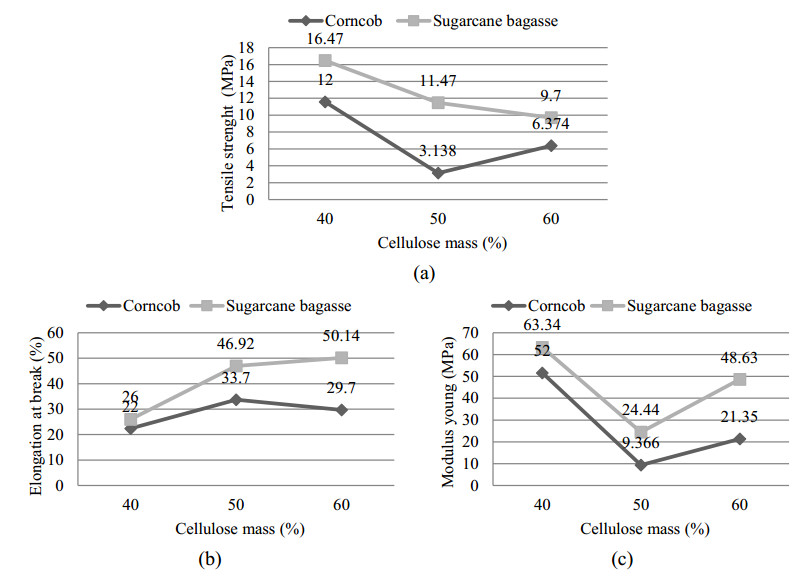
Sago starch and cellulose fiber can be used as a raw material for making degradable plastics to replace commercial plastics. This research used corn cob fiber and sugarcane bagasse fiber as filler to improve the properties of degradable plastic. The research method consists of several stages, cellulose fiber preparation, degradable plastic synthesis and plastic characterization. The result showed tensile strength of plastic with corn cob and sugarcane bagasse filler was 6.37–11.5 MPa and 9.70–16.47 MPa, respectively. The compound composition test through Fourier Transformation Infra-Red (FTIR) exhibited hydrophilic behavior, hence plastic easily degraded by soil. Differential Scanning Calorimetry (DSC) shows that degradable plastic with corn cob fiber filler denoted a melting point of 163.84 ℃, while sugarcane bagasse fiber filler at 163.47 ℃. Thermogravimetric Analysis (TGA) analysis indicated degradable plastic had a good thermal stability. Scanning Electron Microscopy (SEM) exhibited few white lumps and indentations on the surface, indicating that the solubility was not homogeny and could be due to the influence of stirring process. In term of ability to absorb water, both plastic with fiber filler had a small water absorption with a range of 5–6%. Melt Flow Rate (MFR) analysis of degradable plastics with corn cob fiber and sugarcane bagasse pointed the value that was suitable for injection molding processing technique. The degradation of both plastics ranged about 50–85 days to completely decomposed naturally in soil, as supported by FTIR analysis.
Citation: Rozanna Dewi, Novi Sylvia, Zulnazri, Medyan Riza, Januar Parlaungan Siregar, Tezara Cionita, Budhi Santri Kusuma. Characterization of sago starch-based degradable plastic with agricultural waste cellulose fiber as filler[J]. AIMS Environmental Science, 2024, 11(2): 304-323. doi: 10.3934/environsci.2024014
[1] | Rozanna Dewi, Novi Sylvia, Zulnazri Zulnazri, Medyan Riza, Januar Parlaungan Siregar, Tezara Cionita . Use calcium silicate filler to improve the properties of sago starch based degradable plastic. AIMS Environmental Science, 2025, 12(1): 1-15. doi: 10.3934/environsci.2025001 |
[2] | PA Stapleton . Toxicological considerations of nano-sized plastics. AIMS Environmental Science, 2019, 6(5): 367-378. doi: 10.3934/environsci.2019.5.367 |
[3] | Nguyen Trinh Trong, Phu Huynh Le Tan, Dat Nguyen Ngoc, Ba Le Huy, Dat Tran Thanh, Nam Thai Van . Optimizing the synthesis conditions of aerogels based on cellulose fiber extracted from rambutan peel using response surface methodology. AIMS Environmental Science, 2024, 11(4): 576-592. doi: 10.3934/environsci.2024028 |
[4] | Pablo Andrés–Meza, Noé Aguilar–Rivera, Isaac Meneses–Márquez, José Luis Del Rosario–Arellano, Gloria Ivette Bolio–López, Otto Raúl Leyva–Ovalle . Cassava cultivation; current and potential use of agroindustrial co–products. AIMS Environmental Science, 2024, 11(2): 248-278. doi: 10.3934/environsci.2024012 |
[5] | Katharina Meixner, Mona Kubiczek, Ines Fritz . Microplastic in soil–current status in Europe with special focus on method tests with Austrian samples. AIMS Environmental Science, 2020, 7(2): 174-191. doi: 10.3934/environsci.2020011 |
[6] | Serpil Guran . Options to feed plastic waste back into the manufacturing industry to achieve a circular carbon economy. AIMS Environmental Science, 2019, 6(5): 341-355. doi: 10.3934/environsci.2019.5.341 |
[7] | Goshu Desalegn, Anita Tangl, Maria Fekete-Farkas . Greening through taxation: assessing the potential opportunities and challenges of plastic products in Ethiopia. AIMS Environmental Science, 2022, 9(4): 432-443. doi: 10.3934/environsci.2022026 |
[8] | Carlos Garcia, Teresa Hernandez, Maria D Coll, Sara Ondoño . Organic amendments for soil restoration in arid and semiarid areas: a review. AIMS Environmental Science, 2017, 4(5): 640-676. doi: 10.3934/environsci.2017.5.640 |
[9] | Voke O. Urhibo, Bernard O. Ejechi . Crude oil degradation potential of bacteria isolated from oil-polluted soil and animal wastes in soil amended with animal wastes. AIMS Environmental Science, 2017, 4(2): 277-286. doi: 10.3934/environsci.2017.2.277 |
[10] | R. Kajaste, P. Oinas . Plastics value chain - Abatement of greenhouse gas emissions. AIMS Environmental Science, 2021, 8(4): 371-392. doi: 10.3934/environsci.2021024 |
Sago starch and cellulose fiber can be used as a raw material for making degradable plastics to replace commercial plastics. This research used corn cob fiber and sugarcane bagasse fiber as filler to improve the properties of degradable plastic. The research method consists of several stages, cellulose fiber preparation, degradable plastic synthesis and plastic characterization. The result showed tensile strength of plastic with corn cob and sugarcane bagasse filler was 6.37–11.5 MPa and 9.70–16.47 MPa, respectively. The compound composition test through Fourier Transformation Infra-Red (FTIR) exhibited hydrophilic behavior, hence plastic easily degraded by soil. Differential Scanning Calorimetry (DSC) shows that degradable plastic with corn cob fiber filler denoted a melting point of 163.84 ℃, while sugarcane bagasse fiber filler at 163.47 ℃. Thermogravimetric Analysis (TGA) analysis indicated degradable plastic had a good thermal stability. Scanning Electron Microscopy (SEM) exhibited few white lumps and indentations on the surface, indicating that the solubility was not homogeny and could be due to the influence of stirring process. In term of ability to absorb water, both plastic with fiber filler had a small water absorption with a range of 5–6%. Melt Flow Rate (MFR) analysis of degradable plastics with corn cob fiber and sugarcane bagasse pointed the value that was suitable for injection molding processing technique. The degradation of both plastics ranged about 50–85 days to completely decomposed naturally in soil, as supported by FTIR analysis.
Types of commercial plastics used today produce a lot of waste and are harmful to human health and the environment because they cannot be decomposed naturally for thousands of years. The issue of recycled plastics still remains controversial due to its safety and health concerns and high processing costs. Today, the world needs a solution to the growing problem of plastic waste. Conventional plastics such as PET take about 23 to 48 years to break down in the environment [1]. Some ways to deal with plastic waste are recycling, incineration, and burial. However, burning plastic waste can produce toxic substances that are harmful to living things and the environment. Meanwhile, bury waste is ineffective because plastic is difficult to degraded [2].
One of the solutions is to develop plastic products with materials that are easily decomposed by microbe, with starch and cellulose sources as the basic ingredients. Starch has been used from various plastic bases in an effort to develop biodegradable plastics and as an alternative to petroleum-based plastics. Starch is widely used as a thickener, emulsifier, and binding agent in the food and non-food sectors. Since starch is biodegradable, low cost, renewable, and abundant, it is considered a "green line" as a raw material to produce porous substances such as aerogels, biofoams, and bioplastic [3]. Sago contains starch, fiber, protein, fat, and ash. Sago starch contains cellulose as a macromolecular material [4]. Sago starch can be used as a base material for producing biodegradable plastic. Sago is abundant in Southeast Asia and has a low cost compared to other starches [5]. One of the weaknesses of degradable plastic from starch is the mechanical properties still not yet comparable to conventional plastics, so technology is needed to improve their performance. Nowadays, cellulose has taken center stage for researchers as a potential raw material for biopolymers. Cellulose fibers, cellulose derivatives, and nanocellulose have been used in the manufacture of composites and nanocomposites as matrices and fillers [6].
Binling Ai et al. examined banana stem-based cellulose films using ionic liquids for mango preservation. Produced good water vapor transmission rate and gas transmission rate than PE plastic and decomposed in soil within 4 weeks showing excellent biodegradability compared to PE plastic [7]. Naresh S et al. in his research on the manufacture of environmentally friendly plastics from the extraction of cellulose nanofiber (CNF) and bagasse using the hot press method produces very high mechanical properties [8].
This research was conducted to study the effect of cellulose fiber addition ratio in the synthesis of degradable plastic based on sago starch using hot press method. In this paper, the type of fiber used was cellulose from corn cob and bagasse with a mass ratio of 40, 50, 60%. The composition of corn cob is 38% cellulose, 18.5% lignin, 26% pentosane and 5.1% ash content, while sugar cane bagasse contains 32–45% cellulose, 20–32% hemicellulose, 17–32% lignin, and 1.0–9% ash content [9]. Jiang et al. [10] study proposed a simple, efficient, and energy-saving one-pot strategy to produce nanofibrillated cellulose (NFC) from bleached corn stalk, with tailored surface modifications. The effects of different surface functionalizations on the morphological, crystalline, chemical, and thermal properties of the NFC were investigated. The results suggested that the bleached corn stalk fibers were decomposed into microfibrils through intensive mechanical shearing. To enhance the mechanical properties and interfacial compatibility of thermoplastic starch (TPS) highly filled poly(butylene adipate co-terephthalate) (PBAT) composite films, esterified NFC through ball-milling was innovatively fabricated and introduced into the composite system. Notably, the tensile properties of the composite films reached their maximums at a 7 wt% NFC content, displaying a tensile strength of 6.2 MPa and an elastic modulus of 263 MPa [11]. This research also utilized Polypropylene graft Maleic Anhydrous (PP-g-MA) as a compatibilizer. Alper Aksit et al. mentioned the addition of compatibilizer Polyphenylene Ether graft Maleic Anhydrous (PPE-g-MA) can increase 10% of tensile strength and 70% of elongation at break [12]. Different weight variations of corn cob and bagasse fibers were used to determine the best characteristics of degradable plastics produced in terms of mechanical properties, thermal properties, functional groups, morphology, water absorption and melt flow behavior for best producing technique.
Equipment used in this research were beaker glass 500 mL, beaker glass 1000 mL, measuring cup 500 mL, measuring cup 1000 mL, mesh size 50, digital balance, tray, spatula, stirrer, thermometer, hot plate, hot press, blender. The materials used in this research are sago starch, corn cob cellulose fiber, sugarcane bagasse cellulose fiber, NaOH, NaOCl, xylene, maleic anhydrous, polypropylene (PP), benzoyl peroxide, and distilled water. All the materials are obtained from Merck and used without further purification.
The research method consists of several stages: milling stage, cellulose extraction with pre-delignification and delignification stages, preparation of degradable plastics and characterization of degradable plastics produced.
Prepare corn cobs and sugarcane bagasse of 1 kilogram each. Wash the corn cobs and sugarcane bagasse thoroughly. Dry the corn cobs and sugarcane bagasse for 24 hours outdoors. Corn cobs and sugarcane bagasse are cut into small pieces of 2 cm. Corn cob and sugarcane bagasse were blended to form powder and were sifted using a 50 mesh sieve until 1 mm powder was obtained.
Pre-delignification stage with steps consisting of corn cob powder and sugarcane bagasse were each added with distilled water 1:10. Heated at 100ºC for 3 hours and stirred homogeneously. The reflux was filtered to obtain solids and then drying with oven at 105 ℃.
The delignification stage was as follows: corn cob powder and bagasse from pre-hydrolysis was dissolved in NaOH of 20, 25, 30% concetration by weight. Heated at 160 ℃ for 60 minutes. The reflux was filtered to obtain solids. The solid was mixed with 3.5% NaOCl solution by weight and distilled water with the ratio of distilled water and 3.5% NaOCl solution by weight in the ratio of 1:1. Simmer for 10 minutes followed by filtering, washing, and drying in the oven at 105 ℃. The result obtained was alpha-cellulose dry powder.
The first stage of the grafting preparation process was 70 g, 75 g, 80 g of polypropylene was diluted in 100 mL of xylene, maleic anhydrous (MAH) 1% of the volume of xylene was added, then followed by benzoyl peroxide of 0.1% of the weight of MAH. Stirred until homogeneous at 125 ℃ to produce PP-g-MA. The next step was the preparation of degradable plastics by heating and mixing between corn cob and sugar cane bagasse alpha-cellulose with variation of 40, 50, 60% respectively, and sago starch of 100 g and PP-g-MA, then stirred evenly. After homogeny, molded using a hot press for 10 minutes with a temperature of 165 ℃.
Mechanical characteristics of degradable plastics were performed by tensile test, elongation and young's modulus. Tensile test conducted by ASTM D-638 (American Standard Testing and Material). Tensile strength analysis was carried out using a Mechanical Universal Testing Machine. Cut the sample according to the size. Chemical characterization was carried out with Fourier Transformation Infra-Red (FTIR) to determine the functional groups contained in the degradable plastic produced. Testing the thermal properties of degradable plastics was done by Differential Scanning Calorimetry (DSC) analysis to determine the energy absorbed and Thermogravimetric Analysis (TGA) analysis to determine the thermal stability. Melt Flow Rate (MFR) analysis aimed to determine the flow rate (melt) of degradable plastics. Scanning Electron Microscopy (SEM) analysis to determine the morphology of degradable plastics. Analysis of the resistance of degradable plastics to water was done by water absorption test. Finally, Biodegradability rate was done using soil burial method to obtain soil ability to degrade the plastic in nature when attacked by microorganism.
In this study, the measurement of tensile strength was carried out using a texture analyzer. Tensile strength is the maximum ability to withstand external forces before the degradable plastic is damaged or broken. Damage can occur by splitting due to excessive stress or possibly by structural deformation. The results obtained show that the addition of fibers tends to decrease the tensile strength value of degradable plastics. The results of the tensile strength test with variations in the weight of corn cob cellulose fiber and sugar bagasse cellulose fiber of 25% NaOH with cellulose mass of 40, 50 and 60% were presented in Figure 1.
To identify chemical bonds in organic materials, polymers, metals and various materials, Fourier Transform Infrared Spectroscopy (FTIR) can be used. The FTIR analysis method uses infrared light to scan the test sample and observe chemical properties. When a material is irradiated with infrared radiation, the absorbed IR radiation usually keeps the molecules at a higher vibrational state. The wavelength absorbed by the sample is characteristic of its molecular structure. Figures 2 and 3 indicated FTIR analysis for sago starch-based degradable plastic using corn cob cellulose fiber and sugar cane bagasse cellulose fiber of 25% NaOH variation and cellulose fiber mass of 60%.
Thermal properties of degradable plastics are measured by Thermogravimetric analysis (TGA), Differential Scanning Calorimetry (DSC) and Melt Flow Rate (MFR). Thermal degradation of polymers is the molecular decay and loss of hydrogen atoms from the polymer chain as a result of excessive heat. Thermal degradation serves as an upper bound for the operating temperature of the polymer. Thermal stability of degradable plastics was measured by Thermogravimetric (TGA). The heat capacity and absorbed energy was measured by Differential Scanning Calorimetry (DSC), meanwhile flow rate or melting point of degradable plastics was measured by Melt Flow Rate (MFR).
TGA tests are commonly used to determine sample purity, decomposition, thermal degradation, chemical reactions involving weight changes of materials due to adsorption, desorption and chemical kinetics. TGA is a measurement technique using weight variation as a function of heating temperature. This characterization is used to determine the weight loss or weight increase of a sample (gas fixation). The TGA test results of sago starch-based degradable plastics using corn cob cellulose fiber and bagasse cellulose at 60% cellulose mass and 25% NaOH can be seen in Figure 4 (a), (b).
One of the indicators of plastic quality is its resistance to heat, which can be analyzed by Differential Scanning Calorimetry (DSC). Basic principle underlying DSC analysis technique is when a sample undergoes a physical transformation such as a phase transition, a change in heat will be required to flow from the reference and sample to maintain both at same temperature. Whether less or more heat is required to flow into the sample depends on the process is exothermic (heat release) or endothermic (heat absorption). In this study, DSC was conducted to determine how much energy was absorbed by the degradable plastic. The DSC test equipment used was DSC 8000 Perkin Elmer using ASTM D3418-15 standard. The results of degradable plastics using corn cob and bagasse cellulose fiber with 60% cellulose mass and 25% of NaOH concentration can be seen in Figure 5 (a), (b).
Plastic material specifications that describe the flow rate (melt) of polymer material in a certain unit of time (gr/10/min) can be measured by Melt Flow Rate (MFR). The MFR test parameters in this study used CEAST Model 7026.000 test equipment with ASTM E1238-20 at 230 ℃/5 kg. Table 1 showed melt mass flow rate test results of sago starch-based degradable plastics using corn cob and sugarcane bagasse cellulose fibers.
Sample Name | MFR [g/10 menit] |
Corn cob cellulose-based degradable plastics | Not measured (the sample did not melt completely so the measurement is invalid) |
Sugarcane bagasse cellulose-based degradable plastics | 1.02 ± 0.68 |
Scanning Electron Microscopy (SEM) is a tool to study the surface morphology structure and cross section of a material. SEM produces images of surfaces by scanning them with a focused beam of electrons. The electrons interact with atoms in the surface, producing a variety of signals that contain information about the topography and composition of the surface. SEM can produce high resolution in the nano meter scale. The sample is observed in liquid state in a controlled environment. The SEM test equipment used in this study is JSM-6510LA JEOL SEM with Au coating (30 mA; 40 seconds), 20 kV at 100X, 500X and 1000X magnification (1 area). SEM morphology images of sago starch-based degradable plastics using corn cob and bagasse cellulose fibers of 60% cellulose mass and 25% NaOH concentration can be seen in Figures 6 and 7.
The water absorption test was conducted to determine the resistance of degradable plastics to water absorption. The water absorption test was carried out by calculating the weight change that occurred due to the amount of water absorbed after being dipped in water within 1 minute. The amount of water absorbed is written as percent water absorbed. The results of the water absorption test of sago starch-based degradable plastics using corn cob cellulose fiber and sugarcane bagasse cellulose fiber were presented in Figure 8 (a), (b).
The biodegradability test aims to determine the degradation rate of degradable plastic, therefore, it takes time for the degradation of degradable plastics. The biodegradability rate was done by burial test in the soil which will be degraded by microbes. The results of the biodegradability test of sago starch-based degradable plastics using corn cob cellulose fibers and bagasse cellulose fibers were presented in Tables 2 and 3.
Days | Cellulose Mass (%) | ||||||||
NaOH 20% | NaOH 25% | NaOH 30% | |||||||
40 | 50 | 60 | 40 | 50 | 60 | 40 | 50 | 60 | |
3 | 0.35 | 0.68 | 0.43 | 0.17 | 0.21 | 0.20 | 0.21 | 0.28 | 0.23 |
6 | 3.26 | 3.89 | 3.78 | 1.78 | 2.61 | 1.60 | 1.99 | 2.86 | 2.67 |
9 | 12.09 | 13.63 | 12.55 | 7.20 | 9.93 | 8.70 | 9.95 | 10.57 | 11.52 |
12 | 18.49 | 21.32 | 20.94 | 13.76 | 15.10 | 13.67 | 15.47 | 18.52 | 17.16 |
16 | 25.06 | 27.9 | 26.94 | 19.19 | 23.68 | 20.7 | 22.48 | 25.58 | 24.21 |
18 | 29.58 | 33.17 | 32.15 | 22.18 | 26.71 | 23.60 | 25.98 | 29.77 | 28.31 |
21 | 35.62 | 39.88 | 38.70 | 26.88 | 32.30 | 28.59 | 31.42 | 35.98 | 34.16 |
24 | 41.67 | 46.60 | 45.25 | 31.57 | 37.89 | 33.58 | 36.87 | 42.19 | 40.00 |
27 | 47.72 | 53.31 | 51.81 | 36.26 | 43.49 | 38.57 | 42.31 | 48.40 | 45.85 |
30 | 53.76 | 60.02 | 58.36 | 40.96 | 49.08 | 43.56 | 47.75 | 54.61 | 51.70 |
33 | 59.81 | 66.73 | 64.91 | 45.65 | 54.67 | 48.54 | 53.20 | 60.82 | 57.55 |
36 | 65.85 | 73.45 | 71.47 | 50.34 | 60.27 | 53.53 | 58.64 | 67.03 | 63.40 |
39 | 71.90 | 80.16 | 78.02 | 55.04 | 65.86 | 58.52 | 64.08 | 73.24 | 69.24 |
42 | 77.94 | 86.87 | 84.57 | 59.73 | 71.45 | 63.51 | 69.53 | 79.45 | 75.09 |
45 | 83.99 | 93.59 | 91.12 | 64.42 | 77.05 | 68.50 | 74.97 | 85.66 | 80.94 |
48 | 90.04 | 100 | 97.68 | 69.12 | 82.64 | 73.49 | 80.41 | 91.87 | 86.79 |
51 | 96.08 | - | 100 | 73.81 | 88.23 | 78.47 | 85.86 | 98.08 | 92.64 |
54 | 100 | - | - | 78.50 | 93.83 | 83.46 | 91.30 | 100 | 98.49 |
57 | - | - | - | 83.20 | 99.42 | 88.45 | 96.74 | - | 100 |
60 | - | - | - | 87.89 | 100 | 93.44 | 100 | - | - |
63 | - | - | - | 92.59 | - | 98.43 | - | - | - |
66 | - | - | - | 97.28 | - | 100 | - | - | - |
69 | - | - | - | 100 | - | - | - | - | - |
Days | Cellulose Mass (%) | ||||||||
NaOH 20% | NaOH 25% | NaOH 30% | |||||||
40 | 50 | 60 | 40 | 50 | 60 | 40 | 50 | 60 | |
3 | 0.73 | 0.81 | 0.84 | 0.34 | 0.38 | 0.46 | 0.45 | 0.58 | 0.64 |
6 | 1.96 | 1.80 | 2.55 | 0.89 | 1.00 | 1.34 | 1.45 | 1.70 | 2.08 |
9 | 6.01 | 7.94 | 8.95 | 5.40 | 5.95 | 6.18 | 5.53 | 6.26 | 7.82 |
12 | 15.52 | 16.97 | 17.60 | 10.22 | 11.00 | 12.58 | 13.09 | 15.11 | 16.18 |
15 | 26.23 | 27.37 | 28.32 | 15.02 | 15.89 | 16.36 | 20.61 | 21.08 | 24.70 |
18 | 28.05 | 29.91 | 27.32 | 17.05 | 18.15 | 19.20 | 22.62 | 23.95 | 27.49 |
21 | 34.17 | 36.37 | 32.99 | 20.68 | 22.00 | 23.23 | 27.54 | 29.07 | 33.36 |
24 | 40.29 | 42.83 | 38.65 | 24.32 | 25.86 | 27.26 | 32.45 | 34.19 | 39.23 |
27 | 46.42 | 49.29 | 44.32 | 27.96 | 29.71 | 31.29 | 37.36 | 39.31 | 45.10 |
30 | 52.54 | 55.74 | 49.99 | 31.60 | 33.57 | 35.32 | 42.27 | 44.42 | 50.96 |
33 | 58.66 | 62.20 | 55.66 | 35.24 | 37.42 | 39.35 | 47.18 | 39.31 | 56.83 |
36 | 64.79 | 68.66 | 61.32 | 38.88 | 41.28 | 43.38 | 52.09 | 44.42 | 62.70 |
39 | 70.91 | 75.11 | 66.99 | 42.52 | 45.14 | 47.41 | 57.00 | 49.54 | 68.57 |
42 | 77.03 | 81.57 | 72.66 | 46.16 | 48.99 | 51.44 | 61.91 | 54.66 | 74.44 |
45 | 83.16 | 88.03 | 78.33 | 49.80 | 52.85 | 55.47 | 66.82 | 59.78 | 80.30 |
48 | 89.28 | 95.49 | 84.00 | 53.44 | 56.70 | 59.50 | 71.73 | 64.89 | 86.17 |
51 | 95.40 | 100 | 89.66 | 57.08 | 60.56 | 63.53 | 76.64 | 70.01 | 92.04 |
54 | 100 | - | 95.33 | 60.72 | 64.41 | 67.56 | 81.55 | 75.13 | 97.91 |
57 | - | - | 100 | 64.36 | 68.27 | 71.59 | 86.46 | 80.25 | 100 |
60 | - | - | - | 68.00 | 72.12 | 75.62 | 91.37 | 95.60 | - |
63 | - | - | - | 71.64 | 75.98 | 79.65 | 96.28 | 100 | - |
66 | - | - | - | 75.28 | 79.83 | 83.68 | 100 | - | - |
69 | - | - | - | 78.92 | 83.68 | 87.71 | - | - | - |
72 | - | - | - | 82.56 | 87.54 | 91.74 | - | - | - |
75 | - | - | - | 86.20 | 91.40 | 95.77 | - | - | - |
78 | - | - | - | 89.84 | 95.25 | 99.80 | - | - | - |
81 84 |
- - |
- - |
- - |
93.48 97.12 |
99.11 100 |
100 - |
- - |
- - |
- - |
Mechanical properties were carried out to determine the value of tensile strength, elongation and modulus of elasticity in degradable plastics. In Figure 1 (a), the tensile strength value of sago starch-based degradable plastic using corn cob cellulose fiber obtained in this study ranged from 6.37–11.5 MPa. The lowest tensile strength was obtained at 50% cellulose mass and the highest tensile strength was obtained with 40% cellulose mass. At the use of 60% corn cob cellulose fiber has a tendency to increase the tensile strength, it may be the effect of less homogenized stirring that resulted in the surface unevenness of the degradable plastic film. The tensile strength values of sago starch-based degradable plastics using sugarcane bagasse cellulose fibers ranged from 9.70–16.47 MPa, with the lowest tensile strength at 60% cellulose mass and the highest at 40% cellulose mass. From Figure 1 (a), it can be seen that the addition of cellulose mass at a certain concentration can increase the tensile strength, but if it is too much, it tends to reduce the tensile strength value of degradable plastics. The tensile strength value using 40% cellulose mass in sago starch-based degradable plastics using corn cob and sugarcane bagasse cellulose fibers in this study was comparable to the tensile strength obtained in LDPE (10–12 MPa) [13]. The stirring factor also affects the preparation of degradable plastic synthesis to obtain the optimal tensile strength.
Elongation of a material was a measure of the material's ability to stretch when pulled and determines the elasticity of a material. The higher the elongation value, the more elastic the degradable plastic, hence the material has a large creep value. From Figure 1 (b), it can be seen that the highest elongation value of degradable plastics was found in 50% cellulose mass of 33.70% for corn cob cellulose and 46.92% for bagasse cellulose. The elongation value obtained was comparable to the elongation value of PET (15–165%) [13].
The elastic modulus of the material was proportional to the elongation value, where the elastic modulus is a measure of the stiffness of the elastic material and is a quantity used to characterize the material, which is related to the size of the stress and strain of an object. In Figure 1 (c), the elastic modulus values of sago starch-based degradable plastic using corn cob cellulose fibers obtained of 9.366–51.62 MPa, while for sugarcane bagasse cellulose fiber was 24.44–63.34 MPa. If the force or stress is stopped, the object will return to its original state. The ratio of stress and strain is constant and the magnitude of the constant is called the modulus of elasticity. The greater the value of the modulus of elasticity, the more rigid the material will be and not easily deformed.
This research also used PP graft Maleic Anhydrous (PP-g-Ma) to improve mechanical properties. Waryat et al. [14] used maleic anhydrous compatibilizer to improve the morphological, physical and mechanical characteristics of biodegradable plastics made from polyethylene thermoplastic starch. Compatibilizer acts as a connector for materials with different characteristics between hydrophobic LLDPE and hydrophilic thermoplastic starch (TPS). The used of compatibilizer cause degradable plastics more compatible and homogeneous and can improve physical and mechanical properties. Compatibilizer is able to improve the adhesively of the interface between LLDPE and TPS. This was indicated by the increasing trend of physical and mechanical characteristics of biodegradable plastics.
Chemical characterization was obtained by FTIR analysis which aims to determine the functional groups contained in the degradable plastic produced. FTIR analysis in this research was conducted at wavenumbers of 550–4000 cm-1. In Figure 2, it can be observed that the wave number 3140.11 cm-1, 3570.24 cm-1, and 3753.48 cm-1 showed the presence of O-H stretching vibrations on the sodium hydroxide compound contained in cellulose. The absorption peak at wave number of 2968.45 cm-1, 2873.94 cm-1, 2833.43 cm-1 and 2721.56 cm-1 was characterized as an asymmetric stretching vibration of the C-H bond in the methyl group contained in sago starch. At wavenumber of of 1654.92 cm-1, 1707.00 cm-1 and 1751.36 cm-1 characterized as C = C stretching vibrations found in PP-g-MA compounds. In Figure 3. it can be seen that there are O-H stretching vibrations at wavenumber of 3429.43 cm-1, 3674.39 cm-1 and 3753.48 cm-1 on sodium hydroxide compounds found in cellulose, while the absorption peak at wavenumber of 2954.95 cm-1, 2873.94 cm-1 and 2833.43 cm-1 which is the C-H stretching vibration of the methyl group obtained from sago starch. C = C stretching vibration with wave number of 1560.41 cm-1, 1456.26 cm-1 and 1373.32 cm-1 on PP-g-MA compound. The presence of various functional groups can potentially affect the interfacial interaction between cellulose and PP-g-MA molecules in degradable plastics, and can play a role in determining mechanical and physical properties.
The cluster content contained in the FTIR analysis of sago starch degradable plastic using corn cob fiber and sugarcane bagasse fiber was an organic group, the plastic was hydrophilic which binds to water so that it is easily degraded by soil. This also indicated that the degradable plastic has more free hydroxyl groups -OH due to the reduction of atoms that can bond with hydrogen. Shiou et al. [15] in their research stated that hydrogen bonding between OH groups from starch and COOH groups from Cellulose Nanocrystals (CNC) has a high tensile strength value and has a low elongation value.
The thermal stability of degradable plastics is evaluated by monitoring the weight change as a function of temperature at a predetermined heating rate by DSC and the effects of polymer heating during physical changes (glass transition and melting) by TGA. Addition of extractive substances doesn't significantly affect thermal properties of degradable plastic based sago starch, while the addition of cellulose improves the decomposition temperature of the degradable plastic.
TGA testing was taken from the use of 60% cellulose mass; 25% NaOH on sago starch-based degradable plastics using corn cob cellulose fiber and sugarcane bagasse cellulose fiber. The resulting curve in the TGA analysis is the change in mass vs. temperature as the TGA curve shown in Figure 4 (a), (b). The TGA curve was a plot of % mass loss on the y-axis and temperature increase on the x-axis. Figure 4 (a), (b) illustrated the thermal temperature of each variation, it has undergone an endothermic process due to the formation between starch, extractive substances used and cellulose fibers from materials used in degradable plastics. Figure 4 (a) shows the mass loss (decomposition) of the sample which starts slowly at 31.64 ℃. At this temperature the weight loss is caused by contaminants and other additives contained in the degradable plastic. In Figure 4 (a) the extreme weight loss starts at 456.12 ℃ to 484.06 ℃. Under these conditions most of the material is decomposed and completely depleted at 600℃. Meanwhile, Figure 4 (b) also shows a decrease in mass (decomposition) in the sample which starts slowly at 30 ℃ and extreme weight loss starts at 433.55 ℃ to 460.12 ℃. At this condition, most of the material is decomposed and completely depleted at 600 ℃. In this study, degradable plastics experienced a high degree of thermal degradation and at this stage the loss of hydrogen groups, and decomposition and depolymerization occurred. Zheng Cao et al. [16] stated the use of too much cellulose can inhibit the decomposition of polymers. The total weight loss for the two samples was slightly different; 93% for degradable plastic with corn cob cellulose (11.16 mg) and 95.69% for degradable plastic bagasse cellulose (10.81 mg). The change of TGA thermogram occured due to the heat change of the degradable plastic and also the reaction of the structure change and phase change of the degradable plastic. It can be concluded that the higher the residual weight decomposed, the better the thermal resistance of degradable plastics. Sago starch-based degradable plastics using corn cob fiber and sugarcane bagasse revealed good thermal stability.
Differential Scanning Calorimetry (DSC) can determine melting point, crystallization, mesomorphic transition temperature, corresponding enthalpy and entropy changes, and characterization of glass transition and other effects featuring either changes in heat capacity or latent heat. DSC tests were taken from the use of 60% cellulose mass; 25% NaOH on sago starch-based degradable plastics using corn cob and sugarcane bagasse cellulose fibers. In this study, PP-g-MA was used as compatibilizer. From thermal analysis through DSC carried out on plastic samples that use the most cellulose fiber is at 60% by weight cellulose. Figure 5 (a) illustrated sago starch-based degradable plastics using corn cob cellulose fibers have a melting temperature at Tm of 163.84 ℃ and latent heat of melting (ΔH) of 60.5532 J/g. Figure 5 (b) sago starch-based degradable plastics using sugarcane bagasse cellulose fibers have melting temperatures at Tm of 163.47 ℃ and latent heat of melting (ΔH) of 31.0530 J/g. Melting temperature (Tm) in both degradable plastic samples showed homogenization formation between starch, corn cob fiber and sugarcane bagasse, when compared to the Tm of sago starch which is only about 70 ℃. The Tm values obtained in both degradable plastics have an endothermic peak in the glass transition state. If the polymer in the molten state is cooled, it will reach the glass transition (Tg). At this point, the mechanical properties of the polymer change from an elastic material to a brittle material due to changes in chain mobility. This point is important for the preparation of compound lattices in degradable plastics. Pooja et al. [17] in the thermal analysis of polymer blends by DSC, DSC results for Polyvinylidene fluoride and Polysulfone (PVDF-PSF) blend samples obtained glass transition (Tg) at temperature of163.1℃. A glass transition peak can be seen at the level where the temperature of the amorphous solid is found to increase.
Chunhua et al. [18] in the research of corn stalk-based composites using epoxy resin has a Tg at 175 ℃. As previously reported by Gadaleta et al. [19] Tg of 127 ℃ for bioplastics from cellulose acetate plasticized (CAT). In the bioplastic CAT modified with LDPE, the glass transition value obtained was about 198 ℃. However, this Tg value is too close to the limit of the temperature range considered in DSC measurements so that the loss of triacetin compound during the extrusion process causes the CAT to return to its original form.
MFR values are needed to determine material specifications, control the quality of raw materials, choose the right process method, and compare the modified material with the original material. To be moldable, thermoplastic starch must be mixed with polyethylene (PE) or polypropylene (PP) in a certain ratio. In order to maintain decomposability, careful adjustment of the amount of PE/PP added should be made. The molding capability will depend on the Melt Flow Rate (MFR), which is one of the important aspects in the plastics industry. Table 1 above was the result of MFR test on sago starch-based degradable plastic using corn cob cellulose fiber and sugarcane bagasse. It can be seen in Table 3 that the degradable plastic with bagasse cellulose fiber has an MFR value that can be measured by its flow speed (melt) with a value obtained of 1.02 ± 0.68 g/10 min at temperature 230 ℃/5kg. While degradable plastic with corn cob cellulose fiber has a value that cannot be measured its flow velocity (melt) because the sample does not melt completely so the measurement was invalid. The addition of cellulose and Polypropylene grafting Maleic Anhydrous (PP-g-MA) blend affected the flow value of the resulting cellulose degradable plastic blend. The MFR values obtained for sugarcane bagasse cellulose-based degradable plastics are comparable to the standard MFR values of polypropylene, which are 1–3 gr/10 min [20].
Our previous research on different type of plastic MFR showed on blends of thermoplastic starch with polypropylene and polyethylene which type of test parameter results (gr/10 min) of thermoplastic starch + polypropylene Melt Flow Rate [230 ℃/2.16 kg] was 10.9 ± 0.1. Meanwhile, thermoplastic starch + polyethylene Melt Flow Rate [190 ℃/2.16 kg] was13.5 ± 0.1 [21]. It can be seen that blending polypropylene and polyethylene materials with thermoplastic starch significantly increases the MFR value of plastics. The MFR value of thermoplastic starch blends with polypropylene/polyethylene is higher than the standard MFR value of polypropylene/polyethylene. This is due to starch particles/granules that have low flow properties that bind to the polymer matrix (PP/PE) with the addition of compatibilizer. The bonding between polyethylene and sago starch occurs because the carboxylic groups on PP/PE and ketones can react with the carboxylic groups of starch to form bonds between these components. Higher MFR values also affect the viscosity of the flow rate during the injection process. The MFR value of pure polypropylene using injection molding generally is 5–20 [230 ℃/5 kg], while the MFR value of polyethylene using injection molding molds is generally 13–25 [190 ℃/5 kg]. If using compression molding, the standard values of polypropylene and polyethylene MFR are 2 [230 ℃/5 kg] and 0.05–0.15 [190 ℃/5 kg] for molds with blow molding, the standard values of MFR of polypropylene and polyethylene are 1–5 [230 ℃/5 kg] dan 1.3–3 [190 ℃/5 kg]. From the MFR values obtained in Table 1, it can be concluded that the most suitable plastic processing technique is injection molding. The addition of thermoplastic starch also tends to decrease the MFR value. Thermoplastic starch serves as an ingredient that can increase the viscosity of the mixture. In determining the MFR value, the viscosity value is also influential. The higher MFR value will affect the viscosity of the flow rate during the injection process [21].
The results of SEM analysis are used to show the morphology of the filler particles in the matrix so that it can be seen that the morphology of the particles in the matrix is evenly or unevenly distributed. This testing process was intended to see the comparison between 2 samples with different types of cellulose fibers. Corn cob and bagasse cellulose-based degradable plastics analyzed by Scanning Electron Microscopy magnification of 100x, 500x and 1000x can be seen in Figures 6 and 7 above. Morphological results are more clearly visible at 1000x magnification. In Figures 6 and 7 parts (a), (b), there are white lumps and indentations on the surface of corn cob cellulose and sugarcane bagasse degradable plastics. In both pictures, there are white lumps and indentations on the surface of corn cob cellulose and sugarcane bagasse degradable plastics. The morphological results show that the sago starch and fiber in the degradable plastic have not been completely dissolved so that they show uneven morphology. The influential factor was stirring because it affects the solubility of sago starch and fiber, the longer the stirring time, the solubility of sago starch and fiber will also be better, while the faster the stirring time will cause the solubility of sago starch and fiber to be poor. The viscosity of the polymer matrix can affect the morphology and density of the plastic. Less viscous starch content cannot retain vapor bubbles as effectively as more viscous starch content [22].
The addition of glycerol affects the physical properties of plastic films. Research by Lopez et al. [23] made corn starch-based thermoplastics using corn husk fibers, stalks and cobs with the addition of glycerol, chitin and chitosan plasticizers so that SEM analysis produced a homogeneous morphology on the surface of the thermoplastic sample. This is due to the addition of glycerol plasticizers resulting in a homogeneous and smooth surface, without pores and cracks. Films with high glycerol content are more homogeneous than those with low glycerol concentration. The SEM results on the degradable plastics could not show the improvement of the material properties in terms of microstructure. properties in terms of microstructure, so further research will be conducted to complete the microstructure of the plane and cross section of the prepared material with different amounts of cellulose addition in order to obtain optimal SEM results on degradable plastics.
Water absorption was done to see the plastic's resistance to water. From Figure 8 (a), (b), it can be seen that the variation of NaOH concentration, the addition of cellulose amount and the type of cellulose used in some variations can increase the water resistance of degradable plastics. Degradable plastic using corn cob fiber has a greater water absorption value of about 6.33–35.84% than using sugarcane bagasse fiber of about 5.01–26.89%. The used of 25% NaOH with a mass of 40% of corn cob cellulose and sugarcane bagasse has a small water absorption with a range of 5–6%. A low percentage of water absorption can inhibit mold growth on the surface of degradable plastics. Since, higher water absorption is a major drawback of cellulose fibers and is also a major cause of degradation in the mechanical performance. Cellulose fibers absorb moisture due to their hydrophilic nature caused by the presence of several H-bonds (-OH groups) between the cell wall macromolecules in the fibers. When the fiber comes into contact with moisture, the H-bond will be broken and the -OH group will form a new H-bond with the water molecule. Thus, it can be concluded that hydrophilic -OH groups were the main source of water absorption in cellulose fibers. Water absorption in cellulose fibers can be overcome by removing these groups. The water absorption of cellulose fibers was successfully overcome by surface modification methods and polymer coating on the fiber surface [24].
The hydrophilic nature is also attributed to the hydroxyl groups of hemicellulose, cellulose, and lignin that are the main constituents of cellulose fibers, which hold water molecules with hydrogen bonds. This fact shows that the chemical composition of cellulose fibers is a major factor for water absorption. Cellulose with different fibers exhibit different water absorption capacity due to variations in their chemical composition [24]. Celia Dolza et al. [25] in their study concluded that the addition of PE-g-MA into wood cellulose-based composite plastics resulted in almost no water absorption with a value of 0.03%. According to them, PE-g-MA contains highly hydrophilic groups that contribute to an increased affinity for water. Several important factors affect the water absorption capacity, such as volume fraction of cellulose fibers, properties of cellulose fibers, type of cellulose fibers, permeability of cellulose fibers, ambient temperature, type of media (different types of media such as humid environment, seawater, rainwater, distilled water, etc. with different pH values), air humidity and strength of the fiber itself [26]. Akil at el was also mentioned some other factors such as surface area exposed to water, polymer viscosity, degree of crosslinking, degree of crystallinity, polarity of molecular structure, diffusivity, surface modification, interfacial bonding between cellulose fibers and polymer [27].
Microorganisms such as bacteria and fungi in the soil cause degradation of degradable plastics after burial. Samples should be buried in soil of known weight for different time intervals, depending on the material and application of the plastic product used. From Tables 2 and 3, it can be seen that the biodegradation results of sago starch-based degradable plastics using corn cob cellulose and sugarcane bagasse decomposed completely within 50–85 days in the soil. The addition of sago starch, cellulose fiber mass and NaOH percent influenced the degradation of degradable plastics. The use of 20% NaOH with 50% corn cob and sugarcane bagasse cellulose mass degraded faster in the span of 50 days. Lignin in cellulose fibers, on the other hand, can inhibit degradation. Lignin can be removed by using several lignin-degrading compounds, one of which is NaOH, which has a significant effect on lignin removal by delignification [28], as has been done in this study at the cellulose extraction stage. Subramanian N. [29] researching degradable plastic from sago starch, there was an improvement in degradation with the use of increasing NaOH concentration, 79% and 74% weight loss of plastics was observed with amylase from sago starch after 3 days. From these degraded results that sago starch contains amylase resistance.
Based on the ASTM 5336 international plastic standard, the biodegradation time takes 60 days to fully degrade PLA plastic from Japan and PLC from the UK. Sago starch-based degradable plastic using corn cob cellulose and sugarcane bagasse in this study can be degraded in accordance with the plastic standards of PLA from Japan and PLC from the UK [30]. Factors such as ingredients used in the polymer, soil moisture or environmental conditions affect degradation rate of plastics [31].
The tensile strength values of corn cob cellulose-based degradable plastics ranged from 11.5–6.37 MPa and bagasse cellulose-based degradable plastics ranged from 16.47–9.70 MPa. The highest elongation test values of degradable plastics were found in 50% cellulose mass with elongation values of 33.70% in corn cob cellulose and 46.92% in bagasse cellulose. The elastic modulus values of corn cob cellulose degradable plastics ranged from 9.366–51.62 MPa and bagasse cellulose starch-based degradable plastics ranged from 24.44–63.34 MPa. The cluster content contained in the FTIR analysis of the two degradable plastics is organic and hydrophilic groups that bind to water so that they are easily degraded by soil. From the TGA results, the degradable plastics have good thermal stability. The results of DSC analysis, the Tm values obtained in both degradable plastics occurred endothermic peaks in the glass transition state. MFR analysis results of sago starch-based degradable plastics using bagasse fiber + PP-g-MA, the most suitable plastic processing technique is injection molding. While the sago starch-based degradable plastic using corn cob fiber + PP-g-MA needs further research to get the optimal MFR value. SEM analysis of the degradable plastic showed white lumps and indentations on the surface of the plastic. The use of 25% NaOH with a mass of corn cob cellulose and bagasse 40% has a small water absorption with a range of 5–6%. The cellulose-based degradable plastic in this study was completely degraded at 50 days.
The authors declare they have not used Artificial Intelligence (AI) tools in the creation of this article.
This research was funded by Funds Non-Tax State Revenue (PNBP) in the Budget Implementation List (DIPA) Malikussaleh University Academic Year of 2023. This research was done at Chemical Engineering Laboratory, Engineering Faculty, Universitas Malikussaleh, Aceh, Indonesia.
The authors declare no conflict of interest.
[1] |
Robert Adhitama, Jesica Viona Setiawan, Mangihot Tua Goeltom, et al. (2023) Utilization of breadfruit (artocarpus altilis) peel waste and blood clam shell waste (anadara granosa) as raw materials for glycerol-plasticized degradable bioplastic production. Indonesian J Biotechnol Biodivers 1: 12–21. https://doi.org/10.47007/ijobb.v7i1.167. doi: 10.47007/ijobb.v7i1.167
![]() |
[2] |
Denny Akbar Tanjung, Novesar Jamarun, Syukri Arief, et al. (2022) Influence of LLDPE-g-MA on mechanical properties, degradation performance, and water absorption of thermoplastic sago starch blends. Indones J Chem 1: 171–178. https://doi.org/10.22146/ijc.68558. doi: 10.22146/ijc.68558
![]() |
[3] |
K J Falua, A Fokharel, A Babaei-Ghazvini, et al. (2022) Valorization of starch to biobased materials: a review. Polymers 14: 2215. https://doi.org/10.3390/polym14112215. doi: 10.3390/polym14112215
![]() |
[4] | E R M Saleh, K A Rakhman, S Samad (2022) Synthesis of biofoam from sago waste as a biodegradable food storage candidate. In First Asian PGPR Indonesian Chapter International eConference 2021, KnE Life Science 162–169. https://doi.org/10.18502/kls.v7i3.11117. |
[5] | R Alebooyeh, A Mohammadi Nafchi, M Jokar (2012) The Effects of ZnOnanorodson the Characteristics of Sago Starch Biodegradable Films. J Chem Health Risks 2: 13–16. |
[6] |
Hiba Shaghaleh, Xu Xu, Shifa Wang (2018) Current progress in production of biopolymeric materials based on cellulose, cellulose nanofibers, and cellulose derivatives. Roy Soc Chem RSC Adv 8: 825–842. https://doi.org/10.1039/C7RA11157F. doi: 10.1039/C7RA11157F
![]() |
[7] |
Binling Ai, Lili Zheng, Wenqi Li, et al. (2021) Biodegradable Cellulose Film Prepared From Banana Pseudo-Stem Using an Ionic Liquid for Mango Preservation Binling. Front Plant Sci 12: 625878. https://doi.org/10.3389/fpls.2021.625878. doi: 10.3389/fpls.2021.625878
![]() |
[8] |
Naresh Shahi, Byungjin Min, Bedanga Sapkota, et al. (2020) Rangari, Eco-Friendly Cellulose Nanofiber Extraction from Sugarcane Bagasse and Film Fabrication. Sustainability 12: 6015. https://doi.org/10.3390/su12156015. doi: 10.3390/su12156015
![]() |
[9] |
Alokika, Anu, Anil Kumar, Vinod Kumar, et al. (2021) Cellulosic and hemicellulosic fractions of sugarcane bagasse: Potential, challenges and future perspective. Int J Biol Macromol 169: 564–582. https://doi.org/10.1016/j.ijbiomac.2020.12.175. doi: 10.1016/j.ijbiomac.2020.12.175
![]() |
[10] | Jiarong Tian, Shaoping Qian, Zhaoyan Zhang et al. (2023) A facile approach for preparing nanofibrillated cellulose from bleached corn stalk with tailored surface functions. Cellulose 30: 5641–5656. |
[11] |
Yingqi Kong, Shaoping Qian, Zhaoyan Zhang, et al. (2023) The impact of esterified nanofibrillated cellulose content on the properties of thermoplastic starch/PBAT biocomposite films through ball-milling. Int J Biol Macromol 253: 127462. https://doi.org/10.1016/j.ijbiomac.2023.127462 doi: 10.1016/j.ijbiomac.2023.127462
![]() |
[12] |
Alper Aksit, Teresa Menzel, Merve Aksit, et al. (2020) Properties of Styrene–Maleic Anhydride Copolymer Compatibilized Polyamide 66/Poly (Phenylene Ether) Blends: Effect of Maleic Anhydride Concentration and Copolymer Content. Materials 13: 1237. https://doi.org/10.3390/ma13051237. doi: 10.3390/ma13051237
![]() |
[13] |
Nor Izaida Ibrahim, Farah Syazwani Shahar, Mohamed Thariq Hameed Sultan, et al. (2021) Overview of Bioplastic Introduction and Its Applications in Product Packaging. Coatings 11: 1423. https://doi.org/10.3390/coatings11111423. doi: 10.3390/coatings11111423
![]() |
[14] | Waryat., M. Romli., A. Suryani., et al. (2013) Using of a Compatibilizer to Improve Morphological, Physical and Mechanical Properties of Biodegradable Plastic From Thermoplastic Starch/LLDPE Blends. Indones J Mater Sci 3: 214 – 221. |
[15] |
Shiou Xuan Tan, Andri Andriyana, Hwai Chyuan Ong, et al. (2022) A Comprehensive Review on the Emerging Roles of Nanofillers and Plasticizers towards Sustainable Starch-Based Bioplastic Fabrication. Polymers 14: 664. https://doi.org/10.3390/polym14040664. doi: 10.3390/polym14040664
![]() |
[16] | Zheng Cao, Ying Lu, Cheng Zhang, et al. (2017) Effects of the chain-extender content on the structure and performance of poly (lactic acid)–poly (butylene succinate)–microcrystalline cellulose composites. J Appl Polym Sci 22: 44895. |
[17] |
Pooja Saxena, Prashant Shukla, MS Gaur (2021) Thermal analysis of polymer blends and double layer by DSC. Sage J Polym Polym Compos 29: 9. https://doi.org/10.1177/0967391120984606. doi: 10.1177/0967391120984606
![]() |
[18] |
Chunhua Lou, Siyu Jiang, An Yan, et al. (2022) Self-extracted corn-stalk cellulose/epoxy resin composites. Sci Rep 12: 20968. https://doi.org/10.1038/s41598-022-25695-0. doi: 10.1038/s41598-022-25695-0
![]() |
[19] | Gadaleta G, De Gisi S, Chong ZK, et al. (2023) Degradation of thermoplastic cellulose acetate-based bioplastics by full-scale experimentation of industrial anaerobic digestion and composting. Chem Eng J 462: 142301. |
[20] | K Hamad, M Kaseem, F Deri (2011) Melt Rheology of Poly (Lactic Acid)/Low Density Polyethylene Polymer Blends. Adv Chem Eng 1: 208–214. |
[21] |
Rozanna Dewi, Novi Sylvia, Zulnazri, et al. (2023) Melt flow Index (MFI) analysis of sago based thermoplastic starch blend with polypropylene and polyethylene. Mater Today 87: 2214–7853. https://doi.org/10.1016/j.matpr.2023.04.173. doi: 10.1016/j.matpr.2023.04.173
![]() |
[22] | J. B. Engel, A. Ambrosi, I. C. Tessaro (2019) Development of biodegrdable starch-based foams incorporated with grape stalks for food packaging. Carbohydr Polym 225, 115234. |
[23] | Lopez, O, Garcia, M.A, Villar, M.A, Gentili, A, Rodriguez, M.S, Albertengo, L (2014) Thermo-compression of biodegradable thermoplastic corn starch films containing chitin and chitosan. LWT-Food Sci Technol 57: 106–115. |
[24] |
Parul Sahu, MK Gupta (2022) Water absorption behavior of cellulosic fibres polymer composites: A review on its effects and remedies. J Ind Text 51: 7480S–7512S. https://doi.org/10.1177/1528083720974424. doi: 10.1177/1528083720974424
![]() |
[25] | Celia Dolza, Eduardo Fages, Eloi Gonga, et al. (2021) Development and Characterization of Environmentally Friendly Wood Plastic Composites from Biobased Polyethylene and Short Natural Fibers Processed by Injection Moulding. Polymers 131692. https://doi.org/10.3390/polym13111692. |
[26] | Akil HM, Santulli C, Sarasini F, et al. (2014) Environmental effects on the mechanical behaviour of pultruded jute/glass fibre-reinforced polyester hybrid composites. Composite Sci Technol 94: 62–70. |
[27] | Azwa ZN, Yousif BF, Manalo AC, et al. (2013) A review on the degradability of polymeric composites based on natural fibres. Material Des 47: 424–442. |
[28] |
Jung W, Savithri D, Sharma-Shivappa R, et al. (2020) Effect of Sodium Hydroxide Pretreatment on Lignin Monomeric Components of Miscanthus×giganteus and Enzymatic Hydrolysis. Waste Biomass Valor 11: 5891–5900. https://doi.org/10.1007/s12649-019-00859-8. doi: 10.1007/s12649-019-00859-8
![]() |
[29] | Subramanian N (2021) Biodegradable Plastic From Mixed Starch. Int J Mech Eng 3: 1009–1020. |
[30] |
Averous L (2004) Biodegradable multiphase systems based on plasticized starch: A review. J Macromol Sci–Polymer Reviews 3: 231–274. https://doi.org/10.1081/MC-200029326. doi: 10.1081/MC-200029326
![]() |
[31] |
Gerardo Coppola, Maria Teresa Gaudio, Catia Giovanna Lopresto, et al. (2021) Bioplastic from Renewable Biomass: A Facile Solution for a Greener Environment. Earth Syst Environ 5: 231–251. https://doi.org/10.1007/s41748-021-00208-7 doi: 10.1007/s41748-021-00208-7
![]() |
1. | Rozanna Dewi, Novi Sylvia, Zulnazri Zulnazri, Herman Fithra, Medyan Riza, Januar Parlaungan Siregar, Tezara Cionita, Deni Fajar Fitriyana, Samsudin Anis, The Optimization of Avocado-Seed-Starch-Based Degradable Plastic Synthesis with a Polylactic Acid (PLA) Blend Using Response Surface Methodology (RSM), 2024, 16, 2073-4360, 2384, 10.3390/polym16162384 | |
2. | Rozanna Dewi, Novi Sylvia, Medyan Riza, 2025, Effect of Polylactic Acid (PLA) as Reinforcement for Jackfruit Seed Starch-Based Degradable Plastic, 14, 10.3390/engproc2025084014 |
Sample Name | MFR [g/10 menit] |
Corn cob cellulose-based degradable plastics | Not measured (the sample did not melt completely so the measurement is invalid) |
Sugarcane bagasse cellulose-based degradable plastics | 1.02 ± 0.68 |
Days | Cellulose Mass (%) | ||||||||
NaOH 20% | NaOH 25% | NaOH 30% | |||||||
40 | 50 | 60 | 40 | 50 | 60 | 40 | 50 | 60 | |
3 | 0.35 | 0.68 | 0.43 | 0.17 | 0.21 | 0.20 | 0.21 | 0.28 | 0.23 |
6 | 3.26 | 3.89 | 3.78 | 1.78 | 2.61 | 1.60 | 1.99 | 2.86 | 2.67 |
9 | 12.09 | 13.63 | 12.55 | 7.20 | 9.93 | 8.70 | 9.95 | 10.57 | 11.52 |
12 | 18.49 | 21.32 | 20.94 | 13.76 | 15.10 | 13.67 | 15.47 | 18.52 | 17.16 |
16 | 25.06 | 27.9 | 26.94 | 19.19 | 23.68 | 20.7 | 22.48 | 25.58 | 24.21 |
18 | 29.58 | 33.17 | 32.15 | 22.18 | 26.71 | 23.60 | 25.98 | 29.77 | 28.31 |
21 | 35.62 | 39.88 | 38.70 | 26.88 | 32.30 | 28.59 | 31.42 | 35.98 | 34.16 |
24 | 41.67 | 46.60 | 45.25 | 31.57 | 37.89 | 33.58 | 36.87 | 42.19 | 40.00 |
27 | 47.72 | 53.31 | 51.81 | 36.26 | 43.49 | 38.57 | 42.31 | 48.40 | 45.85 |
30 | 53.76 | 60.02 | 58.36 | 40.96 | 49.08 | 43.56 | 47.75 | 54.61 | 51.70 |
33 | 59.81 | 66.73 | 64.91 | 45.65 | 54.67 | 48.54 | 53.20 | 60.82 | 57.55 |
36 | 65.85 | 73.45 | 71.47 | 50.34 | 60.27 | 53.53 | 58.64 | 67.03 | 63.40 |
39 | 71.90 | 80.16 | 78.02 | 55.04 | 65.86 | 58.52 | 64.08 | 73.24 | 69.24 |
42 | 77.94 | 86.87 | 84.57 | 59.73 | 71.45 | 63.51 | 69.53 | 79.45 | 75.09 |
45 | 83.99 | 93.59 | 91.12 | 64.42 | 77.05 | 68.50 | 74.97 | 85.66 | 80.94 |
48 | 90.04 | 100 | 97.68 | 69.12 | 82.64 | 73.49 | 80.41 | 91.87 | 86.79 |
51 | 96.08 | - | 100 | 73.81 | 88.23 | 78.47 | 85.86 | 98.08 | 92.64 |
54 | 100 | - | - | 78.50 | 93.83 | 83.46 | 91.30 | 100 | 98.49 |
57 | - | - | - | 83.20 | 99.42 | 88.45 | 96.74 | - | 100 |
60 | - | - | - | 87.89 | 100 | 93.44 | 100 | - | - |
63 | - | - | - | 92.59 | - | 98.43 | - | - | - |
66 | - | - | - | 97.28 | - | 100 | - | - | - |
69 | - | - | - | 100 | - | - | - | - | - |
Days | Cellulose Mass (%) | ||||||||
NaOH 20% | NaOH 25% | NaOH 30% | |||||||
40 | 50 | 60 | 40 | 50 | 60 | 40 | 50 | 60 | |
3 | 0.73 | 0.81 | 0.84 | 0.34 | 0.38 | 0.46 | 0.45 | 0.58 | 0.64 |
6 | 1.96 | 1.80 | 2.55 | 0.89 | 1.00 | 1.34 | 1.45 | 1.70 | 2.08 |
9 | 6.01 | 7.94 | 8.95 | 5.40 | 5.95 | 6.18 | 5.53 | 6.26 | 7.82 |
12 | 15.52 | 16.97 | 17.60 | 10.22 | 11.00 | 12.58 | 13.09 | 15.11 | 16.18 |
15 | 26.23 | 27.37 | 28.32 | 15.02 | 15.89 | 16.36 | 20.61 | 21.08 | 24.70 |
18 | 28.05 | 29.91 | 27.32 | 17.05 | 18.15 | 19.20 | 22.62 | 23.95 | 27.49 |
21 | 34.17 | 36.37 | 32.99 | 20.68 | 22.00 | 23.23 | 27.54 | 29.07 | 33.36 |
24 | 40.29 | 42.83 | 38.65 | 24.32 | 25.86 | 27.26 | 32.45 | 34.19 | 39.23 |
27 | 46.42 | 49.29 | 44.32 | 27.96 | 29.71 | 31.29 | 37.36 | 39.31 | 45.10 |
30 | 52.54 | 55.74 | 49.99 | 31.60 | 33.57 | 35.32 | 42.27 | 44.42 | 50.96 |
33 | 58.66 | 62.20 | 55.66 | 35.24 | 37.42 | 39.35 | 47.18 | 39.31 | 56.83 |
36 | 64.79 | 68.66 | 61.32 | 38.88 | 41.28 | 43.38 | 52.09 | 44.42 | 62.70 |
39 | 70.91 | 75.11 | 66.99 | 42.52 | 45.14 | 47.41 | 57.00 | 49.54 | 68.57 |
42 | 77.03 | 81.57 | 72.66 | 46.16 | 48.99 | 51.44 | 61.91 | 54.66 | 74.44 |
45 | 83.16 | 88.03 | 78.33 | 49.80 | 52.85 | 55.47 | 66.82 | 59.78 | 80.30 |
48 | 89.28 | 95.49 | 84.00 | 53.44 | 56.70 | 59.50 | 71.73 | 64.89 | 86.17 |
51 | 95.40 | 100 | 89.66 | 57.08 | 60.56 | 63.53 | 76.64 | 70.01 | 92.04 |
54 | 100 | - | 95.33 | 60.72 | 64.41 | 67.56 | 81.55 | 75.13 | 97.91 |
57 | - | - | 100 | 64.36 | 68.27 | 71.59 | 86.46 | 80.25 | 100 |
60 | - | - | - | 68.00 | 72.12 | 75.62 | 91.37 | 95.60 | - |
63 | - | - | - | 71.64 | 75.98 | 79.65 | 96.28 | 100 | - |
66 | - | - | - | 75.28 | 79.83 | 83.68 | 100 | - | - |
69 | - | - | - | 78.92 | 83.68 | 87.71 | - | - | - |
72 | - | - | - | 82.56 | 87.54 | 91.74 | - | - | - |
75 | - | - | - | 86.20 | 91.40 | 95.77 | - | - | - |
78 | - | - | - | 89.84 | 95.25 | 99.80 | - | - | - |
81 84 |
- - |
- - |
- - |
93.48 97.12 |
99.11 100 |
100 - |
- - |
- - |
- - |
Sample Name | MFR [g/10 menit] |
Corn cob cellulose-based degradable plastics | Not measured (the sample did not melt completely so the measurement is invalid) |
Sugarcane bagasse cellulose-based degradable plastics | 1.02 ± 0.68 |
Days | Cellulose Mass (%) | ||||||||
NaOH 20% | NaOH 25% | NaOH 30% | |||||||
40 | 50 | 60 | 40 | 50 | 60 | 40 | 50 | 60 | |
3 | 0.35 | 0.68 | 0.43 | 0.17 | 0.21 | 0.20 | 0.21 | 0.28 | 0.23 |
6 | 3.26 | 3.89 | 3.78 | 1.78 | 2.61 | 1.60 | 1.99 | 2.86 | 2.67 |
9 | 12.09 | 13.63 | 12.55 | 7.20 | 9.93 | 8.70 | 9.95 | 10.57 | 11.52 |
12 | 18.49 | 21.32 | 20.94 | 13.76 | 15.10 | 13.67 | 15.47 | 18.52 | 17.16 |
16 | 25.06 | 27.9 | 26.94 | 19.19 | 23.68 | 20.7 | 22.48 | 25.58 | 24.21 |
18 | 29.58 | 33.17 | 32.15 | 22.18 | 26.71 | 23.60 | 25.98 | 29.77 | 28.31 |
21 | 35.62 | 39.88 | 38.70 | 26.88 | 32.30 | 28.59 | 31.42 | 35.98 | 34.16 |
24 | 41.67 | 46.60 | 45.25 | 31.57 | 37.89 | 33.58 | 36.87 | 42.19 | 40.00 |
27 | 47.72 | 53.31 | 51.81 | 36.26 | 43.49 | 38.57 | 42.31 | 48.40 | 45.85 |
30 | 53.76 | 60.02 | 58.36 | 40.96 | 49.08 | 43.56 | 47.75 | 54.61 | 51.70 |
33 | 59.81 | 66.73 | 64.91 | 45.65 | 54.67 | 48.54 | 53.20 | 60.82 | 57.55 |
36 | 65.85 | 73.45 | 71.47 | 50.34 | 60.27 | 53.53 | 58.64 | 67.03 | 63.40 |
39 | 71.90 | 80.16 | 78.02 | 55.04 | 65.86 | 58.52 | 64.08 | 73.24 | 69.24 |
42 | 77.94 | 86.87 | 84.57 | 59.73 | 71.45 | 63.51 | 69.53 | 79.45 | 75.09 |
45 | 83.99 | 93.59 | 91.12 | 64.42 | 77.05 | 68.50 | 74.97 | 85.66 | 80.94 |
48 | 90.04 | 100 | 97.68 | 69.12 | 82.64 | 73.49 | 80.41 | 91.87 | 86.79 |
51 | 96.08 | - | 100 | 73.81 | 88.23 | 78.47 | 85.86 | 98.08 | 92.64 |
54 | 100 | - | - | 78.50 | 93.83 | 83.46 | 91.30 | 100 | 98.49 |
57 | - | - | - | 83.20 | 99.42 | 88.45 | 96.74 | - | 100 |
60 | - | - | - | 87.89 | 100 | 93.44 | 100 | - | - |
63 | - | - | - | 92.59 | - | 98.43 | - | - | - |
66 | - | - | - | 97.28 | - | 100 | - | - | - |
69 | - | - | - | 100 | - | - | - | - | - |
Days | Cellulose Mass (%) | ||||||||
NaOH 20% | NaOH 25% | NaOH 30% | |||||||
40 | 50 | 60 | 40 | 50 | 60 | 40 | 50 | 60 | |
3 | 0.73 | 0.81 | 0.84 | 0.34 | 0.38 | 0.46 | 0.45 | 0.58 | 0.64 |
6 | 1.96 | 1.80 | 2.55 | 0.89 | 1.00 | 1.34 | 1.45 | 1.70 | 2.08 |
9 | 6.01 | 7.94 | 8.95 | 5.40 | 5.95 | 6.18 | 5.53 | 6.26 | 7.82 |
12 | 15.52 | 16.97 | 17.60 | 10.22 | 11.00 | 12.58 | 13.09 | 15.11 | 16.18 |
15 | 26.23 | 27.37 | 28.32 | 15.02 | 15.89 | 16.36 | 20.61 | 21.08 | 24.70 |
18 | 28.05 | 29.91 | 27.32 | 17.05 | 18.15 | 19.20 | 22.62 | 23.95 | 27.49 |
21 | 34.17 | 36.37 | 32.99 | 20.68 | 22.00 | 23.23 | 27.54 | 29.07 | 33.36 |
24 | 40.29 | 42.83 | 38.65 | 24.32 | 25.86 | 27.26 | 32.45 | 34.19 | 39.23 |
27 | 46.42 | 49.29 | 44.32 | 27.96 | 29.71 | 31.29 | 37.36 | 39.31 | 45.10 |
30 | 52.54 | 55.74 | 49.99 | 31.60 | 33.57 | 35.32 | 42.27 | 44.42 | 50.96 |
33 | 58.66 | 62.20 | 55.66 | 35.24 | 37.42 | 39.35 | 47.18 | 39.31 | 56.83 |
36 | 64.79 | 68.66 | 61.32 | 38.88 | 41.28 | 43.38 | 52.09 | 44.42 | 62.70 |
39 | 70.91 | 75.11 | 66.99 | 42.52 | 45.14 | 47.41 | 57.00 | 49.54 | 68.57 |
42 | 77.03 | 81.57 | 72.66 | 46.16 | 48.99 | 51.44 | 61.91 | 54.66 | 74.44 |
45 | 83.16 | 88.03 | 78.33 | 49.80 | 52.85 | 55.47 | 66.82 | 59.78 | 80.30 |
48 | 89.28 | 95.49 | 84.00 | 53.44 | 56.70 | 59.50 | 71.73 | 64.89 | 86.17 |
51 | 95.40 | 100 | 89.66 | 57.08 | 60.56 | 63.53 | 76.64 | 70.01 | 92.04 |
54 | 100 | - | 95.33 | 60.72 | 64.41 | 67.56 | 81.55 | 75.13 | 97.91 |
57 | - | - | 100 | 64.36 | 68.27 | 71.59 | 86.46 | 80.25 | 100 |
60 | - | - | - | 68.00 | 72.12 | 75.62 | 91.37 | 95.60 | - |
63 | - | - | - | 71.64 | 75.98 | 79.65 | 96.28 | 100 | - |
66 | - | - | - | 75.28 | 79.83 | 83.68 | 100 | - | - |
69 | - | - | - | 78.92 | 83.68 | 87.71 | - | - | - |
72 | - | - | - | 82.56 | 87.54 | 91.74 | - | - | - |
75 | - | - | - | 86.20 | 91.40 | 95.77 | - | - | - |
78 | - | - | - | 89.84 | 95.25 | 99.80 | - | - | - |
81 84 |
- - |
- - |
- - |
93.48 97.12 |
99.11 100 |
100 - |
- - |
- - |
- - |