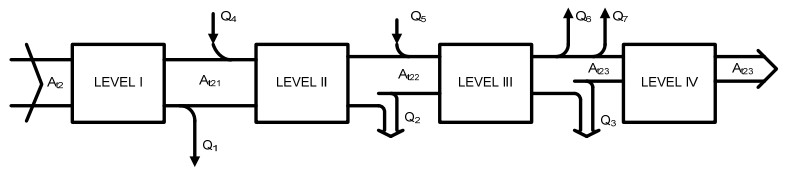
Citation: Janusz Wojdalski, Magdalena Krajnik, Piotr F. Borowski, Bogdan Dróżdż, Adam Kupczyk. Energy and water efficiency in the gelatine production plant[J]. AIMS Geosciences, 2020, 6(4): 491-503. doi: 10.3934/geosci.2020027
[1] | Piotr F. Borowski . Nexus between water, energy, food and climate change as challenges facing the modern global, European and Polish economy. AIMS Geosciences, 2020, 6(4): 397-421. doi: 10.3934/geosci.2020022 |
[2] | Kimon Kardakaris, Dimitrios N Konispoliatis, Takvor H Soukissian . Theoretical evaluation of the power efficiency of a moored hybrid floating platform for wind and wave energy production in the Greek seas. AIMS Geosciences, 2023, 9(1): 153-183. doi: 10.3934/geosci.2023009 |
[3] | Alan K Betts . Climate change and society. AIMS Geosciences, 2021, 7(2): 194-218. doi: 10.3934/geosci.2021012 |
[4] | Seyed Hossein Hashemi, Abas Niknam, Amir Karimian Torghabeh, Nuno Pimentel . Thermodynamic and geochemical studies of formation water in Rag-e Sefid oil and gas field, Iran. AIMS Geosciences, 2023, 9(3): 578-594. doi: 10.3934/geosci.2023031 |
[5] | Maurizio Iaccarino . Why there is water scarcity. AIMS Geosciences, 2021, 7(3): 529-541. doi: 10.3934/geosci.2021030 |
[6] | Joseph J. Kelly, Christopher I. McDermott . Numerical modelling of a deep closed-loop geothermal system: evaluating the Eavor-Loop. AIMS Geosciences, 2022, 8(2): 175-212. doi: 10.3934/geosci.2022011 |
[7] | Hongmei Yin, Mohamed E Zayed, Ahmed S Menesy, Jun Zhao, Kashif Irshad, Shafiqur Rehman . Present status and sustainable utilization of hydrothermal geothermal resources in Tianjin, China: a critical review. AIMS Geosciences, 2023, 9(4): 734-753. doi: 10.3934/geosci.2023039 |
[8] | Ayesha Nadeem, Muhammad Farhan Hanif, Muhammad Sabir Naveed, Muhammad Tahir Hassan, Mustabshirha Gul, Naveed Husnain, Jianchun Mi . AI-Driven precision in solar forecasting: Breakthroughs in machine learning and deep learning. AIMS Geosciences, 2024, 10(4): 684-734. doi: 10.3934/geosci.2024035 |
[9] | Jianzhao Yin, Haoyu Yin, Yuhong Chao, Hongyun Shi . Energy and tellurium deposits. AIMS Geosciences, 2024, 10(1): 28-42. doi: 10.3934/geosci.2024002 |
[10] | Angel Paniagua . Use and abuse of the planet in non-rich regions: histories of fracking and windmills in a more than human geographical perspective. AIMS Geosciences, 2022, 8(1): 1-15. doi: 10.3934/geosci.2022001 |
Abbreviations: ee CO2: CO2 emissions per 1 kW·h of generated electrical energy (0.90–1.02 kg CO2/ kW·h); ete CO2: CO2 emissions associated with gas fuel combustion (55.82 kg/GJ); An: energy consumption; Ate: monthly consumption of thermal energy (Ate = BrzQrw·10-6), GJ; Ae: monthly active electricity consumption, kW·h/month; At1: total energy consumption (including conversion factor 1 kW·h = 0.012 GJ), GJ; At2: total energy consumption (including conversion factor 1 kW·h = 0.0036 GJ), GJ; Aw: monthly water consumption, m3; Brz: monthly real fuel consumption (fuel gas), m3; Ee CO2 = We·ee CO2: Specific CO2 emission associated with electricity generation in the plant kg CO2/Mg of product; Ete CO2 = Wte·ete CO2: Specific CO2 emission associated with gas fuel combustion in the plant kg CO2/Mg of product; EEe: efficiency of electricity consumption, [kg of product/kW·h]; EEse: efficiency of consumption of steam equivalent [kg of product/Mg]; EEte: efficiency of thermal energy consumption [kg of product/GJ]; EW: water consumption efficiency [kg of product/m3]; K: relations between production and the number of employees, [Mg gelatine/person]; K1: cubature of production space of the plant for Mg of gelatine, [m3/Mg]; Km: installed capacity of electrical devices on Mg of produced gelatine per 24h, (Km = P∙Zd−1) kW/Mg of product; P: installed capacity of electrical appliances, kW; r: correlation coefficient; R2: coefficient of determination (r2·100%); Qce: calorific value of fuel equivalent, 29.3076 MJ/kg c.e.; Qn: energy streams; Qse: energy value of water vapour (steam) equivalent, 2.6796 MJ/kg s.e.; Qrw: real fuel calorific value, MJ/m3, GJ/m3; Wst: specific steam consumption in the plant, GJ/Mg of product; Wte: specific heat consumption in the plant, GJ/Mg of product; We: specific electrical energy consumption in the plant, kW·h/Mg of product; Wce1: specific consumption of equivalent fuel, taking into account the relation 1 kW·h = 0.012 GJ, kg c.e./Mg of product; Wce2: specific equivalent fuel consumption, calculated based on 1 kW·h = 0.0036 GJ, kg c.e./Mg of product; Wse: specific steam equivalent consumption in the plant, kg/Mg of product; Wrs: specific actual steam consumption, kg/Mg of product; Wr1: overall specific energy consumption contained in real fuel (calculated based on 1 kW·h = 0.012 GJ), GJ/Mg of product; Wr2: overall specific energy consumption contained in real fuel (calculated based on 1 kW·h = 0.0036 GJ), GJ/Mg of product; Wt1: overall specific energy consumption (calculated based on 1 kW·h = 0.012 GJ), GJ/Mg of product; Wt2: overall specific energy consumption (calculated based on 1 kW·h = 0.0036 GJ), GJ/Mg of product; Ww: specific water consumption for the monthly period (Ww = Aw·Z−1), m3/Mg of product; Zm: monthly production of gelatine, Mg; Z24: daily production of gelatine, Mg; η: energy transformation ratio; ηb: efficiency of the steam boiler
The agri-food industry is highly dependent on the extraction of fossil fuels and contributes significantly to greenhouse gas emissions. The world population is also growing and the demand for food is expected to increase by 60% by 2050 [1] while at the same time water consumption will increase and the demand for energy (including electricity) [2]. For people managing the company, the effectiveness of the company's operation is an important issue. Efficiency can be considered, inter alia, as production efficiency or as energy efficiency. Production efficiency is defined as the result of economic (industrial) activity which is the quotient of the obtained effect to the expenditure. Energy efficiency is expressed analogously or can be defined as a reduction in energy consumption. The reduction in energy consumption takes place at the stage of production (transformation), transmission, distribution or end use, mainly as a result of changes in technology. The use of innovative technological solutions that provide the same or higher level of production or services [3] has a positive impact on the enterprise and its environment [2]. One of the possibilities of expressing energy efficiency is the energy consumption of production, i.e. energy demand to carry out a specific production process. It is closely related to eco-efficiency consisting in achieving high environmental results consisting in reducing the consumption of natural resources, reducing emissions of environmental pollutants and reducing the mass of generated waste [4,5]. Gelatin is an important biopolymer used in food to improve flexibility, consistency and structural stability. It can be obtained not only from the skin and bones of land animals, but also from fish and insects. Two methods are usually used in the production of gelatine: acidic and alkaline to obtain gelatin A type and B type respectively [6]. The raw materials for the production of gelatine are post-production waste from the food industry in the meat, poultry and fish industries. Pork gelatins are the most popular and widely used, but they are subject to severe limitations and skepticism among consumers due to socio-cultural and health problems [7]. Gelatin and gelling agents improve the quality and shelf life of stored food products [8,9]. Gelatin-based products can be used as foils for packing various products to reduce the negative impact on the environment [10,11]. Issues related to the production of gelatine (health, cultural, religious issues) based on various raw materials (mammals, fish, poultry, insects) and the possibility of its wide use in the economy are issues that constitute a research area in many academic centers [12,13,14]. An example of obtaining gelatine from tuna skin on a laboratory and industrial scale is presented in the work of Montero [15]. Meyer presented the processing of collagen-based biomaterials and the properties of the obtained materials [16].
The consumption of energy carriers in rendering plants depends on many factors, the most common of which are the physical and chemical properties of the processed raw material, production technology [12,17,18]. The literature also mentions numerous applications of gelatin in the food, pharmaceutical and electronic industries [7,19,20]. The purified and demineralized gelatin solution consists of more than 95% water. As a rule, concentration takes place in a multi-stage vacuum system with the use of plate, circulation or thin-film evaporators. Dried gelatine has a residual water content of 10–12% and has a long shelf life from a microbiological point of view [21]. The strong influence of pre-treatment and extraction conditions on the yield and properties of fish gelatine need to be taken into consideration in an industrial setting, and usually a compromise between yield, desired properties, and energy efficiency needs to be considered for optimal production [22]. The set of requirements and principles aimed at effective environmental protection in accordance with the requirements of the best available production technique is included in the document [23]. Although the discussed issues are devoted to sample publications [21,24,25,26], many issues related to the production process in the plant in operational terms have not been fully explained. Therefore, it is new to explain the reasons for the variability in the consumption of energy and water, especially the impact of the production volume, the degree of mechanization of production operations and the degree of capacity utilization on energy and water consumption. The aim of the study was to determine the efficiency of energy and water management in a gelatine production plant. The literature review shows that so far no studies have been carried out on energy and water consumption, taking into account the general characteristics of the production plant. In addition, the work was to provide materials helpful for the construction of models of plants in this industry as energy users and the search for the relationship between the adopted independent variable—the amount of gelatine production and the demand for energy carriers that may be one of the elements of the analysis of production efficiency. It is also an innovation compared to the method presented in [27].
Research materials were collected in 2019 at a rendering plant that produces pork gelatin for food and pharmaceutical purposes. Direct measurements of energy and water consumption were carried out and the production volume was obtained from the plant's accounts. The plant employs 144 people, including 120 production workers. The total area of the enterprise is 53,000 m2. The cubature of all working space is 32,350 m3, including production space—21,456 m3. The monthly production volume of Zm gelatine was within the range of 565.2–631.3 Mg, the average daily Zd is about 18.5 Mg. The total installed electric power of rendering plant P was 1150 kW.
Figure 1 shows the levels of energy transformation in the plant. The scope of the research carried out covered the total consumption of energy and water at level I. Level II covers the transformation of energy carriers. On level Ⅲ, there are energy and water receivers in the waste processing line for meat production and gelatine production.
Figure 2 shows the most important processes that are implemented at level Ⅲ, which make up the gelatine production technology in the examined plant. From the point of view of energy consumption and energy efficiency of production, the aim should be to maximize the value of At23 (at level IV, Figure 1) as the so-called energy input, i.e. simultaneously strive to increase the total energy transformation coefficient ηIII = At23/At2.
Previous studies most often present the consumption of heat or electricity separately at level Ⅲ [22,28,29]. It should be noted that from the point of view of costs and the choice of a specific technology, it is important to use the cumulative energy consumption of a product or an indicator that would include the total energy consumption both in the production plant (At2) as well as converted to primary energy (At1). For this purpose, the following indicators of specific energy consumption were adopted:
Wt1=At1Z=0,012⋅Ae+Brz⋅Qrw⋅10−6Z GJ /Mg of gelatine | (1) |
Wt2=At2Z=0,0036⋅Ae+Brz⋅Qrw⋅10−6Z GJ / Mg of gelatine | (2) |
In the formula above, At2 is the total energy consumption entered into level Ⅰ.
The above energy consumption rates were converted into fuel equivalent (Wce) or water vapor (steam) equivalent (Wse) rates using the following formulas:
Wcel=Wt1/Qce=3412.08⋅10−2Wt1 | (3) |
Wce2=Wt2/Qce=3412.08⋅10−2Wt2 | (4) |
Wse=Wte/Qse=373.19⋅Qse⋅Wte | (5) |
At the same time, the Wce1 and Wce2 indices were converted into energy that can be obtained, for example, from renewable sources, using the following formulas expressing the specific actual fuel consumption rates Wr1 and Wr2.
Wr1=Wt1/Qrw | (6) |
Wr2=Wt2/Qrw | (7) |
The inverse of the energy and water consumption indicators are the corresponding energy and water consumption efficiency indicators.
It was assumed that the production volume (Z) influences the consumption of energy carriers in a production plant. This factor was adopted due to the greatest suitability for the assessment of the environmental impact of plants in this industry and determination of the best available production techniques [25,30].
In order to explain the dependence of energy carrier consumption (A) on the independent variable (Z)—which is the actual value observed in practice, the following equation was adopted:
A=b+aZ | (8) |
in which: A—consumption of energy carriers (dependent variable—Ae, Ac, Aw, We, Wc, Ww), Z—production volume (independent variables; Zm or Z24).
Under the conditions:
aZ≥b and Z≥0 | (9) |
The application of the obtained regression equations [31] taking into account the correlation and determination coefficients (r and R2) allows to partially explain the discussed problem in the analyzed gelatine production plant.
The Table 1 presents the ranges of technical and organizational indicators characterizing the tested plant. The Km, K1 and K indices express the relationship between the technical equipment and the production volume as well as the number of employees in the production departments of the plant. The K index can also be partially used to evaluate the production efficiency of an entire production plant.
Lp | Indicator | Unites of measure | Range | |
Minimum | Maximum | |||
1 | K | Mg gelatine/person | 0.156 | 0.175 |
2 | K1 | m3production space/Mg gelatine | 1.132 | 1.265 |
3 | Km | kW/Mg gelatine | 52.5 | 68.0 |
In order to achieve the aim of the study, a model of the agri-food industry plant as a user of energy carriers was used, as well as company indices of unit consumption of energy and water carriers defined in the methodology presented in publications on other sectors of the agri-food industry [32,33]. The average value of the Km index for the daily period was 62.2 kW/Mg.
The obtained research results refer to the production conditions specified in Table 1 and may be important for industrial practice. Technological innovations implemented in the enterprise reduce energy and water consumption at level Ⅲ (Figure 1). The energy intensity of production and water consumption indicators included in the paper are factors used to assess the functioning of the whole production plant covering level I (Figure 1). These indicators include the consumption of energy carriers for production and non-production purposes, losses and operating conditions. It is an innovative approach in relation to previous studies, as it covers not only the production process, but the entire operation of the plant.
Table 2 shows the ranges of variability in the consumption of energy carriers during the annual period.
Dependent variable, indicators | Range | Medium | ||
Electricity | We [kW∙h/Mg gelatine] | 1154.9–1202.7 | 1174.8 | |
EE [kg gelatine/kW∙h] | 0.831–0.866 | 0.851 | ||
Thermal energy | Wte [GJ/Mg gelatine] | 20.16–24.66 | 22.39 | |
EEte [kg gelatine /GJ] | 40.55–49.60 | 44.66 | ||
Equivalent water vapour | Wse [kg vapour/Mg gelatine] | 7523–9202 | 8355 | |
EEse [kg gelatine/Mg vapour] | 108.7–132.9 | 119.7 | ||
Total energy | Wt1 [GJ/Mg gelatine] | 34.02–39.09 | 36.49 | |
Wt2 [GJ/Mg gelatine] | 24.32–28.99 | 26.62 | ||
Fuel equivalent | Wce1 [kg/Mg gelatine] | 1160.8–1333.8 | 1245.0 | |
Wce2 [kg/Mg gelatine] | 829.8–989.1 | 908.3 | ||
CO2 emissions | Ee CO2 [kg CO2/Mg of gelatin] | 1107–1154 | 1127 | |
Ete CO2 [kg CO2/Mg of gelatin] | 1065–1303 | 1183 | ||
Water | Ww [m3/Mg of gelatine] | 10.23–25.84 | 18.97 | |
EW [kg gelatine/m3] | 38.7–97.8 | 52.7 |
The average unit electricity consumption We (Table 2) in particular months showed seasonal fluctuations amounting to over 4%. Unit heat energy consumption Wte in extreme cases differed from each other by approx. 22%. Unit water consumption showed the greatest differentiation (approx. 2.5 times). Assuming daily or monthly periods, regression equations were obtained expressing the variability of energy and water consumption presented in Table 3. Only equations for which regression was significant were taken into account.
Regression equation | The range of variability of production Z | Correlation coefficient r | Coefficient R2 = r2∙100% |
Ae = 1424.4 Zm − 147450 | 565.2–631.3 | 0.878 | 77.3 |
Ac = 21.986Z24 + 7.6436 | 16.9–21.9 | 0.791 | 62.6 |
Aw = 95.655Z24 − 1439.1 | 16.9–21.9 | 0.883 | 77.9 |
Ww = 3.8879 Z24 – 54.464 | 16.9–21.9 | 0.818 | 67.0 |
EW= −13.561Z24 + 320.74 | 16.9–21.9 | 0.612 | 37.42 |
The production volume Zm in approximately 77.3% influenced the consumption of electric energy Ae, and the consumption of heat energy in 62.6%. It was also shown that the variability of water consumption was in 77.9% conditioned by the volume of gelatine production.
The obtained results were compared with the data contained in the work [21] in which the consumption of energy carriers for gelatine production with the use of various technologies was investigated. As a result of the conducted research, it was observed that depending on the technology used, different amounts of energy and water are required. The lowest consumption was in the production of pork gelatine using the acid method. The production of 1 kg of gelatine required the supply of 20–25 kg of steam, 3–5 kW·h of electricity and approximately 150 dm3 of water. In the case of the alkaline technology with the use of animal skin, the water requirement increased to approximately 400 dm3/kg of gelatine. According to [17,18], the energy consumption of the production of rendering plants (expressed by the We index) is on average 100–2000 kW∙h /Mg of raw material. Water vapour (steam) consumption is Wrs = 0.9–1.3 Mg/Mg of raw material (with the efficiency of a steam boiler η = 0.5–0.6, located at level Ⅱ). The unit water consumption rate Ww was 7–65 m3/Mg of the final product. The conducted research shows that the unit consumption of electricity and real steam was significantly lower than the data in the literature, as it accounted for 50–60% of the numerical values of these indicators included in the quoted literature. Water consumption per product unit was within the limits for these indicators mentioned in the cited literature. The reduced unit energy consumption could have been influenced by the increased technological progress and the application of energy-saving production technology and apparatus at levels Ⅱ and Ⅲ. Generally speaking, the reduced energy consumption resulted from the increased utilization of the processing capacity, which at the same time increased the production efficiency in the examined plant. The energy consumption was also conditioned by the seasonality of the plant’s operation. The correlation coefficients “r” listed in Table 3 prove the existence of secondary (side), non-production energy consumption Q1–Q3, Q6 and Q7. Streams Q4 and Q5 represent energy recovery.
Referring also to the works [23,26], the results of the presented research, partially answer the question of how to optimize the efficiency of gelatine production in terms of energy and water consumption. The efficiency of thermal energy consumption (EEte) in individual months differed by 22.3%. There was no significant correlation between the volume of gelatin production and the EEte index. The observations of the production course also lead to the conclusion that reducing the energy consumption of the compaction process and other thermal treatment processes (at level Ⅲ, Figure 1), may reduce Q3 losses and increase the efficiency of energy transformation ηIII = At23/At22 at the same time. As a result, the coefficient η and the efficiency of heat energy consumption EEte will also increase.
In turn, the specific water consumption of Ww could have been influenced by the use of closed circuits. The indicators presented in Table 2 may be used in the analysis of a production plant’s environmental impact.
As a result of the conversion of the Wt1 and Wt2 indices, taking into account the calorific values of various fuels contained in the literature [34], Table 4 shows the consumption of the above-mentioned energy carriers (real fuel). Calorific valueQrwexpressed in GJ/kg of real fuel was used for the calculations.
Energy carriers | Calorific value Qrw, [MJ/kg] | Individual fuel consumption indicators | |
Wr1 [kg/Mg gelatine] | Wr2 [kg/Mg gelatine] | ||
Lignite | 14.0 | 2606.4 | 1901.4 |
Coal | 26.0 | 1403.5 | 1023.8 |
Natural gas | 32.0 | 1140.3 | 831.9 |
Heating oil | 42.6 | 856.6 | 624.9 |
Vegetable oil | 37.5 | 973.1 | 65.6 |
Liquid flammable waste | 37.2 | 980.9 | 715.6 |
Wheat straw | 17.3 | 2109.2 | 1538.7 |
Barley straw | 16.1 | 2266.4 | 1653.4 |
Corn straw | 16.8 | 2172.0 | 1584.5 |
Rapeseed straw | 15.0 | 2432.7 | 1774.7 |
Wood dust | 17.0 | 2146.5 | 1565.9 |
Scobs | 19.3 | 1890.7 | 1379.3 |
Willow chips | 16.5 | 2211.5 | 1613.3 |
Pelets | 18.0 | 2027.2 | 1478.9 |
Straw briquettes | 17.1 | 2133.9 | 1556.7 |
Wood briquettes | 18.0 | 2027.2 | 1478.9 |
From the point of view of energy production from fossil fuels and next reducing energy consumption, it is very important to use alternative fuels properly. Selected figures included in Table 4 may be important when analyzing the possibility of replacing traditional fuels with energy from renewable sources. In individual cases, the efficiency of transformation of a given carrier into thermal energy should be taken into account, especially at level Ⅱ. The results contained in the study can be used for comparison with other plants in the gelatine production industry [7,8,35,36,37,38,39,40,41] as well as supplement the knowledge on the use of energy from renewable sources in other sectors of the food industry [30,32,33,42,43,44]. The nexus of energy and water consumption in industrial production is an important issue in the sustainable development of the economy [45] and the nexus between water-energy-food is being used to indicate the importance of managing them together [46].
In the analyzed plant, the energy consumption indicators had lower values as compared to the cited literature (lower even 50–60%). This was due to the increased use of the existing processing capacity. These results showed that it is possible to reduce energy consumption through better management of the technological process. The obtained results allow for the conclusion that it is possible to reduce the negative impact on the environment (lower energy demand, more effective water management) and to reduce the plant operating costs. Moreover, these results lead to the conclusion that after the implementation of technological innovations, it will be possible to further reduce energy consumption. As we can observe, the technical aspects are important as well as economic and ecological aspects. At management techniques in combination with the current production volume.
The presented results can be used to define environmental standards or their verification as well as to implement the principles of cleaner production as they relate to the existing organizational and production conditions as well as the degree of use of the installed power of electrical devices. It has been demonstrated and justified that on the micro-scale it is possible to introduce the nexus water-energy-food. Moreover, the indicators included in the work can be used to estimate the production costs and the emission of pollutants into the atmosphere and the pollutant load into the waters. In the same time, the unit water consumption proves the high eco-efficiency of using this medium. Therefore, as recommendation for company managers, justifies active monitoring as one of the best energy.
In the future, further research could be focused on reducing energy consumption in the evaporation and drying process at the level Ⅲ, as these are high-energy processes. In addition, it is worth exploring the possibilities of energy recovery from processes at the level Ⅱ. It also will be important to pay attention to the overall reduction of water consumption in the enterprise.
All authors declare no conflicts of interest in this paper.
[1] |
Ladha-Sabur A, Bakalis S, Fryer PJ, et al. (2019) Mapping energy consumption in food manufacturing. Trends in Food Sci Technol 86: 270-280. doi: 10.1016/j.tifs.2019.02.034
![]() |
[2] |
Borowski PF (2020) Zonal and Nodal Models of Energy Market in European Union. Energies 13: 4182. doi: 10.3390/en13164182
![]() |
[3] |
Giacone E, Mancò S (2012) Energy efficiency measurement in industrial processes. Energy 38: 331-345. doi: 10.1016/j.energy.2011.11.054
![]() |
[4] | Prasad P, Pagan R, Kauter M, et al. (2004) Eco-efficiency for the Dairy Processing Industry. Environmental Management Centre, The University of Queensland, St Lucia, 43-48, 57-66. |
[5] |
Jayathilakan K, Sultana K, Radhakrishna K, et al. (2012) Utilization of byproducts and waste materials from meat, poultry and fish processing industries: a review. J Food Sci Technol 49: 278-293. doi: 10.1007/s13197-011-0290-7
![]() |
[6] | Mariod AA, Fadul H (2013) Gelatin, source, extraction and industrial applications. Acta Sci Po Technol Aliment 12: 135-147. |
[7] |
Karim AA, Bhat R (2009) Fish gelatin: properties, challenges, and prospects as an alternative to mammalian gelatins. Food Hydrocolloids 23: 563-576. doi: 10.1016/j.foodhyd.2008.07.002
![]() |
[8] | Poppe J (1992) Gelatin. In Imeson AP, Thickening and gelling agents for food. Springer, Boston, MA, 98-101. |
[9] |
Schieber A, Stintzing FC, Carle R (2001) By-products of plant food processing as a source of functional compounds—recent developments. Trends Food Sci Technol 12: 401-413. doi: 10.1016/S0924-2244(02)00012-2
![]() |
[10] |
Etxabide A, Leceta I, Cabezudo S, et al. (2016) Sustainable fish gelatin films: From food processing waste to compost. ACS Sustainable Chem Eng 4: 4626-4634. doi: 10.1021/acssuschemeng.6b00750
![]() |
[11] | Senevirathne M, Kim SK (2012) Utilization of seafood processing by-products: medicinal applications. In Advances in food and nutrition research. Academic Press, 65: 495-512. |
[12] |
Wasswa J, Tang J, Gu X (2007) Utilization of fish processing by-products in the gelatin industry. Food Rev Int 23: 159-174. doi: 10.1080/87559120701225029
![]() |
[13] |
Abedinia A, Nafchi AM, Sharifi M, et al. (2020) Poultry gelatin: Characteristics, developments, challenges, and future outlooks as a sustainable alternative for mammalian gelatin. Trends Food Sci Technol 104: 14-26. doi: 10.1016/j.tifs.2020.08.001
![]() |
[14] |
Mirzapour-Kouhdasht A, Moosavi-Nasab M, Krishnaswamy K, et al. (2020) Optimization of gelatin production from Barred mackerel by-products: Characterization and hydrolysis using native and commercial proteases. Food Hydrocolloids 108: 105970. doi: 10.1016/j.foodhyd.2020.105970
![]() |
[15] |
Montero M, Acosta ÓG (2020) Tuna skin gelatin production: optimization of extraction steps and process scale-up. CyTA-J Food 18: 580-590. doi: 10.1080/19476337.2020.1801849
![]() |
[16] |
Meyer M (2019) Processing of collagen based biomaterials and the resulting materials properties. Biomed Eng Online 18: 24. doi: 10.1186/s12938-019-0647-0
![]() |
[17] |
da Trindade Alfaro A, Balbinot E, Weber CI, et al. (2015) Fish gelatin: Characteristics, functional properties, applications and future potentials. Food Eng Rev 7: 33-44. doi: 10.1007/s12393-014-9096-5
![]() |
[18] | See SF, Hong PK, Ng KL, et al. (2010) Physicochemical properties of gelatins extracted from skins of different freshwater fish species. Int Food Res J 17: 809-816. |
[19] | Gelatin Manufactureres Institute of America (2019) Gelatin Handbook. Available from: http://www.gelatin-gmia.com/uploads/1/1/8/4/118450438/gmia_gelatin_manual_2019.pdf. |
[20] |
Zhang XP, Ye TY, Meng XH, et al. (2020) Sustainable and Transparent Fish Gelatin Films for Flexible Electroluminescent Devices. ACS nano 14: 3876-3884. doi: 10.1021/acsnano.9b09880
![]() |
[21] | Schrieber R, Gareis H (2007) Gelatine handbook: theory and industrial practice. Wiley-VCH, 96-97 |
[22] |
Milovanovic I, Hayes M (2018) Marine Gelatine from rest raw materials. Appl Sci 8: 2407. doi: 10.3390/app8122407
![]() |
[23] | EC (2005) Integrated Pollution Prevention and Control Reference Document on Best Available Techniques in the Slaughterhouses and Animal By-products Industries, 141-145. Available from: https://eippcb.jrc.ec.europa.eu/sites/default/files/2020-01/sa_bref_0505.pdf. |
[24] | WS Atkins International (1998) Ochrona środowiska w przemyśle rolno-spożywczym. Standardy środowiskowe. FAPA, Warszawa, 32-36, 85-89,105-108. |
[25] | Cavey A, Eyars R, Hill S, et al. (1998) Ochrona środowiska w przemyśle utylizacyjnym, Wyd. FAPA, Warszawa, 18-21. |
[26] | Gündem A, Tarhan Ö (2020) Extraction of collagen and gelatine from animal wastes. Bull Biotechnol 1: 30-33. |
[27] |
Muller DCA, Marechal FMA, Wolewinski T, et al. (2007) An energy management method for the food industry. Appl Therm Eng 27: 2677-2686. doi: 10.1016/j.applthermaleng.2007.06.005
![]() |
[28] | Cole C (2000) Gelatin. In Frederick FJ, Encyclopedia of Food Science and Technology, 2: 1183. |
[29] |
Ma Y, Zeng X, Ma X, et al. (2019) A simple and eco-friendly method of gelatin production from bone: One-step biocatalysis. J Cleaner Prod 209: 916-926. doi: 10.1016/j.jclepro.2018.10.313
![]() |
[30] | Wojdalski J, Dróżdż B, Lubach M (2007) Factors influencing energy consumption in fruit and vegetable processing plants. TEKA Kom Mot Energ Roln-OL PAN 7: 277-285. |
[31] |
Abonyi J, Kulcsar T, Balaton M, et al. (2014) Energy monitoring of process systems: time-series segmentation-based targeting models. Clean Technol Environ Policy 16: 1245-1253. doi: 10.1007/s10098-014-0808-6
![]() |
[32] |
Wojdalski J, Dróżdż B, Grochowicz J, et al. (2013) Assessment of energy consumption in a meat-processing plant—a case study. Food Bioprocess Technol 6: 2621-2629. doi: 10.1007/s11947-012-0924-4
![]() |
[33] |
Wojdalski J, Grochowicz J, Dróżdż B, et al. (2015) Energy efficiency of a confectionery plant-Case study. J Food Eng 146: 182-191. doi: 10.1016/j.jfoodeng.2014.08.019
![]() |
[34] | Niedziółka I, Zuchniarz A (2006) An energetic analysis of selected plant biomass samples (in Polish: Analiza energetyczna wybranych rodzajów biomasy pochodzenia roślinnego). MOTROL, Motoryzacja i Energetyka Rolnictwa. Lublin, tom 8A, 232-237. |
[35] |
Keijzers G (2002) The transition to the sustainable enterprise. J Cleaner Prod 10: 349-359. doi: 10.1016/S0959-6526(01)00051-8
![]() |
[36] | Kolomaznik K, Janacova D, Solc J, et al. (2011) Mathematical modeling of gelatine production processes. In Proceedings of the 13th WSEAS international conference on Mathematical and computational methods in science and engineering. World Scientific and Engineering Academy and Society (WSEAS), 317-321. |
[37] |
Makarichi L, Jutidamrongphan W, Techato KA (2018) The evolution of waste-to-energy incineration: A review. Renewable Sustainable Energy Rev 91: 812-821. doi: 10.1016/j.rser.2018.04.088
![]() |
[38] | Mariod AA, Adam HF (2013) Review: gelatin, source, extraction and industrial applications. Acta Sci Pol Technol Aliment 12: 135-147. |
[39] |
Meyer M, Trommer K (2015) Soft collagen-gelatine sponges by convection drying. Braz Arch Biol Technol 58: 109-117. doi: 10.1590/S1516-8913201400139
![]() |
[40] |
Mokrejs P, Langmaier F, Mladek M, et al. (2009) Extraction of collagen and gelatine from meat industry by-products for food and non food uses. Waste Manage Res 27: 31-37. doi: 10.1177/0734242X07081483
![]() |
[41] | Ableeva AM, Salimova GA, Rafikova NT, et al. (2019) Economic evaluation of the efficiency of supply chain management in agricultural production based on multidimensional research methods. Int J Sup Chain Mgt 8: 328-338. |
[42] | Wittich WJ (2005) New automated industrial technologies for improving chemical penetration of bovine pieces in the raw material processing and conditioning areas of gelatine manufacture. University of Canterbury, Christchurch, New Zealand. |
[43] |
Cascarosa E, Gea G, Arauzo J (2012) Thermochemical processing of meat and bone meal: A review. Renewable Sustainable Energy Rev 16: 942-957. doi: 10.1016/j.rser.2011.09.015
![]() |
[44] |
Kowalski Z, Krupa-Żuczek K (2007) A model of the meat waste management. Pol J Chem Technol 9: 91-97. doi: 10.2478/v10026-007-0098-4
![]() |
[45] |
Borowski PF (2020) Nexus between water, energy, food and climate change as challenges facing the modern global, European and Polish economy. AIMS Geosci 6: 397-421. doi: 10.3934/geosci.2020022
![]() |
[46] |
Tashtoush FM, Al-Zubari WK, Shah A (2019) A review of the water-energy-food nexus measurement and management approach. Int J Energy Water Res 3: 361-374. doi: 10.1007/s42108-019-00042-8
![]() |
1. | Piotr F. Borowski, Innovative Processes in Managing an Enterprise from the Energy and Food Sector in the Era of Industry 4.0, 2021, 9, 2227-9717, 381, 10.3390/pr9020381 | |
2. | Piotr F. Borowski, Digitization, Digital Twins, Blockchain, and Industry 4.0 as Elements of Management Process in Enterprises in the Energy Sector, 2021, 14, 1996-1073, 1885, 10.3390/en14071885 | |
3. | Rongjia Wang, Ziwu Guo, Chunju Cai, Jianfeng Zhang, Fangyuan Bian, Shiyong Sun, Qingbing Wang, Practices and roles of bamboo industry development for alleviating poverty in China, 2021, 1618-954X, 10.1007/s10098-021-02074-3 | |
4. | Feng-Fan Liao, Wun-Hwa Chen, Will the Management Structure of Energy Administrators Affect the Achievement of the Electrical Efficiency Mandatory Target for Taiwan Factories?, 2021, 14, 1996-1073, 2021, 10.3390/en14072021 | |
5. | Hail Jung, Jinsu Jeon, Dahui Choi, Jung-Ywn Park, Application of Machine Learning Techniques in Injection Molding Quality Prediction: Implications on Sustainable Manufacturing Industry, 2021, 13, 2071-1050, 4120, 10.3390/su13084120 | |
6. | Ghulam Mujtaba, Rifat Hayat, Qaiser Hussain, Mukhtar Ahmed, Physio-Chemical Characterization of Biochar, Compost and Co-Composted Biochar Derived from Green Waste, 2021, 13, 2071-1050, 4628, 10.3390/su13094628 | |
7. | Tomislav Gelo, Nika Šimurina, Jurica Šimurina, The Economic Impact of Investment in Renewables in Croatia by 2030, 2021, 14, 1996-1073, 8215, 10.3390/en14248215 | |
8. | Feng Wu, Xiaopeng Fu, Ting Zhang, Dan Wu, Stavros Sindakis, Examining Whether Government Environmental Regulation Promotes Green Innovation Efficiency—Evidence from China’s Yangtze River Economic Belt, 2022, 14, 2071-1050, 1827, 10.3390/su14031827 | |
9. | Ying Tan, Feng Hai, József Popp, Judit Oláh, Minimizing Waste in the Food Supply Chain: Role of Information System, Supply Chain Strategy, and Network Design, 2022, 14, 2071-1050, 11515, 10.3390/su141811515 | |
10. | Piotr F. Borowski, 2023, Chapter 6, 978-3-031-16597-9, 129, 10.1007/978-3-031-16598-6_6 | |
11. | Zixiang Weng, Shuiqin Lu, Xuekun Cheng, Chunyu Pan, Guangyu Wang, Dejin Dong, Zhengcai Li, Ziliang Zhao, Lei Gu, Linghui Dong, Zhengwen Niu, Chong Li, Lin Xu, Yufeng Zhou, Guomo Zhou, Greenhouse gas emissions and carbon and water footprints during processing of Lei bamboo shoots, 2024, 469, 09596526, 143110, 10.1016/j.jclepro.2024.143110 |
Lp | Indicator | Unites of measure | Range | |
Minimum | Maximum | |||
1 | K | Mg gelatine/person | 0.156 | 0.175 |
2 | K1 | m3production space/Mg gelatine | 1.132 | 1.265 |
3 | Km | kW/Mg gelatine | 52.5 | 68.0 |
Dependent variable, indicators | Range | Medium | ||
Electricity | We [kW∙h/Mg gelatine] | 1154.9–1202.7 | 1174.8 | |
EE [kg gelatine/kW∙h] | 0.831–0.866 | 0.851 | ||
Thermal energy | Wte [GJ/Mg gelatine] | 20.16–24.66 | 22.39 | |
EEte [kg gelatine /GJ] | 40.55–49.60 | 44.66 | ||
Equivalent water vapour | Wse [kg vapour/Mg gelatine] | 7523–9202 | 8355 | |
EEse [kg gelatine/Mg vapour] | 108.7–132.9 | 119.7 | ||
Total energy | Wt1 [GJ/Mg gelatine] | 34.02–39.09 | 36.49 | |
Wt2 [GJ/Mg gelatine] | 24.32–28.99 | 26.62 | ||
Fuel equivalent | Wce1 [kg/Mg gelatine] | 1160.8–1333.8 | 1245.0 | |
Wce2 [kg/Mg gelatine] | 829.8–989.1 | 908.3 | ||
CO2 emissions | Ee CO2 [kg CO2/Mg of gelatin] | 1107–1154 | 1127 | |
Ete CO2 [kg CO2/Mg of gelatin] | 1065–1303 | 1183 | ||
Water | Ww [m3/Mg of gelatine] | 10.23–25.84 | 18.97 | |
EW [kg gelatine/m3] | 38.7–97.8 | 52.7 |
Regression equation | The range of variability of production Z | Correlation coefficient r | Coefficient R2 = r2∙100% |
Ae = 1424.4 Zm − 147450 | 565.2–631.3 | 0.878 | 77.3 |
Ac = 21.986Z24 + 7.6436 | 16.9–21.9 | 0.791 | 62.6 |
Aw = 95.655Z24 − 1439.1 | 16.9–21.9 | 0.883 | 77.9 |
Ww = 3.8879 Z24 – 54.464 | 16.9–21.9 | 0.818 | 67.0 |
EW= −13.561Z24 + 320.74 | 16.9–21.9 | 0.612 | 37.42 |
Energy carriers | Calorific value Qrw, [MJ/kg] | Individual fuel consumption indicators | |
Wr1 [kg/Mg gelatine] | Wr2 [kg/Mg gelatine] | ||
Lignite | 14.0 | 2606.4 | 1901.4 |
Coal | 26.0 | 1403.5 | 1023.8 |
Natural gas | 32.0 | 1140.3 | 831.9 |
Heating oil | 42.6 | 856.6 | 624.9 |
Vegetable oil | 37.5 | 973.1 | 65.6 |
Liquid flammable waste | 37.2 | 980.9 | 715.6 |
Wheat straw | 17.3 | 2109.2 | 1538.7 |
Barley straw | 16.1 | 2266.4 | 1653.4 |
Corn straw | 16.8 | 2172.0 | 1584.5 |
Rapeseed straw | 15.0 | 2432.7 | 1774.7 |
Wood dust | 17.0 | 2146.5 | 1565.9 |
Scobs | 19.3 | 1890.7 | 1379.3 |
Willow chips | 16.5 | 2211.5 | 1613.3 |
Pelets | 18.0 | 2027.2 | 1478.9 |
Straw briquettes | 17.1 | 2133.9 | 1556.7 |
Wood briquettes | 18.0 | 2027.2 | 1478.9 |
Lp | Indicator | Unites of measure | Range | |
Minimum | Maximum | |||
1 | K | Mg gelatine/person | 0.156 | 0.175 |
2 | K1 | m3production space/Mg gelatine | 1.132 | 1.265 |
3 | Km | kW/Mg gelatine | 52.5 | 68.0 |
Dependent variable, indicators | Range | Medium | ||
Electricity | We [kW∙h/Mg gelatine] | 1154.9–1202.7 | 1174.8 | |
EE [kg gelatine/kW∙h] | 0.831–0.866 | 0.851 | ||
Thermal energy | Wte [GJ/Mg gelatine] | 20.16–24.66 | 22.39 | |
EEte [kg gelatine /GJ] | 40.55–49.60 | 44.66 | ||
Equivalent water vapour | Wse [kg vapour/Mg gelatine] | 7523–9202 | 8355 | |
EEse [kg gelatine/Mg vapour] | 108.7–132.9 | 119.7 | ||
Total energy | Wt1 [GJ/Mg gelatine] | 34.02–39.09 | 36.49 | |
Wt2 [GJ/Mg gelatine] | 24.32–28.99 | 26.62 | ||
Fuel equivalent | Wce1 [kg/Mg gelatine] | 1160.8–1333.8 | 1245.0 | |
Wce2 [kg/Mg gelatine] | 829.8–989.1 | 908.3 | ||
CO2 emissions | Ee CO2 [kg CO2/Mg of gelatin] | 1107–1154 | 1127 | |
Ete CO2 [kg CO2/Mg of gelatin] | 1065–1303 | 1183 | ||
Water | Ww [m3/Mg of gelatine] | 10.23–25.84 | 18.97 | |
EW [kg gelatine/m3] | 38.7–97.8 | 52.7 |
Regression equation | The range of variability of production Z | Correlation coefficient r | Coefficient R2 = r2∙100% |
Ae = 1424.4 Zm − 147450 | 565.2–631.3 | 0.878 | 77.3 |
Ac = 21.986Z24 + 7.6436 | 16.9–21.9 | 0.791 | 62.6 |
Aw = 95.655Z24 − 1439.1 | 16.9–21.9 | 0.883 | 77.9 |
Ww = 3.8879 Z24 – 54.464 | 16.9–21.9 | 0.818 | 67.0 |
EW= −13.561Z24 + 320.74 | 16.9–21.9 | 0.612 | 37.42 |
Energy carriers | Calorific value Qrw, [MJ/kg] | Individual fuel consumption indicators | |
Wr1 [kg/Mg gelatine] | Wr2 [kg/Mg gelatine] | ||
Lignite | 14.0 | 2606.4 | 1901.4 |
Coal | 26.0 | 1403.5 | 1023.8 |
Natural gas | 32.0 | 1140.3 | 831.9 |
Heating oil | 42.6 | 856.6 | 624.9 |
Vegetable oil | 37.5 | 973.1 | 65.6 |
Liquid flammable waste | 37.2 | 980.9 | 715.6 |
Wheat straw | 17.3 | 2109.2 | 1538.7 |
Barley straw | 16.1 | 2266.4 | 1653.4 |
Corn straw | 16.8 | 2172.0 | 1584.5 |
Rapeseed straw | 15.0 | 2432.7 | 1774.7 |
Wood dust | 17.0 | 2146.5 | 1565.9 |
Scobs | 19.3 | 1890.7 | 1379.3 |
Willow chips | 16.5 | 2211.5 | 1613.3 |
Pelets | 18.0 | 2027.2 | 1478.9 |
Straw briquettes | 17.1 | 2133.9 | 1556.7 |
Wood briquettes | 18.0 | 2027.2 | 1478.9 |