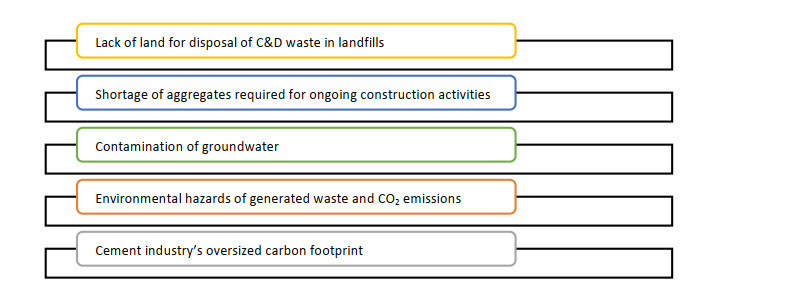
The cement industry's carbon emissions present a major global challenge, particularly the increase in atmospheric carbon dioxide (CO2) levels. The concrete industry is responsible for a significant portion of these emissions, accounting for approximately 5–9% of the total emissions. This underscores the urgent need for effective strategies to curb carbon emissions. In this work, we propose to use artificial intelligence (AI) to predict future emission trends by performing a detailed analysis of cement industry's CO2 emissions data. The AI predictive model shows a significant increase in overall carbon emissions from the cement sector which is attributed to population growth and increased demand for housing and infrastructure. To address this issue, we propose a framework that emphasizes on implementing carbon sequestration through reuse of construction and demolition (C & D) waste by using recycled aggregates. The paper proposes a framework addressing carbon sequestration through use of C & D waste. The framework is applied specifically to Maharashtra State in India to calculate the potential reduction in carbon emissions by construction industry resulting from recycled aggregates. The study reveals a projected saving of 24% in carbon emissions by adopting the suggested framework. The process and outcomes of the study aim to address the concerns of climate change through reduced carbon emissions in the construction industry promoting recycle and reuse of construction waste.
Citation: Sayali Sandbhor, Sayali Apte, Vaishnavi Dabir, Ketan Kotecha, Rajkumar Balasubramaniyan, Tanupriya Choudhury. AI-based carbon emission forecast and mitigation framework using recycled concrete aggregates: A sustainable approach for the construction industry[J]. AIMS Environmental Science, 2023, 10(6): 894-910. doi: 10.3934/environsci.2023048
[1] | Jordan Brown, Corona Chen, Deborah Carr . Endolithic microbes may alter the carbon profile of concrete. AIMS Environmental Science, 2024, 11(2): 221-247. doi: 10.3934/environsci.2024011 |
[2] | Osarumwense Osabuohien-Irabor, Igor M. Drapkin . Toward achieving zero-emissions in European Union countries: The contributions of trade and overseas direct investments in consumption-based carbon emissions. AIMS Environmental Science, 2023, 10(1): 129-156. doi: 10.3934/environsci.2023008 |
[3] | Richi Singh, Dharmendra Yadav, S.R. Singh, Ashok Kumar, Biswajit Sarkar . Reduction of carbon emissions under sustainable supply chain management with uncertain human learning. AIMS Environmental Science, 2023, 10(4): 559-592. doi: 10.3934/environsci.2023032 |
[4] | Izlawanie Muhammad . Carbon tax as the most appropriate carbon pricing mechanism for developing countries and strategies to design an effective policy. AIMS Environmental Science, 2022, 9(2): 161-184. doi: 10.3934/environsci.20220012 |
[5] | Serpil Guran . Options to feed plastic waste back into the manufacturing industry to achieve a circular carbon economy. AIMS Environmental Science, 2019, 6(5): 341-355. doi: 10.3934/environsci.2019.5.341 |
[6] | Sergey Orlov, Elena Rovenskaya, Julia Puaschunder, Willi Semmler . Green bonds, transition to a low-carbon economy, and intertemporal welfare allocation: Evidence from an extended DICE model. AIMS Environmental Science, 2024, 11(4): 628-648. doi: 10.3934/environsci.2024031 |
[7] | Kumari Anjali, YSC Khuman, Jaswant Sokhi . A Review of the interrelations of terrestrial carbon sequestration and urban forests. AIMS Environmental Science, 2020, 7(6): 464-485. doi: 10.3934/environsci.2020030 |
[8] | Nicola Lovecchio, Faiz Shaikh, Michele Rosano, Rosario Ceravolo, Wahidul Biswas . Environmental assessment of supplementary cementitious materials and engineered nanomaterials concrete. AIMS Environmental Science, 2020, 7(1): 13-30. doi: 10.3934/environsci.2020002 |
[9] | Subhash Kumar, Ashok Kumar, Rekha Guchhait, Biswajit Sarkar . An environmental decision support system for manufacturer-retailer within a closed-loop supply chain management using remanufacturing. AIMS Environmental Science, 2023, 10(5): 644-676. doi: 10.3934/environsci.2023036 |
[10] | Benjamin M. Sleeter, Jinxun Liu, Colin Daniel, Leonardo Frid, Zhiliang Zhu . An integrated approach to modeling changes in land use, land cover, and disturbance and their impact on ecosystem carbon dynamics: a case study in the Sierra Nevada Mountains of California. AIMS Environmental Science, 2015, 2(3): 577-606. doi: 10.3934/environsci.2015.3.577 |
The cement industry's carbon emissions present a major global challenge, particularly the increase in atmospheric carbon dioxide (CO2) levels. The concrete industry is responsible for a significant portion of these emissions, accounting for approximately 5–9% of the total emissions. This underscores the urgent need for effective strategies to curb carbon emissions. In this work, we propose to use artificial intelligence (AI) to predict future emission trends by performing a detailed analysis of cement industry's CO2 emissions data. The AI predictive model shows a significant increase in overall carbon emissions from the cement sector which is attributed to population growth and increased demand for housing and infrastructure. To address this issue, we propose a framework that emphasizes on implementing carbon sequestration through reuse of construction and demolition (C & D) waste by using recycled aggregates. The paper proposes a framework addressing carbon sequestration through use of C & D waste. The framework is applied specifically to Maharashtra State in India to calculate the potential reduction in carbon emissions by construction industry resulting from recycled aggregates. The study reveals a projected saving of 24% in carbon emissions by adopting the suggested framework. The process and outcomes of the study aim to address the concerns of climate change through reduced carbon emissions in the construction industry promoting recycle and reuse of construction waste.
Concrete stands as a ubiquitous engineering material and is intricately linked to CO2 emissions. Balancing these emissions through the carbonation of cement-based materials assumes a pivotal role in achieving carbon neutrality within the cement industry, a concept underscored by research [1]. Cement emits around 0.79 tons of CO2 per ton, forming a significant portion of global CO2 emissions, with the concrete industry contributing approximately 5-9% of this total [2,3]. This percentage has surged due to increased cement production and dwindling emission reduction initiatives [2,4]. The confluence of soaring infrastructure demands and restricted construction resources has led to challenges. Most construction and demolition (C & D) waste ends up in landfills, contributing to urban landfill shortages. India alone produces about 100 million metric tons (MT) of C & D waste, a staggering volume. Unfortunately, only 2% of Maharashtra's C & D waste undergoes recycling, accentuating the need for innovative solutions. Furthermore, the construction sector in India grapples with a deficit of aggregates, surpassing 55 billion MT, straining precious natural resources. Amid these concerns, global warming casts its shadow. Although many mechanical measures exist to counter the emissions, like increasing the water-cement ratio, the dehydration of the concrete is a challenge, especially in cold climates [5] (Nilimaa et al., 2023). Other measures include having a comprehensive approach covering all stages of cement usage in construction. Phases including raw material extraction to production, transportation and eventual disposal contribute to CO2 accumulation. Incorporating strategies of using alternative cementitious materials is the need of the hour. Promoting supplementary cementitious materials (SCMs) such as fly ash and slag and relying on technologies to reduce carbon emission at source and usage location is important [6]. An innovative framework dealing with carbon impact can aid in wastage reduction on site thereby leading to indirect CO2 emission control [7]. The climate action demands use of innovative yet sustainable practices and materials in construction to address the environmental impact and challenges due to amplified carbon emissions [8]. Integrating multidimensional methodologies is necessary for making the concrete industry a more sustainable industry [9]. Exploring innovative concrete technologies and sustainable construction methods is the way forward [10]. Carbon sequestration emerges as a promising countermeasure comprising of capturing and reusing emitted CO2. Although C & D waste is abundant worldwide, the use of recycled aggregates (RA) remains limited due to discrete properties such as heterogeneity, porosity and lower strength compared to natural aggregates [11,12]. Figure 1 outlines the extensive environmental impact of the construction industry, highlighting the urgency of addressing these challenges. Using RA infused with CO2, in combination with carbon sequestration, aligns with sustainable development goals (SDGs) 9, 11, 12 and 13. Integrating CO2 into RA reduces carbon dioxide emissions, a primary greenhouse gas (GHG). RA adoption further trims the demand for natural aggregates (NA), lessening environmental pressures associated with aggregate extraction. The magnitude of aggregate extraction's impact resonates with SDGs 14 and 15, which champion the integrity of terrestrial and aquatic ecosystems [13]. A comprehensive exploration of the cement industry's historical and ongoing carbon footprint is fundamental to addressing these intricacies.
The proposed study analyses carbon emission data from cement manufacturing industries and its correlation with global CO2 emissions. The study further provides a prediction of the future CO2 emissions in India if carbon compensation techniques are not designed or implemented. The study also proposes a framework for carbon compensation techniques through carbon sequestration and recycled aggregates in the Indian scenario.
To understand the global CO2 emissions trend and cement-CO2 trend, data from Feenstra et al. [14] Penn World Table v10.0 via Our World in Data and Max Roser [15] is considered for the study.
The cement manufacturing process involves releasing large amounts of carbon dioxide (CO2), primarily due to the calcination of limestone and the energy-intensive nature of production. As concerns about climate change and environmental degradation intensify, the cement industry has recognized the need to address its carbon footprint and transition towards more sustainable operations. Based on data on population, cement CO2 and cumulative global share of cement CO2 for the year 2021, China is a leading country with a global cement CO2 contribution of 34.74% among all nations, cement-CO2 emission of 852.961 at a population of 1425893504 in 2021. Countries including India, Afghanistan, the United States of America and the United Kingdom are among the top contributors to global CO2 due to cement consumption. They can directly correlate with the country's population curve (Figures 2-4).
The 153 countries considered for the present analysis are grouped based on income into four categories: low-income, lower-middle income, upper-middle income and high-income (Figure 5). 50% of the global CO2 emission through cement usage is attributed to upper middle-income countries, which can be directly related to the infrastructural advancements and developments in the developing countries and their high demand for construction activities and thus manufacturing and usage of cement (Table 1).
Group of Countries | Cement CO2 |
Low-income countries | 15.36 |
Lower-middle-income countries | 378.49 |
Upper-middle-income countries | 1055.12 |
High-income countries | 223.61 |
India is witnessing a rapid demand for built environment and infrastructure projects, resulting in a paucity of construction materials and a cost upsurge. The majority of C & D waste is dumped in landfills causing a shortage of leaving places in urban areas. In India, 100 million MT is the closest approximation for nationwide C & D waste production and accounts for 35-40% of the global C & D waste annually [16,17]. India recycles only 1% of the C & D waste that is produced, according to the Center for Science and Environment estimates (CSE, 2020). For instance, out of the total C & D waste generated in Maharashtra, only about 2% is recycled and the rest goes to landfills without processing. Hence, in-place technology has a massive potential to address C & D waste in Maharashtra. The Indian construction industry is dealing with an aggregate shortage of approximately 55, 000 million MT, putting an enormous burden on natural resources. Another grave concern is the cement industry's oversized carbon footprint (8% of the total global CO2 emissions) which needs to be inhibited. The proposed solution aligns with five of the United Nations (UN) SDGs and plans, presenting a way forward to realize the collective goals. India has provisions for protecting and improving the environment in its constitution. The demand for aggregates in 2007 increased by five percent to over 21 billion tons, the largest being in developing countries like India.
Figure 6 shows the methodology of the work. The dataset used in the present study is the carbon dioxide emission data from 1930-2021. The data also contains yearly contributions of carbon dioxide emissions by the cement industry. The data is analysed to understand the future trend of CO2 emission in India if carbon compensation techniques are not adopted.
Regression-based prediction of the trend is shown in Figure 7 and 8 below. The polynomial trendline equation helps in predicting the pattern of CO2 emissions in India caused by cement usage.
It is observed in Figure 7 that there is an exponential increase in CO2 emissions after the 1980s. This can be attributed to rapid industrialization and urbanization in India, which is highlighted in India's 5-year plan and continues thereafter. The share of CO2 emission from the cement manufacturing industry (Figure 8) shows an increasing polynomial trend, purely due to rapid urbanization.
It is essential to interpret the root mean squared error (RMSE) value in the context of the scale and variability of the CO2 emission data. It is a good practice to compare the RMSE value with the range of CO2 emissions over time. If the range of CO2 emissions is substantial and the RMSE is relatively small compared to the range, it indicates a reasonable predictive performance. On the other hand, if the range is small and the RMSE is close to the average or maximum CO2 emission value, it might suggest that the model is not adequately capturing the data's variability.
Overall, the RMSE value of 75.24 suggests that the polynomial regression model performs well on the given data. Using time series forecasting techniques is favourable for longer-term predictions and are beneficial especially for complex time-series data. Sophisticated regression models or advanced time series forecasting techniques like season autoregressive integrated moving average (SARIMA) are useful for such datasets. Autoregressive integrated moving average (ARIMA) focuses on non-seasonal data. SARIMA is ideal for handling seasonal fluctuations as it captures and models both seasonal variations and non-seasonal trends. This makes SARIMA predominantly useful for predicting CO2 emissions with varying seasonal effects over larger periods. Employing SARIMA for time series analysis and forecasting entails identifying the appropriate model parameters, both seasonal and non-seasonal orders. This can be achieved through autocorrelation and partial autocorrelation analysis, grid search or optimization algorithms. Once the model is fitted to the data, it can generate predictions for future years. Therefore, opting for ARIMA and SARIMA represents a more advanced and potent approach to time series forecasting, especially when addressing data exhibiting seasonality and other time-related patterns.
The RMSE value from ARIMA is 2274.70. Therefore, Therefore, this study proceeds with SARIMA for a better analysis.
The glitch observed at the end of the graph is due to the pandemic year wherein the CO2 emissions have had an abrupt stop for the majority of activity for a quarter of the year, due to which the cumulative emissions have had a disruptive downfall and picked back again after the particular event.
Figure 11 illustrates the recalibrated graph after the exclusion of data from the pandemic year, projecting CO2 emissions trends up to the year 2030. The extrapolation reveals a worrisome trajectory of heightened global CO2 emissions without proactive mitigation measures. The patterns depicted in Figures 9-11 reveal that by 2030, the carbon emissions from cement industry would increase exponentially demanding immediate attention and action.
Majority of the construction industry's overall carbon emission is due to material production process, sustainable development goals set for the world by the UN provide a guideline to frame policies around practices [18]. The following sections offer a methodology for reducing carbon emissions by using recycled aggregates, which in turn reduces a substantial amount of carbon emissions. By emphasizing the treatment and reuse of C & D waste, the framework supports circular economy in the construction sector through carbon sequestration. The extent to which the reuse of recycled aggregates reduces the requirement for raw materials and the emissions connected with them in the Indian context is also addressed in the article through a case study. The construction industry presents an avenue for emission reduction through the strategic implementation of waste reuse practices. Enhanced utilization of RA holds the potential to mitigate ecological impacts on both aquatic and terrestrial ecosystems. The outlined project aligns with SDGs 9, 11, 12 and 13, fostering innovation and sustainable resource utilization for resilient infrastructure and concurrently addressing urban environmental challenges.
In construction, RA offer a potent strategy to mitigate carbon dioxide emissions. Traditional aggregate production demands substantial energy for raw material extraction, processing and transportation. In contrast, recycled aggregates necessitate less energy derived from construction waste. Moreover, transporting virgin aggregates over long distances generates significant emissions, which can be avoided by sourcing recycled aggregates locally.
Recycled aggregates play a pivotal role in minimizing carbon dioxide emissions in the concrete industry. The aim is to reduce the quantity of cement utilized in concrete production. One of the promising alternatives could be using recycled aggregate and effective concrete mix design. Studies suggest emission reductions from 5-50% through recycled aggregate adoption in concrete production. Deriving aggregates from C & D waste and using them in concrete poses challenges if used in their original form. This is attributed to reduced physical and mechanical properties as compared with crushed coarse aggregates. Hence, carbonation of C & D-RA is ideal for enhancing its workability, reducing shrinkage and enhancing mechanical performance.
The efficiency of carbonation is dependent on environmental and sample-specific factors. thermal gravimetric analysis (TGA), differential thermal analysis (DTA), x-ray diffraction (XRD) and mass gain methods assess CO2 absorption. These tools facilitate understanding of behavioural patterns of recycled aggregates after CO2 infusion. The literature underlines the need for comprehensive research on concrete with C & D waste reuse, evaluating its potential as a CO2 capture medium and its performance as a core construction material alternative. The objective of the present study aligns well with the broader pursuit of environmentally sustainable construction materials.
The utilization of aggregates sourced from C & D waste in concrete naturally hamper the quality and result in poor physical and mechanical properties as compared to conventional concrete. This is due to the higher void content in RA [19]. Performing carbonation of the C & D-RA is a better alternative to address this challenge [20,21,22]. The use of carbonated recycled aggregates in the production of concrete results in enhanced workability and a reduction in shrinkage as compared to concrete with uncarbonated RA. A noticeable improvement in the properties of the concrete mix motivates further research and builds confidence in using such mixes for structural and non-structural members [23]. The process of carbonating C & D-RA is characterized by accelerated kinetics which is due to the additional presence of calcium hydroxide (Ca(OH)2) within the aggregate matrix. This triggers formation of calcium carbonate (CaCO3) upon exposure to CO2. The calcium carbonate permeates into the voids of C & D-RA, thereby increasing the overall performance, quality and strength output of the aggregates and the mix [24]. The efficiency of the carbonation process is related to ambient temperature, relative humidity, CO2 concentration, exposure duration and particle size [25]. Out of the methods employed to quantify the absorbed CO2, TGA and DTA have proved to be very reliable tools. Additionally, XRD and mass gain methods are most commonly used [26]. The literature highlights the need for further investigation into concrete with recycled concrete aggregates, focusing on its potential as an eco-friendly alternative [27].
The recycled aggregate is a sustainable alternative to virgin aggregate, as it reduces the need to extract and process new materials. This can lead to significant carbon savings, as the production of virgin aggregate is a primary source of greenhouse gas emissions. According to the Global Alliance for Resources, producing concrete and other construction materials accounts for around 7% of global CO2 emissions. Recycled aggregate can help in a significant reduction of CO2 emission, depending on the type of aggregate and the concrete mix. Table 2 provides a figure for the C & D waste generation in Maharashtra, India and the quantum of waste processed and recycled in metric tons per year. The analysis uses data from the annual report of the central pollution control board (CPCB), India.
Year | Total C & D waste in MT per year | Amount of C & D waste processing and recycling in MT per year |
2019 | 1658864.3 | 27402 |
2020 | 4704568.7 | 44004 |
2021 | 3729636.1 | 80098.1 |
2022 | 6256093 | 129304 |
2023 | 3008585 | 218678 |
It is inferred from Figure 13 that the quantum of C & D waste recycled is insignificant as compared to the total amount of waste generated and sent to landfills. The huge amount of landfill C & D waste puts pressure on the available landfill resources and contributes to the carbon footprint. The paper attempts to understand the carbon emissions of recycling and reusing recycled concrete aggregates (RCA) and compare the carbon emission savings due to the recycling of C & D waste to understand the benefits of RCA usage. Table 3 provides the data for carbon equivalents corresponding to the processing, recycling, and transportation of C & D waste. The study assumes 100% conversion of C & D waste sent for recycling into usable RCA.
Sr.no | (A) Year |
(B) Total C & D waste generated | (C) Processing and recycling of C & D waste | (D) Carbon equivalent processing /recycling kg CO2 /ton of waste (+) | (E) Carbon equivalent transportation of C & D waste kg CO2 kg /ton (+) |
(F) Carbon equivalent saved due to recycling credits x kg /ton (-) | (G) Total carbon equivalent generated in kg CO2 / ton |
1 | 2019 | 1658864 | 27402 | 36324 | 94631 | 31857 | 99098 |
2 | 2020 | 4704569 | 44004 | 58332 | 151965 | 51158 | 159138 |
3 | 2021 | 3729637 | 80098 | 276615 | 106179 | 93121 | 289672 |
4 | 2022 | 6256093 | 129304 | 171407 | 446545 | 150328 | 467624 |
5 | 2023 | 3008585 | 218678 | 289882 | 755194 | 254233 | 790842 |
From the literature, the carbon dioxide emission due to concrete is estimated to be around 73.1 kg of CO2 per ton of C & D waste generated. Based on the estimated carbon dioxide emission, the value of total carbon emissions due to recycling and reuse of the C & D waste is provided in column D. The carbon emissions due to transportation related to recycling and reuse are also covered in column E. The amount of carbon emission during reuse, recycling and transportation is considered as per [27,28] given in column E. The savings due to recycling and reusing are considered, and the total carbon equivalent is calculated for the present recycling status in Maharashtra, given in Table 4. The total usage of the recycled aggregates is considered to be 25 % as per IS 383-2016. The entire recycled waste, if utilized, leads to savings of around 23% in carbon emissions. Figure 14 provides a visual representation of a comparison between the carbon equivalent of conventional concrete and 25% RCA-replaced concrete. Figure 14 shows a significant saving in carbon emissions.
Sr. No. | Year | Total quantity of conventional concrete | Total quantity of concrete with RCA (75%) | Aggregates replaced with RCA (25 %) | The carbon equivalent of conventional concrete | Carbon equivalent of 75% concrete | Carbon equivalent of 25% RCA concrete | Total carbon equivalent if RCA is used in construction (75% + 25% RCA) | Difference between the carbon equivalent of conventional concrete and RCA replaced concrete | % saving |
1 | 2019 | 109608 | 82206 | 27402 | 8012329 | 6009247 | 99098 | 6108345 | 1903984 | 23.76 |
2 | 2020 | 176015 | 132011 | 44004 | 12866682 | 9650011 | 159138 | 9809150 | 3057532 | |
3 | 2021 | 320392 | 240294 | 80098 | 23420679 | 17565509 | 289672 | 17855181 | 5565497 | |
4 | 2022 | 517216 | 387912 | 129304 | 37808490 | 28356367 | 467624 | 28823991 | 8984498 | |
5 | 2023 | 874712 | 656034 | 218678 | 63941447 | 47956085 | 790842 | 48746928 | 15194519 |
If the entirety of C & D waste were considered a resource, it would result in huge carbon emissions savings. Table 5 provides the computation of concrete replacement potential and carbon equivalent for the total quantity of C & D waste generated.
Sr. No. | Year | Total quantity of conventional concrete for 100% C & D waste utilization | Total quantity of concrete with RCA (75%) for 100% C & D waste utilization | Aggregates replaced with RCA (25 %) for 100% C & D waste utilization | Carbon equivalent of conventional concrete for 100% C & D waste utilization | Carbon equivalent of 75% concrete for 100% C & D waste utilization | Carbon equivalent of 25% RCA concrete for 100% C & D waste utilization | Total carbon equivalent if RCA is used in construction (75% + 25% RCA) for 100% C & D waste utilization | Difference between the carbon equivalent of conventional concrete and RCA replaced concrete for 100% C & D waste utilization | % saving |
1 | 2019 | 6635457 | 4976593 | 1658864 | 485051909 | 363788931 | 99098 | 363888030 | 121163879 | 24.99 |
2 | 2020 | 18818275 | 14113706 | 4704569 | 1375615882 | 1031711912 | 159138 | 1031871050 | 343744832 | |
3 | 2021 | 14918544 | 11188908 | 3729636 | 1090545596 | 817909197 | 289672 | 818198869 | 272346727 | |
4 | 2022 | 25024372 | 18768279 | 6256093 | 1829281593 | 1371961195 | 467624 | 1372428819 | 456852774 | |
5 | 2023 | 12034340 | 9025755 | 3008585 | 879710254 | 659782691 | 790842 | 660573533 | 219136721 |
The analysis indicates a huge savings of around 25% in carbon emissions due to the full utilization of RCA in construction (Figure 15). The amount of C & D waste is increasing in Maharashtra as well as increasing globally. If measures addressing recycling and reuse are promoted and adapted, significant carbon saving can be achieved.
The growing population and rapid urbanization are causing a significant demand for residential and infrastructure facilities. This, in turn, leads to a problem of waste disposal as cities generate large amounts of C & D waste. Additionally, the construction industry's need for natural aggregates negatively impacts the ecological balance and air and water quality. To address these issues, our study proposes detailed data analytics to predict future CO2 emissions, focusing on the cement industry's contribution. Our findings suggest carbon dioxide emissions will reach 4-6 billion tons within 30 years. Therefore, it is crucial to implement carbon sequestration methods and prioritize using RA. Furthermore, it is planned to analyse the carbon footprint in select regions of India utilizing this approach and conduct feasibility studies with the involvement of stakeholders for global impact. The present study promotes treating and reusing RA with carbon sequestration techniques as an effective way to reduce the overall carbon footprint. It can contribute towards achieving a circular economy by utilizing RCAs from C & D waste. The goal of the framework is to decrease the demand for cement in the concrete mix without compromising the strength of the concrete. The effectiveness of the framework is assessed by using a case study of Maharashtra data on C & D waste and exploring the potential for recycling this waste. The findings reveal a significant reduction of approximately 23-25% in carbon emissions that would have otherwise contributed to greenhouse gases and global warming. This paper advocates for a circular economy by reusing and recycling C & D waste.
The RMSE value of 75.24 generally indicates that the polynomial regression model is functioning effectively on the provided data. However, since it was crucial to consider more advanced time series forecasting methods for longer-term predictions and when dealing with more intricate time-related patterns, more sophisticated regression models or advanced time series forecasting techniques such as ARIMA or SARIMA are utilized. In this study, when carbonated recycled aggregates are used in producing mortars and concrete, results showed enhanced workability while reducing shrinkage compared to those made with uncarbonated RA.
The authors declare they used the open-source Google Colab tool to analyse data in creating this article.
All the sources are duly acknowledged.
All authors declare no conflicts of interest in this paper.
[1] |
Wang Y, Li X, Liu R (2022) The Capture and Transformation of Carbon Dioxide in Concrete: A Review. Symmetry 14: 2615. https://doi.org/10.3390/sym14122615 doi: 10.3390/sym14122615
![]() |
[2] |
Ali M B, Saidur R, Hossain M S (2011) A review on emission analysis in cement industries. Renew. Sustain. Energy Rev 15: 2252–2261. https://doi.org/10.1016/j.rser.2011.02.014 doi: 10.1016/j.rser.2011.02.014
![]() |
[3] |
Deja J, Uliasz-Bochenczyk A, Mokrzycki E (2010) CO2 emissions from the Polish cement industry. Int J Greenh Gas Control 4: 583–588. https://doi.org/10.1016/j.ijggc.2010.02.002 doi: 10.1016/j.ijggc.2010.02.002
![]() |
[4] |
Damineli B L, Kemeid F M, Aguiar P S, et al. (2010) Measuring the eco-efficiency of cement use. Cem Concr Compos 32: 555–562. https://doi.org/10.1016/j.cemconcomp.2010.07.009 doi: 10.1016/j.cemconcomp.2010.07.009
![]() |
[5] |
Nilimaa J, Zhaka V (2023) Material and Environmental Aspects of Concrete Flooring in Cold Climate. Constr Mat 3: 180-201. https://doi.org/10.3390/constrmater3020012 doi: 10.3390/constrmater3020012
![]() |
[6] | Scrivener, Karen, Vanderley M. John, and Ellis Bentz. Sustainable Concrete Construction. John Wiley & Sons, 2018. |
[7] |
Nilimaa J, Gamil Y, Zhaka V (2023) Formwork Engineering for Sustainable Concrete Construction. Civi lEng 4: 1098-1120. https://doi.org/10.3390/civileng4040060 doi: 10.3390/civileng4040060
![]() |
[8] |
Tam V W Y, Butera A, Le K N, et al. (2021) CO2 concrete and its practical value utilizing living lab methodologies. Clean Eng Technol 3: 100131. https://doi.org/10.1016/j.clet.2021.100131 doi: 10.1016/j.clet.2021.100131
![]() |
[9] | Dhir, Ravindra K., Moray D (2012) Newlands, and Kenneth W. Paine. Concrete Sustainability. CRC Press. |
[10] |
Nilimaa J (2023) Smart materials and technologies for sustainable concrete construction. Dev Built Environ 2023: 100177. https://doi.org/10.1016/j.dibe.2023.100177 doi: 10.1016/j.dibe.2023.100177
![]() |
[11] |
Feenstra R C, Inklaar R, Timmer M P (2015) The next generation of the Penn World Table. Am Econ Rev 105: 3150-3182. https://doi.org/10.1257/aer.20130954 doi: 10.1257/aer.20130954
![]() |
[12] | Max Roser (2013) Economic Growth Published online at OurWorldInData.org. Retrieved from: https://ourworldindata.org/economic-growth |
[13] |
Blengini G A, Garbarino E (2010) Resources and waste management in Turin (Italy): the role of recycled aggregates in the sustainable supply mix. J Clean Prod 18: 1021-1030. https://doi.org/10.1016/j.jclepro.2010.01.027 doi: 10.1016/j.jclepro.2010.01.027
![]() |
[14] |
Liu Z, Meng W (2021) Fundamental understanding of carbonation curing and durability of carbonation-cured cement-based composites: A review. J CO2 Util 44: 101428. https://doi.org/10.1016/j.jcou.2020.101428 doi: 10.1016/j.jcou.2020.101428
![]() |
[15] | Zhang D, Ghouleh Z, Shao Y (2017) Review on carbonation curing of cement-based materials. J CO2 Util 21: 119-131. ttps://doi.org/10.1016/j.jcou.2017.07.003 |
[16] | Jain M S. A mini review on generation, handling, and initiatives to tackle construction and demolition waste in India. Environ Technol Inno 22: 101490. https://doi.org/10.1016/j.eti.2021.101490 |
[17] |
Tezeswi T P, MVN S K (2022) Implementing construction waste management in India: An extended theory of planned behaviour approach. Environ Technol Inno 27: 102401. https://doi.org/10.1016/j.eti.2022.102401 doi: 10.1016/j.eti.2022.102401
![]() |
[18] | Hertwich E G (2021) Increased carbon footprint of materials production driven by rise in investments. Nat Geosci 14: 151-155. |
[19] |
Shi C, Li Y, Zhang J, et al. (2016) Performance enhancement of recycled concrete aggregate–a review. J Clean Prod 112: 466-472. https://doi.org/10.1016/j.jclepro.2015.08.057 doi: 10.1016/j.jclepro.2015.08.057
![]() |
[20] |
Younis K H, Pilakoutas K (2013) Strength prediction model and methods for improving recycled aggregate concrete. Constr Build Mater 49: 688-701. https://doi.org/10.1016/j.conbuildmat.2013.09.003 doi: 10.1016/j.conbuildmat.2013.09.003
![]() |
[21] |
Gomes M, de Brito J (2009) Structural concrete with incorporation of coarse recycled concrete and ceramic aggregates: durability performance. Mater Struct 42: 663-675. https://doi.org/10.1617/s11527-008-9411-9 doi: 10.1617/s11527-008-9411-9
![]() |
[22] |
Chen Y, Liu P, Yu Z (2018) Effects of environmental factors on concrete carbonation depth and compressive strength. Materials 11: 2167. https://doi.org/10.3390/ma11112167 doi: 10.3390/ma11112167
![]() |
[23] | He P, Shi C, Poon C S (2018) Methods for the assessment of carbon dioxide absorbed by cementitious materials[M]//Carbon Dioxide Sequestration in Cementitious Construction Materials. Woodhead Publishing, 2018: 103-126. https://doi.org/10.1016/B978-0-08-102444-7.00006-X |
[24] |
Gomes H C, Reis E D, Azevedo R C, et al. (2023) Carbonation of Aggregates from Construction and Demolition Waste Applied to Concrete: A Review. Buildings 13: 1097. https://doi.org/10.3390/buildings13041097 doi: 10.3390/buildings13041097
![]() |
[25] |
Gomes R I, Farinha C B, Veiga R, et al. (2021) CO2 sequestration by construction and demolition waste aggregates and effect on mortars and concrete performance-An overview. Renew Sust Energ Rev 152: 111668. https://doi.org/10.1016/j.rser.2021.111668 doi: 10.1016/j.rser.2021.111668
![]() |
[26] |
Xiao J, Zhang H, Tang Y, et al. (2022) Fully utilizing carbonated recycled aggregates in concrete: Strength, drying shrinkage and carbon emissions analysis. J Clean Prod 377: 134520. https://doi.org/10.1016/j.jclepro.2022.134520 doi: 10.1016/j.jclepro.2022.134520
![]() |
[27] |
Wang T, Li K, Liu D, et al. (2022) Estimating the carbon emission of construction waste recycling using grey model and life cycle assessment: a case study of Shanghai. Int J Environ Res Public Health 19: 8507. https://doi.org/10.3390/ijerph19148507 doi: 10.3390/ijerph19148507
![]() |
[28] |
Liu H, Guo R, Tian J, et al. (2022) Quantifying the carbon reduction potential of recycling construction waste based on life cycle assessment: a case of Jiangsu province. Int J Environ Res Public Health 19: 12628. https://doi.org/10.3390/ijerph191912628 doi: 10.3390/ijerph191912628
![]() |
1. | Lusy Widowati, Mohammad Gousuddin, Mohammad Nizamuddin Inamdar, Emil R. Kaburuan, 2024, Toward Indonesia Cement Decarbonization: A Survey on Machine Learning Model, 979-8-3315-2360-2, 1, 10.1109/ICOT64290.2024.10936965 |
Group of Countries | Cement CO2 |
Low-income countries | 15.36 |
Lower-middle-income countries | 378.49 |
Upper-middle-income countries | 1055.12 |
High-income countries | 223.61 |
Year | Total C & D waste in MT per year | Amount of C & D waste processing and recycling in MT per year |
2019 | 1658864.3 | 27402 |
2020 | 4704568.7 | 44004 |
2021 | 3729636.1 | 80098.1 |
2022 | 6256093 | 129304 |
2023 | 3008585 | 218678 |
Sr.no | (A) Year |
(B) Total C & D waste generated | (C) Processing and recycling of C & D waste | (D) Carbon equivalent processing /recycling kg CO2 /ton of waste (+) | (E) Carbon equivalent transportation of C & D waste kg CO2 kg /ton (+) |
(F) Carbon equivalent saved due to recycling credits x kg /ton (-) | (G) Total carbon equivalent generated in kg CO2 / ton |
1 | 2019 | 1658864 | 27402 | 36324 | 94631 | 31857 | 99098 |
2 | 2020 | 4704569 | 44004 | 58332 | 151965 | 51158 | 159138 |
3 | 2021 | 3729637 | 80098 | 276615 | 106179 | 93121 | 289672 |
4 | 2022 | 6256093 | 129304 | 171407 | 446545 | 150328 | 467624 |
5 | 2023 | 3008585 | 218678 | 289882 | 755194 | 254233 | 790842 |
Sr. No. | Year | Total quantity of conventional concrete | Total quantity of concrete with RCA (75%) | Aggregates replaced with RCA (25 %) | The carbon equivalent of conventional concrete | Carbon equivalent of 75% concrete | Carbon equivalent of 25% RCA concrete | Total carbon equivalent if RCA is used in construction (75% + 25% RCA) | Difference between the carbon equivalent of conventional concrete and RCA replaced concrete | % saving |
1 | 2019 | 109608 | 82206 | 27402 | 8012329 | 6009247 | 99098 | 6108345 | 1903984 | 23.76 |
2 | 2020 | 176015 | 132011 | 44004 | 12866682 | 9650011 | 159138 | 9809150 | 3057532 | |
3 | 2021 | 320392 | 240294 | 80098 | 23420679 | 17565509 | 289672 | 17855181 | 5565497 | |
4 | 2022 | 517216 | 387912 | 129304 | 37808490 | 28356367 | 467624 | 28823991 | 8984498 | |
5 | 2023 | 874712 | 656034 | 218678 | 63941447 | 47956085 | 790842 | 48746928 | 15194519 |
Sr. No. | Year | Total quantity of conventional concrete for 100% C & D waste utilization | Total quantity of concrete with RCA (75%) for 100% C & D waste utilization | Aggregates replaced with RCA (25 %) for 100% C & D waste utilization | Carbon equivalent of conventional concrete for 100% C & D waste utilization | Carbon equivalent of 75% concrete for 100% C & D waste utilization | Carbon equivalent of 25% RCA concrete for 100% C & D waste utilization | Total carbon equivalent if RCA is used in construction (75% + 25% RCA) for 100% C & D waste utilization | Difference between the carbon equivalent of conventional concrete and RCA replaced concrete for 100% C & D waste utilization | % saving |
1 | 2019 | 6635457 | 4976593 | 1658864 | 485051909 | 363788931 | 99098 | 363888030 | 121163879 | 24.99 |
2 | 2020 | 18818275 | 14113706 | 4704569 | 1375615882 | 1031711912 | 159138 | 1031871050 | 343744832 | |
3 | 2021 | 14918544 | 11188908 | 3729636 | 1090545596 | 817909197 | 289672 | 818198869 | 272346727 | |
4 | 2022 | 25024372 | 18768279 | 6256093 | 1829281593 | 1371961195 | 467624 | 1372428819 | 456852774 | |
5 | 2023 | 12034340 | 9025755 | 3008585 | 879710254 | 659782691 | 790842 | 660573533 | 219136721 |
Group of Countries | Cement CO2 |
Low-income countries | 15.36 |
Lower-middle-income countries | 378.49 |
Upper-middle-income countries | 1055.12 |
High-income countries | 223.61 |
Year | Total C & D waste in MT per year | Amount of C & D waste processing and recycling in MT per year |
2019 | 1658864.3 | 27402 |
2020 | 4704568.7 | 44004 |
2021 | 3729636.1 | 80098.1 |
2022 | 6256093 | 129304 |
2023 | 3008585 | 218678 |
Sr.no | (A) Year |
(B) Total C & D waste generated | (C) Processing and recycling of C & D waste | (D) Carbon equivalent processing /recycling kg CO2 /ton of waste (+) | (E) Carbon equivalent transportation of C & D waste kg CO2 kg /ton (+) |
(F) Carbon equivalent saved due to recycling credits x kg /ton (-) | (G) Total carbon equivalent generated in kg CO2 / ton |
1 | 2019 | 1658864 | 27402 | 36324 | 94631 | 31857 | 99098 |
2 | 2020 | 4704569 | 44004 | 58332 | 151965 | 51158 | 159138 |
3 | 2021 | 3729637 | 80098 | 276615 | 106179 | 93121 | 289672 |
4 | 2022 | 6256093 | 129304 | 171407 | 446545 | 150328 | 467624 |
5 | 2023 | 3008585 | 218678 | 289882 | 755194 | 254233 | 790842 |
Sr. No. | Year | Total quantity of conventional concrete | Total quantity of concrete with RCA (75%) | Aggregates replaced with RCA (25 %) | The carbon equivalent of conventional concrete | Carbon equivalent of 75% concrete | Carbon equivalent of 25% RCA concrete | Total carbon equivalent if RCA is used in construction (75% + 25% RCA) | Difference between the carbon equivalent of conventional concrete and RCA replaced concrete | % saving |
1 | 2019 | 109608 | 82206 | 27402 | 8012329 | 6009247 | 99098 | 6108345 | 1903984 | 23.76 |
2 | 2020 | 176015 | 132011 | 44004 | 12866682 | 9650011 | 159138 | 9809150 | 3057532 | |
3 | 2021 | 320392 | 240294 | 80098 | 23420679 | 17565509 | 289672 | 17855181 | 5565497 | |
4 | 2022 | 517216 | 387912 | 129304 | 37808490 | 28356367 | 467624 | 28823991 | 8984498 | |
5 | 2023 | 874712 | 656034 | 218678 | 63941447 | 47956085 | 790842 | 48746928 | 15194519 |
Sr. No. | Year | Total quantity of conventional concrete for 100% C & D waste utilization | Total quantity of concrete with RCA (75%) for 100% C & D waste utilization | Aggregates replaced with RCA (25 %) for 100% C & D waste utilization | Carbon equivalent of conventional concrete for 100% C & D waste utilization | Carbon equivalent of 75% concrete for 100% C & D waste utilization | Carbon equivalent of 25% RCA concrete for 100% C & D waste utilization | Total carbon equivalent if RCA is used in construction (75% + 25% RCA) for 100% C & D waste utilization | Difference between the carbon equivalent of conventional concrete and RCA replaced concrete for 100% C & D waste utilization | % saving |
1 | 2019 | 6635457 | 4976593 | 1658864 | 485051909 | 363788931 | 99098 | 363888030 | 121163879 | 24.99 |
2 | 2020 | 18818275 | 14113706 | 4704569 | 1375615882 | 1031711912 | 159138 | 1031871050 | 343744832 | |
3 | 2021 | 14918544 | 11188908 | 3729636 | 1090545596 | 817909197 | 289672 | 818198869 | 272346727 | |
4 | 2022 | 25024372 | 18768279 | 6256093 | 1829281593 | 1371961195 | 467624 | 1372428819 | 456852774 | |
5 | 2023 | 12034340 | 9025755 | 3008585 | 879710254 | 659782691 | 790842 | 660573533 | 219136721 |