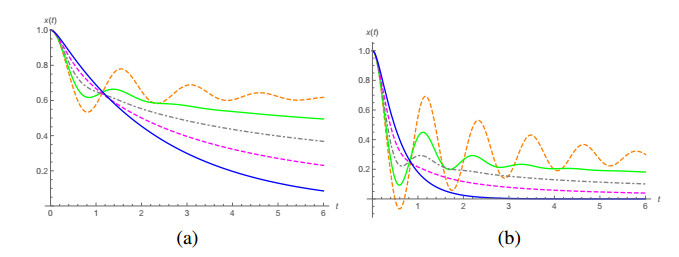
The convergence of additive manufacturing (AM), sustainability, and innovation holds significant importance within the framework of Industry 4.0. This article examines the environmentally friendly and sustainable aspects of AM, more commonly referred to as 3D printing, a cutting-edge technology. It describes the fundamentals of AM in addition to its diverse materials, processes, and applications. This paper demonstrates how several 3D printing techniques can revolutionize sustainable production by examining their environmental impacts. The properties, applications, and challenges of sustainable materials, such as biodegradable polymers and recyclable plastics, are thoroughly examined. Additionally, the research explores the implications of 3D printing in domains including renewable energy component fabrication, water and wastewater treatment, and environmental monitoring. In addition, potential pitfalls and challenges associated with sustainable 3D printing are examined, underscoring the criticality of continuous research and advancement in this domain. To effectively align sustainability goals with functional performance requirements, it is imperative to address complexities within fused deposition modeling (FDM) printing processes, including suboptimal bonding and uneven fiber distribution, which can compromise the structural integrity and durability of biodegradable materials. Ongoing research and innovation are essential to overcome these challenges and enhance the viability of biodegradable FDM 3D printing materials for broader applications.
Citation: Muhammad Ali Saqib, Muhammad Sohail Abbas, Hiroyuki Tanaka. Sustainability and innovation in 3D printing: Outlook and trends[J]. Clean Technologies and Recycling, 2024, 4(1): 1-21. doi: 10.3934/ctr.2024001
[1] | Jianping Li, Leshi Qiu, Jianbin Zhang . Proof of a conjecture on the ϵ-spectral radius of trees. AIMS Mathematics, 2023, 8(2): 4363-4371. doi: 10.3934/math.2023217 |
[2] | Igal Sason . Observations on graph invariants with the Lovász ϑ-function. AIMS Mathematics, 2024, 9(6): 15385-15468. doi: 10.3934/math.2024747 |
[3] | Jahfar T K, Chithra A V . Central vertex join and central edge join of two graphs. AIMS Mathematics, 2020, 5(6): 7214-7233. doi: 10.3934/math.2020461 |
[4] | He Song, Longmin Wang, Kainan Xiang, Qingpei Zang . The continuity of biased random walk's spectral radius on free product graphs. AIMS Mathematics, 2024, 9(7): 19529-19545. doi: 10.3934/math.2024952 |
[5] | Wafaa Fakieh, Zakeiah Alkhamisi, Hanaa Alashwali . On the Aα−-spectra of graphs and the relation between Aα- and Aα−-spectra. AIMS Mathematics, 2024, 9(2): 4587-4603. doi: 10.3934/math.2024221 |
[6] | Sumaira Hafeez, Rashid Farooq . On generalized inverse sum indeg index and energy of graphs. AIMS Mathematics, 2020, 5(3): 2388-2411. doi: 10.3934/math.2020158 |
[7] | Ali Raza, Mobeen Munir, Tasawar Abbas, Sayed M Eldin, Ilyas Khan . Spectrum of prism graph and relation with network related quantities. AIMS Mathematics, 2023, 8(2): 2634-2647. doi: 10.3934/math.2023137 |
[8] | Yufei Huang, Hechao Liu . Bounds of modified Sombor index, spectral radius and energy. AIMS Mathematics, 2021, 6(10): 11263-11274. doi: 10.3934/math.2021653 |
[9] | Maria Adam, Dimitra Aggeli, Aikaterini Aretaki . Some new bounds on the spectral radius of nonnegative matrices. AIMS Mathematics, 2020, 5(1): 701-716. doi: 10.3934/math.2020047 |
[10] | Qin Zhong . Some new inequalities for nonnegative matrices involving Schur product. AIMS Mathematics, 2023, 8(12): 29667-29680. doi: 10.3934/math.20231518 |
The convergence of additive manufacturing (AM), sustainability, and innovation holds significant importance within the framework of Industry 4.0. This article examines the environmentally friendly and sustainable aspects of AM, more commonly referred to as 3D printing, a cutting-edge technology. It describes the fundamentals of AM in addition to its diverse materials, processes, and applications. This paper demonstrates how several 3D printing techniques can revolutionize sustainable production by examining their environmental impacts. The properties, applications, and challenges of sustainable materials, such as biodegradable polymers and recyclable plastics, are thoroughly examined. Additionally, the research explores the implications of 3D printing in domains including renewable energy component fabrication, water and wastewater treatment, and environmental monitoring. In addition, potential pitfalls and challenges associated with sustainable 3D printing are examined, underscoring the criticality of continuous research and advancement in this domain. To effectively align sustainability goals with functional performance requirements, it is imperative to address complexities within fused deposition modeling (FDM) printing processes, including suboptimal bonding and uneven fiber distribution, which can compromise the structural integrity and durability of biodegradable materials. Ongoing research and innovation are essential to overcome these challenges and enhance the viability of biodegradable FDM 3D printing materials for broader applications.
Oscillation is a phenomenon found in various situations and in different areas, and is therefore a phenomenon of fundamental importance in the sciences. The study of the harmonic oscillator problem with damping is a paradigm in the study of oscillations and one of the most important examples of applications of differential equations. In engineering, oscillations play such a central role that, if on the one hand their study is important because we are interested in avoiding them as in excessive vibrations in structures, on the other hand we are sometimes interested in inducing them very precisely, as for example in the use of forced oscillations for the rheological characterization of materials. The investigation of possible generalizations of the mathematical description of damped oscillations is consequently a problem of practical and theoretical interest.
Fractional calculus [1,2,3,4] is a branch of mathematical analysis that has been shown to be very useful in the study of generalizations of differential equations, the so called fractional differential equations [5,6,7]. Accordingly it is not a surprise that some authors [8,9,10,11,12,13,14,15] studied generalizations of the damped harmonic oscillator equation using the concept of fractional derivative. In [16] the different approaches to fractional generalizations of the damped harmonic oscillator equation have been classified into three classes. Class Ⅰ contains models for which a fractional derivative of order α (1<α≤2) appears in the inertial term mdαx(t)/dtα, like in [8,9,10,11]; class Ⅱ contains models for which a fractional derivative of order β (0<β≤1) appears in the damping term γdβx(t)/dtβ, like in [12,13]; and class Ⅲ includes models for which a fractional derivative appears both in the mass term and in the damping term, like in [14,15]. Closed form solutions for fractional oscillator models in class Ⅰ are well-known, but not in class Ⅱ and Ⅲ. A closed from solution of a model in class Ⅲ have been provided recently in [14] for the case when α=2β, where α and β are the order of the fractional derivatives of the mass and damping terms, respectively.
In this paper we will study a model in class Ⅱ called fractional Kelvin-Voigt oscillator [17,18]. A subject where the Kelvin-Voigt oscillator is a relevant model is viscoelasticity [19,20]. The basic model for the study of viscoelasticity consists of the combination of a spring and a dashpot; if this combination is made in series it is called Maxwell model, and if it is done in parallel, it is called Kelvin-Voigt model. Based on molecular theories for the description of viscoelastic materials, in [21,22] Bagley and Torvik established the basis for the use of fractional calculus in describing the behaviour of viscoelastic damping [23,24]. An element with constitutive law described by a fractional derivative of order α∈(0,1) is placed between the behaviour of a spring and a dashpot, being called therefore a springpot [24]. A fractional Kelvin-Voigt oscillator is an oscillator model where the dashpot is replaced by a springpot in parallel with the spring. In our opinion, this is the most orthodox choice of all when compared with the classical model of an harmonic oscillator with damping; indeed there is a term associated with Hooke's law and another term corresponding to the usual definitions of momentum and mass, and the change is made only in the form of the damping term. However, to the best of our knowledge, this is the less studied type of model, and we believe that this is due to the mathematical difficulties in expressing its solution, as the functions necessary in the problem are the least known compared to those of the other classes. Indeed typical models in class Ⅰ and Ⅲ have solutions that can be expressed in terms of Mittag-Leffler functions of one and two parameters, while the case we will study requires a generalization of these functions called multivariate Mittag-Leffler functions (see Section 3).
We organized this paper as follows. In Section 2 we introduce the concept of Caputo fractional derivative and use it to write the damping force term in our fractional differential equation. There are some different definitions of fractional derivative [25,26], and the Caputo one is particularly suitable for initial value problems. In Section 3 we recall the definition of the Mittag-Leffler functions with one and two parameters and discuss the lesser-known multivariate Mittag-Leffler function, and some of its properties. In Section 4 we provided the solution of the initial value problem for our fractional damped oscillator in terms of the bivariate Mittag-Leffler function and explore some of its properties. In Section 5 we consider some specific examples of our fractional oscillator and compare them with the classical damped harmonic oscillator. In the Appendix we prove some results used throughout the text, the proof of which has technical details whose discussion we believe would not be necessary in a first reading.
The Caputo fractional derivative (also called Caputo-Dzhrbashyan fractional derivative) of order α, with (n−1)<α<n (n∈N), is defined as [27]
Dαt[f(t)]=dαf(t)dtα=1Γ(n−α)∫t0f(n)(τ)(t−τ)α+1−ndτ, | (2.1) |
where f(n) denotes the derivative of order n of f(t) and Γ(⋅) is the gamma function. The Caputo derivative has two very interesting properties for its use in differential equations. One property is the fact that Dαt[1]=0, unlike other definitions as Riemann-Liouville's one, for which the DRLDαt[1]=t−α/Γ(1−α) for 0<α<1. The other property is related to the fact that its Laplace transform involves only the initial values of derivatives of integer orders of the original function, that is,
L[Dαt[f(t)]](s)=snF(s)−n−1∑k=0skf(n−k−1)(0), | (2.2) |
where F(s)=L[f(t)](s). One important characteristic of Caputo fractional derivative is the presence of the initial value of integer order derivatives f(n−k−1)(0) in the right hand side of Eq (2.2), unlike, for example, in the Riemann-Liouville definition [25,26].
Among the differential equations where the Caputo derivative finds interesting applications, as for example the relaxation equation (see [27] and references therein), we are interested in the harmonic oscillator equation. As commented in the Introduction, our approach is conservative, with the difference in relation to the classic expression for the damped harmonic oscillator given only by a modification in the damping term. Our fractional oscillator equation is
d2xdt2+2γdαxdtα+ω20x=f(t), | (2.3) |
where 0<α≤1, with initial conditions
x(0)=x0,dxdt(0)=v0, | (2.4) |
and f(t) is an external force. The damping force is therefore 2mγDαt[x(t)]. For α=1 we have the usual damping term 2mγx′(t). The model based on Eq (2.3) is the fractional Kelvin-Voigt oscillator [17].
Although Eq (2.3) seems to be a simple modification of the classical damped harmonic oscillator equation, its solution is more obscure than the ones for other apparently more difficult equations, like for example
d2αxdt2α+2γdαxdtα+ω20x=f(t), | (2.5) |
whose solution can be expressed in terms of Mittag-Leffler functions of two parameters. In fact, our equation is as difficult as
dβxdtβ+2γdαxdtα+ω20x=f(t), | (2.6) |
with β≠2α, but we will keep our attention in Eq (2.3) because a fractional inertial term lacks a natural interpretation in our opinion.
The Mittag-Leffler function is a generalization of the exponential function, and is discussed, for example, in [28,29], as well as some of its generalizations. Let us recall the main definitions and results.
The Mittag-Leffler function Ea(z) is defined as
Ea(z)=∞∑n=0znΓ(na+1), | (3.1) |
where Γ(⋅) is the gamma function. This series converges for all values in the complex plane provided Rea>0. A very useful result is the Laplace transform of Ea(−σta), which can be easily calculated from its definition, that is,
L[Ea(−σta)](s)=sa−1sa+σ. | (3.2) |
The two-parametric Mittag-Leffler function Ea,b(z) is defined as
Ea,b(z)=∞∑n=0znΓ(na+b), | (3.3) |
for Rea>0 and b∈C. The Laplace transforms involving Ea,b(z) is [28]
L[tb−1Ea,b(−σta)](s)=sa−bsa+σ. | (3.4) |
Another generalization of the Mittag-Leffler function is the multivariate Mittag-Leffler function E(a1,…,an)(z), defined as [29]
E(a1,…,an),b(z1,…,zn)=∞∑k1=0⋯∞∑kn=0(k1+⋯+kn)!k1!⋯kn!(z1)k1⋯(zn)knΓ(a1k1+⋯+ankn+b). | (3.5) |
From this definition we see that
E(…,ai,…,aj,…),b(…,zi,…,zj,…)=E(…,aj,…,ai,…),b(…,zj,…,zi,…) | (3.6) |
for any i and j, and
E(a1,…,an),b(z1,…,zn−1,0)=E(a1,…,an−1),b(z1,…,zn−1) | (3.7) |
When two indexes are equal, a n-variate Mittag-Leffler function reduces to a (n−1)-variate one; in fact, considering, without loss of generality, that an−1=an=a, we have (see Appendix)
E(a1,…,an−2,a,a),b(z1,…,zn−2,zn−1,zn)=E(a1,…,an−2,a),b(z1,…,zn−2,zn−1+zn). | (3.8) |
We have a special interest in the particular case zi=−Aitai (i=1,2,…,n) since in this case we can define a one variable function E(a1,…,an),b(−A1ta1,…,−Antan) with the Laplace transform
L[tb−1E(a1,…,an),b(−A1ta1,…,−Antan)](s)=s−b1+Ans−an+⋯+A1s−a1, | (3.9) |
whose proof is given in the Appendix. This is a fundamental result for the application of the multivariant Mittag-Leffler functions in the study of fractional differential equations. A comparison with Section 5.6 of [5] clearly indicates that the function E(a1,…,an),b(−A1ta1,…,−Antan) can be expressed in terms of a series involving three-parameter Mittag-Leffler functions [28].
The bivariate Mittag-Leffler function, that is,
E(a1,a2),b(z1,z2)=∞∑k1=0∞∑k2=0(k1+k2)!k1!k2!(z1)k1(z2)k2Γ(a1k1+a2k2+b), | (3.10) |
plays a major role in this work. We see in Eq (3.9) that for z1=−A1ta1 and z2=−A2ta2 we have the Laplace transform
L[tb−1E(a1,a2),b(−A1ta1,−A2ta2)](s)=s−b1+A1s−a1+A2s−a2. | (3.11) |
A particularly important case is the one where a2=2a1. Let us denote in this case a1=a, and consider the function
E(a,2a),b(−A1ta,−A2t2a)=∞∑k1=0∞∑k2=0(k1+k2)!k1!k2!(−A1ta)k1(−A2t2a)k2Γ(ak1+2ak2+b). | (3.12) |
In the Appendix we prove that
E(a,2a),b(−A1ta,−A2t2a)=1A+−A−[A+Ea,b(−A+ta)−A−Ea,b(−A−ta)], | (3.13) |
or, equivalently,
E(a,2a),b(−A1ta,−A2t2a)=t−aA+−A−[Ea,b−a(−A−ta)−Ea,b−a(−A+ta)], | (3.14) |
where
A±=A12±√(A12)2−A2. | (3.15) |
Our objetive is to find the analytical solution of the initial value problem given by the fractional differential equation (2.3) with the initial conditions given by Eq (2.4), that is,
d2xdt2+2γdαxdtα+ω20x=f(t), | (4.1) |
x(0)=x0,dxdt(0)=v0, | (4.2) |
where 0<α≤1 and f(t) is an external force. Using the Laplace transform and denoting X(s)=L[x(t)](s), the transformed equation gives
X(s)=sx0+2γsα−1x0+v0s2+2γsα+ω20+F(s)s2+2γsα+ω20, | (4.3) |
where F(s)=L[f(t)](s). The solution x(t) of the problem is therefore
x(t)=x0[Gα,1(t)+2γGα,α−1(t)]+v0Gα,0(t)+(f∗Gα,0)(t), | (4.4) |
with t>0 and where we denoted
Gα,β(t)=L−1[sβs2+2γsα+ω20](t), | (4.5) |
for β={α−1,0,1} and ∗ denotes the convolution product.
We can see from Eq (3.11) that the inverse Laplace transform in Eq (4.5) can be expressed in terms of the bivariate Mittag-Leffler function. Comparing Eqs (4.5) and (3.11), we see that, with the identifications
a1=2−α,a2=2,b=2−β,A1=−2γ,A2=−ω20, | (4.6) |
we have
Gα,β(t)=t1−βE(2−α,2),2−β(−2γt2−α,−ω20t2). | (4.7) |
In eq.(4.4) we have the terms Gα,0 and Gα,1(t)+2γGα,α−1(t). The first one is
Gα,0(t)=tE(2−α,2),2(−2γt2−α,−ω20t2). | (4.8) |
The term Gα,1(t)+2γGα,α−1(t) in Eq (4.4) can be simplified using the identity
E(a1,a2),b(z1,z2)=1Γ(b)+z1E(a1,a2),b+a1(z1,z2)+z2E(a1,a2),b+a2(z1,z2), | (4.9) |
which is the generalization of Eq (B.12) for Ea,b(z) (see Appendix), and whose proof follows directly from the definition of E(a1,a2),b(z1,z2). Using this identity and Eq (4.7), we obtain
Gα,β(t)=t1−βΓ(2−β)−2γGα,β+α−2(t)−ω20Gα,β−2(t). | (4.10) |
Consequently, we have
Gα,1(t)+2γGα,α−1(t)=1−ω20t2E(2−α,2),3(−2γt2−α,−ω20t2) | (4.11) |
or
Gα,1(t)+2γGα,α−1(t)=1−ω20Gα,−1(t). | (4.12) |
The solution of Eq (2.3) is given by Eq (4.4) with Gα,0(t) and Gα,1(t)+2γGα,α−1(t) given by Eq (4.8) and Eq (4.11), respectively.
Properties of the derivative of Gα,β(t). There is one interesting property involving the derivative of Gα,β(t), which follow directly from its definition, namely
G′α,β(t)=Gα,β+1(t),β≠{1,2,3,…} | (4.13) |
The cases β={1,2,3,…} can be handled using Eq (4.10). We must remember, however, that in Eq (4.4) we are considering t>0. It may be appropriate in this case to work with the Heaviside step function H(t), and then we can deal with the term t1−β/Γ(2−β) in Eq (4.10) using the definition of the Gelfand-Shilov distribution Gν(t) [33,34]
Gν(t)=tν−1Γ(ν)H(t), | (4.14) |
for which we have
limν→0Gν(t)=δ(t), | (4.15) |
and
G(n)ν(t)=Gν−n(t). | (4.16) |
However, since we are interested in t>0, we can work with derivatives of functions instead of derivative of functions; in other words, we will simply write, for example, the derivative 1′=0 instead of considering the derivative H′(t)=δ(t) when calculating the derivative in Eq (4.10) for β=1, and analogously for β={2,3,…}.
Using β=1 in Eq (4.10) it follows that
G′α,1(t)=−2γGα,α(t)−ω20Gα,0(t). | (4.17) |
For the cases β={2,3,…}, we use, for β=2,
Gα,2(t)=−2γGα,α(t)−ω20Gα,0(t), | (4.18) |
and then
G′α,2(t)=−2γGα,α+1(t)−ω20Gα,1(t). | (4.19) |
For β={3,4,…} the calculation is analogous.
Equation (4.13) can be generalized, for β<1 and 0<μ≤1, as
DμGα,β(t)=Gα,β+μ(t), | (4.20) |
which follows using the definition of Gα,β(t) and Dμtν=(Γ(ν+1)/Γ(ν−μ+1))tν−μ with ν>0 and Dμ1=0.
The velocity of the oscillator can be easily calculated using the above properties of the time derivative of Gα,β(t). From Eqs (4.4) and (4.13) we obtain
v(t)=−x0ω20Gα,0(t)+v0Gα,1(t)+(f∗Gα,1)(t). | (4.21) |
Moreover, since our fractional oscillator model has the same inertial term of the classical one, the momentum p is mv, where v=v(t) is given by Eq (4.21).
Examples of responses to external forces. For the simple case of an impulsive external force f(t)=f0δ(t), we have
(f∗Gα,0)=f0Gα,0(t), | (4.22) |
where the response function Gα,0(t) is the Laplace transform of H(s),
H(s)=1s2+2γsα+ω20. | (4.23) |
Let us also consider sinusoidal external forces. For an external force f(t) of the form
f(t)=f0cosωt, | (4.24) |
the convolution f∗Gα,0=f0cosωt∗Gα,0(t) can be written as
cosωt∗Gα,0(t)=L−1[s(s2+ω2)H(s)] | (4.25) |
Comparing the above expression with Eq (3.9), we can conclude that
cosωt∗Gα,0(t)=t2E(2−α,2,4−α,4),3(−2γt2−α,−(ω2+ω20)t2,−2γω2t4−α,−ω2ω20t4). | (4.26) |
The case of an external force of the form
f(t)=f0sinωt | (4.27) |
is completely analogous, and the result is
sinωt∗Gα,0(t)=ωtE(2−α,2,4−α,4),2(−2γt2−α,−(ω2+ω20)t2,−2γω2t4−α,−ω2ω20t4). | (4.28) |
Therefore, the response to an arbitrary sinusoidal force is given in terms of a combination of 4-variate Mittag-Leffler functions.
The case α=1 corresponds to the usual harmonic oscillator with frictional force −2γdx/dt. This corresponds to α=1 in Eq (4.8) and in Eq (4.11), that is,
G1,0(t)=tE(1,2),2(−2γt,−ω20t2) | (4.29) |
and
G1,1(t)+2γG1,0(t)=1−ω20t2E(1,2),3(−2γt,−ω20t2). | (4.30) |
Now we can use Eq (3.13) or Eq (3.14). In order to use the latter equation, we need [28]
E1,1(z)=ez,E1,2(z)=ez−1z. | (4.31) |
This gives
E(1,2),2(−2γt,−ω20t2)=e−γtt(eΩt−e−Ωt2Ω) | (4.32) |
and
E(1,2),3(−2γt,−ω20t2)=1ω20t2[1−γe−γt(eΩt−e−Ωt2Ω)−e−γt(eΩt+e−Ωt2)] | (4.33) |
where we denoted
Ω=√γ2−ω20. | (4.34) |
Using the above expressions in Eq (4.29) and in Eq (4.30) give the well-known solution of the harmonic oscillator with frictional force −2γdx/dt for the overdamped and underdamped cases, while the critically damped solution follows from the limit Ω→0 in these solutions.
In this section we will study speficic solutions for some values of γ, ω0 and α. Although, as we will see, the classification of cases as overdamped, underdamped and critically damped is justified only for α=1, we will continue using it for preciseness.
Let us consider the case with x0=1 and v0=0. The plots corresponding to the solutions for α={1,0.8,0.6,0.4,0.2} are given in Figure 1 for (a) γ=1/2 and ω0=2 and for (b) γ=1/2 and ω0=4. In Figure 2 we plot the curves in phase space for the fractional oscillator with γ=1/2 and ω=2 for (a) α=0.8, (b) α=0.6, (c) α=0.4 and (d) α=0.2, and compare these curves with the one for α=1. We used in Figure 2 the vertical axis as p/mω20 in order to have the direct identification of this quantity with −Gα,0(t). The plots in Figure 1 have been done using Mathematica 12.2 and were based on the inversion of the Laplace transform as in Eq (4.5), for which we employed the numerical inversion codes provided in [35] for Mathematica. The code used in these plots is based on the Post-Widder inversion formula [35,36]. However, the plots in Figure 2 have been done using the inverse Laplace transform routine in Mathematica 12.2, as it produces better results in this case.
Although all curves in Figure 1 show a decay of an oscillatory amplitude, only the curve for α=1 has an exponential decay envelope. We can expect to find a damped oscillator with α=1 such that for given values γ∗ and ω∗0 the behaviour of its solution resembles the solution for a given α≠1 for small values of t, but not for larger values due to deviations from the exponential decay behaviour. For example, let us consider the case α=0.4, γ=1/2 and ω0=4. The poles of Laplace transform L[Gα,β(t)](s) are located in s0.4=−0.126764−4.17572i and s∗0.4=−0.126764+4.17572i. If we choose γ∗=−(s0.4+s∗0.4)/2 and ω∗0=√s0.4s∗0.4, we obtain a solution for the case α=1 which can be compared with the solution for the α=0.4, γ=1/2 and ω0=4 case, as in plot (a) in Figure 3. The phase space plot of the corresponding curves are in plot (b). The plot of x(t) clearly shows the similar behaviour of the solutions for small values of t, and the deviation of the decaying behaviour as t increases. Notwithstanding, the solution with α=0.4 approaches zero for large t with a rate slower than the exponential one. This can be seen from the asymptotic expansion of Gα,β(t) for α≠1. We show in the Appendix that for t→∞ we have Gα,1+2γGα,α−1(t)∼t−α – see Eq (C.7). In other words, and borrowing a jargon from the study of statistical distributions, we can say that the solution for α=0.4 has a heavy tailed profile.
We proceed like the underdamped case, with x0=1 and v0=0. The plots corresponding to the solutions for α={1,0.8,0.6,0.4,0.2} are given by the top plots in Figure 4 for (a) γ=4 and ω0=2 and (b) for ω0=3. Figure 5 shows the plots of the curves in phase space corresponding to the case γ=4 and ω0=3 for (a) α=0.8, (b) α=0.6, (c) α=0.4 and (d) α=0.2, and compare these curves with the one for α=1.
The overdamped case has a distinguished characteristic, that is, while with α=1 we have real solutions of s2+2γs+ω20=0 (when γ>ω0), this is not the case for α≠1 since we have complex conjugated solutions s0 and ˉs0 for s2+2γsα+ω20=0 for 0<α<1. We expect, therefore, to see an oscillatory behaviour, which is suggested by the plots in Figure 4, where we see the presence of a small oscillation for α=0.6 when γ=4 and ω0=3 but apparently none for γ=4 and ω0=2, as well as the presence of higher oscillation amplitudes for γ=4 and ω0=3 than for γ4 and ω0=2 for the cases α=0.4 and α=0.2. We also see that, when we have a clear oscillatory behaviour, the local wavelength inscreases with inscreasing t, while the amplitude of the oscillations decreases with increasing t. Let us consider, for example, the case α=0.2, γ=4 and ω0=2, represented by the dashed orange curve in the left plot in Figure 4. If we measure the local wavelength by the difference between successive minima m1=0.884, m2=2.558, m3=4.239, m4=5.926 and m5=7.623, we obtain, for λi=mi+1−mi, λ1=1.674, λ2=1.681, λ3=1.687 and λ4=1.707, while the decreasing in the amplitude of the oscillations is clear in the plots. The values of the local minima were obtained using the FindMinimum routine in Mathematica. For α=0.2, γ=4 and ω0=3 (dashed orange curve in the right plot), we have m1=0.741, m2=2.167, m3=3.596, m4=5.026 and m5=6.460, we have λ1=1.426, λ2=1.429, λ3=1.430, λ4=1.434, so the increase in the local wavelength is slower than in the previous case, as well as the rate in which the amplitude of the oscillations decreases.
The plots in Figures 4 and 5 suggest that there may be a critical value α∗ such that for α<α∗ an oscillatory behaviour appears. It is reasonable to suppose that such critical value depends on γ and ω0. On the other hand, the presence of singularities in the complex plane for α≠1 with a non-null imaginary part suggests that this may not be the case, that is, we can always have an oscillatory behavior for α<1, although in some cases with a very small amplitude. This is an issue that deserves attention but it is outside the scope of the present work.
In relation to the critically damped case, in the bottom plots in Figure 4 we have the plots of the solutions for the cases (c) γ=2 and ω0=2 and (d) γ=6 and ω0=6. As we see, the concept of critical damping makes sense only in the case α=1. The behaviour of the solutions is similar to the overdamped case. In fact, we can see a deviation of the pure decaying solution even in the case α=0.8 in plot (d).
Equation (4.26) gives the response of a damped harmonic oscillator to an external force of the form cosωt and initial conditions x0=0 and v0=0. In Figure 6 we show the plots of the response in the case γ=1/2, ω0=4, and driving frequency (a) ω=3, (b) ω=4 and (c) ω=5. As suggested in the previous plots, as α decreases, so the damping decreases and the response increases, and the effect of resonance is clearly manifested when the driving frequency equals the natural frequency.
In Figure 7 we have plots for the response to an unit impulse force with x0=0 and v0=0 for the cases (a) γ=1/2 and ω0=2 and (b) γ=4 and ω0=3. As in this case the response function is the Laplace inverse transform of the transfer function H(s) in Eq (4.23), it is interesting to look in more details the profile of H(s) for different values of α. Let us take case γ=4 and ω0=3 as an example. Using the frequency ω as a variable through s=iω, in Figure 8 we have the plots of |H(iω)| and argH(iω) in terms of ω.
It is also interesting to observe how the poles of the H(s) function move through the complex plane. In Figure 9 we have the phase portraits (made with Mathematica 12) of H(s) for (a) α=0.2, (b) α=0.4, (c) α=0.6, (d) α=0.8, (e) α=0.95 and (f) α=1, in the rectangular region |Res|≤8 and |Ims|≤6. In the HSL color model, the hue is an angular variable with values in [0,2π] or [−π,π], and this fact is used in the phase portrait of a function H(s) where points of the plane are colored according to relation between hue and the angle associated with the argument argH(s), as shown in the plot legend in Figure 9. The absolute value |H(s)| can be illustrated using contour lines, and this is done by means of a gray coloring in a logarithmic scale, as shown in the plot legend in Figure 9, which creates an effect of contour lines of constant values of |H(s)| – for more details about the illustration of complex functions, see [37]. The white line segment in the plots in Figure 9 is the branch cut of H(s). The analysis of the phase portraits clearly shows the localization of the poles of H(s) as the center of closed curves with an approximate circular shape. We have two poles, and for small values of α (in plot (a) α=0.2), these two poles are located close to the imaginary axis. As the value of α increases, they move away from the imaginary axis towards the real negative direction, with the imaginary part of the poles decreasing, as can be seen in the sequence of plots. As α→1, these two poles approach each other, while in a region along the branch cut (where we can see the emergence of a curve that resembles an ellipse) the values of |H(s)| increase. When α=1 these two poles merge into a single pole along the negative imaginary axis, while in the region where |H(s)| increased, a new pole appeared on the real negative axis, which is no longer a branch cut.
In this paper we described a model of fractional oscillator with the fractional derivative appearing in the damping term. This is, to the best of our knowledge, the model of a fractional oscillator less discussed in the literature, although in our opinion it is the most natural and conservative one because it keeps the inertial and restoring force terms with their usual form. Our approach used the so called bivariate Mittag-Leffer function. Some properties of this function have been discussed and proved, and numerical examples of some particular solutions of the model for different values of the order α of the fractional derivative were provided, and compared with the usual α=1 damped oscillator. The examples show that the damping decreases as the order of the fractional derivative decreases, so that for certain values, even in the cases classically classified as overdamped or critically damped, oscillations may appear. The existence and identification of a value for the order of the fractional derivative below which oscillations can be noticed even in overdamped cases is an issue that deserves further investigations.
The authors declare no conflict of interest.
Equation (3.5) with an−1=an=a is
E(a1,…,a,a),b(z1,…,zn−1,zn)=∞∑k1=0⋯∞∑kn−1=0∞∑kn=0(k1+⋯+kn−1+kn)!k1!⋯kn−1!kn!(z1)k1⋯(zn−1)kn−1(zn)knΓ(a1k1+⋯+a(kn−1+kn)+b). | (A.1) |
Replacing the summation index kn−1 by m=kn−1+kn, we have
E(a1,…,a,a),b(z1,…,zn−1,zn)=∞∑k1=0⋯∞∑m=0(k1+⋯+m)!k1!⋯kn−2!m!(z1)k1⋯(zn−2)kn−2(zn−1)mΓ(a1k1+⋯+am+b)m∑kn=0(mkn)(znzn−1)kn, | (A.2) |
and since
(zn−1)mm∑kn=0(mkn)(znzn−1)kn=(zn−1)m(1+znzn−1)m=(zn−1+zn)m | (A.3) |
we obtain Eq (3.8).
Using the definition of the multivariate Mittag-Leffler function as in Eq (3.5), we have
L[tb−1E(a1,…,an),b(−A1ta1,…,−Antan)](s)=∞∑k1=0⋯∞∑kn=0(k1+⋯+kn)!k1!…kn!(−A1)k1⋯(−An)knΓ(a1k1+⋯+ankn+b)L[ta1k1+⋯+ankn+b−1](s)=∞∑k1=0⋯∞∑kn=0(k1+⋯+kn)!k1!…kn!(−A1)k1⋯(−An)knsa1k1+⋯+ankn+b=s−b∞∑k1=0⋯∞∑kn−1=0(k1+⋯+kn−1)!k1!…kn−1!(−A1sa1)k1⋯(−An−1san−1)kn−1Tn | (A.4) |
with
Tn=∞∑kn=0(k1+⋯+kn−1+kn)!(k1+⋯+kn−1)!kn!(−Ansan)kn=∞∑kn=0(k1+⋯+kn−1+1)knkn!(−Ansan)kn, | (A.5) |
where we used the notation of the Pochhammer symbol (α)n, that is,
(α)n=Γ(α+n)Γ(α). | (A.6) |
It is well-known [30] that
(1−z)−α=∞∑n=0(α)nznn!,|z|<1. | (A.7) |
Therefore, for |s|>|An|1/an we have
Tn=1(1+Ans−an)k1+⋯+kn−1+1, | (A.8) |
and then
L[tb−1E(a1,…,an),b(−A1ta1,…,−Antan)](s)=s−b(1+Ans−an)∞∑k1=0⋯∞∑kn−1=0(k1+⋯+kn−1)!k1!…kn−1!(−A1sa1(1+Ans−an))k1⋯=s−b(1+Ans−an)∞∑k1=0⋯∞∑kn−1=0(k1+⋯)!k1!…⋯(−An−1san−1(1+Ans−an))kn−1==s−b(1+Ans−an)∞∑k1=0⋯∞∑kn−2=0(k1+⋯+kn−2)!k1!…kn−2!(−A1sa1(1+Ans−an))k1⋯=s−b(1+Ans−an)∞∑k1=0⋯∞∑kn−1=0(k1)!k1!⋯(−An−2san−2(1+Ans−an))kn−2Tn−1, | (A.9) |
where
Tn−1=∞∑kn−1=0(k1+⋯+kn−2)kn−1kn−1!(−An−1san−1(1+Ans−an))kn−1. | (A.10) |
For |s|>(2|An|)1/an the condition for Eq (A.8) holds, and with |s|>(2|An−1)1/an−1 it follows, from the triangle inequality, that |An−1s−an−1/(1+Ans−an)|<1, and then
Tn−1=(1+Ans−an)k1+⋯+kn−2+1(1+Ans−an+An−1s−an−1)k1+⋯+kn−2+1, | (A.11) |
which gives
L[tb−1E(a1,…,an),b(−A1ta1,…,−Antan)](s)=s−b(1+Ans−an+An−1s−an−1)∞∑k1=0⋯∞∑kn−2=0(k1+⋯+kn−2)!k1!…kn−2!⋅⋅(−A1sa1(1+Ans−an+An−1s−an−1))k1⋯(−An−2san−2(1+Ans−an+An−1s−an−1))kn−2. | (A.12) |
We repeat the same procedure for Tn−2 given by
Tn−2=∞∑kn−2=0(k1+⋯+kn−3)kn−2kn−2!(−An−2san−2(1+Ans−an+An−1s−an−1))kn−2. | (A.13) |
For |s|>(3|An|)1/an, |s|>(3|An−1)1/an−1 and (3|An−2|)1/an−2, we still have the validity of Eqs (A.8) and (A.11), and it follows, from the triangle inequality, that |An−2s−an−2/(1+Ans−an+An−1s−an−1)|<1, and then
Tn−2=(1+Ans−an+An−1s−an−1)k1+⋯+kn−3+1(1+Ans−an+An−1s−an−1+An−2s−an−2)k1+⋯+kn−3+1, | (A.14) |
and then
L[tb−1E(a1,…,an),b(−A1ta1,…,−Antan)](s)=s−b(1+Ans−an+An−1s−an−1+An−2s−an−2)∞∑k1=0⋯∞∑kn−3=0(k1+⋯+kn−3)!k1!…kn−3!⋅⋅(−A1sa1(1+Ans−an+An−1s−an−1+An−2s−an−2))k1⋯⋯(−An−3san−3(1+Ans−an+An−1s−an−1+An−2s−an−2))kn−3. | (A.15) |
After performing the same calculation for Tn−3,…,T2, we obtain
L[tb−1E(a1,…,an),b(−A1ta1,…,−Antan)](s)=s−b(1+Ans−an+⋯+A2s−a2)∞∑k1=0(−A1sa1(1+Ans−an+⋯+A2s−s2))k1. | (A.16) |
For |s|>max{(n|A1|)1/a1,…,(n|An|)1/an}, the conditions for the validity of Tn,…,T2 are still satisfied, and the triangle inequality gives |A1/sa1(1+Ans−an+⋯+A2s−s2)|<1, and consequently
L[tb−1E(a1,…,an),b(−A1ta1,…,−Antan)](s)=s−b1+Ans−an+⋯+A1s−a1, | (A.17) |
which is the result we want to prove.
We can prove Eqs (3.13) and (3.14) from Eq (3.12) using the same series manipulations done in [31]. Let us define A+ and A− as in Eq (3.15), that is, A±=(A1/2)±√(A1/2)2−A2, in such a way that
A1=A++A−,A2=A+A−. | (B.1) |
Equation (3.12) can be written as
E(a,2a),b(−A1ta,−A2t2a)=∞∑k1=0∞∑k2=0(k1+k2)!k1!k2!(−A+A−t2a)k2(−1)k1tak1(A++A−)k1Γ(ak1+2ak2+b). | (B.2) |
Using the binomial theorem in (A++A−)k1 we obtain
E(a,2a),b(−A1ta,−A2t2a)=∞∑k1=0∞∑k2=0k1∑n=0(k1+k2)!k1!k2!(−A+A−t2a)k2(−1)k1tak1Γ(ak1+2ak2+b)k1!(k1−n)!n!(A+)k1−n(A−)n. | (B.3) |
Using the summation index m defined as k1=n+m we can write
E(a,2a),b(−A1ta,−A2t2a)=∞∑k2=0∞∑n=0∞∑m=0(−1)k2+n+m(A+)k2+m(A−)k2+nt2ak2+an+am(k2+m+n)!Γ(2ak2+an+am+b)k2!m!n!. | (B.4) |
Employing the summation index m′=k2+m we have
E(a,2a),b(−A1ta,−A2t2a)=∞∑m′=0∞∑n=0∞∑k2=0(−1)m′+n′(A+)m′tam′(A−)k2+ntak2+an(m′+n)!Γ(ak2+an+am′+b)k2!(m′−k2)!n!, | (B.5) |
where we have used (m′−k2)!=0 for k2>m′. Using the summation index n′=k2+n we have
E(a,2a),b(−A1ta,−A2t2a)=∞∑m′=0∞∑n′=0(−A+)m′(−A−)n′tam′tan′Γ(an′+am′+b)n′∑k2=0(−1)k2(n′+m′−k2)!k2!(m′−k2)!(n′−k2)!. | (B.6) |
The last series is
n′∑k2=0(−1)k2(n′+m′−k2)!k2!(m′−k2)!(n′−k2)!=n′∑k2=0(−1)k2(nk2)(n′+m′−k2n)=1, | (B.7) |
where we have used [32] (Eq (56), page 619)
n∑k=0(−1)k(nk)(a−km)=(a−nm−n) | (B.8) |
with m=n. Then
E(a,2a),b(−A1ta,−A2t2a)=∞∑m′=0∞∑n′=0(−A+)m′(−A−)n′tam′tan′Γ(an′+am′+b), | (B.9) |
and using the summation index r=m′+n′,
E(a,2a),b(−A1ta,−A2t2a)=∞∑r=0(−A+)rtarΓ(ar+b)r∑n′=0(A−/A+)n′=1A+−A−∞∑r=0(−1)rtarΓ(ar+b)(Ar+1+−Ar+1−), | (B.10) |
where we used the sum of the geometric series. Using the definition of Ea,b(z) as in Eq (3.3), we obtain
E(a,2a),b(−A1ta,−A2t2a)=1A+−A−[A+Ea,b(−A+ta)−A−Ea,b(−A−ta)], | (B.11) |
which is Eq (3.13). From the definition of Ea,b(z) it follows the identity
Ea,b(z)=1Γ(b)+zEa,b+a(z), | (B.12) |
which in Eq (B.11) gives
E(a,2a),b(−A1ta,−A2t2a)=t−aA+−A−[Ea,b−a(−A−ta)−Ea,b−a(−A+ta)], | (B.13) |
which is Eq (3.14).
In Appendix A.2 we showed that, for |s|>σ=max{(n|A1|)1/a1,…,(n|An|)1/an}, the Laplace transform of the series in Eq (3.5), multiplied by tb−1, can be written as
H(a1,…,an),b(s)=san−bsan+A1san−a1+A2san−a2+…+An, | (C.1) |
where we supposed that an>aj (j=1,…,n−1). This function H(a1,…,an),b(s) is the analytical continuation of the Laplace transformed series to other regions with |s|≤σ, particularly in the neighbourhood of s=0.
Let us now consider n=2 and suppose that a2>a1>0. We know, from Watson's lemma [36], that the behaviour of a function f(t) for t→∞ is related to the behaviour of its Laplace transform for s→0. Then, using Eq (3.11), we have, for s→0 and a2>a1,
L[tb−1E(a1,a2),b(−A1ta1,−A2ta2)](s)=H(a1,a2),b(s)=sa2−bA2−A1s2a2−b−a1A22−s2a2−bA22+O(s2(a2−a1)), | (C.2) |
and therefore, for t→∞,
tb−1E(a1,a2),b(−A1ta1,−A2ta2)=tb−a2−1A2[1Γ(b−a2)−A1t−(a2−a1)A2Γ(b−2a2+a1)−t−a2Γ(b−2a2)+O(t−2(a2−a1)]. | (C.3) |
We also assume b−a2−1>0.
After using the above expression in Eq (4.7) we obtain
Gα,β(t)=t−β−1ω20[1Γ(−β)−2γt−αω20Γ(−β−α)−t−2ω20Γ(−β−2)+O(t−2α)] | (C.4) |
for t→∞. We are interested in the cases β=0 as in Eq (4.8) and β=−1 as in Eq (4.12). For β=0 we have
Gα,0(t)=2αγt−α−1ω40Γ(1−α)+O(t−2α−1),(t→∞) | (C.5) |
and for β=−1 we have
Gα,−1(t)=1ω20[1−2γt−αω20Γ(1−α)+O(t−2α)], | (C.6) |
which gives
Gα,1(t)+2γGα,α−1(t)=2γt−αω40Γ(1−α)+O(t−2α),(t→∞). | (C.7) |
[1] |
Ul Haq MI, Khuroo S, Raina A, et al. (2020) 3D printing for development of medical equipment amidst coronavirus (COVID-19) pandemic—review and advancements. Res Biomed Eng 38: 305–315. https://doi.org/10.1007/s42600-020-00098-0 doi: 10.1007/s42600-020-00098-0
![]() |
[2] |
Aziz R, Ul Haq MI, Raina A (2020) Effect of surface texturing on friction behaviour of 3D printed polylactic acid (PLA). Polym Test 85: 106434. https://doi.org/10.1016/j.polymertesting.2020.106434 doi: 10.1016/j.polymertesting.2020.106434
![]() |
[3] |
Chadha A, Ul Haq MI, Raina A, et al. (2019) Effect of fused deposition modelling process parameters on mechanical properties of 3D printed parts. World J Eng 6: 550–559. https://doi.org/10.1108/WJE-09-2018-0329 doi: 10.1108/WJE-09-2018-0329
![]() |
[4] |
Naveed N (2020) Investigate the effects of process parameters on material properties and microstructural changes of 3D-printed specimens using fused deposition modelling (FDM). Mater Technol 36: 317–330. https://doi.org/10.1080/10667857.2020.1758475 doi: 10.1080/10667857.2020.1758475
![]() |
[5] |
Naveed N (2021) Investigating the Material Properties and Microstructural Changes of Fused Filament Fabricated PLA and Tough-PLA Parts. Polym 13: 1487. https://doi.org/10.3390/polym13091487 doi: 10.3390/polym13091487
![]() |
[6] |
Ashrafi N, Duarte JP, Nazarian S, et al. (2018) Evaluating the relationship between deposition and layer quality in large-scale additive manufacturing of concrete. Virtual Phys Prototyping 14: 135–140. https://doi.org/10.1080/17452759.2018.1532800 doi: 10.1080/17452759.2018.1532800
![]() |
[7] | Kumar MB, Sathiya P (2021) Methods and materials for additive manufacturing: A critical review on advancements and challenges. Thin-Walled Struct 159: 107228. https://www.sciencedirect.com/science/article/pii/S0263823120311009 |
[8] |
Rouf S, Raina A, Ul Haq MI, et al. (2022) 3D printed parts and mechanical properties: influencing parameters, sustainability aspects, global market scenario, challenges and applications. Adv Ind Eng Polym 5: 143–158. https://doi.org/10.1016/j.aiepr.2022.02.001 doi: 10.1016/j.aiepr.2022.02.001
![]() |
[9] | Ul Haq MI, Raina A, Ghazali MJ, et al. (2021) Potential of 3D printing technologies in developing applications of polymeric nanocomposites, In: Jena H, Katiyar JK, Patnaik A, Tribology of Polymer and Polymer Composites for Industry 4.0, 193–210. https://doi.org/10.1007/978-981-16-3903-6_10 |
[10] |
Clarissa WHY, Chia CH, Zakaria S, et al. (2022) Recent advancement in 3-D printing: nanocomposites with added functionality. Prog Addit Manuf 7: 325–350. https://doi.org/10.1007/s40964-021-00232-z doi: 10.1007/s40964-021-00232-z
![]() |
[11] |
Birosz MT, Andó M, Jeganmohan S (2021) Finite element method modeling of additive manufactured compressor wheel. J Inst Eng (India): Ser D 102: 79–85. https://doi.org/10.1007/s40033-021-00251-8 doi: 10.1007/s40033-021-00251-8
![]() |
[12] |
Andó M, Birosz M, Jeganmohan S (2021) Surface bonding of additive manufactured parts from multi-colored PLA materials. Measurement 169: 108583. https://doi.org/10.1016/j.measurement.2020.108583 doi: 10.1016/j.measurement.2020.108583
![]() |
[13] |
Saini JS, Dowling L, Kennedy J, et al. (2020) Investigations of the mechanical properties on different print orientations in SLA 3D printed resin. Proc Inst Mech Eng Part C 234: 2279–2293. https://doi.org/10.1177/0954406220904106 doi: 10.1177/0954406220904106
![]() |
[14] | Węgrzyn N (2022) The use of additive manufacturing for production of commercial airplane power plants components: A review. Saf Def 8: 2. Available from: https://sd-magazine.eu/index.php/sd/article/view/185. |
[15] | Wohlers T, Gornet T, Mostow N, et al. (2016) History of additive manufacturing. Wohlers Rep 2016–2022, 1–38. Available from: https://papers.ssrn.com/sol3/papers.cfm?abstract_id = 4474824. |
[16] |
Bourell DL (2016) Perspectives on additive manufacturing. Annu Rev Mater Res 46: 1–18. https://doi.org/10.1146/annurev-matsci-070115-031606 doi: 10.1146/annurev-matsci-070115-031606
![]() |
[17] |
Chiarini A, Belvedere V, Grando A (2020) Industry 4.0 strategies and technological developments. an exploratory research from Italian manufacturing companies. Prod Plann Control 31: 1385–1398. https://doi.org/10.1080/09537287.2019.1710304 doi: 10.1080/09537287.2019.1710304
![]() |
[18] |
Wu P, Wang J, Wang XY (2016) A critical review of the use of 3-D printing in the construction industry. Autom Constr 68: 21–31. https://doi.org/10.1016/j.autcon.2016.04.005 doi: 10.1016/j.autcon.2016.04.005
![]() |
[19] |
Ryan MJ, Eyers DR, Potter AT, et al. (2017) 3D printing the future: scenarios for supply chains reviewed. Int J Phys Distrib Logist Manage 47: 992–1014. https://doi.org/10.1108/IJPDLM-12-2016-0359 doi: 10.1108/IJPDLM-12-2016-0359
![]() |
[20] |
Marchi B, Zanoni S (2017) Supply chain management for improved energy efficiency: Review and opportunities. Energies 10: 1618. https://doi.org/10.3390/en10101618 doi: 10.3390/en10101618
![]() |
[21] | Ford S, Despeisse M (2016) Additive manufacturing and sustainability: an exploratory study of the advantages and challenges. J Cleaner Prod 137: 1573–1587. Available from: https://www.sciencedirect.com/science/article/pii/S0959652616304395. |
[22] |
Mehrpouya M, Dehghanghadikolaei A, Fotovvati B, et al. (2019) The potential of additive manufacturing in the smart factory industrial 4.0: A review. Appl Sci 9: 3865. https://doi.org/10.3390/app9183865 doi: 10.3390/app9183865
![]() |
[23] |
Majeed A, Zhang YF, Ren S, et al. (2021) A big data-driven framework for sustainable and smart additive manufacturing. Rob Comput Integr Manuf 67: 102026. https://doi.org/10.1016/j.rcim.2020.102026 doi: 10.1016/j.rcim.2020.102026
![]() |
[24] |
May G, Psarommatis F (2023) Maximizing energy efficiency in additive manufacturing: A review and framework for future research. Energies 16: 4179. https://doi.org/10.3390/en16104179 doi: 10.3390/en16104179
![]() |
[25] | Hegab H, Khanna N, Monib N, et al. (2023) Design for sustainable additive manufacturing: A review. Sustainable Mater Technol 35: e00576. Available from: https://www.sciencedirect.com/science/article/pii/S2214993723000118. |
[26] |
Ingarao G, Priarone PC, Deng YL, et al. (2018) Environmental modelling of aluminium based components manufacturing routes: additive manufacturing versus machining versus forming. J Cleaner Prod 176: 261–275. https://doi.org/10.1016/j.jclepro.2017.12.115 doi: 10.1016/j.jclepro.2017.12.115
![]() |
[27] |
Kishawy HA, Hegab H, Saad E (2018) Design for sustainable manufacturing: approach, implementation, and assessment. Sustainability 10: 3604. https://doi.org/10.3390/su10103604 doi: 10.3390/su10103604
![]() |
[28] |
Giudice F, Barbagallo R, Fargione G (2021) A design for additive manufacturing approach based on process energy efficiency: electron beam melted components. J Cleaner Prod 290: 125185. https://doi.org/10.1016/j.jclepro.2020.125185 doi: 10.1016/j.jclepro.2020.125185
![]() |
[29] | DeBoer B, Nguyen N, Diba F, et al. (2021) Additive, subtractive, and formative manufacturing of metal components: a life cycle assessment comparison. Int J Adv Manuf Technol 115: 413–432. Available from: https://link.springer.com/article/10.1007/s00170-021-07173-5. |
[30] |
Yoris-Nobile AI, Lizasoain-Arteagab E, Slebi-Acevedo CJ, et al. (2022) Life cycle assessment (LCA) and multi-criteria decision-making (MCDM) analysis to determine the performance of 3D printed cement mortars and geopolymers. J Sustainable Cem-Based Mater 12: 609–626. https://doi.org/10.1080/21650373.2022.2099479 doi: 10.1080/21650373.2022.2099479
![]() |
[31] |
Jayawardane H, Davies IJ, Leadbeater G, et al. (2021) 'Techno-eco-efficiency' performance of 3D printed impellers: an application of life cycle assessment. Int J Sustainable Manuf 5: 44–80. https://doi.org/10.1504/IJSM.2021.116871 doi: 10.1504/IJSM.2021.116871
![]() |
[32] | Kreiger M, Pearce JM (2013) Environmental life cycle analysis of distributed three-dimensional printing and conventional manufacturing of polymer products. ACS Sustainable Chem Eng 1: 1511–1519. Available from: https://pubs.acs.org/doi/abs/10.1021/sc400093k. |
[33] |
Gopal M, Lemu HG (2023) Sustainable additive manufacturing and environmental implications: Literature review. Sustainability 15: 504. https://doi.org/10.3390/su15010504 doi: 10.3390/su15010504
![]() |
[34] | Peng T, Kellens K, Tang RZ, et al. (2018) Sustainability of additive manufacturing: An overview on its energy demand and environmental impact. Addit Manuf 21: 694–704. Available from: https://www.sciencedirect.com/science/article/pii/S2214860417302646. |
[35] |
Mecheter A, Tarlochan F, Kucukvar M (2023) A review of conventional versus additive manufacturing for metals: life-cycle environmental and economic analysis. Sustainability 15: 12299. https://doi.org/10.3390/su151612299 doi: 10.3390/su151612299
![]() |
[36] |
Tinoco MP, Mendonç a É M, Fernandez LIC, et al. (2022) Life cycle assessment (LCA) and environmental sustainability of cementitious materials for 3D concrete printing: A systematic literature review. J Build Eng 52: 104456. https://doi.org/10.1016/j.jobe.2022.104456 doi: 10.1016/j.jobe.2022.104456
![]() |
[37] |
Shuaib M, Haleem A, Kumar S, et al. (2021) Impact of 3D printing on the environment: A literature-based study. Sustainable Oper Comput 2: 57–63. https://doi.org/10.1016/j.susoc.2021.04.001 doi: 10.1016/j.susoc.2021.04.001
![]() |
[38] | Kokare S, Oliveira JP, Godina R (2023) Life cycle assessment of additive manufacturing processes: A review. J Manuf Syst 68: 536–559. Available from: https://www.sciencedirect.com/science/article/pii/S027861252300081X. |
[39] | Mehrpouya M, Vosooghnia A, Dehghanghadikolaei A, et al. (2021) The benefits of additive manufacturing for sustainable design and production. Sustainable Manuf 29–59. https://doi.org/10.1016/B978-0-12-818115-7.00009-2 |
[40] | Javaid M, Haleem A, Singh RP, et al. (2021) Role of additive manufacturing applications towards environmental sustainability. Adv Ind Eng Polym Res 4: 312–322. Available from: https://www.sciencedirect.com/science/article/pii/S254250482100049X. |
[41] | Woodward DG (1997) Life cycle costing—theory, information acquisition and application. Int J Proj Manage 15: 335–344. Available from: https://www.sciencedirect.com/science/article/pii/S0263786396000890. |
[42] | Camacho DD, Clayton P, O'Brien WJ, et al. (2018) Applications of additive manufacturing in the construction industry—A forward-looking review. Autom Constr 89: 110–119. Available from: https://www.sciencedirect.com/science/article/pii/S0926580517307847. |
[43] |
Sepasgozar SME, Shi A, Yang LM, et al. (2020) Additive manufacturing applications for industry 4.0: A systematic critical review. Buildings 10: 231. https://doi.org/10.3390/buildings10120231 doi: 10.3390/buildings10120231
![]() |
[44] |
Paolini A, Kollmannsberger S, Rank E (2019) Additive manufacturing in construction: A review on processes, applications, and digital planning methods. Addit Manuf 30: 100894. https://doi.org/10.1016/j.addma.2019.100894 doi: 10.1016/j.addma.2019.100894
![]() |
[45] |
Valino AD, Dizon JRC, Espera Jr AH, et al. (2019) Advances in 3D printing of thermoplastic polymer composites and nanocomposites. Prog Polym Sci 98: 101162. https://doi.org/10.1016/j.progpolymsci.2019.101162 doi: 10.1016/j.progpolymsci.2019.101162
![]() |
[46] |
Lee JY, An J, Chua CK (2017) Fundamentals and applications of 3D printing for novel materials. Appl Mater Today 7: 120–133. https://doi.org/10.1016/j.apmt.2017.02.004 doi: 10.1016/j.apmt.2017.02.004
![]() |
[47] | Prabhakar MM, Saravanan AK, Lenin AH, et al. (2021) A short review on 3D printing methods, process parameters and materials. Mater Today: Proc 45: 6108–6114. Available from: https://www.sciencedirect.com/science/article/pii/S2214785320378317. |
[48] | Picard M, Mohanty AK, Misra M (2020) Recent advances in additive manufacturing of engineering thermoplastics: challenges and opportunities. RSC Adv 10: 36058–36089. Available from: https://pubs.rsc.org/en/content/articlehtml/2020/ra/d0ra04857g. |
[49] |
Blok LG, Longana ML, Yu H, et al. (2018) An investigation into 3D printing of fibre reinforced thermoplastic composites. Addit Manuf 22: 176–186. https://doi.org/10.1016/j.addma.2018.04.039 doi: 10.1016/j.addma.2018.04.039
![]() |
[50] | Singh S, Ramakrishna S, Berto F (2019) 3D Printing of polymer composites: A short review. Mater Des Process Commun 2: e97. https://doi.org/10.1002/mdp2.97 |
[51] | Fred Fischer, Stratasys, Inc. Thermoplastics: the best choice for 3D printing. WHITE PAPER. Available from: https://www.smg3d.co.uk/files/ssys-wp-thermoplastics-09-11_ashx.pdf. |
[52] | Ramya A, Vanapalli SI (2016) 3D printing technologies in various applications. Int J Mech Eng Technol 7: 396–409. Available from: https://www.robolab.in/wp-content/uploads/2017/12/IJMET_07_03_036.pdf. |
[53] |
Martinez DW, Espino MT, Cascolan HM, et al. (2022) A comprehensive review on the application of 3D printing in the aerospace industry. Key Eng Mater 913: 27–34. https://doi.org/10.4028/p-94a9zb doi: 10.4028/p-94a9zb
![]() |
[54] |
Jagadeesh P, Rangappa SM, Siengchin S, et al. (2022) Sustainable recycling technologies for thermoplastic polymers and their composites: A review of the state of the art. Polym Compos 43: 5831–5862. https://doi.org/10.1002/pc.27000 doi: 10.1002/pc.27000
![]() |
[55] | Sethi B (2016) Methods of recycling. Recycl Polym: Methods, Charact Appl, 55–114. https://doi.org/10.1002/9783527689002.ch3 |
[56] |
Dogu O, Pelucchi M, Vijver RV, et al. (2021) The chemistry of chemical recycling of solid plastic waste via pyrolysis and gasification: state-of-the-art, challenges, and future directions. Prog Energy Combust 84: 100901. https://doi.org/10.1016/j.pecs.2020.100901 doi: 10.1016/j.pecs.2020.100901
![]() |
[57] | Jubinville D, Esmizadeh E, Saikrishnan S, et al. (2020) A comprehensive review of global production and recycling methods of polyolefin (PO) based products and their post-recycling applications. Sustainable Mater Technol 25: e00188. https://doi.org/10.1016/j.susmat.2020.e00188 |
[58] | Zhang F, Zhao YT, Wang DD, et al. (2021) Current technologies for plastic waste treatment: A review. J Cleaner Prod 282: 124523. Available from: https://www.sciencedirect.com/science/article/pii/S0959652620345674. |
[59] | Markandeya N, Joshi AN, Chavan NN, et al. (2023) Plastic recycling: challenges, opportunities, and future aspects. Adv Mater Recycled Waste, 317–356. Available from: https://www.sciencedirect.com/science/article/pii/B9780323856041000147. |
[60] |
Kumar M, Bolan S, Padhye LP, et al. (2023) Retrieving back plastic wastes for conversion to value added petrochemicals: Opportunities, challenges and outlooks. Appl Energy 345: 121307. https://doi.org/10.1016/j.apenergy.2023.121307 doi: 10.1016/j.apenergy.2023.121307
![]() |
[61] |
Kazemi M, Kabir SF, Fini EH (2021) State of the art in recycling waste thermoplastics and thermosets and their applications in construction. Resour Conserv Recycl 174: 105776. https://doi.org/10.1016/j.resconrec.2021.105776 doi: 10.1016/j.resconrec.2021.105776
![]() |
[62] |
Cheng FM, Li HD, Jiang W, et al. (2006) Properties of compatibilized nylon 6/ABS polymer blends. J Macromol Sci, Part B: Phys 45: 557–561. https://doi.org/10.1080/00222340600770095 doi: 10.1080/00222340600770095
![]() |
[63] |
Lay M, Thajudin NLN, Hamid ZAA, et al. (2019) Comparison of physical and mechanical properties of PLA, ABS and nylon 6 fabricated using fused deposition modeling and injection molding. Composites Part B 176: 107341. https://doi.org/10.1016/j.compositesb.2019.107341 doi: 10.1016/j.compositesb.2019.107341
![]() |
[64] |
Al-Mazrouei N, Al-Marzouqi AH, Ahmed W (2022) Characterization and sustainability potential of recycling 3D-printed nylon composite wastes. Sustainability 14: 10458. https://doi.org/10.3390/su141710458 doi: 10.3390/su141710458
![]() |
[65] |
Kuram E, Ozcelik B, Yilmaz F (2015) The effects of recycling process on thermal, chemical, rheological, and mechanical properties of PC/ABS binary and PA6/PC/ABS ternary blends. J Elastomers Plast 48: 164–181. https://doi.org/10.1177/0095244315576239 doi: 10.1177/0095244315576239
![]() |
[66] |
Farina I, Singh N, Colangelo F, et al. (2019) High-performance nylon-6 sustainable filaments for additive manufacturing. Materials 12: 3955. https://doi.org/10.3390/ma12233955 doi: 10.3390/ma12233955
![]() |
[67] |
Gomes TE, Cadete MS, Dias-de-Oliveira J, et al. (2022) Controlling the properties of parts 3D printed from recycled thermoplastics: A review of current practices. Polym Degrad Stab 196: 109850. https://doi.org/10.1016/j.polymdegradstab.2022.109850 doi: 10.1016/j.polymdegradstab.2022.109850
![]() |
[68] |
Andrady AL, Barnes PW, Bornman JF, et al. (2022) Oxidation and fragmentation of plastics in a changing environment; from UV-radiation to biological degradation. Sci Total Environ 851: 158022. https://doi.org/10.1016/j.scitotenv.2022.158022 doi: 10.1016/j.scitotenv.2022.158022
![]() |
[69] | Dilkes-Hoffman LS, Pratt S, Lant PA, et al. (2019) The role of biodegradable plastic in solving plastic solid waste accumulation. Plast Energy, 469–505. https://doi.org/10.1016/B978-0-12-813140-4.00019-4 |
[70] | Cano-Vicent A, Tambuwala MM, Hassan SS, et al. (2021) Fused deposition modelling: current status, methodology, applications and future prospects. Addit Manuf 47: 102378. Available from: https://www.sciencedirect.com/science/article/pii/S2214860421005327. |
[71] |
Gregory DA, Fricker ATR, Mitrev P, et al. (2023) Additive manufacturing of polyhydroxyalkanoate-based blends using fused deposition modelling for the development of biomedical devices. J Funct Biomater 14: 40. https://doi.org/10.3390/jfb14010040 doi: 10.3390/jfb14010040
![]() |
[72] |
Vaes D, Puyvelde PV (2021) Semi-crystalline feedstock for filament-based 3D printing of polymers. Prog Polym Sci 118: 101411. https://doi.org/10.1016/j.progpolymsci.2021.101411 doi: 10.1016/j.progpolymsci.2021.101411
![]() |
[73] |
Bakır AA, Atik R, Ö zerinç S (2021) Mechanical properties of thermoplastic parts produced by fused deposition modeling: A review. Rapid Prototyping J 27: 537–561. https://doi.org/10.1108/RPJ-03-2020-0061 doi: 10.1108/RPJ-03-2020-0061
![]() |
[74] |
Fico D, Rizzo D, Casciaro R, et al. (2022) A review of polymer-based materials for fused filament fabrication (FFF): Focus on sustainability and recycled materials. Polymers 14: 465. https://doi.org/10.3390/polym14030465 doi: 10.3390/polym14030465
![]() |
[75] |
Squires AD, Lewis RA (2018) Feasibility and characterization of common and exotic filaments for use in 3D printed terahertz devices. J Infrared Millimeter Terahertz Waves 39: 614–635. https://doi.org/10.1007/s10762-018-0498-y doi: 10.1007/s10762-018-0498-y
![]() |
[76] |
Atakok G, Kam M, Koc HB (2022) A review of mechanical and thermal properties of products printed with recycled filaments for use in 3D printers. Surf Rev Lett 29: 2230002. https://doi.org/10.1142/S0218625X22300027 doi: 10.1142/S0218625X22300027
![]() |
[77] |
Gilding DK, Reed AM (1979) Biodegradable polymers for use in surgery—poly (ethylene oxide) poly (ethylene terephthalate) (PEO/PET) copolymers: 1. Polymer 20: 1454–1458. https://doi.org/10.1016/0032-3861(79)90008-9 doi: 10.1016/0032-3861(79)90008-9
![]() |
[78] | Alshehrei F (2017) Biodegradation of synthetic and natural plastic by microorganisms. J Appl Environ Microbiol 5: 8–19. Available from: https://pubs.sciepub.com/jaem/5/1/2/. |
[79] | Sharma M, Sharma P, Sharma A, et al. (2015) Microbial degradation of plastic-A brief review. CIBTech J Microbiol 4: 85–89. Available from: https://www.cibtech.org/J-Microbiology/PUBLICATIONS/2015/Vol-4-No-1/13-CJM-MARCH-013-SUBHASH-MICROBIAL.pdf. |
[80] | Zeenat, Elahi A, Bukhari DA, et al. (2021) Plastics degradation by microbes: a sustainable approach. J King Saud Univ Sci 33: 101538. Available from: https://www.sciencedirect.com/science/article/pii/S1018364721001993. |
[81] |
Bhagia S, Bornani K, Agrawal R, et al. (2021) Critical review of FDM 3D printing of PLA biocomposites filled with biomass resources, characterization, biodegradability, upcycling and opportunities for biorefineries. Appl Mater Today 24: 101078. https://doi.org/10.1016/j.apmt.2021.101078 doi: 10.1016/j.apmt.2021.101078
![]() |
[82] |
Hassan M, Mohanty AK, Misra M (2024) 3D printing in upcycling plastic and biomass waste to sustainable polymer blends and composites: A review. Mater Des 237: 112558. https://doi.org/10.1016/j.matdes.2023.112558 doi: 10.1016/j.matdes.2023.112558
![]() |
[83] |
Anwajler B, Zdybel E, Tomaszewska-Ciosk E (2023) Innovative polymer composites with natural fillers produced by additive manufacturing (3D Printing)—A literature review. Polymers 15: 3534. https://doi.org/10.3390/polym15173534 doi: 10.3390/polym15173534
![]() |
[84] |
Rett JP, Traore YL, Ho EA (2021) Sustainable materials for fused deposition modeling 3D printing applications. Adv Eng Mater 23: 2001472. https://doi.org/10.1002/adem.202001472 doi: 10.1002/adem.202001472
![]() |
[85] | Ji AQ (2023) Utilization of biomass and industrial waste on 3D printing. Available from: https://experts.esf.edu/view/pdfCoverPage?instCode = 01SUNY_ESF & filePid = 1368217480004826 & download = true. |
[86] |
Zhao HY, Jia Y, Chen GX, et al. (2023) Research status and progress of biomass-based 3D printing materials. Innovative Technol Print Packag 991: 608–615. https://doi.org/10.1007/978-981-19-9024-3_79 doi: 10.1007/978-981-19-9024-3_79
![]() |
[87] |
Zander NE, Park JH, Boelter ZR, et al. (2019) Recycled cellulose polypropylene composite feedstocks for material extrusion additive manufacturing. ACS Omega 4: 13879–13888. https://doi.org/10.1021/acsomega.9b01564 doi: 10.1021/acsomega.9b01564
![]() |
[88] |
Kuhnt T, Camarero-Espinosa S (2021) Additive manufacturing of nanocellulose based scaffolds for tissue engineering: Beyond a reinforcement filler. Carbohydr Polym 252: 117159. https://doi.org/10.1016/j.carbpol.2020.117159 doi: 10.1016/j.carbpol.2020.117159
![]() |
[89] | Pereira C, Pereira AM, Freire C, et al. (2020) Nanoengineered textiles: from advanced functional nanomaterials to groundbreaking high-performance clothing. Handbook of Functionalized Nanomaterials for Industrial Applications, 611–714. https://doi.org/10.1016/B978-0-12-816787-8.00021-1 |
[90] |
Henke K, Treml S (2013) Wood based bulk material in 3D printing processes for applications in construction. Eur J Wood Prod 71: 139–141. https://doi.org/10.1007/s00107-012-0658-z doi: 10.1007/s00107-012-0658-z
![]() |
[91] |
Kariz M, Sernek M, Kuzman MK (2015) Use of wood powder and adhesive as a mixture for 3D printing. Eur J Wood Prod 74: 123–126. https://doi.org/10.1007/s00107-015-0987-9 doi: 10.1007/s00107-015-0987-9
![]() |
[92] |
Kromoser B, Reichenbach S, Hellmayr R, et al. (2022) Circular economy in wood construction—Additive manufacturing of fully recyclable walls made from renewables: proof of concept and preliminary data. Constr Build Mater 344: 128219. https://doi.org/10.1016/j.conbuildmat.2022.128219 doi: 10.1016/j.conbuildmat.2022.128219
![]() |
[93] |
Nadagouda MN, Ginn M, Rastogi V (2020) A review of 3D printing techniques for environmental applications. Curr Opin Chem Eng 28: 173–178. https://doi.org/10.1016/j.coche.2020.08.002 doi: 10.1016/j.coche.2020.08.002
![]() |
[94] |
Khosravani MR, Reinicke T (2020) On the environmental impacts of 3D printing technology. Appl Mater Today 20: 100689. https://doi.org/10.1016/j.apmt.2020.100689 doi: 10.1016/j.apmt.2020.100689
![]() |
[95] | Gao CJ, Wolff S, Wang S (2021) Eco-friendly additive manufacturing of metals: Energy efficiency and life cycle analysis. J Manuf Syst 60: 459–472. Available from: https://www.sciencedirect.com/science/article/pii/S0278612521001357. |
[96] | Peng T (2016) Analysis of energy utilization in 3D printing processes. Proc CIRP 40: 62–67. Available from: https://www.sciencedirect.com/science/article/pii/S2212827116000706. |
[97] |
Kanyilmaz A, Demir AG, Chierici M, et al. (2022) Role of metal 3D printing to increase quality and resource-efficiency in the construction sector. Addit Manuf 50: 102541. https://doi.org/10.1016/j.addma.2021.102541 doi: 10.1016/j.addma.2021.102541
![]() |
[98] |
Abdalla H, Fattah KP, Abdallah M, et al. (2021) Environmental footprint and economics of a full-scale 3D-printed house. Sustainability 13: 11978. https://doi.org/10.3390/su132111978 doi: 10.3390/su132111978
![]() |
[99] | Kamran M, Saxena A (2016) A comprehensive study on 3D printing technology. MIT Int J Mech Eng 6: 63–69. Available from: https://www.researchgate.net/publication/310961474_A_Comprehensive_Study_on_3D_Printing_Technology. |
[100] |
Weng YW, Li MY, Ruan SQ, et al. (2020) Comparative economic, environmental and productivity assessment of a concrete bathroom unit fabricated through 3D printing and a precast approach. J Cleaner Prod 261: 121245. https://doi.org/10.1016/j.jclepro.2020.121245 doi: 10.1016/j.jclepro.2020.121245
![]() |
[101] |
Maffia S, Chiappini F, Maggiani G, et al. (2023) Enhancing productivity and efficiency in conventional laser metal deposition process for Inconel 718—Part Ⅱ: advancing the process performance. Int J Adv Manuf Technol 129: 279–298. https://doi.org/10.1007/s00170-023-12197-0. doi: 10.1007/s00170-023-12197-0
![]() |
[102] |
Nguyen D, Murialdo M, Hornbostel K, et al. (2019) 3D Printed polymer composites for CO2 capture. Ind Eng Chem Res 58: 22015–22020. https://doi.org/10.1021/acs.iecr.9b04375 doi: 10.1021/acs.iecr.9b04375
![]() |
[103] |
Thakkar H, Eastman S, Hajari A, et al. (2016) 3D-printed zeolite monoliths for CO2 removal from enclosed environments. ACS Appl Mater Interface 8: 27753–27761. https://doi.org/10.1021/acsami.6b09647 doi: 10.1021/acsami.6b09647
![]() |
[104] |
Ligon SC, Liska R, Stampfl J, et al. (2017) Polymers for 3D printing and customized additive manufacturing. Chem Rev 117: 10212–10290. https://doi.org/10.1021/acs.chemrev.7b00074 doi: 10.1021/acs.chemrev.7b00074
![]() |
[105] |
Soliman A, AlAmoodi N, Karanikolos GN, et al. (2020) A review on new 3-D printed materials' geometries for catalysis and adsorption: paradigms from reforming reactions and CO2 capture. Nanomaterials 10: 2198. https://doi.org/10.3390/nano10112198 doi: 10.3390/nano10112198
![]() |
[106] |
Sola A (2022) Materials requirements in fused filament fabrication: A framework for the design of next-generation 3D printable thermoplastics and composites. Macromol Mater Eng 307: 2200197. https://doi.org/10.1002/mame.202200197 doi: 10.1002/mame.202200197
![]() |
[107] | Nazir MH, Al-Marzouqi AH, Ahmed W, et al. (2023) The potential of adopting natural fibers reinforcements for fused deposition modeling: Characterization and implications. Heliyon 9: e15023. Available from: https://www.cell.com/heliyon/pdf/S2405-8440(23)02230-2.pdf. |
[108] |
Salamone F, Danza L, Meroni I, et al. (2017) A low-cost environmental monitoring system: How to prevent systematic errors in the design phase through the combined use of additive manufacturing and thermographic techniques. Sensors 17: 828. https://doi.org/10.3390/s17040828 doi: 10.3390/s17040828
![]() |
[109] |
Zhao L, Yao YJ, Huang S, et al. (2023) Design and implementation of a low-cost and multi-parameter indoor air quality detector based on IoT. Int J Comput Appl T 72: 296–307. https://doi.org/10.1504/IJCAT.2023.133879 doi: 10.1504/IJCAT.2023.133879
![]() |
[110] |
Aizlewood C, Dimitroulopoulou C (2006) The HOPE project: The UK experience. Indoor Built Environ 15: 393–409. https://doi.org/10.1177/1420326X06069578 doi: 10.1177/1420326X06069578
![]() |
[111] | Wang Y, Mackenzie FV, Ingenhut B, et al. (2018) AP4. 1-miniaturized 3D printed particulate matter sensor for personal monitoring. 17th International Meeting on Chemical Sensors. https://doi.org/10.5162/IMCS2018/AP4.1 |
[112] |
Xu X, Xiao SN, Willy HJ, et al. (2020) 3D-printed grids with polymeric photocatalytic system as flexible air filter. Appl Catal B 262: 118307. https://doi.org/10.1016/j.apcatb.2019.118307 doi: 10.1016/j.apcatb.2019.118307
![]() |
[113] | Kumar AR, Arya S, Levy A, et al. (2020) Scale and numerical modeling to determine operating points of a non-clogging vortecone filter in mining operation. Prog Scale Model Int J 1, Article 7. Available from: https://uknowledge.uky.edu/psmij/vol1/iss1/7/. |
[114] |
Aghaei A, Firouzjaei MD, Karami P, et al. (2022) The implications of 3D-printed membranes for water and wastewater treatment and resource recovery. Can J Chem Eng 100: 2309–2321. https://doi.org/10.1002/cjce.24488 doi: 10.1002/cjce.24488
![]() |
[115] | Tijing LD, Dizon JRC, Ibrahim I, et al. (2020) 3D printing for membrane separation, desalination and water treatment. Appl Mater Today 18: 100486. Available from: https://www.sciencedirect.com/science/article/pii/S2352940719306055. |
[116] |
Ye YY, Du Y, Hu TY, et al. (2021) 3D printing of integrated ceramic membranes by the DLP method. Ind Eng Chem Res 60: 9368–9377. https://doi.org/10.1021/acs.iecr.1c02224 doi: 10.1021/acs.iecr.1c02224
![]() |
[117] | Kotz F, Helmer D, Rapp BE (2020) Emerging technologies and materials for high-resolution 3D printing of microfluidic chips. Microfluidics in Biotechnology 37–66. https://doi.org/10.1007/10_2020_141 |
[118] |
Jonhson W, Xu X, Bian K, et al. (2022) 3D-printed hierarchical ceramic architectures for ultrafast emulsion treatment and simultaneous oil-water filtration. ACS Mater Lett 4: 740–750. https://doi.org/10.1021/acsmaterialslett.2c00147 doi: 10.1021/acsmaterialslett.2c00147
![]() |
[119] | Jin Z, Mei H, Liu H, et al. (2022) High-strength, superhydrophilic/underwater superoleophobic multifunctional ceramics for high efficiency oil-water separation and water purification. Mater Today Nano 18: 100199. Available from: https://www.sciencedirect.com/science/article/pii/S258884202200027X. |
[120] |
Sreedhar N, Kumar M, Al Jitan S, et al. (2022) 3D printed photocatalytic feed spacers functionalized with β-FeOOH nanorods inducing pollutant degradation and membrane cleaning capabilities in water treatment. Appl Catal B 300: 120318. https://doi.org/10.1016/j.apcatb.2021.120318 doi: 10.1016/j.apcatb.2021.120318
![]() |
[121] |
Sreelekshmy BR, Rajappan AJ, Basheer R, et al. (2020) Tuning of surface characteristics of anodes for efficient and sustained power generation in microbial fuel cells. ACS Appl Bio Mater 3: 6224–6236. https://doi.org/10.1021/acsabm.0c00753 doi: 10.1021/acsabm.0c00753
![]() |
[122] | Cai T, Meng LJ, Chen G, et al. (2020) Application of advanced anodes in microbial fuel cells for power generation: A review. Chemosphere 248: 125985. Available from: https://www.sciencedirect.com/science/article/pii/S0045653520301776. |
[123] |
Mishra S, Ghosh S, Singh T (2020) Progress in materials development for flexible perovskite solar cells and future prospects. ChemSusChem 14: 512–538. https://doi.org/10.1002/cssc.202002095 doi: 10.1002/cssc.202002095
![]() |
[124] |
Liu CH, Xiao CY, Xie CC, et al. (2021) Flexible organic solar cells: materials, large-area fabrication techniques and potential applications. Nano Energy 89: 106399. https://doi.org/10.1016/j.nanoen.2021.106399 doi: 10.1016/j.nanoen.2021.106399
![]() |
[125] | Tian YX, Wang XQ, Li J, et al. (2022) Rapid manufacturing of turbine blades based on reverse engineering and 3D printing technology. Proceedings of 2022 Chinese Intelligent Systems Conference, 540–553. https://doi.org/10.1007/978-981-19-6203-5_53 |
[126] |
Rahimizadeh A, Kalman J, Fayazbakhsh K, et al. (2021) Mechanical and thermal study of 3D printing composite filaments from wind turbine waste. Polym Compos 42: 2305–2316. https://doi.org/10.1002/pc.25978 doi: 10.1002/pc.25978
![]() |
[127] | Dzogbewu TC, Beer DJ (2023) Additive manufacturing of selected ecofriendly energy devices. Virtual Phys Prototyp 18: e2150230. https://doi.org/10.1080/17452759.2023.2276245 |
[128] |
Browne MP, Redondo E, Pumera M (2020) 3D printing for electrochemical energy applications. Chem Rev 120: 2783–2810. https://doi.org/10.1021/acs.chemrev.9b00783 doi: 10.1021/acs.chemrev.9b00783
![]() |
[129] | Wang H, Xiong BD, Zhang ZT, et al. (2023) Small wind turbines and their potential for internet of things applications. iScience 26: 107674. Available from: https://www.ncbi.nlm.nih.gov/pmc/articles/PMC10497799/. |
[130] |
Kantaros A, Soulis E, Petrescu FIT, et al. (2023) Advanced composite materials utilized in FDM/FFF 3D printing manufacturing processes: the case of filled filaments. Materials 16: 6210. https://doi.org/10.3390/ma16186210 doi: 10.3390/ma16186210
![]() |
[131] |
Al-Maharma AY, Patil SP, Markert B (2020) Effects of porosity on the mechanical properties of additively manufactured components: A critical review. Mater Res Express 7: 122001. https://doi.org/10.1088/2053-1591/abcc5d doi: 10.1088/2053-1591/abcc5d
![]() |
[132] |
Okolie O, Kumar A, Edwards C, et al. (2023) Bio-based sustainable polymers and materials: From processing to biodegradation. J Compos Sci 7: 213. https://doi.org/10.3390/jcs7060213 doi: 10.3390/jcs7060213
![]() |
1. | Jing Zeng, Hechao Liu, Lihua You, Extremal Results on ℓ-Connected Graphs or Pancyclic Graphs Based on Wiener-Type Indices, 2024, 13, 2227-7390, 10, 10.3390/math13010010 |