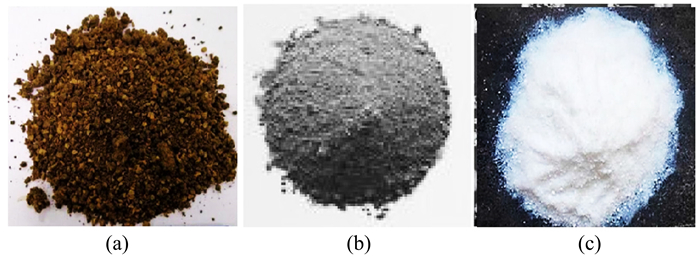
This study evaluates the utilization of biomass olive oil waste ash (OA) as a concrete paving material. Concrete pavement was produced by replacing a portion of Portland cement with OA at different percentages up to 15%. An additional set of concrete pavement was prepared by incorporating OA with nano-silica (NS) at various contents up to 1.5%. The optimal replacement contents of OA or OA and NS were investigated in terms of workability, compressive strength, strength development rate, and durability. The results showed that the optimal replacement level of OA content was 7.5%. The incorporation of NS with OA increased the optimal replacement level to 15%. The incorporation of NS with OA improved the strength, durability, and workability of all mixes. The utilization of OA with NS at optimal levels can produce concrete pavements. Using NS and OA, approximately 10 % cost savings could be achieved, together with a sustainable, environmentally friendly disposal method of olive oil waste.
Citation: Hashem Al-Mattarneh, Musab Abuaddous, Rabah Ismail, Ahmad B. Malkawi, Yaser Jaradat, Hamsa Nimer, Mohanad Khodier. Performance of concrete paving materials incorporating biomass olive oil waste ash and nano-silica[J]. AIMS Materials Science, 2024, 11(5): 1035-1055. doi: 10.3934/matersci.2024049
[1] | M. Kanta Rao, Ch. N. Satish Kumar . Influence of fly ash on hydration compounds of high-volume fly ash concrete. AIMS Materials Science, 2021, 8(2): 301-320. doi: 10.3934/matersci.2021020 |
[2] | Stelladriana Volpe, Andrea Petrella, Valentino Sangiorgio, Michele Notarnicola, Francesco Fiorito . Preparation and characterization of novel environmentally sustainable mortars based on magnesium potassium phosphate cement for additive manufacturing. AIMS Materials Science, 2021, 8(4): 640-658. doi: 10.3934/matersci.2021039 |
[3] | Mohamed Samy El-Feky, Passant Youssef, Ahmed Maher El-Tair, Sara Ibrahim, Mohamed Serag . Effect of nano silica addition on enhancing the performance of cement composites reinforced with nano cellulose fibers. AIMS Materials Science, 2019, 6(6): 864-883. doi: 10.3934/matersci.2019.6.864 |
[4] | Grzegorz Ludwik Golewski . Mechanical properties and brittleness of concrete made by combined fly ash, silica fume and nanosilica with ordinary Portland cement. AIMS Materials Science, 2023, 10(3): 390-404. doi: 10.3934/matersci.2023021 |
[5] | Erno Widayanto, Agoes Soehardjono, Wisnumurti Wisnumurti, Achfas Zacoeb . The effect of vibropressing compaction process on the compressive strength based concrete paving blocks. AIMS Materials Science, 2020, 7(3): 203-216. doi: 10.3934/matersci.2020.3.203 |
[6] | Jawad Ahmad, Osama Zaid, Muhammad Shahzaib, Muhammad Usman Abdullah, Asmat Ullah, Rahat Ullah . Mechanical properties of sustainable concrete modified by adding marble slurry as cement substitution. AIMS Materials Science, 2021, 8(3): 343-358. doi: 10.3934/matersci.2021022 |
[7] | Salmia Beddu, Mushtaq Ahmad, Daud Mohamad, Muhamed Imran bin Noorul Ameen, Zarina Itam, Nur Liyana Mohd Kamal, Nur Amalina Nadiah Basri . Utilization of fly ash cenosphere to study mechanical and thermal properties of lightweight concrete. AIMS Materials Science, 2020, 7(6): 911-925. doi: 10.3934/matersci.2020.6.911 |
[8] | Ahmed Ali Farhan Ogaili, Ehsan S. Al-Ameen, Mohammed Salman Kadhim, Muhanad Nazar Mustafa . Evaluation of mechanical and electrical properties of GFRP composite strengthened with hybrid nanomaterial fillers. AIMS Materials Science, 2020, 7(1): 93-102. doi: 10.3934/matersci.2020.1.93 |
[9] | Temitope Awolusi, Marc Azab, Oussama Accouche, Precious Ajayi, Emeka Nnochiri . Effect of binder-aggregate ratio and glass powder on the performance of concrete cured in different media. AIMS Materials Science, 2025, 12(1): 68-84. doi: 10.3934/matersci.2025006 |
[10] | Kong Fah Tee, Sayedali Mostofizadeh . Numerical and experimental investigation of concrete with various dosages of fly ash. AIMS Materials Science, 2021, 8(4): 587-607. doi: 10.3934/matersci.2021036 |
This study evaluates the utilization of biomass olive oil waste ash (OA) as a concrete paving material. Concrete pavement was produced by replacing a portion of Portland cement with OA at different percentages up to 15%. An additional set of concrete pavement was prepared by incorporating OA with nano-silica (NS) at various contents up to 1.5%. The optimal replacement contents of OA or OA and NS were investigated in terms of workability, compressive strength, strength development rate, and durability. The results showed that the optimal replacement level of OA content was 7.5%. The incorporation of NS with OA increased the optimal replacement level to 15%. The incorporation of NS with OA improved the strength, durability, and workability of all mixes. The utilization of OA with NS at optimal levels can produce concrete pavements. Using NS and OA, approximately 10 % cost savings could be achieved, together with a sustainable, environmentally friendly disposal method of olive oil waste.
Like many Mediterranean countries, such as Tunisia, France, Spain, and Turkey, Jordan has extensive olive tree farms that are solely committed to olive oil production. About 750 million olive trees exist in Mediterranean countries, and future growth in olive tree cultivation is anticipated due to the worldwide rising demand for olive oil [1]. Many olive mills existed in Jordan, especially in the northern part of the Irbid region. During the process of olive oil extraction, large amounts of by-products or waste are generated. This waste is divided into two categories: liquids (olive oil wastewater) and solids (pomace). Pomace is mainly composed of olive pulp, skin, and stones. The remainder of depleted pomace is known as "nocciolino", which is used as fuel for home heating in the winter due to its lower costs compared to petroleum-based products. Pomace can be used for other applications including animal feeding due to its high fiber contents [2], as compost to produce organic fertilizer [3], as a source of bioactive compounds for use in pharmaceutical and cosmetic industries [4], and as biofilter for toxic metal removal [5]. However, such applications still present disadvantages and limitations. For example, significant reduction in soil germination capacity, leaf necrosis, and increased phytotoxicity are known disadvantages of the use of pomace as soil fertilizer [6]. Also, pomace contamination with substances such as pesticides, heavy metals, or mycotoxins can pose health risks when used for animal feeding and cosmetic applications [7].
The demand for alternative fuels and renewable energy has increased, and the energy supply has diversified accordingly due to pressure on environment preservation and energy conservation. Biomass contributes significantly to the production of ash, necessitating management that respects the environment [8]. The use of additives to improve the strength and longevity of concrete has been studied by numerous researchers. Fly ash has been thoroughly investigated for its potential to enhance concrete performance. The successful integration of fly ash into concrete has the potential to yield substantial cost savings in the repair and rehabilitation of concrete structures and rigid asphalt pavements. Over 75, 000 tons of waste from olive oil extraction manufacturing are produced each year in Jordan [1]. These wastes, when burned as biofuel, yield a sizable amount of ash, which is normally dumped in sanitary landfills resulting in groundwater pollution and other environmental problems. Recycling this waste could help to reduce negative environmental effects. Furthermore, it could support long-term growth and contribute to the sustainable development of some construction materials, like concrete pavement [9]. To maximize the use of biomass resources as renewable alternatives to fossil fuels, proper management of ash is essential [1,7].
Transforming agricultural and industrial waste from a pollutant into a useful resource can significantly aid sustainable development. This waste can be recycled and used as a partial substitute for materials such as cement in construction industries [10,11,12]. However, using these materials in larger proportions often negatively impacts the strength and durability of the building materials [13,14,15]. The possible use of biomass olive oil waste ash (OA) in the manufacturing of Portland cement has been investigated in many studies [16,17,18]. These investigations revealed that adding up to 10% OA by weight of cement increased the Portland cement concrete mixtures' stability at high temperatures. However, unfavorable effects on strength and long-term durability were noted when OA was added to concrete pavement in percentages above 10% [19]. This restriction limits the amount of OA that can be recycled and used in concrete pavement [9]. A potential solution is to combine multiple materials to increase the recycling rates of this waste [20].
Recent studies have demonstrated that the use of nano-silica can enhance the strength and durability of concrete [21]. The use of nanoparticles results in a major change in the microstructure properties of the bulk product. The high surface areas and large numbers of sites introduced by the nanomaterials when used as additives are known to affect particle dispersion, formation of cementing products, kinetics, densification, porosity, and reducing grain growth [22]. The amount of nano-silica to be used in the concrete mixture can vary from 2% to 4% as a replacement for cement weight to improve the performance of the concrete [23]. Exceeding this suitable replacement range can weaken the enhancement effect on the mechanical properties [24]. The use of nano-additives results in improvements in rheological properties, mechanical strength, and temperature resistance of the structure [24,25]. The above advantages increase the durability of the structure built [26]. The particle size distribution of nanoparticles can substantially improve the integrity of micro and macrostructure. Moreover, it accelerates the cement hydration and promotes the pozzolanic reaction, which leads to the increment of the produced C-S-H gel [27].
Concrete is the most extensively used construction material in the world [28]. Concrete has numerous applications, including the rigid pavement that is used for the construction of highways and airport runways. Cement is the main binding material in concrete and its production is responsible for the production of a large percentage of CO2 emissions [28]. Many studies have investigated the enhancement of the environmental effect of concrete by reducing the amount of used cement. Fly ash from agricultural and industrial waste has been employed as a partial or full replacement material for cement. Applications included the production of self-consolidating concrete pavement [29,30], lightweight concrete using palm oil ash [31,32], and geopolymer concrete [33,34,35]. User-friendly software and artificial intelligence have been developed to predict and optimize the mix proportions of geopolymer concrete and self-compacting concrete incorporating byproduct waste ash [36,37,38]. Recently, studies have demonstrated the benefits of using industrial, agricultural, and olive waste ash to enhance construction materials such as asphalt pavement mixtures and concrete pavement [39,40,41]. Limited studies have evaluated the effect of OA on concrete properties. However, OA has been used to improve the properties of cement mortars [1,42], enhance the alkali-silica reaction in concrete [16], and enhance the fire performance of concrete pavement when it is exposed to extreme heat levels [43]. Additionally, olive pomace could replace traditional aggregates (e.g., sand or gravel) in concrete, reducing the demand for natural resources like river sand [44].
This study aims to investigate the use of olive oil ash to improve the performance of concrete pavement, offering a sustainable and environmentally friendly way to dispose of this toxic waste. This approach supports the circular economy, turning agricultural waste into a resource for construction, and reducing the environmental footprint of both industries. The effects of OA incorporation on concrete properties, including strength, durability, and workability, were investigated to determine the optimal replacement percentage. Moreover, this study investigates the use of nano-silica as a boosting agent to increase the percentage of OA utilization in concrete pavement. This approach could facilitate the recycling of larger quantities of industrial and agricultural waste, reduce their environmental impact, and reduce concrete pavement production costs and emissions. The combination of OA and nano-silica represents a novel composite material in concrete paving materials [9]. While both materials have been individually investigated in concrete, the use of their combination is an area that remains relatively unexplored. Nano-silica's contribution to improving water tightness and chemical resistance, along with olive pomace's potential for improving thermal performance, can lead to pavements that perform better in extreme climates or environments with high freeze-thaw cycles. This can result in concrete pavement with a longer lifespan and reduced life-cycle costs. This area is relatively unexplored and may provide additional opportunities for research and development in green construction materials. It can motivate future studies and innovations in using OA in construction.
The materials that were used to produce the concrete pavement were ordinary Portland cement type I, OA, nano-silica, and fine and coarse aggregate. The raw olive oil waste (pomace), OA, and nano-silica are shown in Figure 1. Raw pomace was collected from Alwasatiah in the North of Jordan, west of Irbid City. The source of raw pomace is presented in Figure 2. Special treatment of the raw pomace was required to transfer it into usable material, including incineration and milling. The incineration was applied by self-combustion in an oven that is usually used for home heating; the process lasted three hours until the solid waste was burnt and transformed into gray-colored ash. After incineration, some of the OA formed large particle sizes; therefore, it underwent ball milling for 2 h using steel balls of 5-10 mm size at a ball-to-ash weight ratio of 10 and then sieved using a #200 sieve. The specific gravity of OA was 2.06, and its size ranged from 1.0 to 20.0 µm. The smaller particle size of OA could make the ash more reactive due to the larger surface area and could also work as a better filler to bridge the smaller voids in concrete pavement. A larger surface area and smaller particle size of OA could aid in reacting with the available water and enhance the bond with the product of cement hydration in concrete pavement. This could lead to an improvement in concrete pavement strength and durability.
The characteristics of OA were evaluated using scanning electron microscopy (SEM) and X-ray diffractometer (XRD). The SEM micrographs of OA before and after implementing the ball milling techniques are presented in Figure 3a, b, respectively. The micrographs show that before milling, OA has irregular angular shapes with agglomerations of fine and coarse particles. After the milling process, the particles provided less angularity or curved shapes with lower agglomeration of particles. The XRD results of the milled OA are given in Figure 4. The XRD analysis shows the formation of various peaks pointing to the existence of crystalline phases in the treated OA. The primary phases were calcite, quartz, magnesium silicon phosphide, sylvite, and fluorapatite. A small deviation at 2θ angle from 27 to 45° is typical of amorphous compounds.
The chemical composition of the used cement, OA, and nano-silica was analyzed using X-ray Fluorescence (XRF) analysis and is given in Table 1. OA was composed of 20.10%, 30.21%, 30.0%, and 5.51% of SiO2, CaO, K2O, and MgO, respectively. The chemical percentages of SiO2, CaO, K2O, and MgO in cement were 21.98%, 65.95%, 0.63%, and 2.16%, respectively. These results show that the binding properties of OA are lower than those of cement because of low lime (CaO) content. The used nano-silica is solely composed of SiO2 (99%), with a highly dispersive white color powder appearance, and an average particle size from 10 to 25 nm. The used cement was the ordinary Portland cement type I that conforms to the ASTM C150/C150M [45] standards, with a specific gravity of 3.1.
Material | Chemical composition content (%) | ||||||||
SiO2 | Al2O3 | CaO | Fe2O3 | MgO | Na2O | K2O | P2O5 | Losses | |
Portland cement | 21.98 | 5.42 | 65.95 | 4.87 | 2.16 | 0.16 | 0.63 | 0.06 | 1.52 |
OA | 20.10 | 4.51 | 30.21 | 2.51 | 5.51 | 0.41 | 30.0 | 60 | 2.81 |
Natural river sand as fine aggregate and limestone as coarse aggregate were used in the preparation of the concrete pavement mixtures. The gradation of both fine and coarse aggregates meets the requirements of ASTM C33/C33M [46] for concrete aggregate. The details of physical properties and the gradation of aggregates are shown in Table 2 and Figure 5, respectively. The limestone coarse aggregate (maximum size of 20 mm) and river sand fine aggregate (maximum aggregate size of 5 mm) were incorporated into this concrete pavement mix. Tap drinking water was used for the mixing.
Properties | Natural river sand | Limestone aggregate |
Specific gravity | 2.45 | 2.81 |
Absorption | 1.43 | 0.73 |
Unit weight (kg/m3) | - | 93.31 |
Fineness modulus | 2.94 | - |
Seven concrete pavement material were prepared. The mix proportions of concrete mixes including cement, OA, fine aggregate (FA), coarse aggregate (CA), water and superplastisizer (SP) are given in Table 3. The water-to-cement ratio was kept at 0.50 for all mixes. Seven mixes were produced with different OA percentages replacing part of the cement. The replacement percentages of cement by OA ranged from 0.0% (control) to 15%. The details of these concrete mixes are given in Table 3.
Concrete mix | Cement (kg) | OA% (kg) | FA (kg) | CA (kg) | Water (L) | SP (L) |
M0-OA0.0 | 360 | 0.0 (0) | 722 | 1098 | 180 | 0.0 |
M1-OA2.5 | 351 | 2.5 (9) | 722 | 1098 | 180 | 0.0 |
M2-OA5.0 | 342 | 5.0 (18) | 722 | 1098 | 180 | 0.0 |
M3-OA7.5 | 333 | 7.5 (27) | 722 | 1098 | 180 | 0.0 |
M4-OA10.0 | 324 | 10.0 (36) | 722 | 1098 | 180 | 0.0 |
M5-OA12.5 | 315 | 12.5 (45) | 722 | 1098 | 180 | 0.0 |
M6-OA15.0 | 306 | 15.0 (54) | 722 | 1098 | 180 | 0.0 |
To increase the percentage of OA in concrete pavement and enhance the performance of concrete in strength and absorption, nano-silica (NS) was added at increasing percentages with increasing OA in the mix. To improve the workability of concrete, a 3-L superplasticizer was added to all mixes. Six concrete pavement mixes were prepared by incorporating OA and NS. The NS amount was calculated as a percentage of cement weight starting from 0% to 1.5% and was added as a replacement for some fine aggregate. The mix proportions of these mixes are presented in Table 4.
Portland cement | Cement (kg) | OA% (kg) | NS% (kg) | FA (kg) | CA (kg) | Water (L) | SP (L) |
MN0-OA0.0-NS0.00 | 360 | 0.0 (0) | 0.00 (0) | 722.0 | 1098 | 180 | 3.0 |
MN1-OA2.5-NS0.25 | 351 | 2.5 (9) | 0.25 (0.9) | 721.1 | 1098 | 180 | 3.0 |
MN2-OA5.0-NS0.50 | 342 | 5.0 (18) | 0.50 (1.8) | 720.2 | 1098 | 180 | 3.0 |
MN3-OA7.5-NS0.75 | 333 | 7.5 (27) | 0.75 (2.7) | 719.3 | 1098 | 180 | 3.0 |
MN4-OA10.0-NS1.00 | 324 | 10.0 (36) | 1.00 (3.6) | 718.4 | 1098 | 180 | 3.0 |
MN5-OA12.5-NS1.25 | 315 | 12.5 (45) | 1.25 (4.5) | 717.5 | 1098 | 180 | 3.0 |
MN6-OA15.0-NS1.50 | 306 | 15.0 (54) | 1.50 (5.4) | 716.6 | 1098 | 180 | 3.0 |
The concrete pavement mixtures were prepared using a 16-L Hobart mixer. Mixing procedures started by dry mixing the binding materials including Portland cement, OA, and nano-silica together for at least 2 min until a uniform blend was noted. Then, mixing water and superplasticizer (previously mixed) were added to the rotating mixer and mixed for an additional 2 min until a homogenous mixture was observed. Then, the coarse aggregate was added, followed by the fine aggregate, and mixed for an additional 3 min until a homogenous mixture was observed. The mixture was then poured into 15 cm cubes in three layers and vibrated using the vibration table. The cubes were de-molded after 24 h and cured in water until the day of testing.
The experimental program involved testing the fresh mixtures for workability using the slump cone test conforming to the BS, EN 12350-2 [47] standard procedures. The hardened concrete cubes were tested for their compressive strength at 3, 7, 21, and 28 days. The test was conducted using a universal testing machine of 3000 kN capacity conforming to the BS, EN 12390-3 [48] standard procedures. The results were calculated as an average of three cubes. The durability of concrete pavement mixtures was measured in terms of their absorption. The absorption test was conducted conforming to BS, EN 1881-122 [49] standard procedures. The test was conducted using 75 mm diameter core drilled specimens from 15 cm concrete cubes.
This section is divided into two parts. The first part presents the performance of concrete pavement incorporating OA only. The second part provides the performance of concrete pavement including OA and nano-silica.
The slump test was performed for all mixes with OA ranging from 0.0% to 15.0%. The slump of concrete pavement containing OA is shown in Figure 6. The findings show that when the amount of OA in fresh concrete increases, its slump and workability decrease. This could be related to OA's greater surface area and smaller size. Also, the angular shape of the OA particles is expected to reduce the workability of the mixture and increase the friction between constituents. Furthermore, the specific gravity of OA is lower than that of cement. A larger volume of OA will result from replacing cement by weight, which will cause the mix to use more water. When this slump lessens, the workability will be greatly diminished. A greater reduction in slump will result from the higher OA content. One could model the relationship between OA content and a slump as a linear relationship using Eq 1.
Slump=106−10.714(OA) | (1) |
Where OA represents the percentage of OA content. Figure 6 provides the values of the model parameters and correlation coefficients. The R2 was 0.9973, which suggests that the data fit well the linear regression model.
Figure 7 shows the results of compressive strength versus curing time at all OA content. The findings show that compressive strength increased as OA content increased up to 7.5%. As the OA content surpassed 7.5%, compressive strength declined. The same trend was noted for different curing times. According to the results, compressive strength increased to a higher value at 7.5% OA content. Because OA has a lower specific gravity and a larger volume than a similar weight of cement, it improves compressive strength. Furthermore, the OA particles are smaller, which may lower the effective water-to-cement ratio (w/c) in concrete containing OA. According to Abraham's laws, the most important factor influencing the strength of concrete pavement is the (w/c): a reduction in w/c can increase compressive strength. OA contains silica and alumina, which can act as pozzolanic materials. When combined with calcium hydroxide, which is considered a weak by-product of cement hydration, these pozzolans react to form additional calcium silicate hydrate (C-S-H), which is responsible for the strength of concrete. This increases the density and strength of the concrete over time. Also, due to its fine size, OA provides a filler effect similar to the microvoids within the concrete matrix. OA at 2.5%, 5.0%, and 7.5% improved the concrete pavement strength by 6.25%, 10.63%, and 13.13%, respectively. The strength of concrete pavement decreased with 10% of OA. The strength development of concrete pavement incorporating OA is presented in Figure 8. The figure shows that the utilization of OA did not provide significant effects on the strength development rate.
Regression analysis was used to establish the relationship between the compressive strength of concrete after 28 days of curing and the OA content in order to better visualize the effect of OA content on concrete pavement compressive strength. Figure 9 presents the findings. The quadratic formula in Eq 2 was the best model to fit the data.
Compressive strength=29.086+3.7595(OA)−0.5976(OA)2 | (2) |
Where OA is the OA content in percentage. The R2 = 0.8945 indicates the existence of a good correlation between the measured values.
Concrete absorption was used to gauge how durable the concrete was. Figure 10 shows the absorption of OA integrated into concrete. According to the data, concrete absorption decreased as OA content increased to 7.5%, at which point the trend reversed. This is a result of the fine OA particles' ability to fill in the pores and voids in the concrete, particularly in the interfacial zone. Additionally, OA lowers the effective w/c ratio, which lowers the concrete's pore structure. This leads to enhancing the durability of concrete. Olive oil ash at 2.5%, 5.0%, and 7.5% improved concrete pavement durability, measured by water absorption, by 3.95%, 11.84%, and 15.13%, respectively. The strength of concrete pavement decreased after 10% of olive waste ash. After 7.5% of OA, the absorption increased due to large voids produced by OA. This can be attributed to the reduced workability, which resulted in lower compaction of concrete.
Regression analysis was used to establish the relationship between the OA content and the absorption of concrete pavement in order to better visualize the effect of OA content on concrete absorption. The quadratic formula in Eq 3 was the model that best fit the data. Figure 10 provides R2 and model parameters. R2 = 0.7876 is the square correlation coefficient. The results show that the ideal replacement content to increase the durability of concrete is 7.5% of OWA.
Absorption=1.6486+−0.1632(OA)+0.0239(OA)2 | (3) |
Incorporating OA to improve concrete properties shows an optimum value in terms of strength and durability, after which degradation will be obtained. The optimum replacement content was 7.5%. Hence, we investigated if replacing a small part of fine aggregate with nano-silica would contribute to increasing the recycling rate of OA without negatively affecting the properties of concrete. Below are the results of adding nano-silica from 0.25% to 1.5% of cement.
The slump test was conducted for all mixes with OA content ranging from 0% to 15% and NS content from 0.25% to 1.5%. The slump of concrete pavement containing OA and NS is illustrated in Figure 11. The concrete slump decreased as the percentage of olive oil ash increased, and this decrease was further amplified by the addition of nano-silica. This was expected since nano-silica has a very high surface area and will require additional amounts of water to wet the surface of the particles. Consequently, a 3 L superplasticizer was added to all mixtures to compensate for the workability reduction. The results demonstrated that while the use of OA and nano-silica reduced the slump, the addition of the superplasticizer significantly improved it, achieving the required slump for concrete operation. The relationship between slump and OA content can be modeled by a linear relationship, represented by the formula in Eq 4.
Slump=Y=bo+b1(OA) | (4) |
Where b0 and b1 are the model parameters, and OA is the OA content in percentage. The model parameters and correlation coefficients are given in Figure 11. The R2 was 0.9918. This suggests that the data fit the linear regression model well.
The compressive strength of concrete pavement containing OA and nano-silica after 28 days is shown in Figures 12 and 13. The results show that a significant improvement in the strength of concrete was achieved when using nano-silica, which may be due to the small-sized nano-silica filling the voids in the concrete pavement and reducing the weak interfacial zone between the aggregate and cement paste in concrete. Nano-silica can also act as a filling material, leading to the refinement of the microstructure, improving the bond with aggregate, and providing the pozzolanic effect in reducing the weak calcium hydroxide products. This made it possible to obtain grade 30 MPa concrete pavement with an increase in OA up to 15%, which in turn increases the recycling rate of this waste, reduces the costs by replacing cement, and reduces carbon dioxide emissions resulting from cement manufacturing. Figure 13 shows the increase in strength development rate at higher nano-silica content. The presence of nano-silica accelerates the hydration process of cement. It acts as a nucleation site for the formation of hydration products. The increment in the hydration rate means the formation of more C-S-H in early stages, leading to faster strength gain. Moreover, the high surface area allows for a faster pozzolanic effect in which the calcium hydroxide is transferred to the additional stronger binder of C-S-H.
To understand the relationship between the strength of concrete pavement containing OA and nano-silica, statistical analysis shows that the relationship of the strength of concrete pavement can be represented by a quadratic relationship with a regression coefficient of 0.8169 at 28 days of curing and 0.6833 at 7 days of curing, which is a good representation of the relationship. Concrete strength's best improvement occurs at 7.5% OA; however, this improvement continues up to 15% and achieves a strength of grade 30 MPA concrete (see Figures 14 and 15). The quadratic regression model is presented by Eq 5.
Compressive strength=Y=bo+b1(OA)+b2(OA)2 | (5) |
Figure 16 shows the absorption of concrete with incorporated OA and nano-silica. According to the data, absorption decreased as OA content increased to 7.5%, at which point the trend reversed. This is a result of the ability of fine OA particles to fill in the pores and voids in the concrete, particularly in the interfacial zone. Additionally, OA lowers the effective w/c ratio, which lowers the concrete's pore structure and improves the concrete's durability. The addition of nano-silica increased absorption in all mixes. This is attributed to nano-silica filling porous voids, enhancing the interfacial zone, and further reducing the effective w/c ratio. This contributes to increasing concrete strength and density by reducing the porosity and limiting the penetration of water into concrete material. This will enhance the durability of concrete pavement.
A regression analysis was used to establish the relationship between the absorption of concrete pavement and the OA content in order to better visualize the effect of OA and NS content on concrete absorption. The quadratic formula, was the best model to fit the data based on regression analysis. The quadratic model is given by Eq 6. Figure 16 provides the R2 and model parameters; the model parameters denoted by b0, b1, and b2 are 1.7029, −0.02002, and 0.024, respectively. R2 = 0.909 is the square correlation coefficient. It is clear that if NS is utilized, 15% of OA can be recycled without compromising the durability and strength of the concrete.
Absorption=Y=bo+b1(OA)+b2(OA)2 | (6) |
The findings of this study support the viability of utilizing and recycling OA in the manufacturing of concrete pavement. Replacing cement with OA and nano-silica increases the strength and durability of concrete pavement for building construction materials. The findings can be summarized as follows:
• The ideal replacement of cement by OA in concrete pavement, in terms of strength and durability, is 7.5%. At this concentration, the strength and durability increased by 13.13% and 15.13%, respectively.
• OA content decreases the workability of concrete. This problem could be solved by the addition of a superplasticizer to achieve the same concrete slump.
• The incorporation of nano-silica with OA enables the duplication of the cement replacement level while maintaining durability and a concrete strength grade of 30 MPa. This makes it possible to reuse OA at a higher percentage, up to 15%.
• According to the results, savings of 10% and 15% in cost and CO2 emissions are expected.
• This study suggests that instead of disposing of OA in sanitary landfills, it can be recycled into concrete pavement, which offers several benefits. First, it reduces the amount of cement used, thereby
lowering both production costs and CO2 emissions. Second, replacing cement with agricultural waste creates a more sustainable construction material and results in more durable concrete pavement.
• Future research directions shall consider the effect of the OA treatment process such as combustion time, temperature, and milling duration to create a more reactive OA content. Also, other binding systems like geopolymerization or carbon dioxide curing should be investigated for possible OA increment.
The authors declare they have not used Artificial Intelligence (AI) tools in the creation of this article.
The researchers express gratitude for the support provided by the Research Deanship and the Faculty of Engineering at Yarmouk University.
All authors contributed equally to the manuscript. All authors wrote the manuscript, conducted the experimental testing, performed empirical models, reviewed the manuscript, and helped in the result analysis.
The authors declare no conflict of interest.
This research received no external funding.
The data presented in this study are available on request from the corresponding author.
[1] |
Jaradat Y, Matalkah F (2021) Olive biomass ash-based geopolymer composite: Development and characterisation. Adv Appl Ceram 120: 1–9. https://doi.org/10.1080/17436753.2020.1839848 doi: 10.1080/17436753.2020.1839848
![]() |
[2] |
Ribeiro TB, Campos D, Oliveira A, et al. (2021) Study of olive pomace antioxidant dietary fibre powder throughout gastrointestinal tract as multisource of phenolics, fatty acids and dietary fibre. Food Res Int 142: 110032. https://doi.org/10.1016/j.foodres.2020.110032 doi: 10.1016/j.foodres.2020.110032
![]() |
[3] |
Rueda MP, Domínguez-Vidal A, Llorent-Martínez EJ, et al. (2024) Monitoring organic matter transformation of olive oil production residues in a full-scale composting plant by fluorescence spectroscopy. Environ Technol Inno 35: 103695. https://doi.org/10.1016/j.eti.2024.103695 doi: 10.1016/j.eti.2024.103695
![]() |
[4] |
Tsoupras A, Panagopoulou E, Kyzas GZ (2024) Olive pomace bioactives for functional foods and cosmetics. AIMS Agric Food 9: 743–766. https://doi.org/10.3934/agrfood.2024040 doi: 10.3934/agrfood.2024040
![]() |
[5] |
Pachaiappan R, Cornejo-Ponce L, Rajendran R, et al. (2022) A review on biofiltration techniques: Recent advancements in the removal of volatile organic compounds and heavy metals in the treatment of polluted water. Bioengineered 13: 8432–8477. https://doi.org/10.1080/21655979.2022.2050538 doi: 10.1080/21655979.2022.2050538
![]() |
[6] |
Arvanitoyannis IS, Kassaveti A (2007) Current and potential uses of composted olive oil waste. Int J Food Sci Tech 42: 281–295. https://doi.org/10.1111/j.1365-2621.2006.01211.x doi: 10.1111/j.1365-2621.2006.01211.x
![]() |
[7] |
Keskes MA, Zouari A, Houssin R, et al. (2022) An overview on olive oil waste valorization scenarios: Life cycle approach. IFAC-Pap 55: 1477–1482. https://doi.org/10.1016/j.ifacol.2022.09.599 doi: 10.1016/j.ifacol.2022.09.599
![]() |
[8] |
Capablo J, Jensen PA, Pedersen KH, et al. (2009) Ash properties of alternative biomass. Energy Fuels 23: 1965–1976. https://doi.org/10.1021/ef8008426 doi: 10.1021/ef8008426
![]() |
[9] |
Alyami M, Hakeem IY, Amin M, et al. (2023) Effect of agricultural olive, rice husk and sugarcane leaf waste ashes on sustainable ultra-high-performance concrete. J Build Eng 72: 106689. https://doi.org/10.1016/j.jobe.2023.106689 doi: 10.1016/j.jobe.2023.106689
![]() |
[10] |
Ismail R, Dahim M, Jaradat A, et al. (2021) Field dielectric sensor for soil pollution application. IOP Conf Ser Earth Environ Sci 801: 012003. https://doi.org/10.1088/1755-1315/801/1/012003 doi: 10.1088/1755-1315/801/1/012003
![]() |
[11] |
Al-Mattarneh H, Dahim M (2021) Comparison of nondestructive testing method for strength prediction of asphalt concrete material. Civ Eng J 7: 165–178. https://doi.org/10.28991/cej-2021-03091645 doi: 10.28991/cej-2021-03091645
![]() |
[12] |
Rosario RD, Cruz ADL, Guzman MPD (2024) A review of biomineralization as solution for roads and infrastructures concrete sustainability. Civ Eng J 10: 2745–2760. http://dx.doi.org/10.28991/CEJ-2024-010-08-020 doi: 10.28991/CEJ-2024-010-08-020
![]() |
[13] |
Tayeh BA, Hadzima-Nyarko M, Zeyad AM, et al. (2021) Properties and durability of concrete with olive waste ash as a partial cement replacement. Adv Concr Constr 11: 59–71. https://doi.org/10.12989/acc.2021.11.1.059 doi: 10.12989/acc.2021.11.1.059
![]() |
[14] |
Malkawi AB, Nuruddin MF, Fauzi A. et al. (2017) Effect of plasticizers and water on properties of HCFA geopolymers. Key Eng Mater 733: 76–79. https://doi.org/10.4028/www.scientific.net/KEM.733.76 doi: 10.4028/www.scientific.net/KEM.733.76
![]() |
[15] | Nuruddin MF, Malkawi AB, Fauzi A, et al. (2016) Effects of alkaline solution on the microstructure of HCFA geopolymers, In: Wan Abdullah Zawawi NA, Engineering Challenges for Sustainable Future, London: CRC Press. |
[16] |
Alkheder S, Obaidat YT, Taamneh M (2016) Effect of olive waste (husk) on behavior of cement paste. Case Stud Constr Mat 5: 19–25. https://doi.org/10.1016/j.cscm.2016.05.001 doi: 10.1016/j.cscm.2016.05.001
![]() |
[17] |
Aras U, Kalaycıoğlu H, Yel H, et al. (2022) Utilization of olive mill solid waste in the manufacturing of cement-bonded particleboard. J Build Eng 49: 104055. https://doi.org/10.1016/j.jobe.2022.104055 doi: 10.1016/j.jobe.2022.104055
![]() |
[18] |
Mohamed AM, Tayeh BA, Aisheh YIA, et al. (2023) Utilising olive-stone biomass ash and examining its effect on green concrete: A review paper. J Mater Res Technol 24: 7091–7107. https://doi.org/10.1016/j.jmrt.2023.05.039 doi: 10.1016/j.jmrt.2023.05.039
![]() |
[19] |
Thomas BS, Yang J, Mo KH, et al. (2021) Biomass ashes from agricultural wastes as supplementary cementitious materials or aggregate replacement in cement/geopolymer concrete: A comprehensive review. J Build Eng 40: 102332. https://doi.org/10.1016/j.jobe.2021.102332 doi: 10.1016/j.jobe.2021.102332
![]() |
[20] |
Hakeem IY, Agwa IS, Tayeh BA, et al. (2022) Effect of using a combination of rice husk and olive waste ashes on high-strength concrete properties. Case Stud Constr Mat 17: 01486. https://doi.org/10.1016/j.cscm.2022.e01486 doi: 10.1016/j.cscm.2022.e01486
![]() |
[21] |
Wang C, Zhang P, Guo J (2023) Durability and microstructure of cementitious composites under the complex environment: Synergistic effects of nano-SiO2 and polyvinyl alcohol fiber. Constr Build Mater 400: 132621. https://doi.org/10.1016/j.conbuildmat.2023.132621 doi: 10.1016/j.conbuildmat.2023.132621
![]() |
[22] |
Zhang XH, Ahmad J, Jebur YM, et al. (2024) A review on partial substitution of nanosilica in concrete. Rev Adv Mater Sci 63: 20230157. https://doi.org/10.1515/rams-2023-0157 10.1515/rams-2023-0157 doi: 10.1515/rams-2023-015710.1515/rams-2023-0157
![]() |
[23] | Althoey F, Zaid O, Martínez-García R, et al. (2023) Impact of nano-silica on the hydration, strength, durability, and microstructural properties of concrete: A state-of-the-art review. Case Stud Constr Mat 18: e01997. https://doi.org/10.1016/j.cscm.e01997 |
[24] |
Sun Y, Zhang P, Guo J (2024) Rheological properties and workability of PVA fiber and nano-SiO2 modified cement-based materials. Dev Built Environ 18: 100396. https://doi.org/10.1016/j.dibe.2024.100396 doi: 10.1016/j.dibe.2024.100396
![]() |
[25] |
Zhang P, SunY, Wu J, et al. (2023) Mechanical properties and microstructure of nano-modified geopolymer concrete containing hybrid fibers after exposure to elevated temperature. Constr Build Mater 409: 134044. https://doi.org/10.1016/j.conbuildmat.2023.134044 doi: 10.1016/j.conbuildmat.2023.134044
![]() |
[26] |
Zhang X, Zhang P, Yuan W, et al. (2023) Durability prediction of geopolymer mortar reinforced with nanoparticles and PVA fiber using particle swarm optimized BP neural network. Nanotechnol Rev 13: 1. https://doi.org/10.1515/ntrev-2023-0214 doi: 10.1515/ntrev-2023-0214
![]() |
[27] |
Chen JJ, Ng PL, Xu L, et al. (2024) Use of nano-silica sol in concrete: Performance and influence mechanisms. Constr Build Mater 411: 134582. https://doi.org/10.1016/j.conbuildmat.2023.134582 doi: 10.1016/j.conbuildmat.2023.134582
![]() |
[28] |
Dahim M, Abuaddous M, Ismail R, et al. (2021) Using a dielectric capacitance cell to determine the dielectric properties of pure sand artificially contaminated with Pb, Cd, Fe, and Zn. Appl Environ Soil Sci 2021: 8838054. https://doi.org/10.1155/2020/8838054 doi: 10.1155/2020/8838054
![]() |
[29] |
Zain MFM, Karim MR, Islam MN, et al. (2015) Prediction of strength and slump of silica fume incorporated high-performance concrete. Asian J Sci Res 8: 264–277. https://doi.org/10.3923/ajsr.2015.264.277 doi: 10.3923/ajsr.2015.264.277
![]() |
[30] |
Mohammed BS, Nuruddin MF, Aswin M, et al. (2016) Structural behavior of reinforced self-compacted engineered cementitious composite beams. Adv Mater Sci Eng 2016: 1–12. https://doi.org/10.1155/2016/5615124 doi: 10.1155/2016/5615124
![]() |
[31] | Abdullahi M, Al-Mattarneh H, Mohammed B (2009) Equations for mix design of structural lightweight concrete. Eur J Sci Res 31: 132–141. |
[32] | Abdullahi M, Al-Mattarneh H, Mohammed B (2009) Statistical modeling of lightweight concrete mixtures. Eur J Sci Res. |
[33] | Malkawi AB, Habib M, Alzubi Y, et al. (2020) Engineering properties of lightweight geopolymer concrete using palm oil clinker aggregate. Int J Geomate 18: 132–139. https://geomatejournal.com/geomate/article/view/414 |
[34] |
Hanjitsuwan S, Chindaprasirt P, Pimraksa K (2011) Electrical conductivity and dielectric property of fly ash geopolymer pastes. Int J Miner Metall Mater 18: 94–99. https://doi.org/10.1007/s12613-011-0406-0 doi: 10.1007/s12613-011-0406-0
![]() |
[35] |
Nuruddin MF, Malkawi AB, Fauzi A, et al. (2016) Geopolymer concrete for structural use: Recent findings and limitations. IOP Conf Ser Mater Sci Eng 133: 012021. https://doi.org/10.1088/1757-899X/133/1/012021 doi: 10.1088/1757-899X/133/1/012021
![]() |
[36] |
Cabrera M, Martinez-Echevarria MJ, López-Alonso M, et al. (2021) Self-compacting recycled concrete using biomass bottom ash. Materials 14: 6084. https://doi.org/10.3390/ma14206084 doi: 10.3390/ma14206084
![]() |
[37] |
Mahameid AA, Yasin AA, Malkawi AB (2024) Prediction of the compressive and tensile strengths of geopolymer concrete using artificial neural networks. Civ Eng Archit 12: 3193–3206. https://doi.org/10.13189/cea.2024.120506 doi: 10.13189/cea.2024.120506
![]() |
[38] |
Rojo-López G, Nunes S, González-Fonteboa B, et al. (2020) Fernando Martínez-Abella, Quaternary blends of portland cement, metakaolin, biomass ash and granite powder for production of self-compacting concrete. J Clean Prod 266: 121666. https://doi.org/10.1016/j.jclepro.2020.121666 doi: 10.1016/j.jclepro.2020.121666
![]() |
[39] |
Abuaddous M, Dahim M, Ismail R, et al. (2021) Sustainable asphalt concrete for road construction and building material. IOP Conf Ser Earth Environ Sci 801: 012023. https://doi.org/10.1088/1755-1315/801/1/012023 doi: 10.1088/1755-1315/801/1/012023
![]() |
[40] |
Woszuk A, Bandura L, Franus W (2019) Fly ash as low cost and environmentally friendly filler and its effect on the properties of mix asphalt. J Clean Prod 235: 493–502. https://doi.org/10.1016/j.jclepro.2019.06.353 doi: 10.1016/j.jclepro.2019.06.353
![]() |
[41] |
Dahim M, Abuaddous M, Al-Mattarneh H, et al. (2021) Enhancement of road pavement material using conventional and nano-crude oil fly ash. Appl Nanosci 11: 2517–2524. https://doi.org/10.1007/s13204-021-02103-z doi: 10.1007/s13204-021-02103-z
![]() |
[42] |
El Boukhari M, Merroun O, Maalouf C, et al. (2023) Mechanical performance of cement mortar with olive pomace aggregates and olive mill wastewater: An experimental investigation. Cogent Eng 10: 2212522. https://doi.org/10.1080/23311916.2023.2212522 doi: 10.1080/23311916.2023.2212522
![]() |
[43] |
Lila K, Belaadi S, Solimando R, et al. (2020) Valorisation of organic waste: Use of olive kernels and pomace for cement manufacture. J Clean Prod 277: 123703. https://doi.org/10.1016/j.jclepro.2020.123703 doi: 10.1016/j.jclepro.2020.123703
![]() |
[44] | Antoun M, Issa CA, Aouad G, et al. (2021) Sustainable masonry blocks: Olive wood waste as substitute for fine aggregates. Case Stud Constr Mat 15: e00590. https://doi.org/10.1016/j.cscm.2021.e00590 |
[45] | ASTM International (2012) Standard Specification for Portland Cement, West Conshohocken, PA, ASTM C150-07. |
[46] | ASTM International (2016) Standard Specification for Concrete Aggregates, West Conshohocken, PA, ASTM C33/C33M-16e1. |
[47] | British Standards Institution (2000) Testing fresh concrete—Part 2: Slump test. |
[48] | British Standards Institution (2019) Testing hardened concrete—Part 3: Compressive strength of test specimens. |
[49] | British Standards Institution (2020) Testing concrete—Method for determination of water absorption. |
1. | Alaa A. Mahmoud, Alaa A. El-Sayed, Ayman M. Aboraya, Islam N. Fathy, Mohamed A. Abouelnour, Maged E. Elfakharany, Mohy S. Fattouh, Abdelmoniem E. Alahmer, Islam M. Nabil, Influence of elevated temperature exposure on the residual compressive strength and radiation shielding efficiency of ordinary concrete incorporating granodiorite and ceramic powders, 2025, 15, 2045-2322, 10.1038/s41598-024-85043-2 | |
2. | Hashem Al-Mattarneh, Rabah Ismail, Adnan Rawashdeh, Hamsa Nimer, Mohanad Khodier, Randa Hatamleh, Dua'a Telfah, Yaser Jaradat, Development of new dielectric models for soil moisture content using mixture theory, empirical methods, and artificial neural network, 2025, 12, 2372-0352, 137, 10.3934/environsci.2025007 | |
3. | Hashem Al-Mattarneh, Rabah Ismail, Issam Trrad, Hamsa Nimer, Mohanad Khodier, Yaser Jaradat, Ahmad B. Malkawi, Bashar S. Mohammed, Using artificial neural networks and electromagnetic capacitive NDT sensors for wood engineering application, 2025, 21, 1687-4048, 211, 10.1080/16874048.2025.2471122 |
Material | Chemical composition content (%) | ||||||||
SiO2 | Al2O3 | CaO | Fe2O3 | MgO | Na2O | K2O | P2O5 | Losses | |
Portland cement | 21.98 | 5.42 | 65.95 | 4.87 | 2.16 | 0.16 | 0.63 | 0.06 | 1.52 |
OA | 20.10 | 4.51 | 30.21 | 2.51 | 5.51 | 0.41 | 30.0 | 60 | 2.81 |
Properties | Natural river sand | Limestone aggregate |
Specific gravity | 2.45 | 2.81 |
Absorption | 1.43 | 0.73 |
Unit weight (kg/m3) | - | 93.31 |
Fineness modulus | 2.94 | - |
Concrete mix | Cement (kg) | OA% (kg) | FA (kg) | CA (kg) | Water (L) | SP (L) |
M0-OA0.0 | 360 | 0.0 (0) | 722 | 1098 | 180 | 0.0 |
M1-OA2.5 | 351 | 2.5 (9) | 722 | 1098 | 180 | 0.0 |
M2-OA5.0 | 342 | 5.0 (18) | 722 | 1098 | 180 | 0.0 |
M3-OA7.5 | 333 | 7.5 (27) | 722 | 1098 | 180 | 0.0 |
M4-OA10.0 | 324 | 10.0 (36) | 722 | 1098 | 180 | 0.0 |
M5-OA12.5 | 315 | 12.5 (45) | 722 | 1098 | 180 | 0.0 |
M6-OA15.0 | 306 | 15.0 (54) | 722 | 1098 | 180 | 0.0 |
Portland cement | Cement (kg) | OA% (kg) | NS% (kg) | FA (kg) | CA (kg) | Water (L) | SP (L) |
MN0-OA0.0-NS0.00 | 360 | 0.0 (0) | 0.00 (0) | 722.0 | 1098 | 180 | 3.0 |
MN1-OA2.5-NS0.25 | 351 | 2.5 (9) | 0.25 (0.9) | 721.1 | 1098 | 180 | 3.0 |
MN2-OA5.0-NS0.50 | 342 | 5.0 (18) | 0.50 (1.8) | 720.2 | 1098 | 180 | 3.0 |
MN3-OA7.5-NS0.75 | 333 | 7.5 (27) | 0.75 (2.7) | 719.3 | 1098 | 180 | 3.0 |
MN4-OA10.0-NS1.00 | 324 | 10.0 (36) | 1.00 (3.6) | 718.4 | 1098 | 180 | 3.0 |
MN5-OA12.5-NS1.25 | 315 | 12.5 (45) | 1.25 (4.5) | 717.5 | 1098 | 180 | 3.0 |
MN6-OA15.0-NS1.50 | 306 | 15.0 (54) | 1.50 (5.4) | 716.6 | 1098 | 180 | 3.0 |
Material | Chemical composition content (%) | ||||||||
SiO2 | Al2O3 | CaO | Fe2O3 | MgO | Na2O | K2O | P2O5 | Losses | |
Portland cement | 21.98 | 5.42 | 65.95 | 4.87 | 2.16 | 0.16 | 0.63 | 0.06 | 1.52 |
OA | 20.10 | 4.51 | 30.21 | 2.51 | 5.51 | 0.41 | 30.0 | 60 | 2.81 |
Properties | Natural river sand | Limestone aggregate |
Specific gravity | 2.45 | 2.81 |
Absorption | 1.43 | 0.73 |
Unit weight (kg/m3) | - | 93.31 |
Fineness modulus | 2.94 | - |
Concrete mix | Cement (kg) | OA% (kg) | FA (kg) | CA (kg) | Water (L) | SP (L) |
M0-OA0.0 | 360 | 0.0 (0) | 722 | 1098 | 180 | 0.0 |
M1-OA2.5 | 351 | 2.5 (9) | 722 | 1098 | 180 | 0.0 |
M2-OA5.0 | 342 | 5.0 (18) | 722 | 1098 | 180 | 0.0 |
M3-OA7.5 | 333 | 7.5 (27) | 722 | 1098 | 180 | 0.0 |
M4-OA10.0 | 324 | 10.0 (36) | 722 | 1098 | 180 | 0.0 |
M5-OA12.5 | 315 | 12.5 (45) | 722 | 1098 | 180 | 0.0 |
M6-OA15.0 | 306 | 15.0 (54) | 722 | 1098 | 180 | 0.0 |
Portland cement | Cement (kg) | OA% (kg) | NS% (kg) | FA (kg) | CA (kg) | Water (L) | SP (L) |
MN0-OA0.0-NS0.00 | 360 | 0.0 (0) | 0.00 (0) | 722.0 | 1098 | 180 | 3.0 |
MN1-OA2.5-NS0.25 | 351 | 2.5 (9) | 0.25 (0.9) | 721.1 | 1098 | 180 | 3.0 |
MN2-OA5.0-NS0.50 | 342 | 5.0 (18) | 0.50 (1.8) | 720.2 | 1098 | 180 | 3.0 |
MN3-OA7.5-NS0.75 | 333 | 7.5 (27) | 0.75 (2.7) | 719.3 | 1098 | 180 | 3.0 |
MN4-OA10.0-NS1.00 | 324 | 10.0 (36) | 1.00 (3.6) | 718.4 | 1098 | 180 | 3.0 |
MN5-OA12.5-NS1.25 | 315 | 12.5 (45) | 1.25 (4.5) | 717.5 | 1098 | 180 | 3.0 |
MN6-OA15.0-NS1.50 | 306 | 15.0 (54) | 1.50 (5.4) | 716.6 | 1098 | 180 | 3.0 |