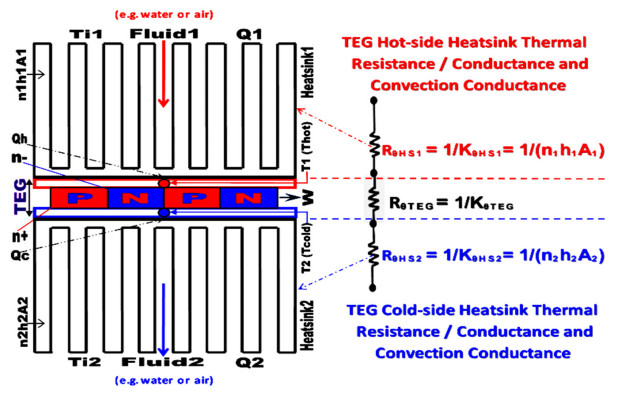
Energy sustainability is becoming paramount today with the focus being on renewable and alternative energy. This manuscript therefore embarks on clean alternative energy rooted in thermoelectricity with focus on thermoelectric generator (TEG). However, a TEG do practically needs heat-exchangers or heatsinks to properly and reliably work but heatsinks present another problem—thermal resistance, which affects a TEG power output and efficiency and thus, must be addressed. Consequently, we investigate a TEG with heatsinks model based-on dimensional analysis using Matlab and Simulink. Our research has three unique contributions. Firstly, we derived the analytical formulas for direct calculations of TEG dimensionless hot and cold sides temperature and by introducing and applying a new dimensionless parameter, the dimensionless temperature difference (DTs). Secondly, we simplified further the new TEG dimensionless hot and cold sides temperature analytical formulas to obtain simpler and simplest forms. Thirdly, we implemented a TEG with heatsinks Matlab/Simulink theoretical model, that employs the simplified dimensional analysis, in which a TEG with heatsinks parameters of interest can be simulated to variously determine the analytical, numerical and graphical results with various optimal options to opt for, before doing a practical design.
Citation: Nganyang Paul Bayendang, Mohamed Tariq Kahn, Vipin Balyan. Simplified thermoelectric generator (TEG) with heatsinks modeling and simulation using Matlab and Simulink based-on dimensional analysis[J]. AIMS Energy, 2021, 9(6): 1213-1240. doi: 10.3934/energy.2021056
[1] | Nganyang Paul Bayendang, Mohamed Tariq Kahn, Vipin Balyan . Thermoelectric Generators (TEGs) modules—Optimum electrical configurations and performance determination. AIMS Energy, 2022, 10(1): 102-130. doi: 10.3934/energy.2022007 |
[2] | Tan Nguyen Tien, Quang Khong Vu, Vinh Nguyen Duy . Novel designs of thermoelectric generator for automotive waste heat recovery: A review. AIMS Energy, 2022, 10(4): 922-942. doi: 10.3934/energy.2022042 |
[3] | Bowen Li, Qiang Cheng, Jinlin Song, Kun Zhou, Lu Lu, Zixue Luo . Thermodynamic performance of near-field electroluminescence and negative electroluminescent refrigeration systems. AIMS Energy, 2021, 9(3): 465-482. doi: 10.3934/energy.2021023 |
[4] | Kaovinath Appalasamy, R Mamat, Sudhakar Kumarasamy . Smart thermal management of photovoltaic systems: Innovative strategies. AIMS Energy, 2025, 13(2): 309-353. doi: 10.3934/energy.2025013 |
[5] | Lin Dong, Michael Grissom, Frank T. Fisher . Resonant frequency of mass-loaded membranes for vibration energy harvesting applications. AIMS Energy, 2015, 3(3): 344-359. doi: 10.3934/energy.2015.3.344 |
[6] | Ayman B. Attya, T. Hartkopf . Wind Turbines Support Techniques during Frequency Drops — Energy Utilization Comparison. AIMS Energy, 2014, 2(3): 260-275. doi: 10.3934/energy.2014.3.260 |
[7] | Lei Liu, Takeyoshi Kato, Paras Mandal, Alexey Mikhaylov, Ashraf M. Hemeida, Hiroshi Takahashi, Tomonobu Senjyu . Two cases studies of Model Predictive Control approach for hybrid Renewable Energy Systems. AIMS Energy, 2021, 9(6): 1241-1259. doi: 10.3934/energy.2021057 |
[8] | Wan Nabila Mohd Fairuz, Illani Mohd Nawi, Mohamad Radzi Ahmad, Ramani Kannan . Design analysis and simulation of serpentine-shaped piezoelectric cantilever beam for pipeline vibration-based energy harvester. AIMS Energy, 2024, 12(3): 561-599. doi: 10.3934/energy.2024027 |
[9] | Virendra Sharma, Lata Gidwani . Recognition of disturbances in hybrid power system interfaced with battery energy storage system using combined features of Stockwell transform and Hilbert transform. AIMS Energy, 2019, 7(5): 671-687. doi: 10.3934/energy.2019.5.671 |
[10] | Albert K. Awopone, Ahmed F. Zobaa . Analyses of optimum generation scenarios for sustainable power generation in Ghana. AIMS Energy, 2017, 5(2): 193-208. doi: 10.3934/energy.2017.2.193 |
Energy sustainability is becoming paramount today with the focus being on renewable and alternative energy. This manuscript therefore embarks on clean alternative energy rooted in thermoelectricity with focus on thermoelectric generator (TEG). However, a TEG do practically needs heat-exchangers or heatsinks to properly and reliably work but heatsinks present another problem—thermal resistance, which affects a TEG power output and efficiency and thus, must be addressed. Consequently, we investigate a TEG with heatsinks model based-on dimensional analysis using Matlab and Simulink. Our research has three unique contributions. Firstly, we derived the analytical formulas for direct calculations of TEG dimensionless hot and cold sides temperature and by introducing and applying a new dimensionless parameter, the dimensionless temperature difference (DTs). Secondly, we simplified further the new TEG dimensionless hot and cold sides temperature analytical formulas to obtain simpler and simplest forms. Thirdly, we implemented a TEG with heatsinks Matlab/Simulink theoretical model, that employs the simplified dimensional analysis, in which a TEG with heatsinks parameters of interest can be simulated to variously determine the analytical, numerical and graphical results with various optimal options to opt for, before doing a practical design.
Abbreviations and Symbols: a: TEG p-n junction thermocouple area in m2; A1: TEG hot side heatsink1 total surface area in m2; A2: TEG cold side heatsink2 total surface area in m2; Ab: Heatsink base area in m2; ΔT: TEG(s) temperature difference (Th – Tc) in ℃ or kelvin; DTs: TEG dimensionless temperature difference; Eff*: TEG dimensionless conversion efficiency; h1: TEG hot side heatsink1 convection coefficient; h2: TEG cold side heatsink2 convection coefficient; HFD: TEG heat flux density in W/m2; HS: Heatsinks; I: TEGs output current in ampere through the TEG; k: TEG/TEC effective thermal conductivity in W/mK; K: TEG/TEC thermal conductance in (W/K); K1: TEG hot side heatsink1 thermal conductance; K2: TEG cold side heatsink2 thermal conductance; L: TEG/TEC p-n junction thermocouple length in meter; LHS: Left Hand Side; n: TEG/TEC manufacturer p-n thermocouples amount used in a TEG/TEC; N: TEG number of modules required; Nh: TEG dimensionless convection conductance; Ni: TEG-HS dimensionless output current; Nk: TEG dimensionless thermal conductance; Nv: TEG-HS dimensionless output voltage (Vos); ɳ: TEG thermal/electrical/conversion efficiency; Ƞ1: TEG hot side heatsink1 fin efficiency; Ƞ2: TEG cold side heatsink2 fin efficiency; ɳhA: TEG convection conductance; ɳ1h1A1: TEG hot side heatsink1 convection conductance; ɳ2h2A2: TEG cold side heatsink2 convection conductance; ρ: TEG/TEC electrical resistivity in Ωm; ρe: TEG/TEC effective electrical resistivity in Ωm; Pn: TEG normalized output power; Po: TEG output power in watt, is the difference between Qh and Qc; Pos: TEG dimensionless output power, is the difference between Qh*(Qs1) and Qc*(Qs2); Qc: TEG heat emitted on its cold side in watt; Qh: TEG heat absorbed on its hot side in watt; Qs1: TEG hot side dimensionless heat absorbed (Qh*); Qs2: TEG cold side dimensionless heat released (Qc*);
Indicated in [1], South Africa has pledged its commitments to become a carbon reduced and green economic system, by considering a mixture of energy sources to secure energy sustainability. Upon ratifying the Paris agreement on climate change, renewable energy and energy efficiency frameworks as well as the regulatory policies have been developed and continuously fine-tuned taking into cognizance the current energy dynamics. In this regard, there is necessity and increasing demand for renewable energy to supplement and stabilize the unstable national grid, as well as for private use. These circumstances, warrant our research for an alternative energy rooted in thermoelectricity, with focus on basic residential energy sources and energy efficient loads. Basically, TEGs convert heat to DC power, whereas their dual thermoelectric coolers (TECs), reversibly converts DC power to cold and heat depending on the applied voltage polarity. If TEGs and TECs are properly designed, both can be relatively energy efficient and helpful for essential domestic energy use such as low-voltage DC power, lighting, heating and cooling. Theoretical frameworks and applications of both TEG and TEC were comprehensively presented in [2,3,4,5]; however, they fell short of some practical aspects—which this article seeks to advance as articulated next.
In [4,5,6,7,8,9], thermoelectricity or thermoelectric (TE) devices (TEGs and TECs), require heatsinks or heat-exchangers to physically and reliably function and maintain a working temperature difference on the TEG and TEC hot and cold sides and most significantly to discharge the internal heat resulting from Joule (Ohmic) heating cause by the current flowing through the TEG/TEC. This Ohmic heating is irreversible and will become excessive if not properly managed and consequently, will cause drop in the output/cooling powers and inefficiency (change in entropy-heat flow will change direction due to increase in the cold side junction temperature). This can as well damage the TEG and TEC as a result of over-heating exceeding the hot and cold sides maximum temperature limit—which will melt the thermoelectric devices p-n junction thermocouples solder joints. The inclusion of heatsinks as a solution to alleviate this over-heating practical limitations in thermoelectric devices, unfortunately as well add/increase the TEGs and TECs hot and cold sides thermal resistances, which then oppose the ideal heat flow, hence making the TE devices inefficient.
To circumvent this thermal resistance problem resulting from adding heatsinks/heat-exchangers, various approaches have been investigated and some are stated briefly as follows. Simplified in [6] is a dimensional analysis by converting thermal resistance to convection conductance when using TEC with heatsinks—which was researched originally in [7]; however, the presentation lacks key analytical formulas. In [8], a TEG with heatsink for waste energy harvesting was analysed and optimised as a Thevenin equivalent circuit and investigated in [9] is a dimensionless model of a TEC functioning at real heat transfer state. Examined in [10], a multi-physics simulations were conducted to examine the thermal and electrical performances of a TEG module sand-witched between hot and cold blocks, whereas in [11], a parametric thermal analysis of TEG performance was done using dimensional analysis and presented in [12] is a numerical simulation and performance analysis of a TEC based-on the lattice Boltzmann method. Studied in [13] is a multi-parameters analysis and optimization of a typical TEC using dimensional analysis. Proposed in [14] is a thermal resistance matching for TEC systems whereas examined in [15], is an optimal design of a multi-couple TEG, meanwhile [16] employed a graphical approach to design TEC systems. Demonstrated in [17] is an electron-transparent TEC using nano-particles and condensation thermometry and investigated in [18] is an optimal heat-exchanger in different automobile exhaust temperatures for TEG system using dimensional analysis. From the reviewed studies, the dimensional analysis technique, especially the unique and practical approach presented in [7] to improve TE devices efficiency when used with heatsinks, is of interest. This paper with keen focus on TEG as exemplified in Figure 1, further develops the dimensional analysis, by now employing a simplified Matlab implementation to derive novel analytical formulas to directly calculate a TEG hot and cold sides dimensionless temperature.
Our study was structured around the following points. We begin with the TEG with heatsinks applicable maths developed from [6,7] with now emphasis on the new additional analytical formulas. We derived the TEG hot and cold sides dimensionless temperature, as well as the further optimal simplifications contributed relative to the shortcomings of the formulas/approach used in [7]. In a next step, we depict the TEG with heatsinks simulator easy user interface modeled with Matlab/Simulink. The presentation of our results is followed by discussions as well as validations and lastly we conclude our study with a summary.
The relevant mathematics for a TEG with heatsinks is expressed herein and we then introduce the new dimensionless temperature difference (DTs)—which is employed to simplify the apt approach given by [7]. Dimensional analysis is a technique that enables parameters with the same unit to be normalized within a minimum and maximum value, thus making them dimensionless and easier to work with, without worrying about their dimensions or unit of measurement. Nonetheless, novel in [7] is the conversion of TEG heatsinks thermal resistance to their convection conductance. This optimization technique gets rid of the TEG heatsinks thermal resistance which are harder to work with, in favour of the TEG heatsinks fluid convection conductance which are related to the TEG heatsinks fluid temperature and physically simpler to work with. This approach is pragmatic and the mathematical analysis is articulated in what follows.
TEG with heatsinks general heat flow equations:
Herein, the TEG heat flow equations, the heatsinks thermal resistance, their corresponding thermal conductance and convection conductance relationships developed from [6] are constituted as follows:
Q1=K1(Ti1−T1)(W) | (1) |
Q2=K2(T2−Ti2)(W) | (2) |
With Q1 and Q2 being respectively the heat flow rates on the TEG heatsinks hot and cold sides, K1 and K2 are respectively the TEG hot and cold sides heatsinks thermal conductance, Ti1 and Ti2 are respectively the temperatures of the heatsinks fluid on the TEG hot and cold sides and lastly T1 and T2 are respectively the TEG hot and cold sides p-n junction temperatures. It is worthy of note that thermal resistance is the reciprocal of thermal conductance K—which corresponds to the convection conductance (ȠhA) and thus, Eqs 1 and 2 in respect of the convection conductance, can be re-written as:
Q1=Ƞ1h1A1(Ti1−T1)(W) | (3) |
Q2=Ƞ2h2A2(T2−Ti2)(W) | (4) |
With Ƞ1 being the fin efficiency of heatsink1 (on the TEG hot-side), h1 is the convection coefficient of heatsink1 and A1 is the total surface area of heatsink1. Similarly, Ƞ2 is the fin efficiency of heatsink2 (on the TEG cold-side), h2 is the convection coefficient of heatsink2 and lastly A2 is the total surface area of heatsink2.
The TEG standard ideal heat flow equations are defined as:
Qh=n[(SIT1)+(KΔT)]−0.5I2R(W) | (5) |
Qc=n[(SIT2)+(KΔT)]+0.5I2R(W) | (6) |
where Qh is the heat absorbed on the TEG hot side, n is the number of p-n junction thermocouples used in the TEG, S being the Seebeck coefficient, I being the output current from the TEG, K is the thermal conductance (computed as ak/L, with a being the area of the TEG p-n junction thermocouple, k is the TEG thermocouple p-n junction thermal conductivity and L is the TEG thermocouple p-n junction length). ΔT = T1 − T2 is the temperature difference between the TEG hot and cold sides, R = nr is the TEG module resistance, with r being the resistance of the TEG thermocouple p-n junction and Qc is the heat released on the TEG cold side. The three terms on the right side of Eqs 5 and 6 are the Seebeck, Fourier and Ohmic terms respectively; with S, K and R considered as temperature invariant. Now, taking into account the energy balance of the TEG with heatsinks system, Eqs 1, 3 and 5 are respectively equivalent now to Eqs 2, 4 and 6—which boils down to (with parameters T1, T2 and I being the unknowns):
Q1=Qh=K1(Ti1−T1)=Ƞ1h1A1(Ti1−T1)=n[(SIT1)+(KΔT)]−0.5I2R(W) | (7) |
Q2=Qc=K2(T2−Ti2)=Ƞ2h2A2(T2−Ti2)=n[(SIT2)+(KΔT)]+0.5I2R(W) | (8) |
With recognition to [7], TEG with heatsinks (HS) is optimised by defining the dimensionless parameters with regards to fluid 2 (water or air on the TEG cold side of heatsink2) and because the optimization is rendered dimensionless relative to fluid 2, fluid 2 temperature (Ti2) and convection conductance must be given initially. The following dimensionless maths is developed further from [6,7] as:
TEG-HS dimensionless thermal conductance (Nk):
This is the ratio of the thermal conductance K and the convection conductance ȠhA in fluid 2, deduced as:
Nk=K/ȠhA=(ak/l)/Ƞ2h2A2 | (9) |
TEG-HS dimensionless convection (Nh):
This is the ratio of fluid 1 and fluid 2 convection conductances, denoted as:
Nh=Ƞ1h1A1/Ƞ2h2A2 | (10) |
TEG-HS dimensionless current (Ni):
Ni=SI/K=SI/(ak/l)=ZTi2(Ts1−Ts2)/(Rr+1) | (11) |
TEG dimensionless temperatures (Ts1, Ts2, Ti and DTs):
TEG dimensionless temperatures are presented as:
T1 dimensionless temperature: Ts1=T1/Ti2 | (12) |
T2 dimensionless temperature: Ts2=T2/Ti2 | (13) |
Fluids dimensionless temperature: Ti(Tis)=Ti1/Ti2 | (14) |
Dimensionless temperature difference DTs=Ts1−Ts2=ΔT/Ti2 | (15) |
TEG-HS dimensionless heat absorbed (Qs1):
Qs1=Q1/Ƞ2h2A2Ti2 | (16) |
TEG-HS dimensionless heat released (Qs2):
Qs2=Q2/Ƞ2h2A2Ti2 | (17) |
TEG dimensionless output power (Pout* or Pos):
Pout ∗=Pout /Ƞ2h2A2Ti2 | (18) |
Pos=Pout∗=Qs1−Qs2 | (19) |
where Pout is the TEG output power (power delivered to the electrical load)
TEG dimensionless output voltage (Vos or Nv):
Nv=V/nSTi2 | (20) |
Nv=Vos=Pos/NiNk | (21) |
TEG dimensionless conversion efficiency (Eff*):
Eff∗=Pos/Qs1 | (22) |
NB: TEG conversion efficiency by default is dimensionless. The mentioned of dimensionless in front conversion efficiency is just for emphasis on the dimensionless analysis technique used.
TEG-HS dimensionless heat absorbed (Qs1) in terms of Ts1:
Qs1=Nh(Ti−Ts1) | (23) |
TEG-HS dimensionless heat released (Qs2) in terms of Ts2:
Qs2=Ts2−1 | (24) |
TEG-HS dimensionless internal electrical resistance (Rr):
Rr=RL/Rt | (25) |
where RL is the electrical load connected to the TEG output and Rt is the TEG module internal electrical resistance. NB: Rr is denoted as rr in the TEG-HS simulator in Figure 2.
As per [7], using the dimensionless Eqs 9–14, Eqs 3–6 reduce to the following two expressions (26) and (27) having five unknowns that must be found for Ts1 and Ts2 in terms of five independent dimensionless parameters of ZTi2 (dimensionless figure of merit at Ti2), Ti, Nh, Nk and Rr.
Nh(Ti−Ts1)/Nk=((ZTi2(Ts1−Ts2)Ts1)/(Rr+1))−(((ZTi2(Ts1−Ts2)2))/(2(Rr+1)2))+(Ts1−Ts2) | (26) |
(Ts2−1)/Nk=((ZTi2(Ts1−Ts2)Ts2)/(Rr+1))+(((ZTi2(Ts1−Ts2)2))/(2(Rr+1)2))+(Ts1−Ts2) | (27) |
As noticeable, Eqs 26 and 27 are cumbersome and unsolved further in [7] in terms of Ts1 and Ts2; therefore, there are no exact analytical equations to directly compute Ts1 and Ts2. Eqs 26 and 27 are awkward closed-form expressions of Ts1 and Ts2, which can only be solved by using numerical analysis; as a result, a numerical method using iterations, tables, graphs and approximations were employed by [7], as well as using a computer programme (NEDO) was further recommended. Consequently, because Eqs 26 and 27 could not be simplified further by [7], Ts1 and Ts2 could only be expressed as in Eqs 28 and 29 as functions of ZTi2, Ti, Nh, Nk and Rr for solving numerically.
Ts1=f(ZTi2,Ti,Nh,Nk,Rr) | (28) |
Ts2=f(ZTi2,Ti,Nh,Nk,Rr) | (29) |
This entire numerical process is tedious to determine Ts1 and Ts2; thus, this limitation motivated our study to seek for a direct analytical and better solution(s) which are asserted next.
We now introduce Eq 15—the dimensionless temperature difference DTs, which is used to replace Ts1 − Ts2 in Eqs 26 and 27 to give Eqs 30 and 31 as:
Nh(Ti−Ts1)/Nk=((ZTi2(DTs)Ts1)/(Rr+1))−(((ZTi2(DTs)2))/(2(Rr+1)2))+(DTs) | (30) |
(Ts2−1)/Nk=((ZTi2(DTs)Ts2)/(Rr+1))+(((ZTi2(DTs)2))/(2(Rr+1)2))+(DTs) | (31) |
As instantly apparent, Eqs 30 and 31 can respectively and directly be solved for Ts1 and Ts2 independently in terms of the five dimensionless parameters ZTi2, Ti, Nh, Nk and Rr. Now, making Ts1 and Ts2 subjects of their respective Eqs 30 and 31, we derived new analytical equations for Ts1 and Ts2 as given in Eqs 32 and 33 as:
Ts1=(NkZTi2DT2s−2NkDTsR2r−4NkDTsRr−2NkDTs+2NhTiR2r+4NhTiRr+2NhTi)/(2(Rr+1)(Nh+NhRr+DTsZTi2Nk)) | (32) |
Ts2=(NkZTi2DT2s+2NkDTsR2r+4NkDTsRr+2NkDTs+2R2r+4Rr+2)/(2(Rr+1)(Rr−DTsNkZTi2+1)) | (33) |
Furthermore, by adding Eqs 26 and 27 or Eqs 30 and 31; we can easily get rid of the nonlinear quadratic terms as shown in Eqs 34 and 35 and by re-arranging and solving for Ts1 and Ts2, we can further derive a simpler Ts1 and Ts2 novel analytical formula as shown in Eqs 36 and 37.
Nh(Ti−Ts1)/Nk+(Ts2−1)/Nk=(ZTi2DTsTs1)/(Rr+1)+(ZTi2DTsTs2)/(Rr+1)+DTs+DTs | (34) |
Nh(Ti−Ts1)/Nk−((ZTi2DTsTs1)/(Rr+1))−DTs=((ZTi2DTsTs2)/(Rr+1))+(Ts2−1)/Nk+DTs | (35) |
Equation (34) was re-arranged to give Eq 35, such that the left hand side (LHS) of Eq (35) constitutes Ts1 without Ts2 and the right hand side (RHS) of Eq 35 constitutes Ts2 without Ts1. Finally, the LHS and RHS were both solved independently by equating each to zero, to easily obtain Ts1 in terms of ZTi2, Ti, Nh, Nk, Rr and DTs (NB: now six unknown parameters) and similarly to obtain Ts2 in terms of ZTi2, Nk, Rr and DTs (NB: now four unknown parameters) to respectively give Eqs 36 and 37 expressed as:
Ts1=(NhTi−DTsNk)(Rr+1)/(Nh+NhRr+DTsNkZTi2) | (36) |
Ts2=(DTsNk+1)(Rr+1)/(Rr−DTsNkZTi2+1) | (37) |
As seen, Ti and Nh are absent in Eqs 33 and 37, meaning these two dimensionless parameters, don't directly affects Ts2 or affects Ts2 indirectly through Ts1 and DTs; thus, making these equations insightful.
Finally, we furthermore obtained the simplest optimal analytical relationship to calculate Ts1 and Ts2 by utilizing a set of optimal numerical values given in [7] as: ZTi2 = 1, Ti = 2.6, Nh = 1, Nk = 0.3, Rr = 1.7 and DTs = 0.8 and by substituting these values in Eq 35 and solving further, we obtain Eqs 38 and 39 as:
Ts1=41Ts2/49+(36/35) | (38) |
Ts2=49(Ts1−(36/35))/41 | (39) |
It should be noted that, the ZTi2 = 1, Ti = 2.6, Nh = 1, at Nk = 0.3, Rr = 1.7 and now DTs = 0.8 optimal values set are not arbitrarily chosen but specifically deduced optimal values, that are inter-linked to each other and obtained under the same specified operating conditions. Furthermore, parameters ZTi2, Ti and Nh are initially provided or can be calculated from a chosen TEG-HS operating parameters and finally the optimal combinations of Nk, Rr and now DTs, can all be established from the above specified dimensionless equations. NB: other optimal values set can be used in Eq 35 to get new Eqs 38 and 39 also.
Now, to validate our new Ts1 and Ts2 formulas, we substitute this the same chosen set of optimal values (given in [7]) of ZTi2 = 1, Ti = 2.6, Nh = 1, Nk = 0.3, Rr = 1.7 and DTs = 0.8 to finally determine, compare and verify the Ts1 and Ts2 values by using our newly derived simple, simpler and simplest analytical formulas; respectively using Eqs 32 and 33, Eqs 36 and 37 and Eqs 38 and 39 as follows:
Using the now simple formulas (Eqs 32 and 33), Ts1 and Ts2 are optimally directly computed as:
Ts1=2.1794Ts2=1.3754 |
Using the now simpler formulas (Eqs 36 and 37), Ts1 and Ts2 are optimally directly deduced as:
Ts1=2.1673Ts2=1.3610 |
As seen, both these new simple and simpler optimal solutions are approximately the same. We can then also easily verify both with Eqs 38 and 39 to get the simplest solution, by substituting Ts2 to calculate Ts1 or vice versa. We've now introduced three new analytical sets of formulas to easily compute Ts1 and Ts2 without going through the cumbersome numerical process. With Ts1 and Ts2 easily deduced, the other dimensionless parameters and ultimately all their physical dimensional parameters, can then be worked out using Eqs 1–25.
The relevant TEG with heatsinks mathematics based on dimensional analysis was articulated in Section 2 and the formulas for Ts1 and Ts2 were developed and expressed analytically in respect of the now six independent parameters ZTi2, Ti, Nk, Nh, Rr and DTs. Furthermore, Ts1 and Ts2 were optimally simplified and validated in terms of Ts1 and Ts2 using Eqs 38 and 39. As apparent, the entire numerical as well as analytical procedures could be very tedious and as well subject to errors if manually done. In view of this, a Matlab and Simulink TEG model with heatsinks on both the TEG hot and cold sides, was then implemented using the formulas asserted in Section 2. Enclosed in the simulated TEG with heatsinks model, are the followings: i) The TEG parameters analysed in Section 2, which include; S the Seebeck coefficient, 273.15 the absolute temperature in kelvin, Ti1 fluid temperature of heatsink1, Ti2 fluid temperature of heatsink2, if required the TEG configuration in series Ts and or in parallel Tp, r the TEG thermocouple p-n junction resistance, k the TEG thermocouple p-n junction thermal conductivity, Ῥ the TEG thermocouple p-n junction electrical resistivity, a the TEG thermocouple p-n junction area, L the TEG thermocouple p-n junction length and Preq the TEG total output power required. ii) The heatsinks parameters, which include; Ab the heatsink base area, n1 fins efficiency of heatsink1, h1 convection coefficient of heatsink1 fluid, A1 total area of heatsink1 with fins sides, n2 fins efficiency of heatsink2, h2 convection coefficient of heatsink2 fluid and A2 total area of heatsink2 with fins sides. All these parameters can easily be input in the model simulator and the TEG optimal parameters value computed as depicted in Figure 2.
Additionally, the TEG dimensionless parameters such as; Ni the dimensionless output current, Nk the dimensionless thermal conductance, Eff* (nth) the conversion efficiency, Pos (Ws1) the dimensionless output power, Ts1 the TEG hot-side dimensionless temperature, Ts2 the TEG cold-side dimensionless temperature and Nv the dimensionless output voltage, can all be either manually entered (as depicted in Figure 2 on the left side of the TEG with heatsinks model) or computed automatically. They're then used to finally calculate the TEG practical parameters values in SI units (as shown in Figure 2 on the right side of the TEG with heatsinks model). Some of the TEG physical parameters of interest that are computed include; Z the TEG figure of merit, n the TEG amount of p-n junction thermocouples, Qh (Q1) the TEG hot side heat absorbed, Qc (Q2) the TEG cold side heat released, Po the TEG output power, T1 (Th) the TEG hot side temperature, T2 (Tc) the TEG cold side temperature, RR (Rt) the TEG internal resistance, Vo the TEG output voltage, Voc is the TEG ideal output voltage, I the TEG output current, N the total amount of TEG modules required, DT or ΔT the TEG temperature difference and QPD is TEG with heatsinks heat flux density. The computed heatsinks parameters are: nhA the dimensionless convection conductance of heatsinks 1 or 2 fluid, Ti1 and Ti2 are fluids 1 and 2 hot and cold temperatures respectively, Ti the dimensionless fluid temperature, Nh the dimensionless convection conductance, ZTi2 the dimensionless figure of merit at Ti2, ZTA the TEG dimensionless figure of merit at TA. The TEG with heatsinks normalised, maximum and effective parameters are also computed.
In terms of the aesthetics, the TEG-HS output and inputs parameters were sorted together based on their commonalities, as well as labeled and colour coded accordingly to make the TEG with heatsinks model simple to comprehend and as well user friendly as shown in Figure 2.
Finally, in addition to the TEG with heatsinks numeric model computations, miscellaneous characteristics curves of some of the TEG crucial parameters of interest such as Qs1, Qs2, Pos, Eff*, Ts1 and Ts2; were plotted against Nk, Rr and DTs to graphically calculate Qs1, Qs2, Pos, Eff*, Ts1 and Ts2 different optimal values for ZTi2 = 1, Nh = 1, Ti = 2.6, Nk = 0.1 − 0.4, Rr = 0.5 − 2 and DTS = 0.1 − 1. These graphical results are in details, variously demonstrated next in Figures 3 to 6 and with the highlights summarised in Table 1.
Rr | Nk | DTS | Ts1-Ts2 | Qs1 | Qs2 | Pos | Eff* | Ts1 | Ts2 | |
Using "Simple" Eqs 32 and 33 |
2 | 0.3 | 0.8 | 0.83564 | 0.404938 | 0.35942 | 0.045518 | 0.112407 | 2.19506 | 1.35942 |
1.7 | 0.3 | 0.8 | 0.80401 | 0.420599 | 0.375429 | 0.0451302 | 0.10731 | 2.17944 | 1.37543 | |
1.1 | 0.3 | 0.8 | 0.7129 | 0.462515 | 0.424578 | 0.0379377 | 0.0820247 | 2.13748 | 1.42458 | |
1 | 0.3 | 0.8 | 0.69221 | 0.471429 | 0.436364 | 0.0350649 | 0.0743802 | 2.12857 | 1.43636 | |
0.5 | 0.3 | 0.8 | 0.54428 | 0.528736 | 0.526984 | 0.00175151 | 0.00331263 | 2.07126 | 1.52698 | |
Using "Simpler" Eqs 36 and 37 |
2 | 0.3 | 0.8 | 0.83736 | 0.414815 | 0.347826 | 0.0669887 | 0.161491 | 2.18519 | 1.34783 |
1.7 | 0.3 | 0.8 | 0.80637 | 0.432653 | 0.360976 | 0.0716775 | 0.16567 | 2.16735 | 1.36098 | |
1.1 | 0.3 | 0.8 | 0.71795 | 0.482051 | 0.4 | 0.0820513 | 0.170213 | 2.11795 | 1.4 | |
1 | 0.3 | 0.8 | 0.69805 | 0.492857 | 0.409091 | 0.0837662 | 0.16996 | 2.10714 | 1.40909 | |
0.5 | 0.3 | 0.8 | 0.55829 | 0.565517 | 0.47619 | 0.0893268 | 0.157956 | 2.03448 | 1.47619 |
In Section 3, the TEG with heatsinks simulated model was presented with highlights on its various parameters and the numeric results, as exemplified in Figure 2 and summarised in Table 2. These results as well as the numerous graphical results displayed extensively next, are based on the new simple and simpler analytical Ts1 and Ts2 formulas derived in Section 2. These are comparatively engaged and displayed next and various comparisons of Qs1, Qs2, Pos, Ts1, Ts2 and Eff* with different combinations of ZTi2, Nh Ti, Nk, Rr and DTS using the simple Eqs 32 and 33 as well as using the simpler Eqs 36 and 37 are shown and organised as follows. i) all the figures on the left are based on using the simple Eqs 32 and 33 Ts1 and Ts2 values, whereas all the figures on the right are based on using the simpler Eqs 36 and 37 Ts1 and Ts2 values. ii) Figure 3 graphs depict Qs1, Qs2, Pos, Ts1, Ts2 and Eff* results using ZTi2 = 1, Nh = 1, Ti = 2.6, Nk = 0.1 − 0.4, Rr = 0 − 6 and DTS = 0.8. iii) Figure 4 graphs depict Qs1, Qs2, Pos, Ts1, Ts2 and Eff* results using ZTi2 = 1, Nh = 1, Ti = 2.6, Nk = 0.05 − 0.5, Rr = 0.5 − 2 and DTS = 0.8. iv) Figure 5 graphs depict in 3D Qs1, Qs2, Pos, Ts1, Ts2 and Eff* results with ZTi2 = 1, Nh = 1, Ti = 2.6, Nk = 0.3, Rr = 0.2 − 3.2 and DTS = 0.1 − 1. v) Figure 6 graphs depict in 3D Qs1, Qs2, Pos, Ts1, Ts2 and Eff* results using ZTi2 = 1, Nh = 1, Ti = 2.6, Nk = 0.05 − 0.5, Rr = 1.7 and DTS = 0.1 − 1. Table 1 summarises the comparison of the simple Eqs 32 and 33 results and the simpler Eqs 36 and 37 results. Figures 2–6 results are also provided as supplementary picture files to enable every aspect of our findings to be viewed clearly in high quality without ambiguities.
Input Parameters | Output Parameters | ||||||
TEG Parameters | Heatsinks Parameters | Heatsink Fluids Temps | Convection Conductances | ||||
S (V/K) | 0.00044 | Ab (W/cm2) | 25 | Ti1 (K) | 773.15 | ɳ1h1A1 (W/K) | 4.8 |
Absolute T (K) | 273.15 | n1 | 0.8 | Ti2 (K) | 298.15 | ɳ2h2A2 (W/K) | 4.8 |
Ti1 (℃) | 500 | h1 (W/m2K) | 60 | Ti | 2.593 | Nh | 1 |
Ti2 (℃) | 25 | A1 (m2) | 0.1 | Figures of Merit | Dimensionless Heat Flows | ||
Ts | 1 | n2 | 0.8 | Z (K−1) | 0.003457 | Qs1 | 0.420599 |
Tp | 1 | h2 (W/m2K) | 60 | ZTi2 | 1.031 | Qs2 | 0.375429 |
R (Ω) | 0.01 | A2 (m2) | 0.1 | TEG Practical Performance Parameters | |||
k (W/mK) | 2.8 | RR (Ω) | 2.571 | Rr (rr) | 1.679 | ||
Ῥ (Ωm) | 0.00002 | Dimensionless Parameters | n | 257.1 | N | 18.63 | |
a (m2) | 0.000002 | Ni | 0.306 | Qh (Q1) (W) | 611.5 | Qc (Q2) (W) | 544.7 |
L (m) | 0.001 | Nk | 0.3 | Po (W) | 64.4 | Wn (W) | 65.69 |
RL (Ω) | 4.32 | nth (Eff*) | 0.108 | T1 (Th) (℃) | 374.4 | T1 (Th) (K) | 647.6 |
Preq (W) | 1200 | Ws1 (Pos) | 0.045 | T2 (Tc) (℃) | 134.4 | T2 (Tc) (K) | 407.6 |
Ts1 | 2.172 | QPD (W/cm2) | 24.46 | Nc | 0.3706 | ||
Ts1 | 1.367 | Vo (V) | 16.87 | Vmax (V) | 27.16 | ||
Nv | 0.5 | Io (A) | 3.896 | Imax (A) | 10.56 | ||
DTs | 0.8 | Voc (V) | 27.16 | Wmax (W) | 71.69 | ||
NB: the dimensionless parameters here can both be inputs and outputs | ΔT (℃) | 240 | Nmax | 0.1092 | |||
TA (℃) | 527.6 | Nmpmax (%) | 10.29 | ||||
ZTA (℃) | 1.824 | ΔT (K) | 240 |
Figure 3 graphs depict Qs1, Qs2, Pos, Ts1, Ts2 and Eff* results using ZTi2 = 1, Nh = 1, Ti = 2.6, Nk = 0.1 − 0.4, Rr = 0 − 6 and DTS = 0.8. It also compares the newly introduced simple vs simpler equations results.
Figure 4 graphs depict Qs1, Qs2, Pos, Ts1, Ts2 and Eff* results using ZTi2 = 1, Nh = 1, Ti = 2.6, Nk = 0.05 − 0.5, Rr = 0.5 − 2 and DTS = 0.8. It also compares the newly introduced simple vs simpler formulas results.
Figure 5 graphs depict in 3D Qs1, Qs2, Pos, Ts1, Ts2 and Eff* results with ZTi2 = 1, Nh = 1, Ti = 2.6, Nk = 0.3, Rr = 0.2 − 3.2 and DTS = 0.1 − 1. The newly introduced simple vs simpler equations results are also correlated.
Figure 6 graphs depict in 3D Qs1, Qs2, Pos, Ts1, Ts2 and Eff* results using ZTi2 = 1, Nh = 1, Ti = 2.6, Nk = 0.05 − 0.5, Rr = 1.7 and DTS = 0.1 − 1. The newly introduced simple vs simpler formulas results are compared.
In the first part of Section 4, the study results were variously and extensively displayed, revealing what combinations of Rr vs Nk vs DTs values that will give optimal Qs1, Qs2, Pos, Ts1, Ts2 and Eff* outcomes; by employing our newly introduced analytical Eqs 32 and 33 which are termed the "simple equations" and comparing with the further simplified versions, Eqs 36 and 37 which as well are termed the "simpler equations". It should be noted that each set of figures results, validate each other set of figures results. That is, Figure 3 results validates Figure 4 results which in turn validates Figure 5 results and consequently which validates Figure 6 results. Furthermore, the figures on the left results (based on Eqs 32 and 33 exclusively) validate the figures on the right results (based on Eqs 36 and 37 exclusively). In the second part of Section 4, the highlights of our presented findings are discussed next and lastly the results are validated where applicable with reference to the original results presented in [7].
Beginning with Figure 3, parameters Qs1, Qs2, Pos, Ts1, Ts2 and Eff* are plotted against Rr with Nk = 0.1 − 0.4 and DTs = 0.8 as well as ZTi2 = 1, Nh = 1, Ti = 2.6—which were fixed throughout our entire study and therefore have no relevance in our results/discussions. NB: Nk = 0.1 − 0.4 instead of just Nk = 0.3 was used to see the effects of different Nk values on Qs1, Qs2, Pos, Ts1, Ts2 and Eff* at also different Rr values. As evident, Qs1, Qs2 and Ts2 are inversely proportional to Rr with Nk = 0.3 and DTs = 0.8. Ts1 is directly proportional to Rr whereas Pos and Eff* are initially directly proportional to Rr, until Pos and Eff* reach their respective maximum value and then becomes inversely proportional to Rr and also with the rates of Pos and Eff* incline and decline, being faster using the "simpler" Eqs 36 and 37. With the "simple" equations, our optimal values for Pos is 0.045518 and for Eff* is 0.112407 and both occur at approximately Rr = 2 and not at exactly Rr = 1.7 as reported in [7]; however, at Rr = 1.7, our Pos and Eff* values of 0.0451302 and 0.10731 respectively, are exactly the same as those reported in [7]. With the "simpler" equations, our optimal values for Pos is 0.0893268 and for Eff* is 0.170213 and both occur at different Rr values—at Rr = 0.5 for Pos and at Rr = 1.1 for Eff*; however, at Rr = 1.7, both the Pos and Eff* values are respectively 0.0716775 and 0.16567, as well as respectively 0.0669887 and 0.161491 at Rr = 2. The rest parameters Qs1, Qs2, Ts1 and Ts2 values are closely the same using either the "simple" or "simpler" analytical equations. Further observable, the results dynamics have the following interesting aspects. i) Qs1, Qs2 and Ts2 values increase with increasing Nk values; however, they decrease with increasing Rr values as noticed and explained already. ii) Ts1 values increase with decreasing Nk values; as well as increase with decreasing Rr values as noticed and already explained. iii) Eff* values also increases with decreasing Nk values with the increase being more significant at lower values of Rr, especially at Rr values below 1.0. iv) Pos values are interesting—as the dynamics are irregular with different Nk values, with Pos values sharply increasing initially with decreasing Nk values and at very low Rr values and once after their respective optimal points, Pos values again increase but with now increasing Nk values and at high Rr values.
In Figure 4, parameters Qs1, Qs2, Pos, Ts1, Ts2 and Eff* are plotted against Nk with Rr = 0.5 − 2 and DTs = 0.8 and using ZTi2 = 1, Nh = 1, Ti = 2.6—which were fixed throughout the study. Rr = 0.5 − 2 instead of only Rr = 1.7 was used to see the effects of different Rr values on Qs1, Qs2, Pos, Ts1, Ts2 and Eff* at also over different Nk values. As can be seen, Qs1, Qs2 and Ts2 values are directly proportional to Nk. However, Ts1 and Eff* values are inversely proportional to Nk values. Pos initially increases proportionally to Nk till it reaches optimal point at Nk = 0.25 in Figure 4c (simple equation) and Nk = 0.3 in Figure 4i (simpler equation); after which Pos values becomes inversely proportional to Nk. Further noticeable, Qs1, Qs2 and Ts2 values are inversely proportional to Rr values, though directly proportional to Nk values as indicated earlier. Nevertheless, Ts1 is directly proportional to Rr values but indirectly proportional to Nk. Initially, with increasing Nk, Pos increases more with less Rr at mostly low Nk values till maximum Pos is attained and thereafter, Pos decreases more with less Rr at high Nk values. The optimal Pos of 0.0478788 using our simple equation occurs at Rr = 1.1 with Nk = 0.2, whereas at Rr = 1.7, the optimal Pos = 0.0474483 with Nk = 0.25—slightly contrary to [7] which reported an optimal Pos of 0.045 at Rr = 1.7 with Nk = 0.3—which we also have exactly the same result of Pos = 0.0451302 at Rr = 1.7 with Nk = 0.3; however, this result was not the exact optimal outcome in our case. Using our simpler equation, we have at Rr = 0.5, two Pos optimal values of 0.0966733 and 0.0977376 at respectively Nk = 0.2 and Nk = 0.25. Initially Eff* with increasing Nk, decreases more with more Rr at mostly low Nk values till optimal Eff* is attained and thereafter, Eff* decreases more with less Rr at high Nk values. This Eff* dynamics is mostly and clearly noticeable in Figure 4l using our simpler equation.
Figure 5 is a 3D plot of Qs1, Qs2, Pos, Ts1, Ts2 and Eff* parameters against Rr = 0.2 − 3.2 but with now DTs = 0 − 1 and Nk fixed at 0.3. The results summarily reveal that Pos and Eff* increase proportionally with increasing DTs, reach maximum and decrease, especially at lower Rr values but at higher Rr, Pos and Eff* increase linearly with DTs. Also, Qs1, Qs2, Ts1 and Ts parameters exhibit comparable dynamics to those of Figures 3 and 4 results.
Figure 6 is another 3D plot of Qs1, Qs2, Pos, Ts1, Ts2 and Eff* parameters against Nk = 0.05 − 0.5 but now with DTs = 0 − 1 and Rr fixed at 1.7. As apparent, Qs1, Qs2 and Ts2 have similar dynamics as already noted and discussed earlier in the previous figures. The only difference now is, these dynamics happen across different values of DTs. The same dynamics applies to Ts1 and Eff*. Pos generally increases proportionally to DTs at especially lower Nk values but at higher Nk values, Pos decreases with DTs as revealed.
It's worth stating that, these different plots simply show the different dynamics involved and generally, it's up to designers to now choose optimal values depending on the design constraints and design objectives.
To validate our findings in Figures 2–6 and Tables 1 and 2 where applicable, Figure 7 and Table 3 results adapted from [7] were used. In summary, validating our findings using [7] results affirms i) exactly the accuracy of our simple equations results and ii) fairly the approximation of our simpler equations results. It should be noted that, just reference [7] was used to validate our findings because a) reference [7] is the original research now developed and simplified with direct analytical formulas to easily calculate Ts1 and Ts2 and therefore it's only prudent to validate the new developments with the original study and b) reference [7] is the only study we know with the aforementioned method and having the stated datasets that we can use.
![]() |
Sustainable energy is transcending to become the future of energy to complement the national grid and for private use. As a result, we've researched thermoelectricity (TEG) as an alternative energy source for household applications requiring low DC power and lighting. However, practical TEG use requires heatsinks to work efficiently and reliably but regrettably adding heatsinks add thermal resistances, which consequently degrades the TEG efficiency as well as its output power. We investigated various techniques, especially dimensional analysis and shortlisted the approach by [7]—which converts thermal resistance to convection conductance, making it easier for practical use. However, the formulations in [7] could not find the exact analytical formulas to directly calculate Ts1 and Ts2; as a result, [7] used numerical analysis (a bit cumbersome) which we developed further by introducing DTs to simplify and derive new simple accurate analytical formulas that can be applied to compute Ts1 and Ts2 directly. Furthermore, these simple formulas were further simplified to obtain simpler analytical equations for Ts1 and Ts2. Finally, our simplest Ts1 and Ts2 formulas and their optimal relationships were established. These formulas were all verified with chosen optimal values and all gave approximate results that correlated each other. We further used these newly introduced formulas to model, numerically simulate and plotted various characteristics curves of Qs1, Qs2, Pos, Ts1, Ts2 and Eff* against Rr vs Nk vs DTs using Matlab and Simulink. These results were articulated variously in both 2D and 3D plots and finally the equivalent outcomes were comparatively discussed and validated using each other and as well with results asserted in [7]. In [7], Pos of 0.045 is optimal with Nk = 0.3 at Rr = 1.7, contrary to our study which gave optimal Pos of 0.0474483 at Nk = 0.25 using our simple equations; however, using our simpler equations, it gave optimal Pos of 0.0716775 at Nk = 0.3. Notwithstanding, our simple equations gave Pos of 0.0451302 at Nk = 0.3 (though not optimal in our case) which corresponds exactly to optimal Pos value of 0.045 with Nk = 0.3 as in [7]. In addition, the magnitude of Pos and Eff* are more (almost doubled) using our simpler Eqs 36 and 37, compared to using our simple Eqs 32 and 33. Furthermore, the optimal values of Pos and Eff* using both our "simple" and "simpler" equations, respectively occurred at different values of Rr. In sum, Eff* is best at very low Nk values. The highlights of our study are marked in the various figures and also summarised in Tables 1 and 2. It's worth mentioning that, DTs = 0.8 for this set of optimal values, is rightly only equal to Ts1 − Ts2 = ~0.8 only at Rr = 1.7 and Nk = 0.3 as summarised in Table 1 and not at any other values when used in both our simple and simpler equations. Finally, in as much as our newly introduced simpler analytical formulas didn't give exact Pos and Eff* results correlating those in i) [7] and ii) our newly introduced analytical simple equations (that gave accurate results), we reckon the simpler equations can be used as first approximation to quickly find Ts1 and Ts2 as well as Qs1 and Qs2 values with fair accuracy. In sum, Ts1 and Ts2 are the most vital physical parameters, as they're those that can be easily practically manipulated to achieve the other values. However, first ascertaining the electrical load or Rr value to ensure maximum power transfer is most paramount to achieve optimal result, as a TEG as well TEC, are non-linear devices whose dynamics must be well understood before embarking on a practical design. The next phase of our research is to validate and refine our study practically and then design a household TEG alternative DC power source.
Thanks to the Cape Peninsula University of Technology (CPUT) and HySA Systems at the University of the Western Cape (UWC), Cape Town, South Africa for funding the study.
The authors declare no conflict of interest.
Figures 1–6 are provided in link below in picture format for better quality viewing/review.
https://drive.google.com/drive/folders/1VHN2mHJ_wtYaztunL_Sn21XJmppc0o8z?usp=sharing
[1] | Van der Walt ML, Van den Berg J, Cameron M (2017) South Africa department of energy, state of renewable energy in South Africa. Available from: http://www.energy.gov.za/files/media/Pub/2017-State-of-Renewable-Energy-in-South-Africa.pdf. |
[2] | Bayendang NP, Kahn MT, Balyan V, et al. (2020) A comprehensive thermoelectric generator (TEG) Modelling. AIUE Congress 2020: Energy and Human Habitat Conference, Cape Town, South Africa, 2020; Zenodo: Geneva, Switzerland, 2020: 1-7. Available from: http://doi.org/10.5281/zenodo.4289574. |
[3] | Bayendang NP, Kahn MT, Balyan V, et al. (2020) A comprehensive thermoelectric cooler (TEC) modelling. AIUE Congress 2020: International Conference on Use of Energy, Cape Town, South Africa; SSRN: Rochester, NY, USA, 2021: 1-7. Available from: https://ssrn.com/abstract=3735378 or http://dx.doi.org/10.2139/ssrn.3735378. |
[4] |
Twaha S, Zhu J, Yan Y, et al. (2016) A comprehensive review of thermoelectric technology: materials, applications, modelling and performance improvement. Renewable Sustainable Energy Rev 65: 698-726. doi: 10.1016/j.rser.2016.07.034
![]() |
[5] |
Jouhara H, Żabnieńska-Góra A, Khordehgah N, et al. (2021) Thermoelectric Generator (TEG) technologies and applications. Int J Thermofluids 9: 100063. doi: 10.1016/j.ijft.2021.100063
![]() |
[6] | Bayendang NP, Kahn MT, Balyan V (2021) Simplified thermoelectric cooler (TEC) with heatsinks modeling and simulation using Matlab and Simulink based-on dimensional analysis. AIUE Conference 2021: 2nd Energy and Human Habitat Conference, Cape Town, South Africa; SSRN: Rochester, NY, USA, 1-8. Available from: http://dx.doi.org/10.2139/ssrn.3900757. |
[7] |
Lee H (2013) Optimal design of thermoelectric devices with dimensional analysis. Appl Energy 106: 79-88. doi: 10.1016/j.apenergy.2013.01.052
![]() |
[8] | Lineykin S, Ruchaevski I, Kuperman A (2014) Analysis and optimization of TEG-heatsink waste energy harvesting system for low temperature gradients. 16th European conference on power electronics and applications, Lappeenranta, Finland, 1-10. |
[9] |
Melnikov AA, Kostishin VG, Alenkov VV (2017) Dimensionless model of a thermoelectric cooling device operating at real heat transfer conditions maximum cooling capacity mode. J Electron Mater 46: 2737-2745. doi: 10.1007/s11664-016-4952-0
![]() |
[10] | Li W, Paul MC, Montecucco A, et al. (2015) Multiphysics simulations of a thermoelectric generator. The 7th international conference on applied energy—ICAE 2015, Energy Proc 75: 633-638. |
[11] | Casano G, Piva S (2012) Parametric thermal analysis of the performance of a thermoelectric generator. 6th European thermal sciences conference (Eurotherm 2012), Poitiers, France, J Physics: Conference Series, 395: 2156. |
[12] |
Dos Santos Guzella M, Dos Santos GR, Cabezas-Gómez L, et al. (2021) Numerical simulation of the two-dimensional heat diffusion in the cold substrate and performance analysis of a thermoelectric air cooler using the lattice Boltzmann method. Int J Appl Comput Math 7: 130. doi: 10.1007/s40819-021-01073-8
![]() |
[13] |
Hao J, Qiu H, Ren J, et al. (2020) Multi-parameters analysis and optimization of a typical thermoelectric cooler based on the dimensional analysis and experimental validation. Energy 205: 118043. doi: 10.1016/j.energy.2020.118043
![]() |
[14] |
Lu X, Zhao D, Ma T, et al. (2018) Thermal resistance matching for thermoelectric cooling systems. Energy Convers Manage 169: 186-193. doi: 10.1016/j.enconman.2018.05.052
![]() |
[15] |
Chen J, Lin B, Wang H, et al. (2000) Optimal design of a multi-couple thermoelectric generator. Semicond, Sci Technol 15: 184-188. doi: 10.1088/0268-1242/15/2/318
![]() |
[16] | Lineykin S, Ben-Yaakov S (2006) A Simple and intuitive graphical approach to the design of thermoelectric cooling systems. 37th IEEE Power Electronics Specialists Conference, Jeju, Korea (South), 1-5. |
[17] |
Hubbard WA, Mecklenburg M, Lodico JJ, et al. (2020) Electron-transparent thermoelectric coolers demonstrated with nano-particle and condensation thermometry. ACS Nano 14: 11510-11517. doi: 10.1021/acsnano.0c03958
![]() |
[18] |
He W, Wang S, Yang Y (2016) Optimal heat exchanger dimensional analysis under different automobile exhaust temperatures for thermoelectric generator system.Energy Proc 104: 366-371. doi: 10.1016/j.egypro.2016.12.062
![]() |
Rr | Nk | DTS | Ts1-Ts2 | Qs1 | Qs2 | Pos | Eff* | Ts1 | Ts2 | |
Using "Simple" Eqs 32 and 33 |
2 | 0.3 | 0.8 | 0.83564 | 0.404938 | 0.35942 | 0.045518 | 0.112407 | 2.19506 | 1.35942 |
1.7 | 0.3 | 0.8 | 0.80401 | 0.420599 | 0.375429 | 0.0451302 | 0.10731 | 2.17944 | 1.37543 | |
1.1 | 0.3 | 0.8 | 0.7129 | 0.462515 | 0.424578 | 0.0379377 | 0.0820247 | 2.13748 | 1.42458 | |
1 | 0.3 | 0.8 | 0.69221 | 0.471429 | 0.436364 | 0.0350649 | 0.0743802 | 2.12857 | 1.43636 | |
0.5 | 0.3 | 0.8 | 0.54428 | 0.528736 | 0.526984 | 0.00175151 | 0.00331263 | 2.07126 | 1.52698 | |
Using "Simpler" Eqs 36 and 37 |
2 | 0.3 | 0.8 | 0.83736 | 0.414815 | 0.347826 | 0.0669887 | 0.161491 | 2.18519 | 1.34783 |
1.7 | 0.3 | 0.8 | 0.80637 | 0.432653 | 0.360976 | 0.0716775 | 0.16567 | 2.16735 | 1.36098 | |
1.1 | 0.3 | 0.8 | 0.71795 | 0.482051 | 0.4 | 0.0820513 | 0.170213 | 2.11795 | 1.4 | |
1 | 0.3 | 0.8 | 0.69805 | 0.492857 | 0.409091 | 0.0837662 | 0.16996 | 2.10714 | 1.40909 | |
0.5 | 0.3 | 0.8 | 0.55829 | 0.565517 | 0.47619 | 0.0893268 | 0.157956 | 2.03448 | 1.47619 |
Input Parameters | Output Parameters | ||||||
TEG Parameters | Heatsinks Parameters | Heatsink Fluids Temps | Convection Conductances | ||||
S (V/K) | 0.00044 | Ab (W/cm2) | 25 | Ti1 (K) | 773.15 | ɳ1h1A1 (W/K) | 4.8 |
Absolute T (K) | 273.15 | n1 | 0.8 | Ti2 (K) | 298.15 | ɳ2h2A2 (W/K) | 4.8 |
Ti1 (℃) | 500 | h1 (W/m2K) | 60 | Ti | 2.593 | Nh | 1 |
Ti2 (℃) | 25 | A1 (m2) | 0.1 | Figures of Merit | Dimensionless Heat Flows | ||
Ts | 1 | n2 | 0.8 | Z (K−1) | 0.003457 | Qs1 | 0.420599 |
Tp | 1 | h2 (W/m2K) | 60 | ZTi2 | 1.031 | Qs2 | 0.375429 |
R (Ω) | 0.01 | A2 (m2) | 0.1 | TEG Practical Performance Parameters | |||
k (W/mK) | 2.8 | RR (Ω) | 2.571 | Rr (rr) | 1.679 | ||
Ῥ (Ωm) | 0.00002 | Dimensionless Parameters | n | 257.1 | N | 18.63 | |
a (m2) | 0.000002 | Ni | 0.306 | Qh (Q1) (W) | 611.5 | Qc (Q2) (W) | 544.7 |
L (m) | 0.001 | Nk | 0.3 | Po (W) | 64.4 | Wn (W) | 65.69 |
RL (Ω) | 4.32 | nth (Eff*) | 0.108 | T1 (Th) (℃) | 374.4 | T1 (Th) (K) | 647.6 |
Preq (W) | 1200 | Ws1 (Pos) | 0.045 | T2 (Tc) (℃) | 134.4 | T2 (Tc) (K) | 407.6 |
Ts1 | 2.172 | QPD (W/cm2) | 24.46 | Nc | 0.3706 | ||
Ts1 | 1.367 | Vo (V) | 16.87 | Vmax (V) | 27.16 | ||
Nv | 0.5 | Io (A) | 3.896 | Imax (A) | 10.56 | ||
DTs | 0.8 | Voc (V) | 27.16 | Wmax (W) | 71.69 | ||
NB: the dimensionless parameters here can both be inputs and outputs | ΔT (℃) | 240 | Nmax | 0.1092 | |||
TA (℃) | 527.6 | Nmpmax (%) | 10.29 | ||||
ZTA (℃) | 1.824 | ΔT (K) | 240 |
Rr | Nk | DTS | Ts1-Ts2 | Qs1 | Qs2 | Pos | Eff* | Ts1 | Ts2 | |
Using "Simple" Eqs 32 and 33 |
2 | 0.3 | 0.8 | 0.83564 | 0.404938 | 0.35942 | 0.045518 | 0.112407 | 2.19506 | 1.35942 |
1.7 | 0.3 | 0.8 | 0.80401 | 0.420599 | 0.375429 | 0.0451302 | 0.10731 | 2.17944 | 1.37543 | |
1.1 | 0.3 | 0.8 | 0.7129 | 0.462515 | 0.424578 | 0.0379377 | 0.0820247 | 2.13748 | 1.42458 | |
1 | 0.3 | 0.8 | 0.69221 | 0.471429 | 0.436364 | 0.0350649 | 0.0743802 | 2.12857 | 1.43636 | |
0.5 | 0.3 | 0.8 | 0.54428 | 0.528736 | 0.526984 | 0.00175151 | 0.00331263 | 2.07126 | 1.52698 | |
Using "Simpler" Eqs 36 and 37 |
2 | 0.3 | 0.8 | 0.83736 | 0.414815 | 0.347826 | 0.0669887 | 0.161491 | 2.18519 | 1.34783 |
1.7 | 0.3 | 0.8 | 0.80637 | 0.432653 | 0.360976 | 0.0716775 | 0.16567 | 2.16735 | 1.36098 | |
1.1 | 0.3 | 0.8 | 0.71795 | 0.482051 | 0.4 | 0.0820513 | 0.170213 | 2.11795 | 1.4 | |
1 | 0.3 | 0.8 | 0.69805 | 0.492857 | 0.409091 | 0.0837662 | 0.16996 | 2.10714 | 1.40909 | |
0.5 | 0.3 | 0.8 | 0.55829 | 0.565517 | 0.47619 | 0.0893268 | 0.157956 | 2.03448 | 1.47619 |
Input Parameters | Output Parameters | ||||||
TEG Parameters | Heatsinks Parameters | Heatsink Fluids Temps | Convection Conductances | ||||
S (V/K) | 0.00044 | Ab (W/cm2) | 25 | Ti1 (K) | 773.15 | ɳ1h1A1 (W/K) | 4.8 |
Absolute T (K) | 273.15 | n1 | 0.8 | Ti2 (K) | 298.15 | ɳ2h2A2 (W/K) | 4.8 |
Ti1 (℃) | 500 | h1 (W/m2K) | 60 | Ti | 2.593 | Nh | 1 |
Ti2 (℃) | 25 | A1 (m2) | 0.1 | Figures of Merit | Dimensionless Heat Flows | ||
Ts | 1 | n2 | 0.8 | Z (K−1) | 0.003457 | Qs1 | 0.420599 |
Tp | 1 | h2 (W/m2K) | 60 | ZTi2 | 1.031 | Qs2 | 0.375429 |
R (Ω) | 0.01 | A2 (m2) | 0.1 | TEG Practical Performance Parameters | |||
k (W/mK) | 2.8 | RR (Ω) | 2.571 | Rr (rr) | 1.679 | ||
Ῥ (Ωm) | 0.00002 | Dimensionless Parameters | n | 257.1 | N | 18.63 | |
a (m2) | 0.000002 | Ni | 0.306 | Qh (Q1) (W) | 611.5 | Qc (Q2) (W) | 544.7 |
L (m) | 0.001 | Nk | 0.3 | Po (W) | 64.4 | Wn (W) | 65.69 |
RL (Ω) | 4.32 | nth (Eff*) | 0.108 | T1 (Th) (℃) | 374.4 | T1 (Th) (K) | 647.6 |
Preq (W) | 1200 | Ws1 (Pos) | 0.045 | T2 (Tc) (℃) | 134.4 | T2 (Tc) (K) | 407.6 |
Ts1 | 2.172 | QPD (W/cm2) | 24.46 | Nc | 0.3706 | ||
Ts1 | 1.367 | Vo (V) | 16.87 | Vmax (V) | 27.16 | ||
Nv | 0.5 | Io (A) | 3.896 | Imax (A) | 10.56 | ||
DTs | 0.8 | Voc (V) | 27.16 | Wmax (W) | 71.69 | ||
NB: the dimensionless parameters here can both be inputs and outputs | ΔT (℃) | 240 | Nmax | 0.1092 | |||
TA (℃) | 527.6 | Nmpmax (%) | 10.29 | ||||
ZTA (℃) | 1.824 | ΔT (K) | 240 |
![]() |