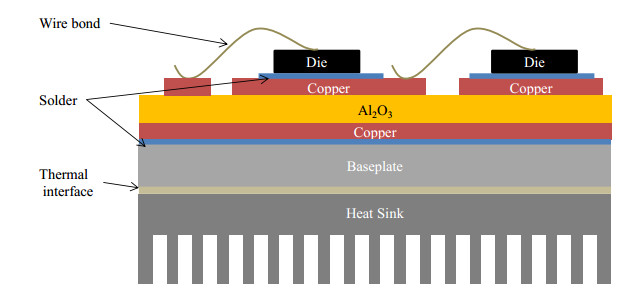
Citation: Nicolas Degrenne, Romain Delamea, Stefan Mollov. Electro-thermal modelling and Tj estimation of wire-bonded IGBT power module with multi-chip switches subject to wire-bond lift-off[J]. AIMS Electronics and Electrical Engineering, 2020, 4(2): 154-168. doi: 10.3934/ElectrEng.2020.2.154
[1] | Rasool M. Imran, Kadhim Hamzah Chalok, Siraj A. M. Nasrallah . Innovative two-stage thermal control of DC-DC converter for hybrid PV-battery system. AIMS Electronics and Electrical Engineering, 2025, 9(1): 26-45. doi: 10.3934/electreng.2025002 |
[2] | Martin Seilmayer, Varun Kumar Katepally . Thermal conductivity survey of different manufactured insulation systems of rectangular copper wires. AIMS Electronics and Electrical Engineering, 2018, 2(1): 27-36. doi: 10.3934/ElectrEng.2018.1.27 |
[3] | José M. Campos-Salazar, Roya Rafiezadeh, Juan L. Aguayo-Lazcano, Constanza Márquez . Reduction of harmonic distortion in electromagnetic torque of a single-phase reluctance motor using a multilevel neutral-point-clamped DC-AC converter. AIMS Electronics and Electrical Engineering, 2025, 9(2): 215-242. doi: 10.3934/electreng.2025011 |
[4] | Gavin C Rider . A critique of the approach to controlling electrostatic risk in semiconductor production and identification of a potential risk from the use of equipotential bonding. AIMS Electronics and Electrical Engineering, 2019, 3(4): 397-414. doi: 10.3934/ElectrEng.2019.4.397 |
[5] | Charles Aimiuwu Osaretin, Tariq Iqbal, Stephen Butt . Optimal sizing and techno-economic analysis of a renewable power system for a remote oil well. AIMS Electronics and Electrical Engineering, 2020, 4(2): 132-153. doi: 10.3934/ElectrEng.2020.2.132 |
[6] | I.E.S. Naidu, S. Srikanth, A. Siva sarapakara Rao, Adabala Venkatanarayana . A novel mine blast optimization algorithm (MBOA) based MPPT controlling for grid-PV systems. AIMS Electronics and Electrical Engineering, 2023, 7(2): 135-155. doi: 10.3934/electreng.2023008 |
[7] | K.V. Dhana Lakshmi, P.K. Panigrahi, Ravi kumar Goli . Machine learning assessment of IoT managed microgrid protection in existence of SVC using wavelet methodology. AIMS Electronics and Electrical Engineering, 2022, 6(4): 370-384. doi: 10.3934/electreng.2022022 |
[8] | Tarun Naruka, Debasis Tripathy, Prangya Mohanty . Power quality enhancement by a solar photovoltaic-based distribution static compensator. AIMS Electronics and Electrical Engineering, 2025, 9(2): 192-214. doi: 10.3934/electreng.2025010 |
[9] | Ashraf A. Ahmad, Ameer Mohammed, Mohammed Ajiya, Zainab Yunusa, Habibu Rabiu . Estimation of time-parameters of Barker binary phase coded radar signal using instantaneous power based methods. AIMS Electronics and Electrical Engineering, 2020, 4(4): 347-358. doi: 10.3934/ElectrEng.2020.4.347 |
[10] | Masoud Kiani, Jafar Adabi, Firuz Zare . Increasing LTCC inductance density by using inverse coupling technique and multi-permeability structure. AIMS Electronics and Electrical Engineering, 2018, 2(3): 85-102. doi: 10.3934/ElectrEng.2018.3.85 |
Wire-bonded multi-chip IGBT power modules constitute the heart of high-current power electronic motor drives. They are used in many reliability-critical applications such as traction and wind energy. In these applications, they constitute a large proportion of the total number of failures [1]. The failure either causes the triggering of a detection and protection circuit or results in catastrophic failures such as explosion, eventually also damaging connected equipment. The general structure is presented in Figure 1. For most modules and mission profiles, the main wear-out failure mechanism is the degradation of the top-side wires as a consequence to thermo-mechanical stress [2]. It was found that cracks develop at the interface between the aluminium wires and the metallization of the dies. Ultimately, the wires lift off, and do not ensure electrical contact. This degradation process can be reproduced in power cycling test benches [3].
Health monitoring is an enabler to condition-based maintenance which is of particular interest in availability-critical applications. This is especially true in industrial context where motors or other actuators are monitored. Health-monitoring can also accelerate the integration of new technologies such as SiC which present excellent performances but for which long term reliability is not yet acknowledged in all industries. A review on health monitoring applied to power modules [4] classifies health monitoring methods in two types:
● Damage-accumulation-based methods count and weight the temperature cycles.
● Condition-based methods follow the evolution of a failure precursor.
The review highlights the importance of temperature estimation in both approaches, as a value representative of stress, as a value representative of a failure, and as a value on which other measured parameters depend. In a multi-chip-switch power module, the individual die temperatures may vary as a consequence to thermal and/or electrical mismatch [5]. The degradation of the top-side connection modifies the individual electrical connections of the dies and thus also influence the temperature distribution within the different dies. This temperature distribution impacts the ageing progression. It is thus of particular interest to know and understand the mechanisms of the temperature distribution when degradation increases. It is also critical to estimate the equivalent temperature in on-line applications, and to understand what it really represents, for example the average, minimum or maximum value of the different dies in parallel.
Estimating the temperature of the power dies was extensively studied in the past decades, with a strong focus on TSEPs (Temperature Sensitive Electrical Parameters) [6]. When multi-chip power modules are concerned, the individual die temperatures may vary as a consequence to thermal and/or electrical mismatch. In [7], a method is presented and evaluated for evaluating the temperature of each die independently with individual gate access. However, in the vast majority of large-current power modules, individual gate access is not available. One of the most common TSEPs is the on-state voltage Von. It can be implemented in different ways as listed in [8]. The method of Von at low-load current can be implemented in a wide majority of switching power cycling test benches that are used to investigate the failure mechanisms in a realistic way. The on-state voltage being sensitive to the quality of the top-side connection, the obtained temperature estimate is drifting with degradation. This drift naturally tends to under-estimate the temperature, thus reducing the capability of health monitoring with either of the two methods. Drift compensation methods based on re-calibration are possible in single-chip switches [8], but this paper will show that their performances are compromised in multi-chip switches.
This paper addresses the relation between wire-bond degradation and temperature in multi-chip modules and proposes a simple model to explain and reproduce the electro-thermal behaviours. The model is based on experimental results where the degradation of wire-bonds is reproduced by cutting the wires sequentially. The model is further used to explain the drift in temperature estimation and the performance of the drift compensation methods based on re-calibration. Overall, the paper provides new results and understandings of the thermo-electrical behaviour of multi-chip power IGBT modules subject to wear-out.
A six-pack 1200V/150A industrial power module was used as a DUT (Device Under Test). Each top-side IGBT die of this module is connected by 15 wires and 23 contacts as shown in Figure 2. The top-side dies were identified to be more often subject to wire-bond failures during power cycling. The three half-bridges of the module were connected in parallel so as to reproduce a multi-chip power module, each switch being constituted of 3 dies in parallel. The insulating gel was removed and the power module surface was black-painted. The DUT was mounted on a cold plate using a thermal interface foil covering only two third of the surface of the baseplate to create an initial temperature unbalance. The set-up was connected in a back-to-back power converter as previously described in [9] in unipolar modulation mode operating at 600 V.
A sequence of (re-)calibration, operation with measures of Von at low load current, and wire-bond cuts was performed as in Figure 3.
(Re)-calibration was performed by generating current pulses in a wide range (7 to 180 A) at various heat-sink temperatures. In between pulses, the current is null and the switches are not commutated, to prevent any self-heating. The obtained calibration data is used for estimation of Tj from Von and Ion. The data obtained with low current pulses in the range 7 to 13 A are used for temperature estimation. The data obtained with high-current pulses in the range 150 to 180 A are used for estimating the electrical resistance increase.
The power module was operated with a current of 100 A, a switching frequency of 13.3 kHz, and a duty-cycle of 0.5. The losses are thus a realistic combination of conduction and switching losses. A thermal IR (Infra-Red) camera was used to capture the average temperature of the area of each die. At regular intervals, the current was quickly reduced to preform measurements of Von at low load current. These measurements are used to estimate the temperature using the calibration data.
The initially hottest die 3 (due to the artificial thermal imbalance) was identified during the first temperature observation. If this thermally unbalanced power module would have been power cycled, it is most likely that the wires on the hottest die would have degraded faster, leading to their failure first. The wire-bonds of the initially hottest die were thus cut one by one, in a sequence previously studied in [3].
The evolution of the die temperature, measured with the IR camera, is plotted in Figure 4 as a function of the number of wire-bond cuts on the initially hottest die 3. The error due to errors in area definition and to wire-bond masking is estimated to be ± 2℃. The temperature of die 3 is decreasing and the temperature of the two other dies are increasing as wires are sectioned. After 11 cuts, die 3 is not the hottest die anymore. Ultimately, when all the 15 wires of die 3 are cut, its temperature is only 67.5℃. The intuitive explanation for this temperature evolution is that, as the electrical connection of the die 3 is degraded, the current flow through it is reduced, and the conduction and switching losses are themselves reduced correspondingly. This hypothesis is supported by the evolution of the equivalent electrical resistance increase ∆Req in Figure 5. This curve was obtained based on the Von measurements at high current between each cut. The points follow a shape with 3 zones. During the first 6 cuts, i.e. corresponding to the long wires in Figure 2, the ∆Req increases from 0 to 0.3 mΩ. From 6 to 11 cuts corresponding to the first short wires, ∆Req is relatively constant. When the last wires are sectioned, the equivalent resistance increases in an accelerated way until 1 mΩ corresponding to the value when all the wires but the Kelvin connection (K in Figure 2) are cut.
In this section, the intuitive sequence of electro-thermal effects resulting from wire-bond cut is modelled. First, the electrical interconnection is modelled electrically. Second, the dies are modelled electro-thermally. Both models are then combined.
The main objective of this model is to estimate the electrical resistance increase ∆R3 of the die 3. The input of the model is the equivalent electrical resistance increase ∆Req across the 3 parallel dies, measured with high-current pulses in the condition of negligible self-heating. This model assumes that the 3 dies have the same temperature (i.e. Tji = Tc) and the same linear static characteristics in the current of interest. The equivalent static characteristic of the 3 dies in parallel is thus expressed in the simple form (1), A and B being temperature-dependent parameters that are estimated based on the fitting of the Von measured during calibration at Tc and various high-current pulses in the range 110 A to 190 A.
VON0=A(Tc).ION+B(Tc) | (1) |
The corresponding equivalent and individual lumped models are shown in Figure 6. The equality between these models results in (2), where N is the number of dies in parallel.
ΔR3=ΔREQ.N21−(N−1)ΔREQA(Tc) | (2) |
The evolution of ∆R3 as a function of cut wires is shown in Figure 7. After 15 cuts, the value of ∆R3 is 30 mΩ and not infinity, thanks to the remaining Kelvin connection. The evolution of the die temperatures, plotted as a function of the electrical resistance increase of die 3, ∆R3, is presented in Figure 8. The mean temperature is also displayed and is relatively constant, i.e. comprised between 87.5 and 90℃ during the whole experiment.
Now that the electrical resistance increase ∆R3 was computed, the objective of the electro-thermal model of the dies is to estimate the consequent voltage, currents, losses, and thermal distribution in the power module. The framework is illustrated in Figure 9 and forms a loop that is run until convergence. This section details the models and their outputs obtained after convergence.
The linear static curves according to the Eq. (1) are assumed with their individual dependency on the junction temperature Tji. The parameters A(Tji) and B(Tji) are extracted from the initial calibration in the region of operation, i.e. between 70 A and 130 A. Note that for a high number of cuts, the current distribution is expected to be very unbalanced, and the error in the parameters A and B is expected to increase.
For a given temperature distribution (Tj1, Tj2, Tj3) resulting in the coefficients (A1, A2, A3) and (B1, B2, B3), and a given electrical resistance increase (0, 0, ∆R3), the equivalent Von and individual Ii are derived using Kirchhoff’s laws from the lumped electrical model in Figure 6, expressed by (3) and (4), and plotted in Figures 10 and 11 for the 3 IGBT dies. A similar calculation is performed for the bottom diodes, which losses also impact the case temperature.
Von=Itot.A1.A2.(A3+ΔR3)+B2.A1.(A3+ΔR3)+A1.B3.A2+B1.A2.(A3+ΔR3)A2.(A3+ΔR3)+A1.(A3+ΔR3)+A1.A2 | (3) |
Ii=Von−Bi(Ai+ΔRi) | (4) |
The losses in the IGBT and diode dies are expressed in (5) and (6), where α ( = 0.5) is the duty-cycle, Eon ( = 16.6e-3J) is the turn-on energy, Eoff ( = 17.6e-3J) is the turn-off energy, Err ( = 10.8e-3J) is the reverse recovery energy as indicated in the datasheet for 150 A. The losses in the IGBT dies are shown in Figure 12.
PlossIi=α.VonI.IonIi+fsw.(Eon+Eoff).Ii/150 | (5) |
PlossDi=(1−α).VonD.IonDi+fsw.Err.Ii/150 | (6) |
The thermal model is presented in Figure 13. It distinguishes the 3 DBCs corresponding to the 3 legs, for which a specific case temperature is computed based on the losses of the IGBT and diode dies. The junction to case thermal resistances are defined based on the datasheet (i.e. 0.16 K/W for IGBT dies). The case to heat-sink thermistances are identified to obtain similar initial temperatures as in the experimental conditions. The resulting evolution of the temperature distribution is presented in Figure 14.
The superimposed measured and estimated temperatures are in Figure 15. The model estimates fit correctly the trend of the temperature evolution. For high number of wire-bond cuts, the measured temperature unbalance is more pronounced than the one estimated. The reason for this may be inaccuracies in the models, for example in the thermal model where a homogeneous heat-sink temperature of 20℃ was assumed. Overall, the qualitative trends are correct and confirm the mechanisms involved in the evolution of the temperature distribution.
During power cycling in high-frequency test benches, temperature can be estimated in different ways. In [8], the temperature is estimated using Von at low load current pulses of 10 A. In the experiment described in this paper, a similar temperature estimation is studied. The initial calibration is used to establish the relation between Von, Ion, and Tj. The temperature was estimated with this method after each wire cut. The evolution of the equivalent junction Tjeq estimates is presented in Figure 16. Initially, in the absence of degradation, the Tjeq estimation is accurately identifying the mean temperature. However, as the degradation develops, the Tjeq is under-estimated. This phenomenon was already observed and explained in [8] in the case of a single-die switch. A method was proposed to correct the calibration model based on the estimation of the (equivalent) electrical resistance increase. The same compensation method was tested on the multi-chip module, and the results are also presented in Figure 16. As can be seen, the error is decreased by a factor of 2, but not fully cancelled as it was demonstrated in the case of a single chip module. The previously developed models are adapted and used in the next section to explain this observation.
The process of temperature estimation was reproduced using the electrical models previously developed. The parameters A(Tji) and B(Tji) were identified based on the calibration data at low current using (1). For every value of ∆R3 and corresponding previously estimated temperature, the equivalent Von was derived using (3) for a total current of 10 A. The equivalent Von was used together with the parameters A and B at low current to estimate the equivalent temperature. The resulting estimation is shown in Figure 17.
The process of compensation was also mimicked using the models. The Eq. (2) was inversed to find the equivalent electrical resistance increase at high current and constant die temperature. This value was used to correct the calibration coefficient A at low current, and the equivalent temperature with compensation was estimated as also shown in Figure 17. The modelled compensated temperature shows a reduction of the error of a factor 2, in agreement with the experimental results.
In order to explain this partial compensation, the equivalent resistance increase at low current and real measured temperatures is computed. For each value of ∆R3 and of estimated individual temperatures, Von is calculated using (3). The Von increase is used to obtain the ∆Req increase at low current and to estimate the temperature.
The estimations of ∆Req at low current and at high current are in Figure 18. It can be seen that the ∆Req at low current is around double that of ∆Req at high current, mostly due to the differences in linearized static characteristics. For instance, in the low-current region, the dI/dV is lower (A is larger) and the result is a lower current unbalance, leading to more current in the degraded die, and a higher ∆Req. This is particularly enhanced by the experimental protocol consisting of cutting the wire-bonds of the same die 3, which leads to a high current unbalance.
Overall, the temperature estimates obtained directly through experimental measurement of Von and obtained with the models are plotted in Figure 19. The experimental and model results match relatively well. The description of mechanisms involved during the temperature estimation without and with compensation are thus well covered by the models. It is important to note that the scenario of sectioning the wire-bonds of a single die is a particular case, that leads to high current unbalances, and as a result, of low performance of the compensation due to very different estimations of ∆Req. In a more realistic scenario, less temperature unbalance and a higher performance of the compensation are expected.
This paper addresses the temperature distribution and estimation in a multi-chip wire-bonded power module subject to degradation. A controlled and reproducible experimental protocol is used. First, it is shown that the degradation of the top-side connection of a specific die leads to the redistribution of the current towards healthy dies, and consequently tends to decrease its temperature. This negative feedback is modelled in this paper. It tends to equilibrate the lifetime of the different dies even in the presence of an initial imbalance. Second, Von at low load current as a TSEP under-estimates the equivalent temperature when the degradation propagates. A method of re-calibration based on the estimation at high current of the equivalent electrical resistance increase reduces the error of a factor of 2. This imperfect compensation is due to the different conditions during the phases of degradation estimation and temperature estimation. The obtained results should be considered as a worst-case, since the experimental protocol favours a high degradation unbalance.
In the future, it is first necessary to improve the temperature estimation method based on Von. Research directions includes correcting the measured electrical resistance increase with models, or defining more efficient ways to perform calibration, for example that include compensation. It is also necessary to develop technologies to assess and eventually control the temperature of each die individually, which is proposed in [8] and will offer benefits in condition monitoring and reliability. Finally, the understanding of fault propagation in complex multi-chip systems will be useful to interpret power cycling results. It will contribute to design for reliability, health monitoring, diagnostics and prognostics of power electronic systems.
The authors declare that there is no conflict of interest.
[1] |
Bryant A, Yang S, Mawby P, et al. (2011) Investigation Into IGBT dV/dt During Turn-Off and Its Temperature Dependence. IEEE T Power Electr 26: 3019-3031. doi: 10.1109/TPEL.2011.2125803
![]() |
[2] | Lutz J, Schlangenotto H, Scheuermann U, et al. (2011) Semiconductor power devices: Physics, characteristics, reliability. Berlin, Heidelberg: Springer Berlin Heidelberg. |
[3] | Degrenne N, Mollov S (2018) Experimentally-Validated Models of On-State Voltage for Remaining Useful Life Estimation and Design for Reliability of Power Modules. CIPS 2018. |
[4] | Degrenne N, Ewanchuk J, David E, et al. (2015) A review of prognostics and health management for power semiconductor modules. Proceedings of the Annual Conference of the Prognostics and Health Management Society, PHM. |
[5] | Piton M, Chauchat B, Servière JF (2018) Implementation of direct Chip junction temperature measurement in high power IGBT module in operation-Railway traction converter. Microelectron Reliab 88: 1305-1310. |
[6] |
Avenas Y, Dupont L, Khatir Z (2012) Temperature Measurement of Power Semiconductor Devices by Thermo-Sensitive Electrical Parameters-A Review. IEEE T Power Electr 27: 3081-3092. doi: 10.1109/TPEL.2011.2178433
![]() |
[7] | Brandelero J, Ewanchuk J, Degrenne N, et al. (2018) Lifetime extension through Tj equalisation by use of intelligent gate driver with multi-chip power module. Microelectron Reliab 88: 428-432. |
[8] | Degrenne N, Mollov S (2019) Robust On-line Junction Temperature Estimation of IGBT Power Modules based on Von during PWM Power Cycling. 2019 IEEE International Workshop on Integrated Power Packaging (IWIPP). |
[9] | Degrenne N, Mollov S (2018) On-line Health Monitoring of Wire-Bonded IGBT Power Modules using On-State Voltage at Zero-Temperature-Coefficient. In PCIM 2018. |
1. | N. Degrenne, R. Delamea, S. Mollov, 2020, Temperature Evolution as an effect of Wire-bond Failures in a Multi-Chip IGBT Power Module, 978-9-0758-1536-8, P.1, 10.23919/EPE20ECCEEurope43536.2020.9215944 | |
2. | Cuili Chen, Volker Pickert, Maher Al-Greer, Zhiqiang Wang, Alois Christian Knoll, Temperature distribution in multichip IGBT module and its impact on collector current sharing, 2023, 143, 00262714, 114935, 10.1016/j.microrel.2023.114935 | |
3. | P. Loganathan, P. Selvam, Amalgam Illogical Controller Design Using Amended Moth System for Heat Reduction in Insulated Gate Bipolar Transistor, 2022, 16, 1998-0159, 67, 10.46300/9102.2022.16.11 | |
4. | P. Loganathan, P. Selvam, Amalgam illogical controller design using amended moth system for heat reduction in insulated gate bipolar transistor, 2022, 135, 00262714, 114576, 10.1016/j.microrel.2022.114576 |