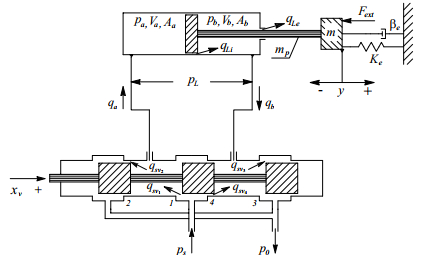
In this paper, the mechanism for the fault estimation (FE) problem for a hydraulic servo actuator (HSA) with sensor faults is investigated. To deal with the design issues, we transformed the nonlinear model of HSA into a new coordinate system to estimate the sensor faults. In the new coordinate system, the Lipschitz conditions and system uncertainties are also considered. Then, we implement a sliding mode observer (SMO) approach to introduce the transformation scheme to make the system rational. The proposed fault estimation scheme essentially transforms the original system into two subsystems where the first one includes system uncertainties, but is free from sensor faults and the second one has sensor faults but without uncertainties. The effects of system uncertainties on the estimation errors of states and faults are minimized by integrating an H∞ uncertainty attenuation level into the observer. The sufficient conditions for the state estimation error to be bounded and satisfy a prescribed H∞ performance are derived and expressed as a linear matrix inequality (LMI) optimization problem. Finally, the numerical example with simulation results is provided to validate the practicability and efficacy of the developed control strategy.
Citation: Vladimir Djordjevic, Ljubisa Dubonjic, Marcelo Menezes Morato, Dragan Prsic, Vladimir Stojanovic. Sensor fault estimation for hydraulic servo actuator based on sliding mode observer[J]. Mathematical Modelling and Control, 2022, 2(1): 34-43. doi: 10.3934/mmc.2022005
[1] | Vladimir Stojanovic . Fault-tolerant control of a hydraulic servo actuator via adaptive dynamic programming. Mathematical Modelling and Control, 2023, 3(3): 181-191. doi: 10.3934/mmc.2023016 |
[2] | Naveen Kumar, Km Shelly Chaudhary . Position tracking control of nonholonomic mobile robots via $ H_\infty $-based adaptive fractional-order sliding mode controller. Mathematical Modelling and Control, 2025, 5(1): 121-130. doi: 10.3934/mmc.2025009 |
[3] | Weiwei Han, Zhipeng Zhang, Chengyi Xia . Modeling and analysis of networked finite state machine subject to random communication losses. Mathematical Modelling and Control, 2023, 3(1): 50-60. doi: 10.3934/mmc.2023005 |
[4] | Wen Zhang, Jinjun Fan, Yuanyuan Peng . On the discontinuous dynamics of a class of 2-DOF frictional vibration systems with asymmetric elastic constraints. Mathematical Modelling and Control, 2023, 3(4): 278-305. doi: 10.3934/mmc.2023024 |
[5] | Weisong Zhou, Kaihe Wang, Wei Zhu . Synchronization for discrete coupled fuzzy neural networks with uncertain information via observer-based impulsive control. Mathematical Modelling and Control, 2024, 4(1): 17-31. doi: 10.3934/mmc.2024003 |
[6] | Yuyang Zhao, Yang Liu . Output controllability and observability of mix-valued logic control networks. Mathematical Modelling and Control, 2021, 1(3): 145-156. doi: 10.3934/mmc.2021013 |
[7] | Xiaoyu Ren, Ting Hou . Pareto optimal filter design with hybrid $ H_{2} /H_{\infty} $ optimization. Mathematical Modelling and Control, 2023, 3(2): 80-87. doi: 10.3934/mmc.2023008 |
[8] | Biresh Kumar Dakua, Bibhuti Bhusan Pati . A frequency domain-based loop shaping procedure for the parameter estimation of the fractional-order tilt integral derivative controller. Mathematical Modelling and Control, 2024, 4(4): 374-389. doi: 10.3934/mmc.2024030 |
[9] | Ihtisham Ul Haq, Nigar Ali, Shabir Ahmad . A fractional mathematical model for COVID-19 outbreak transmission dynamics with the impact of isolation and social distancing. Mathematical Modelling and Control, 2022, 2(4): 228-242. doi: 10.3934/mmc.2022022 |
[10] | Hongli Lyu, Yanan Lyu, Yongchao Gao, Heng Qian, Shan Du . MIMO fuzzy adaptive control systems based on fuzzy semi-tensor product. Mathematical Modelling and Control, 2023, 3(4): 316-330. doi: 10.3934/mmc.2023026 |
In this paper, the mechanism for the fault estimation (FE) problem for a hydraulic servo actuator (HSA) with sensor faults is investigated. To deal with the design issues, we transformed the nonlinear model of HSA into a new coordinate system to estimate the sensor faults. In the new coordinate system, the Lipschitz conditions and system uncertainties are also considered. Then, we implement a sliding mode observer (SMO) approach to introduce the transformation scheme to make the system rational. The proposed fault estimation scheme essentially transforms the original system into two subsystems where the first one includes system uncertainties, but is free from sensor faults and the second one has sensor faults but without uncertainties. The effects of system uncertainties on the estimation errors of states and faults are minimized by integrating an H∞ uncertainty attenuation level into the observer. The sufficient conditions for the state estimation error to be bounded and satisfy a prescribed H∞ performance are derived and expressed as a linear matrix inequality (LMI) optimization problem. Finally, the numerical example with simulation results is provided to validate the practicability and efficacy of the developed control strategy.
Important properties of the HSA, such as fast and accurate responses, high force/mass ratio, and relatively good stiffness, have attracted the great interest on the HSA and their applications. In the last two decades, high-performance controller design of the HSA has attracted increasing attention due to the expanded performance requirements of technical systems in industry [1,2,3].
Modern control systems are prone to faults, which can damage the systems themselves or the environments in which they operate. For this reason, fault detection and isolation (FDI) algotihms become essential, since they enable fault-tolerant actions that minimize the effect of faults and improve the overall system's reliability and safety. The research on FDI has received considerable attention during the last two decades due to the increasing demand for safety and reliability of automatic control systems [4,5]. Naturally, the nonlinear control problem for different dynamics systems is always a hot topic and has attracted compelling attention from scholars, see [6,7,8]. With the development of modern technology, autonomous systems are more and more dependent on sensors which often carry the most important information in automated/feedback control systems. Faults occurring in sensors may lead to poor regulation or tracking performance, or even affect the stability of the control system. On the other side, the stability analysis in dynamical systems has attracted widespread interests on both theoretical and practical fronts in recent years [9,10,11,12,13]. Therefore, the study of sensor fault diagnosis is becoming increasingly important.
The approaches of FDI developed in the past can be grouped into three fundamental categories: knowledge-based FDI methods, signal-based FDI and model-based FDI [14]. Among the possible approaches, the model-based FDI ones have been recognized as a handy tool by the scientific community and have been applied successfully to many physical systems, for example, lateral dynamics of a vehicle [15], aircraft [16], satellites [17], unmanned aerial vehicles (UAVs) [18], and wind turbines [19], among others. The basic idea of the observer-based FDI approaches, which fall into the category of model-based FDI, is to generally compare the actual system's behavior with the predicted or estimated behavior based on its mathematical model. Hence, the success of this type of technique directly relates to the mathematical model, which in reality is not a perfect representation. As a consequence, any discrepancies between the system and the model, which appear in the form of system uncertainties in the model, can cause a misleading alarm and make the FDI ineffective. Therefore, there is a need for a robust FDI which is sensitive to faults but insensitive to model uncertainties [20].
On the other side, fault estiamtion (FE) is different from the majority of fault detection and isolation (FDI) in the sense that it not only detects and isolates the fault, but also provides details of the fault, such as the location, size, and duration. Thus, it is especially useful for incipient faults and slow drifts, which are very difficult to detect. Also FE is vital in fault-tolerant control (FTC) systems which improve the system's performance. During the last two decades, considerable research results have been reported on sensor FE. In [21], an online estimation approach based on adaptive observer technique was adopted to reconstruct the sensor fault with an incipient time profile. A descriptor system approach was introduced to investigate sensor fault diagnosis for nonlinear systems in [22], which is applicable for sensor faults of any forms. Most physical systems are nonlinear, and therefore FDI should employ nonlinear algorithms, which are difficult to generalize and apply in many cases. It is well known that sliding mode techniques offer good potential for increasing the robustness of FDI by including a nonlinear discontinuous term that depends on the output estimation error into the observer [23,24]. During the last two decades, the research on sliding-mode observers (SMO)-based FE has received considerable attention. Several results have been reported on this topic [25,26,27,28].
In this paper, a sensor FE scheme is proposed for uncertain Lipschitz nonlinear systems. By applying coordinate transformations, we first transform the the original system into two subsystems (subsystem-1 and 2) where subsystem-1 includes the effects of system uncertainties but is free from sensor faults and subsystem-2 has sensor faults but without any uncertainties. Therefore, the FE can be carried out independently and is not affected in the presence of uncertainties. This offers a significant advantage over some of the existing methods. For example in [22,29,30] the effects of uncertainties on the estimation of faults can only be minimized. The proposed method extends the results of [31,32] in which actuator FE of linear systems was studied to sensor FE for uncertain Lipschitz nonlinear systems. Moreover, most of the existing FE methods such as those reported in [22,33,34] assume that the value of the Lipschitz constant Lf is known and they incorporate this knowledge to obtain feasible LMI solutions. However, determining the value of Lf of a nonlinear system is often difficult. Further, if the value of Lf exceeds the admissible value, those methods often fail to find feasible LMI solutions. In this paper, the value of Lf is assumed to be unknown and adaptation laws are integrated into the proposed schemes such that Lf does not appear in the LMI formulation and the feasibility of LMIs is not dependent on the knowledge of this parameter. Therefore, the proposed method offer distinct advantages over some of the existing methods.
The remainder of the paper is organized as follows: Section 2 briefly describe model of the hydraulic servo actuator. Section 3 describes the mathematical preliminaries required for developing the FDI method and design procedure of the implemented SMO. The results of the simulation are shown in Section 4 and conclusions are given in Section 5.
The HSA under study is shown in Fig. 1, which consists of the servo valve and the hydraulic cylinder. The analysis of the properties of the HSA comes out from dynamics of its components that involves the piston motion dynamics, pressure dynamics at the cylinder, and servo valve dynamics. Hence, the model of the HSA is derived from complex nonlinear equations that depend on many parameters which cannot be accurately obtained [35].
See Table 1 for the description of the HSA parameters. Using the notation in Figure 1, and defining the area ratio of the piston α=Ab/Aa, Va=Va0+yAa, Vb=Vb0+(L−y)αAa, qLi=cLi(pa−pb), where cLi is the internal leakage flow coefficient, cvi>0 are discharge coefficients, the sign function sg(x)={x,x≥00,x<0, and assuming an external leakage negligible, the considered model can be described by the following equations:
mt¨y=Aapa−Abpb−Ff(˙y)−Key−Fext, | (2.1) |
˙pa=βeVa(y)(qa−Aa˙y−qLi−qLea), | (2.2) |
˙pb=βeVb(y)(qb+αAa˙y+qLi−qLeb), | (2.3) |
qa=qsv1−qsv2=cv1sg(xv)sign(ps−pa)√|ps−pa|−cv2sg(−xv)sign(pa−p0)√|pa−p0|, | (2.4) |
qb=qsv3−qsv4=cv3sg(−xv)sign(ps−pb)√|ps−pb|−cv4sg(xv)sign(pb−p0)√|pb−p0|. | (2.5) |
Notations | Denotes |
xv | The spool valve displacement |
pa, pb | Forward and the return pressure |
qa, qb | Forward and the return flows |
y | Piston displacement |
L | Piston stroke |
Ke | Load spring gradient |
pS, p0 | Supply and tank pressure |
mt, mp, m | total mass, piston mass, payload mass |
Ff | Friction forces |
Fext | Disturbance forces |
Aa, Ab | Effective areas of the head and rod |
piston side | |
Va, Vb, Va0, Vb0 | Fluid volumes of the head and rod |
piston side and corresponding initial | |
volumes | |
qLi, qLe | Internal and external leakage flow |
βe | Bulk modulus of the fluid |
According to Eqs (2.1)-(2.5) and defining the state and input variables as
x(t)=[x1(t)x2(t)x3(t)x4(t)]T≜[y(t)˙y(t)pa(t)pb(t)]T, | (2.6) |
u(t)=xv(t), | (2.7) |
the governing nonlinear continuous-time dynamics of the HSA can be expressed in a state-space form as follows
˙x(t)=f(x(t))+g(x(t),u(t))+h(t),y(t)=η(x(t)), | (2.8) |
where f(x(t)) and g(x(t),u(t)) are the state dynamics and the input function, respectively
f(x(t))=[x21mt(Aax3−αAax4−Ff(x2)−Kex1)−βeAax1+Va0(Aax2+cLi(x3−x4))βeαAa(L−x1)+Vb0(αAax2+cLi(x3−x4))] | (2.9) |
g(x(t),u(t))=[00βeAax1+Va0(cv1sg(u)sign(ps−x3)√|ps−x3|−−cv4sg(−u)sign(x3−p0)√|x3−p0|)βeαAa(L−x1)+Vb0(cv3sg(−u)sign(ps−x4)⋅⋅√|ps−x4|−cv2sg(u)sign(x4−p0)√|x4−p0|)] | (2.10) |
and output function η(x(t))=x1(t), and disturbance function h(t)=[h1(t)−Fext/mt+h2(t)h3(t)h4(t)] includes loads, unmodelled dynamics and parameter uncertainties, fS(t) includes sensor faults.
Consider a non-linear system described by
˙x(t)=Ax(t)+Wf(x,t)+Bu(t)+EΔψ(t),y=Cx(t)+Dfs(t), | (3.1) |
where the state vector is x∈Rn, the input vector is u∈Rm, the output vector is y∈Rp, the sensor fault is denoted as fs∈Rq. The known constant matrices are A∈Rn×n, B∈Rn×m, C∈Rp×n, D∈Rp×q, E∈Rn×r (p≥q+r) and W∈Rn×j with D and E both being of full rank.
Remark 1. It should be noted that the system uncertainty under consideration is unstructured, which is more general than the type of structured uncertainty that has been considered for fault diagnosis of Lipschitz nonlinear systems in the literature [33,36]. In the case of structured system uncertainty, certain rank conditions of the uncertainty distribution matrix are assumed to be satisfied such that the fault can be completely decoupled from the uncertainty.
For the objective of achieving sensor fault diagnosis, the following assumptions and Lemmas are intoduced. The nonlinear term f(x,t)∈Rj is assumed to be known and Lipschitz about x uniformly ∀x,ˆx∈Rn
‖f(x,t)−f(ˆx,t)‖≤Lf‖x−ˆx‖ | (3.2) |
where Lf is the known Lipschitz constant.
The unknown nonlinear term Δψ(t) is structured modelling uncertainty, but bounded, and satisfies Δψ(t)≤ξ. Also, the unknown sensor fault and its derivative are norm bounded, i.e. fs(t)≤ρ and ˙f(t)≤ρs.
Lemma 3.1. Let's assume rank(CE)=rank(E). There exist linear transformations of coordinates
z=[z1z2]=Txandw=[w1w2]=Sy | (3.3) |
such that in the new coordinates, the system matrices become
TAT−1=[A1A2A3A4],TB=[B1B2],TE=[E10],SCT−1=[C100C4],SD=[0D2],TW=[W1W2] | (3.4) |
where T∈Rn×n, S∈Rp×p, T1∈Rr×n, S1∈Rr×p, z1∈Rr, w1∈Rr, A1∈Rr×r, A4∈R(n−r)×(n−r), B1∈Rr×m, E1∈Rr×r, W1∈Rr×j, C1∈Rr×r, C4∈R(p−r)×(n−r) and D2∈R(p−r)×q. C1 is invertible.
After introducing the state and output transformations (3.3), the original system is converted into two subsystems:
Subsystem1:{˙z1=A1z1+A2z2+W1f(T−1z,t)+B1u++E1Δψ(t)w1=C1z1 | (3.5) |
Subsystem2:{˙z2=A3z1+A4z2+W2f(T−1z,t)+B2uw2=C4z2+D2fs | (3.6) |
For Subsystem 1, we define a new state z3=t∫0w2(τ)dτ so that ˙z3=C4z2+D2fs. An augmented system with the new state z3 is therefore given as:
[˙z2˙z3]=[A40C40][z2z3]+[A30]z1+[W2f(T−1z,t)0]++[B20]u+[0D2]fs,w3=z3 | (3.7) |
Subsystem (3.5) can be rewriten as in a more compact form as
˙z1=A1z1+ˉA2z0+W1f(T−1z,t)+B1u+E1Δψ(t)w1=C1z1 | (3.8) |
where z0∈Rn+p−2r, ˉA2=[A20]∈Rr×(n+p−2r). Also, Subsystem (3.6) can be stated as
˙z0=A0z0+ˉA3z1+ˉW2f(T−1z,t)+B0u+D0fsw3=C0z0 | (3.9) |
in which w3∈Rp−r, A0=[A40C40]∈R(n+p−2r)×(n+p−2r), ˉA3=[A30]∈R(n+p−2r)×r, B0=[B20]∈R(n+p−2r)×m, D0=[0D2]∈R(n+p−2r)×q, C0=[0Ip−r]∈R(p−r)×(n+p−2r), ˉW2=[W20].
Lemma 3.2. [37,38] The pair (A0,C0) is detectable if and only if the minimum phase condition holds
rank[sIn−AEC0]=n+rank(E) | (3.10) |
for every complex number s with nonnegative real part.
Now, a scheme which consists of two SMOs to estimate sensor faults is develepod. One of the SMOs is designed for subsystem (3.8) to estimate sensor faults, while other one is designed for subsystem (3.9) to eliminate the effects of system uncertainties.
For subsystem (3.8), the proposed SMO has the following form:
˙ˆz1=A1ˆz1+ˉA2ˆz0+W1f(T−1ˆz,t)+B1u++12ˆk1P1C−11(w1−ˆw1)+(A1−As1)C−11(w1−ˆw1)+v1ˆw1=C1ˆz1 | (3.11) |
where As1∈Rr×r is a stable matrix which needs to be determined, P1 is the Lyapunov matrix of As1, ˆz:=[(C−11S1y)T([In−r0]ˆz0)T]T. The discontinuous output error injection term v1, which is used to eliminate the effects of uncertainties, is defined by
v1={(‖E1‖ξ+η1)P1(C−11w1−ˆz1)‖P1(C−11w1−ˆz1)‖,C−11w1−ˆz1≠00otherwise | (3.12) |
where η1 is a positive scalar to be determined. It should be noted that state z1 can be obtained by the measured output y as z1=C−11S1y. ˆk1 satisfies the following adaption law:
˙ˆk1=lk1‖P1(C−11w1−ˆz1)‖2, | (3.13) |
where lk1 is a positive constant. For subsystem (3.9), the proposed SMO has the following form:
˙ˆz0=A0ˆz0+ˉA3C−11w1+ˉW2f(T−1ˆz,t)+B0u++L0(w3−ˆw3)+12ˆk2ˉW2H0(w3−ˆw3)+D0v2ˆw3=C0ˆz0 | (3.14) |
where the observer gain L0=[L01L02]∈R(n+p−2r)×(p−r), in which L01∈R(n−r)×(p−r), H0∈Rj×(p−r), P0=PT0∈R(n+p−2r)×(n+p−2r). The discontinuous output error injection term v2 is defined by
v2={(ρs+η2)F0(w3−ˆw3)‖F0(w3−ˆw3)‖,w3−ˆw3≠00otherwise | (3.15) |
where F0∈Rq×(p−r) is a matrix to be determined and η2 is a positive scalar. ˆk2 satisfies the following adaption law:
˙ˆk2=lk2‖H0(w3−ˆw3)‖2, | (3.16) |
where lk1 is a positive constant.
We now present the following theorem which provides sufficient conditions for the existence of the proposed SMOs.
Theorem 3.3. Let's consider system (3.1) with introduced assumptions and lemmas. If there exist matrices As1, L0, F0, H0, P0=PT0>0, P1=PT1>0 such that
DT0P0=F0C0 | (3.17) |
ˉWT2P0=H0C0 | (3.18) |
[Π1P1ˉA2ˉAT2P1Π2+2In+p−2r]<0 | (3.19) |
where Π1=As1TP1+P1As1, Π2=(A0−L0C0)TP0+P0(A0−L0C0) then the error dynamics, after the occurrence of sensor faults
˙e1=As1e1ˉA2e0+W1(f(T−1z,t)−f(T−1ˆz,t))−12ˆk1P1e1+E1Δψ−v1 | (3.20) |
˙e0=(A0−L0C0)e0+ˉW2(f(T−1z,t)−f(T−1ˆz,t))−12ˆk2ˉW2H0C0e0+D0(fs−v2) | (3.21) |
are assymtoticaly stable, in which the state estimation errors are defined as e1=z1−ˆz1 and e0=z0−ˆz0. The Proof of Theorem 3.3 can be seen in [39].
In practice, it is often difficult to know precisely the value of the Lipschitz constant in (3.2). This parameter plays an important role in the design of observers for nonlinear systems. It should be noted that in [22,33,36,40] the Lipschitz constant Lf is assumed to be known and is one of the parameters in the LMI formulation. This can be considered as one of the limitations of those methods. We have observed that it often fails to solve LMI if the value of Lf is too large. In order to find a feasible solution of LMI, the value of Lf may be reduced by introducing coordinate transformations for certain structures of the Lipshcitz function [41]. However, this may bring in an extra difficulty in the design of observers. In contrast to some of the existing methods, the Lipschitz constant Lf in this paper is assumed to be unknown and adaptive SMOs are proposed to deal with this situation. Specifically, the Lipschitz constants Lf1 and Lf are injected into the constants k1 and k2 which can be adjusted by the adaptation laws (3.13) and (3.16). Note that the asymptotic estimation of states can be guaranteed even if the estimates of k1 and k2 do not approach to their actual values [39].
Theorem 3.3 has shown that the error dynamics (3.20) and (3.21) are asymptotically stable. The objective now is to choose constants η1 and η2 such that the error dynamics can be driven to the sliding surface in finite time and a sliding motion can be maintained on it thereafter. For error dynamics (3.20) and (3.21), we define the sliding-mode surface as
S={(e1,e0)|e1=0,C0e0=0} | (3.22) |
The problem of finding matrices As1, L0, F0, H0, P0=PT0>0, P1=PT1>0 to simultaneously satisfy the Inequality (3.19) and Equalities (3.17) and (3.18) can be transformed into the following LMI optimization problem:
Minimize γ1+γ2
subject to
P0>0, P1>0
and
[X+XTP1ˉA2ˉAT2P1P0A0+AT0P0−Y0C0−CT0YT0+2In+2p−r]<0 | (3.23) |
[γ1IqDT0P0−F0C0(DT0P0−F0C0)Tγ1In+p−2r]>0 | (3.24) |
[γ2IjˉWT2P0−H0C0(ˉWT2P0−H0C0)Tγ2In+p−2r]>0 | (3.25) |
where X=P1As1 and Y0=P0L0.
Theorem 3.4. Let's consider system (3.1) with introduced assumptions, lemmas and the proposed observers (3.11) and (3.14). Then the error dynamics (3.20) and (3.21) can be driven to the sliding surface (3.22) in finite time and remain on it if LMIs (3.23)-(3.25) are solvable and the gains η1 and η2 satisfy
η1≥(‖ˉA2‖Lf‖T−1‖‖W1‖)‖e0‖+η3, | (3.26) |
η2≥Lf‖T−1‖‖W2‖‖e0‖‖D0‖+η4, | (3.27) |
where η3 and η4 are positive scalars. The Proof of Theorem 3.4 can be seen in [39].
After reaching the sliding surface, the sliding motion will be maintained thereafter, i.e., C0e0=0. It follows from (3.21) that
0= C0A0e0+C0ˉW2(f(T−1z,t)−f(T−1ˆz,t))+D2(fs−v2eq) | (3.28) |
where v2eq is the equivalent output error injection signal representing the average behavior of the discontinuous function v2. Since limt→∞e0=0 according to Theorem 3.3, it also holds that limt→∞f(T−1z,t)−f(T−1ˆz,t)=0. From (3.28) it follows that the sensor fault can be approximated as
ˆfs=limt→∞fs=v2eq | (3.29) |
in which the equivalent output error injection signal v2eq can be obtained as
v2eq=(ρs+η2)F0ew3‖F0ew3‖+δ | (3.30) |
where δ is a small positive scalar to reduce the chattering effect.
Effectiveness of the sensor FE approach will be considered on HSA model with following parameters: the viscous friction BC=200Nsm, the supply pressure pS=45bar, the tank pressure p0=1.6bar, the bulk modulus of the fluid βe=2⋅108Pa, the total mass m=25kg, the initial chamber volumes Va0=Vb0=8.2⋅10−6m3, the load spring gradient Ke=10−1, the effective area of the head side of the piston Aa=4.91⋅10−4m2, the effective area of the rod side of the piston Ab=2.43⋅10−4m2, the internal leakage coefficient cLi=5⋅10−14, the piston stroke L=1m, discharge coefficients of valve orifices cvi=1.15, i=¯1,4.
It is assumed that there is an complex sensor fault composed of a combination of abrupt, ramp, and sine-type faults, which is represented as:
fs={0t<500.05sin(0.15πt)50≤t<90090≤t<1200.002(t−120)120≤t<1500.025+0.01sin(0.2πt)150≤t<1800180≤t≤200 | (4.1) |
For simulation purposes, we set the control input u(t) as sinus function sin(πt) and the system uncertainty Δψ(t) as
Δψ(t)=[0.1sin(0.2t)20.1sin(0.1t)20.2sin(t)20.3sin(t)2] | (4.2) |
The results of fault estimation are illustrated in Figure 2. This figure clearly demonstrate that the proposed observer is able to estimate the sensor faults successfully, irrespective of uncertainties in the system. In addition to gradual and slow faults, such as a ramp and sinusoidal faults, it should be noted that fs changes abruptly at time instants 150s and 180s, which indicates that the proposed observer has the ability to track abrupt faults.
Figure 3 shows the trajectories of the actual states and their estimates. It can be seen from the figures that the proposed observer can estimate the states accurately, before and after the occurrence of any fault.
It can be seen that despite the presence of system uncertainties and measurement noises, the tracking performances of states x and sensor fault fs have achieved an ideal performance.
In this paper, a new sensor FE scheme for uncertain Lipschitz nonlinear systems is developed. The proposed FE scheme essentially transforms the original system into two subsystems where the first one includes system uncertainties, but is free from sensor faults and the second one has sensor faults but without uncertainties. Using the integral observer based approach, sensor faults in the second subsystem are transformed into actuator faults. In the proposed scheme, two SMOs are designed. One of which is used to eliminate the effect of system uncertainties, while the other one is used to estimate sensor faults. Adaptation laws are integrated into the scheme to deal with the situation when the Lipschitz constant is unknown or too large. The observer design parameters can be obtained using LMI techniques in a systematic way. Effectiveness of the proposed FE scheme has been demonstrated considering the example of hydraulic servo actuator. Simulation results have shown that the proposed FE scheme is effective and feasible in the presence of system uncertainties. Future research may include extending the proposed methodology to a single link robotic arm with a revolute elastic joint.
This research has been supported by the Serbian Ministry of Education, Science and Technological Development under grant 451-03-68/2022-14/200108, and CNPq under grant 304032/2019-0.
The authors declare that there is no conflict of interest.
[1] | J. Vyas, B. Gopalsamy, H. Joshi, Electro-Hydraulic Actuation Systems: Design, Testing, Identification and Validation, 1st Eds., Singapore: Springer, 2019. https://doi.org/10.1007/978-981-13-2547-2 |
[2] | A. Vacca, G. Franzoni, Hydraulic Fluid Power: Fundamentals, Applications, and Circuit Design, 1st Eds., New Jersey: Wiley, 2021. https://doi.org/10.1002/9781119569145 |
[3] | N. Manring, Fluid Power Pumps and Motors: Analysis, Design and Control, 1st Eds., New York: McGraw-Hill Education, 2013. |
[4] |
J. Zhang, A. Swain, S. Nguang, Detection and isolation of incipient sensor faults for a class of uncertain nonlinear systems, IET Contr. Theory Appl., 6 (2012), 1870–1880. https://doi.org/10.1049/iet-cta.2011.0440 doi: 10.1049/iet-cta.2011.0440
![]() |
[5] |
P. Zhang, J. Zou, Observer-based fault diagnosis and self-restore control for systems with measurement delays, Asian J. Control, 14 (2012), 1717–1723. https://doi.org/10.1002/asjc.458 doi: 10.1002/asjc.458
![]() |
[6] |
D. Jayamaha, N. Lidula, A. Rajapakse, Wavelet-multi resolution analysis based ANN architecture for fault detection and localization in DC microgrids, IEEE Access, 3 (2019), 145371–145384. https://doi.org/10.1109/ACCESS.2019.2945397 doi: 10.1109/ACCESS.2019.2945397
![]() |
[7] |
Z. Wang, Y. Shen, X. Zhang, Actuator fault estimation for a class of nonlinear descriptor systems, Int. J. Syst. Sci., 45 (2014), 487–496. https://doi.org/10.1080/00207721.2012.724100 doi: 10.1080/00207721.2012.724100
![]() |
[8] |
J. Yang, Y. Guo, W. Zhao, Long short-term memory neural network based fault detection and isolation for electro-mechanical actuators, Neurocomputing, 360 (2019), 85–96. https://doi.org/10.1016/j.neucom.2019.06.029 doi: 10.1016/j.neucom.2019.06.029
![]() |
[9] |
X. Li, J. Shen, H. Akca, R. Rakkiyappan, LMI-based stability for singularly perturbed nonlinear impulsive differential systems with delays of small parameter, Appl. Math. Comput., 250 (2015), 798–804. https://doi.org/10.1016/j.amc.2014.10.113 doi: 10.1016/j.amc.2014.10.113
![]() |
[10] |
X. Lv and X. Li, Finite time stability and controller design for nonlinear impulsive sampled-data systems with applications, ISA T., 70 (2017), 30–36. https://doi.org/10.1016/j.isatra.2017.07.025 doi: 10.1016/j.isatra.2017.07.025
![]() |
[11] |
X. Zhang, X. Li, Input-to-state stability of non-linear systems with distributed-delayed impulses, IET Control Theory A., 11 (2017), 81–89. https://doi.org/10.1049/iet-cta.2016.0469 doi: 10.1049/iet-cta.2016.0469
![]() |
[12] |
H. Zhang, R. Ye, S. Liu, J. Cao, A. Alsaedi, X. Li, LMI-based approach to stability analysis for fractional-order neural networks with discrete and distributed delays, Int. J. Syst. Sci., 49 (2018), 537–545. https://doi.org/10.1080/00207721.2017.1412534 doi: 10.1080/00207721.2017.1412534
![]() |
[13] |
X. Li, X. Yang, S. Song, Lyapunov conditions for finite-time stability of time-varying time-delay systems, Automatica, 103 (2019), 135–140. https://doi.org/10.1016/j.automatica.2019.01.031 doi: 10.1016/j.automatica.2019.01.031
![]() |
[14] | F. Ferracuti, V. Artists, A. Monteriù, Algorithms for Fault Detection and Diagnosis, 1st Eds., Basel: MDPI, 2021. |
[15] |
S. Gómez-Peñate, G. Valencia-Palomo, F. R. López-Estrada, C. M. Astorga-Zaragoza, R. A. Osornio-Rios, I. Santos-Ruiz, Sensor fault diagnosis based on a sliding mode and unknown input observer for Takagi-Sugeno systems with uncertain premise variables, Asian J. Control, 21(1) (2019), 339–353. https://doi.org/10.1002/asjc.1913 doi: 10.1002/asjc.1913
![]() |
[16] |
D. Henry, J. Cieslak, A. Zolghadri, D. Efimov, H∞/ HLPV solutions for fault detection of aircraft actuator faults: Bridging the gap between theory and practice, Int. J. Robust Nonlin., 25 (2015), 649–672. https://doi.org/10.1002/rnc.3157 doi: 10.1002/rnc.3157
![]() |
[17] |
Q. Jia, W. Chen, Y. Zhang, X. Chen, Robust fault reconstruction via learning observers in linear parameter-varying systems subject to loss of actuator effectiveness, IET Control Theory A., 8 (2014), 42–50. https://doi.org/10.1049/iet-cta.2013.0417 doi: 10.1049/iet-cta.2013.0417
![]() |
[18] |
D. Rotondo, A. Cristofaro, T. Johansen, F. Nejjari, V. Puig, Robust fault and icing diagnosis in unmanned aerial vehicles using LPV interval observers, Int. J. Robust Nonlin., 29 (2019), 5456–5480. https://doi.org/10.1002/rnc.4381 doi: 10.1002/rnc.4381
![]() |
[19] | S. Li, H. Wang, A. Aitouche, N. Christov, Unknown input observer design for faults estimation using linear parameter varying model: application to wind turbine systems, Proceedings of the 7th International Conference on Systems and Control, (2018), 45–50. https://doi.org/10.1109/ICoSC.2018.8587778 |
[20] |
J. Zhang, A. Swain, S. Nguang, Robust sliding mode observer based fault estimation for certain class of uncertain nonlinear systems, Asian J. Control, 17 (2015), 1296–1309. https://doi.org/10.1002/asjc.987 doi: 10.1002/asjc.987
![]() |
[21] |
C. Bonivento, A. Isidoria, L. Marconia, A. Paolia, Implicitfault-tolerant control: application to induction motors, Automatica, 40 (2004), 355–371. https://doi.org/10.1016/j.automatica.2003.9.003 doi: 10.1016/j.automatica.2003.9.003
![]() |
[22] |
Z. Gao, S. Ding, Sensor fault reconstruction and sensor compensation for a class of nonlinear state-space systems via a descriptor system approach, IET Control Theory A., 1 (2007), 578–585. https://doi.org/10.1049/iet-cta:20050509 doi: 10.1049/iet-cta:20050509
![]() |
[23] |
C. Tan, C. Edwards, An LMI approach for designing sliding mode observers, Int. J. Control, 74 (2001), 1559–1568. https://doi.org/10.1080/00207170110081723 doi: 10.1080/00207170110081723
![]() |
[24] | V. Utkin, Sliding Modes in Control and Optimization, 1st Eds., Berlin: Springer Science & Business Media, 2013. |
[25] |
C. Tan, C. Edwards, Sliding mode observers for detection and reconstruction of sensor faults, Automatica, 38 (2002), 1815–1821. https://doi.org/10.1016/S0005-1098(02)00098-5 doi: 10.1016/S0005-1098(02)00098-5
![]() |
[26] |
B. Jiang, M. Staroswiecki, V. Cocquempot, Fault estimation in nonlinear uncertain systems using robust/slidingmode observers, IEE Proceedings-Control Theory and Applications, 151 (2004), 29–37. https://doi.org/10.1049/ip-cta:20040074 doi: 10.1049/ip-cta:20040074
![]() |
[27] |
I. Castillo, T. Edgar, B. Fernández, Robust model-based fault detection and isolation for nonlinear processes using sliding modes, Int. J. Robust Nonlin., 22 (2012), 89–104. https://doi.org/10.1002/rnc.1807 doi: 10.1002/rnc.1807
![]() |
[28] |
C. Edwards, S. Spurgeon, R. Patton, Sliding mode observers for fault detection and isolation, Automatica, 36 (2000), 541–553. https://doi.org/10.1016/S0005-1098(99)00177-6 doi: 10.1016/S0005-1098(99)00177-6
![]() |
[29] |
C. Tan, C. Edwards, A robust sensor fault tolerant control scheme implemented on a crane, Asian J. Control, 9 (2007), 340–344. https://doi.org/10.1111/j.1934-6093.1907.tb00420.x doi: 10.1111/j.1934-6093.1907.tb00420.x
![]() |
[30] |
H. Alwi, C. Edwards, C. Tan, Sliding mode estimation schemes for incipient sensor faults, Automatica, 45 (2009), 1679–1685. https://doi.org/10.1016/j.automatica.2009.02.031 doi: 10.1016/j.automatica.2009.02.031
![]() |
[31] | K. Zhang, B. Jiang, V. Cocquempot, Adaptive observer-based fast fault estimation, Int. J. Control Autom. Syst., 6 (2008), 320–326. |
[32] |
K. Zhang, B. Jiang, P. Shi, Fast fault estimation and accommodation for dynamical systems, IET Control Theory Appl., 3 (2009), 189–199. https://doi.org/10.1049/iet-cta:20070283 doi: 10.1049/iet-cta:20070283
![]() |
[33] |
X. Yan, C. Edwards, Nonlinear robust fault reconstruction and estimation using a sliding mode observer, Automatica, 43 (2007), 1605–1614. https://doi.org/10.1016/j.automatica.2007.02.008 doi: 10.1016/j.automatica.2007.02.008
![]() |
[34] |
B. Jiang, M. Staroswiecki, V. Cocquempot, Fault accommodation for nonlinear dynamic systems, IEEE T. Automat. Contr., 51 (2006), 1578–1583. https://doi.org/10.1109/TAC.2006.878732 doi: 10.1109/TAC.2006.878732
![]() |
[35] | M. Jelali, A. Kroll, Hydraulic Servo-systems: Modelling, Identification and Control, 1st Eds., London: Springer-Verlag, 2003. https://doi.org/10.1007/978-1-4471-0099-7 |
[36] |
R. Raoufi, H. Marquez, A. Zinober, H∞ sliding mode observer for uncertain nonlinear Lipschitz systems with fault estimation synthesis, Int. J. Robust Nonlin., 20 (2010), 1785–1801. https://doi.org/10.1002/rnc.1545 doi: 10.1002/rnc.1545
![]() |
[37] |
M. Corless, J. Tu, State and input estimation for a class of uncertain systems, Automatica, 34 (1998), 757–764. https://doi.org/10.1016/S0005-1098(98)00013-2 doi: 10.1016/S0005-1098(98)00013-2
![]() |
[38] | S. Hui, S. Zak, Observer design for system with unknown inputs, Int. J. Appl. Math. Comput. Sci, 15 (2005), 431–446. |
[39] | J. Zhang, A. Swain, S. Nguang, Robust Observer-Based Fault Diagnosis for Nonlinear Systems Using MATLAB®, 1st Eds., Cham: Springer, 2016. https://doi.org/10.1007/978-3-319-32324-4_1 |
[40] |
C. Gao, Q. Zhao, G. Duan, Robust actuator fault diagnosis scheme for satellite attitude control systems, J. Franklin I., 350 (2013), 2560–2580. https://doi.org/10.1016/j.jfranklin.2013.02.021 doi: 10.1016/j.jfranklin.2013.02.021
![]() |
[41] |
F. Zhu, Z. Han, A note on observers for lipschitz nonlinear systems, IEEE T. Automat. Contr., 47 (2002), 1751–1754. https://doi.org/10.1109/TAC.2002.803552 doi: 10.1109/TAC.2002.803552
![]() |
1. | Rupak Datta, Ramasamy Saravanakumar, Rajeeb Dey, Baby Bhattacharya, Further results on stability analysis of Takagi–Sugeno fuzzy time-delay systems via improved Lyapunov–Krasovskii functional, 2022, 7, 2473-6988, 16464, 10.3934/math.2022901 | |
2. | Xiaoxuan Pei, Kewen Li, Yongming Li, A survey of adaptive optimal control theory, 2022, 19, 1551-0018, 12058, 10.3934/mbe.2022561 | |
3. | Xiao-peng Han, Wuliji Hasi, Ying Guo, Yun-dong Zhang, Si-yu Lin, Fan Wang, Research and assessment of high sensitivity intensity modulation vector curvature sensor based on cascaded bamboo-joint microcavity structure, 2023, 222, 02632241, 113649, 10.1016/j.measurement.2023.113649 | |
4. | Alessio Dallabona, Mogens Blanke, Henrik C. Pedersen, Dimitrios Papageorgiou, Fault diagnosis and prognosis capabilities for wind turbine hydraulic pitch systems, 2025, 224, 08883270, 111941, 10.1016/j.ymssp.2024.111941 | |
5. | Ljubiša Dubonjić, Saša Prodanović, Vladimir Stojanović, Morato Menezes, PD controller design for a system of a valve controlled hydromotor, 2023, 2, 2812-9474, 53, 10.5937/engtoday2300012D | |
6. | Yi-Yi Zhu, Xuexi Zhang, Jie Tao, Renquan Lu, Asynchronous fault detection for hidden Markov jump systems with dynamic event-triggered mechanism, 2024, 112, 0924-090X, 6461, 10.1007/s11071-024-09401-5 | |
7. | Khalid M. Alsaif, Aiiad A. Albeshri, Maher A. Khemakhem, Fathy E. Eassa, Multimodal Large Language Model-Based Fault Detection and Diagnosis in Context of Industry 4.0, 2024, 13, 2079-9292, 4912, 10.3390/electronics13244912 | |
8. | Meng Li, Yong Chen, Meng Zhang, Tao Ding, Fuzzy-Sliding-Mode Strategy for Multi-Channel Nonlinear Delay System With Disturbance, 2025, 22, 1545-5955, 1791, 10.1109/TASE.2024.3370173 |
Notations | Denotes |
xv | The spool valve displacement |
pa, pb | Forward and the return pressure |
qa, qb | Forward and the return flows |
y | Piston displacement |
L | Piston stroke |
Ke | Load spring gradient |
pS, p0 | Supply and tank pressure |
mt, mp, m | total mass, piston mass, payload mass |
Ff | Friction forces |
Fext | Disturbance forces |
Aa, Ab | Effective areas of the head and rod |
piston side | |
Va, Vb, Va0, Vb0 | Fluid volumes of the head and rod |
piston side and corresponding initial | |
volumes | |
qLi, qLe | Internal and external leakage flow |
βe | Bulk modulus of the fluid |
Notations | Denotes |
xv | The spool valve displacement |
pa, pb | Forward and the return pressure |
qa, qb | Forward and the return flows |
y | Piston displacement |
L | Piston stroke |
Ke | Load spring gradient |
pS, p0 | Supply and tank pressure |
mt, mp, m | total mass, piston mass, payload mass |
Ff | Friction forces |
Fext | Disturbance forces |
Aa, Ab | Effective areas of the head and rod |
piston side | |
Va, Vb, Va0, Vb0 | Fluid volumes of the head and rod |
piston side and corresponding initial | |
volumes | |
qLi, qLe | Internal and external leakage flow |
βe | Bulk modulus of the fluid |