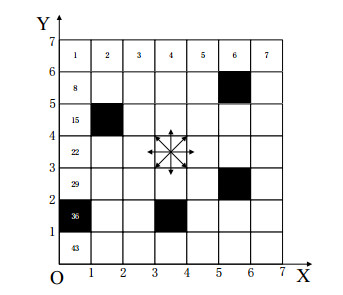
The Indonesian Presidential Regulation No. 35 of 2018 heralds a transformative agenda for producing electrical energy from biomass in an environmentally conscious manner. Jakarta emerges as a pivotal area in this transformation, with its strategic adoption of Waste to Energy (WtE) systems. In this study, we probe into the multiple layers of community preferences and the acceptance of WtE developments in Jakarta, factoring in an array of local concerns and policy-driven directives. Through a methodologically structured choice experiment, participants weighed in on various scenarios delineating shifts from the status quo to innovative WtE technological adoptions. we scrutinize a spectrum of attributes, each with defined status quo levels and proposed advancements: From enhancing awareness of landfill impacts (P1), escalating local policy commitments (K1) and integrating waste treatment facilities (F1) to diversifying waste processing outputs into liquid (PP1), solid (PP2), gas (PP3) and electricity (PP4). We also consider the transition from unmanaged landfills to controlled applications of landfill gas (PA1) and thermal treatment (PA2), as well as the initiation of emission and pollutant monitoring (M1).Our findings illuminate a significant public inclination to move beyond the current paradigms towards embracing WtE conversions, with particular willingness to support socialization of new waste processing technologies (P1), generation of energy in various forms especially liquid (PP1) and electricity (PP4) and implementation of environmental monitoring measures (M1). These attributes were marked by a notable willingness to accept (WTA) the proposed changes, signaling a readiness for policy and infrastructural advancements in waste management.
Citation: Aarce Tehupeiory, Iva Yenis Septiariva, I Wayan Koko Suryawan. Evaluating Community Preferences for Waste-to-Energy Development in Jakarta: An Analysis Using the Choice Experiment Method[J]. AIMS Environmental Science, 2023, 10(6): 809-831. doi: 10.3934/environsci.2023044
[1] | Jinzhuang Xiao, Xuele Yu, Keke Sun, Zhen Zhou, Gang Zhou . Multiobjective path optimization of an indoor AGV based on an improved ACO-DWA. Mathematical Biosciences and Engineering, 2022, 19(12): 12532-12557. doi: 10.3934/mbe.2022585 |
[2] | Yejun Hu, Liangcai Dong, Lei Xu . Multi-AGV dispatching and routing problem based on a three-stage decomposition method. Mathematical Biosciences and Engineering, 2020, 17(5): 5150-5172. doi: 10.3934/mbe.2020279 |
[3] | Zhen Zhou, Chenchen Geng, Buhu Qi, Aiwen Meng, Jinzhuang Xiao . Research and experiment on global path planning for indoor AGV via improved ACO and fuzzy DWA. Mathematical Biosciences and Engineering, 2023, 20(11): 19152-19173. doi: 10.3934/mbe.2023846 |
[4] | Li-zhen Du, Shanfu Ke, Zhen Wang, Jing Tao, Lianqing Yu, Hongjun Li . Research on multi-load AGV path planning of weaving workshop based on time priority. Mathematical Biosciences and Engineering, 2019, 16(4): 2277-2292. doi: 10.3934/mbe.2019113 |
[5] | Baoye Song, Shumin Tang, Yao Li . A new path planning strategy integrating improved ACO and DWA algorithms for mobile robots in dynamic environments. Mathematical Biosciences and Engineering, 2024, 21(2): 2189-2211. doi: 10.3934/mbe.2024096 |
[6] | Xiaoyong Xiong, Haitao Min, Yuanbin Yu, Pengyu Wang . Application improvement of A* algorithm in intelligent vehicle trajectory planning. Mathematical Biosciences and Engineering, 2021, 18(1): 1-21. doi: 10.3934/mbe.2021001 |
[7] | Liwei Yang, Lixia Fu, Ping Li, Jianlin Mao, Ning Guo, Linghao Du . LF-ACO: an effective formation path planning for multi-mobile robot. Mathematical Biosciences and Engineering, 2022, 19(1): 225-252. doi: 10.3934/mbe.2022012 |
[8] | Tian Xue, Liu Li, Liu Shuang, Du Zhiping, Pang Ming . Path planning of mobile robot based on improved ant colony algorithm for logistics. Mathematical Biosciences and Engineering, 2021, 18(4): 3034-3045. doi: 10.3934/mbe.2021152 |
[9] | Xuewu Wang, Bin Tang, Xin Zhou, Xingsheng Gu . Double-robot obstacle avoidance path optimization for welding process. Mathematical Biosciences and Engineering, 2019, 16(5): 5697-5708. doi: 10.3934/mbe.2019284 |
[10] | Yuzhuo Shi, Huijie Zhang, Zhisheng Li, Kun Hao, Yonglei Liu, Lu Zhao . Path planning for mobile robots in complex environments based on improved ant colony algorithm. Mathematical Biosciences and Engineering, 2023, 20(9): 15568-15602. doi: 10.3934/mbe.2023695 |
The Indonesian Presidential Regulation No. 35 of 2018 heralds a transformative agenda for producing electrical energy from biomass in an environmentally conscious manner. Jakarta emerges as a pivotal area in this transformation, with its strategic adoption of Waste to Energy (WtE) systems. In this study, we probe into the multiple layers of community preferences and the acceptance of WtE developments in Jakarta, factoring in an array of local concerns and policy-driven directives. Through a methodologically structured choice experiment, participants weighed in on various scenarios delineating shifts from the status quo to innovative WtE technological adoptions. we scrutinize a spectrum of attributes, each with defined status quo levels and proposed advancements: From enhancing awareness of landfill impacts (P1), escalating local policy commitments (K1) and integrating waste treatment facilities (F1) to diversifying waste processing outputs into liquid (PP1), solid (PP2), gas (PP3) and electricity (PP4). We also consider the transition from unmanaged landfills to controlled applications of landfill gas (PA1) and thermal treatment (PA2), as well as the initiation of emission and pollutant monitoring (M1).Our findings illuminate a significant public inclination to move beyond the current paradigms towards embracing WtE conversions, with particular willingness to support socialization of new waste processing technologies (P1), generation of energy in various forms especially liquid (PP1) and electricity (PP4) and implementation of environmental monitoring measures (M1). These attributes were marked by a notable willingness to accept (WTA) the proposed changes, signaling a readiness for policy and infrastructural advancements in waste management.
Sensible logistics are essential for advancing the manufacturing industry in the context of intelligent manufacturing. Intelligent logistics achieves process automation and intelligence by fusing cutting-edge technologies like the Internet with intelligent instruments like smart robots, in line with the objectives of intelligent manufacturing. Modern technologies like the Internet of Things, cloud computing, big data, and artificial intelligence are essential to the smart logistics distribution system. In order to ensure seamless job completion and minimize the need for human and material resources, they expedite the design of order tasks, material distribution routes, vehicle scheduling, and load capacity. This all-encompassing strategy significantly improves production and logistical efficiencies [1]. Both software and hardware are needed to construct a smart logistics system. Stackers, different conveying equipment, and automated guided vehicles (AGV) are foundational elements. The enhancement of intelligent logistics is ensured by the digital workshop control system, path planning, navigation algorithm, and optimization algorithm.
Studies show that throughout the whole product production process, transportation, loading and unloading, and other links use three quarters of the time, while production and processing take up one quarter. Forklifts and other equipment are used in traditional transportation methods, which are dangerous, labor-intensive, and prone to mistakes. Deploying robots or AGVs as a substitute is beneficial in places with high labor costs, scarce human resources, or hazardous situations. As a component of intelligent logistics, AGV automates and simplifies the logistics transportation process, lowering labor costs in warehouses and enhancing operational effectiveness. This is in accordance with the trend of building intelligent and automated logistic systems in industrial development.
AGVs have taken on a variety of complex responsibilities in recent years. The main goal of material distribution using AGVs is to minimize human interaction by guaranteeing efficient conveyance to the work site. Therefore, solving the AGV path planning problem in the intelligent distribution system is necessary to realize intelligent logistics in the digital workshop [2,3].
AGV path planning has drawn a lot of interest due to its widespread applicability. The Dijkstra algorithm, A* algorithm, deep reinforcement learning algorithm, and ant colony algorithm are some of the most widely used path planning techniques. Based on the Dijkstra algorithm, Zhou and Huang [4] presented an improved method that uses the ant colony optimization strategy to optimize AGV pathways in airport situations. This model takes obstacle-filled situations into account. Results from simulations demonstrate that the combined algorithm in the airport baggage check-in path planning model performs better than three different methods. It is noteworthy that it reduces path lengths by 2.3, 2.64 and 6.06%. In order to provide collision avoidance when crossing known moving obstacles, He [5] and colleagues developed a dynamic search mechanism within the DAA (Dynamic A* Algorithm) that takes temporal considerations into account. The results of the simulations show that the DAA star algorithm performs better than the dynamic A* algorithm and the conventional A* algorithm in complex navigation scenarios. In order to learn the best decisions, Gu [6] and his associates used the Munchausen deep Q-learning network (m-DQN) for mobile robot applications. The simulation findings highlight how this approach learns more effectively and converges more quickly than DQN, Dueling DQN, and m-DQN counterparts, especially in static and dynamic situations. The technique is also very good at creating pathways that avoid collisions and go around obstructions. A group of researchers led by Miao [7] presented an improved adaptable ant colony algorithm (IaACO). Initially, angle guidance and obstacle removal parameters were integrated into the traditional ant colony algorithm (ACO) to increase the transmission probability. Second, adaptive pheromone volatilization factors and heuristic information adaptive adjustment were included to improve the pheromone update algorithms. The results of the experiment show that IaACO allows the robot to achieve global optimal pathways, exhibiting excellent planning stability and real-time performance.
In digital manufacturing workshops, the higher computer system must quickly determine an appropriate path for the AGV in order to guarantee the effectiveness of AGV logistics. Unfortunately, the training procedure for algorithms like the ant colony algorithm, DQN, and others takes a long time [8,9,10,11,12], which makes it difficult to increase the workshop's AGV's logistical efficiency. The Dijkstra algorithm wastes time by having to search through an excessive number of nodes in the search path. As a result, the A* algorithm is selected as the fundamental algorithm in this article.
The frequency of AGV starts and pauses, as well as the amount of time they spend navigating turns on the path, can both be greatly reduced with a streamlined path. This optimization is essential to increasing the overall effectiveness of logistics. Five spiral transition curve templates with monotonic (increasing or decreasing) curvature and cubic Bezier curve configurations were presented by Bibi et al. [13]. The benefits of cubic Bezier spiral path smoothing technology were illustrated through experimental validation. To tackle the issue of excessive nodes and spikes during path design, Duraklı [14] presented a novel solution based on Bezier curves. The results of the experiments demonstrated the effectiveness of the strategy in determining the best routes between the beginning and target points in well-known areas. Global smooth path planning for mobile robots with motion constraints was examined by Song [15]. They developed a method that combines spline curves and an improved particle swarm optimization technique. The efficiency of this strategy was demonstrated decisively by the outcomes of the experiment.
There are still a number of issues with path smoothing, despite the large amount of research on the subject. Interestingly, a great deal of current path smoothing research projects unintentionally introduce curvature to the straight regions of the path by applying smoothing algorithms to such segments. Once smoothed, this curvature becomes detrimental to the best possible operating of AGVs. Therefore, there is a strong need to present a novel method of path smoothing that successfully takes care of this issue.
To sum up, this post will enhance the A* algorithm on the inside as well as the outside. In order to increase the efficiency of the A* algorithm, the traditional heuristic function is first replaced with a diagonal heuristic function, and the turning cost is increased. Afterwards, redundant turns and path optimization at corners are reduced by enhancing the forward search algorithm and the Bezier curve method outside of the A* algorithm.
The main contributions of this paper are as follows:
1) Enhance the A* algorithm internally. We improve node traversal logic to stop pathways from intersecting barriers diagonally, which would produce erroneous paths. The search efficiency of the algorithm can be increased by using a diagonal distance heuristic function for 8 neighborhood search directions, which can more precisely estimate the expected cost from the current node to the target node. We reduce the number of nodes traveled during the path search of the A* algorithm and increase search efficiency by adding turning weights to the method's formula.
2) On the output path of the internally improved A* algorithm, we do external optimization. The forward search optimization technique is improved and a new algorithm is suggested in this paper. This technique can identify important turning points in the path and eliminate unnecessary ones. To smooth out important turning points, this article uses an optimization technique based on Bessel curves.
A digital manufacturing workshop serves as the path planning algorithm's application scenario in this article. Inside the manufacturing workshop, there are numerous production scenarios, unlike in ports, airports, and storage facilities. AGVs can go straight from the conclusion of one task to the beginning of the next, eliminating the requirement for them to stop and return to a fixed node while in operation. As a result, the AGVs' starting point and destination in the production workplace are dynamic, and they must be able to swiftly plan their route from one task node to the next.
The manufacturing areas in the workshop have a basic layout, and that is where the impediments are positioned. For map modeling, this tutorial opts to utilize the grid map method. The area where an AGV may walk is shown by the white area in the grid map (Figure 1), while the area with obstacles is represented by the black area. The grid's numbering is represented by the numbers on the grid, which are written as 1,2,3,...,w from top to bottom and left to right. Arrows in eight directions grant authorization to search for paths from those eight directions. Specifically, the positive X-axis direction is defined from left to right, and the positive Y-axis direction is specified from bottom to top, starting from the bottom left corner of the grid area. Define the grid length as the unit length to establish a two-dimensional coordinate plane XOY [16]. The following is the correspondence between the grid number and coordinates:
{x=mod(W,N)−0.5,x>0x=N−0.5,x<0y=N+0.5−ceil(W/N) | (1) |
In this formula, x,y represents the horizontal and vertical coordinates of the grid map, mod is a remainder operation, W is the number of the grid, N is the number of rows and columns in the grid, and ceil is the rounding function.
The A* algorithm [19] constitutes a heuristic search-driven routing algorithm, designed for identifying the shortest path between a given starting point and an end point within a graph (or grid) structure. This approach employs an evaluation function to assess potential pathways and subsequently opts for the most promising route based on the outcome of the evaluation. Equation (2) delineates the evaluation function employed by the A* algorithm.
f(n)=g(n)+h(n) | (2) |
where f(n)is the total cost of current node n, g(n) is the actual cost from the starting point to node n, and h(n) is the estimated cost from node n to the end point.
The algorithm maintains an open list that contains the nodes to be evaluated and a closed list that contains the evaluated nodes. The flow chart of the A* algorithm is shown in Figure 2.
At present, the Euclidean distance, Manhattan distance, and Chebyshev distance are commonly used in the A* algorithm. The Euclidean distance is expressed as
ho=√(xe−xn)2+(ye−yn)2 | (3) |
The Manhattan distance is expressed as
hm=|xe−xn|+|ye−yn| | (4) |
The Chebyshev distance is expressed as
hc=max(|xe−xn|,|ye−yn|) | (5) |
where (xe,ye) is the endpoint coordinate, and (xn,yn) is the current node coordinate.
Given that this paper designates the AGV's movement direction on the map as comprising 8 directions, both straight-line and diagonal motions of the AGV are factored into consideration. Specifically, this study presumes the cost of straight-line motion as 1 and the cost of diagonal motion as 1.4, expressed mathematically as
g(n)={1 ,xn=xn+1 or yn=yn+1 1.4 ,other | (6) |
where (xn,yn) is the coordinates of the current node and (xn+1,yn+1) is the coordinates of the child nodes of the current node.
The estimated cost significantly influences the search direction of the A* algorithm. An accurate estimated cost effectively gauges the expense from the present node to the destination, thereby steering the A* algorithm toward a correct search direction. The trajectories corresponding to three distinct estimated costs are illustrated in Figure 3.
The evaluation criteria for the estimated cost function encompass the actual path cost, the count of turns, and the number of traversed nodes. As depicted in Figure 1, when employing Euclidean distance as the metric, the path's actual cost totals 30, involving 9 turns and traversing 117 nodes. Utilization of the Manhattan distance results in the algorithm primarily navigating through nodes during its search. Due to the sparse number of traversed nodes, the path derived from this estimation function might not necessarily represent the optimal trajectory. Specifically, the path under Manhattan distance exhibits an actual cost of 31.2, accompanied by 13 turns and 26 traversed nodes. When employing Chebyshev distance, the path incurs the highest tally of turns and traversed nodes, at 14 turns and 172 nodes, with an actual cost of 30. A comprehensive comparison of evaluation metrics under the three distinct estimated cost functions is detailed in Table 1.
h(n) | Actual cost | Number of turns | traversal nodes |
Euclidean distance | 30 | 9 | 117 |
Manhattan distance | 31.2 | 13 | 26 |
Chebyshev distance | 30 | 14 | 172 |
To sum up, this paper selects Euclidean distance as the estimated cost function when improving the A* algorithm.
1) Optimize node traversal logic. In the conventional employment of the A* algorithm for path planning, the algorithm stores the traversed nodes within a closed list. Within this list, any two nodes that share a relationship are regarded as interconnected. However, this approach can lead to an issue wherein the final planned path navigates between the vertices of two obstacles, as visually demonstrated in Figure 4. Consequently, the planned path might prove impractical for real-world applications.
To address the aforementioned issues, this study enhances the node traversal logic within the traditional A* algorithm. The function Node_traversal() is constructed. When the A* algorithm is traversing the nodes, it judges whether the upper, lower, left, and right adjacent nodes of the visited node (i,j) are obstacles. When the upper and right adjacent nodes of the node are obstacles, it skips traversing the adjacent node (i+1,j+1) in the upper right direction of the node and does not put it into the close list, so as to avoid the nodes. This adjustment prevents scenarios where paths inadvertently pass through the interstices between two obstacles located at opposing corners, as depicted in Figure 5. Under the refined node traversal logic, as the traversal progresses to node (2.5, 1.5), the presence of obstacles above and to the right of this node prevents the inclusion of point (3.5, 2.5) in the closed list.
The pseudo code of function Node_traversal() is shown in Algorithm 1.
Algorithm 1 |
1. Direction = [(0, 1), (0, -1), (1, 0), (-1, 0)] |
2. Current = (i, j) |
3. For each direction in Direction do |
4. Neighbor = Current + each direction |
5. If up_ Neighbor = obstacle and right_ Neighbor = obstacle do |
6. Pass |
7. If up_ Neighbor = obstacle and left_ Neighbor = obstacle do |
8. Pass |
9. If down_ Neighbor = obstacle and right_ Neighbor = obstacle do |
10. Pass |
11. If down_ Neighbor = obstacle and left_ Neighbor = obstacle do |
12. Pass |
13. End |
In the pseudo code, the initial line defines the four cardinal directions: up, down, left, and right. The second line designates the presently traversed node, referred to as "current". Subsequently, lines 3 and 4 establish a loop to sequentially access the four adjacent nodes to the current node through the iterative process. Lines 5 and 6 are formulated to avoid traversing the upper-right node if both the upper and right sides of the current node are obstructed. Similarly, lines 7 and 8 are designed to bypass traversal of the upper-left node in scenarios where the upper and left sides of the current node are obstructed. Analogously, lines 9 and 10, as well as lines 11 and 12, serve to prevent traversal of the lower-right and lower-left nodes, respectively, under conditions where the corresponding sides of the current node are occupied by obstacles.
The improved A* algorithm successfully mitigates the challenge of navigating through the vertices within obstacles, thereby enabling the A* algorithm to formulate a more rational path. The operational outcome of the improved A* approach is visually illustrated in Figure 6. Notably, as demonstrated in the figure, when the node's traversal reaches the coordinates (10.5, 11.5), the search does not encompass a node located at (11.5, 12.5).
2) Replacing the conventional cost estimation function. While the A* algorithm utilizing Euclidean distance can find the shortest path with fewer traversed nodes, it might result in a higher number of turns within the path, as illustrated in Figure 7.
Under such circumstances, the smooth operation of the AGV would be compromised. Therefore, this study replaces the Euclidean distance with diagonal distance in order to achieve a more accurate representation of the cost estimation function from the current point to the destination. This enhancement better guides the A* algorithm in finding the optimal path. The formula for diagonal distance is as follows:
hd(n)=min(|xn−xe|,|yn−ye|),hs(n)=|xn−xe|+|yn−ye|,htotal(n)=D1×hd+D2×(hs−2×hd), | (7) |
Among these, hd represents the cost in the diagonal direction, hs represents the cost in the straight line direction, (xn,yn) represents the current node coordinate, (xe,ye) represents the target node coordinate, htotal represents the diagonal distance calculation formula, and D1, D2 represent parameters, where D1 is 1 and D2 is 1.4.
Upon employing diagonal distance, the planned path effectively reduces the count of redundant turns and the number of traversed nodes, as depicted in Figure 8.
3) Increase the cost of turning. The conventional A* algorithm predominantly employs length as the primary criterion, prioritizing the attainment of the shortest overall distance as the optimal path. However, an exclusive focus on minimizing length may result in frequent turns by the AGV during its movement. In practical scenarios, the act of acceleration and deceleration during turning substantially escalates the time expense, rendering it considerably higher than that incurred during linear motion. This divergence in time costs undermines overall efficiency and hampers the attainment of a smooth path. To address this concern, this paper introduces an enhancement to the calculation formula of the conventional A* algorithm. This enhancement entails the incorporation of a turning cost into the original calculation formula. By introducing this turning cost, the aim is to curtail the frequency of turns within the path, thereby fostering a more streamlined trajectory.
When accounting for the turning cost, it becomes imperative to initially assess the occurrence of a turn. In this investigation, the analysis employs the three-point collinear method for turn detection. This method involves utilizing three nodes and applying Eq (8) to perform the calculation.
K=(xn−xn−1)×(yn+1−yn)−(yn−yn−1)×(xn+1−xn) | (8) |
where (xn−1,yn−1) is the parent node of the current node, (xn,yn) is the current node, and (xn+1,yn+1) is the current node sub node. The node relationship is shown in Figure 9.
For a straight-line path, Eq (8) yields a K value of 0. However, during turning maneuvers, distinct K values emerge. Specifically, based on the outcomes of Eq (8), a left turn corresponds to a K value of -1, while a right turn corresponds to a K value of 1. In this study, the costs associated with left and right turns are not individually considered, but rather are collectively regarded as turning costs. Consequently, the expression for the C value is illustrated in Eq (9).
C={1 ,K=01.2 ,others | (9) |
where C is the turning cost.
To sum up, the improved A* formula is:
f(n)=g(n)+C×htotal(n) | (10) |
Under these conditions, the A* algorithm with improved heuristic function will give priority to traversing nodes in the current direction during the node search process, which will minimize the exploration of nodes in other directions. In Figure 10, the concept is displayed. Figure 10(a), (b) depict the search procedure using conventional heuristic functions and weighted heuristic functions, respectively. It is evident that node (2.5, 1.5) determines which child nodes are selected differently between the two. When choosing child nodes, weighted heuristic functions incur a higher cost at point (2.5, 2.5) since (2.5, 1.5) is the turning point, whereas traditional heuristic functions execute a turning point at node (2.5, 1.5). Therefore, the weighted heuristic functions continue to search in the original direction, reducing the number of turning points and traversing nodes in the path.
The objective of this section is to conduct further path optimization based on the output path generated by the A* algorithm. This process is chiefly divided into two primary steps: Path Optimization: Initially, the path is optimized to eliminate extraneous turning points present within it; Bezier Curve Fitting: Subsequently, the remaining turning points are subjected to a fitting process using Bezier curves.
1) Path optimization
While the internal enhancements applied to the A* algorithm effectively curtail the occurrence of turns within the path, it is important to acknowledge that the path's optimality remains contingent on the constraints of the grid map. Consequently, the resultant path might not always be the absolute optimal solution, and some degree of turns may still persist. As illustrated in Figure 11, an excessive number of turns can extend the logistics duration, thereby substantially diminishing logistics efficiency within the production workshop setting.
To solve this problem, this paper adopts a path optimization method based on forward search optimization [25]. The optimization process of this method is shown in Figure 12: First, define the set of input path nodes. Then, take the starting node of the path as the current vertex, search the subsequent path nodes, find the last key node k1 connected with the starting point (connectivity means that the connection between the starting point and k1 point does not pass through obstacles), connect the starting point with k1, then take k1 as the starting point, search the points after k1 with the same logic, and set these key points to k2, k3 in turn. Then, insert the sampling point si on the path, take s10 (the k2 point in the previous step) as the current key point, and check whether the connection between s1−s5 and s10 will pass through obstacles. If there are none, take s13 (the k3 point in the previous step) as the current key point, and check whether the connection between s1−s9 and s10 will pass through obstacles. Since point s7 is the first point that can be connected with s13, s7 is taken as the new key point k2. Then, connect s7 and s13 to form the second optimization path, and s1−s7 is optimized by using similar methods. Finally, the final optimization path is obtained.
While the concept behind the path optimization method is viable, the execution process proves excessively intricate. Consequently, this paper introduces an improved forward search optimization approach. This improved method is primarily segmented into the subsequent steps:
Step 1. The output path set P=([x1,y1],[x2,y2],⋯,[xi,yi]) of the A* algorithm is interpolated. The interpolation method employed here is uniform interpolation, wherein a new node is inserted between two given points. This process can be mathematically represented as
{xnew=xn+1−xn2ynew=yn+1−yn2 | (11) |
where (xnew,ynew) are the coordinates of the inserted new node, (xn,yn) are the coordinates of the current node, and (xn+1,yn+1) are the coordinates of the child nodes of the current node.
Take the interpolated path set Pnew=([x1,y1],[xnew,ynew],[x2,y2],⋯,[xi,yi]) as a new path set.
Step 2. Construct a key point set K and an obstacle vertex set Ovc. Starting from the initial point, perform a forward search to identify the first point connected to the initial point and also present in the set Ovc. Label this point as k1 and add it to K.
Step 3. Set k1 as the new starting point, repeat Step 2, and designate the subsequent points as k2,k3,⋯,ki, with i representing the number of key points.
Step 4. Repeat Step 3 to obtain the final set of key points, denoted as K.
Step 5. Connect all key points in K to achieve path optimization.
The process diagram of the improved forward search optimization method proposed in this paper is shown in Figure 13.
The pseudo code is shown in Algorithm 2
Algorithm 2 |
1: function INSERT_NEW_NODES_BETWEEN_POINTS(P) |
2: p_new←{} |
3: for i←0 to len (P)-1 do |
4: p_new.append (P [i]) |
5: x1, y1←P [i] |
6: x2, y2←P [i + 1] |
7: new_node←((x1 + x2) / 2, (y1 + y2) / 2) |
8: p_new.append (new_node) |
9: end for |
10: p_new.append (P [-1]) |
11: return p_new |
12: end function |
13: function FIND_PATH (P) |
14: p_new←insert_new_nodes_between_points (P) |
15: Ovc←[] |
16: K←[] |
17: K.append(p_new [0]) |
18: start←p_new [0] |
19: for j←p_new.index (start) + 1 to len (p_new) do |
20: if line (start, p_new [j]) and p_new [j-1]∈Ovc then |
21: K. append (p_new [j-1]) |
22: start←p_new [j-1] |
23: end if |
24: end for |
25: K.append (p_new [-1]) |
26: return K |
27: end function |
In the pseudo code of Algorithm 2, lines 1 to 12 correspond to the process in Step 1. Lines 13 to 26 correspond to the process in Steps 2–4. The line(start,p_new[j]) function is used to determine whether start points are connected with p_new[j] points.
2) Path smoothing
The smoothing of the path refers to the use of Bezier curves, spline interpolation curves, and other methods to fit the path by using the curve to improve the smoothness of the path.
Although the optimized path greatly reduces turning, the turning point intersects with the vertex of the obstacle, and the AGV may collide with the obstacle when passing by. Therefore, the path must be adjusted for obstacle avoidance before curve fitting.
First, the relationship between the optimized path and the nearby obstacles is analyzed, as shown in Figure 14, where the gray grid indicates the location of the possible obstacles.
Based on this, to ensure a certain safe distance between the path and the obstacle, the obstacle avoidance adjustment process proposed in this paper is presented as follows:
Step 1. Calculate the direction vector of k1 and obstacle coordinates according to Eq (12).
→a=(xobstacle−xk1,yobstacle−yk1) | (12) |
where →a is the direction vector, (xobstacle,yobstacle) is the obstacle coordinate, and (xk1,yk1) is the k1 coordinate.
Step 2. Move one half of the grid distance in the opposite direction of k1 along the direction vector as follows:
(xk1_n,yk1_n)=(xk1,yk1)−L2→a | (13) |
where (xk1_n,yk1_n) represents the new coordinates of k1, and L represents the width of the grid.
Step 3. Update k1 coordinates, build the linear equation from the starting point to k1, and assess the distance between the obstacle coordinates and the straight line. When the distance is less than L, set the nearest vertex from the obstacle to the straight line to kinsert and repeat Steps 1 and 2. At this time, k1 in Steps 1 and 2 is kinsert, and the obstacle avoidance of the path is completed. kinsert is located between the starting point and k1.
Step 4. After completing the obstacle avoidance operation from the starting point to k1, make k1 a new starting point and repeat Steps 1 to 3 to complete the obstacle avoidance of the entire road.
The process is shown in Figure 15.
Then, the second-order Bezier curve is used to fit the rotation angle. The second-order Bezier curve is mathematically expressed as
B(t)=(1−t)2P0+2t(1−t)P1+t2P2,t∈[0,1] | (14) |
where P0, P1, and P2 are the three control points, and t is a parameter.
In this paper, the selection method of control points P0 and P2 is explained as follows. First, calculate the direction vectors of kinsert and k1 coordinates and the starting line and the next node line. Second, use a similar method in obstacle avoidance adjustment to select P0 and P2 control points on the two paths with length L as the distance. Finally, kinsert and k1 are used as P1 control points to achieve curve fitting at turns, as shown in Figure 16.
After improving the traditional A* algorithm in Sections 4.1 and 4.2, the AGV path planning method based on the improved A* algorithm can be illustrated by the flow chart in Figure 17.
Comprehensive experiments were conducted on the Pycharm 2022.3 platform. The programming language is Python 3.10. The performance of the proposed improved A* algorithm was tested, and the framework used by the DQN network was TensorFlow. The performance parameters of the execution host are Windows 10, and the hardware parameters are Intel(R) core(TM) i5-8250U CPU, 1.6 GHz, x64, 8 GB (RAM).
The obstacles in the production workshop are each production area. These production areas are usually large in area and simple in shape. Therefore, this article simulates and constructs maps with sizes of 20 × 20, 30 × 30, and 40 × 40 based on the characteristics of obstacles in the production workshop, as shown in Figure 18.
This study uses path length, turning angle, number of traversal nodes, and algorithm running time as evaluation indices. The length of the path indicates the true cost of the path. The turning angle is the total of the degrees the AGV must turn in order to travel down the course. The number of nodes that the algorithm traverses in order to locate the path is represented by the number of traversal nodes. The algorithm's running time shows how long the path is searched throughout that period.
This paper uses both theoretical and simulated experiments for its experimental section. In the theoretical experimental part, the internal improved A* algorithm is first compared with other algorithms, and then the improved forward search optimization algorithm is verified. A custom path planner in the ROS system is used in the simulation experiment section of this article to use the traditional A* algorithm, internally improved A* algorithm, and improved A* algorithm as plugins. Simulation verification is carried out by calling algorithm plugins.
The algorithms involved in the comparison include the traditional A* algorithm, Dijkstra algorithm, bidirectional A* algorithm, ant colony algorithm, DQN algorithm, and the internal improved A* algorithm in this paper. The starting point is the (0.5, 0.5) point, and the ending point is the point in the upper right corner. The cyan and red grids in the grid graph represent the traversed nodes. The parameters of the ant colony algorithm are shown in Table 2, and the parameters of the DQN algorithm are shown in Table 3.
parameter | value |
Number of ants | 20 |
Number of iterations | 150 |
Pheromone evaporation rate | 0.5 |
pheromone factor | 1.1 |
heuristic function factor | 4 |
parameter | value |
Learning rate | 0.001 |
Discount factor | 0.995 |
Exploration rate | 0.4 |
Batch size | 64 |
As shown in Figure 19, when comparing the ant colony method to other algorithms at a 20 × 20 grid map, it yielded the longest path length, with the other algorithms obtaining the same path length. The turning angle of the traditional A*, bidirectional A*, ant colony algorithm, DQN algorithm, and Dijkstra method has grown by 135,135,315,135, and 90°, respectively. The ant colony algorithm and DQN algorithm have distinct search algorithms from the others, therefore, the indicator of the number of traversal nodes is not considered, however, the traditional A* algorithm, bidirectional A* algorithm, and Dijkstra algorithm have increased by 43, 35, and 285, respectively. Algorithm running times rose by 0.51 s for the traditional A* algorithm, 0.24 s for the bidirectional A* method, 4.59 s for the ant colony algorithm, 4.33 s for the DQN algorithm, and 1.59 s for the Dijkstra algorithm.
As shown in Figure 20, the conventional A* algorithm outperforms the internal improved A* algorithm on a 30 × 30 grid map in terms of path length, number of traversed nodes, and algorithm running time. The bidirectional A* algorithm outperforms the internal improved A* algorithm in terms of both these metrics. The ant colony and DQN algorithms outperform the internal improved A* algorithm in terms of path length. Although in some indicators the comparison algorithm outperforms the internal improved A* algorithm, the comparison algorithm's planned path, which goes from nodes (20.5, 19.5) to (21.5, 20.5), diagonally passes through two obstacle nodes (20.5, 20.5) and (19.5, 21.5), making the expected path AGV invalid. This illustration confirms that the A* algorithm's internal improvement can prevent the creation of erroneous pathways.
As shown in Figure 21, the ant colony algorithm produced the longest path length on a 40 × 40 grid map when compared to other algorithms, and the other algorithms produced the same path length. The turning angle of the traditional A*, bidirectional A*, ant colony algorithm, DQN algorithm, and the Dijkstra algorithm has risen by 135,315,360,225, and 45°, respectively. Regarding traversing the number of nodes, the traditional A* algorithm, bidirectional A* algorithm, and Dijkstra algorithm have increased by 12, 87, and 863 respectively; however, there is no need to traverse the number of nodes because the ant colony algorithm and DQN algorithm have different search mechanisms than the others. Algorithm running times rose by 0.76 s for the traditional A* algorithm, 0.47 s for the bidirectional A* method, 10.47 s for the ant colony algorithm, 9.54 s for the DQN algorithm, and 2.05 s for the Dijkstra algorithm.
The specific experimental results of each algorithm are shown in Table 4.
Map | Algorithm | Length | Turning angle | Number of traversal nodes | Algorithm run time |
20 × 20 | Traditional A* | 30.2 | 270° | 104 | 1.29 s |
Bidirectional A* | 30.2 | 270° | 96 | 1.02 s | |
Ant Colony | 31.6 | 450° | \ | 5.37 s | |
DQN | 30.2 | 270° | \ | 5.11 s | |
Dijk stra | 30.2 | 225° | 346 | 2.37 s | |
Internally improved A* | 30.2 | 135° | 61 | 0.78 s | |
30 × 30 | Traditional A* | 43.6 | 360° | 151 | 1.35 s |
Bidirectional A* | 45.4 | 315° | 162 | 1.24 s | |
Ant Colony | 43.6 | 540° | \ | 8.32 s | |
DQN | 43.6 | 225° | \ | 9.43 s | |
Dijk stra | 43.6 | 405° | 764 | 2.43 s | |
Internally improved A* | 45.4 | 225° | 206 | 1.34 s | |
40 × 40 | Traditional A* | 60.6 | 270° | 362 | 2.32 s |
Bidirectional A* | 65.2 | 450° | 437 | 2.03 s | |
Ant Colony | 68.6 | 495° | \ | 12.03 s | |
DQN | 65.4 | 360° | \ | 11.10 s | |
Dijk stra | 62.2 | 180° | 1213 | 3.61 s | |
Internally improved A* | 60.6 | 135° | 350 | 1.56 s |
In summary, this comparison demonstrates the usefulness of the internal modification of the A* algorithm in this work by demonstrating the modified algorithm's good performance in terms of path length, turning angle, number of traversal nodes, and algorithm running time.
This part is dedicated to path optimization and smoothing verification. The path generated by the internally enhanced A* algorithm serves as the initial path input and is subsequently smoothed and optimized. The comparative algorithms are the internally enhanced A* algorithm and the improved A* algorithm (with both external and internal enhancements). The turning angle and length of the path act as assessment marks. In Figure 22, the blue dotted line represents the initial path, the green dotted line represents the optimized path, and the red solid line represents the final smoothed path.
As can be seen from Table 5, based on the internal improved A* algorithm, after optimizing and smoothing the path, the path length and turning angle obtained are both shorter than the path obtained by the internal improved A* algorithm. In the 20 × 20 map, compared with the internal improved A* algorithm results, the final improved A* algorithm path length is reduced by 4.4, and the turning angle is reduced by 88.49°. In the 30 × 30 map, compared with the internal improved A* algorithm results, the final improved A* algorithm path length is reduced by 4.7, and the turning angle is reduced by 176.79°. In the 40 × 40 map, compared with the internal improved A* algorithm results, the final improved A* algorithm path length is reduced by 5.2, and the turning angle is reduced by 85.69°. It shows that the improved A* algorithm proposed in this article can effectively reduce the length of the path and the turning angle in the path, and can effectively reduce the distance and steering angle of the AGV, ensuring the smoothness of AGV driving.
Map | Algorithm | Length | Turning angle |
20 × 20 | Internally improved A* | 30.2 | 135° |
Improved A* | 25.8 | 46.51° | |
30 × 30 | Internally improved A* | 45.4 | 225° |
Improved A* | 40.7 | 48.21° | |
40 × 40 | Internally improved A* | 60.6 | 135° |
Improved A* | 55.4 | 49.31° |
This article's suggested algorithm has been verified in ROS. Using the 20 × 20 map as an example, just the essential components of the map were built during the modeling of the map SLAM technique in order to conserve computing power. Figure 23 displays the simulation results. The path is represented by the green line, open space is represented by the gray section, and obstacle boundaries are displayed by the black part.
The paths designed by the conventional A* algorithm are depicted in Figure 23(a), the internally improved A* method in Figure 23(b), and the improved A* algorithm in Figure 23(c). The three paths take the AGV 21, 15, and 9 seconds to complete, respectively. This demonstrates that the path quality predicted by the revised A* method put forth in this research is high, which can shorten the AGV's running time and increase its effectiveness.
Although the A* algorithm has the advantages of being a simple algorithm and having a fast search speed, the planned path may involve more turns and the path may not be smooth enough. In order to solve this problem, this paper improves the internal and external properties of the traditional A* algorithm. The node traversal logic of the A* algorithm is internally optimized to avoid the path passing between two obstacle vertices. Subsequently, the cost estimation function was modified to replace the traditional Euclidean distance with the diagonal distance, thereby improving the accuracy of cost prediction. This adjustment effectively reduces the number of redundant turns within the path. Then, the weight of the cost estimation function of the A* algorithm is added to give priority to the current search direction when finding a path, thereby reducing the number of nodes traversed and the number of turns compared to the traditional A* algorithm. Finally, a path optimization smoothing method based on the improved forward search optimization method and Bezier curve method is proposed. This method is used in addition to the A* algorithm to eliminate redundant turning points in the path and perform curve fitting at turns to improve the smoothness of the path.
Finally, the experimental results show that the internal modification of the A* algorithm avoids planning invalid paths, reduces the number of turns, reduces the number of traversed nodes, and shortens the search time. After external modifications to the A* algorithm, the number of turns in the path is further reduced and the length of the path is shortened.
Although the path planning method based on the improved A* algorithm proposed in this article can effectively make up for the shortcomings of the traditional A* algorithm, it still encounters some shortcomings and defects:
1) In the actual workshop environment, the location of obstacles cannot be accurately located, but dynamic obstacles may appear, and the method proposed in this article is based on the path planning method in a static obstacle environment.
2) The improved A* algorithm proposed in this article is suitable for environments with concentrated obstacles such as workshops, but is not suitable for areas with many and scattered obstacles, such as in warehousing environments.
The authors declare they have not used Artificial Intelligence (AI) tools in the creation of this article.
The authors thank the anonymous reviewers for their valuable comments. This work was supported by high level Project of Shihezi University (No. RCZK2021B16); The high-level project led by Professor Baoqin Wen at Shihezi University (No. RCZK202310).
The authors declare there is no conflict of interest
[1] | M. Binkley et al., "Defining Twenty-First Century Skills BT - Assessment and Teaching of 21st Century Skills, " P. Griffin, B. McGaw, and E. Care, Eds. Dordrecht: Springer Netherlands, 2012, pp. 17–66. |
[2] | Harman K, Bich NTN (2010) Reforming Teaching and Learning in Vietnam's Higher Education System BT - Reforming Higher Education in Vietnam: Challenges and Priorities. In: Harman G, Hayden M, Nghi PT (eds). Springer Netherlands, Dordrecht, pp 65–86 |
[3] |
Pakpour AH, Zeidi IM, Emamjomeh MM, et al (2014) Household waste behaviours among a community sample in Iran: An application of the theory of planned behaviour. Waste Manag 34: 980–986. https://doi.org/https://doi.org/10.1016/j.wasman.2013.10.028 doi: 10.1016/j.wasman.2013.10.028
![]() |
[4] | Peraturan Presiden Indonesia, Perpres No 83/2018. 2018. |
[5] |
Sugiyono A, Adiarso (2021) Development of Natural Gas Infrastructure to Enhance National Energy Security in Indonesia. IOP Conf Ser Mater Sci Eng 1053: 12099. https://doi.org/10.1088/1757-899x/1053/1/012099 doi: 10.1088/1757-899x/1053/1/012099
![]() |
[6] | Erahman QF, Purwanto WW (2021) Energy Security: A Case Study of Indonesia BT - Energy and Environmental Security in Developing Countries. In: Asif M (ed). Springer International Publishing, Cham, pp 49–74 |
[7] | Kumara INS, Ariastina WG, Sukerayasa IW, Giriantari IAD (2014) On the potential and progress of renewable electricity generation in Bali. In: 2014 6th International Conference on Information Technology and Electrical Engineering (ICITEE). pp 1–6 |
[8] |
Yana S, Nizar M, Irhamni, Mulyati D (2022) Biomass waste as a renewable energy in developing bio-based economies in Indonesia: A review. Renew Sustain Energy Rev 160: 112268. https://doi.org/https://doi.org/10.1016/j.rser.2022.112268 doi: 10.1016/j.rser.2022.112268
![]() |
[9] |
Sharvini SR, Noor ZZ, Chong CS, et al (2018) Energy consumption trends and their linkages with renewable energy policies in East and Southeast Asian countries: Challenges and opportunities. Sustain Environ Res 28: 257–266. https://doi.org/https://doi.org/10.1016/j.serj.2018.08.006 doi: 10.1016/j.serj.2018.08.006
![]() |
[10] | Pambudi NA, Firdaus RA, Rizkiana R, et al (2023) Renewable Energy in Indonesia: Current Status, Potential, and Future Development. Sustainability 15 |
[11] | Soonmin H, Lomi A, Okoroigwe EC, Urrego LR (2019) Investigation of Solar Energy: The Case Study in. 9: |
[12] |
Anitha K, Verchot L V, Joseph S, et al (2015) A review of forest and tree plantation biomass equations in Indonesia. Ann For Sci 72: 981–997. https://doi.org/10.1007/s13595-015-0507-4 doi: 10.1007/s13595-015-0507-4
![]() |
[13] |
Afifah AS, Suryawan IWK, Sarwono A (2020) Microalgae production using photo-bioreactor with intermittent aeration for municipal wastewater substrate and nutrient removal. Commun Sci Technol 5: 107–111. https://doi.org/10.21924/cst.5.2.2020.200 doi: 10.21924/cst.5.2.2020.200
![]() |
[14] | Sari MM, Inoue T, Harryes RK, et al (2022) Potential of Recycle Marine Debris in Pluit Emplacement, Jakarta to Achieve Sustainable Reduction of Marine Waste Generation. Int J Sustain Dev Plan 17: 119–125 |
[15] |
Malico I, Nepomuceno Pereira R, Gonçalves AC, Sousa AMO (2019) Current status and future perspectives for energy production from solid biomass in the European industry. Renew Sustain Energy Rev 112: 960–977. https://doi.org/https://doi.org/10.1016/j.rser.2019.06.022 doi: 10.1016/j.rser.2019.06.022
![]() |
[16] |
Sirohi R, Kumar Gaur V, Kumar Pandey A, et al (2021) Harnessing fruit waste for poly-3-hydroxybutyrate production: A review. Bioresour Technol 326: 124734. https://doi.org/https://doi.org/10.1016/j.biortech.2021.124734 doi: 10.1016/j.biortech.2021.124734
![]() |
[17] |
Amen R, Hameed J, Albashar G, et al (2021) Modelling the higher heating value of municipal solid waste for assessment of waste-to-energy potential: A sustainable case study. J Clean Prod 287: 125575. https://doi.org/https://doi.org/10.1016/j.jclepro.2020.125575 doi: 10.1016/j.jclepro.2020.125575
![]() |
[18] |
Ali Shah SA, Longsheng C, Solangi YA, et al (2021) Energy trilemma based prioritization of waste-to-energy technologies: Implications for post-COVID-19 green economic recovery in Pakistan. J Clean Prod 284: 124729. https://doi.org/https://doi.org/10.1016/j.jclepro.2020.124729 doi: 10.1016/j.jclepro.2020.124729
![]() |
[19] |
Jakobsson C, Fujii S, Gä rling T (2000) Determinants of private car users' acceptance of road pricing. Transp Policy 7: 153–158. https://doi.org/https://doi.org/10.1016/S0967-070X(00)00005-6 doi: 10.1016/S0967-070X(00)00005-6
![]() |
[20] |
Mills B, Schleich J (2010) What's driving energy efficient appliance label awareness and purchase propensity? Energy Policy 38: 814–825. https://doi.org/https://doi.org/10.1016/j.enpol.2009.10.028 doi: 10.1016/j.enpol.2009.10.028
![]() |
[21] |
Achillas C, Vlachokostas C, Moussiopoulos N, et al (2011) Social acceptance for the development of a waste-to-energy plant in an urban area. Resour Conserv Recycl 55: 857–863. https://doi.org/https://doi.org/10.1016/j.resconrec.2011.04.012 doi: 10.1016/j.resconrec.2011.04.012
![]() |
[22] |
Upreti BR, van der Horst D (2004) National renewable energy policy and local opposition in the UK: the failed development of a biomass electricity plant. Biomass Bioenergy 26: 61–69. https://doi.org/https://doi.org/10.1016/S0961-9534(03)00099-0 doi: 10.1016/S0961-9534(03)00099-0
![]() |
[23] |
Baxter J, Ho Y, Rollins Y, Maclaren V (2016) Attitudes toward waste to energy facilities and impacts on diversion in Ontario, Canada. Waste Manag 50: 75–85. https://doi.org/https://doi.org/10.1016/j.wasman.2016.02.017 doi: 10.1016/j.wasman.2016.02.017
![]() |
[24] |
He J, Lin B (2019) Assessment of waste incineration power with considerations of subsidies and emissions in China. Energy Policy 126: 190–199. https://doi.org/https://doi.org/10.1016/j.enpol.2018.11.025 doi: 10.1016/j.enpol.2018.11.025
![]() |
[25] |
Bondes M, Johnson T (2017) Beyond Localized Environmental Contention: Horizontal and Vertical Diffusion in a Chinese Anti-Incinerator Campaign. J Contemp China 26: 504–520. https://doi.org/10.1080/10670564.2017.1275079 doi: 10.1080/10670564.2017.1275079
![]() |
[26] |
Damayanti P, Moersidik SS, Haryanto JT (2021) Waste to Energy in Sunter, Jakarta, Indonesia: Plans and Challenges. IOP Conf Ser Earth Environ Sci 940: 012033. https://doi.org/10.1088/1755-1315/940/1/012033 doi: 10.1088/1755-1315/940/1/012033
![]() |
[27] |
Mulyadin R M, Ariawan K, Iqbal M (2018)Conflict of waste management in DKI Jakarta and its recomended solutions. J Analisis Kebijakan Kehutanan 15: 179–191. https://doi.org/10.20886/jakk.2018.15.2.179-191 doi: 10.20886/jakk.2018.15.2.179-191
![]() |
[28] |
Sagala G, Kristanto GA, Kusuma MA, Rizki S (2018) Assessment of municipal solid waste as refuse derived fuel in the cement industry. Int J Adv Sci Eng Inf Technol 8: 1062–1070. https://doi.org/10.18517/ijaseit.8.4.3469 doi: 10.18517/ijaseit.8.4.3469
![]() |
[29] | Guo M, Nowakowska-Grunt J, Gorbanyov V, Egorova M (2020) Green Technology and Sustainable Development: Assessment and Green Growth Frameworks. Sustain. 12 |
[30] |
Haghani M, Bliemer MCJ, Rose JM, et al (2021) Hypothetical bias in stated choice experiments: Part I. Macro-scale analysis of literature and integrative synthesis of empirical evidence from applied economics, experimental psychology and neuroimaging. J Choice Model 41: 100309. https://doi.org/https://doi.org/10.1016/j.jocm.2021.100309 doi: 10.1016/j.jocm.2021.100309
![]() |
[31] |
Rahaman MM, Iqbal MH (2021) Willingness-to-pay for improved cyclone early warning services across coastal Bangladesh: Application of choice experiment. Int J Disaster Risk Reduct 61: 102344. https://doi.org/https://doi.org/10.1016/j.ijdrr.2021.102344 doi: 10.1016/j.ijdrr.2021.102344
![]() |
[32] | Mazzocchi C, Orsi L, Sali G (2021) Consumers' Attitudes for Sustainable Mountain Cheese. Sustain. 13 |
[33] | Medeiros G, Florindo T, Talamini E, et al (2020) Optimising Tree Plantation Land Use in Brazil by Analysing Trade-Offs between Economic and Environmental Factors Using Multi-Objective Programming. For. 11 |
[34] |
Grilli G, Tyllianakis E, Luisetti T, et al (2021) Prospective tourist preferences for sustainable tourism development in Small Island Developing States. Tour Manag 82: 104178. https://doi.org/https://doi.org/10.1016/j.tourman.2020.104178 doi: 10.1016/j.tourman.2020.104178
![]() |
[35] |
Tomić T, Schneider DR (2020) Circular economy in waste management – Socio-economic effect of changes in waste management system structure. J Environ Manage 267: 110564. https://doi.org/https://doi.org/10.1016/j.jenvman.2020.110564 doi: 10.1016/j.jenvman.2020.110564
![]() |
[36] |
Khan AH, López-Maldonado EA, Alam SS, et al (2022) Municipal solid waste generation and the current state of waste-to-energy potential: State of art review. Energy Convers Manag 267: 115905. https://doi.org/https://doi.org/10.1016/j.enconman.2022.115905 doi: 10.1016/j.enconman.2022.115905
![]() |
[37] |
Iqbal A, Liu X, Chen G-H (2020) Municipal solid waste: Review of best practices in application of life cycle assessment and sustainable management techniques. Sci Total Environ 729: 138622. https://doi.org/https://doi.org/10.1016/j.scitotenv.2020.138622 doi: 10.1016/j.scitotenv.2020.138622
![]() |
[38] |
Istrate I-R, Iribarren D, Gálvez-Martos J-L, Dufour J (2020) Review of life-cycle environmental consequences of waste-to-energy solutions on the municipal solid waste management system. Resour Conserv Recycl 157: 104778. https://doi.org/https://doi.org/10.1016/j.resconrec.2020.104778 doi: 10.1016/j.resconrec.2020.104778
![]() |
[39] |
Al-Shetwi AQ (2022) Sustainable development of renewable energy integrated power sector: Trends, environmental impacts, and recent challenges. Sci Total Environ 822: 153645. https://doi.org/https://doi.org/10.1016/j.scitotenv.2022.153645 doi: 10.1016/j.scitotenv.2022.153645
![]() |
[40] |
Gutberlet J, Sorroche S, Martins Baeder A, et al (2021) Waste Pickers and Their Practices of Insurgency and Environmental Stewardship. J Environ Dev 30: 369–394. https://doi.org/10.1177/10704965211055328 doi: 10.1177/10704965211055328
![]() |
[41] |
Mö slinger M, Ulpiani G, Vetters N (2023) Circular economy and waste management to empower a climate-neutral urban future. J Clean Prod 421: 138454. https://doi.org/https://doi.org/10.1016/j.jclepro.2023.138454 doi: 10.1016/j.jclepro.2023.138454
![]() |
[42] | Nie P, Dahanayake KC, Sumanarathna N (2023) Exploring UAE's transition towards circular economy through construction and demolition waste management in the pre-construction stage–A case study approach. Smart Sustain Built Environ ahead-of-p: https://doi.org/10.1108/SASBE-06-2022-0115 |
[43] |
Suryawan IWK, Lee C-H (2023a) Citizens' willingness to pay for adaptive municipal solid waste management services in Jakarta, Indonesia. Sustain Cities Soc 97. https://doi.org/https://doi.org/10.1016/j.scs.2023.104765 doi: 10.1016/j.scs.2023.104765
![]() |
[44] | Montorsi L, Milani M, Venturelli M (2018) Economic assessment of an integrated waste to energy system for an urban sewage treatment plant: A numerical approach Energy, 158: 105-110. |
[45] |
Malinauskaite J, Jouhara H, Czajczyńska D, et al (2017) Municipal solid waste management and waste-to-energy in the context of a circular economy and energy recycling in Europe. Energy 141: 2013–2044. https://doi.org/https://doi.org/10.1016/j.energy.2017.11.128 doi: 10.1016/j.energy.2017.11.128
![]() |
[46] | Suryawan IWK, Septiariva IY, Fauziah EN, et al (2022) Municipal Solid Waste to Energy : Palletization of Paper and Garden Waste into Refuse Derived Fuel. J Ecol Eng 23: 64–74 |
[47] |
Tozlu A, Ö zahi E, Abuşoğlu A (2016) Waste to energy technologies for municipal solid waste management in Gaziantep. Renew Sustain Energy Rev 54: 809–815. https://doi.org/https://doi.org/10.1016/j.rser.2015.10.097 doi: 10.1016/j.rser.2015.10.097
![]() |
[48] |
Duan Z, Kjeldsen P, Scheutz C (2021) Trace gas composition in landfill gas at Danish landfills receiving low-organic waste. Waste Manag 122: 113–123. https://doi.org/https://doi.org/10.1016/j.wasman.2021.01.001 doi: 10.1016/j.wasman.2021.01.001
![]() |
[49] |
Fetanat A, Mofid H, Mehrannia M, Shafipour G (2019) Informing energy justice based decision-making framework for waste-to-energy technologies selection in sustainable waste management: A case of Iran. J Clean Prod 228: 1377–1390. https://doi.org/https://doi.org/10.1016/j.jclepro.2019.04.215 doi: 10.1016/j.jclepro.2019.04.215
![]() |
[50] |
Huang GC-L, Chen R-Y (2021) Injustices in phasing out nuclear power?: Exploring limited public participation and transparency in Taiwan's transition away from nuclear energy. Energy Res Soc Sci 71: 101808. https://doi.org/https://doi.org/10.1016/j.erss.2020.101808 doi: 10.1016/j.erss.2020.101808
![]() |
[51] | Badan Pusat Statistik provinsi DKI Jakarta, "Provinsi DKI Jakarta Dalam Angka 2021, " Provinsi DKI Jakarta Dalam Angka 2021, 2021. |
[52] |
Suryawan IWK, Lee C-H (2023) Community preferences in carbon reduction: Unveiling the importance of adaptive capacity for solid waste management. Ecol Indic 157: 111226. https://doi.org/https://doi.org/10.1016/j.ecolind.2023.111226 doi: 10.1016/j.ecolind.2023.111226
![]() |
[53] | Suryawan IWK, Septiariva IY, Sari MM, et al (2023) Acceptance of Waste to Energy (WtE) Technology by Local Residents of Jakarta City, Indonesia to Achieve Sustainable Clean and Environmentally Friendly Energy. J Sustain Dev Energy, Water Environ Syst 11: 1004 |
[54] | Shipe ME, Deppen SA, Farjah F, Grogan EL (2019) Developing prediction models for clinical use using logistic regression: an overview. J Thorac Dis 11: S574–S584. https://doi.org/10.21037/jtd.2019.01.25 |
[55] |
Li W, Long R, Chen H, et al (2020) Willingness to pay for hydrogen fuel cell electric vehicles in China: A choice experiment analysis. Int J Hydrogen Energy 45: 34346–34353. https://doi.org/https://doi.org/10.1016/j.ijhydene.2020.01.046 doi: 10.1016/j.ijhydene.2020.01.046
![]() |
[56] |
Crouch GI, Del Chiappa G, Perdue RR (2019) International convention tourism: A choice modelling experiment of host city competition. Tour Manag 71: 530–542. https://doi.org/https://doi.org/10.1016/j.tourman.2018.10.002 doi: 10.1016/j.tourman.2018.10.002
![]() |
[57] |
Deliormanlı AH (2012) Cerchar abrasivity index (CAI) and its relation to strength and abrasion test methods for marble stones. Constr Build Mater 30: 16–21. https://doi.org/https://doi.org/10.1016/j.conbuildmat.2011.11.023 doi: 10.1016/j.conbuildmat.2011.11.023
![]() |
[58] |
McDermott R, O'Dell C (2001) Overcoming cultural barriers to sharing knowledge. J Knowl Manag 5: 76–85. https://doi.org/10.1108/13673270110384428 doi: 10.1108/13673270110384428
![]() |
[59] |
Iorfa SK, Ottu IFA, Oguntayo R, et al (2020) COVID-19 Knowledge, Risk Perception, and Precautionary Behavior Among Nigerians: A Moderated Mediation Approach. Front Psychol 11: 1–10. https://doi.org/10.3389/fpsyg.2020.566773 doi: 10.3389/fpsyg.2020.566773
![]() |
[60] |
Gubbels J, van der Put CE, Assink M (2019) Risk Factors for School Absenteeism and Dropout: A Meta-Analytic Review. J Youth Adolesc 48: 1637–1667. https://doi.org/10.1007/s10964-019-01072-5 doi: 10.1007/s10964-019-01072-5
![]() |
[61] |
Ulhasanah N, Goto N (2018) Assessment of citizens' environmental behavior toward municipal solid waste management for a better and appropriate system in Indonesia: a case study of Padang City. J Mater Cycles Waste Manag 20: 1257–1272. https://doi.org/10.1007/s10163-017-0691-4 doi: 10.1007/s10163-017-0691-4
![]() |
[62] |
Singh A, Sushil (2021) Integrated approach for finding the causal effect of waste management over sustainability in the organization. Benchmarking An Int J 28: 3040–3073. https://doi.org/10.1108/BIJ-08-2020-0419 doi: 10.1108/BIJ-08-2020-0419
![]() |
[63] | Nurany F, Ismail I, Ferdaus Noor Aulady M, et al (2020) Article Review: The Policy Implementation of Waste to Energy Power Plant – Pilot Project in Surabaya, Indonesia. E3S Web Conf 190: |
[64] |
Mustia DI, Edy S, Nurul A (2021) Analysis of waste composition as a source of refuse-derived fuel in Cilacap. IOP Conf Ser Earth Environ Sci 896: 12063. https://doi.org/10.1088/1755-1315/896/1/012063 doi: 10.1088/1755-1315/896/1/012063
![]() |
[65] | Rachman SA, Hamdi M, Djaenuri A, Sartika I (2020) Model of Public Policy Implementation for Refused Derived Fuel (RDF) Waste Management in Cilacap Regency. Int J Sci Soc 2. https://doi.org/10.200609/ijsoc.v2i4.239 |
[66] |
Siregar SRH, Saragih BR, Surjosatyo A (2018) Evaluation of Waste Energy Conversion Technology using Analitycal Hierarchy Process in Bantargebang Landfill, Indonesia. E3S Web Conf 67: 1–5. https://doi.org/10.1051/e3sconf/20186702012 doi: 10.1051/e3sconf/20186702012
![]() |
[67] |
Kristanto GA, Koven W (2019) Estimating greenhouse gas emissions from municipal solid waste management in Depok, Indonesia. City Environ Interact 4: 100027. https://doi.org/https://doi.org/10.1016/j.cacint.2020.100027 doi: 10.1016/j.cacint.2020.100027
![]() |
[68] | Legino S, Arianto R, Pasra N (2019) The attainment of 100 percent electrification ratio in the archipelago of Indonesia by people way electricity initiative. J Phys Conf Ser 1282. https://doi.org/10.1088/1742-6596/1282/1/012057 |
[69] |
Legino S, Hidayawanti R, Putra IS, Pribadi A (2019) Reducing coal consumption by people empowerment using local waste processing unit. J Phys Conf Ser 1217: 12028. https://doi.org/10.1088/1742-6596/1217/1/012028 doi: 10.1088/1742-6596/1217/1/012028
![]() |
[70] | Brunner IMIM, Norhidayat A, Brunner SM (2021) Processing of Organic Waste and Biomass Waste with Waste Processing Technology at the Source. VI: 2085–2095. https://doi.org/10.32672/jse.v6i3.3120 |
[71] |
Nasruddin, Idrus Alhamid M, Daud Y, et al (2016) Potential of geothermal energy for electricity generation in Indonesia: A review. Renew Sustain Energy Rev 53: 733–740. https://doi.org/https://doi.org/10.1016/j.rser.2015.09.032 doi: 10.1016/j.rser.2015.09.032
![]() |
[72] |
Saxinger G, Krasnoshtanova NE, Illmeier G (2018) In limbo between state and corporate responsibility: Transport infrastructure in the oil village Verkhnemarkovo, Irkutskaya Oblast in Russia. IOP Conf Ser Earth Environ Sci 190: 12062. https://doi.org/10.1088/1755-1315/190/1/012062 doi: 10.1088/1755-1315/190/1/012062
![]() |
[73] |
Gupta D, Garg A (2020) Sustainable development and carbon neutrality: Integrated assessment of transport transitions in India. Transp Res Part D Transp Environ 85: 102474. https://doi.org/https://doi.org/10.1016/j.trd.2020.102474 doi: 10.1016/j.trd.2020.102474
![]() |
[74] |
Persyn D, Díaz-Lanchas J, Barbero J (2022) Estimating road transport costs between and within European Union regions. Transp Policy 124: 33–42. https://doi.org/https://doi.org/10.1016/j.tranpol.2020.04.006 doi: 10.1016/j.tranpol.2020.04.006
![]() |
[75] |
Chu Van T, Ramirez J, Rainey T, et al (2019) Global impacts of recent IMO regulations on marine fuel oil refining processes and ship emissions. Transp Res Part D Transp Environ 70: 123–134. https://doi.org/https://doi.org/10.1016/j.trd.2019.04.001 doi: 10.1016/j.trd.2019.04.001
![]() |
[76] |
Marafi A, Albazzaz H, Rana MS (2019) Hydroprocessing of heavy residual oil: Opportunities and challenges. Catal Today 329: 125–134. https://doi.org/https://doi.org/10.1016/j.cattod.2018.10.067 doi: 10.1016/j.cattod.2018.10.067
![]() |
[77] |
Gabdulkhakov RR, Rudko VA, Pyagay IN (2022) Methods for modifying needle coke raw materials by introducing additives of various origin (review). Fuel 310: 122265. https://doi.org/https://doi.org/10.1016/j.fuel.2021.122265 doi: 10.1016/j.fuel.2021.122265
![]() |
[78] |
Mbazima SJ, Masekameni MD, Mmereki D (2022) Waste-to-energy in a developing country: The state of landfill gas to energy in the Republic of South Africa. Energy Explor Exploit 40: 1287–1312. https://doi.org/10.1177/01445987221084376 doi: 10.1177/01445987221084376
![]() |
[79] | Palaniandy P, Aziz HA, Wang LK, et al (2022) Sanitary Landfill Types and Design BT - Solid Waste Engineering and Management: Volume 2. In: Wang LK, Wang M-HS, Hung Y-T (eds). Springer International Publishing, Cham, pp 543–597 |
[80] | Roswulandari A, Daerobi A, Gravitiani E (2019) Waste to Energy (WTE) Putri Cempo As Urban Innovation: A Financial Analysis. 8th International Conference on Sustainable Environment and Architecture. https://doi.org/10.2991/senvar-18.2019.25 |
[81] |
Sunarto, Sulistyaningsih T (2018) Integrated sustainable waste management in Malang City, East Java, Indonesia. AIP Conf Proc 1977: 30043. https://doi.org/10.1063/1.5042963 doi: 10.1063/1.5042963
![]() |
[82] | Prasetya DA, Sanusi A, Chandrarin G, et al (2019) Small and Medium Enterprises Problem and Potential Solutions for Waste Management. J Southwest Jiaotong Univ 54. https://doi.org/10.35741/issn.0258-2724.54.6.21 |
[83] | Prayitno G, Hakim AN, Meidiana C (2020) Community Participation on the Self Help Group of Methane Gas (Biogas) Management as Renewable Energy in Indonesia. Int J Energy Econ Policy 11: 200–211 |
[84] |
Purmessur B, Surroop D (2019) Power generation using landfill gas generated from new cell at the existing landfill site. J Environ Chem Eng 7: 103060. https://doi.org/https://doi.org/10.1016/j.jece.2019.103060 doi: 10.1016/j.jece.2019.103060
![]() |
[85] | USEPA, "Bioreactors, " 2018. https://archive.epa.gov/epawaste/nonhaz/municipal/web/html/bioreactors.html. (accessed Apr. 25, 2022). |
[86] | Grossule V, Morello L, Cossu R, Lavagnolo M (2018) BIOREACTOR LANDFILLS: COMPARISON AND KINETICS OF THE DIFFERENT SYSTEMS. Detritus In Press: 1. https://doi.org/10.31025/2611-4135/2018.13703 |
[87] | Lin C-Y, Chai WS, Lay C-H, et al (2021) Optimization of Hydrolysis-Acidogenesis Phase of Swine Manure for Biogas Production Using Two-Stage Anaerobic Fermentation. Process. 9 |
[88] |
Kumarasiri B, Dissanayake P (2021) Barriers to implementing waste-to-energy projects in Sri Lanka: a PESTEL analysis. Built Environ Proj Asset Manag 11: 544–558. https://doi.org/10.1108/BEPAM-03-2020-0051 doi: 10.1108/BEPAM-03-2020-0051
![]() |
[89] | Panepinto D, Zanetti M (2021) Technical and Environmental Comparison among Different Municipal Solid Waste Management Scenarios. Sustain. 13 |
[90] |
Sütterlin B, Siegrist M (2017) Public acceptance of renewable energy technologies from an abstract versus concrete perspective and the positive imagery of solar power. Energy Policy 106: 356–366. https://doi.org/https://doi.org/10.1016/j.enpol.2017.03.061 doi: 10.1016/j.enpol.2017.03.061
![]() |
[91] | Gayatri SU (2019) ANALISIS JEJARING KEBIJAKAN DALAM PENGELOLAAN SAMPAH MENJADI ENERGI LISTRIK DI DKI JAKARTA. Universitas Gadjah Mada, Yogyakarta |
[92] |
Come Zebra EI, van der Windt HJ, Nhumaio G, Faaij APC (2021) A review of hybrid renewable energy systems in mini-grids for off-grid electrification in developing countries. Renew Sustain Energy Rev 144: 111036. https://doi.org/https://doi.org/10.1016/j.rser.2021.111036 doi: 10.1016/j.rser.2021.111036
![]() |
[93] |
Carley S, Konisky DM (2020) The justice and equity implications of the clean energy transition. Nat Energy 5: 569–577. https://doi.org/10.1038/s41560-020-0641-6 doi: 10.1038/s41560-020-0641-6
![]() |
[94] |
Hoang AT, Sandro Nižetić, Olcer AI, et al (2021) Impacts of COVID-19 pandemic on the global energy system and the shift progress to renewable energy: Opportunities, challenges, and policy implications. Energy Policy 154: 112322. https://doi.org/https://doi.org/10.1016/j.enpol.2021.112322 doi: 10.1016/j.enpol.2021.112322
![]() |
[95] |
Koengkan M, Poveda YE, Fuinhas JA (2020) Globalisation as a motor of renewable energy development in Latin America countries. GeoJournal 85: 1591–1602. https://doi.org/10.1007/s10708-019-10042-0 doi: 10.1007/s10708-019-10042-0
![]() |
[96] |
Sari MM, Suryawan IWK, Septiariva IY (2023) Processing of Biodegradable Waste from Ceremonial Activities in Bali with Black Soldier Fly (BSF) Larvae. J Multidiscip Appl Nat Sci 3: 138–148. https://doi.org/10.47352/jmans.2774-3047.175 doi: 10.47352/jmans.2774-3047.175
![]() |
1. | Junpeng Zhang, Zhiyong Ma, Lidi Quan, 2024, Research on Path Planning for Dense Storage Systems Based on an Improved Orthogonal Jump Point Search Algorithm, 979-8-3503-7507-7, 417, 10.1109/MLISE62164.2024.10674348 |
h(n) | Actual cost | Number of turns | traversal nodes |
Euclidean distance | 30 | 9 | 117 |
Manhattan distance | 31.2 | 13 | 26 |
Chebyshev distance | 30 | 14 | 172 |
parameter | value |
Number of ants | 20 |
Number of iterations | 150 |
Pheromone evaporation rate | 0.5 |
pheromone factor | 1.1 |
heuristic function factor | 4 |
parameter | value |
Learning rate | 0.001 |
Discount factor | 0.995 |
Exploration rate | 0.4 |
Batch size | 64 |
Map | Algorithm | Length | Turning angle | Number of traversal nodes | Algorithm run time |
20 × 20 | Traditional A* | 30.2 | 270° | 104 | 1.29 s |
Bidirectional A* | 30.2 | 270° | 96 | 1.02 s | |
Ant Colony | 31.6 | 450° | \ | 5.37 s | |
DQN | 30.2 | 270° | \ | 5.11 s | |
Dijk stra | 30.2 | 225° | 346 | 2.37 s | |
Internally improved A* | 30.2 | 135° | 61 | 0.78 s | |
30 × 30 | Traditional A* | 43.6 | 360° | 151 | 1.35 s |
Bidirectional A* | 45.4 | 315° | 162 | 1.24 s | |
Ant Colony | 43.6 | 540° | \ | 8.32 s | |
DQN | 43.6 | 225° | \ | 9.43 s | |
Dijk stra | 43.6 | 405° | 764 | 2.43 s | |
Internally improved A* | 45.4 | 225° | 206 | 1.34 s | |
40 × 40 | Traditional A* | 60.6 | 270° | 362 | 2.32 s |
Bidirectional A* | 65.2 | 450° | 437 | 2.03 s | |
Ant Colony | 68.6 | 495° | \ | 12.03 s | |
DQN | 65.4 | 360° | \ | 11.10 s | |
Dijk stra | 62.2 | 180° | 1213 | 3.61 s | |
Internally improved A* | 60.6 | 135° | 350 | 1.56 s |
Map | Algorithm | Length | Turning angle |
20 × 20 | Internally improved A* | 30.2 | 135° |
Improved A* | 25.8 | 46.51° | |
30 × 30 | Internally improved A* | 45.4 | 225° |
Improved A* | 40.7 | 48.21° | |
40 × 40 | Internally improved A* | 60.6 | 135° |
Improved A* | 55.4 | 49.31° |
h(n) | Actual cost | Number of turns | traversal nodes |
Euclidean distance | 30 | 9 | 117 |
Manhattan distance | 31.2 | 13 | 26 |
Chebyshev distance | 30 | 14 | 172 |
parameter | value |
Number of ants | 20 |
Number of iterations | 150 |
Pheromone evaporation rate | 0.5 |
pheromone factor | 1.1 |
heuristic function factor | 4 |
parameter | value |
Learning rate | 0.001 |
Discount factor | 0.995 |
Exploration rate | 0.4 |
Batch size | 64 |
Map | Algorithm | Length | Turning angle | Number of traversal nodes | Algorithm run time |
20 × 20 | Traditional A* | 30.2 | 270° | 104 | 1.29 s |
Bidirectional A* | 30.2 | 270° | 96 | 1.02 s | |
Ant Colony | 31.6 | 450° | \ | 5.37 s | |
DQN | 30.2 | 270° | \ | 5.11 s | |
Dijk stra | 30.2 | 225° | 346 | 2.37 s | |
Internally improved A* | 30.2 | 135° | 61 | 0.78 s | |
30 × 30 | Traditional A* | 43.6 | 360° | 151 | 1.35 s |
Bidirectional A* | 45.4 | 315° | 162 | 1.24 s | |
Ant Colony | 43.6 | 540° | \ | 8.32 s | |
DQN | 43.6 | 225° | \ | 9.43 s | |
Dijk stra | 43.6 | 405° | 764 | 2.43 s | |
Internally improved A* | 45.4 | 225° | 206 | 1.34 s | |
40 × 40 | Traditional A* | 60.6 | 270° | 362 | 2.32 s |
Bidirectional A* | 65.2 | 450° | 437 | 2.03 s | |
Ant Colony | 68.6 | 495° | \ | 12.03 s | |
DQN | 65.4 | 360° | \ | 11.10 s | |
Dijk stra | 62.2 | 180° | 1213 | 3.61 s | |
Internally improved A* | 60.6 | 135° | 350 | 1.56 s |
Map | Algorithm | Length | Turning angle |
20 × 20 | Internally improved A* | 30.2 | 135° |
Improved A* | 25.8 | 46.51° | |
30 × 30 | Internally improved A* | 45.4 | 225° |
Improved A* | 40.7 | 48.21° | |
40 × 40 | Internally improved A* | 60.6 | 135° |
Improved A* | 55.4 | 49.31° |