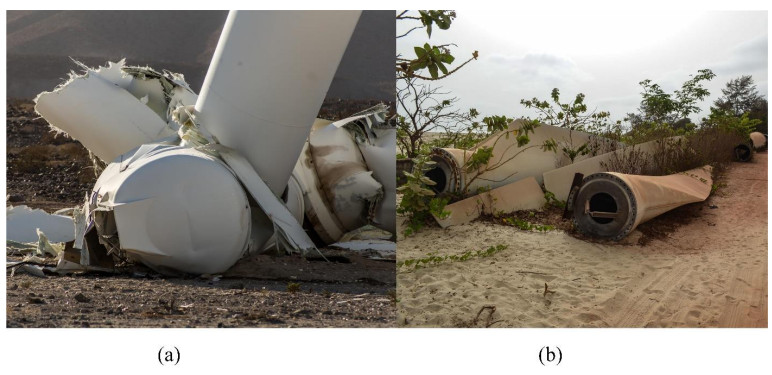
Rapid global industrialization has increased the amounts of greenhouse gas emissions leading to global warming and severe weather conditions. To lower such emissions, several countries are swiftly seeking sustainable and low-carbon energy alternatives. As a green energy source, wind power has gained recent popularity due to its low cost and lower carbon footprint; but with a short blade life span, the industry faces a blade waste issue. Wind turbine blade recyclability is challenging due to factors such as blade sheer size, material complexity, low economic feasibility, and a lack of suitable recycling policies; yet, many blades are still being constructed and others are being decommissioned. This paper aims to discuss different wind turbine blade recyclability routes under the pavement sector. Wind turbine blades are made of composite materials, and based on literature data, it was found that recycled fibers can be extracted from the composites using methods such as pyrolysis, solvolysis, and mechanical processing; of these methods, solvolysis provides cleaner and better fibers. The recycled fibers, when incorporated in both asphalt and concrete, improved their mechanical properties; nevertheless, recycling of fibers from carbon fiber-reinforced polymers (CFRPs) was more economical than glass fiber-reinforced polymers (GFRPs). Waste wind turbine blades can take other routes, such as processing them into waste wind turbine aggregates, roadside bicycle shades, bridge girders, and road acoustic barriers.
Citation: Shuwen Zhang, Noah Kirumira. Techniques of recycling end-of-life wind turbine blades in the pavement industry: A literature review[J]. Clean Technologies and Recycling, 2024, 4(1): 89-107. doi: 10.3934/ctr.2024005
[1] | Kyle Pender, Liu Yang . Glass fibre composites recycling using the fluidised bed: A study into the economic viability in the UK. Clean Technologies and Recycling, 2023, 3(3): 221-240. doi: 10.3934/ctr.2023014 |
[2] | Dmitry Baturkin, Ousmane A. Hisseine, Radhouane Masmoudi, Arezki Tagnit-Hamou, Slimane Metiche, Luc Massicotte . Compressive behavior of FRP-tube-confined concrete short columns using recycled FRP materials from wind turbine blades: Experimental investigation and analytical modelling. Clean Technologies and Recycling, 2022, 2(3): 136-164. doi: 10.3934/ctr.2022008 |
[3] | Wilson Uzochukwu Eze, Reginald Umunakwe, Henry Chinedu Obasi, Michael Ifeanyichukwu Ugbaja, Cosmas Chinedu Uche, Innocent Chimezie Madufor . Plastics waste management: A review of pyrolysis technology. Clean Technologies and Recycling, 2021, 1(1): 50-69. doi: 10.3934/ctr.2021003 |
[4] | Wilson Uzochukwu Eze, Reginald Umunakwe, Michael Ifeanyichukwu Ugbaja, Mohammed Kabiru Yakubu, Narcillina Nkechi Adegboro, Amina Hassan Bayero, Maryann Ifeoma Uzochukwu . Utilization of commodity plastic wastes in flexible pavement: A review. Clean Technologies and Recycling, 2023, 3(1): 71-91. doi: 10.3934/ctr.2023005 |
[5] | Asiye Bilgili, Kerem Gül . Forecasting power generation of wind turbine with real-time data using machine learning algorithms. Clean Technologies and Recycling, 2024, 4(2): 108-124. doi: 10.3934/ctr.2024006 |
[6] | Arun Kumar M, Rithick Joshua K, Sahana Rajesh, Caroline Dorathy Esther J, Kavitha Devi MK . Predicting wind power using LSTM, Transformer, and other techniques. Clean Technologies and Recycling, 2024, 4(2): 125-145. doi: 10.3934/ctr.2024007 |
[7] | Congying Wang, Fu Zhao, Carol Handwerker . Transforming and integrating informal sectors into formal e-waste management system: A case study in Guiyu, China. Clean Technologies and Recycling, 2022, 2(4): 225-246. doi: 10.3934/ctr.2022012 |
[8] | Chukwuebuka C. Okafor, Chinelo A. Nzekwe, Nixon N. Nduji, Charles C. Ajaero, Juliet C. Ibekwe . Energy and material recovery potential from municipal solid wastes (MSW) in Nigeria: Challenges and opportunities. Clean Technologies and Recycling, 2022, 2(4): 282-307. doi: 10.3934/ctr.2022015 |
[9] | Christiana Alexandridou, George N. Angelopoulos, Frank A. Coutelieris . Is concrete produced by recycled aggregates from construction and demolition wastes appropriate for use in building industry?. Clean Technologies and Recycling, 2022, 2(3): 165-169. doi: 10.3934/ctr.2022009 |
[10] | Suman Kunwar . MWaste: An app that uses deep learning to manage household waste. Clean Technologies and Recycling, 2023, 3(3): 119-133. doi: 10.3934/ctr.2023008 |
Rapid global industrialization has increased the amounts of greenhouse gas emissions leading to global warming and severe weather conditions. To lower such emissions, several countries are swiftly seeking sustainable and low-carbon energy alternatives. As a green energy source, wind power has gained recent popularity due to its low cost and lower carbon footprint; but with a short blade life span, the industry faces a blade waste issue. Wind turbine blade recyclability is challenging due to factors such as blade sheer size, material complexity, low economic feasibility, and a lack of suitable recycling policies; yet, many blades are still being constructed and others are being decommissioned. This paper aims to discuss different wind turbine blade recyclability routes under the pavement sector. Wind turbine blades are made of composite materials, and based on literature data, it was found that recycled fibers can be extracted from the composites using methods such as pyrolysis, solvolysis, and mechanical processing; of these methods, solvolysis provides cleaner and better fibers. The recycled fibers, when incorporated in both asphalt and concrete, improved their mechanical properties; nevertheless, recycling of fibers from carbon fiber-reinforced polymers (CFRPs) was more economical than glass fiber-reinforced polymers (GFRPs). Waste wind turbine blades can take other routes, such as processing them into waste wind turbine aggregates, roadside bicycle shades, bridge girders, and road acoustic barriers.
Global industrialization is rapidly increasing; according to a study in the United Nations Industrial Statistics Yearbook 2023, global industrial trends from 2020 to 2023 outpaced previous years, with more significant increases in sectors such as waste management and water supply, power generation, and manufacturing [1]. Rapid industrialization, coupled with improper management of industrial waste and by-products, is one of the leading causes of increased amounts of greenhouse gas emissions [2]. The presence of greenhouse gases in the atmosphere, such as carbon dioxide, methane, nitrous oxide, and fluorinated gases, can cause a blanketing effect on Earth [3]. For instance, when the sun's radiation heats the earth's surface, trees, plants, and other bodies absorb these thermal radiations; then, during cooling, they all have to radiate this heat of the earth into outer space. However, the presence of greenhouse gases in the atmosphere traps these thermal radiations and continuously re-emits them within the earth's atmosphere, causing a buildup of heat and increasing overall global temperatures, resulting in global warming [4]. In recent years, global warming has become a worldwide concern as the outcomes of this phenomenon are becoming more obvious, with the global energy sector remaining the lead contributor to greenhouse gases [5].
Many large economies around the world are opting for cleaner energy sources such as nuclear, hydro, solar, and wind power to lower their carbon emissions [8]. As of today, wind power has proven to be a more sustainable and cheaper alternative compared to other green energy sources, which has created a high demand for wind turbine installations both on land and offshore [9]. According to the World Wind Energy Association (WWEA) half-year report of 2023, it was estimated that in the first half of 2023, there were 38% more wind turbine installations globally in comparison to 2022; with an annual growth rate of 11.4%, the worldwide total wind energy capacity is projected to exceed 1045 gigawatts by the end of 2023 [10]. On the other hand, the rapid growth rate of wind turbine installation generates more blade waste, as there are fewer means of recycling them efficiently. A typical wind turbine blade has a service life span of approximately 20–25 years, after which they will be decommissioned. Due to the challenges involved in recycling them, most of these blades will eventually end up in a landfill or discarded, as shown in Figure 1 [11].
By 2050, annual global blade waste is projected to go up to 2 million metric tons, whereas if no proper action is taken, the accumulative amount of blade waste will be about 43 million metric tons [12]; this is illustrated in Figure 2. Due to their short lifespan, wind turbines installed during the 20th century are nearing the end of their service life, which creates a need to devise ways of dealing with such waste. Currently, many industries are doing their part in reducing the blade waste issue; the pavement industry is also formulating feasible techniques and ideas [13,14]. Pavement refers to a surface or section of the road where vehicles pass; these can be divided into two categories, namely asphalt pavements and concrete pavements, depending on the materials used [15]. A typical asphalt pavement mainly consists of a mixture of binder and aggregates. Bitumen is commonly used as a binder, which is a byproduct from the petroleum industry, whereas the aggregates are rocks, e.g., limestone or sandstone. In asphalt pavements, the binder provides structural bonding with the aggregates, hence allowing flexible characteristics of the pavement. The type and quality of the binder used greatly define the quality and applications of the asphalt mixture; hence, modifications made to the binder will directly impact the overall mix performance [16].
Concrete pavements, on the other hand, are made of a mixture of cement mortar as the binder and aggregates, which provide the void-filling role as well as additional structural support to the pavement. Of the two kinds, asphalt pavements are more popular and typically preferred due to their numerous advantages, including being less expensive in terms of material, construction, and maintenance, being easy to recycle, creating less noise, and having improved road surface tire traction [17]. On the other hand, concrete pavements also have their merits; namely, they can easily hold shape under loading, hence being able to carry more load, and are also less prone to weather changes [18]. With ongoing research and advancements in the pavement industry, a variety of new materials are being studied to improve the performance of asphalt and concrete pavements. Most of these are recycled materials, and this is usually done to promote sustainability and give a second life to what could be waste from other industries [19]. For instance, in both research and field practice, asphalt pavements have been key to utilizing recycled materials. These materials may range from recycled rubber tires, plastic, waste fly ash, asphalt roof shingles, and reclaimed asphalt [20,21]. Every year, over a million kilometers of road networks are laid or rehabilitated around the world; it is estimated that by 2050, the length of paved roads around the globe will have increased by about 14.8–25.3 million km [22]. Therefore, with the ever-growing road network, it is imperative to utilize more recycled materials to promote sustainability. As wind turbines ascend toward becoming a global waste problem, this study aims to discuss some of the methods of recycling and repurposing wind turbine blades in the pavement industry.
Wind turbine blades consist of a wide variety of materials ranging from polymer composites, natural materials, and metallic parts; therefore, a thorough understanding of wind turbine blade material constituents is required to determine which parts can be recycled in asphalt. Wind turbines have been used to generate electricity for nearly a century. In 1887, James Blyth, a Glasgow-based Scottish professor, built the world's first vertical-axis wind turbine [23]. Since then, this industry has undergone numerous developments as new materials are discovered. In the early days, wind turbine blades were made of cloth sails, steel, aluminum, wood, and other materials [24]. The wind turbines of today are large and tall enough to meet the ever-growing demand for green electricity. These wind turbines experience far more rigorous conditions; therefore, this has driven the use of advanced composite materials in blade manufacturing to offer high strength and durability while being light in weight. Figure 3 illustrates the various components of wind turbines and their possible material constituents, from which carbon fiber-reinforced polymers (CFRPs) and glass fiber-reinforced polymers (GFRPs) are some of the most popular [25]. The wind turbine blade manufacturing industry adopts the use of fiber-reinforced polymers due to their numerous advantages in comparison to other materials [26].
GFRP and CFRP composites are some of the most commonly used materials in blade production. These are generally made using woven fiber mats that are placed into blade molds, and a polymer matrix is added; the polymer matrix serves as the main bond between the two components and provides the required rigidity of the fiber mat after curing. When well cured, these composites are hard and flexible to a designed degree and hence can act as critical structural support sections in wind turbine blades [27]. Composite materials are also well-known for their ability to provide high strength, light weight, durability, and fire resistance [28,29]. A study by Jensen and Skelton found that a large portion of wind turbine blades is composed of GFRP, attributed to its lower cost compared to CFRP composites [30]. Blade material designs vary depending on the application; in some cases, both carbon fiber and glass fiber composites are used on a single blade. Figure 4 illustrates the complex distribution of materials in wind turbine blades, with some regions made of carbon fiber composites, glass fiber composites, gel coats, and balsa wood. Such inconsistency in materials can also create huddles during blade recycling.
Blade recycling is quite challenging for a wide range of reasons. Their enormous size creates a logistic issue during both installation and decommissioning. Wind turbine blades can span over 100 feet; for instance, one of the largest currently installed blades has a diameter of approximately 853 feet, installed by Three Gorges Energy [33]. The sheer size makes it hard to transport through densely populated cities to recycling facilities, leading to traffic and disruption of city activities. This process will sometimes require rigorous planning to obtain viable routes, hence increasing the cost of the recycling process [34].
Offshore-based wind turbine power plants create a hazardous working environment since some of these regions are usually prone to high waves, fog, and strong winds that could disrupt workers carrying out the decommissioning process (Figure 5). In such conditions, the size and weight of the blades require extensive preliminary planning and sophisticated machinery to detach the old blades and transport them from the site to recycling facilities. In some cases, on-site cutting is done to create smaller segments that are easier to transport. While this may seem sophisticated in offshore power plants, it is more feasible for land-based wind power plants. Segmentation is usually done using a diamond wire saw; precautions need to be taken as the extremely fine dust produced during this process is also a biohazard if inhaled [37]. Extracting and separating the blade constituents will require a lot of energy; therefore, recycling processes like mechanical crushing, thermal recycling, and chemical recycling are usually adopted [38]. Even though some of these recycling methods have proven to be functional, the end products tend to be of lesser quality yet require a higher cost to produce, rendering them less economically viable. Therefore, faced with all these difficulties, a cost-saving alternative is to place them at dump fills.
Fillers are fine-grained mineral particles that are added to asphalt mixtures primarily to fill voids; these can also help enhance the mechanical properties of asphalt pavement mixes. The commonly used fillers include limestone dust, cement, fly ash, and hydrated lime, among others. Asphalt mixes modified with fillers possess outstanding qualities such as better elasticity at high temperatures, hence becoming less susceptible to rutting failure, and higher resistance to fatigue cracking, which increases their service life. Factors such as particle physical interactions, adhesion properties, and chemical properties contribute to the performance modification ability of filler particles [39]. The physical properties of fillers, such as particle size, particle density, specific surface area, and surface texture, can determine the overall performance of the asphalt mixture. For instance, a rough surface texture can help boost the interfacial adhesive forces between the filler and binder, mainly due to the presence of more contact area for bonding to occur; this enhances the contribution of the filler particles in resisting stresses applied to the asphalt matrix [40].
Some studies are currently focusing on the possibility of turning E.O.L or scrap wind turbine blades into high-value filler powders, testing their effects on the performance of asphalt mixtures. For instance, one study by Lan et al. successfully converted E.O.L wind turbine blades into a fine powder that can be used as filler using the steps summarized in Figure 6. First, blades are cut into square meter–sized segments or panels using a diamond wire saw; panels are then passed through a shredder; the shredded material is then ground to form a powder; and finally, the powder material is passed through vibrating sieves of #200 mesh to obtain a fine powder of particle size ranging from 5 to 80 µm. The resulting powder is known as glass fiber-reinforced powder fillers (GFRP fillers) or wind turbine blade-GFRP fillers (WTB-GFRP fillers) [43]. Table 1 summarizes the effects of adding recycled wind turbine blade GFRP fillers into asphalt mixtures.
Asphalt attributes | Observations | Explanation | Sources |
High and medium temperature performance | The complex modulus of asphalt increases in the WTB-GFRP filler content, whereas the phase angle is reduced. | WTB-GFRP fillers enhance asphalt elasticity at higher temperatures through absorption of free binder, hence leading to a stiffer asphalt mixture. | [42] |
Fatigue cracking | GFRP filler specimens had lesser fatigue values compared to typical limestone when subjected to similar strain levels | WTB-GFRP filler mastics possess better resistance to fatigue cracking failure compared with the commonly used limestone fillers. | [42,44] |
Rutting resistance | Dynamic stability values from a wheel tracking test increased with the addition of WTB-GFRP filler powder to the asphalt mixture. | The addition of WTB-GFRP filler can improve the pavement's rutting failure resistance. | [43] |
Low temperature cracking | The addition of WTB-GFRP fillers to asphalt increases its stiffness value and reduces the M-value. | Higher stiffness values depict more brittle asphalt mastic, which therefore carries a greater risk of crack formation at low temperatures. | [45] |
Moisture resistance | Boiling water test results showed WTB-GFRP filler asphalt specimens had lesser shade offs compared to limestone. | Presence of WTB-GFRP fillers in asphalt greatly enhances moisture resistance by improving it's adhesive and cohesive capabilities. | [42] |
Aging resistance | Long term aged WTB-GFRP filler asphalt mastics had a lower complex modulus aging index and higher phase angle aging index. | WTB-GFRP fillers improve asphalt long-term aging compared to typical limestone | [42,46] |
The extremely hard bonds linking fibers with the epoxy matrix make it hard to extract fibers from wind turbine blade composite waste. Yang et al. [47] outlined some methods that can be used to separate fibers from wind turbine blade composites. Fibers extracted using mechanical processing are damaged and possess lower mechanical strength; hence, alternative methods for extracting fibers from composites can be used, which include pyrolysis and solvolysis, among others. These methods are preferable in most cases because, when compared with a mechanical extraction of fibers, they produce cleaner fibers with better mechanical properties.
Pyrolysis refers to the high-temperature combustion of material in the absence of oxygen. The separation can be achieved because of the varying degradation temperatures of the fibers and the matrix (polymers or plastics). During pyrolysis, high temperatures will burn the matrix, converting it into char and leaving behind glass fibers. Studies have been conducted on this issue; for instance, Xu et al. [48] utilized E.O.L wind turbine blades obtained from a wind farm in Inner Mongolia; their blade composites consisted of 76.49 wt.% E-glass fibers and 23.51 wt.% epoxy resins. Using a fixed-bed pyrolysis reactor, the sliced GFRP bars were pyrolyzed at 500 ℃ in the presence of reactive gases and managed to yield 78.8% solid products (fibers and char), 14.88% oil, and 6.32% gas. Their study also stated that further processing of solid products by oxidation produced clean fibers with a substantial tensile strength of about 822.39 MPa. Åkesson et al. [49] explored the option of utilizing microwave heating to pyrolyze scrap wind turbine blades under a nitrogen atmosphere. Microwaving at low temperatures around 300 ℃ had no effect, whereas high temperatures of 600 ℃ produced lower-quality, brittle fibers. This process was able to recover fibers of about 70% of the initial WTB-GFRP mass. Figure 7 clearly outlines some of the steps involved in the pyrolysis extraction of fibers from wind turbine blade segments.
The solvolysis method utilizes the chemical decomposition of the epoxy matrix. This is achieved using reactive solvents such as nitric acid, ammonia glycol water, or ethanol under favorable critical temperatures [50]. Protsenko et al. [51] conducted an experimental study to extract fibers from fiberglass-reinforced polymer composites (FGRP) using solvolysis. In their study, when a 2% catalyst was used, a fiber content of 6% was obtained; when the catalyst increased to 5%, the reaction time was reduced to 2 hours and the fiber contents increased five times. Glass fibers obtained from their study possessed a residual strength of about 98% and were extremely cleaner compared to pyrolysis. Another study by Mattsson et al. performed several solvolysis reaction tests and found that fibers can be successfully extracted from their epoxy matrix by following a two-stage process that involves heating at 270 ℃ for 16 hours under ethylene glycol, followed by heating at 330 ℃ in water/1-propanol/KOH for 3 hours. Their study resulted in 75% epoxy resin removal from the composites, leaving behind clean fibers [52]. Solvolysis has proven to be a more sustainable way of breaking down polymer composite materials for recycling because it produces higher-quality fibers; on the other hand, the process is extremely time-consuming and also dependent on the WTB-GFRP material constituents [52,53].
Fibers recycled from wind turbine blades can be incorporated into asphalt mixes to enhance their performance. A wide range of studies has been conducted on utilizing glass fibers in asphalt, as discussed below. Glass fibers are strong materials with tensile strengths of up to 4600 MPa for virgin specimens. Recycled glass fibers will possess lower strength properties, i.e., after pyrolysis extraction, tensile strengths were found to drop by nearly 50% [54], whereas fibers obtained using hydrolysis reactions had their tensile strengths dropped by 35% [55]; strength properties are ideally dependent on reaction time and temperature. Regardless of slight degradation during these fiber extraction methods, recovered glass fibers still possess strength properties worthy of their use in asphalt mixes.
Recycled glass fibers obtained from waste GFRP aircraft cabins when added to asphalt can greatly improve its durability in terms of resistance to aging and moisture damage; furthermore, the presence of polymer residues on the fiber surface enhances the fiber surface's binder bonding capabilities, therefore proving the recycled fibers are a more economical and environmentally friendly alternative in comparison to new glass fibers [56]. In an experimental study conducted by Khater et al. [57], it was observed that glass fibers mixed with asphalt can effectively enhance the low-temperature stability of the mixes by increasing their bending strain. The fiberglass strands form a dense reinforcing network within the matrix, which effectively disperses stresses as well as limits microcrack propagation due to thermo-stresses. Rutting refers to longitudinal permanent deformation or consolidation that accumulates on an asphalt pavement surface during its service life; this is typically shown by the wheel path being engraved in the road. In a wheel track test conducted by Mahrez and Karim [58], it was observed that asphalt mixes containing 0.3% fiber content exhibited better resistance to rut formation, which could primarily be due to the randomly distributed fibers resisting shear deformation within the matrix. Factors such as the surface texture of the fiber, length of the fiber, or fiber mechanical properties affect glass fibers' contribution to the performance enhancement of the asphalt [59].
Figure 8 summarizes the various recycling routes for Waste Wind Turbine Blades (WWTB) in concrete mixtures, which are further discussed here. Ortega-López et al. conducted experimental tests incorporating raw crushed wind turbine blades (RCWTB) in concrete. It was found that specimens under compressive loading were more resistant to transverse elastic deformation and with higher failure strain; this was mainly attributed to the stitching effect provided by the RCWTB fibers. Under tensile loading, the tensile strength of specimens remained constant with the addition of 3% RCWTB; with further addition, a decline was observed. The study further concluded that the utilization of RCWTB can undoubtedly improve the ductility and load-bearing capacity of concrete per unit strength and carbon footprint [60].
Scarp wind turbine blades can also be cut and processed into needle-like structures, which can effectively replace standard aggregates. Yazdanbakhsh et al. explored this idea in their study, where needle-like elements were added to concrete at 5% and 10% replacement of aggregates by volume. Overall, the incorporation of these needle-like structures improved the toughness of the concrete while not affecting the stability and workability of the final mix [61]. Baturkin et al. conducted an experimental investigation in which fibers and powder were successfully obtained from recycled wind turbine blades. Findings such as reduction of both compressive and flexural strength of concrete were observed with the addition of powders, whereas the addition of recycled fibers increased the concrete flexural strength by 15% [62]. By utilizing mechanical processing, Fu et al. obtained macro fibers from fiber reinforced polymer (FRP) wastes; in their experimental investigation, concrete with 1.5% macro fibers content attained a slump value of over 80 mm without superplasticizers, whereas the compressive strength increased by 4.4% at the same fiber content. It was concluded that macro fibers significantly boosted the concrete peak strength, residual strength, and toughness compared to the control group [63].
Fully replacing standard aggregates with waste wind turbine blade GFRP aggregates in concrete will consequently lower its mechanical strength; nevertheless, the overall mixture performance is suitable for applications such as lightweight concrete since it offers a compressive strength of about 17 MPa and density of 1820 kg/m3. Otherwise, the low mechanical performance could be attributed to the fact that Waste Wind Turbine Blade-GFRP (WWTB-GFRP) aggregates possess low adhesive properties; other issues such as debonding due to concrete shrinkages are also prominent [64]. Akbar et al. found that fibers recycled from CFRPs can enhance the elastic modulus and splitting tensile strength of cement mortar at an optimum content of 1%. This was due to the rough surface of recycled carbon fibers that improve the interlocking capabilities within the cement matrix. They further concluded that utilizing recycled carbon fiber contents at 1% reduces global CO2 emissions by 13.69% in comparison with plain cement paste, while remaining cost-effective [65].
Besides the rigorous processing methods of turning wind turbine blades into powder fillers, fibers, and other high-value materials, old wind turbines can alternatively be repurposed in various key structures for instance, Ruane et al. outlined the possibility of utilizing E.O.L wind turbine blades as bridge girders for a 5 m long and 3 m wide pedestrian bridge. Their study conducted an experimental bending test from which it was concluded that after a life span of 27 years, the blade was able to withstand a bending force of about 70 KN without failure, which was sufficient for the strength requirements of pedestrian bridge girders [66]. In a cost analysis conducted by Ruane et al. [67], repurposing wind turbines as blade bridges was confirmed to be more economical compared with those using conventional concrete or steel. Broniewicz et al. [68] discussed utilizing wind turbine blades as highway-side noise barriers. The idea involved the use of panels cut from various sections of the E.O.L wind turbine blade. Through finite element analysis (FEA), it was found that panels could withstand forces exerted by traffic wind pressure with very minimal deflections that met the EN 1794-2: 2003 specifications, hence making them a viable alternative. Roadside curb stones are usually made of concrete, which can also be an alternative means of recycling wind turbine blades in this concrete product; in fact, several studies have discussed blade recycling ideas in concrete [69]. Wind turbine blades, even after their service life, still possess remarkable structural properties that can be viable for a wide range of structures. The sheer size of these blades makes them viable in other alternative recycling methods, as discussed by André et al. and Martini et al. [70,71] for example using them as shelter roofings [72], children's playground structures [73], bicycle shades and bus stop seats [74] and many more.
Balancing the economic aspects of recycling is key for any recycling initiative to qualify as viable. Certain aspects, such as the market value of final materials, the cost of technologies used, landfilling taxes, wind turbine dismantling expenses, transportation, and labor costs, are highly fluctuating, which creates a large error estimate in recycling costs[75]. CFRPs have a higher market value compared to GFRPs; thus, methods such as pyrolysis and solvolysis could be used to efficiently extract clean recycled carbon fibers that are more economical compared to using virgin fibers, whereas GFRPs could be recycled in the cement manufacturing process or through other means, such as mechanical processing [76]. Wind turbine blade recycling costs can be significantly reduced. According to a discussion by Cooperman et al., blade transportation costs could be effectively reduced by shredding wind turbine blades into sections of about 1–3 cm or cutting them into large segments. That work also stated that the E.O.L costs for wind turbines could range from 19 to 39 USD per KW while accounting for costs such as teardown, transportation fees, size reduction, and tip fees [77]. Hasheminezhad et al. discussed an estimate of some costs involved in blade recycling, namely the need for large wind turbine blades to be cut to a reduced size to ease transportation. Viable cutting methods include water jets and saw machine cutting, and these services have an approximate daily fee of 2200; transportation of 14 tons of segmented blade waste could cost about 660 [78]. Cost-effectiveness can be a major drawback while dealing with recyclables, though key aspects and policies can be implemented to boost this process. These may involve early-design stage planning for the decommissioning of wind turbines, development of on-site preprocessing facilities, increasing accessibility to blade recycling technologies, tracing material constituents, and establishing material passports [79].
Wind turbine blade waste is increasing, exceeding what can be recycled, while more blades are still being installed globally. Landfilling, which is one of the common destinations for most decommissioned blades, has proven to be unreliable as its costs keep fluctuating over time, hence creating a need for recycling routes for old blades. In the current study, methods for recycling waste wind turbine blades in the pavement industrial sector are discussed and summarized herein:
(1) Wind turbine blade waste can be processed and recycled into asphalt pavement mixtures as filler powders. These powders play a key role in improving the mixture's mechanical properties; for instance, the addition of fillers can help boost the mixture's elasticity at high temperatures, therefore making pavements more resistant to damage. Filler particles can improve other properties of asphalt pavements, such as the fatigue life of asphalt pavements, rutting resistance, aging, and moisture susceptibility.
(2) Processing methods such as pyrolysis, solvolysis, and mechanical processing can be used to extract fibers from blade composite waste. Adding these fibers to concrete or asphalt pavement can boost their mechanical properties. For instance, fibers help improve flexural behavior in concrete, whereas they regulate cracking failure in asphalt.
(3) Wind turbine blades can be converted into crushed aggregates or cut into needle-like elements that can be added to concrete as a partial aggregate replacement. This helps boost the load-bearing capacity and ductility of concrete. Using these aggregates reduces the weight of concrete, hence making it suitable for lightweight structural applications.
(4) Wind turbine blades could also be repurposed into structures around roads such as bicycle shades, pedestrian bridge girders, road acoustic barriers, affordable housing, and playground art. While these recycling routes exist, there are still challenges, such as cost-effectiveness, to feasibly recycle wind turbine blades. For instance, the market value of the final product is, in some cases, very low, and in the case of recycled fibers, they have reduced strength properties compared to new ones.
Composite materials used in blade making have limited recycling routes since they are hard to break down; therefore, it is recommended that industrial manufacturers conduct a feasible recyclability analysis before implementing composites into wind turbine blades. Filler powders extracted and processed from wind turbine blades have promising applications in asphalt pavement mixes in high-temperature regions; regardless, more research and testing are needed using field specimens and also various ways of boosting mixtures' low-temperature performance. A comparative cost analysis study can also be done to compare the cost-effectiveness of various blade recycling routes in the pavement industry.
The authors declare they have not used Artificial Intelligence (AI) tools in the creation of this article.
The authors declare no conflict of interest.
Conceptualization: Shuwen Zhang and Noah Kirumira; Guidance and formal review: Shuwen Zhang; original drafting and editing: Noah Kirumira and Shuwen Zhang; Preliminary revisions: Shuwen Zhang and Noah Kirumira; manuscript submission process; Noah Kirumira; Final Revisions: Shuwen Zhang and Noah Kirumira.
[1] | United Nations Industrial Development Organization, International Yearbook of Industrial Statistics-2023. 2023. Available from: https://www.unido.org/publications/international-yearbook-industrial-statistics. |
[2] |
Kumar A, Singh P, Raizada P, et al. (2022) Impact of COVID-19 on greenhouse gases emissions: A critical review. Sci Total Environ 806: 150349. https://doi.org/10.1016/j.scitotenv.2021.150349 doi: 10.1016/j.scitotenv.2021.150349
![]() |
[3] | Overview of Greenhouse Gases. 2024. Available from: https://www.epa.gov/ghgemissions/overview-greenhouse-gases. |
[4] |
Filonchyk M, Peterson MP, Zhang L, et al. (2024) Greenhouse gases emissions and global climate change: Examining the influence of CO2, CH4, and N2O. Sci Total Environ 935: 173359. https://doi.org/10.1016/j.scitotenv.2024.173359 doi: 10.1016/j.scitotenv.2024.173359
![]() |
[5] | Shuka PR (2023) Climate Change 2022: Mitigation of Climate Change: Working Group Ⅲ Contribution to the Sixth Assessment Report of the Intergovernmental Panel on Climate Change, Cambridgeshire: Cambridge University Press. https://dx.doi.org/10.1017/9781009157926 |
[6] | Siemens 2.37MW-108 SWT Wind Turbine Collapse in Ocotillo, 2016. Available from: https://www.flickr.com/photos/slworking/31210614186/in/photostream/. |
[7] | Wind Turbine Blades Along a Road, Gambia, 2013. Available from: https://www.flickr.com/photos/jbdodane/. |
[8] | Jaynes CH, Green Energy is Set to Match the World's Growing Electricity Demand-IEA Report. 2024. Available from: https://www.weforum.org/agenda/2024/02/green-energy-electricity-demand-growth-iea-report/. |
[9] | Fernández L, Global Wind Power Market-Statistics & Facts. 2024. Available from: https://www.statista.com/topics/4564/global-wind-energy/#topicOverview. |
[10] | WWEA Half-year Report 2023: Additional Momentum for Windpower in 2023. 2023. Available from: https://wwindea.org/wwea-half-year-report-2023-additional-momentum-for-windpower-in-2023. |
[11] |
Heng H, Meng F, McKechnie J (2021) Wind turbine blade wastes and the environmental impacts in Canada. Waste Manag 133: 59–70. https://doi.org/10.1016/j.wasman.2021.07.032 doi: 10.1016/j.wasman.2021.07.032
![]() |
[12] |
Liu P, Barlow CY (2017) Wind turbine blade waste in 2050. Waste Manag 62: 229–240. https://doi.org/10.1016/j.wasman.2017.02.007 doi: 10.1016/j.wasman.2017.02.007
![]() |
[13] | Canary Staff, 15 Companies Working to Recycle Wind Turbines, Solar Panels and Batteries. 2022. Available from: https://www.canarymedia.com/articles/clean-energy/15-companies-working-to-recycle-wind-turbines-solar-panels-and-batteries. |
[14] | Americanrecycler Wind Turbine Blade Recycling Market to Reach 5.6 Billion by 2033. Available from: https://americanrecycler.com/wind-turbine-blade-recycling-market-to-reach-usd-5-6-billion-by-2033/. |
[15] |
Shtayat A, Moridpour S, Best B, et al. (2020) A review of monitoring systems of pavement condition in paved and unpaved roads. J Traffic Transp Eng Engl Ed 7: 629–638. https://doi.org/10.1016/j.jtte.2020.03.004 doi: 10.1016/j.jtte.2020.03.004
![]() |
[16] |
Setyawan A, Irfansyah PA, Shidiq AM, et al. (2017) Design and properties of asphalt concrete mixtures using renewable bioasphalt binder. IOP Conf Ser Mater Sci Eng 176: 012028. https://doi.org/10.1088/1757-899X/176/1/012028 doi: 10.1088/1757-899X/176/1/012028
![]() |
[17] |
Ye Z (2021) Research on asphalt pavement diseases and construction quality control under the background of big data. J Phys Conf Ser 1744: 042139. https://doi.org/10.1088/1742-6596/1744/4/042139 doi: 10.1088/1742-6596/1744/4/042139
![]() |
[18] |
Taher SA, Alyousify S, Hassan HJA, et al. (2020) Comparative study of using flexible and rigid pavements for roads: A review study. J Univ Duhok 23: 222–234. https://doi.org/10.26682/csjuod.2020.23.2.18 doi: 10.26682/csjuod.2020.23.2.18
![]() |
[19] |
Yaro NSA, Sutanto MH, Baloo L, et al. (2023) A comprehensive overview of the utilization of recycled waste materials and technologies in asphalt pavements: Towards environmental and sustainable low-carbon roads. Processes 11: 2095. https://doi.org/10.3390/pr11072095 doi: 10.3390/pr11072095
![]() |
[20] |
Sulyman M, Sienkiewicz M, Haponiuk J (2014) Asphalt pavement material improvement: A review. Int J Environ Sci Dev 5: 444–454. https://doi.org/10.7763/IJESD.2014.V5.525 doi: 10.7763/IJESD.2014.V5.525
![]() |
[21] |
Rahman MT, Mohajerani A, Giustozzi F (2020) Recycling of waste materials for asphalt concrete and bitumen: A review. Materials 13: 1495. https://doi.org/10.3390/ma13071495 doi: 10.3390/ma13071495
![]() |
[22] |
Meijer JR, Huijbregts MAJ, Schotten KCGJ, et al. (2018) Global patterns of current and future road infrastructure. Environ Res Lett 13: 064006. https://doi.org/10.1088/1748-9326/aabd42 doi: 10.1088/1748-9326/aabd42
![]() |
[23] |
Price TJ (2006) UK large-scale wind power programme from 1970 to 1990: The carmarthen bay experiments and the musgrove vertical-axis turbines. Wind Eng 30: 225–242. https://doi.org/10.1260/030952406778606214 doi: 10.1260/030952406778606214
![]() |
[24] |
Gipe P, Möllerström E (2022) An overview of the history of wind turbine development: Part Ⅰ—The early wind turbines until the 1960s. Wind Eng 46: 1973–2004. https://journals.sagepub.com/doi/10.1177/0309524X221117825 doi: 10.1177/0309524X221117825
![]() |
[25] |
Kale SA, Kulkarni SR, Shravagi SD, et al. (2021) Materials for small wind turbine blades. Renew Energ Sustain Develop 43–54. https://doi.org/10.13140/RG.2.2.22099.09762 doi: 10.13140/RG.2.2.22099.09762
![]() |
[26] |
Bulent E, Aysegul A, Ali V (2006) Using of composite material in wind turbine blades. J Appl Sci 6: 2917–2921. https://doi.org/10.3923/jas.2006.2917.2921 doi: 10.3923/jas.2006.2917.2921
![]() |
[27] |
Olabi AG, Wilberforce T, Elsaid K, et al. (2021) A review on failure modes of wind turbine components. Energies 14: 5241. https://doi.org/10.3390/en14175241 doi: 10.3390/en14175241
![]() |
[28] |
Rajak D, Pagar D, Menezes P, et al. (2019) Fiber-reinforced polymer composites: Manufacturing, properties, and applications. Polymers 11: 1667. https://doi.org/10.3390/polym11101667 doi: 10.3390/polym11101667
![]() |
[29] |
Chan YWS, Zhou Z (2014) Advances of FRP-based smart components and structures. Pac Sci Rev 16: 1–7. https://doi.org/10.1016/j.pscr.2014.08.001 doi: 10.1016/j.pscr.2014.08.001
![]() |
[30] |
Jensen JP, Skelton K (2018) Wind turbine blade recycling: Experiences, challenges and possibilities in a circular economy. Renew Sustain Energy Rev 97: 165–176. https://doi.org/10.1016/j.rser.2018.08.041 doi: 10.1016/j.rser.2018.08.041
![]() |
[31] |
Mishnaevsky L, Branner K, Petersen H, et al. (2017) Materials for wind turbine blades: An overview. Materials 10: 1285. https://doi.org/10.3390/ma10111285 doi: 10.3390/ma10111285
![]() |
[32] |
Martin RW, Sabato A, Schoenberg A, et al. (2018) Comparison of nondestructive testing techniques for the inspection of wind turbine blades' spar caps. Wind Energy 21: 980–996. https://doi.org/10.1002/we.2208 doi: 10.1002/we.2208
![]() |
[33] | Blain L, World's Largest Wind Turbine Is Now Fully Operational and Connected. 2023. Available from: https://newatlas.com/energy/worlds-largest-wind-turbine-myse-16-260/. |
[34] |
Cotrell J, Stehly T, Johnson J, et al. (2014) Analysis of transportation and logistics challenges affecting the deployment of larger wind turbines: Summary of results. Natl Renew Energ Lab 6664. https://doi.org/10.2172/1123207 doi: 10.2172/1123207
![]() |
[35] | Dennis S, Heavy Seas Engulf the Block Island Wind Farm. 2016. Available from: https://www.flickr.com/photos/nrel/30353919862/in/photostream/. |
[36] | Ian S, 75 Metre Wind Turbine Blade, 2017. Available from: https://commons.wikimedia.org/wiki/File: 75_metre_Wind_Turbine_Blade_-_geograph.org.uk_-_5247445.jpg. |
[37] | Andersen PD, Bonou A, Beauson J, et al. (2014) Recycling of wind turbines, In: Larsen HH, Petersen LS, DTU International Energy Report 2014: Wind Energy—Drivers and Barriers for Higher Shares of Wind in the Global Power Generation Mix, Copenhagen: Technical University of Denmark. 91–97. https://orbit.dtu.dk/en/publications/recycling-ofwind-turbines |
[38] |
Sorte S, Martins N, Oliveira MSA, et al. (2023) Unlocking the potential of wind turbine blade recycling: Assessing techniques and metrics for sustainability. Energies 16: 7624. https://doi.org/10.3390/en16227624 doi: 10.3390/en16227624
![]() |
[39] |
Nanjegowda VH, Rathankumar MN, Anirudh N (2023) Fillers influence on hot-mix asphalt mixture design and performance assessment. IOP Conf Ser Earth Environ Sci 1149: 012013. https://doi.org/10.1088/1755-1315/1149/1/012013 doi: 10.1088/1755-1315/1149/1/012013
![]() |
[40] |
Fischer HR, Dillingh EC, Hermse CGM (2013) On the interfacial interaction between bituminous binders and mineral surfaces as present in asphalt mixtures. Appl Surf Sci 265: 495–499. https://doi.org/10.1016/j.apsusc.2012.11.034 doi: 10.1016/j.apsusc.2012.11.034
![]() |
[41] |
Mumtaz H, Sobek S, Sajdak M, et al. (2023) An experimental investigation and process optimization of the oxidative liquefaction process as the recycling method of the end-of-life wind turbine blades. Renew Energy 211: 269–278. https://doi.org/10.1016/j.renene.2023.04.120 doi: 10.1016/j.renene.2023.04.120
![]() |
[42] |
Lin J, Guo Z, Hong B, et al. (2022) Using recycled waste glass fiber reinforced polymer (GFRP) as filler to improve the performance of asphalt mastics. J Clean Prod 336: 130357. https://doi.org/10.1016/j.jclepro.2022.130357 doi: 10.1016/j.jclepro.2022.130357
![]() |
[43] |
Lan T, Wang B, Zhang J, et al. (2023) Utilization of waste wind turbine blades in performance improvement of asphalt mixture. Front Mater 10: 1164693. https://doi.org/10.3389/fmats.2023.1164693 doi: 10.3389/fmats.2023.1164693
![]() |
[44] |
Liao MC, Chen JS, Tsou KW (2012) Fatigue characteristics of bitumen-filler mastics and asphalt mixtures. J Mater Civ Eng 24: 916–923. https://doi.org/10.1061/(ASCE)MT.1943-5533.0000450 doi: 10.1061/(ASCE)MT.1943-5533.0000450
![]() |
[45] |
Zhen T, Zhao P, Zhang X, et al. (2023) The effect of GFRP powder on the high and low-temperature properties of asphalt mastic. Materials 16: 2662. https://doi.org/10.3390/ma16072662 doi: 10.3390/ma16072662
![]() |
[46] |
Liu G, Yang T, Li J, et al. (2018) Effects of aging on rheological properties of asphalt materials and asphalt-filler interaction ability. Constr Build Mater 168: 501–511. https://doi.org/10.1016/j.conbuildmat.2018.02.171 doi: 10.1016/j.conbuildmat.2018.02.171
![]() |
[47] |
Yang W, Kim KH, Lee J (2022) Upcycling of decommissioned wind turbine blades through pyrolysis. J Clean Prod 376: 134292. https://doi.org/10.1016/j.jclepro.2022.134292 doi: 10.1016/j.jclepro.2022.134292
![]() |
[48] |
Xu M, Ji H, Wu Y, et al. (2023) The pyrolysis of end-of-life wind turbine blades under different atmospheres and their effects on the recovered glass fibers. Compos Part B Eng 251: 110493. https://doi.org/10.1016/j.compositesb.2022.110493 doi: 10.1016/j.compositesb.2022.110493
![]() |
[49] |
Åkesson D, Foltynowicz Z, Christéen J, et al. (2012) Microwave pyrolysis as a method of recycling glass fibre from used blades of wind turbines. J Reinf Plast Compos 31: 1136–1142. https://doi.org/10.1177/0731684412453512 doi: 10.1177/0731684412453512
![]() |
[50] |
Mishnaevsky L (2021) Sustainable end-of-life management of wind turbine blades: Overview of current and coming solutions. Materials 14: 1124. https://doi.org/10.3390/ma14051124 doi: 10.3390/ma14051124
![]() |
[51] |
Protsenko AE, Protsenko AN, Shakirova OG, et al. (2023) Recycling of epoxy/fiberglass composite using supercritical ethanol with (2, 3, 5-Triphenyltetrazolium)2[CuCl4] complex. Polymers 15: 1559. https://doi.org/10.3390/polym15061559 doi: 10.3390/polym15061559
![]() |
[52] |
Mattsson C, André A, Juntikka M, et al. (2020) Chemical recycling of end-of-life wind turbine blades by solvolysis/HTL. IOP Conf Ser Mater Sci Eng 942: 012013. https://doi.org/10.1088/1757-899X/942/1/012013 doi: 10.1088/1757-899X/942/1/012013
![]() |
[53] |
Sokoli HU (2016) Chemical solvolysis as an approach to recycle fibre reinforced thermoset polymer composites and close the end-of the life cycle. Aalborg University https://doi.org/10.5278/VBN.PHD.ENGSCI.00171 doi: 10.5278/VBN.PHD.ENGSCI.00171
![]() |
[54] |
Pickering SJ, Kelly RM, Kennerley JR, et al. (2000) A fluidised-bed process for the recovery of glass fibres from scrap thermoset composites. Compos Sci Technol 60: 509–523. https://doi.org/10.1016/S0266-3538(99)00154-2 doi: 10.1016/S0266-3538(99)00154-2
![]() |
[55] |
Oliveux G, Bailleul JL, Salle ELG (2012) Chemical recycling of glass fibre reinforced composites using subcritical water. Compos Part Appl Sci Manuf 43: 1809–1818. https://doi.org/10.1016/j.compositesa.2012.06.008 doi: 10.1016/j.compositesa.2012.06.008
![]() |
[56] |
Yang Q, Fan Z, Yang X, et al. (2023) Recycling waste fiber-reinforced polymer composites for low-carbon asphalt concrete: The effects of recycled glass fibers on the durability of bituminous composites. J Clean Prod 423: 138692. https://doi.org/10.1016/j.jclepro.2023.138692 doi: 10.1016/j.jclepro.2023.138692
![]() |
[57] |
Khater A, Luo D, Abdelsalam M, et al. (2021) Laboratory evaluation of asphalt mixture performance using composite admixtures of lignin and glass fibers. Appl Sci 11: 364. https://doi.org/10.3390/app11010364 doi: 10.3390/app11010364
![]() |
[58] |
Mahrez A, Karim MR, Katman HY (2005) Fatigue and deformation properties of glass fiber reinforced bituminous mixes. J Eastern Asia Society Transport Studies 6: 997–1007. https://doi.org/10.11175/easts.6.997 doi: 10.11175/easts.6.997
![]() |
[59] |
Jiao Y, Du W, Yang H, et al. (2024) Low temperature failure behavior analysis of fiber reinforced asphalt concrete under indirect tension test using acoustic emission and digital image correlation. Case Stud Constr Mater 20: e02720. https://doi.org/10.1016/j.cscm.2023.e02720 doi: 10.1016/j.cscm.2023.e02720
![]() |
[60] |
Ortega-López V, Faleschini F, Hurtado-Alonso N, et al. (2024) Analysis of raw-crushed wind-turbine blade as an overall concrete addition: Stress–strain and deflection performance effects. Compos Struct 340: 118170. https://doi.org/10.1016/j.compstruct.2024.118170 doi: 10.1016/j.compstruct.2024.118170
![]() |
[61] |
Yazdanbakhsh A, Bank LC, Rieder KA, et al. (2018) Concrete with discrete slender elements from mechanically recycled wind turbine blades. Resour Conserv Recycl 128: 11–21. https://doi.org/10.1016/j.resconrec.2017.08.005 doi: 10.1016/j.resconrec.2017.08.005
![]() |
[62] |
Baturkin D, Hisseine OA, Masmoudi R, et al. (2022) Compressive behavior of FRP-tube-confined concrete short columns using recycled FRP materials from wind turbine blades: Experimental investigation and analytical modelling. Clean Technol Recycl 2: 136–164. https://doi.org/10.3934/ctr.2022008 doi: 10.3934/ctr.2022008
![]() |
[63] |
Fu B, Liu KC, Chen JF, et al. (2021) Concrete reinforced with macro fibres recycled from waste GFRP. Constr Build Mater 310: 125063. https://doi.org/10.1016/j.conbuildmat.2021.125063 doi: 10.1016/j.conbuildmat.2021.125063
![]() |
[64] |
Baturkin D, Hisseine OA, Masmoudi R, et al. (2021) Valorization of recycled FRP materials from wind turbine blades in concrete. Resour Conserv Recycl 174: 105807. https://doi.org/10.1016/j.resconrec.2021.105807 doi: 10.1016/j.resconrec.2021.105807
![]() |
[65] |
Akbar A, Liew KM (2020) Assessing recycling potential of carbon fiber reinforced plastic waste in production of eco-efficient cement-based materials. J Clean Prod 274: 123001. https://doi.org/10.1016/j.jclepro.2020.123001 doi: 10.1016/j.jclepro.2020.123001
![]() |
[66] |
Ruane K, Zhang Z, Nagle A, et al. (2022) Material and structural characterization of a wind turbine blade for use as a bridge girder. Transport Res Rec 2676: 354–362. https://doi.org/10.1177/03611981221083619 doi: 10.1177/03611981221083619
![]() |
[67] |
Ruane K, Soutsos M, Huynh A, et al. (2023) Construction and cost analysis of bladebridges made from decommissioned FRP wind turbine blades. Sustainability 15: 3366. https://doi.org/10.3390/su15043366 doi: 10.3390/su15043366
![]() |
[68] |
Broniewicz M, Broniewicz F, Dec K, et al. (2024) The concept of using wind turbine propellers in the construction of acoustic screens as an example of a circular economy model. Econ Environ 87: 1–18. https://doi.org/10.34659/eis.2023.87.4.726 doi: 10.34659/eis.2023.87.4.726
![]() |
[69] |
Revilla-Cuesta V, Skaf M, Ortega-López V, et al. (2023) Raw-crushed wind-turbine blade: Waste characterization and suitability for use in concrete production. Resour Conserv Recycl 198: 107160. https://doi.org/10.1016/j.resconrec.2023.107160 doi: 10.1016/j.resconrec.2023.107160
![]() |
[70] |
André A, Kullberg J, Nygren D, et al. (2020) Re-use of wind turbine blade for construction and infrastructure applications. IOP Conf Ser Mater Sci Eng 942: 012015. https://doi.org/10.1088/1757-899X/942/1/012015 doi: 10.1088/1757-899X/942/1/012015
![]() |
[71] |
Martini R, Xydis G (2023) Repurposing and recycling wind turbine blades in the United States. Environ Prog Sustain 42: e13932. https://doi.org/10.1002/ep.13932 doi: 10.1002/ep.13932
![]() |
[72] |
Bank L, Arias F, Yazdanbakhsh A, et al. (2018) Concepts for reusing composite materials from decommissioned wind turbine blades in affordable housing. Recycling 3: 3. https://doi.org/10.3390/recycling3010003 doi: 10.3390/recycling3010003
![]() |
[73] | McGlasson R, These Awesome Playgrounds Are Made Out of Old, Used-Up Wind Turbines—Here's Why That's Special. 2023. Available from: https://www.thecooldown.com/green-tech/blade-made-playground-wind-turbine-blades-recycled/. |
[74] | Yelland C, Denmark Is Repurposing Discarded Wind Turbine Blades As Bike Shelters. 2021. Available from: https://www.designboom.com/design/denmark-repurposing-wind-turbine-blades-bike-garages-09-27-2021/. |
[75] |
Cherrington R, Goodship V, Meredith J, et al. (2012) Producer responsibility: Defining the incentive for recycling composite wind turbine blades in Europe. Energy Policy 47: 13–21. https://doi.org/10.1016/j.enpol.2012.03.076 doi: 10.1016/j.enpol.2012.03.076
![]() |
[76] |
Spini F, Bettini P (2024) End-of-Life wind turbine blades: Review on recycling strategies. Compos Part B Eng 275: 111290. https://doi.org/10.1016/j.compositesb.2024.111290 doi: 10.1016/j.compositesb.2024.111290
![]() |
[77] |
Cooperman A, Eberle A, Lantz E (2021) Wind turbine blade material in the United States: Quantities, costs, and end-of-life options. Resour Conserv Recycl 168: 105439. https://doi.org/10.1016/j.resconrec.2021.105439 doi: 10.1016/j.resconrec.2021.105439
![]() |
[78] |
Hasheminezhad A, Nazari Z, Yang B, et al. (2024) A comprehensive review of sustainable solutions for reusing wind turbine blade waste materials. J Environ Manage 366: 121735. https://doi.org/10.1016/j.jenvman.2024.121735 doi: 10.1016/j.jenvman.2024.121735
![]() |
[79] |
Tyurkay A, Kirkelund GM, Lima ATM (2024) State-of-the-art circular economy practices for end-of-life wind turbine blades for use in the construction industry. Sustain Prod Consum 47: 17–36. https://doi.org/10.1016/j.spc.2024.03.018 doi: 10.1016/j.spc.2024.03.018
![]() |
Asphalt attributes | Observations | Explanation | Sources |
High and medium temperature performance | The complex modulus of asphalt increases in the WTB-GFRP filler content, whereas the phase angle is reduced. | WTB-GFRP fillers enhance asphalt elasticity at higher temperatures through absorption of free binder, hence leading to a stiffer asphalt mixture. | [42] |
Fatigue cracking | GFRP filler specimens had lesser fatigue values compared to typical limestone when subjected to similar strain levels | WTB-GFRP filler mastics possess better resistance to fatigue cracking failure compared with the commonly used limestone fillers. | [42,44] |
Rutting resistance | Dynamic stability values from a wheel tracking test increased with the addition of WTB-GFRP filler powder to the asphalt mixture. | The addition of WTB-GFRP filler can improve the pavement's rutting failure resistance. | [43] |
Low temperature cracking | The addition of WTB-GFRP fillers to asphalt increases its stiffness value and reduces the M-value. | Higher stiffness values depict more brittle asphalt mastic, which therefore carries a greater risk of crack formation at low temperatures. | [45] |
Moisture resistance | Boiling water test results showed WTB-GFRP filler asphalt specimens had lesser shade offs compared to limestone. | Presence of WTB-GFRP fillers in asphalt greatly enhances moisture resistance by improving it's adhesive and cohesive capabilities. | [42] |
Aging resistance | Long term aged WTB-GFRP filler asphalt mastics had a lower complex modulus aging index and higher phase angle aging index. | WTB-GFRP fillers improve asphalt long-term aging compared to typical limestone | [42,46] |
Asphalt attributes | Observations | Explanation | Sources |
High and medium temperature performance | The complex modulus of asphalt increases in the WTB-GFRP filler content, whereas the phase angle is reduced. | WTB-GFRP fillers enhance asphalt elasticity at higher temperatures through absorption of free binder, hence leading to a stiffer asphalt mixture. | [42] |
Fatigue cracking | GFRP filler specimens had lesser fatigue values compared to typical limestone when subjected to similar strain levels | WTB-GFRP filler mastics possess better resistance to fatigue cracking failure compared with the commonly used limestone fillers. | [42,44] |
Rutting resistance | Dynamic stability values from a wheel tracking test increased with the addition of WTB-GFRP filler powder to the asphalt mixture. | The addition of WTB-GFRP filler can improve the pavement's rutting failure resistance. | [43] |
Low temperature cracking | The addition of WTB-GFRP fillers to asphalt increases its stiffness value and reduces the M-value. | Higher stiffness values depict more brittle asphalt mastic, which therefore carries a greater risk of crack formation at low temperatures. | [45] |
Moisture resistance | Boiling water test results showed WTB-GFRP filler asphalt specimens had lesser shade offs compared to limestone. | Presence of WTB-GFRP fillers in asphalt greatly enhances moisture resistance by improving it's adhesive and cohesive capabilities. | [42] |
Aging resistance | Long term aged WTB-GFRP filler asphalt mastics had a lower complex modulus aging index and higher phase angle aging index. | WTB-GFRP fillers improve asphalt long-term aging compared to typical limestone | [42,46] |