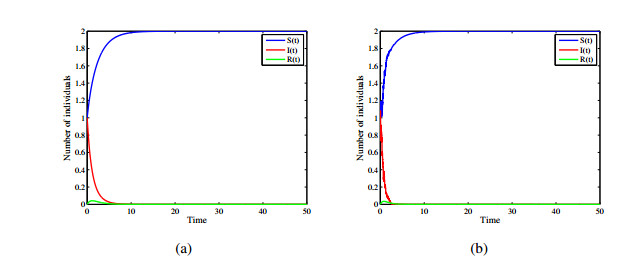
Citation: Ojo Sunday Isaac Fayomi, Adedamola Sode, Itopa Godwin Akande, Abimbola Patricia Idowu Popoola, Oluranti Agboola. Improving the structural properties and corrosion behaviour of electroless deposited Ni-P-Zn coatings on mild steel for advanced processes[J]. AIMS Materials Science, 2020, 7(4): 441-452. doi: 10.3934/matersci.2020.4.441
[1] | Wenjie Yang, Qianqian Zheng, Jianwei Shen, Linan Guan . Bifurcation and pattern dynamics in the nutrient-plankton network. Mathematical Biosciences and Engineering, 2023, 20(12): 21337-21358. doi: 10.3934/mbe.2023944 |
[2] | Xuehui Ji, Sanling Yuan, Tonghua Zhang, Huaiping Zhu . Stochastic modeling of algal bloom dynamics with delayed nutrient recycling. Mathematical Biosciences and Engineering, 2019, 16(1): 1-24. doi: 10.3934/mbe.2019001 |
[3] | Abdelheq Mezouaghi, Salih Djillali, Anwar Zeb, Kottakkaran Sooppy Nisar . Global proprieties of a delayed epidemic model with partial susceptible protection. Mathematical Biosciences and Engineering, 2022, 19(1): 209-224. doi: 10.3934/mbe.2022011 |
[4] | Lizhong Qiang, Ren-Hu Wang, Ruofan An, Zhi-Cheng Wang . A stage-structured SEIR model with time-dependent delays in an almost periodic environment. Mathematical Biosciences and Engineering, 2020, 17(6): 7732-7750. doi: 10.3934/mbe.2020393 |
[5] | Jean-Jacques Kengwoung-Keumo . Competition between a nonallelopathic phytoplankton and an allelopathic phytoplankton species under predation. Mathematical Biosciences and Engineering, 2016, 13(4): 787-812. doi: 10.3934/mbe.2016018 |
[6] | Da Song, Meng Fan, Ming Chen, Hao Wang . Dynamics of a periodic stoichiometric model with application in predicting and controlling algal bloom in Bohai Sea off China. Mathematical Biosciences and Engineering, 2019, 16(1): 119-138. doi: 10.3934/mbe.2019006 |
[7] | Kazuo Yamazaki, Xueying Wang . Global stability and uniform persistence of the reaction-convection-diffusion cholera epidemic model. Mathematical Biosciences and Engineering, 2017, 14(2): 559-579. doi: 10.3934/mbe.2017033 |
[8] | Lin Zhao, Zhi-Cheng Wang, Liang Zhang . Threshold dynamics of a time periodic and two–group epidemic model with distributed delay. Mathematical Biosciences and Engineering, 2017, 14(5&6): 1535-1563. doi: 10.3934/mbe.2017080 |
[9] | Yun Kang, Sourav Kumar Sasmal, Amiya Ranjan Bhowmick, Joydev Chattopadhyay . Dynamics of a predator-prey system with prey subject to Allee effects and disease. Mathematical Biosciences and Engineering, 2014, 11(4): 877-918. doi: 10.3934/mbe.2014.11.877 |
[10] | Shengqiang Liu, Lin Wang . Global stability of an HIV-1 model with distributed intracellular delays and a combination therapy. Mathematical Biosciences and Engineering, 2010, 7(3): 675-685. doi: 10.3934/mbe.2010.7.675 |
Mathematical models describing the population dynamics of infectious diseases have been playing an important role in better understanding of epidemiological patterns and disease control for a long time (see [1,2,3,4]). Some infectious diseases confer temporary or permanent immunity. For some diseases, such as cholera, pertussis and influenza, temporary immunity may disappear after some time. And recovered individuals will become susceptible after losing the temporary immunity. This kind of diseases can be modeled by SIRS models (see [5,6]). In addition, for some bacterial agent diseases such as meningitis and venereal diseases, recovery cannot generate immunity for a long time. Infected individuals may recover after some treatments and go back directly to the susceptible class on account of the presence of temporary antibodies. In [6], the authors investigated the following SIRS epidemic model with a nonlinear incidence βSf(I) and transfer from the infected class to the susceptible class
{˙S(t)=Λ−μS(t)−βS(t)f(I(t))+γ1I(t)+δR(t),˙I(t)=βS(t)f(I(t))−(μ+γ1+γ2+α)I(t),˙R(t)=γ2I(t)−(μ+δ)R(t), | (1.1) |
with the initial conditions
S(0)=S0≥0,I(0)=I0≥0,R(0)=R0≥0, | (1.2) |
where S(t), I(t) and R(t) are respectively the number of susceptible, infectious and recovered individuals at time t. Λ is the recruitment rate of susceptible individuals, μ is the natural death rate, α is the mortality caused by the disease, γ1 denotes the transfer rate from the infected class to the susceptible class, γ2 is the recovery rate of the infective individuals, δ is the rate constant for loss of immunity. Suppose that Λ and μ are positive, while α, γ1, γ2 and δ are nonnegative. f is a real locally Lipschitz function on R+=[0,∞) satisfying f(0)=0, f(I)>0, f(I)/I is nonincreasing for I>0 and limI→0+f(I)I=f′(0)>0.
Denote R3+={(x,y,z)∈R3:x>0,y>0,z>0}. From [6], model (1.1) always has a disease-free equilibrium E0=(S0,I0,R0)=(Λμ,0,0). By using the next generation matrix method, [6] obtained the basic reproduction number R0=Λβf′(0)μ(μ+γ1+γ2+α). Further, E0 is globally asymptotically stable in D if R0<1, where D={(S,I,R)∈R3+:S+I+R≤Λμ}. If R0>1, there exists a globally asymptotically stable endemic equilibrium E∗=(S∗,I∗,R∗).
However, model (1.1) is just a deterministic model. In the real world, epidemic models are always affected by the environmental noise. Stochastic models may be a more appropriate way of modeling epidemics in many circumstances (see [7,8,9,10]). In [11,12,13], the authors investigated the stochastic SIS epidemic models. In [14,15,16,17,18,19,20], the authors investigated the stochastic SIRS epidemic models. In this paper, we investigate the following stochastic SIRS epidemic model
{dS=[Λ−μS−βSf(I)+γ1I+δR]dt−σSf(I)dB(t),dI=[βSf(I)−(μ+γ1+γ2+α)I]dt+σSf(I)dB(t),dR=[γ2I−(μ+δ)R]dt, | (1.3) |
with initial values S0>0,I0>0,R0>0. Here we consider random perturbation in the environment, which is assumed to be affected by the contact rate, so that β→β+σ˙B(t), where B(t) is a standard Brownian motions defined on the compete probability space (Ω,F,P) with a filtration {Ft}t≥0 satisfying the usual conditions (i.e. it is right continuous and F0 contains all P-null sets). σ2 represents the intensity of B(t). Other parameters are defined as system (1.1). Model (1.3) covers many existing stochastic models in [6,9,21,22,23] as special cases. For example, an epidemic model with relapse and bilinear incidence was formulated in [9]. In [21], the authors investigated the dynamics of a stochastic SIR epidemic model with saturated incidence. In [22], extinction and persistence of a stochastic SIRS epidemic model with saturated incidence rate and transfer from infectious to susceptible were considered. In [23], the authors proposed a class of stochastic SIRS epidemic models with nonlinear incidence
{dS=[Λ−μS−βh(S)f(I)+δR]dt−σh(S)f(I)dB(t),dI=[βh(S)f(I)−(μ+γ+α)I]dt+σh(S)f(I)dB(t),dR=[γI−(μ+δ)R]dt, | (1.4) |
where h(S) is continuously differentiable and monotonically increasing with respect to S, h(0)=0 and for any constant l>0, Ml:=sup0<S≤lh(S)S<∞; f(I) is nonnegative and twice continuously differentiable, f(I)/I is monotonically decreasing with respect to I, f(0)=0 and f′(0)>0. Other parameters are defined as those of system (1.3). In [23], the sufficient conditions for the extinction and persistence of the disease for model (1.4) were discussed. Compared with model (1.3), model (1.4) does not include the transfer from infectious to susceptible, although the incidence rate is more general.
Denote a∧b=min{a,b} for a,b∈R and E(X) represents the exception of random variable X. Throughout this paper, we give the following assumptions.
(H1) f(0)=0, f(I)>0 holds for I>0 and f is a real locally Lipschitz function on R+;
(H2) f(I)/I is nonincreasing on (0,+∞) and f′(0)>0;
(H3) There is a constant ϑ>0, such that
|f(x1)/x1−f(x2)/x2|≤ϑ|x1−x2|foranyx1,x2∈(0,Λ/μ]. |
One can easily see from (H2) that
f(I)≤f′(0)IforI∈R+. | (1.5) |
Our general results can be applied to some specific forms of the incidence rate, for instance:
(ⅰ) linear type: f(I)=I (see [9]);
(ⅱ) saturated incidence rate: f(I)=I1+aI (see [21,22]);
(ⅲ) non-monotonic incidence rate: f(I)=I1+aI2 (see [24]);
(ⅳ) incidence rate with "media coverage": f(I)=Ie−mI, where m is a positive constant (see [25]);
(ⅴ) incidence rate with "media coverage": f(I)=(1−˜βIβ(m+I))I, where m,β,˜β are all positive constants and β>˜β (see [26]).
Our aim is to investigate how white noise affects the spread of disease, as described by model (1.3). The remaining part of this paper is organized as follows. In Section 2, a unique global positive solution of stochastic model (1.3) with any positive initial value is proved. Sufficient conditions for disease extinction and persistence in the mean are given in Sections 3 and 4, respectively. In addition, we discuss the relationship between R0 and Rs for different values of white noise intensity σ2, and summarize a useful criterion for the extinction and persistence of the disease of model (1.3). In Section 5, some examples and numerical simulations are provided to illustrate the theoretical results. The paper ends with a conclusion that the intensity of noise plays an important role in epidemic dynamics.
Since S(t), I(t) and R(t) in model (1.3) are respectively the numbers of the susceptible individuals, infected individuals and recovered individuals at time t, they should be non-negative. Therefore, we are only interested in its positive solutions. In this section, we show that model (1.3) has a unique global positive solution with positive initial value by using the Lyapunov analysis method.
Theorem 1. Suppose that (H1) and (H2) hold. Model (1.3) has a unique global positive solution (S(t),I(t),R(t)) on [0,∞) for any (S0,I0,R0)∈R3+, that is, the solution will remain in R3+ with probability one.
Proof. From (H1), it is easy to show that the coefficients of (1.3) are locally Lipschitz continuous. Thus, for any given initial value (S0,I0,R0)∈R3+, there is a unique maximal local solution (S(t),I(t),R(t)) on [0,τe), where τe is the explosion time. Now we show τe=∞ a.s. Let n0>0 be sufficiently large such that S0,I0 and R0 all lie within the interval (1n0,n0). For each integer n≥n0, define the stopping time
τn=inf{t∈[0,τe):min{S,I,R}≤1normax{S,I,R}≥n}, |
where throughout this paper, we set inf∅=∞. Clearly, τn is increasing as n→∞. Let τ∞=limn→∞τn. Thus τ∞≤τe a.s. If we can show that τ∞=∞ a.s., then τe=∞ and (S(t),I(t),R(t))∈R3+ a.s. for all t≥0.
Now, we show that τ∞=∞ a.s. Otherwise, there is a pair of constants T>0 and ε∈(0,1) such that P{τ∞≤T}>ε. Hence, for all n≥n0
P(Ωn)≥ε, | (2.1) |
where Ωn={ω∈Ω:τn(ω)≤T}. Moreover, for any n≥n0 and t≤τn,
d[S(t)+I(t)+R(t)]≤[Λ−μ(S(t)+I(t)+R(t))]dt, |
which implies
S(t)+I(t)+R(t)≤{Λμ,ifS0+I0+R0≤Λμ,S0+I0+R0,ifS0+I0+R0>Λμ. |
Denote K=max{Λμ,S0+I0+R0}. Then
S(t)+I(t)+R(t)≤K | (2.2) |
for any t≤τn. Define a C2-function V:R3+→R+ by
V(S,I,R)=(S−1−lnS)+(I−1−lnI)+(R−1−lnR). |
For any n≥n0, the Itˆo formula shows that
EV(S(τn∧T),I(τn∧T),R(τn∧T))=V(S0,I0,R0)+E∫τn∧T0LV(S(s),I(s),R(s))ds, | (2.3) |
where LV:R3+→R is defined by
LV(S,I,R)=(1−1S)(Λ−μS−βSf(I)+γ1I+δR)+(1−1I)(βSf(I)−(μ+γ1+γ2+α)I)+(1−1R)(γ2I−(μ+δ)R)+σ2f2(I)2+σ2S2f2(I)2I2=Λ+μ+(μ+γ1+γ2+α)+(μ+δ)+βf(I)−(μ+α)I+σ2f2(I)2+σ2S2f2(I)2I2−ΛS−γ1IS−δRS−γ2IR−βSf(I)I−μS−μR. |
From (1.5) and (2.2), for any 0≤t≤τn∧T
LV(S,I,R)≤Λ+μ+(μ+γ1+γ2+α)+(μ+δ)+βf′(0)I+σ22I2+σ22S2≤Λ+μ+(μ+γ1+γ2+α)+(μ+δ)+βf′(0)K+σ2K2=:M |
Thus, from (2.3), it follows that
EV(S(τn∧T),I(τn∧T),R(τn∧T))≤V(S0,I0,R0)+ME(τn∧T)≤V(S0,I0,R0)+MT, |
for any n≥n0. Note that for every ω∈Ωn, there exists S(τn,ω), I(τn,ω) or R(τn,ω) that equals either 1/n or n. Hence
V(S(τn,ω),I(τn,ω),R(τn,ω))≥(n−1−lnn)∧(1n−1+lnn). |
It follows from (2.1) that
V(S0,I0,R0)+MT≥E[IΩn(ω)V(S(τn,ω),I(τn,ω),R(τn,ω))]≥ε[(n−1−lnn)∧(1n−1+lnn)], |
where IΩn is the indicator function of Ωn. Letting n→∞ leads to the contradiction
∞>V(S0,I0,R0)+MT=∞, |
therefore we have τ∞=∞ a.s. The proof is therefore complete.
Remark 1. Theorem 1 shows that for any initial value (S0,I0,R0)∈R3+, model (1.3) has a unique global solution (S(t),I(t),R(t))∈R3+ a.s. In addition, it follows from model (1.3) that
d[S(t)+I(t)+R(t)]=[Λ−μ(S(t)+I(t)+R(t))−αI(t)]dt≤[Λ−μ(S(t)+I(t)+R(t))]dt. |
Thus, S(t)+I(t)+R(t)≤(S0+I0+R0−Λμ)e−μt+Λμ, which implies
lim supt→∞(S(t)+I(t)+R(t))≤Λμ. |
Moreover, if S0+I0+R0≤Λμ, then S(t)+I(t)+R(t)≤Λμ a.s.. Therefore, the region
D={(S,I,R)∈R3+:S+I+R≤Λμ} |
is a positively invariant set of model (1.3).
For simplicity, we introduce the notations X(t)=S(t)+I(t)+R(t), ⟨x(t)⟩=1t∫t0x(s)ds.
One of the main concerns in epidemiology is how we can regulate the disease dynamics so that the disease will be eradicated in a long term. In this section, we provide the sufficient conditions for extinction of the disease in model (1.3). Denote
Rs=Λβf′(0)μ(μ+γ1+γ2+α)−Λ2σ2(f′(0))22μ2(μ+γ1+γ2+α),Φ(x)=−σ22x2+βx−(μ+γ1+γ2+α). |
For model (1.3), we give the following conditions.
(C1) Rs<1, σ2≤βμΛf′(0) and σ2≤βμΛf′(0)⋅R02;
(C2) Rs<1, βμΛf′(0)⋅R02<σ2<βμΛf′(0);
(C3) Rs<1, σ2≥βμΛf′(0) and σ2>βμΛf′(0)⋅R02;
(C4) Rs≥1, σ2>βμΛf′(0)⋅R02.
In addition, denote A1=(μ+γ1+γ2+α)(Rs−1), A2=−[(μ+γ1+γ2+α)−β22σ2].
Theorem 2. Suppose that (H1) and (H2) hold. Let (S(t),I(t),R(t)) be the solution of model (1.3) with any given initial condition (S0,I0,R0)∈R3+.
(i) If (C1) holds, then lim supt→∞lnI(t)t≤A1<0a.s.
(ii) If (C2) holds, then lim supt→∞lnI(t)t≤min{A1,A2}<0a.s.
(iii) If (C3) or (C4) holds, then lim supt→∞lnI(t)t≤A2<0a.s.
Furthermore,
limt→∞S(t)=Λμ,limt→∞I(t)=0,limt→∞R(t)=0a.s. |
Proof. Applying Itˆo formula to the second equation of model (1.3) leads to
dlnI(t)=[βSf(I)I−(μ+γ1+γ2+α)−σ22(Sf(I)I)2]dt+σSf(I)IdB(t). |
Integrating both sides of the above equation from 0 to t, yields
lnI(t)=∫t0[βSf(I)I−(μ+γ1+γ2+α)−σ22(Sf(I)I)2]ds+∫t0σSf(I)IdB(s)+lnI0=∫t0Φ(Sf(I)I)ds+M1(t)+lnI0, | (3.1) |
where M1(t)=∫t0σSf(I)IdB(s).
Let us discuss three cases separately.
Case 1. Assume that Rs<1 and σ2<βμΛf′(0). Then Λf′(0)μ<βσ2 and Φ(Λf′(0)μ)=(μ+γ1+γ2+α)(Rs−1)<0. For any 0<ε<βσ2f′(0)−Λμ sufficiently small, we have (Λμ+ε)f′(0)<βσ2 and Φ((Λμ+ε)f′(0))<0. From Remark 1, for any ε>0, there exists a constant T=T(ε)>0 such that S(t)≤Λμ+ε for all t>T. Then it follows from (1.5) that
Φ(Sf(I)I)≤Φ(f′(0)S)≤Φ(f′(0)(Λμ+ε))<0. |
Substituting this into (3.1), we have
lnI(t)t=1t∫T0Φ(Sf(I)I)ds+1t∫tTΦ(Sf(I)I)ds+M1(t)t+lnI0t≤1t∫T0Φ(Sf(I)I)ds+1t∫tTΦ(f′(0)(Λμ+ε))ds+M1(t)t+lnI0t=1t∫T0Φ(Sf(I)I)ds+Φ(f′(0)(Λμ+ε))(1−Tt)+M1(t)t+lnI0t. | (3.2) |
Clearly, M1(t) is a real-valued continuous local martingale vanishing at time 0 and
⟨M1,M1⟩t=∫T0[σSf(I)I]2ds+∫tT[σSf(I)I]2ds≤∫T0[σSf(I)I]2ds+σ2(f′(0))2(Λμ+ε)2(t−T). |
Note that
lim supt→∞⟨M1,M1⟩tt≤σ2(f′(0))2(Λμ+ε)2<∞, |
then, from the strong law of large numbers (see [27]), it follows that
limt→∞M1(t)t=limt→∞1t∫t0σSf(I)IdB(s)=0a.s. | (3.3) |
From (3.2) and (3.3), we have
lim supt→∞lnI(t)t≤Φ(f′(0)(Λμ+ε))<0a.s. |
By the continuity of Φ(t) and the arbitrariness of ε, we obtain
lim supt→∞lnI(t)t≤Φ(Λf′(0)μ)=(μ+γ1+γ2+α)(Rs−1)<0a.s. |
Case 2. Assume that Rs<1 and σ2=βμΛf′(0). Then Λf′(0)μ=βσ2 and Φ(Sf(I)I)≤Φ(Λf′(0)μ)<0. The following proof is similar to that of Case 1.
Case 3. Assume that σ2>βμΛf′(0)⋅R02. Since
Φ(x)=−σ22(x−βσ2)2+β22σ2−(μ+γ1+γ2+α)≤−[(μ+γ1+γ2+α)−β22σ2]. |
Substituting this into (3.1), we have
lnI(t)t≤−[(μ+γ1+γ2+α)−β22σ2]+M1(t)t+lnI0t. | (3.4) |
This, together with (3.3), yields
lim supt→∞lnI(t)t≤−[(μ+γ1+γ2+α)−β22σ2]<0a.s.. |
From the proofs of Cases 1-3, it is easy to see that conclusions (ⅰ)-(ⅲ) hold. Further, if one of conditions (C1)–(C4) holds, then
limt→∞I(t)=0a.s. | (3.5) |
That is to say, the disease I(t) dies out with probability one.
Next, we show limt→∞R(t)=0 a.s. Let Ω1={ω∈Ω:limt→∞I(t,ω)=0}, then (3.5) implies P(Ω1)=1. Hence, for any ω∈Ω1 and any constant ε1>0, there exists a constant T1=T1(ω,ε1)>0 such that for any t≥T1
I(t,ω)≤ε1. | (3.6) |
Substituting this into the third equation of model (1.3), we obtain
dR(t,ω)≤[γ2ε1−(μ+δ)R(t,ω)]dt,ω∈Ω1,t≥T1. |
Then, from the comparison theorem, it follows that
lim supt→∞R(t,ω)≤γ2ε1μ+δ,ω∈Ω1. |
Since R(t,ω)>0 for all ω∈Ω1 and t>0, by the arbitrariness of ε1, we get limt→∞R(t,ω)=0, ω∈Ω1. It follows from P(Ω1)=1 that
limt→∞R(t)=0a.s. | (3.7) |
At last, we prove the assertion limt→∞S(t)=Λμ a.s. It follows from model (1.3) that
dX(t)=[Λ−μX(t)−αI(t)]dt, |
which implies
d(eμtX(t))=eμt[Λ−αI(t)]dt. | (3.8) |
For any t>T, integrating both sides of (3.8) from T to t and using (3.6), we obtain that for any ω∈Ω1
X(t,ω)=e−μ(t−T)X(T,ω)+∫tTe−μ(t−s)[Λ−αI(s)]ds≥e−μ(t−T)X(T,ω)+∫tTe−μ(t−s)[Λ−αε1]ds=e−μ(t−T)X(T,ω)+Λ−αε1μ[1−e−μ(t−T)]. |
Thus, for any ω∈Ω1, we have lim inft→∞X(t,ω)≥Λ−αε1μ, which, together with the arbitrariness of ε1, yields
lim inft→∞X(t,ω)≥Λμ,forallω∈Ω1. |
From P(Ω1)=1, we get lim inft→∞X(t)≥Λμ a.s. On the other hand, from Remark 1, it follows that lim supt→∞X(t)≤Λμ. Thus, we have
limt→∞X(t)=limt→∞[S(t)+I(t)+R(t)]=Λμa.s., |
which, together with (3.5) and (3.7), yields
limt→∞S(t)=Λμa.s. |
The proof is therefore complete.
Remark 2. Theorem 2 shows that the disease of system (1.3) dies out with probability one if Rs<1 and σ2<βμΛf′(0). Moreover, we note Rs in Theorem 2 is smaller than the basic reproduction number R0 of system (1.1), and hence environmental noise may lead the disease to extinction. If σ=0, then system (1.3) can be reduced to system (1.1). Further, Theorem 2 is consistent with the result in [6].
Remark 3. If we let f(I)=I1+aI,γ1=0,γ2=γ,δ=0, system (1.3) can be transformed into system (1.3) in [21]. From Theorem 2, it follows that for any initial condition (S0,I0,R0)∈R3+, if one of conditions (C1)–(C4) holds then the disease of system (1.3) will extinct with probability one. However, Theorem 3.1 in [21] shows that for any initial condition (S0,I0,R0)∈Γ, if σ2>β22(μ+γ+α), then the disease of system (1.3) will tend to zero exponentially with probability one. Obviously, Theorem 2 generalizes and improves the corresponding result in [21].
Remark 4. Let f(I)=I1+aI, system (1.3) can be changed into (1.2) in [22]. Theorem 2 shows that the disease of system dies out with probability one. Particularly, if Rs≥1 and βμΛ⋅R02<σ2<βμΛ, Theorem 2 in this paper shows the extinction of the disease; however, Theorem 3.2 in [22] can not show the extinction of the disease. Furthermore, we obtain limt→∞S(t)=Λμ and limt→∞R(t)=0a.s. But, only the disease extinction is found in Theorem 3.2 in [22]. Therefore, Theorem 2 in this paper improves and generalizes Theorem 3.2 in [22].
Remark 5. Let h(S)=S,γ1=0,γ2=γ. From Theorem 2, extinction of model (1.3) requires that f(I) is a real locally Lipschitz function on R+. However, from Corollary 1 in [23], extinction of model (1.3) requires that f(I) is twice continuously differentiable on R+. Obviously, the conditions of Theorem 2 are weaker than those of Corollary 1 in [23].
When considering epidemic models, we are interested in when the disease will prevail in the population. In the deterministic models, the problem can be solved by proving that the endemic equilibrium of the corresponding model is globally asymptotically stable. But for model (1.3), there is no endemic equilibrium. In this section, we will establish sufficient conditions to ensure that the disease in model (1.3) is permanent in the time mean. Now, we give the definition of persistence in the mean as follows.
Definition 1. Model (1.3) is said to be persistent in the mean if lim inft→∞⟨I(t)⟩>0 a.s.
For the convenience, we give the following useful lemma.
Lemma 1. (See [28]). Suppose x∈C(Ω×[0,+∞),R+) and F∈C(Ω×[0,+∞),(−∞,+∞)). If there are three positive constants λ, λ0 and T such that
lnx(t)≥λt−λ0∫t0x(s)ds+F(t),a.s.,forallt≥T, |
where limt→∞F(t)t=0 a.s., then lim inft→∞1t∫t0x(s)ds≥λλ0 a.s.
Theorem 3. Suppose that (H1)−(H3) hold. Let (S(t),I(t),R(t)) be the solution of model (1.3) with any given initial condition (S0,I0,R0)∈R3+. If Rs>1, then
(i)lim inft→∞⟨S(t)⟩≥Λμμ2+Λβf′(0)>0a.s.;(ii)lim inft→∞⟨I(t)⟩≥μ2Φ(Λf′(0)μ)βΛ(f′(0))2(1−Λσ2f′(0)2μβ)(μϑ+β)>0a.s.;(iii)lim inft→∞⟨R(t)⟩≥γ2μ2Φ(Λf′(0)μ)(μ+δ)βΛ(f′(0))2(1−Λσ2f′(0)2μβ)(μϑ+β)>0a.s. |
Proof. From Remark 1, it follows that, for any 0<ε<2βσ2f′(0)(1−Λσ2f′(0)2μβ), there exists a constant T=T(ε)>0 such that X(t)≤Λμ+ε for all t≥T. Note that 0<f(I)≤f′(0)I, then from the first equation of model (1.3), we can derive that
S(t)−S0≥∫T0[Λ−μS(s)−βS(s)f(I(s))]ds+∫tT[Λ−μS(s)−βf′(0)(Λμ+ε)S(s)]ds−∫t0σS(s)f(I(s))dB(s)=∫T0[Λ−μS(s)−βS(s)f(I(s))]ds+∫tT[Λ−(μ+βf′(0)(Λμ+ε))S(s)]ds−∫t0σS(s)f(I(s))dB(s), |
which implies
(μ+βf′(0)(Λμ+ε))1t∫t0S(s)ds≥Λ−ΛTt−S(t)−S0t−M2(t)t+1t∫T0[Λ−μS(s)−βS(s)f(I(s))]ds, | (4.1) |
where M2(t)=∫t0σS(s)f(I(s))dB(s). Clearly, M2(t) is a real-valued continuous local martingale vanishing at time 0 and
⟨M2,M2⟩t=∫T0[σS(s)f(I(s))]2ds+∫tT[σS(s)f(I(s))]2ds≤∫T0[σS(s)f(I(s))]2ds+σ2(f′(0))2(Λμ+ε)4(t−T). |
Note that lim supt→∞⟨M2,M2⟩tt≤σ2(f′(0))2(Λμ+ε)4<∞. Then, from the strong law of large numbers (see [27]), it follows that
limt→∞M2(t)t=limt→∞1t∫t0σS(s)f(I(s))dB(s)=0a.s. | (4.2) |
This, together with (4.1), yields
lim inft→∞1t∫t0S(s)ds≥Λμ+βf′(0)(Λμ+ε)a.s., |
From the arbitrariness of ε, it follows that
lim inft→∞1t∫t0S(s)ds≥Λμμ2+Λβf′(0)>0a.s., |
In the following, we will prove that (ⅱ) holds. Note that S(t)≤Λμ+ε for all t≥T and 0<f(I)≤f′(0)I, then, for any t≥T, 0<Sf(I)I≤f′(0)S≤f′(0)(Λμ+ε), which implies 0<Sf(I)f′(0)(Λμ+ε)I≤1. Then, we have
Φ(Sf(I)I)−Φ(f′(0)(Λμ+ε))≥−βf′(0)[1−σ2f′(0)2β(Λμ+ε)](Λμ+ε−Sf(I)f′(0)I). |
That is,
Φ(Sf(I)I)≥Φ(f′(0)(Λμ+ε))−βf′(0)[1−σ2f′(0)2β(Λμ+ε)](Λμ+ε−Sf(I)f′(0)I). |
Substituting this into (3.1) yields
lnI(t)≥∫T0Φ(Sf(I)I)ds+Φ(f′(0)(Λμ+ε))(t−T)+M1(t)+lnI0−βf′(0)[1−σ2f′(0)2β(Λμ+ε)]∫tT(Λμ+ε−Sf(I)f′(0)I)ds. | (4.3) |
In addition, from the first equation of model (1.3), it follows that
S(t)−S(T)=∫tT[Λ−μS(s)−βS(s)f(I(s))+γ1I(s)+δR(s)]ds−∫tTσS(s)f(I(s))dB(s)≥∫tT[Λ−μS(s)−βS(s)f(I(s))]ds−∫tTσS(s)f(I(s))dB(s)=∫tT[μ(Λμ+ε−S(s)f(I(s))f′(0)I(s))−μS(s)(1−f(I(s))f′(0)I(s))−με−βS(s)f(I(s))]ds−M2(t). | (4.4) |
By the Assumption (H3), we know that there exists a constant ϑ>0, such that 1−f(I)I≤f′(0)ϑI. Note that f(I)≤f′(0)I and S(t)≤Λμ+ε for any t>T, we have
S(t)−S(T)≥∫tT[μ(Λμ+ε−S(s)f(I(s))f′(0)I(s))−f′(0)S(s)(μϑ+β)I(s)−με]ds−M2(t)≥∫tT[μ(Λμ+ε−S(s)f(I(s))f′(0)I(s))−f′(0)(Λμ+ε)(μϑ+β)I(s)−με]ds−M2(t), |
which implies
μ∫tT(Λμ+ε−S(s)f(I(s))f′(0)I(s))ds≤f′(0)(Λμ+ε)(μϑ+β)∫tTI(s)ds+με(t−T)+S(t)−S(T)+M2(t). | (4.5) |
Substituting (4.5) into (4.3), we obtain
lnI(t)≥Φ(f′(0)(Λμ+ε))t−βf′(0)[1−σ2f′(0)2β(Λμ+ε)]εt−β(f′(0))2μ[1−σ2f′(0)2β(Λμ+ε)](Λμ+ε)(μϑ+β)∫t0I(s)ds+F1(t), |
where
F1(t)=∫T0Φ(Sf(I)I)ds−Φ(f′(0)(Λμ+ε))T+M1(t)+lnI0−βf′(0)μ[1−σ2f′(0)2β(Λμ+ε)][−μεT+M2(t)+S(t)−S(T)]. |
From (3.3) and (4.2), it follows that limt→∞F1(t)t=0 a.s. Note that Rs>1. For any ε>0 sufficiently small, we have
Φ(f′(0)(Λμ+ε))=(μ+γ1+γ2+α)(Rs−1)+(β−Λσ2f′(0)μ)f′(0)ε−σ2(f′(0))22ε2>0, |
and 1−σ2f′(0)2β(Λμ+ε)>0. Using Lemma 1, it follows from the arbitrariness of ε that
lim inft→∞⟨I(t)⟩≥μ2Φ(Λf′(0)μ)βΛ(f′(0))2(1−Λσ2f′(0)2μβ)(μϑ+β)>0a.s. | (4.6) |
The assertion (ⅱ) is proved.
Now, we will give the proof of (ⅲ). It follows from the third equation of model (1.3) that
R(t)−R0t=γ2⟨I(t)⟩−(μ+δ)⟨R(t)⟩, | (4.7) |
which, together with (4.6), yields
lim inft→∞⟨R(t)⟩≥γ2μ2Φ(Λf′(0)μ)(μ+δ)βΛ(f′(0))2(1−Λσ2f′(0)2μβ)(μϑ+β)>0a.s. |
The proof is therefore complete.
Remark 6. From Theorem 3, one can see that if Rs>1, the disease persists and prevails. Clearly, if we let σ=0, then Theorem 3 is coincident with the result in [6].
Remark 7. Theorems 2 and 3 imply that Rs is the threshold of system (1.3) if σ2<βμΛf′(0). Namely, the disease dies out with probability one if Rs<1, whereas if Rs>1, the infection may become almost surely persistent in the time mean.
Remark 8. By constructing V(I)=lnI and using Lemma 1, we obtain that, for any (S0,I0,R0)∈R3+, if Rs>1, then lim inft→∞⟨S(t)⟩>0, lim inft→∞⟨I(t)⟩>0, lim inft→∞⟨R(t)⟩>0a.s. However, Theorem 3.5 in [22] only obtained that, for any (S0,I0,R0)∈Γ, lim inft→∞⟨I(t)⟩>0 by constructing V(I)=lnI+aI, which can be seen in the proof.
Remark 9. Let h(S)=S, γ1=0 and γ2=γ, then system (1.3) is consistent with system (1.4). The methods in proofs of Theorem 3 in our paper and [23] are different. Further, the results in [23] and our paper are different. From Theorem 3 in our paper, we have
lim inft→∞⟨I(t)⟩≥(μ+γ+α)(Rs−1)βΛμ2(f′(0))2(1−Λσ2f′(0)2μβ)(μϑ+β)=:A1>0a.s. |
From Theorem 3 in [23], we have lim inft→∞⟨I(t)⟩≥(μ+γ+α)(Rs−1)D∗=:A2>0a.s., where D∗=f′(0)[β(μ+αμ+γμ+δ)+(μ+γ+α)max0≤ζ≤Λμf(ζ)−ζf′(ζ)f2(ζ)].
For general function f, it is difficult to compare A1 with A2. However, when f is a specific function, we can compare A1 with A2. For example, let f(I)=(1−˜βIm+I)I, where m>0 and 0<˜β<1. If 0<m<μ˜β(μ+δ)(μ+γ+α)βδγ(1(1−˜β)2−1), then A3:=2μβΛ[1−D∗μ2mβΛ(μ˜β+β)]<2μβΛ[1−μ(μ+γ+α)βΛ]=:A4. It is easy to show that A3<σ2<A4 yields A1=(μ+γ+α)(Rs−1)βΛμ2(1−Λσ22μβ)(μ˜βm+β)>(μ+γ+α)(Rs−1)D∗=A2. In addition, condition A3<σ2<A4 ensures that the conditions of Theorem 3 in our paper and [23] hold. In this case, our results are better than those in [23].
In the following, we will summarize a useful criterion for the extinction and persistence of the disease of model (1.3). First, we discuss the relationship between R0 and Rs for different values of white noise intensity σ2 in the following three cases.
Case of R0≤1. From Rs=R0−Λ2σ2(f′(0))22μ2(μ+γ1+γ2+α), it follows that Rs<1 for any σ>0. Clearly, βμΛf′(0)>βμΛf′(0)⋅R02. Now, we differ three cases
{ifσ2≥βμΛf′(0)>βμΛf′(0)⋅R02,then(C3)holds;ifβμΛf′(0)>σ2>βμΛf′(0)⋅R02,then(C2)holds;ifβμΛf′(0)>βμΛf′(0)⋅R02≥σ2,then(C1)holds. |
Hence, if R0≤1, then for any σ>0, the disease dies out with probability one.
Case of 1<R0≤2. It follows that
2μ2(μ+γ1+γ2+α)Λ2(f′(0))2(R0−1)≤βμΛf′(0)⋅R02≤βμΛf′(0). |
On the other hand, Rs<1 is equivalent to σ2>2μ2(μ+γ1+γ2+α)Λ2(f′(0))2(R0−1). Now, we differ four cases
{ifσ2<2μ2(μ+γ1+γ2+α)Λ2(f′(0))2(R0−1),thenconditioninTheorem4.1holds;if2μ2(μ+γ1+γ2+α)Λ2(f′(0))2(R0−1)<σ2<βμΛf′(0)⋅R02≤βμΛf′(0),then(C1)holds;if2μ2(μ+γ1+γ2+α)Λ2(f′(0))2(R0−1)≤βμΛf′(0)⋅R02<σ2<βμΛf′(0),then(C2)holds;if2μ2(μ+γ1+γ2+α)Λ2(f′(0))2(R0−1)≤βμΛf′(0)⋅R02≤βμΛf′(0)<σ2,then(C3)holds. |
Thus, for 1<R0≤2, if σ2>2μ2(μ+γ1+γ2+α)Λ2(f′(0))2(R0−1) (i.e. Rs<1), then the disease dies out with probability one, whereas if σ2<2μ2(μ+γ1+γ2+α)Λ2(f′(0))2(R0−1) (i.e. Rs>1), then the infection may become almost surely persistent in the time mean. Therefore, if 1<R0≤2, then Rs is the threshold parameter.
Case of R0>2. On the one hand, it follows that
βμΛf′(0)<2μ2(μ+γ1+γ2+α)Λ2(f′(0))2(R0−1)<βμΛf′(0)⋅R02. |
On the other hand, Rs<1 is equivalent to σ2>2μ2(μ+γ1+γ2+α)Λ2(f′(0))2(R0−1). Now, we differ four cases
{ifσ2≤βμΛf′(0)<2μ2(μ+γ1+γ2+α)Λ2(f′(0))2(R0−1)<βμΛf′(0)⋅R02,thenRs>1;ifβμΛf′(0)<σ2<2μ2(μ+γ1+γ2+α)Λ2(f′(0))2(R0−1)<βμΛf′(0)⋅R02,thenRs>1;ifβμΛf′(0)<2μ2(μ+γ1+γ2+α)Λ2(f′(0))2(R0−1)≤σ2≤βμΛf′(0)⋅R02,thenconditionsinTheorems2and3arenotsatisfied;ifβμΛf′(0)<2μ2(μ+γ1+γ2+α)Λ2(f′(0))2(R0−1)<βμΛf′(0)⋅R02<σ2,then(C3)holds. |
Thus, if σ2<2μ2(μ+γ1+γ2+α)Λ2(f′(0))2(R0−1) (i.e. Rs>1), then the infection may become almost surely persistent in the mean, whereas if σ2>βμΛf′(0)⋅R02 (i.e. (C3) in Theorem 2 holds), then the disease dies out.
We summarize the above analysis as follows.
Corollary 1. Let Assumptions (H1)−(H3) hold and let (S(t),I(t),R(t)) be the solution of model (1.3) with any given initial condition (S0,I0,R0)∈R3+. The solution (S(t),I(t),R(t)) has the property:
(ⅰ) if R0≤1, then the disease dies out with probability one for any σ>0;
(ⅱ) if 1<R0≤2, then Rs is the threshold parameter, i.e., the disease dies out with probability one if Rs<1, whereas if Rs>1, the infection may become almost surely persistent in the time mean;
(ⅲ) if R0>2, then the disease dies out with probability one if σ2>βμΛf′(0)⋅R02, while if σ2<2μ2(μ+γ1+γ2+α)Λ2(f′(0))2(R0−1), the infection may become almost surely persistent in the time mean.
In this section, we analyze the stochastic behaviors of model (1.3) by means of the numerical simulations in order to make readers understand our results more better. Throughout the following numerical simulations, we choose f(I)=I, f(I)=I1+aI2 and f(I)=Ie−mI, respectively. Thus, f(I)≤I. The numerical simulations of epidemic dynamics are carried out for the academic tests with the arbitrary values of the parameters, which do not correspond to some epidemic and exhibit only the theoretical properties of numerical solutions of considered models.
Example 1. Let f(I)=I. Numerical experiments were made by using the following parameters:
Λ=0.8,μ=0.4,γ1=0.4,γ2=0.1,α=0.3,δ=0.5,(S0,I0,R0)=(1,1,0). |
(i) In order to demonstrate the conclusion (i) in Corollary 1, we take β=0.3 and σ2=0.2. By a simple computation, R0=0.5<1. From the numerical simulations given in Figure 1, the disease I(t) in deterministic model (1.1) and stochastic model (1.3) will die out with probability one (Figure 1).
(ⅱ) In order to demonstrate the conclusion (ii) in Corollary 1, we take β=0.8. By a simple computation, we obtain 1<R0≈1.33<2. From the numerical simulations given in Figure 2(a), it is shown that disease I(t) of deterministic model (1.1) is permanent in the population.
1∘ Assume that σ2=0.4. By a simple computation, we obtain Rs≈0.66<1. It can be seen from Figure 2(b) that disease I(t) in model (1.3) will die out with probability one.
2∘ Assume that σ2=0.02. By computing, Rs≈1.297>1. From the numerical simulations given in Figure 3, it is shown that disease I(t) of model (1.3) is permanent in the mean with probability one.
(ⅲ) In order to demonstrate the conclusion (ⅲ) in Corollary 1, we take β=1.5. By a simple computation, R0=2.5>2. From Figure 4(a), it follows that I(t) of (1.1) is permanent in the population.
1∘ Assume that σ2=0.03 (σ2=0.3). By a simple computation, σ2<2μ2(μ+γ1+γ2+α)Λ2(R0−1)=0.9. It can be seen from Figure 4(b) (4(c)) that disease I(t) in model (1.3) is permanent in the time mean.
2∘ Assume that σ2=1. By computing, σ2>βμΛ⋅R02=0.9375. From the numerical simulations given in Figure 4(d), it is shown that disease I(t) of model (1.3) will die out with probability one.
Example 2. Let f(I)=I1+aI2 and a=1. Other parameters are defined as Example 1.
(ⅰ) From the numerical simulations given in Figure 5, the disease I(t) in deterministic model (1.1) and stochastic model (1.3) will die out with probability one.
(ⅱ) From Figure 6(a), we obtain that disease I(t) of (1.1) is permanent in the population.
1∘ If σ2=0.4. From Figure 6(b), disease I(t) in model (1.3) will be extinct with probability one.
2∘ If σ2=0.02. From Figure 7, disease I(t) of model (1.3) is permanent in the mean.
(ⅲ) From the numerical simulations given in Figure 8(a), it is shown that disease I(t) of deterministic model (1.1) is permanent in the population.
1∘ If σ2=0.03 (σ2=0.3). From Figure 8(b) (8(c)), disease I(t) in (1.3) is permanent in mean.
2∘ If σ2=1. From Figure 8(d), we obtain that disease I(t) of model (1.3) will be extinct.
Example 3. Let f(I)=Ie−mI and m=1. Other parameters are defined as Example 1.
(ⅰ) From Figure 9, the disease I(t) in model (1.1) and model (1.3) will die out with probability one.
(ⅱ) From Figure 10(a), we obtain that disease I(t) of (1.1) is permanent in the population.
1∘ If σ2=0.4. From Figure 10(b), disease I(t) in model (1.3) will be extinct with probability one.
2∘ If σ2=0.02. From Figure 11, disease I(t) of model (1.3) is permanent in the mean.
(ⅲ) From the numerical simulations given in Figure 12(a), it is shown that disease I(t) of deterministic model (1.1) is permanent in the population.
1∘ If σ2=0.03 (σ2=0.3) $. From Figure 12(b) (12(c)), we get that disease I(t) in model (1.3) is permanent in the mean.
2∘ If σ2=1. From Figure 12(d), we obtain that disease I(t) of model (1.3) will be extinct with probability one.
From Examples 1, 2 and 3, we can see that different incidence rates of diseases have different effects on the extinction and persistence in the mean of diseases. In addition, the intensity of noise plays an important role in epidemic dynamics. Comparing Figures 3 and 11 (or Figures 7 and 11), we can conclude that massive media coverages are needed to prevent the disease to spread widely in the population. This is consistent with the results in [26].
Comparing Figures 5(a) and 5(b), we conclude that if R0<1, then I(t) becomes extinct regardless of the intensity of noise. From Figures 6(a), 6(b) and 7, if 1<R0<2, then great intensity of the noise can make diseases extinction. From Figure 8(d), if R0>2, the disease becomes extinct as the intensity of the noise is large.
This paper is concerned with the persistence and extinction of a stochastic SIRS epidemic model with nonlinear incidence rate and transfer from infectious to susceptible. To begin with, we consider the global existence and uniqueness of the positive solution to model (1.3) with any positive initial value. Next, sufficient criteria for the persistence and extinction of the disease are established. Then, we discuss the relationship between R0 and Rs for different values of white noise intensity σ2. In addition, we find that in case of neglecting the impact of environmental noises, the deterministic threshold R0 may exist and the threshold parameter will be overestimated. Furthermore, we discover that a large noise has the effect of suppressing the epidemic. So these results show that noises have important effects on the persistence and extinction of the disease. In addition, we can see that different incidence rates of diseases have different effects on epidemic dynamics.
Although there are important discoveries revealed by these studies, there are also limitations for the model. Theorem 2 shows that the particular expression for the nonlinear transmission makes no influence on the extinction of the disease. We leave these as our future work.
This work was supported by the National Natural Science Foundation of China (Nos. 11471197, 11571210, 11501339).
The authors declare there is no conflict of interest.
[1] |
Anawe PAL, Fayomi OSI, Popoola API (2017) Results in physics investigation of microstructural and physical characteristics of nano composite tin oxide-doped Al3+ in Zn2+ based composite coating by DAECD technique. Results Phys 7: 777-788. doi: 10.1016/j.rinp.2017.01.035
![]() |
[2] |
Dai J, Liu X, Zhai H, et al. (2009) Preparation of Ni-coated Si3N4 powders via electroless plating method. Ceram Int 35: 3407-3410. doi: 10.1016/j.ceramint.2009.06.007
![]() |
[3] |
Du N, Pritzker M (2003) Investigation of electroless plating of Ni-W-P alloy films. J Appl Electrochem 33: 1001-1009. doi: 10.1023/A:1026231532006
![]() |
[4] |
Dai J, Liu X, Zhai H, et al. (2009) Preparation of Ni-coated Si3N4 powders via electroless plating method. Ceram Int 35: 3407-3410. doi: 10.1016/j.ceramint.2009.06.007
![]() |
[5] |
Aydoğdu GH, Aydinol MK (2006) Determination of susceptibility to intergranular corrosion and electrochemical reactivation behaviour of AISI 316L type stainless steel. Corros Sci 48: 3565-3583. doi: 10.1016/j.corsci.2006.01.003
![]() |
[6] |
Ayoola AA, Fayomi OSI, Ogunkanmbi SO (2018) Data in brief data on inhibitive performance of chloraphenicol drug on A315 mild steel in acidic medium. Data in Brief 19: 804-809. doi: 10.1016/j.dib.2018.05.108
![]() |
[7] | OO A, Nwaokocha C, Adesanya A (2012) Evaluation of corrosion cost of crude oil processing industry. JESTEC 7: 517-518. |
[8] | Amin MM, Kee LK, Yunus K (2002) The process of electroplating in the presence of nickel salts. Ultra Sci 14: 309-318. |
[9] | Ehteram A, Aish H (2008) Corrosion behavior of mild steel in hydrochloric acid solutions. Int J Electrochem Sci 3: 806-818. |
[10] | Equbal A, Dixit NK, Sood AK (2013) Electroless plating on plastic. IJSER 8: 12-18. |
[11] |
Gao W, Cao D, Jin Y, et al. (2018) Microstructure and properties of Cu-Sn-Zn-TiO2 nano-composite coatings on mild steel. Surf Coat Tech 350: 801-806. doi: 10.1016/j.surfcoat.2018.04.046
![]() |
[12] | Guo D, Zhang M, Jin Z, et al. (2006) Pulse plating of copper-ZrB2 composite coatings. J Mater Sci Technol 22: 514-518. |
[13] |
House K, Sernetz F, Dymock D, et al. (2008) Corrosion of orthodontic appliances-should we care? Am J Orthod Dentofac 133: 584-592. doi: 10.1016/j.ajodo.2007.03.021
![]() |
[14] | Kallappa D, Venkatarangaiah VT (2018) Synthesis of CeO2 doped ZnO nanoparticles and their application in Zn-composite coating on mild steel. Arab J Chem 3: 45-60. |
[15] |
Krishnan KH, John S, Srinivasan KN, et al. (2006) An overall aspect of electroless Ni-P depositions-A review article. Metall Mater Trans A 37: 1917-1926. doi: 10.1007/s11661-006-0134-7
![]() |
[16] |
Balaraju JN, Narayanan TS, Seshadri SK (2003) Electroless Ni-P composite coatings. J Appl Electrochem 33: 807-816. doi: 10.1023/A:1025572410205
![]() |
[17] | Agarwala RC, Agarwala V (2003) Electroless alloy/composite coatings: A review. Sadhana-Acad P Eng S 28: 475-493. |
[18] | Kumar S, Pande S, Verma P (2015) Factor effecting electro-deposition process. IJCET 5: 700-703. |
[19] |
Laudisio G, Seipel B, Ruffini A, et al. (2005) Corrosion behavior of Si3N4-TiN composite in sulphuric acid. Corros Sci 47: 1666-1677. doi: 10.1016/j.corsci.2004.07.042
![]() |
[20] |
Pang JN, Jiang SW, Lin H, et al. (2016) Significance of sensitization process in electroless deposition of Ni on nanosized Al2O3 powders. Ceram Int 42: 4491-4497. doi: 10.1016/j.ceramint.2015.11.137
![]() |
[21] | Popoola API, Fayomi OSI (2016) Effect of some process variables on zinc coated low carbon steel substrates. Sci Res Essays 6: 4264-4272. |
[22] | Zarras P, Stenger-Smith JD (2014) Corrosion processes and strategies for prevention: An introduction, In: Makhlouf ASH, Handbook of Smart Coatings for Materials Protection, Woodhead Publishing 64: 3-28. |
[23] |
Akande IG, Oluwole OO, Fayomi OSI (2018) Optimizing the defensive characteristics of mild steel via the electrodeposition of Zn-Si3N4 reinforcing particles. Def Technol 14: 1-7. doi: 10.1016/j.dt.2017.11.004
![]() |
[24] |
Liu Y, Zhou X, Lyon SB, et al. (2017) An organic coating pigmented with strontium aluminium polyphosphate for corrosion protection of zinc alloy coated steel. Prog Org Coat 102: 29-36. doi: 10.1016/j.porgcoat.2016.02.020
![]() |
[25] |
Ge T, Zhao W, Wu X, et al. (2020) Incorporation of electro conductive carbon fibers to achieve enhanced anti-corrosion performance of zinc rich coatings. J Colloid Interf Sci 567: 113-125. doi: 10.1016/j.jcis.2020.02.002
![]() |
1. | Yu Zhao, Chunjin Wei, Dynamics of a Toxin Producing Plankton-Fish Model with Three-Dimensional Patch and Time Delay, 2022, 32, 0218-1274, 10.1142/S0218127422501838 | |
2. | Cheng-Cheng Zhu, Jiang Zhu, Spread trend of COVID-19 epidemic outbreak in China: using exponential attractor method in a spatial heterogeneous SEIQR model, 2020, 17, 1551-0018, 3062, 10.3934/mbe.2020174 | |
3. | Wang Zhang, Hua Nie, Jianhua Wu, A Reaction–Diffusion–Advection Chemostat Model in a Flowing Habitat: Mathematical Analysis and Numerical Simulations, 2023, 33, 0218-1274, 10.1142/S0218127423500736 | |
4. | Wang Zhang, Xiao Yan, Yimamu Maimaiti, Dynamical behavior of a reaction-diffusion-advection chemostat model with Holling III function, 2024, 0924-090X, 10.1007/s11071-024-10366-8 |