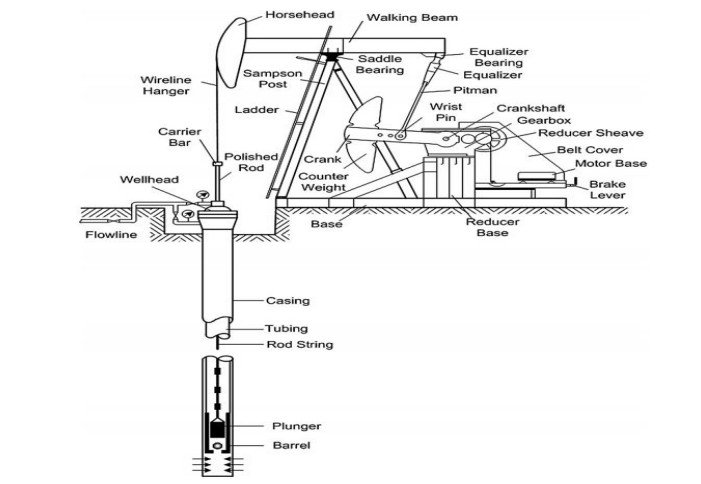
Citation: Charles Aimiuwu Osaretin, Tariq Iqbal, Stephen Butt. Optimal sizing and techno-economic analysis of a renewable power system for a remote oil well[J]. AIMS Electronics and Electrical Engineering, 2020, 4(2): 132-153. doi: 10.3934/ElectrEng.2020.2.132
[1] | Mamun Mishra, Bibhuti Bhusan Pati . A hybrid IDM using wavelet transform for a synchronous generator-based RES with zero non-detection zone. AIMS Electronics and Electrical Engineering, 2024, 8(1): 146-164. doi: 10.3934/electreng.2024006 |
[2] | Samarjit Patnaik, Manas Ranjan Nayak, Meera Viswavandya . Smart deployment of energy storage and renewable energy sources for improving distribution system efficacy. AIMS Electronics and Electrical Engineering, 2022, 6(4): 397-417. doi: 10.3934/electreng.2022024 |
[3] | Mehdi Tabasi, Pouyan Asgharian . Optimal operation of energy storage units in distributed system using social spider optimization algorithm. AIMS Electronics and Electrical Engineering, 2019, 3(4): 309-327. doi: 10.3934/ElectrEng.2019.4.309 |
[4] | Dipak R. Swain, Sunita S. Biswal, Pravat Kumar Rout, P. K. Ray, R. K. Jena . Optimal fractional sliding mode control for the frequency stability of a hybrid industrial microgrid. AIMS Electronics and Electrical Engineering, 2023, 7(1): 14-37. doi: 10.3934/electreng.2023002 |
[5] | I.E.S. Naidu, S. Srikanth, A. Siva sarapakara Rao, Adabala Venkatanarayana . A novel mine blast optimization algorithm (MBOA) based MPPT controlling for grid-PV systems. AIMS Electronics and Electrical Engineering, 2023, 7(2): 135-155. doi: 10.3934/electreng.2023008 |
[6] | Saumen Dhara, Pradip Kumar Sadhu, Alok Kumar Shrivastav . Analysis of over current relay and hybrid filter including the utilization of SFCL in a distribution network with DG. AIMS Electronics and Electrical Engineering, 2022, 6(1): 81-107. doi: 10.3934/electreng.2022006 |
[7] | Lawrence O. Aghenta, M. Tariq Iqbal . Design and implementation of a low-cost, open source IoT-based SCADA system using ESP32 with OLED, ThingsBoard and MQTT protocol. AIMS Electronics and Electrical Engineering, 2020, 4(1): 57-86. doi: 10.3934/ElectrEng.2020.1.57 |
[8] | Olayanju Sunday Akinwale, Dahunsi Folasade Mojisola, Ponnle Akinlolu Adediran . Mitigation strategies for communication networks induced impairments in autonomous microgrids control: A review. AIMS Electronics and Electrical Engineering, 2021, 5(4): 342-375. doi: 10.3934/electreng.2021018 |
[9] | Abdul Yussif Seidu, Elvis Twumasi, Emmanuel Assuming Frimpong . Hybrid optimized artificial neural network using Latin hypercube sampling and Bayesian optimization for detection, classification and location of faults in transmission lines. AIMS Electronics and Electrical Engineering, 2024, 8(4): 508-541. doi: 10.3934/electreng.2024024 |
[10] | K.V. Dhana Lakshmi, P.K. Panigrahi, Ravi kumar Goli . Machine learning assessment of IoT managed microgrid protection in existence of SVC using wavelet methodology. AIMS Electronics and Electrical Engineering, 2022, 6(4): 370-384. doi: 10.3934/electreng.2022022 |
Petroleum production currently faces the reality of low prices, and hence low budget operations are required [1,2]. The reality is that more fields are required to be developed in remote locations and such developments are also more energy intensive [3]. The need for a simple, economical and environmentally sustainable alternative to keep the oil and gas wells onstream and minimize the impact of the depressive market cannot be overemphasized [4]. There is also a pandemic of the indefinite suspension of producing oil wells due to the economics of production, as wells previously considered economical, have suddenly become sub-economical at best and uneconomical at worst. The petroleum production engineer and facility engineer continue to face the challenge of keeping presently producing wells onstream and providing innovative solutions to restore idle facilities to production [5]. Considering the safety and environmental impact of suspending producing oil wells, economic losses due to inactivity and the prohibitive cost of abandonment; it becomes imperative and favorable for operators, jobs, the economy and the environment to minimize losses, defer costs, maintain production and provide innovative alternatives for producing wells classified as marginal/stripper wells [6]. Since wells are subjected to various production schedules, the cost implication of innovative renewable energy-based approaches also needs to be evaluated for feasibility, especially under varying weather and battery storage conditions. This work analyzes the feasibility of different renewable energy scenarios for continuous and intermittent production for an artificially lifted well; taking technical and economic factors into consideration in choosing the best solution in terms of the most suitable combination of energy source and pumping schedule.
The increasing deployment of renewable energy for oil and gas production reflects a shift in paradigm, as the role of renewable energy evolves from competing to a complementary energy source [7]. Deployment of 100% renewable energy for hydrocarbon production has received some attention in literature: Van Heel et at. [8] examined the effect of using concentrated solar power for cyclic production of high-pressure steam required for steam injection, Poythress et al. [9] implemented a solar energy-based system for de-watering an onshore gas well using a low power DC electric motor. A gap still exists in the literature that consider the technical and economic feasibility of deploying 100% renewable energy to produce oil in remote facilities. Finding the least cost and most suitable combination of renewable sources and storage, that satisfies the energy demand for production in different scenarios is the task of this study.
There comes a time in the life of an oil well, when the need arises to provide external energy to sustain or attain a target production. For onshore wells, about 85% of the wells requiring artificial lift deploy sucker rod or beam pumps, as they are simple, durable and familiar to most operators [10,11,12]. Given that the average oil production for a well is taken daily over a period of 12 consecutive months with peak value less than or equal to 15 barrels or when the average gas production considered daily over a period of 12 consecutive months has a peak value of at most 90, 000 cubic feet per day, then for taxation purpose, such a well is considered a stripper well. On land, if a well becomes marginal primarily due to low production, it is usually classified as a stripper well. It should be noted that each oil field or producing well has a unique price that determines its critical profit point (benchmark price for profitable operation), below which a field or well will become unprofitable [13]. The producing well being examined in this work no longer produces adequate oil volumes to generate enough revenue from oil sale and hence is considered for suspension, plugging or abandonment due to either the high cost of operation or low volume of production or both [14]. Continuous operation of such wells requires a higher price [per barrel of oil produced or thousand cubic feet (Mcf) of natural gas] or a reduced cost of operation/production. The system cost component is composite and influenced by the conditions of operation such as access to the site (remoteness), fluid viscosity, depth of the well and energy requirement (artificial lift required), the composition of produced fluids and need for separation, processing and disposal [13].
For various production conditions and at different phases in the life of an oil well, it is often desirable to determine and predict the power requirement for an artificially lifted petroleum production system. It becomes necessary to determine the rating of the prime mover required to drive and sustain production at the desired rate or level [14]. During artificial lift design, after estimating the appropriate fluid load for the well, it is normally difficult to get a standard motor (prime mover) to match the estimated cyclic load. It is a regular practice to settle for the lowest sized motor that satisfies the load requirement. Oversizing the motors inevitably leads to over pumping the wells, reduces pump efficiency and ultimately pump life. It is also typical at the design stage to adjust the pumping mode (stroke length, pump displacement, strokes per minute) [15]. This adjustment changes the speed and torque requirements and results in a pumping system which could over time eventually also over pump the wells [16]. Due to dynamics of well and fluid conditions, it may be necessary to adopt a form of pump scheduling using pump cycle controller (fixed-interval time clocks, percentage timers, and pump off controllers/pump control system) to dynamically match the pump action to the available production rate [17]. A timer is a simple solution, but a pump off controller may be preferable to respond to fluid pound, allow accumulation of reservoir fluids in the wellbore, minimize damage to the pump and ensure high volumetric efficiency [10,14,17]. In this study, the electrical energy from renewable energy generators will be used to power a high slip AC electric motor, which serves as the prime mover for the sucker-rod-pumped artificial lift system as shown in Figure 1.
The renewable microgrid evaluated for simulation exhibits hybrid generation and redundancy. It tentatively consists of two (2) primary power sources: solar PV and wind, one (1) backup source (battery storage) and the prime mover or high slip AC electric motor (NEMA D) as shown in Figure 2. The proposed system is matched with the requirement of the producing well and is to be 100% renewable to ensure minimal interruption of hydrocarbon production, reduce noise and eliminate exhaust gas pollution.
Medicine Hat is a city in southeast Alberta, latitude 5002’32” N and longitude 110048’49” W. It is one of the sunniest parts of Canada with an average of 2, 544 sunshine hours and 330 days of sunshine per year [18]. In recent times a crisis has been looming in the oil and gas sector in Alberta, with the City of Medicine Hat been one of the worse hit due to the low prices. About 2, 000 producing wells in Medicine Hat (75%) are to be shut down, and only the least cost wells are to be left producing [19]. With the oil and gas market going through a depression, massive job losses are anticipated. The approach considers an idealized well, combined with the weather data of Medicine hat to propose a system design.
The monthly average solar radiation data (global horizontal irradiance GHI in kWh/m2/day) and dimensionless clearness index were obtained from NASA surface meteorology and solar energy database [20] and plotted in Figure 3. As shown in Table 1, Medicine Hat has the highest values for solar radiation and peak clearness index in the summer months, with a scaled annual average solar radiation of 3.61 kWh/m2/day.
Month | Clearness index | Daily Radiation (kWh/m2/day) |
January | 0.438 | 1.110 |
February | 0.494 | 1.970 |
March | 0.520 | 3.250 |
April | 0.559 | 4.890 |
May | 0.534 | 5.710 |
June | 0.529 | 6.100 |
July | 0.575 | 6.380 |
August | 0.565 | 5.340 |
September | 0.540 | 3.830 |
October | 0.523 | 2.430 |
November | 0.463 | 1.320 |
December | 0.439 | 0.930 |
Data available from surface meteorology and solar energy database [20] is given in Table 2. The scaled annual average wind speed at 50 m above the earth’s surface for flat terrain in Medicine Hat is given as 5.70 m/s. The average monthly wind speed is obtained from NASA with minimal variation and plotted for one year in Figure 4.
Month | Average Wind Speed (m/s) |
January | 5.670 |
February | 5.620 |
March | 5.640 |
April | 6.180 |
May | 6.320 |
June | 5.830 |
July | 5.260 |
August | 5.100 |
September | 5.480 |
October | 5.910 |
November | 5.590 |
December | 5.770 |
From the data in Table 2 and Figure 4, it can be inferred that at a hub height of 50 m, the average wind speed of Medicine Hat is high enough for wind power generation. Hence it is justifiable to consider wind power as one of the primary sources of power for driving production of the artificially lifted well. It should be noted that apart from generating electricity from a wind turbine to power the AC electric motor, drive sucker-rod pump and produce at the desired flow rate, hydraulic wind pumps can also be tested directly for lifting fluids from the producing well, but such application is beyond the scope of this work.
Several possibilities could be considered as case studies, and different scenarios can thus arise as follows:
Only artificial lift required: Telecommunication, remote monitoring, electronic metering and control, not required. The facility could be:
- a remote gas well that requires de-watering only,
- a remote gas well that requires chemical injection only,
- a remote oil well that requires artificial lift only.
Remote oil wells (in digital oilfields): oil wells powered by artificial lift requiring telecommunications, process automation, remote sensing, instrumentation and advanced process control [SCADA, PLC, etc.]. Such facilities are usually powered by the electric grid and/or diesel/gas power only, as the energy requirement may result in very high system cost, except in shallow oil wells, gas wells requiring dewatering and/or chemical injection.
Remote well requiring artificial lift only (will be considered in this work): This well for technical and/or economic reasons cannot be connected to the grid but is proposed to be powered by a small stand-alone hybrid renewable power system. It should be noted that in practice, between pumping cycles, several combinations of a timer on/off schedules could be used, depending on the downhole conditions, the pumps could be turned off for 5, 10 or as much as 15 minutes before restarting [16]. In this study, two (2) pumping schedules (pump duty cycle) are considered:
- Scenario A: Intermittent production (diurnal, during the day, 12 hours on, 12 hours off).
- Scenario B: Continuous production (uninterrupted).
For intermittent production, the daily and monthly load profile are shown in Figures 5 and 6, respectively. The pump is turned on for 12 hours of daylight from 7 am to 7 pm and off otherwise.
For continuous production, the load is run continuously. It is expected that the cost contribution of the required storage system will be justified by the extra production made possible by continuous operation. The daily and monthly load profile are shown in Figures 7 and 8, respectively.
Estimation of the load requirement begins with the design of a sucker-rod pumped artificial lift system. The sizing begins with selection of a suitable pumping mode (stroke length, stroke per minute, plunger diameter and rod string design) as shown in Figure 9(a), after which a parametric investigation is carried out to determine the effect of API rod number, pump diameter and pump geometry on the energy requirement of the prime mover in an artificial lift simulator QRod (Quick Rod). The parameters chosen from the investigation are subsequently deployed in another simulator PROSPER as shown in Figure 9(b). The well, fluid and pump characteristics are defined, and the design repeated in PROSPER to obtain a more robust rating of sucker-rod pump and appropriately size a high slip AC electric motor, the prime mover rating is shown in Figure 9(c).
HOMER (Hybrid Optimization of Multiple Energy Resources) is the tool that is adopted for simulation, optimization and sensitivity analysis. Based on the selected geographical location (longitude and latitude), the solar, wind and temperature data are updated in HOMER. The energy flow between components is calculated and considering variability in weather conditions and the load profile, the cost of installing and operating the system over the project lifetime is estimated. Simulation entails that given specified conditions, the flow of energy between the components of the system is calculated for each time interval, to find a balance that ensures continuous and consistent operation, hence reliably and optimally balancing the electrical energy demand with supply. Optimization (deploying HOMER Optimizer TM) implies identifying the configuration with the best mix of renewable resources that meets the load requirements all year round at the least cost [21]. Since storage is adopted and the sources are 100% renewable, cycle charging is adopted as the power dispatch strategy, such that a producing generator runs at or close to its rated maximum capacity, without producing any excess electricity; but any excess electricity generated is stored in the battery bank to supply the primary load when needed [22]. The battery bank serves as a backup to deliver power to the load below the cut in or rated speed, at night or on cloudy days. In Homer, feasible solutions are ranked in order of increasing net present cost, but technically any system with the least unmet load is considered the most reliable [23] and hence the most feasible solution among the available alternatives [24].
From a continuous pumping load perspective, the energy consumption of the prime mover (AC electric motor) is 60.11 kWh/d, with a peak load of 4.55 kW. The system is designed with a discount rate of 8%, for 25 years and consists of solar panels (Jinko Eagle PERC60, 300W) with an efficiency of 18.33%, deep cycle batteries [SAGM 12 205 (12V, 219Ah)] with four (4) units per string to obtain a string voltage of 48 V. A 5.5 kW system converter (battery dedicated inverter: Schneider Conext XW +5548) was deployed with 93% efficiency. A wind turbine with a 4.5 m rotor and a hub height of 12 m (AWS HC, 3.3 kW) was also selected as a secondary energy source, as shown in the schematic of the system in Figure 10.
The system types are presented in order of decreasing system cost. The case study is considered sufficiently remote to justify the exclusion of the diesel generator. This approach ensures a 100% renewable power system mix and eliminates the need for refueling, routine maintenance, and servicing operations normally required for operating a diesel generator. The proposed design should economically exploit the solar energy, wind energy or both, with battery storage to sustain hydrocarbon production.
HOMER calculates the energy flow to and from each system component, determines how to run the generators to consistently supply the AC electric loads and charge batteries when possible. It should be noted that solutions obtained from the simulations are considered infeasible either due to capacity shortage constraint, minimum renewable energy fraction or unmet load. The optimized results from HOMER are arranged by default in order of increasing cost [net present cost (NPC), levelized cost of energy (LCOE) and operating cost], with the least cost configuration ranking higher.
Renewable energy fraction is adopted as a constraint criterion in sifting the simulation results considered as feasible options. Additionally, some system types may return “a feasible option with caution”. These will also not be considered, as such system types may experience stability problems due to sufficiently high renewable penetration. Addition of more storage (battery bank or flywheel) may be helpful, but more detailed modelling is required, which is beyond the scope of this study. The system structure for diurnal pumping is shown in Figure 10, with a daily energy consumption of 32.43 kWh/d and a peak load of 4.44 kW.
Scenario A: Intermittent production (diurnal, during the day)
A total of 1, 204 solutions were simulated, 578 were feasible, and 626 were infeasible due to the capacity shortage constraint. Of the 292 omitted solutions, 123 lack a converter, 37 have an unnecessary converter and, 126 have no power generation source. The simulation results for candidate configurations for diurnal production is shown in Table 3(a) and (b), ranked in order of increasing system cost.
![]() |
Solar PV and battery storage.
A solar PV generator rated 27.3 kW, 16.0 strings of battery storage and a system converter of 4.49 kW make up this system type. The battery storage is the dominant cost component in this system type, accounting for 46.7% of the total system cost. The NPC, LCOE, and operating cost are $64, 969.30, $0.4247/kWh and $1, 317.93/yr. On a monthly basis, the produced electricity for this configuration is plotted in Figure 11.
This system generates 39.009 MWh/yr of electricity of which 11.832 MWh/yr is consumed by the AC electric motor, and 65.9% of total generation (25.721 MWhr/yr) is excess electricity. The capacity factor of the solar PV generator is 16.3%. The renewable energy fraction is 100% with 4.55 kWh/yr of unmet electric load. The system storage has a usable nominal capacity 118 kWh and 87.1 hours of autonomy, which is equivalent to almost four (4) days of backup time. In this system type, the solar PV generator is the sole energy source, with the battery serving as the backup at night, on cloudy days or both, as required.
Solar PV, wind and battery storage.
A solar PV generator rated 26.4 kW, 1 unit of 3.3 kW of the wind turbine generator, 15 strings of battery storage and 4.12 kW of system converter make up this system type. The wind generator is the dominant cost component accounting for about 32.1% of the total system cost. The NPC, LCOE, and operating cost of the system are $89, 512.41, $0.5850/kWh, $1, 465.86/yr respectively. The electricity produced by this system type is shown in Figure 12(a), as described by the cost summary plot in Figure 12(b), it is worthy of note that although the wind turbine generator accounts for the highest cost percentage for the system, it contributes only 5, 862 kWh/yr (19.5%) to the total electricity in a year. Hence from a cost-benefit perspective, the electricity output of the wind generator does not justify the cost incurred.
This system generates 37.756 MWh/yr of electricity of which 11.837 MWh/yr is consumed by the AC electric motor and, 70.4% of total generation (30.707 MWhr/yr) is excess electricity, available for charging the battery. The capacity factor of the wind generator is 20.3%. The renewable energy fraction is 100% with 0.0759 kWh/yr of unmet electric load. The battery storage system has a usable nominal capacity of 110 kWh and 81.6 hours of autonomy, which is equivalent to over 3 days of backup time. Hybrid renewable generation is adopted in this system type as solar PV, and wind turbines are deployed as dual sources of energy. When the wind speed is below the cut in or rated speed, at night or on cloudy days, the excess generated electrical energy retained in the battery storage system is made available (after inversion) to drive the AC electric motor.
Wind generator and battery storage.
Four (4) units of 3.3 kW of the wind turbine generator, 20 strings of battery storage and a 3.80 kW of system converter, make up this system type. In this system type, the wind is the sole power resource, as shown in Figure 13, with the wind generators alone accounting for about 72.96% of the total system cost. The net present cost (NPC), levelized cost of energy (LCOE) and annual operating cost are $157, 555.10, $1.03/kWh and $1, 862.76/yr respectively.
This system generates 23. 446 MWhr/yr of electricity of which 11.836 MWh/yr is consumed by the AC electric motor and 43.6% of total generation (10.227 MWhr/yr) is excess electricity, which is available to charge the battery. The capacity factor of the wind generator is 20.3%. The renewable energy fraction is 100% with 0.669 kWh/yr of unmet electric load. The system has a usable nominal capacity 147 kWh and 109 hours of autonomy, which is equivalent to almost 5 days of backup time. The wind turbine is the sole source of energy in this configuration. When the wind speed is below the rated speed, the battery storage system discharges, delivering its stored energy for artificial lift.
Scenario B: Continuous/Uninterrupted pumping
A total of 1, 538 solutions were simulated, 739 were feasible, and 799 were infeasible due to the capacity shortage constraint. Of the 358 omitted, 135 lack a converter, 37 have an unnecessary converter, and 180 have no source of power generation. The simulation results for candidate configurations of continuous production is shown in Table 5(a) and (b), ranked from the lowest to the highest system cost. The system structure for continuous pumping is shown in Figure 14 with a daily energy consumption of 60.11 kWh/d and a peak load of 4.55 kW.
![]() |
Solar PV and battery storage
A solar PV generator rated 50.8 kW, 32 strings of battery storage and a system converter of 4.89 kW make up this system type. As in system type 1A, the battery storage is the dominant cost component in this system type, accounting for 54.1% of the total system cost. The NPC, LCOE and operating cost are $130, 773.60, $0.4614/kWh, $3, 163.08/yr respectively. The plot of monthly electricity distribution is shown in Figure 15.
This system generates 72.70 MWh/yr of electricity of which 21.926 MWh/yr is consumed by the AC electric motor, 64.5% of total generation (46.862 MWhr/yr) is excess electricity. The capacity factor of the solar PV generator is 16.3%. The renewable energy fraction is 100% with 14.0 kWh/yr of unmet electric load. The battery storage system has a usable nominal capacity of 235 kWh and 94.0 hours of autonomy, which is equivalent to about 4 days of backup time. In this system type, the solar PV generator is the sole energy source, with the battery serving as the backup at night or on cloudy days as required.
Solar PV, wind and battery storage
A PV generator rated 50.8 kW, 1 unit of 3.3 kW wind turbine generator, 26 strings of battery storage and 4.67 kW of system converter, make up this system type. Unlike in system type 2A, here the battery is the dominant cost component accounting for about 39.0% of the total system cost. The NPC, LCOE, and operating cost of the system are $145, 150.50, $0.5118/kWh, $3, 056.04/yr respectively. The plot of monthly electricity production is shown in Figure 16.
This system generates 78.562 MWh/yr of electricity of which 21.940 MWh/yr is consumed by the AC electric motor, and 68.2% of total generation (53.598 MWhr/yr) is excess electricity, available for charging the battery storage. The capacity factor of the wind generator is 20.3%. The renewable energy fraction is 100% with 0 kWh/yr of unmet electric load (no unmet load). The battery storage system has a usable nominal capacity of 191 kWh and 76.3 hours of autonomy, which is equivalent to over 3 days of backup time. The effect of variability in weather conditions is reduced as the presence of two power generation sources ensures that the unmet load and capacity storage are both minimized compared to system type 1B.
Wind generator and battery storage
Six (6) units of the wind turbine generator, 40 strings of battery storage and a 6.54 kW of system converter make up this system type. The wind generators alone account for about 67.5% of the total system cost with net present cost (NPC), levelized cost of energy (LCOE) and annual operating cost of $255, 376.90 $0.9011/kWh and $3, 094.82/yr respectively. The plot of monthly electricity distribution is shown in Figure 17.
This system generates 35.17 MWhr/yr of electricity of which 21.922 Mwh/yr is consumed by the AC electric motor, and 39.4% of total generation (10.474 MWhr/yr) is excess electricity, which is available to charge the battery. The capacity factor of the wind generator is 20.3%. The renewable energy fraction is 100% with 17.9 kWh/yr of unmet electric load. The battery storage system has a usable nominal capacity 420 kWh and 117 hours of autonomy, which is equivalent to almost 5 days of backup time. For this system type, the wind turbine is the primary source of energy, while the battery storage system stores energy for petroleum production, when the wind speed is either below the cut in or rated speed.
There are several conditions that could affect the decision on the system type to be chosen as optimal. Several factors could play a significant role in determining the ideal system type. The considerations could include the peculiarities of the petroleum production environment (rural, urban, sub-urban), level of remoteness, the presence of additional loads (apart from the ones imposed on the pump due to produced hydrocarbon) and availability of cheap diesel, natural gas or associated gas to power an internal combustion engine. It is also important to note that in this design, the unmet load is the ultimate criterion in choosing between two equally feasible architectures and not the cost of the system alone.
The least-cost configuration for intermittent and continuous pumping are shown in Table 6.
Solar PV | Type 1A | Type 1B | Unit |
Rated capacity | 27.3 | 50.8 | kW |
Mean output | 4.45 | 8.30 | kW |
Mean daily Output | 107 | 199 | kWh/d |
Capacity factor | 16.3 | 16.3 | % |
Hours of operation | 4, 377 | 4, 377 | hrs/yr |
PV penetration | 330 | 331 | % |
Battery | |||
Number | 64 | 128 | (4bt/string) |
String in parallel | 16 | 32 | Strings |
Bus voltage | 48 | 48 | V |
Nominal capacity | 168 | 336 | kWh |
Usable nominal capacity | 118 | 235 | kWh |
Energy in | 3, 860 | 15, 244 | kWh/yr |
Energy out | 3, 294 | 12, 982 | kWh/yr |
Considering 100% renewable energy fractions with three (3) system configurations, and six (6) scenarios as shown in Figure 18:
- Type 1 (solar photovoltaic + battery storage),
- Type 2 (solar photovoltaic + wind turbine + battery) storage) and
- Type 3 (wind turbine + battery storage).
Type 3 will be ignored in the analysis as it has the highest overall cost of the feasible system configurations. Considering:
Intermittent pumping: (1A, 2A) and, Continuous pumping: (1B and 2B).
The following can be inferred from Figure 18:
(e) Scheduling the load (changing the load cycle time or the number of hours the electric motor prime mover is run), has no effect on which configuration type is considered optimal as system type 1 (solar photovoltaic + battery storage) has proven to be the least cost consideration, irrespective of load scheduling as shown in Figure 18(a).
(f) For the least cost option, if the pumping transitions from intermittent to continuous (type 1A to type 1B), the change in the levelized cost of energy is negligible [Figure 18(b)], but the net present cost and operating cost of the well are increased by 101% and 140% respectively (by over 100%) as shown in Figure 18(a) and 18(c).
(g) Using the electrical energy and system cost criteria to compare the performance of system type 1 and 2, the total production, consumption, excess electricity, unmet electricity and capacity storage are all observed to increase with increase in daily pumping hours for both architectures 1 and 2, except for 2B (continuous pumping with solar photovoltaic, wind turbine and battery storage) where the levelized cost, unmet load and capacity storage reduce with increase in pumping hours.
(h) It can be observed from Figures 18(f), (g) and (h) respectively that (due to hybrid power generation), system type 2 results in a higher level of excess electricity, a lower amount of unmet load and lower capacity storage compared to system 1. All these advantages come at a premium of higher net present cost and higher levelized cost of energy).
(i) It is important to note that continuous production with hybrid renewable power generation (2B) is seen to have the least amount of unmet load (0 kWh/yr) for all the system types and pumping configurations. Transitioning from type 1B to 2B also leads to a cut in operating cost of the system.
In general, for both intermittent and continuous pumping schedules. Comparing system 1 and 2:
system type 1, minimizes [net present cost, levelized cost of energy, total production, consumption and excess electricity], while system type 2, minimizes [unmet load, capacity storage].
Generally, the system cost of type 2 are significantly higher than those of type 1, but instead of merely considering the system cost alone, the total unmet load and unmet load fraction are jointly used as the ultimate criteria for selection. The hybrid generator option: type 2, will be most reliable and hence most preferred (type 2A for intermittent pumping and type 2B for continuous pumping). This makes technical and economic sense, especially in wells where the production due to the extra pumping hours can justify the higher system cost incurred over the life of the well.
Key technical indices are used to compare continuous pumping with intermittent pumping for the proposed system configuration, as shown in Table 7.
Solar PV | Type 2A | Type 2B | Unit |
Rated capacity | 27.3 | 50.8 | kW |
Mean output | 4.45 | 8.30 | kW |
Mean daily output | 107 | 199 | kWh/d |
Capacity factor | 16.3 | 16.3 | % |
Hours of operation | 4, 377 | 4, 377 | hrs/yr |
PV penetration | 330 | 331 | % |
Wind | |||
Total rated capacity | 3.30 | 3.30 | kW |
Mean output | 0.669 | 0.669 | kW |
Total production | 5, 862 | 5, 862 | kWh/yr |
Capacity factor | 20.3 | 20.3 | % |
Hours of operation | 7, 329 | 7, 329 | hrs/yr |
Wind penetration | 49.5 | 26.7 | % |
Battery | |||
Number | 64 | 128 | (4bt/string) |
String in parallel | 16 | 32 | Strings |
Bus voltage | 48 | 48 | V |
Nominal capacity | 168 | 336 | kWh |
Usable nominal capacity | 118 | 235 | kWh |
Energy in | 3, 860 | 15, 244 | kWh/yr |
Energy out | 3, 294 | 12, 982 | kWh/yr |
The architectures obtained are all 100% renewable; hence daily solar radiation and average wind speed will be used as sensitivity variables to examine the response of the key indices (system cost parameters and unmet load) to maximum and minimum variations from the average value. The optimization process is repeated for the system architectures. The daily solar radiation varies sharply from 0.93 kWh/m2/day to 6.38 kWh/m2/day, while the average wind speed varies from 5.10 m/s to 6.32 m/s. The results are shown in Table 8.
SR (kWh/m2/day) | WS (m/s) | PV (kW) | WT (kW) | BS (St) | NPC ($1, 000) | COE ($) | Unmet (%) |
0.93 | 5.1 | 8.09 | 8 | 30 | 304 | 1.07 | 0.0494 |
0.93 | 5.7 | 20.5 | 5 | 29 | 229 | 0.81 | 0.0546 |
0.93 | 6.32 | 4.87 | 5 | 30 | 213 | 0.75 | 0.0583 |
3.61 | 5.1 | 50.8 | - | 32 | 131 | 0.46 | 0.0636 |
3.61 | 5.7 | 50.8 | - | 32 | 131 | 0.46 | 0.0636 |
3.61 | 6.32 | 50.8 | - | 32 | 131 | 0.46 | 0.0636 |
6.38 | 5.1 | 25.2 | - | 27 | 98 | 0.35 | 0.0797 |
6.38 | 5.7 | 25.2 | - | 27 | 98 | 0.35 | 0.0797 |
6.38 | 6.32 | 25.2 | - | 27 | 98 | 0.35 | 0.0797 |
The results from the sensitivity analysis is shown in Table 8 and in the optimization system type plot in Figure 19. It can clearly be inferred that for the italicized section, below the average daily solar radiation (3.61 kWh/m2/day), the hybrid renewable energy system (solar photovoltaic, wind turbine and battery storage: type 2) is the most preferred architecture with the least unmet load percentage and highest system NPC and LCOE. Above the mean daily solar radiation (3.61 kWh/m2/day), type 1 (solar photovoltaic and battery storage) is the most preferred architecture with the least system cost and relatively higher unmet load than type 2.
The sensitivity analysis from Table 8 and the surface plot in Figure 20 jointly demonstrate that the lowest system costs are incurred at the highest mean daily solar radiation and average wind speeds. But as can be inferred from the Table 8, the unmet load percentage is also highest. This can be explained by the fact that type 1 is the most feasible architecture under such conditions and is independent of the wind speed.
From Table 8 and Figure 21, it can be inferred from the sensitivity analysis and the optimization surface plot, that the cost of the least-cost system (type 1), is minimized for photovoltaic systems rated at most 25.2 kW, with battery sizes of at most 27 strings.
Least cost [type 1] = at most [25.2kW of PV, 27 strings]
Such a system is seen to settle at an estimated net present cost of $98, 189.05 and a levelized cost of energy of $0.3465.
Analysis of the six (6) scenarios considered in Figure 18 leads to the conclusion that irrespective of the system architecture deployed, intermittent pumping is seen to be cheaper than continuous pumping for all the indices considered, and for all configurations observed except for continuous pumping with solar photovoltaic, wind turbine and battery storage (type 2B) for which the LCOE is lower than that of type 1, and which is proposed as the most feasible configuration. Type 2B is chosen as the most feasible solution for continuous pumping with 0 kWh/yr of unmet load, capacity storage of 0.56 kWh/yr, the net present cost of $145, 150.50, levelized cost of energy of $0.51/kWh and an operating cost of $3, 056.04/yr. In this case study well and for the location chosen, although the hybrid renewable system (type 2) has a higher net present and higher levelized cost of energy than type 1, continuous pumping with solar PV, wind and battery system has been demonstrated to have the least unmet load and capacity storage. Hybrid generation (type 2: solar PV, wind and battery storage) has a very clear advantage over other configurations, as demonstrated by the sensitivity analysis in Table 8, and plots in Figure 18(g) and (h). This is because the available intermittent energy sources are harnessed economically (for both intermittent and continuous pumping) and are thus optimal for reliably driving the artificially lifted well. In this way, the battery storage system provides extra energy for petroleum production when it is cloudy or nighttime.
The authors will like to appreciate the Tertiary Education Trust Fund (TETFUND) of the Federal Government of Nigeria, for funding this research. We acknowledge the support of Memorial University of Newfoundland for the enabling environment to carry out this research.
The authors declare that there is no conflicts of interests in the execution and publication of this work.
[1] | Aguilera RF and Radetzki M (2016) The price of oil. University Printing House, Cambridge university press, Cambridge, United Kingdom. |
[2] | Armacanqui JS, Eyzaguirre L, Lujan C, et al. (2016) Managing Oil Fields in a Low Oil Price Environment. Society of Petroleum Engineers. |
[3] | Saadawi H (2019) Application of Renewable Energy in the Oil and Gas Industry. Society of Petroleum Engineers. |
[4] | Shedid SA (2009) Effects of Subsurface Pump Size and Setting Depth on Performance of Sucker-Rod Artificial Lift: A Simulation Approach. Society of Petroleum Engineers. |
[5] | Guillory R, Wan Razali WAA, Masoudi R, et al. (2019) Total Well Management: Maximising Well Lifecycle Value - A Regulator Perspective. International Petroleum Technology Conference. |
[6] | Muehlenbachs L (2017) 80,000 Inactive Oil Wells: A Blessing or a Curse? SPP Research paper. |
[7] | Temizel C, Irani M, Canbaz CH, et al. (2010) Technical and Economic Aspects of Use of Solar Energy in Oil & Gas Industry in the Middle East. Society of Petroleum Engineers. |
[8] | Van Heel AP, Van Wunnik JNM, Bentouati S, et al. (2010) The Impact of Daily and Seasonal Cycles in Solar-Generated Steam on Oil Recovery. Society of Petroleum Engineers. |
[9] | Poythress MW, Rowlan OL (2008) Low-Volume Pumping Systems: Moving Gallons to Produce Thousands. Society of Petroleum Engineers. |
[10] | Dave MK, Ghareeb Mustafa M (2017) Performance Evaluations of the Different Sucker Rod Artificial Lift Systems. Society of Petroleum Engineers. |
[11] |
Feng ZM, Tan JJ, Li Q, et al. (2018) A review of beam pumping energy-saving technologies. Journal of Petroleum Exploration and Production Technology 8: 299-311. doi: 10.1007/s13202-017-0383-6
![]() |
[12] | Di Tullio MT, Marfella F (2018) Enhanced Sucker Rod Pumping Model: A Powerful Tool for Optimizing Production, Efficiency and Reliability Beam Pump Motors: The Effect of Cyclical Loading on Optimal Sizing. Society of Petroleum Engineers. |
[13] | National Stripper Well Association (2019) Stripper Well Facts. Available from: http://nswa.us/custom/showpage.php?id=25 |
[14] | Hicks AW (1986) Using Fiberglass Sucker Rods in Deep Wells. Society of Petroleum Engineers. |
[15] | Takacs G (2015) Sucker-Rod Pumping Handbook - Production Engineering Fundamentals and Long Stroke Rod Pumping. 1st edition, Gulf Professional Publishing, Oxford, United Kingdom. |
[16] | Skinner DR (1984) Efficient Use of Electric Power in Production Operations. Society of Petroleum Engineers. |
[17] | Johnson JE (1988) Electrical Savings in Oil Production. Society of Petroleum Engineers. |
[18] | Environment Canada (2019) Canadian Climate Normals 1981-2010 Station Data, 2016. |
[19] | Dorozio J (2019) Alberta's 'Gas City' to shut down 2,000 wells, laying off up to 100 people. Available from: http://www.cbc.ca |
[20] | Surface meteorology and Solar Energy (SSE) Data Archive (2019) POWER projects Data Sets. Available from: https://power.larc.nasa.gov |
[21] | Lambert T, Gilman P, Lilienthal P (2006) Micropower System Modeling with Homer. Wiley & Sons, Hoboken (NJ), USA. |
[22] | Aziz AS, Tajuddin MFN, Adzman MR, et al. (2019) Energy Management and Optimization of a PV/Diesel/Battery Hybrid Energy System Using a Combined Dispatch Strategy. Sustainability 11: 1-26. |
[23] |
Aziz AS, Tajuddin MFN, Adzman MR, et al. (2019) Optimization and sensitivity analysis of standalone hybrid energy systems for rural electrification: A case study of Iraq. Renew Energ 138: 775-792. doi: 10.1016/j.renene.2019.02.004
![]() |
[24] |
Baniasad Askari I, Baniasad Askari L, Kaykhah MM, et al. (2014) Optimisation and techno-economic feasibility analysis of hybrid (photovoltaic/wind/fuel cell) energy systems in Kerman, Iran; Considering the effects of electrical load and energy storage technology. International Journal of Sustainable Energy 33: 635-649. doi: 10.1080/14786451.2013.769991
![]() |
1. | Zubairu Ismaila, Olugbenga A. Falode, Chukwuemeka J. Diji, Omolayo M. Ikumapayi, Adetokunbo A. Awonusi, Sunday A. Afolalu, Esther T. Akinlabi, A global overview of renewable energy strategies, 2022, 10, 2333-8334, 718, 10.3934/energy.2022034 | |
2. | Mohamed Elyamany, Sameh O. Abdellatif, Hani Ghali, 2023, Chapter 19, 978-3-031-17090-4, 174, 10.1007/978-3-031-17091-1_19 | |
3. | M. Thirunavukkarasu, Yashwant Sawle, Himadri Lala, A comprehensive review on optimization of hybrid renewable energy systems using various optimization techniques, 2023, 176, 13640321, 113192, 10.1016/j.rser.2023.113192 | |
4. | Saumen Dhara, Pradip Kumar Sadhu, Alok Kumar Shrivastav, Analysis of over current relay and hybrid filter including the utilization of SFCL in a distribution network with DG, 2022, 6, 2578-1588, 81, 10.3934/electreng.2022006 | |
5. | Mohammad M. El-Yamany, Sameh O. Abdullatif, Hani A. Ghali, Investigating the Techno-economic Utility of Integrating an Optimized PV/diesel Hybrid System in an Entire Oil Field in the Western-dessert in Egypt, 2021, 16, 2224-350X, 104, 10.37394/232016.2021.16.11 | |
6. | Artur Sagdatullin, 2021, Study of the Energy Consumption of Borehole Systems with Rod Pumps on the Basis of Simulation of an Automated Electromechanical System, 978-1-6654-3981-7, 1075, 10.1109/SUMMA53307.2021.9632090 | |
7. | Takele Ferede Agajie, Ahmed Ali, Armand Fopah-Lele, Isaac Amoussou, Baseem Khan, Carmen Lilí Rodríguez Velasco, Emmanuel Tanyi, A Comprehensive Review on Techno-Economic Analysis and Optimal Sizing of Hybrid Renewable Energy Sources with Energy Storage Systems, 2023, 16, 1996-1073, 642, 10.3390/en16020642 | |
8. | Daniel Alejandro Pérez Uc, Susana Estefany de León Aldaco, Jesús Aguayo Alquicira, Trends in Hybrid Renewable Energy System (HRES) Applications: A Review, 2024, 17, 1996-1073, 2578, 10.3390/en17112578 | |
9. | Omid Motamedisedeh, Sara Omrani, Azharul Karim, Robin Drogemuller, Geoffrey Walker, A comprehensive review of optimum integration of photovoltaic-based energy systems, 2025, 207, 13640321, 114935, 10.1016/j.rser.2024.114935 | |
10. | Vivek Saxena, Narendra Kumar, Saibal Manna, Saurabh Kumar Rajput, Kusum Lata Agarwal, Sourav Diwania, Varun Gupta, Modelling, solution and application of optimization techniques in HRES: From conventional to artificial intelligence, 2025, 380, 03062619, 125047, 10.1016/j.apenergy.2024.125047 |
Month | Clearness index | Daily Radiation (kWh/m2/day) |
January | 0.438 | 1.110 |
February | 0.494 | 1.970 |
March | 0.520 | 3.250 |
April | 0.559 | 4.890 |
May | 0.534 | 5.710 |
June | 0.529 | 6.100 |
July | 0.575 | 6.380 |
August | 0.565 | 5.340 |
September | 0.540 | 3.830 |
October | 0.523 | 2.430 |
November | 0.463 | 1.320 |
December | 0.439 | 0.930 |
Month | Average Wind Speed (m/s) |
January | 5.670 |
February | 5.620 |
March | 5.640 |
April | 6.180 |
May | 6.320 |
June | 5.830 |
July | 5.260 |
August | 5.100 |
September | 5.480 |
October | 5.910 |
November | 5.590 |
December | 5.770 |
![]() |
![]() |
Solar PV | Type 1A | Type 1B | Unit |
Rated capacity | 27.3 | 50.8 | kW |
Mean output | 4.45 | 8.30 | kW |
Mean daily Output | 107 | 199 | kWh/d |
Capacity factor | 16.3 | 16.3 | % |
Hours of operation | 4, 377 | 4, 377 | hrs/yr |
PV penetration | 330 | 331 | % |
Battery | |||
Number | 64 | 128 | (4bt/string) |
String in parallel | 16 | 32 | Strings |
Bus voltage | 48 | 48 | V |
Nominal capacity | 168 | 336 | kWh |
Usable nominal capacity | 118 | 235 | kWh |
Energy in | 3, 860 | 15, 244 | kWh/yr |
Energy out | 3, 294 | 12, 982 | kWh/yr |
Solar PV | Type 2A | Type 2B | Unit |
Rated capacity | 27.3 | 50.8 | kW |
Mean output | 4.45 | 8.30 | kW |
Mean daily output | 107 | 199 | kWh/d |
Capacity factor | 16.3 | 16.3 | % |
Hours of operation | 4, 377 | 4, 377 | hrs/yr |
PV penetration | 330 | 331 | % |
Wind | |||
Total rated capacity | 3.30 | 3.30 | kW |
Mean output | 0.669 | 0.669 | kW |
Total production | 5, 862 | 5, 862 | kWh/yr |
Capacity factor | 20.3 | 20.3 | % |
Hours of operation | 7, 329 | 7, 329 | hrs/yr |
Wind penetration | 49.5 | 26.7 | % |
Battery | |||
Number | 64 | 128 | (4bt/string) |
String in parallel | 16 | 32 | Strings |
Bus voltage | 48 | 48 | V |
Nominal capacity | 168 | 336 | kWh |
Usable nominal capacity | 118 | 235 | kWh |
Energy in | 3, 860 | 15, 244 | kWh/yr |
Energy out | 3, 294 | 12, 982 | kWh/yr |
SR (kWh/m2/day) | WS (m/s) | PV (kW) | WT (kW) | BS (St) | NPC ($1, 000) | COE ($) | Unmet (%) |
0.93 | 5.1 | 8.09 | 8 | 30 | 304 | 1.07 | 0.0494 |
0.93 | 5.7 | 20.5 | 5 | 29 | 229 | 0.81 | 0.0546 |
0.93 | 6.32 | 4.87 | 5 | 30 | 213 | 0.75 | 0.0583 |
3.61 | 5.1 | 50.8 | - | 32 | 131 | 0.46 | 0.0636 |
3.61 | 5.7 | 50.8 | - | 32 | 131 | 0.46 | 0.0636 |
3.61 | 6.32 | 50.8 | - | 32 | 131 | 0.46 | 0.0636 |
6.38 | 5.1 | 25.2 | - | 27 | 98 | 0.35 | 0.0797 |
6.38 | 5.7 | 25.2 | - | 27 | 98 | 0.35 | 0.0797 |
6.38 | 6.32 | 25.2 | - | 27 | 98 | 0.35 | 0.0797 |
Month | Clearness index | Daily Radiation (kWh/m2/day) |
January | 0.438 | 1.110 |
February | 0.494 | 1.970 |
March | 0.520 | 3.250 |
April | 0.559 | 4.890 |
May | 0.534 | 5.710 |
June | 0.529 | 6.100 |
July | 0.575 | 6.380 |
August | 0.565 | 5.340 |
September | 0.540 | 3.830 |
October | 0.523 | 2.430 |
November | 0.463 | 1.320 |
December | 0.439 | 0.930 |
Month | Average Wind Speed (m/s) |
January | 5.670 |
February | 5.620 |
March | 5.640 |
April | 6.180 |
May | 6.320 |
June | 5.830 |
July | 5.260 |
August | 5.100 |
September | 5.480 |
October | 5.910 |
November | 5.590 |
December | 5.770 |
![]() |
![]() |
Solar PV | Type 1A | Type 1B | Unit |
Rated capacity | 27.3 | 50.8 | kW |
Mean output | 4.45 | 8.30 | kW |
Mean daily Output | 107 | 199 | kWh/d |
Capacity factor | 16.3 | 16.3 | % |
Hours of operation | 4, 377 | 4, 377 | hrs/yr |
PV penetration | 330 | 331 | % |
Battery | |||
Number | 64 | 128 | (4bt/string) |
String in parallel | 16 | 32 | Strings |
Bus voltage | 48 | 48 | V |
Nominal capacity | 168 | 336 | kWh |
Usable nominal capacity | 118 | 235 | kWh |
Energy in | 3, 860 | 15, 244 | kWh/yr |
Energy out | 3, 294 | 12, 982 | kWh/yr |
Solar PV | Type 2A | Type 2B | Unit |
Rated capacity | 27.3 | 50.8 | kW |
Mean output | 4.45 | 8.30 | kW |
Mean daily output | 107 | 199 | kWh/d |
Capacity factor | 16.3 | 16.3 | % |
Hours of operation | 4, 377 | 4, 377 | hrs/yr |
PV penetration | 330 | 331 | % |
Wind | |||
Total rated capacity | 3.30 | 3.30 | kW |
Mean output | 0.669 | 0.669 | kW |
Total production | 5, 862 | 5, 862 | kWh/yr |
Capacity factor | 20.3 | 20.3 | % |
Hours of operation | 7, 329 | 7, 329 | hrs/yr |
Wind penetration | 49.5 | 26.7 | % |
Battery | |||
Number | 64 | 128 | (4bt/string) |
String in parallel | 16 | 32 | Strings |
Bus voltage | 48 | 48 | V |
Nominal capacity | 168 | 336 | kWh |
Usable nominal capacity | 118 | 235 | kWh |
Energy in | 3, 860 | 15, 244 | kWh/yr |
Energy out | 3, 294 | 12, 982 | kWh/yr |
SR (kWh/m2/day) | WS (m/s) | PV (kW) | WT (kW) | BS (St) | NPC ($1, 000) | COE ($) | Unmet (%) |
0.93 | 5.1 | 8.09 | 8 | 30 | 304 | 1.07 | 0.0494 |
0.93 | 5.7 | 20.5 | 5 | 29 | 229 | 0.81 | 0.0546 |
0.93 | 6.32 | 4.87 | 5 | 30 | 213 | 0.75 | 0.0583 |
3.61 | 5.1 | 50.8 | - | 32 | 131 | 0.46 | 0.0636 |
3.61 | 5.7 | 50.8 | - | 32 | 131 | 0.46 | 0.0636 |
3.61 | 6.32 | 50.8 | - | 32 | 131 | 0.46 | 0.0636 |
6.38 | 5.1 | 25.2 | - | 27 | 98 | 0.35 | 0.0797 |
6.38 | 5.7 | 25.2 | - | 27 | 98 | 0.35 | 0.0797 |
6.38 | 6.32 | 25.2 | - | 27 | 98 | 0.35 | 0.0797 |