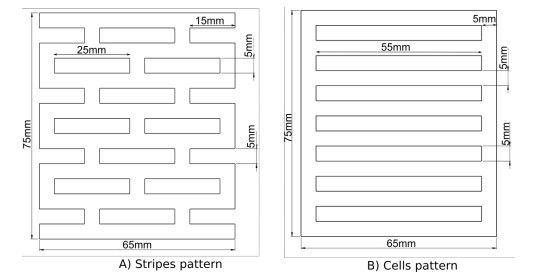
This paper presents the influence of cuts inspired by kirigami art on the outer surface of a soft actuator with cylindrical geometry. Both the kirigami pattern and orientation were varied to achieve expanding, bending, and twisting motions. Two symmetric kirigami patterns are presented, i.e., cells and stripes, in a horizontal, vertical, and tilted configurations, respectively. We also present the tensile response of the kirigami sheets by using the finite element method (FEM). Then, we show that the soft actuator expands, bends or twists when kirigami patterns are wrapped around it. All actuators were analyzed by performing FEM simulations to evaluate the effects of kirigami patterns on the actuator performance. Among the obtained variants of the expanding and bending actuators, the striped pattern provided the best performance for both motions. We show how the number of cuts and the relationship between the gaps affect the expanding performance. For the twisting motion, we obtained two variants; we present the influence of the change of the inclination angle for both patterns, i.e., cells and stripes. The actuators that presented the best performance for each motion were built; a manufacturing process using the casting technique is described. The validation of the hardware by computer vision is presented.
Citation: X. Yamile Sandoval-Castro, Eduardo Castillo-Castaneda, Benigno Munoz-Barron, Maximiano F. Ruiz-Torres. Mechanical programmable design of soft pneumatic actuators with kirigami patterns to generate expanding, bending and twisting motions[J]. STEM Education, 2023, 3(1): 15-27. doi: 10.3934/steme.2023002
[1] | Arosh S. Perera Molligoda Arachchige, Kamel Chebaro, Alice J. M. Jelmoni . Advances in large language models: ChatGPT expands the horizons of neuroscience. STEM Education, 2023, 3(4): 263-272. doi: 10.3934/steme.2023016 |
[2] | Tang Wee Teo, Zi Qi Peh . An exploratory study on eye-gaze patterns of experts and novices of science inference graph items. STEM Education, 2023, 3(3): 205-229. doi: 10.3934/steme.2023013 |
[3] | Tang Wee Teo, Aik Ling Tan, Ban Heng Choy . "It feels different when blindfolded": Developing social empathy through inclusive designs in STEM. STEM Education, 2024, 4(1): 20-34. doi: 10.3934/steme.2024002 |
[4] | Ruiheng Cai, Feng-kuang Chiang . A laser-cutting-centered STEM course for improving engineering problem-solving skills of high school students in China. STEM Education, 2021, 1(3): 199-224. doi: 10.3934/steme.2021015 |
[5] | Rommel AlAli, Wardat Yousef . Enhancing student motivation and achievement in science classrooms through STEM education. STEM Education, 2024, 4(3): 183-198. doi: 10.3934/steme.2024012 |
[6] | Christopher C. Tisdell . Reimagining multiplication as diagrammatic and dynamic concepts via cutting, pasting and rescaling actions. STEM Education, 2021, 1(3): 170-185. doi: 10.3934/steme.2021013 |
[7] | Christopher C. Tisdell, David Bee Olmedo . Beyond the compass: Exploring geometric constructions via a circle arc template and a straightedge. STEM Education, 2022, 2(1): 1-36. doi: 10.3934/steme.2022001 |
[8] | Med Amine LARIBI . Optimal synthesis of a planar mechanism using Matlab: Example of slider crank in a rowing motion. STEM Education, 2023, 3(1): 1-14. doi: 10.3934/steme.2023001 |
[9] | Joshua Oluwatoyin Adeleke, Hameed Adedeji Balogun, Musa Adekunle Ayanwale . Assessment of content and cognitive dimensions of learners' mathematics performance. STEM Education, 2025, 5(3): 383-400. doi: 10.3934/steme.2025019 |
[10] | Fadhilah Jamaluddin, Ahmad Zabidi Abdul Razak, Suzieleez Syrene Abdul Rahim . Navigating the challenges and future pathways of STEM education in Asia-Pacific region: A comprehensive scoping review. STEM Education, 2025, 5(1): 53-88. doi: 10.3934/steme.2025004 |
This paper presents the influence of cuts inspired by kirigami art on the outer surface of a soft actuator with cylindrical geometry. Both the kirigami pattern and orientation were varied to achieve expanding, bending, and twisting motions. Two symmetric kirigami patterns are presented, i.e., cells and stripes, in a horizontal, vertical, and tilted configurations, respectively. We also present the tensile response of the kirigami sheets by using the finite element method (FEM). Then, we show that the soft actuator expands, bends or twists when kirigami patterns are wrapped around it. All actuators were analyzed by performing FEM simulations to evaluate the effects of kirigami patterns on the actuator performance. Among the obtained variants of the expanding and bending actuators, the striped pattern provided the best performance for both motions. We show how the number of cuts and the relationship between the gaps affect the expanding performance. For the twisting motion, we obtained two variants; we present the influence of the change of the inclination angle for both patterns, i.e., cells and stripes. The actuators that presented the best performance for each motion were built; a manufacturing process using the casting technique is described. The validation of the hardware by computer vision is presented.
In recent years, several investigations have focused on the study of elastic inflatable actuators (EIAs) [1,2,3,4,5,6,7,8,9]. Actuators have been developed that can generate expanding [1], contraction [2], bending [3] and twisting motions [6,7] using chambers [3], channels [8], and reinforcing fibers [1]. Multiple motions have even been studied in a single soft actuator. On the other hand, these motions have been generated by using origami inspired designs [10,11,12] that are mainly used for artificial muscles [13,14] and manipulators [15,16].
Moreover, kirigami, the Japanese art of cutting, has not been widely used for EIA design. However, interesting results have been presented in different fields. kirigami comes from the Japanese words "kiru" (to cut) and "kami" (paper), and this technique presents several variants. The pop-up pattern enables the creation of 3D structures from 2D sheets and is commonly used to create actuation mechanisms and sensors that can be easily assembled and disassembled [17]. The self-similar repeating fractal kirigami pattern can be enlarged or reduced to create a variety of sizes and shapes [18]; this pattern is often used to develop soft and flexible sensors. A recurring pattern in kirigami that looks like the bones in a fish's skeleton is called the herringbone pattern, and it is used to create flexible, lightweight structures with high strength and stiffness [19]. Several kirigami patterns exist, each with a unique geometry and set of characteristics. Since its features include being lightweight with high strength, flexibility and variable stiffness, kirigami has been studied in different research areas. Further, most designs are generally symmetrical.
Kirigami has been studied primarily for its highly stretchable properties, particularly in fields such as mathematics [20], physics [21], materials science [22,23,24,25,26,27], medicine [28,29], energy [30] and even smart textiles and architecture. In soft robotics, a snake-inspired synthetic skin was designed to provide locomotion to a simple expanding soft actuator [31]. Then, the authors introduced a synthetic skin that dramatically improved the locomotion performance of the actuator [32].
Because kirigami features create geometric deformations that dominate the inherent elasticity of matter, particularly the properties and structures of kirigami metamaterials are controlled by the pattern and orientation of the cuts [33].
In this research, we show that a kirigami pattern wrapped in a simple cylindrical soft actuator can generate expanding, bending and twisting motions. kirigami enables the transformation of versatile shapes into complex architectures with simplified fabrication and unconventional structural geometries. We present a comparison between the kirigami patterns, stripes and cells. Furthermore, a manufacturing process that employs a casting technique is reported. Experimental validation was also performed.
In this section we present the proposal for two kirigami patterns, A) cells and B) stripes, as shown in Figure 1; the geometrical parameters consider cut sections of 5 mm in width with the same distance between them and a depth of 2 mm.
We have studied the mechanical response of these patterns in soft structures in horizontal, vertical, and tilted configurations under uniaxial tension. We considered a rubber sheet made of Mold Star 15 SLOW from the manufacturer Smooth-On; it is a hyperelastic material that allows repeated elastic loading and unloading without undergoing plastic deformation under large stress [21,28,29,30].
The uniaxial tensile response of kirigami sheets was performed by stretching patterns with different cuts. We performed this test using finite element method (FEM) simulations. The boundary conditions consider the fixation of the top of the structures, gravity and the stress at the bottom. Yeoh's hyperelastic model for the Mold Star 15 SLOW material, as described in [34] was used.
In Figure 2 we show the simulated stress-strain responses for the kirigami patterns. Figure 2A shows the pattern of horizontal cells reaching strains above 66% (50mm displacement). The structure of the horizontal cells resists the tensile force. Figure 2B shows the pattern of vertical cells, which reaches strains over 310% (233.2mm displacement). Figure 2C shows the pattern of horizontal stripes, which reaches strains over 333% (250mm displacement). This kirigami pattern achieves higher strains compared to the cell patterns because the stiffness is lower. Figure 2D shows the same pattern in a vertical configuration, reaching a strain of 333.3% (250mm displacement). Figure 2E and Figure 2F show the cell and stripe patterns tilted 45∘, reaching elongation of 315.9% (236mm displacement) and 333.3% (250mm displacement), respectively. In Figures 2E and 2F it can be seen that the inclined patterns stretch a high percentage, but also suffer a slight twist.
We designed a cylindrical soft actuator as a base for applying cuts to the outer surface by considering the kirigami patterns proposed in the previous section. Figure 3 shows the geometrical parameters of the actuator, such as the length, inner and outer radii and wall thickness. The cuts of the patterns were 5mm deep.
We proposed to wrap the cylindrical actuator with the cell and stripe patterns in both configurations, i.e., horizontal and vertical, obtaining four different soft expanding actuators as shown in Figure 3.
We evaluated the effects of the cuts on actuator performance during the expanding motion. The four soft expanding actuators shown in Figure 3 were activated with a maximum pressure of 34 kPa.
Figure 4 A-D graphically represent the results of the FEM simulations at the initial and final steps of the simulations. These figures show a comparison between the cylindrical actuator and the actuators wrapped with the horizontal and vertical cells and stripe patterns. Figure 4E shows the pressure-displacement relationship for the expanding motion.
To calculate the elongation, we used the Connolly's methodology described in [1], considering nodal coordinates placed on the top and bottom covers. Figure 4 reports that the horizontal stripe pattern allows the largest displacement, reaching 32.12mm in the axial direction.
However, geometric parameters such as the width, gap and the number of cuts can significantly modify the actuator's performance.
We present variations in the number of cuts, width, and gap of the horizontal stripes, maintaining the dimensions of the cylindrical actuator. The FEM simulations demonstrated that the number of cuts directly affects the performance of the actuator in the axial direction. However, the width-to-gap ratio of the stripe pattern has a greater influence on the actuator's performance in both directions, i.e. axial and radial. Figure 5 presents the relationship between displacement and pressure for the stripe pattern variations. The configuration with better performance in the axial direction is the 14 stripes width-to-gap ratio of 3–5 mm.
We proposed to make cuts in the center of the outer surface of the cylindrical actuator. Using the cells and the striped kirigami patterns in their horizontal and vertical configurations, we obtained four soft bending actuators (shown in Figure 3).
The four soft bending actuators were activated with a maximum pressure of 35 kPa; the bending angle was calculated by using the Connolly method [1]. Figure 6 shows the pressure-angle relationship for the bending motion. The graph shows that the horizontal stripe cuts give the best performance in bending, reaching 38.503∘. In terms of the stripe pattern, we used the configuration of 14 stripes with a width-to-gap ratio of 3–5 mm.
As can be seen in Figure 1, in their tilted configurations, both patterns, i.e., the cells and stripes, suffer a slight twist in the middle part during stress analysis. Using this concept, we made cuts on the outer surface of the cylindrical actuator, resulting in the two variants. The tilt angle (φ) on the kirigami pattern affects the performance of the pressure-angle relationship during torsion. We investigated the influence of the tilt angle for both patterns, i.e., cells and stripes.
Figure 7 reports the results of the FEM simulations for the variations in the tilt angle for the striped kirigami patterns of 20∘, 30∘, 40∘ and 50∘. The maximum angle, 100.3∘, was reached with an inclination of 20∘ at maximum pressure of 13 kPa.
Figure 8 shows the performance of the twisting motion due to the tilt angle variations in the cells pattern. The pattern inclined at 20∘ achieved 84.82∘ at 13 kPa.
The evaluations of the FEM simulations show that the horizontal stripe pattern has better performance in extension motion (14 stripes 5mm:3mm), as well as in bending and twisting.
The expanding, bending and twisting actuators based on the stripe pattern were manufactured by casting, using Mold Star 15 SLOW material from Smooth-On. Figure 9 shows the manufacturing process for the expanding actuator; the bending and twisting actuators were manufactured similarly. The main molds (Part A and Part B) were assembled with the channel molds as shown in Step 1; in this step, the elastomer is poured. The molds were then placed in a vacuum oven for 10 minutes at 35 kPa of pressure to remove the bubbles, as is shown in Step 2; the material was cured for four hours. Once the material had cured, we removed the channel molds from Parts A and B and insert a cylindrical mold in Part B.
In Step 3, a thin elastomer layer is placed around the mold of Part B; the elastomer layer serves as an adhesive to bond Part A and Part B during assembly. The cylindrical shape allows for proper assembly. The material must cure for 2 hours.
In step 4, the main body of the soft actuators is made by disassembling the molds. In Step 5, some elastomer is poured into the top cover mold to create a cover and an air inlet. The fresh elastomer form the connection between the top cover and the main body. The material is allowed to cure for 2 hours, then the actuator is removed from the mold.
In Step 6, the procedure of Step 5 is repeated, but with the lower cover mold. Finally, in Step 7, the expanding soft actuator for the stripe kirigami pattern is created.
The manufactured process described previously was used to construct the soft pneumatic actuators for the expanding, bending and twisting motions. The design of the actuators was set to be the stripes pattern; for expanding and bending we used the configuration of 14 stripes with a width-to-gap ratio of 3–5 mm. For twisting, we manufactured the configuration of 20∘.
We performed simulations of these configurations at higher pressures to allow for more broadly applicable experimental validations.
Validation of the hardware was performed by using computer vision. We placed circular markers on the top and bottom covers of each manufactured soft actuator; these markers were tracked during movement. The actuator to be evaluated was fixed; a camera was used to capture pictures in the position corresponding to each value of pressure. We performed six tests for each movement. We processed the images and calculated the linear and angular displacements for the three actuators.
Figure 10 reports the experimental performance of the expanding soft pneumatic actuator for the striped kirigami pattern versus the FEM simulations. The maximum value of pressure applied was 40 kPa; at this value, the maximum displacement in the axial direction was 46.83 mm.
On the other hand, we evaluated the performance of the bending soft actuator. By applying a maximum value of pressure of 43 kPa a bending angle of 64.36∘ was obtained. As is shown in Figure 11 the bending actuator tended toward a constant curvature.
The experimental evaluation for the twisting soft actuator using the kirigami pattern oriented at 20∘ is presented. Figure 12 shows that the actuator achieves a twisting angle of 105.56∘ at 13 kPa.
In this research, we investigated the use of irigami–the Japanese art of paper cutting– as a tool for the development of soft pneumatic actuators.
We have studied two patterns, i.e., cells and stripes in horizontal, vertical, and tilted configurations. Kirigami enables the transformation of versatile shapes into complex architectures with a simplified fabrication and unconventional structural geometries. We show that the studied kirigami patterns wrapped in a simple cylindrical soft actuator can generate expanding, bending, and twisting motions.
Kirigami patterns must be symmetrical so as not to restrict the range of motion of soft actuators. In addition, the use of smaller cuts in kirigami patterns significantly changes the deformation performance of the soft actuators, resulting in variations of the stiffness, strain, expanding, bending, and torsion twisting.
The horizontal stripe pattern maximizes the elongation of the spreading actuator and restricts its deformation in the radial direction. The number of cuts, width and spacing significantly change the performance of the actuator. We have specified a width-to-gap ratio of 2:1. This ratio reduces expanding in the radial direction and maintains stiffness. In contrast, the vertical stripe cuts favor expanding in the radial direction and limit the strain. The cuts in the center of the cylindrical actuator have higher stiffness for both patterns in the horizontal and vertical configurations.
The cell pattern showed greater stiffness in the twisting actuator, but the angle was limited. On the other hand, we report a simplified manufacturing process using the casting technique. The design of the molds prevents the formation of bubbles on the walls. We presented the fabrication process for the expanding actuator based on the horizontally striped kirigami, but we can fabricate any kirigami pattern. The validation of the hardware showed a very similar performance compared to the FEM simulations.
The proposed kirigami soft actuators were fabricated by using a single material and post-manufacturing process was not necessary, contrary to the actuators reported in [1]. An advantage of the kirigami as a concept for soft actuator design the development of lightweight structures with high strength and stiffness, in addition to the motion controlled by the kirigami patterns geometry.
We believe that our kirigami strategy for developing soft actuators opens the way for developing more complex and harder soft structures. As future work, we will study the effect of depth of cut on the actuator's stiffness; we propose to define a relationship between strain and stiffness, as well as the bending and twisting angle-to-stiffness ratios. In such a study, we will use the actuators in soft manipulation.
All authors declare no conflicts of interest in this paper.
[1] |
Connolly, F., Walsh, C.J. and Bertoldi, K., Automatic design of fiber-reinforced soft actuators for trajectory matching. Proceedings of the National Academy of Sciences, 2016,114(1): 51–56. https://doi.org/10.1073/pnas.1615140114 doi: 10.1073/pnas.1615140114
![]() |
[2] |
Gollob, S., Park, C., Koo, B.H.B. and Roche, E., A Modular Geometrical Framework for Modelling the Force-Contraction Profile of Vacuum-Powered Soft Actuators. Frontiers in Robotics and AI, 2021, 8: 606938. https://doi.org/10.3389/frobt.2021.606938 doi: 10.3389/frobt.2021.606938
![]() |
[3] |
She, Y., Chen, J., Shi, H. and Su, H., Modeling and Validation of a Novel Bending Actuator for Soft Robotics Applications. Soft Robotics, 2016, 3(2): 71–81. https://doi.org/10.1089/soro.2015.0022 doi: 10.1089/soro.2015.0022
![]() |
[4] |
Li, Y., Chen, Y., Ren, T., Li, Y. and Choi, S., Precharged Pneumatic Soft Actuators and Their Applications to Untethered Soft Robots. Soft Robotics, 2018, 5(5): 567–575. https://doi.org/10.1089/soro.2017.0090 doi: 10.1089/soro.2017.0090
![]() |
[5] | Wang, T. and Ge, L., Guoying Gu. Programmable design of soft pneu-net actuators with oblique chambers can generate coupled bending and twisting motions. Actuators A: Physical, 2021,271: 131–138. https://doi.org/10.1016/j.sna.2018.01.018 |
[6] |
Ainla, A., Verma, M.S., Yang, D. and Whitesides, G.M., Soft, Rotating Pneumatic Actuator. Soft Robotics, 2017, 4(3): 297–304. https://doi.org/10.1089/soro.2017.0090 doi: 10.1089/soro.2017.0090
![]() |
[7] |
Yan, J., Zhang, X., Xu, B. and Zhao, J.A., New Spiral-Type Inflatable Pure Torsional Soft Actuator. Soft Robotics, 2018, 5(5): 527–540. https://doi.org/10.1089/soro.2017.0040 doi: 10.1089/soro.2017.0040
![]() |
[8] | Zhang, Q. and Zhang, Z., A novel double layer, multi-channel soft pneumatic actuator that can achieve multiple motions, in 23rd International Conference on Mechatronics and Machine Vision In Practice (M2VIP). Nanjing, China, 2016, 1–6. https://doi.org/10.1109/M2VIP.2016.7827343 |
[9] |
Chen, W., Xiong, C., Liu, C., Li, P. and Chen, Y., Fabrication and Dynamic Modeling of Bidirectional Bending Soft Actuator Integrated with Optical Waveguide Curvature Sensor. Soft Robotics, 2019, 6(4): 495–506. https://doi.org/10.1089/soro.2018.0061 doi: 10.1089/soro.2018.0061
![]() |
[10] | Sandoval-Castro, X.Y., Garcia-morales, D.S., Raatz, A. and Castillo-Castaneda, E., Robust 3D Printed Modular Soft Pneumatic Actuator using Origami Concept for High Contraction Soft Systems, in 5th IEEE/IFToMM International Conference on Reconfigurable Mechanisms and Robots (ReMAR 2021). Canada, 2021,598–607. https://doi.org/10.32920/19469876.v1 |
[11] |
Zaghloul, A. and Bone, G.M., Origami-Inspired Soft Pneumatic Actuators: Generalization and Design Optimization. Actuators, 2023, 12(2): 72. https://doi.org/10.3390/act12020072 doi: 10.3390/act12020072
![]() |
[12] |
Shao, Z., Zhao, W., Zuo, Z., Li, J. and Chen, I., An Origami-Inspired Negative Pressure Folding Actuator Coupling Hardness with Softness. Actuators, 2023, 12(1): 35. https://doi.org/10.3390/act12010035 doi: 10.3390/act12010035
![]() |
[13] | Keya, J.J., Akter, M., Kabir, A., Ishii, S. and Kakugo, A., Fabrication of Artificial Muscle from Microtubules, Kinesins, and DNA Origami Nanostructures. Microtubules. Methods in Molecular Biology, 2022,231–240. https://doi.org/10.1007/978-1-0716-1983-4_15 |
[14] | Zhang, Q., Fang, H. and Xu, J., Tunable dynamics in Yoshimura origami by harnessing pneumatic pressure. Journal of Sound and Vibration, 2023,544. https://doi.org/10.1016/j.jsv.2022.117407 |
[15] |
Suzuki, H., Wood, R.J., Origami-inspired miniature manipulator for teleoperated microsurgery. Nature Machine Intelligence, 2020, 2(8): 437–446. https://doi.org/10.1038/s42256-020-0203-4 doi: 10.1038/s42256-020-0203-4
![]() |
[16] |
Huang, J., Zhou, J., Wang, Z., Law, J., Cao, H., Li, Y., et al., Modular Origami Soft Robot with the Perception of Interaction Force and Body Configuration. Advanced Intelligence Systems, 2022, 4: 2200081. https://doi.org/10.1002/aisy.202200081 doi: 10.1002/aisy.202200081
![]() |
[17] |
Overvelde, J.T.B., Kloek, T., D'haen, J.J.A. and Bertoldi, K., Amplifying the response of soft actuators by harnessing snap-through instabilities. Proceedings of the National Academy of Sciences, 2015,113(51): 14579–14584. https://doi.org/10.1073/pnas.1504947112 doi: 10.1073/pnas.1504947112
![]() |
[18] |
Lei, M., Hong, W., Zhao, Z., Hamel, C., Chen, M., Lu, H., et al., 3D Printing of Auxetic Metamaterials with Digitally Reprogrammable Shape. ACS Applied Materials and Interfaces, 2019, 11(25): 22768–22776. https://doi.org/10.1021/acsami.9b06081 doi: 10.1021/acsami.9b06081
![]() |
[19] |
Choi, W.J., Cheng, G., Huang, Z., Zhang, S., Norris, T.B. and Kotov, N.A., Terahertz circular dichroism spectroscopy of biomaterials enabled by kirigami polarization modulators. Nature Materials, 2019, 18: 820–826. https://doi.org/10.1038/s41563-019-0404-6 doi: 10.1038/s41563-019-0404-6
![]() |
[20] |
Castle, T., Sussman, D.M., Tanis, M. and Kamien, R.D., Additive lattice kirigami. Science Advances, 2016, 2(9): 8200–8205. https://doi.org/10.1126/sciadv.1601258 doi: 10.1126/sciadv.1601258
![]() |
[21] |
Rafsanjani, A. and Bertoldi, K., Buckling-Induced Kirigami. Physical review letters, 2017,118(8): 084301. https://doi.org/10.1103/PhysRevLett.118.084301 doi: 10.1103/PhysRevLett.118.084301
![]() |
[22] |
Shyu, T.C., Damasceno, P.F., Dodd, P.M., Lamoureux, A., Xu, L., Shlian, M.A., et al., kirigami approach to engineering elasticity in nanocomposites through patterned defects. Nature Materials, 2015, 14: 785–789. https://doi.org/10.1038/nmat4327 doi: 10.1038/nmat4327
![]() |
[23] |
Guan, Y.S., Zhang, Z., Tang, Y., Yin, J. and Ren, S., Kirigami-Inspired nanoconfined polymer conducting nanosheets with 2000% stretchability. Advanced Materials, 2018, 30: 1706390. https://doi.org/10.1002/adma.201706390 doi: 10.1002/adma.201706390
![]() |
[24] |
Wang, W., Li, C., Rodrigue, H., Yuan, F., Han, M.W., Cho, M., et al., Kirigami/Origami‐Based Soft Deployable Reflector for Optical Beam Steering. Advanced Materials, 2017, 27: 1604214. https://doi.org/10.1002/adfm.201604214 doi: 10.1002/adfm.201604214
![]() |
[25] |
Neville, R.M., Scarpa, F. and Pirrera, A., Shape morphing Kirigami mechanical metamaterials. Scientific Reports, 2016, 6: 31067. https://doi.org/10.1038/srep31067 doi: 10.1038/srep31067
![]() |
[26] |
Blees, M.K., Barnard, A.W., Rose, P.A., Roberts, S.P., McGill, K.L., Huang, P.Y., et al., Graphene Kirigami. Nature, 2015,524: 204–207. https://doi.org/10.1038/nature14588 doi: 10.1038/nature14588
![]() |
[27] |
Song, Z., Wang, X., Lv, C., An, Y., Liang, M., Ma, T., et al., Kirigami-based stretchable lithium-ion batteries. Scientific Reports, 2015, 5: 10988. https://doi.org/10.1038/srep10988 doi: 10.1038/srep10988
![]() |
[28] |
Zhao, R., Lin, S., Yuk, H. and Zhao, X., Kirigami enhances film adhesion. Soft Matter, 2018, 14: 2515–2525. https://doi.org/10.1039/C7SM02338C doi: 10.1039/C7SM02338C
![]() |
[29] |
Morikawa, Y., Yamagiwa, S., Sawahata, H., Numano, R., Koida, K., Ishida, M., et al., Ultrastretchable Kirigami Bioprobes. Advanced Healthcare Materials, 2018, 7: 1701100. https://doi.org/10.1002/adhm.201701100 doi: 10.1002/adhm.201701100
![]() |
[30] |
Lamoureux, A., Lee, K., Shlian, M., Forrest, S.R. and Shtein, M., Dynamic kirigami structures for integrated solar tracking. Nature Communications, 2015, 6: 8092. https://doi.org/10.1038/ncomms9092 doi: 10.1038/ncomms9092
![]() |
[31] |
Rafsanjani, A., Zhang, Y., Liu, B., Rubinstein, S.M. and Bertoldi, K., Kirigami skins make a simple soft actuator crawl. Science Robotics, 2018, 3(15): 75–55. 10.1126/scirobotics.aar7555 doi: 10.1126/scirobotics.aar7555
![]() |
[32] |
Rafsanjani, A., Jin, L., Deng, B. and Bertoldi, K., Propagation of pop ups in kirigami shells. Proceedings of the National Academy of Sciences, 2019,116(7): 8200–8205. https://doi.org/10.1073/pnas.1817763116 doi: 10.1073/pnas.1817763116
![]() |
[33] |
Hwang, D.G. and Bartlett, M.D., Tunable Mechanical Metamaterials through HybridKirigami Structures. Scientific Reports, 2018, 8: 3378. https://doi.org/10.1038/s41598-018-21479-7 doi: 10.1038/s41598-018-21479-7
![]() |
[34] | Cruz-Santos, N., Caracterización de elastómeros líquidos para análisis de deformaciones en Actuadores Inflables Elásticos, a través de la evaluación de modelos hiperelásticos. MSc thesis, 2020, 35. Instituto Politécnico Nacional, México. |