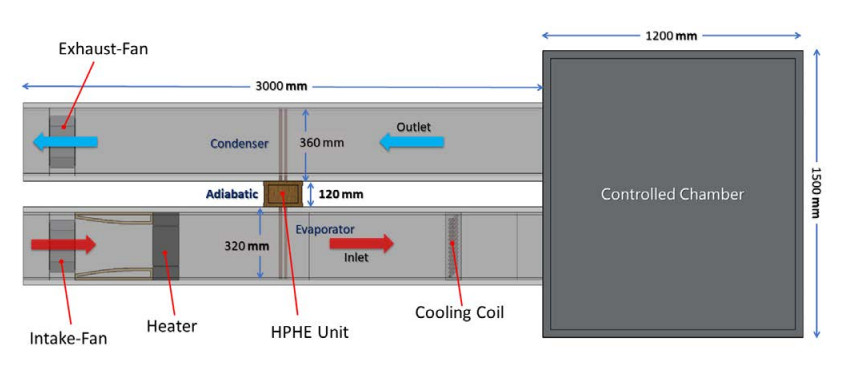
The air conditioning system is the most common way to provide comfortable room temperature for its inhabitants. However, the energy required for its operation is extremely high and cost-intensive. Therefore, a more efficient HVAC system with a lower energy consumption is desirable. The experimental results and performance analysis demonstrated that the outlet air temperature through the evaporator side of HPHE (precooling) has the potential to save some amount of energy utilizing an HVAC system equipped with HPHE. This research aims to study the performance of HPHE with the precooling process applied in commercial room HVAC system applications. This research on the utilization of HPHE for heat recovery in air conditioning systems was carried out with variations in temperature of fresh air intake ranging between 32–42 ℃. The airflow speed was set constant at 1.0 m/s. This experiment demonstrated the highest effectiveness at a value of 21%. The HPHE heat recovery analysis results show that the best heat recovery performance is achieved when the fresh air intake temperature exceeds the exhaust air leaving the room. The phenomenon was compared at a low fresh air intake temperature of 32 ℃, which succeeded in recovering 0.05 W, and when the temperature rose to 42 ℃, 0.21 W was recovered.
Citation: Fazri Amir, Hafiz Muhammad, Nasruddin A. Abdullah, Samsul Rizal, Razali Thaib, Hamdani Umar. Performance analysis of heat recovery in Heat Pipe Heat Exchanger on room air conditioning systems[J]. AIMS Energy, 2023, 11(4): 612-627. doi: 10.3934/energy.2023031
[1] | Tan Nguyen Tien, Quang Khong Vu, Vinh Nguyen Duy . Novel designs of thermoelectric generator for automotive waste heat recovery: A review. AIMS Energy, 2022, 10(4): 922-942. doi: 10.3934/energy.2022042 |
[2] | Kaovinath Appalasamy, R Mamat, Sudhakar Kumarasamy . Smart thermal management of photovoltaic systems: Innovative strategies. AIMS Energy, 2025, 13(2): 309-353. doi: 10.3934/energy.2025013 |
[3] | Junaid Akhlas, Silvia Baesso, Alberto Bertucco, Fabio Ruggeri . Coal gasification by indirect heating in a single moving bed reactor: Process development & simulation. AIMS Energy, 2015, 3(4): 635-665. doi: 10.3934/energy.2015.4.635 |
[4] | Kokou Aménuvéla Toka, Yawovi Nougbléga, Komi Apélété Amou . Optimization of hybrid photovoltaic-thermal systems integrated into buildings: Impact of bi-fluid exchangers and filling gases on the thermal and electrical performances of solar cells. AIMS Energy, 2024, 12(5): 1075-1095. doi: 10.3934/energy.2024051 |
[5] | Khaled M. Bataineh, Assem N. AL-Karasneh . Direct solar steam generation inside evacuated tube absorber. AIMS Energy, 2016, 4(6): 921-935. doi: 10.3934/energy.2016.6.921 |
[6] | Ruaa Al Mezrakchi . Investigation of various hybrid nanofluids to enhance the performance of a shell and tube heat exchanger. AIMS Energy, 2024, 12(1): 235-255. doi: 10.3934/energy.2024011 |
[7] | Xiaolong Wang, Lingning Zhang, Yuan Chang, Yang Song, Liang Wang . Numerical simulation study on heat performance and pressure loss of solar air heater with sinusoidal baffles. AIMS Energy, 2024, 12(3): 617-638. doi: 10.3934/energy.2024029 |
[8] | Jialin Song, Haoyi Zhang, Yanming Zhang, Zhongjiao Ma, Mingfei He . Research progress on industrial waste heat recycling and seasonal energy storage. AIMS Energy, 2025, 13(1): 147-187. doi: 10.3934/energy.2025006 |
[9] | Hong-Yu Pan, Chuang Sun, Xue Chen . Transient thermal characteristics of infrared window coupled radiative transfer subjected to high heat flux. AIMS Energy, 2021, 9(5): 882-898. doi: 10.3934/energy.2021041 |
[10] | Maria Ferrer, Joshua Nott, Joseph Prinke, Sofia Goodrich, Fred Massicotte, Karim Rebeiz, Steve Nesbit, Ted B. Flanagan, Andrew Craft . Evidence for hydrogen-assisted recovery of cold-worked palladium: hydrogen solubility and mechanical properties studies. AIMS Energy, 2017, 5(4): 625-635. doi: 10.3934/energy.2017.4.625 |
The air conditioning system is the most common way to provide comfortable room temperature for its inhabitants. However, the energy required for its operation is extremely high and cost-intensive. Therefore, a more efficient HVAC system with a lower energy consumption is desirable. The experimental results and performance analysis demonstrated that the outlet air temperature through the evaporator side of HPHE (precooling) has the potential to save some amount of energy utilizing an HVAC system equipped with HPHE. This research aims to study the performance of HPHE with the precooling process applied in commercial room HVAC system applications. This research on the utilization of HPHE for heat recovery in air conditioning systems was carried out with variations in temperature of fresh air intake ranging between 32–42 ℃. The airflow speed was set constant at 1.0 m/s. This experiment demonstrated the highest effectiveness at a value of 21%. The HPHE heat recovery analysis results show that the best heat recovery performance is achieved when the fresh air intake temperature exceeds the exhaust air leaving the room. The phenomenon was compared at a low fresh air intake temperature of 32 ℃, which succeeded in recovering 0.05 W, and when the temperature rose to 42 ℃, 0.21 W was recovered.
Nomenclatures: HP: Heat pipe; HPHE: Heat pipe heat exchanger; AC: Air conditioning; HVAC: Heating, ventilation, and air conditioning; AHU: AHU; FR: Filling Ratio (%); Te: Evaporator Temperature (ºC); Tc: Condenser Temperature (ºC); ΔT: Temperature difference (ºC); ε: Effectiveness (%); Tch: Chiller Temperature (ºC); Tc, r: Chamber Temperature (ºC); Tci: Condenser Input (ºC); Tco: Condenser Output (ºC); Teo: Evaporator Output-Outgoing Air (ºC); Tei: Evaporator Input-Air Inlet (ºC); R: Thermal resistance (℃/W); ∆T: Inlet and outlet air ratio (℃); m: Mass flow rate (kg/s); Cp: Fluid heat capacity (kJ/kg.℃)
Energy consumption in Heating, Ventilation and Air Conditioning (HVAC) applications is notably elevated, particularly in office spaces in subtropical and tropical climates [1]. Air conditioning (AC) is indispensable in creating a comfortable temperature environment in public spaces, including waiting rooms, stadiums and medical emergency areas [2,3]. The pursuit of comfort and air purity in buildings, including precise requirements for temperature, relative humidity and air exchange, often necessitates the continuous operation of the air handling unit (AHU). To achieve this objective, an enhanced control system is imperative in HVAC to reduce energy consumption [4]. As per Yau and Lee, controlling and restricting the AHU is crucial to prevent continuous energy consumption increases. This control is inversely related to maintaining room comfort in buildings with relatively high energy demands [5].
The total energy requirement for HVAC system operation in commercial buildings accounts for 40–60% of the total energy use [6,7]. The HVAC system serves a crucial function by efficiently distributing cool air at precise temperatures, ensuring users' comfort while also playing a critical role in facilitating the exchange of indoor air. However, it is essential to note that this air exchange process contributes significantly to most energy loss within the building [8,9,10]. Numerous endeavors have been undertaken to discover innovative methods of decreasing energy consumption in buildings while maintaining comfort and indoor air quality. One well-established approach for enhancing energy efficiency in HVAC systems involves employing new configurations of pre-existing components [11]. By implementing a more efficient system, it becomes feasible to simultaneously reduce exhaust emissions and recover heat from the exhaust air of the HVAC system. Heat recovery from HVAC system exhaust air is an energy-saving measure, enabling efficient energy utilization and substantially reducing exhaust emissions [12]. Energy savings in the HVAC system are achieved by incorporating a heat recovery system into the AHU ducting system, which effectively harnesses the exhaust air for improved efficiency [13,14].
Air conditioning systems have minimum requirements to ensure thermal comfort in conditioned rooms. However, maintaining thermal comfort in tropical climates necessitates a higher energy demand [15,16,17]. According to the ASHRAE standard, the recommendation for a comfortable indoor temperature for humans is 22–27 ºC and humidity of about 30–60% [18]. As Ahmadzadehtalatapeh and Huang Yau stated, indoor air conditioning performance achieves an appropriate level within the comfort zone when utilizing the cooling coil. It is important to note that the energy consumption of the HVAC system increases as the desired temperature decreases [19]. Energy savings can be achieved by reducing the cooling coil load or cooling system requirements by utilizing cooler and drier exhaust air. One practical approach is the recovery of exhaust air, which is an alternative for cooling the fresh air entering the system. The heat recovery from exhaust heat plays a pivotal role in significantly reducing energy consumption within HVAC systems [20,21].
Hill and Lau conducted six field studies on applying Heat Pipe Heat Exchangers (HPHE) in HVAC systems, specifically in air conditioning systems within supermarkets. The studies evaluated two basic configurations: single line and double line. The findings demonstrated a notable reduction in cooling energy consumption [22]. Wu et al. conducted a study investigating the application of Heat Pipe Heat Exchangers (HPHE) for humidity control in air conditioning systems. The research revealed that HPHE could be a viable alternative to conventional coil reheat methods, leading to energy savings while enhancing the cooling capability of cooling coils with minimal or no external energy requirements [23]. HPHE is a widely utilized method for recovering cool air in HVAC systems, among other heat transfer techniques [24,25,26,27].
HPHE plays a considerable role in various AHU fields, especially for heat transfer over a certain distance with an appropriate temperature difference. In HPHE operation of heat transfer through capillary wicking or gravitational force in the thermosyphon heat pipe [28], heat pipes (HP) excel among other passive heat transfer methods due to their ability to operate without requiring an external driving force. With remarkably high thermal conductivity in steady-state operation, heat pipes exhibit outstanding performance. The steady-state encompasses working fluid velocity, period and the temperature difference between the heat pipe's condenser and evaporator sections. Heat transfer within heat pipes transpires through the effective circuit, considering thermal resistance during the temperature change process [29]. The higher the evaporator (inlet) temperature, the smaller the thermal resistance, thus impacting HP heat transfer's high effectiveness [30]. Heat pipes are passively used in the exhaust-air-heat-recovery process, which is cheaper than other heat recovery technologies due to their high conductance potential.
HPHE plays a good role in individual heat recovery. According to Abdallah et al., if the effectiveness of HPHE fresh air temperature increases, the mass concentration increases and energy recovery is strongly influenced by the inlet air velocity and working fluid [29]. Khaled et al. showed that ambient temperature dramatically affects the technical and economic feasibility of the proposed energy recovery system. Reducing the pressure operating at an economically desirable temperature, the higher the comfort of the energy recovery system, the higher the flow rate and the lower the pressure in the air conditioning system [31]. Economic analysis shows that energy savings lower electricity consumption costs with a payback period of about three years [32,33,34,35]. Heat recovery can be made by installing HPHE in the ducting system as an air precooling medium as it passes through the cooling coil so that energy consumption for cooling can be reduced and the time needed to reach the dew point will be faster [11,36,37].
The literature study reveals that increasing the number of rows in HPHE leads to decreased outlet temperature on the evaporator side. Additionally, this increase in the number of rows enhances the effectiveness of the heat exchanger, resulting in higher energy savings [38,39,40]. During dehumidification, HPHE in the reheating process also significantly increases energy savings [23,41,42]. Previous research has consistently demonstrated the importance of utilizing HPHE in achieving energy savings within air conditioning systems.
A literature review reveals that the utilization of HPHE positively reduces energy consumption in HVAC systems. However, further development of HPHE is necessary to enhance its performance and achieve even more significant energy savings. With the growing number of new buildings and facilities, the demand for comfortable spaces is also rising, resulting in an increased need for HVAC systems. Hence, the primary objective of this research is to establish the performance standards of HPHE for commercial space HVAC system applications.
In this study, the materials employed include heat pipes arranged in 2 rows, specifically HPHE. Each row consists of 10 HP rods and straight copper heat pipe tubes. The HPs utilized have a length of 800 mm and a diameter of 10 mm, employing water as the working mass. The HPHE size includes an evaporator of 320 mm, an adiabatic side of 120 mm and a condenser side of 360 mm. The adiabatic side is tightly insulated with 120 x 200 mm dimensions, made of Polyurethane (PU) material and aluminum adhesive. The test equipment and its dimensions are shown in Figures 1 and 2. The air system (room chamber) is insulated using PU material. The heat recovery system in the air conditioning system, HPHE, is mounted on polyisocyanurate (PIR) ducting before the cooling coil. The cooling coil with 330-watt power serves to cool the room. A blower is used to channel the inlet and outlet air for distributing the air in the system, while the room to be cooled is scaled down to a 1:10 ratio of a commercial room. The HPHE (Heat Pipe Heat Exchanger) is positioned between the inlet and outlet channels, with the adiabatic side of the HPHE isolated by PU (Polyurethane) material.
The research was conducted by experimental method to determine the temperature distribution and heat recovery of straight HPHE in the air system, as shown in schematic Figure 3. HP is installed in the ducting section of inlet air and returns air. In observing the inlet and outlet air temperature distribution, a K-type thermocouple cable was used, which was connected to an Agilent 34790A data logger. Thermocouples are installed to determine the temperature of the air system. The K-type thermocouple sensor has an accuracy level of ±0.02 ºC. A total of 7 (seven) thermocouple units, each of which is installed in the fresh inlet air (Tch), an inlet of the evaporator (Te, i), an outlet of the evaporator (Te, o), air outlet cooling coil (Tcr), room chamber (Tr), an inlet of the condenser (Tc, i) and air outlet of the condenser (Tc, o). The study was conducted 5 (five) times, with the duration of data collection at 1,100 seconds each. The results obtained from the temperature distribution in the air system will be used in calculating the effectiveness of HPHE performance, thermal resistance and heat recovery.
HPHE testing is done by measuring the temperature in several parts. The bottom of the HPHE functions as an evaporator, and the top is a condenser. The air inlet at the bottom uses a blower through a heater, a heat source as a regulator of incoming air variations. The inlet air temperature varies at 32–40 ºC, and the velocity is constant at 1.0 m/s. To avoid heat loss, the evaporator and adiabatic section are isolated, and the condenser section is left open in free contact with the outside air so that the heat release can proceed properly.
The distribution temperature was determined by strategically positioning thermocouples along the fresh air inlet, exhaust air and chamber. A Proportional, Integral and Differential (PID) controller was employed to regulate the temperature of the air inlet, ensuring a constant temperature upon entering the system. Temperature measurements were taken at various points, including the ambient temperature, inlet and outlet of the heater, outlet of the HPHE evaporator, outlet of the chiller, at the controlled chamber, and inlet and outlet of the HPHE condenser. Temperature readings were recorded at intervals of 20 seconds over 1,100 seconds.
Moderate effectiveness is a very relevant parameter to describe the thermal performance of HPHE. Effectiveness is defined as the ratio of the actual heat transfer to the maximum heat transfer in the heat exchanger. It can be determined using the equation for test results as described by Sukarno et al. [43] as follows:
(1) |
Alternatively,
(2) |
The overall thermal resistance of the evaporator and condenser components depends on the conductivity of the working fluid in the wick. Another required property of the wick is compatibility with the working fluid. The thermal resistance can be measured as the temperature difference between the evaporator and condenser divided by total heat transfer. The thermal resistance equation can be considered as follows [44]:
(3) |
Heat recovery in the context of buildings and services is the capture and reuse of heat generated from existing processes, which is usually wasted. In refrigeration and air conditioning systems, wasted heat occurs in the condenser component. About 20% of the heat wasted from the condenser occurs during the superheating process and partly during the condensation process. This study calculates heat recovery at the inlet and outlet evaporator points. The heat recovery equation can be seen in the following equation:
(4) |
Air conditioning occurs in an air system with compressors, condensers, evaporators and expansion valves as its main components. The fresh air flowed from the inlet ducting, and the temperature was increased using a controllable heater; then, the air flowed through the HPHE evaporator to reduce the heat from the air before the room. From the chamber, the air flowed to the outlet and through the condenser of HPHE, the air obtained the heat and released it to the outside. The distribution temperature of these processes is the data displayed in Figure 4, parts A–E, where the inlet temperature was set at 32 ℃, 34 ℃, 36 ℃, 39 ℃ and 42 ℃, respectively.
The temperature at the initial testing stage was uniform at 30 ℃. Part A in Figure 4, using a PID Controller, The steady state at 200 seconds around 32 ℃. At this stage, there is a minimum temperature drop from the evaporator inlet side (Te, i) to the evaporator outlet side (Te, o) with an average value at a steady state of 2.01 ℃. While the heat transfer in the air chamber between before and after the condenser side is 2.0 ℃. The result shows that the evaporator side receives heat sufficient to produce vapor bubbles that can move the liquid and bubble arrangement above it. As a result, the working fluid flows from the evaporator side to the condenser side, even though it is in a relatively small amount.
Figure 4B presents a graph of the relationship between the temperature distribution at a steady state of 34 ℃ and the same period as the other stages. Before reaching a steady temperature, a fluctuating heat transfer phenomenon occurs due to the PID controller. This fluctuation occurs at each stage (A–E). The curve shows that the differential temperature between the air entering and leaving the evaporator is 2.25 ℃ and at the condenser is 1.41 ℃. While in section C the difference between the incoming and outgoing air temperatures from the evaporator is 1.43 ℃ and from the condenser is 1.35 ℃. Section D also from the evaporator is 2.14 ℃ and from the condenser is 1.68 ℃. The unbalance different temperatures between the evaporator and condenser are due to the heat loss in the overall systems. The higher the temperature inlet, the higher the temperature difference between the evaporator and condenser.
Equations 1 and 2 generate the HPHE effectiveness value based on the temperature difference between the hot and cold fluids flowing through the HPHE. The actual temperature difference in one section of the heat pipe evaporator is divided by the maximum temperature difference between the air entering one section of the heat pipe evaporator and the air entering the other section of the heat pipe condenser. However, remember that this equation only considers the temperature difference factor and not other factors, such as airflow and air pressure, which also affect the effectiveness of the HPHE. The effectiveness of heat pipe performance can be calculated based on data from the five tests. The effectiveness graph against the inlet air temperature can be seen in Figure 5:
Figure 5 depicts that the heat pipe demonstrates its lowest performance effectiveness at an inlet air temperature of 32 ℃, amounting to a 7% reduction during the initial test. In contrast, the highest performance effectiveness of the heat pipe is observed when the inlet air temperature reaches 42 ℃, resulting in a remarkable 21% effectiveness level. This observation indicates that the effectiveness of heat pipe operation escalates with higher inlet air temperatures. Remarkably, this finding aligns with multiple research studies conducted by Abdallah et al. [29], Sukarno et al. [33] and Rittidech et al. [45], all of which establish a similar trend of increasing effectiveness as the inlet temperature rises.
To achieve efficient thermal transfer, it is desirable for the thermal resistance of a heat pipe to be as low as possible. Employing Eq 3 from the preceding discussion makes it feasible to calculate the thermal resistance of the heat pipe using data obtained from the five conducted tests. The corresponding table and graph illustrating the relationship between thermal resistance and inlet air temperature are presented in Figure 6.
Based on Figure 6, it can be seen the relationship between thermal resistance to inlet air temperature. The highest thermal resistance of 139.82 ℃/W occurs when the intake air temperature is 32 ℃. The thermal resistance value drops significantly when the incoming air temperature has passed 36 ℃. The lowest thermal resistance value, 44.22 ℃/W, occurred when the inlet air temperature was 36 ℃. It is caused by the heat pipe working fluid that has not fully evaporated when the evaporator temperature is less than 36 ℃. These results align with previous research [29], where the best performance of the heat pipe in flowing fluid is when the inlet air temperature is part C. The heat pipe performance at a temperature of more than 36 ℃, there is no significant change of thermal resistance due to the ability of the heat pipe to transfer thermal from the evaporator to the condenser. The thermal resistance tends to decrease when the fresh air inlet temperature increases, and the slight thermal resistance occurs at the air inlet temperature of 36 ℃. The heat resistance is slightly constant at a temperature of more than 36 ℃ due to the ability of the heat pipe to transfer heat. This phenomenon is according to the research of Sukarno et al. [25] dan Ramos et al. [46], where more excellent heat absorption is obtained when the air inlet temperature increases, thus increasing the air inlet temperature on the evaporator side reduces the thermal resistance.
The graph below provides a visual representation of the correlation between heat recovery and the temperature of the fresh air inlet. It demonstrates how changes in the fresh air inlet temperature impact heat recovery efficiency within the system. This information is essential for understanding the relationship between these two factors and optimizing the heat recovery process in HVAC systems.
Figure 7 shows the relationship between heat recovery and inlet air temperature. The graph shows that the lowest heat recovery occurs when the inlet air temperature is 32 ℃, which is 0.05 W. Heat recovery increases significantly when the inlet air temperature reaches 36 ℃. This value demonstrates that the best heat recovery occurs when the inlet air temperature is 42 ℃, which is 0.21 W. Thus, heat pipe work's heat recovery increases with the fresh air inlet temperature. The temperature is limited to 42 ℃ due to the maximum ambient temperature in the surrounding, and in Indonesia, the temperature rarely exceeds 42 ℃. It is possible to test a temperature of more than 42 ℃, but in this experiment, we limited it to 42 ℃. The effectiveness performance analysis has been compared with research conducted by Abdallah et al. [29], Sukarno et al. [33] and Rittidech et al. [45]. On thermal resistance, the trend has been compared with the results obtained by Sukarno et al. [25] and Ramos et al. [46]. Furthermore, energy recovery analysis has been added to the narrative in the form of energy recovery refers to the process of recovering wasted heat in an HVAC. In the context of HPHE, heat recovery involves the transfer of heat from a wasted hot fluid into a cool fluid that requires heating or cooling. The higher the heat recovery, the more heat is successfully recovered and reused [47,48].
The research findings provide several critical conclusions regarding utilizing Heat Pipe Heat Exchangers (HPHE) for heat recovery in air conditioning systems. The analysis of HPHE performance effectiveness reveals that the highest effectiveness is achieved during the fifth test, where the inlet air temperature reaches 42 ℃, resulting in an effectiveness level of 21%. Notably, the effectiveness demonstrates an increasing trend as the inlet air temperature rises. Therefore, it can be inferred that the performance effectiveness of the heat pipe improves with higher inlet air temperatures.
Additionally, the analysis of HPHE thermal resistance indicates that it absorbs a substantial amount of heat, particularly when the fresh air inlet temperature increases. This behavior leads to a reduction in the thermal resistance of the evaporator at higher fresh air inlet temperatures. The minimum thermal resistance occurs at an inlet air temperature of 36 ℃.
Furthermore, the analysis demonstrates a significant increase in heat recovery as the inlet air temperature reaches 36 ℃. The optimal heat recovery is achieved when the fresh air inlet temperature is 42 ℃, resulting in a value of 0.21 W. Consequently, the active heat recovery of the heat pipe intensifies with higher fresh air inlet temperatures.
The authors declare that AI tools were not used at all stages of research in the studies carried out and presented in this article.
We would like to express our utmost gratitude to all parties who have contributed to the successful implementation of this research. This research received funding support from Lembaga Pengelola Dana Pendidikan (LPDP), managed by the Indonesian Science Fund (ISF), RISPRO/KI/B1/TKL/5/15448/2020. Furthermore, the research also received support from Universitas Syiah Kuala 370/UN11.2.1/PT.01.03/PNBP/2021 and Direktorat Riset, Teknologi, dan Pengabdian Kepada Masyarakat (DRTPM) at Universitas Syiah Kuala, through the Penelitian Disertasi Doktor (PDD), 168/E5/PG.02.00.PL/2023. We would like to acknowledge the invaluable support of the thermal laboratory at Universitas Samudra, which facilitated and contributed to this research.
The authors declare no conflict of interest.
Conceptualization, Hamdani Umar; methodology, Hamdani Umar, Razali Thaib and Nasruddin A.A.; data curation, Hafiz Muhammad and Fazri Amir.; formal analysis, Fazri Umar and Nasruddin A.A.; validation, Samsul Rizal, Hamdani Umar and Razali Thaib.; resources, Hamdani Umar and Nasruddin A.A.; writing—original draft preparation; Fazri Amir, Hafiz Muhammad and Nasrudin A.A.; writing—review and editing, Samusl Rizal, Hamdani Umar, and Razali Thaib. All authors have read and agreed to the published version of the manuscript.
[1] |
Amir F, Rizal S, Thaib R, et al. (2023) Comparison between a thermosiphon and a wick heat pipe performance with temperature difference. Jurnal Polimesin 21. http://dx.doi.org/10.30811/jpl.v21i1.3001 doi: 10.30811/jpl.v21i1.3001
![]() |
[2] |
Horr Y Al, Tashtoush B (2020) Experimental analysis of the cooling performance of a fresh air handling unit. AIMS Energy 8: 299–319. https://doi.org/10.3934/energy.2020.2.299 doi: 10.3934/energy.2020.2.299
![]() |
[3] |
Hamdani H, Sabri FS, Harapan H, et al. (2022) HVAC control systems for a negative air pressure isolation room and its performance. Sustainability 14: 11537. https://doi.org/10.3390/su141811537 doi: 10.3390/su141811537
![]() |
[4] |
Eidan AA, Najim SE, Jalil JM (2017) An experimental and a numerical investigation of HVAC system using thermosyphon heat exchangers for sub-tropical climates. Appl Therm Eng 114: 693–703. https://doi.org/10.1016/j.applthermaleng.2016.12.027 doi: 10.1016/j.applthermaleng.2016.12.027
![]() |
[5] |
Yau YH, Lee SK (2010) Feasibility study of an ice slurry-cooling coil for HVAC and R systems in a tropical building. Appl Energy 87: 2699–2711. https://doi.org/10.1016/j.apenergy.2010.02.025 doi: 10.1016/j.apenergy.2010.02.025
![]() |
[6] |
Teke A, Timur O (2014) Assessing the energy efficiency improvement potentials of HVAC systems considering economic and environmental aspects at the hospitals. Renewable Sustainable Energy Rev 33: 224–235. https://doi.org/10.1016/j.rser.2014.02.002 doi: 10.1016/j.rser.2014.02.002
![]() |
[7] |
Jouhara H, Yang J (2018) Energy efficient HVAC systems. Energy Build 179: 83–85. https://doi.org/10.1016/j.enbuild.2018.09.001 doi: 10.1016/j.enbuild.2018.09.001
![]() |
[8] |
Baudet A, Baurès E, Guegan H, et al. (2021) Indoor air quality in healthcare and care facilities: Chemical pollutants and microbiological contaminants. Atmosphere (Basel) 12. https://doi.org/10.1016/j.scitotenv.2018.06.047 doi: 10.1016/j.scitotenv.2018.06.047
![]() |
[9] |
Mata TM, Felgueiras F, Martins AA, et al. (2022) Indoor air quality in elderly centers: Pollutants emission and health effects. Environments 9: 86. https://doi.org/10.3390/environments9070086 doi: 10.3390/environments9070086
![]() |
[10] |
Hong T, Ferrando M, Luo X, et al. (2020) Modeling and analysis of heat emissions from buildings to ambient air. Appl Energy 277: 115566. https://doi.org/10.1016/j.apenergy.2020.115566 doi: 10.1016/j.apenergy.2020.115566
![]() |
[11] |
Vakiloroaya V, Samali B, Fakhar A, et al. (2014) A review of different strategies for HVAC energy saving. Energy Convers Manage 77: 738–754. https://doi.org/10.1016/j.enconman.2013.10.023 doi: 10.1016/j.enconman.2013.10.023
![]() |
[12] |
Cuce PM, Riffat S (2015) A comprehensive review of heat recovery systems for building applications. Renewable Sustainable Energy Rev 47: 665–682. https://doi.org/10.1016/j.rser.2015.03.087 doi: 10.1016/j.rser.2015.03.087
![]() |
[13] |
Cho K, Cho D, Kim T (2021) Experimental analysis of CO2 concentration changes in an apartment using a residential heat recovery ventilator. Sustainability 13: 10302. https://doi.org/10.3390/su131810302 doi: 10.3390/su131810302
![]() |
[14] |
Fernández-Seara J, Diz R, Uhía FJ, et al. (2011) Experimental analysis of an air-to-air heat recovery unit for balanced ventilation systems in residential buildings. Energy Convers Manage 52: 635–640. https://doi.org/10.1016/j.enconman.2010.07.040 doi: 10.1016/j.enconman.2010.07.040
![]() |
[15] |
Bao Y, Lee WL, Jia J (2018) Exergy analyses and modelling of a novel extra-low temperature dedicated outdoor air system. Energies 11: 1165. https://doi.org/10.3390/en11051165 doi: 10.3390/en11051165
![]() |
[16] |
Chen W, Chan M yin, Deng S, et al. (2018) A direct expansion based enhanced dehumidification air conditioning system for improved year-round indoor humidity control in hot and humid climates. Build Environ 139: 95–109. https://doi.org/10.1016/j.buildenv.2018.05.019 doi: 10.1016/j.buildenv.2018.05.019
![]() |
[17] |
Li Z, Chen W, Deng S, et al. (2006) The characteristics of space cooling load and indoor humidity control for residences in the subtropics. Build Environ 41: 1137–1147. https://doi.org/10.1016/j.buildenv.2005.05.016 doi: 10.1016/j.buildenv.2005.05.016
![]() |
[18] | ASHRAE (2000) ASHRAE Handbook: Systems and equipment. Ashrae. Available from: https://handbook.ashrae.org/Handbook.aspx. |
[19] |
Ahmadzadehtalatapeh M, HuangYau Y (2018) Design and operation optimization of an air conditioning system through simulation: An hour-by-hour simulation study. Energy Equip Syst 6: 155–165. http://10.22059/EES.2018.31534 doi: 10.22059/EES.2018.31534
![]() |
[20] |
Górecki G, Łęcki M, Gutkowski AN, et al. (2021) Experimental and numerical study of heat pipe heat exchanger with individually finned heat pipes. Energies 14: 5317. https://doi.org/10.3390/en14175317 doi: 10.3390/en14175317
![]() |
[21] | Yau YH, Ahmadzadehtalatapeh M (2014) Performance analysis of a heat pipe heat exchanger under different fluid charges. Heat Transfer Eng 35: 1539–1548. http://dx.doi.org/101080/014576322014897581 |
[22] | CH-93-16-3--Performance of Supermarket Air Conditioning Systems Equipped with Heat Pipe Heat Exchangers. Available from: https://www.techstreet.com/standards/ch-93-16-3-performance-of-supermarket-air-conditioning-systems-equipped-with-heat-pipe-heat-exchangers?product_id = 1717155. |
[23] |
Wu XP, Johnson P, Akbarzadeh A (1997) Application of heat pipe heat exchangers to humidity control in air-conditioning systems. Appl Therm Eng 17: 561–568. https://doi.org/10.1016/S1359-4311(96)00058-0 doi: 10.1016/S1359-4311(96)00058-0
![]() |
[24] |
Pakam Y, Soontornchainacksaeng T (2016) Theoretical analysis of heat recovery performance air to water of a Heat Pipe Heat Exchanger (HPHE). King Mongkut's University of Technology North Bangkok Int J Appl Sci Technol. https://doi.org/10.14416/j.ijast.2016.11.007 doi: 10.14416/j.ijast.2016.11.007
![]() |
[25] |
Sukarno R (2021) Multi-stage heat-pipe heat exchanger for improving energy efficiency of the HVAC system in a hospital operating room. Int J Low-Carbon Technol 16: 259–267. https://doi.org/10.1093/ijlct/ctaa048 doi: 10.1093/ijlct/ctaa048
![]() |
[26] |
Kusumah AS, Hakim II, Sukarno R, et al. (2019) The application of u-shape heat pipe heat exchanger to reduce relative humidity for energy conservation in heating, ventilation, and air conditioning (HVAC) systems. Int J Technol 10: 1202–1210. https://doi.org/10.14716/ijtech.v10i6.3650 doi: 10.14716/ijtech.v10i6.3650
![]() |
[27] |
Abd El-Baky MA, Mohamed MM (2007) Heat pipe heat exchanger for heat recovery in air conditioning. Appl Therm Eng 27: 795–801. https://doi.org/10.1016/j.applthermaleng.2006.10.020 doi: 10.1016/j.applthermaleng.2006.10.020
![]() |
[28] |
Yau YH, Ahmadzadehtalatapeh M (2010) A review on the application of horizontal heat pipe heat exchangers in air conditioning systems in the tropics. Appl Therm Eng 30: 77–84. https://doi.org/10.1016/j.applthermaleng.2009.07.011 doi: 10.1016/j.applthermaleng.2009.07.011
![]() |
[29] |
Abdallah AS, Yasin NJ, Ameen HA (2022) Thermal performance enhancement of heat pipe heat exchanger in the air-conditioning system by using nanofluid. Front Heat Mass Transfer 18. https://doi.org/10.5098/hmt.18.10 doi: 10.5098/hmt.18.10
![]() |
[30] |
Alizadeh A, Shafii M, Mirzahosseini A hajiseyed, et al. (2020) Experimental and simulation investigation of pulsed heat pipes in gas compressors. AIMS Energy 8: 438–454. https://doi.org/10.3934/energy.2020.3.438 doi: 10.3934/energy.2020.3.438
![]() |
[31] |
Khaled M, Ali S, Jaber H, et al. (2022) Heating/Cooling fresh air using hot/cold exhaust air of heating, ventilating, and air conditioning systems. Energies 15: 1877. https://doi.org/10.3390/en15051877 doi: 10.3390/en15051877
![]() |
[32] |
Ibnu Hakim I, Sukarno R, Putra N (2021) Utilization of U-shaped finned heat pipe heat exchanger in energy-efficient HVAC systems. Therm Sci Eng Prog 25: 100984. https://doi.org/10.1016/j.tsep.2021.100984 doi: 10.1016/j.tsep.2021.100984
![]() |
[33] |
Sukarno R, Putra N, Hakim II, et al. (2021) Utilizing heat pipe heat exchanger to reduce the energy consumption of airborne infection isolation hospital room HVAC system. J Build Eng 35: 102116. https://doi.org/10.1016/j.jobe.2020.102116 doi: 10.1016/j.jobe.2020.102116
![]() |
[34] |
Eidan AA, Alshukri MJ, Al-Fahham M, et al. (2021) Optimizing the performance of the air conditioning system using an innovative heat pipe heat exchanger. Case Stud Therm Eng 26: 101075. https://doi.org/10.1088/1757-899X/928/2/022124 doi: 10.1088/1757-899X/928/2/022124
![]() |
[35] |
Abdelaziz GB, Abdelbaky MA, Halim MA, et al. (2021) Energy saving via Heat Pipe Heat Exchanger in air conditioning applications "experimental study and economic analysis". J Build Eng 35: 102053. https://doi.org/10.1016/j.jobe.2020.102053 doi: 10.1016/j.jobe.2020.102053
![]() |
[36] |
Atmaca İ, Şenol A, Çağlar A (2022) Performance testing and optimization of a split-type air conditioner with evaporatively-cooled condenser. Eng Sci Technol 32: 101064. https://doi.org/10.1016/j.jestch.2021.09.010 doi: 10.1016/j.jestch.2021.09.010
![]() |
[37] |
Nakkaew S, Chitipalungsri T, Ahn HS, et al. (2019) Application of the heat pipe to enhance the performance of the vapor compression refrigeration system. Case Stud Therm Eng 15: 100531. https://doi.org/10.1016/j.csite.2019.100531 doi: 10.1016/j.csite.2019.100531
![]() |
[38] |
Muhammaddiyah S (2018) Experimental study of multi-fin heat pipe heat exchanger for energy efficiency in operating room air systems. Int J Technol 9: 422–429. https://doi.org/10.14716/ijtech.v9i2.1150 doi: 10.14716/ijtech.v9i2.1150
![]() |
[39] |
Jouhara H (2012) Experimental investigation of a thermosyphon based heat exchanger used in energy efficient air handling units. Energy 39: 82–89. https://doi.org/10.1016/j.energy.2011.08.054 doi: 10.1016/j.energy.2011.08.054
![]() |
[40] |
Noie-Baghban SH, Majideian GR (2000) Waste heat recovery using heat pipe heat exchanger (HPHE) for surgery rooms in hospitals. Appl Therm Eng 20: 1271–1282. https://doi.org/10.1016/S1359-4311(99)00092-7 doi: 10.1016/S1359-4311(99)00092-7
![]() |
[41] |
Monirimanesh N, Nowee SM, Khayyami S, et al. (2016) Performance enhancement of an experimental air conditioning system by using TiO2/methanol nanofluid in heat pipe heat exchangers. Heat Mass Transfer 52: 1025–1035. https://doi.org/10.1007/s00231-015-1615-2 doi: 10.1007/s00231-015-1615-2
![]() |
[42] |
Jouhara H, Meskimmon R (2018) An investigation into the use of water as a working fluid in wraparound loop heat pipe heat exchanger for applications in energy efficient HVAC systems. Energy 156: 597–605. https://doi.org/10.1016/j.energy.2018.05.134 doi: 10.1016/j.energy.2018.05.134
![]() |
[43] | Sukarno R, Putra N, Hakim II, et al. (2021) Multi-stage heat-pipe heat exchanger for improving energy efficiency of the HVAC system in a hospital operating room. 16: 259–267. http://hdl.handle.net/10453/141999 |
[44] | Schmidt P (2011) On the design of a reactor for high temperature heat storage by means of reversible chemical reactions. Energy Technol Master, 71 |
[45] |
Rittidech S, Dangeton W, Soponronnarit S (2005) Closed-ended oscillating heat-pipe (CEOHP) air-preheater for energy thrift in a dryer. Appl Energy 81: 198–208. https://doi.org/10.1016/j.apenergy.2004.06.003 doi: 10.1016/j.apenergy.2004.06.003
![]() |
[46] |
Ramos J, Chong A, Jouhara H (2016) Experimental and numerical investigation of a cross flow air-to-water heat pipe-based heat exchanger used in waste heat recovery. Int J Heat Mass Transf 102: 1267–1281. https://doi.org/10.1016/j.ijheatmasstransfer.2016.06.100 doi: 10.1016/j.ijheatmasstransfer.2016.06.100
![]() |
[47] |
Vizitiu RS, Isopescu DN, Burlacu A, et al. (2019) Energy efficient phase change materials used for an originally designed heat recovery system. Procedia Manuf 32: 496–503 https://doi.org/10.1016/j.promfg.2019.02.245 doi: 10.1016/j.promfg.2019.02.245
![]() |
[48] |
Almahmoud S, Jouhara H (2019) Experimental and theoretical investigation on a radiative flat heat pipe heat exchanger. Energy 174: 972–984. https://doi.org/10.1016/j.energy.2019.03.027 doi: 10.1016/j.energy.2019.03.027
![]() |
1. | Chen Liu, Hongting Ma, Sihan Liu, Hongkuan Zhang, Dandan Ma, Heat recovery technology and energy-saving effect analysis apply to cleanroom exhaust waste heat characteristics, 2024, 306, 03787788, 113935, 10.1016/j.enbuild.2024.113935 | |
2. | Agita Ardelia Kinanti, Hasna Labibah Febrianti, Ni Putu Savitri Mandasari Dewi, Enhancing Energy Efficiency and Ethanol Conversion through the Addition of a Heat Exchanger and Reactor in the Catalytic Dehydration Process for Ethylene Production from Ethanol, 2024, 1, 3032-7059, 108, 10.9767/jcerp.20166 | |
3. | Fazri Amir, Samsul Rizal, Razali Thaib, Hamdani Umar, Ikramullah Ikramullah, Nasruddin A. Abdullah, Teuku Azuar Rizal, Energy conservation of HVAC systems in isolation rooms using heat pipe heat exchangers, 2024, 10, 24058440, e24288, 10.1016/j.heliyon.2024.e24288 | |
4. | M. Tarazona Alvarado, J. L. Salamanca-Coy, K. Forero-Gutièrrez, L. A. Núñez, J. Pisco-Guabave, Fr. Escobar-Diaz, D. Sierra-Porta, Assessing and monitoring air quality in cities and urban areas with a portable, modular and low-cost sensor station: calibration challenges, 2024, 45, 0143-1161, 5713, 10.1080/01431161.2024.2373338 | |
5. | Weihao Zhang, Wenbin Wu, Zhuolei Chen, Meiyan Yu, Hui Dong, 2024, Energy Saving Temperature Control of UAV Nest Inverter Air Conditioning Based on Variable Air Volume and DE Algorithm, 979-8-3315-1655-0, 486, 10.1109/ICMSP64464.2024.10866090 |