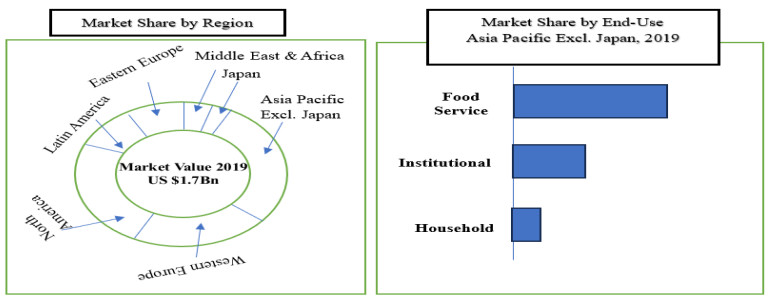
Customers' growing concern for environmentally friendly goods and services has created a competitive and environmentally responsible business scenario. This global awareness of a green environment has motivated several researchers and companies to work on reducing carbon emissions and sustainable supply chain management. This study explores a sustainable supply chain system in the context of an imperfect flexible production system with a single manufacturer and multiple competitive retailers. It aims to reduce the carbon footprints of the developed system through uncertain human learning. Three carbon regulation policies are designed to control carbon emissions caused by various supply chain activities. Despite the retailers being competitive in nature, the smart production system with a sustainable supply chain and two-level screening reduces carbon emissions effectively with maximum profit. Obtained results explore the significance of uncertain human learning, and the total profit of the system increases to 0.039% and 2.23%, respectively. A comparative study of the model under different carbon regulatory policies shows a successful reduction in carbon emissions (beyond 20%), which meets the motive of this research.
Citation: Richi Singh, Dharmendra Yadav, S.R. Singh, Ashok Kumar, Biswajit Sarkar. Reduction of carbon emissions under sustainable supply chain management with uncertain human learning[J]. AIMS Environmental Science, 2023, 10(4): 559-592. doi: 10.3934/environsci.2023032
[1] | Mowmita Mishra, Santanu Kumar Ghosh, Biswajit Sarkar . Maintaining energy efficiencies and reducing carbon emissions under a sustainable supply chain management. AIMS Environmental Science, 2022, 9(5): 603-635. doi: 10.3934/environsci.2022036 |
[2] | Subhash Kumar, Ashok Kumar, Rekha Guchhait, Biswajit Sarkar . An environmental decision support system for manufacturer-retailer within a closed-loop supply chain management using remanufacturing. AIMS Environmental Science, 2023, 10(5): 644-676. doi: 10.3934/environsci.2023036 |
[3] | Antonio Zanin, Ivonez Xavier de Almeida, Francieli Pacassa, Fabricia Silva da Rosa, Paulo Afonso . Maturity level of environmental management in the pulp and paper supply chain. AIMS Environmental Science, 2021, 8(6): 580-596. doi: 10.3934/environsci.2021037 |
[4] | Zeynab Rezazadeh Salteh, Saeed Fazayeli, Saeid Jafarzadeh Ghoushchi . Evaluation and prioritization of barriers to the implementation of the eco-regenerative supply chains using fuzzy ZE-numbers framework in group decision-making. AIMS Environmental Science, 2024, 11(4): 516-550. doi: 10.3934/environsci.2024026 |
[5] | Mehrbakhsh Nilashi, Rabab Ali Abumalloh, Hossein Ahmadi, Mesfer Alrizq, Hamad Abosaq, Abdullah Alghamdi, Murtaza Farooque, Syed Salman Mahmood . Using DEMATEL, clustering, and fuzzy logic for supply chain evaluation of electric vehicles: A SCOR model. AIMS Environmental Science, 2024, 11(2): 129-156. doi: 10.3934/environsci.2024008 |
[6] | Soumya Kanti Hota, Santanu Kumar Ghosh, Biswajit Sarkar . A solution to the transportation hazard problem in a supply chain with an unreliable manufacturer. AIMS Environmental Science, 2022, 9(3): 354-380. doi: 10.3934/environsci.2022023 |
[7] | Jamshid Ali . Environmental resilience: transition to regenerative supply chain management. AIMS Environmental Science, 2024, 11(2): 107-128. doi: 10.3934/environsci.2024007 |
[8] | Soumya Kanti Hota, Santanu Kumar Ghosh, Biswajit Sarkar . Involvement of smart technologies in an advanced supply chain management to solve unreliability under distribution robust approach. AIMS Environmental Science, 2022, 9(4): 461-492. doi: 10.3934/environsci.2022028 |
[9] | Hsin-Yao Hsu, Ming-Hon Hwang, Yuan-Shyi Peter Chiu . Development of a strategic framework for sustainable supply chain management. AIMS Environmental Science, 2021, 8(6): 532-552. doi: 10.3934/environsci.2021034 |
[10] | Seiran Haghgoo, Jamil Amanollahi, Barzan Bahrami Kamangar, Shahryar Sorooshian . Decision models enhancing environmental flow sustainability: A strategic approach to water resource management. AIMS Environmental Science, 2024, 11(6): 900-917. doi: 10.3934/environsci.2024045 |
Customers' growing concern for environmentally friendly goods and services has created a competitive and environmentally responsible business scenario. This global awareness of a green environment has motivated several researchers and companies to work on reducing carbon emissions and sustainable supply chain management. This study explores a sustainable supply chain system in the context of an imperfect flexible production system with a single manufacturer and multiple competitive retailers. It aims to reduce the carbon footprints of the developed system through uncertain human learning. Three carbon regulation policies are designed to control carbon emissions caused by various supply chain activities. Despite the retailers being competitive in nature, the smart production system with a sustainable supply chain and two-level screening reduces carbon emissions effectively with maximum profit. Obtained results explore the significance of uncertain human learning, and the total profit of the system increases to 0.039% and 2.23%, respectively. A comparative study of the model under different carbon regulatory policies shows a successful reduction in carbon emissions (beyond 20%), which meets the motive of this research.
In today's world, customers have added environmental expectations for the products they purchase for their healthy living. That is why the market for sustainable products is becoming competitive and growing fast. In 2018, Nielsen predicted sales of sustainable products in the U.S. to be up to 39.9% greater in 2021 than in 2014 [1]. This creates new business opportunities for industrialists to enter this competitive market by promoting a sustainable and smart product. Although these products are green and sophisticated and make people's lives easier, producing such progressive products releases greenhouse gases, mainly carbon dioxide (CO2), into the atmosphere, which is a threat to our earth.
The American space agency, NASA, has also observed that industrial activities have increased atmospheric CO2 levels from 280 to 400 parts per million in the last 150 years [2]. However, industries could overcome this problem by designing strategies like a sustainable and smart production system, green product management, carbon capture, customer awareness, and so on in a supply chain [3].
Parsaeifar et al. [4] examined the effect of pricing, advertising, and green product management in a competitive supply chain. Ullah et al. [5] worked on remanufacturing and repair of returned products in a closed-loop supply chain management (CLSCM). Xiao et al. [6] worked on a sustainable supply chain (SSC) where the producer motivates its suppliers to invest in sustainable technology through price and cost-sharing contracts. They found a positive effect of these contracts on the sustainable technology level and profit of all supply chain members. The pricing strategy of retailers was very effective in the purchasing trend of consumers.
Due to strict governmental laws and regulations against plastic, the demand for biodegradable disposable cutlery made of wood is high. Figure 1 presents a global market analysis of disposable cutlery. Therefore, the government has designed policies to introduce eco-friendly and sustainable products in the market. In India, the Bharat stage emission standards (BSES) have been implemented by the government to control increasing air pollution. In 2016, the government of India urged the adoption of Bharat Stage-6 (BS-VI) norms for vehicular emissions by 2020 rather than the BS-V norms [7]. All this compels the manufacturer to design their production strategies with an environmentally conscious approach and attract customers by spreading awareness toward eco-friendly products. Ecoware is India's largest sustainable food packaging industry and produces 100% natural and biodegradable products made from plant biomass, thereby keeping costs and carbon footprint low. Magnus Eco Concepts is a leading producer of ecological/green commodities produced of areca palm leaf. Environmental attributes of a product are sometimes very confusing for a consumer to assess and trust compared to other available products. In this direction, Singh et al. [8] studied the Ecomark, a tag introduced by the Indian government to identify green products. Bai et al. [9] formulated an inventory system considering a single manufacturer and two competing retailers. They thought of deteriorating products with vendor-managed inventory (VMI) and studied the model under carbon emission policy and green technology investment for centralized and decentralized systems. Li et al. [10] presented a sustainable design for a coal supply chain under four carbon regulation policies.
Carbon footprints are hypersensitive to the technology implemented in the production process. Therefore, manufacturers should produce smart products along with the smart production process for environmental sustainability. Sarkar and Guchhait [11] presented a production system with hybrid carbon policies for reducing emissions from the production and logistics system. They found that a hybrid emissions policy is better than a single carbon policy within a production system.
Getting motivation from the above research studies and keeping the above-described market analysis with environmental conditions in mind, this study proposes the following research in an SSC model. The purpose of the present study is to design an SSC (for one manufacturer and multiple competitive retailers) to
(ⅰ) optimize the total profit along with optimizing the production rate of the manufacturer, order quantities, and selling prices of retailers through an imperfect production system in a coordinated and competitive supply chain,
(ⅱ) reduce the rate of deterioration using preservation technology,
(ⅲ) study the effect of learning in fuzziness, and
(ⅳ) reduce carbon emissions by applying three carbon regulation policies.
We have tried to find the answers to the following research questions in this study:
1) How do the manufacturer and competitive retailers coordinate to optimize their production rate, competitive prices, and order levels in an SSC?
2) How do human learning and two-stage screening enhance the overall performance of a smart production system?
3) How are awareness programs, competitive price-dependent demand, and preservation technology beneficial for smart production and sustainability?
4) How does the concept of learning in fuzziness help to tackle the uncertainty and competitive market scenario?
5) How are flexible production and carbon reduction policies effective for the SSC to achieve sustainability goals?
6) How is the competitive advantage of a carbon-efficient supply chain sustained?
To answer these questions, a supply chain network (one manufacturer and multiple retailers) with an imperfect production system is addressed. An attempt has been made to add the following three key areas of sustainability in the supply chain to enrich its significance.
• Environmental sustainability: This is maintained by manufacturing green products, continuous carbon emission monitoring at each stage (production, holding, waste disposal, transportation, and product deterioration) of the supply chain, and employing carbon reduction policies to lower it. The manufacturer manages the waste disposal setup to avoid unnecessary landfills for throwing away waste [12,13].
• Economic sustainability: This is achieved by
(ⅰ) a smart/flexible production system and maintaining cooperation among members of the supply network (besides, retailers have a competition on price),
(ⅱ) retailer strategies to raise customer awareness through awareness programs (that their products are eco-friendly) and competitive prices,
(ⅲ) variable rate of deterioration (a function of a maximum lifetime and the cost due to preservation policies) at the retailer end, and
(ⅳ) a strong inspection process to maintain goodwill toward the product in the market. In this process, first, the manufacturer carries out the screening through a machine. Second, the retailer inspects it manually and returns defective products to the manufacturer. The learning effect can reduce errors in the manual screening process. Low-quality products are sent to an alternate market to gain profit [14].
• Social sustainability: This is covered by adding
(ⅰ) learning in fuzziness to reduce market ambiguity,
(ⅱ) human learning in screening to reduce the percentage of defectives,
(ⅲ) awareness programs of retailers to increase customer consciousness toward the purchase of environmentally friendly products, and
(ⅳ) implementation of carbon emission policies along with proper waste management setup to reduce the negative impact on ecology [15,16].
In this section, the review of literature based on the contribution of the study is presented.
Nowadays, industries focus on carbon-efficient supply chains to take the market's competitive advantage. Usually, supply chain members design some pricing strategies that attract customers to overcome market competitiveness. Figure 2 shows the annual total CO2 emissions variations across the world. From 1950 to 2018, emissions increased rapidly. From Figure 2, it is clear that carbon emissions in India exceed 15 billion tons. In this direction, Wee and Chung [14] worked on an integrated buyer and supplier system consisting of decaying and green component (computer power-supply) production with just-in-time (JIT) deliveries and remanufacturing. In that model, a new approach was applied to coordinating the storage time and the supplier's production level. Wu and Kung [16] addressed SSC with competitive prices to reduce carbon emissions. It was concluded that financial risk is a significant factor in controlling emissions, which government initiatives should balance. Bonney and Jaber [17] investigated the effects of inventory planning on environmentally responsible models in detail. They included non-traditional costs related to packaging, waste management, and transportation for promoting green production. Tayyab et al. [18] developed a multi-stage SSC considering product quality from a textile production process. They discussed the carbon emissions from the production process for sustainable development.
Mukhopadhyay and Goswami [20] presented an economical manufacturing system containing defective products under two cases. In the first case, the pollution cost was constant, while in the other case, it was variable. Dye and Yang [21] worked on developing a sustainable model by adding commercial borrowing with environmental regulations. The demand was assumed to depend on the borrowing period and carbon cap-and-trade regulation. Further, using an algebraic method, Sarkar et al. [22] derived a supplier-manufacturer-retailer model under carbon emissions and variable shipping costs. Mishra et al. [23] discussed carbon policies for an integrated emission-controlled system. They found minimum cost with less deterioration and emissions. Tiwari et al. [24] analyzed a coordinated vendor-buyer manufacturing process model, which includes the production of defectives along with perfect items. Kundu and Chakrabarti [25] examined a manufacturing model, including remanufacturing with waste disposal, and investigated the impact of carbon emission policies (carbon cap and trade, carbon tax, and strict carbon cap) on optimal results and amount of carbon emissions. It was assumed that the company sells its product in two markets, and the return rate of the used items depended on the buyback price of the company. Jamali and Rasti-Barzoki [26] worked on a competitive pricing scenario for green and non-green item producers to maintain economic and environmental sustainability in a supply chain using game theory. The model was analyzed under integrated and non-integrated scenarios, and it was found that the integrated policy was beneficial. Garai and Sarkar [27] incorporated a customer-centric supply chain where products from the first chain are sent to the second chain through remanufacturing. Their SSC system was emissions-controlled. Hosseini-Motlagh et al. [28] designed an acquisition price strategy for producers to enhance the collection of used products in a sustainable closed-loop supply chain (CLSC). That strategy increased the market demand as well as a collection of used items. Yadav et al. [29] introduced a selection procedure of cross-price elasticity between multiple deteriorated products. They designed an SSC by reducing emissions from the supply chain. Sarkar et al. [30] discussed a CLSC for sustainable supplier selection within the SSC. They found a cost-efficient policy through a metaheuristic approach for returnable packaging products. Huang et al. [31] and Manupati et al. [32] studied various carbon reduction policies in SSC. Mishra et al. [33] examined green technology investment and preservation technology to control emissions and deterioration in a supply chain with trade credit. The model was studied under full, partial, and no backorder. With green investment, Sarkar and Bhuniya [34] introduced a flexible manufacturing system under SSC. They examined the connection between service and green investment within a flexible production system. Recently, Alamri et al. [35] developed an economic order quantity (EOQ) model with a learning effect, carbon emissions, and inflation. Wang et al. [36] studied global value chains and carbon reduction in developing countries. They explored a value-added accounting method under a new trade accounting framework to calculate the real emissions embodied in trade using the fuzzy C-means clustering method. Sun and Zhong [37] developed a low-carbon supply chain to study the effects of fairness concerns on optimal policy and utility. Kang and Tan [38] investigated a sustainable supply chain game model under the cap-and-trade policy to study the investment decisions of manufacturers and suppliers. It suggested investing in decarbonization technologies to reduce carbon emissions.
Learning-based supply chains under inflation are rarely studied. It is a clear research gap that should be covered. Although the models presented above introduced low-carbon practices in SSC, no one had worked on implementing government policies to curb emissions, such as carbon caps and carbon trade policies in competitive SSC.
Many researchers in the literature have considered the production rate as constant. Most of the carbon emissions are caused during the manufacturing process, holding off the inventories, solid waste disposal, deterioration, and damage in the transportation of the product. Therefore, nowadays, manufacturers prefer smart production systems to curb overall carbon footprints. Generally, smart production is referred to as a controllable/variable production rate. The basic traditional production models could be transformed into smart production systems by utilizing a flexible production rate, strong screening, and emission reduction. Sarkar et al. [39] discussed the environmental effects of a hybrid manufacturing-remanufacturing system without incorporating a smart production system. Glock [40] examined flexible production on total cost by reducing production at different time intervals in a two-level inventory system. It was concluded that reducing the production rate resulted in a lesser overall cost. Glock [41] extended the Glock [40] model into a multi-level system with varying production rates and made a comparison with a constant rate of production. Singhal and Singh [42] worked on a volume-flexible inventory process with machine breakdown under uncertainty and shortages. Singhal and Singh [43] extended the Singhal and Singh [42] model, assuming damageable items with partially fulfilled shortages and the backorder rate as random. In addition, the uncertainty of the market was covered by the concept of randomness and the learning effect. Sarkar et al. [23] examined a system considering a fixed lifetime of decaying items and a variable backorder rate. Tayal et al. [44] applied preservation technology to decrease the product deterioration rate in a two-stage coordinated production model with shortages and delays in deficits.
In addition, a Stackelberg game method was applied to find the solution to the problem. Manna et al. [45] worked on a defective manufacturing system assuming variable demand with screening. The production rate was variable, but they did not consider shortages in their model. Sarkar and Chung [46] designed a supply chain network with a flexible production system in which the production rate lies within a prescribed interval. Gautam et al. [12] emphasized reducing defects and carbon emissions in a two-level supply network production system. The study involved a strong (multiple) inspection process to decrease waste, and they constructed two different models using the integrated problem-solving approach and Stackelberg policy, respectively. The results showed that the integrated policy is beneficial for reducing emissions without affecting the profit of green SSC rather than the Stackelberg policy. Dey et al. [47] proved that autonomation policy can converge over human inspection error through the automated inspection process, but all industries may not support the investment in the automated inspection system. Thus, the industry may have human inspection if autonomation is not utilized. Sarkar and Sarkar [48] developed a production model of pure biofuel, ensuring minimum energy consumption and carbon emission. They applied a controllable production rate to minimize the impurities and impure fuel was again reworked to produce pure fuel. Mridha et al. [49] showed combined effects of improved quality of biofuel and carbon emission control with a flexible production rate in an SSC. The models presented above did not introduce emission reduction policies for smart production and focused neither on reducing deterioration nor on implementing preservation technology, which is a clear research gap.
Learning in fuzziness has broad applications. It is a concept that handles the uncertainty level of the existing information base, usually gained by time or the number of times work is done. It is a mixture of fuzzy systems and learning specialties. Although many researchers have worked on learning in fuzziness, it is still a new concept for the majority. Bera et al. [50] incorporated the effect of learning in the setup cost of every production cycle in a deteriorating model. Glock et al. [51] introduced a learning effect in fuzzy demand in an EOQ model. It was observed that the fuzziness of the information decreased as the learning rate decreased. Pathak et al. [52] studied the learning and forgetting effects in a production process with shortages. It included two models with fixed and fuzzy costs assuming variable demand and decay rates. Two models were analyzed with the help of three examples. Yadav et al. [53] studied the effects of human learning in an inventory model of imperfect production with fuzzy demand and error in screening. Kumar and Goswami [54] added a learning effect in a production model in an imprecise environment. The faulty items were reworked in that model, and shortages were partially fulfilled. Kazemi et al. [55] developed a fuzzy model considering learning and backorders. It was found that learning in fuzziness reduces the cost and increases the performance of the system. Shekarian et al. [56] extended an imperfect quality model with two different holding costs under learning in an imprecise environment. In the model, the nature of the demand parameter is fuzzy and a function of marketing cost. Sarkar et al. [57] investigated a coordination supply chain model for advertisement-dependent demand under a fuzzy environment. They considered the market demand fuzzy and compared results for crisp and fuzzy scenarios. Giri and Masanta [58] examined the effect of learning in the manufacturing process of a CLSCM. Saha and Chakrabarti [59] studied the effect of learning on the production cost in a supply chain with a return policy. Dey et al. [60] analyzed an SSC with an automated inspection facility such that the supply chain could face a minimum loss due to imperfect production. They did not consider uncertainty within the model. Recently, Jayaswal et al. [61] developed an inventory model with trade credit and backorders. In the model, there were effects of learning and trade credit financing with fuzzy and fuzzy learning scenarios. Poursoltan et al. [62] studied the impact of human learning in a vendor-managed closed-loop supply network. Alsaedi et al. [63] developed a sustainable green supply chain model with carbon emissions and two-stage inspection under learning in a fuzzy environment. Supply chain models that implement two stages of human learning are rarely studied. The studies presented above show that no one focused on SSC with learning in fuzziness. It is a major research gap in the existing literature.
From the above literature survey and gap analysis from Table 1, it is observed that there is a clear research gap in introducing learning in fuzziness in an environmentally sensitive and imperfect production system with two-level screening and variable deterioration rate along with awareness program and price-sensitive demand. Hence, attempting to cover this research gap, the present study was done. To the best of our knowledge, no research has yet used the idea of learning in fuzziness in an SSC. The present study has not been previously labeled.
Author(s) | Sustainable supply chain | Variable deterioration | Learning in fuzziness | Carbon emissions policies | Variable demand | Imperfect production | Inspection error | Partial backlogging | Scope |
Ullah et al. [5] | Yes | - | - | - | - | - | - | - | Used product collection and remanufacturing |
Bai et al. [9] | - | - | Yes | Yes | - | - | - | - | One distributor, two purchasers |
Sarkar and Guchhait [11] | Yes | - | - | Yes | - | Yes | - | - | Closed-loop logistic system |
Gautam et al. [12] | Yes | - | - | - | - | Yes | - | - | One distributor, one purchaser |
Ullah and Sarkar [13] | Yes | - | - | Yes | Yes | - | - | - | Product quality and radio frequency identification |
Tayyab et al. [18] | - | - | - | Yes | Yes | Yes | Yes | - | Multi-stage textile production system |
Mukhopadhyay and Goswami [20] | - | - | - | Yes | - | Yes | - | - | One manufacturer |
Dye and Yang [21] | Yes | Yes | - | - | Yes | Yes | - | Yes | One manufacturer |
Kundu and Chakrabarti [25] | - | Yes | - | Yes | - | - | - | - | One distributor, one purchaser |
Daryanto et al. [27] | - | Yes | - | - | - | - | - | - | One distributor, one purchaser |
Manna et al. [45] | - | Yes | - | - | Yes | - | - | One manufacture | |
Kumar and Goswami [54] | - | - | Yes | - | - | Yes | - | - | One manufacturer |
Habib et al. [64] | - | - | - | - | - | - | - | - | Possibilistic programming approach |
Lee and Kim [65] | - | Yes | - | - | - | Yes | - | - | One distributor, one purchaser |
Singh et al. [66] | Yes | - | - | Yes | - | Yes | - | - | SSC for waste management |
This paper | Yes | Yes | Yes | Yes | Yes | Yes | Yes | Yes | Single supplier, multiple competitive buyer |
The current study concerns a supply chain network containing a single manufacturer and multiple competitive retailers. The manufacturer performs the screening process during production with the machine's help. The screening process segregates the produced lot into the following three categories:
(ⅰ) perfect products, which are delivered to multiple retailers;
(ⅱ) products with some design flaws, which the manufacturer sells in an alternate market with low prices, and
(ⅲ) waste products, which the manufacturer disposes of at some disposal cost. Figure 3 illustrates the variations of product level in the described supply network.
When retailers receive the products, they also perform manual screening. Due to manual selection, error in screening is evident, which can be reduced by introducing the learning effect. After screening, retailers use the perfect products to satisfy their market demands and send the waste products to the manufacturer, as the manufacturer has waste management set up. First, a basic (crisp) mathematical structure for manufacturers and retailers is established. Then, it is formulated with a coordinated supply chain model, including carbon emissions. Further, the model is fuzzified by using a triangular fuzzy number and defuzzified with the help of the signed distance method. After defuzzification, the obtained fuzzy model is extended to the model with learning in fuzziness. Three carbon emissions policies are designed to check carbon emissions in the model with learning in fuzziness.
The following notation is used to design the mathematical model.
Notation for the manufacturer
to machine setup time
IM(t) height of the manufacturer's inventory with time (t) during the production cycle
COM fixed setup cost per cycle ($/setup)
T length of the production cycle of the manufacturer (year)
P1 probability of perfect products produced during the production process
P2 probability of products having some design flaws, produced during the production process
P3 probability of waste/scrap products produced during the production process
CM unit manufacturing cost ($/unit)
CSM unit screening cost for the manufacturer ($/unit)
CW unit disposal cost of waste/scrap products ($/unit)
CTA unit shipment cost of the product for shipment from the manufacturer to an alternate market ($/unit)
CPA unit selling price in alternate market ($/unit)
HM unit holding cost for the manufacturer ($/unit)
Q units produced in each production cycle
CTMi unit shipment cost of the product for shipment from the manufacturer to the ith retailer ($/unit)
ξM emissions element of production (tonyear2/unit3)
ηM emissions element of production (tonyear/unit2)
λM emissions element of production (ton/unit)
EHM carbon emissions in inventory holding at the manufacturer's end (ton/unit)
EWM carbon emissions in the waste disposal process of the manufacturer (ton/unit)
ETMi carbon emissions in shipping products from the manufacturer to the ith retailer (ton/unit)
ETA carbon emissions in shipping products with design flaws from the manufacturer to an alternate market (ton/unit)
Notation for ith retailer
IRi inventory level of the ith retailer
Qi order quantity of the ith retailer
Li lost sale quantity for the ith retailer
Di(N,y1,y2,...,yn) demand rate of the ith retailer
N frequency of advertisement of the ith retailer
CORi ordering cost of the ith retailer ($/order)
HRi unit holding cost of the ith retailer ($/unit)
HDRi unit deterioration cost of inventory of the ith retailer ($/unit)
HWRi unit holding cost of waste products (which is less than HRi ) ($/unit)
CSRi unit screening cost of the ith retailer ($/order)
CBi unit backlogging cost of the ith retailer ($/order/time)
CLi Unit lost sale for the ith retailer ($/order/time)
δi(m) Percentage of defective products, where m is the number of shipments
ϵ Preservation technology cost for each retailer ($/unit)
α Learning exponent
ki(ϵ) Effect of cost of preservation technology cost of the ith retailer
θi(t) Rate of deterioration of the product at the ith retailer
αi(t) Reduced rate of deterioration of the product at the ith retailer
A Error in screening (Type 1)
B Error in screening (Type 2)
xi Unit screening rate for the ith retailer
Bi Unit backlogging rate for the ith retailer
Si Total shortage per cycle for the ith retailer
CAi Advertisement cost per advertisement for the ith retailer
EHRi Carbon emissions in inventory holding from ith retailer (ton/unit)
EDRi Carbon emissions from deteriorating products for the ith retailer (ton/unit)
EHWRi Carbon emissions in holding waste products by ith retailer (ton/unit)
ϑ Carbon tax per unit of carbon emissions
Ccap Carbon emissions cap
∈1 Unit buying cost of carbon emissions credit
∈2 Unit selling cost of carbon emissions credit
EC Total amount of carbon emissions generated
Decision variables
wi unit wholesale purchasing price for the ith retailer ($/unit)
yi unit selling price of the ith retailer ($/unit) ($/unit)
P rate of production (unit/year)
The model is designed according to these assumptions.
1) In this study, the proposed supply chain considers one manufacturer and multiple retailers over an infinite planning horizon.
2) The manufacturer produces eco-friendly products, and the production rate is the decision variable, i.e., volume flexibility is considered.
3) The manufacturer adopts the lot-for-lot policy during each production cycle for delivering finished products to retailers.
4) During production, 100% of the screening process through the machine is carried out at the manufacturer's end. The screening process ends as the production cycle completes. Based on screening, products are segregated into three different categories.
5) Due to transportation, wear and tear is unavoidable. Retailers with a high screening rate carry out a screening process manually.
6) Lead time from ordering products to the supply of products to the retailers is negligible.
7) On the increasing number of shipments, the percentage (%) of defective products is defined as δi(m)=bg+ecm, where b, g are model parameters, c is the learning exponent, and m is the cumulative number of shipments.
8) With the help of advertisement policy, retailers can make the customers aware that their products are eco-friendly to get a competitive edge in the market. As retailers are considered competitors, the pricing policy of one will influence the market of the other. Thus, a retailer's demand depends on the frequency of advertisement, the selling price proposed by retailers, and the selling price fixed by other retailers.
Di(N,y1,y2,...,yn)=Nρi(ai+∑n(j=1,j≠i)γjyjyβii), |
where N is the number of advertisements, ai(>0) is the market base, βi(>0) is the elasticity of demand regarding the selling price, and γi(>0) and ρi(>0) are the effects of the competitor's selling price and advertisements on demand, respectively.
9) Rate of deterioration θi(t)=11+li−t is considered as the function of maximum lifetime. Here, li is the lifetime (maximum) of the product for the ith retailer, and limt→liθi(t)=1.
10) A product's lifetime (maximum) can be improved by adopting different preservation policies. The rate of deterioration at the retailer's end is considered as the function of maximum lifetime and cost due to the adaptation of preservation policies. The resultant deterioration rate is αi(t)=11+li+ki(ϵ)−t.
11) The effect of preservation technology cost is defined as ki(ϵ)=ui+viϵ, where (ui>0) and (vi>0) are model parameters.
12) Partial backlogging is considered here at the retailer's end.
13) Carbon emissions costs are considered for manufacturing, transportation, waste disposal, inventory holding, and keeping the deteriorating items.
Here, a basic model for the manufacturer and retailers is presented. After that, supply chain models are developed in a crisp, fuzzy, and fuzzy learning environment considering without any carbon regulatory authority. Further, it is extended with some carbon regulatory mechanisms.
Formulation of manufacturer inventory model
The inventory level at the manufacturer end follows the pattern depicted in Figure 4. During production, the inventory size of the manufacturer increases (time to) continually up to time T. In [to, T], the change in inventory size can be written as
dIM(t)dt=P,to≤t<T. | (1) |
Using initial condition IM(to)=0, the solution of Eq 1 is given by
IM(t)=P(t−to),to≤t<T. | (2) |
Total products manufactured per cycle
Q=P(T−to). | (3) |
The screening process is completed as soon as the production is completed. It separates the manufactured products into three categories: (ⅰ) perfect products with probability P1, (ⅱ) products with design flaws with probability P2 and (ⅲ) waste or scrap products with probability P3. Out of the total of manufactured products, P1Q are delivered to retailers with zero lead time.
The total cost of the manufacture is the summation of the total holding cost, setup price, manufacturing cost, screening cost, waste disposal cost, and transportation cost. For a detailed calculation of these costs, see Appendix 1.
TCM=HMP(T−to)22+CMP(T−to)+COM+CSMP(T−to)+CWP3P(T−to)+∑ni=1CTMiP1P(T−to)+CTAP2P(T−to). | (4) |
Carbon emissions in production is (ξMP2−ηMP+λM)P(T−to).
Carbon emission in inventory holding is (EHMP(T−tO)2)/2.
Carbon emissions in waste disposal is EWMP3P(T−to).
Therefore, total carbon emissions in the transportation process is ∑ni=1ETMiP1P(T−to)+ETAP2P(T−to).
Total carbon emissions in the manufacturing process is
EM=(ξMP2−ηMP+λM)P(T−to)+(EHMP(T−tO)2)/2+EWMP3P(T−to)+∑ni=1ETMiP1P(T−to)+ETAP2P(T−to). | (5) |
The total profit of the manufacturer considering carbon emissions is as follows:
ZM(P,wi)=∑ni=1wiQi+CPAP2P(T−to)−[HMP(T−to)22+CMP(T−to)+COM+CSMP(T−to)+CWP3P(T−to)+∑ni=1CTMiP1P(T−to)+CTAP2P(T−to)]. | (6) |
Formulation of the retailer's model
The inventory level of the ith retailer is shown in Figure 5. When the ith retailer receives Qi products at time T, some of the products in the lot are found to be damaged. Damage to products may be caused by many reasons, mainly due to the combined pressure of piled stocks during transportation. So, the retailer needs to perform manual screening to sort the defective products. The retailer manually carries out This screening process with a high screening rate. In the proposed model, the retailer's screening process is assumed to be error-prone while screening the products. That is, some of the useful items will be categorized as defective with a probability (1−δi(m))A, whereas some faulty items will be classified as non-defective, with a probability δi(m)B.
The total fraction of defectives for the ith retailer becomes
pi(m)=(1−δi(m))A+δi(m)(1−B). | (7) |
When screening ends, Qi(1−pi(m)) units are found to be perfect quality products, which retailers use to fulfill their demand, and Qipi(m) units of product are found defective. For the ith retailer, the stock at T is Qi. In [T,T1], the inventory level of the ith retailer continuously decreases due to demand and deterioration.
dIRi1(t)dt=−Di−(11+li+ki(ϵ)−t)IRi1(t),T≤t<T1. | (8) |
Using initial condition IRi1(T)=Qi, the solution of Eq 8 is given by
IRi1(t)=Di(1+li+ki(ϵ)−t)log(1+li+ki(ϵ)−t1+li+ki(ϵ)−T)+(1+li+ki(ϵ)−t1+li+ki(ϵ)−T)Qi,T≤t<T1. | (9) |
At time T1, the screening process ends, and the inventory level decreases by Qipi(m) units. In interval [T1,T2], the inventory level of the ith retailer is
dIRi2(t)dt=−Di−(11+li+ki(ϵ)−t)IRi2(t),T1≤t<T2. | (10) |
Using the condition IRi2(T2)=0, Eq 10 gives the solution as
IRi2(t)=Di(1+li+ki(ϵ)−t)log(1+li+ki(ϵ)−t1+li+ki(ϵ)−T2),T1≤t<T2. | (11) |
Using the condition IRi1(T1)=Qipi(m)+IRi2(T1), T1 is obtained as
T1=1+li+ki(ϵ)−Qi(1−pi(m))Dilog(1+li+ki(ϵ)−T1+li+ki(ϵ)−T2). | (12) |
In [T2,2T], a shortage occurs, from which some are backlogged with a backlogging rate Bi.
dIRi3(t)dt=−BiDi,T2≤t<2T. | (13) |
Using the condition IRi3(T2)=0, Eq 13 gives the solution as
IRi3(t)=BiDi(T2−t),T2≤t<2T. | (14) |
Using the condition IRi3(2T)=−Si, T2 is obtained as
T2=2T−SiBiDi. | (15) |
The total cost for the ith retailer can be obtained by summation of ordering cost, buying cost, preservation technology cost, total holding cost of perfect products and waste products, screening cost, backlogging cost, lost sale cost and advertisement cost. For a detailed calculation of these costs, see Appendix 2. The total cost of the ith retailer
=CORi+CSRiQi+wiQi+ϵT++HDRi[Qi−(Qi)2(1−pi(m))Di(1+li+ki(ϵ)−T)log(1+li+ki(ϵ)−T1+li+ki(ϵ)−2T+SiBiDi)−Di(T−SiBiDi)+Qi(1−pi(m))]+CBi2(Si2BiDi)+CLi(1−Bi)(SiBi)+NCAi. | (16) |
Carbon emissions in inventory holding of the ith retailer
=EHRi[(Qi)2(1−pi(m))22Dilog(1+li+ki(ϵ)−T1+li+ki(ϵ)−2T+SiBiDi)+Di4((1+li+ki(ϵ)−2T+SiBiDi)2−(1+li+ki(ϵ)−T)2)+Qi2(1+li+ki(ϵ)−T)((Qi)2(1−pi(m))2Dilog(1+li+ki(ϵ)−T1+li+ki(ϵ)−2T+SiBiDi)2−(1+li+ki(ϵ)−T)2)]+HWRi((Qi)2pi(m)xi)+EHWRi((Qi)2pi(m)xi). |
Carbon emissions from deteriorating products of the ith retailer
=EDRi[Qi−(Qi)2(1−pi(m))Di(1+li+ki(ϵ)−T)log(1+li+ki(ϵ)−T1+li+ki(ϵ)−2T+SiBiDi)−Di(T−SiBiDi)+Qi(1−pi(m))]. |
Total carbon emissions for ith retailer is
ERi=EHRi[(Qi)2(1−pi(m))22Dilog(1+li+ki(ϵ)−T1+li+ki(ϵ)−2T+SiBiDi)+Di4((1+li+ki(ϵ)−2T+SiBiDi)2−(1+li+ki(ϵ)−T)2)+Qi2(1+li+ki(ϵ)−T)((Qi)2(1−pi(m))2Dilog(1+li+ki(ϵ)−T1+li+ki(ϵ)−2T+SiBiDi)2−(1+li+ki(ϵ)−T)2)]+HWRi((Qi)2pi(m)xi)+EHWRi((Qi)2pi(m)xi)+EDRi[Qi−(Qi)2(1−pi(m))Di(1+li+ki(ϵ)−T)log(1+li+ki(ϵ)−T1+li+ki(ϵ)−2T+SiBiDi)−Di(T−SiBiDi)+Qi(1−pi(m))]. |
The total profit of ith retailer is
ZRi(yi,Qi)=yiDi−[CORi+CSRiQi+wiQi+ϵT+NCAi+HRi[(Qi)2(1−pi(m))22Dilog(1+li+ki(ϵ)−T1+li+ki(ϵ)−2T+SiBiDi)+Di4((1+li+ki(ϵ)−2T+SiBiDi)2−(1+li+ki(ϵ)−T)2)+Qi2(1+li+ki(ϵ)−T)((Qi)2(1−pi(m))2Dilog(1+li+ki(ϵ)−T1+li+ki(ϵ)−2T+SiBiDi)2−(1+li+ki(ϵ)−T)2)]+HWRi((Qi)2pi(m)xi)+HWRi((Qi)2pi(m)xi)+HDRi[Qi−Di(T−SiBiDi)−(Qi)2(1−pi(m))Di(1+li+ki(ϵ)−T)log(1+li+ki(ϵ)−T1+li+ki(ϵ)−2T+SiBiDi)+Qi(1−pi(m))]+CBi2(Si2BiDi)+CLi(1−Bi)(SiBi)]. | (17) |
The total profit of n retailers is
ZRi(yi,Qi)=∑ni=1[yiDi−[(CORi+(ΔuCORi−ΔlCORi)4+wiQi)+(CSRi+(ΔuCSRi−ΔlCSRi)4)Qi+(ϵ+(Δuϵ−Δlϵ)4)T+(HRi+(ΔuHRi−ΔlHRi)4)[(Qi)2(1−pi(m))22Dilog(1+li+ki(ϵ)−T1+li+ki(ϵ)−2T+SiBiDi)+Di4((1+li+ki(ϵ)−2T+SiBiDi)2−(1+li+ki(ϵ)−T)2)+Qi2(1+li+ki(ϵ)−T)((Qi(1−pi(m))Dilog(1+li+ki(ϵ)−T1+li+ki(ϵ)−2T+SiBiDi))−(1+li+ki(ϵ)−T)2)]+NCAi2+(HWRi+(ΔuHWRi−ΔlHWRi)4)((Qi)2pi(m)xi)+(HDRi+(ΔuHDRi−ΔlHDRi)4)[Qi−Di(T−SiBiDi)−(Qi)2(1−pi(m))Di(1+li+ki(ϵ)−T)log(1+li+ki(ϵ)−T1+li+ki(ϵ)−2T+SiBiDi)+Qi(1−pi(m))]+(CBi+(ΔuCBi−ΔlCBi)4)(Si22BiDi)+(CLi+(ΔuCLi−ΔlCLi)4)(1−Bi)(SiBi). | (18) |
The different costs are imprecise in nature, and due to learning, impreciseness decreases. Thus, it is important to study models under three scenarios: the crisp case, the fuzzy case, and learning in fuzziness. Therefore, in this sub-section, this study develops three different models for a centralized system by assuming no regulatory body controls carbon emissions. These models are as follows:
Model 1. Centralized supply chain model including carbon emission without any carbon control mechanism (crisp case).
Model 2. Centralized supply chain model including carbon emission without any carbon control mechanism (fuzzy case).
Model 3. Centralized supply chain model including carbon emission without any carbon control mechanism (learning in fuzziness).
For the integrated model, the manufacturer and n retailers work as team members and find the optimal values of P, Qi and yi to optimize the total profit of a system in each cycle. The emissions caused during manufacturing, warehousing, deterioration, waste disposal and transportation activities are investigated throughout the supply chain. The total carbon emissions per cycle of the system is
EC=(ξMP2−ηMP+λM)P(T−to)+(EHMP(T−tO)2)/2+EWMP3P(T−to)+∑ni=1ETMiP1P(T−to)+ETAP2P(T−to)+EHRi[(Qi)2(1−pi(m))22Dilog(1+li+ki(ϵ)−T1+li+ki(ϵ)−2T+SiBiDi)+Di4((1+li+ki(ϵ)−2T+SiBiDi)2−(1+li+ki(ϵ)−T)2)+Qi2(1+li+ki(ϵ)−T)((Qi)2(1−pi(m))2Dilog(1+li+ki(ϵ)−T1+li+ki(ϵ)−2T+SiBiDi)2−(1+li+ki(ϵ)−T)2)]+HWRi((Qi)2pi(m)xi)+EHWRi((Qi)2pi(m)xi)+EDRi[Qi−(Qi)2(1−pi(m))Di(1+li+ki(ϵ)−T)log(1+li+ki(ϵ)−T1+li+ki(ϵ)−2T+SiBiDi)−Di(T−SiBiDi)+Qi(1−pi(m))]. | (19) |
The total profit of the system in each cycle is
ZC(P,Qi,yi)=ZM(P,wi)+ZRi(yi,Qi) | (20) |
where ZM(P,wi) and ZRi(yi,Qi) are defined by Eq 6 and Eq 18. Thus, the objective function in Model 1 is defined as
Max(ZC(P,Qi,yi)). | (21) |
Let CM, CW, COM, CSM, CTA, CPA, CTMi, CORi, CSRi, CBi, CLi, HM, HRi, HWRi, HDRi and ϵ be fuzzy and expressed by triangular fuzzy numbers ~CM, ~CW, ~COM, ~CSM, ~CTA, ~CPA, ~CTMi, ~CORi, ~CSRi, ~CBi, ~CLi, ~HM, ~HRi, ~HWRi, ~HDRi and ˜ϵ, respectively.
For the definition of fuzzy numbers, see Appendix 3. The total fuzzy profit of the manufacturer using Eq 6 is
~ZM(P,wi)=∑ni=1wiQi+~CPAP2P(T−to)−[~HMP(T−to)22+~CMP(T−to)+~COM+~CSMP(T−to)+~CWP3P(T−to)+∑ni=1~CTMiP1P(T−to)+~CTAP2P(T−to)]. | (22) |
The total fuzzy profit of the ith retailer using Eq 18 is
~ZRi(yi,Qi)=yiDi−[~CORi+~CSRiQi+wiQi+˜ϵT+~HRi[(Qi)2(1−pi(m))22Dilog(1+li+ki(ϵ)−T1+li+ki(ϵ)−2T+SiBiDi)+Di4((1+li+ki(ϵ)−2T+SiBiDi)2−(1+li+ki(ϵ)−T)2)+Qi2(1+li+ki(ϵ)−T)((Qi)2(1−pi(m))2Dilog(1+li+ki(ϵ)−T1+li+ki(ϵ)−2T+SiBiDi)2−(1+li+ki(ϵ)−T)2)]+HWRi((Qi)2pi(m)xi)−(1+li+ki(ϵ)−T)2+~HWRi((Qi)2pi(m)xi)+~HDRi[Qi−(Qi)2(1−pi(m))Di(1+li+ki(ϵ)−T)log(1+li+ki(ϵ)−T1+li+ki(ϵ)−2T+SiBiDi)−Di(T−SiBiDi)+Qi(1−pi(m))]+~CBi(Si22BiDi)+~CLi(1−Bi)(SiBi)+NCAi]. | (23) |
Now, to defuzzify ~ZM(P,wi) and ~ZRi(yi), the signed distance method is applied. The signed distance of ~ZM(P,wi) to ˜0 is as follows:
d(~ZM(P,wi),˜0)=∑ni=1wiQi+d(~CPA,˜0)P2P(T−to)−[d(~HM,˜0)P(T−to)22+d(~CM,˜0)P(T−to)+d(~COM,˜0)+d(~CSM,˜0)P(T−to)+d(~CW,˜0)P3P(T−to)+∑ni=1d(~CTMi,˜0)P1P(T−to)+d(~CTA,˜0)P2P(T−to)]. | (24) |
The signed distance of ~ZRi(yi) to ˜0 is as follows:
d(~ZRi(yi,Qi),˜0)=yiDi−[d(~CORi,˜0)+d(~CSRi,˜0)Qi+wiQi+d(˜ϵ,˜0)T+d(~HRi,˜0)[(Qi)2(1−pi(m))22Dilog(1+li+ki(ϵ)−T1+li+ki(ϵ)−2T+SiBiDi)+Di4((1+li+ki(ϵ)−2T+SiBiDi)2−(1+li+ki(ϵ)−T)2)+Qi2(1+li+ki(ϵ)−T)((Qi)2(1−pi(m))2Dilog(1+li+ki(ϵ)−T1+li+ki(ϵ)−2T+SiBiDi)2−(1+li+ki(ϵ)−T)2)]+HWRi((Qi)2pi(m)xi)+d(~HWRi,˜0)((Qi)2pi(m)xi)+d(~HDRi,˜0)[Qi−(Qi)2(1−pi(m))Di(1+li+ki(ϵ)−T)log(1+li+ki(ϵ)−T1+li+ki(ϵ)−2T+SiBiDi)−Di(T−SiBiDi)+Qi(1−pi(m))]+d(~CBi,˜0)(Si22BiDi)+d(~CLi,˜0)(1−Bi)(SiBi)+NCAi]. | (25) |
For the defuzzification process, the signed distance method is applied. For this, see Appendix 4. Substituting the above values in Eq 22 and Eq 23, crisp functions for total fuzzy costs of the manufacturer and ith retailer is obtained as follows:
πF(ZM(P,wi))=∑ni=1wiQi+(CPA+(ΔuCPA−ΔlCPA)4)P2P(T−to)−[(HM+(ΔuHM−ΔlHM)4)P(T−to)22+(CM+(ΔuCM−ΔlCM)4)P(T−to)+(COM+(ΔuCOM−ΔlCOM)4)+(CSM+(ΔuCSM−ΔlCSM)4)P(T−to)+(CW+(ΔuCW−ΔlCW)4)P3P(T−to)+∑ni=1(CTMi+(ΔuCTMi−ΔlCTMi)4)P1P(T−to)+(CTA+(ΔuCTA−ΔlCTA)4)P2P(T−to)]. | (26) |
πF(ZRi(yi,Qi))=yiDi−[(CORi+(ΔuCORi−ΔlCORi)4+wiQi)+(CSRi+(ΔuCSRi−ΔlCSRi)4)Qi+(ϵ+(Δuϵ−Δlϵ)4)T+(HRi+(ΔuHRi−ΔlHRi)4)[(Qi)2(1−pi(m))22Dilog(1+li+ki(ϵ)−T1+li+ki(ϵ)−2T+SiBiDi)+Di4((1+li+ki(ϵ)−2T+SiBiDi)2−(1+li+ki(ϵ)−T)2)+Qi2(1+li+ki(ϵ)−T)((Qi)2(1−pi(m))2Dilog(1+li+ki(ϵ)−T1+li+ki(ϵ)−2T+SiBiDi)2−(1+li+ki(ϵ)−T)2)]+HWRi((Qi)2pi(m)xi)+(CBi+(ΔuCBi−ΔlCBi)4)(Si22BiDi)+(CLi+(ΔuCLi−ΔlCLi)4)(1−Bi)(SiBi)]. | (27) |
The total fuzzy profit of the centralized system in each cycle is
πF(ZC(P,Qi,yi))=πF(ZM(P,wi))+πF(ZRi(yi,Qi)) | (28) |
where πF(ZM(P,wi)) and πF(ZRi(yi,Qi)) are defined by Eq 26 and Eq 27. Thus, the objective function of Model 2 is defined as
MaxπF(ZC(P,Qi,yi)). | (29) |
The decision maker's learning in estimating the fuzziness values has been used in this sub-section. It is provided that the build-up of knowledge occurs with the number of shipments. It is assumed that decision-makers learn with time and use their expertise to reduce the fuzziness of the parameters while giving a fuzziness value for the parameters. The learning curve follows Wright's [67] power learning curve. If learning affects the fuzzy parameters and if their value changes according to the number of shipments, then for k= CM, CW, COM, CSM, CTA, CPA, CTMi, CORi, CSRi, CBi, CLi, HM, HRi, HWRi, HDRi and ϵ, the values of the mth upper and lower fuzziness parameters at the time of the mth shipment will be
Δuk,m={Δuk,mm=1Δuk,1(m)−αm>1 | (30) |
Δlk,m={Δlk,mm=1Δlk,1(m)−αm>1. | (31) |
The total fuzzy profit functions using Eq 6 and Eq 18 with learning for the kth shipment (k≥1) of the manufacturer and the ith retailer are given as
πL(ZM(P,wi))=∑ni=1wiQi+(CPA+(ΔuCPA,1(m)−α−ΔlCPA,1(m)−α)4)P2P(T−to)−[(HM+(ΔuHM,1(m)−α−ΔlHM,1(m)−α)4)P(T−to)22+(CM+(ΔuCM,1(m)−α−ΔlCM,1(m)−α)4)P(T−to)+(COM+(ΔuCOM,1(m)−α−ΔlCOM,1(m)−α)4)+(CSM+(ΔuCSM,1(m)−α−ΔlCSM,1(m)−α)4)P(T−to)+(CW+(ΔuCW,1(m)−α−ΔlCW,1(m)−α)4)P3P(T−to)+∑ni=1(CTMi+(ΔuCTMi,1(m)−α−ΔlCTMi,1(m)−α)4)P1P(T−to)+(CTA+(ΔuCTA,1(m)−α−ΔlCTA,1(m)−α)4)P2P(T−to)]. | (32) |
πL(ZRi(yi,Qi))=yiDi−[(CORi+(ΔuCORi,1(m)−α−ΔlCORi,1(m)−α)4)+(CSRi+(ΔuCSRi,1(m)−α−ΔlCSRi(m)−α,1)4)Qi+wiQi+(ϵ+(Δuϵ,1(m)−α−Δlϵ,1(m)−α)4)T+(HRi+(ΔuHRi,1(m)−α−ΔlHRi,1(m)−α)4)[(Qi)2(1−pi(m))22Dilog(1+li+ki(ϵ)−T1+li+ki(ϵ)−2T+SiBiDi)+Di4((1+li+ki(ϵ)−2T+SiBiDi)2−(1+li+ki(ϵ)−T)2)+Qi2(1+li+ki(ϵ)−T)((Qi)2(1−pi(m))2Dilog(1+li+ki(ϵ)−T1+li+ki(ϵ)−2T+SiBiDi)2−(1+li+ki(ϵ)−T)2)]+HWRi((Qi)2pi(m)xi)+(HWRi+(ΔuHWRi,1(m)−α−ΔlHWRi,1(m)−α)4)((Qi)2pi(m)xi)+(HDRi+(ΔuHDRi,1(m)−α−ΔlHDRi,1(m)−α)4)[Qi−(Qi)2(1−pi(m))Di(1+li+ki(ϵ)−T)log(1+li+ki(ϵ)−T1+li+ki(ϵ)−2T+SiBiDi)−Di(T−SiBiDi)+Qi(1−pi(m))]+NCAi+(CBi+(ΔuCBi,1(m)−α−ΔlCBi,1(m)−α)4)(Si22BiDi)+(CLi+(ΔuCLi,1(m)−α−ΔlCLi,1(m)−α)4)(1−Bi)(SiBi)]. | (33) |
The total fuzzy profit of the centralized system in each cycle is
πL(ZC(P,Qi,yi))=πL(ZM(P,wi))+πL(ZRi(yi,Qi)) | (34) |
where πL(ZM(P,wi)) and πL(ZRi(yi,Qi)) are defined by Eq 32 and Eq 33. Thus, the objective function of Model 2 is defined as
MaxπL(ZC(P,Qi,yi)) | (35) |
where total emissions per cycle of the system are given by the Eq 19.
This section extends Model 3 by adopting the policies given by the regulatory authority to reduce the carbon footprint in the system. These three models are as follows:
Model 4. Centralized supply chain model with carbon tax policy under the effect of learning in fuzziness
Model 5. Centralized supply chain model with carbon cap policy under the effect of learning in fuzziness
Model 6. Centralized supply chain model with carbon cap and trade policy under the effect of learning in fuzziness
According to this policy, the supply chain manager (company) has to pay a tax on the quantity of carbon emitted in various processes. Suppose ϑ is the per unit carbon tax. Then, the optimization model is represented as
Max[πL(ZC(P,Qi,yi))−ϑEC] | (36) |
where πL(ZC(P,Qi,yi)) and EC are defined by Eq 35 and Eq 19.
According to this regulation, the supply chain manager (company) has an essential restriction, i.e., cap, on the quantity of carbon emitted by them. Suppose Ccap is the carbon cap. Thus, the optimization model can be written as
Max[πL(ZC(P,Qi,yi))]subjecttoEC≤Ccap | (37) |
where πL(ZC(P,Qi,yi)) and EC are defined by Eq 37 and Eq 19.
This policy provides the supply chain manager (company) with an option to purchase an emission limit. According to this policy, a fixed carbon emission limit is provided to the company. Extra emission limits can be purchased (if needed). Suppose ∈1 and ∈2 are the purchasing and selling prices per unit carbon emissions. Then, the optimization model can be written as
Max[πL(ZC(P,Qi,yi))−∈1(EC−Ccap)++∈2(Ccap−EC)+] | (38) |
where πL(ZC(P,Qi,yi)) and EC are defined by Eq 37 and Eq 19.
With appropriate modifications, the following data from Sarkar et al. [22] and Kundu and Chakrabarti [25], with appropriate modifications, is used to demonstrate the performance of the proposed models developed in the previous section with the help of MATHEMATICA software. The optimal results of the proposed models taking i = 2 (the number of retailers is 2) under crisp, fuzzy, and fuzzy-learning situations are presented in Table 2. CM=25($/unit), CW=1.5($/unit), COM=100($/set-up), CSM=0.5($/unit), CTA=0.4($/unit), CPA=150($/unit), CTM1=0.5($/unit), CTM2=0.5($/unit), COR1=150($/set-up), COR2=150($/set-up), CSR1=0.8($/unit), CSR2=0.8($/unit), CB1=3($/unit), CB2=3($/unit), CL1=4($/unit), CL2=4($/unit), HM=2($/unit), HR1=3($/unit), HR2=3($/unit), HWR1=2($/unit), HWR2=2($/unit), HDR1=1.5($/unit), HDR2=1.5($/unit), ϵ=1($/unit), N=1, m=5, P1=0.5, P2=0.3, P3=0.2, T=1 year, to=0.15 year, A=0.02, B=0.03, α=0.0862, S1=80, S2=80, B1=1000, B2=1000, x1=1750, x2=1750, l1=0.8, l2=0.8, u1=4, u2=6, v1=0.5, v2=0.5, a1=20, a2=20, b=0.03, g=999, c=0.862, EHR2=0.0010(ton/unit), EHM=0.0010(ton/unit), EWM=0.005(ton/unit), ETM1=0.0015(ton/unit), ETM2=0.0015(ton/unit), ETA=0.0015(ton/unit), EHR1=0.0010(ton/unit), EDR1=0.0010(ton/unit), EDR2=0.0010(ton/unit), EWHR1=0.008(ton/unit), EWHR2=0.008(ton/unit), ξM=0.000000084, ηM=0.000336, λM=0.190, ρ1=0.5, ρ2=0.5, β1=0.25, β2=0.23, γ1=0.1, γ2=0.1, ϑ=1.2(in /ton), {C}_{cap} = 14 (inton/year), {\in }_{1} = 1.4 ($/unit), {\in }_{2} = 3 ($/unit).Thefuzzyvaluesoftheparametersaresolvedusing \widetilde{C} = \left(C-{\Delta }_{2{\mathrm{i}}-1},C,\;{\mathrm{C}}+{\Delta }_{2{\mathrm{i}}}\right) ,anditisassumedthat {\Delta }_{2{\mathrm{i}}-1} = {\Delta }_{2{\mathrm{i}}-1} = 5{\mathrm{\%}}\;{\mathrm{o}}{\mathrm{f}}\;{\mathrm{C}} $.
Optimal values | P | Q1 | Q2 | y1 | y2 | Total profit ($/year) | Carbon emissions (tons/year) |
Model 1 (crisp) | 147.22 | 1.54 | 1.63 | 76.36 | 76.76 | 13,823.1 | 17.82 |
Model 2 (fuzzy) | 137.72 | 3.15 | 2.98 | 71.77 | 72.60 | 14,131.8 | 17.03 |
Model 3 (learning in fuzziness) | 144.23 | 1.34 | 2.26 | 75.02 | 76.34 | 13,828.5 | 17.59 |
The optimal results of the proposed models under crisp, fuzzy, and fuzzy learning situations are presented in Table 2. It is analyzed that
1) The overall profit increases by 2.23% and 0.39% in the fuzzy and fuzzy learning models. The profit increment is higher in the fuzzy case than the fuzzy learning one.
2) The optimal production rate decreases in the fuzzy and fuzzy-learning models by 6.45% and 2.03%, respectively, i.e., more in the fuzzy model.
3) The optimal order quantities increase by 104.54% and 82.82% for both retailers in the fuzzy model, which shows an increase in market demand for the product.
4) Selling prices of both retailers decrease by 6.26% and 6.01% in the fuzzy model and by 1.75% and 0.55% in the fuzzy-learning model, i.e., more in the fuzzy case. This motivates the customer to buy more.
5) Carbon emissions are decreased by 4.41% and 1.35% in the fuzzy and fuzzy learning models.
Results reveal that the models with fuzziness and learning in fuzziness both increase the system's profit without increasing the production rate. The fuzzy model generates more profit and less emissions than the fuzzy-learning model, whereas market uncertainty can be best handled through the fuzzy-learning model. It is observed that results obtained in the learning in fuzziness model are closer to crisp models, which shows the significance of learning in fuzziness over fuzziness and proves that learning in fuzziness is an appropriate tool to reduce cloudiness. Hence, the learning in fuzziness Model 3 is recommended as an optimal strategy for decision-makers.
From the results of Table 3, the following are observed on applying carbon regulation policies in Model 3:
Variables | P | Q1 | Q2 | y1 | y2 | Total profit ($/year) | Carbon emissions (tons/year) |
Model (3) | 144.23 | 1.34 | 2.26 | 75.02 | 76.34 | 13,828.5 | 17.59 |
Model (4) | 114.45 | 2.92 | 2.81 | 65.05 | 68.43 | 13,768.8 | 14.9 |
Model (5) | 105.35 | 3.93 | 3.62 | 89.42 | 91.95 | 11,996.2 | 14.0 |
Model (6) | 114.44 | 2.92 | 2.80 | 65.04 | 68.42 | 13,785.6 | 14.9 |
1) The optimal production rate decreases by 20.65%, 26.96%, and 20.65%, corresponding to all three policies, but for the carbon cap policy (Model 5), it decreases the most.
2) The optimal order quantity for retailer 1 increases by 117.91%, 193.28%, and 117.91%, and for retailer 2, it increases by 24.34%, 60.18%, and 23.89%, respective to all three policies applied, with the maximum with the carbon cap policy (Model 5).
3) Selling prices increase in the carbon cap policy (Model 5) for retailer 1 by 19.19% and for retailer 2 by 20.45%.
4) The total profit of the system decreases due to carbon emission cost for all three policies by 0.32%, 0.13%, and 0.31%, respectively.
5) Carbon emissions are reduced in all the policies by 15.24%, 20.36% and 15.24%.
6) Comparing all policies discussed, the carbon cap policy (Model 5) shows a maximum drop in carbon emission and production rate, but the total profit of the system corresponding to this policy is minimal in comparison with others.
7) The carbon cap and trade policy (Model 6) shows effective drops in production rate and in carbon footprints along with little decrements in the total profit of the system.
8) The selection of a strategy for controlling carbon footprints should be customized to the requirements of the supply network in order to make a perfect balance between the needs of a successful SSC and carbon control goals for a cleaner production system.
9) It is concluded that among all the three policies, the carbon cap-and-trade policy in Model 6 is best for environmental and economic sustainability. As it reduces emissions, the rate of production, and competitive prices efficiently and enhances the profitability of the system.
In this section, optimal results obtained for Model 3, Model 4, Model 5, and Model 6 are examined concerning all essential parameters of the system.
For sensitivity analysis, important parameters of Model 3 are increased or decreased by 20%, and the results are presented in Table 4. Based on Table 4, the following conclusions are drawn:
Parameters | Change | Total profit | P | Q1 | Q2 | y1 | y2 |
to | fall | rise | rise | _ | _ | _ | _ |
COM | rise | fall | _ | _ | _ | rise | rise |
T | fall | rise | rise | _ | _ | _ | _ |
CM | rise | rise | rise | _ | _ | fall | fall |
CSM | rise | fall | fall | fall | rise | rise | rise |
CW | rise | fall | rise | rise | rise | rise | rise |
HM | fall | rise | rise | _ | _ | fall | fall |
CTMi | fall | rise | rise | rise | fall | fall | fall |
CORi | rise | rise | None | fall | rise | fall | fall |
HRi | rise | fall | fall | None | None | rise | rise |
HDRi | rise | fall | fall | _ | _ | rise | rise |
HWRi | rise | fall | None | rise | rise | fall | fall |
CSR1 | fall | rise | rise | None | None | None | None |
CBi | rise | fall | fall | fall | rise | rise | rise |
CLi | rise | fall | None | fall | None | None | None |
ϵ | rise | fall | fall | None | rise | None | None |
li | rise | rise | fall | None | rise | fall | rise |
ai | rise | None | None | _ | _ | None | None |
ᵞ | rise | rise | rise | _ | _ | rise | rise |
β | rise | rise | rise | _ | _ | rise | rise |
1) On increasing traditional cost parameters (setup cost, holding cost, deterioration cost) of the manufacturer and retailers, total profit and production rate decrease, but competitive prices increase.
2) On increasing the selling price of the product by the manufacturer in an alternate market, total profit and production rate increase, but competitive prices decrease.
3) On increasing the maximum lifetime of the product, the total profit increases, and the production rate decreases. Meanwhile, total profit and production rate drop on increasing preservation technology cost.
4) Since this is the base model for other models defined, these parameters behave the same in all models.
Table 5 shows variations in the total profit of the coordinated supply chain under the competitive prices of two retailers. If the selling price of one retailer decreases from $77/unit to $74/unit while keeping the other retailer's selling price fixed, the total profit increases. If the selling prices of both retailers decrease together, the total profit again increases. This implies that the manufacturer could convince retailers to reduce their competitive prices to gain profit and increase market demand for a green product. In this way, the competitive advantage of the supply chain could be sustained.
Competitive prices | y1=74 | y1=75 | y1=76 | y1=77 |
y2=74 | 13,834.5 | 13,830.7 | 13,826.3 | 13,821.5 |
y2=75 | 13,833.9 | 13,830.2 | 13,826.1 | 13,821.5 |
y2=76 | 13,832.8 | 13,829.3 | 13,825.4 | 13,821.0 |
y2=77 | 13,831.2 | 13,828.0 | 13,824.3 | 13,820.1 |
Table 6 shows changes in optimal profit when learning rate changes from 0.862 to 0.074 and for different numbers of shipments from m = 25 to m = 100. On increasing the rate of learning, the profitability of the company also increases. Figure 6 shows the improvement due to learning. On the other hand, the optimal profit decreases with an increase in the frequency of shipments (with a fixed learning rate). However, whenever shipments increase, the learning rate usually increases (resulting in increasing total profit). In this way, learning in fuzziness removes the illusion of optimal profit and helps the decision-maker to make an appropriate decision.
α | m=25 | m=50 | m=75 | m=100 |
0.862 | 13,842.0 | 13,833.3 | 13,830.1 | 13,828.5 |
0.737 | 13,851.5 | 13,840.0 | 13,835.5 | 13,833.0 |
0.621 | 13,864.6 | 13,849.9 | 13,843.9 | 13,840.4 |
0.515 | 13,881.7 | 13,856.2 | 13,864.0 | 13,851.7 |
0.415 | 13,904.1 | 13,883.8 | 13,874.3 | 13,868.5 |
0.322 | 13,932.6 | 13,910.6 | 13,899.8 | 13,893.0 |
0.234 | 13,968.6 | 13,946.7 | 13,935.5 | 13,928.1 |
0.152 | 14,012.6 | 13,993.7 | 13,993.3 | 13,976.5 |
0.074 | 1466.9 | 14,054.7 | 14,047.8 | 14,043.1 |
From the results of Table 7, it is interesting that on increasing carbon tax from $1.2/ton to $1.9/ton in Model 4, carbon emissions are reduced from 14.90 tons/year to 14.74 tons/year, and the total profit is reduced due to the carbon tax. Changes in the total profit with carbon tax can be studied in Figure 7.
Carbon tax ($/ton) | P | Q1 | Q2 | y1 | y2 | Total profit ($/year) | Carbon emissions (tons/year) |
1.2 | 114.447 | 2.9248 | 2.8056 | 65.0461 | 68.428 | 13,768.8 | 14.900 |
1.3 | 114.345 | 2.9249 | 2.8056 | 65.0459 | 68.428 | 13,767.1 | 14.892 |
1.6 | 113.979 | 2.9878 | 2.7934 | 65.0425 | 68.388 | 13,762.9 | 14.856 |
1.9 | 112.794 | 3.0745 | 2.7895 | 65.0423 | 69.036 | 13,753.4 | 14.739 |
A carbon cap is a critical parameter in this model. Increasing the carbon cap, the total profit of the system changes, while other variables are almost insensitive to changes in the carbon cap. Figure 8 shows a change in total profit with a change in carbon cap.
The above Table 8 shows higher price decreases the total profits.
∈1 | P | Q1 | Q2 | y1 | y2 | Total profit ($/year) |
1.4 | 114.44 | 2.92 | 2.80 | 65.04 | 68.42 | 13,785.6 |
5.0 | 114.44 | 2.92 | 2.80 | 65.04 | 68.42 | 13,782.2 |
7.0 | 114.44 | 2.92 | 2.80 | 65.04 | 68.42 | 13,780.4 |
9.0 | 114.44 | 2.92 | 2.80 | 65.04 | 68.42 | 13,778.6 |
This paper suggests some insights for supply chain and production managers of industries.
• For maintaining sustainability, the production manager should first focus on decisions related to production rate. The controllable production rate applied in this study is a very effective strategy for producing a green and innovative product. It not only reduces the cost due to overproduction or underproduction but also lowers industrial waste and extra energy consumption.
• Three different strategies, (ⅰ) a strong (two-level) inspection with human learning to reduce inspection error, (ⅱ) an alternate market for selling defective products, and (ⅲ) a waste management setup to dispose of overall waste, help the decision maker of the production system, where the production process is not perfect, to reduce waste. Hence, the policy for smart production considered in this paper would optimize the sustainability goals of production managers.
• The results of the current study give the direction to the supply chain managers that they should motivate their members to set their prices competitively, work with team spirit, and enhance customer awareness towards green purchases through promotional activities.
• For the sustainability of the supply chain, the results of this paper suggest that managers should continuously monitor emissions generated at each stage of the supply chain and apply emission-reducing policies to minimize them. The optimal solutions under different schemes show that each reduces emissions, but carbon cap and trade policy is optimal for environmental and economic sustainability. Therefore, the carbon cap and trade policy with learning in fuzziness should be the most favorable policy for decision-makers to gain profit and minimize carbon footprints.
• The sensitivity analysis of different inventory parameters advises inventory planners to take appropriate values of the highly sensitive inventory parameters like learning rates, maximum lifetime of product, and preservation technology cost to enhance the gain of this centralized system, along with respective parameters of carbon control policy adopted for overall sustainability.
Carbon regulation policies and learning in fuzziness were the two practical tools to handle the present competitive market situations. In this study, a two-echelon competitive supply network was presented in the shape of a (single manufacturer and multiple retailers) flexible production model for deteriorating products under learning in fuzziness. A manufacturer produced green products, which undergo two-stage screening before dispatching in the market. The deterioration rate was presumed to depend on the maximum lifetime and preservation technology costs. Retailers promoted the product to increase its market demand. The model for a coordinated supply network was investigated under three scenarios: crisp, fuzzy, and fuzzy-learning. Further, the model was extended by implementing different carbon regulation policies. The main findings of this study are summarized as follows:
• Fuzziness and learning in fuzziness enhanced the total profit by 2.23% and 0.04%, along with decreasing the system's carbon footprint by 4.41% and 1.35%, respectively. Results confirmed that human learning affects maintaining the SSC management for the smart product subject to the reduction of carbon footprints.
• Retailer awareness programs and competitive demand attracted customers to buy more. Thus, industrial managers should motivate their supply team members correspondingly.
• The production process, transportation, and deterioration were the main contributors to carbon footprints in the system. The applications of three carbon control policies, carbon tax, carbon cap, and carbon cap and trade, showed (ⅰ) decreases in total profit by 0.32%, 0.13%, and 0.31%; (ⅱ) drops in carbon footprints by 15.24%, 20.36%, and 15.24%; and (ⅲ) increases in an order quantity of retailer 1 by 117.91%, 193.28%, and 117.91% and of retailer 2 by 24.34%, 60.18% and 23.89%, respectively.
• The results suggested optimal planning of the SSC under learning in fuzziness along with controlling carbon footprints through cap-and-trade policy.
• Although implementing a carbon regulation policy reduced emissions, it increased the financial liabilities of firms. Further, the execution of human learning did not require much investment from industries. Instead, it effectively reduced carbon emissions, market ambiguity, and defective products. Hence, learning in fuzziness and human learning were both important tools to maintain sustainability.
• The present study could be helpful for inventory managers in decision-making to gain profit, reduce waste by human learning, and decrease vagueness through the fuzzy-learning effect, along with efficient carbon management. In this way, it served all three expectations, i.e., economic, social, and environmental, for an SSC and led the research to move toward a cleaner and safer planet.
• The past research in this field had not touched these critical areas together. This study narrowed this gap.
This study has significant applicability to give a new direction to research, and its numerical results are appealing. Still, the effects of competitive prices and advertisement-based demand could be better demonstrated if they were studied in centralized and decentralized scenarios, both using a game-theoretical approach. Therefore, in future research, this study can be considered accordingly.
Further, it can be extended into a closed-loop structure under reverse logistics. The following study can be done with random production, rework, different demand patterns, and shortages. Moreover, another attractive extension can be done by adding different profit-sharing contracts and government schemes to motivate eco-friendly production [68].
The authors declare they have not used Artificial Intelligence (AI) tools in the creation of this article.
The authors declare no conflict of interest.
[1] | https://www.foodbusinessnews.net/articles/13133-sustainable-product-market-could-hit-150-billion-in-us-by-2021. |
[2] | https://ecowarriorprincess.net/2018/04/carbon-intensive-industries-industry-sectors-emit-the-most-carbon |
[3] |
Olatunji OO, Ayo OO, Akinlabi S, et al.Competitive advantage of carbon efficient supply chain in manufacturing industry. J Clean Prod, 2019,238: 117937. https://doi.org/10.1016/j.jclepro.2019.117937 doi: 10.1016/j.jclepro.2019.117937
![]() |
[4] |
Parsaeifar S, Bozorgi-Amiri A, Naimi-Sadigh A, et al.A game theoretical for coordination of pricing, recycling, and green product decisions in the supply chain. J Clean Prod, 2019,226:37–49. https://doi.org/10.1016/j.jclepro.2019.03.343 doi: 10.1016/j.jclepro.2019.03.343
![]() |
[5] |
Ullah M, Asghar I, Zahid M, et al.Ramification of remanufacturing in a sustainable three-echelon closed-loop supply chain management for returnable products. J Clean Prod, 2021,290: 125609. https://doi.org/10.1016/j.jclepro.2020.125609 doi: 10.1016/j.jclepro.2020.125609
![]() |
[6] |
Xiao D, Wang J, Lu Q. Stimulating sustainability investment level of suppliers with strategic commitment to price and cost sharing in supply chain. J Clean Prod, 2020,252: 119732. https://doi.org/10.1016/j.jclepro.2019.119732 doi: 10.1016/j.jclepro.2019.119732
![]() |
[7] | Indian Emission Booklet 2018. https://www.araiindia.com/pdf/Indian_Emission_Regulation_Booklet.pdf |
[8] | Singh A, Raman N, Waghe U. Ecomark Scheme IN India. Int J Pharma Med Biol Sci, 2012, 1(2): 109-122. |
[9] |
Bai Q, Jin M, Xu X. Effects of carbon emission reduction on supply chain coordination withvendor-managed deteriorating product inventory. Int J Prod Econ, 2019,208: 83–99. https://doi.org/10.1016/j.ijpe.2018.11.008 doi: 10.1016/j.ijpe.2018.11.008
![]() |
[10] |
Li J, Wang L, Tan X. Sustainable design and optimization of coal supply chain network under different carbon emission policies. J Clean Prod, 2020,250: 119548. https://doi.org/10.1016/j.jclepro.2019.119548 doi: 10.1016/j.jclepro.2019.119548
![]() |
[11] |
Sarkar B, Guchhait R. Ramification of information asymmetry on a green supply chain management with the cap-trade, service, and vendor-managed inventory strategies. Elect Comm Res App, 2023, 60: 101274. https://doi.org/10.1016/j.elerap.2023.101274 doi: 10.1016/j.elerap.2023.101274
![]() |
[12] |
Gautam P, Kishore A, Khanna A. et al.Strategic defect management for a sustainable green supply chain. J Clean Prod, 2019,233: 226-241. https://doi.org/10.1016/j.jclepro.2019.06.005 doi: 10.1016/j.jclepro.2019.06.005
![]() |
[13] |
Ullah M. Sarkar B. Recovery-channel selection in a hybrid manufacturing-remanufacturing production model with RFID and product quality. Int J Prod Econ, 2020,219: 360–374. https://doi.org/10.1016/j.ijpe.2019.07.017 doi: 10.1016/j.ijpe.2019.07.017
![]() |
[14] |
Wee H, Chung C. Optimising replenishment policy for an integrated production inventory deteriorating model considering green component-value design and remanufacturing. Int J Prod Res, 2009, 47: 1343–1368. https://doi.org/10.1080/00207540701570182 doi: 10.1080/00207540701570182
![]() |
[15] |
Hovelaque V, Bironneau L. The carbon-constrained EOQ model with carbon emission dependent demand. Int J Prod Econ, 2015,164: 285–291. https://doi.org/10.1016/j.ijpe.2014.11.022 doi: 10.1016/j.ijpe.2014.11.022
![]() |
[16] |
Wu T, Kung C. Carbon emissions, technology upgradation and financing risk of the green supply chain competition. Technol For Forecast Soc, 2020,152: 119884. https://doi.org/10.1016/j.techfore.2019.119884 doi: 10.1016/j.techfore.2019.119884
![]() |
[17] |
Bonney M, Jaber M. Environmentally responsible inventory models: Non-classical models for a non-classical era. Int J Prod Econ, 2011,133: 43–53. https://doi.org/10.1016/j.ijpe.2009.10.033 doi: 10.1016/j.ijpe.2009.10.033
![]() |
[18] |
Tayyab M, Jemai J, Lim H, et al.A sustainable development framework for a cleaner multi-item multi-stage textile production system with a process improvement initiative. J Clean Prod, 2020,246: 119055. https://doi.org/10.1016/j.jclepro.2019.119055 doi: 10.1016/j.jclepro.2019.119055
![]() |
[19] | https://ourworldindata.org/grapher/annual-co-emissions-by-region |
[20] |
Mukhopadhyay A, Goswami A. Economic production quantity (EPQ) model for three type imperfect items with rework and learning in setup. An International. J Opt Control Theor Appl, 2014, 4: 57–65. https://doi.org/10.11121/ijocta.01.2014.00170 doi: 10.11121/ijocta.01.2014.00170
![]() |
[21] |
Dye C, Yang C. Sustainable trade credit and replenishment decisions with credit-linked demand under carbon emission constraints. Eur J Oper Res, 2015,244: 187–200. https://doi.org/10.1016/j.ejor.2015.01.026 doi: 10.1016/j.ejor.2015.01.026
![]() |
[22] |
Sarkar B, Sarkar M, Ganguly B, et al.Combined effects of carbon emission and production quality improvement for fixed lifetime products in a sustainable supply chain management. Int J Prod Econ, 2021,231: 107867. https://doi.org/10.1016/j.ijpe.2020.107867 doi: 10.1016/j.ijpe.2020.107867
![]() |
[23] |
Mishra U. Wu Z. Sarkar B. Optimum sustainable inventory management with backorder and deterioration under controllable carbon emissions. J Clean Prod, 2021,279: 123699. https://doi.org/10.1016/j.jclepro.2020.123699 doi: 10.1016/j.jclepro.2020.123699
![]() |
[24] |
Tiwari S, Daryanto Y, Wee H. Sustainable inventory management with deteriorating and imperfect quality items considering carbon emission. J Clean Prod, 2018,192: 281–292. https://doi.org/10.1016/j.jclepro.2018.04.261 doi: 10.1016/j.jclepro.2018.04.261
![]() |
[25] |
Kundu S, Chakrabarti T. Impact of carbon emission policies on manufacturing, remanufacturing and collection of used item decisions with price dependent return rate. Opsearch, 2018, 55: 532–555. https://doi.org/10.1007/s12597-018-0336-y doi: 10.1007/s12597-018-0336-y
![]() |
[26] |
Jamali M, Rasti-Barzoki M. A game theoretic approach for green and non-green product pricing in chain-to-chain competitive sustainable and regular dual-channel supply chains. J Clean Prod 170: 1029–1043. https://doi.org/10.1016/j.jclepro.2017.09, 2018181 doi: 10.1016/j.jclepro.2017.09.181
![]() |
[27] |
Garai A, Sarkar B. Economically independent reverse logistics of customer-centric closed-loop supply chain for herbal medicines and biofuel. J Clean Prod, 2022,334: 129977. https://doi.org/10.1016/j.jclepro.2021.129977 doi: 10.1016/j.jclepro.2021.129977
![]() |
[28] |
Hosseini-Motlagh S, Ebrahimi S, Zirakpourdehkordi R. Coordination of dual-function acquisition price and corporate social responsibility in a sustainable closed-loop supply chain. J Clean Prod, 2020,251: 119629. https://doi.org/10.1016/j.jclepro.2019.119629 doi: 10.1016/j.jclepro.2019.119629
![]() |
[29] |
Yadav D, Kumari R, Kumar N, et al.Reduction of waste and carbon emission through the selection of items with cross-price elasticity of demand to form a sustainable supply chain with preservation technology. J Clean Prod, 2021,297: 126298. https://doi.org/10.1016/j.jclepro.2021.126298 doi: 10.1016/j.jclepro.2021.126298
![]() |
[30] |
Sarkar B, Tayyab M, Kim N, et al.Optimal production delivery policies for supplier and manufacturer in a constrained closed-loop supply chain for returnable transport packaging through metaheuristic approach. Comp Indust Eng, 2020,135: 987-1003. https://doi.org/10.1016/j.cie.2019.05.035 doi: 10.1016/j.cie.2019.05.035
![]() |
[31] |
Huang Y, Fang C, Lin Y. Inventory management in supply chains with consideration of logistics, green investment and different carbon emissions policies. Compt Indust Eng, 2020,139: 106207. https://doi.org/10.1016/j.cie.2019.106207 doi: 10.1016/j.cie.2019.106207
![]() |
[32] |
Manupati V, Jedidah S, Gupta S, et al.Optimization of a multiechelon sustainable production-distribution supply chain system with lead time consideration under carbon emission policies. Comput Ind Eng, 2019,135: 1312–1323. https://doi.org/10.1016/j.cie.2018.10.010 doi: 10.1016/j.cie.2018.10.010
![]() |
[33] |
Mishra U, Mashud A, Tseng M, et al.Optimizing a sustainable supply chain inventory model for controllable deterioration and emission rates in a greenhouse farm. Mathematics, 2021, 9: 495. https://doi.org/10.3390/math9050495 doi: 10.3390/math9050495
![]() |
[34] |
Sarkar B, Bhuniya S. A sustainable flexible manufacturing–remanufacturing model with improved service and green investment under variable demand. Exp Syst App 202, 117154. https://doi.org/10.1016/j.eswa.2022, 2022117154 doi: 10.1016/j.eswa.2022.117154
![]() |
[35] |
Alamri O, Jayaswal M, Khan F, et al.An EOQ model with carbon emissions and inflation for deteriorating imperfect quality items under learning effect. Sustainability, 2022, 14: 1365. https://doi.org/10.3390/su14031365 doi: 10.3390/su14031365
![]() |
[36] |
Wang S, Wang X, Chen S. Global value chains and carbon emission reduction in developing countries: does industrial upgrading matter? Environ Impact Assess, 2022, 97: 106895. https://doi.org/10.1016/j.eiar.2022.106895 doi: 10.1016/j.eiar.2022.106895
![]() |
[37] |
Sun H, Zhong Y. Carbon emission reduction and green marketing decisions in a two-echelon low-carbon supply chain considering fairness concern. J Bus Ind Mark, 2023, 38: 905–29. https://doi.org/10.1108/JBIM-02-2021-0090 doi: 10.1108/JBIM-02-2021-0090
![]() |
[38] |
Kang K, Tan BQ. Carbon emission reduction investment in sustainable supply chains under cap-and-trade regulation: An evolutionary game-theoretical perspective. Expert Syst Appl, 2023,227: 120335. ttps://doi.org/10.1016/j.eswa.2023.120335 doi: 10.1016/j.eswa.2023.120335
![]() |
[39] |
Sarkar B, Ullah M, Sarkar M. Environmental and economic sustainability through innovative green products by remanufacturing. J Clean Prod, 2022,332: 129813. https://doi.org/10.1016/j.jclepro.2021.129813 doi: 10.1016/j.jclepro.2021.129813
![]() |
[40] |
Glock C. Batch sizing with controllable production rates. Int J Prod Res, 2010, 48: 5925–5942. https://doi.org/10.1080/00207540903170906 doi: 10.1080/00207540903170906
![]() |
[41] |
Glock C. Batch sizing with controllable production rates in a multi-stage production system. Int J Prod Res, 2011, 49: 6017–6039. https://doi.org/10.1080/00207543.2010.528058 doi: 10.1080/00207543.2010.528058
![]() |
[42] |
Singhal S, Singh S. Volume flexible multi-items inventory system with imprecise environment. Int J Ind Eng Comp, 2013, 4: 457–468. https://doi.org/10.5267/j.ijiec.2013.07.002 doi: 10.5267/j.ijiec.2013.07.002
![]() |
[43] |
Singhal S, Singh S. Modeling of an inventory system with multi variate demand under volume flexibility and learning. Uncertain Supply Chain Manag, 2015, 3: 147–158. https://doi.org/10.5267/j.uscm.2014.12.006 doi: 10.5267/j.uscm.2014.12.006
![]() |
[44] |
Tayal S, Singh S, Sharma R. An integrated production inventory model for perishable products with trade credit period and investment in preservation technology. Int J Mathematics Oper Res, 2016, 8: 137–163. https://doi.org/10.1504/IJMOR.2016.074852 doi: 10.1504/IJMOR.2016.074852
![]() |
[45] |
Manna A, Dey J, Mondal S. Imperfect production inventory model with production rate dependent defective rate and advertisement dependent demand. Comput Ind Eng, 2017,104: 9–22. https://doi.org/10.1016/j.cie.2016.11.027 doi: 10.1016/j.cie.2016.11.027
![]() |
[46] |
Sarkar M, Chung B. Flexible work-in-process production system in supply chain management under quality improvement. Int J Prod Res, 2020, 58: 3821–3838. https://doi.org/10.1080/00207543.2019.1634851 doi: 10.1080/00207543.2019.1634851
![]() |
[47] |
Dey B, Pareek S, Tayyab M, et al.Autonomation policy to control work-in-process inventory in a smart production system. Int J Prod Res, 2021, 59: 1258–1280. https://doi.org/10.1080/00207543.2020.1722325 doi: 10.1080/00207543.2020.1722325
![]() |
[48] |
Sarkar M, Sarkar B. How does an industry reduce waste and consumed energy within a multi-stage smart sustainable biofuel production system? J Clean Prod, 2020,262: 121200. https://doi.org/10.1016/j.jclepro.2020.121200 doi: 10.1016/j.jclepro.2020.121200
![]() |
[49] |
Mridha B, Pareek S, Goswami A, et al.Joint effects of production quality improvement of biofuel and carbon emissions towards a smart sustainable supply chain management. J Clean Prod, 2023,386: 135629. https://doi.org/10.1016/j.jclepro.2022.135629 doi: 10.1016/j.jclepro.2022.135629
![]() |
[50] |
Bera U, Mahapatra N, Maiti M. An imperfect fuzzy production-inventory model over a finite time horizon under the effect of learning. Int J Mathematics Oper Res, 2009, 1: 351–371. https://doi.org/10.1504/IJMOR.2009.024290 doi: 10.1504/IJMOR.2009.024290
![]() |
[51] |
Glock C, Schwindl K, Jaber M. An EOQ model with fuzzy demand and learning in fuzziness. Int J Serv Op Manag, 2012, 12: 90–100. https://doi.org/10.1504/IJSOM.2012.046675 doi: 10.1504/IJSOM.2012.046675
![]() |
[52] |
Pathak S, Kar S, Sarkar S. Fuzzy production inventory model for deteriorating items with shortages under the effect of time dependent learning and forgetting: A possibility/necessity approach. Opsearch, 2013, 50: 149–181. https://doi.org/10.1007/s12597-012-0102-5 doi: 10.1007/s12597-012-0102-5
![]() |
[53] |
Yadav D, Singh S, Kumari R. Inventory model with learning effect and imprecise market demand under screening error. Opsearch, 2013, 50: 418–432. https://doi.org/10.1007/s12597-012-0118-x doi: 10.1007/s12597-012-0118-x
![]() |
[54] | Kumar R, Goswami A. EPQ model with learning consideration, imperfect production and partial backlogging in fuzzy random environment. Int J Syst Sci, 2015, 46: 1486–1497. |
[55] |
Kazemi N, Shekarian E, Cárdenas-Barrón L E, et al.Incorporating human learning into a fuzzy EOQ inventory model with backorders. Comput Indust Eng, 2015, 87: 540–542. https://doi.org/10.1016/j.cie.2015.05.014 doi: 10.1016/j.cie.2015.05.014
![]() |
[56] |
Shekarian E, Olugu E, Abdul-Rashid S, et al.An economic order quantity model considering different holding costs for imperfect quality items subject to fuzziness and learning. J Intell Fuzzy Syst, 2016, 30: 2985–2997. https://doi.org/10.3233/IFS-151907 doi: 10.3233/IFS-151907
![]() |
[57] |
Sarkar B, Omair M, Kim N. A cooperative advertising collaboration policy in supply chain management under uncertain conditions. App Soft Comput, 2020, 88: 105948. https://doi.org/10.1016/j.asoc.2019.105948 doi: 10.1016/j.asoc.2019.105948
![]() |
[58] |
Giri B, Masanta M. Developing a closed-loop supply chain model with price and quality dependent demand and learning in production in a stochastic environment. Int J Syst Sci Oper, 2020, 7: 147–163. https://doi.org/10.1080/23302674.2018.1542042 doi: 10.1080/23302674.2018.1542042
![]() |
[59] |
Saha S, Chakrabarti T. A supply chain model under return policy considering refurbishment, learning effect and inspection error. Croat Oper Res Rev, 2020, 11: 53–66. https://doi.org/10.17535/crorr.2020.0005 doi: 10.17535/crorr.2020.0005
![]() |
[60] |
Dey BK, Bhuniya S, Sarkar B. Involvement of controllable lead time and variable demand for a smart manufacturing system under a supply chain management. Exp Syst App, 2021,184: 115464. https://doi.org/10.1016/j.eswa.2021.115464 doi: 10.1016/j.eswa.2021.115464
![]() |
[61] |
Jayaswal M, Mittal M, Sangal I, et al.Fuzzy-based EOQ model with credit financing and backorders under human learning. Int J Fuzzy Syst Appl, 2021, 10: 14–36. https://doi.org/10.4018/IJFSA.2021100102 doi: 10.4018/IJFSA.2021100102
![]() |
[62] |
Poursoltan L, Mohammad Seyedhosseini S, Jabbarzadeh A. A two-level closed-loop supply chain under the constract of vendor managed inventory with learning: A novel hybrid algorithm. J Ind Prod Eng, 2021, 38: 254–270. https://doi.org/10.1080/21681015.2021.1878301 doi: 10.1080/21681015.2021.1878301
![]() |
[63] |
Alsaedi BS, Alamri OA, Jayaswal MK, et al.A sustainable green supply chain model with carbon emissions for defective items under learning in a fuzzy environment. Mathematics, 2023, 11: 301. https://doi.org/10.3390/math11020301 doi: 10.3390/math11020301
![]() |
[64] |
Habib MS, Asghar O, Hussain A, et al.A robust possibilistic programming approach toward animal fat-based biodiesel supply chain network design under uncertain environment. J Clean Prod, 2021,278: 122403. https://doi.org/10.1016/j.jclepro.2020.122403 doi: 10.1016/j.jclepro.2020.122403
![]() |
[65] |
Lee S, Kim D (2104) An optimal policy for a single-vendor single-buyer integrated production–distribution model with both deteriorating and defective items. Int J Prod Econ 147: 161–170. https://doi.org/10.1016/j.ijpe.2013.09.011 doi: 10.1016/j.ijpe.2013.09.011
![]() |
[66] |
Singh SK, Chauhan A, Sarkar B. Sustainable biodiesel supply chain model based on waste animal fat with subsidy and advertisement. J Clean Prod, 2023,382: 134806. https://doi.org/10.1016/j.jclepro.2022.134806 doi: 10.1016/j.jclepro.2022.134806
![]() |
[67] |
Wright T. Factors affecting the cost of airplanes. J Aeronaut Sci, 1936, 3: 122–128. https://doi.org/10.2514/8.155 doi: 10.2514/8.155
![]() |
[68] |
Saxena N, Sarkar B, Wee HM, et al.A reverse logistic model with eco-design under the Stackelberg-Nash equilibrium and centralized framework. J Clean Prod, 2023,387: 135789. https://doi.org/10.1016/j.jclepro.2022.135789 doi: 10.1016/j.jclepro.2022.135789
![]() |
![]() |
![]() |
Author(s) | Sustainable supply chain | Variable deterioration | Learning in fuzziness | Carbon emissions policies | Variable demand | Imperfect production | Inspection error | Partial backlogging | Scope |
Ullah et al. [5] | Yes | - | - | - | - | - | - | - | Used product collection and remanufacturing |
Bai et al. [9] | - | - | Yes | Yes | - | - | - | - | One distributor, two purchasers |
Sarkar and Guchhait [11] | Yes | - | - | Yes | - | Yes | - | - | Closed-loop logistic system |
Gautam et al. [12] | Yes | - | - | - | - | Yes | - | - | One distributor, one purchaser |
Ullah and Sarkar [13] | Yes | - | - | Yes | Yes | - | - | - | Product quality and radio frequency identification |
Tayyab et al. [18] | - | - | - | Yes | Yes | Yes | Yes | - | Multi-stage textile production system |
Mukhopadhyay and Goswami [20] | - | - | - | Yes | - | Yes | - | - | One manufacturer |
Dye and Yang [21] | Yes | Yes | - | - | Yes | Yes | - | Yes | One manufacturer |
Kundu and Chakrabarti [25] | - | Yes | - | Yes | - | - | - | - | One distributor, one purchaser |
Daryanto et al. [27] | - | Yes | - | - | - | - | - | - | One distributor, one purchaser |
Manna et al. [45] | - | Yes | - | - | Yes | - | - | One manufacture | |
Kumar and Goswami [54] | - | - | Yes | - | - | Yes | - | - | One manufacturer |
Habib et al. [64] | - | - | - | - | - | - | - | - | Possibilistic programming approach |
Lee and Kim [65] | - | Yes | - | - | - | Yes | - | - | One distributor, one purchaser |
Singh et al. [66] | Yes | - | - | Yes | - | Yes | - | - | SSC for waste management |
This paper | Yes | Yes | Yes | Yes | Yes | Yes | Yes | Yes | Single supplier, multiple competitive buyer |
Optimal values | P | Q1 | Q2 | y1 | y2 | Total profit ($/year) | Carbon emissions (tons/year) |
Model 1 (crisp) | 147.22 | 1.54 | 1.63 | 76.36 | 76.76 | 13,823.1 | 17.82 |
Model 2 (fuzzy) | 137.72 | 3.15 | 2.98 | 71.77 | 72.60 | 14,131.8 | 17.03 |
Model 3 (learning in fuzziness) | 144.23 | 1.34 | 2.26 | 75.02 | 76.34 | 13,828.5 | 17.59 |
Variables | P | Q1 | Q2 | y1 | y2 | Total profit ($/year) | Carbon emissions (tons/year) |
Model (3) | 144.23 | 1.34 | 2.26 | 75.02 | 76.34 | 13,828.5 | 17.59 |
Model (4) | 114.45 | 2.92 | 2.81 | 65.05 | 68.43 | 13,768.8 | 14.9 |
Model (5) | 105.35 | 3.93 | 3.62 | 89.42 | 91.95 | 11,996.2 | 14.0 |
Model (6) | 114.44 | 2.92 | 2.80 | 65.04 | 68.42 | 13,785.6 | 14.9 |
Parameters | Change | Total profit | P | Q1 | Q2 | y1 | y2 |
to | fall | rise | rise | _ | _ | _ | _ |
COM | rise | fall | _ | _ | _ | rise | rise |
T | fall | rise | rise | _ | _ | _ | _ |
CM | rise | rise | rise | _ | _ | fall | fall |
CSM | rise | fall | fall | fall | rise | rise | rise |
CW | rise | fall | rise | rise | rise | rise | rise |
HM | fall | rise | rise | _ | _ | fall | fall |
CTMi | fall | rise | rise | rise | fall | fall | fall |
CORi | rise | rise | None | fall | rise | fall | fall |
HRi | rise | fall | fall | None | None | rise | rise |
HDRi | rise | fall | fall | _ | _ | rise | rise |
HWRi | rise | fall | None | rise | rise | fall | fall |
CSR1 | fall | rise | rise | None | None | None | None |
CBi | rise | fall | fall | fall | rise | rise | rise |
CLi | rise | fall | None | fall | None | None | None |
ϵ | rise | fall | fall | None | rise | None | None |
li | rise | rise | fall | None | rise | fall | rise |
ai | rise | None | None | _ | _ | None | None |
ᵞ | rise | rise | rise | _ | _ | rise | rise |
β | rise | rise | rise | _ | _ | rise | rise |
Competitive prices | y1=74 | y1=75 | y1=76 | y1=77 |
y2=74 | 13,834.5 | 13,830.7 | 13,826.3 | 13,821.5 |
y2=75 | 13,833.9 | 13,830.2 | 13,826.1 | 13,821.5 |
y2=76 | 13,832.8 | 13,829.3 | 13,825.4 | 13,821.0 |
y2=77 | 13,831.2 | 13,828.0 | 13,824.3 | 13,820.1 |
α | m=25 | m=50 | m=75 | m=100 |
0.862 | 13,842.0 | 13,833.3 | 13,830.1 | 13,828.5 |
0.737 | 13,851.5 | 13,840.0 | 13,835.5 | 13,833.0 |
0.621 | 13,864.6 | 13,849.9 | 13,843.9 | 13,840.4 |
0.515 | 13,881.7 | 13,856.2 | 13,864.0 | 13,851.7 |
0.415 | 13,904.1 | 13,883.8 | 13,874.3 | 13,868.5 |
0.322 | 13,932.6 | 13,910.6 | 13,899.8 | 13,893.0 |
0.234 | 13,968.6 | 13,946.7 | 13,935.5 | 13,928.1 |
0.152 | 14,012.6 | 13,993.7 | 13,993.3 | 13,976.5 |
0.074 | 1466.9 | 14,054.7 | 14,047.8 | 14,043.1 |
Carbon tax ($/ton) | P | Q1 | Q2 | y1 | y2 | Total profit ($/year) | Carbon emissions (tons/year) |
1.2 | 114.447 | 2.9248 | 2.8056 | 65.0461 | 68.428 | 13,768.8 | 14.900 |
1.3 | 114.345 | 2.9249 | 2.8056 | 65.0459 | 68.428 | 13,767.1 | 14.892 |
1.6 | 113.979 | 2.9878 | 2.7934 | 65.0425 | 68.388 | 13,762.9 | 14.856 |
1.9 | 112.794 | 3.0745 | 2.7895 | 65.0423 | 69.036 | 13,753.4 | 14.739 |
∈1 | P | Q1 | Q2 | y1 | y2 | Total profit ($/year) |
1.4 | 114.44 | 2.92 | 2.80 | 65.04 | 68.42 | 13,785.6 |
5.0 | 114.44 | 2.92 | 2.80 | 65.04 | 68.42 | 13,782.2 |
7.0 | 114.44 | 2.92 | 2.80 | 65.04 | 68.42 | 13,780.4 |
9.0 | 114.44 | 2.92 | 2.80 | 65.04 | 68.42 | 13,778.6 |
Author(s) | Sustainable supply chain | Variable deterioration | Learning in fuzziness | Carbon emissions policies | Variable demand | Imperfect production | Inspection error | Partial backlogging | Scope |
Ullah et al. [5] | Yes | - | - | - | - | - | - | - | Used product collection and remanufacturing |
Bai et al. [9] | - | - | Yes | Yes | - | - | - | - | One distributor, two purchasers |
Sarkar and Guchhait [11] | Yes | - | - | Yes | - | Yes | - | - | Closed-loop logistic system |
Gautam et al. [12] | Yes | - | - | - | - | Yes | - | - | One distributor, one purchaser |
Ullah and Sarkar [13] | Yes | - | - | Yes | Yes | - | - | - | Product quality and radio frequency identification |
Tayyab et al. [18] | - | - | - | Yes | Yes | Yes | Yes | - | Multi-stage textile production system |
Mukhopadhyay and Goswami [20] | - | - | - | Yes | - | Yes | - | - | One manufacturer |
Dye and Yang [21] | Yes | Yes | - | - | Yes | Yes | - | Yes | One manufacturer |
Kundu and Chakrabarti [25] | - | Yes | - | Yes | - | - | - | - | One distributor, one purchaser |
Daryanto et al. [27] | - | Yes | - | - | - | - | - | - | One distributor, one purchaser |
Manna et al. [45] | - | Yes | - | - | Yes | - | - | One manufacture | |
Kumar and Goswami [54] | - | - | Yes | - | - | Yes | - | - | One manufacturer |
Habib et al. [64] | - | - | - | - | - | - | - | - | Possibilistic programming approach |
Lee and Kim [65] | - | Yes | - | - | - | Yes | - | - | One distributor, one purchaser |
Singh et al. [66] | Yes | - | - | Yes | - | Yes | - | - | SSC for waste management |
This paper | Yes | Yes | Yes | Yes | Yes | Yes | Yes | Yes | Single supplier, multiple competitive buyer |
Optimal values | P | Q1 | Q2 | y1 | y2 | Total profit ($/year) | Carbon emissions (tons/year) |
Model 1 (crisp) | 147.22 | 1.54 | 1.63 | 76.36 | 76.76 | 13,823.1 | 17.82 |
Model 2 (fuzzy) | 137.72 | 3.15 | 2.98 | 71.77 | 72.60 | 14,131.8 | 17.03 |
Model 3 (learning in fuzziness) | 144.23 | 1.34 | 2.26 | 75.02 | 76.34 | 13,828.5 | 17.59 |
Variables | P | Q1 | Q2 | y1 | y2 | Total profit ($/year) | Carbon emissions (tons/year) |
Model (3) | 144.23 | 1.34 | 2.26 | 75.02 | 76.34 | 13,828.5 | 17.59 |
Model (4) | 114.45 | 2.92 | 2.81 | 65.05 | 68.43 | 13,768.8 | 14.9 |
Model (5) | 105.35 | 3.93 | 3.62 | 89.42 | 91.95 | 11,996.2 | 14.0 |
Model (6) | 114.44 | 2.92 | 2.80 | 65.04 | 68.42 | 13,785.6 | 14.9 |
Parameters | Change | Total profit | P | Q1 | Q2 | y1 | y2 |
to | fall | rise | rise | _ | _ | _ | _ |
COM | rise | fall | _ | _ | _ | rise | rise |
T | fall | rise | rise | _ | _ | _ | _ |
CM | rise | rise | rise | _ | _ | fall | fall |
CSM | rise | fall | fall | fall | rise | rise | rise |
CW | rise | fall | rise | rise | rise | rise | rise |
HM | fall | rise | rise | _ | _ | fall | fall |
CTMi | fall | rise | rise | rise | fall | fall | fall |
CORi | rise | rise | None | fall | rise | fall | fall |
HRi | rise | fall | fall | None | None | rise | rise |
HDRi | rise | fall | fall | _ | _ | rise | rise |
HWRi | rise | fall | None | rise | rise | fall | fall |
CSR1 | fall | rise | rise | None | None | None | None |
CBi | rise | fall | fall | fall | rise | rise | rise |
CLi | rise | fall | None | fall | None | None | None |
ϵ | rise | fall | fall | None | rise | None | None |
li | rise | rise | fall | None | rise | fall | rise |
ai | rise | None | None | _ | _ | None | None |
ᵞ | rise | rise | rise | _ | _ | rise | rise |
β | rise | rise | rise | _ | _ | rise | rise |
Competitive prices | y1=74 | y1=75 | y1=76 | y1=77 |
y2=74 | 13,834.5 | 13,830.7 | 13,826.3 | 13,821.5 |
y2=75 | 13,833.9 | 13,830.2 | 13,826.1 | 13,821.5 |
y2=76 | 13,832.8 | 13,829.3 | 13,825.4 | 13,821.0 |
y2=77 | 13,831.2 | 13,828.0 | 13,824.3 | 13,820.1 |
α | m=25 | m=50 | m=75 | m=100 |
0.862 | 13,842.0 | 13,833.3 | 13,830.1 | 13,828.5 |
0.737 | 13,851.5 | 13,840.0 | 13,835.5 | 13,833.0 |
0.621 | 13,864.6 | 13,849.9 | 13,843.9 | 13,840.4 |
0.515 | 13,881.7 | 13,856.2 | 13,864.0 | 13,851.7 |
0.415 | 13,904.1 | 13,883.8 | 13,874.3 | 13,868.5 |
0.322 | 13,932.6 | 13,910.6 | 13,899.8 | 13,893.0 |
0.234 | 13,968.6 | 13,946.7 | 13,935.5 | 13,928.1 |
0.152 | 14,012.6 | 13,993.7 | 13,993.3 | 13,976.5 |
0.074 | 1466.9 | 14,054.7 | 14,047.8 | 14,043.1 |
Carbon tax ($/ton) | P | Q1 | Q2 | y1 | y2 | Total profit ($/year) | Carbon emissions (tons/year) |
1.2 | 114.447 | 2.9248 | 2.8056 | 65.0461 | 68.428 | 13,768.8 | 14.900 |
1.3 | 114.345 | 2.9249 | 2.8056 | 65.0459 | 68.428 | 13,767.1 | 14.892 |
1.6 | 113.979 | 2.9878 | 2.7934 | 65.0425 | 68.388 | 13,762.9 | 14.856 |
1.9 | 112.794 | 3.0745 | 2.7895 | 65.0423 | 69.036 | 13,753.4 | 14.739 |
∈1 | P | Q1 | Q2 | y1 | y2 | Total profit ($/year) |
1.4 | 114.44 | 2.92 | 2.80 | 65.04 | 68.42 | 13,785.6 |
5.0 | 114.44 | 2.92 | 2.80 | 65.04 | 68.42 | 13,782.2 |
7.0 | 114.44 | 2.92 | 2.80 | 65.04 | 68.42 | 13,780.4 |
9.0 | 114.44 | 2.92 | 2.80 | 65.04 | 68.42 | 13,778.6 |