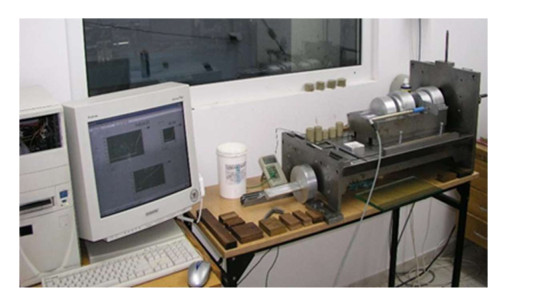
The article discusses the selected mechanical and plastic properties of modelling materials based on plasticine and filia wax utilized in the physical modelling. Application of the physical modelling with the utilize of soft model materials as well as plasticine and waxes with different inoculants, is a frequently used method applied as an alternative or verification of FE modelling of volumetric plastic working processes. First, in the ring test, the friction coefficients for the base model materials for various lubricants were determined. Then, in the compression test, the flow curves for model materials modified with various modifying substances (kaolin, lanolin, paraffin, chalk, etc.) were determined. The last step of the research studies was to verify the correctness of determining the flow curves using the inverse method. Based on the research carried out, a database was developed for soft model materials, covering the entire spectrum of flow curves and selected mechanical (friction coefficient, true and critical stress) and plastic properties (plastic deformation), which allows the selection of an appropriate mixture of model material to the real metallic material. Based on the obtained results, it can be concluded that both in the case of plasticine and filia wax, both of these materials together with modifiers very well simulate the behavior of warm and hot deformed metallic materials (with softening), much worse for materials with a clear hardening, characterizing cold work. In the case of filia wax, more stable properties were observed compared to plasticine-based materials.
Citation: Marek Hawryluk, Jan Marzec, Tatiana Karczewska, Łukasz Dudkiewicz. Determination of the characteristics and mechanical properties for soft materials based on plasticine and filia wax with inoculants[J]. AIMS Materials Science, 2022, 9(2): 325-343. doi: 10.3934/matersci.2022020
[1] | Nikolay A. Voronin . Analysis of the mechanisms of deformation of topocomposites by modeling of the indentation load-displacement curves. AIMS Materials Science, 2019, 6(3): 397-405. doi: 10.3934/matersci.2019.3.397 |
[2] | Nuriya М. Mukhamedova, Mazhyn K. Skakov, Wojciech Wieleba . Determination of phase composition and mechanical properties of surface of the material obtained on the basis of silicon and carbon by spark-plasma sintering method. AIMS Materials Science, 2019, 6(1): 1-9. doi: 10.3934/matersci.2019.1.1 |
[3] | SYED HABIBUNNISA, Ruben Nerella, Srirama Chand Madduru, RajaGopal Reddy S . Physicochemical characterization of lignocellulose fibers obtained from seedpods of Wrightia tinctoria plant. AIMS Materials Science, 2022, 9(1): 135-149. doi: 10.3934/matersci.2022009 |
[4] | Jui-Hung Chang, Weihan Wu . Evaluation of effective hyperelastic material coefficients for multi-defected solids under large deformation. AIMS Materials Science, 2016, 3(4): 1773-1795. doi: 10.3934/matersci.2016.4.1773 |
[5] | Fabian Pöhl, Corinna Hardes, Werner Theisen . Scratch behavior of soft metallic materials. AIMS Materials Science, 2016, 3(2): 390-403. doi: 10.3934/matersci.2016.2.390 |
[6] | G. A. El-Awadi . Review of effective techniques for surface engineering material modification for a variety of applications. AIMS Materials Science, 2023, 10(4): 652-692. doi: 10.3934/matersci.2023037 |
[7] | Didar Yeskermessov, Bauyrzhan Rakhadilov, Laila Zhurerova, Akbota Apsezhanova, Zarina Aringozhina, Matthew Booth, Yerkezhan Tabiyeva . Surface modification of coatings based on Ni-Cr-Al by pulsed plasma treatment. AIMS Materials Science, 2023, 10(5): 755-766. doi: 10.3934/matersci.2023042 |
[8] | Yerbolat Koyanbayev . Applying the Hollomon-Jaffe parameter to predict changes in mechanical properties of irradiated austenitic chromium-nickel steels during isothermal exposure. AIMS Materials Science, 2024, 11(2): 216-230. doi: 10.3934/matersci.2024012 |
[9] | Mohammed Nizam Khan, Sumesh Narayan, Ananthanarayanan Rajeshkannan . Influence of process parameters on the workability characteristics of sintered Al and Al–Cu composites during cold deformation. AIMS Materials Science, 2019, 6(3): 441-453. doi: 10.3934/matersci.2019.3.441 |
[10] | Zhonggang Feng, Tadashi Kosawada, Takao Nakamura, Daisuke Sato, Tatsuo Kitajima, Mitsuo Umezu . Theoretical methods and models for mechanical properties of soft biomaterials. AIMS Materials Science, 2017, 4(3): 680-705. doi: 10.3934/matersci.2017.3.680 |
The article discusses the selected mechanical and plastic properties of modelling materials based on plasticine and filia wax utilized in the physical modelling. Application of the physical modelling with the utilize of soft model materials as well as plasticine and waxes with different inoculants, is a frequently used method applied as an alternative or verification of FE modelling of volumetric plastic working processes. First, in the ring test, the friction coefficients for the base model materials for various lubricants were determined. Then, in the compression test, the flow curves for model materials modified with various modifying substances (kaolin, lanolin, paraffin, chalk, etc.) were determined. The last step of the research studies was to verify the correctness of determining the flow curves using the inverse method. Based on the research carried out, a database was developed for soft model materials, covering the entire spectrum of flow curves and selected mechanical (friction coefficient, true and critical stress) and plastic properties (plastic deformation), which allows the selection of an appropriate mixture of model material to the real metallic material. Based on the obtained results, it can be concluded that both in the case of plasticine and filia wax, both of these materials together with modifiers very well simulate the behavior of warm and hot deformed metallic materials (with softening), much worse for materials with a clear hardening, characterizing cold work. In the case of filia wax, more stable properties were observed compared to plasticine-based materials.
The interest in soft model materials used in plastic processing results from the more and more wide use of physical modelling in the simulation and analysis of plastic forming of metallic materials. Physical modelling with the use of soft metallic materials enables a quick, precise and inexpensive analysis of the real metal forming processes by means of cheaper shaping tools made of wood, plastic and other transparent materials, and it also makes it possible to use machines with lower pressures than in the case of real processes. Physical modelling can be applied as supplementation or verification of the relatively expensive numerical modelling, as it does not allow for the so called "big mistakes" during simulation, which, in the case of an engineer performing numerical modelling who does not have sufficient experience and knowledge, is unfortunately quite a common phenomenon [1,2].
Physical modelling methods reduce design time and diminish the cost of the experiment itself, thanks to the use of model materials, which, thanks to various inoculant additions, provide the possibility to determine the characteristics of most metals and their alloys [3]. The literature offers a different classification of model materials used in modelling plastic working processes. Generally, these materials can be classified into two large groups: metallic and non-metallic. The metallic materials include: aluminum, lead, sodium, copper and 'transparent metal compounds" (AgCl, AgBr, TlCl, CsCl, CsBr, etc.). However, for non-metallic materials: plastics, rubber, petroleum jelly, various types of pure waxes and plasticine and their mixtures with various additives. Wax materials are very popular among non-metallic model materials. The research conducted so far in many research centers on non-metallic model materials separated the two groups. The first group consists of model materials based on natural or synthetic waxes with various additives [4,5,6,7]. There are two subgroups. Based on soft waxes (synthetic filia wax, mixtures of filia with microwax, resin and kaolin and microwax mixtures with resin and kaolin). These materials are deformable at room temperatures and constitute the first subgroup [8]. The second subgroup consists of hard wax-based materials (mixtures based on paraffin and ceresin with beeswax and carnauba additives, as well as pure paraffin wax).
At room temperatures, these materials are very brittle and may be deformed at elevated temperatures (35-43 ℃) [4,9]. On the other hand, the second group of non-metallic model materials are materials based on various types of pure plasticine or their mixtures containing both softening and hardening additives [10,11,12,13]. The non-metallic soft model materials used in physical modelling include various types of mixtures of clays and waxes. The most commonly used waxes are paraffin waxes and microcrystalline waxes; both groups of waxes may be of natural origin or obtained by chemical synthesis. They are obtained by distillation of crude oil and consist of branched, linear or sometimes cyclic hydrocarbon chains. Paraffin waxes are usually brittle and their plasticity increases with increasing melting point. Microcrystalline waxes contain smaller crystals and more cyclic hydrocarbons than paraffin waxes. The content of oily substances for microcrystalline waxes ranges from 2 to 12%, while for paraffin waxes it does not exceed 0.5%. Both types of wax can be distinguished after dissolving and separating oily and dry substances from the solution [14].
Plasticines and waxes, commonly used for modelling, characterize above all in low Young's modulus (about 1-3 MPa), relatively large elastic strains, high sensitivity to temperature changes and strain rates, and usually also weakening of deformations. Owing to this kind of properties, they are appropriate for the modelling of metal at elevated temperature processes, and in the case of cold metalforming, a physical modelling with soft model materials is much more difficult. Model materials based on plasticines demonstrate higher structural heterogeneity, which makes them appropriate mainly for a qualitative assessment of the processes under study, especially images of the flow of a deformed material. In turn, model materials based on waxes characterized by less degree of structural heterogeneities and so, their properties are more stable. For this reason, they are more commonly used in examinations of the force parameters of the analyzed processes. In the literature, we can find many applications of physical modelling for the analysis of industrial processes (bulk metal forming), where compression is the dominant state of stress. Due to their unique design, non-metallic soft model materials have been used in simulations of the processes of forging, pressing and upsetting or extrusion [15,16,17]. On the other hand, it is not often possible to come across research on the results of simulation of processes taking into account stress states other than compression. These few cases include: physical modelling of rolling of semi-finished pipes [18], longitudinal rolling of sections [19,20], bending of thick pipes, helical rolling of pipes [21] or specific manufacturing process, such as forming rotor blade or forging outer race [22]. The choice of model material also depends on the simulated process or phenomenon. For example, during crack simulation, paraffin can be used as a model material, which well reveals and shows micro- and macrocracks on the surface [14,16]. On the other hand, when simulation tests require large plastic strains, a much more plastic and adequate model material should be used. [23], for example plasticine. Synthetic filia wax simulates lead formed at ambient temperature, or typical steel, e.g. C45, behaves very well, which undergoes the process of hot deformation [1,24,25]. The transformation of the physical modelling results into an industrial process takes place based on the similarity conditions of the model material to the real metallic material and, in the case of plastic processing, on the plasticity theory [23]. The main similarity conditions include: similarity in the elastic and plastic scope, geometrical similarity, similarity of friction conditions, thermal similarity, and others. Of course, it is impossible to fulfill all the similarity conditions at the same time, but rather those which are crucial in terms of the modelling objective are selected. In the case of plastic forming, the most important condition is the plastic similarity condition, which consists in maintaining a similar course of the model material's flow curve to that of the real material, with the assumption that the level of yield stress for the model material is a few to a few hundred times lower than the yield stress for the model material. It should be emphasized that, by changing the composition of these materials based on waxes (by adding lanolin, kaolin, chalk, paraffin, and different) and changing the temperature and strain rate, we can archive models of true stress-plastic strain flow curves for various real metallic materials [3,26]. Other important conditions are the friction condition similarity and the geometrical similarity. For the description of the plastic similarity condition, e.g., the Alder and Philip's model is used [27], in which the condition is maintained when the reinforcement and strain rate sensitivity for the modelling material and the real material are the same. In the literature, we can also find another approach to the plastic similarity condition, in which a qualitative and quantitative assessment of the flow curve shape similarity is assumed. The stress-strain courses are usually determined for the model materials, due to their specificity in the compression test. In turn, the friction conditions are usually described during the ring test or the cigar test, or possibly in the so-called "cup test" as well as direct-indirect extrusion into the letter H [28]. Due to the specificity of soft model materials based on filia wax and plasticine, in order to determine the friction conditions, the ring upsetting method is usually used, which is the most common method of designating friction coefficient and selecting the type of lubrication for forging processes [28,29]. Based on numerous tests, it was established that, for the sample dimension proportions Do:do:ho = 6:3:2 (initial ring outer diameter, ring inner diameter and height), the obtained results best match those achieved in reality. During compression of such a sample, between the parallel non-deformable boards, its dimensions change, which is directly connected with the existing friction conditions. This method is very much suitable for a comparative test of friction under various conditions, e.g. with different lubricants, tool surface roughnesses, etc. If the knowledge of the friction coefficient values is not necessary, it is enough to compare the internal diameters of the rings after upsetting under different conditions, whereby the initial dimensions of the examined rings and the deformation degree have to be identical. A comparison of the ring test results for the real material and the model material makes it possible to determine whether in both cases identical friction conditions were maintained. The test results constitute the guidelines for the selection of the lubricating agent [30,31,32]. μ
We should clearly note that the selection of the model material is crucial for the appropriate design and simulation of the chosen industrial process. Usually, it is made on the basis of experience and knowledge of the scientist-modeller, although there are also attempts of another approach to this issue, e.g. through the use of decision trees [33], or other IT tools. We can also find proposals of a different description of the plastic similarity, based on a qualitative and quantitative analysis of the matching of the model material flow curve to that of the real metallic material [34]. Nonetheless, in any case, it is very important to determine the characteristics of the model material (mainly the flow curves: stress-strain) as well as other parameters and properties in technological trials, which enables the selection and matching of the model material to the actual metallic materials in such a way so that the model materials are used in the best possible way in the simulation of industrial processes of metal forming. In the case of determining the flow curves for soft model materials, due to their specificity, a compression test in a uniaxial deformation state is usually performed. In the case of hard model materials (based on ceresin), sometimes, the flow curves can be determined in a tensile test. This said, in order to obtain high deformation values and uniaxial compression, we should ensure a minimized effect of friction through providing the appropriate lubrication conditions to eliminate barreling.
For this reason, further investigations in the area of determining the flow curves and tribological conditions for model materials is justified, as it makes it possible to describe the most important mechanical and plastic parameters, based on which we can perform analyses of their behaviour and application for stimulations of metallic materials and industrial processes.
The main aim of the study is determination of the coefficient of friction as well as the flow curves for soft model materials based on pure plasticine and filia wax modified with various inoculants (kaolin, lanolin, petrolatum). The tests were carried out on the developed and constructed horizontal press, the driving device of which is a Lenze geared motor with a torque of 20 Nm and a power of 1.1 kW. The measuring system has an application developed in the Labview environment, which allows you to steering, control and archive data, as well as is equipped with a computer and inverter with a 16-bit measurement card and Hottinger amplifiers. The measurement of forces is carried out by a ZEWPN measuring sensor with a range of 0-7 kN, while the measurement of displacement is carried out by an inductive sensor with a range of 0-200 mm (Figure 1).
The obtained results will enable a complex analysis of the behaviors of soft model materials as well as the possibilities of transformation into industrial processes, which will make it possible to more precisely illustrate and optimize the metal forming processes.
To determine the tribology (friction) conditions as well as flow curves for various mixtures of model materials, the base component, that is synthetic filia wax and plasticine, is necessary in order to prepare special samples in a proper way. The synthetic filia wax applied in the tests was produced at the "Filia" Enterprise in Ølsted, Denmark, whereas the white plasticine—at "Astra-Zenith" S.A. in Częstochowa, Poland. The samples were prepared by way of weighing the appropriate proportions of individual components, and then such mixtures were melted in a furnace at a temperature of about 180 ℃ and poured into steel pipes constituting the moulds. During solidification, the moulds were mounted on a vibrating table to de-aerate and obtain a homogeneous composition. After the samples solidified and reached the ambient temperature, they were placed in a freezer (−20 ℃), which, after 4 h, facilitated the removal of the cylindrical sample from the mold. After reaching the ambient temperature again, the samples were cut into proper dimensions and then the appropriate samples were prepared for the ring test (ring-shaped samples to determine the friction coefficient) and upsetting tests (cylindrical samples to determine the flow curves).
One of the basic similarity conditions between the model material and the real material is the friction similarity condition. And so, it was necessary to select the appropriate lubrication conditions which would ensure similar coefficients of friction in the model and the real process, and this would enable a proper representation of the tribological conditions. For the model material, the Coulomb's friction model was assumed, and for the determination of the friction value, the ring test was selected, which is the simplest and most common test ensuring good agreement and repeatability of results. Also, it was assumed that the coefficient of friction depended only on the lubricating agent. The determination of the numerical value of the coefficients consists in comparing the real dimensions of the rings after upsetting (internal diameter and height) with the theoretical solution, which describes the effect of friction on the shape of the upset ring. With low friction, the ring expands and the internal diameter of the sample becomes bigger. (Figure 2a). In the case of high friction forces, at a certain diameter, the material adheres to the tool, and so, a part of the material shifts to the inside, and a part of it to the outside. And so, the internal diameter can decrease or, in a borderline case, it may not change. The bigger the internal diameter of the ring after upsetting, the lower the friction forces (Figure 2b). After the calculation of the appropriate relations referring to the changes in the internal diameter and the height for the designation of the particular coefficient of friction, appropriate nomograms or diameters are applied (Figure 2c), from which for the known dimensions h0, d0 as well as h1 and d1, we can read out the value of the coefficient of friction.
Each ring compression test was repeated 5 times to ensure the repeatability of the results, as the soft model materials based on plasticine and filia wax used are sensitive to changes in temperature and strain rate. If the lubricant was used during the ring test, it was applied with a brush, which was used to cover the working surfaces of the tools with a thin layer of lubricant.
The tools used in the ring test (friction coefficient) as well as for the compression test (flow curves) were made of aluminum with a hardness of 25 HB and a surface roughness of Ra = 0.32. They were not transparent.
In order to facilitate the selection of the model materials in reference to the real materials, a database was created containing the yield stress-strain curves as well as the chemical compositions of different mixtures of model materials, whose base material was filia and plasticine. It turns out that modifying their compositions by adding various amounts of the following substances: paraffin, kaolin and chalk, as well as changing the temperature makes it possible to obtain σ-ε curve models for different real materials.
The reinforcement curves of the model materials were designed in compression test of axisymmetrical cylindrical samples with diameter of 60 mm and height of 60 mm. The test was realized until a crack appeared on the side surface of the cylinders, 14 d after the model samples were prepared. The primary tests were conducted at an ambient temperature (22 ℃) and the strain rate of 0.01 s−1. The investigations were carried out also for other deformation conditions in order to determine the sensitivity of the model materials to the temperature and strain rate. Additionally, with the purpose to reduce the coefficient of friction, before the test, special openings were made (shaped as regular pyramids with the height of 2 mm and the base of a square with the side length of 2 mm) on the front surfaces of the samples, with the tool shown in Figure 3a. It was assumed that, during the test, the formation of a barrel on the side surface of the cylinder is unacceptable in order to obtain a very low coefficient of friction and so, its effect on the yield stress was omitted (Figure 3b).
Each test was repeated 5 times to ensure the repeatability of the results, as the model materials are sensitive to changes in the temperature and strain rate.
A major limitation in determining the flow and friction curves is the need to have an accurate description of the properties of the shaped material and the phenomena accompanying deformation. It turns out that the problem of evaluating rheological parameters as well as mechanical and thermal boundary conditions can be defined as an inverse problem [35,36]. The algorithm to solve it was called the inverse method. In the inverse method, the yield stress model and the friction coefficient are identified by looking for the minimum of the goal function, which is defined as the mean square error between the determined and calculated loads and the shape of the samples. The form of the adopted objective function, called the error functional, which depends on the type of assessed parameters and conducted experiment. In the analysis used, the following form of the error functional was adopted, the specific formula is as follows (Eq 1):
Φ=√1NptNpt∑i=1[1NpsNps∑j=1(Fcji(x,pi)−FmjiFmji)2+(βci(x,pi)−βmiβmi)2] | (1) |
Where: Fmji, Fcji are force values: measured and calculated, ®mi, ®ci, barrel shape of the sample measured and calculated after upset, Npt, number of tests, Nps, number of forces recorded during each upsetting test, p, vector of the process input values (strain rate), x, vectors of coefficients in the model (friction factor, rheological parameters).
The barrel nature of the sample is described by the relationship (Eq 2):
β=1−VV0 | (2) |
Where: V0, initial sample volume, V = 0.25 π Dk2 Hk, cylinder volume, the base of which is the contact surface of the sample with the tool surface with a height determined at the end of the upsetting test, Df, diameter of the sample after upsetting on the tool contact surface, Df = 0.5 (Du + Dl).
The above error function was minimized due to the rheological parameters and the friction factor with the use of appropriate optimization methods [37]. In the discussed solution, in the description of the boundary conditions, due to the possibility of sticking the material to the punch, the friction model developed by Chen and Kobayashi [38] as used, described by the relationship:
τ=mσp√3[2πtan−1(|vs|a)] | (3) |
Where: m is friction factor, depending on the properties of the tool, material and grease, roughness of the contacting surfaces and temperature, vs is material sliding velocity in relation to the tool, a is constant, several orders lower than the sliding velocity (if the value of sliding velocity vs is equal to a, then Eq 3 takes the classic form of the Tresca friction model: τ = mτmax, τmax is shear yield point).
It was assumed that if the flow curves determined from the measurements in an analytical manner for the above-mentioned materials coincide with the curves obtained by the reverse method for the respective materials, the results obtained in the upsetting test are correct.
In the ring test, samples of the following dimensions were used: height 24 mm, internal diameter 40 mm and external diameter 80 mm. The tests were performed for samples without a lubricant as well as for the following lubricants: oil, teflon + graphite, magnesium stearate with denaturated alcohol, industrial grade petroleum jelly. Based on the changes in the internal diameter and reduction of the ring's height after deformation, the friction coefficient values were determined from the diagram shown in Figure 2c). For each model material (plasticine and filia) and test condition variant, 5 trials were conducted. The obtained results have been presented in Table 1 (plasticine) and Table 2 (filia wax).
Type of lubricant | Dp | Dk | Δ D/Dp (%) | Hp | Hk | Δ H/Hp (%) | μ | R (Error) (%) |
No lubricant | 40, 2 | 36.4 | 9.4 | 24 | 16 | 30 | 0.15 | 0.22 |
Teflon + graphite | 40.1 | 44.2 | 10 | 24 | 16 | 30 | 0.08 | 0.12 |
Machine oil | 40.2 | 40.8 | −1.5 | 24 | 16 | 30 | 0.07 | 0.09 |
Industrial grade petrolatum | 40.15 | 41.7 | −3.9 | 24 | 16 | 30 | 0.057 | 0.07 |
Magnesium stearate | 40.15 | 19.65 | 2.2 | 24 | 16 | 30 | 0.1 | 0.13 |
Type of lubricant | Dp | Dk | ΔD/Dp (%) | Hp | Hk | ΔH/Hp (%) | μ | R (Error) (%) |
No lubricant | 40.20 | 36.40 | 9.4 | 24 | 16 | 30 | 0.14 | 0.13 |
Teflon + graphite | 40.10 | 44.20 | 10 | 24 | 16 | 30 | 0.07 | 0.09 |
Machine oil | 40.20 | 40.80 | −1.5 | 24 | 16 | 30 | 0.06 | 0.07 |
Industrial grade petrolatum | 40.15 | 41.70 | −3.9 | 24 | 16 | 30 | 0.052 | 0.06 |
Magnesium stearate | 40.15 | 19.65 | 2.2 | 24 | 16 | 30 | 0.1 | 0.08 |
Where: Dp, Dk initial and finish inner ring diameter, Hp Hk initial and finish high of ring, µ average friction coefficient read from the chart in Figure 2c, R = 1 ∕ 2 (µmax−µmin) 100%
In the ring test for plasticine, for dry friction, the coefficient of friction equalled 0.15. The lowest coefficient of friction was obtained for industrial grade petroleum jelly 0.057 and machine oil 0.07, and slightly higher for teflon with graphite µ = 0.08.
For filia wax, in the case of dry friction, the coefficient of friction equalled 0.14. The lowest coefficient of friction was obtained for industrial grade petroleum jelly 0.052 and machine oil 0.06, and slightly higher for teflon with graphite µ = 0.08.
In the ring test for filia wax, similar friction coefficient values were obtained to those for plasticine, whereby we should note a bit bigger error for 5 samples, which can confirm a slightly less stable behaviour of filia wax than that of plasticine. In light of the obtained results, it was established that, because of the smallest error and the lowest friction coefficient values, the upsetting tests would be performed with the use of industrial grade petroleum jelly.
The yield stress of pure plasticine for the strain rate of 0.01 s−1, after reaching the maximum value for the deformation of 0.3, becomes lower. A kaolin addition in various amounts slightly increases the stress level but does not change the shape of the curves (Figure 4a). On the other hand, the addition of lanolin and paraffin do reduction of the yield stress in the whole deformation scope (Figure 4b). A lanolin addition lowers the yield stress more intensively than a paraffin addition. With plasticine as the basic component, it was not possible to obtain a mixture which would reinforce in the whole plastic strain scope, and so, it can be applied mainly to model hot metal forming processes.
The tests determining the effect of the strain rate and temperature on the shape of the yield stress-strain curves showed that plasticine reacts similarly to a change of these parameters as filia and its mixtures (Figure 5a, b).
Increasing the strain rate causes an increase in the level of yield stress, while maintaining the nature of the flow curves (Figure 5a). On the other hand, increasing the temperature by 2 degrees Celsius causes the opposite effect, i.e., lowering the level of plasticizing stress, also while maintaining a similar character of the shape of the flow curves (Figure 5b)
The curves of true stress-starin for filia with the strain rate of 0.01s−1, after reaching the maximal value with the plastic strain of about 0.35, becomes slightly lower. The addition of kaolin to the filia wax increases its strength, which increases with the kaolin increase. For mixtures containing over 8-10% kaolin, we obtain an increase of true stress in the whole deformation range. These flow curves can be applied for the modelling of the metal forming process of real materials under the conditions of cold work (Figure 6a).
An increase in the content of kaolin causes a reduction of the limit deformation; filia containing over 24% kaolin is so brittle that it is unsuitable for modelling. For this reason, in order to increase the limit deformations, a small amount of lanolin was added to mixtures containing large amounts of kaolin. A lanolin addition in the amount of up to 4% does not change the shape of the reinforcement curve, while causing an increase of the limit deformations by about 25%. The reinforcement curves of such materials have been shown in Figure 6b. If only lanolin is added to the pure filia, we obtain curves for which the yield stress after reaching the maximal value becomes significantly lower. This reduction increases with the increase of the lanolin content in the mixture (Figure 7).
An increase of the lanolin amount also causes lowering of the critical deformations (Figure 7a). Such mixtures can be used to model of the hot metal processes. Similar influence on the stress-strain curves shape for filia can be observed in the case of paraffin, except that it also it significantly increases the level of stress (Figure 7b). The effect of the strain rate on the character of the true stress-strain curves of the tested compositions was also designated. From the courses presented in Figure 8a, b it can be inferred that a changes in the value of strain rates from 0.01 to 0.1 s−1 do not change in the character of the reinforcement curves of the tested mixtures but only quite a big increase of yield stress.
The model materials also characterize in a very high sensitivity to the deformation temperature. Lowering the temperature by 4−5 ℃ causes an increase of filia's yield stress by about 15%, whereby the temperature change is accompanied by a clear change in the shape of the reinforcement curves (Figure 9).
Table 3 compiles the following properties of the examined model materials: σmax is maximal value of yield stress, εcr is critical deformation (no values means that, for the composition of model material, the critical strain was not reached), εlim is limit strains (determined during cracks appeared on the cylinder's side surface).
Base material | Inoculant | Test conditions | Properties | |||
T (℃) | έ (s−1) | σmax (MPa) | εcr | εlim | ||
filia | kaolin 2/4% | 22 | 0.01 | 0.128/0.136 | 0.38/0.39 | 1/1.05 |
filia | kaolin 8/24% | 22 | 0.01 | 0.209/0.507 | - | 0.8/0.9 |
filia | kaolin 10/28% + lanolin 2/5% | 22 | 0.01 | 0.182/0.505 | 0.91 | 0.95/1.05 |
filia | lanolin 6/14% | 22 | 0.01-0.1 | 0.083/0.095 | 0.03/0.29 | 1.2 |
filia | - | 22 | 0.01-0.1 | 0.13/0.17 | 0.3/0.41 | 0.9/1 |
filia | kaolin 16% | 22 | 0.01-0.1 | 0.385/0.47 | - | 0.8/0.95 |
filia | paraffin 5/10% | 22 | 0.01-0.1 | 0.176/0.356 | 0.03/0.09 | 0.9/1.05 |
filia | - | 17-22 | 0.01 | 0.13/0.18 | 0.3/0.36 | 0.9/1.1 |
filia | kaolin 20% | 18-24 | 0.01 | 0.41/0.46 | - | 0.8/0.9 |
plasticine | - | 22 | 0.01-0.1 | 0.37/0.416 | 0.17/0.2 | 0.9/1.05 |
plasticine | kaolin 2/20% | 22 | 0.01 | 0.386/0.51 | 0.19/0.32 | 0.8/0.95 |
plasticine | paraffin 5/10% | 22 | 0.01 | 0.323/0.38 | 0.21/0.29 | 0.85/1 |
plasticine | lanolin 5/10% | 22 | 0.01 | 0.12/0.17 | 0.11/0.14 | 0.9/1.05 |
plasticine | kaolin 15%, chalk 5%, paraffin 1% | 20-24 | 0.01 | 0.417/0.614 | 0.14/0.27 | 0.8/0.9 |
plasticine | kaolin 5%, chalk 5% | 20-24 | 0.01 | 0.3/0.42 | 0.19/0.22 | 0.8/0.9 |
The realized tests performed on model materials demonstrated that modifying their composition (by adding paraffin, kaolin, lanolin, chalk) and changing the temperature and strain rate and makes it possible to obtain models of the true stress-strain curves for different real materials. Addition of lanolin or chalk causes an increase of the stress level. Such curves can be used for real materials under cold metal forming conditions. However, it is difficult to find materials for which an intensive increase of yield stress can be observed in the whole deformation scope. In the case of an addition of lanolin or paraffin, we obtain curves in which the yield stress, after reaching the maximal value, becomes lower. Such mixtures can be used to model hot plastic forming processes. A change in the strain rate from 0.01 to 0.1 s−1 as well as temperature within the scope of 17-25 ℃ it does not cause a significant change in the nature of the flow curves for the tested mixtures, but only a change in the level of the yield point. A similar phenomenon is observed in the case of lowering the temperature. Plasticine and its mixtures exhibit a similar reaction to additions, as well as a change in the strain rate and temperature, as filia mixtures. This said, the shape of filia's reinforcement curves can be modified to a larger extent by way of adding different components than the shape of the reinforcement curves for plasticine. On this basis we can state that, based on the obtained properties and behaviour of the model materials depending on the applied inoculants (amount and substance) as well as the temperature changes, it was possible to develop an extensive database, which can be the basis for selecting a model material for any actual metallic material.
Additionally, in order to verify the obtained results, the reinforcement curves were determined for the selected model material based on the inverse method. Pure filia wax was chosen as the representative model material. In the experiment, an upsetting test of cylindrical samples made of filia wax with the dimensions of 60 × 60 mm was conducted with the use of industrial grade petroleum jelly as the lubricant and with a constant temperature of 22 ℃. During the process, the force in the function of tool displacement was measured. The obtained courses were the input data for the inverse model.
Table 4 presents the measurements of the samples' barelling and the coefficients of friction determined by means of the inverse method for filia wax. In turn, Figure 10 shows the reinforcement curves for the model material determined in an analytical manner as well as the reinforcement curves obtained in the inverse method.
Test | Bareling | Coefficient of friction (m) |
filia, έ = 0.01 s−1 | 0.0123 | 0.021 |
filia, έ = 0.05 s−1 | 0.0151 | 0.027 |
filia, έ = 0.1 s−1 | 0.0169 | 0.031 |
The presented investigation results referring to the flow curves of the model material obtained by means of the inverse method show quite a good agreement with the reinforcement curve results determined analytically. The effect of friction is visible only with the deformation over 0.4, whereby, the higher the strain rate, the bigger the influence of friction on the yield stress. The low value of barelling for this material, with relatively large dimensions, points to a small effect of friction on the yield stress. The inverse method based on an analysis of the geometry changes in the sample during upsetting makes it possible to verify the correctness of the determined flow curves, which, in consequence, translates to precision in the matching of the model material to the selected real material.
The work discusses physical modelling, its idea and similarity conditions needed to transform the results into a real process, and the use of the physical model for comprehensive analysis, verification and optimization of bulk metal forming processes. The main problems of using physical modelling methods are the difficulties related to the transfer of modelling results into real processes, which results from the difficulty of maintaining all the conditions of similarity simultaneously. This said, as it has been demonstrated in the study, the key similarity conditions of the model material to the real metallic material is the plastic similarity. This condition usually comes down to the selection of such a chemical composition and such deformation conditions so that the shape of the reinforcement curve for the model material is similar to that of the metallic material, which means that the state of plastic similarity has been met, which guarantees an appropriate quality of the results of physical modelling in the given industrial process. Within the studies, in the first place, the coefficients of friction for different lubrication conditions were determined for plasticine and filia wax. The obtained results have shown that the lowest friction coefficient value was obtained in both cases (plasticine and filia wax) for the industrial petroleum jelly lubricant. This said, for plasticine, a slightly bigger scatter of results was recorded than in the case of filia wax, which may point to less stable properties of this base material. Next, for the selected lubrication agent, compression tests were carried out for both model base materials, with a simultaneous addition of other modifying substances. The obtained results in the form of a database make it possible to estimate the value of the selected key parameters of the model material, based on both plasticine and filia (σmax, maximal value of yield stress, εcr, critical deformation, εlim, limit deformation), on the basis of the established percentage composition of the main modifying elements: kaolin, paraffin, chalk and lanolin. Based on the obtained results, it can be concluded that both in the case of plasticine and filia wax together with modifiers very well simulate the behavior of warm and hot deformed metallic materials (with softening), much worse for materials with a clear hardening, characterizing cold work. As it has been demonstrated, such parameters and other values may be the basis for the selection of a model material for real metallic material.
The authors declare no conflict of interest.
[1] |
Hawryluk M, Polak S, Gronostajski Z, et al. (2019) Application of physical similarity utilizing soft modeling materials and numerical simulations to analyses the plastic flow of uc1 steel and the evolution of forces in a specific multi-operational industrial precision forging process with a constant-velocity joint housing. Exp Tech 43: 225-235. https://doi.org/10.1007/s40799-018-0288-4 doi: 10.1007/s40799-018-0288-4
![]() |
[2] |
Vazquez V, Altan T (2000) New concepts in die design—physical and computer modeling applications. J Mater Process Technol 98: 212-223. https://doi.org/10.1016/S0924-0136(99)00202-2 doi: 10.1016/S0924-0136(99)00202-2
![]() |
[3] |
Arentoft M, Gronostajski Z, Niechajowicz A, et al. (2000) Physical and mathematical modelling of extrusion processes. J Mater Process Technol 106: 2-7. https://doi.org/10.1016/S0924-0136(00)00629-4 doi: 10.1016/S0924-0136(00)00629-4
![]() |
[4] |
Lee RS, Blazynski TZ (1984) Mechanical properties of a composite wax model material simulating plastic flow of metals. J Mech Work Technol 9: 301-312. https://doi.org/10.1016/0378-3804(84)90111-6 doi: 10.1016/0378-3804(84)90111-6
![]() |
[5] | Oudin J, Ravalard Y, Rommens S (1980) On the contribution of waxes to the simulation of metal forming processes, North American Manufacturing Research Conference Proceedings, Rolla: University of Missouri-Rolla, 166-170. |
[6] |
Finér S, Kivivuori S, Kleemola H (1985) Stress—Strain relationships of wax-based model materials. J Mech Work Technol 12: 269-277. https://doi.org/10.1016/0378-3804(85)90142-1 doi: 10.1016/0378-3804(85)90142-1
![]() |
[7] |
Altan T, Henning HJ, Sabroff AM (1970) The use of model materials in predicting forming loads in metalworking. ASME J Eng Ind 92: 444-451. https://doi.org/10.1115/1.3427776 doi: 10.1115/1.3427776
![]() |
[8] | Finer S, Kivivuori S, Kleemola H (1982) Mekaniska och termiska egenskaper av modellmaterial. Del 1: Modellvaxet Filia: SIMON-rapport, Espoo: VTT Technical Research Centre of Finland. |
[9] |
Farzad A, Blazynski TZ (1989) Geometry factor and redundancy effects in extrusion of rod. J Mech Work Technol 19: 357-372. https://doi.org/10.1016/0378-3804(89)90082-X doi: 10.1016/0378-3804(89)90082-X
![]() |
[10] |
Eckerson K, Liechty B, Sorensen CD (2008) Thermomechanical similarity between Van Aken plasticine and metals in hot-forming processes. J Strain Anal Eng Des 43: 383-394. https://doi.org/10.1243/03093247JSA364 doi: 10.1243/03093247JSA364
![]() |
[11] |
Sharma M, Singh AK, Singh P, et al. (2011) Experimental investigation of the effect of die angle on extrusion process using plasticine. Exp Tech 35: 38-44. https://doi.org/10.1111/j.1747-1567.2010.00655.x doi: 10.1111/j.1747-1567.2010.00655.x
![]() |
[12] |
Azushima A, Kudo H (1987) Physical simulation for metal forming with strain rate sensitive model material. Adv Tech Plast 2: 1221-1227. https://doi.org/10.1007/978-3-662-11046-1_68 doi: 10.1007/978-3-662-11046-1_68
![]() |
[13] |
Schö pfer MPJ, Zulauf G (2002) Strain-dependent rheology and the memory of plasticine. Tectonophysics 354: 85-99. https://doi.org/10.1016/S0040-1951(02)00292-5 doi: 10.1016/S0040-1951(02)00292-5
![]() |
[14] | Arentoft M (1997) Prevention of Defects in Forging by Numerical and Physical Simulation, Copenhagen: Technical University of Denmark. |
[15] |
Gouveia BPPA, Rodrigues JMC, Martins PAF, et al. (2001) Physical modelling and numerical simulation of the round-to-square forward extrusion. J Mater Process Tech 112: 244-251. https://doi.org/10.1016/S0924-0136(01)00725-7 doi: 10.1016/S0924-0136(01)00725-7
![]() |
[16] | Gingher GC, Padjen G (1993) Hot strip mill edging practices and plasticine modelling, 34 th Mechanical Working and Steel Processing Conference Proceedings, Montreal: Iron and Steel Society of AIME, 3-12. |
[17] | Hawryluk M (2006) The influence of the condition of plastic similarity on the accuracy of physical modeling of extrusion processes[Dissertation]. Wroclaw University of Science and Technology (in Polish). Available from: http://www.itshc.pwr.edu.pl/language/en/dissertation. |
[18] |
Boucly P, Oudin J, Ravalard Y (1988) Simulation of ring rolling with new wax-based model materials on a flexible experimental machine. J Mech Work Technol 16: 119-143. https://doi.org/10.1016/0378-3804(88)90156-8 doi: 10.1016/0378-3804(88)90156-8
![]() |
[19] |
Adams MJ (1989) A two roll mill as a rheometer for pastes, material resume social symposium process. Mater Res Soc 289: 237-257. https://doi.org/10.1557/PROC-289-245 doi: 10.1557/PROC-289-245
![]() |
[20] |
Shin HW, Kim DW, Kim N (1994) A study of the rolling of I-section beams. Int J Mach Tools Manuf 34: 147-160. https://doi.org/10.1016/0890-6955(94)90097-3 doi: 10.1016/0890-6955(94)90097-3
![]() |
[21] |
Moon YH, Chun MS, Yi JJ, et al. (1993) Physical modelling of edge rolling in plate mill with plasticine. Steel Res 64: 557-563. https://doi.org/10.1002/srin.199301571 doi: 10.1002/srin.199301571
![]() |
[22] |
Mohammadi MM, Sadeghi MH (2010) Simulation and physical modeling of forging sequence of Bj type outer race. Adv Mater Res 83: 150-156. https://doi.org/10.4028/www.scientific.net/AMR.83-86.150 doi: 10.4028/www.scientific.net/AMR.83-86.150
![]() |
[23] |
Pertence AEM, Cetlin PR (2000) Similarity of ductility between model and real materials. J Mater Process Technol 103: 434-438. https://doi.org/10.1016/S0924-0136(00)00513-6 doi: 10.1016/S0924-0136(00)00513-6
![]() |
[24] |
Danckert J, Wanheim T (1976) Slipline wax: An easy way to determine the slipline field in specimens subjected to plastic deformation under plane-strain conditions. Exp Mech 16: 318-320. https://doi.org/10.1007/BF02324022 doi: 10.1007/BF02324022
![]() |
[25] | Gronostajski Z, Hawryluk M, Zwierzchowski M, et al. (2008) Analysis of forging process of constatnt velocity joint body. Steel Res Int 1: 547-554. |
[26] |
Wójcik Ł, Lis K, Pater Z (2016) Plastometric tests for plasticine as physical modelling material. Open Eng 6: 653-659. https://doi.org/10.1515/eng-2016-0093 doi: 10.1515/eng-2016-0093
![]() |
[27] | Alder J, Phillips KA (1954) The effect of strain-rate and temperature on the resistance of aluminum, copper and steel to compression. J Inst Met 83: 80-86. |
[28] |
Sofuoglu H, Rasty J (1999) On the measurement of friction coefficient utilizing the ring compression test. Tribol Int 32: 327-335. https://doi.org/10.1016/S0301-679X(99)00055-9 doi: 10.1016/S0301-679X(99)00055-9
![]() |
[29] |
Petersen SB, Martins PAF, Bay N (1998) An alternative ring-test geometry for the evaluation of friction under low normal pressure. J Mater Process Technol 79: 14-24. https://doi.org/10.1016/S0924-0136(97)00448-2 doi: 10.1016/S0924-0136(97)00448-2
![]() |
[30] |
Bay N, Lassen S, Pedersen CD, et al. (1991) Lubrication limits in backward can extrusion at low reductions. CIRP Ann Manuf Technol 40: 239-242. https://doi.org/10.1016/S0007-8506(07)61977-5 doi: 10.1016/S0007-8506(07)61977-5
![]() |
[31] |
Bennani B, Bay N (1996) Limits of lubrication in backward can extrusion: analysis by the finite-element method and physical modelling experiments. J Mater Process Technol 61: 275-286. https://doi.org/10.1016/0924-0136(95)02181-7 doi: 10.1016/0924-0136(95)02181-7
![]() |
[32] |
Shen G, Vedhanayagram A, Kropp E, et al. (1992) A method for evaluating friction using a backward extrusion-type forging. J Mech Work Technol 33: 109-123. https://doi.org/10.1016/0924-0136(92)90314-I doi: 10.1016/0924-0136(92)90314-I
![]() |
[33] | Hawryluk M, Wilk-Kołodziejczyk D, Regulski K, et al. (2019) Development of an approximation model of selected properties of model materials used for simulations of bulk metal plastic forming processes using induction of decision trees. Arch Metall Mater 64: 1073-1085. |
[34] |
Gronostajski Z, Hawryluk M (2007) Analysis of metal forming processes by using physical modeling and new plastic similarity condition. AIP Conference Proceedings 9: 608-613. https://doi.org/10.1063/1.2729580 doi: 10.1063/1.2729580
![]() |
[35] | Pietrzyk M, Lenard JG (1990) Finite element simulation during metal forming processes, International Heat Transfer Conference 9, Jerusalem: Begell House, 413-418. https: //doi.org/10.1615/IHTC9.1560 |
[36] | Szeliga D, Pietrzyk M (2002) Identification of rheological and tribological parameters, Metal Forming Science and Practice, Amsterdam: Elsevier, 227-258. https: //doi.org/10.1016/B978-008044024-8/50012-6 |
[37] |
Maropoulos PG (1995) Review of research in tooling technology, process modelling and process planning part Ⅱ: Process planning. Comput Integr Manuf Syst 8: 13-20. https://doi.org/10.1016/0951-5240(95)92809-9 doi: 10.1016/0951-5240(95)92809-9
![]() |
[38] | Chen CC, Kobayashi S (1979) Rigid-Plastic Finite-Element Analysis of Plastic Deformation in Metal-Forming Processes, Berkley: University of California. |
1. | Marek Hawryluk, Jan Marzec, Problems related to the operation of machines and devices for the production of ceramic roof tiles with a special consideration of the durability of tools for band extrusion, 2024, 25, 2083-3318, 10.1007/s43452-024-01106-1 |
Type of lubricant | Dp | Dk | Δ D/Dp (%) | Hp | Hk | Δ H/Hp (%) | μ | R (Error) (%) |
No lubricant | 40, 2 | 36.4 | 9.4 | 24 | 16 | 30 | 0.15 | 0.22 |
Teflon + graphite | 40.1 | 44.2 | 10 | 24 | 16 | 30 | 0.08 | 0.12 |
Machine oil | 40.2 | 40.8 | −1.5 | 24 | 16 | 30 | 0.07 | 0.09 |
Industrial grade petrolatum | 40.15 | 41.7 | −3.9 | 24 | 16 | 30 | 0.057 | 0.07 |
Magnesium stearate | 40.15 | 19.65 | 2.2 | 24 | 16 | 30 | 0.1 | 0.13 |
Type of lubricant | Dp | Dk | ΔD/Dp (%) | Hp | Hk | ΔH/Hp (%) | μ | R (Error) (%) |
No lubricant | 40.20 | 36.40 | 9.4 | 24 | 16 | 30 | 0.14 | 0.13 |
Teflon + graphite | 40.10 | 44.20 | 10 | 24 | 16 | 30 | 0.07 | 0.09 |
Machine oil | 40.20 | 40.80 | −1.5 | 24 | 16 | 30 | 0.06 | 0.07 |
Industrial grade petrolatum | 40.15 | 41.70 | −3.9 | 24 | 16 | 30 | 0.052 | 0.06 |
Magnesium stearate | 40.15 | 19.65 | 2.2 | 24 | 16 | 30 | 0.1 | 0.08 |
Base material | Inoculant | Test conditions | Properties | |||
T (℃) | έ (s−1) | σmax (MPa) | εcr | εlim | ||
filia | kaolin 2/4% | 22 | 0.01 | 0.128/0.136 | 0.38/0.39 | 1/1.05 |
filia | kaolin 8/24% | 22 | 0.01 | 0.209/0.507 | - | 0.8/0.9 |
filia | kaolin 10/28% + lanolin 2/5% | 22 | 0.01 | 0.182/0.505 | 0.91 | 0.95/1.05 |
filia | lanolin 6/14% | 22 | 0.01-0.1 | 0.083/0.095 | 0.03/0.29 | 1.2 |
filia | - | 22 | 0.01-0.1 | 0.13/0.17 | 0.3/0.41 | 0.9/1 |
filia | kaolin 16% | 22 | 0.01-0.1 | 0.385/0.47 | - | 0.8/0.95 |
filia | paraffin 5/10% | 22 | 0.01-0.1 | 0.176/0.356 | 0.03/0.09 | 0.9/1.05 |
filia | - | 17-22 | 0.01 | 0.13/0.18 | 0.3/0.36 | 0.9/1.1 |
filia | kaolin 20% | 18-24 | 0.01 | 0.41/0.46 | - | 0.8/0.9 |
plasticine | - | 22 | 0.01-0.1 | 0.37/0.416 | 0.17/0.2 | 0.9/1.05 |
plasticine | kaolin 2/20% | 22 | 0.01 | 0.386/0.51 | 0.19/0.32 | 0.8/0.95 |
plasticine | paraffin 5/10% | 22 | 0.01 | 0.323/0.38 | 0.21/0.29 | 0.85/1 |
plasticine | lanolin 5/10% | 22 | 0.01 | 0.12/0.17 | 0.11/0.14 | 0.9/1.05 |
plasticine | kaolin 15%, chalk 5%, paraffin 1% | 20-24 | 0.01 | 0.417/0.614 | 0.14/0.27 | 0.8/0.9 |
plasticine | kaolin 5%, chalk 5% | 20-24 | 0.01 | 0.3/0.42 | 0.19/0.22 | 0.8/0.9 |
Test | Bareling | Coefficient of friction (m) |
filia, έ = 0.01 s−1 | 0.0123 | 0.021 |
filia, έ = 0.05 s−1 | 0.0151 | 0.027 |
filia, έ = 0.1 s−1 | 0.0169 | 0.031 |
Type of lubricant | Dp | Dk | Δ D/Dp (%) | Hp | Hk | Δ H/Hp (%) | μ | R (Error) (%) |
No lubricant | 40, 2 | 36.4 | 9.4 | 24 | 16 | 30 | 0.15 | 0.22 |
Teflon + graphite | 40.1 | 44.2 | 10 | 24 | 16 | 30 | 0.08 | 0.12 |
Machine oil | 40.2 | 40.8 | −1.5 | 24 | 16 | 30 | 0.07 | 0.09 |
Industrial grade petrolatum | 40.15 | 41.7 | −3.9 | 24 | 16 | 30 | 0.057 | 0.07 |
Magnesium stearate | 40.15 | 19.65 | 2.2 | 24 | 16 | 30 | 0.1 | 0.13 |
Type of lubricant | Dp | Dk | ΔD/Dp (%) | Hp | Hk | ΔH/Hp (%) | μ | R (Error) (%) |
No lubricant | 40.20 | 36.40 | 9.4 | 24 | 16 | 30 | 0.14 | 0.13 |
Teflon + graphite | 40.10 | 44.20 | 10 | 24 | 16 | 30 | 0.07 | 0.09 |
Machine oil | 40.20 | 40.80 | −1.5 | 24 | 16 | 30 | 0.06 | 0.07 |
Industrial grade petrolatum | 40.15 | 41.70 | −3.9 | 24 | 16 | 30 | 0.052 | 0.06 |
Magnesium stearate | 40.15 | 19.65 | 2.2 | 24 | 16 | 30 | 0.1 | 0.08 |
Base material | Inoculant | Test conditions | Properties | |||
T (℃) | έ (s−1) | σmax (MPa) | εcr | εlim | ||
filia | kaolin 2/4% | 22 | 0.01 | 0.128/0.136 | 0.38/0.39 | 1/1.05 |
filia | kaolin 8/24% | 22 | 0.01 | 0.209/0.507 | - | 0.8/0.9 |
filia | kaolin 10/28% + lanolin 2/5% | 22 | 0.01 | 0.182/0.505 | 0.91 | 0.95/1.05 |
filia | lanolin 6/14% | 22 | 0.01-0.1 | 0.083/0.095 | 0.03/0.29 | 1.2 |
filia | - | 22 | 0.01-0.1 | 0.13/0.17 | 0.3/0.41 | 0.9/1 |
filia | kaolin 16% | 22 | 0.01-0.1 | 0.385/0.47 | - | 0.8/0.95 |
filia | paraffin 5/10% | 22 | 0.01-0.1 | 0.176/0.356 | 0.03/0.09 | 0.9/1.05 |
filia | - | 17-22 | 0.01 | 0.13/0.18 | 0.3/0.36 | 0.9/1.1 |
filia | kaolin 20% | 18-24 | 0.01 | 0.41/0.46 | - | 0.8/0.9 |
plasticine | - | 22 | 0.01-0.1 | 0.37/0.416 | 0.17/0.2 | 0.9/1.05 |
plasticine | kaolin 2/20% | 22 | 0.01 | 0.386/0.51 | 0.19/0.32 | 0.8/0.95 |
plasticine | paraffin 5/10% | 22 | 0.01 | 0.323/0.38 | 0.21/0.29 | 0.85/1 |
plasticine | lanolin 5/10% | 22 | 0.01 | 0.12/0.17 | 0.11/0.14 | 0.9/1.05 |
plasticine | kaolin 15%, chalk 5%, paraffin 1% | 20-24 | 0.01 | 0.417/0.614 | 0.14/0.27 | 0.8/0.9 |
plasticine | kaolin 5%, chalk 5% | 20-24 | 0.01 | 0.3/0.42 | 0.19/0.22 | 0.8/0.9 |
Test | Bareling | Coefficient of friction (m) |
filia, έ = 0.01 s−1 | 0.0123 | 0.021 |
filia, έ = 0.05 s−1 | 0.0151 | 0.027 |
filia, έ = 0.1 s−1 | 0.0169 | 0.031 |