: 10.1016/j.compstruct.2011.11.024
![]() |
[15] | Dinesh G, Guru Moorthy A, Balaji AN, Mechanical and corrosion properties of hybrid sisal fibre/cotton fibre/coconut sheath reinforced polymer composites, 2019. Available from: https://www.mzcet.in/naac/documents/cf91.pdf. |
[16] |
Kurt M, Bagci E, Kaynak Y (2009) Application of Taguchi methods in the optimization of cutting parameters for surface finish and hole diameter accuracy in dry drilling processes. Int J Adv Manuf Tech 40: 458–469. https://doi.org/10.1007/s00170-007-1368-2 doi: 10.1007/s00170-007-1368-2
![]() |
[17] |
Davim JP, Reis P (2003) Drilling carbon fiber reinforced plastic manufactured by auto clave experimental and statistical study. Mater Design 24: 315–324. https://doi.org/10.1016/S0261-3069(03)00062-1 doi: 10.1016/S0261-3069(03)00062-1
![]() |
[18] | Korkut I, Kucuk Y (2010) Experimental analysis of the deviation from circularity of bored hole based on the Taguchi method. Stroj Vestn-J Mech E 56: 340–346. |
[19] |
Tsao CC, Hocheng H (2008) Evaluation of thrust force and surface roughness in drilling composite material using Taguchi analysis and neural network. J Mater Process Tech 203: 342–348. https://doi.org/10.1016/j.jmatprotec.2006.04.126 doi: 10.1016/j.jmatprotec.2006.04.126
![]() |
[20] |
Sahoo P, Barman TK, Routara BC (2008) Fractal dimension modelling of surface profile and optimization in CNC end milling using response surface method. Int J Manuf Res 3: 360–377. https://doi.org/10.1504/IJMR.2008.019216 doi: 10.1504/IJMR.2008.019216
![]() |
[21] |
Hadi RM, Mohsen H, Masatoshi K, et al. (2019) Experimental study on drilling of jute fiber reinforced polymer composites. J Compos Mater 53: 283–295. https://doi.org/10.1177/0021998318782376 doi: 10.1177/0021998318782376
![]() |
[22] | Taguchi G, Konishi S (1987) Taguchi Methods, Orthogonal Arrays and Linear Graphs: Tools for Quality Engineering, Dearborn Michigan: American Supplier Institute, 35–38. |
[23] |
Rao RS, Kumar CG, Prakasham RS, et al. (2008) The Taguchi methodology as a statistical tool for biotechnological application: A critical appraisal. Biotechnol J 3: 510–523. https://doi.org/10.1002/biot.200700201 doi: 10.1002/biot.200700201
![]() |
[24] | Yang WP, Tarng Y (1998) Design optimization of cutting parameters for turning operations based on the Taguchi method. J Mater Process Tech 84: 122–129. https://doi.org/10.1016/S0924-0136(98)00079-X |
[25] |
Lotfi A, Li H, Dao DV (2019) Machinability analysis in drilling flax fiber-reinforced polylactic acid bio-composite laminates. Int J Mater Metall Eng 13: 443–447. https://doi.org/10.5281/zenodo.3455743 doi: 10.5281/zenodo.3455743
![]() |
[26] | Philip JR (1996) Taguchi Techniques for Quality Engineering: Loss Function, Orthogonal Experiments, Parameter and Tolerance Design, 2 Eds., Chennai: McGraw-Hill Education (India) Private Limited. |
[27] | Phadke MS (1989) Quality engineering using robust design, London: Prentice-Hall, 07632. https://doi.org/10.1007/978-1-4684-1472-1_3 |
[28] |
Ravishankar B, Nayak SK, Kader MA (2019) Hybrid composites for automotive applications–A review. J Reinf Plast Comp 38: 835–845. https://doi.org/10.1177/0731684419849708 doi: 10.1177/0731684419849708
![]() |
[29] |
Al-Oqla FM, Sapuan SM (2014) Natural fiber reinforced polymer composites in industrial applications: Feasibility of date palm fibers for sustainable automotive industry. J Clean Prod 66: 347–354. https://doi.org/10.1016/j.jclepro.2013.10.050 doi: 10.1016/j.jclepro.2013.10.050
![]() |
1. | Riyadh Benyettou, Salah Amroune, Mohamed Slamani, Yasemin Seki, Alain Dufresne, Mohammad Jawaid, Salman Alamery, Assessment of induced delamination drilling of natural fiber reinforced composites: a statistical analysis, 2022, 21, 22387854, 131, 10.1016/j.jmrt.2022.08.161 | |
2. | Amiya Kumar Sahoo, Dhananjay R. Mishra, Parametric optimization of response parameter of Nd-YAG laser drilling for basalt-PTFE coated glass fibre using genetic algorithm, 2023, 23071877, 10.1016/j.jer.2023.07.014 | |
3. | S. Gowtham, T. Jeevanantham, J. Emelda, J. Edric, Investigation on effect of fibre orientation on mechanical behaviour of polymer matrix natural fibre reinforced composite material, 2024, 22147853, 10.1016/j.matpr.2024.04.022 | |
4. | Chinyere O. Nwankwo, Jeffrey Mahachi, David O. Olukanni, Innocent Musonda, Africa's natural fibres used in polymer composites: A systematic review, 2024, 45, 0272-8397, 9677, 10.1002/pc.28482 | |
5. | Abdelmalek Elhadi, Salah Amroune, Mohamed Slamani, Mohammad Jawaid, Ugur Koklu, Tarek Bidi, Evaluation of drilling by induced delamination of hybrid biocomposites reinforced with natural fibers: A statistical analysis by RSM, 2024, 58, 0021-9983, 2515, 10.1177/00219983241271035 | |
6. | Madani Grine, Mohamed Slamani, Aissa Laouissi, Mustapha Arslane, Mansour Rokbi, Jean-François Chatelain, Enhanced investigations and modeling of surface roughness of epoxy/Alfa fiber biocomposites using optimized neural network architecture with genetic algorithms, 2024, 130, 0268-3768, 3115, 10.1007/s00170-023-12866-0 | |
7. | Syed Altaf Hussain, Manoj Panchal, Kundan Meshram, R Srinivas, Upendra Rajak, Rajan Kumar, Manish Gupta, Turning GFRP composites with multi-response optimisation using TOPSIS method, 2024, 1955-2513, 10.1007/s12008-024-01762-w | |
8. | Veena Chougala, Ashwin C. Gowda, Santhosh Nagaraja, Muhammad Imam Ammarullah, Effect of Chemical Treatments on Mechanical Properties of Sugarcane Bagasse (Gramineae Saccharum Officinarum L) Fiber Based Biocomposites: A Review, 2025, 22, 1544-0478, 10.1080/15440478.2024.2445571 |
Process parameters | Level 1 | Level 2 | Level 3 | Level 4 |
A: Spindle speed (rpm) | 600 | 900 | 1200 | 1600 |
B: Feed rate (mm/min) | 10 | 15 | 20 | 25 |
C: Drill diameter (mm) | 6 | 7 | 8 | 10 |
Experimental runs | Spindle speed (rpm) | Feed rate (mm/min) | Drill diameter (mm) |
1 | 600 | 10 | 6 |
2 | 600 | 15 | 7 |
3 | 600 | 20 | 8 |
4 | 600 | 25 | 10 |
5 | 900 | 10 | 7 |
6 | 900 | 15 | 6 |
7 | 900 | 20 | 10 |
8 | 900 | 25 | 8 |
9 | 1200 | 10 | 8 |
10 | 1200 | 15 | 10 |
11 | 1200 | 20 | 6 |
12 | 1200 | 25 | 7 |
13 | 1600 | 10 | 10 |
14 | 1600 | 15 | 8 |
15 | 1600 | 20 | 7 |
16 | 1600 | 25 | 6 |
Experimental runs | Spindle speed (rpm) |
Feed rate (mm/min) |
Drill diameter (mm) |
Roundness error (mm) |
Surface roughness (Ra) |
1 | 600 | 10 | 6 | 0.10 | 337.29 |
2 | 600 | 15 | 7 | 0.14 | 324.58 |
3 | 600 | 20 | 8 | 0.17 | 306.00 |
4 | 600 | 25 | 10 | 0.25 | 309.81 |
5 | 900 | 10 | 7 | 0.15 | 278.81 |
6 | 900 | 15 | 6 | 0.11 | 250.16 |
7 | 900 | 20 | 10 | 0.26 | 270.61 |
8 | 900 | 25 | 8 | 0.18 | 225.16 |
9 | 1200 | 10 | 8 | 0.19 | 230.40 |
10 | 1200 | 15 | 10 | 0.26 | 233.26 |
11 | 1200 | 20 | 6 | 0.11 | 162.48 |
12 | 1200 | 25 | 7 | 0.15 | 155.24 |
13 | 1600 | 10 | 10 | 0.28 | 175.22 |
14 | 1600 | 15 | 8 | 0.20 | 130.75 |
15 | 1600 | 20 | 7 | 0.16 | 98.40 |
16 | 1600 | 25 | 6 | 0.12 | 66.42 |
Exp. runs | Experimental values (mm) | Predicted values (mm) | Mean error (%) |
1 | 0.10 | 0.101 | 1.00 |
2 | 0.14 | 0.137 | 2.14 |
3 | 0.17 | 0.174 | 2.35 |
4 | 0.25 | 0.247 | 1.20 |
5 | 0.15 | 0.147 | 2.00 |
6 | 0.11 | 0.107 | 3.10 |
7 | 0.26 | 0.258 | 0.60 |
8 | 0.18 | 0.179 | 0.61 |
9 | 0.19 | 0.195 | 2.53 |
10 | 0.26 | 0.269 | 3.58 |
11 | 0.11 | 0.113 | 2.72 |
12 | 0.15 | 0.149 | 0.73 |
13 | 0.28 | 0.283 | 1.07 |
14 | 0.20 | 0.204 | 1.75 |
15 | 0.16 | 0.163 | 1.63 |
16 | 0.12 | 0.122 | 1.66 |
Levels | Spindle speed (rpm) | Feed rate (mm/rev) | Drill diameter(mm) |
1 | 16.21 | 15.35 | 19.05 |
2 | 15.59 | 15.56 | 16.65 |
3 | 15.27 | 15.43 | 14.58 |
4 | 14.75 | 15.48 | 11.54 |
Delta | 1.46 | 0.21 | 7.51 |
Rank | 2 | 3 | 1 |
Source | DF | Seq SS | Contribution | Adj SS | Adj MS | F-value | P-value |
Spindle speed | 3 | 0.001716 | 3.19% | 0.001716 | 0.000572 | 102.81 | 0.000 |
Feed rate | 3 | 0.000137 | 0.25% | 0.000137 | 0.000046 | 8.19 | 0.015 |
Drill diameter | 3 | 0.051877 | 96.49% | 0.051877 | 0.017292 | 3108.72 | 0.000 |
Error | 6 | 0.000033 | 0.06% | 0.000033 | 0.000006 | ||
Total | 15 | 0.053762 | 100.00% |
Exp. runs | Exp. results (Ra) | Predicted results (Ra) | Mean error (%) |
1 | 337.29 | 332.96 | 1.28 |
2 | 324.58 | 321.33 | 1.01 |
3 | 306.00 | 309.70 | 1.21 |
4 | 309.81 | 308.84 | 0.32 |
5 | 278.81 | 283.10 | 1.54 |
6 | 250.16 | 249.91 | 0.10 |
7 | 270.61 | 270.61 | 0.00 |
8 | 225.16 | 226.65 | 0.66 |
9 | 230.40 | 233.24 | 1.23 |
10 | 233.26 | 232.38 | 0.38 |
11 | 162.48 | 166.86 | 2.70 |
12 | 155.24 | 155.23 | 0.01 |
13 | 175.22 | 173.94 | 0.73 |
14 | 130.75 | 129.97 | 0.60 |
15 | 98.40 | 96.79 | 1.64 |
16 | 66.42 | 63.60 | 4.25 |
Level | Spindle speed (rpm) | Feed rate (mm/min) | Drill diameter (mm) |
1 | −50.09 | −47.90 | −44.79 |
2 | −48.14 | −46.95 | −45.69 |
3 | −45.66 | −45.61 | −46.58 |
4 | −40.85 | −44.28 | −47.68 |
Delta | 9.24 | 3.63 | 2.89 |
Rank | 1 | 2 | 3 |
Source | DF | Seq SS | Contribution | Adj SS | Adj MS | F-Value | P-Value |
Spindle Speed (rpm) | 3 | 89509 | 86.33% | 89508.5 | 29836.2 | 5698.72 | 0.000 |
Feed Rate (mm/min) | 3 | 10060 | 9.70% | 10059.5 | 3353.2 | 640.46 | 0.000 |
Drill diameter (mm) | 3 | 4083 | 3.94% | 4083.1 | 1361.0 | 259.96 | 0.000 |
Error | 6 | 31 | 0.03% | 31.4 | 5.2 | ||
Total | 15 | 103683 | 100.00% |
Process parameters | Level 1 | Level 2 | Level 3 | Level 4 |
A: Spindle speed (rpm) | 600 | 900 | 1200 | 1600 |
B: Feed rate (mm/min) | 10 | 15 | 20 | 25 |
C: Drill diameter (mm) | 6 | 7 | 8 | 10 |
Experimental runs | Spindle speed (rpm) | Feed rate (mm/min) | Drill diameter (mm) |
1 | 600 | 10 | 6 |
2 | 600 | 15 | 7 |
3 | 600 | 20 | 8 |
4 | 600 | 25 | 10 |
5 | 900 | 10 | 7 |
6 | 900 | 15 | 6 |
7 | 900 | 20 | 10 |
8 | 900 | 25 | 8 |
9 | 1200 | 10 | 8 |
10 | 1200 | 15 | 10 |
11 | 1200 | 20 | 6 |
12 | 1200 | 25 | 7 |
13 | 1600 | 10 | 10 |
14 | 1600 | 15 | 8 |
15 | 1600 | 20 | 7 |
16 | 1600 | 25 | 6 |
Experimental runs | Spindle speed (rpm) |
Feed rate (mm/min) |
Drill diameter (mm) |
Roundness error (mm) |
Surface roughness (Ra) |
1 | 600 | 10 | 6 | 0.10 | 337.29 |
2 | 600 | 15 | 7 | 0.14 | 324.58 |
3 | 600 | 20 | 8 | 0.17 | 306.00 |
4 | 600 | 25 | 10 | 0.25 | 309.81 |
5 | 900 | 10 | 7 | 0.15 | 278.81 |
6 | 900 | 15 | 6 | 0.11 | 250.16 |
7 | 900 | 20 | 10 | 0.26 | 270.61 |
8 | 900 | 25 | 8 | 0.18 | 225.16 |
9 | 1200 | 10 | 8 | 0.19 | 230.40 |
10 | 1200 | 15 | 10 | 0.26 | 233.26 |
11 | 1200 | 20 | 6 | 0.11 | 162.48 |
12 | 1200 | 25 | 7 | 0.15 | 155.24 |
13 | 1600 | 10 | 10 | 0.28 | 175.22 |
14 | 1600 | 15 | 8 | 0.20 | 130.75 |
15 | 1600 | 20 | 7 | 0.16 | 98.40 |
16 | 1600 | 25 | 6 | 0.12 | 66.42 |
Exp. runs | Experimental values (mm) | Predicted values (mm) | Mean error (%) |
1 | 0.10 | 0.101 | 1.00 |
2 | 0.14 | 0.137 | 2.14 |
3 | 0.17 | 0.174 | 2.35 |
4 | 0.25 | 0.247 | 1.20 |
5 | 0.15 | 0.147 | 2.00 |
6 | 0.11 | 0.107 | 3.10 |
7 | 0.26 | 0.258 | 0.60 |
8 | 0.18 | 0.179 | 0.61 |
9 | 0.19 | 0.195 | 2.53 |
10 | 0.26 | 0.269 | 3.58 |
11 | 0.11 | 0.113 | 2.72 |
12 | 0.15 | 0.149 | 0.73 |
13 | 0.28 | 0.283 | 1.07 |
14 | 0.20 | 0.204 | 1.75 |
15 | 0.16 | 0.163 | 1.63 |
16 | 0.12 | 0.122 | 1.66 |
Levels | Spindle speed (rpm) | Feed rate (mm/rev) | Drill diameter(mm) |
1 | 16.21 | 15.35 | 19.05 |
2 | 15.59 | 15.56 | 16.65 |
3 | 15.27 | 15.43 | 14.58 |
4 | 14.75 | 15.48 | 11.54 |
Delta | 1.46 | 0.21 | 7.51 |
Rank | 2 | 3 | 1 |
Source | DF | Seq SS | Contribution | Adj SS | Adj MS | F-value | P-value |
Spindle speed | 3 | 0.001716 | 3.19% | 0.001716 | 0.000572 | 102.81 | 0.000 |
Feed rate | 3 | 0.000137 | 0.25% | 0.000137 | 0.000046 | 8.19 | 0.015 |
Drill diameter | 3 | 0.051877 | 96.49% | 0.051877 | 0.017292 | 3108.72 | 0.000 |
Error | 6 | 0.000033 | 0.06% | 0.000033 | 0.000006 | ||
Total | 15 | 0.053762 | 100.00% |
Exp. runs | Exp. results (Ra) | Predicted results (Ra) | Mean error (%) |
1 | 337.29 | 332.96 | 1.28 |
2 | 324.58 | 321.33 | 1.01 |
3 | 306.00 | 309.70 | 1.21 |
4 | 309.81 | 308.84 | 0.32 |
5 | 278.81 | 283.10 | 1.54 |
6 | 250.16 | 249.91 | 0.10 |
7 | 270.61 | 270.61 | 0.00 |
8 | 225.16 | 226.65 | 0.66 |
9 | 230.40 | 233.24 | 1.23 |
10 | 233.26 | 232.38 | 0.38 |
11 | 162.48 | 166.86 | 2.70 |
12 | 155.24 | 155.23 | 0.01 |
13 | 175.22 | 173.94 | 0.73 |
14 | 130.75 | 129.97 | 0.60 |
15 | 98.40 | 96.79 | 1.64 |
16 | 66.42 | 63.60 | 4.25 |
Level | Spindle speed (rpm) | Feed rate (mm/min) | Drill diameter (mm) |
1 | −50.09 | −47.90 | −44.79 |
2 | −48.14 | −46.95 | −45.69 |
3 | −45.66 | −45.61 | −46.58 |
4 | −40.85 | −44.28 | −47.68 |
Delta | 9.24 | 3.63 | 2.89 |
Rank | 1 | 2 | 3 |
Source | DF | Seq SS | Contribution | Adj SS | Adj MS | F-Value | P-Value |
Spindle Speed (rpm) | 3 | 89509 | 86.33% | 89508.5 | 29836.2 | 5698.72 | 0.000 |
Feed Rate (mm/min) | 3 | 10060 | 9.70% | 10059.5 | 3353.2 | 640.46 | 0.000 |
Drill diameter (mm) | 3 | 4083 | 3.94% | 4083.1 | 1361.0 | 259.96 | 0.000 |
Error | 6 | 31 | 0.03% | 31.4 | 5.2 | ||
Total | 15 | 103683 | 100.00% |