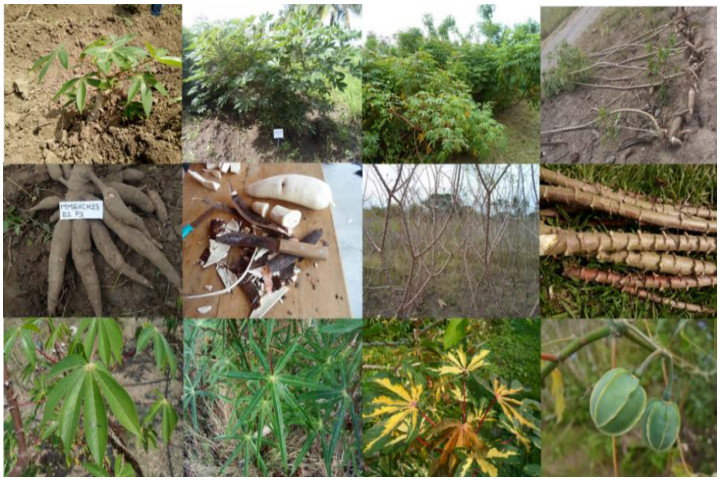
Cassava (Manihot esculenta Crantz) has garnered global attention due to its importance as a crucial raw material for ethanol and other derivative production. Nonetheless, its agroindustry generates a substantial amount of residues. We examined the potential utilization of co–products from both agricultural and industrial sectors concerning starch extraction processes. A total of 319 million tons of fresh cassava roots are globally produced, yielding up to 55% of agricultural co–products during harvesting. For every ton of starch extracted, 2.5 tons of bagasse, along with 100 to 300 kg of peel per ton of fresh processed cassava, and 17.4 m3 of residual liquid tributaries are generated. Consequently, both solid agricultural biomass and solid/liquid residues could be directed towards cogenerating bioenergy such as bioethanol, biobutanol, biodiesel, bio–oil, charcoal, and other bioproducts. In conclusion, the conversion of cassava agroindustrial co–products into food and non–food products with high added value could be promoted, thus fostering a circular economy to enhance profitability, sustainability, and crop promotion.
Citation: Pablo Andrés–Meza, Noé Aguilar–Rivera, Isaac Meneses–Márquez, José Luis Del Rosario–Arellano, Gloria Ivette Bolio–López, Otto Raúl Leyva–Ovalle. Cassava cultivation; current and potential use of agroindustrial co–products[J]. AIMS Environmental Science, 2024, 11(2): 248-278. doi: 10.3934/environsci.2024012
[1] | Bijoy Kumar Shaw, Isha Sangal, Biswajit Sarkar . Reduction of greenhouse gas emissions in an imperfect production process under breakdown consideration. AIMS Environmental Science, 2022, 9(5): 658-691. doi: 10.3934/environsci.2022038 |
[2] | Alaa E. Al-Ahmad, Stéphanie D. Lambert, Julien G. Mahy, Benoît Heinrichs, Wissal Wannoussa, Ludivine Tasseroul, Frédéric Weekers, Philippe Thonart, Serge Hiligsmann . Investigation of the potential effect of encapsulated metal nanoparticles on enhancement of thermophilic anaerobic digestion. AIMS Environmental Science, 2023, 10(6): 764-793. doi: 10.3934/environsci.2023042 |
[3] | Jennifer K. Costanza, Robert C. Abt, Alexa J. McKerrow, Jaime A. Collazo . Linking state-and-transition simulation and timber supply models for forest biomass production scenarios. AIMS Environmental Science, 2015, 2(2): 180-202. doi: 10.3934/environsci.2015.2.180 |
[4] | Anna Lymperatou, Ioannis V. Skiadas, Hariklia N. Gavala . Anaerobic co-digestion of swine manure and crude glycerol derived from animal fat—Effect of hydraulic retention time. AIMS Environmental Science, 2018, 5(2): 105-116. doi: 10.3934/environsci.2018.2.105 |
[5] | Dominic Bowd, Campbell McKay, Wendy S. Shaw . Urban greening: environmentalism or marketable aesthetics. AIMS Environmental Science, 2015, 2(4): 935-949. doi: 10.3934/environsci.2015.4.935 |
[6] | Soumya Kanti Hota, Santanu Kumar Ghosh, Biswajit Sarkar . A solution to the transportation hazard problem in a supply chain with an unreliable manufacturer. AIMS Environmental Science, 2022, 9(3): 354-380. doi: 10.3934/environsci.2022023 |
[7] | Goshu Desalegn, Anita Tangl, Maria Fekete-Farkas . Greening through taxation: assessing the potential opportunities and challenges of plastic products in Ethiopia. AIMS Environmental Science, 2022, 9(4): 432-443. doi: 10.3934/environsci.2022026 |
[8] | Raj Kumar Bachar, Shaktipada Bhuniya, Santanu Kumar Ghosh, Biswajit Sarkar . Sustainable green production model considering variable demand, partial outsourcing, and rework. AIMS Environmental Science, 2022, 9(3): 325-353. doi: 10.3934/environsci.2022022 |
[9] | Wen-Hung Lin, Kuo-Hua Lee, Liang-Tu Chen . The effects of Ganoderma lucidum compound on goat weight and anti-inflammatory: a case study of circular agriculture. AIMS Environmental Science, 2021, 8(6): 553-566. doi: 10.3934/environsci.2021035 |
[10] | R. Kajaste, P. Oinas . Plastics value chain - Abatement of greenhouse gas emissions. AIMS Environmental Science, 2021, 8(4): 371-392. doi: 10.3934/environsci.2021024 |
Cassava (Manihot esculenta Crantz) has garnered global attention due to its importance as a crucial raw material for ethanol and other derivative production. Nonetheless, its agroindustry generates a substantial amount of residues. We examined the potential utilization of co–products from both agricultural and industrial sectors concerning starch extraction processes. A total of 319 million tons of fresh cassava roots are globally produced, yielding up to 55% of agricultural co–products during harvesting. For every ton of starch extracted, 2.5 tons of bagasse, along with 100 to 300 kg of peel per ton of fresh processed cassava, and 17.4 m3 of residual liquid tributaries are generated. Consequently, both solid agricultural biomass and solid/liquid residues could be directed towards cogenerating bioenergy such as bioethanol, biobutanol, biodiesel, bio–oil, charcoal, and other bioproducts. In conclusion, the conversion of cassava agroindustrial co–products into food and non–food products with high added value could be promoted, thus fostering a circular economy to enhance profitability, sustainability, and crop promotion.
Cassava cultivation is primarily distributed in tropical and subtropical regions, typically within the geographical range of up to 30° parallels [1]. Its starch–rich tuberous root serves as a staple for over 800 million low–income individuals, positioning it as the fifth most significant energy crop following maize, rice, wheat, and potato [2]. Furthermore, cassava cultivation contributes to employment generation, while its trade serves as a crucial source of economic income [3,4]. From an agronomic perspective, farmers favor this starchy crop due to its minimal input requirements, attributed to its wide adaptability to various soil and climate conditions, including drought tolerance and resilience in marginal soils [5]. Hence, cassava is cultivated across approximately 29.95 million hectares, predominantly in the African continent (60.9%), followed by Asia (29.4%) and America (9.6%), with a total production exceeding 319 million tons of fresh roots [6].
The cassava harvest highlights two key aspects: First, a substantial amount of biomass remains in the field, including stems and leaves, with proportions typically around 44% and 6%, respectively [7]; and second, solid (bagasse and peel) and liquid (wastewater) co–products from the starch extraction industry are prevalent and widely utilized [8] due to their application as raw materials for high–value food and non–food industrial processes [2]. Despite lignocellulosic solid co–products being historically utilized for biofertilizer [9], and for heat and power cogeneration within the cassava agroindustry [10], these agricultural residues are undervalued. There exists a significant opportunity to integrate them into the biorefinery and circular bioeconomy model, enabling the efficient utilization of biomass by harnessing its potential for multiple bioenergy benefits and bioproducts, thereby advancing sustainability; a focal point of contemporary green technology [11].
While cassava has been promoted for renewable energies generation, such as first–generation bioethanol, as realized in China [12], it has also been suggested that in Brazil, cassava bagasse could substitute up to 24% of sugarcane ethanol [13]. However, not only cassava bagasse but also stems, rhizomes, leaves, and peel can be utilized for this purpose. Moreover, they can be employed in the production of various other bioenergy sources, including biobutanol, biodiesel, bio–oil, biohydrogen, and biochar [14,15,16,17,18,19]. The utilization of lignocellulosic co–products has gained traction in the energy sector [20] due to rising fossil fuel prices and environmental concerns related to emissions of pollutant gases, biodiversity loss, monocultures, and land–use changes. Consequently, bioconversion could yield not only economic benefits but also social and environmental advantages.
Furthermore, agroindustrial co–products from cassava have been proposed for synthesizing various food and non–food bioproducts, particularly in the health sector [21]. For instance, they could be utilized in the development of prebiotics such as xylooligosaccharides [22], exopolymeric substances [23], and the identification of active components with antioxidant, anti–inflammatory, and immune–enhancing properties [21,24,25]. Additionally, there is potential for producing biomaterials for heavy metal removal, dye absorption in contaminated waters [26,27,28], and even bioplastics production [29,30], while also offering a wide range of biochemicals. Interestingly, considering a cassava biorefinery approach could increase the economic value of co–products, strengthen the value chain, and, most importantly, contribute to sustainable production by addressing environmental and social challenges.
Cassava (Figure 1) is among the 100 species of trees, shrubs, and perennial herbs within the genus Manihot, originating from the Americas [31], with distribution primarily in tropical and subtropical regions worldwide, particularly in developing countries [1]. The southern Brazilian Amazon has been identified as the center of origin of cassava, supported by geographic, molecular, and DNA studies indicating Manihot esculenta ssp. Flabellifolia (Pohl) is the wild progenitor species [32,33,34,35]. Domestication likely occurred in this same area, estimated to have taken place between 6 500 to 5 500 BC [36], as well as in the Cerrado savanna ecoregion [37,38,39], and the region known as Mesoamerica [40,41].
Reportedly, at the time of European contact in the 16th century, cassava constituted part of the diet in the lowlands of the Neotropics [42,43]. During this historical event, Portuguese colonizers transported it across the Atlantic Ocean from Brazil to the Congo in Africa. Two hundred years later, it was cultivated in the west and center of the continent and then spread eastward to Mozambique, Kenya, Madagascar, and Zanzibar [44,45,46]. By the 18th and 19th centuries, the species had become established in the south and southeast regions of Asia [47]. Consequently, it is known by a great variety of names: In English–speaking countries, it is called cassava, caxamote, farinha, guacamote, huacamote, mañoco; in Brazil, it is known as aipim, macaxeira, mandioca, and mandiya; in Africa, it is referred to as maniok; and in China, it can be called mu shu, shu ge, and shu shu [48].
Cassava is produced in 103 countries (Figure 2), distributed across Africa (60.9%), Asia (29.4%), and the Americas (9.6%). In 2021, a production of 319 million tons of fresh roots was reported, mostly concentrated in Nigeria, the Democratic Republic of Congo, Thailand, Ghana, Brazil, and Indonesia. Although the world average is 13.02 t ha-1, there is wide variation (ranging from 0.99 to 43.07 t ha-1), among which stand out Guyana (43.07 t ha-1), India (37.93 t ha-1), Zambia (35.54 t ha-1), Laos (32.10 t ha-1), Niger (29.02 t ha-1), St. Vincent and the Grenadines (28.30 t ha-1), Cambodia (27.41 t ha-1), and Indonesia (26.6 t ha-1) [6]. An upward trend in production has been observed compared to the initial reports of commercialization in the 1960s until 2021 (Figure 3), which is explained by the increase in planted area, yield, versatility of use in bioproducts, and government policies promoting cultivation and integrated processing [49].
In this regard, there has been an upward trend in production when comparing the initial marketing reports from the 1960s to the year 2022 (Figure 3). This trend can be attributed to the expansion of cultivated areas, improvements in yield, and government policies aimed at promoting cultivation. For example, Nigeria, the leading global producer of cassava, has experienced a 4.3% annual production increase since the 1990s, largely due to government agricultural programs [50,51]. Similarly, countries like Thailand, Cambodia, Vietnam [52], and Laos have expanded cassava cultivation to meet the demand of the Chinese market, which imports 80% of international cassava trade in various forms including fresh, chilled, frozen, chopped, pellets, or starch [2,53]. Vietnam, for instance, witnessed a 238% increase in planted area (from 237 600 ha in 2000 to 547 883 ha in 2017), accompanied by a yield intensification from 8.4 to 18.83 t ha-1 [54]. However, a slowdown in cassava growth in 2016 was possibly due to the reserve use and technological advancements in maize cultivation in China, leading to reduced utilization of cassava for bioethanol production [12], and other derived products like animal feed and processed food. Consequently, this resulted in the abandonment of cassava cultivation in major exporting countries [2]. Moreover, its commercialization declined during the COVID–19 pandemic, as regions dependent on cassava redirected it for household consumption, with the remaining produce directed towards local sales to generate economic resources [55].
Cassava is typically harvested between 10 to 12 months after planting (MAP) to be available as food [56]. This timeframe coincides with a higher yield of tuber roots, dry matter, and starch [57], as well as lower fiber content [58]. However, it can be harvested between 8 to 24 MAP [59]. Additionally, in the areas of cultivation, cassava production generates employment [4], and the sale of tubers (Figure 4) serves as an income source [3].
Worldwide, approximately 800 million people rely on cassava to meet their food needs [60], with reported average intakes of up to 19.8 kg per year. Consequently, it is considered the fifth most important energy crop after maize, rice, wheat, and potato [2]. This is due to its richness in carbohydrates, primarily starch, although it also contains vitamins and minerals (Table 1). Despite its low protein content, it contains 2.79% mainly unsaturated fatty acids and is a rich source of potassium. Notably, it contains polyphenols and flavonoids (31.95 and 0.85 g per 100 g-1, respectively), as well as superoxide dismutase and DPPH radical scavenger activity. Additionally, it can inhibit α-glucosidase and α-amylase, with values of 69.02% and 36.30%, respectively, which, coupled with its antioxidant capacity, may positively affect its anti–diabetic activity [61].
Item % | Tuberous root | Leaves | |||
Fresh | Dried | Fresh | Sundried whole | Dried milled | |
Protein | 0.01–1.45 | 1.89–2.21 | 2.92–15.96 | 22.3 | 19.9–20.4 |
Fat | 0.28–0.88 | - | 0.59 | - | - |
Crude fiber | 1.01–2.11 | - | 5.8–16.36 | 20.6 | - |
Ash | 0.62–1.89 | - | 1.7–2.3 | 7.1 | 8.4 |
Carbohydrates | 23.14–38.06 | 65.9–71.50 | 56.3–80.2 | - | 18.4–21.8 |
Insoluble dietary fiber | 3.7–6.4 | - | - | - | |
Soluble dietary fiber | 1.8 | 0.7–1.3 | - | - | - |
Indispensable AA | |||||
Histidine | 0.02 | 0.02–0.03 | 0.68 | 0.5 | 0.5 |
Isoleucine | 0.027 | 0.06–0.07 | 1.44 | 1 | 0.9 |
Leucine | 0.039 | 0.08–0.1 | 2.72 | 1.8 | 1.79–3.03 |
Lysine | 0.044 | 0.07–0.09 | 1.77 | 1.2 | 1.2–2.33 |
Methionine | 0.011 | 0.01–0.02 | 0.58 | 0.4 | 0.37–0.67 |
Phenylalanine | 0.026 | 0.05–0.06 | 1.8 | 1.3 | 1.1 |
Threonine | 0.028 | 0.05–0.07 | 1.41 | 1 | 0.9 |
Tryptophan | 0.019 | 0.03 | 0.55 | 0.8 | 0.6 |
Valine | 0.035 | 0.06–0.08 | 1.71 | 1.7 | 1.1 |
Dispensable AA | |||||
Arginine | 0.137 | 0.05–0.08 | 1.7 | 1.3 | 1.1 |
Alanine | 0.038 | 0.11 | 1.74 | 1.3 | 1.2–2.4 |
Aspartic acid | 0.079 | 0.13–0.14 | 2.57 | 3.2 | 1.98–3.32 |
Cysteine | 0.028 | 0.01 | 0.47 | 0.3 | 0.23–0.34 |
Glutamic acid | 0.206 | 0.25–0.3 | 3.05 | 3 | 2.39–4.21 |
Glycine | 0.028 | 0.06–0.07 | 1.59 | 1 | 1 |
Proline | 0.033 | 0.07–0.08 | 1.35 | 1.1 | 1.1 |
Serine | 0.033 | 0.05–0.06 | 1.35 | 1.2 | 1 |
Tyrosine | 0.017 | 0.02–0.03 | 1.24 | 0.9 | 0.8 |
Minerals | |||||
Ca | 0.016 | 0.12–0.18 | 0.50 | 0.57 | 0.39 |
P | 0.027 | 0.12–0.15 | |||
Mg | 0.021 | 0.06–0.10 | 0.15 | 0.16 | 0.08 |
K | 0.271 | 0.74–0.90 | 0.78 | 0.96 | 0.01 |
Na | 0.014 | 0.01 | |||
S | 0.021 | 0.04–0.05 | |||
Cooper (mg kg-1) | 1 | 1.9–4.31 | 401 | 509 | 243 |
Iron (mg kg-1) | 2.7 | 114.38–146.69 | |||
Manganese (mg kg-1) | 3.84 | 6.80–9.89 | 203 | 392 | 59 |
Zinc (mg kg-1) | 3.4 | 8.11–17.4 | 50 | 71.8 | 32.8 |
Dah–Sol & Fumiko [61]: Boakye et al. [65]; da Silva et al. [67]; Boundy–Mills et al. [77]; USDA [78]; Mardina et al. [79]; Chaiareekitwat et al., [80]; Gurdensen et al. [81]; Fanelli et al. [82]. |
However, the presence of anti–nutrients such as nitrates, phytates, tannins, oxalates, saponins [62], and HCN (ranging from 16 to 1212 ppm on a dry basis), which differs by variety and growing region [63], requires various preparation techniques to ensure safety before consumption. According to the Codex Alimentarius, levels of HCN should not exceed 50 and 10 mg kg-1 [64]. Notably, there are biofortified varieties of cassava with yellow pulp (a vitamin A precursor) that could enhance the vitamin and protein intake of consumers due to their nutritional quality [65].
Additionally, cassava leaves play a significant role in human nutrition, particularly in certain regions of the African continent and in Brazil in the Americas, where they are incorporated into various traditional dishes [66,67]. Moreover, the processing and sale of cassava leaves represent a rapidly growing emerging sector [68]. Despite containing cyanogenic glycosides with values ranging from 346 to 7484 ppm on a dry basis [63], the levels can be reduced through techniques such as oven drying, squeezing, boiling, and crushing, resulting in reductions to 55.99%, 50.79%, 32.01%, and 25.15%, respectively, and also decreasing the tannins presence [69]. Compared to the root, the leaves provide a higher protein contribution [70], containing 18 of the 20 amino acids, including all nine essential amino acids [63,71]. Additionally, the leaves are rich in minerals and vitamins, including thiamine, riboflavin, niacin, vitamin A, and vitamin C (Table 1). When processed into flour, the proportions of these nutrients are higher compared to other leafy vegetables, legumes, cereals, eggs, milk, and cheese [72]. Furthermore, cassava leaves contain carotenoids in significant amounts, ranging from 174 to 547 µg per gram on a dry basis [63]. The consumption of these compounds is crucial for nutrition and health [73], making cassava leaves a viable option to address issues of human malnutrition and contribute to food security.
Cassava production varies from complex systems with extensive plantations and mechanized tillage to low–input survival agriculture practices and intercropping [31,74]. Regardless of the system type, there is an imperative to enhance productivity to meet the escalating food demand [75]. Presently, cassava yields, as a carbohydrate source, outperform other roots, tubers, and cereals under tropical conditions due to its drought tolerance and adaptability to marginal soils [76]. This is why cassava cultivation proves more dependable than other species susceptible to such conditions, such as corn [60].
Approximately 1696.28 million hectares of marginal lands worldwide have been identified as potential areas for establishing cassava crops and achieving profitable yields [1]. However, realizing the optimal productivity of the species requires adherence to suitable edaphoclimatic conditions, proper crop management practices [83], and utilization of highly productive varieties developed through biotechnological techniques [84]. It is estimated that yields of between 80 and 100 t ha-1 of tuberous roots could be attained [85,86], highlighting those current yields are only about 10% of its potential productivity.
Following cassava harvesting, stems and leaves are produced, with proportions typically around 44% and 6%, respectively [7], which may vary by genotype and harvesting time [87]. While a portion of the stems is allocated for agronomic seed, the majority is underutilized, akin to the leaves, constituting the initial batch of co–products subject to waste [88]. Consequently, approximately 200 kg of dry matter per ton of harvested tuber is disposed of in situ, facilitating nutrient recycling [74]. However, this biomass could be immediately repurposed; for instance, the stems could serve as a substrate for mushroom cultivation [89], provide thermal energy in households due to its calorific value [90], or be used in the production of briquettes, recognized as environmentally friendly and renewable non–fossil fuels [91]. Therefore, these alternatives represent viable options for adoption by rural dwellers and low–income cassava producers.
Given the post–harvest deterioration issues of cassava roots, processing them to extend their shelf life is a common practice [92]. Among the processed products, starch holds the greatest economic impact [93]. The extraction of starch involves several stages (Figure 5), at an industrial scale, typically conducted in facilities equipped with mechanized systems for each step [94,95]. Such facilities utilize equipment that requires mechanical, heat, and electrical energy, averaging about 2 208 MJ per ton of processed root [96], and 0.20 to 0.50 kWh per kilogram of extracted starch [10]. Nevertheless, less advanced manufacturing processes, equipment, and even artisanal methods are prevalent. The resulting product is typically native starch with a moisture content ranging from 10% to 14%, suitable for marketing [97]. Various factors, including agricultural practices [98], variety, environmental conditions [99,100], and the applied technologies in the extraction process [101], influence the yield, quality, and physicochemical properties of the starch.
Numerous plants store carbohydrates as reserve sources in the form of starch across various plant organs such as roots, tubers, seeds, and grains [102]. The industrial sector derives starch from several crops, including maize, cassava, potato, and wheat, each differing in their field productivity and starch yield (Table 2) [103,104]. Carbohydrates, owing to their physical and chemical properties, are utilized in various high–value food and non–food industrial applications, either in native or modified starch form. These applications span a wide range including paper production, textiles (predominating the food market), pharmaceuticals, cosmetics, adhesives, sweeteners (fructose, glucose, sucrose, and sorbitol), food additives (monosodium glutamate, and maltodextrin), dextrins, dextrose, lactose, animal feed, biofuels, manufacturing of bioplastics and packaging, as well as applications in nanotechnology, regenerative medicine, and 3D printing materials [105,106,107]. Commercial prospects for starch–based products are anticipated to grow annually, driven particularly by the production of bioplastics and packaging [108].
Crop | Cassava | Sugarcane | Corn | Potato | Wheat | Rice |
Biomass (t ha-1 of product marketed) | ||||||
12.65 | 78.53 | 4.81 | 21.72 | 2–4.8 | 4.1 | |
Yield of starch (%) | ||||||
20.94–43.43 | 8.4–16.26a | 66.6–74.4 | 17.26–22.49 | 57 | 76.06–81.66 | |
Bagasse (%) | ||||||
Proportion in root | 30–40 | 26–29 | 67–74e | - | 67–72d | - |
Fiber | 19 | 37.71 | 86–88e | - | - | - |
Starch | 10.3–47 | - | - | - | - | |
Lipids | 0.47 | 2 | - | - | - | - |
Protein | 1.03–2.37 | 1.79 | - | - | - | - |
Ash | 0.16–1.8 | 1.35–8 | - | - | - | - |
Cellulose | 19.4–31.47 | 32–48 | 24–40 | - | 39–45d | - |
Hemicellulose | 0.53–31.3 | 23–32 | 44–55 | - | 25.6–37d | - |
Lignin | 0.4–22 | 13–24 | 9.5–23 | - | 23–28.3d | - |
Peel (%) | ||||||
Proportion in root | 19.41–24.52 | - | - | - | ||
Fiber | 10.15 | - | - | - | ||
Starch | 30.17 | - | - | 16.6–39.7 | - | |
Lipids | 0.67 | - | - | 7.33 | - | 0.3b |
Protein | 1.86–4.8 | - | - | 9.46–25.4 | - | 1.96b |
Ash | 7.78–9.5 | - | 3–4c | 5.82–11.1 | - | 0.36b |
Cellulose | 25.8–38.2 | - | 34–36c | 7.8 | - | 38.6b |
Hemicellulose | 11.6–31.4 | - | 36c | 14.7 | - | 24.9b |
Lignin | 4.29–13.9 | - | 19.2c | 21.6 | - | 18.6b |
a Sucrose, b Husk, c Cob, d Straw ande Stover. FAOstat [6]; de Souza et al. [57]; Boakye et al., [65]; Gundersen et al. [81]; Del Rosario–Arellano et al. [109]; Benesi et al. [117]; Liang et al. [118]; Mangla et al. [119]; Vargas & Pérez et al. [120]; Cao et al. [121]; Park et al. [122]; Awoyale et al. [123]; Biel et al., [124]: Pineda–Gómez et al. [125]; Singh et al. [126]; Ghaffar et al. [127]; Martínez et al. [128]; Yossa et al. [129]; Liu et al., [130]; Thuppahige, et al. [131]; Kovač et al. [132]. |
Similarly, to other industrial crops, cassava–based starch production generates significant amounts of lignocellulosic biomass, including bagasse, peel, and liquid wastewater (Figure 5). Bagasse, accounting for 60% of the total tuberous root, is produced during the filtration stage [109]. To produce one ton of starch, 2.5 tons of this co–product are generated [110]. Peel production ranges between 100 to 300 kg per ton of cassava [9,50], along with more than 17.4 m3 of liquid wastewater. The emission of greenhouse gases is also evident, with values reaching 2.21 kg CO2 eq. per ton of starch [111].
It is highlighted that during the starch extraction process, 75 to 90% of the solid co–products are disposed of in the open air or burned near the processing sites, while liquid wastewater is indiscriminately discharged into drainage or natural water sources [9]. These practices pose potential public health problems [23], damage to riparian flora and fauna caused by turbidity, toxicity, and high chemical oxygen demand has been documented [112]. Thus, the lack of management of co–products poses a threat to water consumption by the population and constitutes an ecocide of aquatic fauna. Urgent solutions are necessary to promote a reduction in the problems associated with the disposal of solid and liquid waste.
The recurring challenge in the agroindustrial sector is the disposal of co–products, partly due to the inherent characteristics of these materials. Although cassava agroindustry residues contain toxic substances, they also encompass structural non–toxic components (Table 2). Bagasse primarily comprises starch [30], alongside structural elements such as holocellulose (cellulose and hemicellulose) and lignin, whereas the peel is characterized by a higher protein and lipids content (Table 2). As for the liquid waste effluent (Table 3), this is an acid or weakly acid liquid composed of organic elements in suspension, thus, starch can be present at a rate of 9.6 to 37.5 g L-1, fibers, minerals [97], cyanogenic compounds, nitrates, nitrites, sulfates, heavy metals [46,113], as well as macronutrients, such as nitrogen and phosphorus, with amounts ranging from 780 to 1 300 mg L-1, in addition to micronutrients [114].
Parameter | Value | Parameter | Value |
pH | 4.20–5.98 | Potassium (mg mL-1) | 894–1247.92 |
Free cyanide (mg L-1) | 3 | Zinc (mg mL-1) | 1.4–1.83 |
DOC (g O2 L-1) | 61.27 | Iron (mg mL-1) | 4.2–15.37 |
Reducing sugars (g L-1) | 13.9–40.60 | Copper (mg mL-1) | 0.3–1.51 |
Non-reducing sugars (g L-1) | 17.51 | Sulfur (mg mL-1) | 150 |
Total carbohydrates (g L-1) | 36.20–58.11 | Aluminum (mg mL-1) | 148 |
Total nitrogen (g L-1) | 1.92–1.99 | Boron | 4 |
Dry material (g 10 mL-1) | 9.51 | Cadmium | < 0.01 |
Calcium (mg mL-1) | 212–241.62 | Chromium | < 0.01 |
Magnesium (mg mL-1) | 288–370.59 | Nickel | < 0.01 |
Manganese (mg mL-1) | 1.6 | Ammonia [NH4+] (mg L-1) | 131 |
Phosphorus (mg mL-1) | 83–246 | Nitrate [NO3-] (mg L-1) | 16.2 |
Sodium (mg mL-1) | 147.55 | ||
Source: Barros et al. [133]; Fleck et al. [134]; Santos et al. [135]. |
In this sense, it is possible to obtain similar or higher yields of cassava starch per hectare due to its high yield of fresh roots per hectare and starch percentage compared to other tubers and cereals. This is not to mention its socioeconomic and environmental advantages, which include sugarcane bagasse, the latter being one of the most abundant and widely used agroindustrial co–products worldwide [115]. Although many of the crops currently used for industrial purposes are staple foods in developing countries in the tropics [116], expanding the secondary sector could jeopardize food security. Therefore, it is necessary to explore other non–conventional sources of starch that are not used for food purposes in specific geographical areas.
Hence, it is possible to demonstrate the broad potential of cassava and its co–products due to their complex chemical composition, which makes them low–cost and highly available raw materials for a range of high–value–added applications. This would bring about an increase in their economic value while also representing a sustainable alternative to mitigate environmental problems [110]. This approach is oriented towards a circular economy, biorefinery [7,10], and the fulfillment of current green technology objectives aimed at finding sustainable and ecological solutions at social, economic, and environmental levels [11]. In this regard, one strategy for sustainable management of ALR involves making certain adjustments to settling ponds to decrease organic sediments and turbidity [97], coupled with the cultivation of microalgae such as Chlorella, Spirulina, and wild strains. These aspects could reduce BOD levels (89–99%), the presence of phosphates, nitrates, and cyanide [112,136]. Additionally, treated waters could be circulated in the starch extraction process, reducing freshwater needs by up to 66% [137]. Thus, to optimize resources, mitigate pollution issues, and enhance economic benefits, the implementation of new techniques and facilities within the industrial process is necessary.
Traditionally, cassava root is often utilized for animal feed in the form of chips, pellets, or silage [31,60]. Even whole plant silage is possible [138], and leaves are often offered in fresh or dehydrated form [139,140]; however, solid and liquid co–products from the starch industry can also fulfill this function. In Brazil, in artisanal farina production, peels are donated to livestock farmers for incorporation into animal feed [141]. In Nigeria, 10 to 25% of the peel and bagasse are disposed of as pig feed [142], representing a viable use option. Furthermore, disposing of bagasse in a fermented state economically achieves a higher net present value, lower investment cost and environmental impact, and a shorter payback period compared to other uses, such as the production of edible mushrooms [110]. The potential of wastewater has also been demonstrated for inclusion in the diets of fattening lambs [143].
However, to enhance the nutritional profile and safety, it is necessary to maximize the protein content and consider additional treatments to decrease HCN presence and antinutrients such as tannins and polyphenols [21,81,144]. Additionally, improving digestibility is essential since protein and fiber are the limiting factors for forage use in the tropics [138]. Techniques such as soaking, boiling, sun drying, or microbial fermentation can be useful to ameliorate these limiting factors [145]. Okike et al. [146] proposed a technique to obtain high–quality peel for animal nutrition, reducing sun drying time from 2 to 3 days to just 6 to 8 hours during the dry season through shredding, mechanical dehydration, fermentation, pulverization, and sieving, followed by subsequent solar drying. Additionally, Marin et al. [147] reported that subjecting a mixture of cassava leaves and bagasse (3:7) to solid–state fermentation (SSF) with the fungus Lentinula edodes decreased cyanide content by 64.8% while increasing protein content by 36.19% and lipid content by 2.36 times.
Similarly, de Sousa et al. [148] observed that cultivating Pleurotus ostreatus on cassava peel for 35 days led to increases in protein (from 3.93% to 8.87%), lipid (from 1.49% to 3.52%), and fiber (from 9.96% to 35.18%) content, along with a slight increase in digestibility (5.2%). Boundy–Mills et al. [77] utilized cassava leaves supplemented with glucose as a substrate for yeasts to convert solubilized structural protein into digestible protein. On the other hand, alternatives such as adding soybean meal, fish meal [139], methionine [145], or mixing cassava root with young leaves, sprouts, peep residues, and bagasse [15], or even silaging cassava pulp with fresh leaves [149], can improve the nutrient profile. Furthermore, a saving of 0.23 and 2.24 tons of soybean and corn, respectively, is possible when using a feed based on cassava and sorghum meal as an energy source and soybean and mulberry meal as protein in diets for pigs [150]. Furthermore, Williams et al. [151] found that dietary cassava peels and leaves in a 5:1 ratio do not affect performance in pigs fed corn and soybean.
Finally, methods such as heat and acid precipitation and spontaneous fermentation have been proposed to produce cassava leaf protein concentrate for feed and animal feed. However, although the protein content and amino acid profile are comparable with soybean, the cyanogenic potential needs to be decreased to ensure its use [81]. Thus, if properly managed, cassava co–products can be used as a substitute for corn or other cereals in diets for the livestock sector, which would undoubtedly improve the income of small and medium–scale livestock producers.
In the area surrounding cassava processing sites, the generation of biofertilizers is one of the main uses of solid co–products [9]. The low moisture content, bulk density, high porosity, and good water absorption capacity of biofertilizers made from this raw material are parameters that positively affect plant growth [152,153], especially when combined with synthetic sources of nutrients. Thus, it has been observed that the combined application of 2.5 tons of cassava peel compost with 25 kg of N ha-1 improved dry matter and nutrient content in Amaranthus cruentus L [154]. However, Nguefack et al. [155] reported an increase in nutritional and antioxidant parameters, as well as a yield enhancement of up to 187% compared to synthetic fertilizers. Additionally, the addition of compost and vermicompost from solid co–products increased fertility, structure, and even lowered soil salinity levels [156]. Moreover, the amount of nutrients contained in liquid waste effluents (Table 2) makes it promising for use as a biofertilizer [135]. Thus, the application of 120 m3 per hectare of this wastewater has the capacity to increase the concentration of available phosphorus and exchangeable potassium in the soil, making it an ideal input for adoption by small–scale farmers [157].
In summary, recycling waste not only serves as a disposal mechanism but also aligns with resource management practices, considering that these materials are highly available in processing areas and are practically inexpensive raw materials.
Lignocellulosic biomass is an alternative renewable energy resource with the potential to replace fossil fuels and GHG emissions. Agroindustrial co–products from cassava cultivation can be combusted for cogeneration of heat and electricity [158] due to their high calorific value since 15.27 to 18.86 MJ kg-1 are generated [159,160].
However, extensive research has focused on the study of stems, rhizomes, leaves, peel, and bagasse for the cogeneration of second–generation biofuels [17,161,162,163,164] such as bioethanol, biobutanol, biodiesel, bio–oil, biochar, and biohydrogen [15,18,123,165], these through biomass disintegration processes, such as biochemical (hydrolysis and fermentation) and thermochemical (direct combustion, gasification, slow pyrolysis, fast pyrolysis, and oxy–combustion) [166,167], although to improve sustainability it is necessary to implement novel strategies such as green technology within biosynthesis processes and circular economy principles [168].
In general, bagasse is considered a co–product with extensive research in bioethanol production [169,170] given its high content of starch, cellulose, hemicellulose, and low concentration of protein and lipids [171]. Moreover, the production yield depends on the chemical composition of the co–product and the process conditions [13,172]. Thus, Huang et al. [173] reported > 0.30 g g-1 and a productivity of ~0.3 g L h-1 of n–butanol in ABE (acetone–butanol–ethanol) fermentation from cassava bagasse.
Economically, it has been shown that it is possible to produce at $0.91 kg-1 or $2.73 gal-1 for 50 000 metric tons of cassava bagasse, compared to $7.41 gal-1 when using dextrose and $5.0 gal-1 if corn starch is used. Biobutanol is an interesting fuel due to its higher–octane rating and lower volatility, which is similar in air–to–fuel ratio to gasoline, compared to ethanol [114]. Thus, cassava bagasse is shown to be an economically attractive feedstock due to its low cost and abundance for biofuel cogeneration.
However, for the peels subjected to enzymatic saccharification, it is also possible to generate bioethanol, with a yield of 0.53 g g-1 [17], a yield that could be maximized using green technology. In this respect, it has been reported that using mild and green chemical pretreatments on lignocellulosic biomass, the latter using green proteins from Amaranthus retroflexus leaves as a biosurfactant in the saccharification process, it is possible to generate an additional 6 400 to 12 400 tons of bioethanol, ten times higher than using soybean seed proteins and chemical surfactants [174], as well as using subcritical hot liquid water and the addition of organic acids (acetic, lactic, and formic), which increases the yield of fermentable sugars [175].
On the other hand, the peel and bagasse are raw materials to produce biogas, a fuel useful to generate heat or achieve electricity cogeneration, representing savings of 4 to 11% in the production costs of the cassava industry [10,176]. Techniques utilizing the principles of green chemistry, such as pretreatment with hot liquid water, can enhance the removal of hemicellulose and starch, increasing methane production rate and yield by 1.6 times and 35%, respectively, compared to untreated bagasse [177]. Moreover, the utilization of pyrolyzed cassava stems and peels combined with cow manure in anaerobic digestion can be implemented in factories to yield multiple benefits, including wastewater treatment, electricity cogeneration, as well as biogas and biofertilizer production [19]. Similarly, it is possible to capture the wastewater effluents in biodigesters [15,167], and cogenerate 357.8 m3 for every 17.6 m3 of wastewater. This approach of circular economy and green technology undoubtedly would enhance the economic and environmental profitability of industrial operations [10].
Now, bagasse, being a waste composed of lignocellulose and carbohydrates, is a perfect substrate for fermentative hydrogen production, in this regard, Chatellard et al. [14] found a yield of < 1 ml H2 g-1 of dry matter for lignocellulosic residues, compared to 240 ml H2 g-1 of dry matter for purified starch, therefore, it is possible to increase the potential of the residues by choosing a good microbial consortium, subjecting the substrates to pretreatments and achieving the optimization of the technical production parameters.
It is also possible to cogenerate bio–oil, which is a precursor of renewable fuels and high–grade petrochemicals, the production of which could minimize dependence on fossil fuels and toxic chemicals [178]. In line with this, Rueangsan et al. [179], extracted bio–oil by fast pyrolysis with a yield of 65 % by weight of dry biomass from stems and rhizomes, the latter being of better quality due to lower oxygen content, higher calorific value and storage stability.
However, other by–products can be derived, such as syngas (CH4, H2, CO, and CO2) [15], and biochar, which, in addition to being directed as a solid biofuel, has the potential as a soil improvement [16], and biosorbent for wastewater dyes [180].
Specifically, although cassava is oriented as a first–generation energy crop with a 2% share, especially in China and Thailand [181], its use is controversial due to the increase in food prices caused by the rising demand for biofuels, a demand that enhances food conversion by planting bioenergy crops [104]. Thus, bioenergy production through its residual biomass is proposed as a promising alternative to minimize land use and safeguard food security [88]. Therefore, it is important to manage co–products from the cassava agroindustry, where biofuel production offers an economically and technologically attractive solution [14] that is capable of significantly reducing energy demand and decreasing greenhouse gas emissions [164], bringing environmental, economic, and social benefits [182], as population growth continues to rise inversely to the production of fossil fuels. It is also necessary for co–products to undergo pretreatment to break down the structure of the structural components and increase extraction efficiency [183]. Thus, co–products constitute an optional source to generate bioenergy in countries that are economically dependent on cassava cultivation [88]; however, barriers such as the lack of technological maturity and the high cost of production hinder significant growth in the energy market [104].
The co–products generated during cassava processing possess enormous potential for synthesizing bioactive compounds such as carotenoids, phenols, and organic acids (including gallic acid, catechin, rutin, chlorogenic acid, caffeic acid, citric acid, acetic acid, lactic acid, and poly–γ–glutamic acid (γ–PGA)), as well as flavonoids. These secondary metabolites offer specific health benefits, including the prevention of certain chronic non–communicable diseases, along with anti–inflammatory, anticarcinogenic, cardiovascular, and antioxidant properties, among others [21,24,25,184]. Regarding the peel, when subjected to physical, chemical, and biological processes, the lignin structure is modified, releasing the hemicellulosic base, a raw material for obtaining xylooligosaccharides (XOS). XOS serves as a useful prebiotic, promoting beneficial microbial activity in the organism [185]. Additionally, bacterial structures can be isolated from the residue to synthesize exopolymeric substances (EPS), particularly from the genus Bacillus [23].
Furthermore, leaves and stems contain various phytochemicals conferring antioxidant, anti–inflammatory, anthelmintic, and antidiabetic properties, offering an alternative to improving various health conditions [72,186]. This makes them suitable for use in the food industry; however, further safety and bioavailability studies of these active compounds are required [22]. Residual liquid effluents also serve as an optimal substrate for the growth of microorganisms that synthesize highly demanded bioproducts in both food and non–food industrial sectors [135].
Additionally, these co–products can be utilized in synthesizing bioplastics such as the copolymer poly (3–hydroxybutyrate–co–3–hydroxyvalerate) [29]. They can also serve as filler materials in polyurethane foams, reducing polyethylene glycol usage by 24% [30]. Furthermore, due to their morphological, physical, chemical, mechanical, and thermal properties, they can act as reinforcing agents in the polymeric matrix of biocomposites [187]. Thus, these co–products represent inexpensive raw materials that, if utilized in the biopolymer industry, could ensure sustainable and profitable production with positive environmental effects.
The peel can remove heavy metals (chromium VI) [26], and can also absorb dyes like methylene blue, making it useful for primary treatments of industrial liquid co–products [27], suggesting its potential in the field of bioremediation. Furthermore, bagasse can be used as an adsorbent material for food dyes, offering a promising application to replace commercial products such as activated carbon. For instance, Santos et al. [28] reported the biosorption of up to 74.4% of the dye tartrazine in effluents from the juice industry using 7.5 g L-1, attributed to its unique characteristics such as an irregular, heterogeneous surface, and the presence of pores. Other alternatives are also depicted in Table 4.
Co–product | Application | Result | Author |
Stems | Chipboard | Agromertified boards were produced with cassava stems and urea–formaldehyde adhesive at a 3:1 ratio, with properties of low water absorption (20 %), swelling thickness (6.26 %) in addition to high values of modulus of rupture (4×106 N m2), and elasticity (2366.74×106 N m2). | Aisien et al. [188]. |
Stems | Carbon quantum dots | Carbon quantum dots were produced by acid/alkali treatments and hydrothermal carbonization, with potential application for drug delivery. | Qiu et al. [189]. |
Stalk | Roofing sheets | Stable roofing sheets were produced by combining the co–products of cassava stems with corn cobs plus glues of animal origin and the use of PVC as a binder. | Aisien et al., [190]. |
Leaves | Medicinal use | Medicinal use through leaf extract (100,250, and 500 mg kg-1) with anti–inflammatory, antipyretic, and analgesic activity. | Bokanisereme & Okechukwu [191]. |
Peel | Wax | With the soxhlet extraction method with benzene and ethanol, it is possible to produce 8.51 % of crude wax, with potential application in the pharmaceutical, cosmetic, paint, and food industries. | Abiaziem & Ojelade [192]. |
Peel | Biopesticides | The peel as a substrate for the production of Trichoderma Brev T069, with a yield of 250 kg (2.89×109 spores/g) in a bioreactor, with control activity on the Fusarium wilt of banana. | Zhang et al. [193]. |
Peel | Sodium cyanide | Sodium cyanide was obtained from direct hydrolysis with better purity compared to its analytical grade counterpart, a green chemistry technique that promotes environmentally friendly, simple, and cost–effective synthesis. | Attahdaniel et al. [194]. |
Peel | ZnO nanorods decorated with carbon nanodots to degrade methylene blue | ZnO nanowires decorated with carbon nanodots were manufactured as a photocatalyst for the degradation of methyl blue, through the green chemistry technique which consisted of simple carbonization of cassava peel at low temperatures followed by an aging process for 6 days in absolute ethanol. | Roza et al. [195]. |
Tuberous root peridermis | Silicon | A silicon content of 6.10 % was reported in the ashes of cassava peridermis, a useful raw material for the pharmaceutical sector, archeology, biomedicine, and electronics (semiconductors). | Adebisi et al. [196]. |
Bagasse and rhizomes | Glass | The addition of bagasse ash and cassava rhizomes (0–10 %) are useful materials in the production of glass bottles. | Sopapan et al. [197]. |
Bagasse | Tissue engineering scaffold | Cassava fibers exhibit considerable strength and stiffness that can be oriented as a filler and reinforcing agent in the mechanical integrity of tissue–engineered polymer scaffolds. | Diabor (2017) [198]. |
The availability of a considerable volume of co–products from the cassava agroindustry leads to exploring their potential use for the development of bioenergy and bioproducts with high added value, especially in those places where cassava represents a fundamental pillar of the rural economy. Energy generation is one of the most studied aspects, which, if implemented within the factories, these methods could lead to a true circular economy, and with the principles of green technology, they would promote energy security, adequate land use, thus increasing the efficiency of low–value resources, and addressing environmental problems associated with cassava co–products, such as the discharge of liquid effluents into water sources, the production of unpleasant odors, and the emission of greenhouse gases. Finally, the potential high–value products that can be derived from these bio–waste products could bring benefits to the agroindustrial chain.
The authors declare that they have not used Artificial Intelligence (AI) tools in the creation of this article.
We thank the Facultad de Ciencias Biológicas y Agropecuarias, Región Córdoba–Orizaba of the Universidad Veracruzana.
All authors declare that there are no competing interests.
[1] | Jiang D, Wang Q, Ding F, et al. (2019) Potential marginal land resources of cassava worldwide: A data–driven analysis. Renew. and Sustain. Energy Rev 104: 167–173. https://doi.org/10.1016/j.rser.2019.01.024 |
[2] | FAO (Food and Agriculture Organization of the United Nations) (2018) Food Outlook–Biannual Report on Global Food Markets–November 2018. Available from: https://reliefweb.int/report/world/food-outlook-biannual-report-global-food-markets-november-2018 |
[3] |
Esuma W, Nanyonjo AR, Miiro R, et al. (2019) Men and women's perception of yellow–root cassava among rural farmers in eastern Uganda. Agri Food Secur 8: 1–9. https://doi.org/10.1186/s40066-019-0253-1 doi: 10.1186/s40066-019-0253-1
![]() |
[4] | Okoruwa VO, Abass AB, Akin–olagunju OA, et al. (2020) Does institution type affect access to finance for cassava actors in Nigeria? J of Agric and Food Res 2(October 2019): 100023. https://doi.org/10.1016/j.jafr.2020.100023 |
[5] |
Kihara J, Bolo P, Kinyua M, et al. (2020) Micronutrient deficiencies in African soils and the human nutritional nexus: opportunities with staple crops. Environ Geochem and Health 42: 3015–3033. https://doi.org/10.1007/s10653-019-00499-w doi: 10.1007/s10653-019-00499-w
![]() |
[6] | FAOStat (2023) Data, production, crops. Rome (Ita): Food and Agriculture Organisation. Available from: http://www.fao.org/faostat/en/#data/QC. 15 |
[7] |
Fernando NML, Amaraweera APSM, Gunawardane, OHP, et al. (2022) Sustainable biorefinery approach for cassava: A Review. Eng: J of the Inst of Eng Sri Lanka 2: 71–88. http://doi.org/10.4038/engineer.v55i2.7510 doi: 10.4038/engineer.v55i2.7510
![]() |
[8] | Ayetigbo O, Latif S, Abass A, et al. (2018). Comparing characteristics of root, flour and starch of biofortified yellow–flesh and white–flesh cassava variants, and sustainability considerations: A review. Sustainability (Switzerland). 10: 1–32. https://doi.org/10.3390/su10093089 |
[9] |
Olukanni DO, Olatunji TO (2018) Cassava waste management and biogas generation potential in selected local government areas in Ogun State, Nigeria. Recycl 3: 1–12. https://doi.org/10.3390/recycling3040058 doi: 10.3390/recycling3040058
![]() |
[10] |
Lerdlattaporn R, Phalakornkula C, Trakulvichean S, et al. (2021) Implementing circular economy concept by converting cassava pulp and wastewater to biogas for sustainable production in starch industry. Sustain Environ Res 31: 1–12. https://doi.org/10.1186/s42834-021-00093-9 doi: 10.1186/s42834-021-00093-9
![]() |
[11] | Bradu P, Biswas A, Nair C, et al. (2023) Recent advances in green technology and Industrial Revolution 4.0 for a sustainable future. Environ Sci Pollution Res 30: 124488–124519. https://doi.org/10.1007/s11356-022-20024-4 |
[12] | OCDE/FAO (2019) OCDE–FAO Perspectivas Agrícolas 2019–2028, OECD Publishing, París/Organización de las Naciones Unidas para la Alimentación y la Agricultura (FAO), Roma. https://doi.org/10.1787/7b2e8ba3-es |
[13] |
Martínez DG, Feiden A, Bariccatti R, et al. (2018) Ethanol production from waste of cassava processing. Appl Sci 8: 1–8. https://doi.org/10.3390/app8112158 doi: 10.3390/app8112158
![]() |
[14] | Chatellard L, Marone A, Carrère H, et al. (2017) Trends and challenges in biohydrogen production from agricultural waste. In: Singh A, Rathore D. Biohydrogen production: sustainability of current technology and future perspective. Springer, New Delhi. p. 69–95. https://doi.org/10.1007/978-81-322-3577-4_4 |
[15] |
Sivamani S, Chandrasekaran AP, Balajii M, et al. (2018) Evaluation of the potential of cassava–based residues for biofuels production. Rev Environ Sci Biotech 17: 553–570. https://doi.org/10.1007/s11157-018-9475-0 doi: 10.1007/s11157-018-9475-0
![]() |
[16] | Gogoi N, Sarma B, Mondal SC, et al. (2019) Use of biochar in sustainable agriculture. In: Farooq, M., and Pisante, M. editors. Innovations in Sustainable Agriculture. Springer, Cham, p. 501–528. https://doi.org/10.1007/978-3-030-23169-9_16 |
[17] | Aruwajoye GS, Faloye FD, Kana EG (2020a) Process optimisation of enzymatic saccharification of soaking assisted and thermal pretreated cassava peels waste for bioethanol production. Waste Biomass Valor 11: 2409–2420 https://doi.org/10.1007/s12649-018-00562-0 |
[18] |
Pason P, Tachaapaikoon C, Panichnumsin P, et al. (2020) One–step biohydrogen production from cassava pulp using novel enrichment of anaerobic thermophilic bacteria community. Biocatal Agric Biotechnol 27: 1–6. https://doi.org/10.1016/j.bcab.2020.101658 doi: 10.1016/j.bcab.2020.101658
![]() |
[19] |
Aduba CC, Ndukwe JK, Onyejiaka CK, et al. (2023) Integrated valorization of cassava wastes for production of bioelectricity, biogas and biofertilizer. Waste Biomass Valori 14: 4003–4019. https://doi.org/10.1007/s12649-023-02126-3 doi: 10.1007/s12649-023-02126-3
![]() |
[20] |
Xiong X, Iris KM, Tsang DC, et al. (2019) Value-added chemicals from food supply chain wastes: State-of-the-art review and future prospects. Chem Eng J 375: 121983. https://doi.org/10.1016/j.cej.2019.121983 doi: 10.1016/j.cej.2019.121983
![]() |
[21] |
Rodrigues CG, Silva VDM, Loyola ACDF, et al. (2022) Characterization and identification of bioactive compounds in agro-food waste flours. Quím N 45: 403–409. http://dx.doi.org/10.21577/0100-4042.20170853 doi: 10.21577/0100-4042.20170853
![]() |
[22] |
Ratnadewi AAI, Santoso AB, Sulistyaningsih E (2016) Application of cassava peel and waste as raw materials for xylooligosaccharide production using endoxylanase from Bacillus subtilis of soil termite abdomen. Procedia Chem 18: 31–38. https://doi.org/10.1016/j.proche.2016.01.007 doi: 10.1016/j.proche.2016.01.007
![]() |
[23] |
AMAO JA, Omojasola PF, Barooah M (2019) Isolation and characterization of some exopolysaccharide producing bacteria from cassava peel heaps. Sci Afr 4: 1–11. https://doi.org/10.1016/j.sciaf.2019.e00093 doi: 10.1016/j.sciaf.2019.e00093
![]() |
[24] |
John T, Salihu A, Onyike E (2020) Assessment of cassava peels as renewable substrate for production of poly–γ–glutamic acid by Bacillus subtilis. Environ Sustain 3: 179–186. https://doi.org/10.1007/s42398-020-00102-4 doi: 10.1007/s42398-020-00102-4
![]() |
[25] | Vishnu D, Dhandapani B, Mahadevan S (2020) Recent advances in organic acid production from microbial sources by utilizing agricultural by–products as substrates for industrial applications. In: Jerold M, Arockiasamy S, Sivasubramanian V. The Handbook of Environmental Chemistry. Springer, Berlin, Heidelberg. p. 67–87. https://doi.org/10.1007/698_2020_577 |
[26] |
Acosta AHA, Barraza YCA, Albis AAR (2017) Adsorción de cromo (VI) utilizando cáscara de yuca (Manihot esculenta) como biosorbente: Estudio cinético. Ing y Desarro 35: 58–79. http://dx.doi.org/10.14482/inde.35.1.8943 doi: 10.14482/inde.35.1.8943
![]() |
[27] |
Albis AA, López AJ, Romero MC (2017) Remoción de azul de metileno de soluciones acuosas utilizando cáscara de yuca (Manihot esculenta) modificada con ácido fosfórico. Prospectiva 15: 60–73. https://doi.org/10.15665/rp.v15i2.777 doi: 10.15665/rp.v15i2.777
![]() |
[28] |
Santos LN, Porto CE, Bulla MK, et al. (2021) Peach palm and cassava wastes as biosorbents of tartrazine yellow dye and their application in industrial effluent. Scientia Plena 17: 1–19. https://doi.org/10.14808/sci.plena.2021.054201 doi: 10.14808/sci.plena.2021.054201
![]() |
[29] |
Salgaonkar BB, Mani K, Bragança JM (2019) Sustainable bioconversion of cassava waste to poly(3–hydroxybutyrate–co–3–hydroxyvalerate) by Halogeometricum borinquense Strain E3. J Polym Environ 27: 299–308. https://doi.org/10.1007/s10924-018-1346-9 doi: 10.1007/s10924-018-1346-9
![]() |
[30] |
Keller M, Ambrosio E, de Oliveira VM et al. (2020). Polyurethane foams synthesis with cassava waste for biodiesel removal from water bodies. Bioresour Technol Rep 10: 1–5. https://doi.org/10.1016/j.biteb.2020.100396 doi: 10.1016/j.biteb.2020.100396
![]() |
[31] | Sharma HK, Kaushal P (2016) Introduction to tropical roots and tubers. In: Sharma HK, Njintang NY, Singhal RS, Kaushal P. Tropical roots and tubers: production, processing and technology. John Wiley & Sons. p. 1–33. https://doi.org/10.1002/9781118992739.ch1 |
[32] |
Olsen KM (2004) SNPs, SSRs and inferences on cassava's origin. Plant Mol Biol 56: 517–526. https://doi.org/10.1007/s11103-004-5043-9 doi: 10.1007/s11103-004-5043-9
![]() |
[33] |
Léotard G, Duputié A, Kjellberg F, et al. (2009) Phylogeography and the origin of cassava: new insights from the northern rim of the Amazonian basin. Mol Phylogenetics and Evol 53: 329–334. https://doi.org/10.1016/j.ympev.2009.05.003 doi: 10.1016/j.ympev.2009.05.003
![]() |
[34] | Tovar E, Bocanegra JL, Villafañe C, et al. (2016). Diversity and genetic structure of cassava landraces and their wild relatives (Manihot spp.) in Colombia revealed by simple sequence repeats. Plant Genet Resour: Charact and Util 14: 200–210. https://doi.org/10.1017/S1479262115000246 |
[35] | Ogbonna AC, Braatz de AL., Mueller LA, et al. (2021) Comprehensive genotyping of a Brazilian cassava (Manihot esculenta Crantz) germplasm bank: insights into diversification and domestication. Theoretical App Genet 134: 1343–1362. https://doi.org/10.1007/s00122-021-03775-5 |
[36] |
Watling J, Shock MP, Mongelo GZ, et al. (2018) Direct archaeological evidence for Southwestern Amazonia as an early plant domestication and food production centre. PLoS ONE 13: 28. https://doi.org/https://doi.org/10.1371/journal.pone.0199868 doi: 10.1371/journal.pone.0199868
![]() |
[37] |
Carvalho LJCB, Schaal BA (2001) Assessing genetic diversity in the cassava (Manihot esculenta Crantz) germplasm collection in Brazil using PCR–based markers. Euphytica 120: 133–142. https://doi.org/10.1023/A:1017548930235 doi: 10.1023/A:1017548930235
![]() |
[38] |
Isendahl C (2011) The Domestication and early spread of manioc (Manihot esculenta Crantz): A Brief Synthesis. Latin American Antiquity 22: 452–468. https://doi.org/10.7183/1045-6635.22.4.452 doi: 10.7183/1045-6635.22.4.452
![]() |
[39] |
Simon MF, Reis TS, Mendoza FJM, et al. (2020) Conservation assessment of cassava wild relatives in central Brazil. Biodiver Conserv 29: 1589–1612. https://doi.org/10.1007/s10531-018-1626-7 doi: 10.1007/s10531-018-1626-7
![]() |
[40] |
Nassar N (2000) Cytogenetics and evolution of cassava (Manihot esculenta Crantz). Genet and Mol Biol 23: 1003–1014. https://doi.org/10.1590/S1415-47572000000400046 doi: 10.1590/S1415-47572000000400046
![]() |
[41] |
Pope KO, Pohl MED, Jones JC, et al. (2001) Origin and environmental setting of ancient agriculture in the lowlands of Mesoamerica. Sci 292: 1370–1373. https://doi.org/10.1126/science.292.5520.1370 doi: 10.1126/science.292.5520.1370
![]() |
[42] | Acosta OG (2005) Asentamiento y sistemas agrícolas en los márgenes del Tonalá bases para el estudio de la paleosubsistencia olmeca en La Venta, Tabasco (ca. 1500-500 aC). Dialogo Antropog 3: 57–72. |
[43] | Cagnato C, Ponce JM (2018) Ancient Maya manioc (Manihot esculenta Crantz) consumption: Starch grain evidence from late to terminal classic (8th-9th century CE) occupation at La Corona, northwestern Petén, Guatemala. J of Archaeol Sci: Rep 16(December 2017): 276–286. https://doi.org/10.1016/j.jasrep.2017.09.035 |
[44] | Carter SE, Fresco LO, Jones PG, et al. (1993) Introduction and diffusion of cassava in Africa. Ibadan: ⅡTA, Research Guide 49. Training Program, International Institute of Tropical Agriculture (ⅡTA). Ibadan, Nigeria. 34 p. https://www.researchgate.net/publication/40207427_Introduction_and_diffusion_of_cassava_in_Africa |
[45] | Jones WO (1959) Manioc in Africa. Michigan (EE. UU.): Stanford Univ. Press, Oxford Univ. Press. 315 p. |
[46] | Cock JH (2019) Cassava: new potential for a neglected crop. New York (EE. UU.): CRC Press, 208 p. |
[47] | Onwueme IC (2002) Cassava in Asia and the Pacific. In: Hillocks RJ, Thresh JM, Bellotti AC. Cassava: Biology, production and utilization. Cab 55–65. |
[48] | Lim TK (2016) Manihot esculenta. In: Lim TK. Edible medicinal and non–medicinal plants. Springer, Dordrecht. p. 308–353. https://doi.org/10.1007/978-94-017-7276-1_17 |
[49] | Aguilar-Rivera N (2024) Life cycle assessment of valorization of root and tuber crop wastes for bio-commodities and biofuels: Cassava as a case study. In: Ray RC editor. Roots, tubers, and bulb crop wastes: Management by biorefinery approaches. Springer, Singapore 333–350 https://doi.org/10.1007/978-981-99-8266-0_15 |
[50] |
Anyanwu CN, Ibeto CN, Ezeoha SL, et al. (2015) Sustainability of cassava (Manihot esculenta Crantz) as industrial feedstock, energy and food crop in Nigeria. Renew Energy 81: 745–752. https://doi.org/10.1016/j.renene.2015.03.075 doi: 10.1016/j.renene.2015.03.075
![]() |
[51] |
Ikuemonisan ES, Mafimisebi TE, Ajibefun I, et al. (2020) Cassava production in Nigeria: trends, instability and decomposition analysis (1970–2018). Heliyon 6: e05089. https://doi.org/10.1016/j.heliyon.2020.e05089 doi: 10.1016/j.heliyon.2020.e05089
![]() |
[52] | Tokunaga H, Tamon B, Ishitani M, Ito K, et al. (2018). Sustainable management of invasive cassava pests in Vietnam, Cambodia, and Thailand. In: Kokubun M, Asanuma S. Crop Production under Stressful Conditions: Application of Cutting–edge Science and Technology in Developing Countries. p. 131–157. https://doi.org/10.1007/978-981-10-7308-3 |
[53] | OEC (The Observatory of Economic Complexity) (2020) Cassava. https://oec.world/en |
[54] | GSOVN (General Statistics Office of Vietnam) (2019) Agriculture, Forestry and Fishing. Vietnam. Available from: https://www.gso.gov.vn/en/agriculture-forestry-and-fishery/ |
[55] | ACIAR (Australian Centre for International Agricultural Research) (2023) A tale of two diseases: Cassava and COVID–19. https://www.aciar.gov.au/media-search/blogs/a-tale-two-diseases-cassava-and-covid-19 |
[56] | Ceballos H, Hershey CH (2017) Cassava (Manihot esculenta Crantz). In: Campos H, Caligari PDS. Genetic Improv of Tropical Crops 129–180. https://doi.org/10.1007/978-3-319-59819-2 |
[57] |
de Souza FD, Rodrigues dos STP, Mazetti FA, et al. (2019) Harvest time optimization leads to the production of native cassava starches with different properties. Int J of Biol Macromol 132: 710–721. https://doi.org/10.1016/j.ijbiomac.2019.03.245 doi: 10.1016/j.ijbiomac.2019.03.245
![]() |
[58] | Vilpoux O, de Oliveira GD, Pascoli CM (2017) Cassava cultivation in Latin America. Burleigh Dodds Science Publishing. 1–26. https://doi.org/10.19103/as.2016.0014.07 |
[59] |
Andrade CI, Andrade LRS, Bharagava RN, et al. (2021) Valorization of cassava residues for biogas production in Brazil based on the circular economy: An updated and comprehensive review. Clean Eng Technol 4: 100196. https://doi.org/10.1016/j.clet.2021.100196 doi: 10.1016/j.clet.2021.100196
![]() |
[60] | Thiele G, Friedmann M, Polar V, et al. (2022) Overview. In: Thiele G, Friedmann M, Campos H, Polar V, Bentley JW. editors. Root, Tuber and Banana Food System Innovations. Springer Cham 3–28. https://doi.org/10.1007/978-3-030-92022-7 |
[61] |
Dah-Sol K, Fumiko I (2023) Nutritional composition of cassava (Manihot esculenta) and its application to elder-friendly food based on enzyme treatment. Int J of Food Prop 26: 1311–1323. https://doi.org/10.1080/10942912.2023.2213410 doi: 10.1080/10942912.2023.2213410
![]() |
[62] | Panghal A, Munezero C, Sharma P, et al. (2019) Cassava toxicity, detoxification and its food applications: a review. Toxin Reviews. https://doi.org/10.1080/15569543.2018.1560334 |
[63] |
Ospina MA, Pizarro M, Tran T, et al. (2021) Cyanogenic, carotenoids and protein composition in leaves and roots across seven diverse population found in the world cassava germplasm collection at CIAT, Colombia. Int J Food Sci Technol 56: 1343–1353. https://doi.org/10.1111/ijfs.14888 doi: 10.1111/ijfs.14888
![]() |
[64] | FAO WHO (2019) Codex Committee on Contaminats in Foods. In: Organisation, FAA, United, WHOOT. & NATIONS U. editors. Discussion paper on the establishment of MLS for HCN in Cassava and Cassava-based Products and Occurrence of Mycotoxins in these Products. 1–4. Rome, Italy, FAO. |
[65] |
Boakye PB, Parkes EY, Harrison OA, et al. (2020) Proximate composition, cyanide content, and carotenoid retention after boiling of provitamin A–rich cassava grown in Ghana. Foods 9: 1800. https://doi.org/10.3390/foods9121800 doi: 10.3390/foods9121800
![]() |
[66] |
Herminingrum S (2019) The genealogy of traditional Javanese cassava–based foods. J Ethn Foods 6: 1–16. https://doi.org/10.1186/s42779-019-0015-5 doi: 10.1186/s42779-019-0015-5
![]() |
[67] |
da Silva Santos BR, Silva EFR, Minho LAC, et al. (2020) Evaluation of the nutritional composition in effect of processing cassava leaves (Manihot esculenta) using multivariate analysis techniques. Microchem J 152: 104271. https://doi.org/10.1016/j.microc.2019.104271 doi: 10.1016/j.microc.2019.104271
![]() |
[68] | Chiwona-Karltun L, Brimer L, Jackson J. (2022) Improving safety of cassava products. In: Thiele G, Friedmann M, Campos H, Polar V, Bentley JW. editors. Root, Tuber and Banana Food System Innovations. Springer Cham, p. 241–258. https://doi.org/10.1007/978-3-030-92022-7 |
[69] | Tambalo FMZ, Capuno RBA, Estrellana CD, et al. (2023) Effect of processing on the antinutrient and protein contents of cassava leaves from selected varieties. Philippine J of Sci 152: 561–570. |
[70] |
Wadhwa M, Singh H, Kumar B, et al. (2021) In vitro evaluation of short duration cassava varieties as llivestock feed. Indian J of Anim Sci 91: 965-970. https://doi.org/10.56093/ijans.v91i11.118142 doi: 10.56093/ijans.v91i11.118142
![]() |
[71] |
Leguizamón AJ, Rompato KM, Hoyos RE, et al. (2021) Nutritional evaluation of three varieties of cassava leaves (Manihot esculenta Crantz) grown in Formosa, Argentina. J Food Compos Anal 101: 103986. https://doi.org/10.1016/j.jfca.2021.103986 doi: 10.1016/j.jfca.2021.103986
![]() |
[72] | Mohidin SRNSP, Moshawih S, Hermansyah A, et al. (2023) Cassava (Manihot esculenta Crantz): A systematic review for the pharmacological activities, traditional uses, nutritional values, and phytochemistry. J Evid–Based Integr Med 28: 2515690X231206227. |
[73] | Ryan PJ, Riechman SE, Fluckey JD, et al. (2021) Interorgan metabolism of amino acids in human health and disease. In: Wu G. editor. Amino Acids in Nutrition and Health, Advances in Experimental Medicine and Biology. Springer, Cham 1332: 129–149. https://doi.org/10.1007/978-3-030-74180-8_8 |
[74] |
Byju G, Suja G (2020) Mineral nutrition of cassava. Adv Agron 159: 169–235. https://doi.org/10.1016/bs.agron.2019.08.005 doi: 10.1016/bs.agron.2019.08.005
![]() |
[75] | Laxminarayana K, Mishra S, Soumya, S (2016) Good agricultural practices in tropical root and tuber crops. In: Sharma HK, Kaushal P. Tropical roots and tubers: production, processing and technology. p. 183–224. https://doi.org/10.1002/9781118060858.ch3 |
[76] |
Morgante CV, Nunes SLP, Chaves ARDM, et al. (2020) Genetic and physiological analysis of early drought response in Manihot esculenta and its wild relative. Acta physiologiae plant 42: 1–11. https://doi.org/10.1007/s11738-019-3005-8 doi: 10.1007/s11738-019-3005-8
![]() |
[77] | Boundy-Mills K, Karuna N, Garay LA, et al. (2019) Conversion of cassava leaf to bioavailable, high-protein yeast cell biomass. J Sci Food Agric 99: 3034–3044. DOI10.1002/jsfa.9517 |
[78] | USDA (U.S. Department of Agriculture) (2019) Food data central, Cassava, raw. https://fdc.nal.usda.gov/fdc-app.html#/food-details/169985/nutrients |
[79] | Mardina P, Irawan C, Putra MD, et al. (2021) Bioethanol production from cassava peel treated with sulfonated carbon catalyzed hydrolysis. Jurnal Kimia Sains dan Aplikasi 24: 1–8. https://doi.0rg/io.i47io/jksa.24.1.1-9 |
[80] |
Chaiareekitwat S, Latif S, Mahayothee B, et al. (2022) Protein composition, chlorophyll, carotenoids, and cyanide content of cassava leaves (Manihot esculenta Crantz) as influenced by cultivar, plant age, and leaf position. Food Chem 372: 131–173. https://doi.org/10.1016/j.foodchem.2021.131173 doi: 10.1016/j.foodchem.2021.131173
![]() |
[81] |
Gundersen E, Christiansen AHC, Jørgensen K, et al. (2022) Production of leaf protein concentrates from cassava: Protein distribution and anti-nutritional factors in biorefining fractions. J Clean Prod 379: 134730. https://doi.org/10.1016/j.jclepro.2022.134730 doi: 10.1016/j.jclepro.2022.134730
![]() |
[82] |
Fanelli NS, Torres-Mendoza LJ, Abelilla JJ, et al. (2023) Chemical composition of cassava-based feed ingredients from South-East Asia. Anim Biosci 36: 908–919. https://doi.org/10.5713/ab.22.0360 doi: 10.5713/ab.22.0360
![]() |
[83] |
Munyahali W, Pypers P, Swennen R, et al. (2017) Responses of cassava growth and yield to leaf harvesting frequency and NPK fertilizer in South Kiv, Democratic Republic of Congo. F Crops Res 214: 194–201. https://doi.org/10.1016/j.fcr.2017.09.018 doi: 10.1016/j.fcr.2017.09.018
![]() |
[84] |
Otun S, Escrich A, Achilonu I, et al. (2023) The future of cassava in the era of biotechnology in Southern Africa. Crit Re Biotechnol 43: 594–612. https://doi.org/10.1080/07388551.2022.2048791 doi: 10.1080/07388551.2022.2048791
![]() |
[85] | Saraiva LL, da Silva LCA, da Silva SV (2019) Effect of harvesting times on agronomic characteristics of industrial cassava genotypes. Revista Brasileira de Ciências Agrárias. 14: 1–6. https://doi.org/10.5039/agraria.v14i2a5647 |
[86] |
Sukara E, Hartati S, Ragamustari SK (2020). State of the art of Indonesian agriculture and the introduction of innovation for added value of cassava. Plant Biotechnol Rep 14: 207–212. https://doi.org/10.1007/s11816-020-00605-w doi: 10.1007/s11816-020-00605-w
![]() |
[87] |
Veiga JPS, Valle TL, Feltran JC, et al. (2016). Characterization and productivity of cassava waste and its use as an energy source. Renew Energy 93: 691–699. https://doi.org/10.1016/j.renene.2016.02.078 doi: 10.1016/j.renene.2016.02.078
![]() |
[88] |
Ozoegwu CG, Eze C, Onwosi CO, et al. (2017) Biomass and bioenergy potential of cassava waste in Nigeria: Estimations based partly on rural–level garri processing case studies. Renew and Sustain Energy Rev 72: 625–638. https://doi.org/10.1016/j.rser.2017.01.031 doi: 10.1016/j.rser.2017.01.031
![]() |
[89] | Howeler R, Lutaladio N, Thomas G (2013) Save and grow cassava: a guide to sustainable production intensification. Available from: http://www.fao.org/3/i3278e/i3278e.pdf |
[90] | Lismeri L, Anggraini M, Sudarno A. et al (2019) Characterization and analysis of cassava stems as potential biomass for bio–oil production via electromagnetic–assisted catalytic liquefaction. Adv Eng Res 202: 292–298. http://repository.lppm.unila.ac.id/16247/1/ICBS%20pdf.pdf |
[91] | Akogun OA, Waheed MA, Ismaila SO, et al. (2020) Co-briquetting characteristics of cassava peel with sawdust at different torrefaction pretreatment conditions. Energy Sources Part A Recovery Utilization Environ Eff 1–19. https://doi.org/10.1080/15567036.2020.1752333 |
[92] |
Mbinda W, Mukami A (2022) Breeding for postharvest physiological deterioration in cassava: problems and strategies. CABI Agric Biosci 3: 30. https://doi.org/10.1186/s43170-022-00097-4 doi: 10.1186/s43170-022-00097-4
![]() |
[93] |
Amelework AB, Bairu MW, Maema O, et al. (2021) Adoption and promotion of resilient crops for climate risk mitigation and import substitution: A case analysis of cassava for South African agriculture. Front Sustain Food Syst 5: 617783. https://doi.org/10.3389/fsufs.2021.617783 doi: 10.3389/fsufs.2021.617783
![]() |
[94] |
Kringel DH, El Halal SLM, Zavareze EDR, et al. (2020) Methods for the extraction of roots, tubers, pulses, pseudocereals, and other unconventional starches sources: a review. Starch-Stärke 72: 1900234. https://doi.org/10.1002/star.201900234 doi: 10.1002/star.201900234
![]() |
[95] |
Guangyu D, Xueting W, Bochao Z, et al. (2021) The transformation and outcome of traditional cassava starch processing in Guangxi, China. Environ Techn 42: 3278–3287. DOI: 10.1080/09593330.2020.1725647 doi: 10.1080/09593330.2020.1725647
![]() |
[96] |
Salla DA, Furlaneto FP, Cabello C, et al. (2010) Energetic analysis of the ethanol production systems of cassava (Manihot esculenta Crantz). Revista Brasileira de Engenharia Agrícola e Ambiental 14: 444–448. https://doi.org/10.1590/S1415-43662010000400015 doi: 10.1590/S1415-43662010000400015
![]() |
[97] |
Santos SA, Lopes SY, Araújo KR, et al. (2017) Waste bio–refineries for the cassava starch industry: New trends and review of alternatives. Renew Sustain Energy Rev 73: 1265–1275. https://doi.org/10.1016/j.rser.2017.02.007 doi: 10.1016/j.rser.2017.02.007
![]() |
[98] |
Tan X, Gu B, Li X, et al. (2017). Effect of growth period on the multi–scale structure and physicochemical properties of cassava starch. Int J Biol Macromol 101: 9–15. https://doi.org/10.1016/j.ijbiomac.2017.03.031 doi: 10.1016/j.ijbiomac.2017.03.031
![]() |
[99] |
Buddhakulsomsiri J, Parthanadee P, Pannakkong W (2018) Prediction models of starch content in fresh cassava roots for a tapioca starch manufacturer in Thailand. Comput Electron Agric 154: 296–303. https://doi.org/10.1016/j.compag.2018.09.016 doi: 10.1016/j.compag.2018.09.016
![]() |
[100] |
Tappiban P, Sraphet S, Srisawad N, et al. (2020) Effects of cassava variety and growth location on starch fine structure and physicochemical properties. Food Hydrocoll 108: 106074. https://doi.org/10.1016/j.foodhyd.2020.106074 doi: 10.1016/j.foodhyd.2020.106074
![]() |
[101] | García–Mogollón C, Salcedo–Mendoza J, Alvis–Bermúdez A (2018) Optimum conditions for the leaching step in the extraction of cassava starch. Biotecnología en el Sect Agropecu y Agroind 16: 62–67. http://www.scielo.org.co/scielo.php?script = sci_arttext & pid = S1692-35612018000100062 |
[102] |
Zhang X, Guo D, Blennow A, et al. (2021) Mineral nutrients and crop starch quality. Trends Food Sci Technol 114: 148–157. https://doi.org/10.1016/j.tifs.2021.05.016 doi: 10.1016/j.tifs.2021.05.016
![]() |
[103] | Agama–Acevedo E, Flores–Silva PC, Bello–Perez LA (2019) Cereal starch production for food applications. In: Silva CMTP, Schmiele M. editors. Starches for Food Application, Chemical, Technological and Health Properties 71–102. https://doi.org/10.1016/B978-0-12-809440-2.00003-4 |
[104] |
Devi A, Bajar S, Sihag P, et al. (2023) A panoramic view of technological landscape for bioethanol production from various generations of feedstocks. Bioeng 14: 81–112. https://doi.org/10.1080/21655979.2022.2095702 doi: 10.1080/21655979.2022.2095702
![]() |
[105] | IFBB (Institute for Bioplastics and Biocomposites) (2019) Biopolymers facts and statistics, Production capacities, processing routes, feedstock, land and water use. https://www.ifbb-hannover.de/en/facts-and-statistics.html |
[106] |
Del Rosario–Arellano JL, Bolio–López GI, Valadez–González A, et al. (2021) Exploration of cassava clones for the development of biocomposite films. AIMS Mater Sci 9: 85–104. doi: 10.3934/matersci.2022006 doi: 10.3934/matersci.2022006
![]() |
[107] |
Sunmonu M, Sanusi M, Lawal H (2021) Effect of different processing conditions on quality of cassava. Croatian J Food Sci Technol 13: 69–77. https://doi.org/10.17508/CJFST.2021.13.1.09 doi: 10.17508/CJFST.2021.13.1.09
![]() |
[108] |
Adewale P, Yancheshmeh MS, Lam E (2022) Starch modification for non-food, industrial applications: Market intelligence and critical review. Carbohydr Polym 291: 119590. https://doi.org/10.1016/j.carbpol.2022.119590 doi: 10.1016/j.carbpol.2022.119590
![]() |
[109] |
Del Rosario–Arellano JL, Meneses–Márquez I, Leyva–Ovalle OR, et al. (2020) Morphoagronomic and industrial performance of cassava (Manihot esculenta Crantz) germplasm for the production of starch and solid byproducts. AIMS Agric Food 5: 617–634. doi: 10.3934/agrfood.2020.4.617 doi: 10.3934/agrfood.2020.4.617
![]() |
[110] |
Trakulvichean S, Chaiprasert P, Otmakhova J, et al. (2017) Integrated economic and environmental assessment of biogas and bioethanol production from cassava cellulosic waste. Waste Biomass Valor 10: 691–700. https://doi.org/10.1007/s12649-017-0076-x doi: 10.1007/s12649-017-0076-x
![]() |
[111] | Giau VV, Van TT. Le LT, et al. (2023) Application of linear programming for cassava starch production optimization in Vietnam within a circular economy framework toward zero emission. Environ Eng Res 28: 220214. https://doi.org/10.4491/eer.2022.214 |
[112] |
de Carvalho JC, Borghetti IA, Cartas LC, et al. (2018) Biorefinery integration of microalgae production into cassava processing industry: Potential and perspectives. Bioresour Technol 247(September 2017): 1165–1172. https://doi.org/10.1016/j.biortech.2017.09.213 doi: 10.1016/j.biortech.2017.09.213
![]() |
[113] | Okunade DA, Adekalu KO (2013) Physico–chemical analysis of contaminated water resources due to cassava wastewater effluent disposal. Eur Int J Sci Technol 2: 75–84. https://www.researchgate.net/publication/263328306_Physico-chemical_analysis_of_contaminated_water_resources_due_to_cassava_wastewater_effluent_disposal |
[114] |
Zhang M, Xie L, Yin Z, et al. (2016) Biorefinery approach for cassava–based industrial wastes: current status and opportunities. Bioresour Technol 215: 50–62. https://doi.org/10.1016/j.biortech.2016.04.026 doi: 10.1016/j.biortech.2016.04.026
![]() |
[115] |
Raza QUA, Bashir MA, Rehim A, et al. (2021) Sugarcane industrial byproducts as challenges to environmental safety and their remedies: A review. Water 13: 3495. https://doi.org/10.3390/w13243495 doi: 10.3390/w13243495
![]() |
[116] | Jennings DL (2019) Starch crops. In: CRC Handbook of plant Science in Agriculture 137–144. CRC press. |
[117] | Benesi IR, Labuschagne MT, Dixon AG, et al. (2004) Stability of native starch quality parameters, starch extraction and root dry matter of cassava genotypes in different environments. J Sci Food Agric 84: 1381–1388. https://doi.org/10.1002/jsfa.1734 |
[118] |
Liang S, Gliniewicz K, Mendes-Soares H, et al. (2015) Comparative analysis of microbial community of novel lactic acid fermentation inoculated with different undefined mixed cultures. Bioresour Technol 179: 268–274. https://doi.org/10.1016/j.biortech.2014.12.032. doi: 10.1016/j.biortech.2014.12.032
![]() |
[119] | Mangla AK, Chawla V, Singh G (2017) Review paper on high temperature corrosion and its control in coal fired boilers. Int J Latest Trends Eng Technol (Special Issue–AFTMME): 088–092. https://www.ijltet.org/pdfviewer.php?id = 925 & j_id = 4238. |
[120] |
Vargas YA, Peréz LI (2018) Aprovechamiento de residuos agroindustriales en el mejoramiento de la calidad del ambiente. Revista Facultad de Ciencias Básicas 1: 59–72. https://doi.org/10.18359/rfcb.3108 doi: 10.18359/rfcb.3108
![]() |
[121] | Cao X, Tong J, Ding M, et al. (2019) Physicochemical properties of starch in relation to rheological properties of wheat dough (Triticum aestivum L.). Food chem 297: 125000. https://doi.org/10.1016/j.foodchem.2019.125000 |
[122] |
Park J, O0h SK, Chun, HJ, et al. (2020) Structural and physicochemical properties of native starches and non-digestible starch residues from Korean rice cultivars with different amylose contents. Food Hydrocoll 102: 105544. https://doi.org/10.1016/j.foodhyd.2019.105544 doi: 10.1016/j.foodhyd.2019.105544
![]() |
[123] |
Awoyale AA, Lokhat D, Eloka-Eboka AC (2021) Experimental characterization of selected Nigerian lignocellulosic biomasses in bioethanol production. Int J Ambient Energy 42: 1343–1351. https://doi.org/10.1080/01430750.2019.1594375 doi: 10.1080/01430750.2019.1594375
![]() |
[124] |
Biel W, Jaroszewska A, Stankowski S, et al. (2021) Comparison of yield, chemical composition and farinograph properties of common and ancient wheat grains. Eur Food Res Technol 247: 1525–1538. https://doi.org/10.1007/s00217-021-03729-7 doi: 10.1007/s00217-021-03729-7
![]() |
[125] |
Pineda-Gómez P, González NM, Contreras-Jiménez B, et al. (2021) Physicochemical characterisation of starches from six potato cultivars native to the Colombian andean region. Potato Res 64: 21–39. https://doi.org/10.1007/s11540-020-09462-0 doi: 10.1007/s11540-020-09462-0
![]() |
[126] |
Singh SP, Jawaid M, Chandrasekar M, et al. (2021) Sugarcane wastes into commercial products: Processing methods, production optimization and challenges. J Clean Prod 328: 129453. https://doi.org/10.1016/j.jclepro.2021.129453 doi: 10.1016/j.jclepro.2021.129453
![]() |
[127] |
Ghaffar Y, Ashraf W, Akhtar N, et al. (2022) Estimation of statistical parameters in candidate wheat genotypes for yield-related traits. J King Saud University-Sci 34: 102364. https://doi.org/10.1016/j.jksus.2022.102364 doi: 10.1016/j.jksus.2022.102364
![]() |
[128] | Martínez RD, Cirilo AG, Cerrudo AA, et al. (2022) Environment affects starch composition and kernel hardness in temperate maize. J Sci Food Agric 102: 5488–5494. DOI10.1002/jsfa.1190 |
[129] | Yossa R, Ahmad FN. Kumari J, et al. (2022) Apparent digestibility coefficients of banana peel, cassava peel, cocoa husk, copra waste, and sugarcane bagasse in the GIFT strain of Nile tilapia (Oreochromis niloticus). J Appl Aquaculture 34: 734–754. https://doi.org/10.1080/10454438.2021.1890304 |
[130] |
Liu H, Lin X, Li X, et al. (2023) Haplotype variations of sucrose phosphate synthase B gene among sugarcane accessions with different sucrose content. BMC Genom 24: 1–12. https://doi.org/10.1186/s12864-023-09139-1 doi: 10.1186/s12864-023-09139-1
![]() |
[131] |
Thuppahige VTW, Moghaddam L, Welsh ZG (2023) Investigation of critical properties of Cassava (Manihot esculenta) peel and bagasse as starch-rich fibrous agro-industrial wastes for biodegradable food packaging. Food Chem 422: 136200. https://doi.org/10.1016/j.foodchem.2023.136200 doi: 10.1016/j.foodchem.2023.136200
![]() |
[132] |
Kovač M, Ravnjak B, Šubarić D, et al. (2024) Isolation and characterization of starch from different potato cultivars grown in Croatia. Applied Sci 14: 909. https://doi.org/10.3390/app14020909 doi: 10.3390/app14020909
![]() |
[133] |
Barros FFC, Ponezi AN, Pastore GM (2008) Production of biosurfactant by Bacillus subtilis LB5a on a pilot scale using cassava wastewater as substrate. J Ind Microbiol Biotech 35: 1071–1078. https://doi.org/10.1007/s10295-008-0385-y doi: 10.1007/s10295-008-0385-y
![]() |
[134] |
Fleck L, Tavares MH, Eyng E, et al. (2017) Optimization of anaerobic treatment of cassava processing wastewater. Engenharia Agríc 37: 574–590. https://doi.org/10.1590/1809-4430-Eng.Agric.v37n3p574-590/2017 doi: 10.1590/1809-4430-Eng.Agric.v37n3p574-590/2017
![]() |
[135] | Santos RJE, da Silva SAM, Martini M, et al. (2019) Rhodotorula glutinis cultivation on cassava wastewater for carotenoids and fatty acids generation. Biocatal Agric Biotechnol. 22: 101419. https://doi.org/10.1016/j.bcab.2019.101419 |
[136] | Muniz, MJ., Santos TT., Ronchesel RM, et al. (2022) Chlorella sorokiniana as bioremediator of wastewater: Nutrient removal, biomass production, and potential profit. Bioresour Technol Rep 17: 100933. https://doi.org/10.1016/j.biteb.2021.100933 |
[137] |
Padi RK, Chimphango A (2020) Commercial viability of integrated waste treatment in cassava starch industries for targeted resource recoveries. J Clean Prod 265: 1–33. https://doi.org/10.1016/j.jclepro.2020.121619 doi: 10.1016/j.jclepro.2020.121619
![]() |
[138] |
Li M, Zhou H, Zi X, et al. (2024) Feeding value assessment of five varieties whole-plant cassava in tropical China. Fermentation 10: 45. https://doi.org/10.3390/fermentation10010045 doi: 10.3390/fermentation10010045
![]() |
[139] |
Parmar A, Sturm B, Hensel O (2017) Crops that feed the world: Production and improvement of cassava for food, feed, and industrial uses. Food Secur 9: 907–927. https://doi.org/10.1007/s12571-017-0717-8 doi: 10.1007/s12571-017-0717-8
![]() |
[140] |
Kombate K, Dansi D, Dossou–Aminon I, et al. (2017) Diversity of cassava (Manihot esculenta Crantz) cultivars in the traditional agriculture of Togo. Int J Curr Res Biosci Plant Biol 4: 98–113. https://doi.org/10.20546/ijcrbp.2017.406.012 doi: 10.20546/ijcrbp.2017.406.012
![]() |
[141] |
Quadros FGS, Gomide IS (2021) Aspectos socioeconômicos e ambientais da produção de farinha de mandioca na comunidade quilombola Amazônica do Cuxiú, Bonito/PA. Nat Conserv 14: 55–61. http://doi.org/10.6008/CBPC2318-2881.2021.001.0006 doi: 10.6008/CBPC2318-2881.2021.001.0006
![]() |
[142] | Achi CG, Coker AO, Sridhar MKC (2018) Cassava processing wastes: options and potentials for resource recovery in Nigeria. In: Ghosh S. Utilization and management of bioresources. Springer, Singapore. p. 77–89 https://doi.org/10.1007/978-981-10-5349-8_8 |
[143] |
Silva PA, Pires AJ, Pina DDS, et al. (2022) Cassava wastewater can be safely used in the diet of feedlot lambs. Anim Prod Sci 62: 601–609. https://doi.org/10.1071/AN20214 doi: 10.1071/AN20214
![]() |
[144] |
Hassan ZM, Manyelo TG, Selaledi L, et al. (2020) The effects of tannins in monogastric animals with special reference to alternative feed ingredients. Mol 25: 4680. https://doi.org/10.3390/molecules25204680. doi: 10.3390/molecules25204680
![]() |
[145] | Apata DF, Babalola TO (2012) The use of cassava, sweet potato and cocoyam, and their by–products by non–ruminants. Int J Food Sci Nutr Eng 2: 54–62. https://www.researchgate.net/publication/233532871_The_Use_of_Cassava_Sweet_Potato_and_Cocoyam_and_Their_By-Products_by_Non_-_Ruminants |
[146] | Okike I, Wigboldus S, Samireddipalle A, et al. (2022) Turning waste to wealth: harnessing the potential of cassava peels for nutritious animal feed. In: Thiele G, Friedmann M, Campos H, Polar V, Bentley JW. editors. Root, Tuber and Banana Food System Innovations. Springer Cham, 173–206. https://doi.org/10.1007/978-3-030-92022-7 |
[147] |
Marin ME, Zajul M, Goldman M, et al. (2020) Effects of solid–state fermentation and the potential use of cassava by–products as fermented food. Waste Biomass Valor 11: 1289–1299 https://doi.org/10.1007/s12649-018-0479-3 doi: 10.1007/s12649-018-0479-3
![]() |
[148] |
de Souza AP, da Silva PGP, de Souza AS, et al. (2020) Changes in biochemical composition of cassava and beet residues during solid state bioprocess with Pleurotus ostreatus. Biocatal Agric Biotechnol 26: 1–8. https://doi.org/10.1016/j.bcab.2020.101641 doi: 10.1016/j.bcab.2020.101641
![]() |
[149] |
Morm S, Lunpha A, Pilajun R, et al. (2023) Gas kinetics, rumen characteristics, and in vitro degradability of varied levels of dried and fresh cassava leaf top fermented with cassava pulp. Tropical Anim Sci J 46: 105–111. https://doi.org/10.5398/tasj.2023.46.1.105 doi: 10.5398/tasj.2023.46.1.105
![]() |
[150] | Contino–Esquijerosa Y, Herrera–González R, Ojeda–García F, et al. (2017) Evaluación del comportamiento productivo en cerdos en crecimiento alimentados con una dieta no convencional. Pastos y Forrajes 40: 152–157. http://scielo.sld.cu/scielo.php?pid = S0864-03942017000200009 & script = sci_arttext & tlng = pt |
[151] |
Williams GA, Akinola OS, Adeleye TM, et al. (2023) Processed cassava peel–leaf blends: effect on performance, carcass yield, organ weights and ileal microflora of growing pigs. Anim Prod Sci 63: 751–760. https://doi.org/10.1071/AN22101 doi: 10.1071/AN22101
![]() |
[152] | Adiaha MS (2017) Potential of cassava peel as a biotechnical nutrient carrier for organic fertilizer production to increase crop production and soil fertility. World Sci News 72: 103–107. https://www.infona.pl/resource/bwmeta1.element.psjd-7cbacb46-5426-45a3-9103-e81f1933267b |
[153] |
Syamala C, Kuzhivilayil SJ, Nair MM, et al. (2017) Management of cassava starch factory solid waste (thippi) through composting to a nutrient-rich organic manure. Commun Soil Sci Plant Anal 48: 595–607. http://dx.doi.org/10.1080/00103624.2016.1243700 doi: 10.1080/00103624.2016.1243700
![]() |
[154] |
Makinde EA, Salau AW (2017) Fortified cassava peel compost amendment for Amaranthus: influence on plant growth, nutrients uptake and on soil nutrient changes. J Plant Nutr 40: 645–655. https://doi.org/10.1080/01904167.2016.1245328 doi: 10.1080/01904167.2016.1245328
![]() |
[155] | Nguefack J, Onguene D, Lekagne JD, et al. (2022) Effect of aqueous extract of clove basil (Ocimum gratissimum L.) and soil amendment with cassava peels compost on nutrients, pesticide residues, yield and antioxidant properties of sweet pepper (Capsicum annuum L.). Sci Hortic 295: 110872. https://doi.org/10.1016/j.scienta.2021.110872 |
[156] |
Oo AN, Iwai CB, Saenjan P (2015) Soil properties and maize growth in saline and nonsaline soils using cassava–industrial waste compost and vermicompost with or without earthworms. L Degrad Dev 26: 300–310. https://doi.org/10.1002/ldr.2208 doi: 10.1002/ldr.2208
![]() |
[157] |
Bezerra MGDS, da Silva GG, Difante GDS, et al. (2019) Chemical attributes of soil under cassava wastewater application in Marandugrass cultivation. Revista Brasileira de Engenharia Agrícola e Ambiental 23: 579–585. https://doi.org/10.1590/1807-1929/agriambi.v23n8p579-585 doi: 10.1590/1807-1929/agriambi.v23n8p579-585
![]() |
[158] |
Ghimire A, Frunzo L, Pirozzi F, et al. (2015) A review on dark fermentative biohydrogen production from organic biomass: process parameters and use of by-products. Applied Energy 144: 73–95. DOI: 10.1016/j.apenergy.2015.01.045 doi: 10.1016/j.apenergy.2015.01.045
![]() |
[159] |
Zanatta ER, Reinehr TO, Awadallak JA, et al. (2016) Kinetic studies of thermal decomposition of sugarcane bagasse and cassava bagasse. J Therm Anal Calorim 125: 437–445. https://doi.org/10.1007/s10973-016-5378-x doi: 10.1007/s10973-016-5378-x
![]() |
[160] |
Cruz G, Rodríguez ADLP, da Silva DF, et al. (2020) Physical–chemical characterization and thermal behavior of cassava harvest waste for application in thermochemical processes. J Therm Anal Calorim 143: 1–12. https://doi.org/10.1007/s10973-020-09330-6 doi: 10.1007/s10973-020-09330-6
![]() |
[161] | Aruwajoye GS, Sewsynker–Sukai Y, Kana EG (2020b) Valorisation of cassava peels through simultaneous saccharification and ethanol production: Effect of prehydrolysis time, kinetic assessment and preliminary scale up. Fuel 278: 118351. https://doi.org/10.1016/j.fuel.2020.118351 |
[162] |
García-Velásquez CA, Daza L, Cardona CA (2020) Economic and energy valorization of cassava stalks as feedstock for ethanol and electricity production. BioEnergy Res 13: 810–823. https://doi.org/10.1007/s12155-020-10098-8 doi: 10.1007/s12155-020-10098-8
![]() |
[163] | Kumar B, Bhardwaj N, Agrawal K, et al. (2020) Bioethanol production: generation–based comparative status measurements. In: Srivastava, N., Srivastava, M., Mishra, P., Gupta, V. editors. Biofuel production technologies: critical analysis for sustainability. Clean Energy Prod Technol Springer, Singapore. p. 155–201. https://doi.org/10.1007/978-981-13-8637-4_7 |
[164] |
Jusakulvijit P, Bezama A, Thrän D (2021) Availability and assessment of potential agricultural residues for the regional development of second-generation bioethanol in Thailand. Waste Biomass Valor 12: 6091–6118. https://doi.org/10.1007/s12649-021-01424-y doi: 10.1007/s12649-021-01424-y
![]() |
[165] | Adeleke KM, Itabiyi OE, Ilori OO (2018) Temperature effect on the product yield from pyrolysis of cassava peels. Int J Sci Eng Res 9: 953. https://www.ijser.org/researchpaper/Temperature-Effect-on-the-Products-Yield-from-Pyrolysis-of-Cassava-Peels.pdf |
[166] |
Budzianowski WM (2017) High–value low–volume bioproducts coupled to bioenergies with potential to enhance business development of sustainable biorefineries. Renew Sustain Energy Rev 70(December 2016): 793–804. https://doi.org/10.1016/j.rser.2016.11.260 doi: 10.1016/j.rser.2016.11.260
![]() |
[167] | Rodrigues ADLP, Sousa AVS, Braz CEM, et al. (2018) Physical–chemical and thermal characterization of cassava harvest residues for application in combustion and pyrolysis processes. In: X Congreso Nacional de Engenharia Mecánica, 20 al 24 de mayo 2018. https://scholar.google.com.mx/scholar?hl = es & as_sdt = 0%2C5 & as_vis = 1 & q = Physical-chemical+and+thermal+characterization+of+cassava+harvest+residues+ & btnG = |
[168] | Ray RC (2024) Roots, Tubers, and Bulb Crop Wastes: Management by Biorefinery Approaches Springer Singapore 1: 1–374. https://doi.org/10.1007/978-981-99-8266-0 |
[169] |
Escaramboni B, Núñez EGF, Carvalho AFA, et al. (2018) Ethanol biosynthesis by fast hydrolysis of cassava bagasse using fungal amylases produced in optimized conditions. Ind Crops Prod 112: 368–377. https://doi.org/10.1016/j.indcrop.2017.12.004 doi: 10.1016/j.indcrop.2017.12.004
![]() |
[170] | Ayutthaya PPN, Charoenrat T, Krusong W, et al. (2019) Repeated cultures of Saccharomyces cerevisiae SC90 to tolerate inhibitors generated during cassava processing waste hydrolysis for bioethanol production. 3 Biotech 9: 1–13. https://doi.org/10.1007/s13205-019-1607-x |
[171] |
Polachini TC, Fachin L, Betiol L, et al. (2016) Water adsorption isotherms and thermodynamic properties of cassava bagasse. Thermochim Acta 632: 79–85. https://doi.org/10.1016/j.tca.2016.03.032 doi: 10.1016/j.tca.2016.03.032
![]() |
[172] |
Hasselmann VI, Lisboa MGL, Pereira FS, et al. (2018) Cassava pulp enzymatic hydrolysate as a promising feedstock for ethanol production. Braz Arch Biol Technol 61: 1–10. https://doi.org/10.1590/1678-4324-2018161214 doi: 10.1590/1678-4324-2018161214
![]() |
[173] |
Huang J, Du Y, Bao T, et al. (2019) Production of n–butanol from cassava bagasse hydrolysate by engineered Clostridium tyrobutyricum overexpressing adhE2: kinetics and cost analysis. Bioresour Technol 292: 1–7. 121969. https://doi.org/10.1016/j.biortech.2019.121969 doi: 10.1016/j.biortech.2019.121969
![]() |
[174] |
Madadi M, Wang Y, Xu C, et al. (2021) Using Amaranthus green proteins as universal biosurfactant and biosorbent for effective enzymatic degradation of diverse lignocellulose residues and efficient multiple trace metals remediation of farming lands. J Hazard Mater 406: 124727. https://doi.org/10.1016/j.jhazmat.2020.124727 doi: 10.1016/j.jhazmat.2020.124727
![]() |
[175] |
Lyu H, Zhang J, Zhou J, et al. (2019) The byproduct-organic acids strengthened pretreatment of cassava straw: Optimization and kinetic study. Bioresource techn 290: 121756. https://doi.org/10.1016/j.biortech.2019.121756 doi: 10.1016/j.biortech.2019.121756
![]() |
[176] | Olaniyan AM, Olawale TT, Alabi KP, et al. (2017) Design, construction and testing of a biogas reactor for production of biogas using cassava peel and cow dung as biomass. Arid Zone J Eng Technol Environ 13: 478–488. https://www.researchgate.net/publication/320842514_Design_Construction_and_Testing_of_a_Biogas_Reactor_for_Production_of_Biogas_using_Cassava_Peel_and_Cow_Dung_as_Biomass |
[177] |
Varongchayakul S, Songkasiri W, Chaiprasert P (2021) Optimization of cassava pulp pretreatment by liquid hot water for biomethane production. BioEner Res 14: 1312–1327. https://doi.org/10.1007/s12155-020-10238-0 doi: 10.1007/s12155-020-10238-0
![]() |
[178] |
Kabir G, Hameed BH (2017) Recent progress on catalytic pyrolysis of lignocellulosic biomass to high–grade bio–oil and bio–chemicals. Renew and Sustain Energy Rev 70(December 2016): 945–967. https://doi.org/10.1016/j.rser.2016.12.001 doi: 10.1016/j.rser.2016.12.001
![]() |
[179] |
Rueangsan K, Suwapaet N, Pattiya A (2018) Bio–oil production by fast pyrolysis of cassava residues in a free–fall reactor using liquid media–assisted condensation. Energy Sour Part A: Recovery Utilization Environ Eff 40: 615–622. https://doi.org/10.1080/15567036.2018.1440874 doi: 10.1080/15567036.2018.1440874
![]() |
[180] |
Wu J, Yang J, Huang G, et al. (2020) Hydrothermal carbonization synthesis of cassava slag biochar with excellent adsorption performance for Rhodamine B. J Clean Prod 251: 119717. https://doi.org/10.1016/j.jclepro.2019.119717 doi: 10.1016/j.jclepro.2019.119717
![]() |
[181] | OECD/FAO (2022) OECD-FAO Agricultural Outlook 2022-2031, OECD Publishing, Paris, https://doi.org/10.1787/f1b0b29c-en |
[182] | Ohimain EI, Silas–Olu DI, Zipamoh JT (2013) Biowastes generation by small scale cassava processing centres in Wilberforce Island, Bayelsa State, Nigeria. Gr J of Environ Manag and Public Saf 2: 51–59. https://www.researchgate.net/publication/236247754_Biowastes_Generation_by_Small_Scale_Cassava_Processing_Centres_in_Wilberforce_Island_Bayelsa_State_Nigeria |
[183] | Niyomvong N, Boondaeng A (2019) Ethanol production from cassava stem using Saccharomyces cerevisiae TISTR 5339 through simultaneous saccharification and fermentation. Agric Nat Resour 53: 667–673. https://li01.tci-thaijo.org/index.php/anres/article/view/232624 |
[184] |
Ajala AS, Adeoye AO, Olaniyan SA, et al. (2020) A study on effect of fermentation conditions on citric acid production from cassava peels. Sci Afr 8: 1–6. https://doi.org/10.1016/j.sciaf.2020.e00396 doi: 10.1016/j.sciaf.2020.e00396
![]() |
[185] |
Rogoski W, Pereira GN, Cesca K, et al. (2023) An overview on pretreatments for the production of cassava peels-based xyloligosaccharides: State of art and challenges. Waste Biomass Valorization 14: 2115–2131. https://doi.org/10.1007/s12649-023-02044-4 doi: 10.1007/s12649-023-02044-4
![]() |
[186] |
He CW, Wei JH, Zeng LY, et al. (2020) Triterpenoids and flavonoids from cassava leaves. Chem Nat Compd 56: 331–333. https://doi.org/10.1007/s10600-020-03022-1 doi: 10.1007/s10600-020-03022-1
![]() |
[187] |
Abotbina W, Sapuan SM, Sultan MTH, et al. (2022) Extraction, characterization, and comparison of properties of cassava bagasse and black seed fibers. J Nat Fibers 19: 14525–14538. https://doi.org/10.1080/15440478.2022.2068103 doi: 10.1080/15440478.2022.2068103
![]() |
[188] |
Aisien FA, Amenaghawon AN, Bienose KC (2015) Particle boards produced from cassava stalks: Evaluation of physical and mechanical properties. S Afr J Sci 111: 1–4. http://dx.doi.org/10.17159/sajs.2015/20140042 doi: 10.17159/sajs.2015/20140042
![]() |
[189] |
Qiu Y, Wang F, Ma X, et al. (2023) Carbon quantum dots derived from cassava stems via acid/alkali-assisted hydrothermal carbonization: formation, mechanism and application in drug release. Ind Crops Prod 204: 117243. https://doi.org/10.1016/j.indcrop.2023.11724 doi: 10.1016/j.indcrop.2023.11724
![]() |
[190] |
Aisien FA, Amenaghawon AN, Onyekezine FD (2013) Roofing sheets produced from cassava stalks and corn cobs: evaluation of physical and mechanical properties. Int J Sci Res Knowl 1: 521–527. http://dx.doi.org/10.12983/ijsrk-2013-p521-527 doi: 10.12983/ijsrk-2013-p521-527
![]() |
[191] | Bokanisereme UF, Okechukwu PN (2013) Anti–inflammatory, analgesic and anti–pyretic activity of cassava leaves extract. Asian J Pharm Clin Res 6: 89–92. https://www.academia.edu/es/50486819/Anti_Inflammatory_Analgesic_and_Anti_Pyretic_Activity_of_Cassava_Leaves_Extract |
[192] | Abiaziem CV, Ojelade IA (2019) Cassava peel wax: its extraction and characterization. J Chem Bio Phys Sci 9: 316–322. http://eprints.federalpolyilaro.edu.ng/345/ |
[193] |
Zhang C, Ali KRA, Wei H, et al. (2022) Rapid and mass production of biopesticide Trichoderma Brev T069 from cassava peels using newly established solid-state fermentation bioreactor system. J Environ manag 313: 114981. https://doi.org/10.1016/j.jenvman.2022.114981 doi: 10.1016/j.jenvman.2022.114981
![]() |
[194] | Attahdaniel EB, Enwerem PO, Lawrence PG, et al. (2020) Green synthesis and characterization of sodium cyanide from cassava (Manihot esculenta Crantz). FUW Trends Sci Technol J 5: 247–251. |
[195] |
Roza L, Fauzia V, Rahman MYA, (2020) ZnO nanorods decorated with carbon nanodots and its metal doping as efficient photocatalyst for degradation of methyl blue solution. Optical Mater 109: 110360. https://doi.org/10.1016/j.optmat.2020.110360 doi: 10.1016/j.optmat.2020.110360
![]() |
[196] | Adebisi JA, Agunsoye JO, Bello SA, et al. (2019) Extraction of silica from sugarcane bagasse, cassava periderm and maize stalk: Proximate analysis and physico-chemical properties of wastes. Waste Biomass Valor 10: 617–629. https://doi.org/10.1007/s12649-017-0089-5 |
[197] |
Sopapan P, Laopaiboon R, Laopaiboon J, et al. (2020) Study of bagasse and cassava rhizome effects on the physical, mechanical and structural properties of soda–lime borate glasses. SN Appl Sci 2: 1–10. https://doi.org/10.1007/s42452-020-2721-4 doi: 10.1007/s42452-020-2721-4
![]() |
[198] | Diabor E (2017) Isolation and characterization of cassava fibre for tissue engineering scaffold application[doctoral dissertation]. Legon (Ghana): University of Ghana, College of Basic and Applied Sciences, Department of Biomedical engineering. 139 p. https://inis.iaea.org/search/search.aspx?orig_q = RN: 52026537 |
1. | Jeyrald Jefferson Cay, Gerald Baniaga, Client William Malinao, Local Production Techniques and Sensory Evaluation of Cassava Wine, 2025, 3, 29848288, 10.69569/jip.2025.090 |
Item % | Tuberous root | Leaves | |||
Fresh | Dried | Fresh | Sundried whole | Dried milled | |
Protein | 0.01–1.45 | 1.89–2.21 | 2.92–15.96 | 22.3 | 19.9–20.4 |
Fat | 0.28–0.88 | - | 0.59 | - | - |
Crude fiber | 1.01–2.11 | - | 5.8–16.36 | 20.6 | - |
Ash | 0.62–1.89 | - | 1.7–2.3 | 7.1 | 8.4 |
Carbohydrates | 23.14–38.06 | 65.9–71.50 | 56.3–80.2 | - | 18.4–21.8 |
Insoluble dietary fiber | 3.7–6.4 | - | - | - | |
Soluble dietary fiber | 1.8 | 0.7–1.3 | - | - | - |
Indispensable AA | |||||
Histidine | 0.02 | 0.02–0.03 | 0.68 | 0.5 | 0.5 |
Isoleucine | 0.027 | 0.06–0.07 | 1.44 | 1 | 0.9 |
Leucine | 0.039 | 0.08–0.1 | 2.72 | 1.8 | 1.79–3.03 |
Lysine | 0.044 | 0.07–0.09 | 1.77 | 1.2 | 1.2–2.33 |
Methionine | 0.011 | 0.01–0.02 | 0.58 | 0.4 | 0.37–0.67 |
Phenylalanine | 0.026 | 0.05–0.06 | 1.8 | 1.3 | 1.1 |
Threonine | 0.028 | 0.05–0.07 | 1.41 | 1 | 0.9 |
Tryptophan | 0.019 | 0.03 | 0.55 | 0.8 | 0.6 |
Valine | 0.035 | 0.06–0.08 | 1.71 | 1.7 | 1.1 |
Dispensable AA | |||||
Arginine | 0.137 | 0.05–0.08 | 1.7 | 1.3 | 1.1 |
Alanine | 0.038 | 0.11 | 1.74 | 1.3 | 1.2–2.4 |
Aspartic acid | 0.079 | 0.13–0.14 | 2.57 | 3.2 | 1.98–3.32 |
Cysteine | 0.028 | 0.01 | 0.47 | 0.3 | 0.23–0.34 |
Glutamic acid | 0.206 | 0.25–0.3 | 3.05 | 3 | 2.39–4.21 |
Glycine | 0.028 | 0.06–0.07 | 1.59 | 1 | 1 |
Proline | 0.033 | 0.07–0.08 | 1.35 | 1.1 | 1.1 |
Serine | 0.033 | 0.05–0.06 | 1.35 | 1.2 | 1 |
Tyrosine | 0.017 | 0.02–0.03 | 1.24 | 0.9 | 0.8 |
Minerals | |||||
Ca | 0.016 | 0.12–0.18 | 0.50 | 0.57 | 0.39 |
P | 0.027 | 0.12–0.15 | |||
Mg | 0.021 | 0.06–0.10 | 0.15 | 0.16 | 0.08 |
K | 0.271 | 0.74–0.90 | 0.78 | 0.96 | 0.01 |
Na | 0.014 | 0.01 | |||
S | 0.021 | 0.04–0.05 | |||
Cooper (mg kg-1) | 1 | 1.9–4.31 | 401 | 509 | 243 |
Iron (mg kg-1) | 2.7 | 114.38–146.69 | |||
Manganese (mg kg-1) | 3.84 | 6.80–9.89 | 203 | 392 | 59 |
Zinc (mg kg-1) | 3.4 | 8.11–17.4 | 50 | 71.8 | 32.8 |
Dah–Sol & Fumiko [61]: Boakye et al. [65]; da Silva et al. [67]; Boundy–Mills et al. [77]; USDA [78]; Mardina et al. [79]; Chaiareekitwat et al., [80]; Gurdensen et al. [81]; Fanelli et al. [82]. |
Crop | Cassava | Sugarcane | Corn | Potato | Wheat | Rice |
Biomass (t ha-1 of product marketed) | ||||||
12.65 | 78.53 | 4.81 | 21.72 | 2–4.8 | 4.1 | |
Yield of starch (%) | ||||||
20.94–43.43 | 8.4–16.26a | 66.6–74.4 | 17.26–22.49 | 57 | 76.06–81.66 | |
Bagasse (%) | ||||||
Proportion in root | 30–40 | 26–29 | 67–74e | - | 67–72d | - |
Fiber | 19 | 37.71 | 86–88e | - | - | - |
Starch | 10.3–47 | - | - | - | - | |
Lipids | 0.47 | 2 | - | - | - | - |
Protein | 1.03–2.37 | 1.79 | - | - | - | - |
Ash | 0.16–1.8 | 1.35–8 | - | - | - | - |
Cellulose | 19.4–31.47 | 32–48 | 24–40 | - | 39–45d | - |
Hemicellulose | 0.53–31.3 | 23–32 | 44–55 | - | 25.6–37d | - |
Lignin | 0.4–22 | 13–24 | 9.5–23 | - | 23–28.3d | - |
Peel (%) | ||||||
Proportion in root | 19.41–24.52 | - | - | - | ||
Fiber | 10.15 | - | - | - | ||
Starch | 30.17 | - | - | 16.6–39.7 | - | |
Lipids | 0.67 | - | - | 7.33 | - | 0.3b |
Protein | 1.86–4.8 | - | - | 9.46–25.4 | - | 1.96b |
Ash | 7.78–9.5 | - | 3–4c | 5.82–11.1 | - | 0.36b |
Cellulose | 25.8–38.2 | - | 34–36c | 7.8 | - | 38.6b |
Hemicellulose | 11.6–31.4 | - | 36c | 14.7 | - | 24.9b |
Lignin | 4.29–13.9 | - | 19.2c | 21.6 | - | 18.6b |
a Sucrose, b Husk, c Cob, d Straw ande Stover. FAOstat [6]; de Souza et al. [57]; Boakye et al., [65]; Gundersen et al. [81]; Del Rosario–Arellano et al. [109]; Benesi et al. [117]; Liang et al. [118]; Mangla et al. [119]; Vargas & Pérez et al. [120]; Cao et al. [121]; Park et al. [122]; Awoyale et al. [123]; Biel et al., [124]: Pineda–Gómez et al. [125]; Singh et al. [126]; Ghaffar et al. [127]; Martínez et al. [128]; Yossa et al. [129]; Liu et al., [130]; Thuppahige, et al. [131]; Kovač et al. [132]. |
Parameter | Value | Parameter | Value |
pH | 4.20–5.98 | Potassium (mg mL-1) | 894–1247.92 |
Free cyanide (mg L-1) | 3 | Zinc (mg mL-1) | 1.4–1.83 |
DOC (g O2 L-1) | 61.27 | Iron (mg mL-1) | 4.2–15.37 |
Reducing sugars (g L-1) | 13.9–40.60 | Copper (mg mL-1) | 0.3–1.51 |
Non-reducing sugars (g L-1) | 17.51 | Sulfur (mg mL-1) | 150 |
Total carbohydrates (g L-1) | 36.20–58.11 | Aluminum (mg mL-1) | 148 |
Total nitrogen (g L-1) | 1.92–1.99 | Boron | 4 |
Dry material (g 10 mL-1) | 9.51 | Cadmium | < 0.01 |
Calcium (mg mL-1) | 212–241.62 | Chromium | < 0.01 |
Magnesium (mg mL-1) | 288–370.59 | Nickel | < 0.01 |
Manganese (mg mL-1) | 1.6 | Ammonia [NH4+] (mg L-1) | 131 |
Phosphorus (mg mL-1) | 83–246 | Nitrate [NO3-] (mg L-1) | 16.2 |
Sodium (mg mL-1) | 147.55 | ||
Source: Barros et al. [133]; Fleck et al. [134]; Santos et al. [135]. |
Co–product | Application | Result | Author |
Stems | Chipboard | Agromertified boards were produced with cassava stems and urea–formaldehyde adhesive at a 3:1 ratio, with properties of low water absorption (20 %), swelling thickness (6.26 %) in addition to high values of modulus of rupture (4×106 N m2), and elasticity (2366.74×106 N m2). | Aisien et al. [188]. |
Stems | Carbon quantum dots | Carbon quantum dots were produced by acid/alkali treatments and hydrothermal carbonization, with potential application for drug delivery. | Qiu et al. [189]. |
Stalk | Roofing sheets | Stable roofing sheets were produced by combining the co–products of cassava stems with corn cobs plus glues of animal origin and the use of PVC as a binder. | Aisien et al., [190]. |
Leaves | Medicinal use | Medicinal use through leaf extract (100,250, and 500 mg kg-1) with anti–inflammatory, antipyretic, and analgesic activity. | Bokanisereme & Okechukwu [191]. |
Peel | Wax | With the soxhlet extraction method with benzene and ethanol, it is possible to produce 8.51 % of crude wax, with potential application in the pharmaceutical, cosmetic, paint, and food industries. | Abiaziem & Ojelade [192]. |
Peel | Biopesticides | The peel as a substrate for the production of Trichoderma Brev T069, with a yield of 250 kg (2.89×109 spores/g) in a bioreactor, with control activity on the Fusarium wilt of banana. | Zhang et al. [193]. |
Peel | Sodium cyanide | Sodium cyanide was obtained from direct hydrolysis with better purity compared to its analytical grade counterpart, a green chemistry technique that promotes environmentally friendly, simple, and cost–effective synthesis. | Attahdaniel et al. [194]. |
Peel | ZnO nanorods decorated with carbon nanodots to degrade methylene blue | ZnO nanowires decorated with carbon nanodots were manufactured as a photocatalyst for the degradation of methyl blue, through the green chemistry technique which consisted of simple carbonization of cassava peel at low temperatures followed by an aging process for 6 days in absolute ethanol. | Roza et al. [195]. |
Tuberous root peridermis | Silicon | A silicon content of 6.10 % was reported in the ashes of cassava peridermis, a useful raw material for the pharmaceutical sector, archeology, biomedicine, and electronics (semiconductors). | Adebisi et al. [196]. |
Bagasse and rhizomes | Glass | The addition of bagasse ash and cassava rhizomes (0–10 %) are useful materials in the production of glass bottles. | Sopapan et al. [197]. |
Bagasse | Tissue engineering scaffold | Cassava fibers exhibit considerable strength and stiffness that can be oriented as a filler and reinforcing agent in the mechanical integrity of tissue–engineered polymer scaffolds. | Diabor (2017) [198]. |
Item % | Tuberous root | Leaves | |||
Fresh | Dried | Fresh | Sundried whole | Dried milled | |
Protein | 0.01–1.45 | 1.89–2.21 | 2.92–15.96 | 22.3 | 19.9–20.4 |
Fat | 0.28–0.88 | - | 0.59 | - | - |
Crude fiber | 1.01–2.11 | - | 5.8–16.36 | 20.6 | - |
Ash | 0.62–1.89 | - | 1.7–2.3 | 7.1 | 8.4 |
Carbohydrates | 23.14–38.06 | 65.9–71.50 | 56.3–80.2 | - | 18.4–21.8 |
Insoluble dietary fiber | 3.7–6.4 | - | - | - | |
Soluble dietary fiber | 1.8 | 0.7–1.3 | - | - | - |
Indispensable AA | |||||
Histidine | 0.02 | 0.02–0.03 | 0.68 | 0.5 | 0.5 |
Isoleucine | 0.027 | 0.06–0.07 | 1.44 | 1 | 0.9 |
Leucine | 0.039 | 0.08–0.1 | 2.72 | 1.8 | 1.79–3.03 |
Lysine | 0.044 | 0.07–0.09 | 1.77 | 1.2 | 1.2–2.33 |
Methionine | 0.011 | 0.01–0.02 | 0.58 | 0.4 | 0.37–0.67 |
Phenylalanine | 0.026 | 0.05–0.06 | 1.8 | 1.3 | 1.1 |
Threonine | 0.028 | 0.05–0.07 | 1.41 | 1 | 0.9 |
Tryptophan | 0.019 | 0.03 | 0.55 | 0.8 | 0.6 |
Valine | 0.035 | 0.06–0.08 | 1.71 | 1.7 | 1.1 |
Dispensable AA | |||||
Arginine | 0.137 | 0.05–0.08 | 1.7 | 1.3 | 1.1 |
Alanine | 0.038 | 0.11 | 1.74 | 1.3 | 1.2–2.4 |
Aspartic acid | 0.079 | 0.13–0.14 | 2.57 | 3.2 | 1.98–3.32 |
Cysteine | 0.028 | 0.01 | 0.47 | 0.3 | 0.23–0.34 |
Glutamic acid | 0.206 | 0.25–0.3 | 3.05 | 3 | 2.39–4.21 |
Glycine | 0.028 | 0.06–0.07 | 1.59 | 1 | 1 |
Proline | 0.033 | 0.07–0.08 | 1.35 | 1.1 | 1.1 |
Serine | 0.033 | 0.05–0.06 | 1.35 | 1.2 | 1 |
Tyrosine | 0.017 | 0.02–0.03 | 1.24 | 0.9 | 0.8 |
Minerals | |||||
Ca | 0.016 | 0.12–0.18 | 0.50 | 0.57 | 0.39 |
P | 0.027 | 0.12–0.15 | |||
Mg | 0.021 | 0.06–0.10 | 0.15 | 0.16 | 0.08 |
K | 0.271 | 0.74–0.90 | 0.78 | 0.96 | 0.01 |
Na | 0.014 | 0.01 | |||
S | 0.021 | 0.04–0.05 | |||
Cooper (mg kg-1) | 1 | 1.9–4.31 | 401 | 509 | 243 |
Iron (mg kg-1) | 2.7 | 114.38–146.69 | |||
Manganese (mg kg-1) | 3.84 | 6.80–9.89 | 203 | 392 | 59 |
Zinc (mg kg-1) | 3.4 | 8.11–17.4 | 50 | 71.8 | 32.8 |
Dah–Sol & Fumiko [61]: Boakye et al. [65]; da Silva et al. [67]; Boundy–Mills et al. [77]; USDA [78]; Mardina et al. [79]; Chaiareekitwat et al., [80]; Gurdensen et al. [81]; Fanelli et al. [82]. |
Crop | Cassava | Sugarcane | Corn | Potato | Wheat | Rice |
Biomass (t ha-1 of product marketed) | ||||||
12.65 | 78.53 | 4.81 | 21.72 | 2–4.8 | 4.1 | |
Yield of starch (%) | ||||||
20.94–43.43 | 8.4–16.26a | 66.6–74.4 | 17.26–22.49 | 57 | 76.06–81.66 | |
Bagasse (%) | ||||||
Proportion in root | 30–40 | 26–29 | 67–74e | - | 67–72d | - |
Fiber | 19 | 37.71 | 86–88e | - | - | - |
Starch | 10.3–47 | - | - | - | - | |
Lipids | 0.47 | 2 | - | - | - | - |
Protein | 1.03–2.37 | 1.79 | - | - | - | - |
Ash | 0.16–1.8 | 1.35–8 | - | - | - | - |
Cellulose | 19.4–31.47 | 32–48 | 24–40 | - | 39–45d | - |
Hemicellulose | 0.53–31.3 | 23–32 | 44–55 | - | 25.6–37d | - |
Lignin | 0.4–22 | 13–24 | 9.5–23 | - | 23–28.3d | - |
Peel (%) | ||||||
Proportion in root | 19.41–24.52 | - | - | - | ||
Fiber | 10.15 | - | - | - | ||
Starch | 30.17 | - | - | 16.6–39.7 | - | |
Lipids | 0.67 | - | - | 7.33 | - | 0.3b |
Protein | 1.86–4.8 | - | - | 9.46–25.4 | - | 1.96b |
Ash | 7.78–9.5 | - | 3–4c | 5.82–11.1 | - | 0.36b |
Cellulose | 25.8–38.2 | - | 34–36c | 7.8 | - | 38.6b |
Hemicellulose | 11.6–31.4 | - | 36c | 14.7 | - | 24.9b |
Lignin | 4.29–13.9 | - | 19.2c | 21.6 | - | 18.6b |
a Sucrose, b Husk, c Cob, d Straw ande Stover. FAOstat [6]; de Souza et al. [57]; Boakye et al., [65]; Gundersen et al. [81]; Del Rosario–Arellano et al. [109]; Benesi et al. [117]; Liang et al. [118]; Mangla et al. [119]; Vargas & Pérez et al. [120]; Cao et al. [121]; Park et al. [122]; Awoyale et al. [123]; Biel et al., [124]: Pineda–Gómez et al. [125]; Singh et al. [126]; Ghaffar et al. [127]; Martínez et al. [128]; Yossa et al. [129]; Liu et al., [130]; Thuppahige, et al. [131]; Kovač et al. [132]. |
Parameter | Value | Parameter | Value |
pH | 4.20–5.98 | Potassium (mg mL-1) | 894–1247.92 |
Free cyanide (mg L-1) | 3 | Zinc (mg mL-1) | 1.4–1.83 |
DOC (g O2 L-1) | 61.27 | Iron (mg mL-1) | 4.2–15.37 |
Reducing sugars (g L-1) | 13.9–40.60 | Copper (mg mL-1) | 0.3–1.51 |
Non-reducing sugars (g L-1) | 17.51 | Sulfur (mg mL-1) | 150 |
Total carbohydrates (g L-1) | 36.20–58.11 | Aluminum (mg mL-1) | 148 |
Total nitrogen (g L-1) | 1.92–1.99 | Boron | 4 |
Dry material (g 10 mL-1) | 9.51 | Cadmium | < 0.01 |
Calcium (mg mL-1) | 212–241.62 | Chromium | < 0.01 |
Magnesium (mg mL-1) | 288–370.59 | Nickel | < 0.01 |
Manganese (mg mL-1) | 1.6 | Ammonia [NH4+] (mg L-1) | 131 |
Phosphorus (mg mL-1) | 83–246 | Nitrate [NO3-] (mg L-1) | 16.2 |
Sodium (mg mL-1) | 147.55 | ||
Source: Barros et al. [133]; Fleck et al. [134]; Santos et al. [135]. |
Co–product | Application | Result | Author |
Stems | Chipboard | Agromertified boards were produced with cassava stems and urea–formaldehyde adhesive at a 3:1 ratio, with properties of low water absorption (20 %), swelling thickness (6.26 %) in addition to high values of modulus of rupture (4×106 N m2), and elasticity (2366.74×106 N m2). | Aisien et al. [188]. |
Stems | Carbon quantum dots | Carbon quantum dots were produced by acid/alkali treatments and hydrothermal carbonization, with potential application for drug delivery. | Qiu et al. [189]. |
Stalk | Roofing sheets | Stable roofing sheets were produced by combining the co–products of cassava stems with corn cobs plus glues of animal origin and the use of PVC as a binder. | Aisien et al., [190]. |
Leaves | Medicinal use | Medicinal use through leaf extract (100,250, and 500 mg kg-1) with anti–inflammatory, antipyretic, and analgesic activity. | Bokanisereme & Okechukwu [191]. |
Peel | Wax | With the soxhlet extraction method with benzene and ethanol, it is possible to produce 8.51 % of crude wax, with potential application in the pharmaceutical, cosmetic, paint, and food industries. | Abiaziem & Ojelade [192]. |
Peel | Biopesticides | The peel as a substrate for the production of Trichoderma Brev T069, with a yield of 250 kg (2.89×109 spores/g) in a bioreactor, with control activity on the Fusarium wilt of banana. | Zhang et al. [193]. |
Peel | Sodium cyanide | Sodium cyanide was obtained from direct hydrolysis with better purity compared to its analytical grade counterpart, a green chemistry technique that promotes environmentally friendly, simple, and cost–effective synthesis. | Attahdaniel et al. [194]. |
Peel | ZnO nanorods decorated with carbon nanodots to degrade methylene blue | ZnO nanowires decorated with carbon nanodots were manufactured as a photocatalyst for the degradation of methyl blue, through the green chemistry technique which consisted of simple carbonization of cassava peel at low temperatures followed by an aging process for 6 days in absolute ethanol. | Roza et al. [195]. |
Tuberous root peridermis | Silicon | A silicon content of 6.10 % was reported in the ashes of cassava peridermis, a useful raw material for the pharmaceutical sector, archeology, biomedicine, and electronics (semiconductors). | Adebisi et al. [196]. |
Bagasse and rhizomes | Glass | The addition of bagasse ash and cassava rhizomes (0–10 %) are useful materials in the production of glass bottles. | Sopapan et al. [197]. |
Bagasse | Tissue engineering scaffold | Cassava fibers exhibit considerable strength and stiffness that can be oriented as a filler and reinforcing agent in the mechanical integrity of tissue–engineered polymer scaffolds. | Diabor (2017) [198]. |