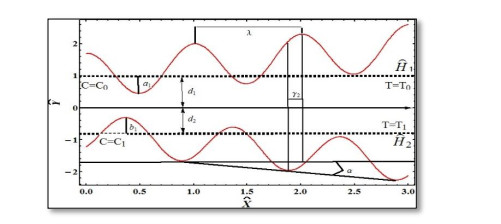
The main goal of this article is to investigate the effects of pseudoplastic, and dilatants behavior of non-Newtonian based nanofluid on peristaltic motion in an asymmetric tapered channel. Buongiorno's nanofluid model is considered for the study to investigate the heat and mass transfer analysis. The Reiner-Philippoff fluid model is considered to depict the non-Newtonian characteristics of the fluid. The Reiner Philippoff fluid model is the most challenging model among other non-Newtonian fluid models in such a way that shear stress and velocity gradient are non-linearly proportional to each other in this model. This model also represents the implicit relation between stress and deformation rate. The governing equations are based on the dispersion model for nanofluid which incorporates the effects of thermophoretic and Brownian diffusions. The governing equations are simplified in the account of the small Reynolds number and long wavelength assumptions. The solution of the equations is retrieved numerically by the help of built in ND-Solve function of MATHEMATICA software. The sound effects of Reiner-Philippoff based nanofluid on the behavior of velocity and temperature profiles of the fluid, streamlines, pressure gradient fields, and concentration of the nanoparticles are discussed thoroughly. The interesting behavior of Reiner-Philippoff fluid for two limiting shear stress cases when shear stress parameter is very small and very large, for which Reiner-Philippoff fluid behaves like a Newtonian fluid, is also verified. It is observed that fluid flow changes its properties from dilatants fluid to Newtonian and from Newtonian to pseudoplastic fluid by varying the Reiner-Philippoff fluid parameter. According to the findings, the temperature graphs rise against higher thermophoretic diffusion and Brownian motion parameters and falls with higher Prandtl number. Further, the impacts of all the significant parameters are investigated briefly by mathematically as well as graphically.
Citation: Muhammad Tahir, Yasir Khan, Adeel Ahmad. Impact of pseudoplastic and dilatants behavior of Reiner-Philippoff nanofluid on peristaltic motion with heat and mass transfer analysis in a tapered channel[J]. AIMS Mathematics, 2023, 8(3): 7115-7141. doi: 10.3934/math.2023359
[1] | Mohammed Alrehili . Managing heat transfer effectiveness in a Darcy medium with a vertically non-linear stretching surface through the flow of an electrically conductive non-Newtonian nanofluid. AIMS Mathematics, 2024, 9(4): 9195-9210. doi: 10.3934/math.2024448 |
[2] | Nadeem Abbas, Wasfi Shatanawi, Taqi A. M. Shatnawi . Innovation of prescribe conditions for radiative Casson micropolar hybrid nanofluid flow with inclined MHD over a stretching sheet/cylinder. AIMS Mathematics, 2025, 10(2): 3561-3580. doi: 10.3934/math.2025164 |
[3] | Asifa, Poom Kumam, Talha Anwar, Zahir Shah, Wiboonsak Watthayu . Analysis and modeling of fractional electro-osmotic ramped flow of chemically reactive and heat absorptive/generative Walters'B fluid with ramped heat and mass transfer rates. AIMS Mathematics, 2021, 6(6): 5942-5976. doi: 10.3934/math.2021352 |
[4] | W. Abbas, Ahmed M. Megahed, Osama M. Morsy, M. A. Ibrahim, Ahmed A. M. Said . Dissipative Williamson fluid flow with double diffusive Cattaneo-Christov model due to a slippery stretching sheet embedded in a porous medium. AIMS Mathematics, 2022, 7(12): 20781-20796. doi: 10.3934/math.20221139 |
[5] | Khalil Ur Rehman, Wasfi Shatanawi, Zeeshan Asghar, Haitham M. S. Bahaidarah . Neural networking analysis for MHD mixed convection Casson flow past a multiple surfaces: A numerical solution. AIMS Mathematics, 2023, 8(7): 15805-15823. doi: 10.3934/math.2023807 |
[6] | S. R. Mishra, Subhajit Panda, Mansoor Alshehri, Nehad Ali Shah, Jae Dong Chung . Sensitivity analysis on optimizing heat transfer rate in hybrid nanofluid flow over a permeable surface for the power law heat flux model: Response surface methodology with ANOVA test. AIMS Mathematics, 2024, 9(5): 12700-12725. doi: 10.3934/math.2024621 |
[7] | Khalil Ur Rehman, Nosheen Fatima, Wasfi Shatanawi, Nabeela Kousar . Mathematical solutions for coupled nonlinear equations based on bioconvection in MHD Casson nanofluid flow. AIMS Mathematics, 2025, 10(1): 598-633. doi: 10.3934/math.2025027 |
[8] | Fahad Alsharari, Mohamed M. Mousa . New application of MOL-PACT for simulating buoyancy convection of a copper-water nanofluid in a square enclosure containing an insulated obstacle. AIMS Mathematics, 2022, 7(11): 20292-20312. doi: 10.3934/math.20221111 |
[9] | C. S. K. Raju, S.V. Siva Rama Raju, S. Mamatha Upadhya, N. Ameer Ahammad, Nehad Ali Shah, Thongchai Botmart . A numerical study of swirling axisymmetric flow characteristics in a cylinder with suspended PEG based magnetite and oxides nanoparticles. AIMS Mathematics, 2023, 8(2): 4575-4595. doi: 10.3934/math.2023226 |
[10] | Subhan Ullah, Hassan Ali Ghazwani, Dolat Khan, Zareen A. Khan . Heat transfer augmentation of Jeffery–Hamel hybrid nanofluid in a stretching convergent/divergent channel through porous medium. AIMS Mathematics, 2025, 10(1): 388-402. doi: 10.3934/math.2025018 |
The main goal of this article is to investigate the effects of pseudoplastic, and dilatants behavior of non-Newtonian based nanofluid on peristaltic motion in an asymmetric tapered channel. Buongiorno's nanofluid model is considered for the study to investigate the heat and mass transfer analysis. The Reiner-Philippoff fluid model is considered to depict the non-Newtonian characteristics of the fluid. The Reiner Philippoff fluid model is the most challenging model among other non-Newtonian fluid models in such a way that shear stress and velocity gradient are non-linearly proportional to each other in this model. This model also represents the implicit relation between stress and deformation rate. The governing equations are based on the dispersion model for nanofluid which incorporates the effects of thermophoretic and Brownian diffusions. The governing equations are simplified in the account of the small Reynolds number and long wavelength assumptions. The solution of the equations is retrieved numerically by the help of built in ND-Solve function of MATHEMATICA software. The sound effects of Reiner-Philippoff based nanofluid on the behavior of velocity and temperature profiles of the fluid, streamlines, pressure gradient fields, and concentration of the nanoparticles are discussed thoroughly. The interesting behavior of Reiner-Philippoff fluid for two limiting shear stress cases when shear stress parameter is very small and very large, for which Reiner-Philippoff fluid behaves like a Newtonian fluid, is also verified. It is observed that fluid flow changes its properties from dilatants fluid to Newtonian and from Newtonian to pseudoplastic fluid by varying the Reiner-Philippoff fluid parameter. According to the findings, the temperature graphs rise against higher thermophoretic diffusion and Brownian motion parameters and falls with higher Prandtl number. Further, the impacts of all the significant parameters are investigated briefly by mathematically as well as graphically.
a1 | Amplitude of the upper wall, m; |
Re | Reynolds number; |
b1 | Amplitude of the lower wall, m; |
Pr | Prandtl number; |
a | Unit-less amplitude of the upper wall; |
Ec | Eckert number; |
b | Unit-less amplitude of the lower wall; |
Br | Brinkman number; |
d1+d2 | Channel width, m; |
Sij | Cauchy stress tensor; |
d | Unit-less half channel width; |
RPh | Reiner-Philippoff; |
(⌢X,⌢Y) | Cartesian coordinates, m; |
⌢t | Time, s; |
u | Velocity vector; |
t | Unit-less time; |
(⌢U,⌢V) | Velocity components, m/s; |
T | Temperature of fluid, K; |
(x,y) | Unit-less Cartesian coordinates; |
Nb | Unit-less Brownian parameter; |
(u,v) | Unit-less velocity components. |
k1 | Dimensionless non-uniformity parameter; |
δ | Wave number, S/m; |
⌢H1 | Geometry of the upper wall, m; |
ζ | Phase difference; |
⌢H2 | Geometry of the lower wall, m; |
λ | Wavelength, m; |
c | Peristaltic wave speed, m/s; |
ψ | Stream function; |
h1 | Unit-less geometry of the upper wall; |
Φ | Viscous dissipation; |
h2 | Unit-less geometry of the lower wall; |
λ1 | RPh fluid parameter; |
ˉC | Specific heat, j/kg.K; |
ρ | Density, kg/m3; |
C | Concentration, mol/m3; |
θ | Unit-less temperature; |
T0 | Reference temperature at upper wall, K; |
μ | Dynamic viscosity, Ns/m2; |
T1 | Reference temperature at lower wall, K; |
ν | Kinematics viscosity; |
C0 | Reference concentration at upper wall; |
⌢τ | Shear stress, N/m2; |
C1 | Reference concentration at lower wall; |
τ | Dimensionless shear stress; |
⌢P | Fluid's pressure, N/m2; |
⌢τ0 | Reference shear stress, N/m2; |
p | Dimensionless fluid's pressure; |
ϕ | Dimensionless concentration; |
⌢Q | Instantaneous volumetric flow rate; |
α | non-uniformity angle, radian; |
ˉQ | Time average flow rate; |
γ | Shear stress parameter; |
η | Dimensionless mean flow rate; |
μ0 | zero shear viscosity, Ns/m2; |
DB | Brownian diffusion coefficient. |
DT | Thermophoretic diffusion coefficient; |
f | Base fluid; |
K | Thermal conductivity, W/mK; |
p | Nanoparticles; |
Nt | Unit-less thermophoretic parameter. |
Demand of getting insight of the peristaltic flow is increasing day by day due to its applications in many fields of science and engineering especially in the fields of biology and medical engineering. Spectrum of research on the topic of peristaltic flow got widen by involving non-Newtonian fluids since most of the fluid involved in different biological systems and other field of engineering are non-Newtonian in nature. Peristalsis is a phenomenon in which the sinusoidal waves arise due to the continuous relaxation and diminution of smooth muscular tissues. Some of the natural and engineering systems involving the application of peristalsis motion are locomotion of earthworm, artificial heart pump, transportation of urine starting from the kidneys to the urinary bladder, vasomotion of tiny blood arteries, motion of the food along the digestive tube and blood transport vessels. The Rotho-peristaltic pump is also one of the applications of peristalsis in chemical industry.
Before Thurston [1], blood was treated as a Newtonian fluid. However, viscoelasticity is a basic rheological property of blood which makes the human blood non-Newtonian. Recently interest in problems of non-Newtonian fluid has grown and many mathematical models for describing the rheological behavior of blood have been extensively developed. Many mathematical structures for elaborating the rheological characteristics of blood have been briefly investigated in references [2,3,4,5]. Latham [6] and Shapiro et al. [7] primary reported the fluid dynamical simulation of peristalsis for 2D Newtonian fluid. Tripathi [8] addressed the peristaltic transport of high viscosity across a finite length of channel under the influence of porosity and heat transmission. Hayat et al. [9] explored the significance of hall current on peristaltic flow of Maxwell's fluid passing via porous medium. The latest research on the peristaltic subject can also be seen through references [10,11,12,13,14].The Reiner-Philippoff fluid model is one of the most challenging non-Newtonian fluid models due to implicit relationship of shear stress and strain. Due to this mathematical difficulty, limited literature is available on Reiner-Philippoff fluid model. In 1994, Na [15] was the first to examine the boundary layer flow of Reiner-Philippoff fluid due to free stream velocity. The boundary layer flow of Reiner-Philippoff fluid over a stretching sheet was studied by Yam et al. [16] Ahmad [17] investigated the boundary layer flow of Reiner-Philippoff based nanofluid past a non-linear stretching sheet. Impact of Brownian and thermophoresis diffusions on thin film flow of Reiner-Philippoff fluid was studied by Asad Ullah [18]. Sajid et al. [19] investigates the impact of triple diffusive convective flowing on Reiner-Philippoff (RPh) fluid past a stretching surface with Avramenko-Blinov-Shevchuk boundary restrictions. Also Reiner-Philippoff (RPh) fluid model is discussed by considering blood as a base fluid by Sajid et al. [20]. Tahir and Ahmad [21] initiated the study of peristaltic transportation of Reiner-Philippoff fluid.
Heat transfer plays a significant role in equipment efficiency and material selection. The importance of peristaltic fluid motion with heat transfer is noticeable in biomedical sciences, metabolic heat generation, blood transport, perfusion hypothermia, thermoregulation and in bio-heat exchange processes. The working capability of every biological and mechanical process decays time to time due to the production of heat by such processes. To improve the efficiency of such mechanism it is compulsory to eliminate the heat regularly from the system. Nanofluids are innovative compounds that can control the heat transfer. Nanofluids are made by nanoprecipitation method in ordinary fluids. The ordinary fluids like water, polymer solutions, engine oil and some lubricants have less thermal conductivity values as compared to solids. Including a specific quantity of solid particles to these fluids, can easily enhance the heat conductance of these fluids. These particles are usually of sizes ranging 1-100 nanometer and known as nanoparticles. The consequential mixture of fluid and nanoparticles is called nanofluid. This idea of constructing nanofluids was primarily introduced by Choi [22,23] in 1995. Xuan [24] talked about the improvements of heat transfers for nanofluids. Buongiorno [25] proposed a model that incorporates thermophoresis and Brownian motion phenomena to evaluate the transport of nanofluids. Nanofluids are also helpful and applicable in the understanding of a variety of phenomenon such as the minimization/enhancement of the thermal magnitude of the system, microchannel clogging, miniaturization of the system and minimal clogging. Recently Rasool et al. [26] investigates and provides a numerical analysis of electro-magneto-hydrodynamic (EMHD) nanofluid flows past a Riga pattern embedded horizontally in a Darcy-Forchheimer porous medium. The more literature regarding heat transfer through nanofluids can be seen through references [27,28,29,30,31,32,33]. Many academics are interested in the combined impacts of heat and mass transfer because of its vast spectrum of uses in industry, science, and engineering. These procedures play a critical role in enhancing the product quality. They're used in a variety of pharmaceutical and chemical operations, as well as magnetic drug targeting and electronic devices cooling. Thermal insulation, thermal energy storage, fossil fuel extraction, the paper industry, food processing, oxygenation, porous solid drying, hemodialysis, subterranean energy transmission and geothermal energy recovery are some additional physical examples. Hina [34] in 2012 explored how the compliant walls affected peristaltic flow, heat transfer, mass transport and chemical reactions. Peristaltic movement study of Eyring-Prandtl fluid in a tube together with heat and mass transfer analysis was investigated by Iftikhar et al. [35]. Researcher's contributions to peristaltic flows are fast expanding due to the relevance of heat and mass transport in several fields of engineering and science (see citations [36,37,38,39]).
As discussed earlier that negligible research was available on non-Newtonian Reiner-Philippoff fluid model. And particularly no literature was available on peristaltic motion of Reiner-Philippoff fluid. In previous work [40] heat transfer analysis of Renner-Philippoff nanofluid was discussed by using conventional nanofluid model. Considering the importance of non-Newtonian fluid in peristaltic flow and role of nanoparticles as an efficient agent of heat transfer control, the aim of this article is to explore heat and mass transfer analysis of non-Newtonian Reiner-Philippoff fluid in peristaltic motion in the presence of nanoparticles by using Buongiorno's nanofluid model. The impact of thermophoretic diffusion parameter, Brownian diffusion parameter and Reiner-Philippoff fluid parameter on different quantities of interest is discussed in detail. I hope this study will be step forward in the field of peristaltic flow, heat and mass transfer of non-Newtonian fluids and also provides new avenues of research for scholars to the way of RPh fluid academics.
Consider Reiner-Philippoff (RPh) fluid flowing through a non-uniform (tapered) two-dimensional asymmetric channel to be incompressible. The fluid movement is caused by the sinusoidal waves having wavelength λ and constant speed c along the channel walls. The walls of the non-uniform channel are separated by width d1(⌢X)+d2(⌢X). The coordinate system for the given problem is Cartesian system (⌢X,⌢Y) introduced in such a way that ⌢Y−axis is chosen alongside the width and the ⌢X−axis is along the length of the channel. Geometrical deformation of the walls for discussed problem can be put mathematically as [41]:
⌢H1(⌢X,⌢t)=d1(⌢X,⌢t)+a1cos(2πλ(⌢X−c⌢t)),upperwall | (1) |
⌢H2(⌢X,⌢t)=−d2(⌢X,⌢t)−b1cos(2πλ(⌢X−c⌢t)+ζ),lowerwall, | (2) |
where, di(⌢X,⌢t)=di+(⌢X−c⌢t)tan(α),(i = 1, 2), is the half width of channel, α is the non-uniformity angle of the channel, ⌢H1(⌢X,⌢t) and ⌢H2(⌢X,⌢t) symbolized to show the geometry of the said problem for topper and lower walls respectively corresponding to the coordinate ⌢Y>0 and ⌢Y<0. a1 and b1 are the amplitudes of the topper and lower waves respectively, ⌢t is for the time and ζ(0≤ζ≤π) represents phase difference between the waves, for ζ=0 the channel is reduced to symmetric in which waves are totally out of phase and for ζ=π waves are totally in phase (see Figure 1). Superscript ⌢. is used to indicate the dimensional quantities. Further, d1,a1,d2 and b1 satisfies the following [42]:
a21+b21+2a21b21cosζ≤(d1+d2)2. | (3) |
Two-dimensional velocity fields are taken with the velocity components as ⌢U(⌢X,⌢Y,⌢t) and ⌢V(⌢X,⌢Y,⌢t) along the ⌢X−axis and ⌢Y−axis respectively.
The governing equations for an incompressible RPh fluid flow can be expressed as the following set of equations [43]:
∇.u=0, | (4) |
ρDuD⌢t=∇.Sij, | (5) |
(ρˉC)fDTD⌢t=Kf∇2T+Φ+(ρˉC)p(DB(∇C.∇T)+DT∇C.∇TTm), | (6) |
DCD⌢t=DTTm∇2T+DB∇2C, | (7) |
where, ρf signifies the base fluid density and ρp is the density of particles, u=u(⌢U(⌢X,⌢Y,⌢t),⌢V(⌢X,⌢Y,⌢t),0) indicate velocity vectors, ⌢t is for time, ˉCf is specific heat of base fluid and ˉCp is particles specific heat, Kf indicates the thermal conductivity, T is temperature, C is concentration, DB and DT are stands for Brownian and thermophoretic diffusion coefficients respectively. Sij and Φ are the Cauchy stress tensor and viscous dissipation terms and are given as [44]:
Sij=−⌢PI+⌢τij, | (8) |
Φ=(⌢τ⌢Y⌢Y−⌢τ⌢X⌢X)∂⌢V∂⌢Y+⌢τ⌢X⌢Y(∂⌢U∂⌢Y+∂⌢V∂⌢X). | (9) |
Where for the Reiner-Philippoff (RPh) fluid model, the stress strain relation is specified as [18]:
⌢τij=[μ∞+μ0−μ∞1+(12⌢τ20)(∑2l=1∑2m=1⌢τlm⌢τml)]⌢eij, | (10) |
with,
∑2l=1∑2m=1⌢τlm⌢τml=∑2l=1[⌢τl1⌢τ1l+⌢τl2⌢τ2l] |
= ⌢τ11⌢τ11+⌢τ21⌢τ12+⌢τ12⌢τ21+⌢τ22⌢τ22 |
= ⌢τ112+2⌢τ122+⌢τ222. |
Using ⌢τ12=⌢τ21.
The RPh fluid model (Eq (10)) contain three positive parameters μ∞,μ0 and ⌢τ0. Here μ∞ represents the higher Newtonian limiting viscosity, μ0 is the viscosity at zero shear stress rate and ⌢τ0 indicates the reference shear stress.
In two dimensional Cartesian coordinates system, the continuity Eq (4), momentum Eq (5), the thermal energy Eq (6) and the concentration Eq (7) in laboratory frame are expressed as:
∂⌢U∂⌢X+∂⌢V∂⌢Y=0, | (11) |
(ρf)(∂∂⌢t+⌢U∂∂⌢X+⌢V∂∂⌢Y)⌢U=−∂⌢P∂⌢X+∂⌢τ⌢X⌢X∂⌢X+∂⌢τ⌢X⌢Y∂⌢Y, | (12) |
(ρf)(∂∂⌢t+⌢U∂∂⌢X+⌢V∂∂⌢Y)⌢V=−∂⌢P∂⌢Y+∂⌢τ⌢Y⌢X∂⌢X+∂⌢τ⌢Y⌢Y∂⌢Y, | (13) |
ρfˉCf(∂T∂⌢t+⌢U∂T∂⌢X+⌢V∂T∂⌢Y)=Kf(∂2T∂⌢X2+∂2T∂⌢Y2)+[(⌢τ⌢Y⌢Y−⌢τ⌢X⌢X)∂⌢V∂⌢Y+⌢τ⌢X⌢Y(∂⌢U∂⌢Y+∂⌢V∂⌢X)] |
+ΓρfˉCf[DB(∂T∂⌢Y∂C∂⌢Y+∂C∂⌢X∂T∂⌢X)+DTTm(∂T∂⌢X+∂T∂⌢Y)2], | (14) |
(∂∂⌢t+⌢U∂∂⌢X+⌢V∂∂⌢Y)C=DTTm(∂2T∂⌢X2+∂2T∂⌢Y2)+DB(∂2C∂⌢X2+∂2C∂⌢Y2), | (15) |
where, Γ=ρpˉCpρfˉCf and Eq (10) in component form can be written as:
⌢τ⌢X⌢X=[μ∞+μ0−μ∞1+(12⌢τ20)(⌢τ⌢X⌢X2+2⌢τ⌢X⌢Y2+⌢τ⌢Y⌢Y2)]⌢e⌢X⌢X, | (16) |
⌢τ⌢X⌢Y=[μ∞+μ0−μ∞1+(12⌢τ20)(⌢τ⌢X⌢X2+2⌢τ⌢X⌢Y2+⌢τ⌢Y⌢Y2)]⌢e⌢X⌢Y, | (17) |
⌢τ⌢Y⌢Y=[μ∞+μ0−μ∞1+(12⌢τ20)(⌢τ⌢X⌢X2+2⌢τ⌢X⌢Y2+⌢τ⌢Y⌢Y2)]⌢e⌢Y⌢Y, | (18) |
where,
⌢e⌢X⌢X=2.∂⌢U∂⌢X,⌢e⌢Y⌢Y=2.∂⌢V∂⌢Y and ⌢e⌢X⌢Y=(∂⌢V∂⌢X+∂⌢U∂⌢Y). | (19) |
The subsequent transformations are used to change the investigated problem from stationary reference frame to moving frame [45]:
{⌢x=⌢X−c⌢t,⌢y=⌢Y,̑v(⌢x,⌢y)=⌢V(⌢X,⌢Y,⌢t)⌢p(⌢x,⌢y)=⌢P(⌢X,⌢Y,⌢t)⌢u(⌢x,⌢y)=⌢U(⌢X,⌢Y,⌢t)−c. | (20) |
And the following dimensionless quantities are used to convert the above dimensional system in dimensionless form:
{x=⌢xλ,y=⌢yd1,t=c⌢tλ,u=⌢uc,v=⌢vcδ,δ=d1λ,τij=d1⌢τijcμf,p=d21⌢pcμfλ,h1=⌢H1d1,h2=⌢H2d1,a=a1d1,b=b1d1,d=d2d1,ν=μfρf,Pr=μfCfKf,Re=cd1ρfμf,Ec=c2CfΔT,Br=Pr.Ec,θ=T−TmT1−T0,ϕ=C−CmC1−C0,Nb=ΓDB(C1−C0)ν,Nt=ΓDT(T1−T0)νTm. | (21) |
Here h1 and h2 represents the dimension free forms of both walls, ν is kinematics viscosity, d is the channel width ratio, ϕ indicates the concentration of nanoparticles, Nb is the parameter of Brownian motion, Nt is indicate the thermophoresis diffusion parameter, θ correspond to dimension free temperature, Pr, Re, Ec and Br are the Prandtl number, Reynolds number, Eckert number and Brinkman number respectively.
The dimensionless form of the governing equations in the wave frame in accounts of Eq (20) and the quantities (21) is as:
∂u∂x+.∂v∂y=0, | (22) |
δRe{[∂∂t+(u+1)∂∂x+v∂∂y](u+1)}=−∂p∂x+δ(∂τxx∂x)+∂τxy∂y, | (23) |
δ3Re{[∂∂t+(u+1)∂∂x+v∂∂y]v}=−∂p∂y+δ2(∂τyx∂x)+δ∂τyy∂y, | (24) |
δRePr{[∂θ∂t+(u+1)∂θ∂x+v∂θ∂y]} |
=(δ2∂2θ∂x2+∂2θ∂y2)+δBr(τyy−τxx)∂v∂y+Brτxy(∂u∂y+δ2∂v∂x) |
+PrNb(∂θ∂y∂ϕ∂y+δ2∂ϕ∂x∂θ∂x)+PrNb(δ2∂θ∂x+∂θ∂y)2, | (25) |
δRe(ΔC.Γ)[∂ϕ∂t+(u+1)∂ϕ∂x+v∂ϕ∂y]=Nt(δ2∂2θ∂x2+∂2θ∂y2)+Nb(δ2∂2ϕ∂x2+∂2ϕ∂y2), | (26) |
and corresponding dimensionless form of Eqs (16)-(18) are as under:
τxx=δ[1+λ1−11+12τ20(τ2xx+2τ2xy+τ2yy)]∂u∂x, | (27) |
τyy=δ[1+λ1−11+12τ20(τ2xx+2τ2xy+τ2yy)]∂v∂y, | (28) |
τxy=[1+λ1−11+12τ20(τ2xx+2τ2xy+τ2yy)]∂u∂y. | (29) |
In above equations λ1=μ0μ∞. Now by using the estimations of lengthy wavelength (δ<<1), small Reynolds number and by using the description of following stream functions:
u=∂ψ∂y and v=−∂ψ∂x. | (30) |
Equation (22) satisfies identically and Eqs (23)-(29) simplifies to the following form:
∂p∂x=∂∂yτxy, | (31) |
∂p∂y=0, | (32) |
∂2θ∂y2+Brτxy(∂2ψ∂y2)+PrNb(∂θ∂y∂ϕ∂y)+PrNt(∂θ∂y)2=0, | (33) |
NbNt(∂2ϕ∂y2)+∂2θ∂y2=0, | (34) |
τxx=0 and τyy=0, | (35) |
and
τxy=(1+λ1−11+(τ2xyτ20))∂2ψ∂y2. | (36) |
From Eqs (31) and (32) we have:
∂2∂y2τxy=0. | (37) |
Which depicts that τxy is a linear function of y and can be written as τxy=A1y+B1, where A1 and B1 are arbitrary parameters. And Eq (36) can be written as:
∂2ψ∂y2=τxy[γ+τ2xyτ2xy+γλ1]. | (38) |
This is explicit relationship between deformation rate and shear stress for RPh nanofluid. Where, λ1=μ0μ∞ and γ=τ20 are RPh fluid parameter and shear stress parameter respectively. For λ1=1 this relation converges to Newtonian fluid.
The dimension freeform of the walls h1(x) and h2(x) are is given as:
{h1(x)=1+k1x+acos[2πx],h2(x)=−d−k1x−bcos[2πx+ζ], | (39) |
where, k1=λtanαd1 is the non-uniformity parameter of the channel.
The instantaneous volumetric flow rate in the laboratory frame of reference is given by:
⌢Q(⌢X,⌢t)=∫⌢H1⌢H2⌢U(⌢X,⌢Y,⌢t)d⌢Y, | (40) |
where, ⌢H1 and ⌢H2 are the functions of ⌢X and ⌢t. Now using Eq (19), Eq (40) becomes:
⌢Q(⌢X,⌢t)=∫⌢h1⌢h2⌢u(⌢x,⌢y)d⌢y+c(⌢h1−⌢h2)=⌢q+c(⌢h1−⌢h2), | (41) |
where, ⌢h1(⌢x) and ⌢h2(⌢x) represents the upper, lower channel walls for wave frame and ⌢q(⌢x,⌢y) is the instantaneous volumetric flow rate in the moving frame and is given by:
⌢q(⌢x,⌢y)=∫⌢h1⌢h2⌢u(⌢x,⌢y)d⌢y. | (42) |
The time average flow rate (over one period T) is given by:
ˉQ=1T∫T0⌢Qd⌢t. | (43) |
Using Eq (41) in Eq (43) we have:
ˉQ=1T∫T0⌢qd⌢t+c(⌢h1−⌢h2) |
=⌢q+cd1+cd2+2c⌢xλtanα |
+ca1cos(2πλ⌢x)+cb1cos(2πλ⌢x+ζ). | (44) |
We note that h1(x) and h2(x) given in Eq (39) are the corresponding dimension free forms of the non-uniform peristaltic channel. So the corresponding dimension free form of Eq (44) is given as:
η=F+1+d+2k1x+acos(2πx)+bcos(2πx+ζ), | (45) |
where, η=ˉQcd1 and F=⌢qcd1 are the dimension free mean flow rates in the fixed and moving frame respectively and the expression of F is given as:
F=∫h1h2u(x,y)dy=∫h1h2∂ψ∂ydy=ψ(h1)−ψ(h2). | (46) |
The associated dimensionless boundary conditions are:
{ψ=F2,ψ'=−1,θ=−0.5,ϕ=−0.5 at upper wall h1(x),ψ=−F2,ψ'=−1,θ=0.5,ϕ=0.5 at lower wall h2(x). | (47) |
Equation (31) depicts that the expression of the pressure function is free from 'y' variable and Eq (36) demonstrates that τxy is a linear function of 'y'. Thus the solution of Eqs (32), (33) and (37) corresponding to the boundary conditions given in Eq (46) is retrieved numerically by the help of built in NDSolve function of MATHEMATICA software. Outcomes of the study are discussed thoroughly by plotting the graphs in rest of this section. We will talk about the effects of RPh nanofluid properties on physical quantities of interest like the axial velocity u, streamline functions ψ, concentration of nanoparticles ϕ, temperature profiles θ, heat transfer rate −θ'(h) and mass transportation rate −ϕ'(h) at the upper boundary and pressure gradient dpdx.
Graphical visualization of velocity profiles against dissimilar values of RPh fluid parameter λ1, shear stress parameter γ, for both pseudoplastic and dilatants fluids and arbitrary parameter A1 is shown in Figures 2-5. Reiner-Philippoff (RPh) fluid behaves like dilatants fluid for λ1<1, as pseudoplastic for λ1 > 1 and as Newtonian fluid for λ1=1. The influence of RPh fluid parameter λ1 on the fluid's velocity profiles is drawing in Figure 2 the blue line in the figure against the value λ1=1 is showing the velocity of Newtonian fluid. Further it is shown that the maximum velocity for pseudoplastic (shear thinning) fluid, corresponding to the value λ1>1, is larger than the velocity of dilatants fluid corresponding to the value of λ1<1. As RPh fluid proceeds as shear thinning (pseudoplastic) fluid for the value λ1>1, therefore its viscosity decreases as compared to shear thickening (dilatants) fluid and that's why the fluid's deformation rate increases and consequently velocity profile improves. RPh fluid model (see Eq (35)) behaves like Newtonian fluid for extreme shear rates. The same case is analyzed in Figures 3 and 4. From these two figures we can see that for γ→0 and for γ→∞. in both cases the fluid's velocity is same for both pseudoplastic (λ1=2.0) and dilatants (λ1=0.25) fluid. The other survey from these two graphs is that velocity is increasing function of shear stress parameter γ for pseudoplastic fluid and decreasing function for dilatants fluid. As in shear thinning case, fluid decreases its viscosity against applied shear stress and in case of shear thickening fluid, fluid gains viscosity that's why in case of pseudoplastic fluid velocity increases and in case of dilatants fluid velocity decreases against shear stress parameter. Figure 5 depicts that by escalating the value of arbitrary parameter A1 the fluid's velocity increase. Initially this increment is notable but after that there is no significant effect of arbitrary parameter A1 on velocity graph.
This section covers physical assessment of parameters like RPh fluid parameter λ1 shear stress parameter γ, Brownian motion parameter Nb, thermophoresis diffusion parameter Nt, Brinkman number Br and Prandtl number Pr on temperature profiles. As a result, Figures 6-12 are required to look for such an analysis briefly. Figure 6 demonstrates that by ascending the value of RPh fluid parameter λ1 the fluid's temperature increases. As at λ1=1 the fluid behaves likes the Newtonian fluid. And so the study shows that in same circumstances the temperature for dilatants fluid is less than the Newtonian's fluid temperature and Newtonian's fluid temperature is smaller than the pseudoplastic fluid's temperature. In Figures 7 and 8 the influences of shear stress parameter γ are deliberated on temperature profiles for pseudoplastic and dilatants fluids respectively. These graphs reveal that the temperature is an increasing function of shear stress parameter γ for pseudoplastic fluids and it behaves totally opposite for dilatants fluids for same values of shear stress parameter γ as decreasing function. The relevance of Brinkman's number on fluid hotness can be seen through Figure 9. This figure proves that fluid becomes hotter by enlarging the value of Brinkman number. Because the Brinkman number occurs as a result of viscous dissipation therefore, extra heat is created with greater Brinkman number, and therefore the temperature rises and hence temperature profile get enlarged. Also see reference [45]. Figure 10 represents that for greater Brownian motion parameter the temperature of the liquid increases. The consequence of Brownian scale tends to increase the relative mobility of nanoparticles compounds from the walls to the substance in response to which an increment in the temperature profile occurs. Figure 11 confirms a similar pattern of temperature distributions in relation to the thermophoresis parameter Nt. Physically greater Nt implies the occurrence of temperature differential phenomenon in which high-temperature nanoparticles transported to cooler region of the channel. As a result temperature is intensified. Figure 12 signifies that by increasing the amount of Prandtl number Pr the temperature of the nanofluid also increases. Because Prandtl number Pr has direct connection with specific heat of the liquid so increased specific heat raise the temperature of fluid.
The influence of sundry factors on the concentration of nanoparticles graphs are scrutinized through Figures 13 to 19. These graphs pointed out that the concentration of nanoparticles at the center of the channel is highly effected by the changing the values of implanted parameters. Figure 13 is plotted to show the effect of RPh fluid parameter λ1 on the concentration of nanoparticles. A decreasing tendency in nanoparticles mass transport rate is observed for enhancing values of λ1. From this we can conclude that concentration of nanoparticles for dilatants fluids is larger as compared to pseudoplastic fluids. Shear stress parameter γ have opposite concern on concentration for pseudoplastic and dilatants fluid which can be seen through Figures 14 and 15. For pseudoplastic fluids the concentration of nanoparticles is decreasing graph of shear stress parameter while for dilatants fluids it depicts increasing behavior. Figure 16 illustrates that with an increment in Brinkman number Br results with a decrease in nanoparticles mass transfer. Figures 17 and 18 reveal the antagonistic effects of Brownian motion parameter Nb and thermophoretic diffusions parameter Nt on concentration graphs. Declining impact is marked by ϕ for increasing thermophoretic diffusion parameter because with the strength of thermophoretic forces the action of diffusion is turned on which depressed the concentration profile of nanofluid. Contrary to this a rising effect in concentration is achieved by enhancing Brownian motion as nanoparticles attained higher densities for stronger Brownian motion which in turn develops concentration. Figure 19 depicts the Prandtl number Pr effects on concentration profile. From figure we can see that by growing values of Prandtl number Pr yields a depressed behavior of concentration profiles near the upper wall but this observation is not hold near lower wall where the significance of Pr is directly proportional to concentration profile.
In Figures 20-23 we will discussed about the effects of and on the pressure gradient profiles within channel. The common observation from these graphs is that the pressure gradient gains its maximum value at the narrowest section of the channel. Figure 20 demonstrates that by intensifying the value of the pressure gradient of RPh nanofluid increases. The rising behavior of pressure gradient field is larger in the contracted as compared to the broader section of the channel. In this figure the blue thick line is the representation of Newtonian fluid's pressure gradient. The lines upper the blue lines against the values correspond to the pseudoplastic fluid and the lines below the blue line against the values characterized the dilatants fluid. In Figure 21 the significance of on the pressure gradient is evaluated for shear thinning fluid. It is investigated from this sketch that pressure gradient of RPh fluid raises by increasing the value of. In Figure 22 the same significance of on pressure gradient is studied for the dilatants fluid. The influence of on pressure gradient for dilatants fluid is quite dissimilar as compared to the pseudoplastic fluid. In the case of dilatants, by increasing the value of the amount of pressure gradient reduces. Figure 23 examined that for, the height of every crest of the pressure gradient is same at narrow section of the channel. However, as we increase the value of parameter, that is, when we increase the width of channel, the height of each succeeding crest of the pressure gradient decreases than the preceding crest. This is because of by adding the value of the width of the channel increases and so the pressure gradient decreases in the wider part. This whole phenomenon can be seen in Figure 23.
This part consists of the physical study of parameters like RPh fluid parameter λ1, phase difference of the waves ζ, shear stress parameter γ and non-uniformity parameter k1 on stream line contours. From Figure 24, it is experimented that by improving the value of λ1 the size of the bolus increases. Bolus is the result of fluid's trapped volume by streamlines with the motion of the fluid, this generates an intriguing phenomenon known as trapping, the construction of an inner flowing bolus of nanofluid which moved together with the waves with wave speed at a fixed mean flow rate. Figure 25 indicates that phase difference of the channel has opposite effect on fluid trapped volume than the λ1 as by increasing the angle of phase difference, the volume of the bolus decreases. Figures 26 and 27 are drawn to understand the impact shear stress parameter γ on streamline functions for shear thinning fluids and shear thickening fluids respectively. From Figure 26 we can see that bolus for pseudoplastic fluids have increasing behavior with greater shear stress parameter. As this fluid is shear thinning fluid so by increasing shear stress parameter the fluid's viscosity decreases and fluid moves more freely, and more fluid's volume get trapped. Contrary to this fluid the size of bolus decreases in case of dilatants fluids for same values of shear stress parameter as we can observe from Figure 27. Figure 28 signifies that the amount of trapping volume of fluid get increases by increasing the non-uniformity of the channel and consequently the dimension of the bolus get increased.
Table 1 presents the numerical assessment of heat and mass transfer rates at the upper border of the channel for various physical parameters. First four lines of the table exhibits that heat transfer (−θ'(h1)) and mass transfer (−ϕ'(h1)) rates are increasing function of RPh fluid parameter λ1, which concludes that RPh fluid parameter improves heat and mass transfer process between the solid boundaries and the base fluid. Secondly, the table 1 predicts that in case of shear thinning fluids, heat (−θ'(h1)) and mass transfer (−ϕ'(h1)) rates raise for greater shear stress parameter and on the other hand for shear thickening fluid these transfer rates decline. Next four lines represent that heat transfer (−θ'(h1)) and mass transfer (−ϕ'(h1)) rates are increases by enlarging Nt. Moreover the ratio of mass transfer (−ϕ'(h1)) is much significant as compared to heat transfer (−θ'(h1)) rate. The table's following four lines anticipated that the Brownian motion parameter has opposing impacts on heat (−θ'(h1)) and mass transfer (−ϕ'(h1)) rates. As with increased Brownian motion parameter, the mass transfer rate (−ϕ'(h1)) drops drastically while the heat transfer rate (−θ'(h1)) increases steadily. The very next four lines of the table demonstrate that the Brinkman's number has a direct influence on heat (−θ'(h1)) and mass transfer (−ϕ'(h1)) rates. As by enlarging the Brinkman number, both the heat (−θ'(h1)) and mass transport (−ϕ'(h1)) rates improved. The last four lines of the table reveals that raising the Prandtl number improved the heat (−θ'(h1)) and mass transfer (−ϕ'(h1)) rates.
λ1 | γ | Nt | Nb | Br | Pr | −θ'(h1) | −ϕ'(h1) |
0.5 | 1.0 | 0.8 | 0.8 | 1.5 | 1.0 | 3.94339 | 3.25946 |
1.0 | 4.24148 | 3.55755 | |||||
1.5 | 4.52987 | 3.84593 | |||||
2.0 | 4.81133 | 4.12740 | |||||
1.5 | 0.5 | 4.39119 | 3.70726 | ||||
1.0 | 4.52987 | 3.84593 | |||||
1.5 | 4.64350 | 3.95957 | |||||
2.0 | 4.73910 | 4.05516 | |||||
0.5 | 0.5 | 4.09858 | 3.41464 | ||||
1.0 | 4.94339 | 3.25946 | |||||
1.5 | 4.81863 | 3.13470 | |||||
2.0 | 3.71590 | 3.03197 | |||||
1.5 | 1.0 | 0.4 | 4.30704 | 1.64057 | |||
0.8 | 4.52987 | 3.84593 | |||||
1.2 | 4.75514 | 6.27779 | |||||
1.6 | 4.98124 | 8.93658 | |||||
0.8 | 0.4 | 4.30703 | 7.58817 | ||||
0.8 | 4.52987 | 3.84593 | |||||
1.2 | 4.75514 | 2.60015 | |||||
1.6 | 4.98124 | 1.97764 | |||||
0.8 | 0.5 | 1.66990 | 1.28304 | ||||
1.0 | 3.28843 | 2.56540 | |||||
1.5 | 4.52987 | 3.84593 | |||||
2.0 | 5.81130 | 5.12737 | |||||
1.5 | 0.5 | 4.08841 | 3.40448 | ||||
1.0 | 4.52987 | 3.84593 | |||||
1.5 | 4.98124 | 4.29731 | |||||
2.0 | 5.43078 | 7.74984 |
Peristaltic flow of non-Newtonian based nanofluid in a tapered asymmetric channel is examined in this research. The governing equations incorporates dispersion model for the nanofluid and RPh fluid model for non-Newtonian fluid. Simplified form of governing equation based on long wavelength and small Reynolds number approximations are solved numerically. The consequential effects of different physical quantities on the velocity of the nanofluid, pressure gradient, temperature and concentration profiles are portrayed graphically. The most important outcomes of the study are given below:
• Velocity is increasing function of shear stress parameter for pseudoplastic fluid and decreasing function of shear stress parameter for dilatants fluid.
• It is noted that by increasing the value of RPh fluid parameter λ1 the temperature of the nanofluid increases.
• It is worth noting that both thermophoretic and Brownian diffusions causes temperature graphs to climb.
• A decreasing tendency in nanoparticles mass transfer is observed for enhancing values of RPh fluid parameter. From this we can conclude that concentration of nanoparticles for dilatants fluid is greater as compared to pseudoplastic fluid.
• Thermophoretic diffusion and Brownian motion factors have opposing influence on concentration of nanoparticles profiles. Concentration graph decreases by increasing thermophoretic diffusion parameter and increases by enhancing Brownian motion parameter.
• Further it is noticed that the addition of Brinkman number results in an enhancement in the nanofluid temperature.
• The pressure gradient of the nanofluid is higher in the occluded section of the channel as compared to the broader section of the channel.
• By increasing the non-uniformity of the channel, the pressure gradient of the nanofluid decreases as the width of the channel increases.
• The addition in the value of RPh fluid parameter λ1 the trapped volume of the nanofluid increases.
• It is also important to observe that the RPh fluid parameter enables heat and mass transfer rates to increase.
• Brownian motion parameter has opposing impacts on heat and mass transfer rates. As with increased Brownian motion parameter, the mass transfer rate drops drastically while the heat transfer rate increases steadily.
• It is analyzed from the study represented that heat transfer and mass transfer rates are increased by enlarging the thermophoretic diffusion parameter.
I hope this study will be step forward in the field of peristaltic flow, heat and mass transfer of non-Newtonian fluids and also provides new avenues of research for scholars to the way of RPh fluid academics.
This research work was funded by institutional fund projects under no. (IFP-A-2022-2-5-24). Therefore, authors gratefully acknowledge technical and financial support from the ministry of education and University of Hafr Al Batin, Saudi Arabia.
The authors declare no conflict of interest.
[1] | G. B. Thurston, N. M. Henderson, M. Jeng, Effects of erythrocytapheresis transfusion on the viscoelasticity of sickle cell blood, Clin. Hemorheol. Microcirc., 30 (2004), 83–97. |
[2] | H. A. Baieth, S. Hamza, Comparative examination of constitutive equations for apparent viscosity of human blood, Egypt. J. Biophys. Biomed. Eng., 7 (2006), 85–96. |
[3] | G. Pedrzzetti, L. Zavatto, F. Domenichini, A. Tortoriello, Pulstile flow inside moderately elastic arteries, its modeling and effects of elasticity, Comput. Methods Biomec. Biomed. Eng., 5 (2002), 219–231. http://doi.org/10.1080/10255840212874 |
[4] |
G. Pontrelli, Nonlinear problems in arterial flows, Nonlinear Anal., 47 (2001), 4905–4915. https://doi.org/10.1016/S0362-546X(01)00603-4 doi: 10.1016/S0362-546X(01)00603-4
![]() |
[5] |
F. J. Walburn, D. J. Scnech, A constitutive equation for whole human blood, Biorheology, 13 (1976), 201–210. https://doi.org/10.3233/bir-1976-13307 doi: 10.3233/bir-1976-13307
![]() |
[6] | T. W. Latham, Fluid motion in a peristaltic pump, In: Massachusetts Institute of Technology, Massachusetts Institute of Technology, 1966. |
[7] |
A. H. Shapiro, M. Y. Jaffrin, S. L. Weinberg, Peristaltic pumping with long wavelengths at low Reynolds number, J. Fluid Mech., 37 (1969), 799–825. https://doi.org/10.1017/S0022112069000899 doi: 10.1017/S0022112069000899
![]() |
[8] |
D. Tripathi, Study of transient peristaltic heat flow through a finite porous channel, Math. Comput. Model., 57 (2013), 1270–1283. https://doi.org/10.1016/j.mcm.2012.10.030 doi: 10.1016/j.mcm.2012.10.030
![]() |
[9] |
T. Hayat, N. Ali, S. Asghar, Hall effects on peristaltic flow of a Maxwell fluid in a porous medium, Phys. Lett. A, 363 (2007) 397–403. https://doi.org/10.1016/j.physleta.2006.10.104 doi: 10.1016/j.physleta.2006.10.104
![]() |
[10] |
S. A. Hussein, S. E. Ahmed, A. A. Arafa, Electrokinetic peristaltic bioconvective Jeffrey nanofluid flow with activation energy for binary chemical reaction, radiation and variable fluid properties, ZAMM‐Z. Angew. Math. Me., 2022, e202200284. https://doi.org/10.1002/zamm.202200284 doi: 10.1002/zamm.202200284
![]() |
[11] |
M. G. Reddy, K. V. Reddy, O. D. Makinde, Hydromagnetic peristaltic motion of a reacting and radiating couple stress fluid in an inclined asymmetric channel filled with a porous medium, Alex. Eng. J., 55 (2016), 1841–1853. https://doi.org/10.1016/j.aej.2016.04.010 doi: 10.1016/j.aej.2016.04.010
![]() |
[12] |
A. A. Arafa, S. E. Ahmed, M. M. Allan, Peristaltic flow of non-homogeneous nanofluids through variable porosity and heat generating porous media with viscous dissipation: Entropy analyses, Case Stud. Therm. Eng., 32 (2022), 101882. https://doi.org/10.1016/j.csite.2022.101882 doi: 10.1016/j.csite.2022.101882
![]() |
[13] |
T. Anwar, M. Tahir, P. Kumam, S. Ahmed, P. Thounthong, Magnetohydrodynamic mixed convective peristaltic slip transport of carbon nanotubes dispersed in water through an inclined channel with Joule heating, Heat Transf., 50 (2020), 2064–2089. https://doi.org/10.1002/htj.21969 doi: 10.1002/htj.21969
![]() |
[14] |
B. B. Divya, G. Manjunatha, C. Rajashekhar, H. Vaidya, K. V. Prasad, The hemodynamics of variable liquid properties on the MHD peristaltic mechanism of Jeffery fluid with heat and mass transfer, Alex. Eng. J., 59 (2020), 693–706. https://doi.org/10.1016/j.aej.2020.01.038 doi: 10.1016/j.aej.2020.01.038
![]() |
[15] |
T. Y. Na, Boundary layer flow of Reiner-Philippoff fluids, Internat. J. Non-Linear Mech., 29 (1994), 871–877. https://doi.org/10.1016/0020-7462(94)90059-0 doi: 10.1016/0020-7462(94)90059-0
![]() |
[16] |
K. S. Yam, S. D. Herris, D. B. Ingham, I. Pop, Boundary-layer flow of Reiner-Philippoff fluids past a stretching wedge, Internat. J. Non-Linear Mech., 44 (2009), 1056–1062. https://doi.org/10.1016/j.ijnonlinmec.2009.08.006 doi: 10.1016/j.ijnonlinmec.2009.08.006
![]() |
[17] |
A. Ahmad, Flow of ReinerPhilippoff based nano-fluid past a stretching sheet, J. Mol. Liq., 219 (2016), 643–646. https://doi.org/10.1016/j.molliq.2016.03.068 doi: 10.1016/j.molliq.2016.03.068
![]() |
[18] |
A. Ullah, E. O. Alzahrani, Z. Shah, M. Ayaz, S. Islam, Nanofluid's thin film flow of Reiner-Philippoff fluid over an unstable stretching surface with Brownian motion and thermophoresis effects, Coatings, 9 (2019), 21. https://doi.org/10.3390/coatings9010021 doi: 10.3390/coatings9010021
![]() |
[19] |
T. Sajid, W. Jamshed, F. Shahzad, I. Ullah, R. W. Ibrahim, M. R. Eid, et al., Insightful into dynamics of magneto Reiner-Philippoff nanofluid flow induced by triple-diffusive convection with zero nanoparticle mass flux, Ain Shams Eng. J., 14 (2022), 101946. https://doi.org/10.1016/j.asej.2022.101946 doi: 10.1016/j.asej.2022.101946
![]() |
[20] | T. Sajid, W. Jamshed, F. Shahzad, M. A. Aiyashi, M. R. Eid, K. S. Nisar, et al., Impact of Maxwell velocity slip and Smoluchowski temperature slip on CNTs with modified Fourier theory: Reiner-Philippoff model, Plos One, 16 (2021), e0258367. http://doi.org/10.1371/journal.pone.0258367 |
[21] |
M. Tahir, A. Ahmad, Impact of pseudoplaticity and dilatancy of fluid on peristaltic flow and heat transfer: Reiner-Philippoff fluid model, Adv. Mech. Eng., 12 (2020). https://doi.org/10.1177/1687814020981184 doi: 10.1177/1687814020981184
![]() |
[22] | S. U. S. Choi, J. A. Eastman, Enhancing thermal conductivity of fluids with nanoparticles, San Francisco: ASME International Mechanical Engineering Congress and Exposition, 1995, 12–17. |
[23] | S. U. S. Choi, J. A. Eastman, Enhancing thermal conductivity of fluid with nanofluids, 1995. |
[24] |
Y. M. Xuan, Q. Li, Heat transfer enhancement of nanofluids, Int. J. Heat Fluid fl., 21 (2000), 58–64. https://doi.org/10.1016/S0142-727X(99)00067-3 doi: 10.1016/S0142-727X(99)00067-3
![]() |
[25] |
J. Buongiorno, Convective transport in nanofluids, ASME J. Heat Mass Transfer., 128 (2006), 240–250. https://doi.org/10.1115/1.2150834 doi: 10.1115/1.2150834
![]() |
[26] | G. Rasool, N. A. Shah, E. R. El-Zahar, A. Wakif, Numerical investigation of EMHD nanofluid flows over a convectively heated riga pattern positioned horizontally in a Darcy-Forchheimer porous medium: application of passive control strategy and generalized transfer laws, Waves Random Complex Media, 2022. https://doi.org/10.1080/17455030.2022.2074571 |
[27] | A. Shahzad, F. Liaqat, Z. Ellahi, M. Sohail, M. Ayub, M. R. Ali, Thin film flow and heat transfer of Cu-nanofluids with slip and convective boundary condition over a stretching sheet, Sci. Rep., 12 (2022), 14254. |
[28] |
A. A. Memon, S. Murtaza, M. A. Memon, K. Bhatti, M. Haque, M. R. Ali, Simulation of thermal decomposition of Calcium Oxide in water with different activation energy and the high Reynolds number, Complexity, 2022 (2022), 3877475. https://doi.org/10.1155/2022/3877475 doi: 10.1155/2022/3877475
![]() |
[29] |
A. F. Abu-Bakr, T. Kanagawa, A. K. Abu-Nab, Analysis of doublet bubble dynamics near a rigid wall in ferroparticle nanofluids, Case Stud. Therm. Eng., 34 (2022), 102060. https://doi.org/10.1016/j.csite.2022.102060 doi: 10.1016/j.csite.2022.102060
![]() |
[30] |
K. Sajjan, N. A. Shah, N. A. Ahammad, S. S. K. Raju, M. D. Kumar, W. Weera, Nonlinear Boussinesq and Rosseland approximations on 3D flow in an interruption of Ternary nanoparticles with various shapes of densities and conductivity properties, AIMS Mathematics, 7 (2022), 18416–18449. https://doi.org/10.3934/math.20221014 doi: 10.3934/math.20221014
![]() |
[31] |
M. Sheikholeslami, D. D. Ganji, Nanofluid flow and heat transfer between parallel plates considering Brownian motion using DTM, Comput. Methods Appl. Mech. Eng., 283 (2015), 651–663. https://doi.org/10.1016/j.cma.2014.09.038 doi: 10.1016/j.cma.2014.09.038
![]() |
[32] |
A. K. Abu-Nab, A. F. Abu-Bakr, Effect of bubble-bubble interaction in Cu-Al2O3/H2O hybrid nanofluids during multibubble growth process, Case Stud. Therm. Eng., 33 (2022), 101973. https://doi.org/10.1016/j.csite.2022.101973 doi: 10.1016/j.csite.2022.101973
![]() |
[33] |
A. Rauf, N. A. Shah, A. Mushtaq, T. Botmart, Heat transport and magnetohydrodynamic hybrid micropolar ferrofluid flow over a non-linearly stretching sheet, AIMS Mathematics, 8 (2023), 164–193. https://doi.org/10.3934/math.2023008 doi: 10.3934/math.2023008
![]() |
[34] |
S. Hina, T. Hayat, S. Asghar, A. A. Hendi, Influence of compliant walls on peristaltic motion with heat/mass transfer and chemical reaction, Int. J. Heat Mass Transfer, 55 (2012), 3386–3394. https://doi.org/10.1016/j.ijheatmasstransfer.2012.02.074 doi: 10.1016/j.ijheatmasstransfer.2012.02.074
![]() |
[35] |
N. Iftikhar, A. Rehman, Peristaltic flow of an Eyring Prandtl fluid in a diverging tube with heat and mass transfer, Int. J. Heat Mass Transfer, 111 (2017), 667–676. https://doi.org/10.1016/j.ijheatmasstransfer.2017.04.013 doi: 10.1016/j.ijheatmasstransfer.2017.04.013
![]() |
[36] |
M. M. Bhatti, A. Zeeshan, R. Ellahi, N. Ijaz, Heat and mass transfer of two-phase flow with electric double layer effects induced due to peristaltic propulsion in the presence of transverse magnetic field, J. Mol. Liq., 230 (2017), 237–246. https://doi.org/10.1016/j.molliq.2017.01.033 doi: 10.1016/j.molliq.2017.01.033
![]() |
[37] |
T. Hayat, S. Farooq, B. Ahmad, A. Alsaedi, Homogeneous-heterogeneous reactions and heat source/sink effects in MHD peristaltic flow of micropolar fluid with Newtonian heating in a curved channel, J. Mol. Liq., 223 (2016), 469–488. https://doi.org/10.1016/j.molliq.2016.08.067 doi: 10.1016/j.molliq.2016.08.067
![]() |
[38] | S. Nadeem, T. Hayat, N. S. Akbar, M. Y. Malik, On the influence of heat transfer in peristalsis with variable viscosity, Int. J. Heat Mass Transfer, 52 (2009), 4722–4730. http://doi.org/10.1016/j.ijheatmasstransfer.2009.04.037 |
[39] |
T. Hayat, A. Tanveer, A. Alsaedi, Mixed convective peristaltic flow of Carreau-Yasuda fluid with thermal deposition and chemical reaction, Int. J. Heat Mass Transfer, 96 (2016), 474–481. https://doi.org/10.1016/j.ijheatmasstransfer.2016.01.055 doi: 10.1016/j.ijheatmasstransfer.2016.01.055
![]() |
[40] |
M. Tahir, A. Ahmad, S. A. Shehzad, Study of pseudoplastic and dilatant behavior of nanofluid in peristaltic flow: Reiner-Philippoff models, Chinese J. Phys., 77 (2022), 2371–2388. https://doi.org/10.1016/j.cjph.2022.04.001 doi: 10.1016/j.cjph.2022.04.001
![]() |
[41] |
G. C. Shit, N. K. Ranjit, Role of slip velocity on peristaltic transport of couple stress fluid through an asymmetric non-uniform channel: Application to digestive system, J. Mol. Liq., 221 (2016), 305–315. https://doi.org/10.1016/j.molliq.2016.06.002 doi: 10.1016/j.molliq.2016.06.002
![]() |
[42] |
M. Awais, S. Farooq, T. Hayat, B. Ahmad, Comparative study of silver and copper water magneto nanoparticles with homogeneous-heterogeneous reactions in a tapered channel, Int. J. Heat Mass Transfer, 115 (2017), 108–114. https://doi.org/10.1016/j.ijheatmasstransfer.2017.07.129 doi: 10.1016/j.ijheatmasstransfer.2017.07.129
![]() |
[43] |
K. Vajravelu, S. Sreenadh, R. Saravana, Combined influence of velocity slip, temperature and concentration jump conditions on MHD peristaltic transport of a Carreau fluid in a non-uniform channel, Appl. Math. Comput., 225 (2013), 656–676. https://doi.org/10.1016/j.amc.2013.10.014 doi: 10.1016/j.amc.2013.10.014
![]() |
[44] |
T. Hayat, R. Iqbal, A. Tanveer, A. Alsaedi, Influence of convective conditions in radiative peristaltic flow of pseudoplastic nanofluid in a tapered asymmetric channel, J. Magn. Magn. Mater., 408 (2016), 168–176. https://doi.org/10.1016/j.jmmm.2016.02.044 doi: 10.1016/j.jmmm.2016.02.044
![]() |
[45] |
T. Hayat, H. Zahir, A. Alsaedi, B. Ahmad, Heat transfer analysis on peristaltic transport of Ree-Eyring fluid in rotating frame, Chinese J. Phys., 55 (2017), 1894–1907. https://doi.org/10.1016/j.cjph.2017.08.016 doi: 10.1016/j.cjph.2017.08.016
![]() |
1. | Bahram Jalili, Amirhossein Rezaeian, Payam Jalili, Fathollah Ommi, Davood Domiri Ganji, Numerical modeling of magnetic field impact on the thermal behavior of a microchannel heat sink, 2023, 45, 2214157X, 102944, 10.1016/j.csite.2023.102944 | |
2. | Iskandar Waini, Nurul Amira Zainal, Najiyah Safwa Khashi'ie, Khairum Bin Hamzah, Abdul Rahman Mohd Kasim, Anuar Ishak, Ioan Pop, Mixed convection of MHD Reiner–Philippoff fluid flow past a vertical shrinking plate with radiative heat transfer, 2023, 05779073, 10.1016/j.cjph.2023.04.001 | |
3. | J. Iqbal, F. M. Abbasi, I. Ali, Heat transfer analysis for magnetohydrodynamic peristalsis of Reiner–Philippoff fluid: Application of an artificial neural network, 2024, 36, 1070-6631, 10.1063/5.0207600 | |
4. | Rajib Kumar Mandal, Hiranmoy Maiti, Samir Kumar Nandy, Bioconvective MHD flow of Williamson nanofluid past an expandable Riga wedge in the presence of activation energy, mass suction and velocity slip, 2023, 1040-7782, 1, 10.1080/10407782.2023.2263155 | |
5. | M. Tahir, A. Ahmad, Y. Khan, R. Nawaz, S. Ahmad, Role of minimization entropy generation and heat transfer on the nanofluid peristaltic flow via Reiner-Philippoff model , 2024, 1040-7790, 1, 10.1080/10407790.2024.2354493 | |
6. | M.P. Mkhatshwa, M. Khumalo, Double diffusion and Hall effects on MHD sinusoidal natural convection flow of silver water-based nanofluid from a porous vertical plate, 2023, 7, 26668181, 100516, 10.1016/j.padiff.2023.100516 | |
7. | Shuguang Li, Sania Naseer, Nazia Shahmir, Muhammad Ramzan, Shalan Alkarni, Seifedine Kadry, Influence of magnetic dipole and thermophoretic particle deposition on the flow of Reiner–Philippoff fluid with Thompson and Troian slip, 2024, 0044-2267, 10.1002/zamm.202400098 | |
8. | M. Alkinidri, Jamshaid Iqbal, F. M. Abbasi, Analysis of thermal transport and wall stresses for MHD peristaltic motion of Reiner‐Philippoff fluid with viscous dissipation and mixed convection effects, 2025, 105, 0044-2267, 10.1002/zamm.202400329 |
λ1 | γ | Nt | Nb | Br | Pr | −θ'(h1) | −ϕ'(h1) |
0.5 | 1.0 | 0.8 | 0.8 | 1.5 | 1.0 | 3.94339 | 3.25946 |
1.0 | 4.24148 | 3.55755 | |||||
1.5 | 4.52987 | 3.84593 | |||||
2.0 | 4.81133 | 4.12740 | |||||
1.5 | 0.5 | 4.39119 | 3.70726 | ||||
1.0 | 4.52987 | 3.84593 | |||||
1.5 | 4.64350 | 3.95957 | |||||
2.0 | 4.73910 | 4.05516 | |||||
0.5 | 0.5 | 4.09858 | 3.41464 | ||||
1.0 | 4.94339 | 3.25946 | |||||
1.5 | 4.81863 | 3.13470 | |||||
2.0 | 3.71590 | 3.03197 | |||||
1.5 | 1.0 | 0.4 | 4.30704 | 1.64057 | |||
0.8 | 4.52987 | 3.84593 | |||||
1.2 | 4.75514 | 6.27779 | |||||
1.6 | 4.98124 | 8.93658 | |||||
0.8 | 0.4 | 4.30703 | 7.58817 | ||||
0.8 | 4.52987 | 3.84593 | |||||
1.2 | 4.75514 | 2.60015 | |||||
1.6 | 4.98124 | 1.97764 | |||||
0.8 | 0.5 | 1.66990 | 1.28304 | ||||
1.0 | 3.28843 | 2.56540 | |||||
1.5 | 4.52987 | 3.84593 | |||||
2.0 | 5.81130 | 5.12737 | |||||
1.5 | 0.5 | 4.08841 | 3.40448 | ||||
1.0 | 4.52987 | 3.84593 | |||||
1.5 | 4.98124 | 4.29731 | |||||
2.0 | 5.43078 | 7.74984 |
λ1 | γ | Nt | Nb | Br | Pr | −θ'(h1) | −ϕ'(h1) |
0.5 | 1.0 | 0.8 | 0.8 | 1.5 | 1.0 | 3.94339 | 3.25946 |
1.0 | 4.24148 | 3.55755 | |||||
1.5 | 4.52987 | 3.84593 | |||||
2.0 | 4.81133 | 4.12740 | |||||
1.5 | 0.5 | 4.39119 | 3.70726 | ||||
1.0 | 4.52987 | 3.84593 | |||||
1.5 | 4.64350 | 3.95957 | |||||
2.0 | 4.73910 | 4.05516 | |||||
0.5 | 0.5 | 4.09858 | 3.41464 | ||||
1.0 | 4.94339 | 3.25946 | |||||
1.5 | 4.81863 | 3.13470 | |||||
2.0 | 3.71590 | 3.03197 | |||||
1.5 | 1.0 | 0.4 | 4.30704 | 1.64057 | |||
0.8 | 4.52987 | 3.84593 | |||||
1.2 | 4.75514 | 6.27779 | |||||
1.6 | 4.98124 | 8.93658 | |||||
0.8 | 0.4 | 4.30703 | 7.58817 | ||||
0.8 | 4.52987 | 3.84593 | |||||
1.2 | 4.75514 | 2.60015 | |||||
1.6 | 4.98124 | 1.97764 | |||||
0.8 | 0.5 | 1.66990 | 1.28304 | ||||
1.0 | 3.28843 | 2.56540 | |||||
1.5 | 4.52987 | 3.84593 | |||||
2.0 | 5.81130 | 5.12737 | |||||
1.5 | 0.5 | 4.08841 | 3.40448 | ||||
1.0 | 4.52987 | 3.84593 | |||||
1.5 | 4.98124 | 4.29731 | |||||
2.0 | 5.43078 | 7.74984 |