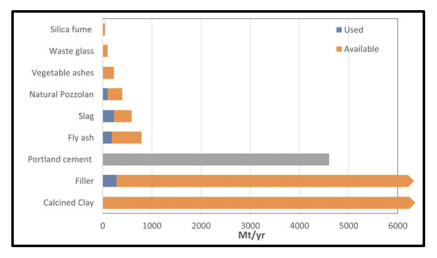
Citation: Rein Terje Thorstensen. Preventing early age chloride migration into low-carbon concrete[J]. AIMS Materials Science, 2019, 6(6): 1020-1032. doi: 10.3934/matersci.2019.6.1020
[1] | V. Flores-Alés, F.J. Alejandre, F.J. Blasco-López, M. Torres-González, J.M. Alducin-Ochoa . Analysis of alterations presented in a white-concrete façade exposed to a marine environment——A case study in Cádiz (Spain). AIMS Materials Science, 2022, 9(2): 255-269. doi: 10.3934/matersci.2022015 |
[2] | Grzegorz Ludwik Golewski . Mechanical properties and brittleness of concrete made by combined fly ash, silica fume and nanosilica with ordinary Portland cement. AIMS Materials Science, 2023, 10(3): 390-404. doi: 10.3934/matersci.2023021 |
[3] | Tayebi M'hammed, Khelafi Hamid . An experimental study on the influence of arid climate on early-age cracking of concrete—A case study of the city of Adrar in Algeria. AIMS Materials Science, 2021, 8(2): 200-220. doi: 10.3934/matersci.2021014 |
[4] | M. Kanta Rao, Ch. N. Satish Kumar . Influence of fly ash on hydration compounds of high-volume fly ash concrete. AIMS Materials Science, 2021, 8(2): 301-320. doi: 10.3934/matersci.2021020 |
[5] | Mahmoud A. Rabah, Mohamed B. El Anadolly, Rabab A. El Shereif, Mohamed Sh. Atrees, Hayat M. El Agamy . Preparation of valuable products from cleaned carbon of fuel ash. AIMS Materials Science, 2017, 4(5): 1186-1201. doi: 10.3934/matersci.2017.5.1186 |
[6] | Aleksei V. Shiverskii, Aleksandr V. Kukharskii, Stepan V. Lomov, Sergey G. Abaimov . Recycling glass fiber-reinforced plastic in asphalt concrete production. AIMS Materials Science, 2024, 11(2): 231-242. doi: 10.3934/matersci.2024013 |
[7] | Ayumu Yasue, Keita Hayashi, Shogo Yamamoto, Toshitsugu Inukai, Shigeru Fujimori . Influence of concrete bleeding due to mix proportion on the drilling speed of hardened surface layer. AIMS Materials Science, 2021, 8(3): 486-500. doi: 10.3934/matersci.2021030 |
[8] | Yustina M Pusparizkita, Vivi A. Fardilah, Christian Aslan, J. Jamari, Athanasius P Bayuseno . Understanding of low-carbon steel marine corrosion through simulation in artificial seawater. AIMS Materials Science, 2023, 10(3): 499-516. doi: 10.3934/matersci.2023028 |
[9] | M. P. Lavin-Lopez, L. Sanchez-Silva, J. L. Valverde, A. Romero . CVD-graphene growth on different polycrystalline transition metals. AIMS Materials Science, 2017, 4(1): 194-208. doi: 10.3934/matersci.2017.1.194 |
[10] | Stelladriana Volpe, Andrea Petrella, Valentino Sangiorgio, Michele Notarnicola, Francesco Fiorito . Preparation and characterization of novel environmentally sustainable mortars based on magnesium potassium phosphate cement for additive manufacturing. AIMS Materials Science, 2021, 8(4): 640-658. doi: 10.3934/matersci.2021039 |
Concrete is essential to the growth and welfare of all modern societies. According to the European Cement Association CEMBUREAU, the total cement production in the world was 4.65 billion tonnes in 2016 [1], roughly estimated to constitute around 2 cubic meters of concrete per capita in the world being built into new structures every year. And these numbers are growing. The world capita is expected to grow from today's 7.6 to 10 billion in 2050 [2]. This population growth alone indicates that the world production of cement will have to grow to 6 billion tonnes in 2050, only to accommodate the population growth [3]. In addition, concrete is needed for supporting the economic growth of societies.
Within the civil and structural industry, "concrete" is commonly understood as a composite material where particles of rock and sand are "glued" together, mainly using Portland Cement (PC) as the binder. PC is locally available in most regions of the world, through a relatively simple process involving calcination of natural minerals at 1450 degrees Celsius. However, it is this process that is responsible for most of the high CO2 footprint from the concrete industry; 600–1000 kg CO2 per 1000 kg PC depending on the production process. Some of this stems from the energy consumption, but near 500kg is due to the elimination of CO2 from the mineral calcite (CaCO3). This CO2-elimination is the main purpose of the calcination process. Hence, the production of PC is not possible without severe emissions of CO2.
Several materials have the potential for substituting parts of the PC in concrete, commonly referred to as Substituting or Supplementary Cementitious Materials (SCM). SCMs are categorized into two groups; latent hydraulic materials and pozzolanic materials. Latent hydraulic materials react with water, but only in the presence of a catalyst like PC. Slag, mainly from the ferroalloy industry is the dominant representative of the latent hydraulic materials. Pozzolanic SCMs do not react with water, however with the Portlandite (calcium-hydroxide, Ca(OH)2) which is a byproduct from the reaction where PC hydrates in water to create calcium-silicate-hydrate (C–S–H)—the "glue" in concrete. A variety of pozzolanic materials are known, both natural (like clays) and industrial byproducts (like ashes from combustion of organic materials or fly-ash from the silicon industry). Dominant scientists like Prof PK Mehta have worked for decades to develop the knowledge of the qualities of SCMs. It is well documented that SCMs have the potential for successfully substituting parts of the PC in concrete and even for improving most qualities, including durability. One example is [4], published in the third edition in 2008. Due to the potential for lowering the CO2 emission, concretes with a high level of PC substitution by SCMs are often referred to as low-carbon concrete.
The concrete industry is commonly accepted to be responsible for 5–7% of the global anthropogenic CO2 emission, e.g., [5]. This is challenging in times when the emission of greenhouse gasses is believed as being responsible for major global warming. The UN Environmental Program Sustainable Building and Climate Initiative are making efforts to meet this challenge. In a report from this effort [6], sources of SCMs and today's utilization of those are demonstrated (Figure 1). Sources of slag are still available, but further utilization is hindered by formal regulations. However, the main available sources of SCMs regards pozzolans, and utilization of those are less restricted by legislations. It seems reasonable to expect that the use of SCMs will increase.
One severe drawback of pozzolanic SCMs is that the chemical reaction where these SCMs adds to the creation of C–S–H through reacting with Portlandite is secondary to the PC hydration. Thus, the pozzolanic reaction is slow compared to the PC hydration, leaving early age low-carbon concrete more prone to the penetration of degrading agents than concrete made of 100% PC. One major degrading mechanism of structural concrete is caused by the penetration of chlorides. Chlorides are common in the structural environment, e.g., in marine environments or stemming from the use of de-icing agents. The main problem with chloride penetration in concrete structures regards reinforcement corrosion. Structural concrete uses steel reinforcement to handle tensile loads. A layer preventing corrosion is created around the steel reinforcement in concrete, caused by the high level of pH in the pore water of PC-based concrete. This protective layer is damaged in the presence of chlorides, leaving the reinforcement exposed for corrosion.
In the above text, a reduction in the emission of CO2 has been the argument for utilization of SCMs in concrete. However, quite another argument is also leading to increased use of SCMs; the heating potential of PC. Hydration of PC is an exothermic reaction, leading to high temperature gradients in hardening concrete. These temperature gradients induce tension in the partly hardened concrete, sufficient for causing cracks, especially in massive concrete structures. The cracks are hardly a problem to the structural capacity but can severely influence the durability of the structures as they open for penetration of degrading agents.
The combination of expectations on the increased use of SCMs and knowledge on the weakness of SCM-based concrete being more prone to early age penetration of degrading agents calls for efforts on finding easily available means to avoid future challenges on degrading structures. The research presented in this paper adds to this knowledge gap by investigating the effects of using hydrophobic paint on the concrete surfaces, to protect against early age penetration of water-soluble agents like chloride.
The development of concrete for these experiments aimed at a high level of PC substitution, while still obtaining high workability represented by the slump of 200 mm +/− 20 mm. Considering that marine environment and the use of de-icing agents were chosen to represent the main degrading environmental challenges, it was decided to add freezing resistance by the use of an air-entraining agent for adjusting the level of air in the concrete to 4.5% +/− 1.5%. The composition is shown in Table 1. The density of this hardened concrete was 2320 kg/m3.
Constituent | Type | Dosage (kg/m3) |
Sand 0–8 | Local source (Reddal) | 940 |
Fine aggregate 8–16 | Local source (TT Anlegg) | 294 |
Coarse aggregate 16–22 | Local source (TT Anlegg) | 644 |
Cem Ⅱ/A–V (81%PC, 15%FA) | Norcem FA | 272 |
FlyAsh class F (ASTM C618) | Supplied by Unicon | 86 |
Silica fume | Elkem 940U (undensified) | 15 |
Added water | Local supply | 173.5 |
HRWRA/SP | Mapei Dynamon SX-N | 2.04 |
Air-entraining agent | Mapei Mapeair 25 | 0.816 |
Water/binder ratio | 0.48 | |
SCM substitution level | % of PC | 64 |
-----------"----------- | % of total binder | 39 |
Hydrophobic paint for surface treatment | StoCryl HG200 (Silane) |
The composition was based on a known concrete expected to develop the compressive strength of 45 MPa after 28 d hardening. However, due to the cement substitution being increased from 15% to 64%, the hardening process was delayed. The achieved compressive strength was 34 MPa after 28 d, increasing to 42 MPa after 56 d. The reference curing time for compressive strength is set to 28 d in today's design standards. However, to accommodate the utilization of pozzolanic SCMs, the revised EN1992—"Eurocode 2: Design of concrete structures" (now on hearing), opens for utilizing 92 d compressive strength in the design of structures.
Though this is an investigation on measures to improve the durability of concrete, the durability of the protective hydrophobic paint is only indirectly discussed (in section 3.1 and 3.2.2). This is due to the consideration that the purpose of the protective surface treatment is to achieve a temporary protection of the structure until the maturity of the concrete itself has developed to the level required for resisting chloride penetration. This is a matter of weeks, and thus expected to be well within the lifetime of the protection from the hydrophobic paint.
The concrete was exposed to two different degrading environments, alternatively:
Ⅰ. Elements (100 mm × 350 mm × 350 mm) submerged in a solution of 3.5% NaCl in water at ambient temperature (0–15 degrees Celsius, averaging around 6). These elements were used to simulate full-scale conditions with uni-axial penetration of chlorides and are hence denoted "site elements" in the paper. Cylinder cores were drilled out to be used for test specimens.
Ⅱ. Test cubes (100 mm × 100 mm × 100 mm) partly submerged in the same NaCl solution, placed in a freezing-thawing cabinet accommodating ASTM C666. 56 full cycles of +/−20 degrees Celsius were executed.
The concrete was poured into non-absorbing moulds made of steel (cubes) or special plywood (site elements), slightly vibrated according to a constant procedure and then covered with plastic film to prevent evaporation from the surface. All were kept in a controlled environment at 20 degrees Celsius +/−2. Demoulding was executed three days after pouring to ensure structural integrity, thus avoiding damaging allowed by the prolonged hardening time of the high SCM-level concrete.
For further maturing, all elements were kept in airtight containers until exposure, to maintain uniform humidity.
The application of hydrophobic paint was executed directly after demoulding, before placement of all specimen in an airtight container. Achieving a uniform layer was endeavored by placing each specimen on a scale during application, aiming at application of 280 g/m2. Achieved standard deviation from this mean was 17.
To determine the chloride content, samples of pulverized concrete was produced by grinding the exposed concrete with a diamond disk. Each pulverized sample was standardized on mass and dissolved in a 10% HNO3-solution. A set of ion-selective electrodes was used together with a voltmeter to identify the content of chlorides in the solution. This set-up was calibrated towards a set of standard solutions with a known content of chlorides. The calibration was executed prior to the measurements and repeated frequently during the measurements.
All measurements are based on several parallel tests. The number of parallel tests vary (3–9) between the different experiments, and are statistically treated as follows:
Average and quartiles are calculated for all results from the parallel measurements. Due to the nature of this highly inhomogeneous material and the rugged methods, nonvalid results are frequently occurring caused by non-homogenous specimens (E.g., voids of entrained air might be invisible, but highly interfering with the results). Outliers amongst the measured data are understood as such nonvalid results. Outliers are handled by excluding single values that exceeds either the upper or the lower quartile. Subsequent to this exclusion, the average of the remaining values is used for further comparison and discussion.
The main test on the overall effect of surface treatment with hydrophobic paint is based on datasets from 9 parallel tests. For this test, the statistical significance of the results is evaluated by presenting the upper and lower limits for the symmetric 95% confidence interval for each of the result sets—both reference and surface treated specimens. The calculation of the confidence interval is based on the data being Student T distributed.
The intention of applying hydrophobic paint is to achieve a water repellent surface, and thus reducing the penetration of water-soluble degrading agents into the slightly porous concrete. To fulfill its purpose, the hydrophobic behavior must endure until the creation of C–S–H from the pozzolanic reaction has supplied the concrete with sufficient properties to resist correspondingly. According to the information given by the producer, the hydrophobic paint should penetrate at least 1 mm into the concrete. The achieved penetration was measured for every 10mm on a cross-section of the specimens. The typical averages values are shown in Figure 2. The typical penetration depth is shown to be substantially better than the requirement from the supplier of the paint. This indicates that the application has been successful. But the high penetration depth also illustrates the porosity at early ages of this high SCM-level concrete.
The majority of the tests were performed by submerging the site elements in a solution of 3.5% sodium chloride dissolved in water, to simulate the salinity in the Norwegian marine environment. The container was placed outdoor, for the whole period starting March 1st. The ambient temperature was varying within the span 0 to 15 degrees Celsius, averaging around 6 degrees. At testing time, test core specimens were drilled out from the site elements. By following this procedure, the penetration direction of chlorides was anticipated to simulate the uniaxial penetration that real structures are exposed to. Three mechanisms were investigated; the potential effect from surface treatment, the effect of exposure time, and the effect of maturity (the concrete hardening and the polymerization of the hydrophobic paint) achieved before the exposure. The results of those three investigations are presented and discussed below.
This test was performed at elements after 6 d of maturity, meaning that the concrete had hardened for three days before the surface treatment, and then another three days for polymerizing the hydrophobic paint. At this age, the elements were submerged in the sodium chloride solution for three weeks. Three cores were drilled from each of the two elements; the reference and the test element having a hydrophobic surface treatment. From each of those, three sets of dust samples were collected from different areas—constituting a total of nine datasets from each of the reference and the test element at each profile. The corresponding chloride profiles for each of the two are presented in Figure 3.
The two solid lines in the diagram in Figure 3 represent the average of all results for the reference and the test element, respectively. In the outer layer, at 0–2 mm depth, the concentration of chlorides is reduced by 50% by the hydrophobic surface treatment, compared to the reference element without any treatment. Already in the layer at 4–6 mm depth from the surface, the chloride concentration is below negligible 0.05%. Only at a depth of approximately 12 mm, the correspondingly low value is achieved for the reference element.
To evaluate the significance of the measured differences towards the reliability of the measurements, the symmetric 95% confidence interval has been calculated anticipating that the data represent a Student T distribution. The upper and lower limits for these confidence intervals are represented by the dotted lines in the diagram. The narrow limitation that these dotted lines represent around the average, demonstrates that the quality of the measurements is good. Also, it becomes visualized that the magnitude of the anticipated effect of the surface treatment by far exceeds the uncertainty of the method, and thus that the concluded effect of the hydrophobic surface treatment is statistically significant.
It seems reasonable to expect that the chloride penetration into the concrete is a function of the exposure time and that this relation represents a function growing by power on the form y = aXb, which decreases with time. Time dependent relations within building materials are often modelled by this simple equation. To investigate this possible effect, specimens were tested after three- and seven-weeks exposure, respectively. This investigation was performed after 10 d of maturing time. The resulting chloride profiles are presented in Figure 4.
The dotted lines represent the development of the reference elements. In the outer layer 0–2 mm from the surface, the chloride concentration had increased from 0.28% to 0.40% when the exposure time increased from three to seven weeks.
Two points are too little information for making a power regression. However, assuming that the graph would go through a point close to origo, e.g. (0.1, 0.1), a close fit (R2 = 0.991) is represented by chloride concentration y = 0.21 × (exposure time)0.32, as illustrated by the solid line in Figure 5. Hence, the assumption that the chloride penetration is growing at a decreasing rate as a function of the time is strengthened.
The dotted line in Figure 5 represents the chloride penetration in the test samples treated with hydrophobic paint. These data points are best fit to a straight line (R2 = 0.999), indicating growth at a constant rate. This somewhat surprising finding might be explained by the protective layer of hydrophobic paint being degraded by the environment, and hence the protective properties being diminished.
The maturity of the site elements prior to the exposure to the chloride-rich environment was expected to influence the chloride penetration rate. To investigate this possible mechanism, three different maturing regimes were tested, respectively comprising a total of 6, 10, and 17 d. The resulting chloride profiles are shown in Figure 6a. By increasing the maturing time from 6 to 17 d, the chloride penetration in the outer layer (0–2 mm) was reduced by a factor of four. This demonstrates that the rate of chloride penetration is a function of maturing time prior to exposure. Figure 6b illustrates that the improving effect of maturing time prior to exposure is decreasing with time, well modeled by an ordinary power function (y = aXb).
The maturing process consists of two independent mechanisms; the hardening of the concrete and the polymerization of the hydrophobic paint. Both are expected to influence the penetration rate of chlorides into the concrete. To conclude on any effects from the hydrophobic paint, it is necessary to evaluate the two mechanisms separately. Figure 7 illustrates the effect of concrete hardening alone, showing that the maturing prior to exposure is significantly influenced by the concrete hardening. The chloride penetration in the outer layer is near halved when the maturity time is increased from 6 to 17 d.
However, from Figure 6a which in addition to the maturity level of the elements treated with hydrophobic paint also contains the reference element with the longest maturing time prior to exposure, it becomes clear that hydrophobic paint adds substantially to the protection against chloride penetration. Even after just 6 d of maturing, the treated element has substantially lower chloride content than the reference element which has matured for 17 d. This added effect was investigated.
All site elements were demoulded three days after pouring. This relatively long curing time before demoulding was chosen to secure the structural integrity of the elements. This is an issue because of the high level of pozzolanic cementitious binder, expected to delay the hardening process of the concrete. As soon as the elements were demoulded, the surfaces were treated with the hydrophobic paint. While the hardening time for the concrete equals the stated maturing time, the polymerization process was three days shorter for all maturity ages.
The effect of the hydrophobic paint on the surface of the elements can be investigated by the filtering effect, expressing the reduction in accumulated mass of chlorides which has penetrated each surface unit of the concrete, relative to the reference without any treatment. The mathematical expression simply becomes:
(1) |
where mcl tot, x = the accumulated mass of chlorides which has penetrated each surface unit of the concrete, accumulated for all layers (g/m2). The filtering effect found by the application of Eq 1 is visualized in Figure 8. The polymerization time expressed along the x-axis equals the maturing time minus three days of concrete hardening in the mould prior to the application of the hydraulic paint. Figure 8 demonstrates that the hydrophobic paint is able to reduce the chloride penetration by 70% after 3 d of polymerization prior to exposure, relative to that of the untreated reference concrete. This filtering effect can be improved by increasing the polymerization time prior to exposure, up to a level of around 90% after 7 d. Further time for polymerization does not add substantially to the protection.
Considering that loads from the marine environment are in the scope of this investigation, influence from repeated freezing-thawing cycles in the splash zone is of special interest. Trying to simulate these harsh conditions, a set of test specimen was exposed to partly submerging in a freezing-thawing cabinet. After 56 full cycles of +/− 20 degrees Celsius, chloride profiles for the splash zone were determined, as illustrated in Figure 9. Also exposed to these harsh conditions, surface treatment with hydrophobic paint seems to have the potential for substantially reducing the penetration of chlorides in early-age low-carbon concrete. Measurements of chloride content in the outmost layer of the concrete are omitted, as surface scaling is an effect of repeated freezing-thawing cycles. Hence, the outer layer (0–4 mm) is hardly existing, and measurements start in the layer 4–6 mm. In this layer, the chloride content is reduced from 0.085% to 0,025% as a consequence of surface treatment with hydrophobic paint.
However, several other investigations at the same exposure regime were rejected due to large deviations in the measured results from parallel tests. Indications are that the combination of freezing-thawing cycles and exposure to chloride penetration at an early age is too challenging for this low-carbon concrete. Maybe using larger test specimens might reduce the problem. If the frost damage leads to the secession of one single particle from the coarse agammaegate, this might substantially influence the determined chloride profile. The size of one particle of the coarse agammaegate constitutes quite a portion of the 100 mm cubes used in this investigation.
1. Hydrophobic paint can protect against penetration of chloride ions into early age low-carbon concrete.
2. The efficiency of the hydrophobic paint to prevent chloride penetration into concrete is expressed by the filtering effect. The filtering effect of the applied product is found to reduce the chloride penetration up to 90%, compared to that of the same concrete without surface treatment. This filtering effect is dependent on the polymerization time prior to exposure; 70% after 3 d polymerization and peeking on 90% after 7 d. Further polymerization time does not add substantially to the protection.
3. While chloride penetration into the (unprotected) reference concrete was found to be time-dependent with a decreasing growth rate, the penetration into the test elements protected with hydrophobic paint was growing at a constant rate. It is suggested that this is due to the protective effect of the hydrophobic paint being degraded already after a few weeks.
4. Tests from the harsh environment of repeated freezing-thawing cycles, while test specimen were partly submerged in 3.5% NaCl-solution, indicate that application of hydrophobic paint have the potential for reducing chloride penetration down to a level of 30% of the (unprotected) reference. However, large variations in the results from this test question the strength of this conclusion, as several other tests under the same conditions were rejected. A suggestion for follow-up investigations is to increase the size of the test specimen.
My sincere thanks to civil engineers Marius Ravnelien, Jørgen Kemal Eidsgård, and Martin Lien, for thoroughly executed efforts in the lab while being "my" students prior to your graduation. You did all the hard work. I am impressed and grateful.
No conflict of interest has been identified.
[1] | Cembureau (The European Cement Association) (2016) Key figures. Available from: https://cembureau.eu/cement-101/key-facts-figures/. |
[2] | United Nations (2017) World Population Prospects: The 2017 revision. Available from: https://www.un.org/development/desa/publications/world-population-prospects-the-2017-revision.html. |
[3] | Larsen IL, Terjesen O, Thorstensen RT, et al. (2019) Use of concrete for road infrastructure: A SWOT analysis related to the three catchwords sustainability, industrialisation and digitalisation. Transportation Research Board (TRB) Annual Meeting, 31-55. |
[4] | Malhotra VM, Mehta PK (2012) High-performance, High-volume Fly Ash Concrete: For Building Sustainable and Durable Structures, Supplementary Cementing Materials for Sustainable Developmen. |
[5] |
Benhelal E, et al. (2013) Global strategies and potentials to curb CO2 emissions in cement industry. J Clean Prod 51: 142-161. doi: 10.1016/j.jclepro.2012.10.049
![]() |
[6] |
Scrivener KL, John VM, Gartner EM (2018) Eco-efficient cements: potential economically viable solutions for a low-CO2 cement-based materials industry. Cement Concrete Res 114: 2-26. doi: 10.1016/j.cemconres.2018.03.015
![]() |
1. | Anrea Di Schino, Marco Corradi, Construction and building materials, 2020, 7, 2372-0484, 157, 10.3934/matersci.2020.2.157 | |
2. | Grzegorz Ludwik Golewski, Fracture Performance of Cementitious Composites Based on Quaternary Blended Cements, 2022, 15, 1996-1944, 6023, 10.3390/ma15176023 | |
3. | Nan Yao, Xiaocheng Zhou, Yongqi Liu, Jinjie Shi, Synergistic effect of red mud and fly ash on passivation and corrosion resistance of 304 stainless steel in alkaline concrete pore solutions, 2022, 132, 09589465, 104637, 10.1016/j.cemconcomp.2022.104637 | |
4. | Ernesto Mora, Erick Castellón, The role of coarse aggregates in hydrophobized hydraulic concrete, 2022, 11, 2046-0147, 209, 10.1680/jemmr.21.00027 | |
5. | Grzegorz Ludwik Golewski, Mechanical properties and brittleness of concrete made by combined fly ash, silica fume and nanosilica with ordinary Portland cement, 2023, 10, 2372-0484, 390, 10.3934/matersci.2023021 |
Constituent | Type | Dosage (kg/m3) |
Sand 0–8 | Local source (Reddal) | 940 |
Fine aggregate 8–16 | Local source (TT Anlegg) | 294 |
Coarse aggregate 16–22 | Local source (TT Anlegg) | 644 |
Cem Ⅱ/A–V (81%PC, 15%FA) | Norcem FA | 272 |
FlyAsh class F (ASTM C618) | Supplied by Unicon | 86 |
Silica fume | Elkem 940U (undensified) | 15 |
Added water | Local supply | 173.5 |
HRWRA/SP | Mapei Dynamon SX-N | 2.04 |
Air-entraining agent | Mapei Mapeair 25 | 0.816 |
Water/binder ratio | 0.48 | |
SCM substitution level | % of PC | 64 |
-----------"----------- | % of total binder | 39 |
Hydrophobic paint for surface treatment | StoCryl HG200 (Silane) |
Constituent | Type | Dosage (kg/m3) |
Sand 0–8 | Local source (Reddal) | 940 |
Fine aggregate 8–16 | Local source (TT Anlegg) | 294 |
Coarse aggregate 16–22 | Local source (TT Anlegg) | 644 |
Cem Ⅱ/A–V (81%PC, 15%FA) | Norcem FA | 272 |
FlyAsh class F (ASTM C618) | Supplied by Unicon | 86 |
Silica fume | Elkem 940U (undensified) | 15 |
Added water | Local supply | 173.5 |
HRWRA/SP | Mapei Dynamon SX-N | 2.04 |
Air-entraining agent | Mapei Mapeair 25 | 0.816 |
Water/binder ratio | 0.48 | |
SCM substitution level | % of PC | 64 |
-----------"----------- | % of total binder | 39 |
Hydrophobic paint for surface treatment | StoCryl HG200 (Silane) |