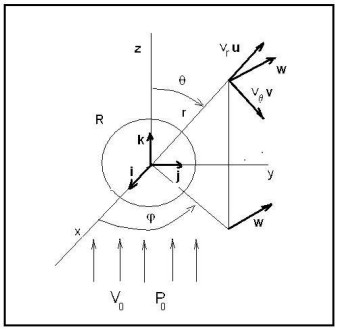
In our research work on the microscopic properties of liquids in relation to biotechnical applications, we were led to use the Stokes formula to calculate the force exerted by a fluid on colloidal suspensions, and to look in the bibliography for the demonstration of this formula. The proofs that we have found are often partial and the applicability conditions not always explicit, which led us to resort to the initial demonstration made by Stokes [
Citation: Jean-Louis Bretonnet, Jean-François Wax. Applicability conditions of the Stokes formula[J]. AIMS Materials Science, 2021, 8(5): 809-822. doi: 10.3934/matersci.2021049
[1] | Jean-Louis Bretonnet . Competing interactions in colloidal suspensions. AIMS Materials Science, 2019, 6(4): 509-548. doi: 10.3934/matersci.2019.4.509 |
[2] | Jean-Marc Bomont, Dino Costa, Jean-Louis Bretonnet . Large effects of tiny structural changes on the cluster formation process in model colloidal fluids: an integral equation study. AIMS Materials Science, 2020, 7(2): 170-181. doi: 10.3934/matersci.2020.2.170 |
[3] | Anna Godymchuk, Alexey Ilyashenko, Yury Konyukhov, Peter Ogbuna Offor, Galiya Baisalova . Agglomeration and dissolution of iron oxide nanoparticles in simplest biological media. AIMS Materials Science, 2022, 9(4): 642-652. doi: 10.3934/matersci.2022039 |
[4] | Domenico Lombardo, Pietro Calandra, Maria Teresa Caccamo, Salvatore Magazù, Mikhail Alekseyevich Kiselev . Colloidal stability of liposomes. AIMS Materials Science, 2019, 6(2): 200-213. doi: 10.3934/matersci.2019.2.200 |
[5] | Velram Balaji Mohan, Casparus J. R. Verbeek . Rheology and processing of bloodmeal-based thermoplastics. AIMS Materials Science, 2015, 2(4): 546-559. doi: 10.3934/matersci.2015.4.546 |
[6] | Julien G. Mahy, Stéphanie D. Lambert, Jérémy Geens, Alain Daniel, David Wicky, Catherine Archambeau, Benoît Heinrichs . Large scale production of photocatalytic TiO2 coating for volatile organic compound (VOC) air remediation. AIMS Materials Science, 2018, 5(5): 945-956. doi: 10.3934/matersci.2018.5.945 |
[7] | Natthakitta Piyarat, Ubolrat Wangrakdiskul, Purinut Maingam . Investigations of the influence of various industrial waste materials containing rice husk ash, waste glass, and sediment soil for eco-friendly production of non-fired tiles. AIMS Materials Science, 2021, 8(3): 469-485. doi: 10.3934/matersci.2021029 |
[8] | Purinut Maingam, Ubolrat Wangrakdiskul, Natthakitta Piyarat . Potential of alternative waste materials: rice husk ash and waste glass cullet with boric acid addition for low-fired unglazed tiles. AIMS Materials Science, 2021, 8(2): 283-300. doi: 10.3934/matersci.2021019 |
[9] | Raghvendra K Pandey, William A Stapleton, Mohammad Shamsuzzoha, Ivan Sutanto . Voltage biased Varistor-Transistor Hybrid Devices: Properties and Applications. AIMS Materials Science, 2015, 2(3): 243-259. doi: 10.3934/matersci.2015.3.243 |
[10] | K.Pandey Raghvendra, A.Stapleto Williamn, Shamsuzzoha Mohammad, Sutanto Ivan . Voltage biased Varistor-Transistor Hybrid Devices: Properties and Applications. AIMS Materials Science, 2015, 2(3): 243-259. doi: 10.3934/matersci.2015.243 |
In our research work on the microscopic properties of liquids in relation to biotechnical applications, we were led to use the Stokes formula to calculate the force exerted by a fluid on colloidal suspensions, and to look in the bibliography for the demonstration of this formula. The proofs that we have found are often partial and the applicability conditions not always explicit, which led us to resort to the initial demonstration made by Stokes [
Note first that Stokes' formula (F=6πηRv) only applies to objects in very viscous fluids with Reynolds numbers Re=ρηLv less than unity, where ρ is the density of fluid in kg⋅m−3, η its dynamic viscosity in kg⋅m−1⋅s−1 (or Pa⋅s), v the velocity of fluid away from the object in m⋅s−1 and L the size of the object in m. For low viscosity fluids (Re>103) the formula must be replaced by F=12ρCxSv2 which does not contain the Reynolds number. On the other hand it contains the coefficient Cx which depends on the shape of the moving object (ranging between 0.1 and 1), the master couple S in m2, i.e., the largest section perpendicular to the direction of motion, and the velocity v of the object in m⋅s−1. In the intermediate domain of viscosity (1<Re<103), there is no simple law for the force of resistance to motion of a object in a fluid. This is due to the vortex zone which develops behind the object and which considerably disturbs its motion.
Most common fluids (water, milk, mineral oils, organic solvents, etc.) have viscosity coefficients which remain constant under standard conditions; these are Newtonian fluids. As an indication, let us give the values of the viscosity of some fluids at room temperature, in Pa⋅s: water (1.5× 10−3), air (1.8× 10−5), mercury (1.6× 10−3), liquid metals have the same viscosities as water, the viscosity of glycerin varies by a coefficient 1000 between 0 ∘C and 20 ∘C (12 at 0 ∘C and 0.015 at 20 ∘C). If the viscosity of a fluid changes when subjected to stress, the fluid is said to be non-Newtonian. The best example is creams such as ketchup, honey, blood, shampoo, paint etc. which become more runny when shaken.
Before demonstrating the Stokes formula, let us note again that it applies to a sphere in motion in an infinite fluid, free from any disturbance induced by the presence of an obstacle, even at a very great distance, because the disturbances of the velocity field decrease very slowly (in r−1). This low damping of the disturbance means that the Stokes formula must be applied with care when the fluid contains several objects. In the phenomenon of sedimentation for example, the resistance to the motion of a moving particle strongly depends on the degree of dilution of the solution [2].
In the following, we will discuss the problem of a stationary sphere in a moving viscous fluid. Then, we will do the kinematic study of fluid allowing to obtain the velocity distribution around the sphere. In the next section, we will determine the viscous stress tensor in the fluid and perform the calculation of the force exerted on the sphere. In the last section, we will present some applications of the Stokes formula to the rheology of colloidal suspensions.
To determine the velocity distribution around a sphere and analyze the particular characteristics of the flow, consider the Navier-Stokes equation which expresses the conservation of the momentum of an elementary volume of fluid [3]:
∂V∂t+(V.∇)V=F−1ρ∇ p+1ρ∇=tη | (2.1) |
where the left-hand side of this equation represents the acceleration, F the external force, p the pressure, =tη the tensor of the viscosity stresses in the elementary volume, and where the nabla operator ∇ is used.
The problem is indifferently that of the uniform rectilinear motion of a sphere in a viscous fluid or that of a fixed sphere in a permanent flow whose velocity is V0 and the pressure P0 at infinity. Let us consider a sphere held vertically by a wire in the upward flow in the direction k (see Figure 1). In addition, suppose that (i) the sphere is not subjected to any external action, therefore F=0, (ii) the flow is permanent (stationary), therefore ∂V∂t=0, (iii) the fluid is incompressible, therefore ∇.V=0, and (iv) the fluid is viscous.
Because the fluid is incompressible, the last term of the second member of the relation (2.1) is expressed as a function of the Laplacian of the velocity, i.e. ∇=tη=ηΔV. With these considerations, all that remains in the Navier-Stokes equation is the term (V.∇)V which represents the convective acceleration (whose order of magnitude is v2L), the term 1ρ∇p and the term ηρΔV. Note that the order of magnitude of this last term is ηvρL2, and that the ratio of the two terms (V.∇)V and ηρΔV is the Reynolds number Re=ρηLv Therefore, for a very low Reynolds number we can neglect the convective acceleration and use the simplified Navier-Stokes equation:
gradp=ηΔV | (2.2) |
Suppose that the origin of the Cartesian coordinate system x, y, z is located at the center of the sphere of radius R. The spherical shape of the object suggests using the spherical coordinate system r, θ, φ to perform the analytical calculations. The vertical axis k being symmetrical for the motion of the fluid, we are dealing with a two-dimensional (rotational) flow for which the velocity at position r is written:
V(r,θ)=vr(r,θ)u+vθ(r,θ)v | (2.3) |
It should be stressed that there are always molecular cohesion forces in the fluid in direct contact with the solid wall, thus producing a thin of fluid layer stuck to the wall in which the velocity is zero. Consequently, the boundary conditions of the equations of motion of the viscous fluid are that it is necessary to cancel the velocity of the fluid on the walls of the object:
if r=R, V(R,θ)=0 | (2.4) |
if r→∞, V(∞,θ)=V0k | (2.5) |
that is to say
vr(R,θ)=vθ(R,θ)=0 | (2.6) |
vr(∞,θ)=V0cosθ and vθ(∞,θ)=−V0sinθ | (2.7) |
a—Due to the two-dimensional nature of the flow, the rotational of the velocity V(r,θ) is perpendicular to the plane (u,v) which is written rot V=Ω=Ωφ(r,θ)w. By applying the rotational operator to the simplified Navier-Stokes equation Eq (2.2), we end up with the following relation:
rot(gradp)=rot (ηΔV) | (2.8) |
0=Δ(rotV) =Δ Ω | (2.9) |
where the components of Ω are:
(rotV)u=1rsinθ[∂∂θ(vφsinθ−∂vθ∂φ]=0 | (2.10) |
(rotV)v=1rsinθ∂vr∂φ−1r∂∂r(rvφ)=0 | (2.11) |
(rotV)w=1r[∂∂r(rvθ)−∂vr∂θ]=Ωφ(r,θ) | (2.12) |
b—To determine the components of the velocity V(r,θ) for the two-dimensional flow of incompressible fluids, it is convenient to use the stream function Ψ(r,θ) defined by:
dΨ=∂Ψ∂θdθ+∂Ψ∂rdr=vrrdθ−vθdr | (2.13) |
where the sum of the partial derivatives:
∂∂r(∂Ψ∂θ)=vr+r∂vr∂r and ∂∂θ(∂Ψ∂r)=−∂vθ∂θ | (2.14) |
is equal to rdivV=vr+r∂vr∂r+∂vθ∂θ=0 in cylindrical coordinates. To prove his formula, Stokes modified the previous stream function to a form that allows the components of velocity to be written as:
vr(r,θ)=1r2sinθ∂Ψ∂θ | (2.15) |
vθ(r,θ)=−1rsinθ∂Ψ∂r | (2.16) |
In order to calculate the velocity field around the sphere in terms of the stream function Ψ(r,θ), we solve Eq (2.9) by using the component of the Laplacian of the vector Ω(0,0,Ωφ) on w, as the components on u and v are identically zero. This equation reads:
(ΔΩ)w=1r∂2(rΩφ)∂r2+1r2∂∂θ[1sinθ∂(Ωφsinθ)∂θ]=0 | (3.1) |
This two-dimensional partial differential equation (Laplace's equation), in spherical coordinates, is conventionally solved by looking for a particular integral in the form Ωφ(r,θ)=P(r)Q(θ). After the substitution of this solution in the Laplace equation, then the separation of the variables and the division by P(r)Q(θ), we obtain the following two equations:
rP(r)d2dr2[rP(r)]=α2 | (3.2) |
1Q(θ)ddθ{1sinθddθ[Q(θ)sinθ]}=−α2 | (3.3) |
If we notice that the function Q(θ)=sinθ is solution of the second equation for α2=2, we can deduce the solving equation of the first equation in the form:
r2d2P(r)dr2+2rdP(r)dr−2P(r)=0 | (3.4) |
The general solution of this differential equation is P(r)=ar+br2, where a and b are two constants to be determined with the boundary conditions. Since the function P(r) must remain finite at large distances, we need that a=0 so that the solution of Laplace's equation Eq (3.1) reduces to:
Ωφ(r,θ)=bsinθr2 | (3.5) |
Using Eq (2.12) in conjunction with Eqs (2.15), (2.16) and (3.5), we get the following partial differential equation:
1r[∂∂r(−1sinθ∂Ψ∂r)−∂∂θ(1r2sinθ∂Ψ∂θ)]=bsinθr2 | (3.6) |
that we solve in the same way as Eq (3.1) by looking for a particular solution in the form Ψ(r,θ)=R(r)T(θ). After replacing this expression and dividing by R(r)T(θ), Eq (3.6) is simplified as follows:
rd2R(r)dr2+R(r)T(θ)r(d2T(θ)dθ2−cosθsinθdT(θ)dθ)=−bsin2θT(θ) | (3.7) |
By noticing that T(θ)=sin2θ is the solution of the angular part of the previous equation, we immediately deduce that the resolving equation of the radial differential equation is:
rd2R(r)dr2−2rR(r)=−b | (3.8) |
A particular solution of this differential equation is R(r)=br2 and the general solution of equation without second member is R(r)=cr2+dr Consequently the stream function Ψ(r,θ) reduces to:
Ψ(r,θ)=R(r)T(θ)=(cr2+dr+br2)sin2θ | (3.9) |
As for the components vr(r,θ) and vθ(r,θ) of the velocity resulting from Eqs (2.15) and (2.16), they are written:
vr(r,θ)=2(c+dr3+b2r)cosθ | (3.10) |
vθ(r,θ)=−(2c−dr3+b2r)sinθ | (3.11) |
where b, c and d are three constants of integration to be determined with the boundary conditions of the velocity. According to Eqs (2.4) and (2.5), vr(r→∞,θ)=V0cosθ and vθ(r→∞,θ)=−V0sinθ,∀θ, and vr(r,θ)>0 and vθ(r,θ)<0 when θ<π2, namely,
vr(∞,θ)= 2ccosθ=V0cosθ | (3.12) |
vθ(∞,θ)=−2csinθ=−V0sinθ | (3.13) |
therefore c=V0/2. As the velocity V(r,θ) of a viscous fluid on the fixed walls is zero (Eq 2.4), the boundary conditions on the sphere (r=R) require the nullity of the normal and tangential components of the velocity, that is:
vr(R,θ)=2(V0/2+dR3+b2R)cosθ=0 | (3.14) |
vθ(R,θ)=−(V0−dR3+b2R)sinθ=0 | (3.15) |
Solving this system of equations leads to the values of the integration constants d=14V0R3 and b=−32V0R, so that the stream function and the velocity components around the sphere are:
Ψ(r,θ)=V0(r22+R34r−3Rr4)sin2θ | (3.16) |
vr(r,θ)=V0(1+R32r3−3R2r)cosθ | (3.17) |
vθ(r,θ)=V0(−1+R34r3+3R4r)sinθ | (3.18) |
This determines the velocity distribution around the sphere, the amplitudes of which attenuate in 1/r.
To calculate the resistance force on a sphere in a uniform flow, we must first calculate the viscous stress tensor. It is by making the macroscopic description of the motion of fluids with the theory of continuous mechanics that we establish the form of the viscous stress tensor =tη to be introduced into the Navier-Stokes equation (Eq (2.1)). Without wishing to go into details [3], let us simply indicate that the viscous stress tensor =tη is a constituent of the total stress tensor =t which is added to the spherical tensor =ts=−p=δ (=δ is the unit tensor) coming from the hydrostatic pressure, namely =t=−p=δ+=tη.
In viscous fluids, the internal friction processes appear only if the different contiguous regions in the fluid move with relative velocities, that is why the elements of viscous stress tensor =tη depend on the derivative of velocity with respect to coordinates (convective acceleration). In non-viscous fluids, as fluids in uniform translation or uniform rotation, there is no internal friction therefore the elements of the viscous stress tensor are zero. In general, the viscous stress tensor =tη depends on two viscosity coefficients, but in incompressible fluids only one coefficient is enough to describe the viscosity.
The expression of the stress tensor of an incompressible viscous fluid in Cartesian coordinates is:
=t =|σxxσyxσzxσxyσyyσzyσxzσyzσzz| | (4.1) |
with the components [3] :
σxx=−p+2η∂vx∂x, σyy=−p+2η∂vy∂y, σzz=−p+2η∂vz∂z | (4.2) |
σxy=σyx=η(∂vx∂y+∂vy∂x) | (4.3) |
σyz=σzy=η(∂vy∂z+∂vz∂y) | (4.4) |
σzx=σxz=η(∂vz∂x+∂vx∂z) | (4.5) |
The nature of flow around a sphere requires the use of spherical coordinates as being done in the previous section. Moreover, as the flow is two-dimensional in the plane (uv), we only need components of the stress tensor in the u and v directions that are:
σrr=−p+2η∂vr∂r | (4.6) |
σrθ=η(1r∂vr∂θ+∂vθ∂r−vθr) | (4.7) |
As for the resistance force F felt by the sphere in the direction of the flow, it is given by the integral on the sphere of radius R of the projections on the axis k of the elementary stresses (σrr)R and (σrθ)R. Since the surface element of the sphere on which the stresses (σrr)R and (σrθ)R are exerted is R2sinθdθdφ, the force F has for expression:
F=2π∫π0[(σrr)Ru+(σrθ)Rv].k.R2sinθdθ | (4.8) |
Before integrating this expression, it remains to determine the stresses (σrr)R and (σrθ)R on the sphere with the partial derivatives of the velocity components (Eqs (3.17) and (3.18)). The following results are easily obtained:
(∂vr∂r)R=(∂vr∂θ)R=(vθr)R=0 and (∂vθ∂r)R=−32ηV0Rsinθ | (4.9) |
so that the stresses on the sphere reduce to:
(σrr)R=−p | (4.10) |
(σrθ)R=−32ηV0Rsinθ | (4.11) |
At first glance, one might think that the viscosity generates the tangential stress (σrθ)R, and does not provide contribution to the normal stress (σrr)R since it only contains the pressure p. In fact, this is wrong because the pressure p is not the usual pressure of the fluid, but it contains a supplementary term provided by the viscosity. To calculate the pressure p, consider the simplified Navier-Stokes equation (Eq (2.2)), and rewrite it as a function of Ω=rotV thanks to the formula ΔV=grad(divV)−rot(rotV), i.e.:
gradp=η ΔV=− ηrotΩ | (4.12) |
The analytical form of this equation in spherical coordinates is easily obtained with Eqs (2.10), (2.11) and (3.5), namely:
∂p∂r=−η (rot Ω)u=−ηrsinθ∂∂θ(Ωφsinθ)=−2ηbr3cosθ | (4.13) |
1r∂p∂θ=−η (rot Ω)v=ηr∂∂r(rΩφ)=− ηbr3sinθ | (4.14) |
The resolution of these two differential equations is done with the method of variation of constants. The solution of the first differential equation is:
p=ηbr2cosθ+h(θ). | (4.15) |
From the second differential equation, we easily obtain the solution h(θ)=P0 which is none other than the usual pressure of the fluid away from the sphere. By replacing the constant b by its value (b=−32V0R), we deduce the expression of the pressure in the vicinity of the sphere:
p=−3ηV0R2r2cosθ+P0 | (4.16) |
and normal stress Eq (4.10) on the sphere:
(σrr)R=32ηV0Rcosθ−P0 | (4.17) |
Only integration of Eq (4.8) remains to be carried out after introducing the constraints on the sphere, namely:
F=2πR2∫π0[(32ηV0Rcosθ−P0)cosθ +(−32ηV0Rsinθ)(−sinθ)]sinθdθ | (4.18) |
It can be verified that the integral of the first term in parentheses is equal to:
F1=−3πηRV0∫π0cos2θ sinθdθ=2πηRV0 | (4.19) |
because the integral of the term P0 is zero and the integral of the second term in parentheses is:
F2=3πηRV0∫π0sin2θ(sinθdθ)=4πηRV0 | (4.20) |
The force exerted by a viscous fluid on a motionless solid sphere consists of two terms depending on viscosity:
F=F1+F2=6πηRV0 | (4.21) |
In the case of an incompressible non-viscous fluid (perfect fluid), it follows that the force is zero, i.e. that the pressures in front and behind the sphere are equal (d'Alembert paradox) [4]. This non-obvious result is explained by the Stokes formula.
In the next section, we will present some applications of the Stokes formula with a particular attention to colloidal suspension systems. Beyond the classic particle problem which is far from being completely resolved, there are more complex systems of colloidal suspensions which remain poorly understood despite their long history and practical relevance. Colloidal suspensions are substances with wide applications both in natural phenomena and in industrial processes. The major difficulty with these systems is that the particles interact directly with each other and by hydrodynamic interactions through the liquid. In the next section, an overview of certain aspects of the dynamics of colloidal suspensions will be provided [5,6].
The Stokes formula can be used to calculate either the pressure of a viscous fluid on a motionless solid sphere or the resistance to motion of a solid sphere in a viscous fluid [7]. If the sphere is at the distance D from a fixed wall, the hydrodynamic force which opposes its motion is given by the expression [8]:
F=6πηRV0λ | (5.1) |
where λ is a complicated function of the distance D between the sphere and the wall. When D>>R, we find the Stokes formula and when D<<R the expression is simplified in the form:
F=6πηR2V0D | (5.2) |
If the sphere is subject to the action of gravitational field, the resistance force of the fluid is opposite to the velocity of the sphere, whose the final value V can be calculated by identifying the resistance force with the gravitational force 43πg(ρs−ρl)R3, where ρs and ρl are the volume masses of the sphere and the liquid. We deduce that:
V=29gη(ρs−ρl)R2 | (5.3) |
For the fall of a liquid drop of viscosity η′≠η, the resistance force has been calculated by Ribtchinsky [9] in the form:
F=2πηRV0(2η+3η′η+η′) | (5.4) |
and the final velocity of the drop is (the case of the solid sphere is found when η′→∞:
V=23g(η+η′)η(2η+3η′)(ρs−ρl)R2 | (5.5) |
As an application, let's use Eq (5.5) to calculate the velocity of a droplet of water forming part of a cloud. With the following values of the different physical properties: g = 9.81 m ⋅ s−2, η′=ηwater∼1.5× 10−3 Pa ⋅ s, η=ηair∼1.8× 10−5 Pa ⋅ s, ρwater∼103 kg ⋅ m−3 and ρair∼1.2 kg ⋅ m−3, we find that the final velocity of a droplet of water of radius 10 µm is ∼ 1 cm ⋅ s−1, whereas a droplet of water of radius 1 µm falls ahundred times slower and a droplet of water of radius 100 µm falls a hundred times faster. Note that in the case of a droplet of water of radius 100 µm, the Stokes formula no longer applies because the Reynolds numberis too large. On the other hand, for bacteria of 3 µm length moving at 10 µm ⋅s−1 in water, Stokes formula can be applied as Re∼10−5.
Since the velocity of a sphere is proportional to R2, the largest particles fall rapidly while the smallest one slowly settle out. The same conclusion can be done by noticing that the resistance force varies in R and not in R2. For very small R values, it follows that the resistance force (F∝R) is greater than it would be if it was proportional to R2. In particular, the Stokes formula cannot be applied to the motion of very small particles as particles cannot sediment out.
The Stokes formula only applies if the flow is stationary and the Reynolds number is less than unity. For suspensions, low Reynolds number flows are distinguished by a large number of particles distributed in a disordered fashion so that the mean values of velocity is required and not the local values around each particle. It is a fact that the Stokes formula is not valid when the sphere is surrounded by other objects which disturb the velocity distribution around the sphere, because the expressions for the velocity components (Eqs (3.17) and (3.18)) at large distances are approximate. The velocity distribution has been calculated by Oseen [10] for large distances. The calculations show that the hydrodynamic force remains unchanged at low distances, while at large distances it is modified and brings a correction to the Stokes formula as follows:
F=6πηRV0(1+3ρRV08η) | (5.6) |
The behavior of suspensions strongly depends on the size of particles. For very small particles (known as Brownian particles) the thermal effects are very important, while for the larger ones the hydrodynamic effects dominate. The relative importance of these two effects is highlighted by the Péclet number, Pe, which is defined by the relation:
Pe=vLD | (5.7) |
where v is the velocity of flow, L the size of particles and D the Brownian diffusion coefficient which combines the Stokes formula and the Einstein-Sutherland formula (D=kBTF/V0), and which is written:
D=kBT6πηR | (5.8) |
where kB is the Boltzmann constant, T the temperature and R the radius of spherical particles. The Péclet number is better defined to be the ratio of the diffusion time τD of particles, on a distance of the order of radius R, to the convection time τC of particles on the same distance R. The diffusion time is τD ∼R2/D, and the convection time is τC ∼R/v∼1/⋅γ with the velocity v=⋅γR and the shear rate ⋅γ. In a simple shear flow, the Péclet number for spherical particles reads [5]:
Pe=τDτC=6πη⋅γR3kBT | (5.9) |
The transition from Brownian behavior to non-Brownian behavior depends mainly on the size of the particles, whose radius varies as R3. To assess the limit between these two regimes, consider particles of R≃ 1 µm in water at room temperature, for a shear rate of ⋅γ≃1s−1 and a Brownian diffusion coefficient D≃1 µm −2⋅s−1. The diffusion time is τD ∼R2/D≃1 s, the convection time is τC ∼1/⋅γ≃1 s and the Péclet number is equal to unity. As a rough approximation of the limit between Brownian and non-Brownian behaviors for suspensions in water, we can retain the indicative values D∼⋅γ∼R∼τD ∼τC∼Pe∼1, where the length is in μm and the time in s, and the corresponding Reynolds number Re=ρηLv=ρη⋅γR2≃23106⋅γR2. Large values of Pe imply strong shear flow where viscous fluid hydrodynamics is significant, and the Brownian motion is dominant in simple fluids composed of small molecules where sizes are very small (∼ 0.2 nm) and relaxation times very short (∼10−12 s) compared to those of colloidal suspensions.
The boundary between Brownian and non-Brownian behaviors depends to a lesser extent on viscosity η and shear rate ⋅γ. Remember that complex fluids are made up of three classes of materials: (i) colloidal suspensions, drops of liquids, etc.; (ii) polymers, surfactant solutions, biological fluids containing dispersed cellular and macromolecular materials, etc.; and (iii) emulsions, foams, gels, micellar systems, etc., which have a wide range of applications. However, fluid characterization is far more complex than what is usually expected, as each material has its own behavior when subjected to flow, deformation or stress. Suspensions differ in an essential way from polymeric liquids where the polymer chains influence rheology through their flexibility. Unlike polymer solutions, where chains introduce elasticity due to their tendency to recover after flow-induced stretching, suspended particles are stressed because they cannot deform.
An important characteristic of viscous fluids depends on the type of flow: (i) the shear flow which is defined by the shear rate ⋅γ and (ii) the elongational flow which is illustrated by the flow through a small orifice and where the velocity gradient along the flow must be taken into account.
For some viscous fluids the viscosity η does not depend on the shear rate ⋅γ, these are the Newtonian fluids, for other one the viscosity η depends on the shear rate ⋅γ, these are the non-Newtonian fluids. Non-Newtonian rheology of suspensions presupposes the well-known dependence of viscosity on the shear rate. When η is an increasing function of ⋅γ, the fluids are called shear-thickening (wet sand, mixture of cornstarch and water, etc.), when η is a decreasing function of ⋅γ, the fluids are said to be shear-thinning (blood, paint, ketchup, etc.). Non-Newtonian behavior of fluids can be caused by several factors, all of them related to structural reorganization of the fluid molecules due to flow. In polymer melts and solutions, it is the alignment of highly anisotropic chains what results in a decreased viscosity. In colloidal suspensions, it is the blending of the different phases in the flow that causes shear thinning behavior (fluidized-bed technique).
As the viscosity of colloidal suspensions is concerned, Einstein showed that the fluid may be assimilated to a homogeneous effective viscosity medium ηeff whose expression is:
ηeff=η(1+52φ) | (5.10) |
where η is the viscosity of initial fluid and φ the particle volume fraction. Equation (5.10) is correct as far as particle volume fraction is lower than φ∼0.4 for which the interparticle distance is between 5R and 10R. For higher particle volume fractions, the presence of neighbor particles can no more be neglected, and the interparticle interactions have to be taken account, leading to a supplementary term proportional to the square of φ, namely:
ηeff=η(1+52φ+kφ2) | (5.11) |
where the parameter k which is between 5 and 7 depends on diffusion time τD. Later, the influence of larger particle volume fractions has been studied by Krieger [11] who proposed the following expression:
ηeff=η(1−φφm)−1.82 | (5.12) |
where φm is the maximum particle volume fraction for which the viscosity of the system diverges, and which is equal to 0.68 for hard spheres. In the limit of low particle volume fractions the effective viscosity is ηeff=η(1+2.68 φ), close to the relationship proposed by Eisntein.
Adding particles to a colloidal suspension increases its viscosity. However, for the rheology of non-Newtonian fluids, great care must be taken before concluding how viscosity depends on the shear rate. It is a matter of fact that the viscosity of a suspension subjected to elongational flow is not the same as that of the same suspension subjected to shear flow due to temporary particle chain formation. Thus, the viscosity depends on nature and velocity of the flow to which the suspension is subjected, and can also depend on time.
Dilute suspensions behave like homogeneous Newtonian fluids with a viscosity ηeff greater than that of the suspending fluid η. This remarkably simple result is general as it does not depend on the Brownian or non-Brownian character of particles, nor on the nature of flow in which the particles are found. The only assumption made for the demonstration of Eq (5.10) is the absence of hydrodynamic interactions between particles, as initially recommended by Einstein.
It has been shown that the sedimentation rate Vs of a dilute suspension of spheres of particle volume fraction φ is lower than that of an isolated sphere Vso. Taking into account the interparticle interactions in a dilute suspension (φ<0.1) towards a distant plane, the sedimentation rate is approximately [12]:
Vs(C)=Vso(1−6.5φ) | (5.13) |
At high concentrations, the interactions between particles increase and their relative motions become negligible as the particle volume fraction φ approaches the value φm∼0.68 corresponding to a static stacking of particles. As long as φ remains below 0.5, the empirical Richardson-Zaki [13] expression is frequently used:
Vs(C)=Vso(1−C)5.5 | (5.14) |
For particles of the same size and values of φ>0.2, it is observed that the distribution of the particles going to aggregate varies with the vertical distance in the solution. Particles at the top of flow move faster than those at the bottom, resulting in a vertical concentration gradient. In addition, situations are often observed in which an alternation of more or less dense zones is formed in which the velocity increases when the concentration decreases, and vice versa according to Eq (5.14). This phenomenon is to be compared to that which is at the origin of traffic jams which form on highways when the traffic becomes too dense. It is also to be compared to the case of a flow with high particle concentration which is similar to the flow in a porous medium, where all the particles remain fixed and the fluid circulates in the cavities.
Sometimes there are heterogeneities of particle concentration in a horizontal plane giving rise to a horizontal concentration gradient which induces a vertical recirculation motion. It then forms two flows of different densities: one loaded with sediments going down to the lower part, the other lighter going up to the upper part. Similar phenomenon has been discovered by Boycott [14] by studying the sedimentation of red blood cells in a test tube; these motions can be favored by the geometry of the walls. A faster sedimentation is observed in an inclined tube than in a vertical tube, as the suspended sediments quickly accumulates against the bottom wall of the tube thus releasing a reflux along the opposite wall [15].
Rheological tools offer large perspectives of analysis which can be applied to complex systems. As already mentioned, flow of suspensions have broad applications both in natural phenomena and industrial processes. Despite its long research activity and its practical relevance, rheology of suspensions is far from being completely understood. Studies have been undertaken to examine how the rheology of dense suspensions is influenced by the nature of fluid (blood [16], biologic fluids [17]) and the shape of particles [18] (dry granular materials [19], suspensions of fibers [20]). We hope that this article will be of interest to people wishing to deepen their knowledge on the rheology of suspensions.
No potential conflict of interest was reported by the authors.
[1] | Stokes GG (1850) On the effect of the internal friction of Fluids on the Motion of pendulums. Trans Camb Phil Soc 9. |
[2] | Guyon E, Hulin JP, Petit L, et al. (2012) Hydrodynamique Physique, France: EDP Sciences. |
[3] | Bretonnet JL (2020) Statistical Mechanics for the Liquid State, Cambridge Scholars Publishing. |
[4] |
Tazzioli R (2017) D'Alembert's paradox, 1900–1974: Levi-Civita and his Italian and French followers. CR Mecanique 345: 488–497. doi: 10.1016/j.crme.2017.05.006
![]() |
[5] |
Morris JF (2009) A review of microstructure in concentrated suspensions and its implications for rheology and bulk flow. Rheol Acta 48: 909–937. doi: 10.1007/s00397-009-0352-1
![]() |
[6] | Guazzeli E, Morris JF (2012) A Physical Introduction to Suspension Dynamics, Cambridge University Press. |
[7] |
Khan AR, Richardson JF (1987) The resistance to motion of a solid sphere in a fluid. Chem Eng Commun 62:135–150. doi: 10.1080/00986448708912056
![]() |
[8] |
Brenner H (1961) The slow motion of a sphere through a viscous fluid towards a plan surface. Chem Eng Sci 16: 242–251. doi: 10.1016/0009-2509(61)80035-3
![]() |
[9] | Landau L, Lifschitz E (1959) Fluid Mechanics, 2 Eds., Pergamon Press. |
[10] | Oseen CW (1910) Über die Stokes'sche formel, und über eine verwandte Aufgabe in der Hydrodynamik. Arkiv Mat Astron Phsik 6: 29. |
[11] | Krieger JM (1972) Rheology of monodisperse latices. Adv Colloid Interfac 3: 111–136. |
[12] | Kim S, Karrila SJ (1991) Microhydrodynamics: Principles and Selected Applications, Butterworth-Heinemann. |
[13] | Richardson JF, Zaki WN (1954) Sedimentation and fluidisation: part I. Trans Inst Chem Eng 32: 35–53. |
[14] | Boycott AE (1920) Sedimentation of blood corpuscles. Nature 104: 532. |
[15] |
Peacock T, Blanchette F, Bush JWM (2005) The stratified Boycott effect. J Fluid Mech 529: 33–49. doi: 10.1017/S002211200500337X
![]() |
[16] |
Brust M, Schaefer C, Doerr R, et al. (2013) Rheology of human blood plasma: Viscoelastic versus Newtonian behavior. Phys Rev Lett 110: 078305. doi: 10.1103/PhysRevLett.110.078305
![]() |
[17] |
Herrera-Valencia EE, Calderas F, Medina-Torres L, et al.(2017) On the pulsating flow behavior of a biological fluid: human blood. Rheol Acta 56: 387–407. doi: 10.1007/s00397-017-0994-3
![]() |
[18] | Lamb H (1945) Hydrodynamics, 6 Eds., Dover publications. |
[19] |
Jop P, Forterre Y, Pouliquen O (2005) Crucial role of sidewalls in granular surface flows: Consequences for the rheology. J Fluid Mech 541: 167–192. doi: 10.1017/S0022112005005987
![]() |
[20] |
Snook B, Davidson LM, Butler JE, et al.(2014) Normal stress differences in suspensions of rigid fibres. J Fluid Mech 758: 486–507. doi: 10.1017/jfm.2014.541
![]() |
1. | Jean François Wax, Nadra Harchaoui, Hong Xu, Stokes-Einstein Relation in Pure Alkali Metals and their Alloys, 2022, 420, 1662-9507, 205, 10.4028/p-5j6wz0 |