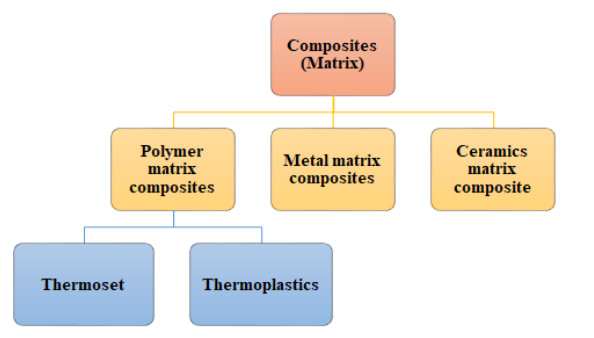
Environmental challenges associated with synthetic reinforcement in polymer composites, such as non-biodegradability and poor recyclability, require the exploration of various natural materials, especially from waste streams, to fully or partially replace such reinforcements. However, these natural fibers also present challenges such as high water absorption, low thermal stability, and average mechanical properties. To circumvent these problems, natural fiber-reinforced hybrid composites, which contain one or more types of natural reinforcement, are gaining increasing research interest. This paper presents a review of natural fiber-reinforced hybrid composites. Both thermoplastics and thermosets reinforced by natural and synthetic fibers (hybrid fibers) are reviewed. The properties of fibers and the resulting composites and processing techniques are summarized.
Citation: Kator Jeff Jomboh, Adele Dzikwi Garkida, Emmanuel Majiyebo Alemaka, Mohammed Kabir Yakubu, Vershima Cephas Alkali, Wilson Uzochukwu Eze, Nuhu Lawal. Properties and applications of natural, synthetic and hybrid fiber reinforced polymer composite: A review[J]. AIMS Materials Science, 2024, 11(4): 774-801. doi: 10.3934/matersci.2024038
[1] | Iketut Suarsana, Igpagus Suryawan, NPG Suardana, Suprapta Winaya, Rudy Soenoko, Budiarsa Suyasa, Wijaya Sunu, Made Rasta . Flexural strength of hybrid composite resin epoxy reinforced stinging nettle fiber with silane chemical treatment. AIMS Materials Science, 2021, 8(2): 185-199. doi: 10.3934/matersci.2021013 |
[2] | Prashant Tripathi, Vivek Kumar Gupta, Anurag Dixit, Raghvendra Kumar Mishra, Satpal Sharma . Development and characterization of low cost jute, bagasse and glass fiber reinforced advanced hybrid epoxy composites. AIMS Materials Science, 2018, 5(2): 320-337. doi: 10.3934/matersci.2018.2.320 |
[3] | Yong X. Gan . A review of electrohydrodynamic casting energy conversion polymer composites. AIMS Materials Science, 2018, 5(2): 206-225. doi: 10.3934/matersci.2018.2.206 |
[4] | Nurhusien Hassen Mohammed, Desalegn Wogaso Wolla . Optimization of machining parameters in drilling hybrid sisal-cotton fiber reinforced polyester composites. AIMS Materials Science, 2022, 9(1): 119-134. doi: 10.3934/matersci.2022008 |
[5] | Araya Abera Betelie, Yonas Tsegaye Megera, Daniel Telahun Redda, Antony Sinclair . Experimental investigation of fracture toughness for treated sisal epoxy composite. AIMS Materials Science, 2018, 5(1): 93-104. doi: 10.3934/matersci.2018.1.93 |
[6] | Mario Ceddia, Bartolomeo Trentadue . A review of carbon fiber-reinforced polymer composite used to solve stress shielding in total hip replacement. AIMS Materials Science, 2024, 11(3): 449-462. doi: 10.3934/matersci.2024023 |
[7] | Yohannes Regassa, Hirpa G. Lemu, Belete Sirhabizu . Investigation of spider web oriented composite fabrics burst strength. AIMS Materials Science, 2021, 8(4): 622-639. doi: 10.3934/matersci.2021038 |
[8] | Araya Abera Betelie, Anthony Nicholas Sinclair, Mark Kortschot, Yanxi Li, Daniel Tilahun Redda . Mechanical properties of sisal-epoxy composites as functions of fiber-to-epoxy ratio. AIMS Materials Science, 2019, 6(6): 985-996. doi: 10.3934/matersci.2019.6.985 |
[9] | Venkatarajan Subbarayalu, Subbu Chinnaraman, Athijayamani Ayyanar, Jayaseelan Chinnapalanisamy . Mechanical properties of vinyl ester hybrid composite laminates reinforced with screw pine and glass fiber. AIMS Materials Science, 2024, 11(1): 114-128. doi: 10.3934/matersci.2024007 |
[10] | Mnvrl Kumar, R. Ramakrishnan, Alnura Omarbekova, Santhosh Kumar. R . Experimental characterization of mechanical properties and microstructure study of polycarbonate (PC) reinforced acrylonitrile-butadiene-styrene (ABS) composite with varying PC loadings. AIMS Materials Science, 2021, 8(1): 18-28. doi: 10.3934/matersci.2021002 |
Environmental challenges associated with synthetic reinforcement in polymer composites, such as non-biodegradability and poor recyclability, require the exploration of various natural materials, especially from waste streams, to fully or partially replace such reinforcements. However, these natural fibers also present challenges such as high water absorption, low thermal stability, and average mechanical properties. To circumvent these problems, natural fiber-reinforced hybrid composites, which contain one or more types of natural reinforcement, are gaining increasing research interest. This paper presents a review of natural fiber-reinforced hybrid composites. Both thermoplastics and thermosets reinforced by natural and synthetic fibers (hybrid fibers) are reviewed. The properties of fibers and the resulting composites and processing techniques are summarized.
Composites have come to be known as versatile and valuable materials that can solve problems in different applications, improve productivity, lower costs, and facilitate the introduction of new properties in materials [1]. The distinctive properties of composites, as outlined by Egbo [2], stem from the unique characteristics of their individual components and their respective volume ratios and arrangements within the material system. Composites can be engineered to meet specific geometrical, structural, mechanical, chemical, thermal, and, in some cases, aesthetic requirements. With a growing demand for durable lightweight materials, the global market size of composites is projected to rise to about 130.83 billion dollars by 2024 [3]. Polymer-based composites are widely used today in industries such as biomedical engineering, automobiles, aerospace, marine, construction, packaging, industrial, sporting goods, and many others due to their numerous advantages, namely their satisfactory mechanical properties like tensile properties, flexural strength, fracture toughness, and strength, among others [4,5,6]. According to De et al. [7], fiber-reinforced polymer (FRP) composites have played a crucial role in replacing metals in numerous applications due to their superior properties, design flexibility, and ease of manufacturing. Before now, synthetic fibers such as carbon, aramid, and glass fibers took the lead in the reinforcement of polymer composite materials due to their strength, durability, and other superior properties. Currently, society has grown conscious of their non-biodegradability and poor recyclable status. Carbon fibers are non-biodegradable, costly, and difficult to recycle, often ending up in landfills [8]. Aramid fibers, like Kevlar, known for excellent thermal resistance with outstanding mechanical properties typical of synthetic fibers, share similar issues of non-biodegradability and have limited recycling options. Glass fibers, while recyclable, require energy-intensive processes and often degrade in quality, leading to a low recycling rate. All this gave natural fibers (e.g., jute, kenaf, hemp, banana, sisal, oil palm, bamboo, flax) an edge in polymer-reinforced composites due to their environmentally friendly nature, biodegradability, good recycling tendencies, low cost, low density, high strength to weight ratio, and availability in nature [9]. This change toward natural fibers is driven by their lower environmental impact, making them a more sustainable choice for the future [8,10,11]. However, natural fibers also present challenges—high water absorption, low thermal stability, and low mechanical properties due to fiber agglomeration and poor interfacial adhesion, among other reasons [12]. Further studies prove that natural fibers cannot rival the strength of synthetic fiber-reinforced composites [13]. To circumvent these problems, the solution according to Almansour [14], Singh and Singh [15], and Sergi et al. [16] is to hybridize natural and synthetic fiber reinforcement to obtain higher performance properties. The characteristic properties of composites are a result of the individual properties of their constituent parts and their respective volume fractions and arrangements in the material system [17].
Polymers are the most commonly used matrix for composite materials today [18]. This is because polymers are cheap and can be easily processed. Polymer matrix composites display ideal matrix materials because they are low-density, are conveniently processed, and display desirable mechanical features. They are either thermosets or thermoplastics polymers [19]. Other matrices include ceramic and metal matrices, as shown in Figure 1. Examples of polymer matrix composites are polyester, epoxy, bismaleimide, and phenolic matrices, while ceramic matrix composites include aluminum, titanium, or magnesium matrices. Examples of metal matrix composites include silicon carbide (SiC), silicon nitride (Si3N4), and aluminum oxide (Al2O3) matrices [20]. Thermosets are characterized by a well-bonded 3D molecular structure built up after curing. They are the most used polymers in composites today, becoming substantially infusible and insoluble when cured by thermal, chemical (catalyst or promoter), or other means. After curing, a thermoset cannot be returned to its uncured state. Thermoset matrices generally provide higher rigidity and are more chemically stable than thermoplastic matrices [12]. They include epoxy, polyester, and polyamide resin matrices. According to Squire et al. [21], thermosetting resins are tougher, with a better adhesion to metal substrates, and are more resistant to solvents and chemicals than thermoplastic. However, once cured, thermosetting resins are heat-stable and, unlike thermoplastic resin, will not revert back to the molten stage when reheated. Thermoset matrices are processed through resin transfer molding (RTM), vacuum-assisted resin transfer molding (VARTM), sheet molding compound (SMC), pultrusion, and hand lay-up. Each processing technique has distinct advantages and limitations depending on the type of matrix used (thermoset or thermoplastic), as shown in Table 1. Additionally, the geometry of the reinforcement materials (shape and size) also plays a significant role in determining the type of processing technique to be used. Fiber geometry can either be particulate, whiskers, or long/continuous fibers. While long fibers may be suitable for pultrusion, filament winding, and hand lay-up techniques, they are not suitable for the injection molding technique. They require careful alignment, which can maintain fiber orientation and achieve high mechanical performance. On the other hand, short fibers and particulate fibers are suitable for high-volume manufacturing techniques like injection molding and extrusion, which can handle the flow and distribution of these reinforcements within the polymer matrix. These techniques significantly influence the final properties of composite materials, such as mechanical strength, surface finish, fiber distribution, and void content. The choice of processing method is usually aligned with the specific requirements of the application, considering factors like part complexity, production volume, and cost considerations. Techniques like RTM and pultrusion produce high-quality and high-performance composites, while methods like hand lay-up and VARTM offer more flexibility and lower costs, making them suitable for different applications and production scales [22,23,24].
Thermoset matrices | Thermoplastic matrices | Influence on final properties | |||
Advantages | Limitations | Advantages | Limitations | ||
1. RTM | High-quality finish, excellent fiber wet-out, suitable for complex shapes, reduced void content | Longer curing times, careful control needed, higher tooling costs | Rapid cycle times, recyclability | Higher temperatures and pressures, challenging impregnation due to viscosity | High fiber volume, superior mechanical properties, reduced voids |
2. VARTM | Lower tooling costs, good for large parts, efficient for low-medium volumes | Longer infusion times, potential for dry spots, limited to low viscosity resins | Lower temperatures, possible use of lower viscosity resins | Difficult fiber wet-out, less effective for thermoplastics | Good mechanical properties, suitable for large parts, cost-effective |
3. Injection molding | High production rates, excellent finish, suitable for complex shapes | Limited to small-medium parts, high tooling costs, short mold life | Fast cycle times, re-processability, high-volume production | High initial costs, fiber length reduction | Efficient production, good finish, fiber orientation affect properties |
4. Compression molding | High fiber content, good dimensional stability, suitable for large shapes | Longer cycles, higher tooling costs, lower volumes | Shorter cycles, suitable for medium-large parts, re-processability | Higher temperatures and pressures, complex molds | High fiber content, good mechanical properties, mold design crucial |
5. Pultrusion | Continuous process, high fiber volume fraction, excellent mechanical properties, consistent cross-sectional shapes | Limited to linear profiles, higher setup costs, less flexibility in design changes | Rapid processing, recyclability, continuous production | High processing temperatures, limited to specific profile shapes | High strength and stiffness, suitable for structural applications like beams and rods |
6. SMC | High production rates, good surface finish, suitable for complex shapes | Limited to medium-sized parts, higher initial costs for equipment, less suited for high-performance applications | Fast cycle times, recyclability, high-volume production capability | High initial costs, reduced fiber length during processing | Balance of mechanical properties and production efficiency, often used in automotive applications |
7. Hand lay-up | Simple and low-cost method, suitable for large parts, flexibility in design | Labor-intensive, inconsistent quality, longer curing times, potential for higher void content | Flexibility in lay-up, recyclability of materials | More difficult to process, requires higher temperatures | Variable mechanical properties, heavily dependent on the skill of the operator, often used for prototypes and small production runs |
Thermoplastics, on the other hand, have a one- or two-dimensional molecular structure. Like thermosets, they also belong to the polymer matrix classification. They have plastic-like properties that can be melted or reshaped by applying heat and regain their shape after the removal of heat. This makes them different compared with thermosetting materials, which cannot be reshaped after heating [5]. They also present some processing challenges because of their relatively high viscosity. According to Rajak et al. [25], thermoplastic composites reinforced with natural fiber, in general, show poor strength performance when compared to thermoset composites; hence the addition of a second reinforcement, preferably a synthetic material. Thermoplastics resins include Nylon, cellulose, polyetheretherketone (PEEK), polycarbonate (PC), polypropylene (PP), and polyethylene (PE) [26].
The widespread adoption of thermoplastic matrices in advanced composites faces significant challenges: high processing temperatures and pressures, difficulties in achieving optimal fiber wetting and impregnation, poor interfacial bonding, limited material selection and compatibility, and higher costs. Researchers are actively addressing these challenges through the development of advanced processing techniques, the use of surface treatments and coupling agents, the incorporation of nanoparticles and additives, improvements in recycling methods, the creation of new thermoplastic resins, and the exploration of hybrid composites. These efforts are aimed at enhancing mechanical performance, reducing costs, and improving the sustainability of thermoplastic composites, thus making them more suitable for a wider range of applications [26,27,28].
Several research works evaluated polymer matrix composites using thermoplastics and thermosetting matrices with natural-, synthetic-, or hybrid-reinforcing materials, characterizing them in terms of mechanical performances, thermal properties, water absorbance behavior, and several other properties. This is due to the low cost, biodegradability, recyclability, and workability nature of polymer composite materials. However, thermosetting matrices have shown superior properties, thus the current trend in developing advanced composites. Also, synthetic wastes remain a challenge that needs continuous recyclability, which has resulted in hybridization with natural fibers.
Composites are also classified according to their reinforcement phases: fiber-reinforced composites (FRCs), laminar composites, or particulate composites (Figure 2). They are further separated into those containing discontinuous or continuous fibers as reinforcements [29]. They can be natural, synthetic, and hybrid fibers.
Natural fibers are made from natural materials of plants, animals, or minerals. They are sustainable materials that are easily available in nature and have advantages like low cost, light weight, renewability, biodegradability, and high specific properties [31]. According to Pecas et al. [32], there are dozens of natural fibers with different properties influencing their use in specific industrial applications across the world. These natural fibers are sourced mainly from plants comprised of cellulose as their major structural component or from animals, which are protein based (Figures 3 and 4). Natural fiber polymer composites are materials that combine natural fibers, such as jute, hemp, flax, sisal, bamboo, or coir, with a polymer matrix, such as polypropylene, polyethylene, or epoxy resin. Minerals are also classified as natural fibers but are avoided due to associated health issues drawn from their carcinogenic nature, which have led to their ban in many countries [33]. Examples of mineral fibers include asbestos, which is obtained from rocks. These rocks undergo unique treatments to produce heat-resistant and non-inflammable asbestos fiber. Various silicate minerals are known as asbestos due to their fibrous crystalline nature, such as the most commonly used anthophyllite, amphibole, and serpentine [34]. Other natural fibers are jute, linen, wool, cotton, wood, rice husk, silk, or hemp.
Lately, studies have focused mainly on natural-reinforced composites due to their low cost, low density, high specific properties, good biodegradability, ease of separation, enhanced energy recovery, CO2 neutrality, and recyclable nature, among other reasons. The automotive sector is one of the major industries that has benefited from natural-reinforced polymer composites, as natural fibers hold significant potential for being lightweight and environmentally friendly materials. Flax, hemp, kenaf, jute, sisal, and, more recently explored, Baobab fiber from a tropical tree in Africa have all found automobile applications in the form of door panels, armrests, seat back panels, headliners, or pillars, while sawdust is used as particleboard in the construction and building industries. Besides automotive applications, natural fiber composites find additional applications in construction, textiles, medical and pharmaceuticals, packaging, bioenergy, and biofuels, among others [4,32,35]. Natural fiber-reinforced composite boards have been manufactured using sawdust and other natural fibers in order to replace conventional materials like wood, metals, and asbestos [36]. Madu et al. [37] utilized rice hush and sawdust (natural-to-natural fiber hybrid reinforcement) as reinforcement in a polymer ceiling board composite using an optimal formulation. The product yielded a ceiling board with toughness, hardness, tensile, compressive, and flexural strengths of 3.72, 180.2, 19.68, 8.72, and 5.79 MPa, respectively, in conformity with ISO specifications. Hence, the study reported that rice husk-sawdust-reinforced polyester composites are suitable for ceiling board production when developed using the optimal formulation. Cost-effectiveness could also be ensured.
However, there are major issues associated with natural fibers; these gave birth to the hybridization of natural fibers with a second fiber (natural, mineral, or synthetic fibers). The essence is to achieve improved or superior properties such as moisture resistance and thermal stability [14]. Scholars have tackled challenges such as absorption, weathering resistance, strength, and tensile, flexural, ductility, and fracture toughness [1,38,39]. Kafi et al. [1] studied the mechanical properties of jute/glass fiber-reinforced unsaturated polyester hybrid composites and the effect of surface modification by ultraviolet radiation. Results showed that composites with a 1:3 ratio of jute to glass demonstrated improved mechanical properties. Also, UV-pretreated jute and glass fibers (1:3) at optimum intensities show the highest mechanical properties compared to untreated jute- and glass-based hybrid composites. The study concluded that jute-reinforced composites incorporated with glass fiber can easily be explored for better commercial structural applications. Also, superior mechanical properties such as tensile, flexural, and impact strengths were reported when Garadimani et al. [40] fabricated polymer hybrid composites using corn cob particles and e-glass fiber as reinforcement.
In a previous study, Rodriquez-Castellanos and Rodrigue [12] reported improved mechanical and thermal properties over neat natural fiber composites, as they follow the rule of hybrid mixture (RoHM) regardless of the matrix, manufacturing processing, and fiber combination. Also, hybrid polymer-based composite architectures that can simultaneously yield results of practical utility have been investigated. Motoc [41] accomplished this by comparing the theoretical predictions with the effective properties using available experimental data. Nurazzi et al. [23] suggested that natural fibers inherit a hydrophilic character, resulting in high moisture absorption, poor matrix-fiber interfacial adhesion, and poor fiber dispersion, thereby limiting their success in polymer reinforcement. They also show high flammable properties, thus limiting their applications. The solution to these limitations was reported to be a surface treatment to the natural fibers, which improves their surface adhesion and enhances the bonding properties of fibers with the matrix by removing the impurities present on the fiber surface. In studying the effect of particle size on the morphology of polyester and epoxy-based auto-hybrid composites, Jomboh et al. [42] reported that improper particle size distribution can also lead to poor interfacial adhesion and surface pores, resulting in high water absorption. High water absorption for composites could be due to geometry parameters, reinforcement volume, type variation, and interface interactions with the matrix system [41,43].
Enhancing desired fiber-matrix interfacial adhesion by chemical surface treatments using treatments like alkaline and silane treatment has come to be known as one major way to remedy the challenges of water absorption, low thermal stability, and inferior mechanical properties of natural fibers. Mohammed et al. [44] reported that the alkali treatment of fibers is the most prevalent and effective way for the chemical modification of fibers. The silane treatment, which resulted in the creation of strong covalent bonds, is known to marginally increase the strength qualities of natural fiber-reinforced composites.
In general, recent advancements in overcoming the challenges of high water absorption, low thermal stability, and inferior mechanical properties of natural fibers include chemical (e.g., silane coupling agents, alkali treatments) and physical treatments of fibers (e.g., plasma, corona), the use of nanotechnology (e.g., nano-fillers, nano-fibrillated cellulose), improved fiber dispersion techniques (e.g., high shear mixing, electrospinning), thermal treatments, modifications to the polymer matrix (e.g., high-performance polymers, additives), and hybrid reinforcement with synthetic fibers, which is the focus of this study. These innovations enhance interfacial adhesion, reduce fiber agglomeration, and improve the thermal stability of natural fiber composites [23,44].
Tailoring hybrid polymer composites with a unique spectrum of properties by taking advantage of structure/property relations and widely deployed measuring techniques is the main aim of the study. We report important implications for improved materials, their processing, and engineering applications.
Natural fiber polymer composites are characterized by being lightweight, low cost, and eco-friendly, and having high specific strength, specific stiffness, and biodegradability, among other properties. Due to these qualities, they are particularly appealing for a wide range of industrial uses. When adopting natural fibers, their safety, mechanical strength, stiffness enhancement of composites, lowering density, and environmental concerns should all be taken into account [47]. Also, the interaction of fiber and matrix at the interphase is a very important property in composites, as many failures can be traced to the type of interfacial interaction [48,49]. Additionally, Sahu and Gupta [50] highlighted the main drawbacks of natural fibers including hydrophilicity, poor thermal stability, and poor durability. Zeleke and Rotich [36] further stated that the properties of natural fibers greatly affect the performance of their reinforced composites. These characteristics include fineness, length, distribution, arrangement, and proportion of the fibers in the composite, as well as the direction of stacking within the composite structure.
Although natural fiber composites possess relatively good specific strength and stiffness properties, they often show relatively poor interfacial adhesion with respect to polymeric matrices, may contain relatively high levels of moisture, and have variable mechanical properties due to the method by which they were gathered and produced. These factors could lead to inconsistent mechanical properties of such composites, especially evident in poor interlaminar fracture toughness [18].
Typically, the reinforcement material of a composite is responsible for the mechanical strength and transfer loads in the composite. The matrix binds and maintains the alignment of the reinforcement material and protects the reinforcement from abrasion or the environment. The discrepancy in mechanical characteristics, according to Pecas et al. [32], is a problem of natural fibers' quality. Awais et al. [34] note that the mechanical properties of natural fibers (especially plant fibers) are influenced by the chemical composition, microfibrillar angle, degree of polymerization, fiber surface morphology, and defects. The chemical composition differs from plant to plant and even among different parts of the same plant. The properties mainly depend upon the content of each component of the fiber.
Natural fibers possess excellent specific strength and stiffness, which means they are strong and rigid relative to their weight. When combined with a polymer matrix, these properties can be further enhanced, resulting in composites that offer good strength-to-weight and stiffness-to-weight ratios. Also, compared to synthetic fibers, natural fibers are less abrasive, which can be advantageous in applications where contact with other materials or surfaces is a concern.
Natural fiber polymer composites offer several beneficial physical properties, including lightweight, high specific strength and stiffness, good impact resistance, low density, thermal insulation, biodegradability, non-abrasiveness, and lower cost compared to synthetic fiber composites. These properties make them suitable for applications where strength, impact resistance, thermal insulation, sustainability, and cost-effectiveness are required, or when lightweight materials are preferred, such as automotive components and sporting goods [24,32,33]. The use of natural fibers as reinforcement in polymer composites can contribute to the overall sustainability and environmental friendliness of the material. They are generally less expensive compared to synthetic fibers, making natural fiber polymer composites a cost-effective alternative in various applications. Natural fibers have relatively low densities, and when incorporated into a polymer matrix, they contribute to the overall reduction in composite density. However, specific properties can vary based on factors like fiber type, treatment, loading, matrix material, and manufacturing process. Mechanical properties are influenced by factors such as fiber alignment, interfacial bonding, and moisture absorption.
Thermal properties of natural fiber polymer composites refer to their behavior and characteristics in response to heat. These can be influenced by factors such as fiber content, fiber-matrix interface, processing conditions, and the presence of additives or reinforcements [33]. Therefore, the specific thermal behavior and performance of these composites may vary based on these factors and the intended application. Among the important thermal properties of these composites are thermal expansion, thermal conductivity, thermal stability, heat resistance, and fire resistance.
Natural fiber polymer composites generally exhibit lower thermal conductivity compared with pure polymer matrices. In other words, natural fibers have inherent thermal insulation properties, making them suitable for applications where thermal insulation is desired. According to Dhaliwal [51] and Patel et al. [52], natural fibers have hemicellulose, cellulose, and lignin as primary components. The high cellulose content in natural fibers results in high flammability, while the presence of silica or ash as well as higher crystallinity and lower polymerization of fiber microstructure may contribute to better fire resistance performance [18].
Natural fiber polymer composites can exhibit varying levels of fire resistance depending on the type of fiber, fiber treatment, and polymer matrix used. Some natural fibers, such as jute or hemp, have inherent fire-retardant properties, while others may require additional treatments or additives to enhance their fire resistance. Fire-resistant polymer matrices can also improve the overall fire performance of the composite. The resulting thermal expansion behavior of the composite depends on the fiber-matrix interaction and fiber orientation. The incorporation of natural fibers can help reduce the overall thermal expansion of the composite. Additionally, the heat resistance of natural fiber polymer composites depends on the thermal stability of both the fibers and the polymer matrix. Natural fibers may undergo thermal degradation at elevated temperatures, which can affect the overall mechanical and physical properties of the composite. Polymer matrices with good heat resistance help to maintain the integrity of the composite at high temperatures.
In summary, natural fiber polymer composites possess several important thermal properties. They generally exhibit lower thermal conductivity, making them suitable for applications requiring thermal insulation. The composite's thermal expansion behavior depends on the interaction between the natural fibers and the polymer matrix. Heat resistance is influenced by the thermal stability of both the fibers and the matrix. Adequate thermal stability ensures the composite can withstand processing temperatures and maintain its properties in high-temperature environments. Fire resistance varies based on fiber type, treatment, and matrix, with some fibers having inherent fire-retardant properties. The thermal properties are affected by factors like fiber content, interface, processing conditions, and additives/reinforcements.
Synthetic, mineral, and man-made fiber polymer composites are materials that combine various types of fibers, such as synthetic fibers (glass, carbon, acrylic, aramid), mineral fibers (glass wool, rock wool), or man-made fibers (ceramic, basalt) with a polymer matrix (Figure 5). These composites offer a range of properties depending on the specific fibers and matrix materials used. They are characterized by high strength and stiffness, excellent chemical resistance, superior thermal properties, low density, electrical conductivity (in some cases), fire resistance (with appropriate additives or fibers), sound absorption (in mineral fiber composites), and dimensional stability. These composites are utilized in various industries, including aerospace, automotive, construction, and electronics, for applications requiring mechanical performance, chemical resistance, thermal stability, lightweight structures, electrical conductivity, fire safety, sound absorption, and dimensional accuracy. The specific properties can be influenced by factors such as fiber type, matrix material, fiber loading, manufacturing processes, fiber orientation, interfacial bonding, and composite architecture.
Synthetic fibers are man-made fibers usually formed through chemical processes. They are typically known to improve specific properties. They are either organic, such as acrylic, nylon, polyester, aramid, and rayon, or inorganic, such as glass, carbon, and boron. They have the advantages of durability, high strength, and low cost and can sustain heavy loads and elasticity. Mineral fibers, on the other hand, are inorganic materials used in composites to enhance properties like strength, fire resistance, and insulation. Man-made fibers can be designed to suit a wide range of applications, from textiles to industrial materials. These man-made fibers can be engineered to possess specific properties, such as improved strength, durability, or flexibility, based on the desired application. These properties provide a broad overview of the characteristics of each type of fiber-polymer composite, bearing in mind that the specific properties of composite materials will depend on the type and combination of fibers and polymers used, as well as the manufacturing process. Also, the modification process can enhance the resistance of man-made fibers to environmental factors like UV radiation, moisture, and chemicals [33,53,54].
Among the advantages of synthetic, mineral, and man-made fibers and their composites are a high strength-to-weight ratio, high chemical resistance, low thermal expansion, low moisture absorption, fire resistance, electromagnetic transparency, corrosion resistance, thermal insulation, tailored properties, enhanced durability, and high dielectric strength. However, the specific properties of these composites can vary based on the types of fibers, fiber/matrix interactions, fiber loading, and manufacturing processes employed. Additionally, composite performance can be tailored by adjusting factors such as fiber orientation, interfacial bonding, and composite architecture. Also, compared with natural fibers, synthetic and mineral fibers are superior in strength and some other properties.
Synthetic fibers or man-made composites offer good mechanical strength and toughness, providing durability in various applications. These composites, especially those reinforced with fibers like carbon or aramid, exhibit high tensile strength and stiffness, contributing to their structural integrity. In terms of flexural strength, these composites show good resistance to bending forces, making them suitable for applications where flexural properties are crucial. Polymer materials reinforced with synthetic fibers such as glass offer high stiffness and weight ratio compared with natural fibers such as wood [55]. Generally, a number of factors influence the mechanical properties of polymer-reinforced composites. Key among those factors are fiber geometry, the secondary plastic processing method employed, fiber treatment, and the interfacial interaction between the phases (Figure 6).
Kafi et al. [1] studied the mechanical properties of jute/glass fiber-reinforced unsaturated polyester hybrid composites and the effect of surface modification by ultraviolet radiation. Results showed that a jute-to-glass ratio demonstrates improved mechanical properties. Synthetic fibers like carbon and aramid exhibit high tensile strength and stiffness, making them suitable for applications requiring lightweight but strong materials. Many synthetic fibers are resistant to chemicals, which makes them suitable for applications in harsh environments [56].
Mamolo and Sodano [57] enhanced the mechanical properties of carbon fiber-reinforced polymer (CFRP) composites by using a chlorinated aramid nanofiber (Cl-ANF) interphase, resulting in a 79.8% increase in interfacial shear strength and a 33.7% increase in short beam strength. This was achieved without compromising the tensile strength of the carbon fibers. Poor interfacial strength can reduce composite performance and cause failure, but ANFs, with their high tensile strength and polar functional groups, improve interfacial reinforcement. The chemically inert nature of carbon fibers was addressed by chlorinating ANFs and treating carbon fibers with oxygen plasma, enabling effective bonding through a dip-coating process. The study highlights Cl-ANFs' potential in high-performance applications like aerospace, automotive, and sports equipment, providing next-generation composites with enhanced properties and durability.
Most synthetic fibers have low moisture absorption rates, which is beneficial for applications where moisture resistance is important, and lower density compared with traditional materials, contributing to lightweight structures. Mineral fiber composites also have moderate-to-high densities, contributing to their structural mass. Man-made composites can be engineered to have a wide range of colors and surface finishes, providing versatility for aesthetic purposes. Depending on the type of mineral fiber used, the surface texture can range from smooth to rough, affecting the tactile and visual aspects of the material. Additionally, these composites exhibit excellent resistance to corrosion and chemical attack, making them suitable for applications in aggressive environments [36,58,59].
Man-made fiber composites are ideal for applications that require heat dissipation, since they can be designed to have controlled thermal conductivity. Depending on the chosen fibers and polymers, these composites can exhibit high thermal stability, making them suitable for applications exposed to elevated temperatures [60]. Feng et al. [61] developed nature-inspired energy dissipation sandwich composites reinforced with high-friction grapheme for vibration suppression. The study reported superior damping properties of sandwich composites compared with those of conventional blended composites and pure epoxy resin. Polydopamine was used to modify reduced graphene oxide and boost surface friction force.
Synthetic fibers generally have low coefficients of thermal expansion, which makes them useful in applications where dimensional stability under varying temperatures is crucial [62,63]. Mineral fibers like basalt and glass fibers have inherently high resistance to fire and high temperatures, making them suitable for applications in fire-prone environments. They are effective insulators, which makes them useful in applications where thermal insulation is required [64]. Certain synthetic fibers, like carbon fibers, are transparent to electromagnetic waves within specific frequency ranges, making them useful in applications requiring electromagnetic shielding [65]. Some mineral fibers, like glass fibers, have high dielectric strength, which is advantageous in applications requiring electrical insulation [66].
The combination of two or more reinforcement materials (natural, mineral, or synthetic) in the same matrix to form superior composites is referred to as hybrid composites (Figure 7). Generally, polymer matrix composites have the advantages of high tensile strength, high stiffness, high fracture toughness, good abrasion resistance, good puncture resistance, good corrosion resistance, and low cost. However, they present low thermal resistance and a high coefficient of thermal expansion. The need to improve such properties of polymer composites gave rise to hybridization.
Begum et al. [67] worked on the hybridization of natural/synthetic fibers as well as polymer hybrid composites that are reinforced with various combinations of nanometer-sized carbon and mineral fillers to improve their applications in the field of engineering and technology. Hybrid composites were developed to improve composites' properties, thereby overcoming challenges such as thermal stability, moisture absorption, brittleness, or surface quality. The idea, according to Rodriguez-Castellanos and Rodrigue [12], is to combine natural fibers with other fibers or particulate reinforcements, which can be of natural or synthetic origin, such as glass or rubber particles.
Umunakwe et al. [68] studied the mechanical properties and microstructure of hybrid vulcanized natural rubber filled with carbon black and nano-CaCO3 from Achatina achatina shells as a partial replacement of carbon black to produce vulcanized natural rubber (NR). They reported a significant improvement in the mechanical properties of vulcanized NR; however, the properties were inferior to those of the carbon black-reinforced sample, which they attributed to the poor dispersion of the nano-CaCO3 in vulcanized NR.
Kim [13] suggested that by hybridization of natural and synthetic fibers, it is possible to achieve a balance between performance properties and cost of the composites, which would not otherwise be obtained with a single kind of reinforcement. Also, Singh et al. [15] affirmed that hybridization of natural and synthetic fibers shows higher performance properties. There are three possible ways to hybridize natural fibers into composites based on the type of materials: natural-synthetic, natural-mineral, and natural-natural fibers [14].
Hybrid polymer composites combine different reinforcing materials with organic polymers to achieve enhanced properties. They offer improved mechanical strength, stiffness, toughness, and thermal stability. These composites can also be tailored for specific electrical, chemical, and thermal conductivities. They exhibit resistance to moisture, chemicals, and fatigue, and can be lightweight. By selecting reinforcing materials carefully, hybrid composites can be cost-effective and environmentally sustainable. Their versatility makes them valuable in automotive, aerospace, construction, and biomedical industries.
Hybrid polymer composites combine different types of reinforcements within a polymer matrix to enhance their mechanical properties. These composites can exhibit improved strength, stiffness, toughness, fatigue resistance, impact resistance, wear resistance, dimensional stability, and environmental resistance compared with pure polymers. The specific mechanical properties depend on factors such as the types, content, and arrangement of reinforcements, as well as the matrix material and manufacturing process. Factors like fiber/matrix interface, interfacial bonding, and reinforcement orientation also influence mechanical behavior. Careful selection and optimization of reinforcement types and their distribution are essential for achieving the desired mechanical properties in hybrid polymer composites [58].
Hybrid polymer composites exhibit superior strength in comparison with pure polymer matrices, primarily attributed to the synergistic effects of various reinforcements. This multifaceted enhancement leads to improved tensile, compressive, and flexural strength. Additionally, the modulus of elasticity, a fundamental property for applications necessitating rigidity and deformation resistance, experiences a substantial increase through hybridization. The utilization of multiple reinforcements further augments a multitude of properties, including toughness, fatigue resistance, impact resistance, wear resistance, and dimensional stability [18,20].
The combination of several reinforcements improves the composite's ability to absorb energy and sustain fracture, hence increasing overall durability. In terms of fatigue resistance, hybrid composites outperform their pure polymer equivalents in terms of cyclic loading and fatigue. The inclusion of numerous reinforcements prevents crack initiation and slows break propagation, eventually extending the fatigue life of the material.
Hybrid polymer composites offer a range of physical properties that can be tailored to meet specific application requirements. These composites can exhibit varying densities, water absorption behavior, surface hardness, and weathering resistance. The specific physical properties are also influenced by the types, content, and arrangement of reinforcements, as well as the matrix material and processing techniques used. Combining multiple types of reinforcements allows for a wide range of composite densities, providing flexibility in material selection for specific applications. The water absorption behavior of hybrid polymer composites is determined by the kind and content of reinforcements as well as the matrix material. Some reinforcements, such as natural fibers, may have inherent water-absorbing qualities, whereas synthetic fibers, such as carbon and glass fibers, have low water absorption. The use of hydrophobic reinforcements can minimize the overall water absorption of the composite [69,70].
Weathering resistance, which is used to determine how a material behaves to specific weather conditions and to forecast potential performance problems, is also an important feature of hybrid polymer composites [71]. The weathering resistance is influenced by the choice of reinforcements and the matrix material. Certain reinforcements, such as glass fibers or nanoparticles, can enhance the composite's resistance to UV radiation, moisture, and other environmental factors, making them suitable for outdoor applications. Also, the incorporation of certain reinforcements, such as ceramic particles or nanoparticles, can improve the surface hardness of hybrid polymer composites. This property is important in applications where resistance to wear and abrasion is required. Furthermore, depending on the type of reinforcements utilized, hybrid polymer composites might have varied optical characteristics. Composites containing glass fibers, for example, can be transparent or translucent, but composites with carbon fibers can be opaque. These optical qualities have applications in optics, displays, and architectural materials.
Thermal properties of hybrid polymer composites refer to their behavior and characteristics in response to heat. These properties are influenced by the type and arrangement of reinforcements as well as the polymer matrix used. Thermal properties of hybrid polymer composites can change depending on elements like the kind, quantity, and organization of reinforcements as well as the chosen polymer matrix. The thermal behavior of these composites can also be influenced by other elements including the fiber/matrix interface, interfacial bonding, and manufacturing procedures. To achieve the desired thermal characteristics in hybrid polymer composites, it is important to carefully choose and optimize the reinforcing types and their distribution within the matrix. These properties include thermal conductivity, heat resistance, thermal stability, thermal insulation, thermal expansion, and flame resistance [72].
The thermal conductivity of hybrid polymer composites can be tailored through strategic reinforcement selection in terms of type and concentration. Incorporating thermally conductive materials such as carbon fibers or ceramic particles represents a strategy for increasing the total thermal conductivity of the composite [73]. This property is critical in applications that require efficient heat transfer. Furthermore, depending on the combination of reinforcements and matrix material, hybrid polymer composites may have a unique coefficient of thermal expansion. The thermal expansion coefficients of various reinforcements vary, and their distribution within the matrix might influence the composite's overall thermal expansion behavior. As a result, the coefficient of thermal expansion of the hybrid composite can be purposely engineered to be either lower or higher than that of the matrix alone, depending on the application's unique requirements [74].
The thermal stability of both the reinforcements and the polymer matrix influences the heat resistance of hybrid polymer composites. The choice of reinforcements with high heat resistance, such as ceramic fibers or carbon fibers, can improve the composite's ability to withstand high temperatures without significant degradation. This property is crucial in applications involving exposure to elevated temperatures. Hybrid polymer composites find practical applications in scenarios necessitating thermal insulation, such as in construction materials or insulation panels, due to their inherent thermal insulating properties that effectively impede heat transfer [75,76]. In terms of thermal stability, these composites demonstrate the capability to endure the elevated temperatures encountered during the manufacturing process while retaining their desirable attributes. This resilience is achieved through the careful selection of reinforcements and matrix materials characterized by robust thermal stability. Additionally, hybrid polymer composites can be engineered to exhibit flame-retardant properties by incorporating specific reinforcements or additives. This enhances their resistance to ignition, flame spread, and heat release, making them suitable for applications requiring fire safety [72,77].
The issues associated with natural fibers, mentioned earlier, are what gave rise to the hybridization of natural fibers with a second fiber (natural, mineral, or synthetic). The essence is to achieve improved or superior properties such as moisture resistance and thermal stability properties [14]. Rodriguez‐Castellanos and Rodrigue [12] proved that the combination of natural and synthetic reinforcement showed improved thermal stability, impact strength, and water intake. Polymers on their own are established to have limitations such as low stiffness and low resistance to impact loading. Hence, the reinforcement of polymers enhances the mechanical as well as other properties that make composites suitable for various applications.
Hybrid composites combine natural and synthetic fibers to achieve a balance between performance and environmental sustainability. Increasing the amount of synthetic fibers generally improves mechanical performance, but it can have a negative impact on the composite's biodegradability and other environmental properties. For example, a higher content of synthetic fibers typically enhances strength, stiffness, and durability, but reduces overall biodegradability and eco-friendliness. Maintaining synthetic fiber content below 50% helps preserve biodegradability [24,78]. Also, balancing performance and biodegradability involves actions such as fiber treatment, surface modification, matrix selection, hybrid layering, and strategic placement of fibers [10,29].
Composites made from recycled materials show promise in material innovation, sustainability, and waste management. There are a lot of competitive composite materials being referred to as waste. Wood, for example, is a natural fiber, which has the advantages of low density, low price, and biodegradability as reinforcement in composites. It is also a natural insulator against heat and cold, making it a competitive composite material [79]. However, it also presents dimensional instability and inhomogeneous quality, resulting in low thermal stability, water absorption, and mechanical properties. Glass as synthetic fiber, on the other hand, is known to have low moisture absorption, good thermal resistance, better mechanical properties, and can transmit light [1,80]. Bringing these two materials together to produce a hybrid polymer composite will result in materials with improved properties. In other words, developing composites from recycled waste (natural and synthetic materials) offers a compromise between the more environmentally friendly and low-cost, but lower-performing, natural-reinforced composites and the improved quality but high-cost and non-biodegradable synthetic-reinforced composites, with the promise of better physical-thermal and mechanical properties.
By combining sawdust (natural fiber) and post-consumer glass (synthetic fiber), Jomboh [81] developed hybrid composite particle board materials with improved physical and thermal properties (Figures 8 and 9). The study established improved flame resistance properties of 3.34, 3.72, and 5.46 mm for hybrid samples of 13/27/60 wt.%, 20/20/60 wt.%, and 20/20/60 wt.%, respectively, compared with sawdust-reinforced particle board composites. Also, improved physical properties were reported, including water absorption with minimum values of 1.76%/1.46% and the highest value of hardness of 76.7/83.0 HV.
In [37], the weathering resistance of hybrid composites of natural and synthetic reinforcements was evaluated. Samples with 5/27.5/67.5 wt.%, 7/33/60 wt.%, and 20/20/60 wt.% and original tensile strength of 11.60, 19.76 and 10.25 MPa, respectively, had an improved tensile strength of 12.63, 22.84, and 12.85 MPa, respectively, indicating good resistance to weathering for particleboard applications. This suggests that the composite material has the ability to withstand outdoor service conditions, agreeing with Krishnaiah [82] and Almansour [14] on the hybridization of natural and synthetic fibers for optimum performance properties.
In summary, natural fibers offer renewable, biodegradable, and low-cost alternatives, contributing to a reduced environmental impact. However, their inherent variability in properties and susceptibility to environmental factors require careful selection and processing techniques. On the other hand, synthetic fibers offer consistent and tailored properties, making them indispensable in high-performance applications. The combination of these reinforcements has shown promise in achieving a balance between strength, stiffness, toughness, and environmental sustainability. The interface between natural and synthetic components, as well as the choice of matrix material, play pivotal roles in determining the final properties of the composite. Furthermore, advances in fabrication techniques, such as hybridization methods and improved matrix formulations, continue to broaden the horizons of these materials.
Applications of natural and synthetic-reinforced hybrid composites span across various industries, including automotive, aerospace, construction, and biomedical fields. Their lightweight nature, coupled with impressive mechanical properties, makes them an attractive choice for replacing conventional materials. Additionally, their potential to mitigate the environmental footprint in manufacturing processes aligns with the growing emphasis on sustainable practices. Nonetheless, challenges remain, including the need for further research in optimizing processing techniques, understanding long-term durability, and addressing end-of-life disposal considerations. Additionally, standardization and certification protocols for these materials will be crucial in ensuring their widespread adoption.
The use of computational methods is crucial for the design, analysis, and optimization of polymer-reinforced composites. Finite element analysis (FEA) is utilized to simulate mechanical behavior, stress distribution, and failure zones under various loading conditions [83,84]. Molecular dynamics (MD) evaluates interactions at the molecular level, with a focus on interfacial properties and adhesion between the polymer matrix and fibers. Multiscale modeling connects molecular interactions to macroscopic properties, bridging different length scales to enhance the optimization of composite materials. Computational fluid dynamics (CFD) is employed to simulate fluid flow and heat transfer during manufacturing processes such as resin transfer molding. Artificial intelligence (AI) and machine learning (ML) techniques are used to predict properties and optimize designs based on large datasets, thereby accelerating material discovery and design [85,86]. Phase-field modeling is utilized to simulate microstructural evolution, particularly for fracture and damage analysis. These methods collectively enhance the understanding, performance, and reliability of polymer-reinforced composites [87,88,89].
Jomboh et al. [38] employed a D-optimal mixture design to formulate an optimum composition of post-consumer glass- (PCG) and sawdust (SD)-reinforced polyester (UPR) hybrid composite using the resin casting technique. They investigated four response parameters: tensile strength, flexural strength, impact strength, and hardness. Their results show that tensile and flexural strength decreased with an increase in reinforcements. The impact strength was highly improved with the hybrid composition. Uzochukwu et al. [90] studied the mechanical properties of natural rubber/Baobab (Adansonia digitata) fiber nanocomposites using response surface methodology (pedagogical approach). They leverage the central composite design (CCD) in response surface methodology (RSM) to elucidate the effects of processing pressure, temperature, pressing time, and reinforcement loading on the mechanical properties of natural rubber/Baobab fiber nanocomposites. They reported that compression pressure had the least impact on the composite's Young's modulus and hardness, whereas processing temperature and reinforcement loading had the most profound impact—38.3% and 34.4% on the Young's modulus and hardness of the composite, respectively.
Furthermore, Adesina et al. [91] examined the influence of process parameters of spark plasma sintering (SPS) technique on the density and hardness properties of graphene (GNP)-reinforced polylactic acid (PLA) nanocomposites. Both the numerical and physical experiments showed hardness and density to be a function of the independent process parameters. Results show that the most desirable SPS processing parameters were 158.2 ℃ and 25.87 MPa. Raak et al. [92] also deployed response surface methodology to simultaneously optimize the electrical and mechanical properties of newly developed conducting biofibers made up of kenaf fiber/polyaniline (KF/PANI). The effect of process parameters such as PANI amount (1-10 wt.%), dopant concentration (5-25 N), and molar ratio of aniline/oxidant solutions (0.5-1.5) were studied. They reported that the responses correlated very well will the experimental values for the electrical and mechanical properties studied.
Johnson et al. [93] evaluated computational methods for predicting impact damage in composite structures and described progress in materials modeling and numerical simulations of the impact response of fiber-reinforced composite structures. They developed a continuum damage-mechanics (CDM) model for fabric-reinforced composites as a framework within which both in-ply and delamination failure may be modeled during impact loading. They were able to derive a damage-development equation and appropriate material parameters were determined from experiments.
Researchers benefit from computational approaches by engineering high-performance polymer composites, saving time, materials, and energy, and ensuring accuracy in material design and selection.
This review explores natural and synthetic reinforced hybrid composites, emphasizing their properties, applications, and environmental impact. It highlights the potential of integrating these materials for improved performance and sustainability. Computational methods in composite design are also reviewed. The review also gathered that composites made from recycled materials show promise in material innovation, sustainability, and waste management. This is a step in the right direction toward environmental sustainability. Natural fibers offer eco-friendly and cost-effective options, while synthetic fibers provide consistent and superior properties. The combination of both creates a balance between strength, stiffness, and environmental benefits. These composites find applications in various industries, from automotive to construction. Challenges include refining processing techniques and addressing end-of-life disposal. Overall, these hybrid composites hold great promise for advancing materials science and sustainability efforts. In conclusion, natural and synthetic-reinforced hybrid composites represent a promising frontier in materials science, poised to revolutionize industries with their remarkable combination of performance and sustainability. Continued research and development in this field will undoubtedly lead to even more innovative applications and a more sustainable future.
The authors declare they have not used Artificial Intelligence (AI) tools in the creation of this article.
Kator Jeff Jomboh: conceptualization, literature review, writing the original draft; Adele Dzikwi Garkida, Emmanuel Majiyebo Alemaka, Mohammed Kabir Yakubu, Vershima Cephas Alkali, Wilson Uzochukwu Eze: research advisors, conceptualization, review and editing, bringing expertise in areas of Glass, Polymer and Ceramics; Nuhu Lawal: assisted with review materials, review and editing.
The authors declare no conflict of interest.
[1] |
Kafi A, Abedin MZ, Beg MDH, et al. (2006) Study on the mechanical properties of jute/glass fibre-reinforced unsaturated polyester hybrid composites: Effect of surface modification by ultraviolet radiation. J Reinf Plast Comp 25: 575–588. https://doi.org/10.1177/0731684405056437 doi: 10.1177/0731684405056437
![]() |
[2] |
Egbo MK (2021) A fundamental review on composite materials and some of their applications in biomedical engineering. J King Saud Univ–Eng Sci 33: 557–568. https://doi.org/10.1016/j.jksues.2020.07.007 doi: 10.1016/j.jksues.2020.07.007
![]() |
[3] | SmiComposites (2018) The most popular composite fabrication methods. Available from: https://www.smicomposites.com/the-most-popular-composite-fabrication-methods/. |
[4] |
Keya KN, Kona NA, Koly FA, et al. (2019) Natural fiber reinforced polymer composites: history, types, advantages, and applications. Mater Eng Res 1: 69–85. https://doi.org/10.25082/MER.2019.02.006 doi: 10.25082/MER.2019.02.006
![]() |
[5] |
Saba N, Tahir PM, Jawaid M (2014) A review on potentiality of nano filler/natural fiber filled polymer hybrid composites. Polymers 6: 2247–2273. https://doi.org/10.3390/polym6082247 doi: 10.3390/polym6082247
![]() |
[6] |
Li H, Wang D, Zhang H, et al. (2022) Optimal design of vibro-impact resistant fiber reinforced composite plates with polyurea coating. Compos Struct 292: 115680. https://doi.org/10.1016/j.compstruct.2022.115680 doi: 10.1016/j.compstruct.2022.115680
![]() |
[7] |
De B, Bera M, Bhattacharjee D, et al. (2024) A comprehensive review on fiber-reinforced polymer composites: Raw materials to applications, recycling, and waste management. Progr Mater Sci 146: 101326. https://doi.org/10.1016/j.pmatsci.2024.101326 doi: 10.1016/j.pmatsci.2024.101326
![]() |
[8] |
Isa A, Nosbi N, Ismail MC, et al. (2022) A review on recycling of carbon fibers: Methods to reinforce and expected fiber composite degradations. Materials 15: 4991. https://doi.org/10.3390/ma15144991 doi: 10.3390/ma15144991
![]() |
[9] | Laouicia H, Benkhelladic A, Drouichea F, et al. (2024) Study of thermal and mechanical properties of fibers extracted from Algerian Agave americana L. and their polymer composites. Int J Mech Sci Adv Mat (IJMSAM) 1: 1–7. Available from: https://ensta.edu.dz/wp-content/uploads/2024/05/IJMSAM-24.pdf. |
[10] |
Ismail SO, Akpan E, Dhakal HN (2022) Review on natural plant fibers and their hybrid composites for structural applications: Recent trends and future perspectives. Compos Part C 9: 100322. https://doi.org/10.1016/j.jcomc.2022.100322 doi: 10.1016/j.jcomc.2022.100322
![]() |
[11] |
Aldosari SM, Alotaibi BM, Alblalaihid KS, et al. (2024) Mechanical recycling of carbon fibee-reinforced polymer in a circular economy. Polymers 16: 1363. https://doi.org/10.3390/polym16101363 doi: 10.3390/polym16101363
![]() |
[12] | Rodriguez‐Castellanos W, Rodrigue D (2016) Production and characterization of hybrid polymer composites based on natural fibers, In: Poletto M, Composites from Renewable and Sustainable Materials, London: IntechOpen Limited. http://dx.doi.org/10.5772/64995 |
[13] | Kim H (2014) Hybrid composites with natural fibers. Available from: Available from: https://core.ac.uk/download/pdf/33528249.pdf. |
[14] | Almansour FA (2009) Interlaminar fracture toughness behaviour of flax/basalt reinforced vinyl ester hybrid composites. Available from: https://researchportal.port.ac.uk/en/studentTheses/interlaminar-fracture-toughness-behaviour-of-flaxbasalt-reinforce. |
[15] |
Singh H, Singh T (2019) Effect of fillers of various sizes on mechanical characterization of natural fibee polymer hybrid composites: A review. Mater Today Proc 18: 5345–5350. https://doi.org/10.1016/j.matpr.2019.07.560 doi: 10.1016/j.matpr.2019.07.560
![]() |
[16] |
Sergi C, Sbardella F, Lilli M, et al. (2020) Hybrid cellulose–basalt polypropylene composites with enhanced compatibility: The role of coupling agent. Molecule 25: 4384. https://doi.org/10.3390/molecules25194384 doi: 10.3390/molecules25194384
![]() |
[17] |
Egbo MK (2020) A fundamental review on composite materials and some of their applications in biomedical engineering. J King Saud Univ–Eng Sci 33: 557–568. https://doi.org/10.1016/j.jksues.2020.07.007 doi: 10.1016/j.jksues.2020.07.007
![]() |
[18] | Techapaitoon M (2015) Tough natural-fiber composites. Available from: https://core.ac.uk/download/pdf/76996962.pdf. |
[19] | Dawoud MM, Saleh HM (2018) Introductory chapter: Background on composite materials, In: Saleh HEM, Koller M, Characterizations of Some Composite Materials, London: IntechOpen Limited. https://doi.org/10.5772/intechopen.80960 |
[20] | Advanced Materials in Transport Aircraft Structures "AMTAS" (2003) Overview of advanced composite materials and structures. Available from: https://courses.washington.edu/mengr450/Overview.pdf. |
[21] | Squire GN, Abhyankar A, Watson KJ (2008) Composite material manufactured from a binder system including waste powder coating powder. WO 2008/020768 A1. Available from: https://patentimages.storage.googleapis.com/07/c5/ce/c86429e304a908/WO2008020768A1.pdf. |
[22] |
Atmakuri A, Palevicius A, Vilkauskas A, et al. (2020) Review of hybrid fiber based composites with nano particles—Material properties and applications. Polymers 12: 2088. https://doi.org/10.3390/polym12092088 doi: 10.3390/polym12092088
![]() |
[23] |
Nurazzi NM, Asyraf MRM, Athiyah SF, et al. (2021) A review on mechanical performance of hybrid natural fiber polymer composites for structural applications. Polymers 13: 2170. https://doi.org/10.3390/polym13132170 doi: 10.3390/polym13132170
![]() |
[24] |
Premnath K, Arunprasath K, Sanjeevi R, et al. (2024) Natural/synthetic fiber reinforced hybrid composites on their mechanical behaviors—A review. Interactions 245: 111. https://doi.org/10.1007/s10751-024-01924-y doi: 10.1007/s10751-024-01924-y
![]() |
[25] |
Rajak DK, Pagar DD, Menezes PL, et al. (2019) Fiber-reinforced polymer composites: manufacturing, properties, and applications. Polymers 11: 1667. https://doi.org/10.3390/polym11101667 doi: 10.3390/polym11101667
![]() |
[26] |
Almushaikeh AM, Alaswad SO, Alsuhybani MS, et al. (2023) Manufacturing of carbon fiber reinforced thermoplastics and its recovery of carbon fiber: A review. Polym Test 122: 108029. https://doi.org/10.1016/j.polymertesting.2023.108029 doi: 10.1016/j.polymertesting.2023.108029
![]() |
[27] |
Obande W, Brádaigh CMO, Ray D (2021) Continuous fiber-reinforced thermoplastic acrylic-matrix composites prepared by liquid resin infusion—A review. Compos Part B-Eng 215: 108771. https://doi.org/10.1016/j.compositesb.2021.108771 doi: 10.1016/j.compositesb.2021.108771
![]() |
[28] |
Periasamy K, Kandare E, Das R, et al. (2023) Interfacial engineering methods in thermoplastic composites: An overview. Polymers 15: 415. https://doi.org/10.3390/polym15020415 doi: 10.3390/polym15020415
![]() |
[29] |
Jawaid M, Abdul Khalil HPS (2011) Cellulosic/synthetic fiber reinforced polymer hybrid composites: A review. Carbohydr Polym 86: 1–18. https://doi.org/10.1016/j.carbpol.2011.04.043 doi: 10.1016/j.carbpol.2011.04.043
![]() |
[30] |
Fredi G, Dorigato A, Fambri L, et al. (2020) Multifunctional structural composites for thermal energy storage. Multifunct Mater 3: 042001. https://doi.org/10.1088/2399-7532/abc60c doi: 10.1088/2399-7532/abc60c
![]() |
[31] | Girijappa YGT, Rangappa SM, Parameswaranpillai J, et al. (2019) Natural fibers as sustainable and renewable resource for development of eco-friendly composites: A comprehensive review. Frontiers Mater 6. https://doi.org/10.3389/fmats.2019.00226 |
[32] |
Peç as P, Carvalho H, Salman H, et al. (2018) Natural fiber composites and their applications. J Compos Sci 2: 66. https://doi.org/10.3390/jcs2040066 doi: 10.3390/jcs2040066
![]() |
[33] |
Pickering KL, Efendy MGA, Le TM (2016) A review of recent developments in natural fiber composites and their mechanical performance. Compos Part A Appl Sci Manuf 83: 98–112. https://doi.org/10.1016/j.compositesa.2015.08.038 doi: 10.1016/j.compositesa.2015.08.038
![]() |
[34] |
Awais H, Nawab Y, Amjad A, et al. (2021) Environmental benign natural fiber reinforced thermoplastic composites: A review. Compos Part C 4: 100082. https://doi.org/10.1016/j.jcomc.2020.100082 doi: 10.1016/j.jcomc.2020.100082
![]() |
[35] |
Uzochukwu MI, Eze WU, Garba P, et al. (2020) Study on the physico-mechanical properties of treated baobab fiber (Adansonia Digitata) nano-filler/epoxy composite. Multiscale and Multidiscip Model Exp and Des 3: 151–159. https://doi.org/10.1007/s41939-020-00068-0 doi: 10.1007/s41939-020-00068-0
![]() |
[36] |
Zeleke Y, Rotich GK (2021) Design and development of false ceiling board using polyvinyl acetate (PVAc) composite reinforced with false banana fibers and filled with sawdust. Int J Polym Sci 2021: 5542329. https://doi.org/10.1155/2021/5542329 doi: 10.1155/2021/5542329
![]() |
[37] | Madu OG, Nwankwojike BN, Ani OI (2018) Optimal design for rice husk-saw dust reinforced polyester ceiling board. AJER 7: 11–16. Available from: https://www.ajer.org/papers/Vol-7-issue-6/B07061116.pdf. |
[38] | Jomboh KJ, Yakubu MK, Eze WU, et al. (2023) Weathering resistance of post-consumer glass and sawdust reinforced polyester composites, In: Li BW, Ghosh D, Olevsky EA, et al, Advances in Powder and Ceramic Materials Science 2023. TMS 2023. The Minerals, Metals & Materials Series, Cham: Springer. https://doi.org/10.1007/978-3-031-22622-9_10 |
[39] | Jomboh KJ, Garkida AD, Alemaka EM, et al. (2023) Optimization of post-consumer glass and sawdust reinforced polyester hybrid composites by mixture design analysis, In: The Minerals, Metals & Materials Society, TMS 2023 152nd Annual Meeting & Exhibition Supplemental Proceedings. TMS 2023. The Minerals, Metals & Materials Series, Cham: Springer. https://doi.org/10.1007/978-3-031-22524-6_70 |
[40] | Garadimani KR, Raju GU, Kodancha KG (2015) Study on mechanical properties of corn cob particle and e-glass fiber reinforced hybrid polymer composites. Am J Mater Sci 5: 86–91. https://doi.10.5923/c.materials.201502.18 |
[41] | Motoc DL (2015) Tailoring the effective properties of hybrid polymer based composite materials. Available from: https://www.unitbv.ro/documente/cercetare/doctorat-postdoctorat/abilitare/teze-de-abilitare/motoc-dana/05-MOTOC_LUCA-Teza_abilitare_ENG.pdf. |
[42] | Jomboh KJ, Garkida AD, Alkali VC (2022) The effect of particle size on the morphology of polyester and epoxy-based auto-hybrid composites. In: The Minerals, Metals & Materials Society, TMS 2022 151st Annual Meeting & Exhibition Supplemental Proceedings. The Minerals, Metals & Materials Series, Cham: Springer, 599–608. https://doi.org/10.1007/978-3-030-92381-5_57 |
[43] | Intertek (2015) Taber Abrasion ASTM D1044 (Haze), ASTM D4060 (Weight Loss). Available from: https://www.intertek.com/polymers/testlopedia/taber-abrasion/. |
[44] |
Mohammed M, Jawad AJM, Mohammed AM, et al. (2023) Challenges and advancement in water absorption of natural fiber-reinforced polymer composites. Polym Test 124: 108083. https://doi.org/10.1016/j.polymertesting.2023.108083 doi: 10.1016/j.polymertesting.2023.108083
![]() |
[45] |
Khalid MA, Imran R, Arif ZU, et al. (2021) Developments in chemical treatments, manufacturing techniques and potential applications of natural-fibers-based biodegradable composites. Coatings 11: 293. https://doi.org/10.3390/coatings11030293 doi: 10.3390/coatings11030293
![]() |
[46] | Midani M, Elseify LA (2022) Natural fiber composites—A practical guide for industrial utilization. Int Fibre J. Available from: https://www.fiberjournal.com/natural-fiber-composites-a-practical-guide-for-industrial-utilization/. |
[47] | Petroudy SRD (2017) 3-Physical and mechanical properties of natural fibers, In: Fan M, Fu F, Advanced High Strength Natural Fibre Composites in Construction, Cambridge: Woodhead Publishing, 59–83. https://doi.org/10.1016/B978-0-08-100411-1.00003-0 |
[48] | Owonubi JS, Agwuncha CS, Anusionwu GC, et al. (2019) Fiber-matrix relationship for composites preparation, In: Pereira AB, Fernandes FAO, Renewable and Sustainable Composites, London: IntechOpen Limited. https://doi.org/10.5772/intechopen.84753 |
[49] | Eze WU, Yakubu MK, Buba MA, et al. (2022) Effect of nano-structured bambara nut shell (Vigna Subterranea (L) Verdc) as filler on the physical mechanical and morphological properties of epoxy matrix. J Mater Environ Sci 13: 1155–1170. Available from: https://www.jmaterenvironsci.com/Document/vol13/vol13_N10/JMES-2022-13104-Eze.pdf. |
[50] |
Sahu P, Gupta MK (2019) A review on the properties of natural fibers and its bio-composites: Effect of alkali treatment. J Mater Des Appl 234: 198–217. https://doi.org/10.1177/1464420719875163 doi: 10.1177/1464420719875163
![]() |
[51] | Dhaliwal JS (2019) Natural fibers: Application, In: Abbas M, Jeon HY, Generation, Development and Modifications of Natural Fibers, London: IntechOpen Limited. https://doi.org/doi:10.5772/intechopen.86884 |
[52] |
Patel R, Dhar P, Babaei-Ghazvini A, et al. (2023) Transforming lignin into renewable fuels, chemicals and materials: A review. Bioresour Technol Rep 22: 101463. https://doi.org/10.1016/j.biteb.2023.101463 doi: 10.1016/j.biteb.2023.101463
![]() |
[53] |
Ahmad R, Hamid R, Osman SA (2019) Physical and chemical modifications of plant fibers for reinforcement in cementitious composites. Adv Civil Eng 2019: 5185806. https://doi.org/10.1155/2019/5185806 doi: 10.1155/2019/5185806
![]() |
[54] |
Kamarudin SH, Basri MSM, Rayung M, et al. (2022) A review on natural fiber reinforced polymer composites (NFRPC) for sustainable industrial applications. Polymers 14: 3698. https://doi.org/10.3390/polym14173698 doi: 10.3390/polym14173698
![]() |
[55] | Begum K, Islam M (2013) Natural fiber as a substitute to synthetic fiber in polymer composites: A review. Res J Eng Sci 2278: 9472. Available from: https://www.isca.me/IJES/Archive/v2/i4/10.ISCA-RJEngS-2013-010.pdf. |
[56] |
Karim MA, Abdullah MZ, Deifalla AF, et al. (2023) An assessment of the processing parameters and application of fiber-reinforced polymers (FRPs) in the petroleum and natural gas industries: A review. Results Eng 18: 101091. https://doi.org/10.1016/j.rineng.2023.101091 doi: 10.1016/j.rineng.2023.101091
![]() |
[57] |
Mamolo SU, Sodano HA (2024) Interfacial reinforcement of carbon fiber composites through a chlorinated aramid nanofiber interphase. Compos Sci Tech 245: 110351. https://doi.org/10.1016/j.compscitech.2023.110351 doi: 10.1016/j.compscitech.2023.110351
![]() |
[58] | Nguyen H, Zatar W, Mutsuyoshi H (2017) Mechanical properties of hybrid polymer composite, In: Thakur VK, Thakur MK, Pappu A, Hybrid Polymer Composite Materials—Properties and Characterization, Cambridge: Woodhead Publishing, 83–113. https://doi.org/10.1016/B978-0-08-100787-7.00004-4 |
[59] |
Bavan DS, Kumar GCM (2012) Finite element analysis of a natural fiber (maize) composite beam. J Eng 2013: 450381. https://doi.org/10.1155/2013/450381 doi: 10.1155/2013/450381
![]() |
[60] |
Gupta MK, Srivastava RK (2016) Mechanical properties of hybrid fibers-reinforced polymer composite: A review. Poly-Plast Technol Eng 55: 626–642. https://doi.org/10.1080/03602559.2015.1098694 doi: 10.1080/03602559.2015.1098694
![]() |
[61] |
Feng J, Safaei B, Qin Z, et al. (2023) Nature-inspired energy dissipation sandwich composites reinforced with high-friction grapheme. Compos Sci Technol 233: 109925. https://doi.org/10.1016/j.compscitech.2023.109925 doi: 10.1016/j.compscitech.2023.109925
![]() |
[62] |
Rajak DK, Wagh PH, Linul E (2022) A review on synthetic fibers for polymer matrix composites: performance, failure modes and applications. Materials 15: 4790. https://doi.org/10.3390/ma15144790 doi: 10.3390/ma15144790
![]() |
[63] |
Zeeshan M, Ali M, Anjum AS, et al. (2021) Optimization of mechanical/thermal properties of glass/flax/waste cotton hybrid composite. J Indust Textil 51: 768–787. https://doi.org/10.1177/1528083719891420 doi: 10.1177/1528083719891420
![]() |
[64] |
Kessler E, Gadow R, Straub J (2016) Basalt, glass and carbon fibers and their fiber reinforced polymer composites under thermal and mechanical load. AIMS Mater Sci 3: 1561–1576. https://doi.org/10.3934/matersci.2016.4.1561 doi: 10.3934/matersci.2016.4.1561
![]() |
[65] | Maiti S, Islam MI, Uddin MA, et al. (2022) Sustainable fiber-reinforced composites: A review. Adv Sustainable Syst 2200258. https://doi.org/10.1002/adsu.202200258 |
[66] |
Munalli D, Dimitrakis G, Chronopoulos D, et al. (2019) Electromagnetic shielding effectiveness of carbon fiber reinforced composites. Compos Part B-Eng 173: 106906. https://doi.org/10.1016/j.compositesb.2019.106906 doi: 10.1016/j.compositesb.2019.106906
![]() |
[67] |
Begum S, Fazia S, Hashmi MSJ (2020) Polymer matrix composite with natural and synthetic fibers. Adv Mater Proc Tech 6: 547–564. https://doi.org/10.1080/2374068X.2020.1728645 doi: 10.1080/2374068X.2020.1728645
![]() |
[68] |
Umunakwe R, Oyetunji A, Adewuyi BO, et al. (2019) Mechanical properties and microstructure of hybrid vulcanized natural rubber filled with carbon black and nano-CaCO3 from achatina achatina shells. J Met Mater Miner 29: 80–89. https://doi.org/10.55713/jmmm.v29i4.555 doi: 10.55713/jmmm.v29i4.555
![]() |
[69] | Kausar A (2017) 5—Physical properties of hybrid polymer/clay composites, In: Thakur VK, Thakur MK, Pappu A, Hybrid Polymer Composite Materials—Properties and Characterization, Cambridge: Woodhead Publishing, 115–132. https://doi.org/10.1016/B978-0-08-100787-7.00005-6 |
[70] |
Abdul-Khalil HPS, Kang CW, Khairul A, et al. (2009) The effect of different laminations on mechanical and physical properties of hybrid composites. J Reinf Plast Compos 28: 1123–1137. https://doi.org/10.1177/0731684407087755 doi: 10.1177/0731684407087755
![]() |
[71] | Corrosionpedia (2018) Weathering test—What does weathering test mean. Available from: https://www.corrosionpedia.com/definition/1396/weathering. |
[72] |
Krishnasamy S, Thiagamani SMK, Kumar CM, et al. (2019) Recent advances in thermal properties of hybrid cellulosic fiber reinforced polymer composites. Int J Biol Macromol 141: 1–13. https://doi.org/10.1016/j.ijbiomac.2019.08.231 doi: 10.1016/j.ijbiomac.2019.08.231
![]() |
[73] |
Zheng X, Kim S, Park CV (2019) Enhancement of thermal conductivity of carbon fiber-reinforced polymer composite with copper and boron nitride particles. Compos Part A Appl Sci Manuf 121: 449–456. https://doi.org/10.1016/j.compositesa.2019.03.030 doi: 10.1016/j.compositesa.2019.03.030
![]() |
[74] |
Yang X, Liang C, Ma T, et al. (2018) A review on thermally conductive polymeric composites: Classification, measurement, model and equations, mechanism and fabrication methods. Adv Compos Hybrid Mater 1: 207–230. https://doi.org/10.1007/s42114-018-0031-8 doi: 10.1007/s42114-018-0031-8
![]() |
[75] |
Neto JSS, de Queiroz HFM, Aguiar RAA, et al. (2021) A review on the thermal characterization of natural and hybrid fiber composites. Polymers 13: 4425. https://doi.org/10.3390/polym13244425 doi: 10.3390/polym13244425
![]() |
[76] |
Ahmad S, Ali S, Salman M, et al. (2021) A comparative study on the effect of carbon-based and ceramic additives on the properties of fiber reinforced polymer matrix composites for high temperature applications. Ceram Inter 47: 33956–33971. https://doi.org/10.1016/j.ceramint.2021.08.356 doi: 10.1016/j.ceramint.2021.08.356
![]() |
[77] |
Kim Y, Lee S, Yoon H (2021) Fire-safe polymer composites: flame-retardant effect of nanofillers. Polymers 13: 540. https://doi.org/10.3390/polym13040540 doi: 10.3390/polym13040540
![]() |
[78] | Ngo TD (2018) Natural fibers for sustainable bio-composites, In: Günay E, Natural and Artificial Fiber-reinforced Composites as Renewable Sources, London: IntechOpen Limited. https://doi.org/10.5772/intechopen.71012 |
[79] |
Corinaldesi V (2012) Study of lightweight mortars made of wooden waste. Adv Mater Res 2012: 34–41. https://doi.org/10.4028/www.scientific.net/AMR.548.34 doi: 10.4028/www.scientific.net/AMR.548.34
![]() |
[80] | Vieitez ER, Eder P, Villanueva A, et al. (2011) End-of-waste criteria (EoW) for glass cullet: Technical proposals. Available from: https://www.researchgate.net/publication/257987351_Study_of_Lightweight_Mortars_Made_of_Wooden_Waste. |
[81] | Jomboh KJ (2023) Development of post-consumer glass and sawdust reinforced unsaturated polyester hybrid composite for particle board application, Ahmadu Bello University, Zaria. |
[82] | Krishnaiah P (2017) Development of polylactide and polypropylene composites reinforced with sisal fibers and halloysite nanotubes for automotive and structural engineering applications. Available from: http://eprints.nottingham.ac.uk/43498/1/PhD%20Thesis_Prakash%20Krishnaiah.pdf. |
[83] | Roylance D (2001) Finite element analysis. Available from: https://resources.saylor.org/wwwresources/archived/site/wp-content/uploads/2012/09/ME1023.2.3.pdf. |
[84] | Nikishkov GP (2004) Introduction to the finite element method. Available from: https://citeseerx.ist.psu.edu/document?repid = rep1 & type = pdf & doi = d3fc5d5051cb464be2e4238f18ddf54d40576ddb. |
[85] |
Liu Y, Zhao T, Ju W, et al. (2017) Materials discovery and design using machine learning. J Materiomics 3: 159–177. https://doi.org/10.1016/j.jmat.2017.08.002 doi: 10.1016/j.jmat.2017.08.002
![]() |
[86] |
Choi W, Advincula RC, Wu HF, et al. (2023) Artificial intelligence and machine learning in the design and additive manufacturing of responsive composites. MRS Communications 13: 714–724. https://doi.org/10.1557/s43579-023-00473-9 doi: 10.1557/s43579-023-00473-9
![]() |
[87] |
Steinhauser MO, Hiermaier S (2009) A review of computational methods in materials science: Examples from shock-wave and polymer physics. Int J Mol Sci 10: 5135–5216. https://doi.org/10.3390/ijms10125135 doi: 10.3390/ijms10125135
![]() |
[88] |
Müzel SD, Bonhin EP, Guimarães NM, et al. (2020) Application of the finite element method in the analysis of composite materials: A review. Polymers 12: 818. https://doi.org/10.3390/polym12040818 doi: 10.3390/polym12040818
![]() |
[89] |
Agarwal M, Pasupathy P, Wu X, et al. (2024) Multiscale computational and artificial intelligence modelsof linear and nonlinear composites. Small Sci 4: 2300185. https://doi.org/10.1002/smsc.202300185 doi: 10.1002/smsc.202300185
![]() |
[90] | Uzochukwu MI, Momoh OJ, Adebisi AA, et al. (2024) Evaluation of the mechanical properties of natural rubber/baobab (adansonia digitata) fiber nanocomposite using response surface methodology: A pedagogical approach. Chem Afr. https://doi.org/10.1007/s42250-024-00957-8 |
[91] |
Adesina OT, Sadiku ER, Jamiru T, et al. (2019) Optimization of SPS processing parameters on the density and hardness properties of graphene reinforced polylactic acid nanocomposite. Int J Adv Manuf Technol 102: 4047–4058. https://doi.org/10.1007/s00170-019-03530-7 doi: 10.1007/s00170-019-03530-7
![]() |
[92] |
Razak SIA, Rahman WAWA, Sharif NFA, et al. (2012) Simultaneous numerical optimization of the mechanical and electrical properties of polyaniline coated kenaf fiber using response surface methodology: Nanostructured polyaniline on natural fiber. Compos Interfaces 19: 411–424. https://doi.org/10.1080/15685543.2012.757957 doi: 10.1080/15685543.2012.757957
![]() |
[93] |
Johnson AF, Pickett AK, Rozycki P (2001) Computational methods for predicting impact damage in composite structures. Compos Sci Tech 61: 2183–2192. https://doi.org/10.1016/S0266-3538(01)00111-7 doi: 10.1016/S0266-3538(01)00111-7
![]() |
1. | Mohammed Fuseini, Moustafa Mahmoud Yousry Zaghloul, Djibrine Abakar, Mai Mahmoud Yousry Zaghloul, Review of epoxy nano-filled hybrid nanocomposite coatings for tribological applications, 2025, 49, 24522627, 100768, 10.1016/j.flatc.2024.100768 | |
2. | Syed Mansoor Ahmad, M C Gowrishankar, Manjunath Shettar, A review on properties of bamboo fiber polymer composites and bamboo/glass fiber/nanoclay hybrid composites, 2025, 12, 2053-1591, 012002, 10.1088/2053-1591/ada875 |
Thermoset matrices | Thermoplastic matrices | Influence on final properties | |||
Advantages | Limitations | Advantages | Limitations | ||
1. RTM | High-quality finish, excellent fiber wet-out, suitable for complex shapes, reduced void content | Longer curing times, careful control needed, higher tooling costs | Rapid cycle times, recyclability | Higher temperatures and pressures, challenging impregnation due to viscosity | High fiber volume, superior mechanical properties, reduced voids |
2. VARTM | Lower tooling costs, good for large parts, efficient for low-medium volumes | Longer infusion times, potential for dry spots, limited to low viscosity resins | Lower temperatures, possible use of lower viscosity resins | Difficult fiber wet-out, less effective for thermoplastics | Good mechanical properties, suitable for large parts, cost-effective |
3. Injection molding | High production rates, excellent finish, suitable for complex shapes | Limited to small-medium parts, high tooling costs, short mold life | Fast cycle times, re-processability, high-volume production | High initial costs, fiber length reduction | Efficient production, good finish, fiber orientation affect properties |
4. Compression molding | High fiber content, good dimensional stability, suitable for large shapes | Longer cycles, higher tooling costs, lower volumes | Shorter cycles, suitable for medium-large parts, re-processability | Higher temperatures and pressures, complex molds | High fiber content, good mechanical properties, mold design crucial |
5. Pultrusion | Continuous process, high fiber volume fraction, excellent mechanical properties, consistent cross-sectional shapes | Limited to linear profiles, higher setup costs, less flexibility in design changes | Rapid processing, recyclability, continuous production | High processing temperatures, limited to specific profile shapes | High strength and stiffness, suitable for structural applications like beams and rods |
6. SMC | High production rates, good surface finish, suitable for complex shapes | Limited to medium-sized parts, higher initial costs for equipment, less suited for high-performance applications | Fast cycle times, recyclability, high-volume production capability | High initial costs, reduced fiber length during processing | Balance of mechanical properties and production efficiency, often used in automotive applications |
7. Hand lay-up | Simple and low-cost method, suitable for large parts, flexibility in design | Labor-intensive, inconsistent quality, longer curing times, potential for higher void content | Flexibility in lay-up, recyclability of materials | More difficult to process, requires higher temperatures | Variable mechanical properties, heavily dependent on the skill of the operator, often used for prototypes and small production runs |
Thermoset matrices | Thermoplastic matrices | Influence on final properties | |||
Advantages | Limitations | Advantages | Limitations | ||
1. RTM | High-quality finish, excellent fiber wet-out, suitable for complex shapes, reduced void content | Longer curing times, careful control needed, higher tooling costs | Rapid cycle times, recyclability | Higher temperatures and pressures, challenging impregnation due to viscosity | High fiber volume, superior mechanical properties, reduced voids |
2. VARTM | Lower tooling costs, good for large parts, efficient for low-medium volumes | Longer infusion times, potential for dry spots, limited to low viscosity resins | Lower temperatures, possible use of lower viscosity resins | Difficult fiber wet-out, less effective for thermoplastics | Good mechanical properties, suitable for large parts, cost-effective |
3. Injection molding | High production rates, excellent finish, suitable for complex shapes | Limited to small-medium parts, high tooling costs, short mold life | Fast cycle times, re-processability, high-volume production | High initial costs, fiber length reduction | Efficient production, good finish, fiber orientation affect properties |
4. Compression molding | High fiber content, good dimensional stability, suitable for large shapes | Longer cycles, higher tooling costs, lower volumes | Shorter cycles, suitable for medium-large parts, re-processability | Higher temperatures and pressures, complex molds | High fiber content, good mechanical properties, mold design crucial |
5. Pultrusion | Continuous process, high fiber volume fraction, excellent mechanical properties, consistent cross-sectional shapes | Limited to linear profiles, higher setup costs, less flexibility in design changes | Rapid processing, recyclability, continuous production | High processing temperatures, limited to specific profile shapes | High strength and stiffness, suitable for structural applications like beams and rods |
6. SMC | High production rates, good surface finish, suitable for complex shapes | Limited to medium-sized parts, higher initial costs for equipment, less suited for high-performance applications | Fast cycle times, recyclability, high-volume production capability | High initial costs, reduced fiber length during processing | Balance of mechanical properties and production efficiency, often used in automotive applications |
7. Hand lay-up | Simple and low-cost method, suitable for large parts, flexibility in design | Labor-intensive, inconsistent quality, longer curing times, potential for higher void content | Flexibility in lay-up, recyclability of materials | More difficult to process, requires higher temperatures | Variable mechanical properties, heavily dependent on the skill of the operator, often used for prototypes and small production runs |