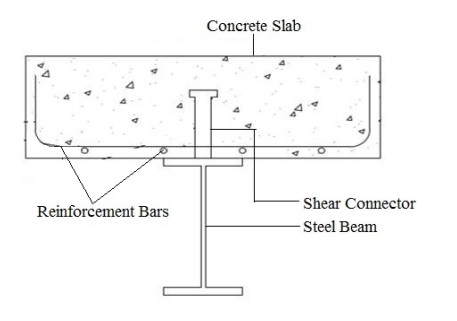
This paper focuses on the investigation of the flexural behaviour of steel-concrete composite beams through non-linear finite element analysis. Both geometries, as well as material non-linearity, are considered. Steel-concrete composite beams are typically made consisting of a hot-rolled I-section steel beam and a concrete slab that is connected monolithically by using a shear connector. A shear connector is one of the key elements for developing the composite action used in steel-concrete composite structures. This paper deals with the flexible shear connectors such as studs and channels designed as per the Indian standards 11384. Initially, the FE models are validated by making comparisons with the experimental test results obtained by previous researchers, as available in the literature. In the present study, thirty three-dimensional simply supported composite beams are created and analysed using finite element commercial software package ANSYS15 workbench version subjected to two-point loads. The degree of shear connection, the strength of steel section and the geometry of stud and channel connectors are the primary parameters considered for the present research work, and the results are compared. The overall flexural response is provided, including failure modes, load-central deformation behaviour, and interface slip, as well as the effects of yield strength of steel, the geometry of the stud and channel shear connector along with the degree of shear interaction, are evaluated. The results show that the degree of interaction, the geometry of shear connectors and steel yield strength have significant influence. Subjected to flexure, steel-concrete composite beam section with channel connector is less evaluated so far; therefore, in the present research work, channel shear connector is taken into account to evaluate the flexural behaviour with the consideration of varying grades of steel section along with the degree of interaction and to compare the results with a different section of shear connectors.
Citation: Sougata Chattopadhyay, Umamaheswari N. Numerical investigation of steel-concrete composite beams using flexible shear connectors[J]. AIMS Materials Science, 2022, 9(5): 668-683. doi: 10.3934/matersci.2022041
[1] | Ayad Ramadan . Shear crack control for a reinforced concrete T-beam using coupled stochastic-multi-objective optimization methods. AIMS Materials Science, 2023, 10(6): 1077-1089. doi: 10.3934/matersci.2023057 |
[2] | G. Sri Harsha, P. Poluraju, Veerendrakumar C. Khed . Computation of shear strength equation for shear deformation of reinforced concrete deep beams using finite element method. AIMS Materials Science, 2021, 8(1): 42-61. doi: 10.3934/matersci.2021004 |
[3] | Marcílio M. A. Filho, Paulo A. G. Piloto, Carlos Balsa . The load-bearing of composite slabs with steel deck under natural fires. AIMS Materials Science, 2022, 9(1): 150-171. doi: 10.3934/matersci.2022010 |
[4] | Phromphat Thansirichaisree, Hisham Mohamad, Mingliang Zhou, Ali Ejaz, Panumas Saingam, Qudeer Hussain, Suniti Suparp . Behavior of shallow concrete beams strengthened using low-cost GCSM and mechanical anchors. AIMS Materials Science, 2024, 11(5): 858-881. doi: 10.3934/matersci.2024042 |
[5] | Abdul Saboor Karzad, Moussa Leblouba, Zaid A. Al-Sadoon, Mohamed Maalej, Salah Altoubat . Modeling the flexural strength of steel fibre reinforced concrete. AIMS Materials Science, 2023, 10(1): 86-111. doi: 10.3934/matersci.2023006 |
[6] | Alexandre Lavrov, Kamila Gawel, Malin Torsæter . Manipulating cement-steel interface by means of electric field: Experiment and potential applications. AIMS Materials Science, 2016, 3(3): 1199-1207. doi: 10.3934/matersci.2016.3.1199 |
[7] | Igor A Chaves, Robert E Melchers, Barbara Jardim do Nascimento, Jordan Philips, Mark Masia . Effects of inter-cavity corrosion on metallic wall ties in masonry structures. AIMS Materials Science, 2022, 9(2): 311-324. doi: 10.3934/matersci.2022019 |
[8] | M.A.R. Loja, André Carvalho, Ines C.J. Barbosa . A study on the static behavior of functionally graded I-shaped beams. AIMS Materials Science, 2024, 11(1): 28-57. doi: 10.3934/matersci.2024002 |
[9] | Pedro Folhento, Manuel Braz-César, Rui Barros . Cyclic response of a reinforced concrete frame: Comparison of experimental results with different hysteretic models. AIMS Materials Science, 2021, 8(6): 917-931. doi: 10.3934/matersci.2021056 |
[10] | Kong Fah Tee, Sayedali Mostofizadeh . Numerical and experimental investigation of concrete with various dosages of fly ash. AIMS Materials Science, 2021, 8(4): 587-607. doi: 10.3934/matersci.2021036 |
This paper focuses on the investigation of the flexural behaviour of steel-concrete composite beams through non-linear finite element analysis. Both geometries, as well as material non-linearity, are considered. Steel-concrete composite beams are typically made consisting of a hot-rolled I-section steel beam and a concrete slab that is connected monolithically by using a shear connector. A shear connector is one of the key elements for developing the composite action used in steel-concrete composite structures. This paper deals with the flexible shear connectors such as studs and channels designed as per the Indian standards 11384. Initially, the FE models are validated by making comparisons with the experimental test results obtained by previous researchers, as available in the literature. In the present study, thirty three-dimensional simply supported composite beams are created and analysed using finite element commercial software package ANSYS15 workbench version subjected to two-point loads. The degree of shear connection, the strength of steel section and the geometry of stud and channel connectors are the primary parameters considered for the present research work, and the results are compared. The overall flexural response is provided, including failure modes, load-central deformation behaviour, and interface slip, as well as the effects of yield strength of steel, the geometry of the stud and channel shear connector along with the degree of shear interaction, are evaluated. The results show that the degree of interaction, the geometry of shear connectors and steel yield strength have significant influence. Subjected to flexure, steel-concrete composite beam section with channel connector is less evaluated so far; therefore, in the present research work, channel shear connector is taken into account to evaluate the flexural behaviour with the consideration of varying grades of steel section along with the degree of interaction and to compare the results with a different section of shear connectors.
In the recent era, the steel-concrete composite structure is gaining its popularity day by day for several advantages like space requirements, speed of construction etc. Generally, composite means two or more material elements act as a single unit. Steel-concrete composite is the typical combination of the two different materials, such as steel and concrete, monolithically connected by a shear connector, as shown in Figure 1. A shear connector is one of the metal components that is commonly used to connect a steel beam to a concrete slab to transfer the horizontal shear and too used to achieve composite action between two dissimilar materials in composite construction. Besides this, slippage can be reduced, and the strength and stiffness of the member can be enhanced with the use of a shear connector in a composite structure. Commonly two types of shear connectors are available in the market such as rigid and flexible shear connectors. Flexible shear connectors have shown some beneficial effects compared to the rigid types in the practical fields. Researchers show flexible connectors are usually more ductile in nature than rigid connectors [1]. Stud and channel are common examples of flexible shear connectors. Stud is one of the most commonly used types of shear connector, which can be easily available in the market and easily installed in the composite structure using a stud gun. Channel connector has shown some more benefits in the steel-concrete composite structure construction when compared to stud. The major advantages are the load-carrying capacity of channel connectors is more compared to stud. Thus, a smaller number of channels can replace [2] large units of stud connectors. As a result, the economy can be maintained by using channels as shear connectors.
Apart from this, shear connectors can establish the composite action, which is one of the key factors considered in composite constructions. Composite interaction [3,4] can be divided into three categories full, partial and no interaction between the two different materials. Full interaction can be considered when the provided shear connectors and required numbers are the same as per design consideration. A partial shear connection can be regarded when the provided numbers of the shear connector are lesser than the required numbers to achieve economy. But in the case of no interaction, two or more different materials act separately by their own corresponding properties and behaviour. Thus, the degree of interaction is playing a vital role in composite construction. The partial shear connection has a beneficial effect on the steel-concrete composite structures [4]. Bridges and multistoried commercial buildings are the major areas of application of steel-concrete composite structures. Even in terms of structural performance, composite construction can be used in the hilly region [5].
Performance of stud and channel shear connectors in a steel-concrete composite beam subjected to push-out test are available in the literature, but the flexural behaviour of steel-concrete composite beam connected with stud connector with the consideration of the degree of interaction and variation of steel grades is limited in the literature. In the present paper, initially, FE models are created and validated by making comparisons with the experimental test results obtained by previous researchers, as available in the literature. Furthermore, the flexural performance of steel-concrete composite beams with variable degrees of shear connection and steel strength is evaluated using two common flexible shear connectors (stud and channel) with different geometrical features constructed according to Indian standard IS 11384 [6].
The main objective of the current study is to investigate the flexural performance of steel-concrete composite beam subjected to four-point bending using non-linear finite element analysis with ANSYS15, with the consideration of varying geometry of stud and channel shear connectors and degree of composite action, different grades of steel beam section.
The commercial finite element software ANSYS15 is used to create three-dimensional finite element models. To assess the models' reliability, the FE models are initially validated against test results available in the literature and furthermore to create numerical models without error. This section deals with the calibration of the FE model, element types, contact behaviour and solution approach.
FE model is created by using ANSYS workbench static structural criteria. Element types and meshing patterns are usually important criteria to solve the numerical analysis without any kind of errors. Eight nodes SOLID65 element is considered for the concrete slab, which has three degrees of freedom on each node along with the capabilities of plastic deformation, cracking and crushing in tension and compression zone, respectively. A graphical presentation of the element of SOLID65 is given in Figure 2a. The brick element SOLID185, which also has eight nodes and three degrees of freedom on each node, depicts the steel beam section along with loading and support plates since it can carry plasticity, large deflection, creep and large strain, as shown in Figure 2b. Besides these elements, BEAM188 (shown in Figure 2c) and four noded element SHELL181, which has six degrees of freedom on each node, are chosen to create the model of the shear connector and reinforcement bars due to the reflection of geometry as well as material non-linearity of the materials. For the proposed model of the finite element analysis, concrete slab with loading and supports plate, steel beam section with stud shear connector and channel shear connectors with reinforcement bars mesh convergence is created and shown in Figure 3a–c respectively.
Contact features are taking a supreme role in the simulation of composite structures. Two or more dissimilar materials act together once proper contact is established between them. Bonded contact was considered to attach the shear connector with the flanges of the steel beam and also for the embedded element to the concrete slab (neglecting relative slip among the elements). Reinforcements were attached to the concrete slab by means of bonded interactions with no-slip between them. CONTA174 and TARGE170 elements are employed to establish proper contact among the steel beam section, shear connector and concrete slab to avoid failure due to improper connection between the elements.
Other than element types and contact characteristics, boundary conditions and solvers are also important for finite element simulation and analysis. In the present non-linear finite element study, roller support at one end and hinged support at the other end is considered as the boundary condition. In the case of solvers, the static structural method with the Newton-Raphson approach was taken into account to evaluate the non-linear behaviour to find deformation and slip characteristics against the loads without errors.
Applying material characteristics is taking a vital role in the non-linear investigation of the structural element using ANSYS because geometric as well as non-linearity of material is considered. The material properties of the associated materials which are involved in the design of steel-concrete composite beams, such as steel beams, concrete slabs, shear connectors and reinforcement bars, are presented in Table 1. Structural steel beam sections along with shear connectors are assumed as elastic-plastic materials whereas reinforcement bar is supposed to be elastic-linear-strain-hardening with a tangent modulus of 1/10,000 of its elastic modulus [3].
Material | Description | Value | Unit |
Concrete slab | Concrete strength | 35 | MPa |
Poisson coefficient | 0.18 | - | |
Steel beam | Modulus of elasticity | 2 × 105 | MPa |
Poisson coefficient | 0.3 | - | |
Yield strength | 300,350 and 450 | MPa | |
Shear connector | Modulus of elasticity | 2 × 105 | MPa |
Poisson coefficient | 0.3 | - | |
Yield strength | 374 | MPa | |
Reinforcement | Modulus of elasticity | 2 × 105 | MPa |
Poisson coefficient | 0.3 | - | |
Yield strength | 430 | MPa |
A multilinear isotropic hardening relationship is being used for a concrete slab. Elastic modulus and poisson coefficient are assumed as linear characteristics. Modulus of elasticity of concrete, Ec specimens is calculated using the relationship available in international standards Eurocode 4 (2004) [7], which is represented as
Ec=9500×(fc+8)0.3×(γc/24)0.5 | (1) |
where γc = 24 kN/m3 and fc = 35 N/mm2.
Non-linear properties have an impact on the evaluation of the non-linear behaviour of any structure. Basically, shear transfer co-efficient, which includes open and closed cracks, are assumed as 0.2 and 0.6, respectively, as inputs. Apart from shear transfer co-efficient, the tensile strength of concrete is taken into account as 0.1 times its compressive strength (fc) to fulfil the non-linear characteristics of concrete.
The finite element numerical model is developed by authors to verify the performance of composite beams (A5, A6, C1 and D1) against the test data reported by Chapman and Balakrishnan [8] available in the literature. The geometric properties of the simply supported composite beam are summarized in Table 2. Figure 4a–d gives the comparison of the load capacity against the corresponding mid-span deformation for all the four beam models under consideration.
Beam model | L (mm) | bc (mm) | tc (mm) | h (mm) | bf (mm) | tf (mm) | tw (mm) | No. of shear connectors |
A5 | 5486.4 | 1219.2 | 152.4 | 304.8 | 152.4 | 18.2 | 10.16 | 44 |
A6 | 32 | |||||||
C1 | 44 | |||||||
D1 | 100 |
From the present finite element study, the almost same amount of load-carrying capacity is achieved against the corresponding mid-span deformation with a curve that follows the same trend as the experimental test findings reported in the literature. Figure 4a, b represents the comparison of results of loads against the central deformation for beam model A5 and A6, respectively. In comparison to the experimental results, the numerical model shows 11.12 and 11.58% more load carrying capability for specimens A5 and A6, respectively. The pattern of the load-deflection curve, with an increment of load for the numerical model developed by authors and the experimental outputs available in the literature, are close to each other. Model C1 and D1 shown a similar trend of the curve in the plastic state compared to the elastic zone, which is represented in Figure 4c, d, respectively. Test load capacity is observed to be around 11.25% lesser compared to the present finite element model in the case of C1 specimen, whereas numerical model D1 is showing 10.20% more load capacity than the experimental one.
Along with central deformation, observation of slip characteristics is equally important for assessing the performance of composite structural elements since it involves the usage of different materials. The interfacial slip has been verified against its corresponding load carrying capacity for A5 and C1 models. Figure 5a, b represents the comparison of slip patterns between test and numerical models. In comparison to test results that appeared in the literature [8], numerical models exhibited reduced slip for both specimens. Table 3 summarized the comparison between test findings (Ptest) available in the literature and present finite element models (PFEA) in terms of ultimate load capacity. FEA results produced by authors are showing more capacity, which is evident from the last column of Table 3.
Beam model | Ptest [8] | PFEA | PFEA/Ptest |
A5 | 459.58 | 512.61 | 1.11 |
A6 | 430.21 | 498.57 | 1.15 |
C1 | 438.14 | 493.72 | 1.12 |
D1 | 482.26 | 493.38 | 1.02 |
The proposed numerical approach, which was successfully validated and followed, is provided in this section. Thirty finite element models of composite beams stud along with channel shear connector to evaluate the performance of composite section are created. Configuration and geometry of stud and channel shear connector, degree of composite action and steel grades used are considered key parameters for the present study. Tables 4 and 5 provide the geometrical parameters of the beam and elements used in this non-linear finite element analysis, respectively. Cross-sectional details of the steel section are represented using h, bf, tf, and tw. h and bf indicate the total height and flange width, whereas tf and tw represent the thickness of flange and web, respectively, of the steel beam section. And bc and tc indicate the width and thickness of the concrete slab, which rests above the steel beam section. The length of the composite beam is given as L. The cross-section of a composite beam comprised of steel and concrete is shown in Figure 6.
L (mm) | h (mm) | bf (mm) | tf (mm) | tw (mm) | tc (mm) | bc (mm) |
1500 | 300 | 140 | 12.4 | 7.50 | 120 | 400 |
Series | Model designation | Stud dimensions | Channel designation | Degree of composite action | Steel yield strength fy (MPa) |
d × H (mm × mm) | |||||
A | CBSC1 | 16 × 75 | - | 0.5 | 300 |
CBSC2 | 20 × 75 | - | 0.5 | 300 | |
CBSC3 | 20 × 100 | - | 0.5 | 300 | |
CBCC4 | - | ISMC75 | 0.5 | 300 | |
CBCC5 | - | ISMC100 | 0.5 | 300 | |
B | CBSC6 | 16 × 75 | - | 0.5 | 350 |
CBSC7 | 20 × 75 | - | 0.5 | 350 | |
CBSC8 | 20 × 100 | - | 0.5 | 350 | |
CBCC9 | - | ISMC75 | 0.5 | 350 | |
CBCC10 | - | ISMC100 | 0.5 | 350 | |
C | CBSC11 | 16 × 75 | - | 0.5 | 450 |
CBSC12 | 20 × 75 | - | 0.5 | 450 | |
CBSC13 | 20 × 100 | - | 0.5 | 450 | |
CBCC14 | - | ISMC75 | 0.5 | 450 | |
CBCC15 | - | ISMC100 | 0.5 | 450 | |
D | CBSC16 | 16 × 75 | - | 1.0 | 300 |
CBSC17 | 20 × 75 | - | 1.0 | 300 | |
CBSC18 | 20 × 100 | - | 1.0 | 300 | |
CBCC19 | - | ISMC75 | 1.0 | 300 | |
CBCC20 | - | ISMC100 | 1.0 | 300 | |
E | CBSC21 | 16 × 75 | - | 1.0 | 350 |
CBSC22 | 20 × 75 | - | 1.0 | 350 | |
CBSC23 | 20 × 100 | - | 1.0 | 350 | |
CBCC24 | - | ISMC75 | 1.0 | 350 | |
CBCC25 | - | ISMC100 | 1.0 | 350 | |
F | CBSC26 | 16 × 75 | - | 1.0 | 450 |
CBSC27 | 20 × 75 | - | 1.0 | 450 | |
CBSC28 | 20 × 100 | - | 1.0 | 450 | |
CBCC29 | - | ISMC75 | 1.0 | 450 | |
CBCC30 | - | ISMC100 | 1.0 | 450 |
Apart from steel and concrete, the geometry of the shear connector is represented by using d and H, where d indicates shank diameter and H represents height of the stud. Besides this, as channel connectors, two channels, ISMC75 and ISMC100, are considered for the present investigation.
All thirty models (CBSC1-CBCC30) are categorized into six series depending on the geometry of stud connector/channel designation, degree of composite action, and steel yield strength. In model designation first two letters (CB) represent composite beam, next two letters, SC and CC, present stud connector or channel connectors, respectively. The number 1 to 30 represents the specimen number of the beam models.
The influence of variables such as the geometry of stud connector, geometry of channel connector, degree of shear connection, and steel yield strength on the present non-linear finite element analysis are evaluated and discussed in this section.
Two shank diameters (16 and 20 mm) along with two lengths of 75 and 100 mm of stud connector are considered to evaluate the performance of geometry of stud connector involved in the composite beam comprised of steel and concrete subjected to the application of two-point load applied on the entire width of the concrete slab. Figure 7a, b represent the ultimate load capacity and central deformation, respectively, of the composite beam based on the shank diameter of the stud connector. Figure 8a, b depict the load-carrying capacity and mid-span deformation, respectively, based on the length of the stud. Load capacity is 7.59 and 7.34% increased with the increment of the diameter from 16 to 20 mm of stud connector under the consideration of partial and full shear connection, respectively. In the comparison of load-carrying capacity, increment of length of stud is shown minimal difference compared to the diameter of the stud. Ultimate load capacity and mid-span deformation of the composite beam is increased by 4.78 and 5.29% respectively, while the stud length increased from 75 to 100 mm.
Two-channel sections, ISMC75 and ISMC100 are considered to evaluate the performance of the channel as a shear connector in a steel-concrete composite beam under four-point bending. Figure 9a represents the ultimate load-carrying capacity of composite beams consisting of ISMC75 and ISMC100 channels as a connector. Ultimate load capacity of the beam is increased by 3.11% when the ISMC100 section is used with a partial shear connection. The effect on maximum deformation is shown in Figure 9b. The geometry of the channel connector is effective in terms of deformation criteria compared to load capacity. Composite beam consisting of ISMC75 is shown 9.76 and 4.08% lesser deflection compared to the ISMC100 section with partial and full shear connection respectively.
Interfacial slip and mid-span deformation of a steel-concrete composite beam subjected to partial and full shear interaction are studied in the present finite element study. End slip is plotted for different degrees of shear interaction and a comparison between the thirty specimens under consideration is presented in Figure 10a. It is observed that in the case of yield strength of steel beam 300 MPa, the slip is reduced by 40.75 and 23.46% while the degree of connection from partial to full in the case of stud connector and channel connector respectively. It can also be observed from the finite element study that the shear connector is prone to slip even in the case of full shear connection due to its finite stiffness.
In addition, maximum mid-span deformation is observed under the consideration of different degrees of shear interaction and a comparison graph is made. Figure 10b depicts the central deformation under two-point loading conditions is reduced by 10.47 and 14.71% with the changes of shear interaction from partial to full for the composite beam specimen with stud and channel connector respectively. Madhusudan and Akhil [4] also concluded through an analytical study that the mid-span deformation of beam of full shear connection was reduced compared to that of partial interaction.
In this section, the effect of using steel beams of different yield strengths is discussed keeping the other related parameters such as the geometry of the shear connector and degree of interaction constant. Figure 11a–f depicts the central deformation versus its corresponding load capacity of composite sections under the consideration of different yield strengths of steel. The ultimate load capacity along with central deformation is considerably increased when the yield strength of the steel beam increases. Ultimate load capacity is increased by 20.32 and 30.51% when yield strength is enhanced from 300 to 350 and 450 MPa respectively under the consideration of partial connection. The load capacity is increased by 11.77 and 30.82% in case of full interaction when the yield strength of steel is increased from 300 to 350 and 450 MPa respectively. Liu et al. [9] have also concluded that the ultimate strength of composite beams was rapidly enhanced with the increment of steel yield strength.
An increase in steel yield strength is shown positive effects on the slip behaviour. End-slip is measured and plotted against the corresponding load which is illustrated in Figure 12a, b. With the enhancement of yield strength of steel beam, slip is found to increase. If yield strength increases from 300 to 350 MPa, slip is increased by 1.58 and 19.70% under the consideration of full and partial interaction respectively. But if yield strength increased from 300 to 450 MPa, slip increase of 8.41 and 20.30% is observed for full and partial shear connection respectively. It is observed that slip is reduced under full shear connection compared to partial one because the stiffness of the beam specimen is increased and therefore strong interaction is established between the steel beam and concrete slab. End-slip is considerably enhanced with the increment of steel yield strength reported by Ban and Mark [10].
This paper includes an investigation of the flexural behaviour of steel-concrete composite beam made up of stud/channel connector, with the employment of finite element model using ANSYS15 analysis. The results of the non-linear FE analysis can be used to drawn the following conclusions.
The ultimate load capacity and mid-span deformation of the steel-concrete composite beam is enhanced by 4.78 and 5.29% while the stud length is increased from 75 to 100 mm. Ultimate load capacity is increased by 3.11% when the ISMC100 section is used compared to ISMC75 with a partial shear connection.
Composite beam consisting of ISMC75 steel beam is shown 9.76 and 4.08% lesser deflection compared to ISMC100 with partial and full shear connection respectively. Slip is reduced by up to 40.75 and 23.46% while the degree of connection is increased from partial to full in the case of stud and channel connector respectively. Mid-span deformation under the loading condition is reduced by up to 10.47 and 14.71% with the degree of shear interaction increased from partial to full for the composite beam specimen of stud and channel connector respectively.
The ultimate load capacity and central deformation are considerably increased with the enhancement in yield strength of the steel beam in a steel-concrete composite beam. Ultimate load capacity is increased by 20.32 and 30.51% when yield strength is enhanced from 300 to 350 and 450 MPa respectively under the consideration of partial connection. The load capacity is increased by 11.77 and 30.82% in case of full interaction when the yield strength of steel is increased from 300 to 350 and 450 MPa respectively. When the yield strength of steel is enhanced from 300 to 350 MPa, slip is increased by 1.58 and 19.70% under full and partial interaction respectively.
The composite beam provided with channel connectors is showing 4.07% more stiffness compared to that with stud connectors. Hence according to the present numerical analysis, it can be inferred that the channel connector proves to be the better alternative compared to the conventional flexible stud connector based on the flexural performance of composite beams. Besides this, the partial connection proves to have positive effects on central deformation of the steel-concrete composite beams with stud and channel connectors subjected to four-point bending loading conditions.
All authors declare no conflicts of interest in this paper.
[1] |
Liang QQ, Brian U, Mark AB, et al. (2005) Strength analysis of steel-concrete composite beams in combined bending and shear. J Struct Eng 131: 1593–1600. https://doi.org/10.1061/(ASCE)0733-9445(2005)131:10(1593) doi: 10.1061/(ASCE)0733-9445(2005)131:10(1593)
![]() |
[2] |
Shervin M, Saman B (2008) Behavior of channel shear connectors Part I: experimental study. J Constr Steel Res 64: 1333–1340. https://doi.org/10.1016/j.jcsr.2008.01.010 doi: 10.1016/j.jcsr.2008.01.010
![]() |
[3] |
Queiroza FD, Vellascob PCGS, Nethercot DA (2007) Finite element modelling of composite beams with full and partial shear connection. J Constr Steel Res 63: 505–521. https://doi.org/10.1016/j.jcsr.2006.06.003 doi: 10.1016/j.jcsr.2006.06.003
![]() |
[4] |
Madhusudan GK, Akhil U (2020) Numerical study on the deformation behavior of steel concrete composite girders considering partial shear interaction. Structures 23: 437–446. https://doi.org/10.1016/j.istruc.2019.10.007 doi: 10.1016/j.istruc.2019.10.007
![]() |
[5] |
Amar P, Monika AP, Anandavalli N (2021) Behaviour of steel-concrete composite (SCC) girder under impact due to rock fall. J Constr Steel Res 177: 106474. https://doi.org/10.1016/j.jcsr.2020.106474 doi: 10.1016/j.jcsr.2020.106474
![]() |
[6] | Bureau of Indian Standards (1986) Code of practice for composite construction in structural steel and concrete. IS 11384. |
[7] | European Committee for standardization (2004) Eurocode 4: Design of composite steel and concrete structures-Part 1-1: General rules and rules for buildings. EN 1994-1-1. |
[8] | Chapman JC, Balakrishnan S (1964) Experiments on composite beams. J Struct Eng 42: 369–383. |
[9] |
Liu X, Bradford MA, Ataei A (2017) Flexural performance of innovative sustainable composite steel-concrete beams. Eng Struct 130: 282–296. https://doi.org/10.1016/j.engstruct.2016.10.009 doi: 10.1016/j.engstruct.2016.10.009
![]() |
[10] |
Ban H, Bradford MA (2013) Flexural behaviour of composite beams with high strength steel. Eng Struct 56: 1130–1141. https://doi.org/10.1016/j.engstruct.2013.06.040 doi: 10.1016/j.engstruct.2013.06.040
![]() |
1. | G. P. Tonkih, D. A. Chesnokov, Strength and Ductility Evaluation of L-Shape Shear Connectors in Composite Floors, 2024, 5, 2949-1614, 27, 10.22227/2949-1622.2024.1.27-44 |
Material | Description | Value | Unit |
Concrete slab | Concrete strength | 35 | MPa |
Poisson coefficient | 0.18 | - | |
Steel beam | Modulus of elasticity | 2 × 105 | MPa |
Poisson coefficient | 0.3 | - | |
Yield strength | 300,350 and 450 | MPa | |
Shear connector | Modulus of elasticity | 2 × 105 | MPa |
Poisson coefficient | 0.3 | - | |
Yield strength | 374 | MPa | |
Reinforcement | Modulus of elasticity | 2 × 105 | MPa |
Poisson coefficient | 0.3 | - | |
Yield strength | 430 | MPa |
Beam model | L (mm) | bc (mm) | tc (mm) | h (mm) | bf (mm) | tf (mm) | tw (mm) | No. of shear connectors |
A5 | 5486.4 | 1219.2 | 152.4 | 304.8 | 152.4 | 18.2 | 10.16 | 44 |
A6 | 32 | |||||||
C1 | 44 | |||||||
D1 | 100 |
Beam model | Ptest [8] | PFEA | PFEA/Ptest |
A5 | 459.58 | 512.61 | 1.11 |
A6 | 430.21 | 498.57 | 1.15 |
C1 | 438.14 | 493.72 | 1.12 |
D1 | 482.26 | 493.38 | 1.02 |
L (mm) | h (mm) | bf (mm) | tf (mm) | tw (mm) | tc (mm) | bc (mm) |
1500 | 300 | 140 | 12.4 | 7.50 | 120 | 400 |
Series | Model designation | Stud dimensions | Channel designation | Degree of composite action | Steel yield strength fy (MPa) |
d × H (mm × mm) | |||||
A | CBSC1 | 16 × 75 | - | 0.5 | 300 |
CBSC2 | 20 × 75 | - | 0.5 | 300 | |
CBSC3 | 20 × 100 | - | 0.5 | 300 | |
CBCC4 | - | ISMC75 | 0.5 | 300 | |
CBCC5 | - | ISMC100 | 0.5 | 300 | |
B | CBSC6 | 16 × 75 | - | 0.5 | 350 |
CBSC7 | 20 × 75 | - | 0.5 | 350 | |
CBSC8 | 20 × 100 | - | 0.5 | 350 | |
CBCC9 | - | ISMC75 | 0.5 | 350 | |
CBCC10 | - | ISMC100 | 0.5 | 350 | |
C | CBSC11 | 16 × 75 | - | 0.5 | 450 |
CBSC12 | 20 × 75 | - | 0.5 | 450 | |
CBSC13 | 20 × 100 | - | 0.5 | 450 | |
CBCC14 | - | ISMC75 | 0.5 | 450 | |
CBCC15 | - | ISMC100 | 0.5 | 450 | |
D | CBSC16 | 16 × 75 | - | 1.0 | 300 |
CBSC17 | 20 × 75 | - | 1.0 | 300 | |
CBSC18 | 20 × 100 | - | 1.0 | 300 | |
CBCC19 | - | ISMC75 | 1.0 | 300 | |
CBCC20 | - | ISMC100 | 1.0 | 300 | |
E | CBSC21 | 16 × 75 | - | 1.0 | 350 |
CBSC22 | 20 × 75 | - | 1.0 | 350 | |
CBSC23 | 20 × 100 | - | 1.0 | 350 | |
CBCC24 | - | ISMC75 | 1.0 | 350 | |
CBCC25 | - | ISMC100 | 1.0 | 350 | |
F | CBSC26 | 16 × 75 | - | 1.0 | 450 |
CBSC27 | 20 × 75 | - | 1.0 | 450 | |
CBSC28 | 20 × 100 | - | 1.0 | 450 | |
CBCC29 | - | ISMC75 | 1.0 | 450 | |
CBCC30 | - | ISMC100 | 1.0 | 450 |
Material | Description | Value | Unit |
Concrete slab | Concrete strength | 35 | MPa |
Poisson coefficient | 0.18 | - | |
Steel beam | Modulus of elasticity | 2 × 105 | MPa |
Poisson coefficient | 0.3 | - | |
Yield strength | 300,350 and 450 | MPa | |
Shear connector | Modulus of elasticity | 2 × 105 | MPa |
Poisson coefficient | 0.3 | - | |
Yield strength | 374 | MPa | |
Reinforcement | Modulus of elasticity | 2 × 105 | MPa |
Poisson coefficient | 0.3 | - | |
Yield strength | 430 | MPa |
Beam model | L (mm) | bc (mm) | tc (mm) | h (mm) | bf (mm) | tf (mm) | tw (mm) | No. of shear connectors |
A5 | 5486.4 | 1219.2 | 152.4 | 304.8 | 152.4 | 18.2 | 10.16 | 44 |
A6 | 32 | |||||||
C1 | 44 | |||||||
D1 | 100 |
Beam model | Ptest [8] | PFEA | PFEA/Ptest |
A5 | 459.58 | 512.61 | 1.11 |
A6 | 430.21 | 498.57 | 1.15 |
C1 | 438.14 | 493.72 | 1.12 |
D1 | 482.26 | 493.38 | 1.02 |
L (mm) | h (mm) | bf (mm) | tf (mm) | tw (mm) | tc (mm) | bc (mm) |
1500 | 300 | 140 | 12.4 | 7.50 | 120 | 400 |
Series | Model designation | Stud dimensions | Channel designation | Degree of composite action | Steel yield strength fy (MPa) |
d × H (mm × mm) | |||||
A | CBSC1 | 16 × 75 | - | 0.5 | 300 |
CBSC2 | 20 × 75 | - | 0.5 | 300 | |
CBSC3 | 20 × 100 | - | 0.5 | 300 | |
CBCC4 | - | ISMC75 | 0.5 | 300 | |
CBCC5 | - | ISMC100 | 0.5 | 300 | |
B | CBSC6 | 16 × 75 | - | 0.5 | 350 |
CBSC7 | 20 × 75 | - | 0.5 | 350 | |
CBSC8 | 20 × 100 | - | 0.5 | 350 | |
CBCC9 | - | ISMC75 | 0.5 | 350 | |
CBCC10 | - | ISMC100 | 0.5 | 350 | |
C | CBSC11 | 16 × 75 | - | 0.5 | 450 |
CBSC12 | 20 × 75 | - | 0.5 | 450 | |
CBSC13 | 20 × 100 | - | 0.5 | 450 | |
CBCC14 | - | ISMC75 | 0.5 | 450 | |
CBCC15 | - | ISMC100 | 0.5 | 450 | |
D | CBSC16 | 16 × 75 | - | 1.0 | 300 |
CBSC17 | 20 × 75 | - | 1.0 | 300 | |
CBSC18 | 20 × 100 | - | 1.0 | 300 | |
CBCC19 | - | ISMC75 | 1.0 | 300 | |
CBCC20 | - | ISMC100 | 1.0 | 300 | |
E | CBSC21 | 16 × 75 | - | 1.0 | 350 |
CBSC22 | 20 × 75 | - | 1.0 | 350 | |
CBSC23 | 20 × 100 | - | 1.0 | 350 | |
CBCC24 | - | ISMC75 | 1.0 | 350 | |
CBCC25 | - | ISMC100 | 1.0 | 350 | |
F | CBSC26 | 16 × 75 | - | 1.0 | 450 |
CBSC27 | 20 × 75 | - | 1.0 | 450 | |
CBSC28 | 20 × 100 | - | 1.0 | 450 | |
CBCC29 | - | ISMC75 | 1.0 | 450 | |
CBCC30 | - | ISMC100 | 1.0 | 450 |