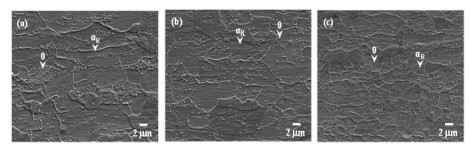
Citation: Toshio Ogawa, Hiroyuki Dannoshita, Yoshitaka Adachi. Evaluation of tensile properties of ferrite single-phase low-carbon steel with different initial microstructures[J]. AIMS Materials Science, 2019, 6(5): 798-805. doi: 10.3934/matersci.2019.5.798
[1] | Kengo Sawai, Keiya Sugiura, Toshio Ogawa, Ta-Te Chen, Fei Sun, Yoshitaka Adachi . Analysis of tensile properties in tempered martensite steels with different cementite particle size distributions. AIMS Materials Science, 2024, 11(5): 1056-1064. doi: 10.3934/matersci.2024050 |
[2] | Pavan Hiremath, Gowrishankar M. C., Manjunath Shettar, Sathyashankara Sharma, Jayashree P. K., Suhas Kowshik . Influence of normalizing post carburizing treatment on microstructure, mechanical properties and fracture behavior of low alloy gear steels. AIMS Materials Science, 2021, 8(5): 836-851. doi: 10.3934/matersci.2021051 |
[3] | ME Makhatha . Effect of titanium addition on sub-structural characteristics of low carbon copper bearing steel in hot rolling. AIMS Materials Science, 2022, 9(4): 604-616. doi: 10.3934/matersci.2022036 |
[4] | Andrea Di Schino . Corrosion behavior of new generation super-ferritic stainless steels. AIMS Materials Science, 2019, 6(5): 646-656. doi: 10.3934/matersci.2019.5.646 |
[5] | Bauyrzhan Rakhadilov, Rinat Kussainov, Aisulu Kalitova, Zarina Satbayeva, Aibek Shynarbek . The impact of technological parameters of electrolytic-plasma treatment on the changes in the mechano-tribological properties of steel 45. AIMS Materials Science, 2024, 11(4): 666-683. doi: 10.3934/matersci.2024034 |
[6] | Rudolf Kawalla, Anett Stöcker, Ulrich Prahl, Xuefei Wei, Jens Dierdorf, Gerhard Hirt, Martin Heller, Stefan Roggenbuck, Sandra Korte-Kerzel, Hannes Alois Weiss, Philipp Tröber, Lucas Böhm, Wolfram Volk, Nora Leuning, Kay Hameyer . Low-loss FeSi sheet for energy-efficient electrical drives. AIMS Materials Science, 2018, 5(6): 1184-1198. doi: 10.3934/matersci.2018.6.1184 |
[7] | Mochamad Asrofi, Mochammad Agus Vian Hidayatulloh, Gaguk Jatisukamto, Hary Sutjahjono, Rahma Rei Sakura . The effect of temperature and volume fraction of mahoni (Swietenia mahogani) wood charcoal on SS400 steel using pack carburizing method: Study of hardness and microstructure characteristics. AIMS Materials Science, 2020, 7(3): 354-363. doi: 10.3934/matersci.2020.3.354 |
[8] | R. Daulath Banu, R. Karunanithi, S. Sivasankaran, B. Subramanian, Abdullah A. Alhomidan . Influence of graphene nanoplatelets (GNPs) and aluminum-carbon layered double hydroxides (Al-C LDH) in polypropylene matrix of hybrid composite structures on the microstructure and mechanical performances. AIMS Materials Science, 2024, 11(5): 882-917. doi: 10.3934/matersci.2024043 |
[9] | Aarne Pohjonen . Numerical simulations of gradient cooling technique for controlled production of differential microstructure in steel strip or plate. AIMS Materials Science, 2021, 8(6): 852-866. doi: 10.3934/matersci.2021052 |
[10] | Marcin Kargul, Marek Konieczny . Copper matrix composites reinforced with steel particles. AIMS Materials Science, 2021, 8(3): 321-342. doi: 10.3934/matersci.2021021 |
The automobile industry strongly demands low-carbon high-strength steel, and the tensile strength of steel continues to increase. Various high-strength steels have been developed to meet this demand. Dual-phase (DP) and transformation-induced plasticity (TRIP) steels are typical high-strength steels with excellent ductility [1,2,3,4]. However, the formabilities (e.g., bendability and hole-expandability) of these steels are inferior compared to single-phase steels, which is a serious problem such as a cracking during press forming [5,6]. Thus, steels with a good combination of ductility and formability are needed.
For DP steels, the effect of martensite distribution on tensile properties has been investigated by several authors [7,8,9,10]. For instance, Tomota et al. [7] have demonstrated that connected martensite in DP steels leaded to an increase in tensile strength and in the strain-hardening exponent. In addition, a decrease in the diameter of the dispersed martensite has been reported to improve the balance between strength and local elongation [9].
Methods of improving the formability of high-strength steels have been proposed in previous studies [5,6]. For instance, a homogeneous microstructure of the steels enhances their formability [5]. The homogeneous microstructure means equiaxed grains, a homogeneous distribution of hard phases and precipitates, and decomposition of the layered microstructure. In the case of low-carbon steel, we have previously demonstrated that the morphology of recrystallized ferrite grains and the distribution of martensite were both strongly dependent on the initial microstructures before annealing [11,12]. In particular, recrystallized ferrite grains are equiaxed and the distribution of martensite is homogeneous after annealing when the initial microstructure includes martensite. Therefore, we have suggested that properly controlling the initial microstructures before annealing was important for improving the formability of low-carbon steels. However, the effect of initial microstructures on the tensile properties of low-carbon steels has not been investigated yet. Achieving a good combination of ductility and formability requires knowledge of the effect of low-carbon steels' initial microstructures on their tensile properties.
Thus, the purpose of the present study is to evaluate the tensile properties of a low-carbon steel and correlate these properties with the steels' initial microstructure. This work is a fundamental study on the tensile properties of the ferrite phase. All of the tests were performed with ferrite single-region annealing.
The chemical composition of the tested steel (in mass%), which was the same as used in our previous studies [11,12] was 0.1C–2.0Mn. The vacuum-melted ingots (approximately 100 mm in thickness) were rough rolled to a thickness of 30 mm. The rough-rolled steels were hot-rolled at a finishing temperature of 900 ℃, which corresponds to the austenite region, to a thickness of 3.0 mm, and subsequently water cooled to 650 ℃ (specimen P), 500 ℃ (specimen B), or less than 100 ℃ (specimen M) by water jet. All specimens were subsequently cooled to room temperature in air. The temperature during cooling was evaluated via measurement of the surface temperature. Specimen P consisted of ferrite and pearlite. Specimen B consisted of bainitic structures, and specimen M consisted of fully martensitic structures. The hot-rolled sheets were cold-rolled to a thickness of 1.0 mm (reduction 67%) in a four-high cold rolling mill at a rolling speed of 15 m/min. The microstructures of the hot-rolled and cold-rolled sheets have been reported for each specimen in our previous article [11].
After cold-rolling, the specimens were heated to each finishing temperature of ferrite recrystallization at a rate of 0.5 ℃/s using an electric furnace, and then water-quenched to room temperature within 2 s after the removal of specimens from the furnace. The finishing temperature of the ferrite recrystallization in specimens P, B, and M was 650,660, and 610 ℃, respectively [11].
The microstructures of nital-etched specimens (etching time approximately 10 s) were observed by scanning electron microscopy (SEM) at an accelerating voltage of 5 kV. Nital etchant has been widely used in the metallography of steels and it was suitable for observing the microstructures in the present study. Tensile test of the specimens was conducted at room temperature and at a strain rate of 1.67 × 10-3 s-1. The JIS Z 2201 standard for the tensile test specimens was used. Standard deviations of the tensile properties were calculated from the results obtained from two specimens. The fracture surfaces of the specimens were observed by SEM. The number and size of dimples in the fracture surfaces were quantified using the image-analysis program ImageJ. The SEM images of fracture surfaces were subjected to binarization processing using ImageJ, and the number of dimples (black region) was estimated. The morphology of dimples was assumed to be oval for purpose of analysis using ImageJ, and the average value of the major and minor axes of the oval dimples was defined as the size of the dimples. Void observations were conducted at distance of approximately 3000 μm from the fractured surface by SEM. The number of void was estimated using twenty SEM images with a total area of approximately 3200 μm2 in each specimen.
Figure 1 shows the microstructures of the specimens immediately after completion of ferrite recrystallization. The recrystallized ferrite grain size decreased in the specimen order of B > P > M. Furthermore, the recrystallized ferrite grains in specimen M were finer and more equiaxed than those in specimens P and B. The distribution of cementite was comparatively homogeneous in specimens B and M, whereas it was heterogeneous in specimen P.
The yield and tensile strengths of the specimens are shown in Figure 2a. The yield and tensile strengths decreased in the specimen order of M > P > B. The local and total elongations of the specimens are shown in Figure 2b. Notably, the total elongation decreased in the specimen order of B > P > M whereas the local elongation was approximately the same in all of the specimens. Here, we focus on the relationship between the recrystallized ferrite grain size of the specimens and their yield strength. According to the Hall–Petch equation [13,14], a smaller grain size resulted in an increase of yield strength. The Hall–Petch equation is expressed as:
where σ is the yield strength; σ0 is the friction stress; k is a material-specific constant, and d is the average grain size. We have reported that the recrystallized ferrite grain size of specimens P, B, and M was 4.6, 5.2, and 3.3 μm, respectively [11]. Moreover, in the case of low-carbon steel, Takaki et al. [15] have proposed estimated values of 100 and 600 for σo and k in the Hall–Petch equation, respectively. Therefore, the yield strength of all specimens can be estimated using the Hall–Petch equation. Figure 3 shows the relationship between the yield strength obtained by tensile test and that calculated using the Hall–Petch equation. The yield strength obtained by tensile test is in good agreement with that calculated using the Hall–Petch equation. Thus, the yield strength of each specimen is mainly dependent on the recrystallized ferrite grain size.
For the dominant factor of yield strength, precipitation strengthening by cementite should be considered. A smaller precipitate size is known to lead to a greater degree of precipitation strengthening. We have previously demonstrated that the spheroidal cementite in specimen M was finer than that in specimens P and B [11]. This observation indicates that the degree of cementite precipitation strengthening in specimen M is greater than that in specimens P and B. In the case of specimen M, the yield strength obtained by tensile test was slightly larger than that calculated using the Hall–Petch equation (Figure 3). Therefore, the difference between the yield strength of specimen M obtained by tensile test and that calculated using the Hall–Petch equation is attributable to the precipitation strengthening of cementite.
In general, the greater the strength of a material, the lower its elongation. As shown in Figure 2, the tensile strength and the total elongation of each specimen also exhibit a trade-off relationship in the present study. Notably, the local elongation was approximately the same in all of the observed specimens. This result implies that specimen M has a good balance between tensile strength and local elongation. The local elongation of metals has been reported to be dependent on the nucleation, growth, and coalescence of voids [16]. Therefore, we discussed void nucleation and coalescence on the basis of the features of dimples in the fracture surfaces. Figure 4 shows SEM micrographs of the fracture surfaces of the specimens. The fracture surface of all specimens was ductile and consisted of multiple dimples; the dimple size in all specimens varied. The average number and size of the dimples in the specimens are shown in Figure 5. The number of dimples decreased in the specimen order of M > B > P (Figure 5a), whereas the size of dimples decreased in the specimen order of P > B > M (Figure 5b).
With respect of void nucleation, voids have been demonstrated to generally nucleate at hard phases and inclusions [17,18,19]. As shown in Figure 6, the voids mainly nucleated at cementite in all specimens. Therefore, the void nucleation sites in specimens B and M are likely distributed homogeneously because the distribution of cementite in these specimens was comparatively homogeneous (Figure 1b, c). In contrast, the void nucleation sites in specimen P should be localized because the distribution of cementite was heterogeneous (Figure 1a). These results suggest that the number of void nucleation sites at cementite in specimens B and M is larger than that in specimen P. Moreover, the voids in interstitial-free (IF) steels mainly nucleate at ferrite/ferrite interfaces (i.e., ferrite grain boundaries) [16]. As shown in Figure 1, the recrystallized ferrite grain size decreased in the specimen order of B > P > M. Thus, the number of void nucleation sites at ferrite grain boundaries in specimens M is likely larger than that in specimens P and B. As shown in Figure 6, the number of void nucleation sites at ferrite grain boundaries in specimen M was larger than that in specimens P and B. From the viewpoint of the void nucleation sites at cementite and ferrite grain boundaries, specimen M likely contains the most void nucleation sites. In addition, the number of dimples in specimen M is apparently larger than that in specimens P and B because the number of the void nucleation sites in specimen M is larger than that in specimens P and B.
Void coalescence has been speculated to depend on the distribution of cementite [19]. Furthermore, Furukimi et al. [20] have revealed that voids nucleate at Cr precipitates in Cr-added steels and that the local elongation increases with increasing mean interparticle spacing of Cr precipitates. These previous studies imply that void coalescence easily occurs when the spacing among the void nucleation sites is small. Therefore, the size of dimples in specimen P is likely larger than that in specimens B and M because the distribution of cementite is heterogeneous and the spacing of cementite is small in specimen P. As shown in Figure 7, the voids nucleated at cementite spherodized in pearlite colonies of specimen P. In addition, void coalescence has been demonstrated to be difficult when the distribution of the void nucleation sites is homogeneous [9]. Accordingly, the size of dimples in specimen M is smaller than that in specimen B because the number of void nucleation sites in specimen M is large and the distribution of the voids is homogeneous.
High local elongation can be obtained by suppressing the growth and coalescence of voids [20]. As previously mentioned, the void coalescence in specimen M was suppressed the most, whereas that was accelerated the most in specimen P. These results indicate that the local elongation of specimen M, which has high tensile strength increases, whereas that of specimen P, which exhibits low tensile strength decreases. Thus, we concluded that the local elongation of each specimen can be explained on the basis of the features (number and size) of dimples.
The tensile properties of ferrite single-phase low-carbon steel with different initial microstructures were evaluated, and the following results were obtained:
(1) The yield and tensile strengths decreased in the specimen order of M > P > B. As a result of calculations using the Hall–Petch equation, the yield strength of each specimen was mainly dependent on the recrystallized ferrite grain size.
(2) The total elongation decreased in the specimen order of B > P > M, whereas the local elongation was approximately the same in all of the specimens.
(3) The number of dimples decreased in the specimen order of M > B > P, whereas the size of dimples decreased in the specimen order of P > B > M. The local elongation of each specimen was explained on the basis of the features (number and size) of its dimples.
This work was supported by a research grant from the Hitachi Metals Materials Science Foundation, Japan.
All authors declare that there is no conflict of interest.
[1] |
Maki T, Onodera H, Tamura I (1975) Trip phenomenon in residual austenite of Fe–Ni–C alloy. J Soc Mater Sci 24: 150–155. doi: 10.2472/jsms.24.150
![]() |
[2] | Matsumura O, Sakuma Y, Takechi H (1987) Enhancement of elongation by retained austenite in intercritical annealed 0.4C–1.5Si–0.8Mn steel. Trans ISIJ 27: 570–579. |
[3] |
Murata M, Kobayashi J, Sugimoto K (2010) Stretch-flangeability of ultra high-strength low alloy TRIP-aided sheet steels with mixed structure matrix of bainitic ferrite and martensite. Tetsu-to-Hagane 96: 84–92. doi: 10.2355/tetsutohagane.96.84
![]() |
[4] |
Moor ED, Speer JG, Matlock DK, et al. (2011) Effect of carbon and manganese on the quenching and partitioning response of CMnSi steels. ISIJ Inter 51: 137–144. doi: 10.2355/isijinternational.51.137
![]() |
[5] |
Nonaka T, Fujita N, Taniguchi Y, et al. (2007) Development of ultra-high-strength steel sheets with excellent formabilities. Materia Jpn 46: 108–110. doi: 10.2320/materia.46.108
![]() |
[6] | Takahashi M (2002) High strength steel sheets for light weight auto-bodies. Bull Iron Steel Inst Jpn 7: 870–877. |
[7] |
Tomota Y, Tanimoto I, Kuroki K (1982) On the deformation behavior of ferrite-martensite: two-ductile-phase steels. T Jpn Soc Mech Eng A 48: 528–536. doi: 10.1299/kikaia.48.528
![]() |
[8] | Sugimoto K, Sakaki T, Fukusato T, et al. (1985) Influence of martensite morphology on initial yielding and strain hardening in a 0.11–1.36Mn dual-phase steel. Tetsu-to-Hagane 71: 994–1001. |
[9] |
Kondo D, Kunishige K, Ueji R (2006) Effects of the grain size and volume fraction of second hard phase on mechanical properties of dual phase steel. Tetsu-to-Hagane 92: 457–463. doi: 10.2355/tetsutohagane1955.92.7_457
![]() |
[10] |
Jiang Z, Guan Z, Lian J (1995) Effects of microstructural variables on the deformation behaviour of dual-phase steel. Mater Sci Eng A-Struct 190: 55–64. doi: 10.1016/0921-5093(94)09594-M
![]() |
[11] |
Ogawa T, Dannoshita H, Maruoka K, et al. (2017) Microstructural evolution during cold rolling and subsequent annealing in low-carbon steel with different initial microstructures. J Mater Eng Perform 26: 3821–3830. doi: 10.1007/s11665-017-2849-6
![]() |
[12] |
Dannoshita H, Ogawa T, Maruoka K, et al. (2019) Effect of initial microstructures on austenite formation behavior during intercritical annealing in low-carbon steel. Mater Trans 60: 165–168. doi: 10.2320/matertrans.M2018298
![]() |
[13] |
Hall EO (1951) The deformation and ageing of mild steel: III discussion of results. Proc Phys Soc B 64: 747–753. doi: 10.1088/0370-1301/64/9/303
![]() |
[14] | Petch NJ (1953) The orientation relationships between cementite and α-iron. J Iron Steel Inst 174: 25–28. |
[15] |
Takaki S, Kawasaki K, Kimura Y (2001) Mechanical properties of ultra fine grained steels. J Mater Process Tech 117: 359–363. doi: 10.1016/S0924-0136(01)00797-X
![]() |
[16] |
Furukimi O, Takeda Y, Yamamoto M, et al. (2017) Voids nucleation and growth examination during tensile deformation for IF steel by synchrotron X-ray laminography and EBSD. Tetsu-to-Hagane 103: 475–482. doi: 10.2355/tetsutohagane.TETSU-2017-011
![]() |
[17] |
Tohgo K, Ishii H, Hiramatsu K, et al. (1993) Influence of cementite volume fraction on mechanical properties and fracture toughness in spheroidized cementite steel: study on fracture behavior of particulate-reinforced composite. T Jpn Soc Mech Eng A 59: 1617–1624. doi: 10.1299/kikaia.59.1617
![]() |
[18] |
Fujita T, Kariya N, Nakamura N, et al. (2005) Effect of microstructure on elongation in cold-rolled high carbon steel sheets. Tetsu-to-Hagane 91: 616–622. doi: 10.2355/tetsutohagane1955.91.7_616
![]() |
[19] |
Maeda M, Shimamura J, Suzuki S (2017) Void formation by cementite and local misorientation evaluation during tensile deformation in high strength steel sheets. Tetsu-to-Hagane 103: 483–490. doi: 10.2355/tetsutohagane.TETSU-2016-106
![]() |
[20] |
Furukimi O, Niigaki S, Yamada N, et al. (2013) Local deformation energy and void formation behavior in 16%Cr ferritic steel. Tetsu-to-Hagane 99: 60–69. doi: 10.2355/tetsutohagane.99.60
![]() |
1. | Anrea Di Schino, Marco Corradi, Construction and building materials, 2020, 7, 2372-0484, 157, 10.3934/matersci.2020.2.157 | |
2. | Toshio Ogawa, Shogo Namizaki, Yoshitaka Adachi, Ken Takata, Dynamic analysis of microstructural evolution during tensile deformation of interstitial-free steel by in-situ electrical resistivity measurements, 2022, 328, 0167577X, 133113, 10.1016/j.matlet.2022.133113 | |
3. | Thomas Altshuler, Grain Boundary Walls Influence Yield Points and Brittle Fracture in Iron and Steel, 2021, 1556-5068, 10.2139/ssrn.3991804 | |
4. | Kenji Hayakawa, Toshio Ogawa, Lei He, Fei Sun, Yoshitaka Adachi, Improvement in the Strength–Ductility Balance of Tempered Martensite Steel by Controlling Cementite Particle Size Distribution, 2024, 33, 1059-9495, 6675, 10.1007/s11665-023-08428-w | |
5. | Thomas Altshuler, Grain Boundary Wall Cracks Create Brittle Fracture in Iron and Steel, 2023, 1556-5068, 10.2139/ssrn.4549905 | |
6. | Kotaro Iguchi, Toshio Ogawa, Fei Sun, Yoshitaka Adachi, Simulation-aided analysis of ferrite recrystallization behavior of pure iron with different dislocation characters, 2023, 24, 22387854, 6558, 10.1016/j.jmrt.2023.04.233 | |
7. | Thomas Altshuler, Brittle Fracture of Iron and Steel and the Sharp Upper Yield Point are Caused by Cementite Grain Boundary Walls, 2023, 1556-5068, 10.2139/ssrn.4588927 | |
8. | Thomas Altshuler, GRAIN BOUNDARY WALLS INFLUENCE YIELD POINTS AND BRITTLE FRACTURE IN IRON AND STEEL, 2024, 1556-5068, 10.2139/ssrn.4707689 | |
9. | Kohei Ogatsu, Toshio Ogawa, Ta-Te Chen, Fei Sun, Yoshitaka Adachi, Dramatic improvement in strength–ductility balance of dual-phase steels by optimizing features of ferrite phase, 2025, 35, 22387854, 289, 10.1016/j.jmrt.2025.01.031 |